目前国内装载机的液压系统普遍采用开芯系统,由定量泵提供恒定的流量,系统压力由装载机的负载决定,为了限制系统的最高工作压力,必须设置一个溢流阀,当系统工作压力达到设定值时,定量泵输出的多余流量通过溢流阀流回油箱,这将导致很高的功率损失,在液压系统中产生大量的热损耗,致使整个系统效率较低。如采用负载敏感(Load Sensing)控制技术可以大幅提高系统效率,达到节能降耗的目的。
1、开芯系统能耗分析
图1为开芯系统简图。通过改变换向阀的方向及阀芯开口的大小,来控制进入液压缸油液的方向及流量ql。定量泵输出的多余流量△q由溢流阀溢回油箱。为了完成调速功能,不仅换向阀的开口量要能够调节,而且溢流阀必须始终处于开启溢流状态。
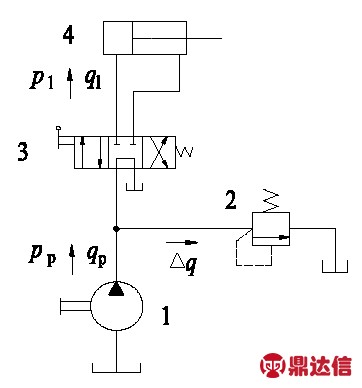
图1 开芯系统简图
系统的功率损失为
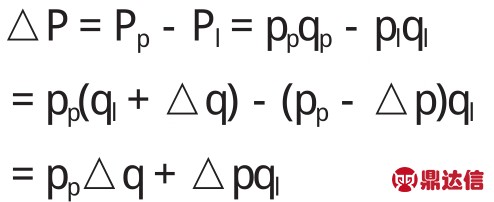
式中:pp—定量泵工作压力;
pl—液压缸工作压力;
qp—定量泵输出流量;
ql—液压缸输入流量;
△q—通过溢流阀的溢流量;
△p—流经换向阀的压力损失。
由上式可知,该系统的功率损失由两部分组成,溢流损失pp△q和节流损失△pql,这两部分功率损失都变成热量使油温升高,因此系统效率较低。据有关资料介绍,当负载恒定或变化很小时,η=0.2~0.6。
2、负载敏感控制系统的原理及能耗分析
采用负载敏感控制技术的系统是一种能感受系统压力-流量需求,且仅提供所需求的流量和压力的液压回路。
负载敏感控制系统(见图2)主要由负载敏感变量泵、负载敏感阀、LS信号反馈通道(梭阀)和执行元件(液压缸)组成。
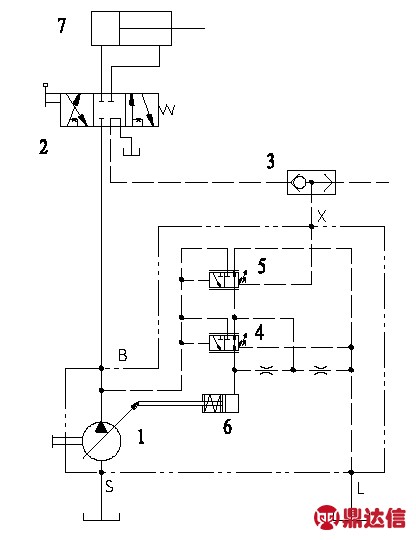
图2 负载敏感控制原理图
1.变量泵 2.负载敏感阀 3.梭阀 4.压力补偿器5.负载敏感控制器 6.变量伺服油缸 7.液压缸
当负载敏感阀2处于中位时,变量泵出口油路被封闭,X口油液通过梭阀及负载敏感阀内部油路返回油箱,变量泵出口压力油可通过变量泵上的负载敏感控制器5、压力补偿器4到达变量伺服油缸6,控制活塞克服复位弹簧力使变量泵斜盘处于接近零排量倾角的位置。此时泵出口压力为负载敏感控制器的设定值,一般为1 MPa~2 MPa,称之为泵的低压待命压力。变量泵输出流量接近零,仅为补偿内部泄漏的流量。
当负载敏感阀2处于左位或右位时,泵出口的压力油流经负载敏感阀内部的节流孔,产生一个压差信号通过反馈通道作用于负载敏感控制器5两端,与控制器内弹簧力共同控制阀芯的移动,这将导致斜盘倾角控制活塞内的部分压力油通过泄油路流回油箱。泵斜盘将到达一个新的角度,变量泵开始向系统提供较大的流量。根据负载敏感阀2内阀芯开口的大小,可实现变量泵输出流量的控制。
当液压缸活塞运行至行程终点时,变量泵出口压力升高至压力补偿器设定压力,压力补偿器阀芯克服弹簧力的作用,打开泵出口至斜盘伺服油缸的通路,高压油进入伺服油缸使斜盘处于零度倾角位置,变量泵输出流量接近于零。这种工况称为变量泵的高压待命状态。
变量泵待命状态时,由于只有极小的泄漏流量,因此功耗极低。
系统工作时的功率损失为

式中:pb--变量泵工作压力;
pL--液压缸工作压力;
q--变量泵输出流量;
△p--负载敏感控制器设定压力。
负载敏感控制系统不存在溢流损失,虽然节流损失仍存在,但节流孔两端压差恒定且较小(1MPa~2 MPa),故功率损耗很小。
系统效率为

可见泵的工作压力越高,系统效率也越高,节能效果越好。
3、负载敏感控制技术的应用
图3为采用负载敏感控制技术的轮式装载机转向与制动液压系统图。
转向系统采用了负载敏感转向器,转向器工作时,同时向优先阀和负载敏感变量泵提供LS信号,LS信号可控制优先阀按照转向油路的需求,优先向其分配流量,剩余流量通过EF口供给制动系统,当转向器处于中位时,全部流量均供给制动系统。
制动系统的蓄能器压力低于设定下限压力时,充液阀会发出LS信号给负载敏感变量泵,变量泵将提供蓄能器充液所需的压力和流量。当蓄能器压力达到设定上限压力时,变量泵X口压力油经梭阀、充液阀返回油箱,变量泵处于待命状态。
4、结语
采用负载敏感控制的液压系统基本消除了溢流损失,可大幅降低功率损耗,达到理想的节能效果。负载敏感变量泵可同时驱动多个负载,为多个系统提供不同的压力和流量需求,且各系统之间互不影响。基于这些特点,负载敏感控制技术在工程机械、农业机械等领域已得到广泛应用。
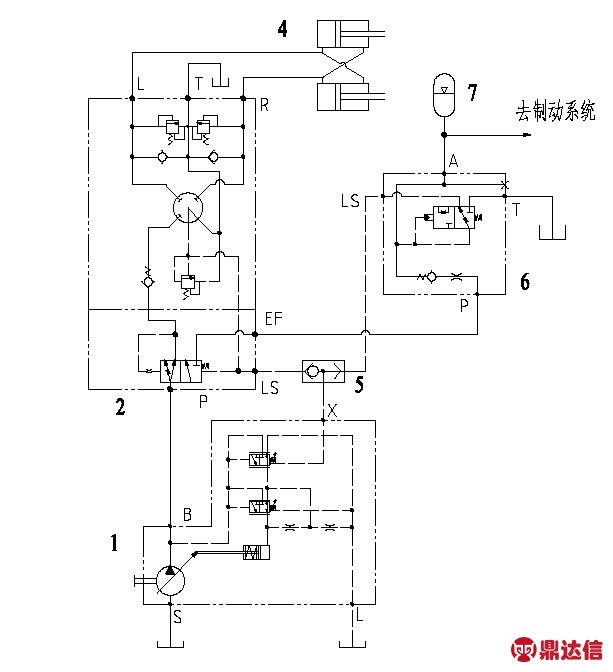
图3 装载机转向及制动液压原理图
1.负载敏感变量泵 2.优先阀 3.转向器4.转向油缸 5.梭阀 6充液阀 7蓄能器