摘 要 对于全尺寸飞机静力试验,通常采用拉压垫技术施加压向载荷,以及胶布带-杠杆技术施加拉向载荷。由于两种技术之间换装复杂,因此对全尺寸飞机静力试验,换装周期长、试验成本高。为了提高试验效率、节约成本,融合两种加载技术,研制了胶布带拉压垫技术。大部分情况压向载荷沿飞机蒙皮法向方向,或者与法向方向成一定较小的角度。现有的胶布带拉压垫技术可满足试验需求;但对某型号全机静力试验某压载工况,载荷方向与机身蒙皮法向方向成较大角度,现有的胶布带拉压垫技术无法实施。对胶布带拉压垫技术进行分析,设计改进方案,实现大倾角拉压垫压载技术。将该技术应用到某型飞机压载试验中,经过数据分析,试验数据真实有效,为以后大倾角压载试验提供解决方法。
关键词 拉压垫 压向载荷 静力试验 线性拟合
新机研制要经历四个重要阶段,包括设计、制造、试验和试飞。飞机结构静力强度试验是验证新机型结构设计强度与制造工艺较为有效的方法[1—3]。
飞机结构静力强度试验就是通过对试验件(全机或者飞机部件)施加载荷(如拉向载荷、压向载荷及充气载荷等)的方式,模拟飞机在执行飞行任务中将会遇到的各种受力情况(如起飞、降落和平飞等)。通过在试验中测量各种传感器(如应变片、位移传感器及压力计等)的响应值,来判断该型号飞机是否满足设计要求,是否安全可靠[4]。
在飞机结构强度试验中,载荷的施加是一个非常重要的环节。一直以来,中国飞机强度研究所沿用苏联的施加载荷方法,采用“胶布带-杠杆系统”施加载荷;虽然该系统只能施加拉向载荷,但该系统承载能力强、连接简单、使用方便、易于拆卸换装、成本低;并且,该技术已经发展的相当成熟,因此仍然是试验中主要加载形式[4,5]。
随着新研型号试验要求、规模、载荷复杂程度越来越高,为了实现在单个翼面施加双向载荷,以达到提高试验效率、避免加载点相互干扰、节省通道、便于检查的目的,拉压垫加载系统技术得到了研发与应用。拉压垫技术采用专用铝板粘贴橡胶块方式,通过橡胶块粘贴蒙皮以及杠杆系统向铝板施加拉压载荷实现对试验件的加载[6,7]。
飞机强度所于2014年开展了拉压垫材料选择、拉压垫制作和粘贴工艺规程的制定、拉压垫疲劳老化性能的研究工作[8,9]。该技术已发展比较成熟,广泛应用于全机试验中,如某隐形战斗机全机静力试验中,某翼面加载工况就采用拉压垫加载技术实现压向载荷的施加。在国外,该技术也得到了广泛的应用,瑞士的F/A—18飞机进行全机试验,采用橡胶块拉压垫-杠杆系统施加拉向载荷和压向载荷[10]。
虽然拉压垫技术具有双向加载功能且精度高、加载速度快等优点,但是在应用过程中拉向承载不足的问题逐渐暴露出来,并且成本高、换装工作复杂,不适用于需要进行多次换装的多工况全机静力试验。为了降低试验成本,在满足加载精度的条件下,飞机强度所融合了胶布带-杠杆系统的拉向承载大、成本低、易于拆卸换装等优点与拉压垫的双向加载、精度高、加载速度快等优点,设计了胶布带拉压垫-杠杆系统加载技术。
该技术采用卡板与胶布带(胶布带粘贴在蒙皮上)固定木块,通过杠杆系统向木块实施压向载荷实现对试验件的压载。该技术所使用的胶布带为可批量生产的标准件,相比于拉压垫技术降低了试验成本;而且去掉木块和卡板后,可更换为传统的胶布带-杠杆拉载系统,便于换装拆卸,缩短了试验加载设备换装周期。
随着试验的新需求,比如大倾角加载,压载方向与蒙皮法线方向成较大角度,上述拉压垫加载技术只能施加倾角在23°内的载荷,无法满足大角度加载要求。该问题已成为试验难点,针对该问题,本文在上述研究的基础上,通过对胶布带拉压垫技术进行改进,提出一种大倾角拉压垫加载技术。首先对胶布带拉压垫-杠杆系统进行原理分析,然后提出增大加载倾角的方法,在不增加试验成本的条件下对胶布带拉压垫进行改进,并将该技术应用到某型飞机某整流罩压载工况试验中,最后验证该技术的有效性和合理性。
1 胶布带拉压垫-杠杆技术原理分析
胶布带拉压垫-杠杆技术如图1所示。在机身蒙皮处加载位置粘贴拉压垫专用胶布带,用于固定压载所需木块。木块上方放置卡板,卡板两端通过通用铝棒(直径为26 mm)与胶布带相连。在设计过程中,木块的厚度设计通常偏小,因此,为了在试验中保证木块固定无滑动现象发生,在实际安装中在卡板与木块之间塞入橡胶垫,保证胶布带两端拉紧。卡板上方通过设计的专用单耳与一级杠杆连接,杠杆与杠杆之间通过设计的专用压盘连接。
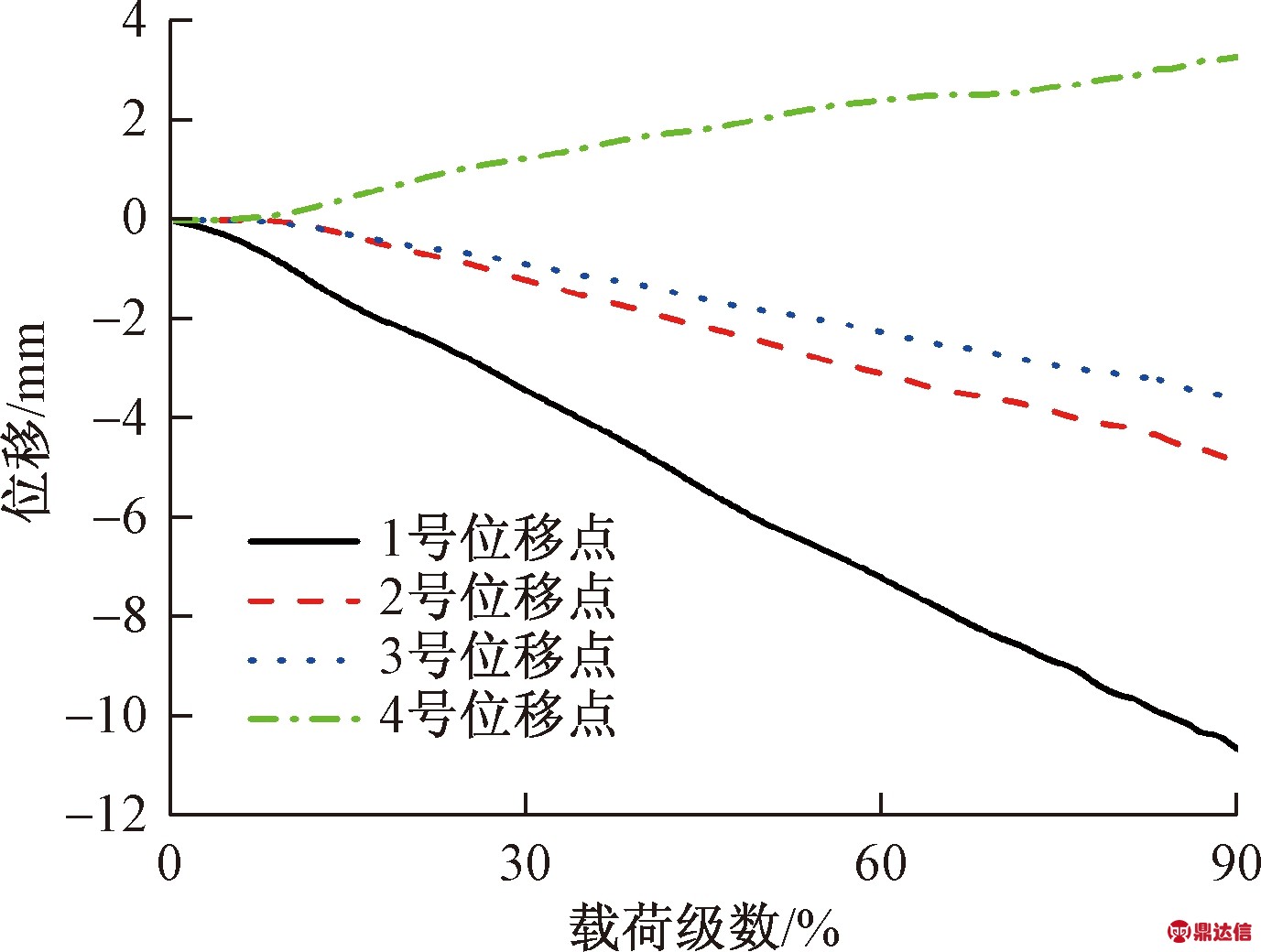
图1 胶布带拉压垫-杠杆示意图
Fig.1 Canvas tension/compression pad-lever diagram
为了保证整套拉压垫-杠杆系统在试验过程中的稳定性,在设计过程中,尽量缩小单耳和压盘的高度,保证它们在加载过程中压杆稳定。
胶布带拉压垫去掉木块后,用连接件(一般用钢丝绳)连接铝棒和杠杆,组成胶布带-杠杆拉载系统,如图2所示。
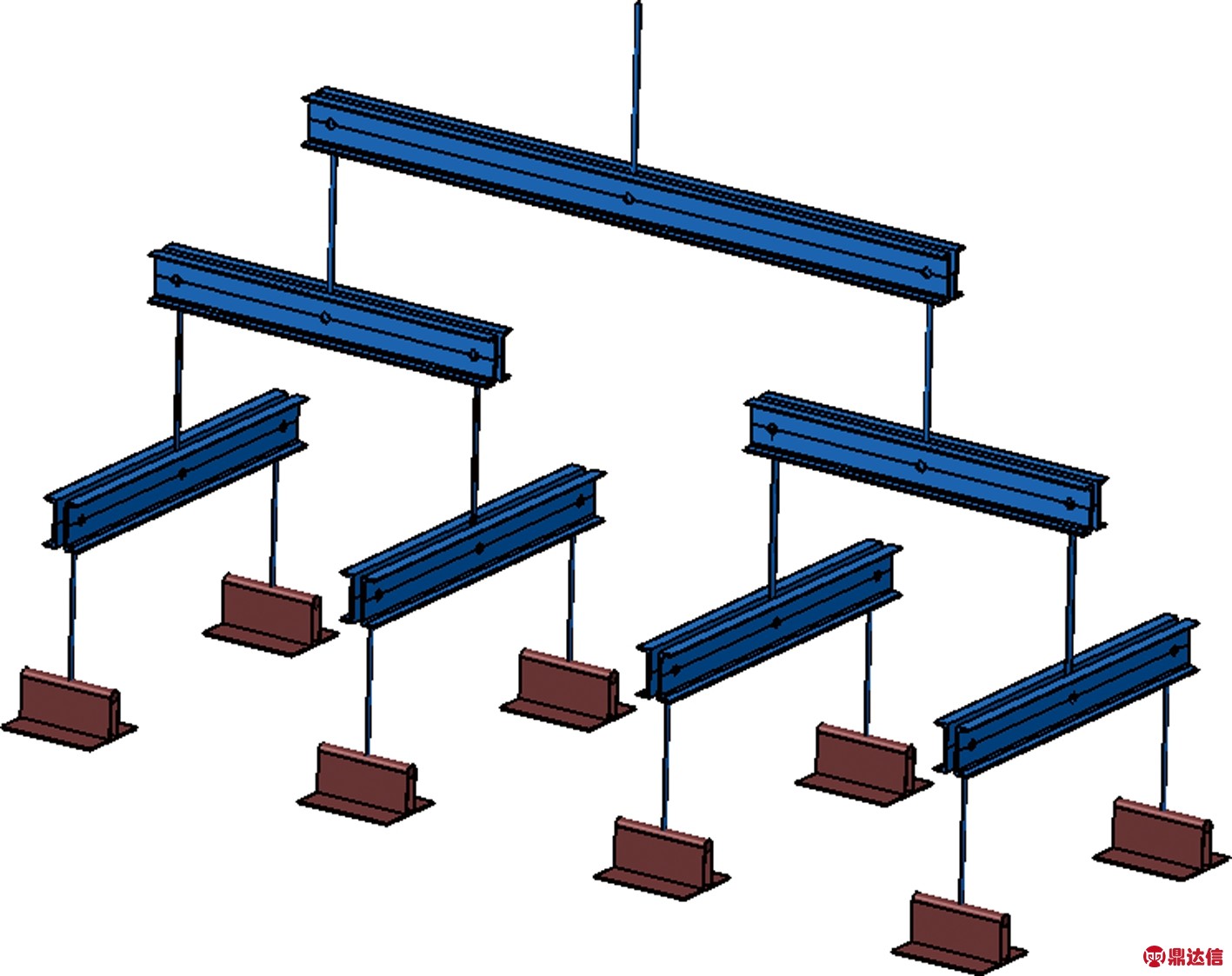
图2 拉压垫-杠杆拉载示意图
Fig.2 Tension/compression pad-lever tension load diagram
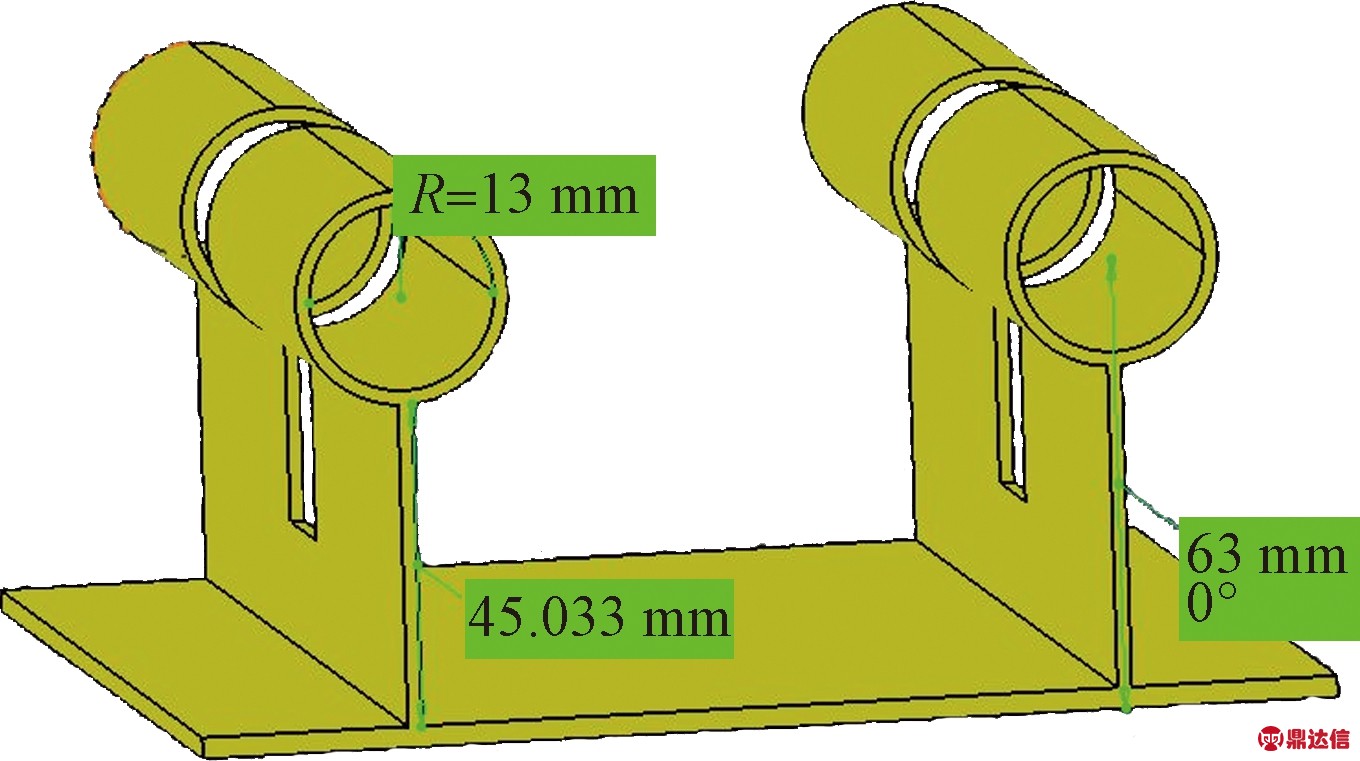
图3 胶布带示意图
Fig.3 Canvas-pad diagram
2 胶布带拉压垫大倾角加载技术设计
2.1 胶布带拉压垫加载技术存在缺陷
胶布带拉压垫专用胶布带如图3所示。调节木块两侧高度便可实现载荷方向与蒙皮法线方向成小角度情况下实施压向载荷。
受胶布带高度限制,木块一侧最高高度为45 mm,最低一侧高度为10 mm,木块底部宽度为90 mm,因此压载载荷倾角最大为arcsin(35/90)=23°。压载倾角大于23°情况下,胶布带拉压垫加载技术无法应用于大倾角压载试验。
2.2 胶布带拉压垫加载技术改进
对于胶布带拉压垫加载技术,胶布带和铝棒为通用件,通常情况下不单独设计加工;卡板和木块为专用件,会根据载荷方向进行单独设计加工。
与设计专用胶布带相比,更改铝棒半径尺寸设计专用铝棒成本更低。因此,本文通过设计专用铝棒、卡板和木块实现大倾角压载载荷的实施。
如图4所示,通过减小铝棒半径,增加铝棒距机身蒙皮高度,提高了木块的许用高度。再更改卡板设计,实现大倾角拉压垫加载的实施。
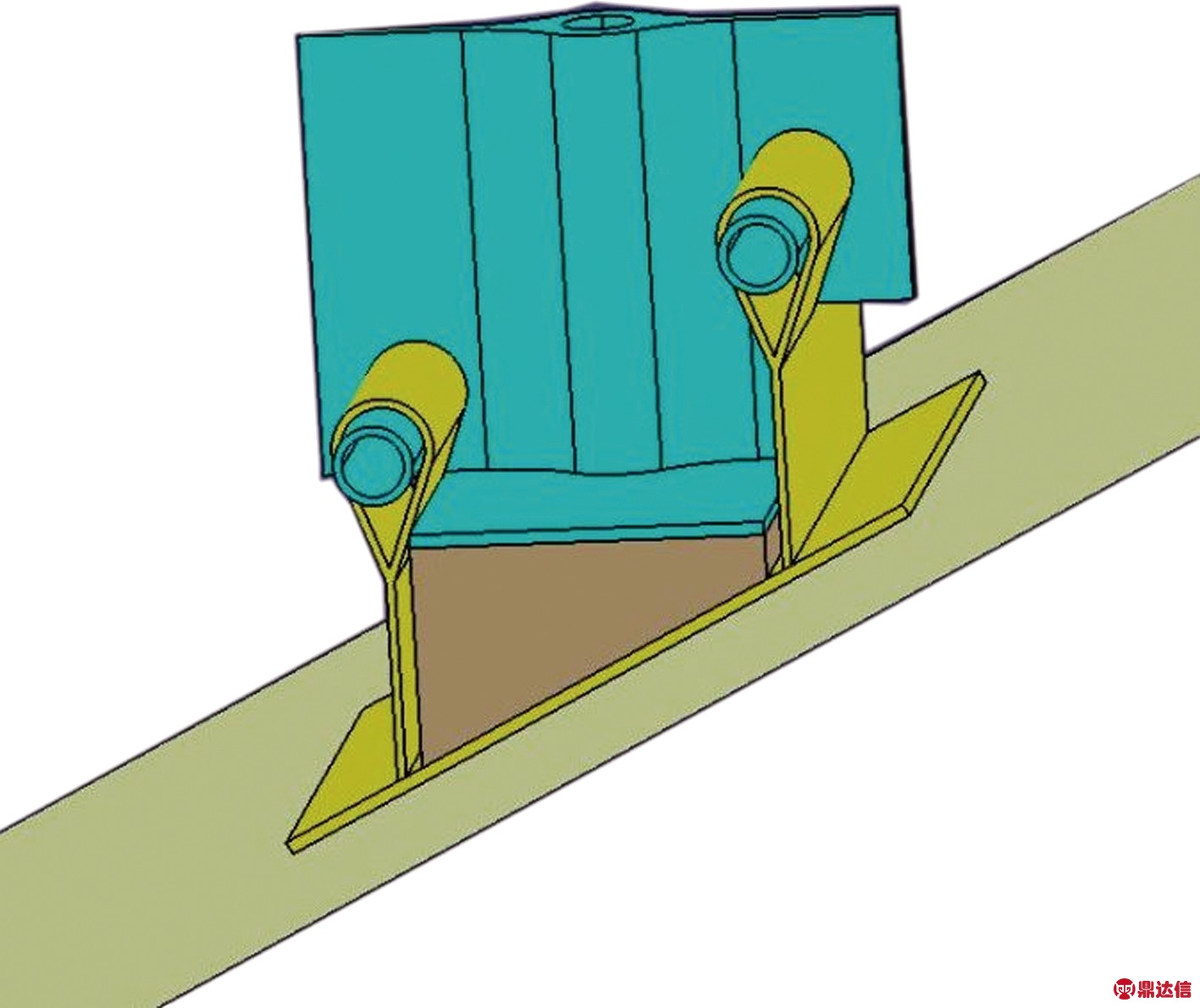
图4 大倾角胶布带拉压垫设计
Fig.4 Design of large dip for canvas tension /compression pad
铝棒半径从13 mm减小至9 mm,胶布带被铝棒拉直,胶布带孔成水滴形,如图4所示。在胶布带孔周长不变的情况下,定义铝棒距蒙皮增加高度为x,因为原半径13 mm铝棒距胶布带孔高度为13 mm,因此半径9 mm铝棒距离胶布带孔底端高度为x+13 mm拉直切线的对角为a,如图5所示。
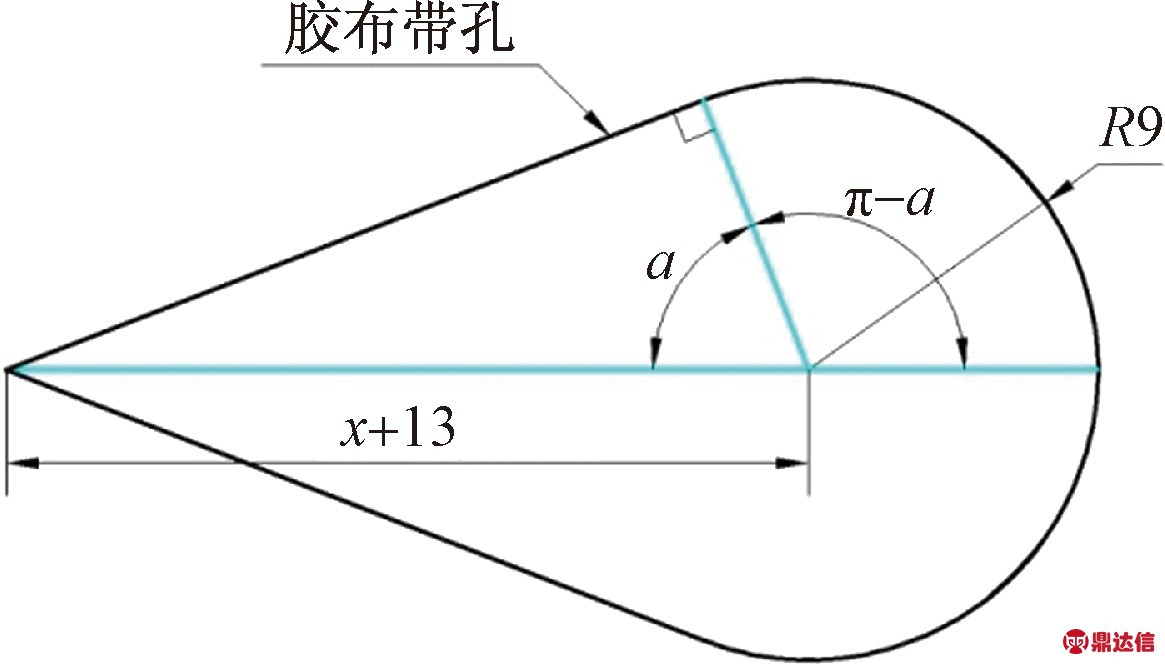
图5 水滴形胶布带孔示意图
Fig.5 Water droplet hole of canvas-pad diagram
由图5可得:
x=9cota-13
(1)
9tana+9(π-a)=13π
(2)
由式(2)可得:
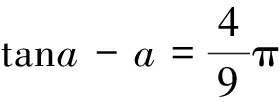
(3)
根据式(3)求角a,因主要为实际工程应用,所以不必求出a的精确解析解,求出满足一定精度的数值解即可。采用循环逼近法求出a的数值解,通过程序计算令a逐渐从0增大到π/2,步长为π/5 000。代入
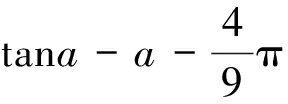
(4)
中,令式(4)最接近于0的值即为a的数值解。求出a数值解为1.203 607 0(即为角a的弧度),代入式(1)中,得铝棒距蒙皮增加高度x=12 mm。
通过将铝棒半径从13 mm减小至9 mm,可将木块一侧的最大高度增加至57 mm,压载载荷倾角最大值提高至arcsin(47/90)=31°。设计如图4的拉压垫加载方式,满足了该试验工况大倾角压载需求。
3 试验应用
3.1 试验方式
试验加载方式主要采用胶布带拉压垫-杠杆系统(如图2所示,用于施加压向载荷)和胶布带-杠杆系统(如图3所示,用于施加拉向载荷)施加载荷。加载设备安装图及胶布带拉压垫-杠杆系统加载试验现场图如图6、图7所示。
试验数据的良好线性规律以及良好重复性是试验真实有效的两个必要条件,下面从这两个方面对试验数据进行分析。
3.2 试验数据线性分析
某飞机结构静力试验中,得到压载部位部分应变测量数据和位移测量数据如图8、图9所示。
由图8可以看出,由于试验厂房受到如噪声、电磁波等干扰,应变-载荷曲线会产生波动,如2号应变片载荷曲线在80%载荷状态下产生较小的波动。
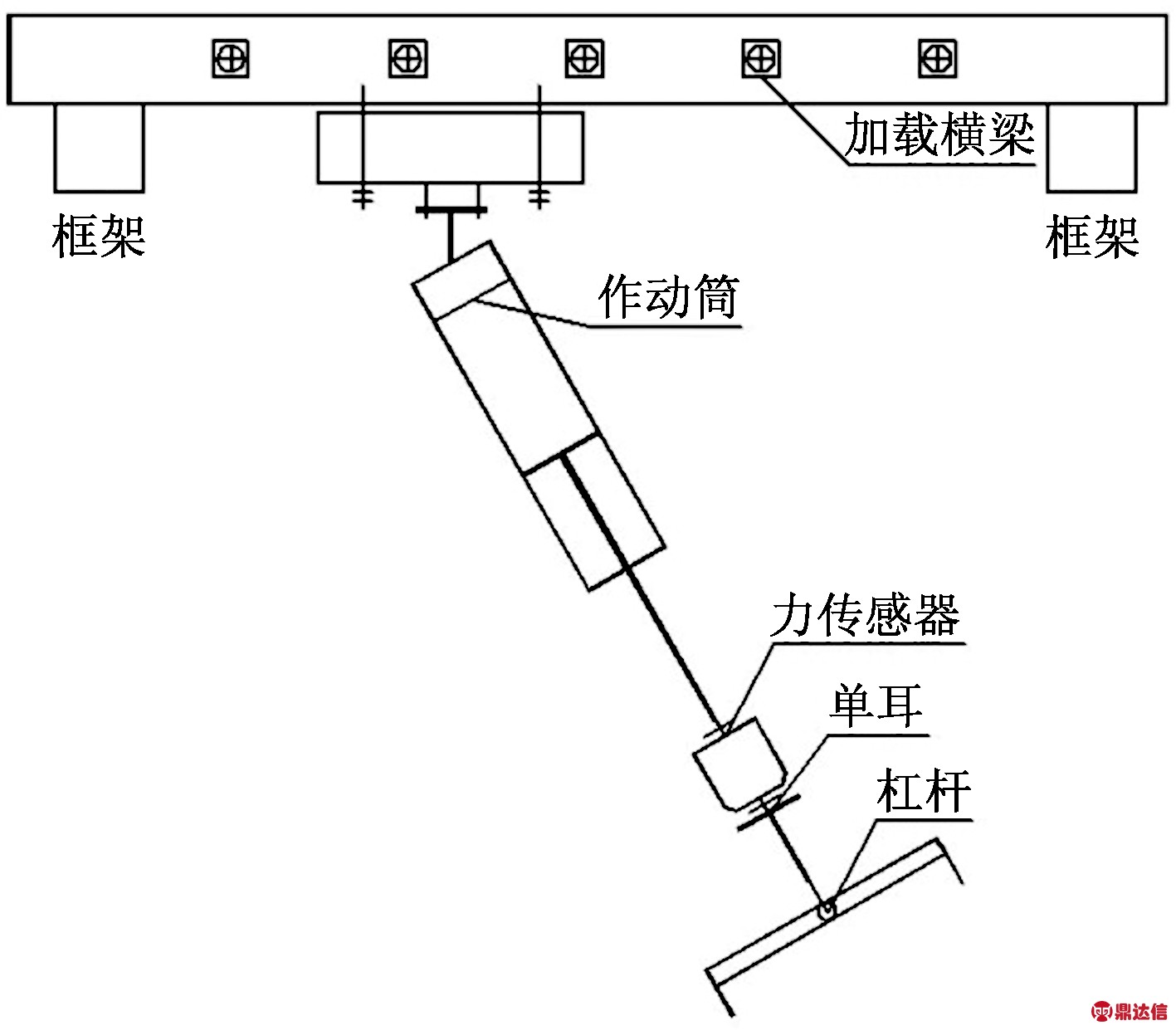
图6 加载设备安装图
Fig.6 Installation of load equipment diagram
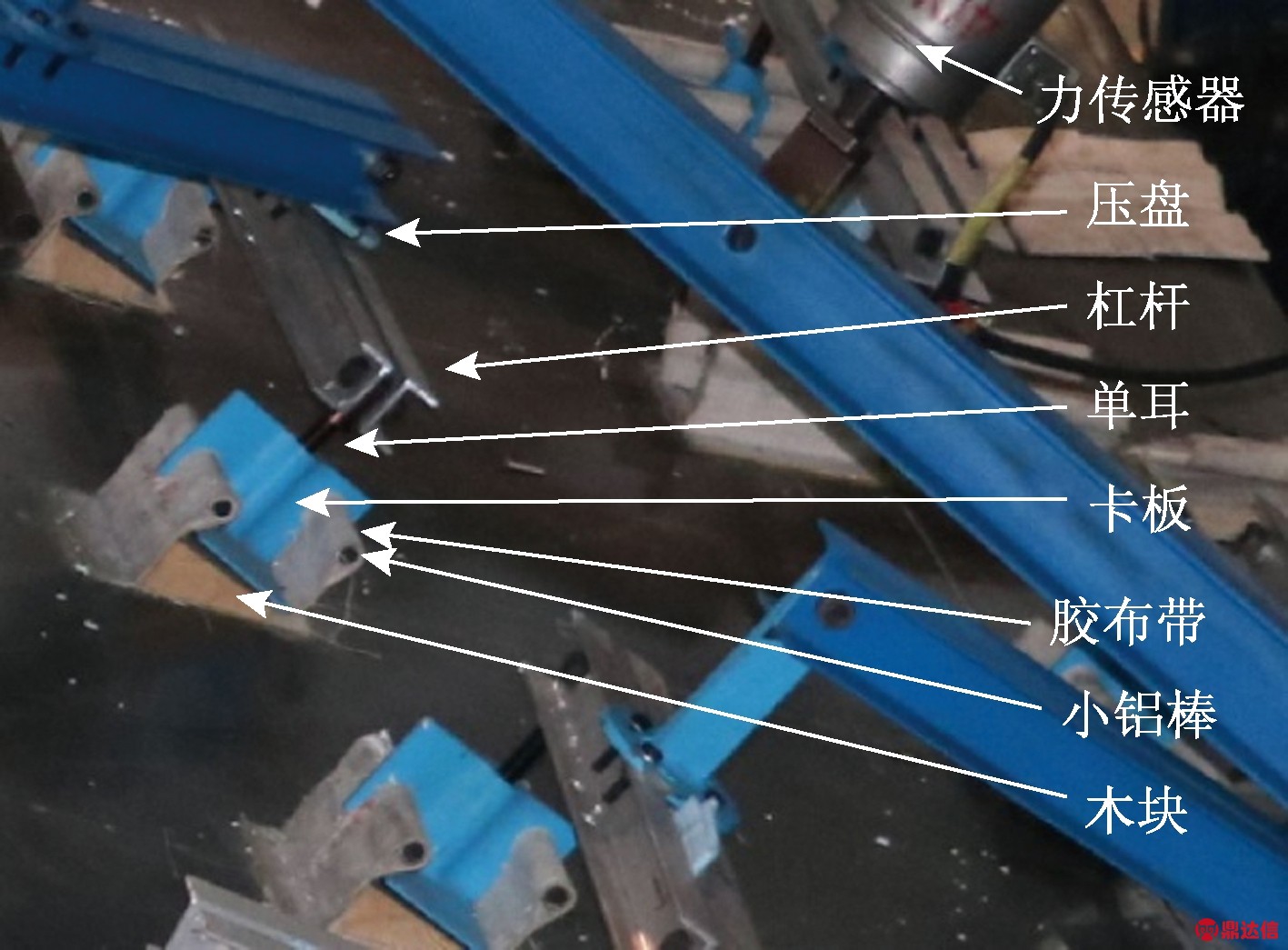
图7 胶布带拉压垫-杠杆加载系统试验现场图
Fig.7 Canvas tension /compression pad-lever loading system test diagram
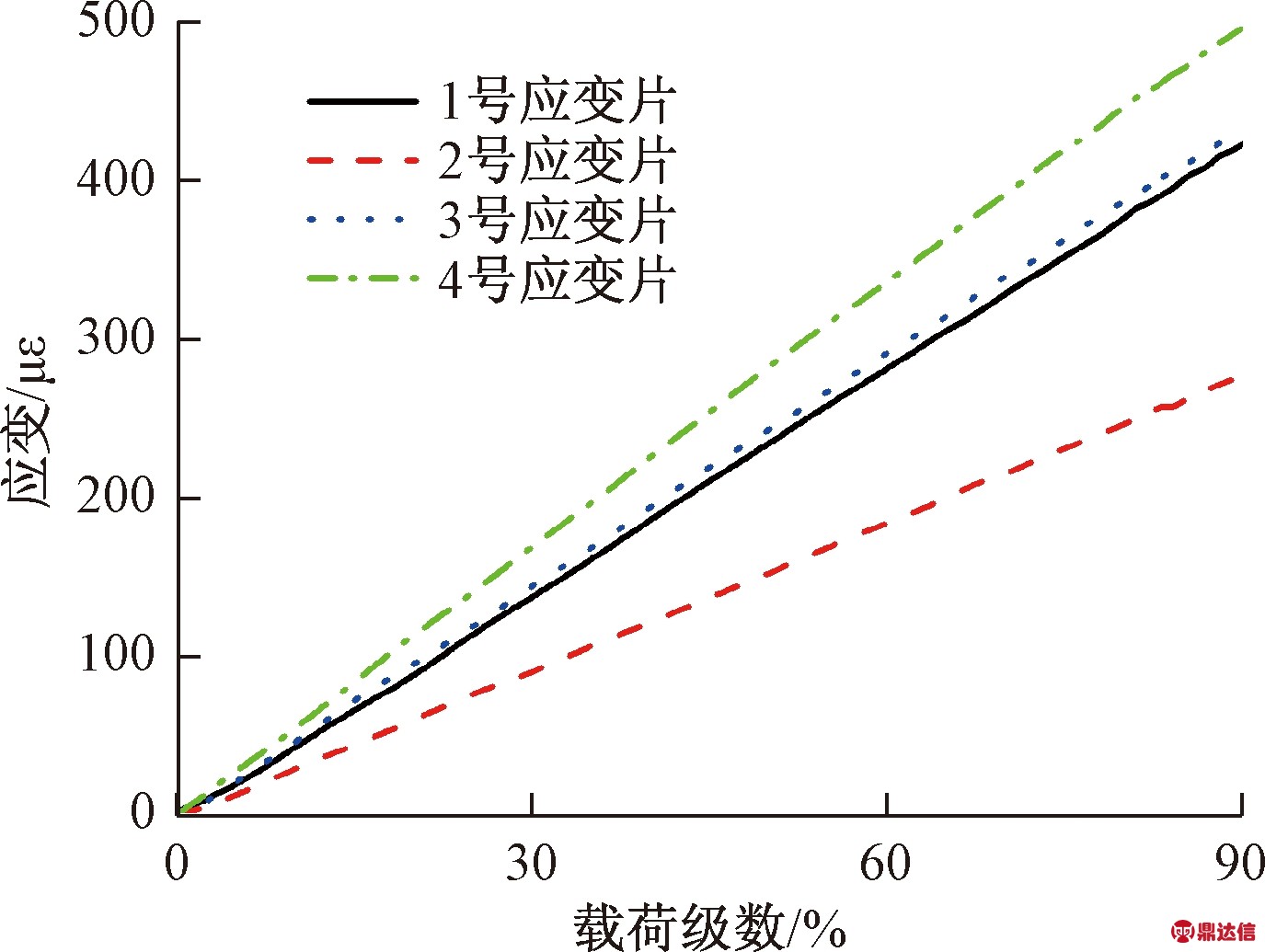
图8 部分应变片应变-载荷曲线
Fig.8 Part of strain gauges stain-load curve
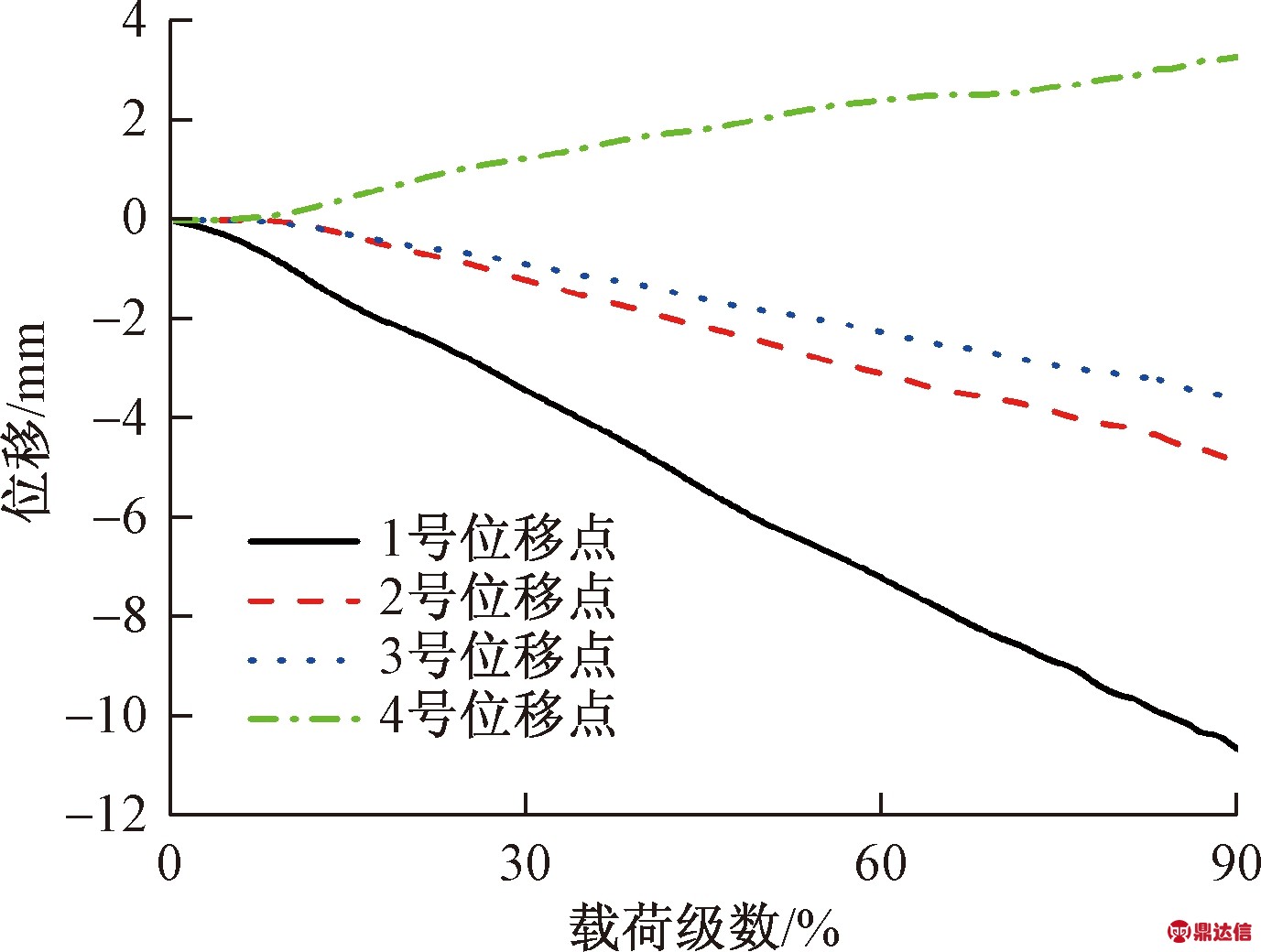
图9 部分位移传感器位移-载荷曲线
Fig.9 Part of displacement sensors displacement-load curve
IT技术的不断发展使得培养应用型人才的大学有必要及时更新教材。将当今社会流行的新方法、新技术源源不断地填充到实际的教学内容中,为学生毕业能够更好地融入行业,具备企业要求的能力打下结实的基础。然而,目前信息工程学院部分教材的内容仍然延续了传统教育的理念,离企业、行业要求的理论和技术还有很大的差距。这需要将大学教科书与企业需求相结合,将理论与实践联系起来,并利用各自的优势。它更符合社会的要求和时代的发展,编写适合应用型人才的新教材。
由图9可以看出,位移数据同样受到噪声、电磁波等干扰,因此,位移-载荷曲线也会产生波动,对于位移变化量较小的位移测量点(如2号、3号和4号点位移变化量不超过4 mm),干扰对位移结果影响较大,产生波动较为明显。因此需要进行线性修正,采用线性拟合方法对该三点进行线性修正。
由于载荷为0%的情况下,位移为0 mm,因此位移线性拟合方程截距为0,拟合公式为
y=bx
(5)
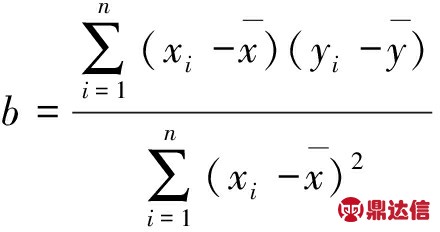
(6)
根据式(5)、式(6)得出2号、3号和4号位移测量数据的线性拟合方程,修正后的2号、3号和4号位移测量点位移-载荷曲线如图10所示。
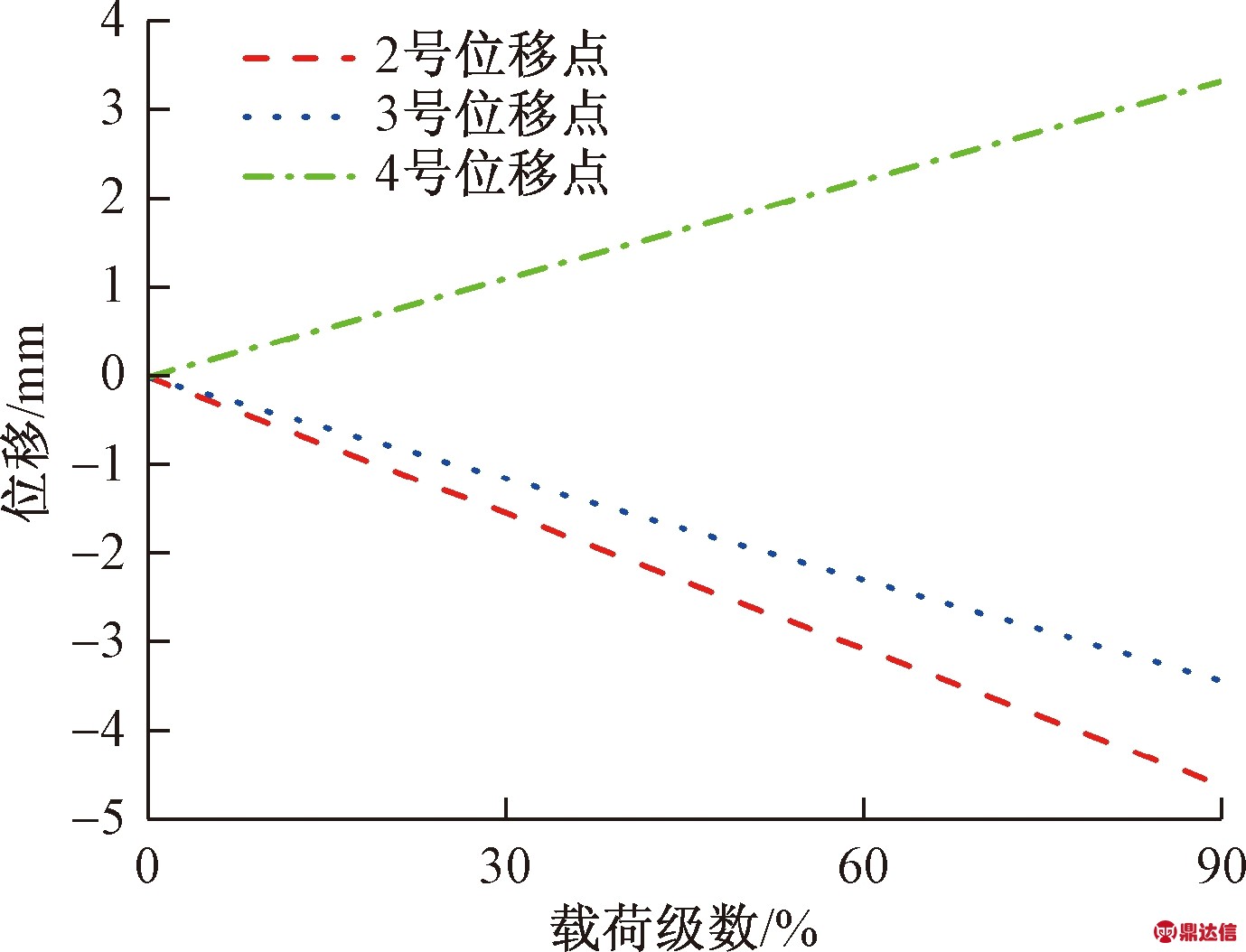
图10 线性修正位移-载荷曲线
Fig.10 Linear correction for displacement-load curve
通过线性修正,应变测量数据和位移测量数据线性良好,满足试验要求。
3.3 试验数据重复性分析
一般情况,一个工况试验要至少做两次,对比两次试验数据。考虑到试验受到现场噪声和电磁波的干扰,重复性误差低于5%则说明试验重复性良好,数据真实有效。
对相同载荷状态下同一测量点的数据进行重复性分析。重复性误差计算公式如下:

(7)
式(7)中:δ为重复性误差;L1为第1次测得的某点位移、应变值;L2为第2次测得的同一载荷状态下某点位移、应变值。
选取同种载荷状态(67%载荷)下的试验数据进行重复性分析,结果如表1所示。
表1 67%载荷状态数据重复性分析
Table 1 Data repeatability analysis of 67% load status
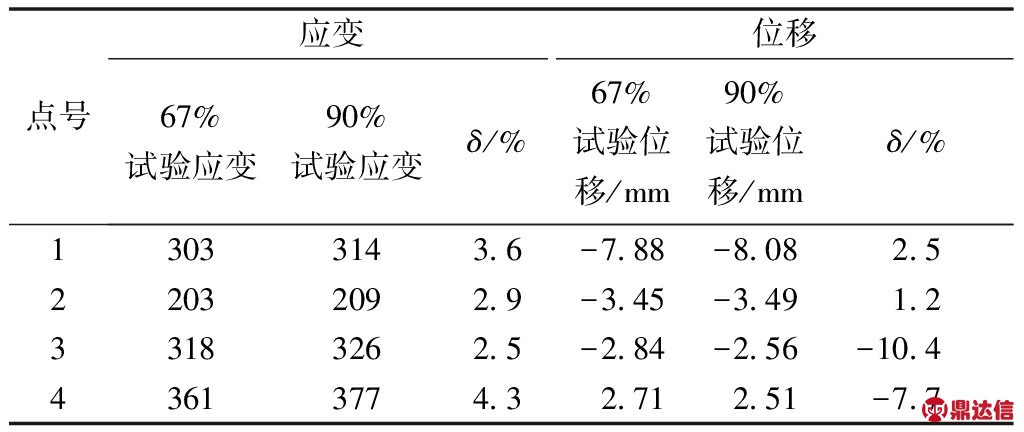
由于3号位移点和4号位移点位移变化量较小(67%载荷状态下测量结果不到3 mm),因此实际测量误差对该两点结果影响较大,导致它们的重复性误差较大。由表1可以看出,大部分测量点试验结果重复性误差都在5%以内,满足试验重复性要求。
4 结论
(1)在不更换胶布带前提下对胶布带拉压垫进行改进,将压载载荷最大倾角由原来23°提高至31°,满足大倾角压载试验需求。
(2)可以通过缩小铝棒直径进一步提高最大倾角角度,该方法为以后大倾角压载试验提供了解决方案。