本文研究了柔性冲压生产线中的工艺分析、装备设计和机器人技术。着重探究了板材充液成形工艺,针对汽车铝合金覆盖件为研究对象,进行了充液成形数值模拟。基于充液成形工艺,研制了高端数控充液成形双动液压机,其中主机系统采用组合框架式设计。最后,针对柔性冲压生产线的设备配置和机器人离线编程技术,详细介绍了天锻压力机公司研制开发的管板复合式充液成形生产线。同时,基于此生产线对汽车铝合金发盖内板进行了试验验证。该生产线的投入使用标志着天锻压力机公司具有自主研发先进水平的钣金零件充液成形生产线的能力。
汽车轻量化发展
汽车轻量化是通过车身优化设计,采用轻体材料如高强度铝合金、镁合金等,以先进的制造技术如板材/管材充液成形技术来实现。然而在车身上还鲜有应用铝合金板材、管材和型材的,这主要是因为没有支撑这些铝合金材料成形的先进大型装备,虽然开始采用刚性模具成形一些铝合金的板材零件,但由于铝合金成形性能差、表面硬度低、容易失稳、连续多道次成形需要中间退火、模具质量要求高等原因,严重阻碍了铝合金板材在汽车整体车身上的应用,现代充液成形技术为汽车铝合金板材成形提供了途径。
汽车铝合金覆盖件充液成形工艺
板材充液成形工艺简介
板材充液成形是在凹模中充满液体,利用凸模(带动板料)进入凹模时建立反向液压的成形方法。由于反向液压的作用,可减小普通拉深成形中凸、凹模之间坯料的悬空区,使该部分坯料紧贴凸模,零件形状尺寸最终靠凸模来保证,还可产生“摩擦保持效果”,缓和板料在凸模圆角处(传统拉深时的危险断面)的径向应力,提高传力区的承载力,抑制坯料减薄和开裂,可有效提高成形极限、减少成形道次。液体从坯料与凹模上表面间溢出,在板料与凹模表面间形成流体润滑,摩擦减小。油液保护作用使得成形零件表面无划伤,缓解了零件表面的划伤,同时使法兰变形所需的径向应力减小。
充液拉深与普通拉深对比如图1所示,先在液压室(凹模)内充满液体,放上拉深坯料,施加一定的压边力,凸模下行进行拉深,同时开动液压泵使液体保持一定的压力,直到拉深结束,然后抬起凸模、压边圈,取出成形零件。
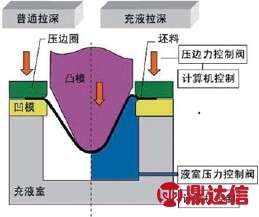
图1 充液拉深和普通拉深对比
基于充液成形工艺的数控液压机设计
根据板材充液成形工艺特点及流程,适用的设备需具有以下特点:
⑴专用液压机为双滑块配置,即双动液压机。
⑵液压机的压边力为拉深力的0.3~0.4倍。这一点区别于传统双动液压机的压边力为拉深力的0.6~0.7倍。
⑶专用液压机受力集中在主机中心处,主机机构与传统双动液压有区别。
⑷板材充液成形一般为小批量生产,生产节拍慢,故油缸速度可适当降低。
⑸板材充液成形对拉深滑块相对工作台的垂直度要求较高。
⑹板材充液成形设备对压边力要求实时可调。
⑺压边滑块及拉深滑块具有各自独立控制系统,防止成形过程中有干扰。
⑻根据工件成形的工艺及材料特性,拉深成形速度一般为1~10mm/s。
⑼成形过程中充液成形液体四处喷溅,设备需具有防水及回收过滤装置。
根据以上特点,设计一种适用中小型板材充液成形液压机。
主机设计
由于成形对滑块的精度要求较高,因此,主机机身采用整体框架式结构。主机主要由机身、拉深滑块、压边滑块、移动工作台及各种油缸组成。机身及滑块和工作台采用优质Q235-A钢板,用二氧化碳气体保护焊接工艺焊接,焊接完成后进行高温退火消除内应力。整机的设计全部采用计算机优化设计并经有限元应力分析,机床的强度高,刚度好,外形美观。
本机滑块分为拉深滑块和压边滑块。拉深滑块和压边滑块以机身左右支柱的导轨为导向做上下运动。导向形式为直角八面,导轨间隙可调,导板采用复合材料,具有自润滑功能。滑块的位置控制采用进口位移传感器检测,显示精度达到0.01mm。在滑块下平面及工作台上平面布置有T形槽,方便固定模具。
同时本机设计时增加了机械锁紧结构,可拓展机器的使用范围,实现单动功能,需要时可人工更换,切换单、双动功能。液压机结构如图2所示。
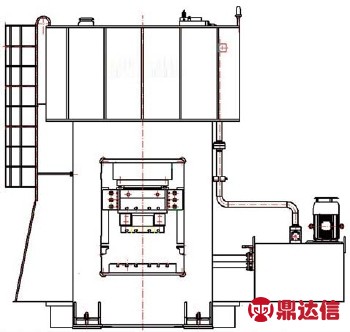
图2 液压机结构
油缸缸体均采用35#锻钢,以保证材质的均匀性。柱塞杆采用45#锻钢,经退火处理后粗加工,表面硬化处理、精加工而成,精度高,耐磨性好。拉深缸采用单一的活塞式油缸,而压边缸采用四个油缸组成,两个活塞缸,两个柱塞缸,四角对称布置,在保证压边力均匀的同时可以降低生产成本。
柔性冲压生产线
机器人柔性生产线作为一个灵活、可靠、通用的加工单元,可以长时间保证工作的稳定性和安全性,只要通过更换端拾器和机器人程序,模具就可以加工板材和管材零件。
生产线设备配置
冲压生产线根据生产线工艺的不同,一般由两台以上的充液设备组成。其典型的工艺组程序为拉延、冲裁、冲孔和翻边。第一台设备主要进行拉延序,因为拉延需要压边力,因此第一台设备是整条生产线中吨位最大的设备。
薄板冲压生产线设备如图3所示。垛料小车开进(左右两侧垛料小车自动更换);拆垛装置上进行磁性分张后,拆垛机器人取料后,每次将1片板料放至皮带线并进行双料检测;板料经过渡磁性皮带机清洗、涂油后送至冲压线首工位的机械自动对中平台,对中后进行二次双料检测;上料机器人送料至首台压机冲压,传送机器人取料、送料,进入下一压机冲压;根据工序数量循环,传送机器人取料、送料后至末端压机冲压;线尾机器人取料、放料至伸缩皮带机输送,后进行人工码垛。
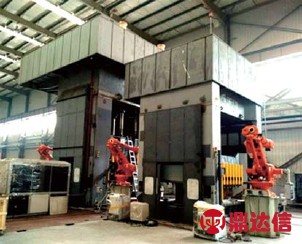
图3 薄板冲压生产线设备
机器人离线编程技术
采用基于RobotStudio软件的离线编程技术,通过对机器人视觉标定、路径规划、碰撞检测、在线编程,及压机和周边的设备模拟仿真,实现了所有设备之间的联动,安全互锁,为生产线的实际生产提供了可靠验证,缩短了调试周期,节约了生产周期,提高了效率又保证了准确和安全。薄板冲压生产线模拟图如图4所示。
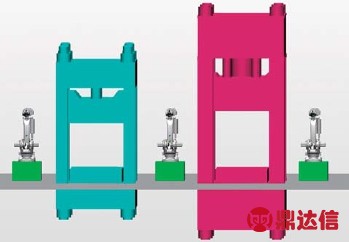
图4 薄板冲压生产线模拟