摘要: 高速列车依靠多组驱动系统的持续运行维持其高速运行,带驱动系统的车辆会表现出不同的动力学特性。在牵引工况下,驱动系统的轮轨粘着特性曲线表现出先升后降的趋势。采用Polach轮轨接触算法,首先建立单轮对驱动系统模型,定性分析了驱动系统的扭转振动特性。然后建立带驱动系统的整车动力学模型,将仿真结果与实验数据对比,验证建立模型的正确性。研究结果表明:在牵引工况下,纵向蠕滑率为负;制动工况下,纵向蠕滑率为正;横向蠕滑率也有一定程度的波动;在牵引和制动工况下磨耗功相比匀速时增大,制动工况比牵引工况增大40%。考虑驱动系统模型转向架其蛇形运动频率低于未考虑驱动系统模型,稳定性有所提高;由于驱动系统的振动引起轮轨系统的振动响应波动,采用考虑驱动装置的车辆模型安全性指标相比未考虑驱动系统模型均有所增大,两种模型平稳性指标两个模型区别不大。
关键词: 高速列车; 轮轨接触; 粘着系数; 驱动系统; 模型验证
引 言
驱动系统是高速列车的重要组成部分,列车的牵引离不开驱动系统的作用。车辆在牵引过程中主要是由于轮轨之间的粘着作用来实现的。在牵引工况下,由于轮轨粘着系数的非线性特性,高速列车在驱动力的作用下会发生扭转自激振动。考虑了驱动系统的车辆系统其动力学特性和拖车也会有所区别。
国内外专家对车辆动力学及传动系统动力学特性已展开相关研究工作。黄伟[1]建立了考虑驱动系统的高速车辆模型,分析了粘滑振动稳定性;姚远[2]建立了考虑驱动系统的机车模型,并分析了粘着状态下其动力学特性,详细分析了粘着曲线各区段的扭转振动特性。Polach[3]在Kallker的基础上改进了Fastsim算法,并使其适合于牵引工况下的切向力计算方法,并与实测数据对比,证明了其方法的有效性。翟婉明[4]建立了机车-轨道耦合动力学模型,并分析了机车牵引电机刚性悬挂和弹性悬挂对轨道的作用。姚远等[5]建立了机车单轮对驱动系统模型,分析了传动系统和纵向振动的耦合特性,结果表明:由于轮轨粘着系数的负斜率,传动系统的扭转振动与轮对的纵向振动为不稳定的自激振动,两者与轮对运行速度和轴重有关,速度越大,轴重越小,振动越稳定,传动系统的扭转与轮对的纵向阻尼能很好抑制这种自激振动。因此,日本学者Hirotsu T等[6]建立了机车-万向轴传动装置模型,研究了在电力机车打滑时驱动系统的自激振动,并与试验进行对比,提出了抑制机车自激振动的措施。罗赟等[7]研究了悬挂结构参数对动力学的影响,并指出牵引驱动装置质量和悬挂横向刚度的变化对刚性架悬式机车的影响比较大,对弹性架悬式机车的影响较小。金鼎昌等[8]研究牵引电机轴悬、架悬、全体悬和半体悬等不同悬挂方式对机车动力学性能的影响。赵怀耘[9]建立了驱动系统的扭转自激振动模型,并结合车辆轨道耦合垂向模型,分析了扭转自激振动对于车辆和轨道的影响。同时计算了电机谐波转矩对车辆动力学的影响。扭转自激振动对纵向动力学影响较大,对横向动力学影响较小。王自超[9]建立完整的考虑齿轮传动系统的空间耦合动力学模型,并通过与传统未考虑齿轮传动系统的重载机车多体动力学模型进行对比,揭示齿轮传动系统对重载机车动力学性能的影响。CHEN等[11]在机车-轨道垂向耦合动力学模型的基础上,加入了驱动系统模型,考虑了轨道不平顺、轮轨非线性接触和齿轮啮合时变刚度等多种激励,其研究结果表明,考虑传动系统对于车辆轨道耦合系统中的各部件有着不同程度的影响,同时啮合刚度对动力学的影响也较大。Chen等[12]在建立了含有齿轮传动系统的机车-轨道垂向耦合动力学模型的基础上,分析了在牵引工况下的动力学特性,并与实验数据对比验证了模型的有效性。黄冠华等[13] 利用有限元方法得到高速列车齿轮传动系统时变啮合刚度,利用傅里叶级数模拟啮合刚度和传动误差,用多项式拟合齿侧间隙,建立考虑时变啮合刚度、传动误差与齿侧间隙等多种非线性因素的高速列车齿轮传动系统弯扭耦合动力学模型。
本文在采用Polach轮轨接触算法,首先建立单轮对驱动系统简化模型,分析了不同粘着系数下的动力学特性。随后建立CRH3高速动车组车辆多体动力学模型,考虑完整的齿轮传动系统的影响,该模型能够实现牵引力矩通过齿轮啮合传递至轮对,进而驱动车辆运行的动态仿真分析;通过与试验结果对比,验证建立的动力学模型的正确性;同时,基于建立的动力学模型,分析齿轮传动系统对车辆动态性能的影响。本文研究工作对更加真实地研究车辆动力学性能具有较好的参考价值。
1 牵引工况滚动接触算法
Polach基于Hertz假设,假定轮轨接触斑为椭圆形状,计算摩擦系数时引入了与滑动速度相关的系数,使得Polach算法同时具有FASTSIM算法的计算速度快和CONTACT精度高的特点,对于实现轮轨接触快速计算具有良好的效果,因此可作为FASTSIM的替代算法[4]。
两接触面内的切向力可表示为
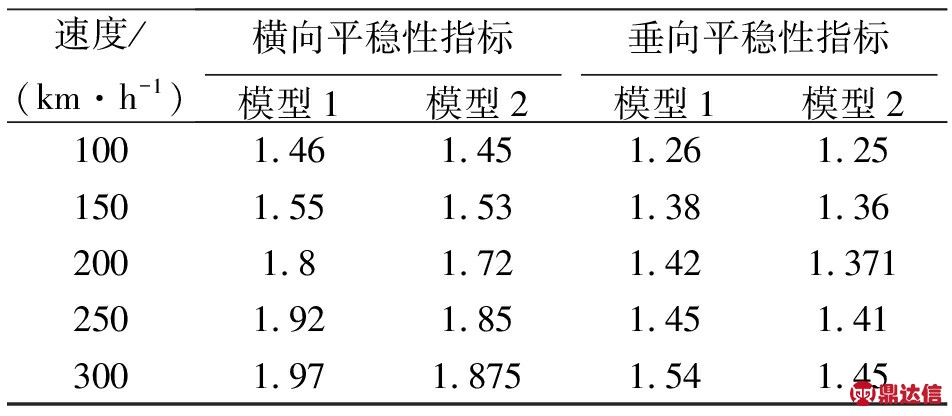
(1)
式中 Area为接触斑的接触面积。通过将椭圆上的分布力转化到半球面上的分布力,求出总切向力。
Polach滚动接触理论首先引入了与滑动速度相关的摩擦系数计算模型
μ=μ0[(1-A)e-Bv+A]
(2)
式中 μ0为滑动速度为0时的最大摩擦系数,A为滑动速度无穷大时对应的摩擦系数μ∞与最大摩擦系数μ0之比,B为摩擦力衰减系数,常数A,B由实验确定。
v为总的相对滑动速度大小
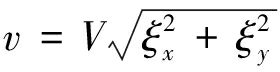
(3)
式中 ξx为纵向蠕滑速度,ξy为横向蠕滑速度。
合成的蠕滑力大小由下式计算

(4)
式中 kA,kS分别表示Kalker系数在粘着区和滑动区内的衰减因子。其中0<kS≤kA≤1,kA,kS的值可以通过实验确定。
最后通过计算可得:

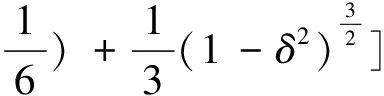
(5)
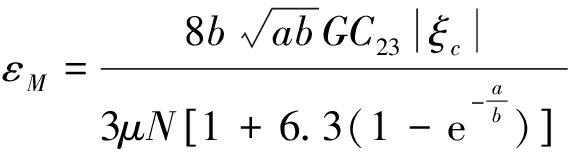
(6)
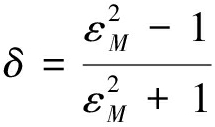
(7)
自旋蠕滑力矩可采用Kalker线性公式并加以修正得到,表示为

(8)
式中 μ为摩擦系数;a为接触斑长轴; b为接触斑短轴; N为法向力; C23,C32,C33为蠕滑系数; G为剪切弹性模数。
图1,2给出了不同的A值和B值下的粘着特性曲线。可以看出参数B对粘着特性曲线影响较小,参数A影响较大,在大蠕滑下,参数B对粘着系数影响较大。
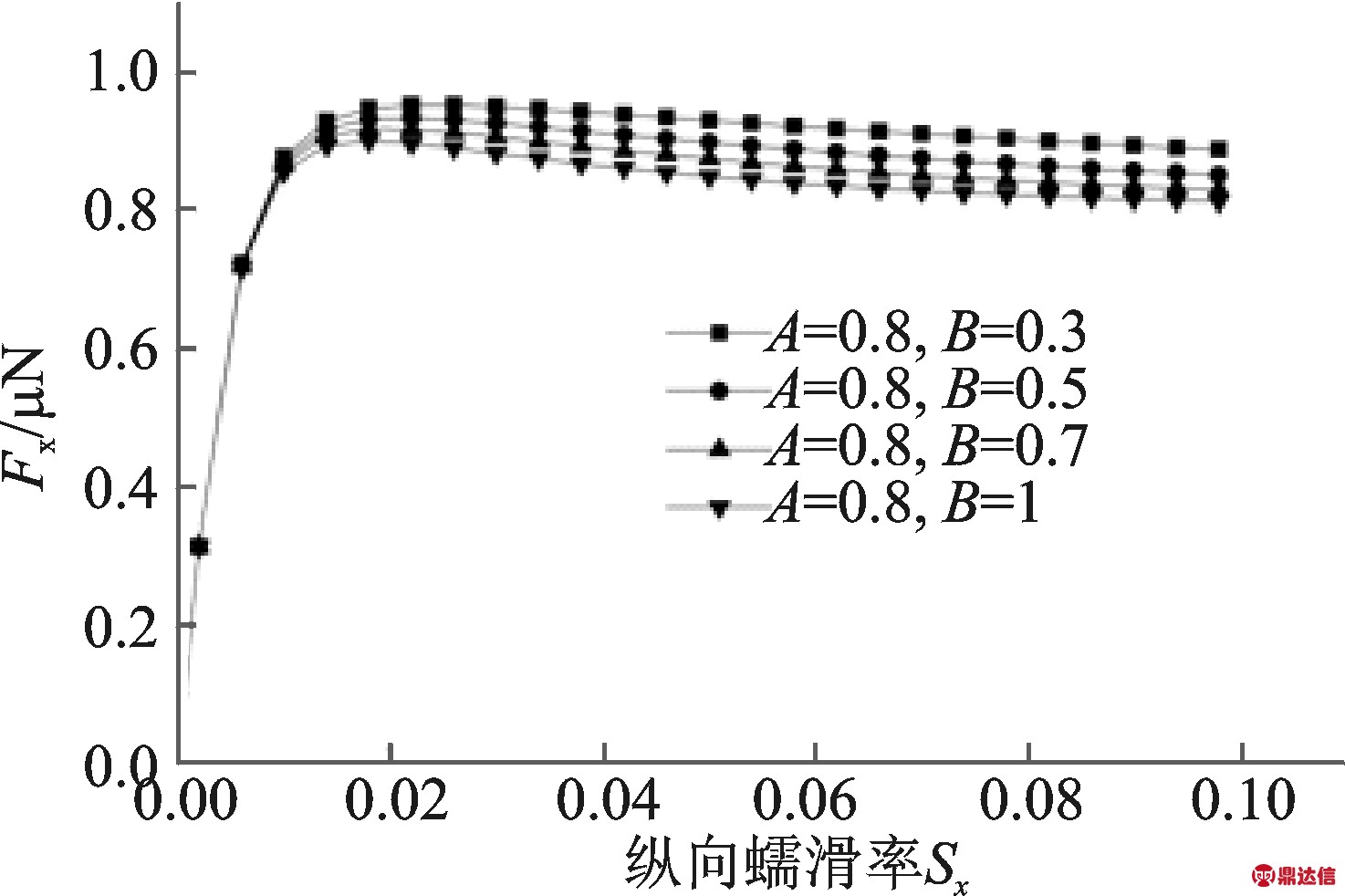
图1 不同B值对粘着特性曲线的影响
Fig.1 The influence of different B values on the adhesion characteristic curve
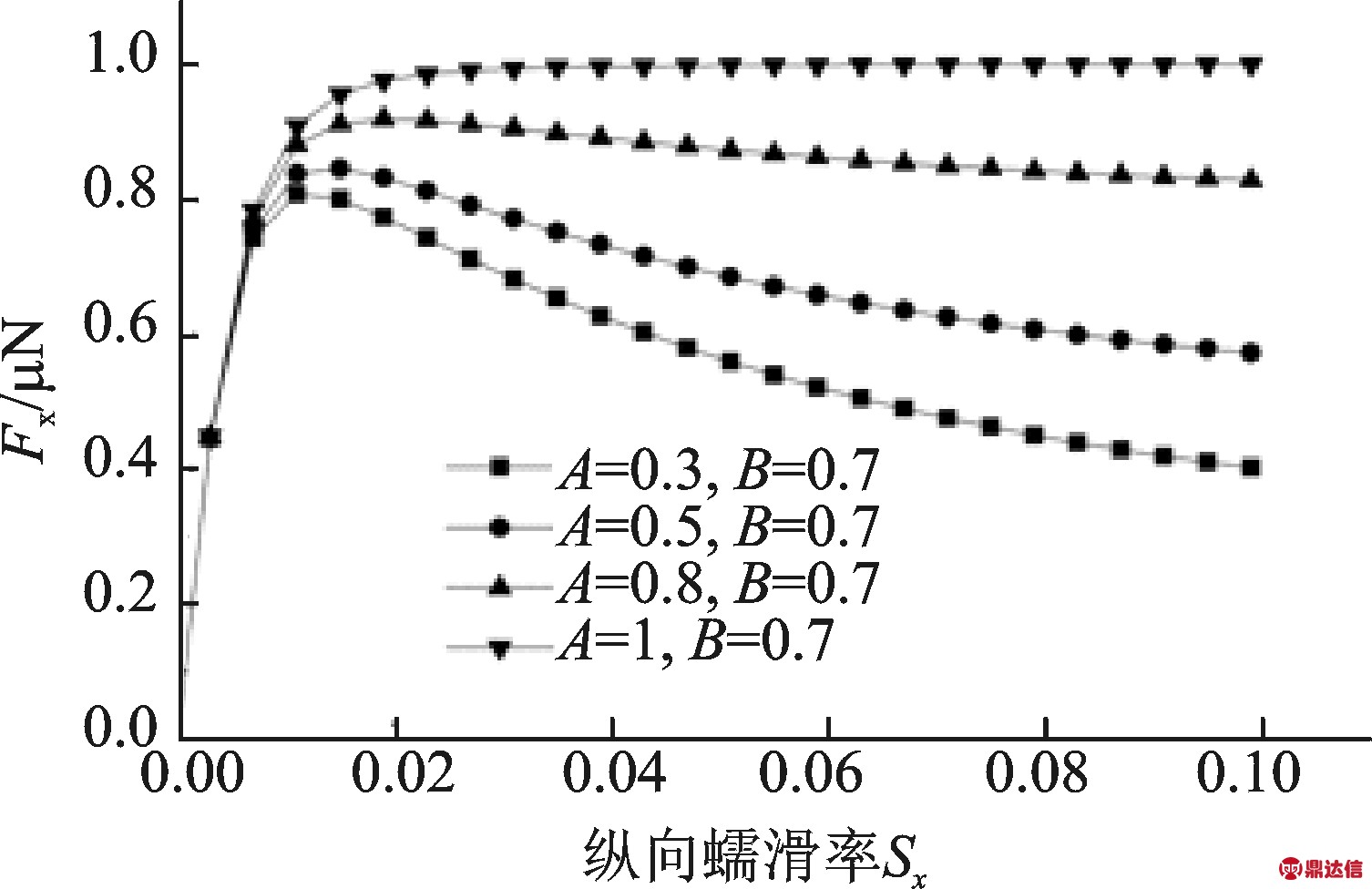
图2 不同A值对粘着特性曲线的影响
Fig.2 The influence of different A values on the adhesion characteristic curve
2 高速列车单轮对驱动系统建模
建立单轮对驱动系统模型,考虑轮对扭转弹性,将驱动轴上的牵引电机转子、小齿轮以及从动轴上的大齿轮的转动惯量一起等效到轮轴上,等效力矩作用在驱动系统上,粘着力矩作用于车轮上,考虑了驱动系统和轮对之间的等效刚度和阻尼,模型示意图如图3所示。
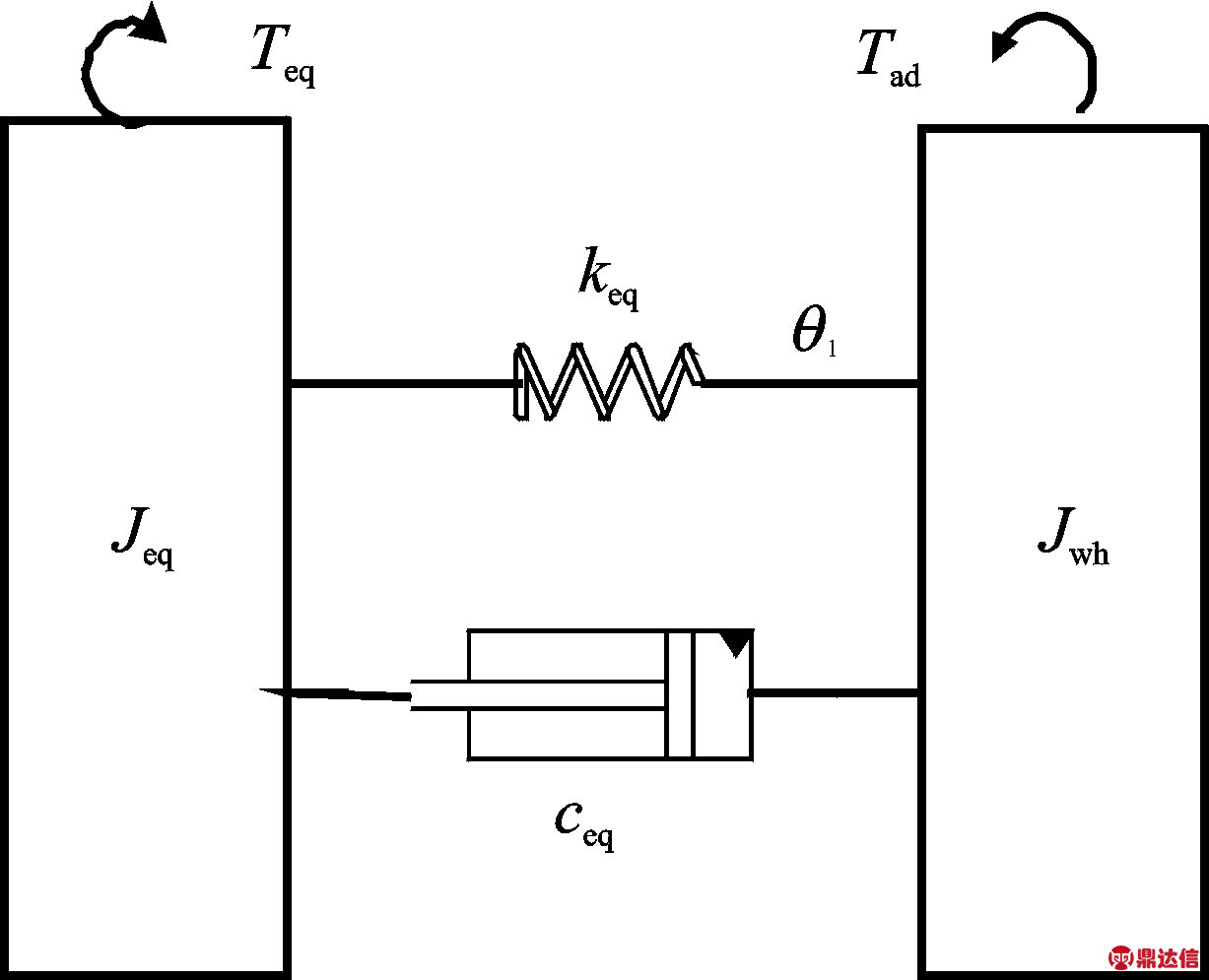
图3 单轮对驱动系统模型
Fig.3 Model of single wheelset with drive system
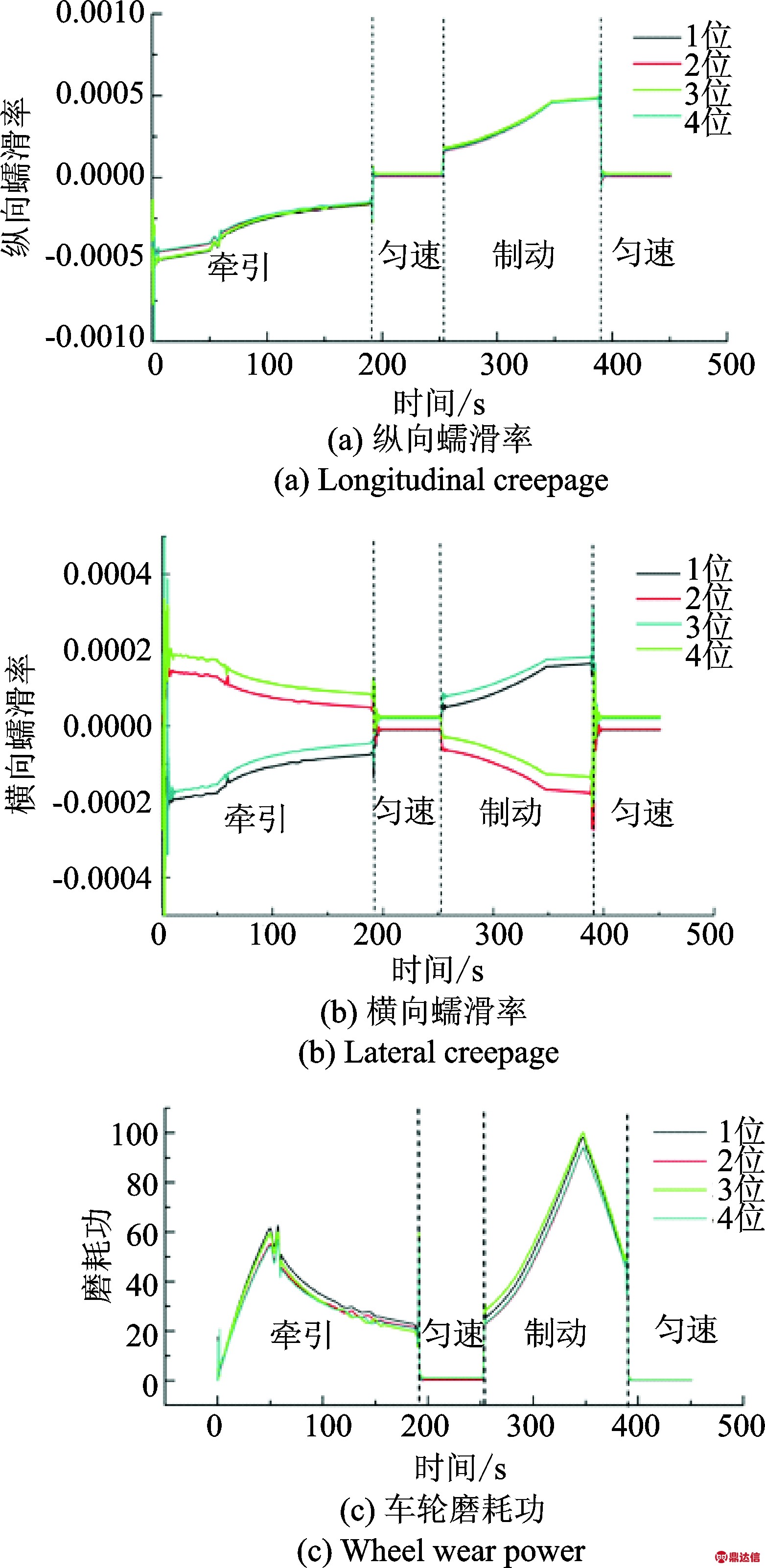
(9)
式中 Jeq为电机等效转动惯量;Jwh为轮对等效转动惯量;θwh为电机扭转角;θeq为轮对扭转角;Teq为等效转矩;Tad为粘着力矩;ceq为电机和轮对之间的等效扭转阻尼;keq为电机和轮对之间的等效扭转刚度。
驱动系统的自激振动主要是由电机和轮对的相对扭转振动引起的,现将其相对扭转角作为研究参数。
令Δθ=θwh-θeq
(10)
则可将式(8)转化为

(11)
式中 C=ceq(1+Jwh/Jeq),K=keq(1+Jwh/Jeq),
C为名义阻尼,K为名义刚度,Rg为传动比。Tm为牵引电机扭矩。
假设电机输出的扭矩是稳定的,令
Θ=Δθ-Δθ0
(12)
则运动方程可以转化为

(13)
定义等效阻尼力为

(14)
若定义平衡状态时稳定蠕滑速度为vslip_0,则瞬时蠕滑速度为
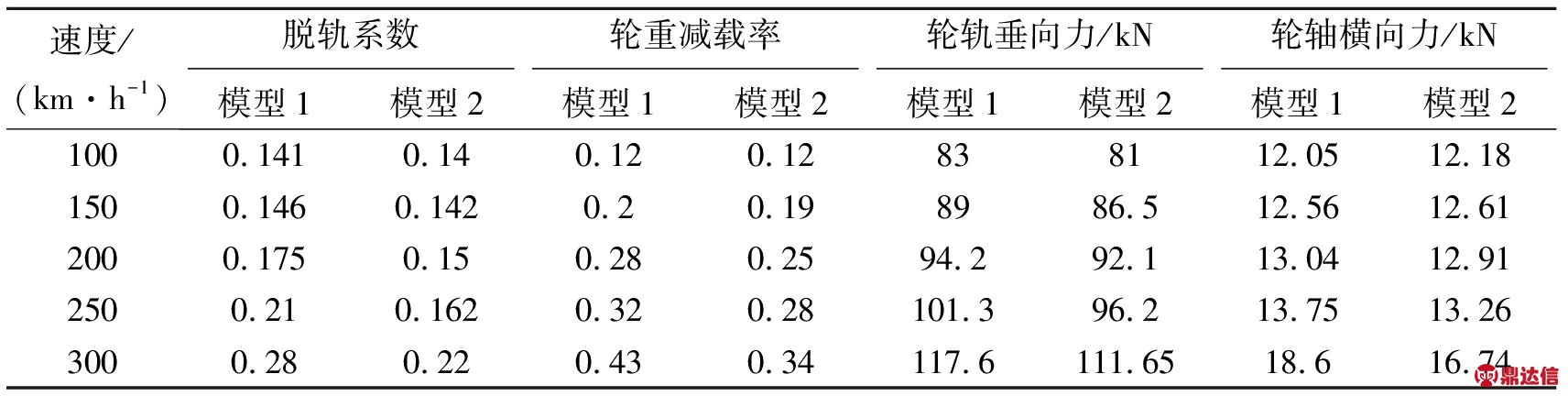
(15)
Tad0-Tad=Mgrwh[μ(vslip_0)-μ(vslip)]
(16)
由此可以得到轮轨粘着力矩Tad和Tad0的计算公式为
Tad0-Tad=Mgrwh[μ(vslip_0)-μ(vslip)]
(17)
Tad0为平衡状态下的轮轨粘着力矩,M为轮对质量, rwh为车轮半径。
图4,5给出了不同蠕滑速度下的扭转角时域响应和相轨迹图。从图中可以看出,转矩比较小时,vslip_0<vm时驱动系统的扭转振动是稳定的,当激励取消后,系统逐渐趋于稳定,其相轨迹为最后趋于原点,此时驱动系统并未发生自激振动,最终归于稳定状态。当电机扭矩增大时,蠕滑速度不断增大,由稳定状态变化为非稳定状态,扭转角逐渐增大,并稳定于一个值。其相轨迹趋向于一条封闭曲线极限环。这说明系统存在自激振动,高速列车驱动系统发生了扭转自激振动。
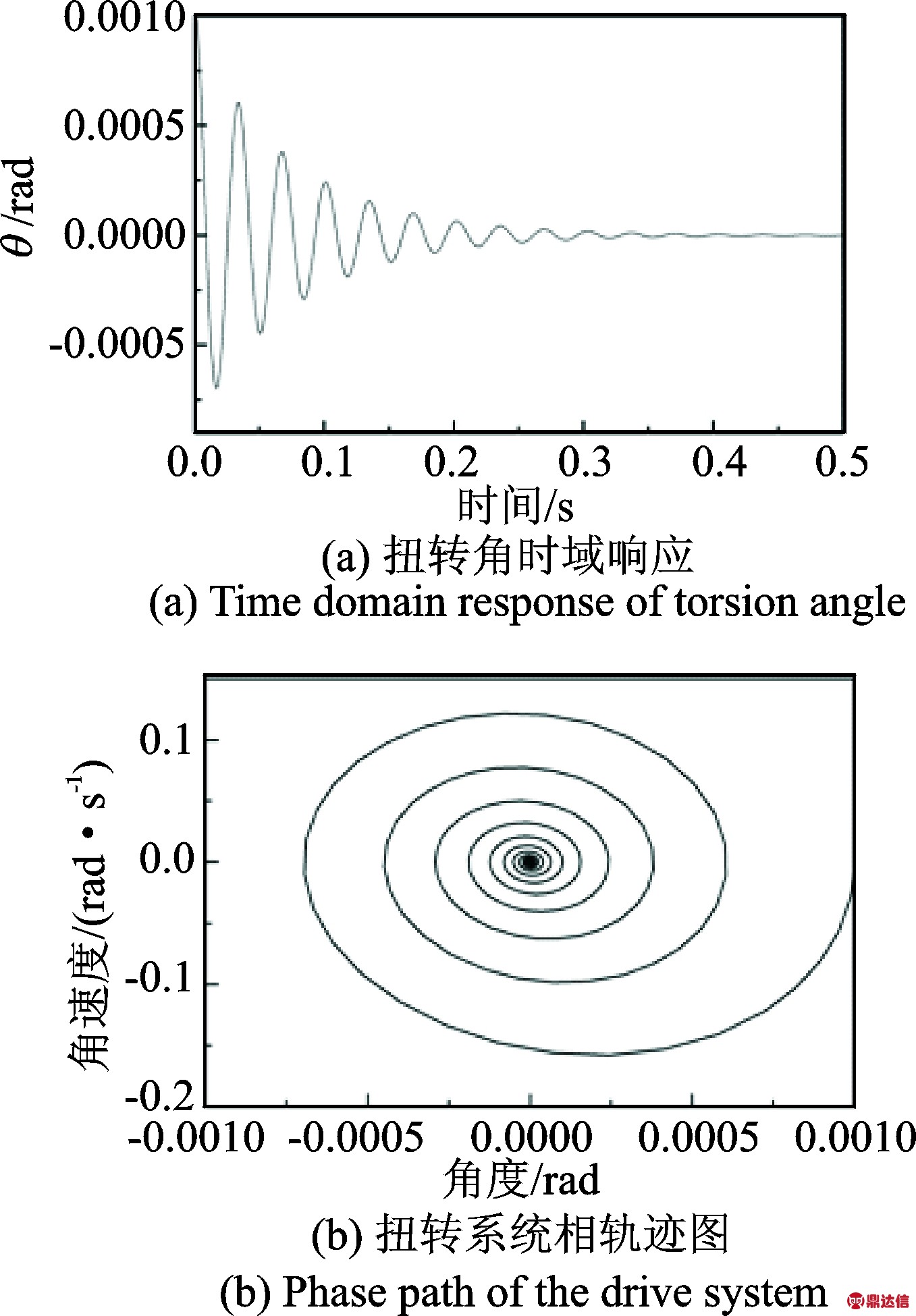
图4 当vslip_0<vm时的时域响应和相轨迹图
Fig.4 Time domain response and phase path when vslip_0<vm
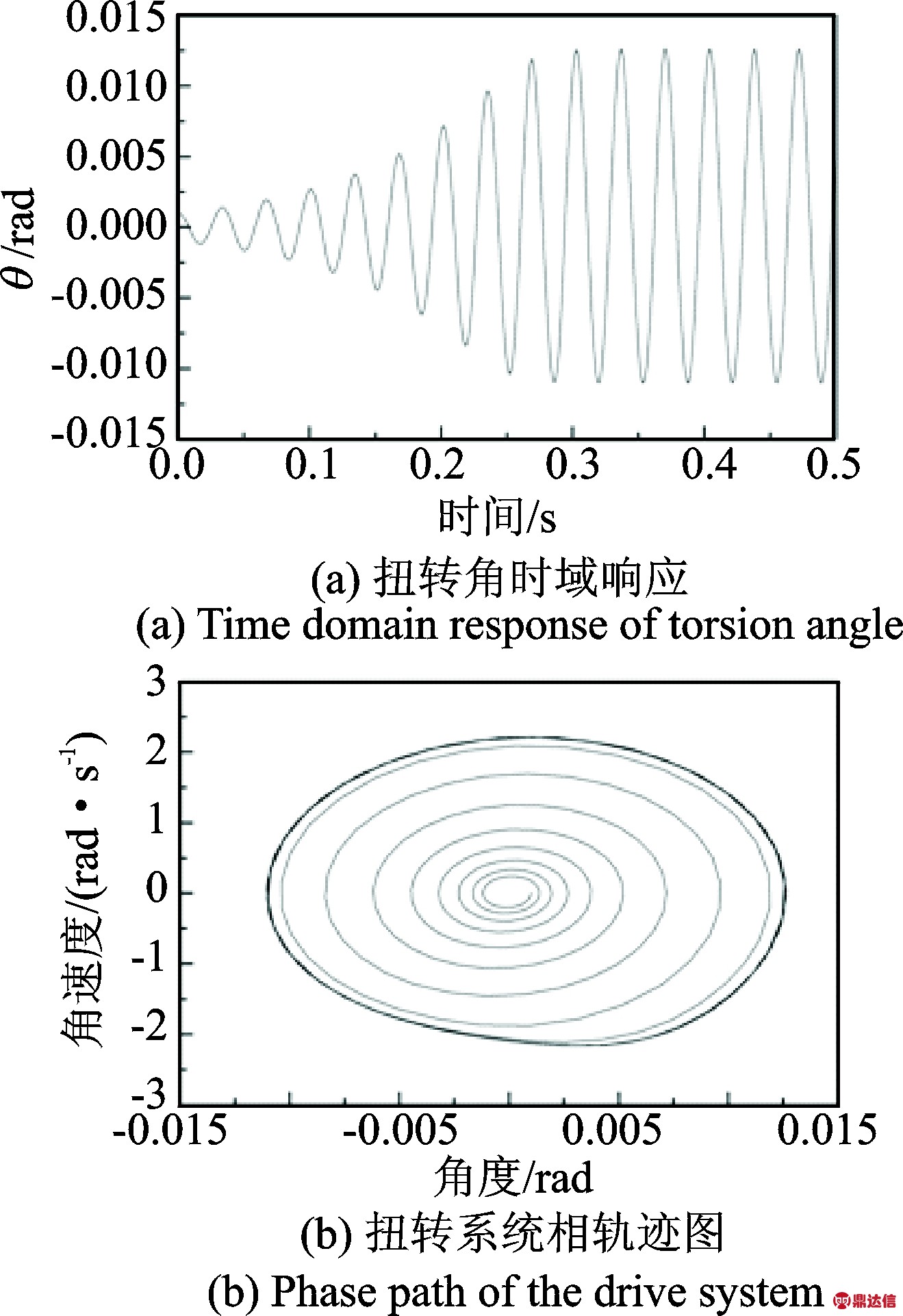
图5 当vslip_0>vm时的时域响应和相轨迹图
Fig.5 Time domain response and phase path when vslip_0>vm
3 考虑驱动系统整车模型建立
驱动装置由齿轮箱、联轴节、安全装置和牵引电机等组成,齿轮箱安装在动力轴上通过联轴节与电机连接,在齿轮箱下部与构架间设有一个两端带有弹性橡胶垫的C型托架(也称反应杆),齿轮装置的一端在车轴的滚动轴承中运动,另一端通过C型托架(反应杆)悬挂在转向架构架上。CRH3动车组的牵引电机通过具有横向弹性的电机吊架及圆销安装在构架的电机吊座上。
建立CRH3高速动车组车辆模型,轴重为17 t,当8节编组时牵引功率为8800 kW,为了仿真牵引工况和制动工况下的车辆动力学响应,故建立了包含驱动系统的车辆模型,其中包括了电机、联轴节、小齿轮、大齿轮、齿轮箱体,如图 6(a)所示,其中轮对、构架、车体、电机考虑了6个自由度,轴箱、齿轮箱、大齿轮、小齿轮和转子考虑1个自由度,具体如表1所示。转矩作用在电机转子上,通过驱动系统将力矩传递至轮对,牵引车辆前行。在多体动力学软件simpack中建立整车动力学模型,在仿真过程中选用武广谱。文中在仿真齿轮啮合力时采用的是225号力元,该力元通过齿面上的柔性穿透量和接触刚度计算轮齿间的啮合力,计算时考虑了齿与齿啮合间的库仑摩擦以及接触时的法向阻尼,同时该力元对齿轮中心距和旋转轴的位置变化,齿廓修形方面也可进行研究。为了建立更加贴合实际的模型,本文采用该力元进行建模,图6(b)是建立的考虑驱动系统的整车动力学模型。
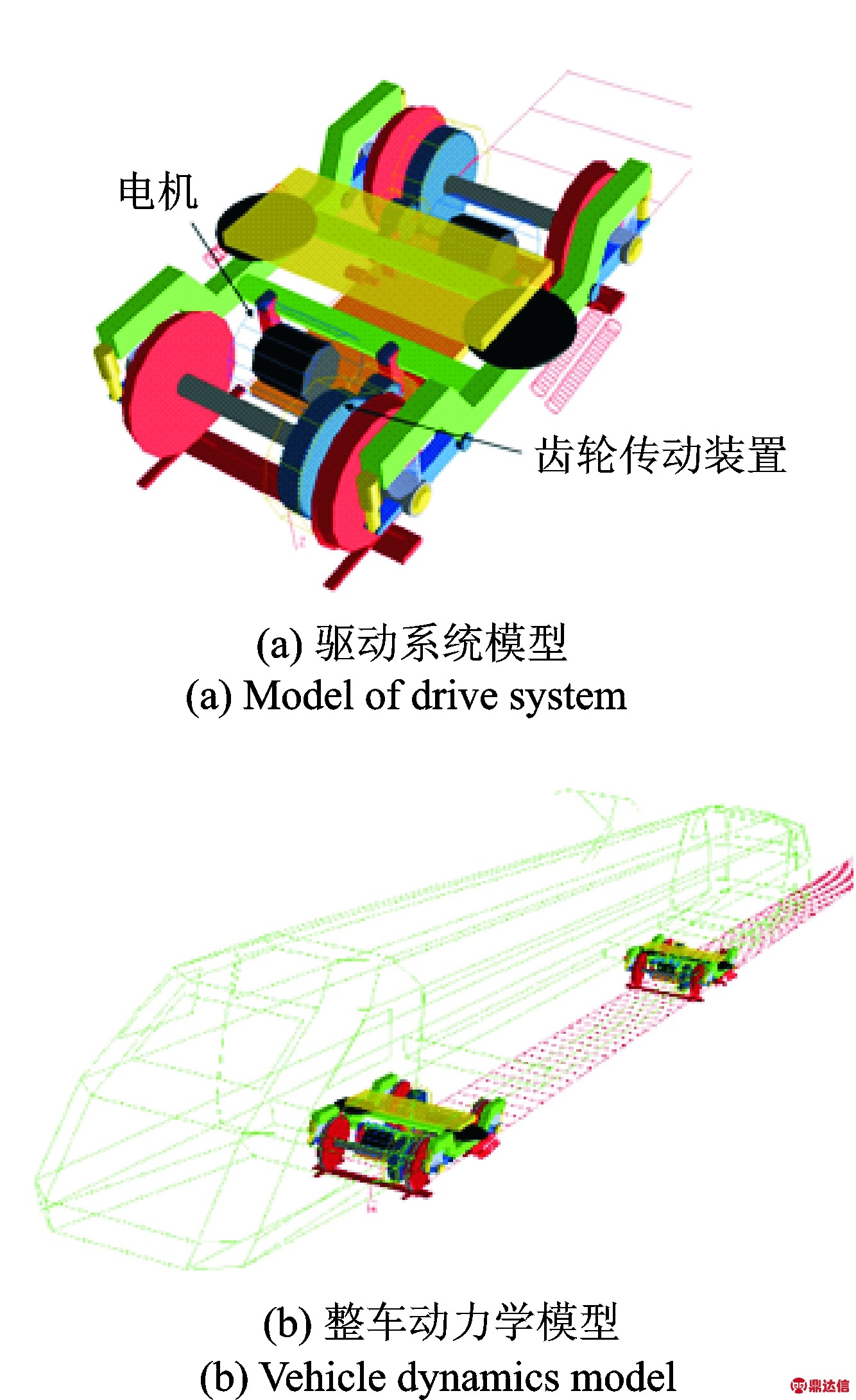
图6 动力学模型
Fig.6 Dynamic model
表1 考虑传动系统的车辆系统自由度
Tab.1 Freedom degree of the vehicle system consideration of the transmission system
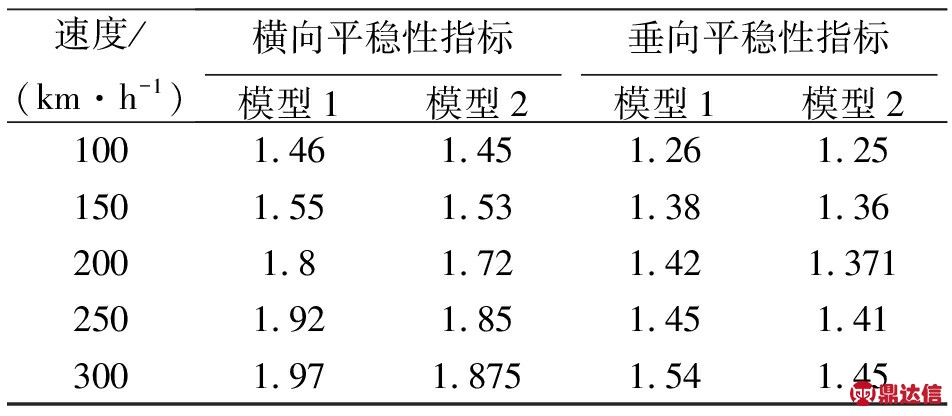
注:i=1-4,j=1-8,k=1-2,角标*表示非独立自由度。
为了使动力学模型最大程度地反映高速列车运行状况,需要对其可靠性进行试验验证。本节利用前面考虑驱动系统的高速列车车辆模型,并与武广线高速列车实测结果对比验证模型的有效性。
结合线路试验的实测数据,分别对比了实测轴箱和构架的车体垂向加速度与模型仿真的结果。仿真计算时轨道谱采用实测武广线轨道谱,以及实测的S1002CN踏面和60轨轨面匹配,轨底坡为1∶40,仿真计算了1位右轴箱与1位右构架的垂向加速度, 牵引电机的电磁转矩通过齿轮传动装置传递至轮对产生牵引力,高速列车从静止到加速过程。试验工况是按照牵引曲线加速至200 km/h,仿真工况为:将牵引特性曲线施加在电机转子上, 车辆速度从0增大至200 km/h。图7是国内某高速动车组线路试验轴箱和构架加速度传感器布置图,获得了加速过程中的轴箱和构架的垂向加速度。图8中对比了理论仿真和试验获得的构架和轴箱加速度。
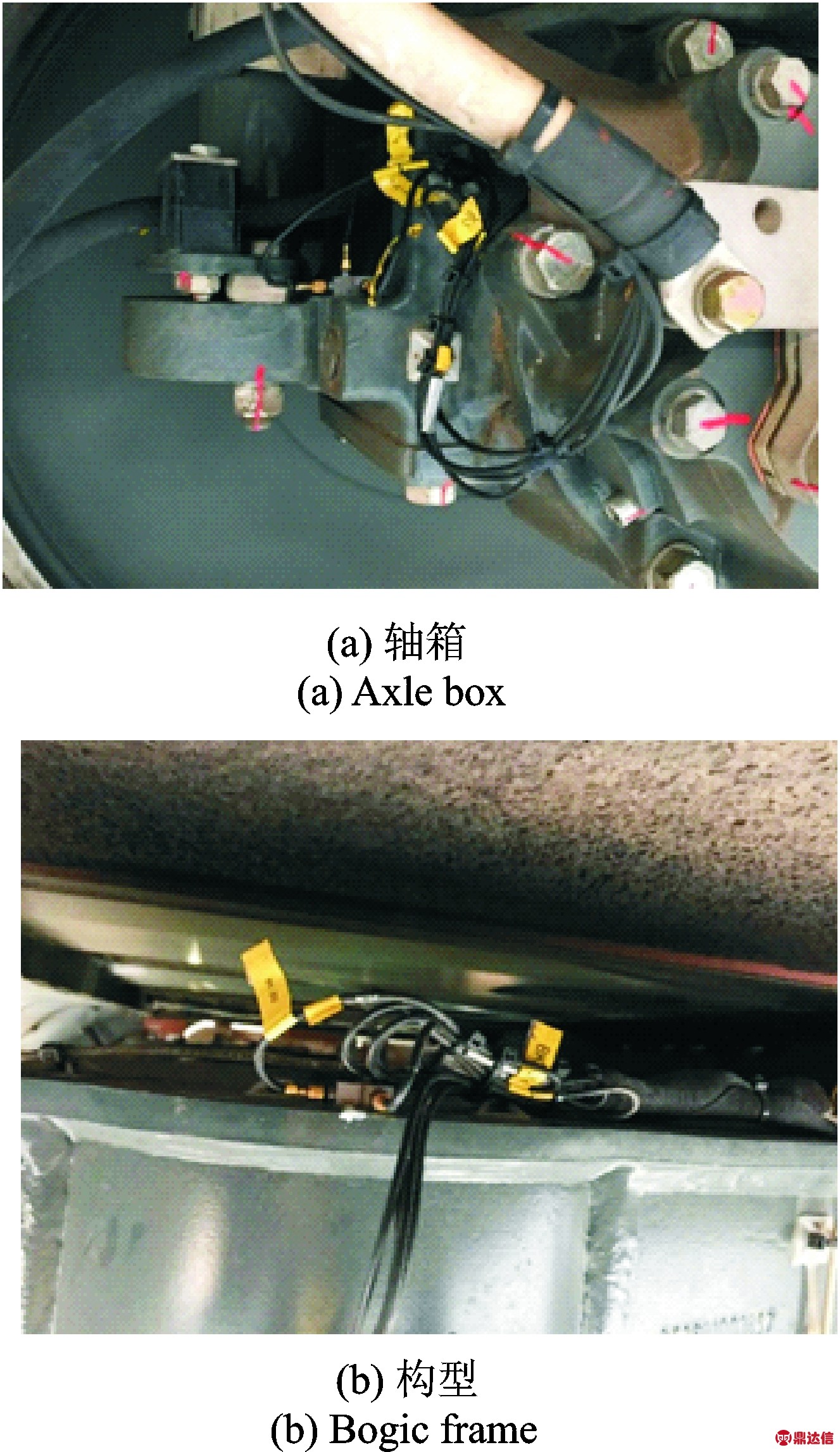
图7 传感器布置图
Fig.7 Sensor arrangement digram
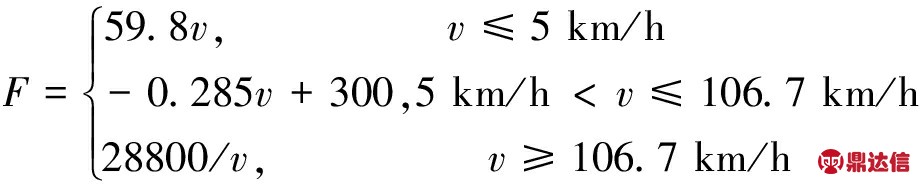
图8 垂向加速度对比
Fig.8 Vertical acceleration contrast
图8中给出了高速列车轴箱和构架处加速度传感器的振动试验测试结果与仿真计算结果的对比。可以看出,在0-70 s过程中,仿真数据和实测数据基本吻合,实测数据由于线路原因,在0-70 s时会有一些波动,但幅值基本吻合。70 s时,轴箱加速度到1.5g左右,构架垂向加速度为0.2g左右。通过以上数据对比,说明考虑驱动系统的情况下,模型可以反映高速列车的动力学特征。验证了模型的可靠性及仿真结果的正确性。
4 动力学计算
4.1 牵引制动曲线
实际的列车运行中包含了牵引、惰行、制动3种工况,特别是牵引和制动对驱动系统影响较大,以下给出牵引和制动工况牵引力和制动力的计算公式,并由此公式绘制了牵引制动转速转矩曲线。将牵引制动曲线施加在电机转子上进行车辆动力学仿真。计算牵引和制动过程中的轮轨接触参数的变化。
牵引工况下,牵引力和速度的数学关系为

(18)
再生制动工况下,制动力和速度的的数学关系为
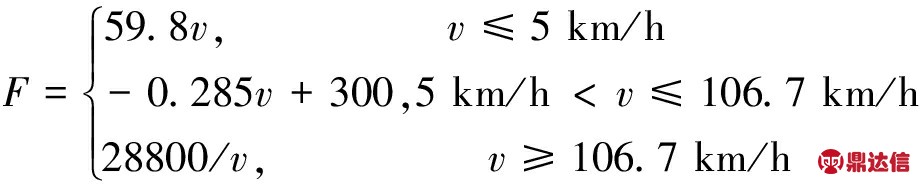
(19)
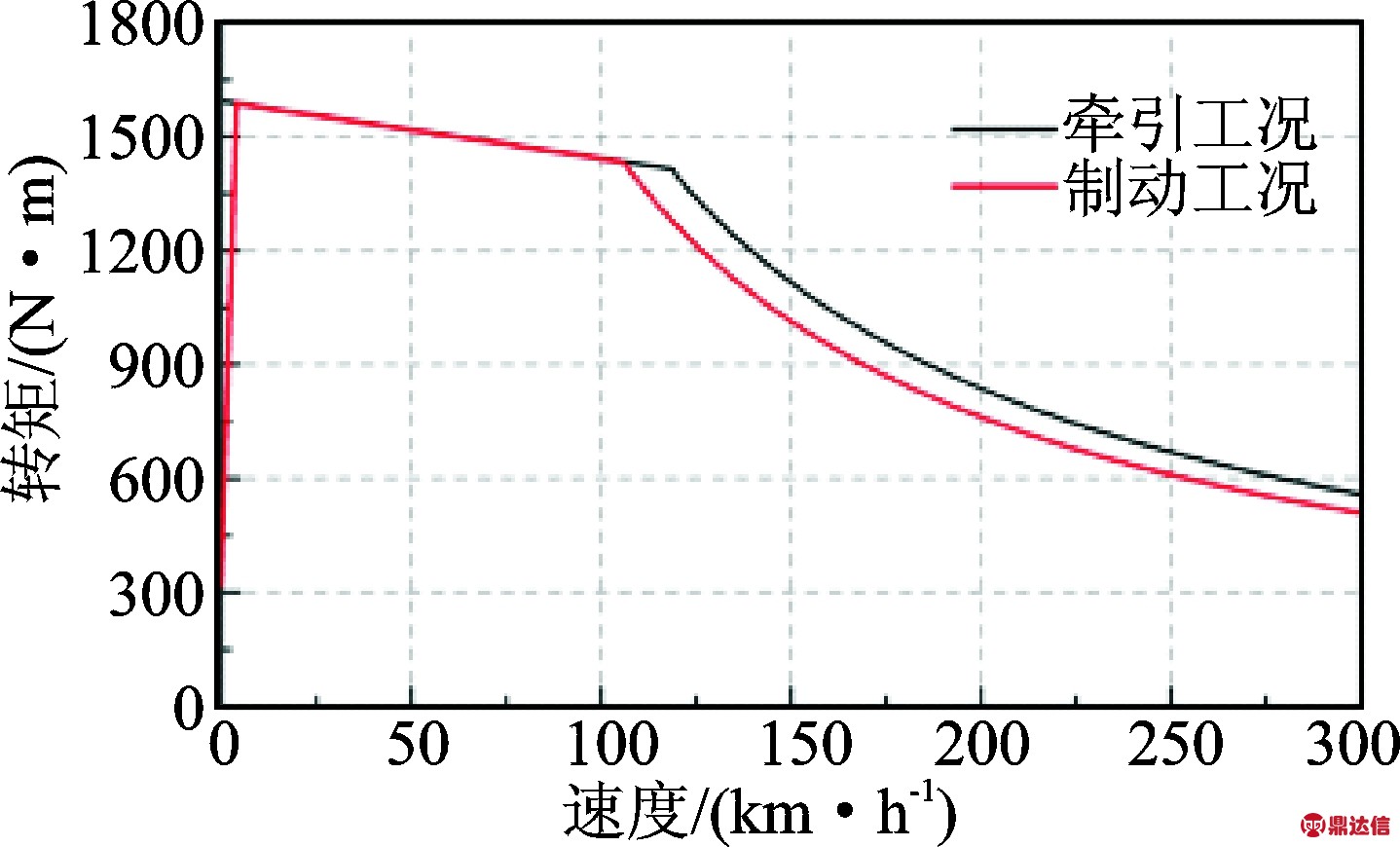
图9 牵引制动速度转矩曲线
Fig.9 Speed-torque curve of traction and braking condition
在列车运行过程中还要考虑其运行阻力,运行阻力是和速度密切相关的参数,现高速动车组运行阻力的计算公式如下
Ff=6.4M′+130n+0.14Mv+
[0.046+0.0065(N-1)]Sv2
(20)
式中 Ff为列车运行阻力;M′为空车质量;M为最大质量;n为轴数;v为列车运行速度;N为车辆数;S为列车正截面面积。
4.2 考虑驱动系统的轮轨参数分析
本节仿真时,忽略了轨道不平顺的影响。去掉轨道激励,采用S1002CN踏面和60轨,仿真工况:施加牵引转矩,先由0牵引加速至300 km/h,然后匀速行驶60 s,随后再施加制动转矩,使列车运行速度降至100 km/h,然后后匀速行驶60 s,整个仿真时间为450 s,主要分析了牵引制动工况下的轮轨纵向蠕滑率、横向蠕滑率和磨耗功的变化趋势。
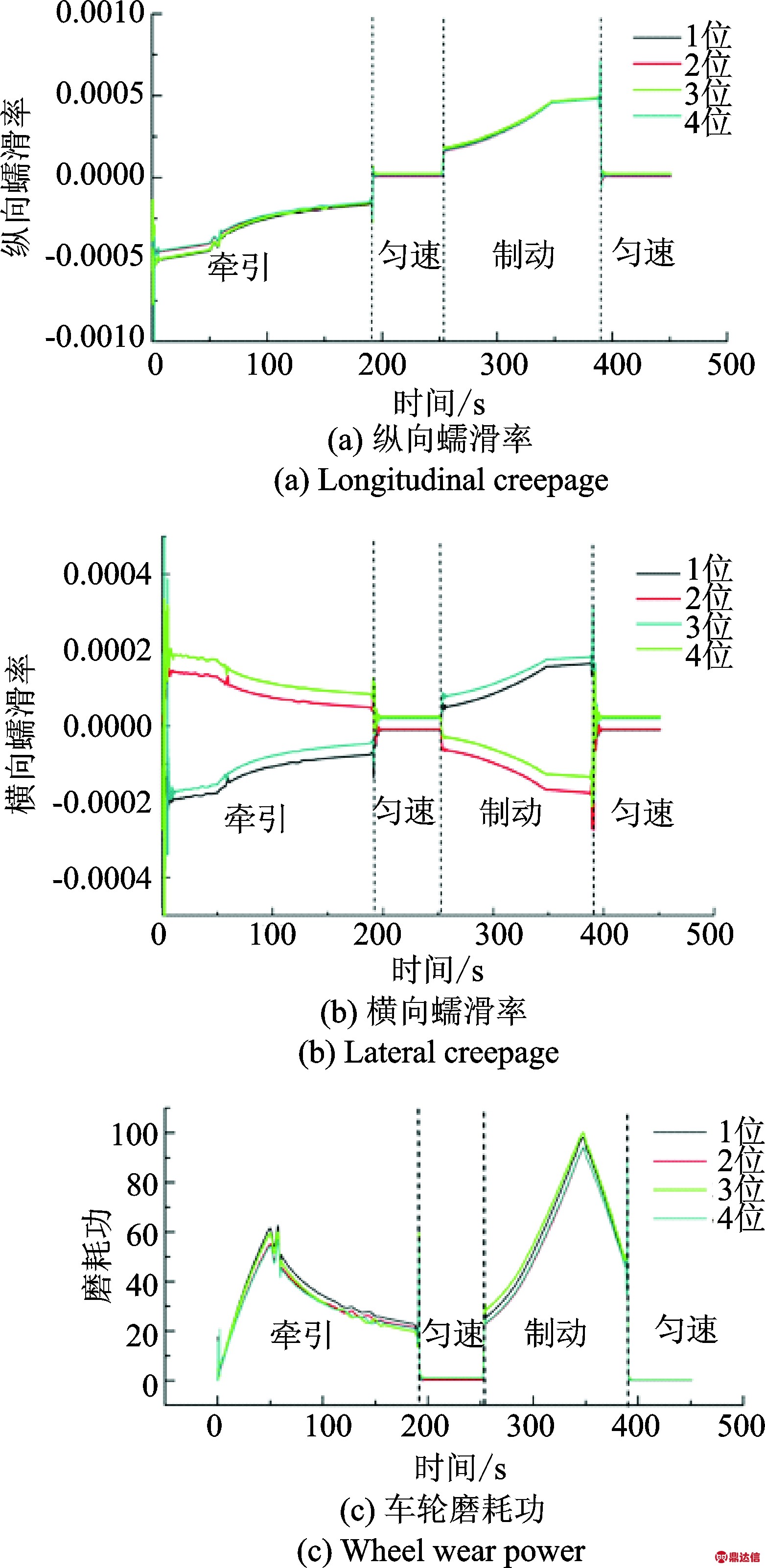
图10 考虑驱动工况的轮轨接触参数
Fig.10 Wheel rail contact parameters considering driving conditions
从以上图10(a)中可以看出,纵向蠕滑率在牵引和制动工况下,4位轮对的纵向蠕滑率相差不大,且变化趋势类似。在牵引工况下,纵向蠕滑率为负,说明该工况下车轮接触椭圆沿X轴的速度分量大于钢轨接触椭圆沿X轴的速度分量;在匀速工况下,轮轨轮对纵向蠕滑率和蠕滑力接近0,说明该工况下车轮接触椭圆沿X轴的速度分量和钢轨接触椭圆沿X轴的速度分量比较接近。制动工况下,纵向蠕滑率为正,车轮接触椭圆沿X轴的速度分量小于钢轨接触椭圆沿X轴的速度分量。从图10(b)中可以看出,在牵引和制动工况下,横向蠕滑率也有一些波动。考虑齿轮传动系统的车辆动力学模型,对电机施加的牵引力矩是按照随车速变化的牵引特性曲线施加的,波动的牵引力矩从电机传至轮对,与轨道几何不平顺、齿轮传动系统动态激励等多种激励共同作用,将在一定程度上加剧轮轨横向作用,从而引起横向蠕滑率的变化。从图10(c)中可以看出牵引工况和制动工况的磨耗功较匀速工况显著增大,同时可以看出制动工况下的磨耗功较大。且制动工况下的磨耗功更大,制动工况下峰值比牵引工况增大40%,这是因为制动工况下制动力矩较大,制动时间较短,蠕滑力和蠕滑力波动相对牵引工况更大。
4.3 考虑驱动系统的车辆动力学分析
本节主要分别采用考虑驱动系统的车辆系统模型1和不考虑驱动系统的车辆模型2进行仿真,采用相同的车轮踏面S1002CN踏面和实测WG谱轨道激励,轨面为60轨,计算了不同速度级下的车辆安全性指标和平稳性指标。
首先对两种模型转向架的特征根频率分析计算,从特征根图中可以看出,模型1的蛇形频率较模型2较小,带驱动系统模型明显降低了转向架蛇形运动频率。
表2 安全性指标分析
Tab.2 Safety index analysis
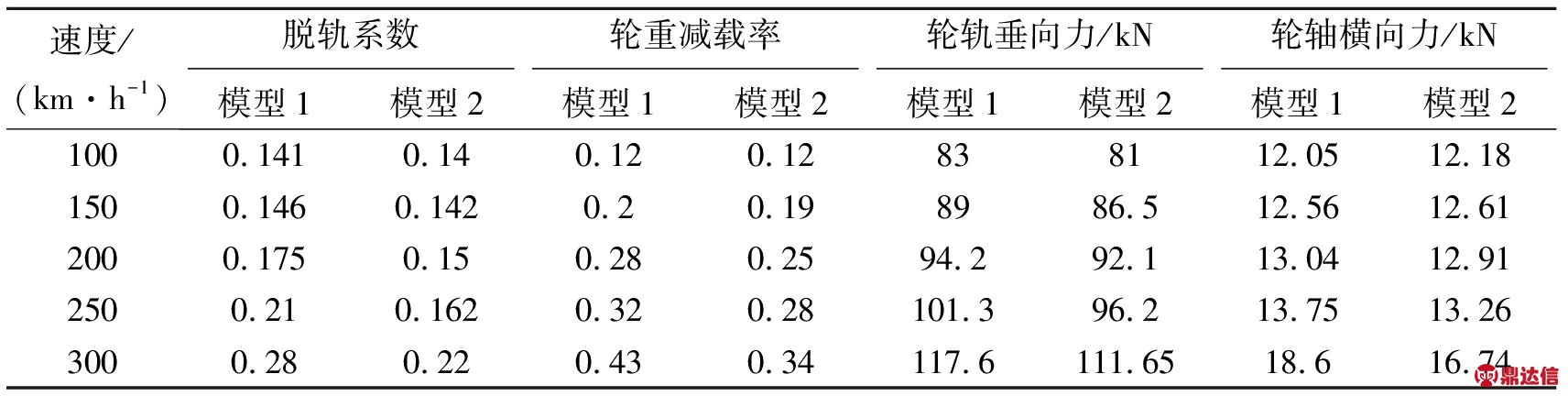
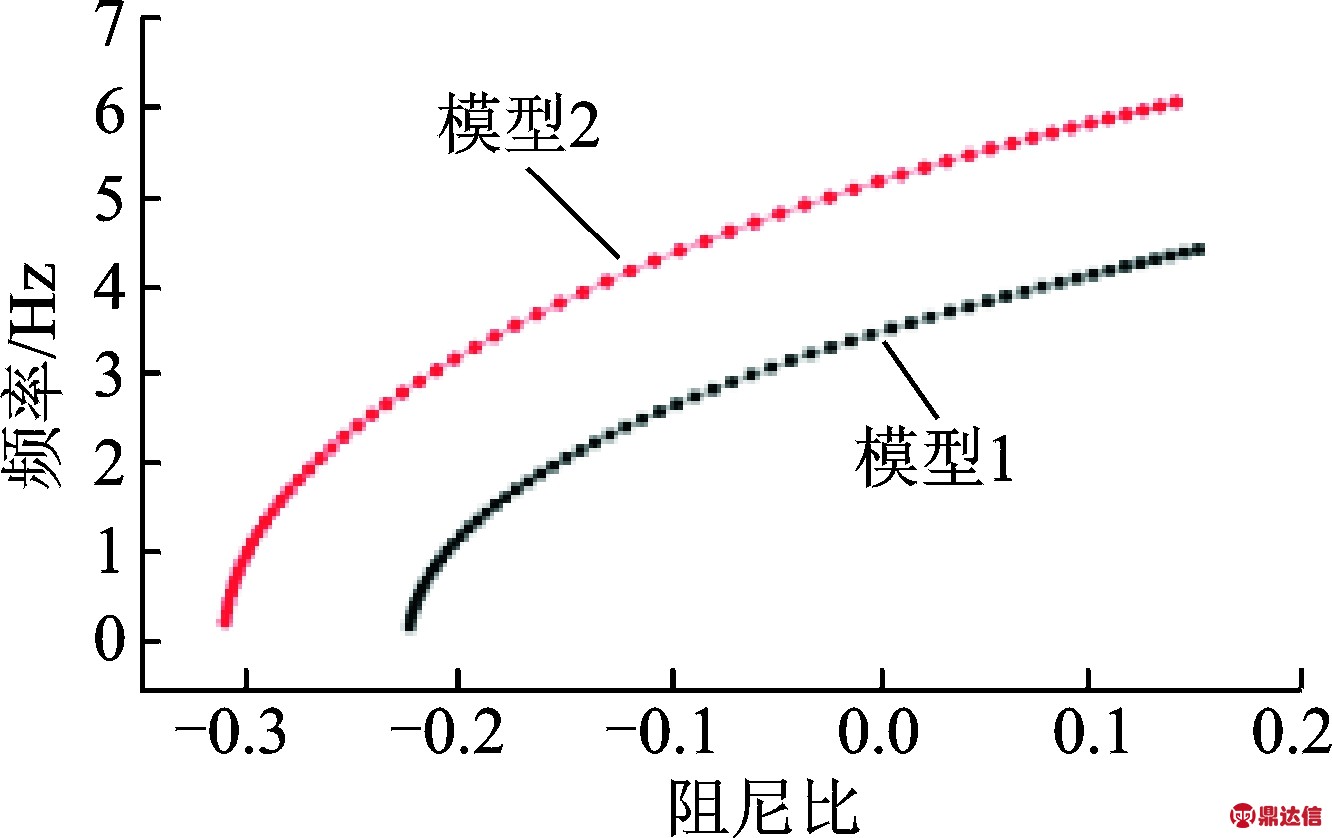
图11 转向架蛇形振型对应的特征根随阻尼比变化
Fig.11 The characteristic root corresponding to the hunting mode of the bogie changes with the damping ratio
表3 平稳性指标分析
Tab.3 Ride index analysis
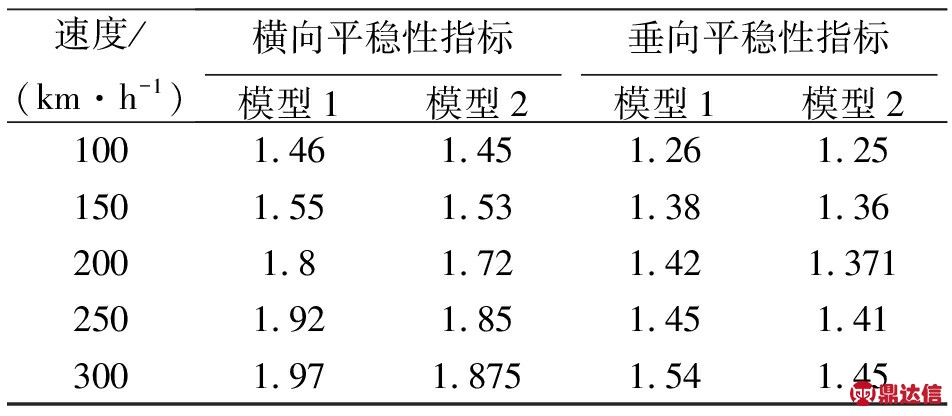
从表2中可以看出,在同一速度级下,模型1的脱轨系数、轮重减载率以及轮轨垂向力和横向力相对于模型2都明显增大,在100 km/h时,脱轨系数增大7.14%,轮重减载率相同,轮轨垂向力增大2.4%,在300 km/h时,脱轨系数增大27.2%,轮重减载率增大26.4%,轮轨垂向力增大8.2%,轮轨横向力增大11.1%。并且随着速度的增加,两种模型的安全性指标差别不断增大,这是因为不考虑驱动系统的传统模型将驱动系统等效为簧上质量和簧下质量,而簧下质量直接影响着轮轨间的动态响应,而本文所建立的考虑驱动系统模型,电机和齿轮箱采用弹性架悬,牵引力矩在作用过程中,驱动系统的振动通过弹性悬挂传递至轮对和构架,在高速工况下,这种响应更加明显,簧下质量的波动最终引起轮轨状态的变化。从表3中可以看出,横向平稳性和垂向平稳性指标区别很小,在300 km/h时,模型1的垂向平稳性指标比模型2增大0.26%,模型1的横向平稳性指标比模型2增大5.84%。说明驱动系统对车辆平稳性的影响较小,这是由于二系悬挂装置有效地减弱了由于簧下质量波动引起的振动,因此对于平稳性指标影响很小。
5 结 论
本文在采用Polach轮轨接触算法,首先建立单轮对驱动系统简化模型,分析了不同蠕滑速度下的动力学特性。建立考虑驱动系统的整车车辆动力学模型,该模型考虑了齿轮啮合刚度变化、牵引转矩特性以及轨道随机不平顺激励,通过线路试验数据验证,其结果良好;进行了轮轨接触动力学参数计算,发现了牵引制动工况下的接触参数变化规律,并与未考虑驱动系统的车辆动力学模型进行对比,分析了安全性指标与平稳性指标,得出以下结论:
(1)通过单轮对模型可以看出,当纵向蠕滑速度较大时,带驱动系统的高速列车系统会发生扭转自激振动。
(2)建立的考虑驱动系统的车辆动力学模型能够更加真实地仿真计高速列车在实际运行中的动态响应。
(3)通过考虑驱动系统整车模型牵引工况和制动工况下的轮轨接触参数可以看出:牵引工况下,纵向蠕滑率为负,制动工况下,纵向蠕滑率为正;横向蠕滑率也有一定程度的波动;同时牵引和制动工况下车轮磨耗功明显大于匀速工况,且制动工况磨耗功比牵引工况增大40%。
(4)考虑驱动系统转向架蛇形频率低于不考虑驱动系统转向架蛇形运行频率;考虑驱动系统模型相对于未考虑驱动系统模型其安全性指标较大,而两种模型对平稳性指标差别很小。