摘要: 以某石化厂区硫磺装置酸性气泄漏事故为例,运用事故后果模拟软件FLACS模拟了不同事故场景下硫化氢气云的落地距离,在考虑泄漏方向以及泄漏方向对泄漏事故影响的前提下,对硫化氢检测器水平布置距离进行了优化研究,得到以下结论: 当泄漏高度H小于3 m时,可按照现行设计规范布置硫化氢检测器;当泄漏高度在3~7 m时,硫化氢检测器水平布置距离L与泄漏高度H应符合: L=11.6H-23.2;当泄漏高度H大于7 m时,应符合: L=7.9H-29。
关键词: 硫化氢检测器 数值模拟 布置优化 模拟软件FLACS
在现代原油加工过程中,高体积分数的硫化氢在许多主要加工装置中均有分布,随之带来了较大的硫化氢泄漏中毒风险,严重危害了厂区内职工的生命安全。有毒气体检测器是否能够有效地发挥作用,及时探测到空气中超标体积分数的硫化氢,第一时间发出警报,使石化企业能够尽快疏散事故风险区域的职工,是有效应对硫化氢泄漏事故的关键一步。有毒气体检测器有效发挥作用的影响条件有4个[1-2]: 是否存在设计缺陷,质量是否达标,固定安装过程是否符合规程,布置位置是否合理。其中,前3项在建厂初期可以经过慎重选型、质量把关、正确安装,并在日常生产中积极加强维护保养,以保证有毒气体检测器的正常运行;而有毒气体检测器的布置位置是否合理,则需要通过对不同事故场景下有毒气体的扩散规律进行研究来确定。
目前针对工业场所可燃及有毒气体检测器的布置优化和设计规范,国内外学者进行了一系列研究: Kelsey等[3]模拟了在海上平台上高压气体泄漏的扩散规律,提出优化检测器布置可以提高对可燃性气体的检测效率,提高检测系统可靠性;Legg等[4]建立了随机规划模型来确定石化厂区装置间可燃及有毒气体检测器位置优化;Hampson等[5]研究证明了一氧化碳检测器布置高度不影响其对于空气中过量一氧化碳的检测。王小平等[6]针对密闭空间,提出以时间优先和浓度优先两个原则对气体检测器进行优化;刘璇等[7]针对海上油气平台的环境及生产特点,研究了可燃气体探测器的布置规律;章博等[8]针对高硫原油加工过程中硫化氢泄漏风险,对气体检测器高度方面进行了布置优化;张兴全等[9]模拟了气田井内硫化氢气体在有风和无风状态下的泄漏扩散过程,提出了有毒气体检测器选择和安装的具体依据。
目前国内外针对石化企业中硫化氢气体检测器的布置研究还较少,同时缺少规律性的探索和总结。在文献[8]的研究中,仅主要讨论了气体检测器高度的优化方案,而有关气体检测器距离泄漏释放源的水平距离研究中国尚没有。本文选用事故后果模拟软件FLACS [10],对石化企业中硫化氢气体检测器的水平布置距离进行了研究,并结合现行的设计规范,提出了改进意见。
1 现有设计规范
现行最新的石化厂区气体检测器设计标准为GB 50493—2009《石油化工可燃气体和有毒气体检测报警设计规范》,该设计规范有关硫化氢气体检测器布置的规定如下 :
1) 有毒气体检测器的测量范围宜设定为0~300%最高容许体积分数(MAC)或0~300%短时间接触容许体积分数(PC-TWA)。规范中规定硫化氢的最高容许体积分数为1×10-5,即硫化氢气体检测器的测量范围为0~3×10-5。
2) 有毒气体检测器的一级报警值应设定为不超过最高容许体积分数或短时间接触容许体积分数,即硫化氢气体检测器的一级报警值为1×10-5。有毒气体二级报警设定值不得超过10%直接致死体积分数。规范中规定硫化氢直接致死体积分数为4.30×10-4,即硫化氢气体检测器二级报警值最大为4.3×10-5。
3) 检测器的安装,当检测密度大于空气的有毒气体时,检测器应靠近泄漏点,安装高度距离所在地坪0.3~0.6 m。
在GB 50493—2009版规范中,关于有毒气体检测器距离泄漏点的水平布置距离没有进行具体规定。在SH 3063—1999《石油化工可燃气体和有毒气体检测报警设计规范》中,规定有毒气体检测器与释放源的距离,室外不宜大于2 m,室内不宜大于1 m。本文将通过模拟验证其规定室外检测器水平布置距离的可行性。
2 模拟场景及条件确定
1) 模拟场景。本文主要讨论在发生硫化氢泄漏事故后,在事故初期,在事故场景近距离内,硫化氢气云首次沉降在地面达到GB 50493—2009中规定的有毒气体检测器一级报警值1×10-5时的距离(以下称落地距离),以此来优化气体检测器的水平布置距离,以达到第一时间探测到空气中异常硫化氢体积分数的目的。
选择建立小尺寸的模拟场景,计算区域为x轴方向: 0~20 m,最小网格0.1 m,最大网格2 m;y轴方向: 0~200 m,最小网格0.1 m,最大网格10 m;z轴方向: 0~20 m,最小网格0.5 m,最大网格1 m,并对泄漏口周围进行网格加密。
2) 泄漏孔径。根据泄漏事故规模,通常把泄漏孔径划分为微型(1~3 mm)、小型(3~10 mm)、中型(10~50 mm)、大型(50~100 mm)和特大型(大于150 mm),硫化氢泄漏点一般在管道上、阀门、法兰和管道与设备接口处,多为中小型泄漏,而管道、容器和装置破裂的概率较小[11],故本文中选取50 mm泄漏孔径作为模拟条件。
3) 风速。硫化氢检测器布置位置的确定需要考虑风速条件,为了使提出的布置方案在全国具有一定的适用性,故在风速设定上,需要考虑国内的气象条件,根据OSGeo中国中心网站2016年最新提供的平均风速分布数据可知,国内石油炼化企业主要集中的东北、华北及华南的平原地区,年平均风速一般不大于5 m/s,考虑到风速对扩散范围的影响,若检测器布置过近,则在高风速情景下可能失去探测功能,故本文选取5 m/s作为模拟风速条件。
4) 泄漏方向和泄漏高度。在石化厂区存在硫化氢泄漏风险的装置中,不同装置易出现泄漏点的位置不同,并且出现泄漏点的朝向也无法确定,为了研究这种不确定性对硫化氢检测器水平布置距离的影响,本文主要针对泄漏方向和泄漏高度2个变量进行研究,考虑到生产实际情况,取泄漏方向为水平和垂直、泄漏高度为1~10 m,研究其对硫化氢泄漏扩散落地距离的影响。
3 模拟结果分析
3.1 垂直泄漏气体检测研究
如图1所示,在硫化氢气体开始由释放源喷射而出时,本身具有1个垂直地面向上的速度,再受与地面水平的风速影响,硫化氢在泄漏初始会向斜上方扩散,该阶段硫化氢扩散的主要影响因素是从压力容器释放后而获得的初始速度。在一段时间后,气云扩散进入重力沉降阶段,由于硫化氢相对分子质量大于空气,且该阶段大气中的硫化氢体积分数较高,故硫化氢气云受重力势能的影响开始向地表扩散。随着硫化氢气云在空气中扩散时间的推移,受大气湍流的卷吸作用影响,空气与硫化氢不断混合稀释,使气云密度逐渐降低,该阶段是向非重气扩散过渡阶段。对比图1a)~图1d)可知,若泄漏高度H较低,则硫化氢气云在重力沉降阶段便会在地表沉降,并随时间沿风速方向在地表不断向前推进,扩散距离不断增大;反之,则在沉降过程中气云密度便逐渐与大气接近,在空中继续沿风向扩散而不会对地表产生影响。
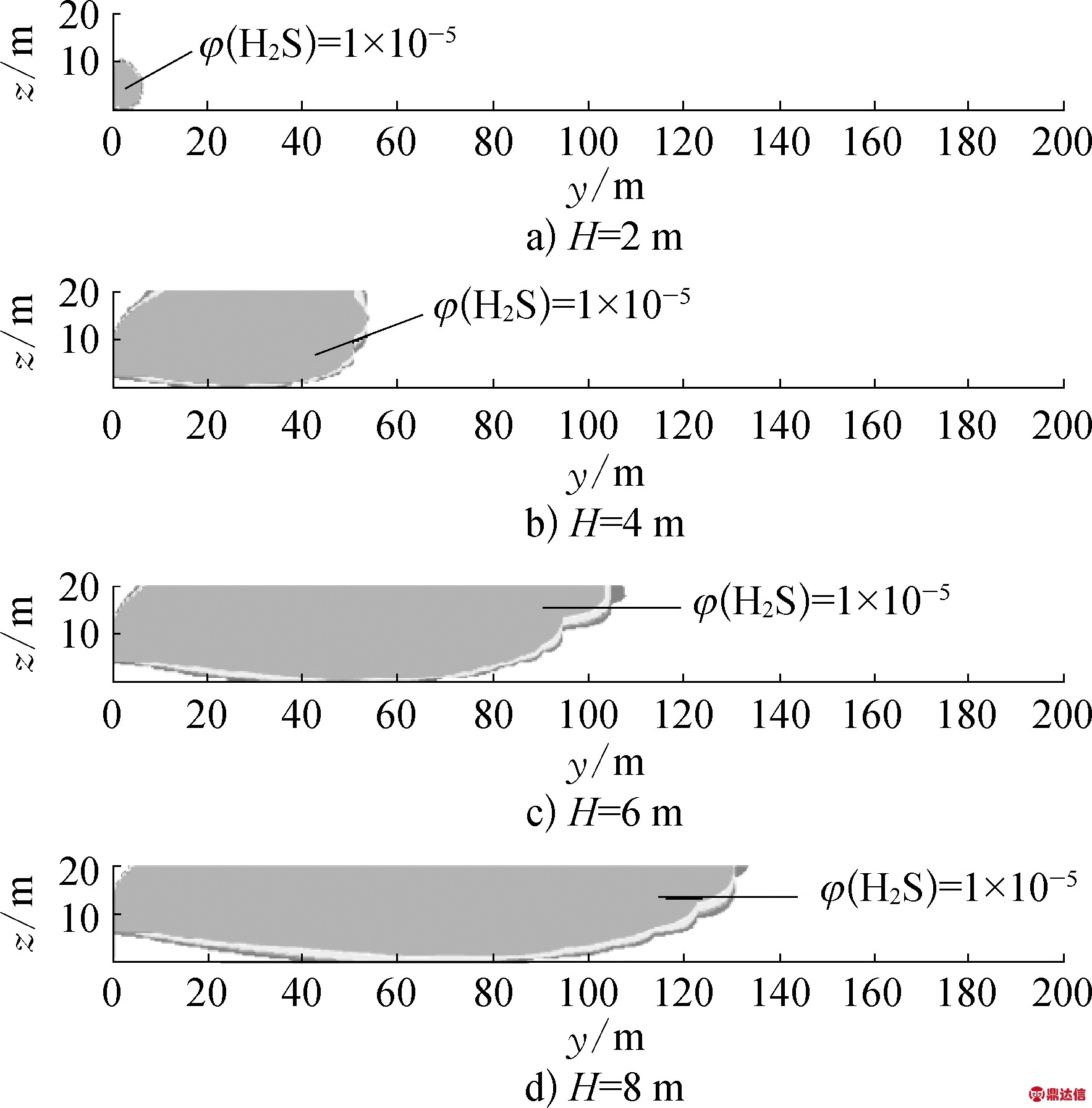
图1 硫化氢在不同高度垂直泄漏模拟结果示意
在垂直泄漏场景下,统计H为1~10 m时硫化氢气云在地表首次出现体积分数大于1×10-5时的落地距离L以及落地时间t,见表1所列。
表1 垂直泄漏气体检测优化数据统计
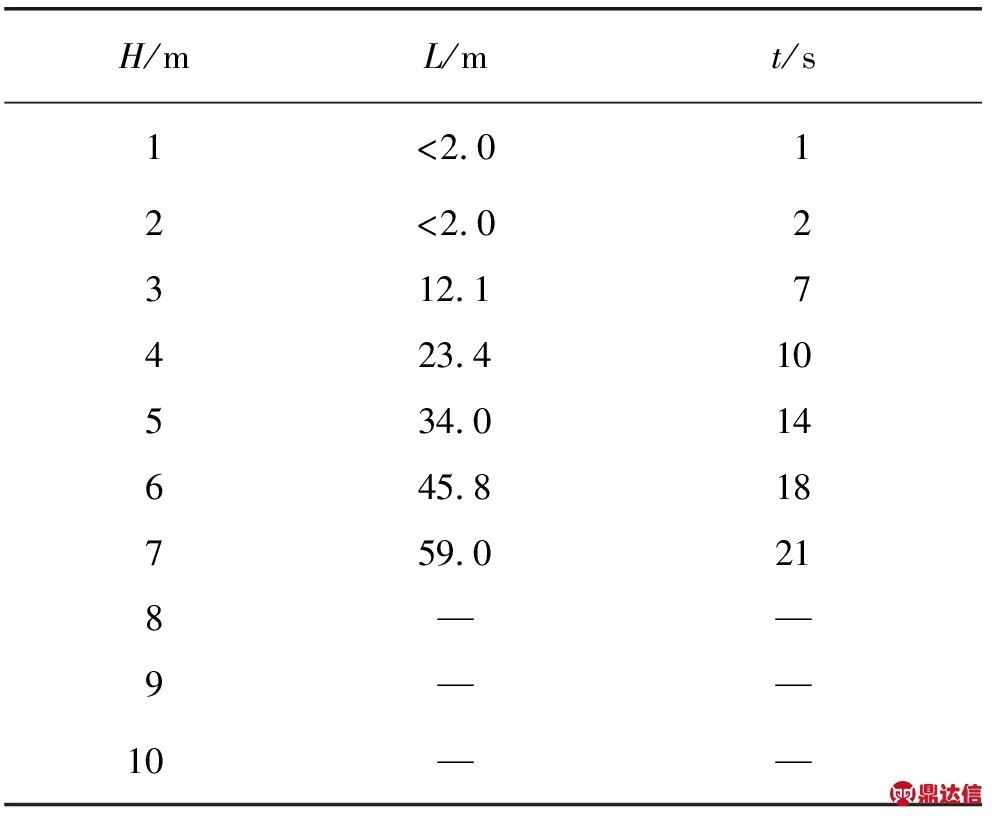
由表1可知,当H<2 m时,硫化氢气云会在释放源附近扩散到地面,t接近瞬时;当H>7 m时,硫化氢气云在风速作用下扩散,将不会在地表沉降,在H不变的情况下随风力继续沿轴向扩散;当3 m<H<7 m时,硫化氢气云的L及t随H增大而变长,气体检测器水平布置距离与H的关系如图2所示。
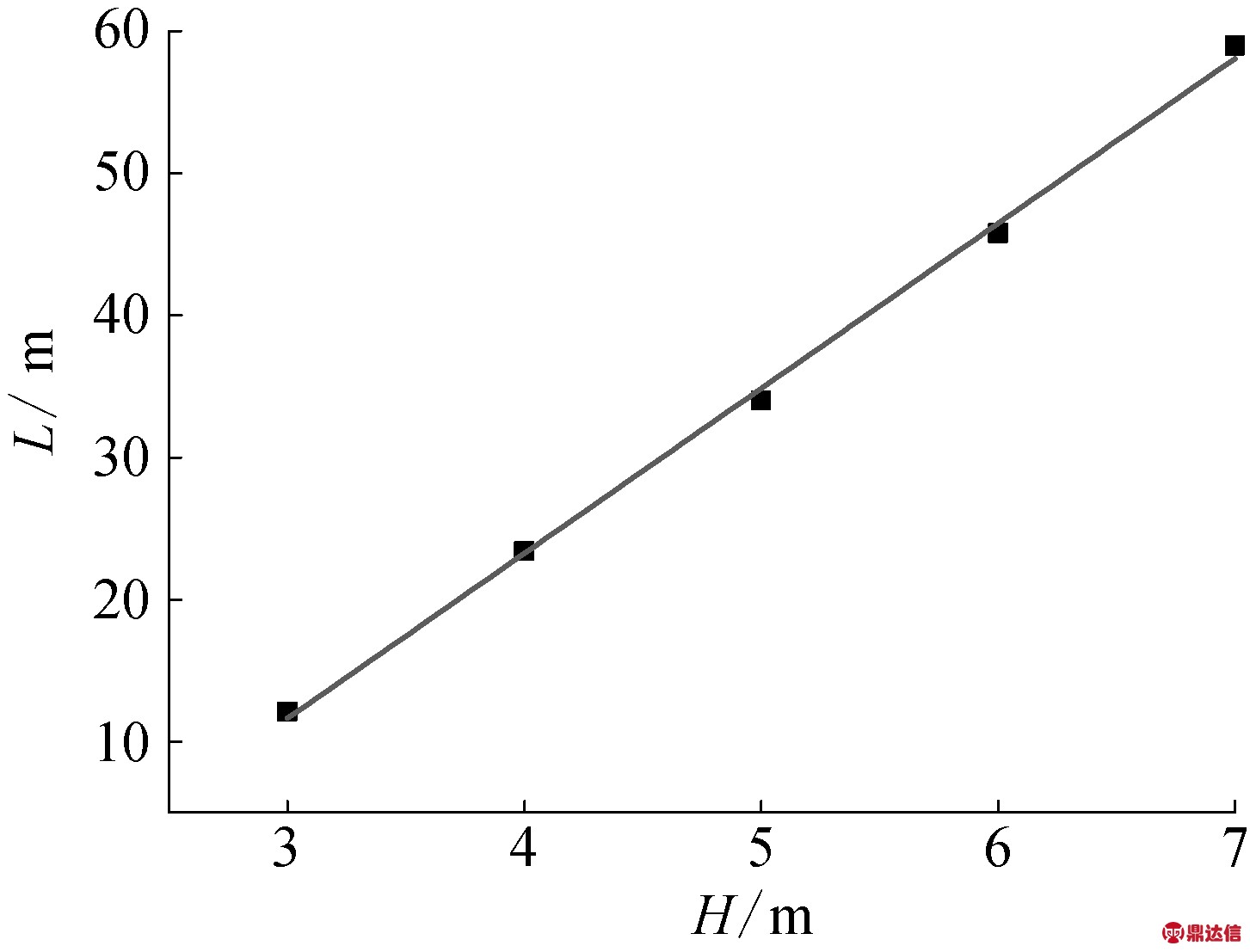
图2 硫化氢垂直泄漏时H与L的关系
由图2可知,在垂直泄漏场景下,H与L呈近似线性关系,将数据拟合得到公式:
L=11.6H-23.2
(1)
结合规范SH 3063—1999可知,当硫化氢泄漏事故发生在H<3 m时,若泄漏方向垂直向上,则可依据设计规范,将有毒气体检测器布置在距泄漏高危点2 m处;若3 m<H<7 m,则依据经验公式(1),在12.1~59.0 m范围内确定气体检测器水平距离;若H>8 m,则在垂直泄漏场景下,硫化氢气云不会在地表沉积,对装置附近地面上作业的职工无生命危害。
3.2 水平泄漏气体检测研究
如图3所示,在水平泄漏场景下,以释放源轴向为分界线,在释放源以下,硫化氢主要表现为重力沉降效应,硫化氢气体在喷射出来后一部分直接沉降到地面,形成高体积分数区域,对比可知,H越高,L越远。在释放源轴向上方,硫化氢气云受大气湍流影响,气云部分向高空扩散,扩散范围增大,体积分数降低。
在水平泄漏场景下,统计1 m<H<10 m时,硫化氢气云在地表首次出现体积分数大于1×10-5的L以及t,见表2所列。
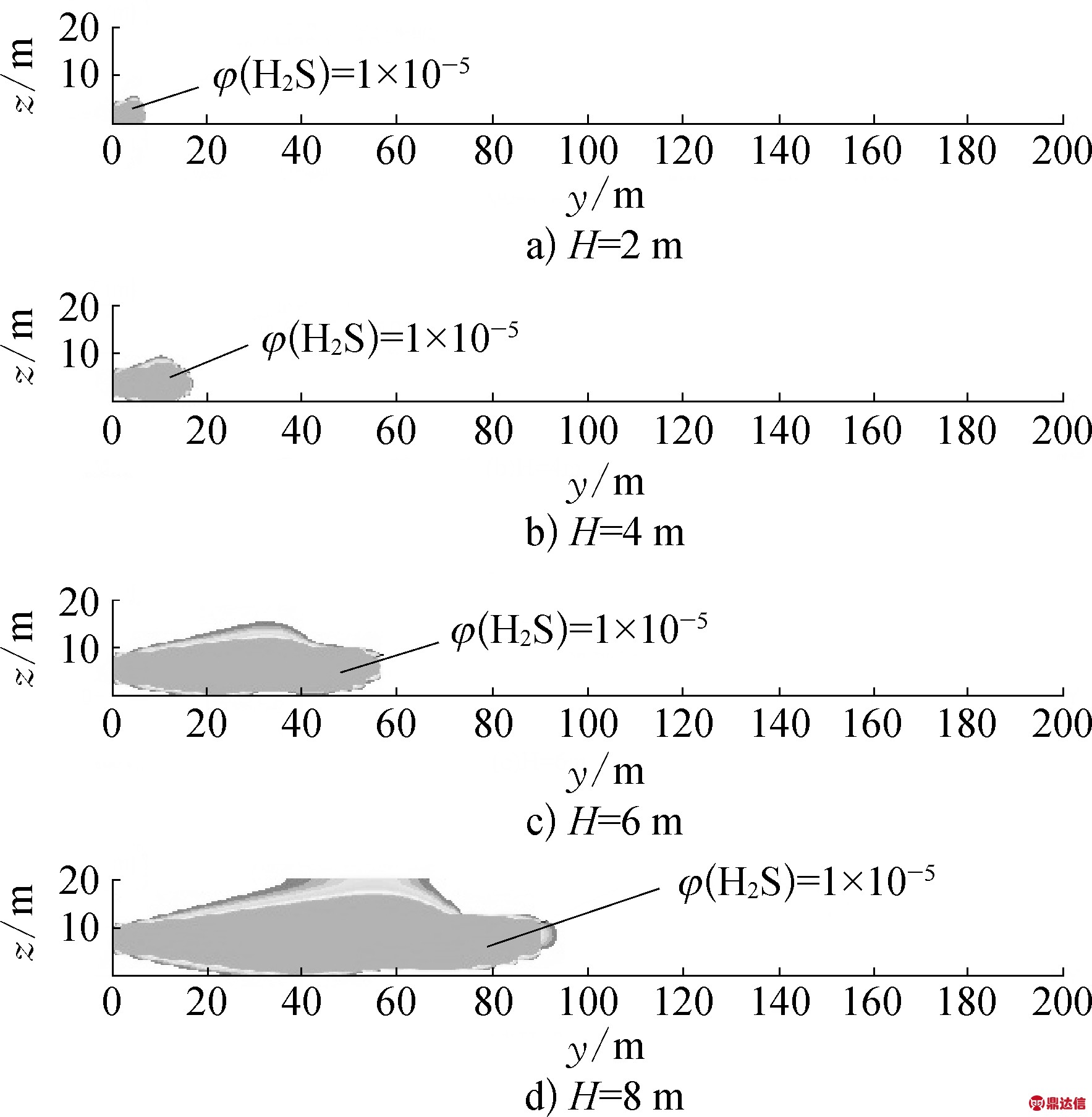
图3 硫化氢在不同高度水平泄漏模拟结果示意
表2 水平泄漏气体检测优化数据统计
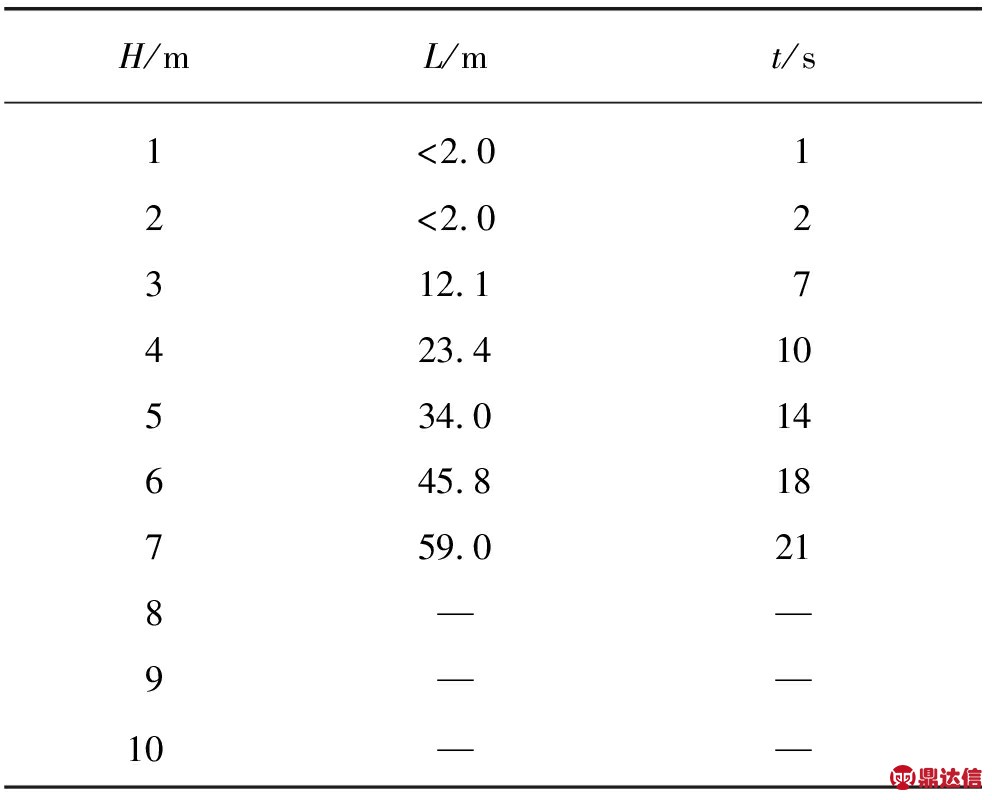
由表2可知,当H<4 m时,硫化氢气云会在释放源附近扩散到地面,t接近瞬时;当H>4 m时,随着H增大,t增长,L越远。水平泄漏场景下,H与L的关系如图4所示。
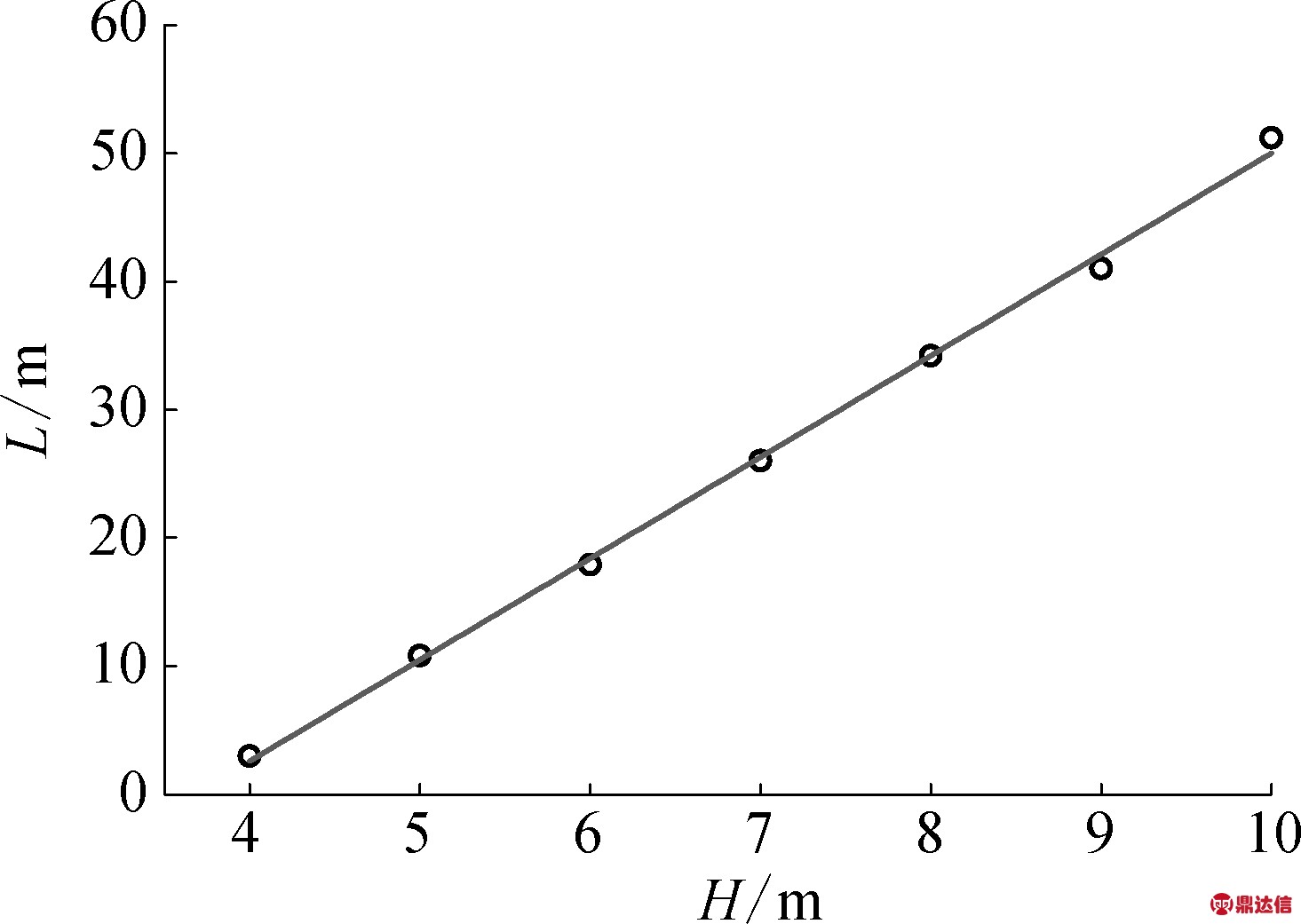
图4 硫化氢水平泄漏时H与L的关系
由图4可知,在水平泄漏场景下,H与L呈近似线性关系,将数据拟合得到公式:
首先,在表1中给出了f30(表1的第一行表示顶点ui(1≤i≤10)的色集合,第二行表示顶点ui(1≤i≤10)的颜色,第三行的34(4)表示顶点v1着色4,v1的关联边u1v1,…,u10v1分别着色3,3,3,3,3,3,3,3,3,3,以下如此类推)。当10≤j≤30时,K10,30的6-VDET染色f30在由X∪{v1,v2,…,vj}所导出的子图上的限制显然是K10,j的6-VDET染色fj。
L=7.9H-29
(2)
3.3 不同泄漏方向对比优化
由上文讨论分析可知,泄漏方向的不同造成了硫化氢气云落地距离有较大差别,而在工业生产中,无法预知事故发生的类型,通常只是针对一种泄漏情况来布置有毒气体检测器,故需要分析在不同的H情况下,水平与垂直两种泄漏场景硫化氢落地距离的特点,分析总结出各范围内能够成功检测到两种泄漏方向及介于其之间方向的泄漏事故的气体检测器布置距离,以达到普遍适用于实际生产的目的,并对现行相关规范、标准提出建设性意见。对比两种泄漏场景气体检测优化如图5所示。
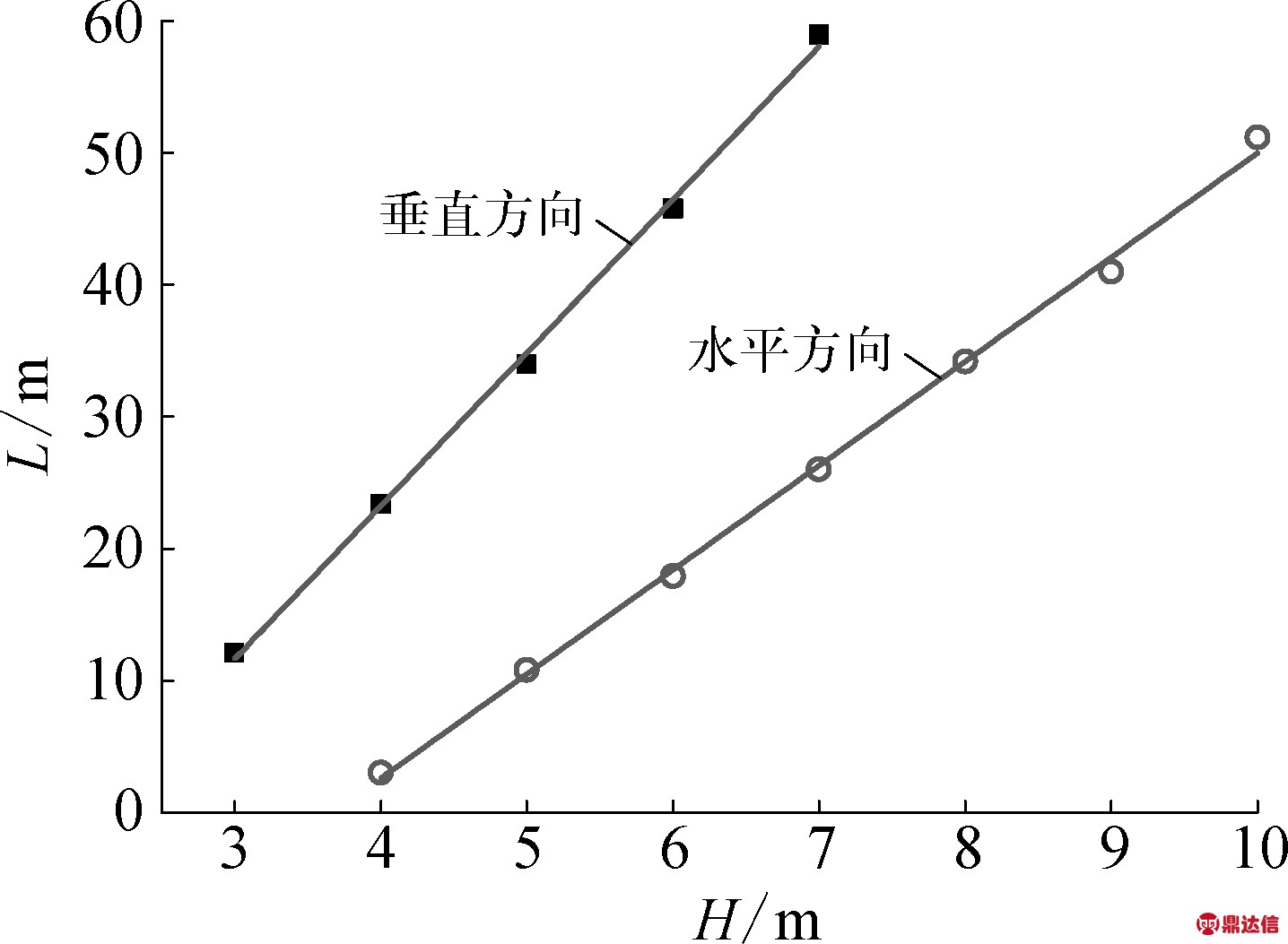
图5 硫化氢泄漏气体检测优化对比示意
1) 当H<3 m时,两种泄漏场景下,硫化氢气云均在装置附近扩散到地面,则按照现行规范对气体检测器进行布置即可。
2) 当3 m≤H<7 m时,垂直泄漏硫化氢气云的L均大于水平泄漏硫化氢气云的L,故选择较远的位置可以更全面地检测各类事故场景。由表1和表2统计的两种泄漏场景气云落地时间可算出,当H为3,4,5,6,7 m场景下,垂直泄漏与水平泄漏的气云落地时间差分别为5,8,10,10,11 s,即在3 m<H<7 m时,选择垂直泄漏作为硫化氢气体检测器布置的目标场景,其因泄漏方向不同而造成的探测时间误差均在10 s以内,这对化工厂区突发硫化氢泄漏事故的应急疏散是可以接受的,故在该泄漏高度范围内,可按照垂直泄漏的硫化氢泄漏扩散规律布置有毒气体检测器。此时,L与H的关系满足式(1)。
当H>7 m时,垂直泄漏的硫化气云在地表沉降将不会高于工业场所硫化氢最高容许体积分数1×10-5,即不会对厂区内地面上的人员造成健康影响,此时只需针对水平泄漏布置有毒气体检测器,其规律符合式(2)要求。
4 结束语
笔者总结了有毒气体检测器布置优化对于硫化氢中毒事故应急救援的意义,介绍了现行石化厂区有毒气体检测器布置设计规范的内容,运用事故后果模拟软件FLACS,基于普遍性原则确定了风速和泄漏孔径条件,结合历史案例和石化装置实际情况,讨论了泄漏高度和泄漏方向2个条件对硫化氢泄漏初期云团扩散的影响,优化了气体检测器布置的水平距离,最后对现行设计规范提出改进意见:
1) 当H<3 m时,可按照现行设计规范布置硫化氢检测器。
2) 当3 m<H<7 m时,L与H应符合式(1)要求。
3) 当H>7 m时,L与H应符合式(2)要求。