摘要:本文通过对某车型前门内板测量支架设计研究,成功实现了在线检测,实现了自动化、数字化、柔性化,替代了传统检具。它在保证冲压件检测结果准确性的同时,最大程度地提高了测量支架base板和附件的通用性,降低了测量支架开发成本,从而实现了精益投资。
关键词:前门内板;测量支架;在线检测;开发成本
随着汽车技术的逐渐成熟,产品更新换代技术加快,行业竞争愈演愈烈,如何在保证产品高品质的同时,降低整车制造成本,实现精益化投资与生产,成为汽车企业关注的重点 [1]。冲压开发工装包括模具、检具和端拾器,工装开发费用高昂,冲压件开发成本约占整个汽车成本的10%~15%[2],固定资产投入非常大,给企业带来较大的资金压力。在项目初期要考虑同平台多车型的同步规划与开发,最大程度地实现模块化、通用化,前期合理的成本控制,对降低汽车成本有着十分重要的意义[3]。
衡量汽车冲压件的好坏主要有两个方面:①零件尺寸,即零件面差、止口和孔径孔位是否和数模保持一致;②面品,即零件表面有无缺陷,AUDIT得分情况。冲压件尺寸是否达标是影响白车身精度的重要因素,高精度的冲压件不但可以改善焊接小总成的精度,而且对提升车身DTS精度有着重要的作用[4]。判断冲压件是否达标,通常使用检具进行检测判定。
随着汽车新技术的大量应用,国外汽车检测技术的发展非常迅速,其中冲压件的在线检测技术已经成熟。传统的冲压件检测方法需要依靠游标卡尺、塞尺、面差仪等专用工具进行检测,对于构造较为复杂的冲压件进行检测通常需要一位在检测方面有丰富经验的专业人员进行几个小时的工作才能完成[5],例如车身外覆盖件。本文介绍一种某车型前门内板测量支架在线检测的设计及应用,支架地板多件多车型共用,实现柔性化设计,并且支架的费用相比普通检具要少的多,可以有效减少工装开发费用。
1 某车型前门内板数模及GD&T要求
1.1 零件特点
某车型左前门内板如图1所示,零件尺寸为1094mm×807mm×173mm,此零件为激光拼焊板,厚度为0.7mm/1.2mm,材料为DC06材质,零件质量6.2kg,右件与左件对称。
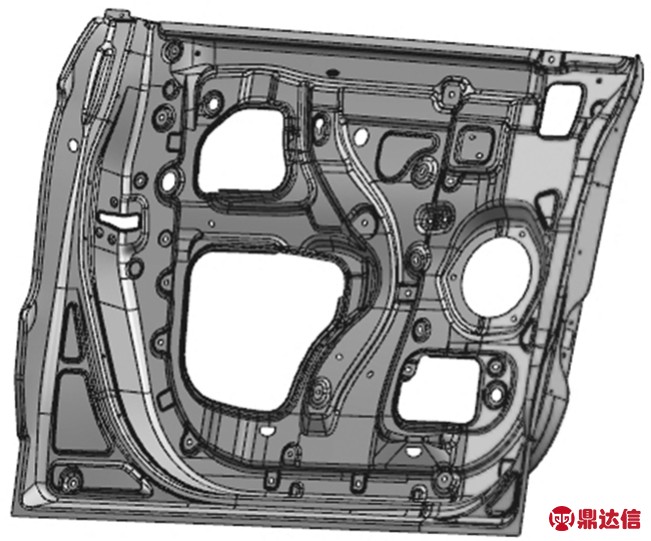
图1 左前门内板数模
1.2GD&T制作
GD&T文件主要包含三大模块。
(1)零件定位基准,根据焊装输入的基准点文件,冲压识别单件基准面数量和位置进行定位夹持,加主基准孔、副基准孔进行孔定位,使冲压单件六个自由度得到约束。原则为尽量保持与焊装基准点一致,保证冲压焊接定位的一致性,为后续车体和冲压件精度的一致性打下基础,但在设计过程中,也需要充分考虑冲压件的定位稳定性,搭接型面、止口、孔等相关要求的可检测性。
(2)检测元素,按照白车身装配搭接关系识别单件需要检测的面、边及孔,同时对有特殊要求的搭接(包括包边面等)及孔进行特殊识别。
(3)检测元素公差要求,根据尺寸工程人员提供的公差信息,对于有特殊要求的按照相应的特殊公差要求,对于无特殊要求的按照常规公差进行设定,同时对有极差要求的进行极差的识别。
2 某车型前门内板测量支架在线检测设计
2.1 测量支架base板的设计
base板采用航空铝精铸板结构形式,底板重量1440kg,底板与支撑单元总重量1579kg,底板孔采用镶套结构,孔距为100mm,镶套上部为覬16定位功能,下部为M10锁紧功能,底板布置4个基准块,X、Y、Z基准面精磨处理,粗糙度<0.8,孔编号由纵横阵列号构成,如图2所示,base板可以不同零件不同车型通用,节省成本。
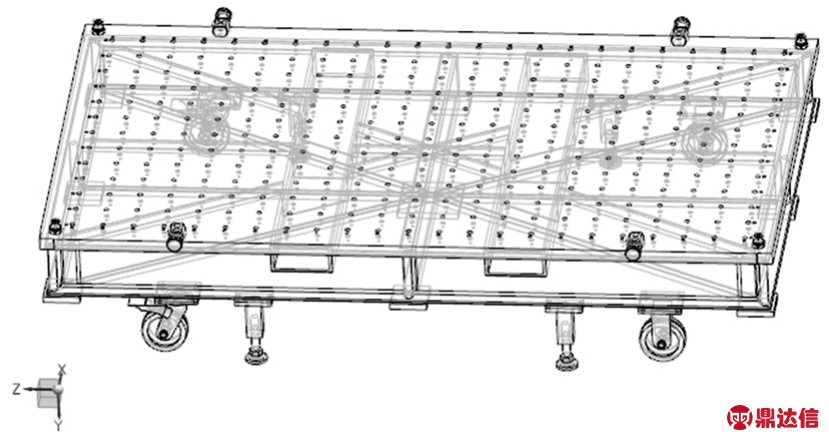
图2 base板整体设计图
2.2 测量支架存放货架设计
测量支架均要求单独制作可搬运的存放货架,货架满足减震、防碰撞、隔断防倾倒功能,货架底板采用16mm钢板,材质为Q235钢;货架存放采用田字形方格形式,护栏高度应为最高支架单元高度的2/3,护栏采用软包形式;货架配置可快速拆卸的滚轮,滚轮为2个带自锁功能的万向轮、2个直轮,滚轮与货架采用螺栓连接,货架底板上方铺一层橡胶垫作为缓冲,采用6mm以上橡胶垫。
2.3 测量支架定位系统设计
按照GD&T文件中所规定的RPS点,将被测零件定位在由第一定位面,第二定位孔,第三定位孔(面)(注:3-2-1定位原则)组成的三维空间中。确保与GD&T保持一致。左前门的定位系统设计如图3所示,右前门与左前门对称。
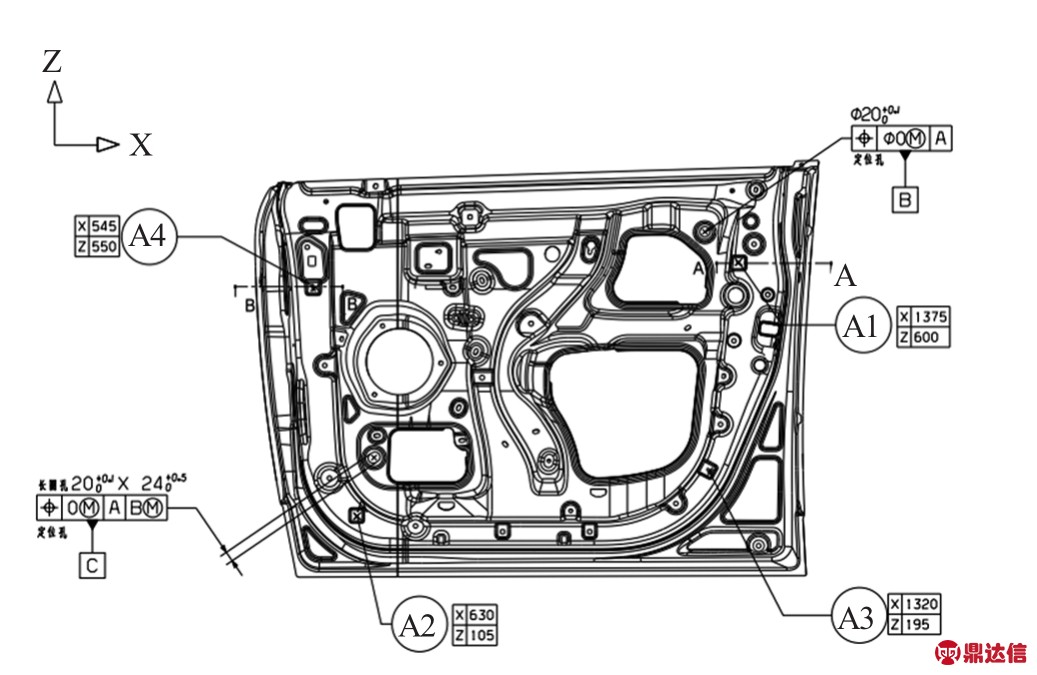
图3 左前门定位系统
2.4 测量支架设计
如图4所示,测量支架设计考虑操作者的人机工程学、被测零件的装和拆容易度、三坐标及蓝光检查的可行性及方便性(即无需拆卸任何部件并具备三坐标及蓝光检测功能)。测量支架各组成部件上刻有编号,号码刻在非工作面上,刻字清晰。支架单元采用80×80标准航空铝型材;连接板采用20mm厚铝板,用于定位支撑结构和底板与支架单元的连接;固定架、夹紧器采用标准件。
每套支架单元通过连接板与底板base固定,需采用2定位销+2锁紧销(对角方式),2个具备定位功能的孔必须镶销套,销孔(套)配 合公差要求满足H7/g6。
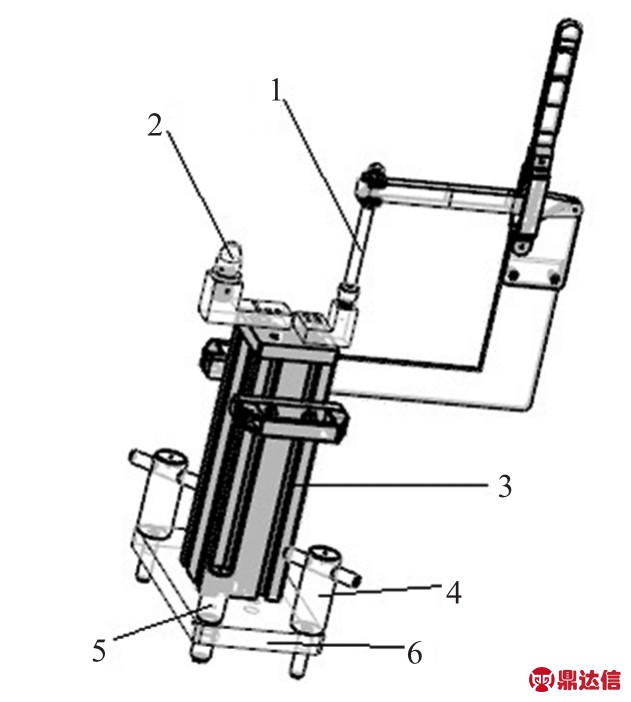
图4 测量支架结构图
1.夹持机构 2.孔定位机构 3.支架单元 4.定位销 5.拧紧销 6.连接板
2.5 某车型前门内板测量支架在线检测整体结构设计
测量支架在线检测检具结构设计主要是进行三维检具结构图设计,按照定位系统对测量支架在线检测检具结构进行详细设计,输出UG或CATIA格式的文件。图5为某车型前门内板测量支架在线检测结构示意图,测量支架通过拧紧销和锁紧销固定在base板上。零件根据孔定位系统放置于测量支架上,然后将夹钳夹持,由于base板设计是要适合所有零件的检测,尺寸以最大零件尺寸为准进行设计。所以为了提高检测速度,将左右前门内板放在base板同时进行检测,实现双臂联动。
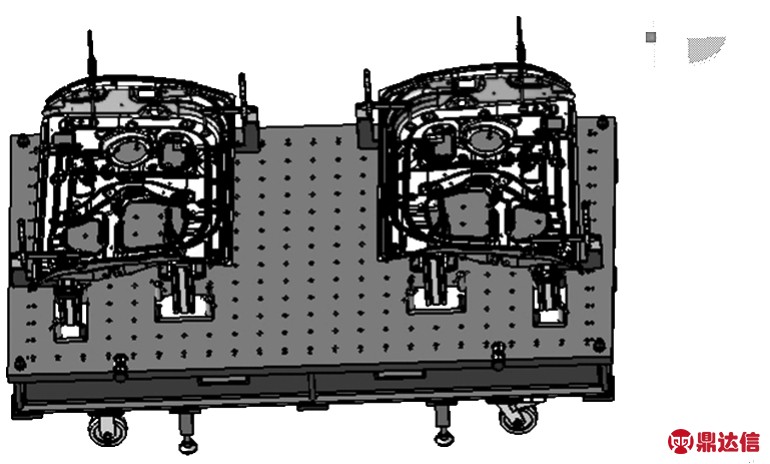
图5 在线检测结构示意图
3 某车型前门内板测量支架在线检测的应用
评审合格的检具结构图指导检具实物加工制作,最终获得某车型前门内板测量支架在线检测检具实物,如图6所示。通过对检测点的编程实现无人化操作,消除了检具测量系统由于人员导致的误差,分辨率达到0.001,检测效率明显提高,同时为后续新车型工装开发有效节约成本,图7为某车型前门内板测量支架存放货架。
4 结束语
(1)通过对某车型前门内板测量支架在线检测设计方法研究,并应用于实际生产,解决主机厂检具工装多元化、通用化并提升了检具柔性化,有效降低了检具开发成本。
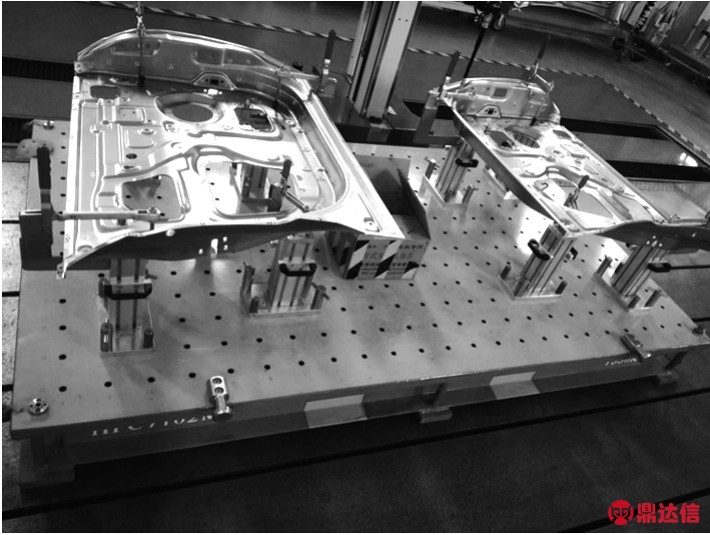
图6 在线检测检具实物
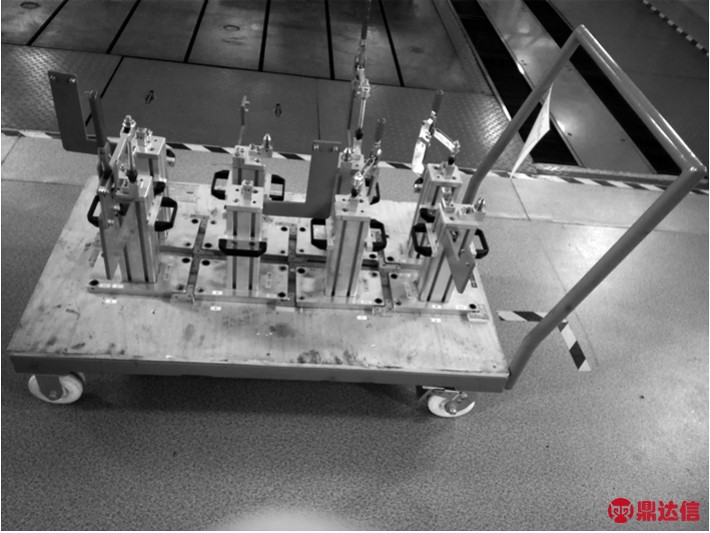
图7 测量支架存放货架
(2)测量支架在线检测技术在先进的测量系统中有着独特的优势,准确、高效、成本低,这就为新设备的应用、推广提供了重要的技术手段。
(3)测量支架在线检测技术成功应用意味着测量自动化、数字化迈开了新的篇章,检具标准化、柔性化、精密化、自动化、智能化得到了进一步的提升,为以后车型提供了宝贵的经验。