摘 要:为研究双金属衬里复合管堆焊及对接焊焊接后焊接处应力变化,针对Φ89(8+2) mm尺寸衬里复合管,基于热-力耦合理论,建立瞬态热-固耦合管端堆焊与对接焊V型槽环焊缝轴对称力学模型。探讨衬里复合管堆焊及对接焊过程中整个焊肉及热影响区的应力变化并对应力区进行完整、详细分析。结果表明:衬里复合管焊接完成后焊区产生较高的残余应力,最高达463.47 MPa;热处理工艺消除了90%的残余应力,然而投入使用的复合管仍然存在3个高应力区:对接焊焊肉内、过渡区中靠近对接焊焊肉的基管上及2次堆焊起始点,其中应力最大的位置在2次堆焊的起始点,最高达46.63 MPa。建立的模型和计算结果可为实际工况下衬里复合管焊接部位的力学性质研究提供参考。
关键词:双金属衬里复合管;堆焊;对接焊;热处理;残余应力
0 引言
随着石油与天然气不断开采,高腐蚀性油气田相继出现,对管道抗腐蚀性能要求不断提高[1-4]。双金属衬里复合管由高强度的外层基管与高抗腐蚀性能的内层衬管组成,具有良好的抗腐蚀性与经济性,因此在石油与天然气集输行业得到广泛应用。然而由于基管与衬管之间材料力学性质具有较大的差异性,管端焊接过后,焊区往往产生残余应力,残余应力导致焊接接头出现裂纹或抗腐蚀性能下降,带来安全隐患,因此急需开展双金属衬里复合管焊接力学方面的研究。
对于管端焊接力学问题,国内外学者进行了相关研究。Karlsso等[5]利用有限元方法研究了管道对接焊开始与结束焊缝区残余应力的变化,但当时仿真过程无法控制冷却速度,导致仿真结果与实验结果相差40 MPa。Terasaki等[6]推导出管道堆焊焊缝中残余应力的计算公式。吕世雄等[7]对20 G内衬316 L复合管接头进行拉伸、弯曲、冲击、压力力学性能实验。Gou等[8]分析了X60输气管焊接区残余应力影响因素,研究发现挤压变形对管道残余应力影响最小。管松军等[9]利用超声波技术对N08825复合管焊接接头残余应力进行了调整,将平均环向拉应力由153.33 MPa调整为压应力,调整后值为293.75 MPa。税正伟等[10]对L245NCS/316L双金属复合管焊接接头进行力学性能实验,研究结果表明焊接接头屈服强度为372 MPa,抗拉强度为500 MPa,力学性能满足SY/T4103-2006标准要求。Fu等[11]对某气田复合管环焊缝失效原因进行了分析,研究发现外应力是导致环焊缝失效的主要原因。Obeid等[12-14]借助有限元软件研究不同钢材双金属复合管焊接应力场问题。Mou等[15]利用有限元的方法研究了残余应力对吸收塔焊接区强度的影响。Ruggieri等[16]研究了双金属复合管环焊缝抵抗断裂的力学性能。
目前针对管端焊接力学性能研究主要集中于研究管道焊接完成后接头失效原因及力学性能分析,并未对复合管管端焊接过程进行力学分析。本文在充分考虑衬管-基管材料热力学参数随温度变化而变化及焊接时热辐射与热交换对残余应力的影响前提下,借助有限元软件对双金属衬里复合管管端堆焊-对接焊-热处理整个工艺过程焊区及焊区附近残余应力的大小及分布进行仿真研究,为实际工况下复合管焊接部位的力学性质研究提供参考。
1 双金属衬里复合管管端焊接有限元力学理论
由于焊接过程为加热-冷却周期性循环过程,随着焊道的不断填充使得热源位置随之发生移动,因此焊件内应力应变场也随之发生改变。焊接过程中由于热源的不断移动及受冷却工艺的影响,材料会经过弹性及塑性变形过程。当材料为弹性变形时总应变增量主要由弹性应变增量及热应变增量组成,在某一应力状态下,考虑到弹性矩阵受温度的影响,弹性应变增量计算公式如式(1)所示:

(1)
式中:{dε}e为弹性应变增量;为弹性矩阵逆矩阵;{σ}为某一应力状态,MPa;{dσ}为应力增量,MPa;dT为温度增量,℃。
热应变增量计算公式如式(2)所示:

(2)
式中:{dε}T为热应变增量;T为温度,℃;α0为复合管初始热膨胀系数向量,1/℃;{α}为复合管温度变化后的热膨胀系数,1/℃。
弹性总应变增量计算公式如式(3)所示:
{dε}={dε}e+{dε}T
(3)
式中:{dε}为弹性总应变增量。
将式(1)~(2)带入式(3)整理得焊接过程弹性区应力增量计算公式如式(4)所示:

(4)
式中:[D]e为弹性区弹性矩阵。
当材料为塑性变形时,总应变由塑性应变增量,弹性应变增量及热应变增量组成,塑性应变增量计算公式如式(5)所示:
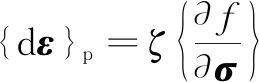
(5)
式中:{dε}p为塑性应变增量;ζ为卸载系数,无量纲,ζ>0为卸载过程;f为复合管屈服函数。
焊接过程塑性区应力增量计算公式如式(6)所示:
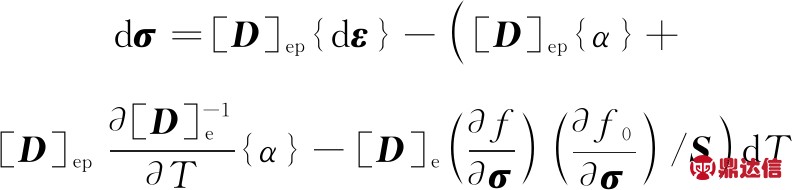
(6)
式中:dσ为塑性应力增量,MPa;[D]ep为弹塑性矩阵;f0为与温度和塑性应变有关的屈服应力函数;S为偏应力张量,MPa。
焊接完成后,平衡条件下焊区截面内的残余应力计算公式如式(7)所示[17]:

(7)
式中:σxx,σyy和σzz分别为X,Y,Z平面的应力分量,MPa;τzy,τyz和τxz分别为切应力分量,MPa;A为焊区横截面积,mm2。
弹性与塑性阶段应力求解过程[18]:弹性阶段,将焊接过程中各节点力学参数代入式(1)~(2)分别求得弹性应变增量{dε}e及热应变增量{dε}T,然后代入式(4)求得各单元的弹性应力增量{dσ};塑性阶段,利用各节点力学参数分别求得塑性应变增量{dε}p,弹性应变增量{dε}e及热应变增量{dε}T,然后代入式(6)求得各单元塑性应力增量dσ。
2 双金属衬里复合管有限元模型建立
针对规格Φ89(8+2) mm尺寸双金属衬里复合管(基管为X52钢材,衬管为8225钢材)管端焊接应力问题,根据现场的管径尺寸,考虑双金属复合管在焊接过程中的几何尺寸、边界条件及载荷都是关于中心线对称,建立瞬态传热-固体力学耦合管端堆焊与对接焊V型槽环焊缝轴对称力学模型,如图1所示。由于在焊接过程中温度的传递不会辐射到整根管材,因此在模型中基管和衬管的总长定义2 m,即一半管长为1 m,其中双金属复合管外半径定义为R,内半径定义为r。同时,为了还原现场连接管端的作业流程,将一端的轴向(即X方向)约束,另一端自由。
在建模过程中将衬管与基管视为弹塑性变形体,其材料热力学参数见表1。由表1可知,衬管和基管的弹性模量、屈服强度及热导率均随着温度增加而降低;而泊松比、热膨胀系数、比热容均随温度增加而增加,这表明在高温条件下的钢材变形机制增多,易发生塑性变形,且形变强化现象减弱,这些因素都会直接影响每道焊道造成的应力场分布。
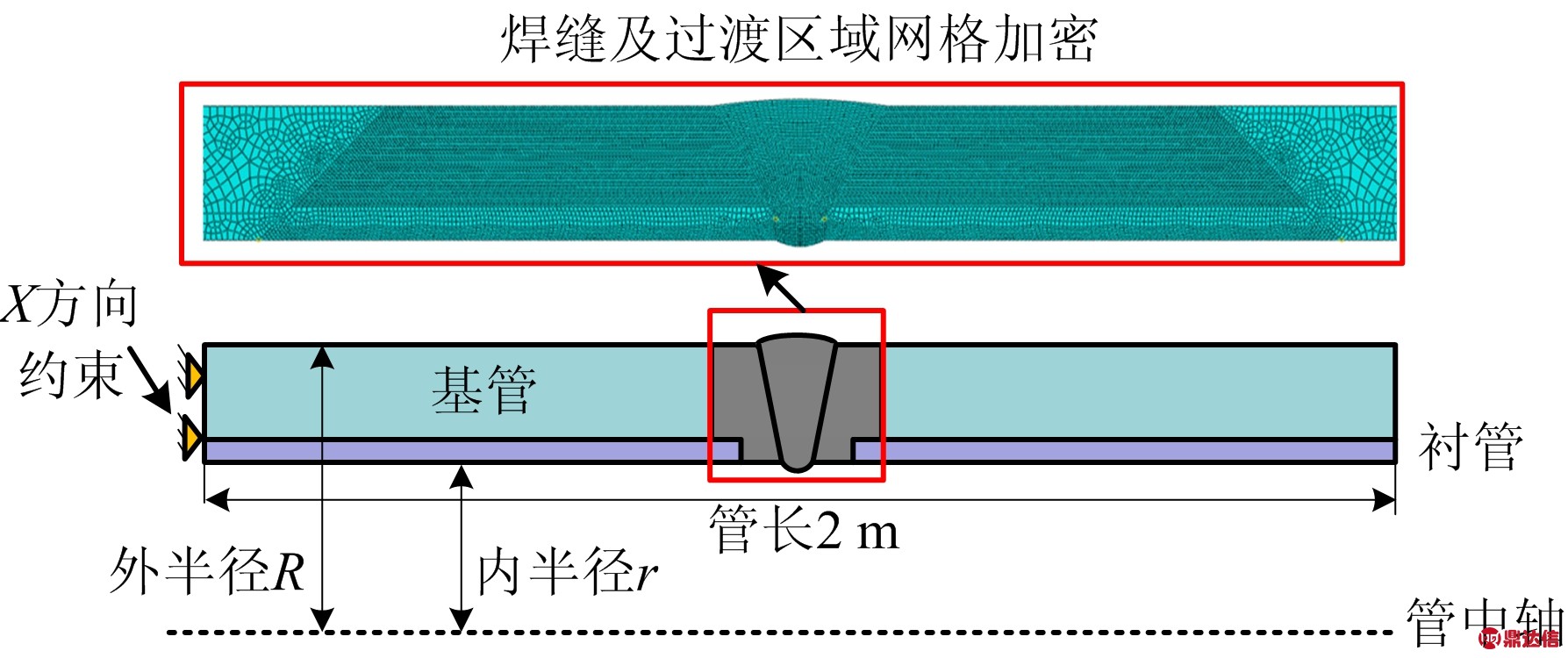
图1 瞬态传热-固体耦合管端堆焊的V型槽环焊缝轴对称力学模型
Fig.1 Axisymmetric mechanical model of V-type groove girth weld in transient thermal-solid coupling pipe end surfacing
表1 X52基管-8225内衬管材料热力学参数
Table 1 Thermodynamic parameters of materials in X52 base pipe and 8225 lined pipe
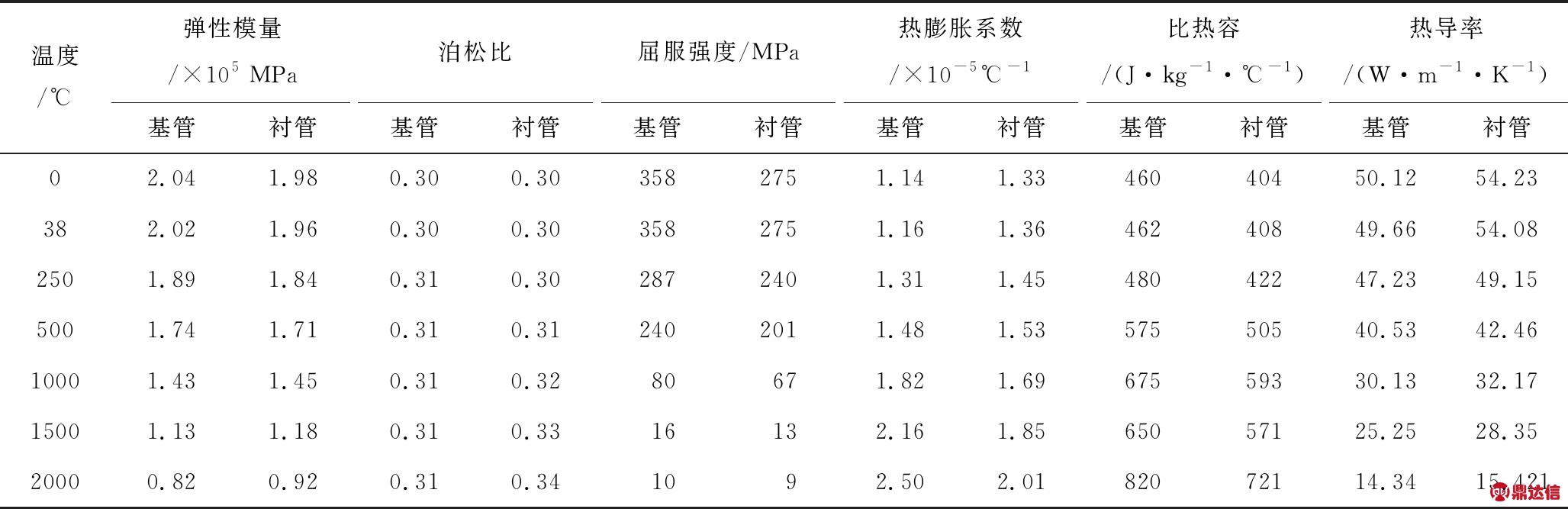
焊接工艺中每道焊道都会在管端区域造成高热应力,这种热应力随每道焊缝的进行呈现周期性循环特征,即在每道焊缝焊接与冷却后都会使得热应力影响区的应力场进行重新分布,因此为了还原这种周期性应力场重分布情况,在有限元模拟中将焊接区域划分为多个焊道,模拟每道焊道焊接与冷却后焊道及焊道周围应力变化情况。模型中堆焊区域与对接焊区域每道焊道的焊接顺序如图2所示。由图2可知,第A~K道焊缝为第1层堆焊顺序,焊接时控制170 A电流,第L~W道焊缝为第2层堆焊顺序,电流180~190 A,此时一端的复合管堆焊工艺完成,另一端如法炮制。图2中数字为对接焊区域的焊接顺序,第1道焊缝为根焊,2~3道焊道为过渡焊,其厚度略小于后续焊道,4~12道焊道为覆盖焊,电流均为180~190 A。
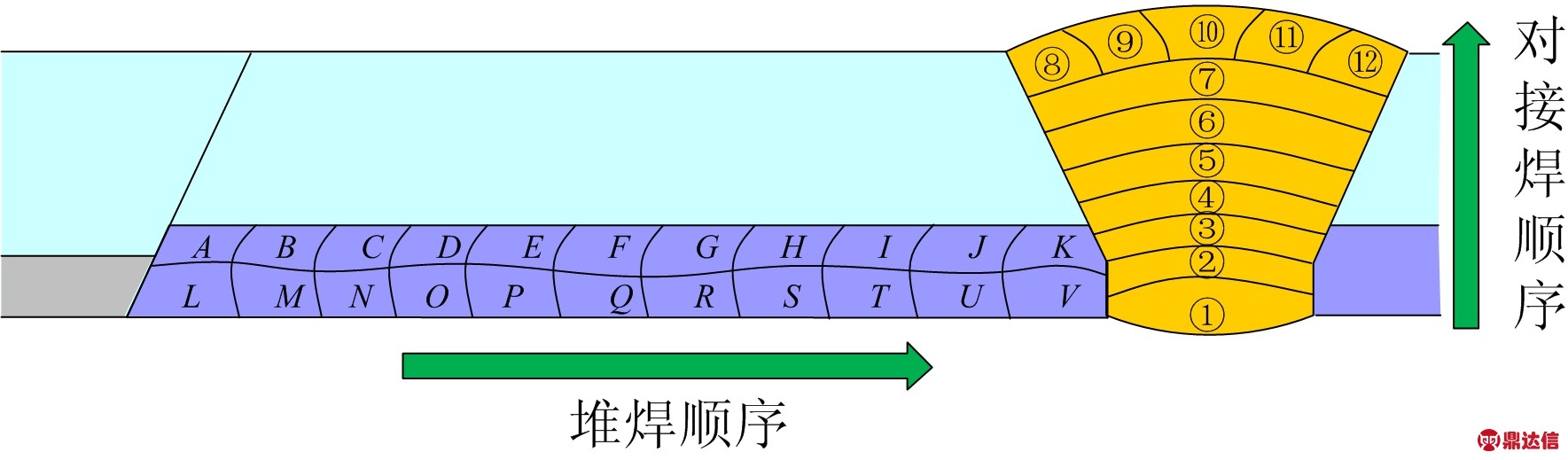
图2 堆焊与对接焊焊道焊接顺序
Fig.2 Welding sequence of surfacing and butt welding bead
3 双金属衬里复合管管端焊接有限元力学分析
3.1 管端堆焊与对接焊工艺管端应力分析
通过对双金属衬里复合管管端堆焊进行有限元分析,得到第K道焊道焊接与冷却过程中应力场分布云图如图3所示,由图3(a)可知,在焊接时,第K道焊区应力较低,应力水平仅为36~73 MPa,这是因为在焊接时第K道焊道焊肉温度已经达到1 430 ℃,由表1材料的热力学参数可知,此时第K道焊道焊肉区域已经近乎熔融状态,因此应力水平较低,而在已经完成焊接的焊肉区域应力较高,临近焊道焊肉区域应力达到最大值,最高达438 MPa左右。由图3(b)可知,在第K道焊道完成焊接并冷却后,整个管材的最高应力回到第K道焊道,最高达到443.41 MPa。这是因为高温急剧下降导致焊肉区域收缩,再加上基管与衬管的热力学参数随温度变化的特性,导致冷却后应力增大。第W道焊道焊接与冷却过程中应力场分布如图4所示,由图4可知第W道焊道焊接与冷却后相对于第K道焊应力均有所增加,分别增加了10.11 MPa,5.53 MPa,堆焊焊接完成并冷却后,堆焊焊肉区域及管端均存在较高的应力,最高达448.94 MPa。
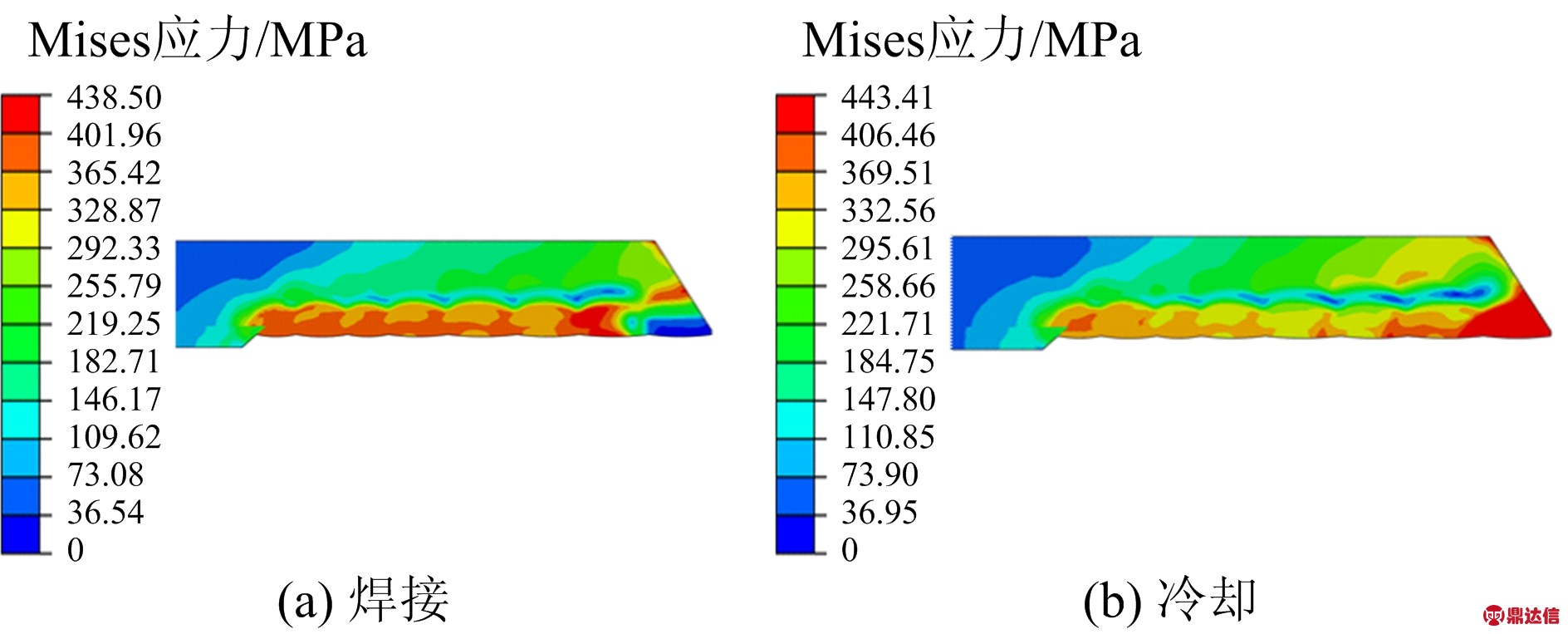
图3 堆焊第K道焊道焊接与冷却
Fig.3 Welding and cooling of Kth welding bead in surfacing
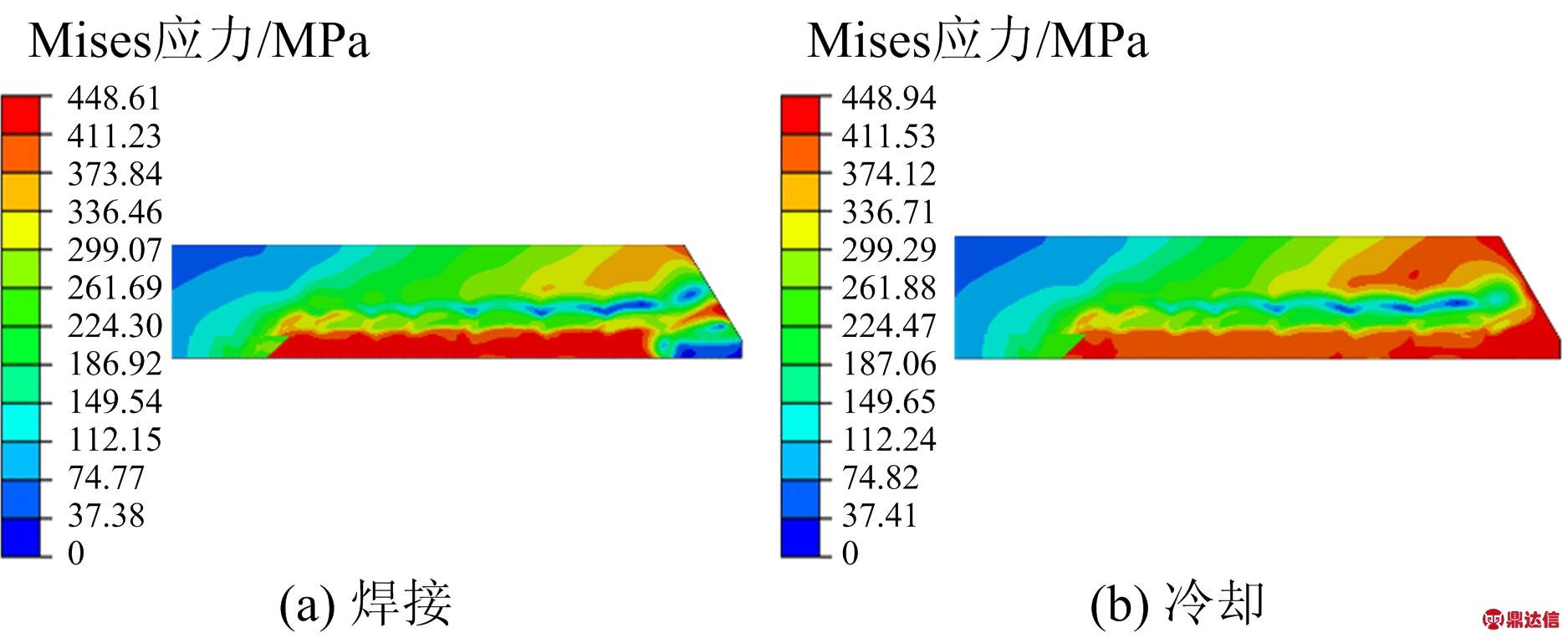
图4 堆焊第W道焊道焊接与冷却
Fig.4 Welding and cooling of Wth welding bead in surfacing
对接焊的第1道焊道(即根焊)的焊接与冷却过程中应力场的分布如图5所示。由图5(a)可知,在焊接的过程中,根焊的应力水平较低,而高温影响了靠近根焊焊接位置的区域,导致靠近根焊的堆焊区域上发生应力集中,最高应力达到448.88 MPa,这主要是高温导致焊道区域附近产生热应力,导致应力升高。由图5(b)可知,冷却后焊肉区域的收缩导致最高应力回到对接焊第1道焊肉区域,最高达到452.62 MPa。对接焊第12道焊道过渡焊与冷却过程中应力场的分布云图如图6所示。由图6(a)可知,焊接完成及冷却后,整个管端应力水平高于堆焊焊道完成冷却时的应力15 MPa左右,这是由于焊道的增加使得焊接区域内的应力变化更加复杂,应力更为集中。
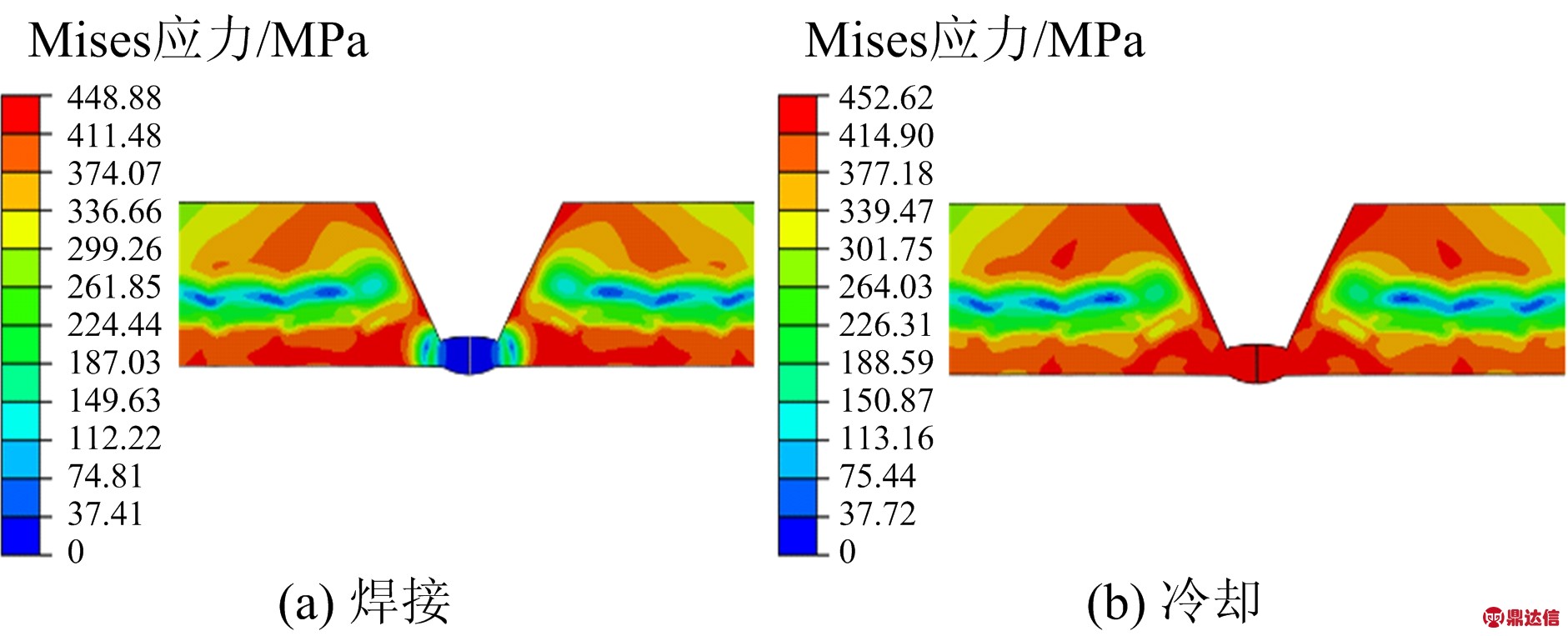
图5 对接焊第1道焊道根焊与冷却
Fig.5 Root welding and cooling of 1st welding bead in butt welding
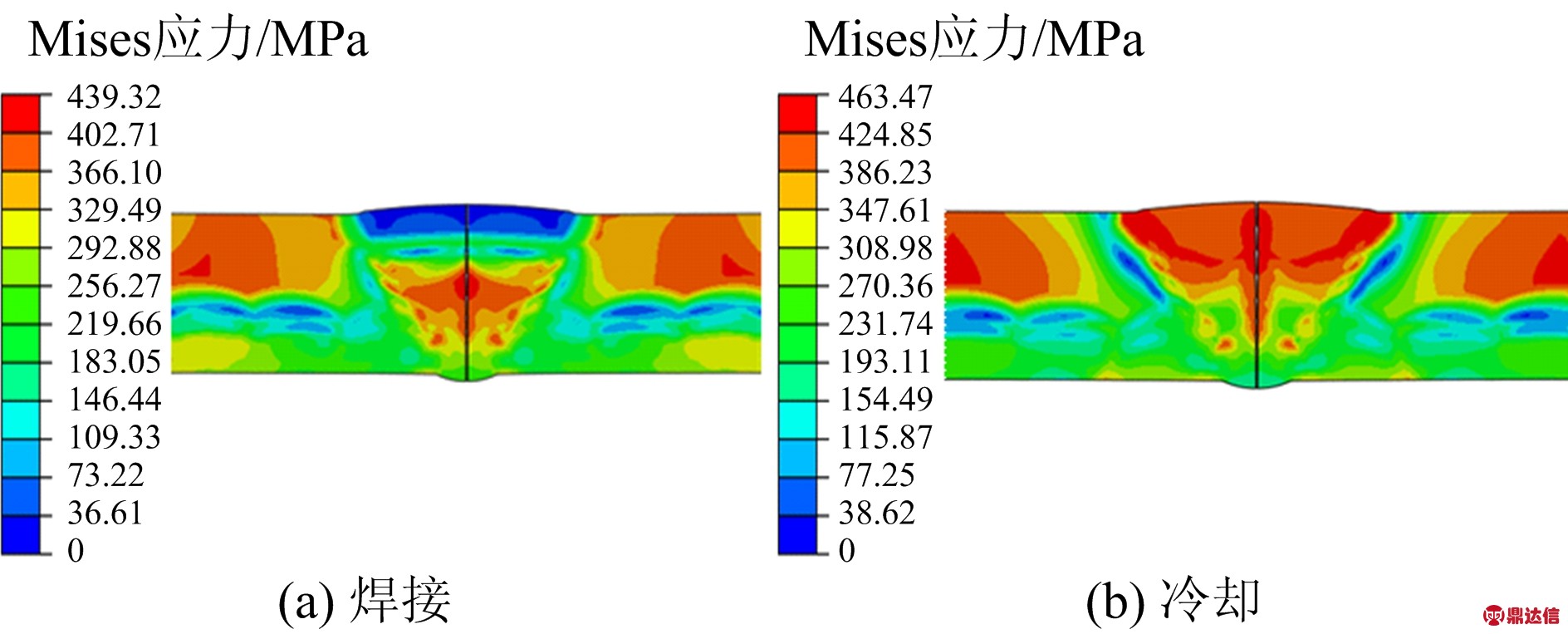
图6 对接焊第12道焊道过渡焊与冷却
Fig.6 Transition welding and cooling of 12th welding bead in butt welding
通过堆焊和对接焊有限元模拟可以发现,堆焊与对接焊完成后,管端一定区域内均存在一定的残余应力,在焊接进行时,由于高温(超过1 000 ℃)以及管材随温度变化的热力学性能使得当前焊接的焊道呈现接近熔融的状态,因此应力较低,最高应力不超过80 MPa;而当焊接完全冷却时,高温的急剧下降导致焊肉区域的收缩,再加上基管与衬管的热力学参数随温度变化的特性,会让焊道在冷却时内部的残余应力上升。
3.2 管端热处理工艺管端应力分析
在实际工况中,堆焊与对接焊完成后带有残余应力的复合管并不是最终投入生产的管材,当焊接完成后会在焊接区域以及靠近焊接的区域进行高温热处理,旨在降低焊接造成的残余应力水平。现场热处理的方法是将带有残余应力的复合管在210~230 ℃的环境中持续一定时间,然后冷却至常温。为还原此步工艺,在有限元软件中将图7(a)中带有残余应力的复合管进行600 ℃的热处理2 000 s,然后再冷却3 000 s至常温(即20 ℃)。
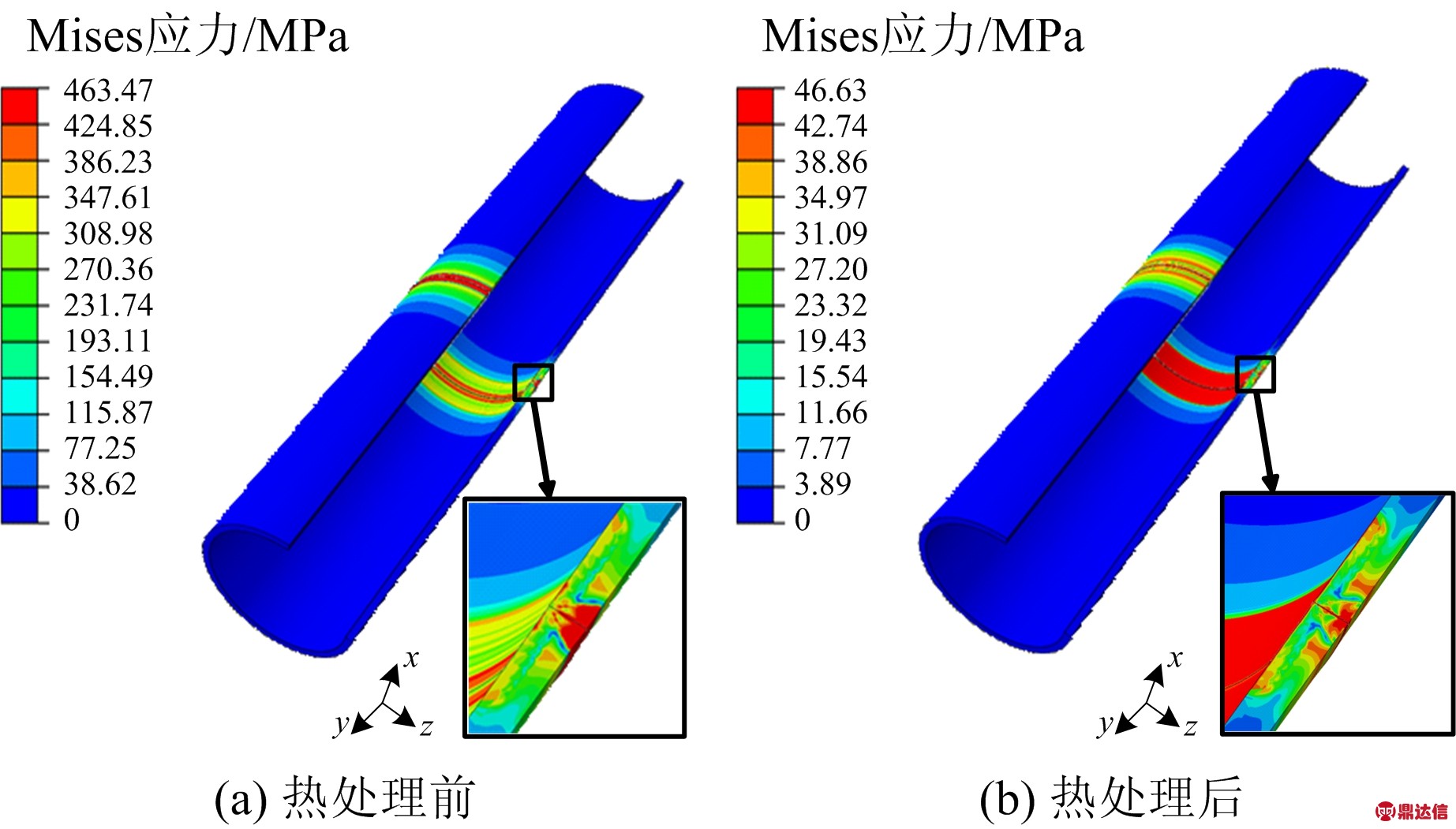
图7 衬里复合管堆焊及过渡带不同阶段应力变化情况
Fig.7 Stress change in different stages of surfacing and transition zone of lined composite pipe
衬里复合管堆焊及过渡带不同阶段应力变化云图如图7所示,当最后一道对接焊焊肉完成冷却后,其应力状态如图7(a)所示,此时由于多次的焊接高温-冷却循环,最大应力达到463.47 MPa;热处理完成后由于温度回降至室温,管材高应力区应力有一定程度的回升,热处理后的管材应力状态如图7(b)所示,焊缝与过渡段的高应力区应力范围降低至19.43~46.63 MPa,最大残余应力减小了90%。由此可见,热处理过程极大程度地消除了焊接工艺造成的残余应力。
3.3 焊缝区域与过渡区应力变化分析
热处理后复合管管端Mises应力分布云图如图8所示。由图8可知,热处理后的复合管存在3个高应力区,包括有对接焊焊肉内、靠近对接焊焊肉的基管上以及2次堆焊的焊接起始点。
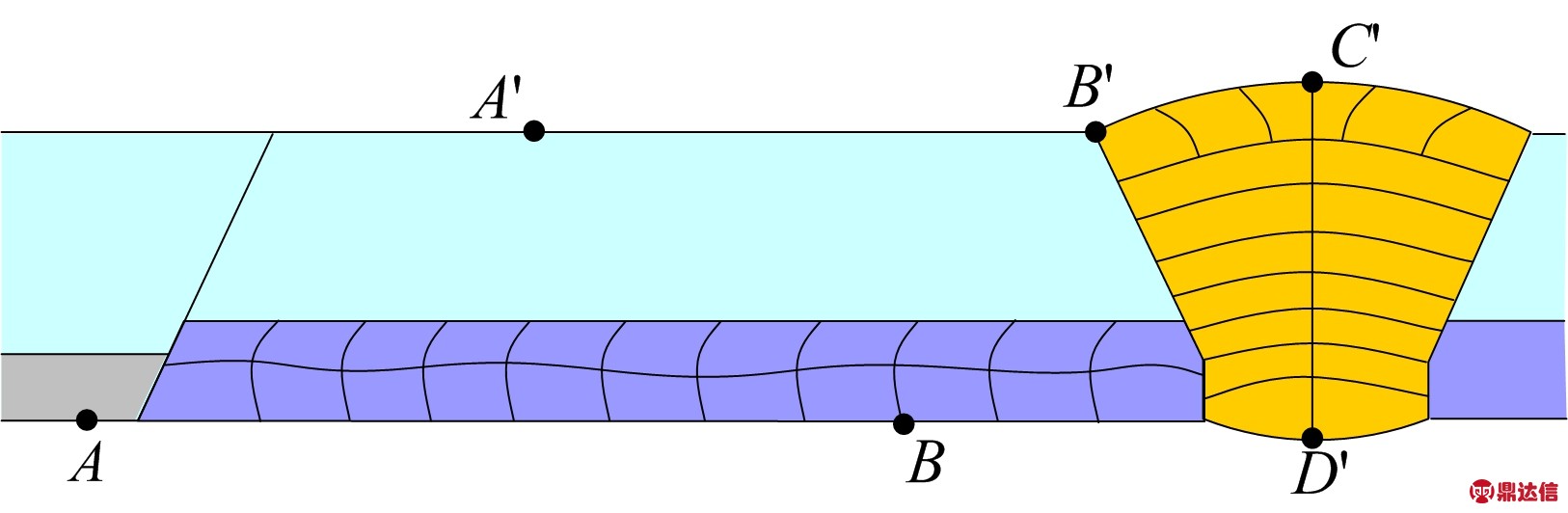
图8 热处理后复合管管端Mises应力分布情况
Fig.8 Distribution of Mises stress at end of composite pipe after heat treatment
为进一步研究热处理后双金属衬里复合管管端应力大小及分布情况,分别沿路径AB,A′B′C′D′提取双金属衬里复合管热处理后的Mises应力,路径示意图如图9所示。衬里复合管热处理后路径AB-Mises应力变化关系曲线如图10所示。由图10可知,沿路径AB堆焊区及堆焊起始点附近均存在残余应力,总体残余应力呈先增大后减小趋势,这是因为堆焊过程中,已堆焊完成的区域受加热冷却循环工艺的影响,残余应力不断累加所致。其中最大残余应力为46.63 MPa,发生在堆焊焊接起始点位置,沿路径AB在距离堆焊起始点10 mm范围内,堆焊区Mises应力高达34.97~46.63 MPa。
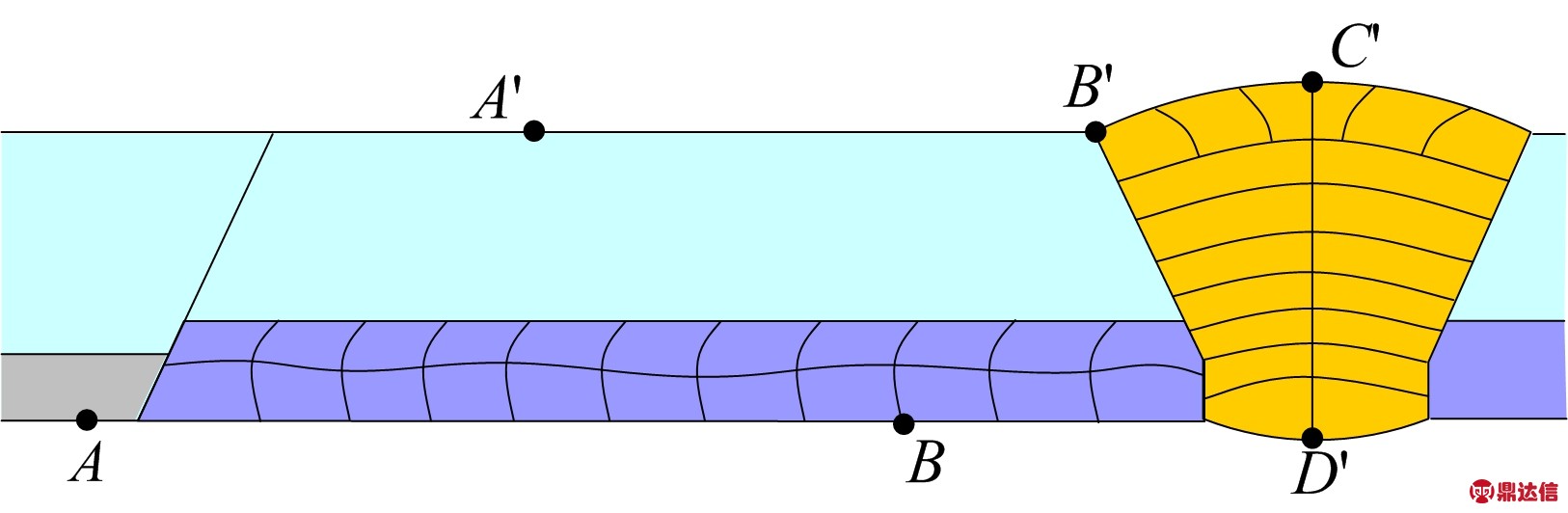
图9 路径示意
Fig.9 Schematic diagram of route
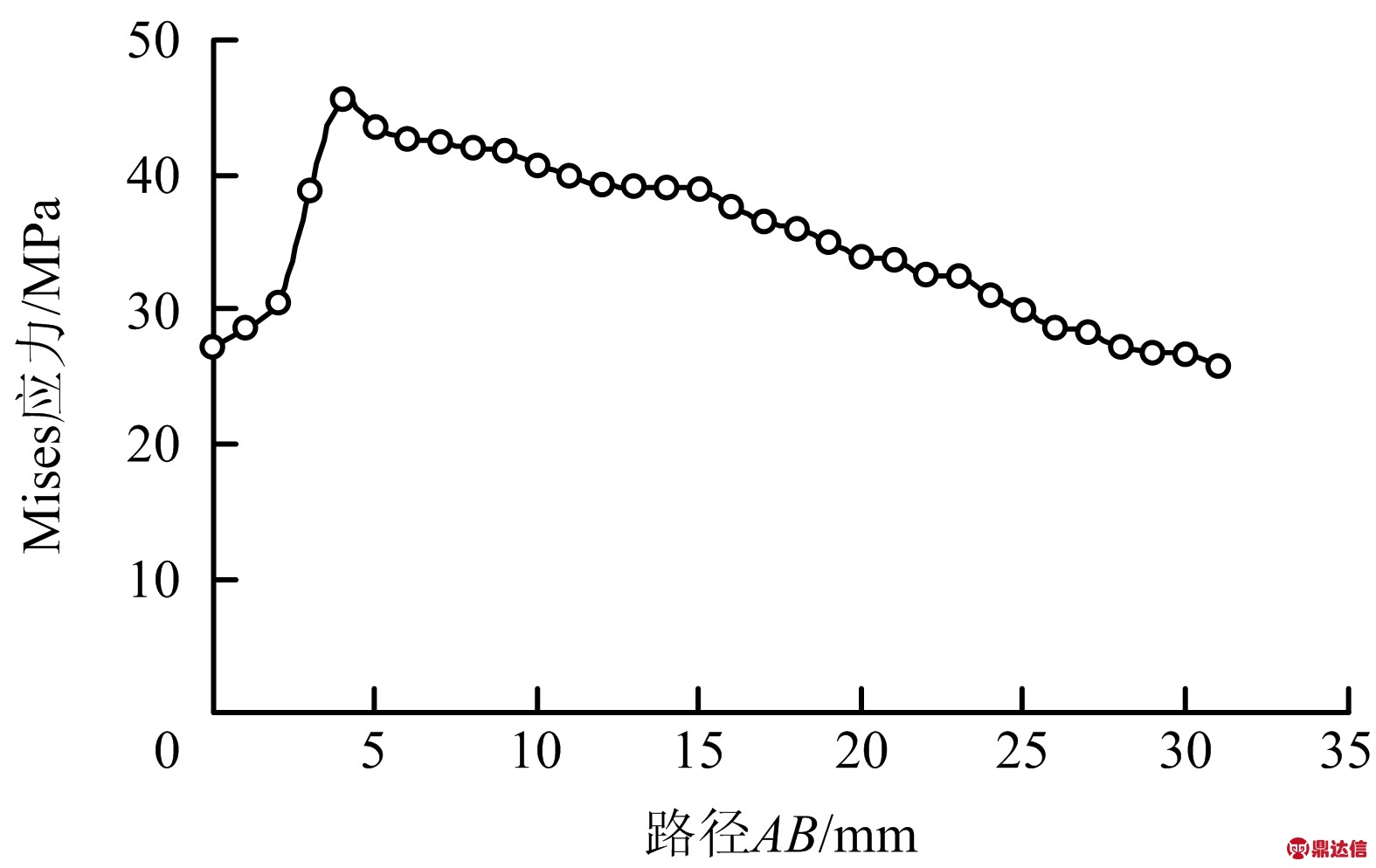
图10 衬里复合管热处理后路径AB-Mises应力变化关系曲线
Fig.10 Change relationship between route AB and Mises stress of lined composite pipe after heat treatment
衬里复合管热处理后路径A′B′C′D′-Mises应力变化关系曲线如图11所示,由图11可以看出,沿路径A′B′C′D′衬里复合管基管外壁及对焊区均存在残余应力,总体Mises应力呈增大-减小-增大-减小趋势。沿路径A′B′最大Mises应力发生在距离对接焊11 mm左右,高达41.58 MPa,沿路径A′B′在8~17 mm范围内衬里复合管外壁残余应力高达34.97~42.74 MPa,这是因为经过堆焊及对接焊多次加热冷却后,在距离堆焊及对接焊较近的区域,残余应力不断累加,进而形成局部高应力区;沿路径B′C′D′可以看出,大部分对接焊区域残余应力均很高,高达38.86~45.52 MPa,这是因为受快速冷却工艺的影响,导致对接焊区焊肉结晶状态不均匀,进而产生局部高应力区。由此可知投入使用的双金属衬里复合管存在3个高应力区,分别为对接焊焊肉内、靠近对接焊焊肉的基管上以及2次堆焊的焊接起始点,其中应力最大的位置在2次堆焊的焊接起始点,最高达到46.63 MPa。
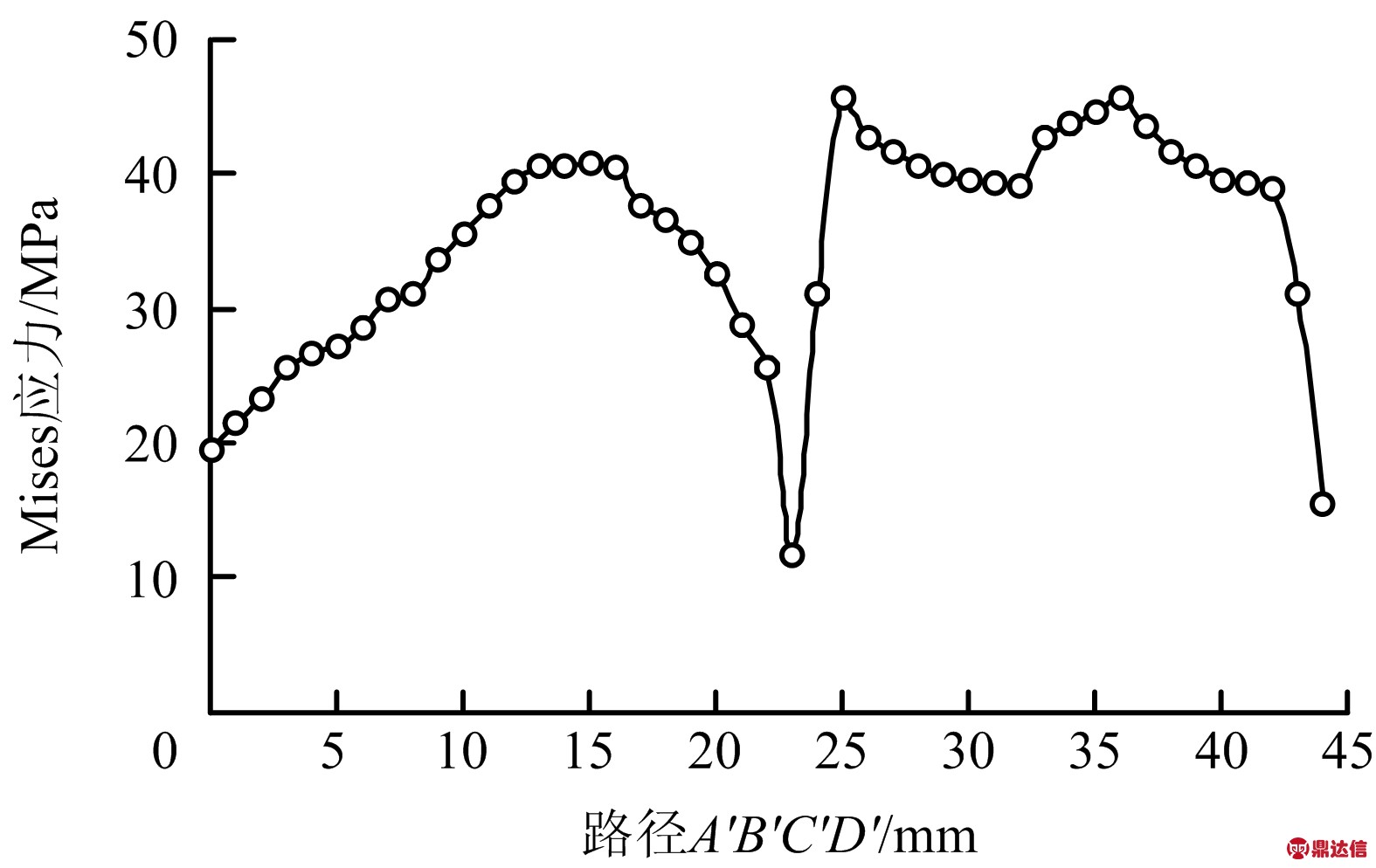
图11 衬里复合管热处理后路径A′B′C′D′-Mises应力变化关系曲线
Fig.11 Change relationship between route A′B′C′D′ and Mises stress of lined composite pipe after heat treatment
4 结论
1)利用有限元软件建立瞬态热-固耦合管端堆焊与对接焊V型槽环焊缝轴对称力学模型,模型充分考虑了焊缝工艺中每道焊道焊接时管材热力学性能、热辐射及热交换对残余应力的影响,同时考虑了焊接过程中由于热源移动造成的循环高热应力以及每道焊缝焊接与冷却后应力场重新分布情况。
2)在焊接进行时,由于高温(超过1 000 ℃)以及管材随温度变化的热力学性能使得当前焊接的焊道呈现接近熔融的状态,因此应力较低,不超过80 MPa;而当焊接完毕冷却时,高温的急剧下降导致了焊肉区域的收缩,再加上基管与衬管的热力学参数随温度变化的特性,会让焊道在冷却时内部的残余应力上升。
3)双金属衬里复合管热处理过程消除了90%的残余应力。然而投入使用的复合管仍然存在3个高应力区,包括对接焊焊肉内、过渡区中靠近对接焊焊肉的基管上和2次堆焊的焊接起始点,其中应力最大位置在2次堆焊的焊接起始点,最高达到46.63 MPa。