本文重点介绍了热成形在冲压工艺、模具设计及制造生产上的不同之处。实际生产表明,热成形冲压工艺方案可有效兼顾轻量化与碰撞安全性及高强度下冲压件回弹与模具磨损等问题。
随着各国法规对节能减排的要求日益严格,特别是对CO2排放惩罚性法规的实施(图1),轻量化成为节能减排的战略核心,成为各主机厂的核心竞争力。为适应这种发展趋势,汽车制造中铝合金、镁合金、塑料及复合材料等得到广泛的应用,钢铁业也开发了多种类型高强度钢,以其高减重潜力、高碰撞吸收能、高抗疲劳强度、高成形性及低平面各向异性等优势,成为汽车工业轻量化的主要材料。高强度钢的应用不仅能减轻车身质量实现节能减排,同时还能提高汽车的安全性能。为兼顾轻量化与碰撞安全性及高强度下冲压件回弹与模具磨损等问题,高强度钢的应用及热成形工艺应运而生。
目前达到E-NCAP碰撞5星级水平的乘用车型,其A/B/C 柱、保险杠、防撞梁等,大多为抗拉强度1500MPa、屈服强度高于1000MPa的高强度钢。并且含硼高强度钢板,可以充分回收利用,有利于降低环境污染。图2为高强度钢在汽车车身上的应用。
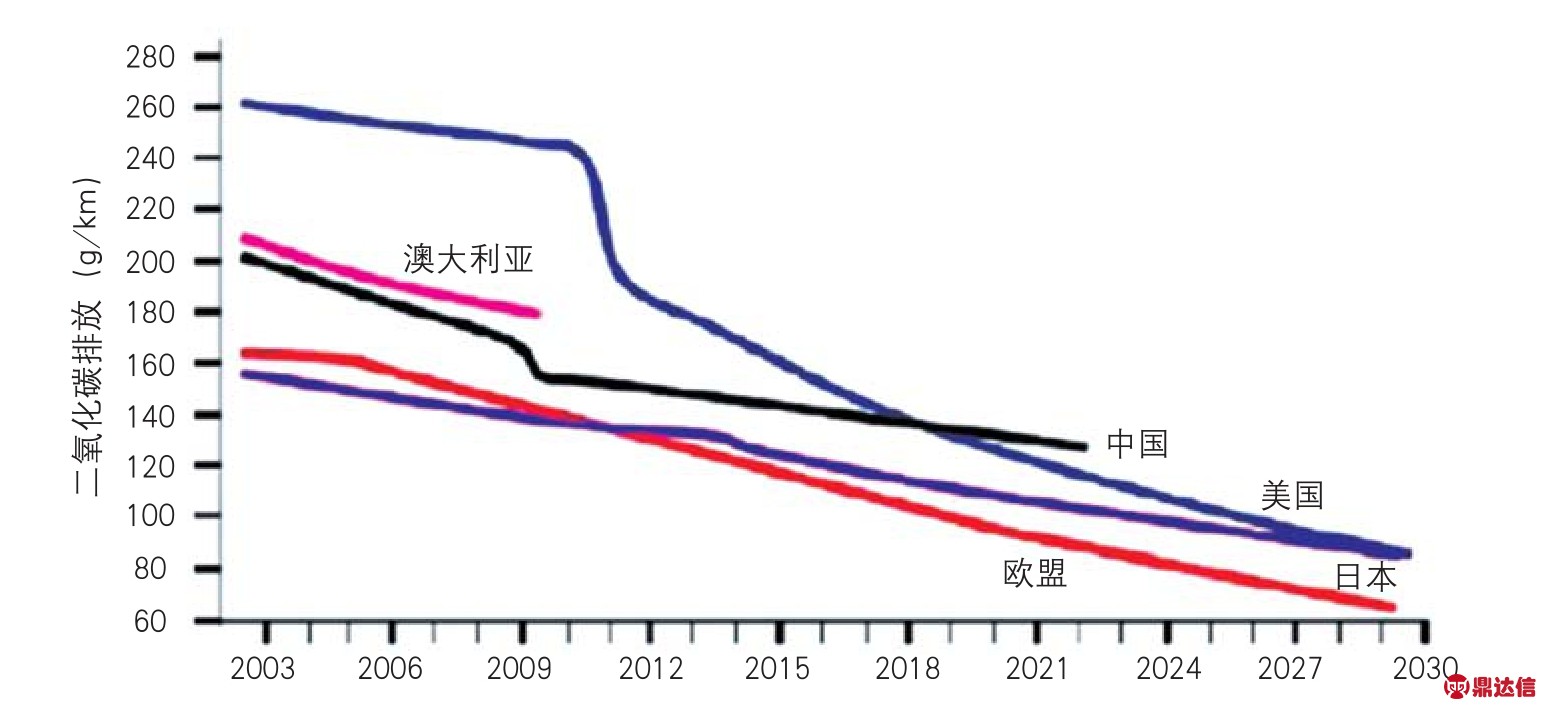
图1 各国对CO2排放的法规要求
热冲压成形工艺原理
首先把常温下强度为400~600MPa的高强度硼合金钢板加热到880~950℃,使之均匀奥氏体化,然后送入内部带有冷却系统的模具内冲压成形,之后保压快速冷却淬火,使奥氏体转变成马氏体,成形件因而得到强化硬化,强度大幅度提高。比如经过模具内的冷却淬火,冲压件强度可以达到1500MPa,强度提高了250%以上,因此该项技术又被称为“冲压硬化”技术。实际生产中,热冲压工艺又分为两种,即直接工艺和间接工艺。直接工艺是下料后,直接把钢板加热然后冲压成形,主要用于形状比较简单变形程度不大的工件。对于一些形状复杂的或者拉深深度较大的工件,则需要采用间接工艺,先把下好料的钢板预变形,然后再加热实施热冲压。
热冲压成形工艺优势
热冲压工艺可成形强度高达1500MPa的零件,可组焊成高强度驾乘单元,承受6t以上的静压而不损坏。热成形技术的主要优势;
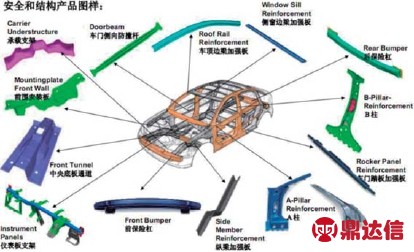
图2 高强度钢应用实例
⑴通过减小壁厚或截面尺寸减轻零件重量(达18%~35%),实现轻量化,并节约材料消耗。
⑵高温下,材料塑性、成形性好,能一次成形复杂的冲压件;冷冲压中需要多套模具多次成形的冲压件可用热成形工艺一次成形;可以减少模具数量和成形工序,成形件也可以设计得更复杂。
⑶高温下成形能消除回弹影响,零件成形质量好,精度高。
热冲压成形工艺流程
热成形工艺流程:首先将常温下抗拉强度在400~600MPa的硼合金钢板加热到880~950℃,保证其充分奥氏体化,然后将其送入热成形模具,完成快速合模、成形,再保压冷却到100~200℃,使奥氏体转变为马氏体,冲压件得到硬化,强度大幅度提升。再随室温冷却,由修冲模/激光切割机进行切边、冲孔。如果采用裸板,则需进行喷丸处理,除去零件表面氧化皮。最后,将得到的抗拉强度在1500MPa的热成形零件,其工艺流程图,如图3所示。
实际冲压生产中,根据零件复杂程度,热成形冲压工艺又分直接热成形工艺(920℃→奥氏体→热成形→淬火)和间接热成形工艺(室温预成形→920℃→奥氏体→热成形→淬火)。对于形状简单且变形程度小的零件,可采用直接热成形工艺;对于形状复杂或拉深较深的零件,则采用间接热成形工艺,即需先对下好料的料片在常温下进行预成形,然后再进行热冲压,以保证形状复杂或拉深较深的零件成形到位。
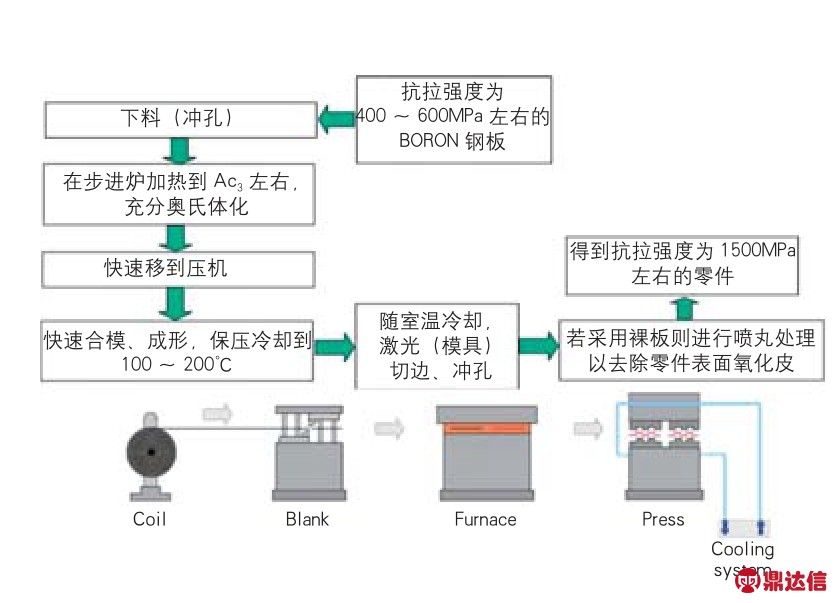
图3 热冲压成形工艺流程图
热冲压成形工艺分析
首先,需要确定是采用直接成形工艺还是间接成形工艺,然后分析除包括冷冲压成形基本工步外,热冲压成形特有的四个工步。
⑴加热:把材料从室温加热到奥氏体化,或者把预成形后的零件加热到消除所有累计的塑性应变和应力(软件会按预设温度加热)。
⑵热等待:设置材料从电炉输送到压机的时间,不涉及工具运动和板料变形,仅考虑热传递。
⑶淬火:淬火时间要足够长,使得所有元素能降温到200℃以下,在这个过程中尽管没有工具运动,但淬火过程中的热交换还是会导致热应变和一些额外的塑性应变,如变薄等。
⑷冷却:冷却工步用来使零件达到室温,只涉及热计算而没有力学方面的计算。
相比于冷冲压成形,热冲压成形有很多不同的地方,如:压边圈未完全闭合,防止成形前压边圈接触导热,造成板料降温出现淬火;不设置拉延筋;热成形过程完成所有零件特征,后续只进行修冲工序。
目前,主要从成形性、变薄率、应力应变分布几个方面对热成形进行成形性评价;通过温度场分布、冷却速率、热通量,评估模拟结果是否合理;采用相变分布,判定零件是否满足对应相变结构要求,而产品性能则通过抗拉强度和硬度评价。
热成形模具设计
在进行热成形模具结构设计时,主要考虑因素包括:镶块冷却系统布置、模具强度、模具密封性等。其中,最关键的是镶块冷却系统的布置,它能保证热成形制件成形后具备一定的冷却速率。目前,热冲压模具的设计制造方法主要有4种,即钻孔式、分层式、淋蓬式及熔铸式,各方法的优缺点见表1。
我司设计开发的热成形模具大部分采用钻孔式或分层式制造模具冷却流道。图4、图5、图6所示为左/右B柱内板加强板热成形模具结构图纸及实物图,其冷却系统采用钻孔式制造方式。
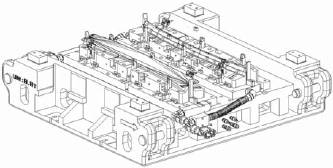
图4 左/右B柱内板加强板热成形下模轴测图
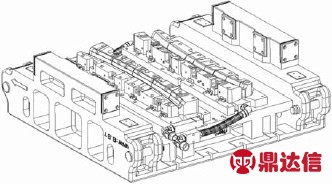
图5 左/右B柱内板加强板热成形上模轴测图
表1 热冲压模具的设计制造方法对比
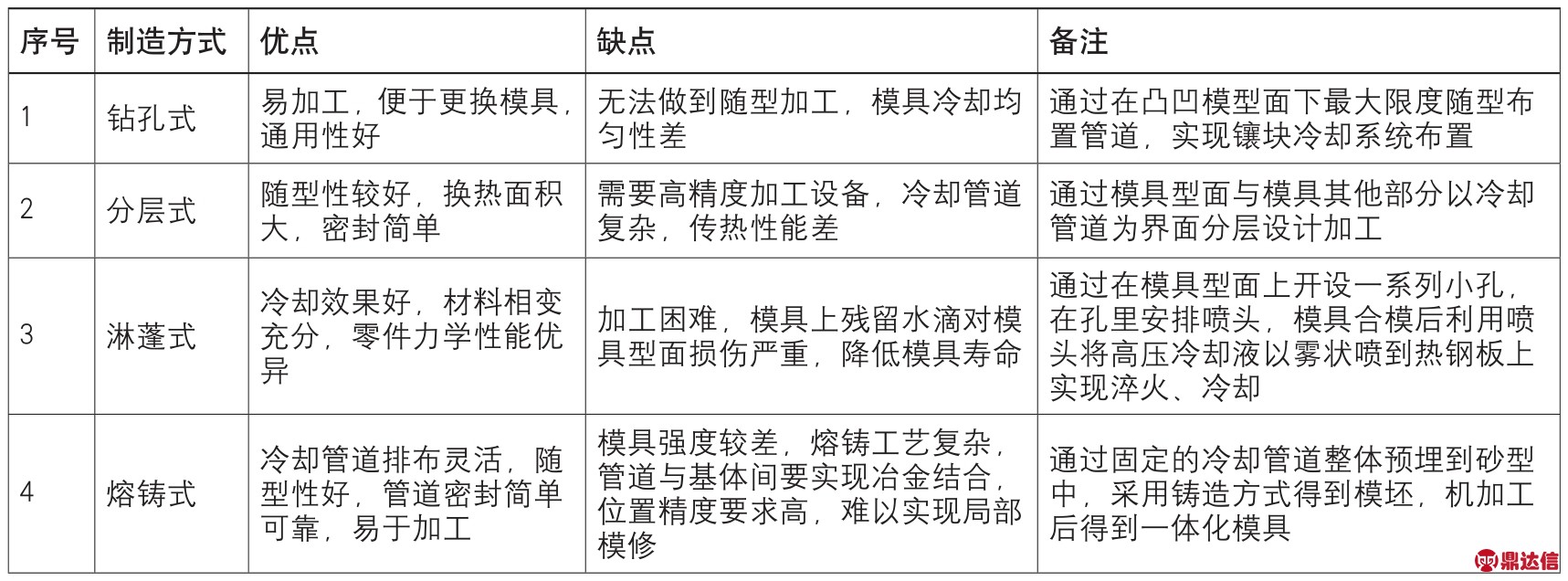
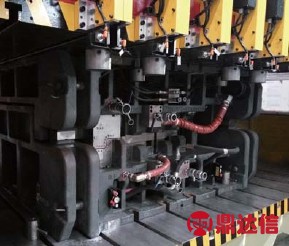
图6 左/右B柱内板加强板热成形模具生产实物图
热成形生产设备
与冷冲压生产相比,热冲压生产需要配套使用高速液压机、加热炉、机器人、生产线集成控制系统,辅助设备包括冷水系统、保护气氛系统,后工序包括激光切割机、抛丸涂油线等。其中加热炉分多层箱式加热炉和辊底式加热炉,其加热方式一般采用电加热、天然气加热或气电混合加热。目前应用最广泛的是陶瓷辊底式加热炉。箱式加热炉一般用于适应试模、试验等需求而进入热冲压领域的,分单腔单层、多腔多层、单腔多层等不同方式,具体可根据不同热冲压工艺要求组合成不同种类的热冲压生产线,如图7所示。
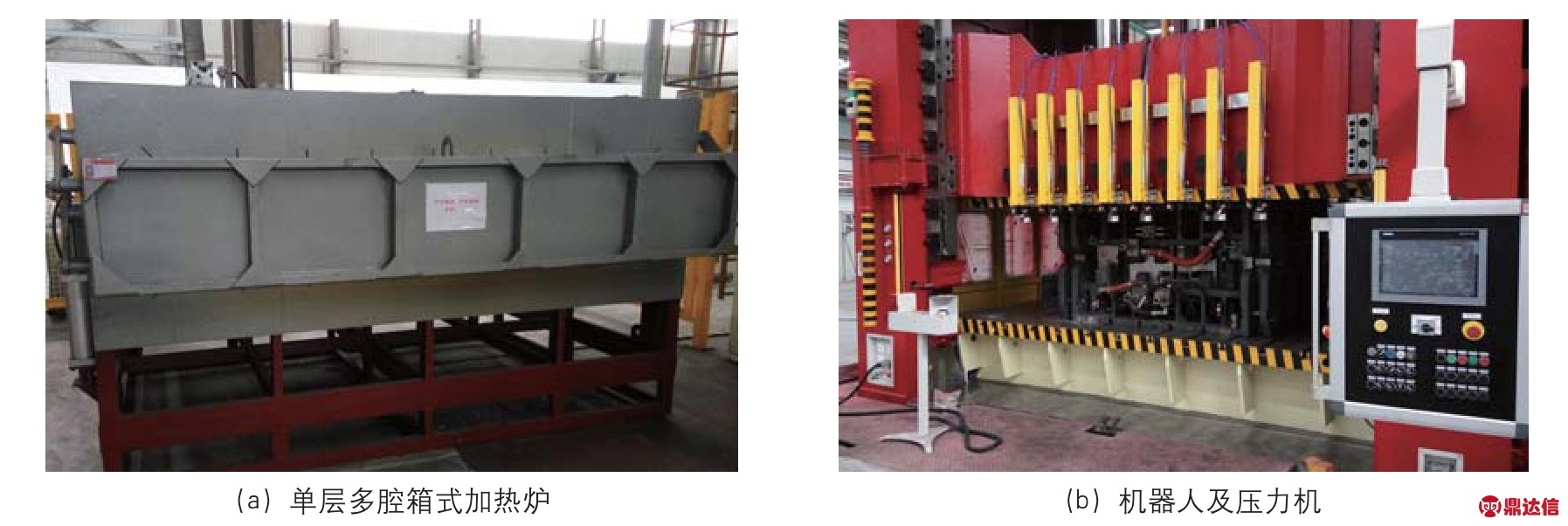
图7 热成形生产设备

图8 热成形制件精度及质量控制工具
热成形制件精度及质量控制
热成形零件检验设备包括机械性能试验机、金相显微镜、硬度计等,工装包括模具、检具、卡具、端拾器等,具体如图8所示。其零件尺寸形位要求包括:
⑴制件尺寸精度。型面公差可控制在±0.5mm,一般型面公差控制在±0.7mm以内;功能孔尺寸公差为±0.2mm,位置公差为±0.2mm;定位孔尺寸公差为±0.1mm;
⑵制件材质力学性能。包括屈服强度(950±100)MPa;抗拉强度(1400±50)MPa。
结束语
目前热冲压技术在欧系和美系车上应用相对较多,日系车热冲压件应用相对较少。除我司外,不少自主品牌如长安、吉利等不少新车型也应有了热成形技术。目前汽车行业普遍应用的是等厚、等强度板热冲压技术。轧制差厚板、激光拼焊板、补丁板热冲压技术正逐步推广应用。汽车未来的发展趋势必定是向着行车更安全、更节能方向走的,热成形件以其高强度、高延展性、高减重潜力、高成形性以及卓越的碰撞性能,必将实现在汽车行业的逐步推广应用。