摘要:为了获取射流自吸式离心泵内部流动信息,以一内置射流喷嘴的自吸式离心泵为研究对象,建立了各过流部件三维水体,采用了RNG k- ε湍流模型,通过6组网格无关性检查,确定了计算所需网格,运用CFX 14.0流场分析软件数值模拟预测了7种不同工况下外特性和内部流动,得到了全流场压力、速度等物理量变化规律,并将数值模拟结果与开式实验台测试结果作了对比分析。结果表明,设计工况下数值模拟与实验扬程、轴功率和效率的相对误差为2.63%、6.16%和14.29%,泵实际效率较低,其值为15.68%;当流量Q<3.5 m3/h时数值模拟和实验的功率曲线呈近似水平直线,变化很平缓;喷嘴到直线段之间的速度分布沿旋转轴对称,扩散段和叶轮进口之间速度呈上大下小分布,液流不均匀进入叶轮进口;L=0.148 m处是静压、速度和湍动能耗散率等物理量剧烈变化的分界点,静压在此处为最小值,而速度和湍动能耗散率为最大值。数值计算结果为该泵性能预测设计提供了直观的理论依据。
关键词:射流自吸式离心泵 性能预测 数值模拟
引言
射流自吸式离心泵是在普通离心泵的进口处增设一个带“文丘里管”的自循环射流器[1],使普通离心泵抽水实现自吸性能。射流自吸式离心泵具有结构新颖、体积小、质量轻、操作方便、自吸时间短等优点,主要适用于无电源地区和丘陵地区农作物的喷灌及排涝等场所[2]。射流自吸式离心泵分为外混式和内混式:外混式射流自吸离心泵由外置射流器和普通离心泵组成;内混式射流自吸离心泵由内置射流器和普通离心泵组成。根据采用的压出室类型又可将射流自吸式离心泵分为蜗壳式和导叶式两种。
目前,由于内混式结构复杂,三维建模较困难,射流自吸式离心泵的研究以外混式居多[3-6],由于射流自吸式离心泵的结构复杂,大部分研究停留在经验和简单的外特性实验[7-8],关于泵内流场的相关理论较为欠缺,尤其对泵运行过程中内部三维湍流流动规律的研究更少,这势必影响对射流自吸式离心泵水力性能和机械性能的研究。
为了全面地研究射流自吸式离心泵内部流场,本文采用CFD数值模拟的方法,结合国内外学者对射流自吸式离心泵的成果,探索射流自吸式离心泵的设计要点和内部流动规律等,为设计小流量、高扬程、高自吸高度的射流自吸式离心泵提供支持。
1 计算策略
1.1 湍流流动控制方程
定常流动计算采用的是二阶隐式时间推进法,湍流模型采用RNG k-ε湍流模型[9-10]。RNGk-ε模型的基本思想是把湍流视为受随机力驱动的输运过程,通过频谱分析的方法消去其中的小尺度涡并将其影响归并到涡粘性中,以得到所需尺度上的输运过程。该模型与标准k-ε模型区别只在于ε方程中增加了一个附加生成项,反映了主流的时均应变率 Eij,改善了精度[11]。
射流自吸式离心泵内不可压缩流体的三维湍流采用雷诺平均动量方程表示为
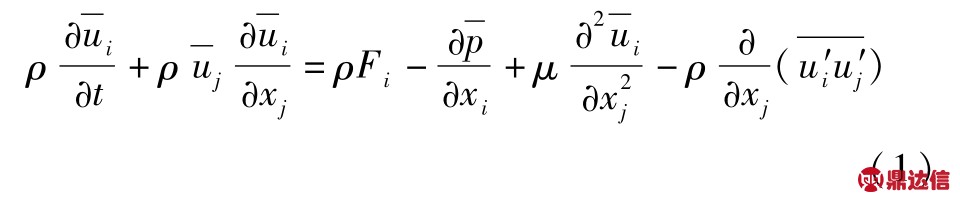

式中 ρ——流体密度 κ——湍动能
——平均雷诺应力
μt——湍流粘性系数
ε——湍流耗散率系数
δij——克罗内克尔数
i——i方向平均速度
j——j方向平均速度
Fi——体积力 μ——动力粘度
xi、xj——i、j方向的长度
采用RNG k- ε双方程模型使雷诺平均方程封闭,其形式为

式中j——应变率张量 νt——运动粘度
R——ε方程中的附加源项 S——应变曲率
模型参数 Cμ=0.084 5,C1ε=1.42,C2ε=1.68,αk=1.0,αε=0.769,β=0.012,η0=4.38。
1.2 射流自吸式离心泵几何模型
本文所研究的带有内置射流器的射流自吸式离心泵的基本参数为:设计流量 Qd=3 m3/h,设计扬程 Hd=30 m,额定转速 n=2 900 r/min,叶轮比转数ns=22,叶轮外径 D2=159 mm,叶轮进口直径 D1=40mm,叶轮出口宽度b2=4mm,叶轮叶片数Zy=6,导叶叶片数 Zd=6,喷嘴直径djet=10 mm,泵进口直径Ds=40 mm。该射流自吸式离心泵为内混式,压水室为导叶,泵部分的总装图如图1所示。
为了使得计算模型尽可能与装配图一致,本文应用Pro/E三维造型软件对包括口环间隙、前后泵腔的所有过流部件进行了造型,模型进、出口延伸长度分别为进、出口直径的4倍和6倍,如图2所示。
1.3 网格处理及无关性检查
网格是数值模拟的基础,合理的网格生成是数值模拟的关键所在,一般占整个数值模拟过程时间的60%~80%,而且射流自吸式离心泵过流部件几何模型的网格生成需要更多的时间来完成。一般网格的好坏直接影响数值模拟的精度和解的正确性,因此,对网格的要求一般包括:贴体性、光滑性、正交性和合理分布性等。
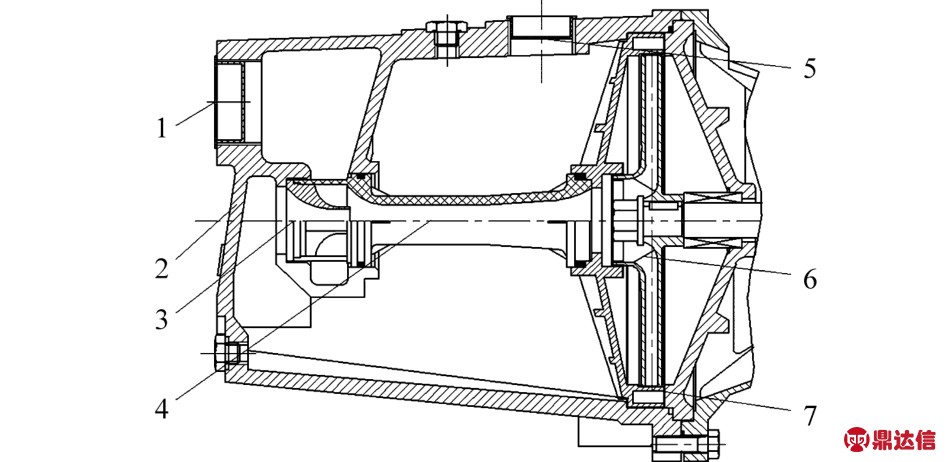
图1 射流自吸式离心泵泵部分总装图
Fig.1 Assembly drawing of pump withoutmotor
1.进口 2.泵体 3.喷嘴 4.混合段 5.出口 6.叶轮 7.导叶
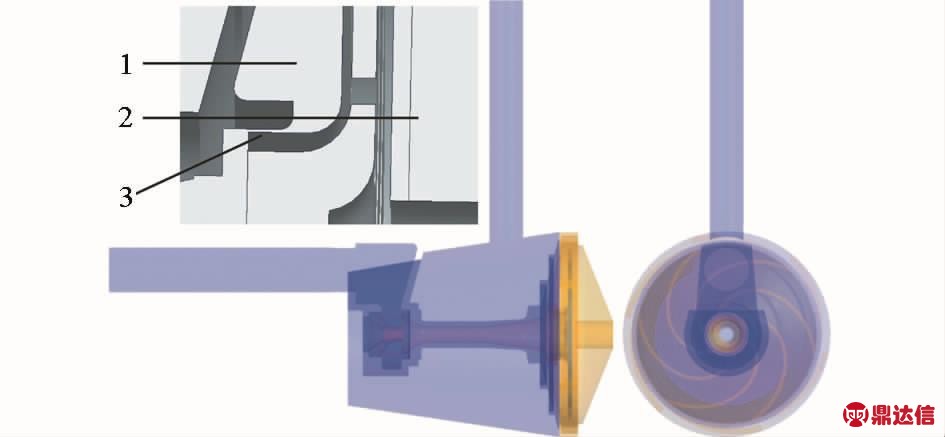
图2 三维几何模型
Fig.2 Three dimensional geometry model
1.前泵腔 2.后泵腔 3.口环间隙
随着网格质量的提高,性能预测的误差将会逐渐减低,为了获得最经济的网格数和计算步长,本文通过网格无关性确定了计算网格数[12-13],导叶、叶轮、射流器和泵腔采用非结构四面体网格,进口和出口延伸段采用6面体结构网格。表1为设计工况下6组网格数计算得到的扬程,且每组网格的雅可比率均在1~5之间,满足质量要求。可以看出随着节点数和网格数增加扬程逐步下降,当扬程相关性低于0.5%时可以认为网格对计算结果无影响,最终确定网格节点数为702 008,网格数总共为3 009 149,其中叶轮网格数为783 461,进口段为449 600,出口段为290 400,如图3所示。
表1 不同网格数下泵扬程
Tab.1 Head w ith differen t grid num bers
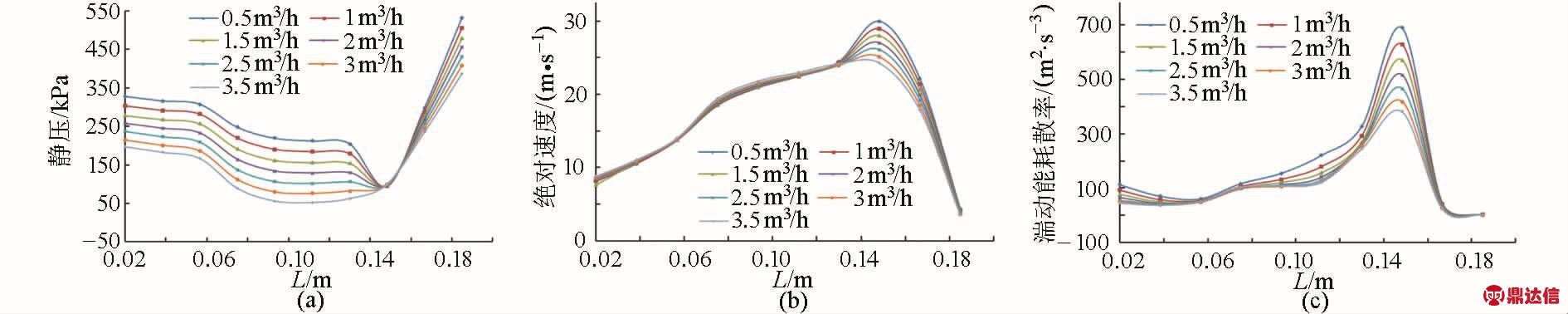
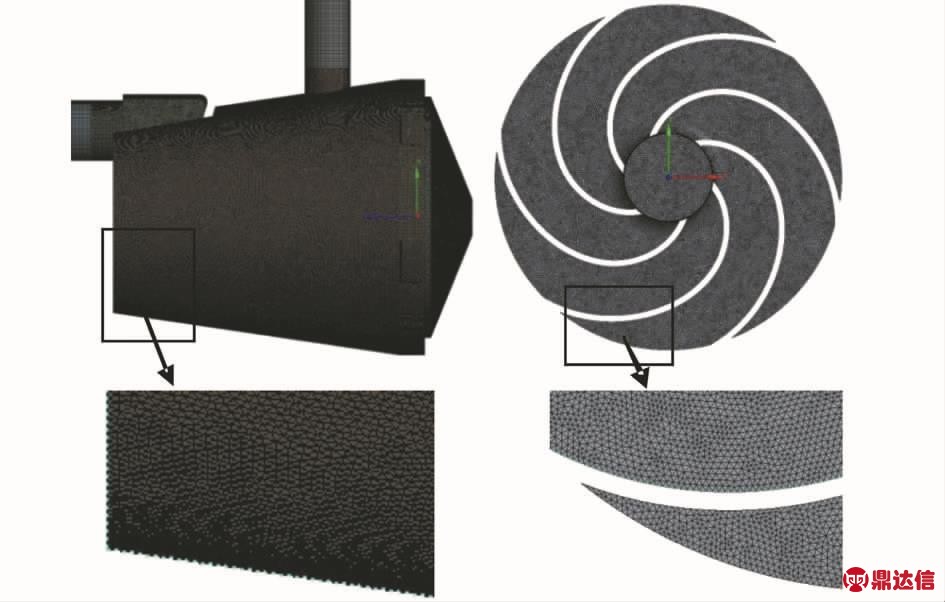
图3 过流部件计算网格及泵体和叶轮网格的放大图
Fig.3 Calculation mesh of flow part and enlarged meshes of pump and impeller
1.4 边界条件及求解
计算时叶轮区域的流场采用旋转坐标系下的控制方程求解,其他静止区域中的流场采用静止坐标系控制方程求解。
进口边界条件:采用总压进口条件,给定压力为101 325 Pa。
出口边界条件:采用速度出口条件或质量出口条件,根据出口处流量设置速度。
壁面边界条件:在靠近固壁的区域采用Scalable函数,固壁面采用无滑移边界条件不考虑粗糙度。
ANSYS CFX提供了多种类型的交界面,本文在定常计算中采用冻结转子法,对静止部件和旋转部件进行耦合。
控制方程采用有限体积法离散,速度项、湍动能项和湍动粘度系数项采用二阶中心差分格式。计算收敛条件为所有残差均小于10-4和每迭代100步长进出口总压之差不超过 10-3[14]。
2 数值模拟性能预测与实验分析
根据模拟结果预测模型泵的能量特性,泵的扬程为

式中 pout——泵出口总压,Pa
pin——泵进口总压,Pa
ρ——输送介质密度,kg/m3
g——重力加速度,m/s2
水力效率计算公式

式中 Q——流量,m3/h H——扬程,m
M——扭矩,N·mω——角速度,rad/s
容积效率计算公式为

机械效率计算公式为

总效率计算公式为

本文数值模拟了 Q为 0.5、1.0、1.5、2.0、2.5、3.0和3.5m3/h等7种工况下的内部流动。根据数值模拟结果和外特性实验结果对比可以对数值模拟的准确性进行评估。图4为实验结果和数值模拟结果对比曲线,在设计工况下,扬程H、轴功率P和效率η的相对误差为2.63%、6.16%和14.29%,这是因为在数值模拟过程中仅考虑了湍流造成的损失,忽略了轴承、摩擦副等引起的机械损失;实验值在Q>3.5 m3/h工况后各个参数的实验曲线发生了突降,该工况与低比转数离心泵大流量工况特性类似[15-16];从图 4b中可看出,当流量 Q<3.5 m3/h时数值模拟和实验测试的轴功率均近似呈水平直线,没有出现最大值,这是该泵与普通离心泵相比一大特点。从图4c中可以看出,泵的最大效率为 Q=3.5 m3/h工况时的15.68%,其值也远小于文献[3]中外混式自吸离心泵,但是叶轮进口设置射流器可以有效改善泵自吸高度和自吸时间[6],效率较低亦是该小流量、高扬程射流自吸式离心泵的特点。本文采用的网格和湍流模型可以较准确预测出射流自吸式离心泵小流量工况和设计工况下的外特性变化,下文着重探讨当流量 Q<3.5 m3/h时泵所具有的内特性。
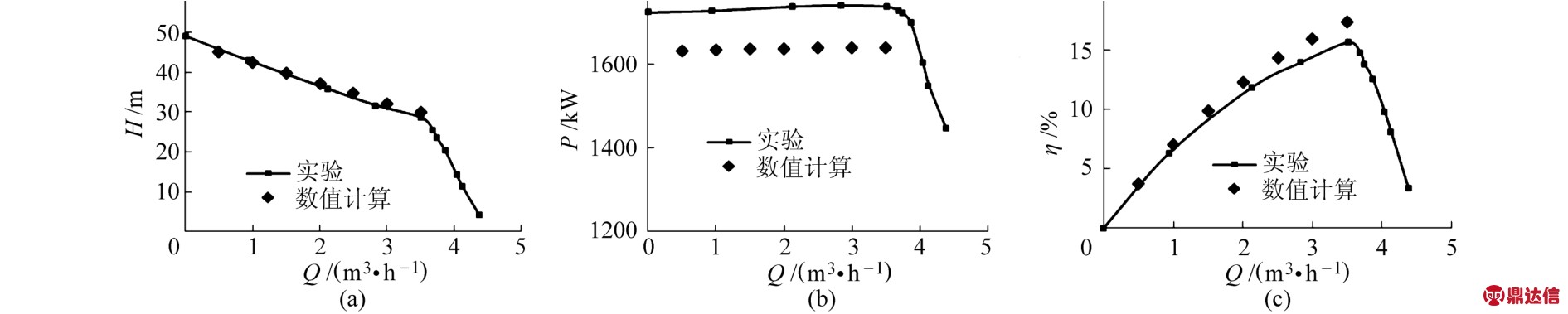
图4 数值模拟和实验结果对比关系
Fig.4 Comparisons between simulative and experimental results
(a)流量 扬程 (b)流量 功率 (c)流量 效率
3 内部流场压力、速度分析
3.1 全流场静压
图5所示为全流场压力分布图。从图5可以看出,射流式自吸喷射泵的叶轮和导叶内的压力分布规律与普通离心泵的较为相似,扬程随着流量的增大 而 减 小,扬 程 分 别 为 37.11、34.65、32.12、29.98m;泵内压力的最大值不在泵出口位置,而是在导叶中,其值分别为 0.483 6、0.469 5、0.4148 9、0.393 8 MPa,这是因为当液体通过导叶进入泵腔时,存在沿程阻力损失和局部阻力损失,使部分压力损失变为液体内能;同样,泵内压力的最小值不在泵进口处,而均位于喷管中,其值分别为0.014 2、0.011 2、0.083 29、0.068 0 MPa,这是因为射流喷嘴在压差作用下产生较强的射流,具有很大的流速,此处速度要比泵进口位置速度大很多,部分压能转化为动能,压力出现了最小值;图5c中黑色椭圆(放大图)所示的喷嘴处压力呈明显的梯度变化,该处的能量变化剧烈,引起湍动能的耗散损失。

图5 不同工况下全流场静压图
Fig.5 Static pressure on plane of X=0 under different flow conditions
(a)Q=2.0 m3/h (b)Q=2.5 m3/h (c)Q=3.0 m3/h (d)Q=3.5 m3/h
3.2 全流场绝对速度
图6所示为全流场绝对速度分布图。从图6可以看出,泵内速度的剧烈变化主要发生在射流器和叶轮中,且射流器中的绝对速度远大于叶轮中的绝对速度;随着流量的增大,喷嘴处的平均速度呈下降趋势,分别为 26.86、25.42、24.58、23.38 m/s;喷嘴产生了高速射流,这股高速射流与从弯管流入的低速流体产生混杂,进行剧烈的能量转换;从喷嘴到直线段之间的速度分布几乎对称,但在扩散段和叶轮进口之间速度呈明显的不对称,其值呈上大下小,在图示框图中出现低速区。
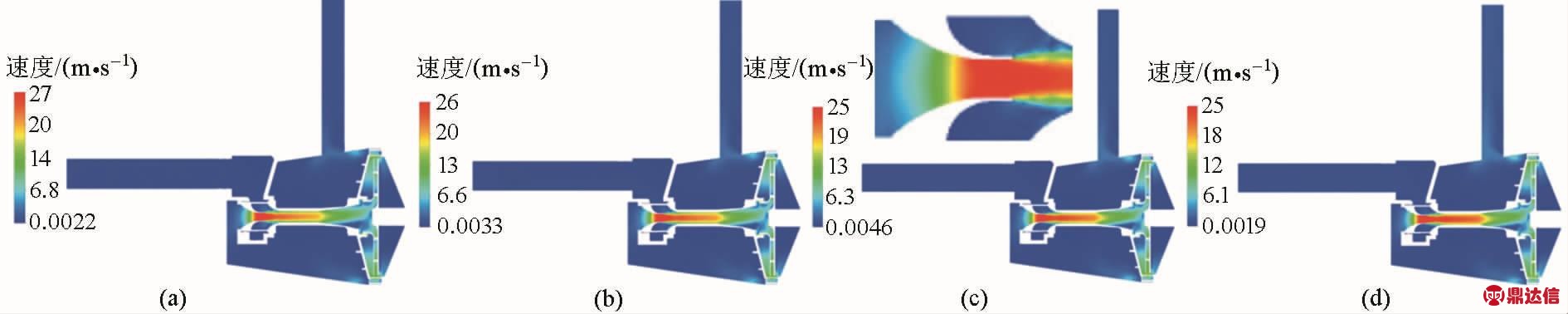
图6 不同工况下全流场绝对速度图
Fig.6 Absolute velocity on plane of X=0 under different flow conditions
(a)Q=2.0 m3/h (b)Q=2.5 m3/h (c)Q=3.0 m3/h (d)Q=3.5 m3/h
3.3 叶轮和导叶内的相对速度
图7所示为叶轮和导叶内的相对速度分布图。从图7可以看出,液体从进口流入,流经叶轮和导叶的相对速度呈现以下规律:叶轮同一半径处,吸力面的相对速度要远高于压力面的相对速度,以流量Q=2.0m3/h时 r=0.25R2(r表示不同半径,R2表示叶轮外径)为例,压力面速度为0.52 m/s,而吸力面的速度为16.24 m/s,二者相差一个数量级,这一现象在靠近叶轮中低部位置尤为明显,随着半径的增加,到叶轮靠近出口时这一现象不复存在;叶轮进口头部位置几乎都存在相对速度最小值,且都位于叶片头部靠近压力面的位置,如图中椭圆处所示,其值分别为 0.80、0.77、0.76、0.7 m/s。
3.4 射流器中的绝对速度与湍动能耗散率
图8所示为射流器中的绝对速度矢量分布。从图8可以看出,同一工况下喷嘴位置的绝度速度矢量断面呈直线分布,在边界周围明显小于中心位置;在直线段Z轴距坐标原点0.06~0.125 m处绝对速度矢量断面呈近似抛物线分布;扩散段处绝对速度矢量断面呈抛物线分布。随着流量的增大,喷嘴处的流速变小,混合能力将会降低,喷嘴处的最大速度分别为:26.68、25.62、24.84、24.52 m/s,喷嘴处的速度并没有随着流量的线性增大而线性变换,4种工况直线段中的最大速度在22 m/s左右。液体从喷嘴中射出到与低速液体混合时几乎完全为轴对称流动,液流核与泵轴线方向重合,呈中心分布,离喷嘴中心越近速度越大;叶轮进口的速度核则偏离了中心,Q为2.0m3/h和2.5m3/h时速度核偏向左上角,Q为3.0 m3/h和 3.5 m3/h时速度核偏向右上角。
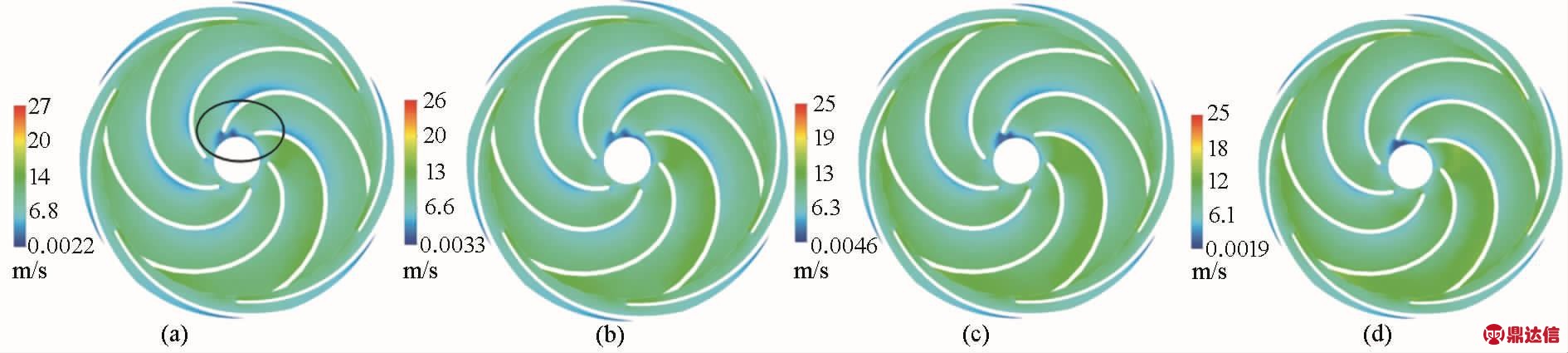
图7 不同工况下叶轮和导叶内相对速度图
Fig.7 Relative velocity on plane of impeller and blades under different flow conditions
(a)Q=2.0 m3/h (b)Q=2.5 m3/h (c)Q=3.0 m3/h (d)Q=3.5 m3/h
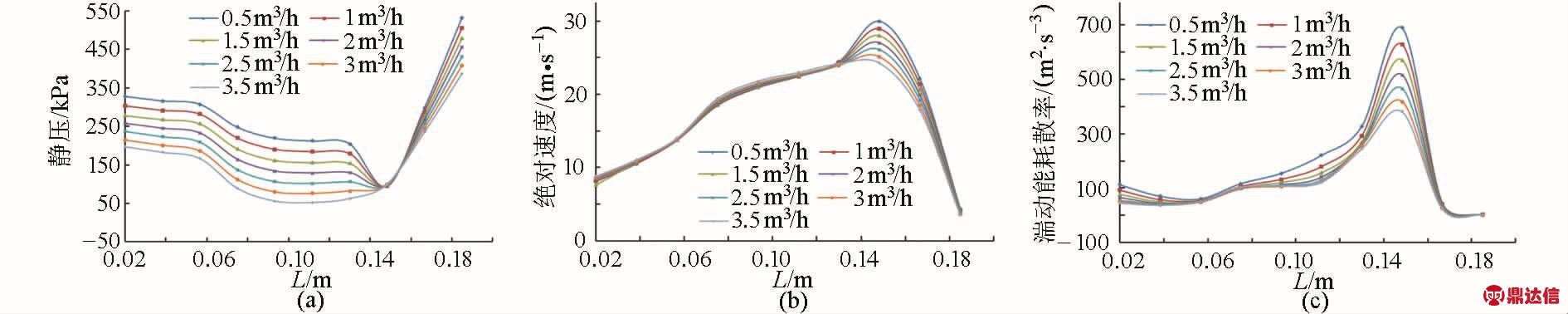
图8 不同工况下射流器中的绝对速度矢量
Fig.8 Absolute velocity of jet under different conditions
(a)Q=2.0 m3/h (b)Q=2.5 m3/h (c)Q=3.0 m3/h (d)Q=3.5 m3/h
从图9a可以看出,同一工况下从喷嘴到叶轮的的变化规律为静压先快速下降到L=0.148 m处的80 kPa,然后逐步增大到叶轮进口位置,随着流量的增大,直线段的静压变化较平缓;不同工况下同一位置处,流量越大静压越小,这一现象在直线段与叶轮之间十分明显。
从图9b可以看出,同一工况下液流流经喷嘴后的速度迅速上升到L=0.148m处的最大值,如Q=0.5 m3/h时速度为29.5 m/s,之后随着与低速液流的混合,速度一直下降到叶轮进口位置的7 m/s左右;不同工况下L=0.148 m位置处流量越大速度越小,其他位置速度差值不大。
从图9 c可以看出,同一工况下喷嘴处的液流速度较大,与低速液流混杂流动时产生较大的动量损失,在L=0.148 m处达到最大,然后剧烈下降,在直线段和叶轮进口之间变化较平缓,叶轮进口前的湍动能耗散率降到了100以下;随着流量的增大,湍动能耗散率减小,且最大值变化值较明显;射流器中的能量损失是造成泵效率较低的主要原因。
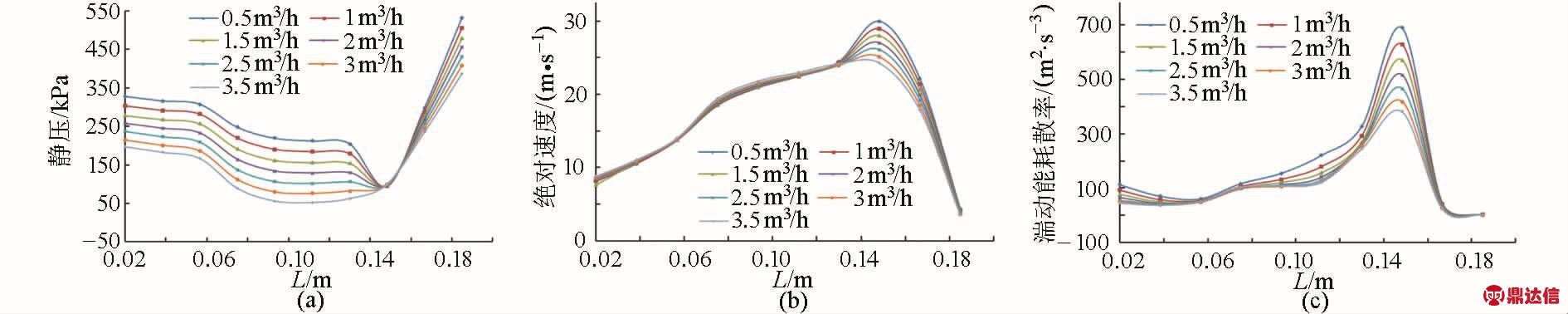
图9 不同工况下喷嘴到叶轮进口之间静压和绝对速度曲线
Fig.9 Static pressure,absolute velocity and turbulence dissipation rate curves between jet and impeller under different conditions
(a)静压曲线 (b)绝对速度曲线 (c)湍动能耗散率曲线
4 结论
(1)本文采用的网格和湍流模型可以较准确地预测射流自吸式喷射泵小流量工况和设计工况下的外特性变化趋势,其中设计工况下扬程、轴功率和效率的相对误差为2.63%、6.16%和14.29%;在 Q<3.5 m3/h工况下泵数值模拟和实验的轴功率近似呈直线;全流量工况内泵效率低的主要原因是由于在叶轮进口位置设置了射流器,造成了较多的能量损失。
(2)泵内部压力最小值出现在射流器直线段,而不是叶轮进口位置,这与普通离心泵不一样。速度的最大值出现在射流器喷嘴处,该处的速度呈中心对称分布,在扩散段和叶轮进口之间速度呈上大下小分布,液流不均匀进入叶轮进口。
(3)距离喷嘴 L=0.148 m处是静压、速度和湍动能耗散率等物理量剧烈变化的分界点,静压在此处为最小值,而速度和湍动能耗散率为最大值。