摘要:采用NiTi合金材料设计一种用于压缩扩张式的封隔器的新型金属密封元件,建立密封元件及其组件的数值模型;提出采用最大应力、坐封力和接触应力对密封元件密封性能进行评价,并分析结构参数变化对其密封性能的影响规律。结果表明:最大应力随膨胀环半径和拱形半径单调增加,随承压环宽度、拱形厚度和卸载槽半径先减小再增大;坐封力随承压环宽度、膨胀环半径、拱形半径和拱形厚度单调增加,随卸载槽半径单调减小;接触应力随承压环宽度、膨胀环半径和拱形厚度非线性增大,随拱形半径和卸载槽半径非线性减小。拱形半径和拱形厚度对密封元件密封性能影响较为显著,且适当减小拱形半径或增大拱形厚度可提高其密封性能。
关键词:金属密封;密封元件;密封性能;封隔器
随着石油勘探和油田开采产业的持续发展,油田的开采对象逐渐转向高温高压并伴有腐蚀的深井,在这种工况下,传统封隔器的密封胶筒易受到破坏,导致密封失效,十分影响油田的生产效益[1]。21世纪初,金属密封技术被首次应用于井下管柱环空密封,后续国内外学者都进行了相关的研究。在国外,Baker Hughes、Caledyne和Owen等公司对井下金属密封技术的研究起步较早,且研究较为深入,但对于密封元件结构的描述不甚清楚。相比于国外,国内在这方面的研究较少,且不够深入。刘合、胡玉志、安少云等[2-4]研制了楔形扩张式的金属密封元件,并进行了测试试验,验证了封隔器金属密封的可行性。崔晓杰、尚晓峰等[5-6]针对井下工况设计了压缩扩张式的金属密封元件,并进行了密封承压性能测试试验,验证密封元件满足使用要求。
上述研究虽然都设计了相应的金属密封元件并进行了相关验证,但并未对影响密封元件性能的相关因素进行深入研究,尤其是密封元件的结构参数。而密封元件的密封性能主要通过密封承压能力来评价,其密封承压能力直接与密封面的接触应力相关,接触应力越大,密封面的变形越大,泄漏通道越小,开启泄漏通道的介质压力越大,密封承压能力越好[7-8]。本文作者设计了一种用于封隔器的新型金属密封元件,建立了密封元件的数值模型,并分析金属密封元件的结构参数对其密封性能的影响,对封隔器金属密封元件的设计有一定的指导意义。
1 金属密封元件的设计与密封原理
1.1 金属密封元件的设计
目前的封隔器金属密封元件主要分为楔形扩张式和压缩扩张式2种类型。文中设计了一种压缩扩张式的封隔器金属密封元件,密封元件主要包括轴向承压环和径向膨胀环两部分,并在二者之间设置卸载槽。密封元件的承压环用来承受轴向推力,并保护密封元件的径向膨胀环不受轴向力破坏,在轴向推力的作用下,径向碰撞环会沿径向扩张,与套管接触进而实现密封。
压缩式封隔器可以为其中的密封机构提供轴向推力,密封机构必须在轴向推力的作用下进行径向扩张并实现封隔环空。根据这一使用特点并结合深井下高温高压(120 ℃,50 MPa)工况,文中采用NiTi合金材料设计了一种金属密封元件,其结构剖面如图1所示。

图1 密封元件结构剖面
Fig 1 Sectional view of the sealing element
该密封元件主要包括2个部分:轴向承压环和径向膨胀环,二者之间设有卸载槽。图1中b为轴向承压环的截面宽度(文中简称承压环宽度),h为轴向承压环截面高度(文中简称承压环高度),R1为径向膨胀环半径(文中简称膨胀环半径),R2为径向膨胀环截面拱形半径(文中简称拱形半径),t为径向膨胀环截面拱形厚度(文中简称拱形厚度),r为卸载槽半径。图2所示是密封组件剖视图,当密封元件受到密封组件中的上、下压环挤压后,径向膨胀环会沿径向进行膨胀扩张,实现封隔环空。
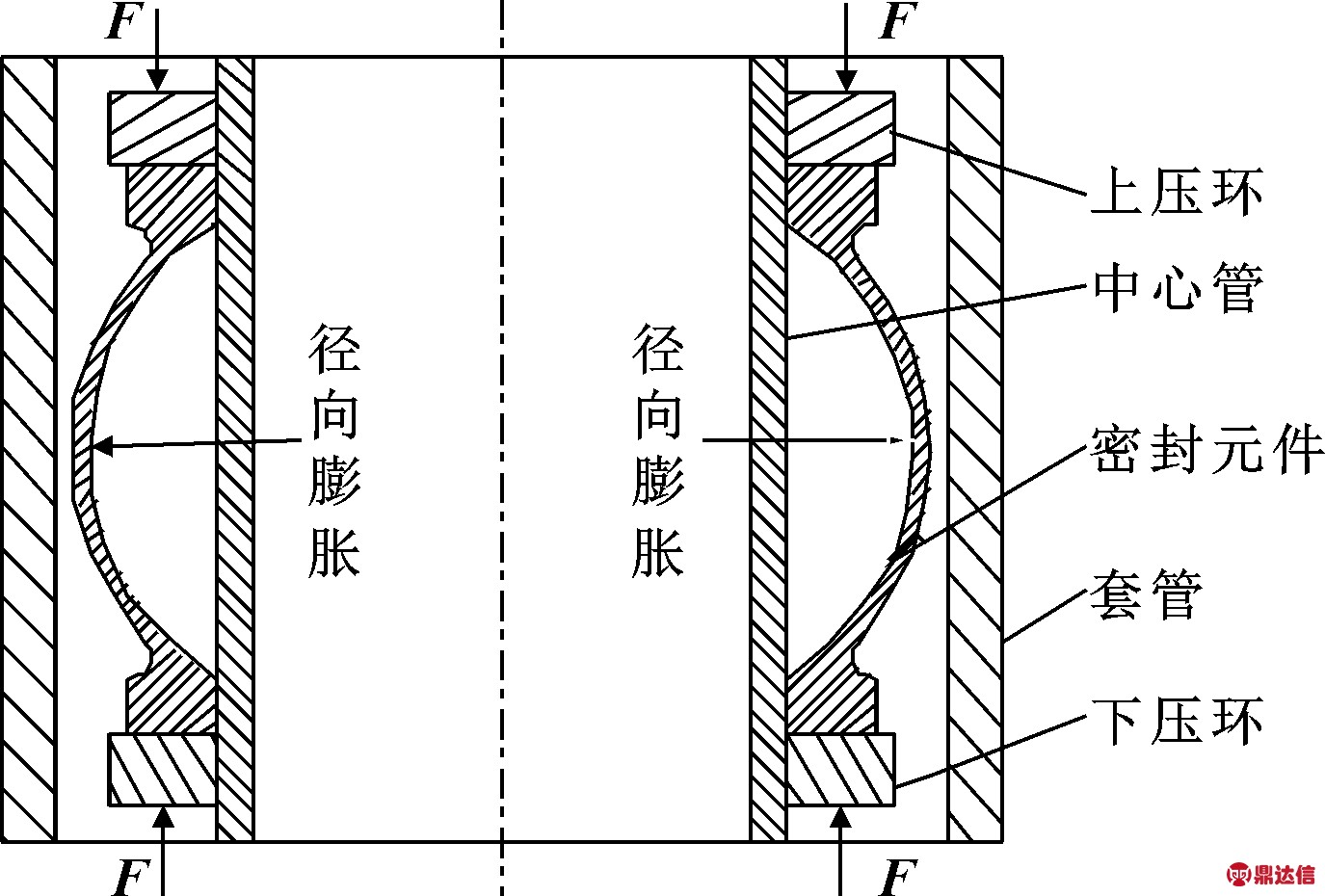
图2 密封组件
Fig 2 The sealing assembly
1.2 金属密封元件的密封原理
金属对金属的密封过程在宏观上表现为密封金属面之间的接触和挤压;从微观上来讲,是金属密封面之间微小间隙的填补过程。金属密封的泄漏方式主要是流体的穿漏,要想实现无泄漏密封,需要密封面形成微观上连续接触的密封环,而且密封环的接触应力要大于或等于管柱内的流体压力。由于金属密封面是粗糙的表面,故其表面有许多波峰和波谷,在密封面刚接触时,只有少量的波峰相互接触,若要实现密封,需要让密封面的接触应力至少达到密封材料屈服极限的2~3倍,只有当密封材料表面发生塑性流动并填补密封面之间的微小间隙,才能实现密封[8-9]。由于文中使用的密封元件材料为NiTi合金,屈服极限较大,为了实现更好的密封效果,在密封元件的有效密封区域镀了一层软金属银[10](银的屈服极限为30 MPa[11]),镀层厚度为0.05 mm。
2 数值模型的建立
2.1 几何模型简化
采用Inventor建立密封组件的几何模型,其结构如图2所示。为了节省计算机资源,提高计算速度,将图2中的结构进行合理地简化:由于几何模型是同轴的,故取模型的1/20进行分析计算;因镀层对结构无影响[12],故简化掉镀层金属。
2.2 材料属性
文中选用的密封元件的材料为具有超弹性的NiTi合金,在Ansys workbench中选用Auricchio[13-14]的材料本构模型进行模拟,本构模型中的各参数值取自120 ℃下的NiTi合金材料拉伸试验的结果[15],并假设该材料具各向同性和拉压对称性。各参数值如表1所示。
表1 材料力学性能
Table 1 Mechanical properties of the material
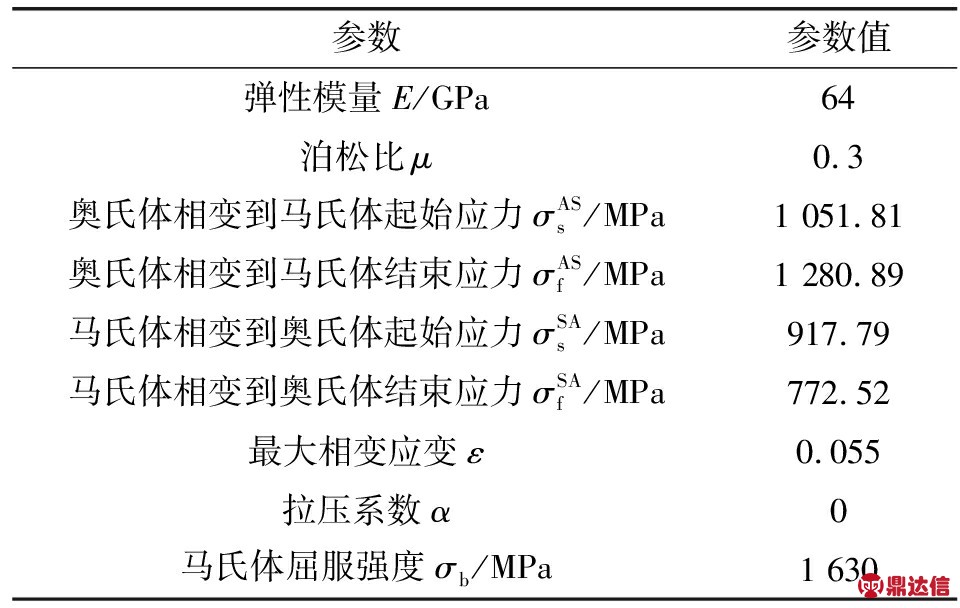
2.3 网格划分与边界条件
为了提高计算速度,在该模型中套管、中心管、上压环和下压环以近似刚体处理,即这些零件的弹性模量设成较大值,并且用3.2 mm的单元尺寸进行网格划分。密封元件是核心零件,划分网格时要细密一些,文中模型中以0.7 mm的单元尺寸对密封元件进行网格划分。密封组件的有限元网格模型如图3所示。
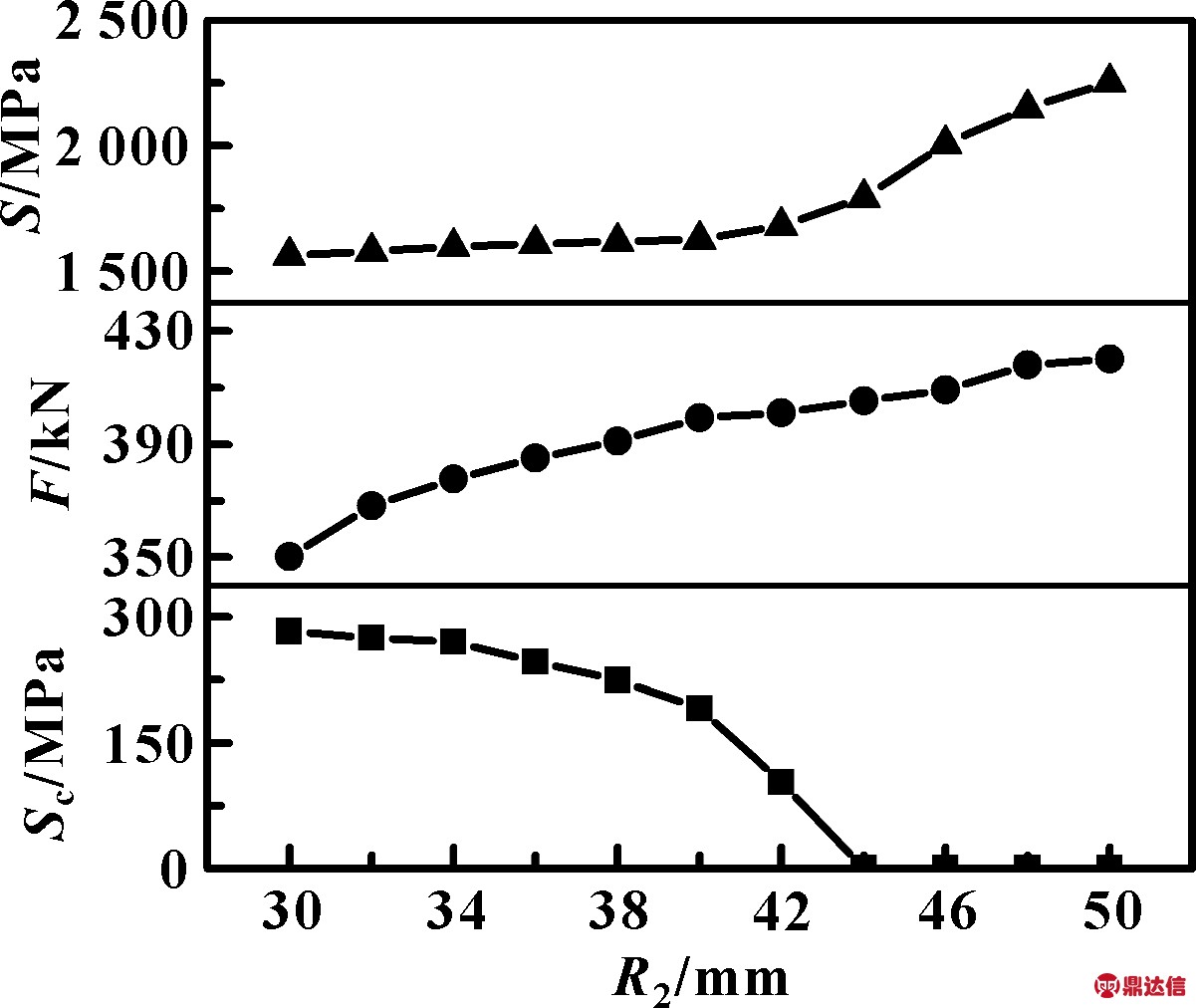
图3 密封组件的网格模型
Fig 3 Mesh model of the seal assembly
在密封元件、套管、中心管、上压环和下压环的对称面上施加法向约束,同时在下压环、套管和中心管的底面也施加法向约束来限制模型轴向移动,并设定上压环沿Y轴负向下压位移为4.2 mm。密封元件与套管、中心管、上压环、下压环4个零件之间设为摩擦接触,摩擦因数为0.15。
3 密封元件密封性能影响因素分析
针对承压环宽度b、承压环高度h、膨胀半径R1、拱形半径R2、拱形厚度t和卸载槽半径r等(各参数标注见图1)结构参数运用单因素分析法对金属密封元件密封性能的影响进行分析,各结构参数的变化范围根据密封元件在封隔器中的实际装配尺寸以及套管尺寸(套管型号为N-80)而选定,密封元件及其组件的关键尺寸如表2所示。
表2 密封元件及其组件结构参数
Table 2 Structural parameters of the sealing
element and its components mm
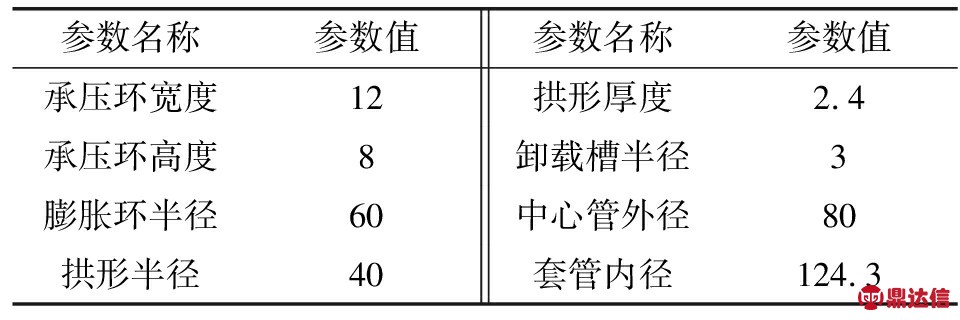
在实际使用中,密封元件密封性能的好坏主要用其密封承压能力来评价,而密封承压能力与密封面的接触应力直接相关,故可以用接触应力来对其评价[3-6]。但只使用接触应力进行评价,不能体现密封元件的整体受力情况,故文中采用密封元件的最大应力S、坐封力F(换算成完整模型后的值)和接触应力Sc(密封元件与套管间接触应力)3个指标对其密封性能进行评价。
3.1 承压环宽度
如图4所示,随着承压环宽度b的增大,密封元件的坐封力F和接触应力Sc非线性增加,其最大应力S先减小后增大。当b≤11.5 mm时,密封元件受压发生失稳,致使密封元件局部应力过大;随着b的增大,密封元件受到失稳效应的影响逐渐减弱;当b≥11.5 mm时,密封元件不再失稳,最大应力S逐渐增大。因此,适当增大b不仅可以消除失稳,提高稳定性,同时还可以获得更大的接触应力Sc,提高密封效果。

图4 密封性能与承压环宽度关系曲线
Fig 4 Curves of sealing performance and width of the support ring
3.2 承压环高度
如图5所示,密封元件的最大应力S、坐封力F和接触应力Sc基本不随承压环高度h的变化而变化,因此h对密封元件的密封性能影响不大,但出于对结构稳定性考虑,h应适当偏大一些。

图5 密封性能与承压环高度关系曲线
Fig 5 Curves of sealing performance and height of the support ring
3.3 膨胀环半径
如图6所示,随着膨胀环半径R1增大,最大应力S和坐封力F都呈非线性增加,且当R1≥59.6 mm时,二者增长迅速,且接触应力Sc大于0,并随着R1增大而增大。R1越大,接触应力Sc越大,密封承压效果越好,但同时坐封力F和最大应力S也快速增加,导致坐封困难、密封元件产生较大塑性变形,不利于密封元件的密封和重复使用,所以R1不宜过大。
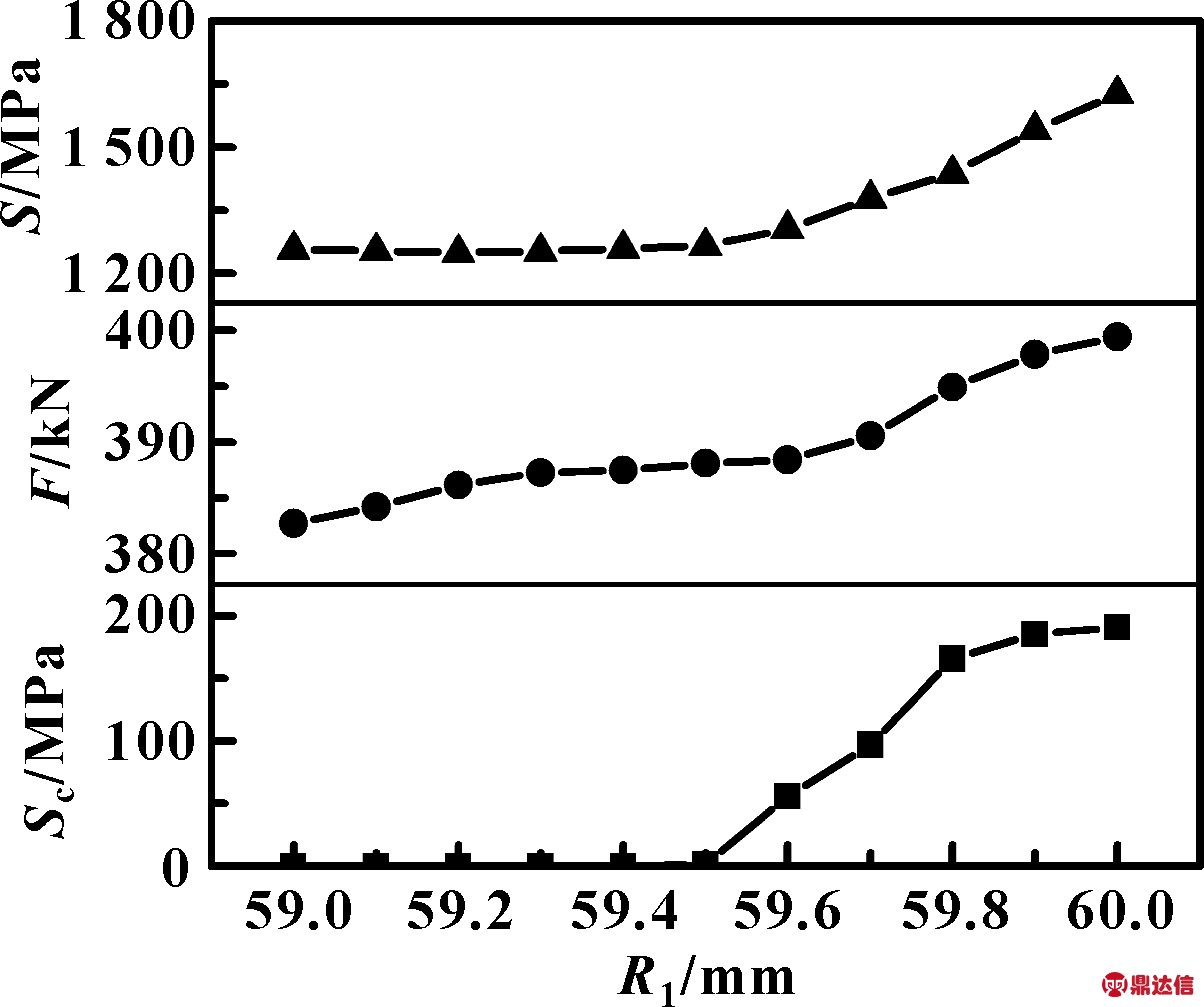
图6 密封性能与膨胀环半径关系曲线
Fig 6 Curves of sealing performance and radius of expansion ring
3.4 拱形半径
如图7所示,最大应力S和坐封力F随拱形半径R2非线性增加;接触应力Sc随R2非线性减小。R2的增大不利于密封元件的径向变形,同时最大应力S和坐封力F也会随之增大。R2越小,最大应力S和坐封力F越小,接触应力Sc越大,故在满足密封要求的条件下,R2应尽可能取小值。
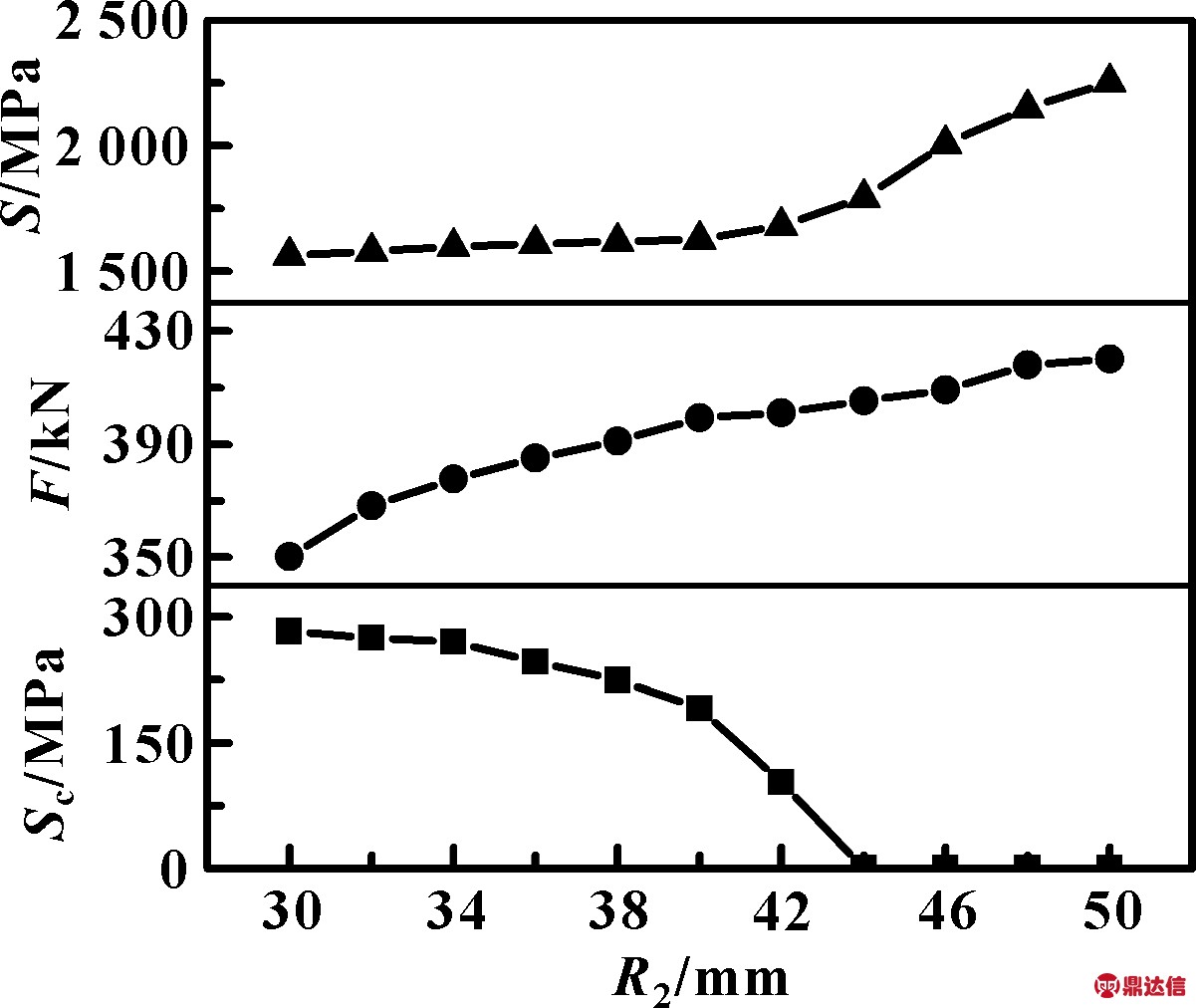
图7 密封性能与拱形半径关系曲线
Fig 7 Curves of sealing performance and arch radius
3.5 拱形厚度
如图8所示,随着拱形厚度t的增大,最大应力S先减小后增大。当t≤2.5 mm时,密封元件强度不足而发生失稳,导致局部应力集中;随着t的增加,失稳逐渐减弱,当t≥2.5 mm时,失稳消失,且最大应力S、坐封力F和接触应力Sc基本呈线性增加。故t=2.5 mm是理想点,设计时t值应在其左右选择。
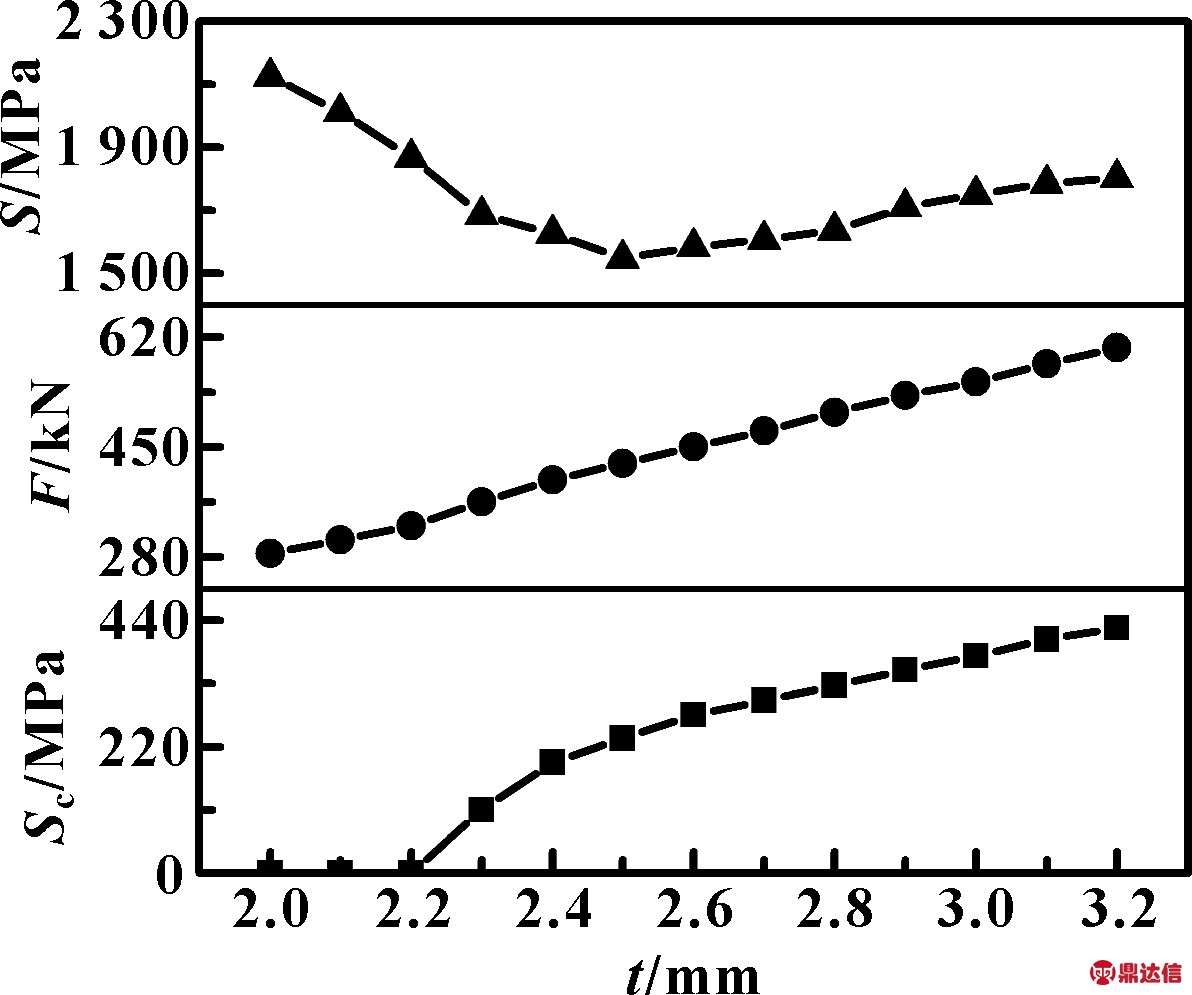
图8 密封性能与拱形厚度关系曲线
Fig 8 Curves of sealing performance and arch thickness
3.6 卸载槽半径
如图9所示,当卸载槽半径r≤3.6 mm时,随着r的增大,最大应力S逐渐减小,坐封力F近似呈线性递减,接触应力Sc呈非线性减小。
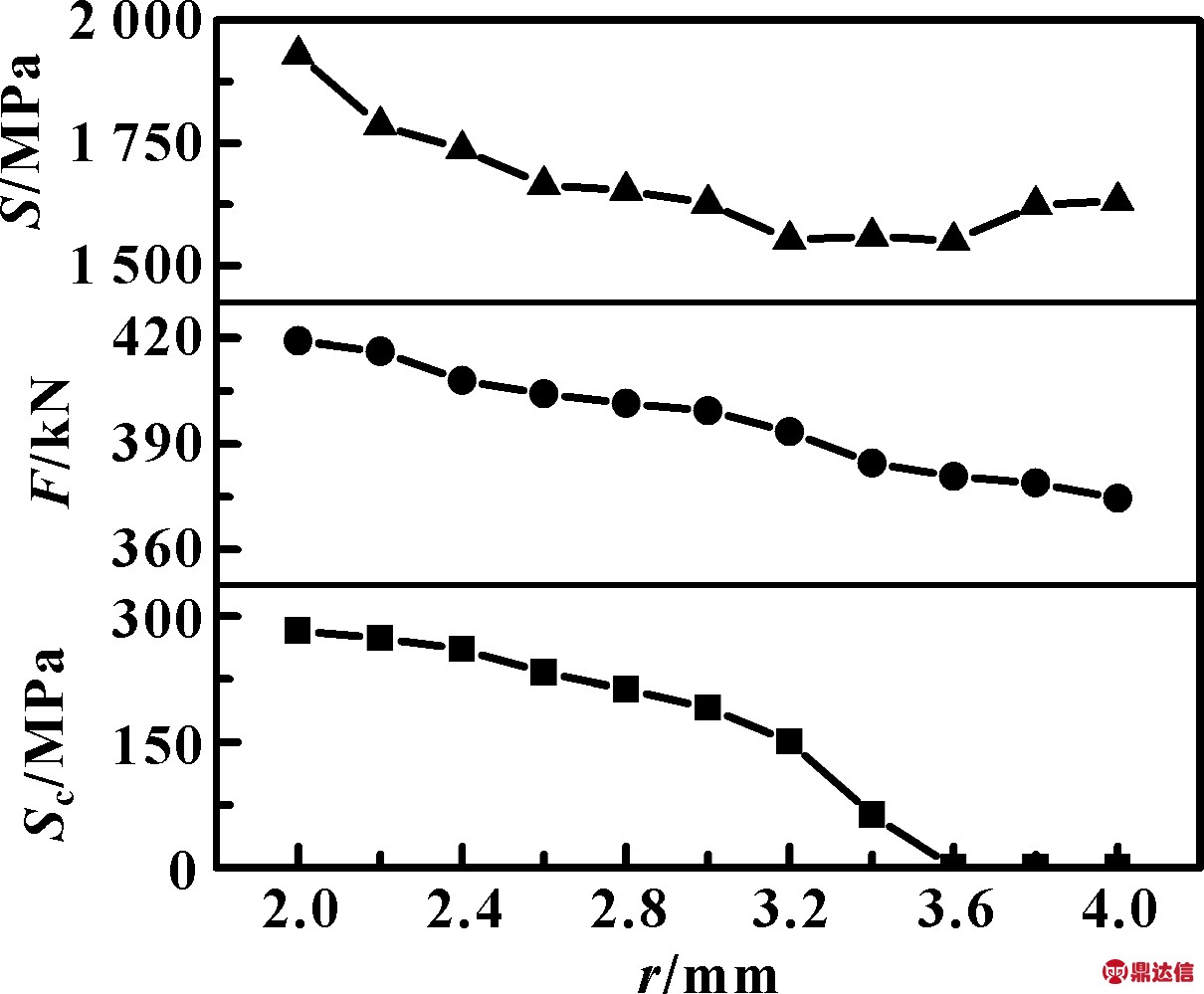
图9 密封性能与卸载槽半径关系曲线
Fig 9 Curves of sealing performance and unloading groove radius
所以在r≤3.6 mm时,增大r能够有效降低应力集中,且r越大,效果越明显,但接触应力Sc也随之减小,不利于密封。而拱形厚度t的增大能够有效提高接触应力Sc,在增大r的同时可考虑增大拱形厚度t来提高接触应力Sc,同时还能增加密封元件的稳定性。
4 结论
(1)设计一种压缩扩张式的封隔器金属密封元件,密封元件主要包括轴向承压环和径向膨胀环两部分,并在二者之间设置卸载槽。
(2)从密封性能随密封元件结构参数的变化趋势来看,密封元件的最大应力S随膨胀环半径R1和拱形半径R2单调增加,随承压环宽度b、拱形厚度t和卸载槽半径r先减小后增大;密封元件的坐封力F随着承压环宽度b、膨胀环半径R1、拱形半径R2和拱形厚度t单调递增,随卸载槽半径r单调递减;密封元件的接触应力在大于0的情况下随承压环宽度b、膨胀环半径R1和拱形厚度t非线性增大,随拱形半径R2和卸载槽半径r非线性减小;密封元件的结构参数承压环高度h对接触应力和坐封力几乎无影响,但出于稳定性考虑,承压环高度值的选取应适当偏大一些。
(3)从密封元件结构参数对密封性能指标的影响程度来看,拱形半径R2和拱形厚度t对密封元件的最大应力S的影响较大,其中拱形半径R2的影响更为显著;承压环宽度b、拱形半径R2和拱形厚度t对密封元件的坐封力F的影响较大,其中拱形厚度t的影响更为显著;承压环宽度b、拱形半径R2、拱形厚度t和卸载槽半径r对密封元件的接触应力的影响较大,其中拱形厚度t的影响更为显著。在密封元件的设计过程中,应着重考虑拱形半径R2和拱形厚度t对密封元件的影响,适当减小拱形半径R2或增大拱形厚度t可以有效提高密封元件的密封性能。