摘要:对现有的一种离子注入机的铝合金腔体铸件进行铸造工艺设计,借助ADSTEFAN模拟软件对其充型过程和凝固过程进行了模拟与方案优化确认。通过修改浇注方式,可以明显改善初始工艺方案中的冲砂、卷气、夹杂等缺陷。通过合理设置冒口和冷铁,充分实现冒口的补缩作用,可望有效减少缩孔、缩松缺陷。
关键词:铝合金;腔体;方案设计;模拟优化
稿件编号:1512-1149
离子注入机是集成电路制造工序中的关键设备,用于对半导体表面附近区域进行离子掺杂工艺,可以满足浅结、低温和精确控制等要求,已成为集成电路制造工艺中必不可少的关键设备。通常由离子源、质量分析器、加速器、四级透镜、扫描系统、靶室和真空系统等部分组成。其原理是将所要注入的元素进行电离,并将正离子分离和加速,形成高能离子流,轰击工件表面,成为置换原子或晶格间的缝隙原子,使材料的化学成分、结构、性能产生变化[1]。靶上腔体作为高能量离子进行离子注入的场所,关系到离子注入工艺质量的好坏,因此要求腔体铸件具有高精度及高的真空密封性。基于对高质量铸件的需求,铸造生产环节就提出了对于铸造工艺方案优化设计的必然要求。
1 腔体铸件结构分析
腔体铸件的结构如图1所示,材料牌号为ZL114A。铸件轮廓尺寸为579×579×948(mm),铸件质量约119 kg,最小壁厚为16 mm,最大壁厚为38.5 mm。腔体主要呈左右轴对称状,顶面(如图1.b)为主要装配面,也是重要加工面,不允许有缩孔缩松、氧化夹杂等铸造缺陷存在。
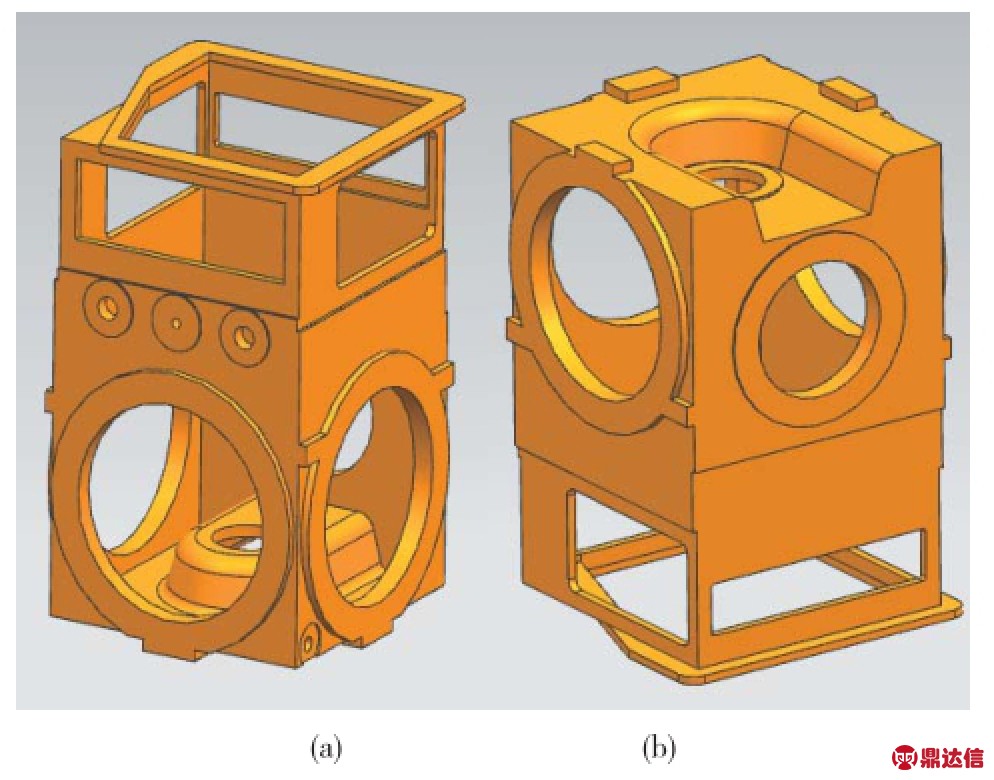
图1 腔体铸件的三维模型
2 铸造工艺设计及分析
铝合金质量轻,热熔小,导热快,极易氧化吸气;由于氧化物的密度近似于铝合金的密度,易引起夹杂;且凝固体收缩率较大,因此易产生缩孔、缩松[2]。该铝合金腔体铸件属于中大型铸件,壁较薄且高度较高,因此设计合理的浇注系统对铸件品质的保证非常重要。
本文采用砂型重力铸造,型砂选用树脂砂。根据腔体结构尺寸,采用一箱一件,手工造型的方式,机械加工余量取5 mm。考虑到顺序凝固原则及便于下芯操作[3],将腔体的大平面置于下部,选择大圆空腔的直径部位作为分型面,内浇道设置在分型面,如图2所示。

图2 分型面与浇注位置选择
浇注系统设计作为铸造工艺设计的重要组成部分,它的合理与否可直接决定铸造工艺设计水平。浇注系统是引导液态金属进入型腔的通道,它能保证铸型充满以及铸件凝固时的补缩。另外,还要保证液态金属流动平稳,不产生飞溅、冲击和紊流,且具防氧化,挡渣的能力,这一点对铝合金铸造尤为重要[4]。
针对铝合金的特性,采用开放式浇注系统,截面比选取为Σ A直∶Σ A横∶Σ A内=1∶4∶6。使用阻流截面设计法,根据奥赞公式[3]计算浇道最小截面积:

式中,Asmin为浇道最小截面积(cm2),GL为浇注所需金属液的总质量(kg),K为流量因数,范围为0.04~0.07,这里取0.06,HP为平均静压头(cm),浇注时间t采用公式(2):

式中,s′为流量系数,可算得,t=23.5 s。由此求出Asmin=15.3 cm2,即为直浇道的截面积。为增加水力学阻力,降低流速,减小紊流程度,初步考虑采用片状直浇道,片数为3。根据所选用的截面比,得到单个内浇道截面积为23 cm2,横浇道截面积为30.6 cm2。
将铸件三维模型导入ADSTEFAN软件中,通过划分网格、设置工艺参数等,进行数值模拟[5,6],设置浇注温度为720 ℃,树脂砂的温度为20 ℃,砂型与外界环境之间的热阻为2 500 s·cm2·K·J-1,铸件和砂型之间的热阻为25 s·cm2·K·J-1。 在无冒口情况下的缩孔预测情况如图3.a所示。针对易产生缩孔部位,在其上端或旁侧设置了相应的冒口进行补缩,如图3.b所示。其中4个顶冒口的尺寸为D=74 mm,h=100 mm,4个浇道侧暗冒口尺寸为D=106 mm,h=188.5 mm,2个中间暗冒口尺寸为D=50 mm, h=76.5 mm。
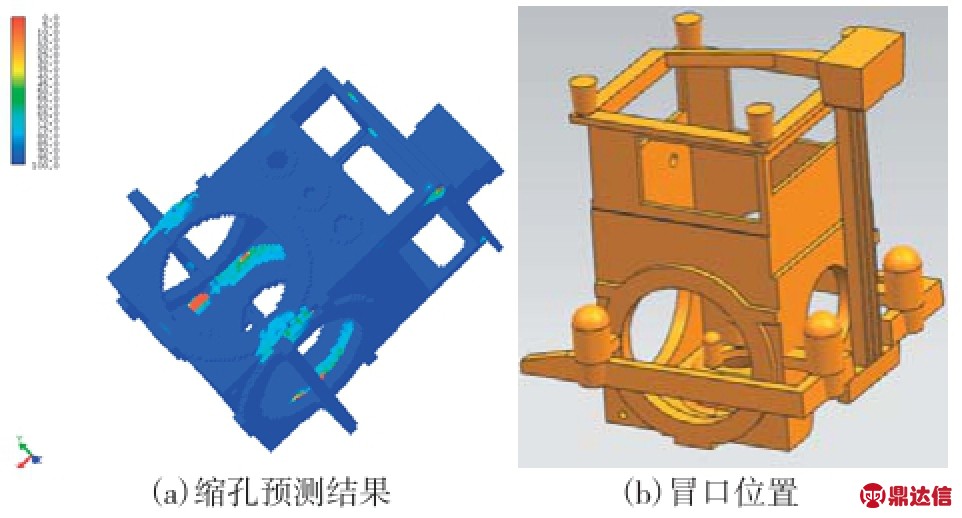
图3 参考初步缩孔预测结果设计的冒口方案
侧冒口体积较大,且离铸件较近,凝固过程中对铸件的热辐射作用将影响铸件的凝固顺序,因此在侧暗冒口上设置厚度为8 mm的保温套筒。
利用ADSTEFAN模拟软件对铸件的充型过程和凝固过程进行了计算机模拟,显示不同时间充型与排气状况的结果如图4和图5所示。
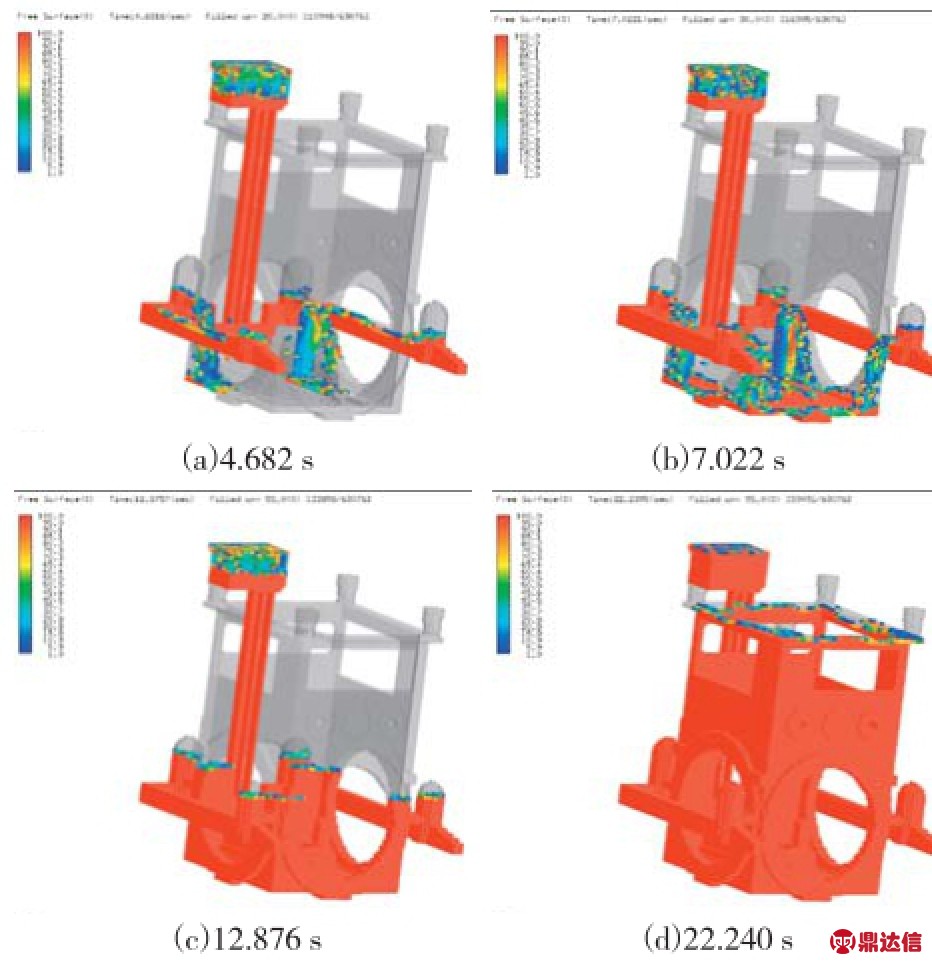
图4 初始方案的充型过程
由图4可见,离直浇道近的两个内浇道先开始充型。金属液沿着型壁向下流动冲刷,充填过程中容易造成冲砂。之后金属液自下而上充满型腔。从图5所示的排气过程可以看出,充型初期较不平稳,易造成卷气,从而引起氧化夹杂等缺陷的产生。
3 方案优化及分析
根据初始方案内浇道所存在的问题,金属液有较明显冲刷现象,易造成冲砂、卷气以及型腔内部的氧化夹杂,作者进行了多次改进与尝试,因篇幅所限无法一一叙述。
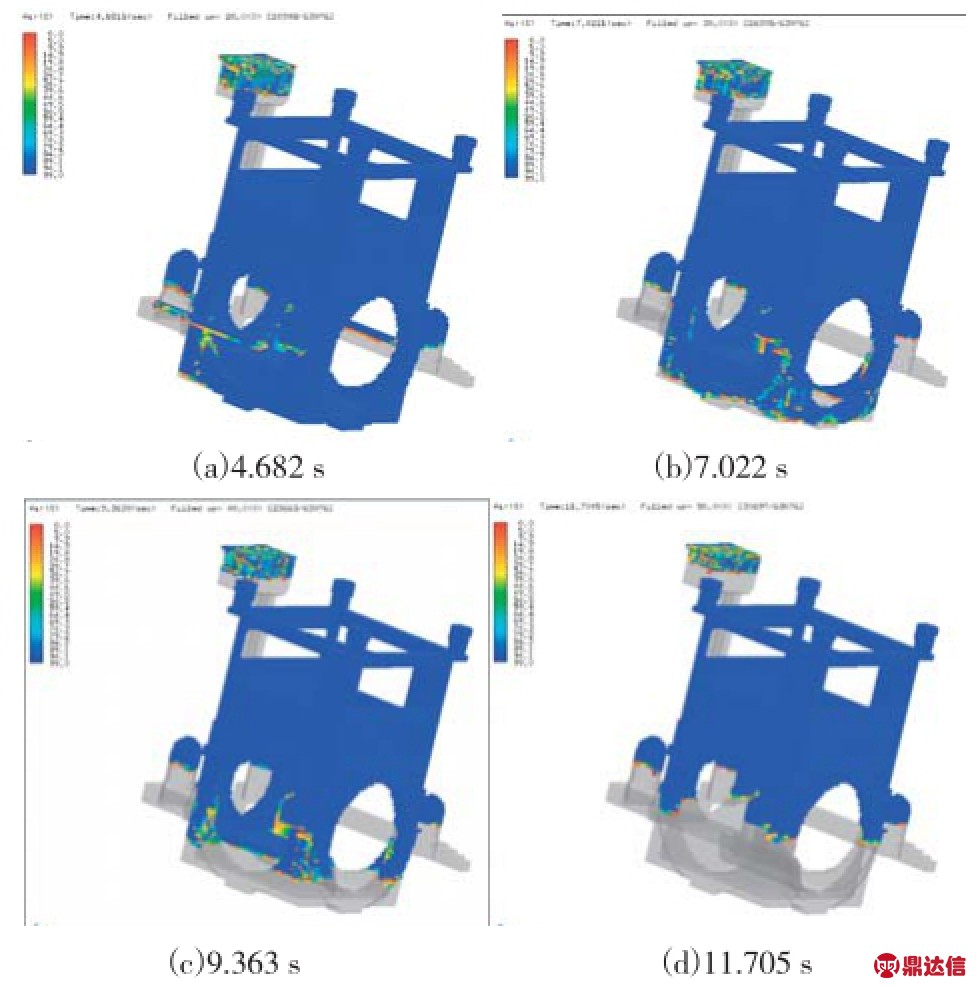
图5 初始方案的排气过程
考虑到浇注时的冲砂、卷气与中注式浇注方式有关,内浇道位置较高,金属液向下流动的时将对底部型砂造成冲击,且液面不平稳,易飞溅卷气,故将内浇口位置改为底注式,同时调整截面比为ΣA直∶ΣA横∶ΣA内=1∶2∶4,分型面的位置不变。考虑到后续拔模问题,浇注系统均采用尺寸为D内=50 mm,D外=62 mm的陶瓷管浇道,浇注位置如图6所示。
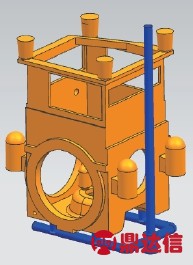
图6 优化后的浇注系统
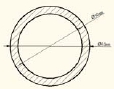
图7 陶瓷管浇道示意图
由于冒口的补缩距离有限,针对冒口难于补缩的部位设置冷铁,以加速个别热节的冷却,从而弥补冒口的不足[7]。冷铁分布如图8所示,在顶冒口和侧冒口之间设置两个L型冷铁,将有效帮助冒口实现分工补缩。
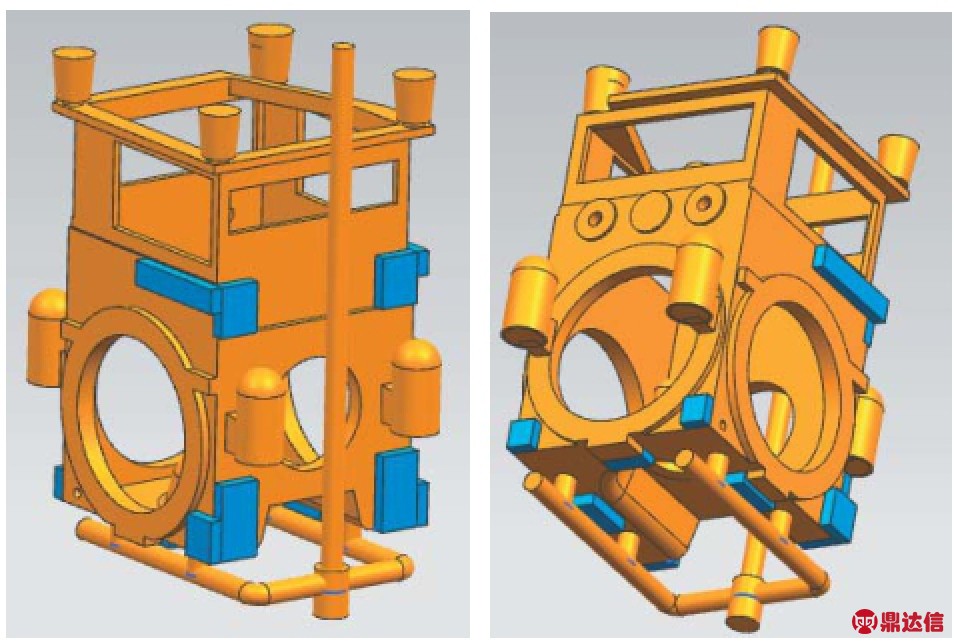
图8 冷铁分布示意图
根据砂芯设计原则,为简化砂芯结构,方便芯模设计制造,最终设计为一个整体的大砂芯,其余部分采用活块配合造出。芯盒采用木质芯盒,四周设有加强板,以增加芯盒强度。如图9所示。
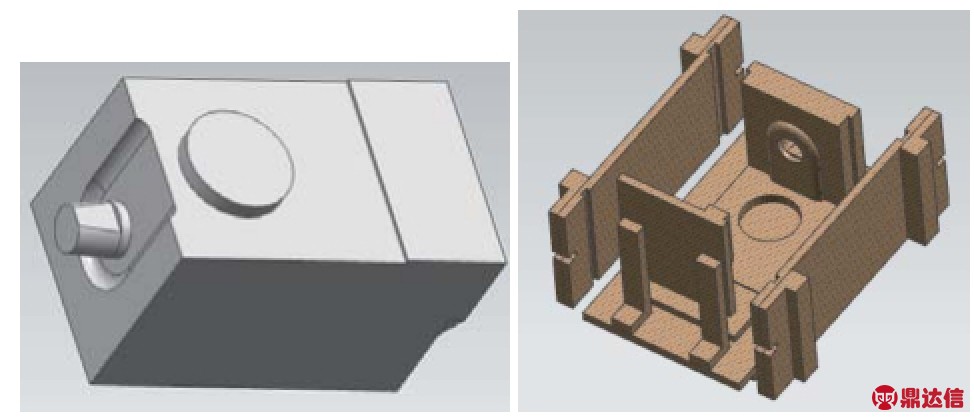
图9 砂芯及芯盒示意图
将优化后的铸件模型导入模拟软件,各工艺参数设置不变,求解结果如图10所示。可以看出金属液从底部内浇道充入型腔,再逐步自下而上依次充满型腔,充型过程非常平稳,型腔内气体顺畅排出,最大限度减少冲砂、卷气等缺陷的产生几率。
从图11的固相率分布图可以看出,冒口部位为最后凝固区域。铸件缩孔分布趋势的求解结果如图12所示,也表明缩孔产生于冒口之内。本方案所设计的冷铁和冒口均达到预期效果,故判断此方案为合理工艺,推荐作为企业的铸造生产工艺方案。
4 结束语
利用ADSTEFAN数值模拟软件对铝合金靶上腔体铸件的充型和凝固过程进行了模拟分析,并不断优化改进,寻求最佳工艺方案。通过调整浇注位置以及合理选择截面比,可确保充型过程平稳,有效避免了冲砂、卷气等缺陷。冒口和冷铁的配合使用,使铸件具有合理的凝固顺序,冒口为最后凝固部位,确认可充分发挥其补缩作用,避免了缩孔和缩松的产生,达到铸件工艺优化的要求。
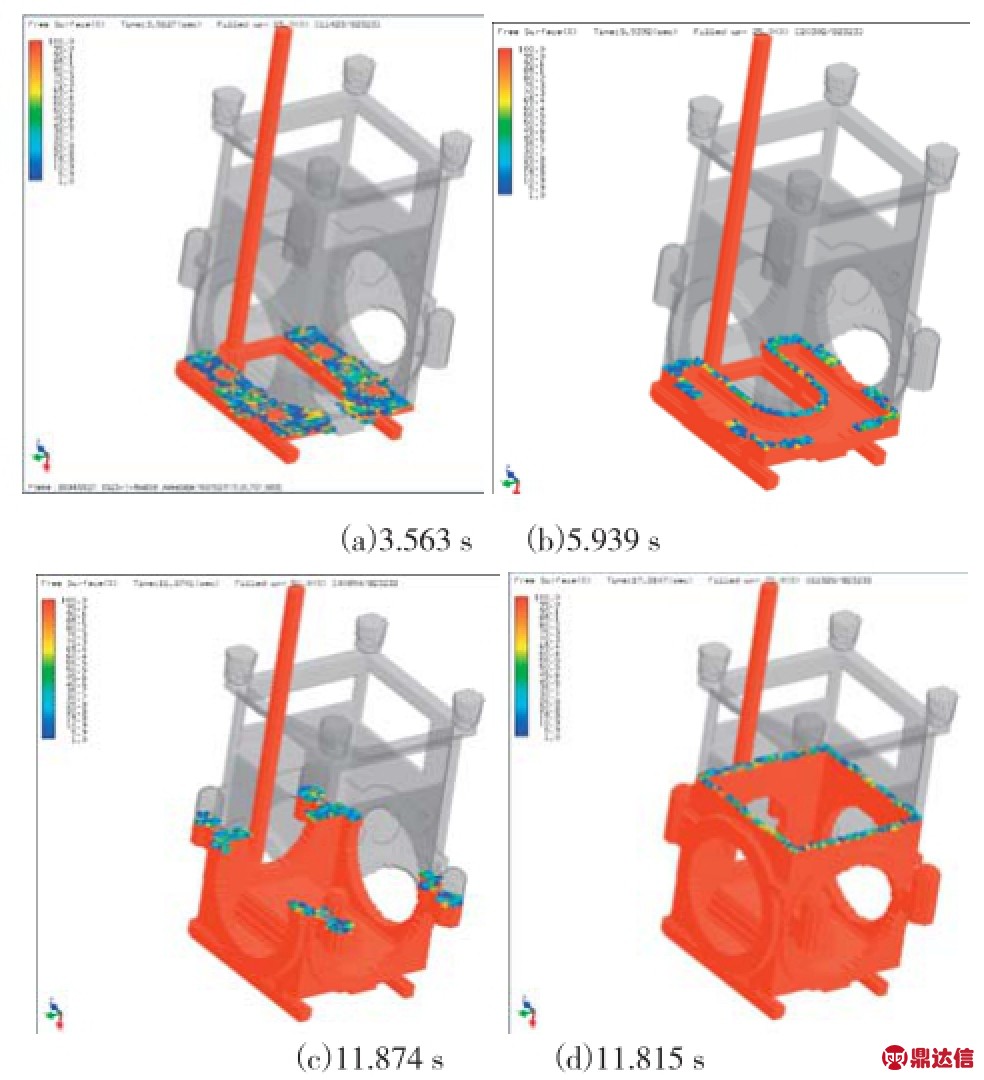
图10 改进方案充型过程
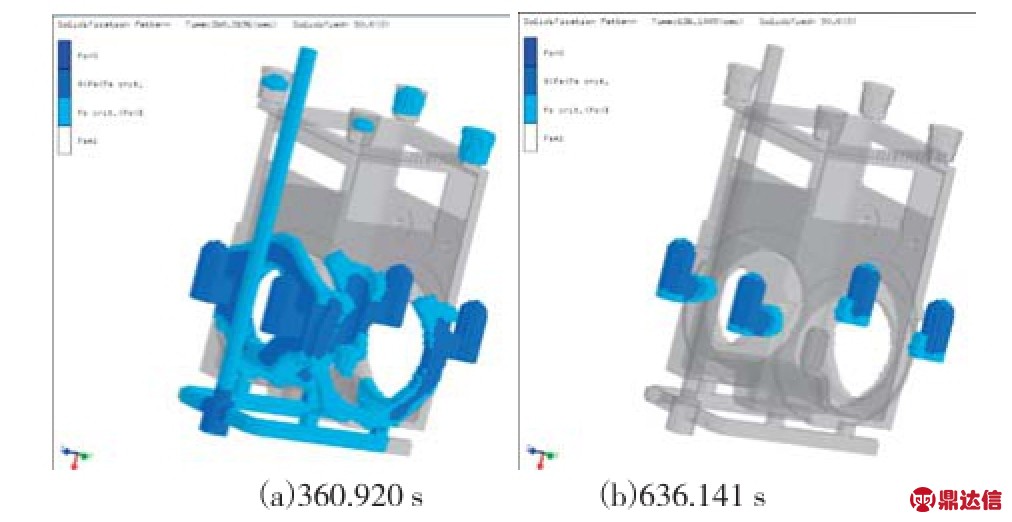
图11 固相率分布图
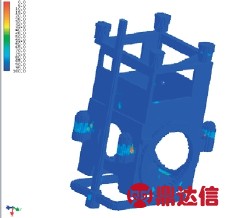
图12 缩孔分布图