摘要:双金属复合管和耐蚀合金预制内补口钢管以其优异的耐腐蚀性能和免补口特点在油田中得到了广泛应用,特别是耐蚀合金预制内补口钢管造价相对低廉,近年来在国内油田高腐蚀地面管道中得到了较大面积的推广,效果良好。由于双金属复合管内、外层金属在化学成分、微观组织、物理性能等方面的差异,常用的对接焊接工艺存在工序复杂、操作难度大、施工成本高、焊工技能要求严的难题,容易造成成分偏析、耐蚀合金成分稀释、内焊道成形不良、虚焊、碳迁移和热输入引起的熔合区组织变化等结果。从影响双金属焊缝质量的因素出发,以不锈钢复合管水平固定对接焊为研究对象,从坡口形式、组对方式、耐蚀合金打底焊层和双金属过渡焊层的焊接方法等方面进行实验研究,提出了复合管内封焊、U型坡口无间隙组对、熔池背部保护、无填充熔化焊打底和无填充熔化焊过渡等新的工艺方法,通过X射线探伤和焊接工艺评定,并结合微观组织分析,对焊接工艺进行了综合评价。
关键词:复合管;耐蚀合金预制内补口钢管;双金属焊缝;无填充熔化焊打底;无填充双金属过渡焊
0 前言
油田单井油气输送用埋地钢质管道孔径较小(不大于φ114 mm),由于没有小孔径钢质管道焊口内防腐补口技术,一般不对管道内壁进行防腐处理,随着油田采出液腐蚀性的增加,管道内腐蚀日趋严重。以胜利油田为例:胜利油田现有单井管道6 000余条,总长超过10 000 km,由于输送介质的复杂性,油田单井、注水、集输管线的内壁腐蚀远远超过管道外壁的腐蚀,调查发现,油田单井、注水和集输管线腐蚀穿孔的部位70%~80%集中在焊口区域。油田管道寿命一般为2~3年,部分管道运行不到一年就发生穿孔现象。据统计,油田金属管道平均每10 km存在2.5处隐患,每年因腐蚀造成的管道维修、污染环境等经济损失超过2亿元,因重复建设造成的经济损失无法估量,这也是开采成本居高不下的原因之一。
双金属复合管和耐蚀合金预制内补口钢管凭借其优异的耐腐蚀性能和免补口特点,在油田中得到了广泛应用,特别是耐蚀合金预制内补口钢管的造价相对低廉,近年来在国内油田高腐蚀埋地管道中得到了较大面积的推广,取得了良好的效果。
耐蚀合金预制内补口钢管是一种在普通碳钢钢管管端内壁通过堆焊或堆焊+内衬预制一层耐蚀合金层,然后对钢管内壁进行防腐处理,在管道焊接连接后,通过耐蚀合金焊缝连接管道内防腐层形成连续有效的钢管。其管端结构相当于不锈钢内衬复合管,如图1所示。
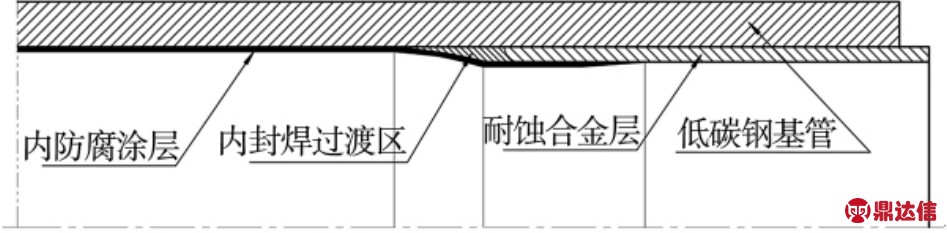
图1 耐蚀合金预制内补口防腐钢管结构
Fig.1 Structure of corrosion-resistant alloy prefabrication inner joint coating and corrosion-resistant steel pipe
由于油田埋地管道必须在地上焊接连接至几百米以上长度后再下沟连头,所以只能采用水平固定管管对接焊接。并且要求双金属焊缝不锈钢打底层中不得熔入碳钢成分、碳钢填充盖面层与打底焊层必须良好熔合等,这就需要技能较高的焊工才能完成。而国内高技能焊工较少,无法完成油田埋地管道巨大的工作量,这限制了不锈钢内衬复合管道和耐蚀合金预制内补口管道的推广应用。
因此,针对双金属复合管的焊接施工难题,从焊接材料、封焊方法、坡口形式、组对方式、焊接方法等因素出发,开发一种更简单可靠的焊接工艺,以降低焊接施工难度,提高焊缝质量,延长管道寿命,降低管道建设和运营综合成本,减少管道安全、环保风险,推动不锈钢双金属复合管道和耐蚀合金预制内补口管道的应用,具有重要意义。
1 影响复合管焊缝质量的主要因素
1.1 复合管封焊位置对打底焊层质量的影响
1.1.1 外封焊对打底焊层质量的影响
复合管的内衬管与基管是机械结合,层间存在间隙,通常采用GB/985.4推荐的坡口形式[1]和外封焊方法[2]。其坡口形式、封焊位置和组对间隙如图2所示。焊接施工方案为不锈钢焊丝氩弧焊打底+309L氩弧焊过渡+J507焊条电弧焊填充盖面。
在复合管焊接中,打底焊层的焊接质量至关重要。传统的复合管焊接工艺采用管口间隙组对的方法,当采用焊条电弧焊时,容易造成内焊道焊瘤、夹渣、未熔透等缺陷;采用TIG焊时,会使外封焊层再次熔化,双金属夹层内的空气会因膨胀而逸出,极易造成熔合区焊缝一侧气孔的产生,严重时会穿透打底焊层,在输送液体导电介质时,引起双金属夹层电偶腐蚀现象而形成刺漏,如图3所示位置。
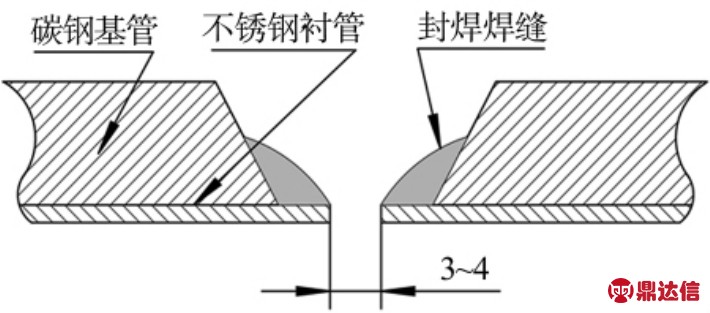
图2 内衬不锈钢复合管管管组对、对接封焊示意
Fig.2 Schematic diagram for assembly and butt welding of lined stainless steel composite pipe

图3 复合管对接环焊缝内焊道刺漏截面照片
Fig.3 Cross section photo of internal weld penetration of butt girth weld of composite pipe
1.1.2 内封焊V型坡口对打底焊层质量的影响
为避免外封焊复合管存在的双金属夹层内空气膨胀造成的熔合区焊缝一侧气孔的产生,耐蚀合金预制内补口钢管采用管端内堆焊方法,使基管与不锈钢层冶金结合,其结构如图4所示。
管端内堆焊复合管的焊接施工方案与机械复合管相同,一般采用不锈钢焊丝氩弧焊打底+309L氩弧焊过渡+J507焊条电弧焊填充盖面。采用手工氩弧焊打底焊接时,氩气电弧极易将坡口面的碳钢成分熔入打底焊层的内表面,由于双金属电位存在差异,同样存在输送液体导电介质时在焊缝碳钢处发生孔蚀[3]的现象。
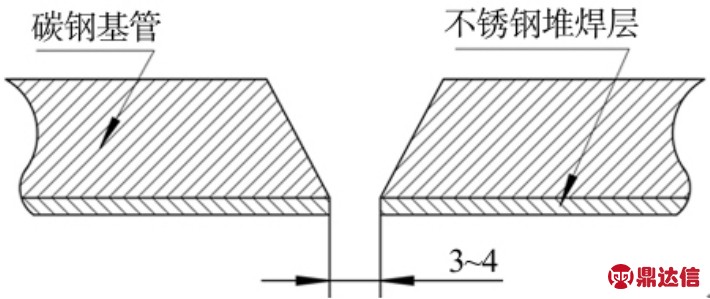
图4 内堆焊复合管管管组对、对接示意
Fig.4 Schematic diagram of pipe assembly and butt joint of composite pipe with internal surfacing
1.2 双金属过渡焊层焊接工艺对焊缝质量的影响
双金属之间的过渡层是熔合耐蚀合金打底焊层、碳钢坡口面和碳钢填充焊层,起到双金属过渡作用的焊层,是影响复合管双金属焊缝质量的关键。由于耐蚀合金内层及不锈钢焊材在化学性能、物理性能等方面与碳钢及焊材存在较大差异,在双金属焊缝焊接过程中会出现许多难以解决的问题。其中碳迁移引起的熔合区脆化、双金属结晶裂纹、热应变引起的焊道裂纹等尤为明显,削弱了焊缝的力学性能和耐腐蚀性能,难以满足工程结构中的实际需要[4]。
采用奥氏体不锈钢焊材在不锈钢打底焊层之上与低碳钢坡口面进行双金属过渡层焊接时,存在许多问题,主要表现在以下两个方面:
(1)钢的熔点在1 500℃左右,不锈钢焊材的熔点与之接近;低碳钢焊材的熔点约1 600℃。当采用奥氏体不锈钢焊材在不锈钢(309L)打底焊层之上进行双金属过渡焊接,且过渡焊层较厚时,由于焊材熔点的差异,309L过渡焊层表面熔化流平遮盖了底部两侧坡口面,致使碳钢坡口表面未达到熔化温度,出现了不锈钢过渡焊层与不锈钢打底焊层之间熔合良好,而与低碳钢坡口面虚焊的现象,如图5所示。
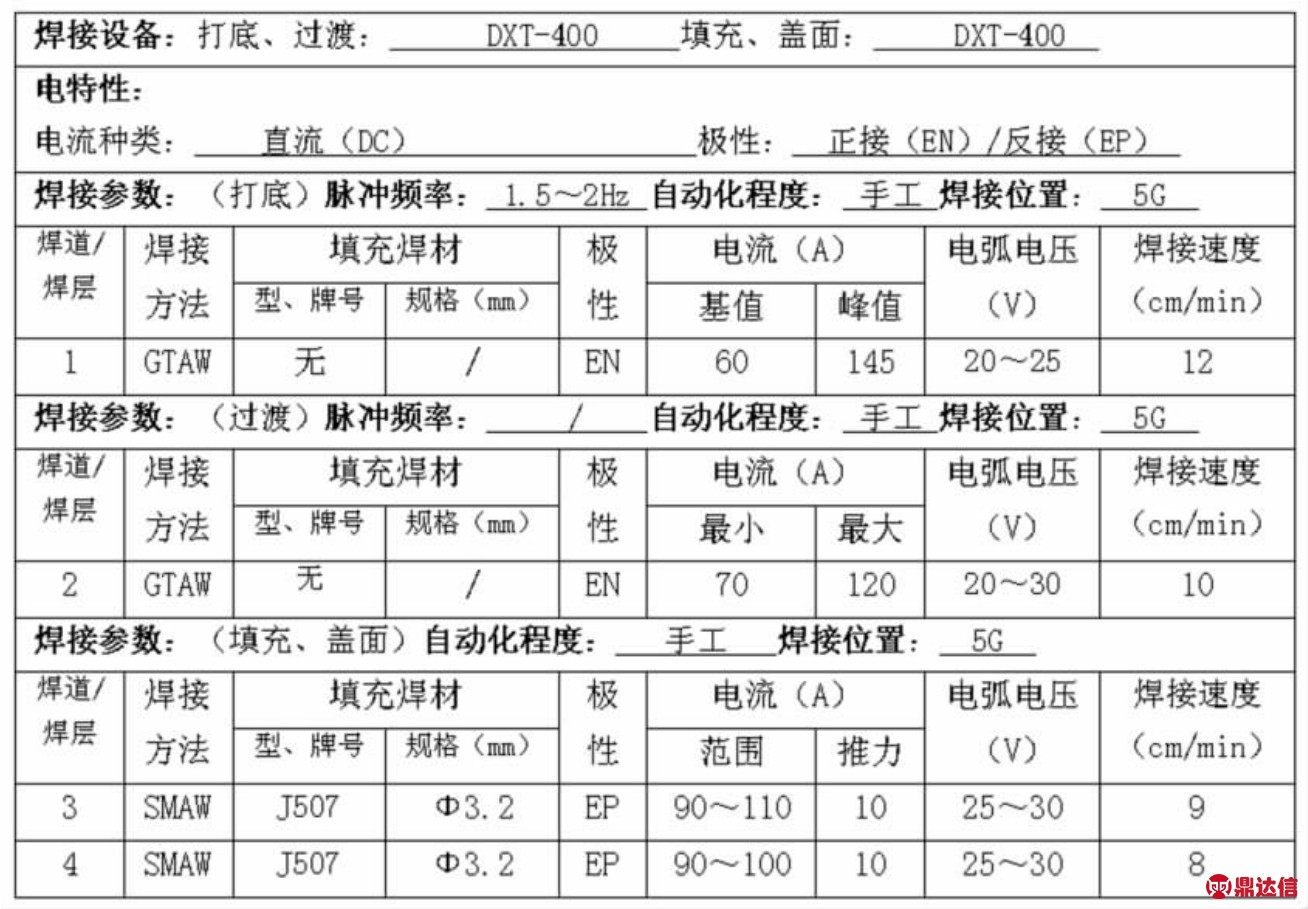
图5 309L过渡层与坡口面虚焊
Fig.5 False welding of 309L transition layer and groove surface
(2)焊道或焊层之间,以及焊缝与母材之间的残余应力对焊缝的力学性能和耐腐蚀性能有害。在同种钢焊缝中,引起此应力原因是焊接热输入造成的应力分布不均匀,该现象可以通过焊后热处理来消除;在异种钢焊缝中,除了上述原因外,不同金属线膨胀系数的差异也会引起焊缝应力,焊后热处理只能使层间应力均匀分布,不能完全消除。
20℃时,20钢的线膨胀系数为12.78×10-6/℃,309L不锈钢焊材的线膨胀系数为15.85×10-6/℃,两者差异较大,焊层中势必存在较大的应力。S2209管端内堆焊复合管如图6所示,采用S2209打底,309L过渡和填充盖面的焊缝侧弯试件,其中S2209的线膨胀系数为13.70×10-6/℃,更接近于20钢。由图6可知,试件侧弯后内焊道有开裂现象,原因是线膨胀系数较大的309L过渡层在焊接过程中受热膨胀,导致线膨胀系数较小的S2209打底焊层与堆焊焊层之间开裂。

图6 堆焊层应力开裂
Fig.6 Stress cracking of hardfacing layer
1.3 小结
由于双金属复合管内、外层金属在化学成分、微观组织、物理性能等方面的差异,传统的对接焊接工艺存在工序复杂、现场操作难度大、施工成本高、焊工技能要求严的问题,容易造成成分偏析、耐蚀合金成分稀释、内焊道成形不良、虚焊、碳迁移和热输入引起的熔合区组织变化,以及层间熔合不良、基管成分熔入内焊道引起电化学腐蚀等结果。
焊接实践证明,如果没有高超的焊接技能,难以控制打底焊层不熔入碳钢成分以及保证309L过渡层与碳钢坡口面的良好熔合,不能保证双金属焊缝质量。因此,需要一种简单可靠的、低技能焊工即可轻易完成的复合管焊接施工工艺,以适应油田管道建设的需要。
2 焊接工艺方案设计
2.1 焊接设备和方法
2.1.1 焊接设备
采用逆变式直流脉冲焊接电源或自动焊机来完成水平固定复合管双金属环焊缝的焊接。
2.1.2 焊接方法
a.打底焊层——TIG不摆动脉冲无填充熔化焊。采用该方法的目的是:(1)无填充熔化焊可避免内焊层熔入碳钢成分,保证通过内焊层连接的耐蚀合金内衬层连续有效。(2)可在确保焊层熔透的前提下,采用脉冲电流打底焊防止热输入过大引起的仰焊位置焊缝内凹。
b.双金属过渡焊层——TIG无填充摆动熔化焊。为防止过渡层与两侧坡口面虚焊,本方案设计采用无填充氩弧摆动,将堆焊熔合区和坡口面的碳钢成分熔化在打底焊层之上,形成含有双金属成分的过渡层,以保证双金属焊层之间熔合良好。
c.填充盖面层——摆动焊。填充盖面焊层的焊接方法采用传统TIG摆动填丝焊或焊条电弧焊。
3 坡口设计和试件制作
3.1 主要设计思想
(1)应确保耐蚀合金熔化焊打底焊层不熔入坡口面碳钢成分。
(2)除适用于手工焊接外,还能适用于自动焊接。
(3)应能以较少的金属填充量完成双金属环焊缝的焊接。
3.2 坡口的适用性分析
3.2.1 U型坡口的适用性分析
如果将GB/T985.4推荐的U型坡口改为无间隙组对(见图7a),则存在如下问题:
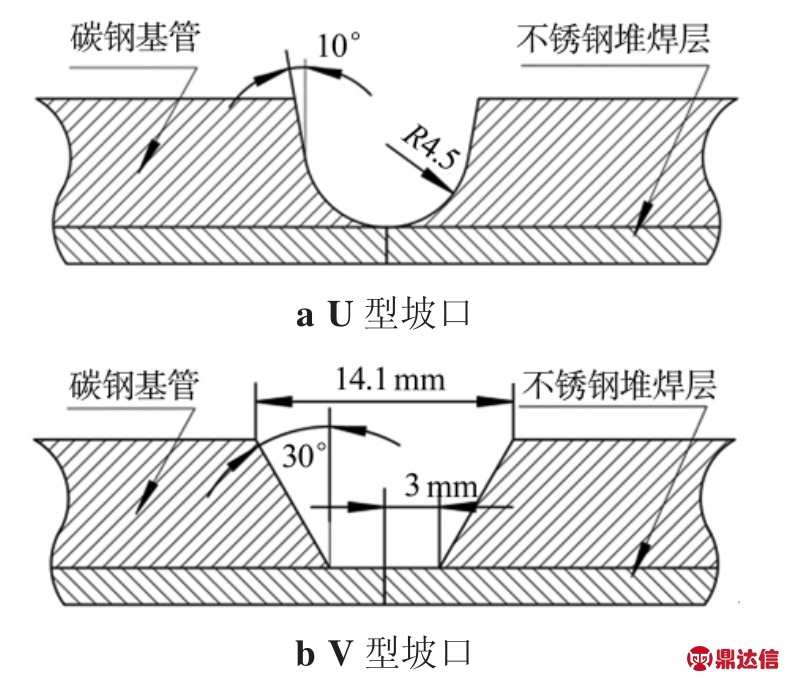
图7 GB/T985.4推荐的坡口形式
Fig.7 Groove type recommended in GB/T985.4
(1)能够实现熔化焊单面焊双面成型的需要,但无法避免碳钢熔入焊层。
(2)自动焊机垂直的钨针氩气电弧无法直接作用于碳钢坡口面,难以形成双金属过渡层。
3.2.2 V型坡口的适用性分析
如果将GB/T985.4推荐的V型坡口改为无间隙组对(见图7b),可以保证熔化焊打底焊层不熔入碳钢成分,但存在以下问题:
(1)钝边宽度较大,无法使坡口面根部熔化流平形成双金属过渡层。
(2)坡口面与钝边交界处的形状增加了焊前清理的难度。
3.2.3 结论
GB/T985.4推荐的复合钢坡口适用于间隙组对、填充金属打底焊接工艺,无法适用于复合管的自动或手工熔化焊打底、过渡的焊接工艺。所以,需要重新设计一种坡口形式,以符合设计思想的要求。
3.3 坡口设计
3.3.1 坡口形状和尺寸
对上述两种坡口进行了改进,以适应设计思想的要求,其形式和尺寸如图8所示。
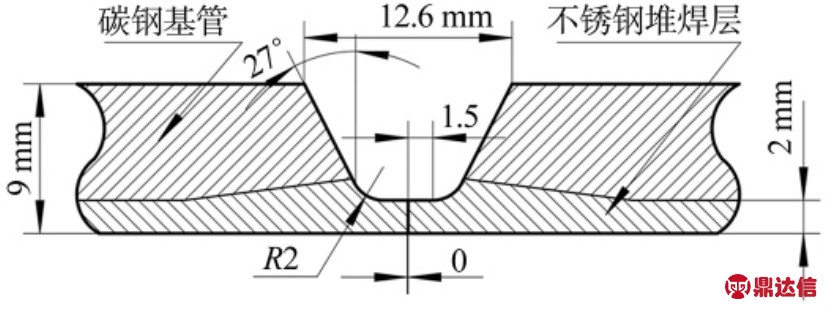
图8 坡口形式和尺寸
Fig.8 Groove type and size
3.3.2 坡口特点
(1)与推荐的V型坡口相比,减少了金属填充量(见图 7、图 8)。
(2)对管口内壁和坡口进行了机械加工,对接管口内径一致,保证了无间隙组对的精度;钝边厚度一致,为自动焊接提供了条件。
(3)钝边和圆弧过渡处由耐蚀合金构成,能够避免熔化焊打底焊层碳钢成分的熔入。
(4)坡口面的角度可使自动焊机的垂直钨针氩气电弧作用于坡口面,有利于通过熔化焊形成双金属过渡层。
(5)钝边与坡口面采用圆弧过渡,方便现场焊接前管口的清理。
3.4 试件制作
3.4.1 复合管内封焊
选择φ76×7 mm 20钢基管,采用2209双相不锈钢堆焊+内衬的预制内补口方法制作管端复合管试件,如图9所示。
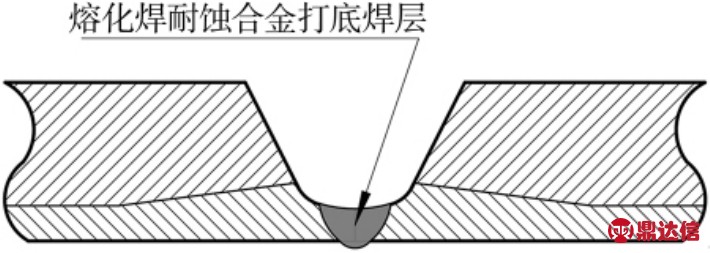
图9 耐蚀合金预制内补口钢管试件
Fig.9 Corrosion resistant alloy prefabricate steel pipe with inner joint
试件中将外封焊改为内封焊是为了防止外封焊焊道在管口对接焊接时的二次熔化引起的双金属夹层中空气的膨胀逸出,从而引起熔合区气孔的产生。
封焊材料选择与碳钢基管线膨胀系数最接近的S2209双相不锈钢,避免因膨胀系数的差异引起较大的层间应力。
封焊层在靠近管端约15 mm宽度位置加厚,是为了参与熔焊的坡口钝边处不含有碳钢成分,防止耐蚀合金成分的稀释。
3.4.2 试件机械加工
根据上述设计,对封焊完成的钢管按设计要求进行机械加工,实物如图10所示。
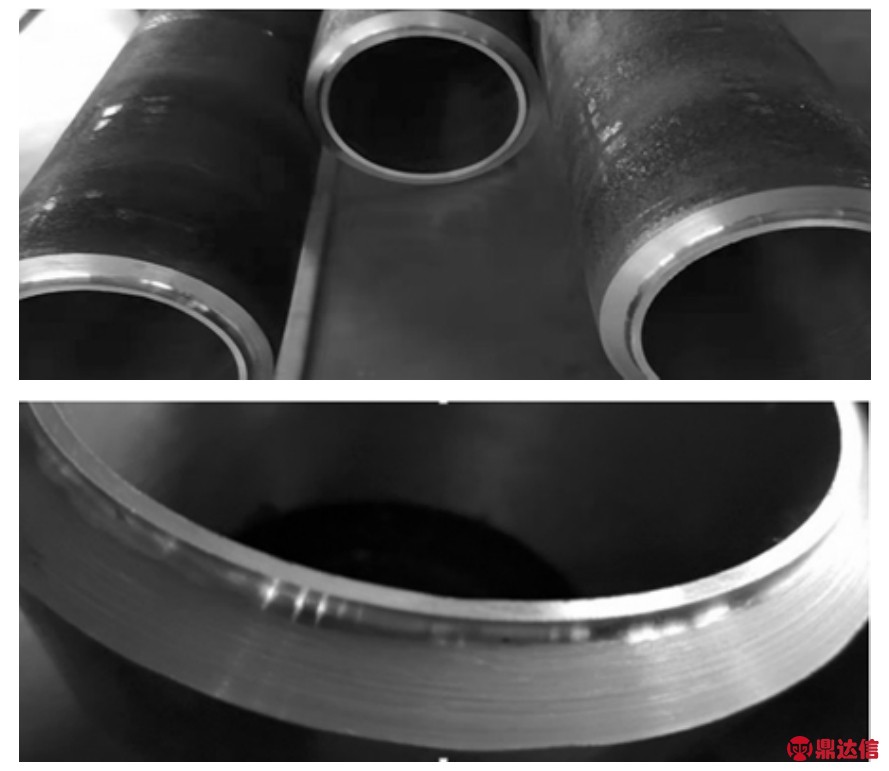
图10 加工完成的管口
Fig.10 Finished nozzle
4 管口的焊接
4.1 焊层设计
φ76×7+2 mm复合管双金属焊缝的焊层设计如图11所示。
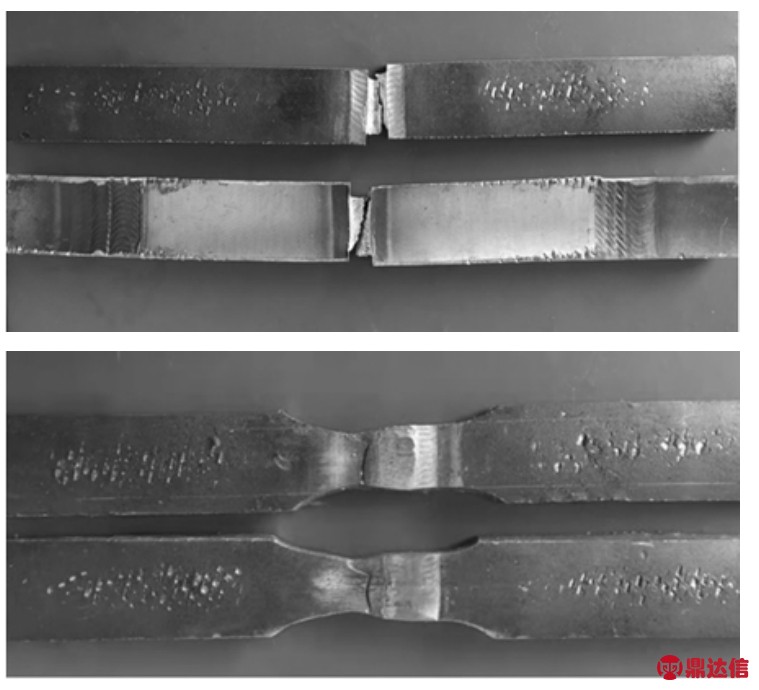
图11 焊层设计简图
Fig.11 Welding layer design diagram
4.2 焊前准备
4.2.1 管口清理
采用钢丝刷清理坡口面,采用砂布轮将管口内、外约10 mm范围内清理干净,待焊接部位丙酮擦拭。
4.2.2 熔池背部保护
管口清理后组对前,在管口内壁约5 mm范围内按说明书均匀涂抹免充氩保护焊剂[5]。然后将钝边处的多余部分擦拭干净。
4.2.3 管口组对
试件采用无间隙组对如图12所示。野外施工现场采用专用对口架组对,组对速度较传统方法快而准确。
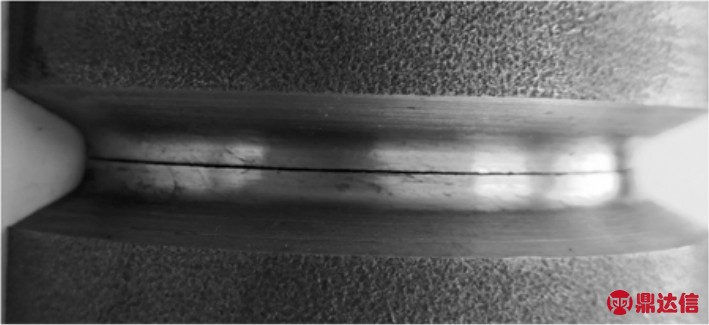
图12 管口无间隙组对
Fig.12 No gap assembly at nozzle
4.2.4 管口定位
采用无填丝氩弧熔化焊定位焊接方法,每段定位焊道的长度不小于15 mm,并均匀分布在圆周上且不少于3处。
4.3 焊接要点
4.3.1 打底层
采用手工氩弧焊将对接的耐蚀合金钝边熔化形成打底焊层,如图13所示。在熔焊过程中无需填充焊材。
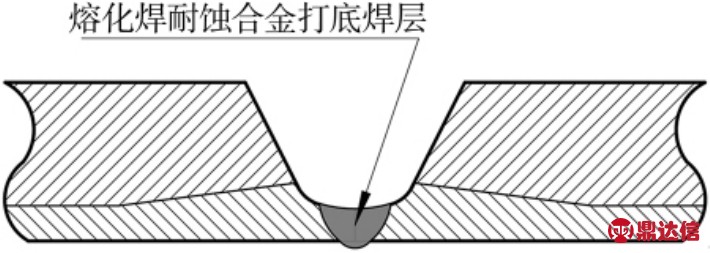
图13 无填充熔焊打底焊层
Fig.13 Unfilled fusion welding backing layer
4.3.2 过渡焊层
打底层完成后,如果直接采用碳钢焊条进行基管焊接,不可避免会出现焊缝耐蚀合金元素的稀释,以及材料膨胀系数的差异引起的层间裂纹,因此,必须进行双金属过渡层焊接[6]。
双金属过渡层的焊接要点是焊层要薄,要保证双金属组织均匀。
具体方法是:钨极氩气电弧主要作用于坡口面根部,在两侧稍作停留,将坡口面的一部分熔化,通过钨极摆动推动熔池在打底焊层上形成较薄的双金属过渡层(约1.5~2 mm),如图14所示,整个焊接过程无需填充金属。
该焊层含有堆焊耐蚀合金和坡口面碳钢成分,与碳钢和耐蚀合金都具有良好的焊接性,且线膨胀系数居于两者之间,层间不会存在较大的残余应力。
4.3.3 填充盖面焊层
采用焊条电弧焊进行填充、盖面层的焊接,完成双金属焊缝的焊接。本试验采用φ1.0 mm的ER50-6焊丝钨极氩弧自动焊接代替焊条电弧焊完成填充、盖面层的焊接。
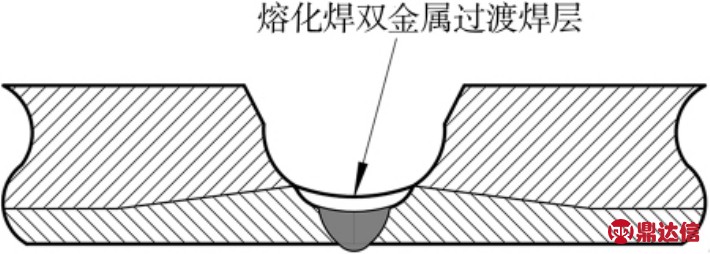
图14 无填充熔化焊过渡焊层
Fig.14 Unfilled fusion welding transfer layer
4.4 焊接工艺参数
手工焊焊接工艺参数如图15所示。本实验在手工氩弧打底、过渡焊层完成后,采用自动焊接机进行了填充、盖面焊层的焊接试验,以检验自动焊机的性能和适用性,其预设的焊接参数如图16所示。
4.5 焊接过程和焊层外观
手工打底、过渡焊层外观如图17所示。自动填充、盖面焊层外观如图18所示。
5 焊缝检测和分析
5.1 焊层外观目测检测
各焊层外观无缺陷,熔合良好。
5.2 焊缝微观组织分析
将焊缝金属截取试件并分区,如图19所示,观察分析其微观组织。其中,熔化焊打底焊层的微观组织如图20所示,过渡焊层微观组织如图21所示,低碳钢填充层与坡口面熔合区微观组织如图22所示。
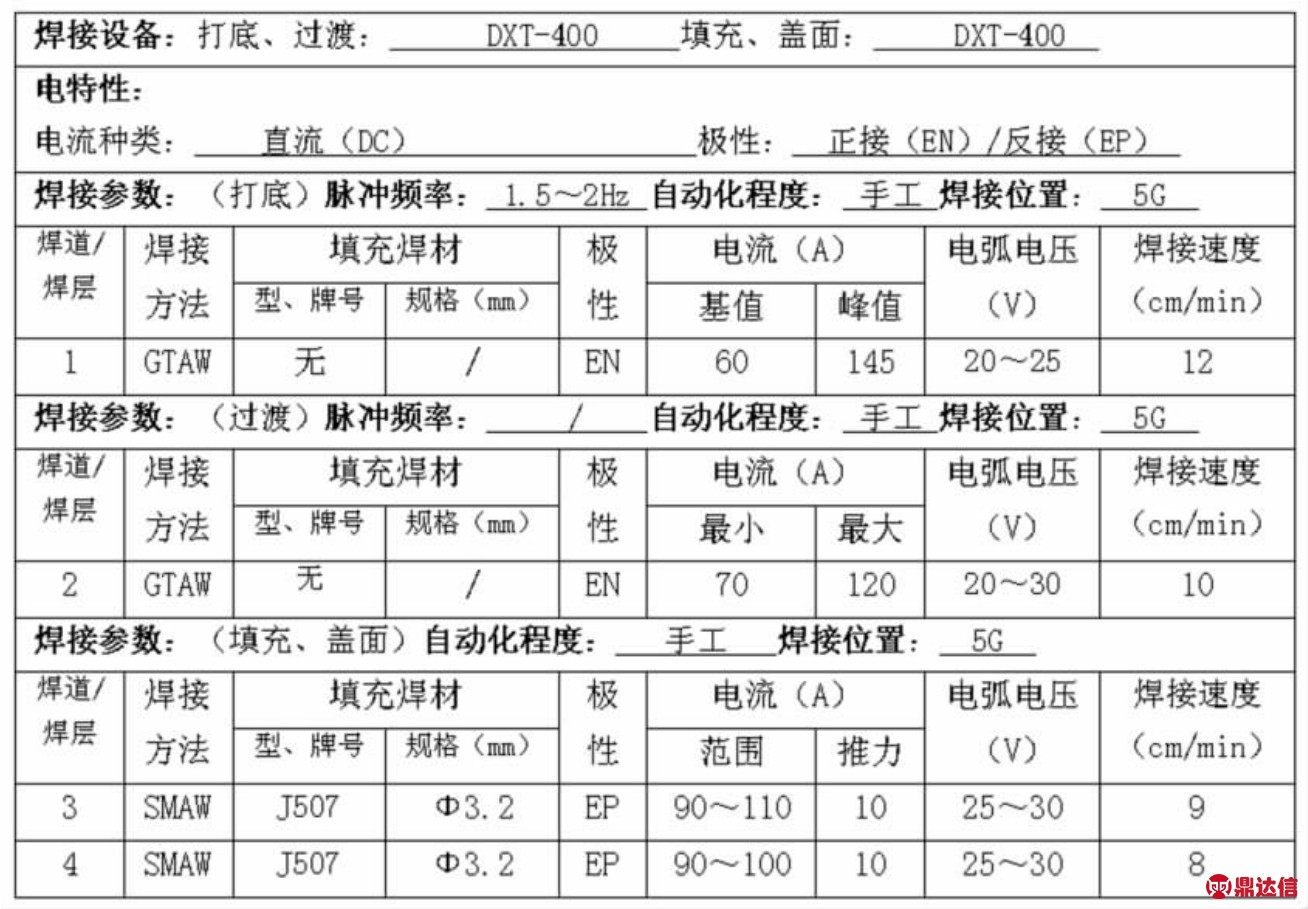
图15 手工焊焊接工艺参数
Fig.15 Manual welding process parameters
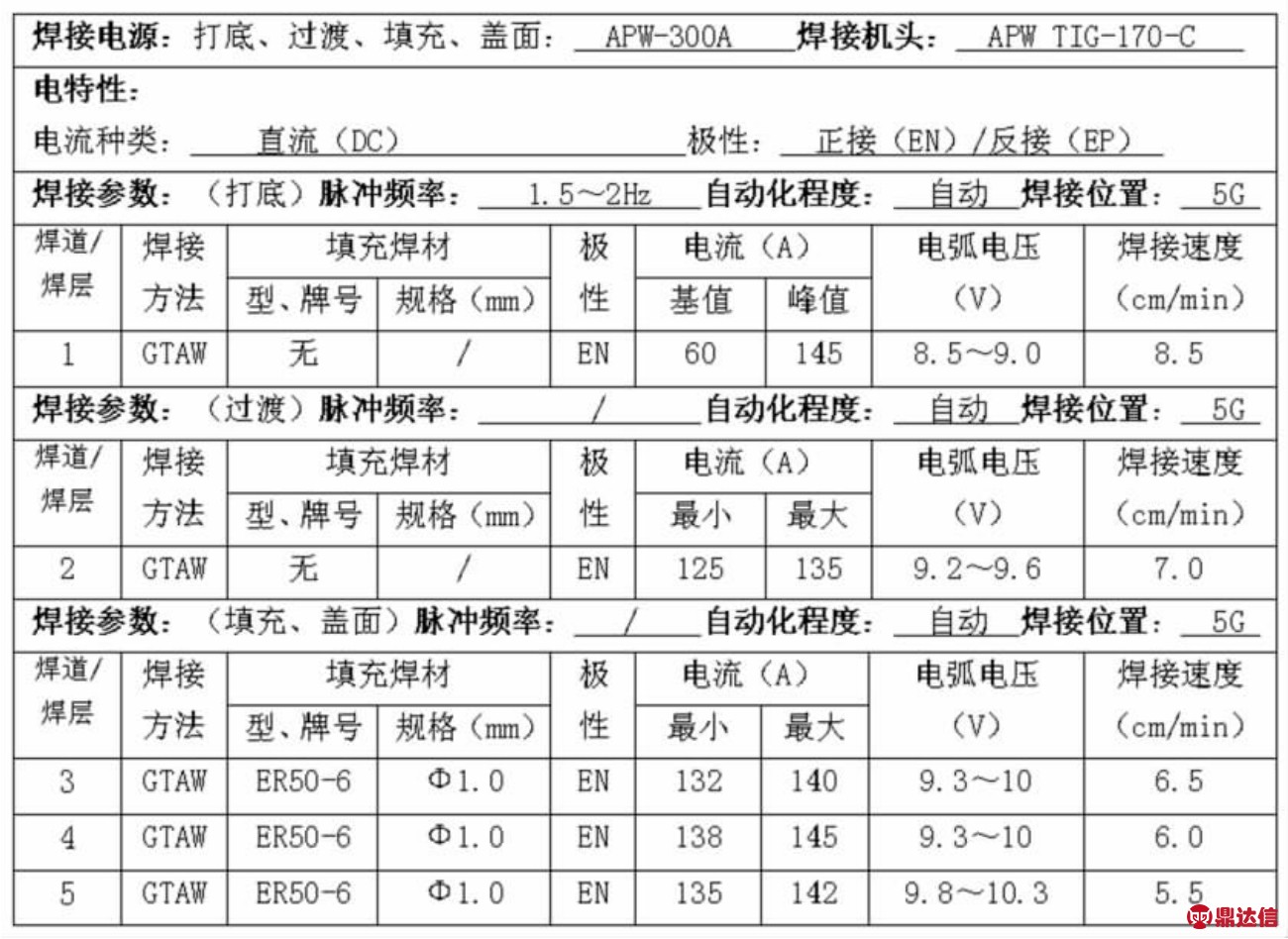
图16 自动焊焊接工艺参数
Fig.16 Automatic welding process parameters
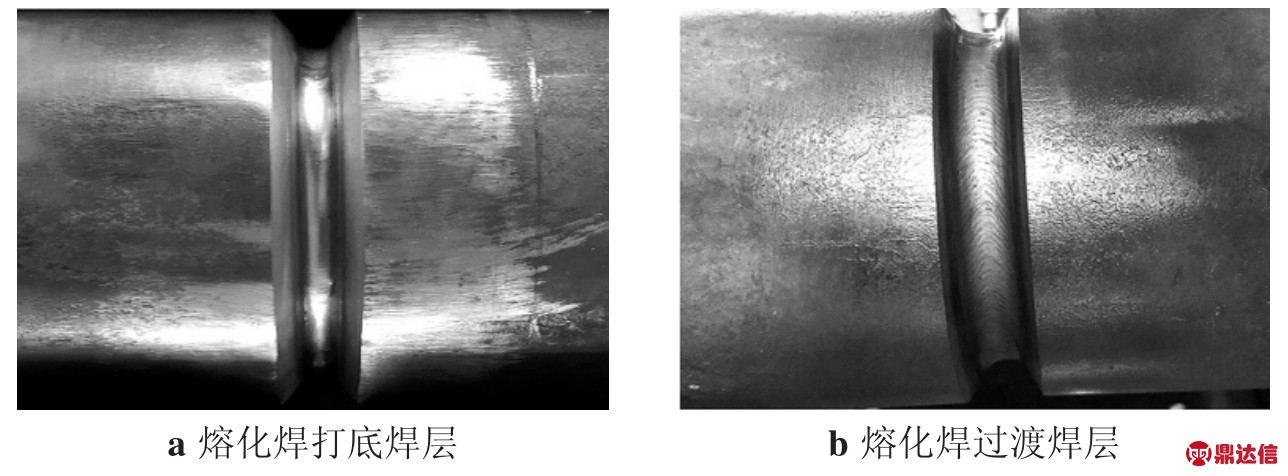
图17 无填充熔化焊打底、过渡焊层
Fig.17 Filling free fusion welding backing and transition welding layer
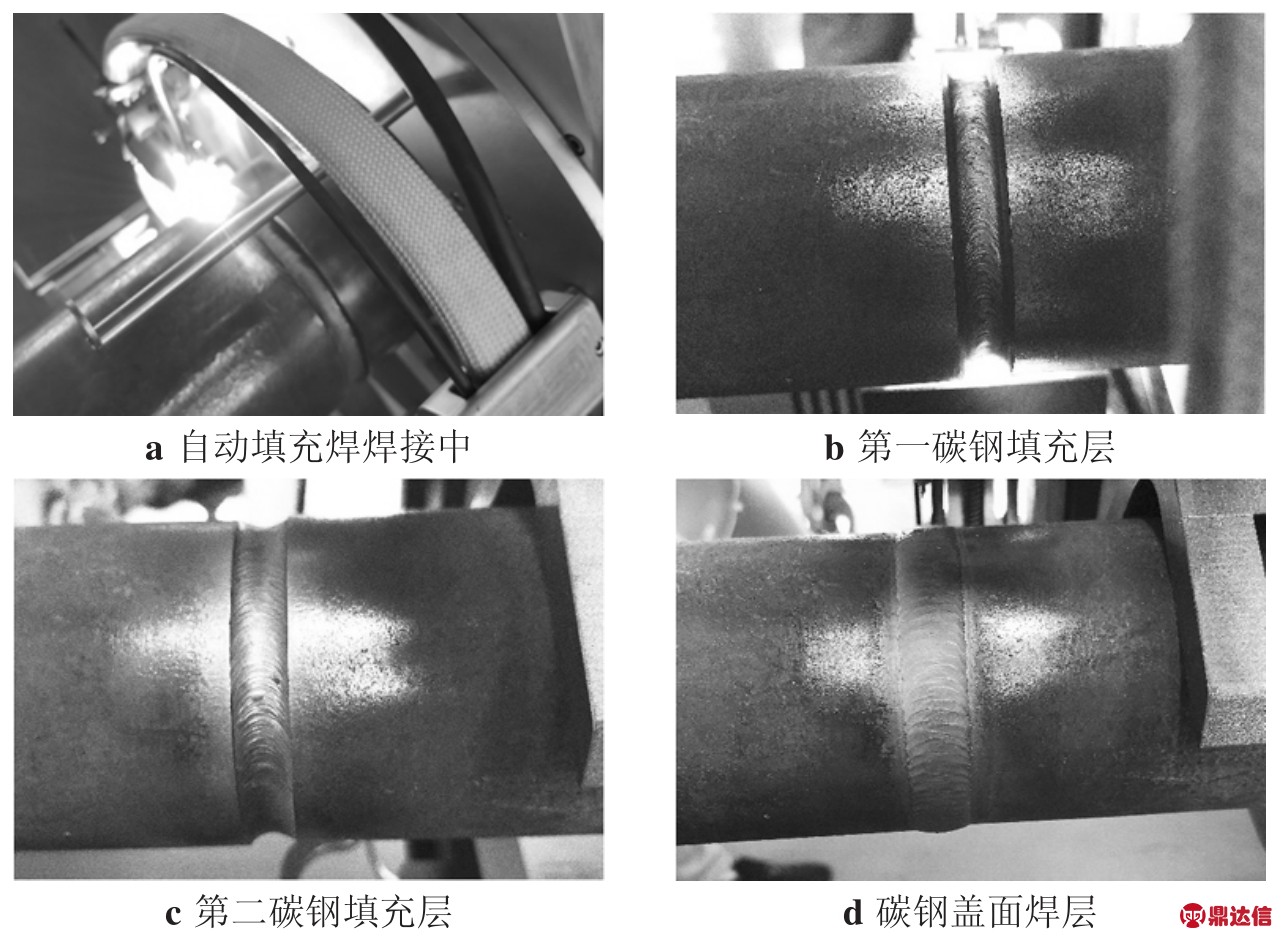
图18 自动焊碳钢填充、盖面焊层外观
Fig.18 Appearance of automatic welding carbon steel filling and cover welding layer
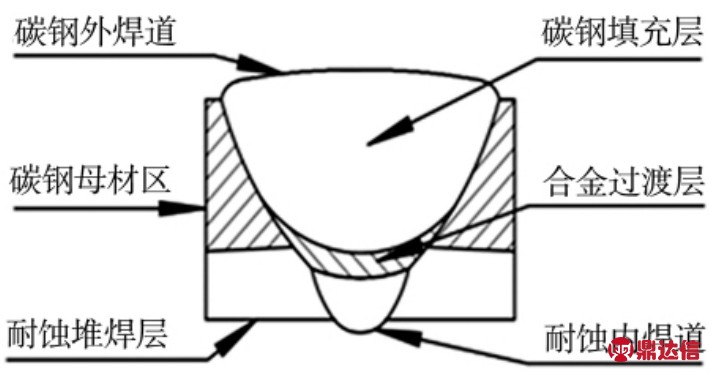
图19 试件分区
Fig.19 Specimen partition
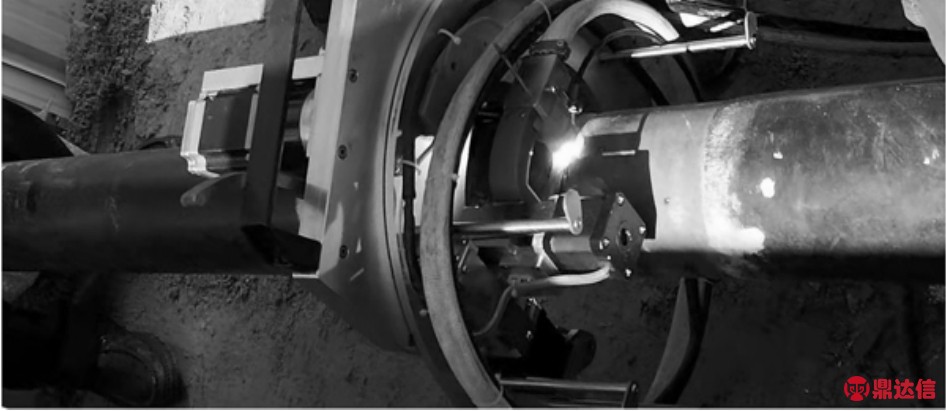
图20 熔焊打底焊层熔合区(200×)
Fig.20 Fusion zone of backing weld(200×)
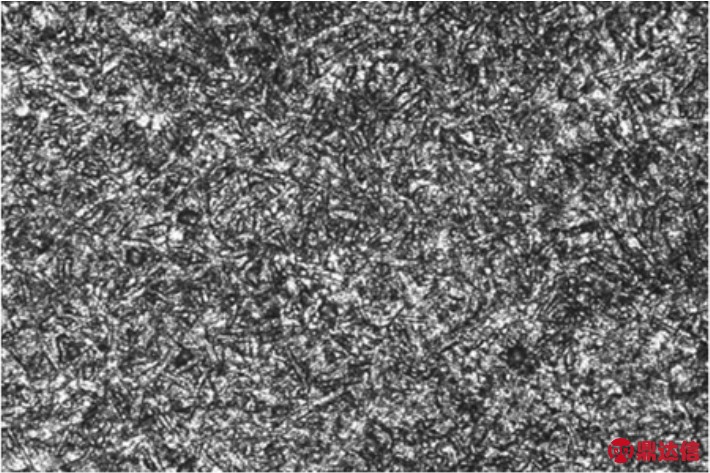
图21 双金属过渡区组织(200×)
Fig.21 Bimetal transition zone structure(200×)
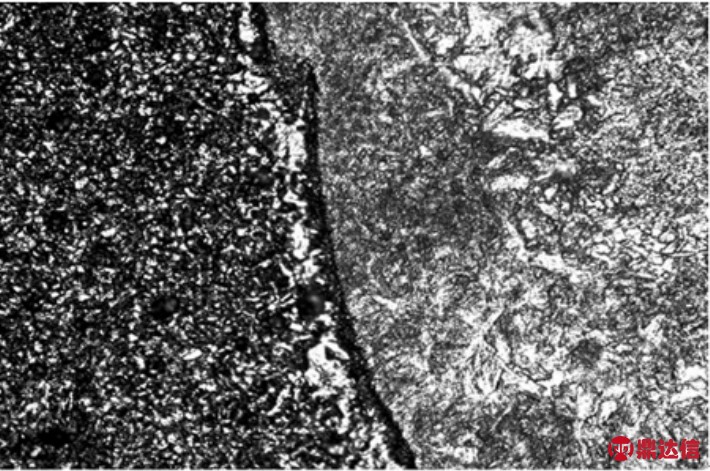
图22 碳钢焊层与坡口面熔合区(200×)
Fig.22 Fusion zone between carbon steel welding layer and groove surface(200×)
图20左侧为预制内补口堆焊区,右侧为熔化焊对接打底焊层。可以看出,焊缝组织由铁素体和奥氏体组织组成,与耐蚀堆焊金属组织相同。熔合线清晰无缺陷。
由图21可知,下部是与打底焊层的熔合区,主要由奥氏体、铁素体和少量珠光体构成,上部是与低碳钢填充焊层的熔合区,珠光体分量增多。各焊层之间熔合良好无缺陷。
图22左侧是低碳钢坡口面,右侧是低碳钢焊材填充金属。焊缝熔合良好,熔合线坡口面一侧有微弱碳增浓,符合焊缝微观组织的一般现象。
5.3 焊缝合金稀释分析
由图20可知,熔化焊打底焊层中均匀分布有少量珠光体组织,这是由于堆焊熔合区合金再次熔化形成的耐蚀合金稀释,其稀释率很小,对打底焊层的耐腐蚀性能影响不大。
5.4 焊缝力学性能和射线探伤
本焊件焊缝经射线检测和力学性能试验合格,其中射线影像共10件,检测比例100%,评定级别全部为Ⅰ级;其中根据SY/T0452-2012标准进行的拉力试验、弯曲试验、冲击试验和刻槽锤断试验结果100%合格,如图23所示。焊件的内焊缝和射线影像如图24所示。
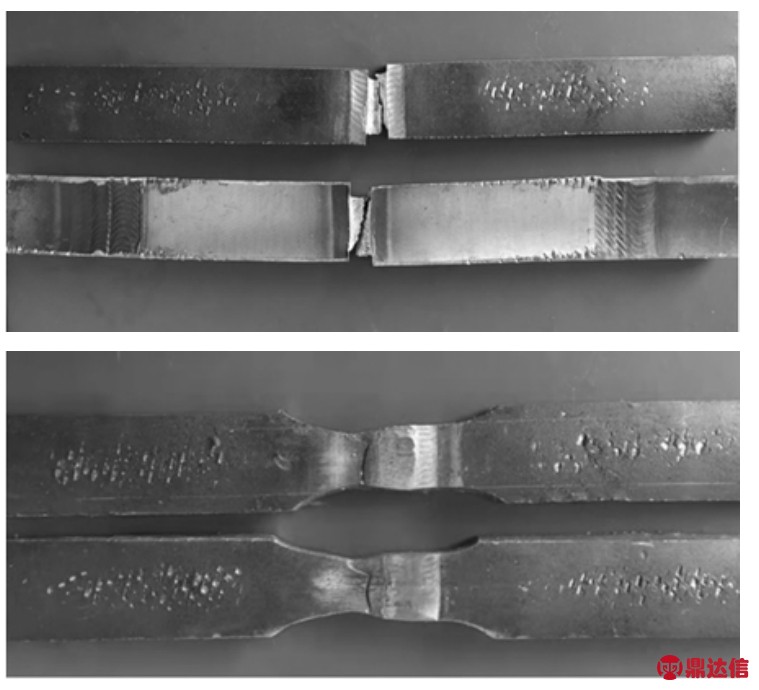
图23 焊件力学性能试件
Fig.23 Mechanical property test piece of weldment
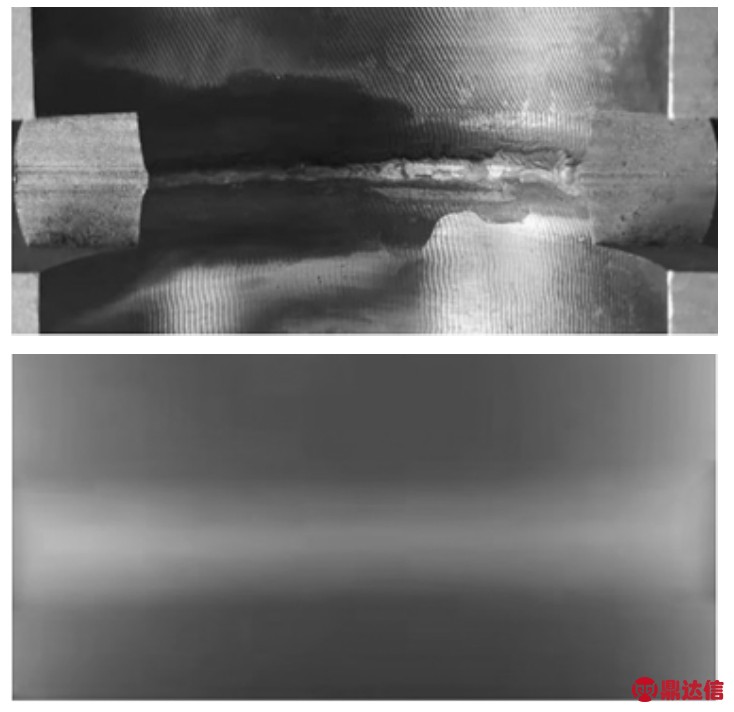
图24 焊件内焊缝和射线影像
Fig.24 Welds and radiographs in Weldments
6 结论
内衬不锈钢复合管道采用管端内封焊、背部焊剂保护、改进型坡口无间隙组对、无填充熔焊打底和无填充熔焊过渡方法,能够简化焊接工艺,降低焊接难度和施工成本,保证焊缝质量,是一种值得推广的不锈钢内衬复合管道或耐蚀合金预制内补口防腐管道的焊接工艺。该工艺已经成功应用于胜利油田埋地复合管道的现场施工中(见图25)。
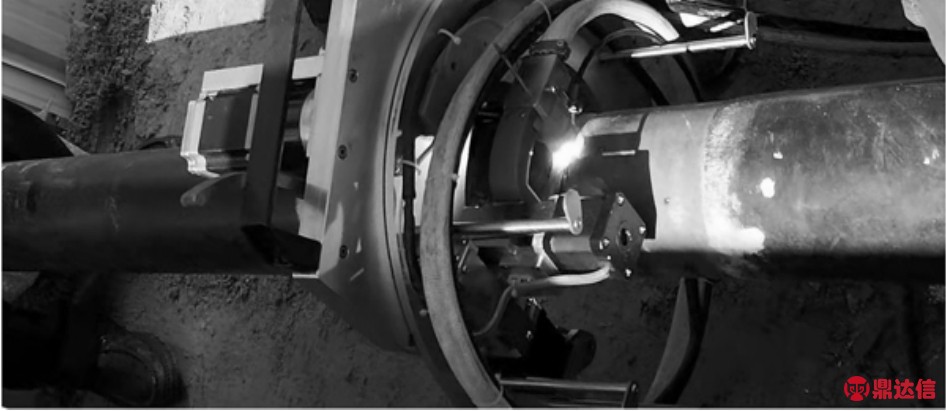
图25 复合管自动焊现场施工
Fig.25 On site construction of composite pipe automatic welding