摘 要: 为实现对金属-含能材料粘接结构界面粘接质量的无损评价,提高其结构安全性,本研究以金属环-含能材料界面脱粘缺陷的无损检测为研究对象,提出了基于电磁超声共振的金属环-含能材料结构界面脱粘缺陷非接触检测方法,制作了专用小型电磁超声探头,搭建了电磁超声环形自动扫查系统,对金属环-含能材料脱粘缺陷模拟试件进行了自动扫查成像,开发了相应的信号处理方法,验证了该技术对于金属环-含能材料界面脱粘缺陷非接触检测的可行性和检测能力。
关键词:脱粘缺陷;金属环;无损检测;电磁超声;非接触
1 引言
金属-含能材料粘接结构在航天和国防等重要工业领域应用广泛。粘接作为连接材料或结构的常用工艺,拥有制作方便、连接应力分散等诸多优点。但是,由于粘接层间界面脱粘而引发的各种灾难事故时有发生,粘接结构的安全与质量问题被人们广泛关注。因此,粘接质量的无损检测和评价是国际上一个非常重要的研究领域和课题[1-3]。多种无损检测方法已被研究并应用于粘接界面的检测,如X 射线、CT 和超声等。其中X 射线和CT 检测可有效检测出体积型缺陷,也可检测出裂纹缺陷,具有空间分辨率高,结果直观等优点,在含能材料研究及其部件制造中一直发挥重要的作用。但X 射线和CT 检测方法对测量条件要求较高,需要线源和探测器分别位于被测部件的两侧,此外射线对人体还存在辐射风险。与之相比,超声检测虽然在空间分辨率和结果直观性方面存在不足,但对于界面分层缺陷,超声检测具有更高的灵敏度,且拥有设备简单、成本低、灵活方便、效率高、对人体无害等优点[4-6]。然而,常规超声检测技术主要采用接触式压电探头,检测时探头与被测试件必须接触且需要液体耦合剂,因此要求试件具有较好的表面状态,保证检测探头与被测试件具有良好的声学耦合,检测时探头与被测试件的接触状态对检测结果有非常大的影响,不但严重影响测量结果的准确性和可靠性,还会限制其检测效率[5,7-8]。
电磁超声作为一种新兴的无损检测技术,依靠电磁感应直接在被测导体中激发和接收超声波,具有非接触、无需耦合、易实现大型构建快速自动化检测等优点。相关研究[9-10]表明,与传统压电超声主要采用纵波检测不同,电磁超声可以非常容易地激发和接收对粘接界面状态更加敏感的横波。然而,与传统压电超声相比,电磁超声最大的缺点就是能量转换率和信噪比较低。电磁超声共振利用一定频率的多周期正弦脉冲驱动探头在试件激发多周期超声脉冲序列,多周期超声脉冲序列在试件上下表面往复反射,当相邻回波信号相位差为周期的整数倍时发生超声共振,信号幅值急剧增大。到目前为止,电磁超声共振技术在金属材料厚度检测和材料特性评价等方面的研究取得了很好的效果[10]。基于电磁超声共振技术,开发金属环-含能材料粘接界面脱粘缺陷电磁超声非接触检测方法,具有非常好的研究和应用前景[11]。
本研究针对小型金属环-含能材料界面脱粘缺陷的无损检测难题,提出了基于电磁超声共振的界面脱粘缺陷增强型电磁超声非接触检测方法和技术,开发了用于金属环的专用小型电磁超声传感器和扫查装置,进行了金属环-含能材料界面脱粘缺陷电磁超声共振自动扫查及成像实验,探究了所开发检测方法和技术对于金属环-含能材料界面脱粘缺陷的检测能力。
2 实验研究
2.1 电磁超声共振检测原理
电磁超声共振法的原理如图1 所示,采用一定频率f 多周期正弦脉冲信号驱动电磁超声探头在试件表面激发持续一定时间的超声脉冲序列p0(t),在试件上下表面间形成反复反射,各反射回波信号pi(t)发生部分重叠,当超声激励频率设定为如式(1)计算值时,即相邻回波信号之间Δt=2h/c=nT=n/f,各回波信号发生同相位叠加,形成超声共振信号[12-13]。

式中,f 为超声激励频率,Hz;n 为共振频率阶次;c 为材料中超声波波速,m·s-1;h 为被检构件厚度,m。电磁超声共振法由于信号幅值及功率明显较常规的短脉冲回波法强,因此具有非常高的信噪比。使用较小型的电磁超声探头也能获得较好的检测性能,可大幅度提高其空间分辨率。此外,还具有可用较低频的信号检测薄板结构,激励的超声剪切波对粘接界面敏感等优点。
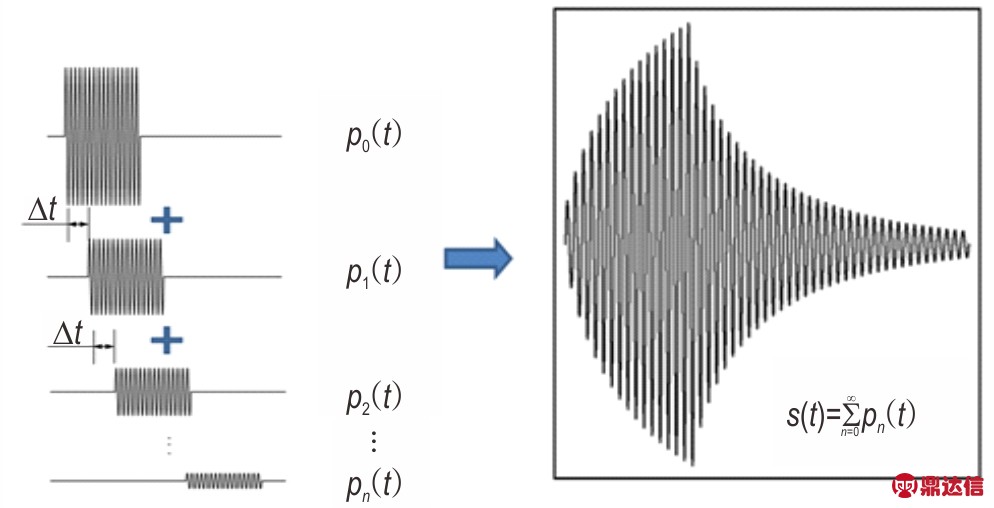
图1 电磁超声共振法基本原理图
Fig.1 Basic principle of the electromagnetic acoustic resonance(EMAR)method
基于电磁超声共振法,本研究开发了针对脱粘缺陷的检测方法。如图2 所示,电磁超声的激励频率为粘接试件金属层的超声共振频率,即满足式(1)。当电磁超声探头位于粘接完好区域上方时,电磁超声探头激发的超声波大部分透过粘接界面传至胶层和下层基底材料内部,仅有少部分超声波能量在金属层底面反射,因此无法形成很强的超声共振效应;而当超声探头位于脱粘区域时,电磁超声激发的超声波在金属层下表面发生全反射(金属层下表面满足自由边界条件),从而在金属层上下表面形成很强的往复反射和超声共振效应。因此根据检测信号幅值和信号包络能量大小可区分粘接完好区域与脱粘区域。
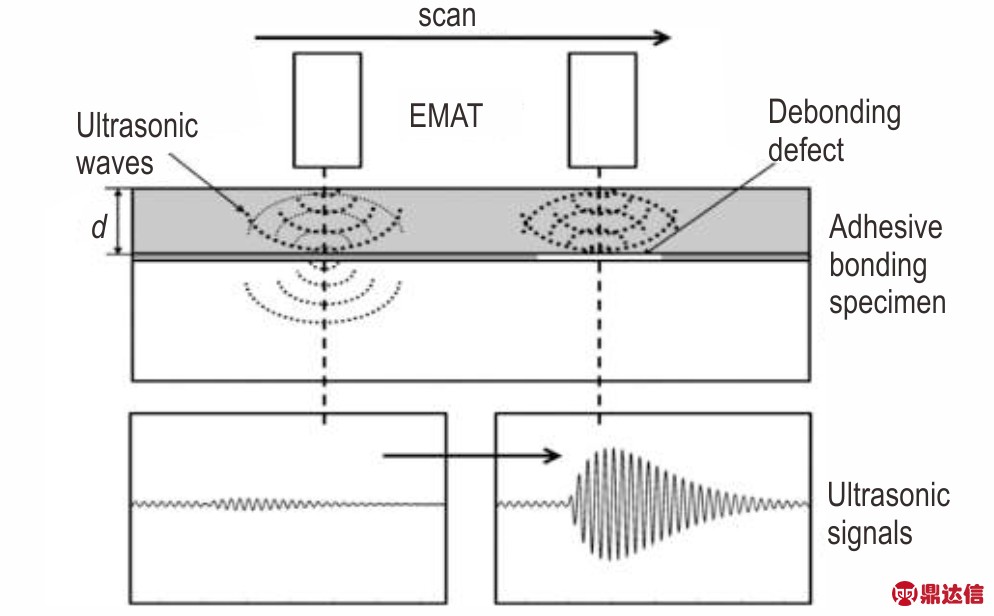
图2 界面脱粘缺陷电磁超声共振检测方法
Fig.2 Adhesive debonding inspection with EMAR method
2.2 信号分析方法
与传统的脉冲回波信号不同,共振信号是一个持续时间较长的连续周期信号。因此,采用基于共振超声信号功率谱分析的信号处理方法,进一步提高电磁超声的信噪比和脱粘缺陷检测能力。如式(2)所示,首先对超声共振信号进行自相关分析:

式中,R(m)是超声共振信号s(n)的自相关函数,n 是信号的采样点。使用自相关分析,随机噪声的干扰可以被显著抑制,因为随机噪声的自相关函数除了在m=0 外,在各处均为0。然后,电磁超声共振信号的功率谱密度(PSD)函数可以被定义为等式(3)。PSD 函数表示超声波功率随频率变化的强度。与离散傅里叶变换(DFT)不同,离散傅里叶变换(DFT)显示信号的频谱含量(信号中谐波的幅度和相位),PSD 描述信号的功率在频率上分布。

式中,P(f)为超声共振信号的功率谱密度,f 为频率分量,Hz;W(m)为窗函数,Δt 为采样间隔,s。
2.3 实验系统及试件
电磁超声自动扫查检测系统如图3 所示,主要由检测单元和扫查单元两部分构成。检测单元主要由RITEC RAM-5000 SNAP 电磁超声检测设备、专用小型EMAT 电磁超声探头、Tektronix DPO4104 数字示波器、带通滤波器,阻抗匹配器和控制计算机组成。为实现小型金属环-含能材料粘接试件的检测,专用小型电磁超声探头线圈直径仅为5 mm,与电磁超声检测设备连接,用于超声波信号的激发和接收。数字示波器与电磁超声检测设备连接实现超声信号的采集,为提高信号的信噪比,示波器采用16 次平均模式进行信号采集和显示。扫查单元由旋转电动扫查台组,运动控制器和控制计算机组成。扫查单元中,采用电动旋转台夹持被检试件旋转,电磁超声探头固定在扫查台支架上进行对被检试件的周向扫查。电磁超声探头与试件的提离距离约为0.5 mm,电磁超声探头端部设有弧形槽,使探头沿金属环周向运动,防止发生偏心。
人工模拟脱粘缺陷试件如图4 所示,由低碳钢金属环(图4 中剖面线部分)和高聚物粘接炸药(polymer bonded explosive,PBX)模拟材料圆柱通过环氧胶粘接而成。为模拟不同大小和不同形状的脱粘缺陷,PBX 模拟材料圆柱上设计长度10 mm,宽度W 分别为1.5,2.0,2.5,3.0,3.5 mm 的矩形通槽和直径Φ分别为1.5,2.0,2.5,3.0,3.5 mm 的圆形通孔,相邻两槽或两圆孔间隔60°。
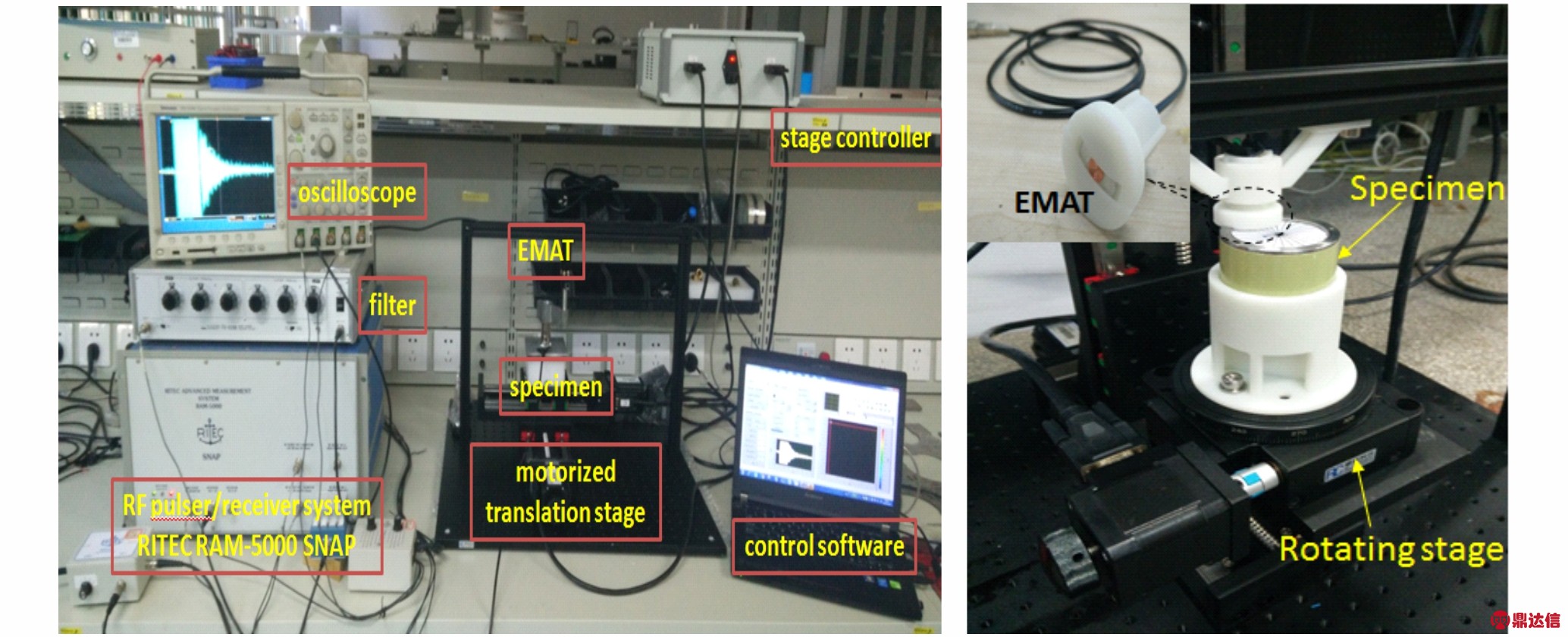
图3 金属环-含能材料界面脱粘缺陷电磁超声自动扫查实验系统
Fig.3 Experiment system of automatic electromagnetic acoustic testing for debonding inspection in the adhesive layer between metal ring and energy-containing material
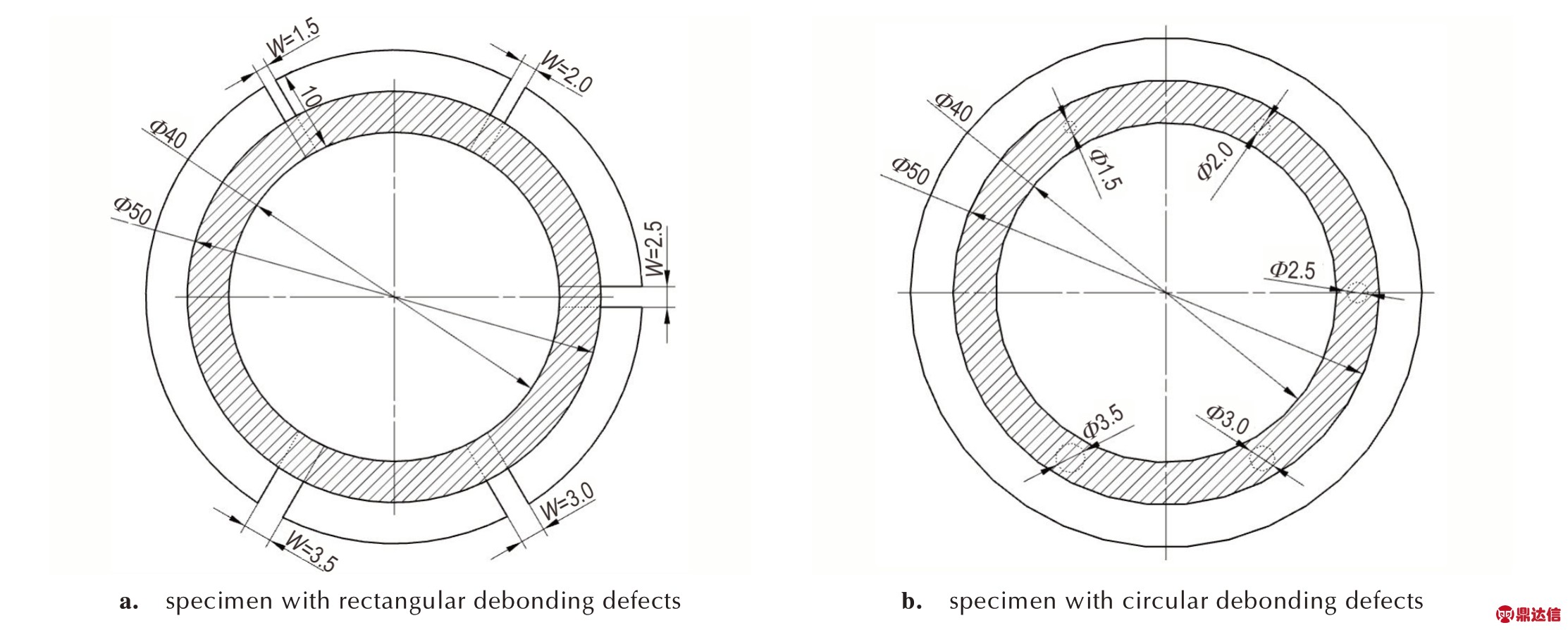
图4 金属环-含能材料界面脱粘缺陷模拟试件
Fig.4 Simulated specimens of interfacial debonding defects between metal rings and energetic materials
3 结果与讨论
3.1 脱粘缺陷电磁超声共振信号分析
根据实验测试结果,选择模拟试验件第3 阶超声共振频率2.8 MHz 为激励频率,脉冲信号持续时间10 μs,开展脱粘缺陷电磁超声共振检测工作。图5 分别为在矩形脱粘缺陷试件中粘接完好区域和宽度W=1.5,2.0,3.0 mm 脱粘缺陷上方的电磁超声共振信号;图6 分别为在圆形脱粘缺陷试件中粘接完好区域和直径Φ=1.5,3.0,3.5 mm 脱粘缺陷上方的电磁超声共振信号。由图5 和图6 可以看出,当电磁超声探头位于粘接完好区域上方时,检测信号幅值较小。当电磁超声探头位于脱粘区域上方时,检测信号幅值明显增大,出现更明显的超声共振现象,且随着脱粘缺陷的增大而增大。因此,可以看出该检测方法对于金属环-含能材料界面脱粘缺陷具有很好的检测效果,可以检测出脱粘缺陷的存在,并一定程度上评价其大小。
3.2 脱粘缺陷电磁超声共振B 扫成像

图5 矩形脱粘试件不同位置对应的电磁超声共振信号
Fig.5 Measured electromagnetic acoustic resonance signals for specimen with rectangular debonding defects of different position
为了进一步验证该检测方法对于金属环-含能材料界面脱粘缺陷的检测能力,采用所开发的电磁超声自动扫查和成像系统对模拟试件进行环形扫查和超声B 扫成像。图7 分别为矩形和圆形脱粘缺陷试件电磁超声共振B 扫图像。从图7a 中可以明显观察到①~⑤五个位置处信号幅值(像素颜色)明显较强,分别为W=3.5,3.0,2.5,2.0 mm 和1.5 mm 脱粘缺陷B 扫成像。从图7b 中可以明显观察到①②③三个位置处信号幅值明显较强,分别为Φ=3.5,3 mm 和2.5 mm 脱粘缺陷B 扫成像。而Φ=2.0 mm 和Φ=1.5 mm 两较小脱粘缺陷却无法看到,是因为脱粘缺陷面积太小,已超出探头的检测灵敏度。
3.3 脱粘缺陷电磁超声共振功率谱成像
从两电磁超声B 扫图可以看出,图中7 部分超声背景信号分布并不均匀,这给缺陷的识别造成一定的困难。为克服这一问题,根据图5 和图6 可以看出当脱粘缺陷存在时,电磁超声共振信号衰减变小,持续时间更长,因此可选择时间靠后的信号进行分析。为更好对缺陷进行识别,提高缺陷信号的成像质量,降低因金属环本身材质导致的超声共振信号变化的影响,截取图7 中黄色虚线框内时间段的时域信号,通过功率谱(PSD)变换将时域信号转为频域信号,生成的频域B 型显示图如图8 所示。图8a 中可很清楚地观察到五个脱粘区域在共振激励频率出现功率谱峰值区域,图8b 中可很清楚地观察到三个脱粘区域在共振激励频率出现功率谱峰值区域,而其他背景区域均无明显的噪声存在。由图8 可见,通过进行功率谱分析处理后,有效抑制背景信号和其他噪声的影响,缺陷成像质量大幅度提高,具有更高的缺陷可识别性。
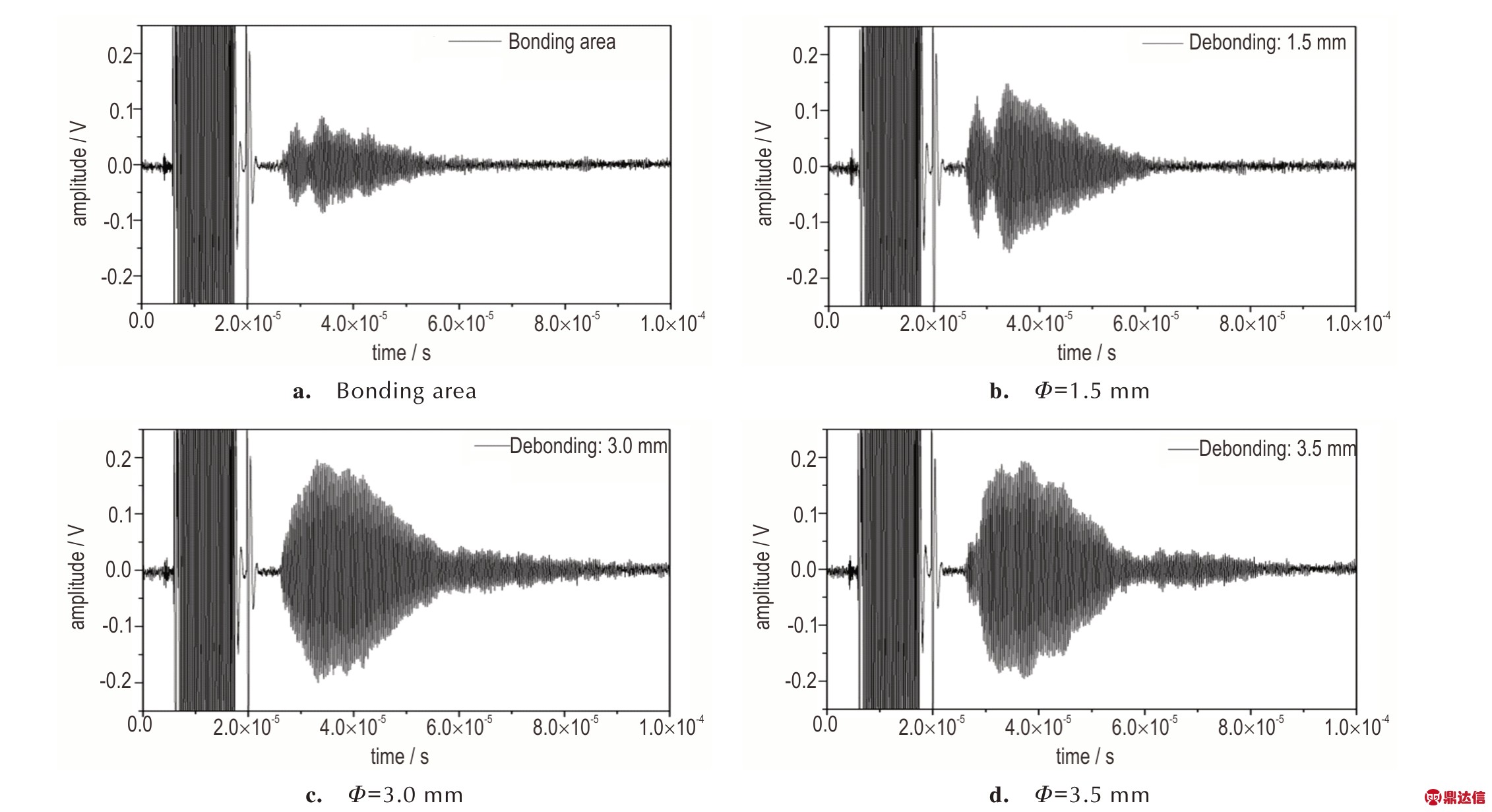
图6 圆形脱粘试件不同位置对应的电磁超声共振信号
Fig.6 Measured electromagnetic acoustic resonance signals for specimen with circular debonding defects of different position
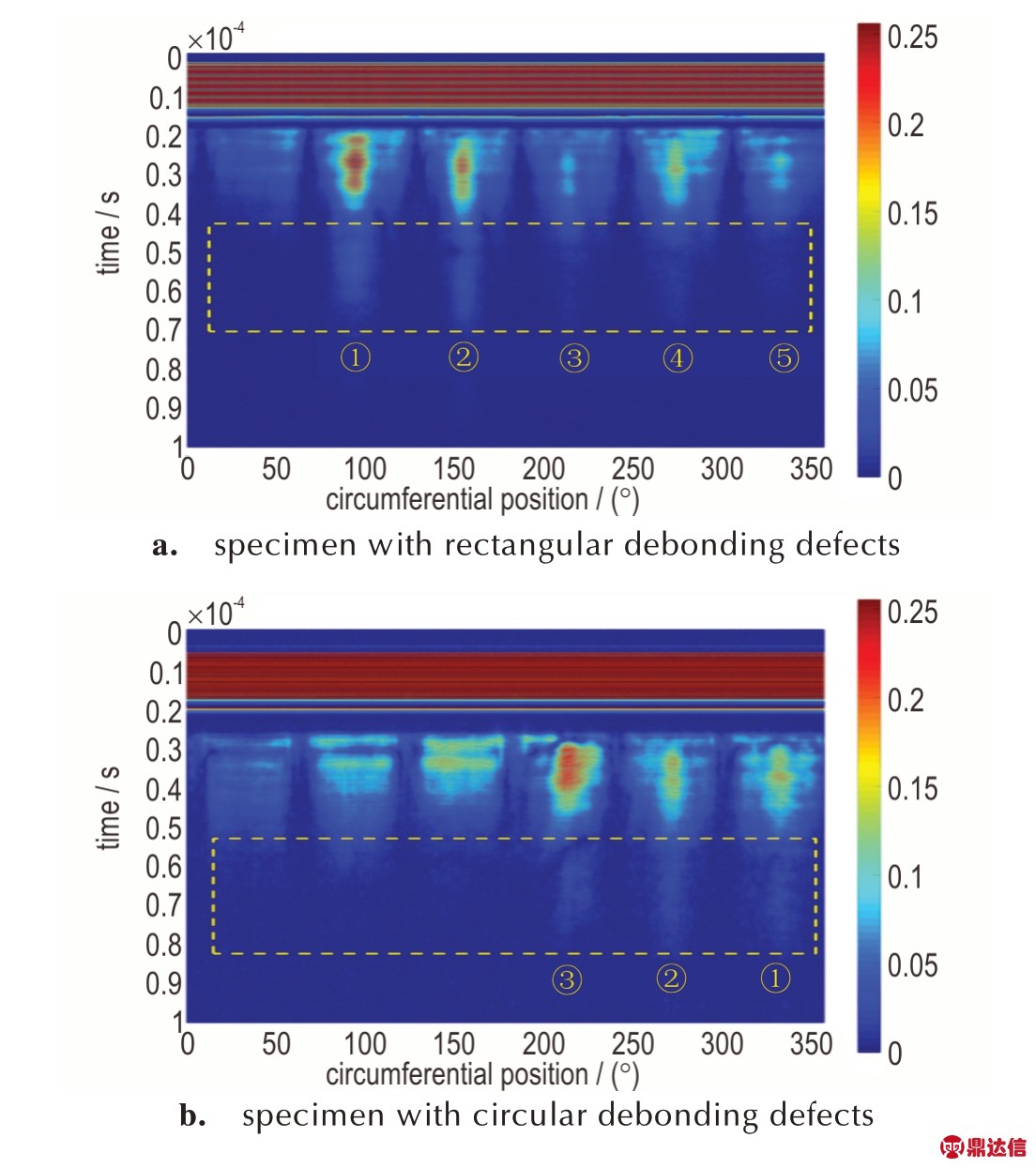
图7 金属环-含能材料试件环形扫查电磁超声共振时域信号B扫图
Fig.7 B-scan images of electromagnetic acoustic resonance time-history signal with rotating scanning of the metal ring /energy-containing material specimen
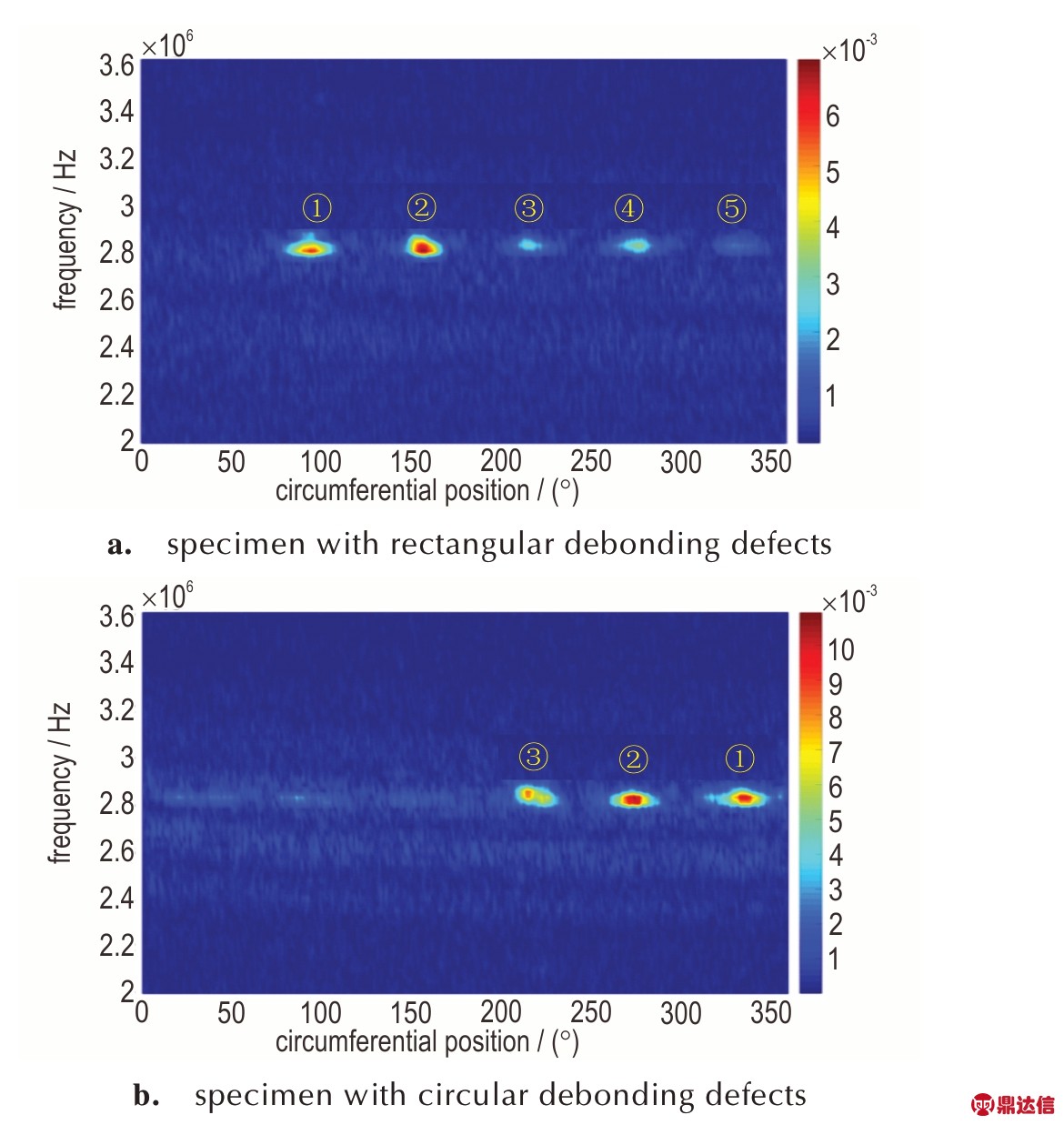
图8 金属环-含能材料试件环形扫查电磁超声共振功率谱密度B扫图
Fig. 8 B-scan images of electromagnetic acoustic resonance PSD with rotating scanning of the metal ring / energy-containing material specimen
4 电磁超声共振脱粘缺陷检测能力分析
图9 为提取图8 中提取功率谱峰值得到其分布曲线。从图9 可以看出,随着缺陷尺寸的减小,功率谱峰值总体分布上也存在下降趋势,但存在较大的误差,如图9 中①号缺陷位置对应功率谱密度峰值应大于②号缺陷位置功率峰幅值,③号缺陷位置功率谱密度峰值应该大于④号缺陷位置功率谱幅值,但受到金属环材质(磁化系数)不均的影响,实际测量结果却与之相反,这给缺陷尺寸定量带来一定困难。
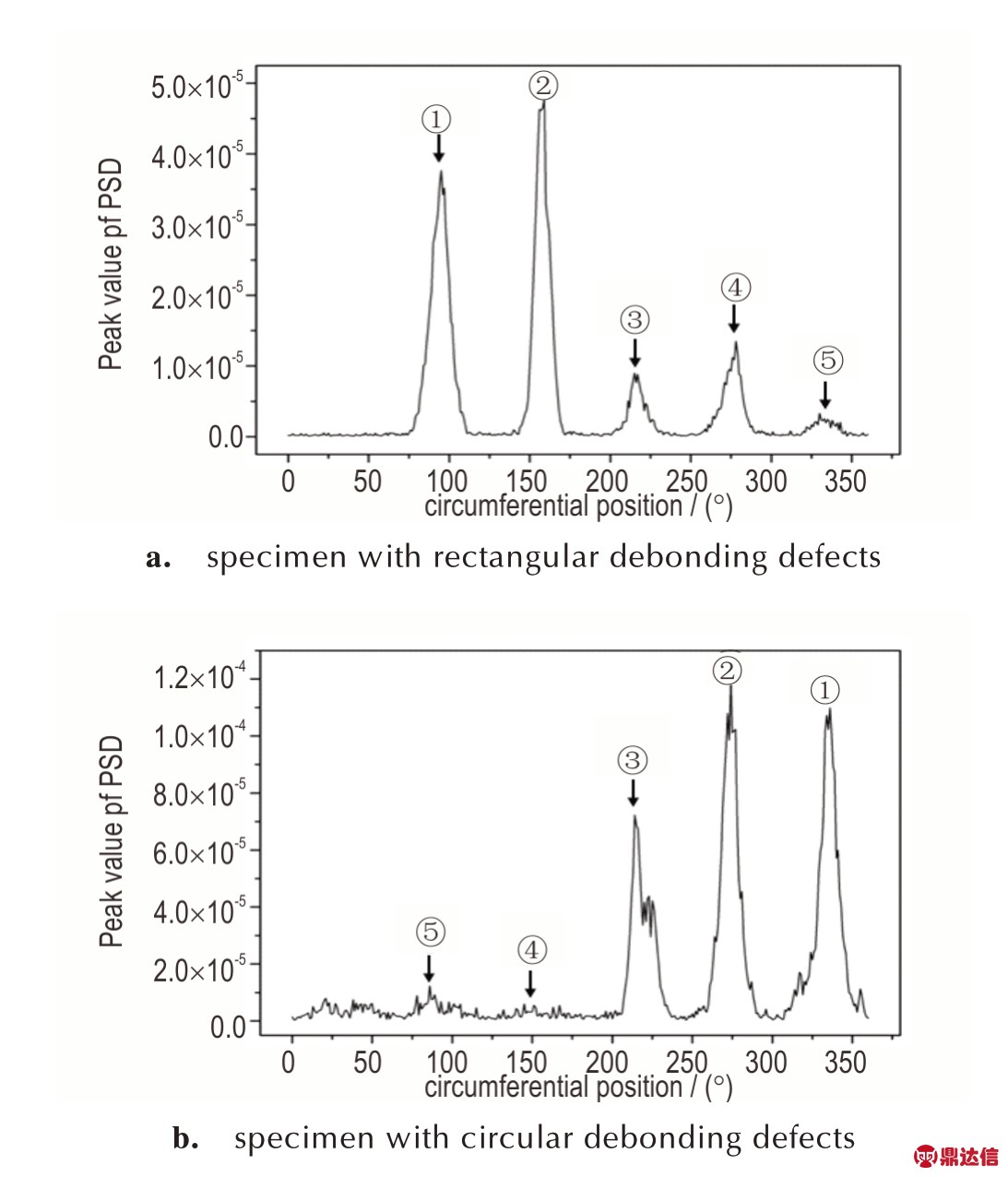
图9 环形扫查电磁超声共振信号PSD 峰值分布曲线
Fig.9 PSD peak distribution curve of electromagnetic acoustic resonance signal by circular scanning
通过上述结果可以看出,由于金属环-含能材料试件中脱粘缺陷的尺寸远小于检测所采用探头的尺寸,超出了探头的分辨极限,因此很难从B 扫图中准确获得缺陷的尺寸和形状信息。为进一步说明该方法对于缺陷的分辨能力,在此借用前期针对平板粘接试件的检测结果进行分析。图10 为一金属-有机玻璃平板粘接试件电磁超声共振C 扫检测结果[11],从中可以看出对于直径2 mm 和3 mm 的圆形脱粘缺陷,其所对应缺陷成像尺寸与实际尺寸相差较大,而接近探头的尺寸(直径5 mm)或更大尺寸的缺陷,其成像结果则与实际尺寸相近,且能分辨缺陷的形状。因此该方法对于缺陷的分辨能力主要受所采用检测探头的尺寸限制,要提高对小缺陷的形状和尺寸的分辨能力,需要进一步研究和开发更小尺寸的电磁超声探头,或者开发聚焦型探头。

图10 金属-有机玻璃平板粘接试件电磁超声共振C 扫检测结果
Fig.10 C-scan image of PSD peak of electromagnetic acoustic resonance signal in metal-plexiglass bonding specimen
5 结论
(1)基于电磁超声共振的金属环-含能材料界面脱粘缺陷检测方法,开发了用于金属环-含能材料粘接试件界面脱粘缺陷检测专用的小型电磁超声探头,搭建了电磁超声自动扫查和成像系统,实现了金属环-含能材料界面脱粘缺陷模拟试件的自动扫描和超声B 扫成像,开发了基于功率谱分析的电磁超声共振信号处理方法。
(2)实验测量结果表明电磁超声共振检测方法对于金属环-含能材料界面脱粘缺陷具有很好的检测灵敏度,可以实现宽度1.5 mm 以上的矩形脱粘缺陷和直径2.5 mm 以上的圆形脱粘缺陷检测和B 扫成像。
ARL(美国研究图书馆协会)与德克萨斯A&M大学合作,通过对SERVQUAL的不断研究与修订,于2000年正式提出LibQUAL+TM。其基于用户对图书馆的服务意见,严格依据网络的调查方法,评价并提高图书馆服务质量。