摘 要:针对弹性支承块枕下胶垫及套靴存在的松动、失效等问题,基于有限元动力分析模型研究块下合理刚度的取值范围,并提出将套靴与块下胶垫合二为一的新型一体化橡胶套靴的设计方案;基于有限元静力分析方法,从理论角度确定新型一体化橡胶套靴的结构参数;通过试样试制、性能测试等方法验证其经济性、可靠性与适用性。
关键词:弹性支承块;块下支承刚度;橡胶套靴;结构优化
弹性支承块整体道床具有弹性好、少维修、便于更换、部件制作及现场施工技术成熟等特点,在国内干线线路长大隧道得到广泛的应用[1-4]。但从目前运营情况来看,橡胶套靴及块下胶垫也存在一些问题,主要表现在容易出现支承块松动等破坏失效现象[5-7]。产生上述病害的原因一方面是橡胶套靴及块下垫板材料采用三元乙丙橡胶制作,此种材料耐老化性好,但其自黏性和互黏性较差,加工困难,导致橡胶套靴及枕下垫的制造精度存在较大的离散性,引起橡胶套靴及块下胶垫的初始安装误差较大,使二者不能很好地协同工作;另一方面是块下刚度与轨下刚度设置不合理。
为解决上述问题,针对目前普遍采用的支承块布置方式及结构参数(每千米1 667对支承块,支承块尺寸:650 mm×300 mm×190 mm),通过理论分析、结构优化设计研制出一种新型一体化套靴,并通过性能测试验证了一体化套靴的可靠性与适用性,为弹性支承块的结构优化提供了参考。
1 一体化套靴垂向合理刚度分析
参考文献[8-11]中块下刚度与轨下胶垫刚度合理匹配的研究方法,基于落轴试验原理及有限元分析方法,研究了块下刚度合理取值。
初步取轨下刚度20~240 kN/mm,块下刚度20~240 kN/mm,间隔20 kN/mm,进行落轴仿真计算,得到钢轨位移、钢轨加速度、支承块位移、支承块加速度、道床位移、道床加速度的动力学响应,根据研究结果最终确定块下及轨下合理刚度取值。鉴于本文主要关注块下支承刚度合理取值范围,以块下刚度为变量研究了不同轨下刚度时钢轨、支承块及道床的各项动力指标随块下刚度的变化规律。研究结果见图1~图6。
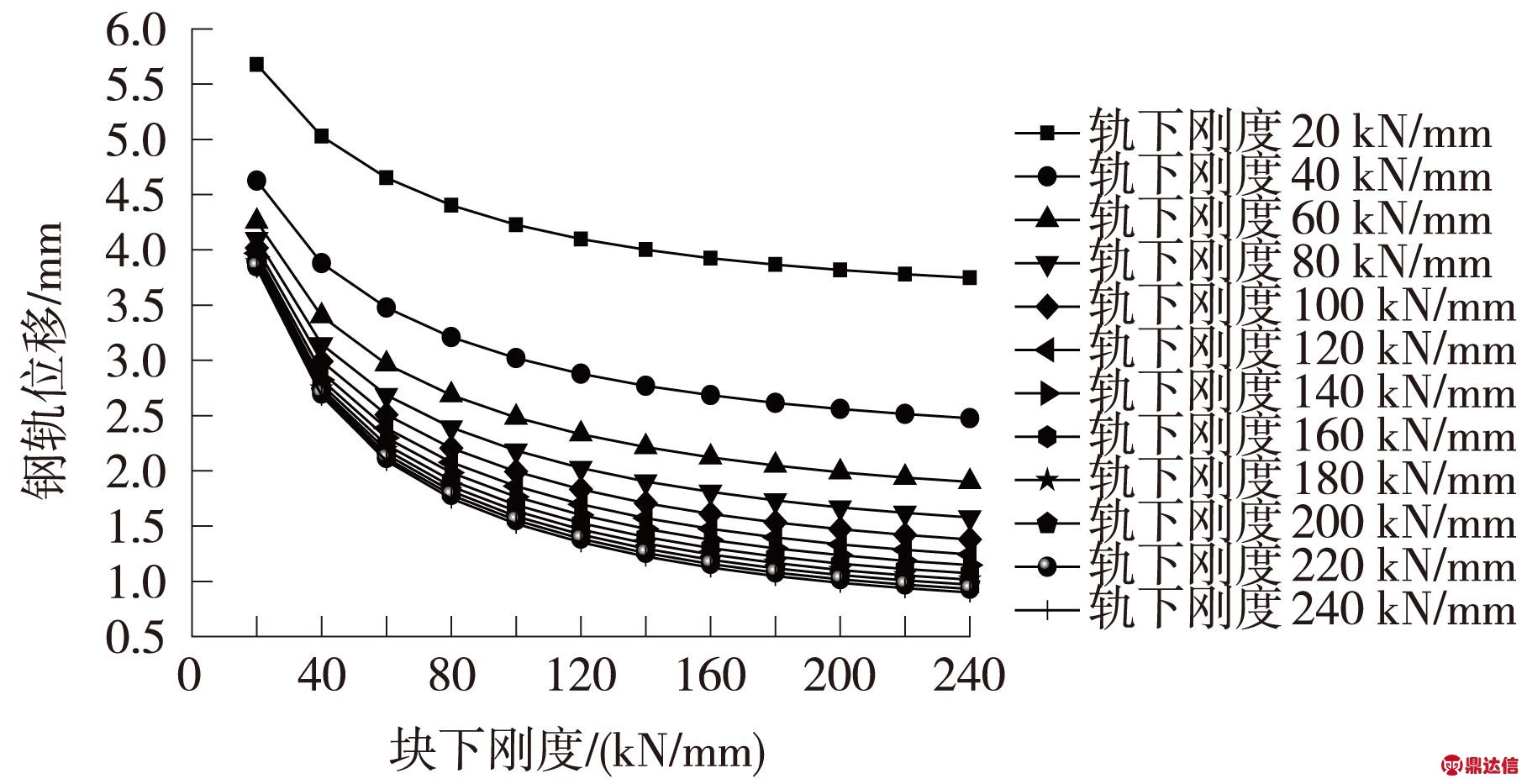
图1 钢轨位移随块下刚度的变化规律
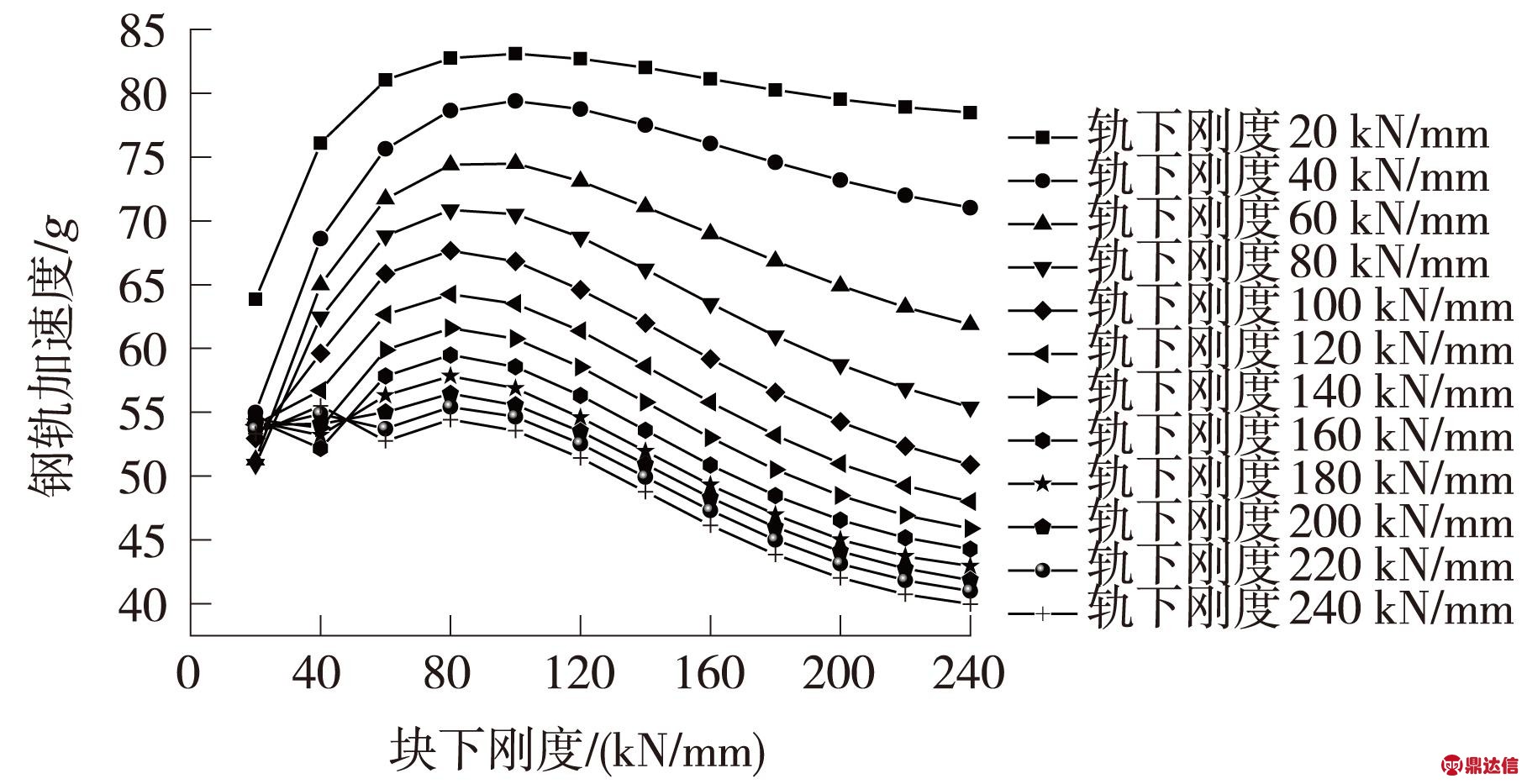
图2 钢轨加速度随块下刚度的变化规律
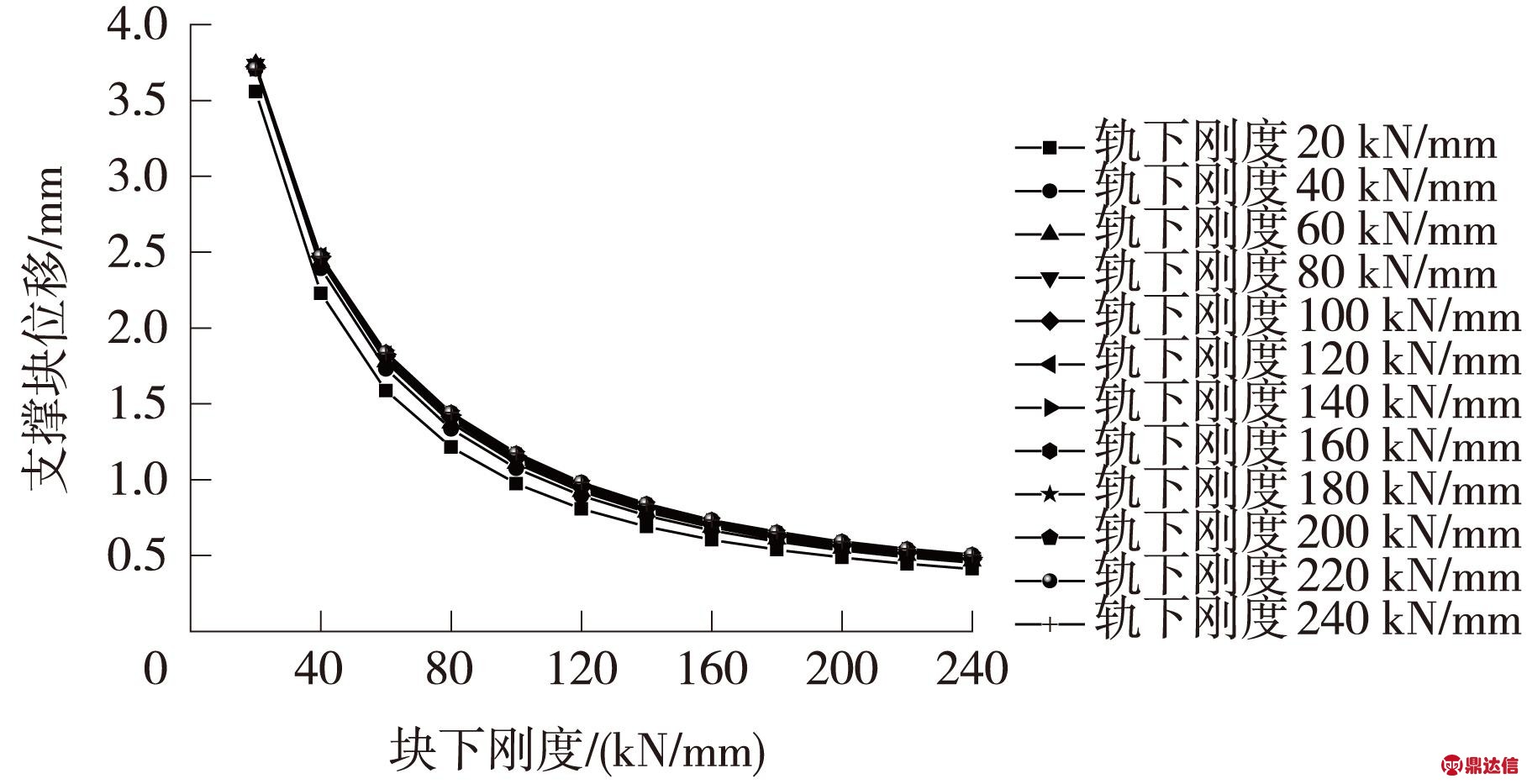
图3 支承块位移随块下刚度的变化规律

图4 支承块加速度随块下刚度的变化规律
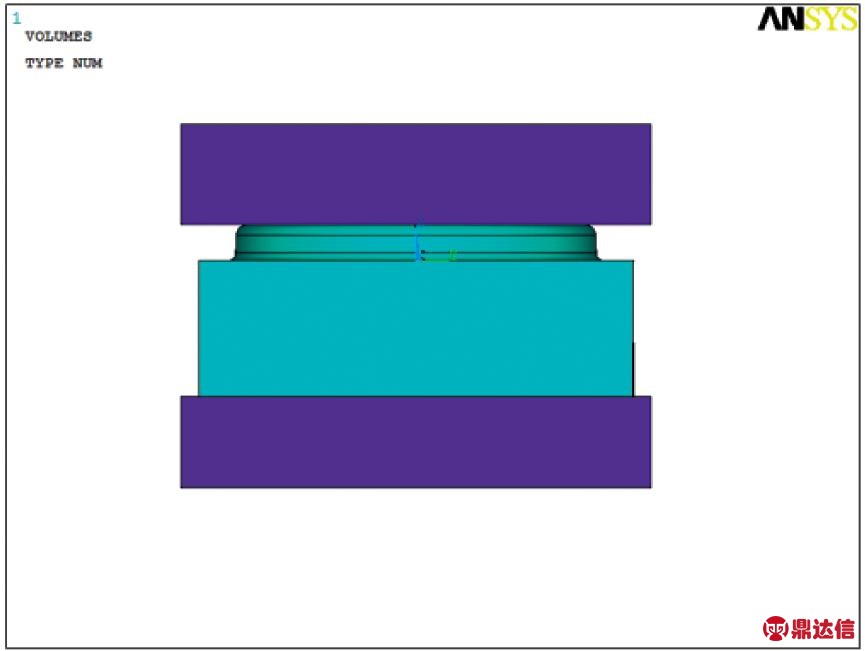
图5 道床位移随块下刚度的变化规律
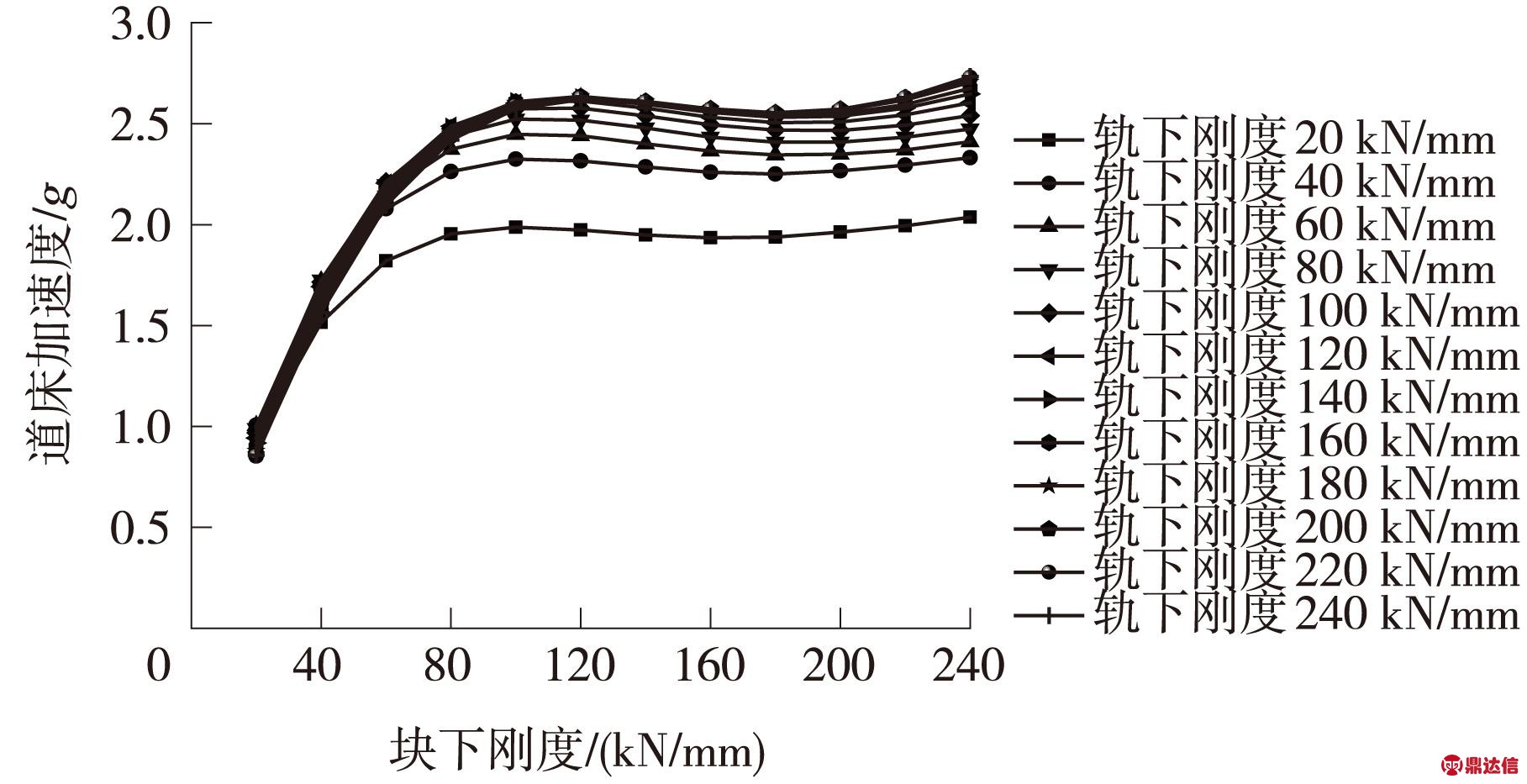
图6 道床加速度随块下刚度的变化规律
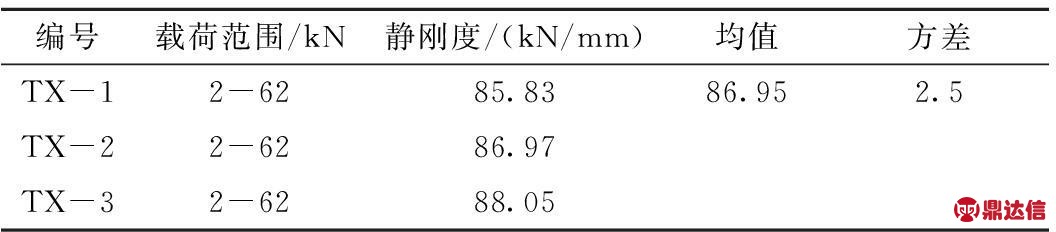
图7 新型套靴的设计效果图
由图1~图6可以看出:随着块下刚度的增加,钢轨及支承块位移快速减小,而道床位移变化不大。块下刚度小于80 kN/mm时,钢轨加速度随块下刚度的增加而增大;当块下刚度大于80 kN/mm,钢轨加速度则逐渐减小。支承块加速度随块下刚度的增加而呈现出逐渐减小的趋势,并在块下刚度大于200 kN/mm后,基本趋于稳定。块下刚度小于120 kN/mm,道床加速度逐渐增大;块下刚度在大于120 kN/mm后,道床加速度变化不大。
综合以上分析,块下刚度取120~200 kN/mm(换算为块下静刚度为80~130 kN/mm)较为合理,此时可兼顾各项动力学指标均处于合理水平。
2 一体化橡胶垫板试制
一体化橡胶垫板试制主要从材料选择、有限元理论分析、产品试制及性能测试等方面进行研究,分别介绍如下。
2.1 一体化橡胶垫板结构优化方案
本文提出的结构优化方案是将橡胶套靴和枕下胶垫合为一体、一次成型的新型结构形式,在套靴底部设置钉柱,并通过调整钉柱的结构参数使套靴刚度在块下合理刚度范围内。新型套靴的设计效果图如图7所示。
2.2 一体化橡胶垫板材料选择
目前,在轨道交通领域,橡胶垫板常用的胶料有天然橡胶、丁苯橡胶、氯丁橡胶及三元乙丙橡胶等[12]。丁苯橡胶作为合成橡胶中产量最大、应用最广泛的胶种,其耐磨性能优秀,氯丁橡胶则具有较高的耐老化性能,但上述两种胶料的耐寒性能偏差。三元乙丙橡胶耐臭氧和耐老化性虽好,但加工困难,厂家往往会添加再生胶改善其加工性能,导致胶垫的实际性能较差。天然橡胶具有良好的机械性能、优异的弹性、耐寒性和电绝缘性能,具有以上胶料优点的同时克服了其不足,因此新型套靴胶料选择天然橡胶,辅以氯化锌、硬脂酸、防老剂、炭黑、促进剂及其他助剂等材料。
为了控制产品质量,对现有胶料配方进行改进,提高了胶料硬度的同时增加了胶料的流动性。经过多次试配得到一种改进的胶料配方,根据此胶料配方试制了试样并对其性能进行了测试,结果如表1所示。
表1 试样性能测试结果
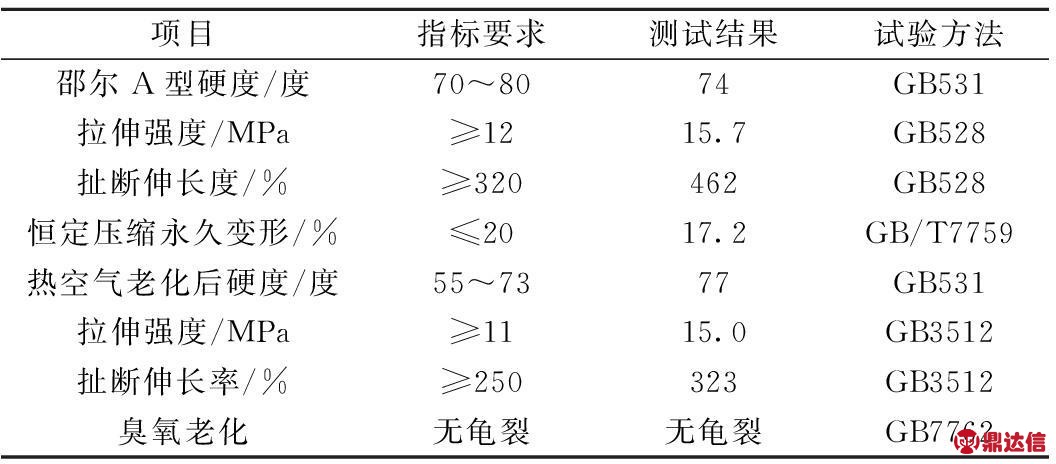
由表1可以看出,试样所有性能均满足相关指标要求,因此该胶料配方可用于后续样品的制备及新型套靴的研究。
2.3 一体化橡胶垫板刚度理论分析
为使新型套靴静刚度在块下合理刚度范围内,基于有限元分析方法建立了单个钉柱的有限元模型如图8所示。
橡胶变形的计算涉及到大位移、大变形、接触非线性边界条件及超弹性材料等多种非线性因素,使数值模拟的准确性受到影响。对模型的简化程度、所采用的橡胶本构关系模型中材料常数测试的准确性都会对计算精度产生影响。本报告在此采用3个参数的M-R模型来模拟硬度74的胶料,其中C10=0.8,C01=0.035,C11=0.05。
为了模拟静刚度加载的情况,在钉柱两侧附加两块金属块,在其中一个金属块的外侧施加X、Y和Z三向的位移约束,在另一金属块的外侧施加均布压力,金属板与钉柱间以赫兹方式接触,如图9所示。
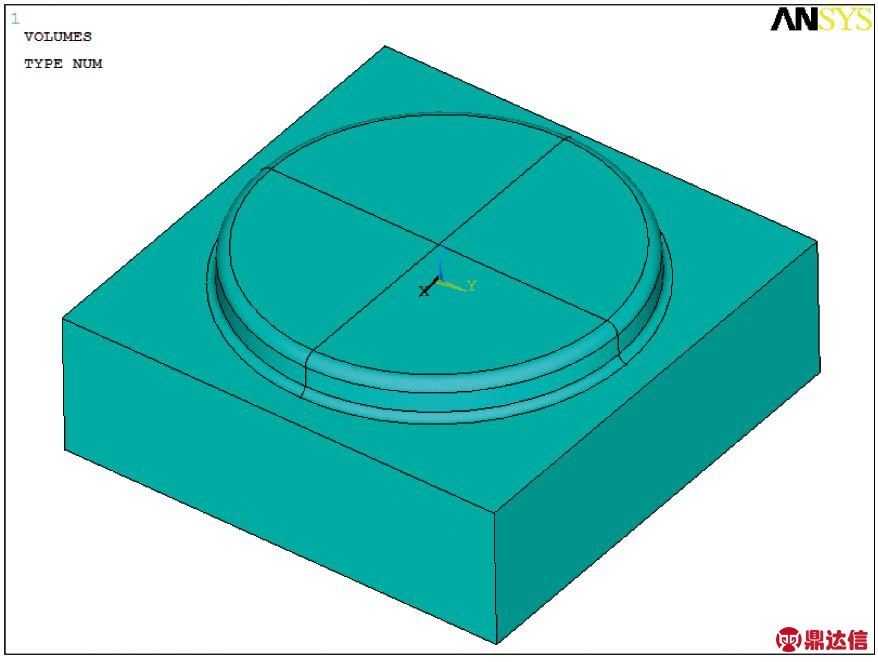
图8 单个钉柱的
有限元模型
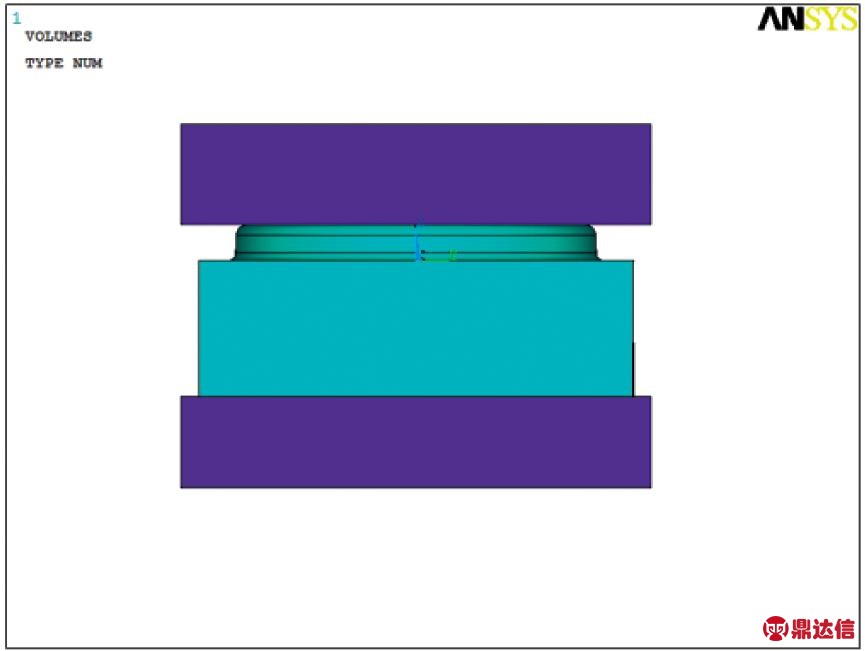
图9 单个钉柱的
有限元模型
首先预估套靴底部分布200个钉柱,并选取钉柱底面半径12 mm,顶面半径7 mm,高为7 mm进行试算。根据试算结果预估整个套靴静刚度仅为36.14 kN/mm,与块下合理刚度80~130 kN/m存在较大的差距。
根据经验,增加胶料硬度、增加钉柱外径、增加钉柱个数和降低钉柱高度等方法可提高钉柱的静刚度。此次设计的胶料硬度已达74,硬度增加的范围有限,且硬度过大会降低其流动性,不利于加工,鉴于此,增加胶料硬度是不可取的。因此主要从钉柱高度、钉柱个数和钉柱直径方面进行了大量的试算研究。由于设计指标对静刚度值要求较高,为了满足要求,在钉柱半径确定后,钉柱个数按所能分布的最大钉柱个数计算(钉柱间最小净距为2 mm)。部分满足要求的计算结果如表2所示。
表2 套靴刚度理论计算工况及结果
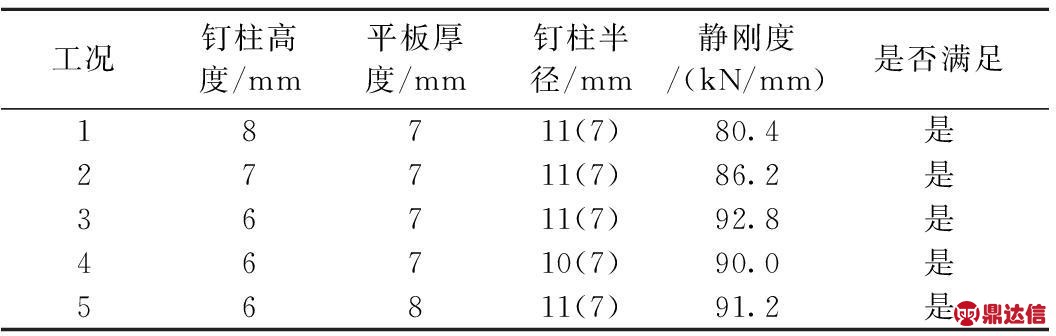
注:钉柱半径括号外为柱底面半径,括号内为柱顶面半径。
考虑到理论计算结果与橡胶垫板的实际刚度会存在一定的偏差,工况3、4比较合理,但考虑这两种工况时套靴底部的厚度为13 mm,会影响实际的安装高度,本文适当将平板部分的厚度增加至8 mm补充计算,所得工况5的理论刚度计算结果与工况3、4相差很小,可用来进行试样的试制。
2.4 一体化橡胶垫板试样试制
根据上述理论分析结果,本文按工况5的参数进行了套靴底部试样的制备。硫化试验在HYL-200P型平板硫化机上进行,该硫化机的模压板上设置有T形槽,可通过螺栓将模具固定在压板上,方便开模,如图10所示。
在首件样品制备时,对加胶量进行测量,为2 880 g,所得首件样品外观平整无缺陷,但发现垫板厚度比设计大1~2 mm。经过调整加胶量和排气次数等加工工艺的控制,最终得到符合要求的样品。样品长601 mm,宽290 mm,总厚度平均值为14.0125 mm,其中平板部分厚度在8 mm±0.3 mm范围内,钉柱高度在6 mm±0.2 mm内,可满足设计公差要求,此时加胶量为2 430 g。
2.5 一体化橡胶垫板试样性能测试
为检验样品性能是否满足设计要求,同时对理论分析结果的可靠性进行评估,本文试制了3组试样,并进行了套靴静刚度及疲劳性能测试,测试照片如图11所示,测试结果如表3、表4所示。
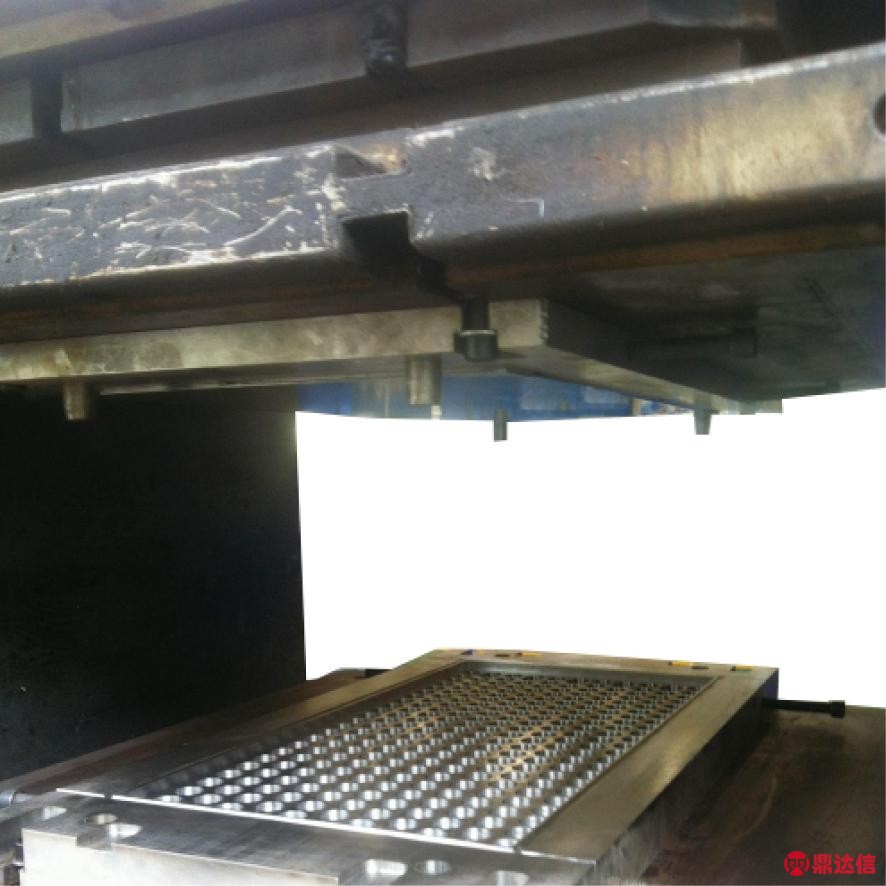
图10 模具安装
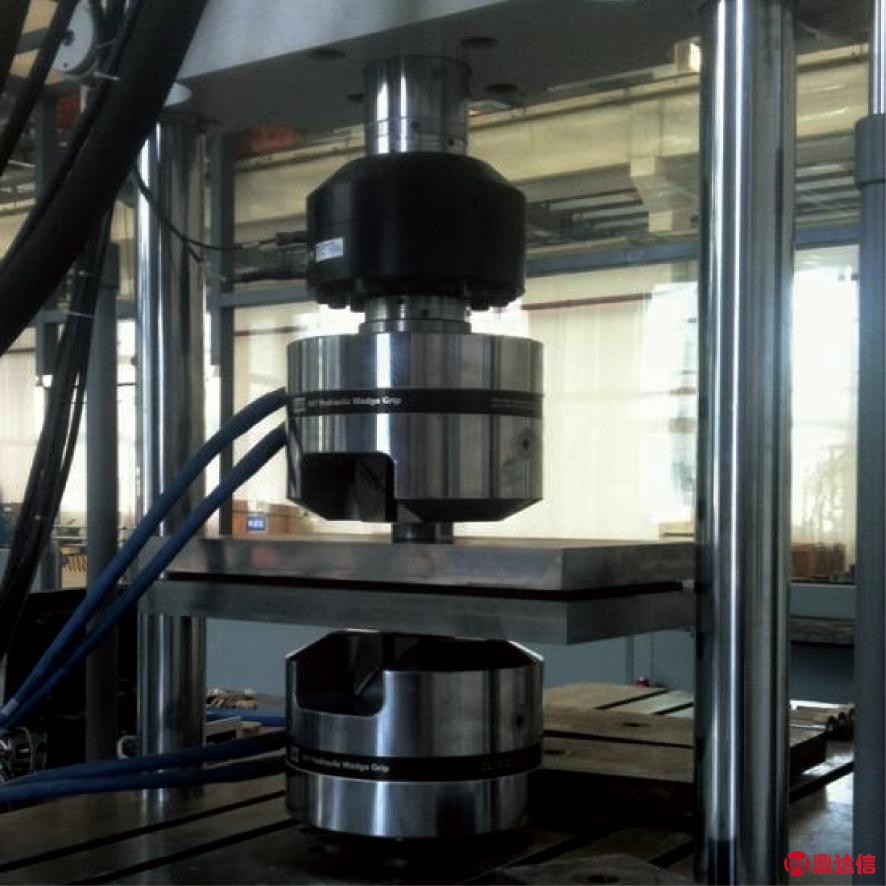
图11 室内试验
表3 套靴底部试样静刚度测试结果
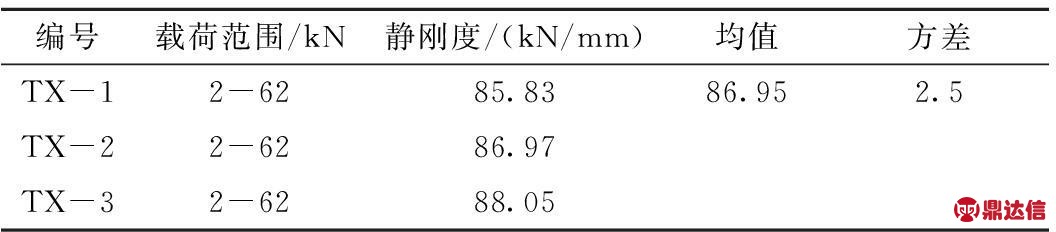
表4 套靴底部试样疲劳测试结果

由表3可知,试样静刚度的最大、最小可能值分别为93.2 kN/mm和80.7 kN/mm,满足块下合理刚度的要求。测试刚度的均值与理论分析结果的相对误差为4.6%,表明理论分析模型是可靠的。
疲劳试验后,样品外观无异常粘着、破裂等情况,经检测和测量后,试样厚度变化率、刚度变化率均远小于变化率指标要求,表明新型一体化套靴的疲劳特性满足要求。
3 一体化橡胶与既有橡胶垫板对比分析
制作成本方面:单个传统套靴的成本约150元左右,新型一体化套靴的成本约140元左右,按轨枕间距0.625 m计算,每铺设1 km,实用新型套靴可节约3.2万元。
制作工艺方面:此次所设计的新型一体化套靴能够一次硫化成型,工艺简单。
实用性能方面:新型一体化套靴部件少,铺设更换更为便捷。
4 结论
本文通过理论分析、结构优化设计研制出一种新型一体化套靴,并通过性能测试验证了一体化套靴的经济性、可靠性与适用性,主要得出如下结论与建议。
(1)对于目前常用的弹性支承块结构布置参数,枕下合理支承静刚度为80~130 kN/mm。
(2)新型一体化橡胶套靴的刚度及疲劳特性能够满足相关设计要求,且具有良好的可靠性、经济性与适用性,建议有条件的情况下进行试用。