摘要:传统设计中四立柱式平板硫化机上横梁大都采用铸铁材料铸造,通常都采用翻砂口上置式结构,这使得上横梁材料分布不合理,抗拉部位材料分布相对较少、承载能力较低,导致硫化机在工作中有时会出现上横梁翻砂口处断裂的现象。本文采用常规应力分析与ANSYS建模分析,针对上横梁分别用于下置式与上置式不同结构时,对比了其应力分布规律,结果表明:当利用好铸铁的抗压能力远远大于抗拉能力这一特性,将平板硫化机上横梁翻砂口由上置式改为下置式结构,能够有效地挖掘材料潜力、改善上横梁的受力,防止上横梁断裂。
关键词:平板硫化机;上横梁; ANSYS分析;翻沙口
四立柱式平板硫化机常用于加工橡胶、塑料制品,在橡塑行业中被广泛的使用着。四立柱式平板硫化机结构示意图如图1所示。
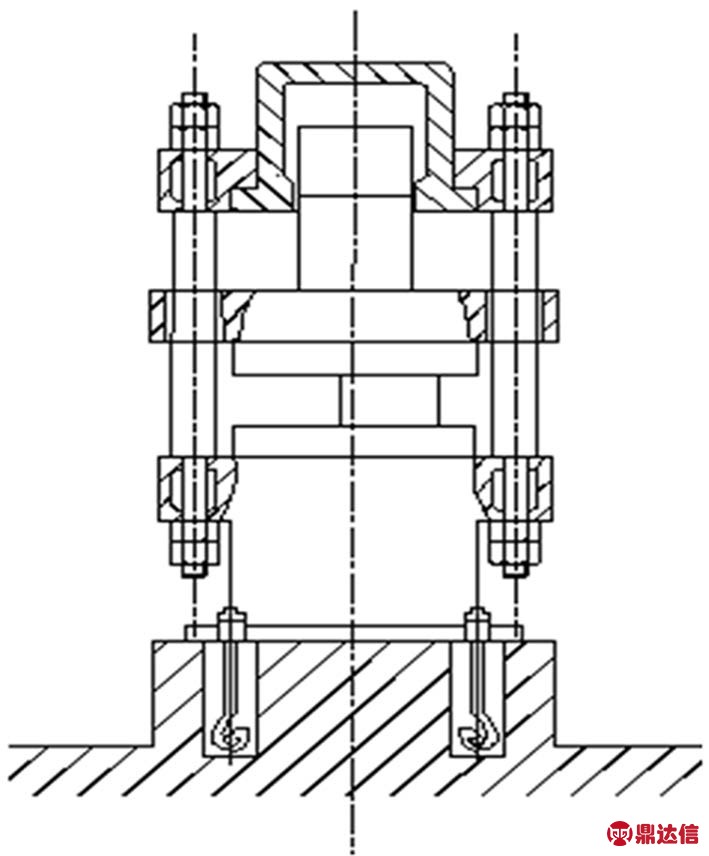
图1 四立柱式平板硫化机结构示意图
目前,工程中四立柱式平板硫化机上横梁多采用铸铁材料铸造,且通常采用翻砂口上置式结构[1],上横梁受拉位置材料分布少,结构设计不合理,导致了在工程使用中,有时会出现上横梁翻砂口处断裂现象。针对这一问题,本文采用了常规应力分析[2]和ANSYS建模分析[3],分别采用当上横梁翻砂口下置式与上置式不同结构状态下,分析了上横梁上、下端面危险位置处应力分布的规律,确认了平板硫化机上横梁翻砂口处断裂的原因所在,并对平板硫化机上横梁翻砂口的位置进行了优化设计,从而能有效地防止平板硫化机上横梁的断裂现象。
1 传统设计的不妥
在传统设计中,四立柱式平板硫化机的上横梁通常采用铸铁材料铸造,翻砂口呈如图2所示上置式结构,这种翻砂口上置式结构设计的不足之处在于:在平板硫化机工作中,立柱承受拉力,上横梁上端部位是受拉应力、下端部位是受压应力。传统上横梁翻砂口采用上置式结构,导致了上横梁上部受拉部位材料分布较少,受压部位材料分布较多,而铸铁材料的特性却是:材料的抗压能力远远大于抗拉能力,因此传统设计上横梁翻砂口上置式结构设计造成材料分配不合理,这是导致平板硫化机底上横梁断裂的现象的原因。所以传统设计既浪费材料,承载能力也低[4]。
2 上横梁结构改进设计
针对传统设计中四立柱式平板硫化机的上横梁翻砂口位置不合理,见图2,本文将上横梁铸造结构的翻砂口改为下置式,充分挖掘材料潜力,利用了铸铁材料抗压能力远远大于抗拉能力的特点,合理地设置铸铁翻砂口下置式位置,同时翻砂口下置式结构也能保证上横梁上端面平整美观度需求。
改进后的四立柱式平板硫化机上横梁翻砂口下置式结构如图3所示。
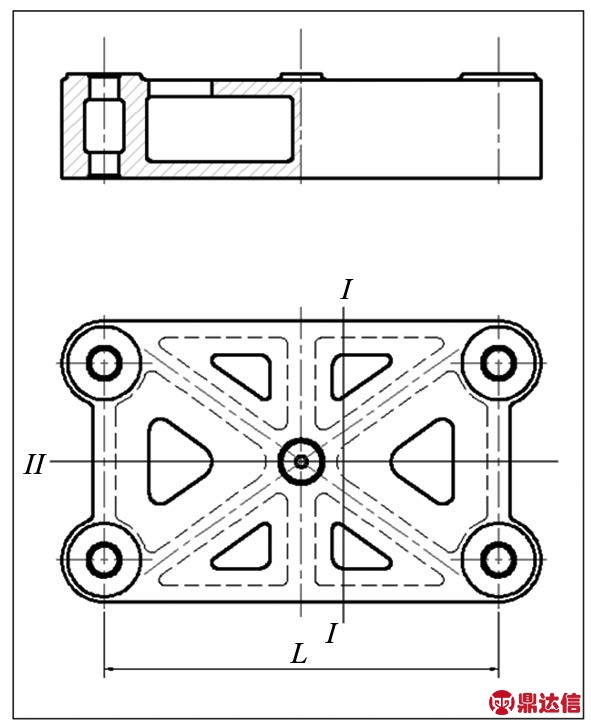
图2 传统上横梁结构示意图

图3 改进后上横梁结构示意图
3 上横梁危险点常规应力分析
在做上横梁的受力分析时,目前教科书及工程设计通常是将上横梁看作一个自由放置在两支点上、受均布载荷的简支梁[1],液压缸内压力经制品或模具作用于上热板,间接作用于上横梁下端面。沿中心线截面上受弯曲应力最大,危险断面取位于板中部加强筋的边缘,即图2所示的I-I断面。此处的弯矩较大、抗弯模量最小,该位置的上端面抗拉应力最大。当采用翻砂口上置式时,导致了该处的抗弯能力最薄弱。由于上横梁通常采用铸铁材料制造,材料的抗压强度是抗拉强度的3~4倍,故用最大拉伸强度理论,仅对上横梁的最大拉伸应力进行计算分析,并略去纵向的剪切应力τ校核。
上横梁受力力学模型示意图如图4所示。
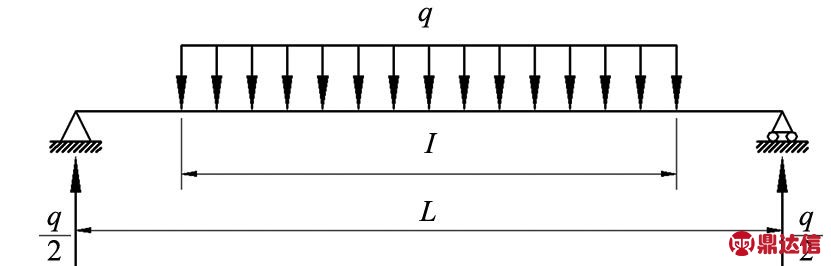
图4 上横梁受力力学模型示意图
参照图2所示翻砂口上置式四立柱平板硫化机,传统设计的翻砂口上置式四立柱平板硫化机上横梁危险截面断面形状如图5所示,改进后的翻砂口下置式上横梁截面断面形状如图6所示,两断面仅翻砂口位置不同,形状、尺寸相同。
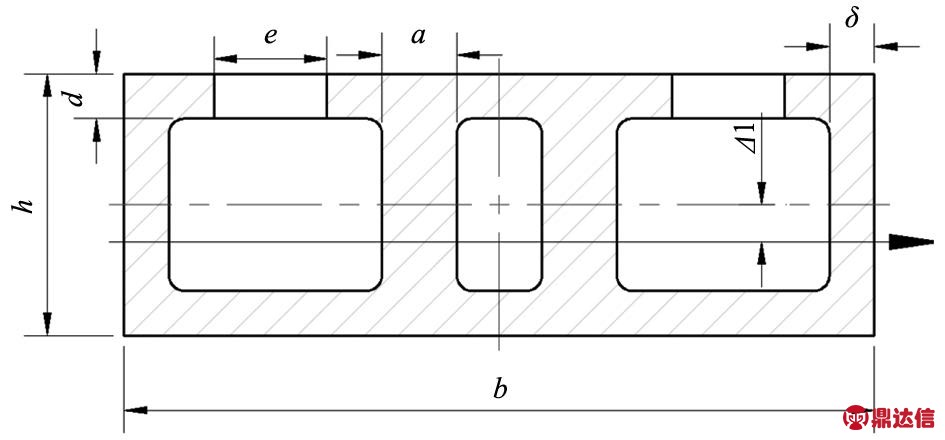
图5 翻砂口上置式I-I断面几何示意图

图6 翻砂口下置式I-I断面几何示意图
图5中的箭头线为截面中性层位置,图中所标注符号含义为: δ—上横梁铸造壁厚;h—上横梁高度;d—上横梁宽度;f—上横梁上下板厚;e—翻砂口开口尺寸;a—加强筋在断面处的厚度;Δ1—翻砂口上置式的中性层偏离无翻砂口时的中性层距离;Δ2—翻砂口下置式的中性层偏离无翻砂口时的中性层距离;
危险点I-I断面位置的上端最大弯矩有。

式中:l—热板的长度,即均布载荷的分布长度;
P—热板对上横梁低端的压力;
q —热板对上横梁压力与上横梁长度的比值,q=;
L—立柱之间的距离。
危险截面I-I断面最大应力(拉伸应力)有:

式中: MImax—I-I断面的弯矩;
Iz—危险截面对中性轴的惯性矩;
ymax—危险截面受拉部分到中性层的最远距离。
I-I断面的强度条件:

式中:[δt]—材料许用拉应力。
针对图5、图6不同结构,I-I断面最大弯曲应力(拉伸应力)计算如下:
(1)上横梁翻砂口上置,I-I断面如图5所示,断面的面积:

以I-I横向对称轴为y轴,以断面高处的横轴为z轴建立坐标系,则断面对z轴的静矩为:

由于h>b ,所以Szl<0 。
翻砂口上置式的中性层偏离无翻砂口时的中性层距离:

翻砂口上置式断面I-I断面对中性层的惯性矩:
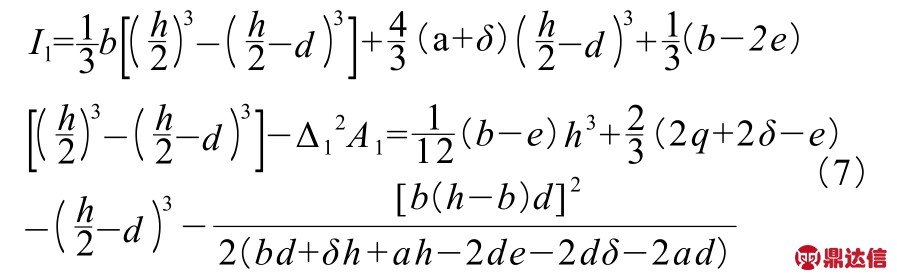
上横梁翻砂口上置,拉伸应力在断面上边缘,最大拉伸应力为:

(2)上横梁翻砂口下置,I-I断面如图5所示,由于其断面与上置式的形状尺寸相同,所以其断面的面积为:

上横梁翻砂口下置,I-I断面对z轴的静矩为:

易知Sz2>0。
翻砂口下置式的中性层偏离无翻砂口时的中性层距离:

翻砂口下置式断面I-I断面对中性层的惯性矩:
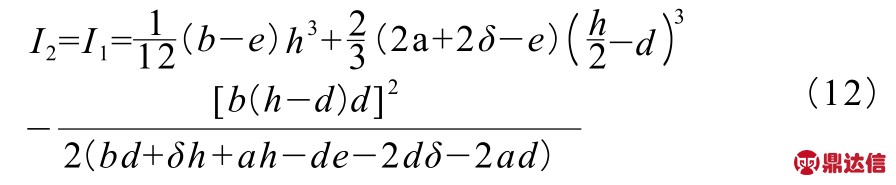
上横梁翻砂口下置,拉伸应力在断面下边缘,最大拉伸应力为:

比较式(8)和式(13),因为两个断面形状尺寸相同I1=I2, Δ1=Δ2, 所以有δtmax1>δtmax2。
综上所述,得出如下结论:图2所示翻砂口上置式结构,I-I截面上端位置处的材料相对分布少、弯曲应力最大,铸铁材料的抗拉能力又弱,上横梁容易被拉断;图3所示翻砂口下置式,I-I截面上端位置处的材料相对分布相对多、弯曲应力相对最小,上横梁不易被拉断,这与工程实际相吻合。
对于上横梁翻砂口下置式结构,虽然I-I截面下端位置处分布的材料少,压应力相对比较大,但是由于铸铁材料的抗压能力远远大于抗拉能力,所以I-I截面下端不会产生破坏,当设计的翻砂口尺寸合适,能够实现上、下端强度相近。
4 上横梁危险位置ANSYS软件应力分析
采用ANSYS软件分别对传统设计中翻砂口上置式和改进设计中翻砂口下置式两种情况进行建模和应力分析。
(1)传统设计的上横梁采用翻砂口上置式结构,将图2进行上横梁的ANSYS建模,其建造的简化模型如图7所示。上端面到四角圆面受向下的压力,下端面由热板提供一均布载荷,受均布载荷的面积小于下端面。对简化模型进行应力分析,得到危险断面的模拟拉应力分布如图8所示。依据图中下部的横条,显示出断面下端面至中性层处受压力,且压力由下向上逐渐变小;中性层至上端面受拉力,且拉力由下向上逐渐增大,在上端面达到最大值,因此而得出最大拉应力就在翻砂口开口处,加之该处的材料抗拉能力弱,该处容易被拉断。
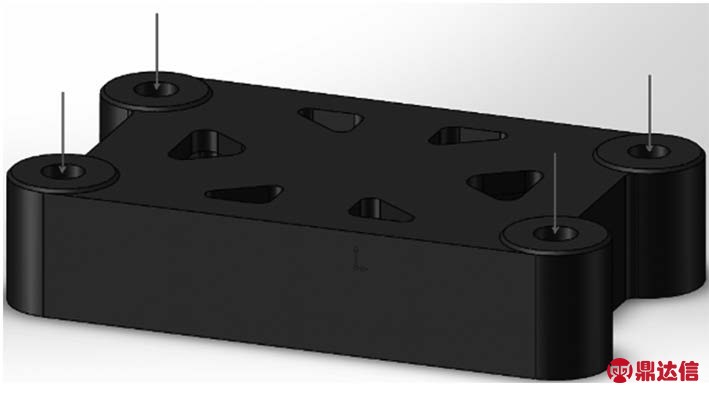
图7 上置式上横梁的简化模型
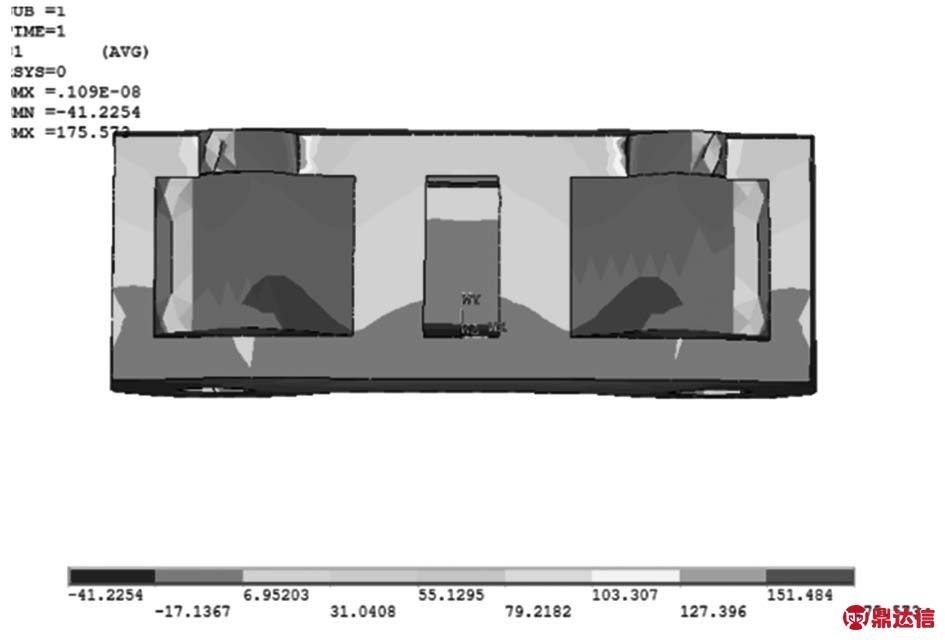
图8 上置式I-I断面的应力图
(2)改进设计的上横梁采用翻砂口下置式结构,将图3进行上横梁的ANSYS建模,其建造的简化模型如图9所示。上端面到四角圆面受向下的压力,下端面由热板提供一均布载荷,受均布载荷的面积小于下端面。对简化模型进行应力分析,得到的I-I断面的模拟应力分布如图10所示,依据图中下部的横条,显示出断面下端面至中性层处受压力,且压力由下向上逐渐变小;中性层至上端面受拉力,且拉力由下向上逐渐增大,在上端面达到最大值,可以清晰的显示出断面的上受压应力,所以该处不是危险点,不易被拉断。
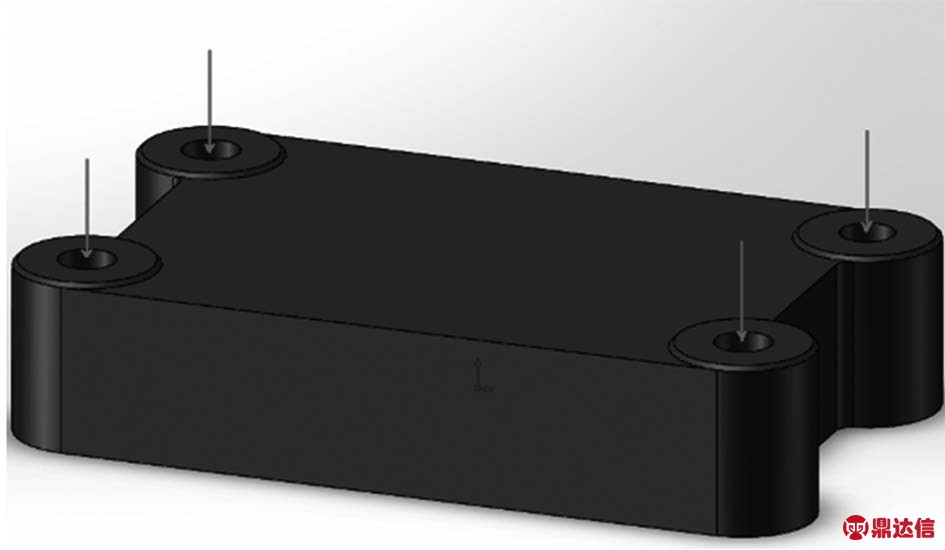
图9 下置式上横梁的简化模型
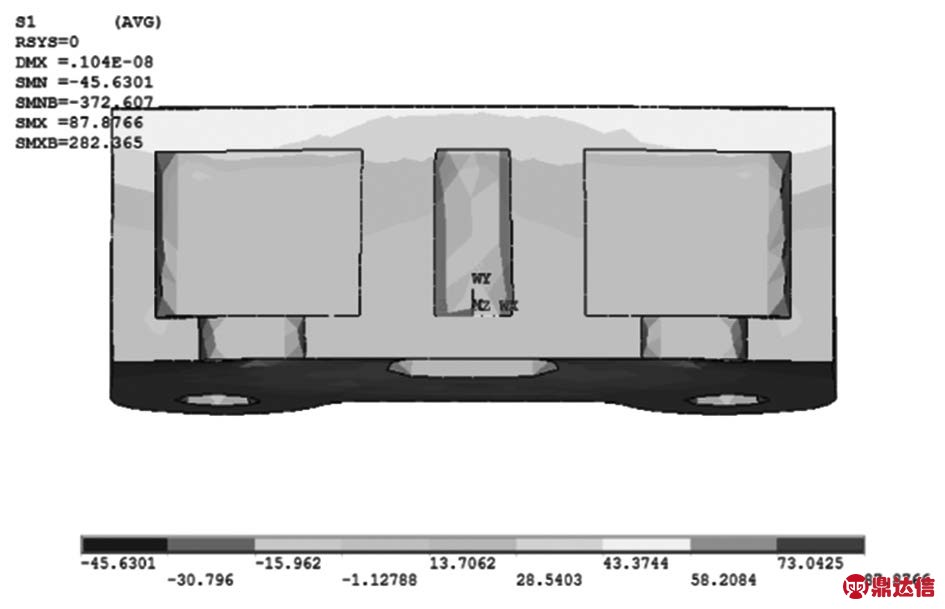
图10 下置式I-I断面的应力图
(3)对比图8和图10,在图8中可以看到,针对传统设计翻砂口上置式结构,上横梁模型的下端所受的压应力较小,但是铸铁材料的许用压应力值[δ]却很大,材料没有得到充分利用;但是在上端,翻砂口周围的拉应力较大,而铸铁材料的许用拉应力值[δ]却很小,所以上横梁结构设计不合理。
在图10中可以看到,针对传统设计翻砂口下置式结构,模型的下部翻砂口周围的压应力较大,但是铸铁材料的许用压应力值[δ]也大,上横梁上部铸铁材料的许用拉应力值[δ]较小,但是对应的拉伸应力也较小,故其结构设计合理。
笔者将上述设计理论应用于工程实际,对某生产平板硫化机企业的产品进行了结构改进[5],仅仅将平板硫化机上横梁的翻砂口由上置式改为下置式,就能很好的挖掘铸铁材料的潜力,避免了硫化机上横梁经常被拉断的现象,收到了极佳的效果。
5 结论
(1)如果上横梁采用铸铁材料,上横梁翻砂口上置式设计,材料分布不合理,结构设计不妥当,上横梁上端翻砂口处应力大、易被拉断;
(2)上横梁翻砂口下置式设计,能提高材料利用率,提高抗拉能力和承载能力,能有效地避免上横梁的断裂现象;
(3)采用上横梁翻砂口下置式设计,上横梁上端为平面结构,美观度更佳;
(4)如果上横梁翻砂口采用下置式,可将翻砂口用马口铁封闭,不影响外观。