摘 要:叶片泵对油液的清洁度要求较高,油液中混入的少量固体颗粒会引起泵内部摩擦副磨损而使其间隙增大,影响叶片泵的容积效率。为了探明颗粒在叶片泵配流副油膜内部的分布状态及其对配流副损坏机制,该研究使用理论分析、数值模拟和试验测试的方法,研究油液中的固体颗粒对高压叶片泵配流副油膜特性的影响。应用Fluent内置的两相流模型,分别改变固体颗粒直径(0.5~13 μm)和固相体积分数(0.2%~1%)、泵的工作压力和转速,开展子母叶片泵配流副油膜内部的固相体积分数分布与温度分布的数值模拟,并对数值模拟结果进行验证。结果表明,油液中的固体颗粒基本不影响配流副油膜的压力数值及其分布,但会引起排油区的油膜温度降低。随着颗粒直径的增大,吸油区油膜固相体积分数减小,最大变化量为0.25%,排油区油膜固相体积分数增大,最大变化量为0.35%,油膜固相体积分数整体上呈增大趋势变化。叶片泵容积效率随着固体颗粒直径的增大而下降,二者近似线性关系。随着颗粒固相体积分数的增加,油膜固相体积分数整体呈增大的趋势变化,最大变化量为0.72%,引起叶片泵容积效率下降,且颗粒固相体积分数与容积效率之间呈非线性关系。油膜表面的温度随颗粒固相体积分数的增加而减小,吸油区各区域油膜温度变化较小,排油区油膜温度最大变化量为2 K。配流副油膜受压差流影响较大的区域内固相体积分数随工作压力升高而减小,最大变化量为0.3%,油膜表面各区域的温度有所上升,核心区域温度变化量为4 K。油膜大部分区域的油膜固相体积分数和温度都随着泵转速的增大而增大,影响较大的区域中固相体积分数最大变化量为0.2%,温度最大变化量为3 K。研究结果可为高压叶片泵配流副的设计提供参考。
关键词:泵;压力;温度;数值模拟;油膜;固体颗粒
0 引 言
高压叶片泵因噪声小、体积小以及流量均匀等优点在流体传动领域得到了广泛应用[1-2]。但泵内的摩擦磨损会严重影响泵的工作寿命,这主要是由泵内摩擦副的运行状况决定的,尤其是配流副建立的润滑油膜特性[3]。高压叶片泵的配流副是轴向处于转子、定子与配流盘之间的密封间隙部分,径向处于轴孔边缘至定子内环的区域,油膜遍及吸油区和排油区。叶片泵工作时,需要配流副滑动面间形成适当的润滑膜,这层润滑膜能够起到润滑剂的作用。油膜太薄,会使配流盘磨损甚至烧盘,油膜太厚,起不到密封作用,且加剧油液的泄漏,因此通过设计和优化得到合理的配流副结构,对提高泵的工作效率和工作寿命有重要作用[4]。叶片泵在实际工程应用中对油液清洁度的要求较高,在环境较为恶劣情况下工作时,由于液压系统自身的振动或外界环境的影响,依然会使油液中混有少量金属颗粒随液压油流动。固体颗粒对泵内的配流副运行状况有较大影响,不仅会影响其内部油液的换热效率,还会对配流盘产生一定的磨损[5-8]。在高压叶片泵中液压油不仅是传送能量的介质,更是配流副两金属表面之间良好的润滑剂,所以在对配流副设计优化之前必须对其流场特性有一定程度的了解,特别是对在恶劣工况下油液含固体颗粒物对配流副油膜特性影响的研究则显得非常重要。
目前含固体颗粒油液摩擦副的摩擦磨损及流场仿真有如下研究成果:马砚英等[9]针对大流量高性能柱塞泵常出现的“烧盘”和“咬死”问题,从磨损机理和原因等方面探讨,提出配流盘的磨损除了与配流副及其油膜设计的合理性有关外,油液中的污染颗粒物是造成配流盘磨损的主要原因。晏小伟[10]采用几种海水泵的污染磨损机理研究方法,将海水中杂质的磨损尺寸、特征参数、海水泵关键摩擦副的尺寸以及对污染磨损的控制进行了有效结合。邓耀初等[11]根据污染敏感度进行理论分析,开展不同工况下齿轮泵污染敏感度的试验设计,与实际情况相结合得到了不同压力和温度下齿轮泵污染寿命影响的机理模型。刘勇等[12]建立了污染颗粒与磨损参数的线性关系,分析了污染颗粒浓度、齿轮泵结构参数等因素对齿轮泵流量的影响,从理论上提出了齿轮泵污染耐受度的估算方法。除此之外,还有一些针对油液含颗粒情况下液压阀流场仿真方面的研究[13-15],为含固体颗粒油液叶片泵配流副油膜的流场仿真提供了一定借鉴。
为了探明油液中固体颗粒对高压叶片泵配流副油膜特性及泵的容积效率影响,改进高压叶片泵配流副设计方法,改善叶片泵对油液清洁度要求较高现状。本文通过理论分析和数值模拟方法得到不同颗粒参数和工况参数下,配流副中颗粒的分布以及油液含颗粒时的油膜温度分布情况,试验测试得到颗粒参数对叶片泵容积效率影响规律,以期为后续的润滑参数建模奠定基础,为恶劣工况条件下高压叶片泵配流副的设计和优化提供一定的理论基础。
1 高压叶片泵配流副结构
本文研究对象为25VQ-21A型双作用子母叶片泵,额定压力为21 MPa,额定转速为1 500 r/min,排量为67.5 mL/min。额定工况下,流量为101.25 L/min,容积效率为88.58%。其泵芯结构如图1a所示,转子两侧各安装一块配流盘,转子上面沿径向放置10个叶片。转子在主轴的驱动作用下旋转,某一组前后叶片、转子外圆表面和定子内表面之间空间形成密闭容腔,即工作腔。叶片顶部沿定子内表面滑动,在定子内曲线矢径增大时,容腔油液体积增大,此时工作腔和吸油口接通,实现泵的吸油过程;反之,叶片顶部运动处定子矢径减小时,密闭容腔体积受压减小,此时和排油口连通,实现泵的排油过程[16]。
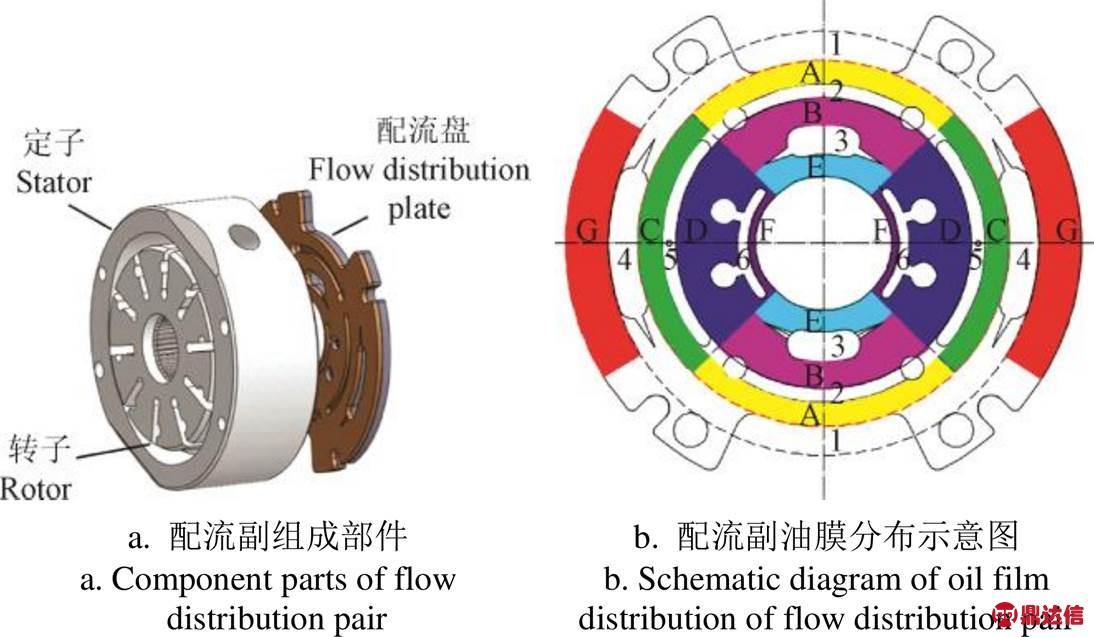
1.吸油口 2.吸油区均压槽 3.吸油区叶片底腔引油槽 4.排油口 5.排油区均压槽 6.排油区叶片底腔阻尼槽
A.吸油口与吸油区均压槽过渡区域 B.吸油区均压槽与叶片底腔引油槽过渡区域 C.排油口与排油区均压槽过渡区域 D.排油区均压槽与叶片底腔阻尼槽过渡区域 E.吸油区叶片底腔引油槽与轴孔过渡区域 F. 排油区叶片底腔阻尼槽与轴孔过渡区域 G.排油口外侧区域 下同。
1.Oil suction port 2.Pressure-equalizing groove in oil suction area 3.Oil groove for bottom of vane in oil suction area 4.Oil discharge port 5.Pressure-equalizing groove in oil discharge area 6.Oil groove for bottom of vane in oil discharge area
A. Transition area between oil suction port and pressure-equalizing groove in oil suction area B. Transition area between pressure-equalizing groove and oil groove for bottom of vane in suction area C. Transition area between oil discharge port and pressure-equalizing groove in oil discharge area D. Transition area between pressure-equalizing groove and oil groove for bottom of vane in oil discharge area E. Transition area between oil groove for bottom of vane in oil suction area and shaft hole F. Transition area between oil groove for bottom of vane in oil discharge area and shaft hole G. Out area of oil discharge port The same below.
图1 配流副结构与油膜分布示意图
Fig.1 Schematic diagram of flow distribution pair structure and oil film distribution
子母叶片泵油膜为配流盘与转子的配合间隙部分,双作用叶片泵配流副油膜遍及吸油区和排油区,且关于原点对称,配流盘上加工多个不同功能的油口和油槽,为了描述方便,对配流盘各部分油槽和油膜分布位置进行命名,文中涉及到的油膜区域分别定义为A、B、C、D、E、F和G区域,其中A~F区域为转子与配流盘相对滑动的核心区域,具体位置如图1b所示[17]。
根据双作用叶片泵的工作原理和结构可知,配流盘上有2个吸油口和2个排油口,则转子每转动1周,相邻两叶片形成的工作腔完成吸油和排油各2次,吸油区和排油区之间的区域属于过渡区域[18]。
2 含固体颗粒油液配流副油膜流场计算方法
2.1 油液中固体颗粒的运动方程
在对油液含固体颗粒时的流场进行数值计算时,除了要考虑质量守恒定律、动量守恒定律和能量守恒定律外,还要考虑其他相关方程[19]。当油液中含有固体颗粒时,颗粒和油液之间也必然会产生相互作用,在这种相互作用的过程中,流体和颗粒之间同样会发生动量转换和能量转换。在油液中运动的固体颗粒会受到多种力的作用,由于双作用叶片泵所要求的工作环境清洁度较高,固体颗粒在油液中的固相体积分数较低,故其主要受液体的阻力和其自身的重力作用[20-21]。
固体颗粒所受的重力是由于地球的吸引而使颗粒所受的力,颗粒重力Fg的计算公式如下:
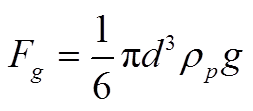
式中d为颗粒直径,m;ρp为颗粒的密度,kg/m3;g为重力加速度。
只要固体颗粒与流体之间存在相对运动,便有黏性阻力作用在颗粒上。实际上,颗粒在流体中的运动阻力受很多因素影响[22],包括阻力系数、颗粒形状及浓度等,运动阻力FD计算公式如下:
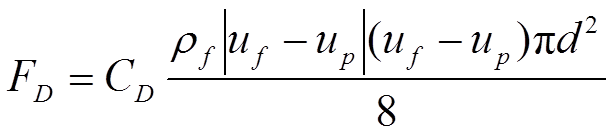
式中CD为阻力系数;uf为流体速度的张量分量,m/s;up为颗粒速度的张量分量,m/s;ρf为流体的密度,kg/m3。
阻力系数CD的取值需要结合颗粒的雷诺数Rep的数值范围来确定[23]。
Rep<1时:
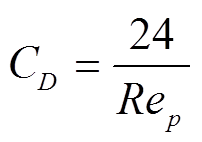
此时颗粒在流场中所受的运动阻力主要是颗粒与流体接触产生相对滑动时的黏性阻力。
1<Rep<1 000时:

此时颗粒在流场中的运动阻力不仅有颗粒和流体侧边由于相对滑动产生的黏性阻力,还存在形体阻力。
Rep>1 000时:
CD=0.44 (5)
此时颗粒的阻力系数为常数,即不再受到雷诺数Rep数值的影响,运动阻力的大小主要受到形体阻力影响。
2.2 配流副流体域计算模型的建立
使用Fluent软件对配流副流体域进行三维流场仿真,配流副的流体域包含油槽和油膜2部分。各油槽的功能、形状各异,所以油槽流体域采用非结构化网格,配流副油膜流体域采用六面体网格[24]。将2部分流体域的有限元网格模型导入ICEM软件进行合并,得到用于配流副油膜CFD解析的有限元模型。为了减少网格数目带来的误差,采用5种方案的不同密度网格对叶片泵的输出流量进行网格无关性验证[25],结果如表1所示。
表1 油膜流场仿真的网格无关性验证
Table 1 Grid independence verification for flow field simulation of oil film
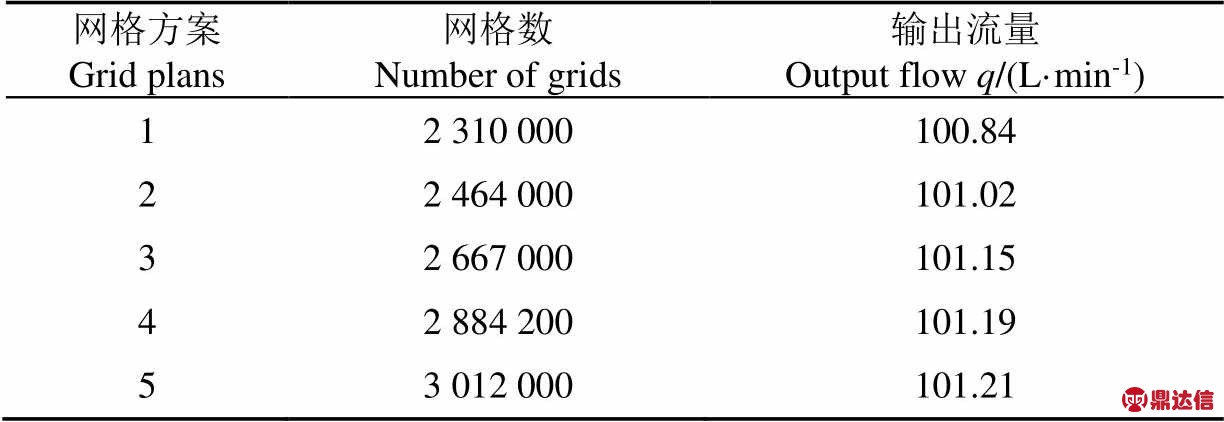
由表1可以看出,叶片泵输出流量随着网格数的增加而不断变化。当网格数达到2 667 000以上时,输出流量与泵额定流量的相对误差在0.1%以内,考虑到计算的准确性和经济性,选择网格数为2 884 200的第4种方案进行模拟计算。
根据油槽在子母叶片泵工作时所起的作用进行边界设置。将吸油口和吸油区叶片底腔引油槽表面设置为压力进口,油膜外环和内环属于泄漏面,设置为低压出口。吸油区和排油区均压槽所处的表面设置为高压进口,排油口和排油区叶片底腔阻尼槽表面设置为高压出口。油膜与阻尼槽和均压槽相接触的面设置为数据交换面。
2.3 配流副油膜流场数值计算的参数设置
叶片泵配流副密封区内部的油膜较薄,通常认为这部分流体区域为层流状态[26],因为是黏性流动,所以还需考虑油液的热交换,在能量方程中包含了黏性产生的热量。叶片泵工作传动介质选为工程机械液压系统常用的46号抗磨液压油,具体特性参数如表2所示。
表2 流体传动介质参数
Table 2 Medium parameters of fluid power transmission
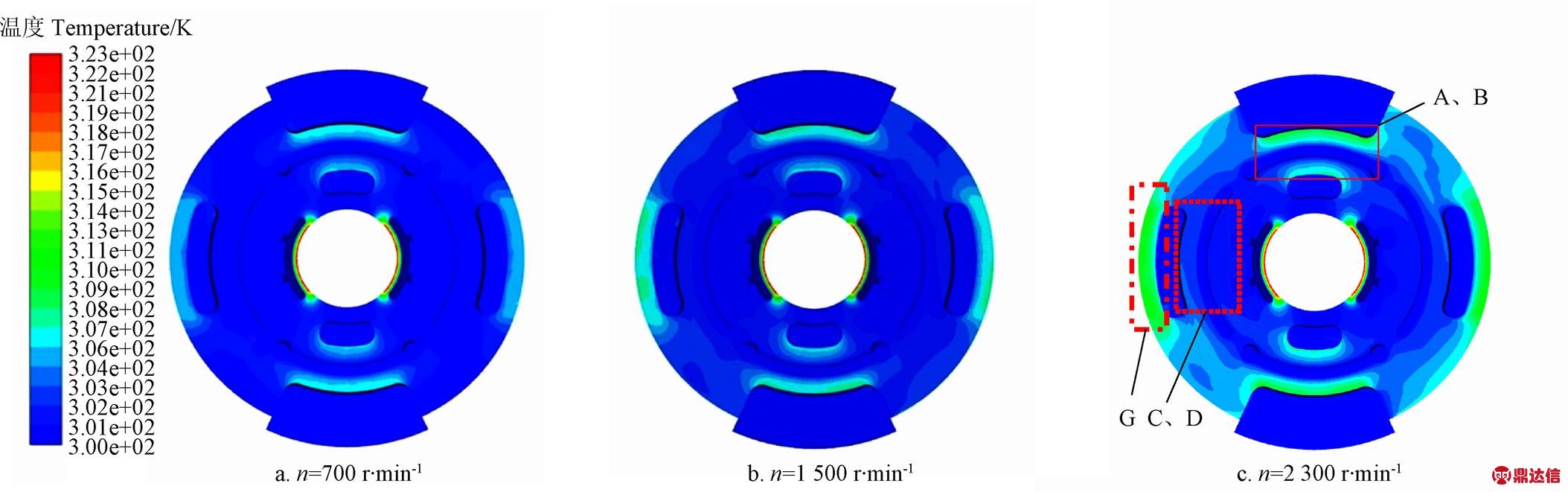
液压油中通常存在的污染物为铁质颗粒物,具体参数如表3所示。对颗粒在黏性流体中的流动进行分析时,必须考虑油液的表面张力作用[27],针对本文研究对象特点,设置其值为0.023 N/m[28]。在叶片泵工作时,配流副油膜内部油液会对颗粒产生曳力作用,作用在颗粒上的力与流体的滑移速度成正比,在层流状态下的阻力系数约为0.3[29]。
表3 固相介质主要参数
Table 3 Main parameters of solid-phase medium
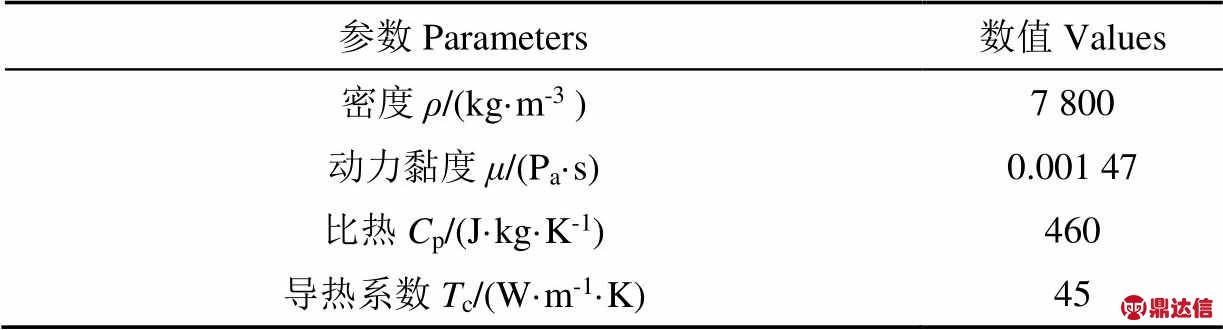
3 仿真结果分析
液压油颗粒度设置参考NAS1638-2011[30]和ISO4406-2017[31],将颗粒度等级按照颗粒最小尺寸段是5~10或者5~15 μm的间隔划分。正常摩擦副磨损颗粒为0.5~15 μm[32],结合高压子母叶片泵对油液清洁度要求,本研究选取的固体颗粒直径d分别为0.005、0.010和0.013 mm,油液中颗粒的固相体积分数φ为0.2%、0.6%和1%。
3.1 颗粒直径对子母叶片泵配流副油膜流场特性的影响
3.1.1 不同颗粒直径下油膜的压力分布
子母叶片泵工况参数取额定工作压力为21 MPa,额定转速为1 500 r/min;为了具有代表性,固相体积分数取中间值φ=0.6%;为了便于仿真结果的比较,颗粒直径取2个边界值d=0.005 mm和d=0.013 mm进行计算,得到配流副油膜压力分布如图2所示。
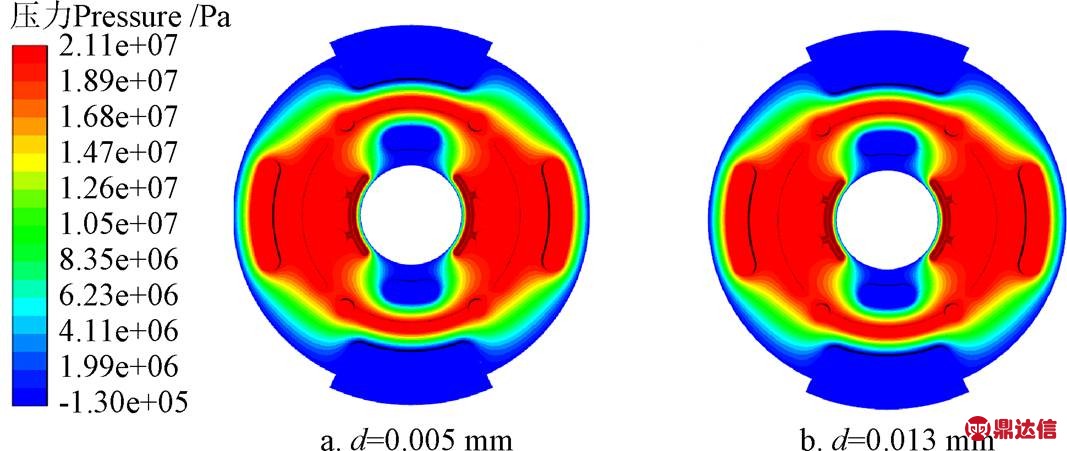
注:额定工作压力21 MPa;额定转速1 500 r·min-1;颗粒固相体积分数0.6%。下同。
Note: The rated working pressure is 21 MPa, the rated speed is 1 500 r·min-1, the particle solid-phase volume fraction is 0.6%. The same below.
图2 不同颗粒直径d下配流副油膜的压力分布
Fig.2 Pressure distribution of oil film in flow distribution pair under different particle diameters d
可以看出,图2所示的2种颗粒直径下,配流副油膜表面不同区域的压力和总体的压力分布规律基本相同。说明颗粒直径的变化对配流副油膜压力值及其分布影响较小,当油液中颗粒含量较小时,基本不会影响子母叶片泵配流副油膜表面的压力分布,所以本文不对配流副油膜的压力分布进行讨论。
3.1.2 不同颗粒直径下油膜的固相体积分数及温度分布
在子母叶片泵在工作压力21 MPa,转速1 500 r/min条件下,按照27 ℃实验室室温设置油液初始温度为300 K,颗粒固相体积分数φ=0.6%时,颗粒直径d分别为0.005、0.01和0.013 mm的配流副油膜的固相体积分数分布如图3所示。
从图3可以看出,随着颗粒直径的增大,配流副油膜固相体积分数多数区域呈增大趋势变化。但是也有几个区域固相体积分数有一定的下降。颗粒直径d=0.005 mm时,油膜表面的固相体积分数分布较均匀。随着颗粒直径的缓慢增大,在吸油区均压槽两侧(A和B区域)、排油口外侧(G区域)和排油区轴孔附近区域(F区域)油膜的固相体积分数逐渐减小,前两区域固相体积分数减小幅度约为0.25%,排油区轴孔附近区域(F区域)固相体积分数减小幅度最大,约为0.35%。在排油区均压槽与排油区叶片底腔阻尼槽过渡区域油膜的固相体积分数则稍有增大。
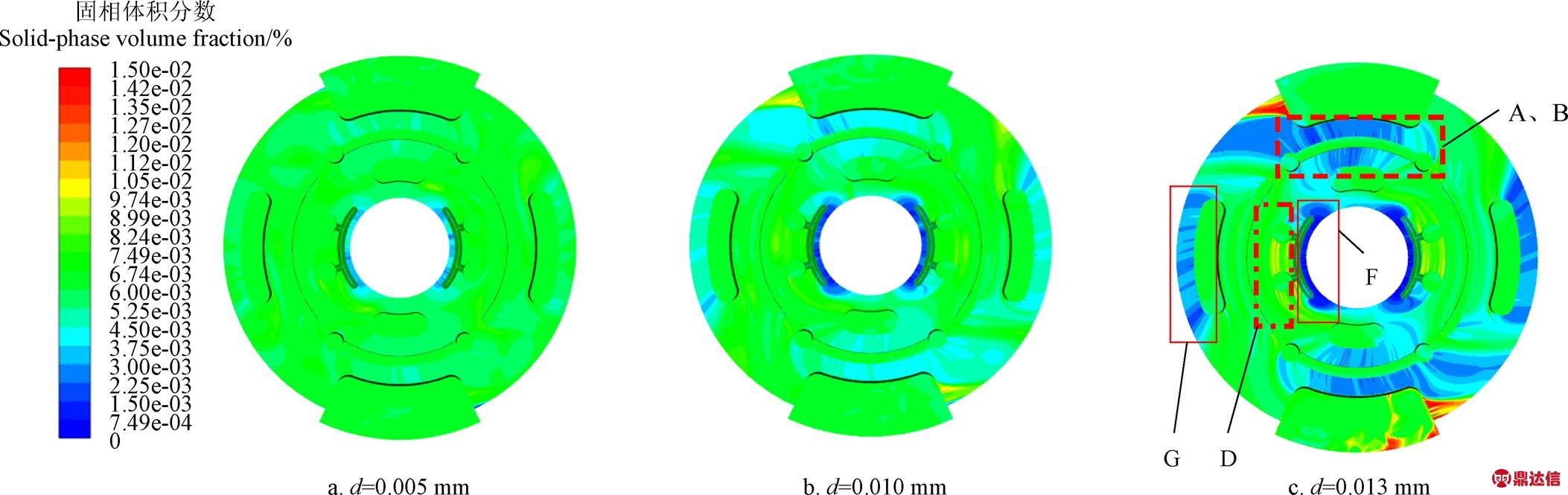
图3 不同颗粒直径d下配流副油膜的固相体积分数分布
Fig.3 Distribution of solid-phase volume fraction in the oil film of flow distribution pair under different particle diameters d
在压差作用下,吸油区均压槽内油液分别通过吸油口与吸油区均压槽过渡区域(A区域)、吸油区均压槽与叶片底腔引油槽过渡区域(B区域)向吸油口和吸油区叶片底腔引油槽流动。当颗粒直径增大后,颗粒受到的惯性力随之增强,从而使颗粒流速增大,导致这2个区域内更多颗粒物流入吸油口和吸油区叶片底腔引油槽,引起附近区域的固相体积分数下降,如图3c中A、B和D所示。排油区叶片底腔阻尼槽和排油口的油液分别向轴孔和壳体方向泄漏,当颗粒直径增大后,颗粒流速的增加会加速颗粒的泄漏,导致这2个区域(F和G区域)的固相体积分数变低,如图3c所示。排油区均压槽与叶片底腔阻尼槽过渡区域(D区域)只受到剪切流的作用,转子旋转带动前面高压区域油膜的油液流速加快,当颗粒直径增大后,该区域的颗粒加速沿转子转动方向运动,沿转动方向堆积的颗粒增多,固相体积分数相应增大,如图3c中D所示。
结合图1b知道,G区域不是滑动摩擦区域,F区域径向尺寸较小,对配流盘摩擦状况影响较小。随着颗粒直径的增大,虽然A、B区域固相体积分数有一定减小,而其他区域固相体积分数在增加,固相体积分数减小的区域小于增加的区域,增体上看配流副油膜固相体积分数呈增大趋势变化,增幅约为0.3%,油膜固相体积分数的增加,会加剧配流盘表面的摩擦,增大配流副间隙,引起泵的容积效率下降。
同样条件下,颗粒直径d分别为0.005、0.01和0.013 mm时,配流副油膜的温度分布如图4所示。
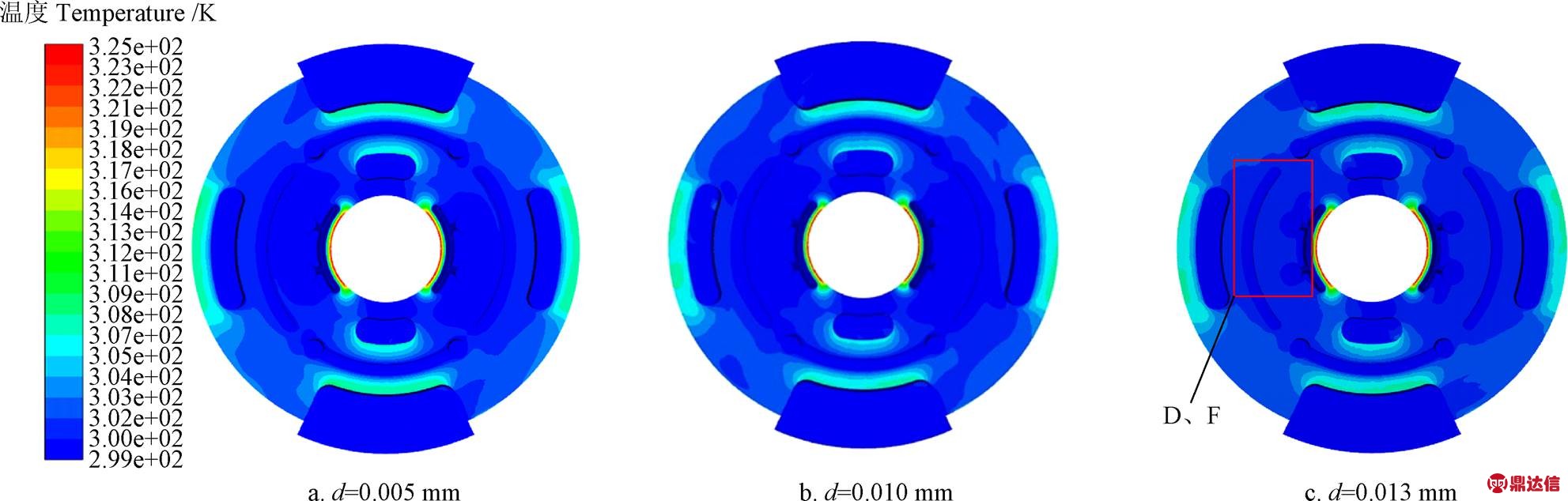
图4 不同颗粒直径d下配流副油膜的温度分布
Fig.4 Temperature distribution of the oil film of the flow distribution pair under different particle diameters d
配流副油膜内部细小而密集的颗粒对流体的运动产生较大的阻力,导致流体在运动时有很大的能量损失。从图4可见,在排油区均压槽径向向外和向内区域(C和D区域),由于不存在压差作用,油膜油液流速较慢,使颗粒在此区域堆积,导致两区域的油膜温度相比油液中不含颗粒时要小3 K。当颗粒直径增加后,虽然颗粒的速度有所增加,但由于油液带动大颗粒运动而消耗更多的能量,反而使这两区域的油液温度有所减小,在颗粒直径从0.005 mm增大到0.013 mm时,温度降低约2 K,如图4c中A、B、G和F所示。油膜其他区域温度变化与油液不含颗粒较为接近,存在颗粒直径增大引起油液流动消耗能量增加导致温度略有减小的现象。
3.2 固相体积分数对叶片泵配流副油膜流场特性的影响
在叶片泵工作压力21 MPa,转速1 500 r/min,油液初始温度为300 K,颗粒直径0.01 mm时,颗粒固相体积分数φ分别为0.2%、0.6%和1%条件下,配流副油膜表面不同位置的固相体积分数如图5所示。
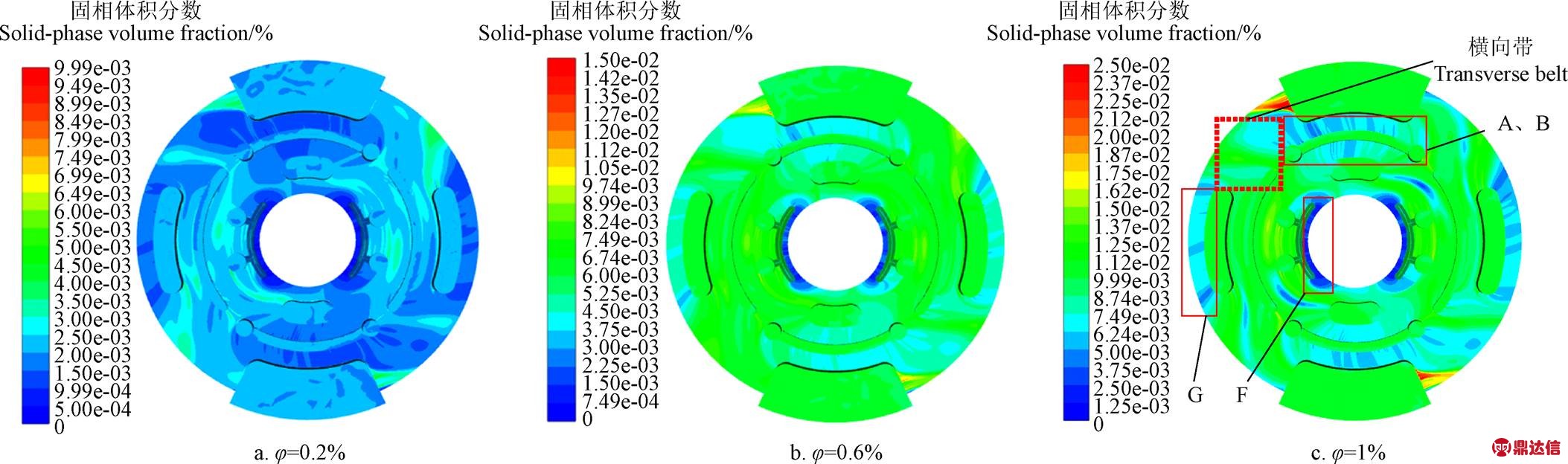
图5 不同固相体积分数φ下配流副油膜的固相体积分数分布
Fig.5 Distribution of solid-phase volume fraction in the oil film of flow distribution pair under different particle solid-phase volume fractions φ
从图5可以看到,颗粒固相体积分数增加后,油膜表面的多数区域的固相体积分数相应增加,增加幅度达到0.72%。但也有几个区域变化较小,排油区均压槽两侧区域(C和D区域)油膜剪切力的作用较弱,有大部分颗粒堆积,固相体积分数的改变并没有改变其分布规律。油液流动受压差流影响较大油膜区域的颗粒大部分流出,使得这些区域固相体积分数较低,当颗粒固相体积分数增大后,这些油膜区域的固相体积分数依旧较低,固相体积分数改变没有对颗粒运动产生较大影响,如图5c中A、B、G和F所示。
颗粒所受的惯性力随着半径的增大而增大,颗粒在不发生碰撞和破碎的情况下,也存在颗粒之间的相互作用。当颗粒固相体积分数增加后,一个颗粒与另一个颗粒的尾迹相遇时,后面的颗粒会拖拽前面的颗粒。在流化床中,这种相互作用结果会形成一个固相体积分数较低的区域横向带来分割固相体积分数高的区域 [33],这同样出现在配流副油膜表面的吸油口至排油口过渡区域,如图5c所示。
所以整体来看,随着颗粒固相体积分数的增加,配流副油膜固相体积分数也在增加,这会加剧配流盘表面的磨损,引起配流副间隙增大,泵的容积效率下降。
图6为不同颗粒固相体积分数条件下配流副油膜的温度分布图。
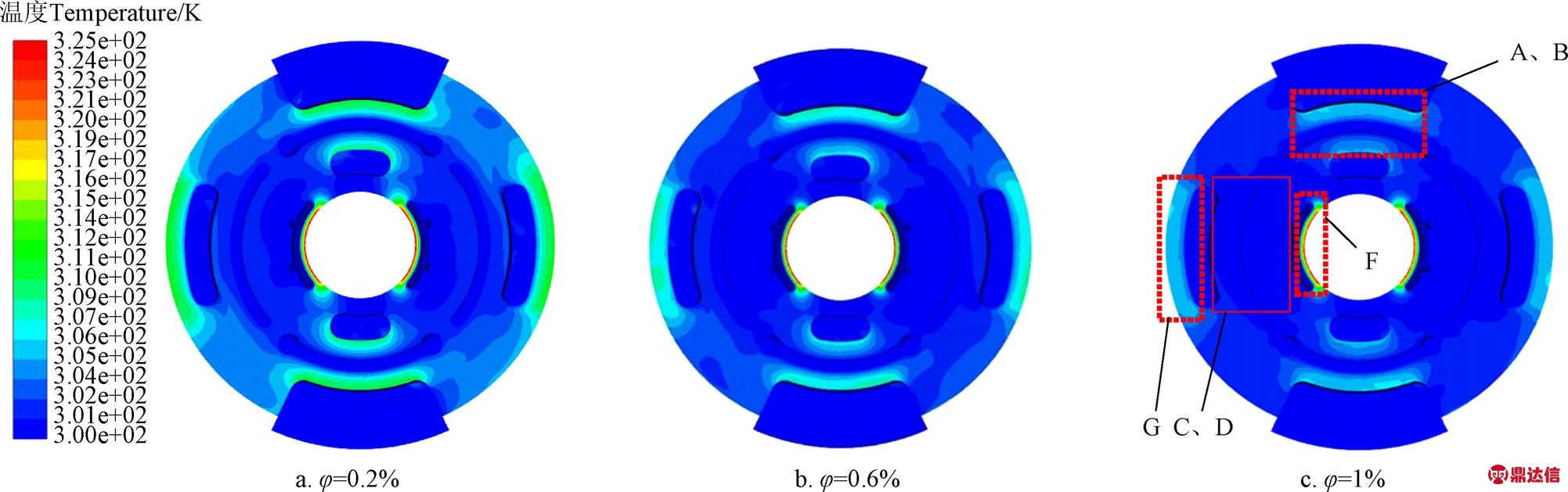
图6 不同颗粒固相体积分数φ下配流副油膜的温度分布
Fig.6 Temperature distribution of the oil film of the flow distribution pair under different particle solid-phase volume fractions φ
从图6可以看出,排油区油膜的温度随着颗粒固相体积分数的上升逐渐下降,温度降低最大值约为2 K,主要是A区域、B区域和D区域,如图6c所示。因为颗粒增多后,油液运动所受的阻力加大,会消耗更多的能量,从而使油膜温度在高固相体积分数区域较低。受压差流影响较大的吸油区均压槽两侧(A和B区域)、排油口外侧(G区域)、排油区轴孔附近区域(F区域)的油膜,在固相分数增加后,压差流带动颗粒运动需要耗费更多能量,使其温度等值区域减小,4个区域的温度值也略有减小,如图6c中的A、B、G和F所示,其中轴孔附近区域温度变化最小,不到1 K。
3.3 工况参数对含颗粒油液配流副油膜流场特性影响
3.3.1 不同工作压力下配流副油膜的固相体积分数和温度分布
在叶片泵的转速1 500 r/min,油液初始温度300 K,固相体积分数0.6%,颗粒直径0.01 mm时,得到的不同工作压力条件下配流副油膜表面的固相体积分数分布如图7所示。
从图7可以看出,随着工作压力的增大,压差流影响较大的区域固相体积分数变化较大,即吸油区均压槽的两侧区域(A和B区域)、排油口外侧区域(G区域)和排油区轴孔附近区域(F区域),压差流对这4个区域颗粒的作用逐渐增强,颗粒运动量增大,颗粒多数流入吸油口和吸油区叶片底腔引油槽内,导致这四个区域配流副油膜的固相体积分数随着工作压力的增大逐渐减小,固相体积分数降低最大的区域为F区域,如图7c中的A、B、G和F所示。
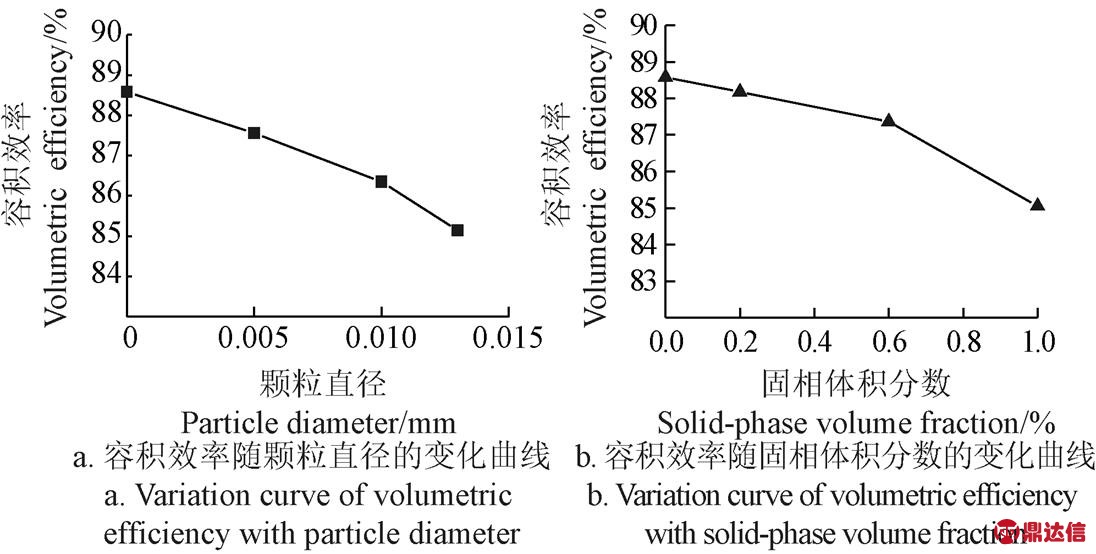
图7 不同工作压力Ps下配流副油膜的固相体积分数分布
Fig.7 Distribution of solid-phase volume fraction in the oil film of flow distribution pair under different working pressures Ps
4个区域油膜固相体积分数受工作压力具体影响情况也不一样。在工作压力较高时,剪切力对排油口外侧区域(G区域)颗粒运动的干扰要大于其它区域,导致在工作压力较高时其固相体积分数要高于吸油区均压槽两侧区域(A和B区域)。靠近排油区轴孔区域(F区域)径向宽度较小,工作压力较大时,压差流的作用增强,使得颗粒通过该区域向轴孔运动,导致该区域固相体积分数值最低。
从图7还可以看出,吸油区叶片底腔引油槽与吸油区轴孔过渡区域(E区域)的固相体积分数随工作压力升高而降低,这是由于该区域受到的剪切力随着工作压力的增大而减小,流向该区域的颗粒减少所致。在排油区均压槽两侧区域(C和D区域),存在的固体颗粒较少,其固相体积分数值基本不随工作压力的变化而变化。吸油口和排油口沿着转子转动方向一侧,如图7a所示,低压时固相体积分数较大,压力升高后固相体积分数降低。
在叶片泵工作压力从小到大变化时,分别监测图1b中A~G区域的油膜固相体积分数变化情况,结果如图8所示。
可以看出,配流副7个区域油膜的固相体积分数中,吸油区均压槽与吸油口过渡区域(A区域)固相体积分数最大,排油区叶片底腔阻尼槽与轴孔过渡区域(F区域)固相体积分数最小。
随着工作压力的增大,除排油口与排油区均压槽过渡区域(C区域)基本不变外,其他区域固相体积分数都在下降。排油区均压槽与叶片底腔阻尼槽过渡区域(D区域)、吸油区叶片底腔引油槽与轴孔过渡区域(E区域)变化较小,排油区叶片底腔阻尼槽与轴孔过渡区域(F区域)变化最大,变化值达到0.3%。排油区均压槽两侧区域(C和D区域)和吸油区叶片底腔引油槽至轴孔区域(E区域)固相体积分数变化最小,这与图7的结果相一致。
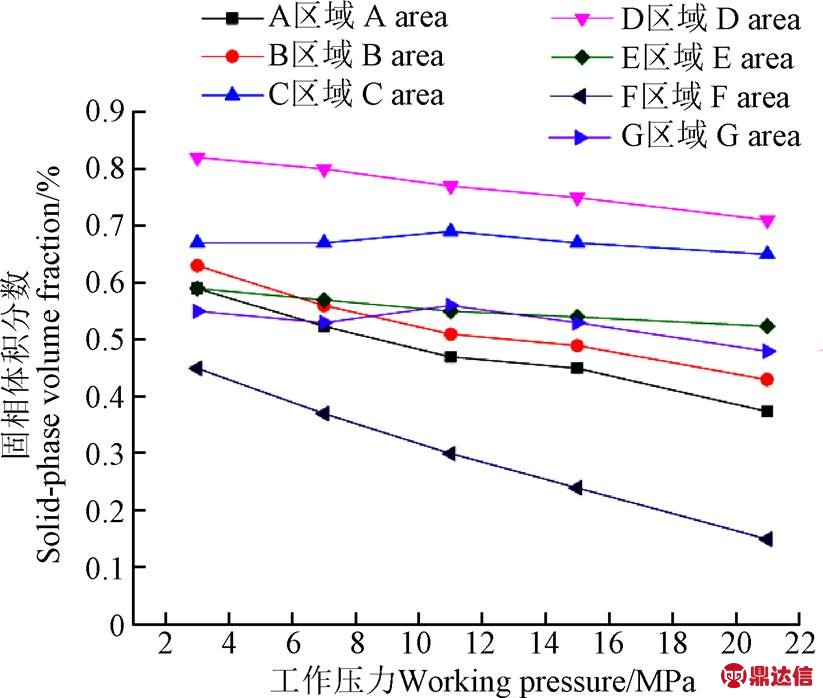
图8 油膜A至G区域固相体积分数随工作压力的变化曲线
Fig.8 Variation curve of solid-phase volume fraction with working pressure from A to G area of oil film
由此可见,增大工作压力能够减小配流副油膜的固相体积分数,提升配流副耐摩性能,减小配流盘机械磨损,提高叶片泵的容积效率。
相同参数条件下,仿真得到的不同工作压力条件下配流副油膜表面温度分布如图9所示。
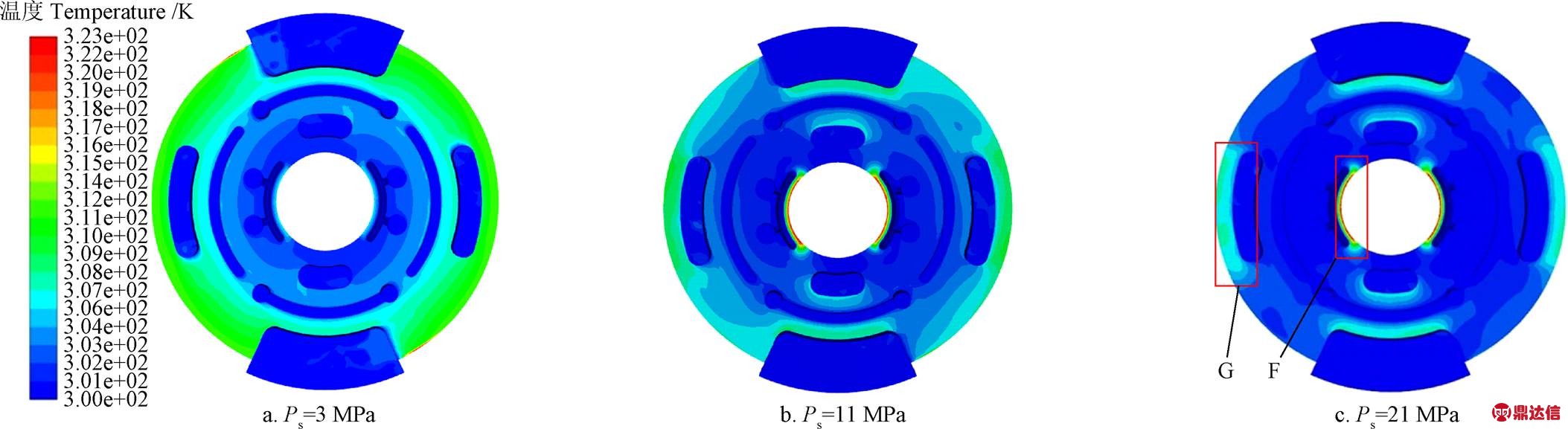
图9 不同工作压力Ps下配流副油膜的温度分布
Fig.9 Temperature distribution of the oil film of the flow distribution pair under different working pressures Ps
可以看出,配流副油膜大部分区域温度有随着工作压力的升高而升高的趋势。工作压力从3 MPa升高到21 MPa时,受到压差流影响较大的区域(A和B区域)温度升高了4 K。排油口外侧区域(G区域)和排油区叶片底腔阻尼槽与轴孔过渡区域(F区域)温度变化幅度较大,G区域最大变化量也为4 K,而F区域局部最大变化量超过10 K,如图9c所示。在排油口外侧区域(G区域),工作压力较低时,该区域向吸油口运动的颗粒较多,温度的等值区域较大,当工作压力升高后,该区域的颗粒在较大压差流的作用下沿径向向壳体方向运动,其温度等值区域面积变小,但油液和颗粒高速运动的共同作用使得该区域的温度值有一定的增加。
工作压力为21 MPa时,排油口与排油区均压槽过渡区域(C区域)的温度与油液初始温度较接近。造成这种现象的原因是在工作压力较低时,颗粒在剪切力的作用下沿转子转动方向运动,产生的能量使油膜表面温度有所升高。工作压力升高后,剪切流作用被压差流削弱,排油区的大部分颗粒沿转子转动方向运动变弱,颗粒的堆积对流体的流动造成一定的能量损失,使得该区域温度有较小幅度的下降。
同样从图1b可以看出,G区域和对油膜运动影响较小,F区域径向尺寸较小。整体上看,随着工作压力的升高,配流副油膜温度呈上升趋势。
3.3.2 不同转速下配流副油膜的固相体积分数和温度分布
图10为工作压力21 MPa,油液初始温度300 K,颗粒固相体积分数0.6%,颗粒直径0.01 mm时,不同转速条件下配流副油膜表面的固相体积分数分布图。
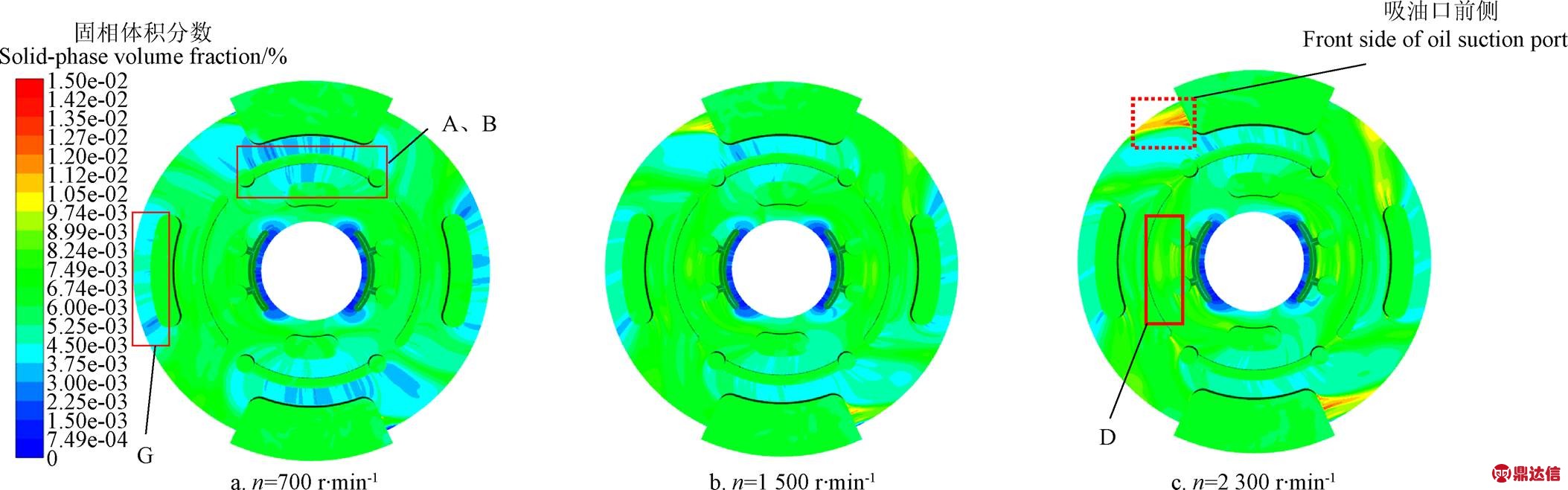
图10 不同转速n下配流副油膜的固相体积分数分布
Fig.10 Distribution of solid-phase volume fraction in the oil film of flow distribution pair under different rotating speeds n
从图10中可以看出,油膜固相体积分数受到转速影响主要是吸油区均压槽内外侧(A和B区域)和排油口外侧区域(G区域),如图10a中A、B、G所示,而其它区域影响较小。当转速较小时,上述区域的固相体积分数都较低,因为这3个区域颗粒运动受到压差流的影响较大,压差作用使大量的颗粒分别向吸油口、吸油区叶片底腔引油槽、轴孔和壳体方向流动,导致这3个区域的固相体积分数较低。转速升高后,油液和颗粒受到剪切流的作用加强,三个区域的颗粒因压差造成的泄漏减少,固相体积分数增大。
从图中还可看出,随着转速升高,排油区均压槽与叶片底腔阻尼槽过渡区域(D区域)油膜固相体积分数变化也较大。因为该区域颗粒的运动主要受剪切流的影响,转速增加使排油区均压槽附近的颗粒向该区域堆积,导致该区域固相体积分数较高的等值区域面积增大,且固相体积分数也随之增大,如图10c中D所示。另外排油区叶片底腔阻尼槽与轴孔过渡区域(F区域)固相体积分数较低,但是受转速变化的影响不大,这是因为该区域颗粒受到的惯性力较小,颗粒主要受压差流的作用而向轴孔方向泄漏。吸油口前侧固相体积分数随着转速的增加而增大,主要是由于剪切流强度增加所致,如图10c所示。
在叶片泵转子转速从小到大变化时,分别监测图1b中A-G区域的油膜固相体积分数变化情况,得到如图11所示的固相体积分数随转速的变化曲线。
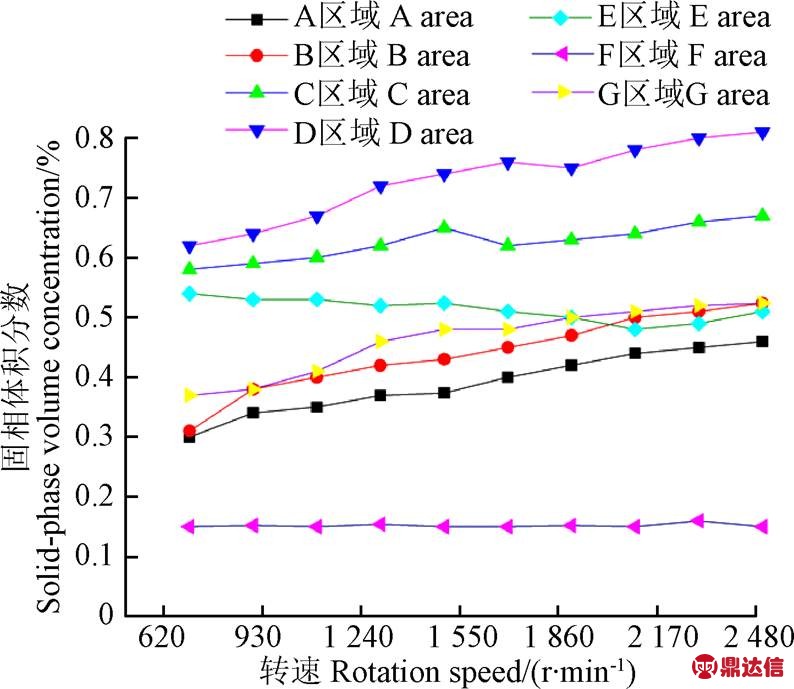
图11 油膜A至G区域固相体积分数随转速变化曲线
Fig.11 Variation curve of solid-phase volume fraction with rotating speed from A to G area of oil film
从图11可以看出,随着转速的增大,配流副7个区域油膜的固相体积分数变化中,只有排油区叶片底腔阻尼槽与轴孔过渡区域(F区域)、吸油区叶片底腔引油槽与轴孔过渡区域(E区域)基本不变,其余区域固相体积分数都是随着转速的增加而增大。核心区域A、B、C和D区域中,排油区均压槽与叶片底腔阻尼槽过渡区域(D区域)固相体积分数变化最大,变化值达到0.2%,这与图10的结果相一致。由此可见,配流副油膜固相体积分数整体上是随着转速的增加而增大,叶片泵低转速工作对减小叶片泵配流副油膜固相体积分数、提升摩擦特性有利。
图12为不同转速条件下配流副油膜温度分布图。可以看出,排油区叶片底腔阻尼槽与轴孔过渡区域油膜温度主要受压差流的影响,转速的变化对其影响不大。受压差流动影响较大的吸油区均压槽两侧区域(A和B区域),温度等值区域面积随着转速的增大而不断向左右两侧扩张,在转速从700 r/min升高到2 300 r/min时,温度值也有一定的增加,温度变化约为2 K,如图12c中的A、B所示。排油区均压槽两侧(C和D区域)主要受油液剪切流动影响,转速升高使得油液和颗粒受到的剪切力增大而引起温度升高,出现了由内向外沿半径方向扩散的扇形等值区域,如图12c中的C、D所示。转速增加后,排油口外侧区域(G区域)油膜的颗粒和油液受到的剪切力随之增强,导致其温度值也相应增加,在转速从700 r/min升高到2 300 r/min时,温度变为约为3 K,如图12c中G所示。
所以随着转速的增加,配流副油膜温度呈升高趋势变化,变化幅度超过2 K。转速对于油膜固相体积分数和温度变化的影响规律正好相反。
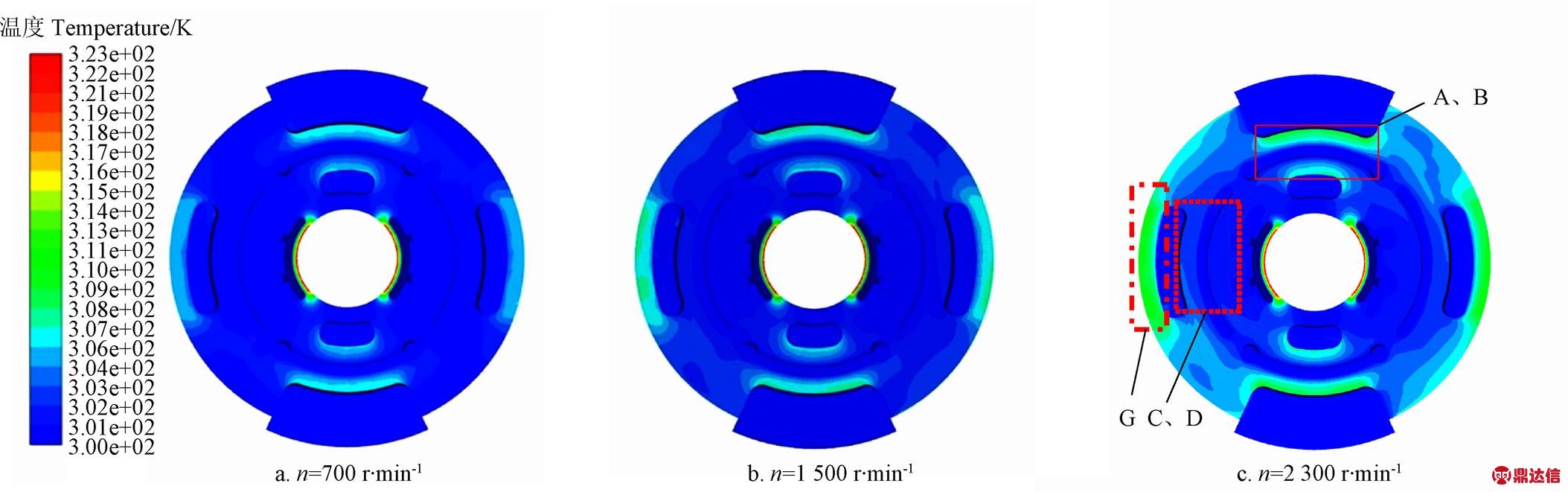
图12 不同转速n下配流副油膜的温度分布
Fig.12 Temperature distribution of the oil film of the flow distribution pair under different rotating speeds n
4 试验验证
为了验证不同直径和固相体积分数的颗粒对高压叶片泵配流盘摩擦磨损及容积效率影响,进行摩擦磨损试验和流量测试试验。因为高压叶片泵对油液清洁度要求非常高,不能将固体颗粒物直接加入油箱,因此采取间接方法进行验证,试验分为2步进行:
1)在摩擦试验机上安装叶片泵试验模型进行摩擦磨损试验。摩擦磨损试验系统由摩擦试验机、液压站、叶片泵试验模型和计算机组成。叶片泵试验模型内部尺寸和结构与仿真泵模型相同,液压站上安装有耐污的齿轮泵。叶片泵模型在试验机的电机驱动下运转,含颗粒油液通过齿轮泵以一定压力注入叶片泵试验模型。输入压力21 MPa,叶片泵转速1 500 r/min,油液中添加的颗粒直径分别为0.005、0.010和0.013 mm,固相体积分数分别为0.2%、0.6%和1%。每次试验1 h,试验机给配流副加载力为200 N,同时由摩擦试验机测试系统测试出摩擦系数,每组试验参数更换一对配流盘。摩擦试验前后用电子微精天平分别测出的配流盘质量得到其质量变化,通过下式得到配流盘的磨损率大小[34]:
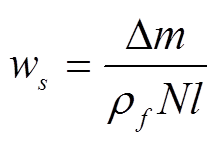
式中ws为磨损率,10-8mm3/Nm;Δm为磨损质量,kg;N为加载力,N;l为转子沿配流盘表面的滑动距离,m。
2)将摩擦磨损试验后的配流盘安装在液压泵流量测试系统的叶片泵上,加入清洁油液开展流量测试试验。系统工作压力21 MPa,转速1 500 r/min。叶片泵正常工作后,通过流量表读出安装有不同配流盘的叶片泵的输出流量,根据容积效率与流量之间的关系式计算得到叶片泵容积效率[35-36]。
叶片泵配流盘摩擦磨损试验系统和流量测试系统如图13所示。
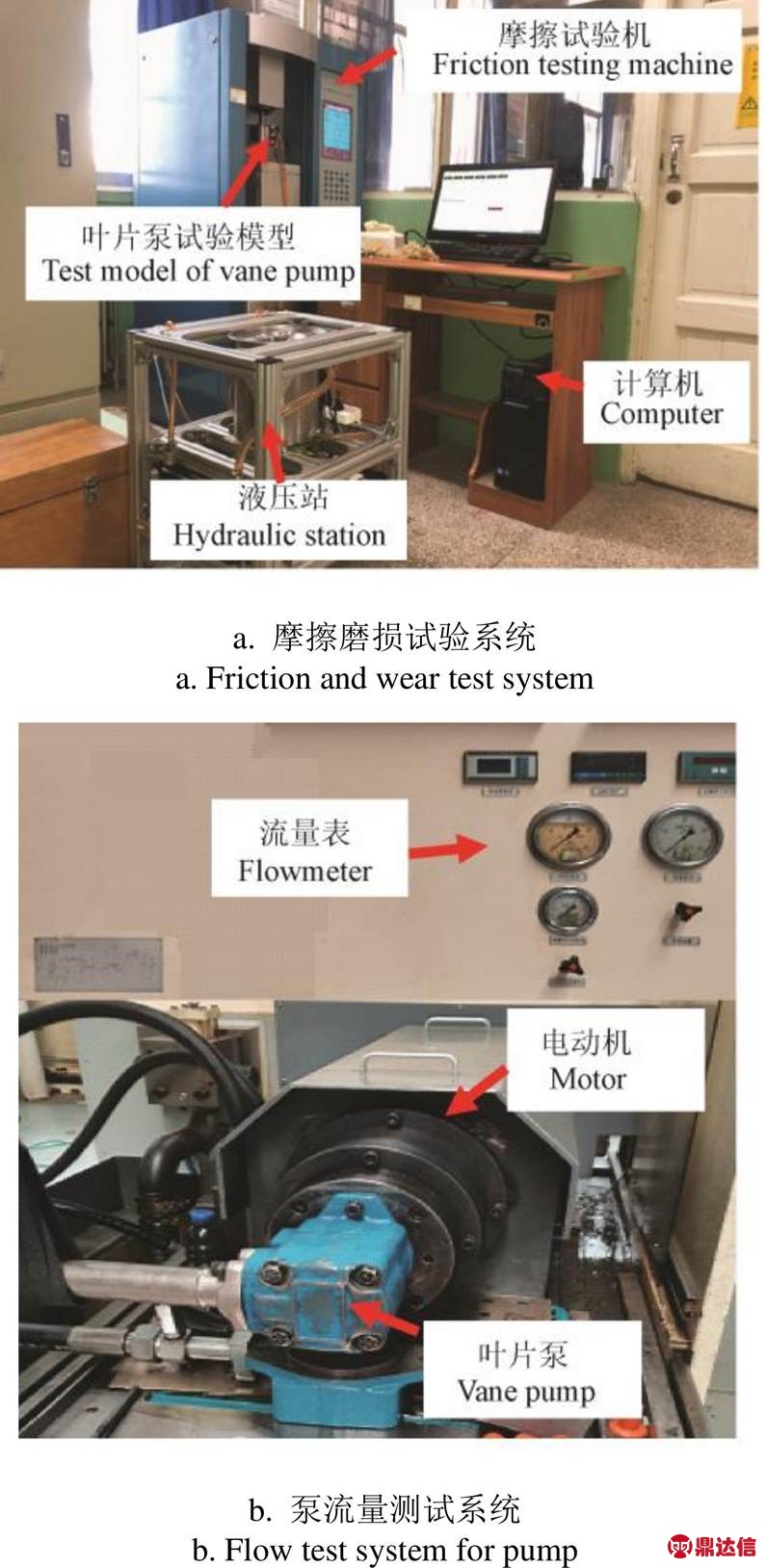
图13 叶片泵配流盘摩擦磨损试验系统和流量测试系统
Fig.13 Friction and wear test system for flow distribution plate and flow test system of vane pump
为了与上文仿真分析相一致,摩擦磨损试验系统的叶片泵试验模型输入压力21 MPa,转速1 500 r/min,所加入的颗粒物直径分别为0.005、0.01和0.013 mm,颗粒固相体积分数分别为0.2%、0.6%和1%。分2组进行摩擦磨损试验。
第1组试验:颗粒固相体积分数φ为0.6%,颗粒直径d分别取0.005、0.01和0.013 mm。
第2组试验:颗粒直径d为0.01mm,颗粒固相体积分数φ分别为0.2%、0.6%和1%。
2组摩擦磨损试验得到配流盘的摩擦系数和磨损率结果如表4所示。
从表4可看出,配流盘摩擦系数和磨损率随着颗粒直径和固相体积分数的增加而增大。在固相体积分数为0.6%时,颗粒直径从0.005增加到0.013 mm,摩擦系数增加了0.012,磨损率增大了2.73×10-8 mm3/N·m。在颗粒直径0.01 mm时,固相体积分数从0.2%增加到1.0%,摩擦系数增加了0.088,磨损率则增加了9.881×10-8 mm3/N·m。
表4 配流盘摩擦系数和磨损率测试结果
Table 4 Test results of friction coefficient and wear rate
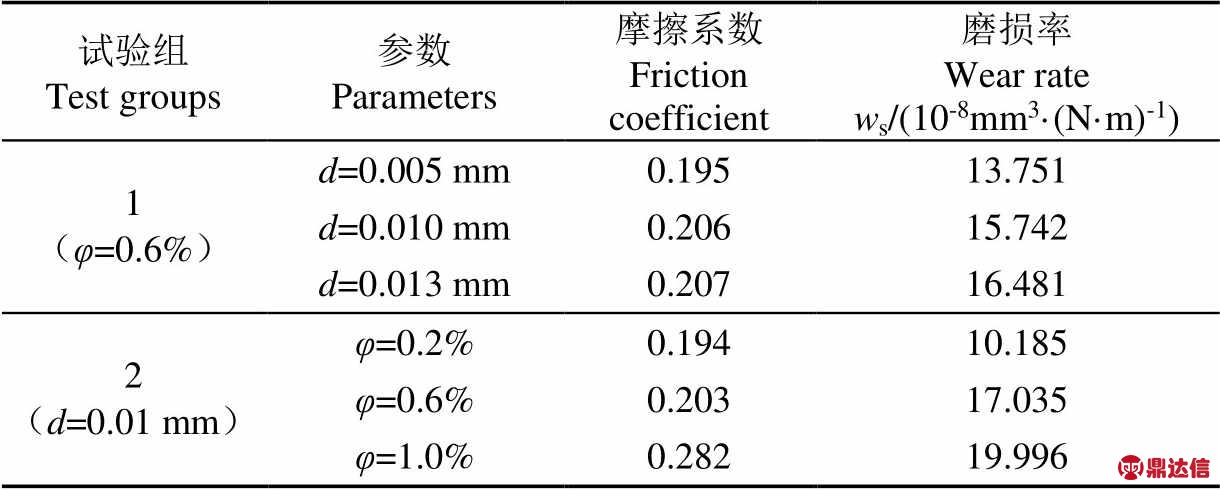
将经过摩擦磨损试验的配流盘分别安装到本文研究的叶片泵上,进行流量测试试验,叶片泵的工作压力和转速按照额定参数设定,根据测得的输出流量计算得到高压叶片泵的容积效率,容积效率随颗粒直径和固相体积分数的变化曲线如图14所示。其中第1个数据点为叶片泵在额定工况下使用清洁油液工作时的容积效率。
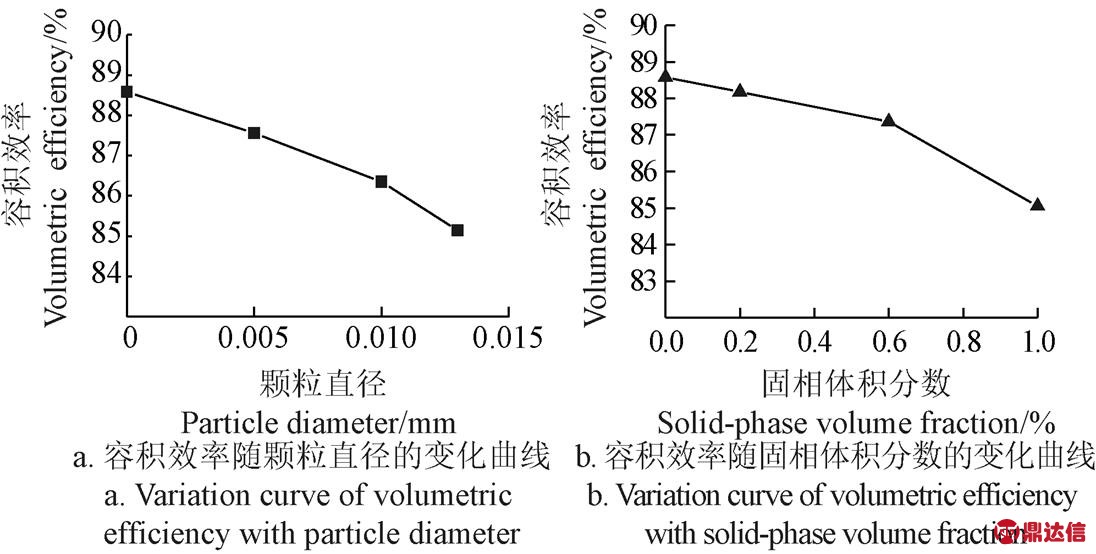
图14 叶片泵容积效率随颗粒直径和固相体积分数的变化
Fig.14 Variation of volumetric efficiency of vane pump with particle diameter and solid-phase volume fraction
从图14可以看出,与清洁油液相比,油液中固体颗粒的存在引起叶片泵容积效率的下降,主要原因是油液中固体颗粒使得高压叶片泵配流盘产生轻微的机械磨损,导致叶片泵的容积效率降低。油液中颗粒直径从0.005 mm增加到0.013 mm,容积效率从88.58%下降到84.95%,容积效率与颗粒直径之间近似呈线性关系。当油液固相体积分数从0增加到0.1%时,容积效率则从88.58%下降到85.05%,容积效率与固相体积分数之间呈非线性关系变化。可见叶片泵油液中含有固体颗粒时,随着颗粒直径和颗粒固相体积分数的增加,配流副油膜不同区域固相体积分数增加,加剧了配流盘表面的机械磨损,导致其容积效率下降。
油液中的颗粒直径和固相体积分数、泵的工作压力和转速等参数对配流副油膜固相体积分数及温度变化的影响不同,工作压力和转速的增大引起油膜温度上升,而固体颗粒直径和固相体积分数增大则引起油膜温度的下降。除了颗粒直径增大引起油膜固相体积分数减小外,泵的工作压力、转速和油液中颗粒的固相体积分数增大均引起油膜固相体积分数增大,特别是受剪切流动影响的区域变化较大。
为了降低配流副摩擦系数、减少摩擦生热,在叶片泵运行中,应该尽量保持额定工作压力和转速工况。但叶片泵工作在低压或者高转速工况能够得到较优的配流副油膜特性,因此,在配流盘设计中,应重点应关注油膜固相体积分数分布较大的区域,即固体颗粒堆积位置,特别是排油区均压槽与叶片底腔阻尼槽过渡区域(D区域),在不改变叶片泵容积效率的前提下,可以采用减小排油区叶片底腔阻尼槽尺寸,将配流盘D区域形状调整为双圆弧扇形,深度约为0~0.01 mm的凹槽,一方面便于油液中固体颗粒的堆积,减小配流副摩擦,另一方面在叶片泵预升压区,能够实现从高压排油口向低压工作腔内的阻尼引油作用。
5 结 论
本文在不同的颗粒固相参数、泵工作压力和转速条件下,对含颗粒油液的高压叶片泵配流副油膜内部的流场进行数值模拟,得到不同条件下的油膜固相体积分数和温度分布及固体颗粒对叶片泵容积效率的影响情况,主要结论如下:
1)油液中颗粒直径变化对配流副油膜固相体积分数和温度分布有一定的影响,而对压力大小及分布几乎不影响。吸油区固相体积分数减小,最大变化量为0.25%,排油区固相体积分数增大,最大变化量为0.35%,整体上油膜固相体积分数呈增大趋势。叶片泵容积效率随着颗粒直径的增大而下降,二者近似线性关系。颗粒直径增加导致排油区油膜温度降低,最大温度变化量为2 K。
2)随着颗粒固相体积分数的增加,配流副油膜固相体积分数整体呈增大趋势,最大变化量为0.72%,导致配流盘磨损加剧,引起叶片泵容积效率下降。油膜表面温度随着固相体积分数的增大而减小。吸油区各区域油膜温度变化较小,排油区油膜温度最大变化量为2 K。
3)随着叶片泵工作压力的升高,配流副油膜以压差流为主的区域固相体积分数减小,且变化幅度较大,最大变化量为0.3%;剪切流为主的区域固相体积分数变化较小。油膜所有区域温度都随着工作压力的升高而升高,核心区域温度变化量为4 K。
4)配流副油膜的固相体积分数整体上随着转速的增加而增加。其中核心区域的吸油口与吸油区均压槽过渡区域(A区域)、吸油区均压槽与叶片底腔引油槽过渡区域(B区域)、排油口与排油区均压槽过渡区域(C区域)和排油区均压槽与叶片底腔阻尼槽过渡区域(D区域)中,D区域的油膜固相体积分数受泵转速的影响最大,最大变化量为0.2%。油膜大部分区域的温度值随转速增大而增大,温度最大变化量为3 K。