摘要: 为了研究高温环境下具有梯度结构的多孔金属纤维吸声性能,应用物性参数与温度之间的关系式,将Johnson-Allard吸声理论模型拓展到高温条件下,建立了多孔金属纤维材料高温吸声理论模型。采用高温阻抗管设备,测量了多孔材料试件,实验测试数据与理论计算结果符合很好,验证了理论模型的有效性。应用声阻抗转移公式,进一步将该理论模型拓展为梯度多孔金属纤维的高温吸声理论模型,并结合优化算法对多层梯度材料结构进行了优化设计。研究结果表明:高温条件下,材料吸声效果相比常温条件下稍差;多孔材料孔隙率和纤维丝径对材料吸声性能影响显著,随着孔隙率或纤维丝直径增大,材料吸声系数在低频段减小,在中频段增大;经过结构优化设计后,在同等条件下,多层梯度金属纤维材料吸声性能明显优于单层结构,具有良好的吸声效果。研究工作对多孔金属纤维材料的高温吸声应用及梯度优化设计具有一定的指导意义。
关键词: 多孔金属纤维;梯度结构;高温;吸声性能
近年来,超轻多孔金属材料得到了越来越多的关注和研究,多孔金属纤维具有减振降噪、缓冲吸能等特性。相比于传统吸声材料,多孔金属纤维材料具有高比刚度、高比强度、耐腐蚀、耐高温等特性,在高温、高声压等恶劣环境中有着广泛的应用前景,可用以制作航空发动机声衬等[1]。
目前,针对多孔金属材料吸声系数的计算方法可分为经验、微结构、等效流体模型。Delany等在大量实验基础上,建立了高孔隙率多孔金属材料在特定频率范围内特征阻抗与流阻率之间的指数经验关系表达式[2],尽管这一模型在很多吸声器中得到了应用,但是该公式不能计算出准确值,特别在低频段会出现较大误差;Morse-Ingard模型建立在严格物理声学定律基础之上,但其需要多孔金属材料微结构的严格描述,这对于多孔金属纤维来说比较困难[3];Allard等考虑了热传导和空气黏性对吸声性能的影响,给出了多孔金属材料等效密度、等效体积模量表达式[4]。但是,这3类模型均没有考虑温度变化对空气物性的影响。
目前,国内外对于多孔金属纤维高温环境下声学性能的理论及实验研究还不够深入,已有的文献针对温度对多孔金属材料吸声性能影响的考虑尚不够全面。张波等采用波动方程法研究了均匀温度场和梯度温度场对多孔金属纤维材料吸声性能的影响[5];孙富贵等从实验和理论两方面研究了多孔金属材料的高温吸声性能[6];吴久汇等采用湍流类比的方法研究了高温高声压下多孔金属材料的吸声性能[7];敖庆波等对多孔FeCrAl纤维多孔材料的高温吸声性能进行了实验研究[8];孟晗等对常温下多孔金属纤维梯度结构进行了优化设计[9]。但是,这些研究都未涉及到高温环境下梯度结构多孔金属纤维的声学性能。
本文充分考虑了温度对空气密度、比热容、热传导系数、普朗特数、流阻率等相关参数的影响,将Johnson-Allard模型拓展到高温条件下,建立了高温环境下多孔金属纤维吸声理论,研究了高温环境下材料参数对吸声性能的影响及梯度多孔结构的吸声特性,并进行了吸声结构的梯度优化设计。
1 声学模型
1.1 Johnson-Allard模型
Allard等在前人工作基础上提出了等效流体模型,考虑了热传导及空气黏性阻力对吸声性能的影响,引入结构形状因子来描述孔结构的影响,得到了多孔材料的等效密度ρe和等效体积模量Ke,并且进一步得出多孔材料特性阻抗Zc、复波数k和吸声系数α的表达式[4]
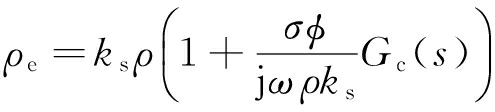
(1)

(2)

(3)
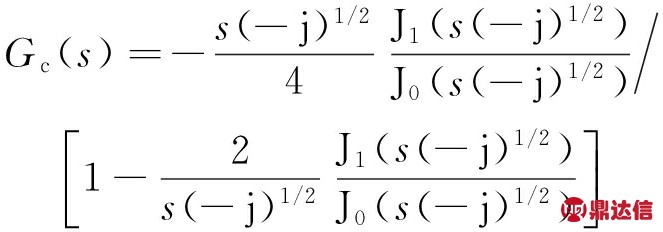
(4)

(5)
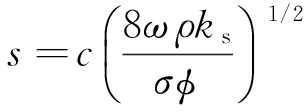
(6)
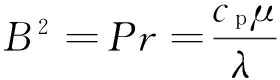
(7)
式中:ks为曲折因子;ρ为空气密度;σ为流阻;φ为孔隙率;ω为角频率;Gc(s)、F(B2ω)均为角频率的函数;γ为比热容比;P0为标准大气压;Zf为表面声阻抗;Z0为空气特性阻抗;B2为普朗特数;J0、J1为零阶Bessel函数、一阶Bessel函数;c为孔形系数;cp、μ、λ为空气的比定压热容、黏性系数、传热系数。18 ℃室温下,空气密度ρ0=1.213 kg/m3,P0=1.013 2×105Pa,γ=1.4,B2=0.71。
刚性背面条件下材料表面声阻抗、空气特性阻抗为
Zf=-jZccot(kh)
(8)
Z0=ρ0c0
(9)
式中:h为材料厚度。
1.2 温度对参数的影响
假定多孔金属纤维材料在高温环境下内部空气温度场均匀分布,而且处于开放的环境,空气密度的变化在标准大气压条件下进行,空气符合理想气体状态方程PM=ρRT,其中P为大气压强,M为空气摩尔质量,ρ为空气密度,R为气体常数,T为空气绝对温度,则
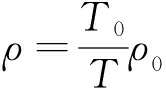
(10)
式中:T0为常温下绝对温度值。
流阻率的表达式为[4]
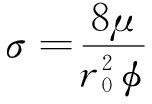
(11)
φ
(12)
式中:r0为多孔材料平均孔半径;d为纤维丝直径。流阻率可改写为
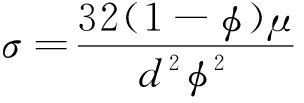
(13)
黏性系数由Sutherland公式[10]给出,即
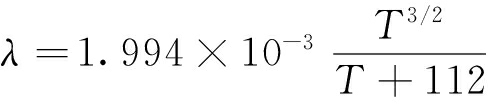
(14)
常温下气体的热物性参数比定压热容、比定容热容和比热容比等均为常数。但是,随着温度的升高,当温度大于800 K时,空气分子振动自由度会被激发,此时空气比热比是温度的函数,空气成为热完全气体;而当温度大于2 500 K时空气分子内部会发生化学反应[11]。本文不考虑化学反应的作用,根据统计热力学及近代量子力学中关于气体热力性质及温度的相关理论,对于单位质量的空气,其内能e等于平动能、转动能和振动能之和,即[12]

(15)
由式(15)可得单位质量空气焓值he的表达式,进而对he求导得定压比热cp的表达式,即
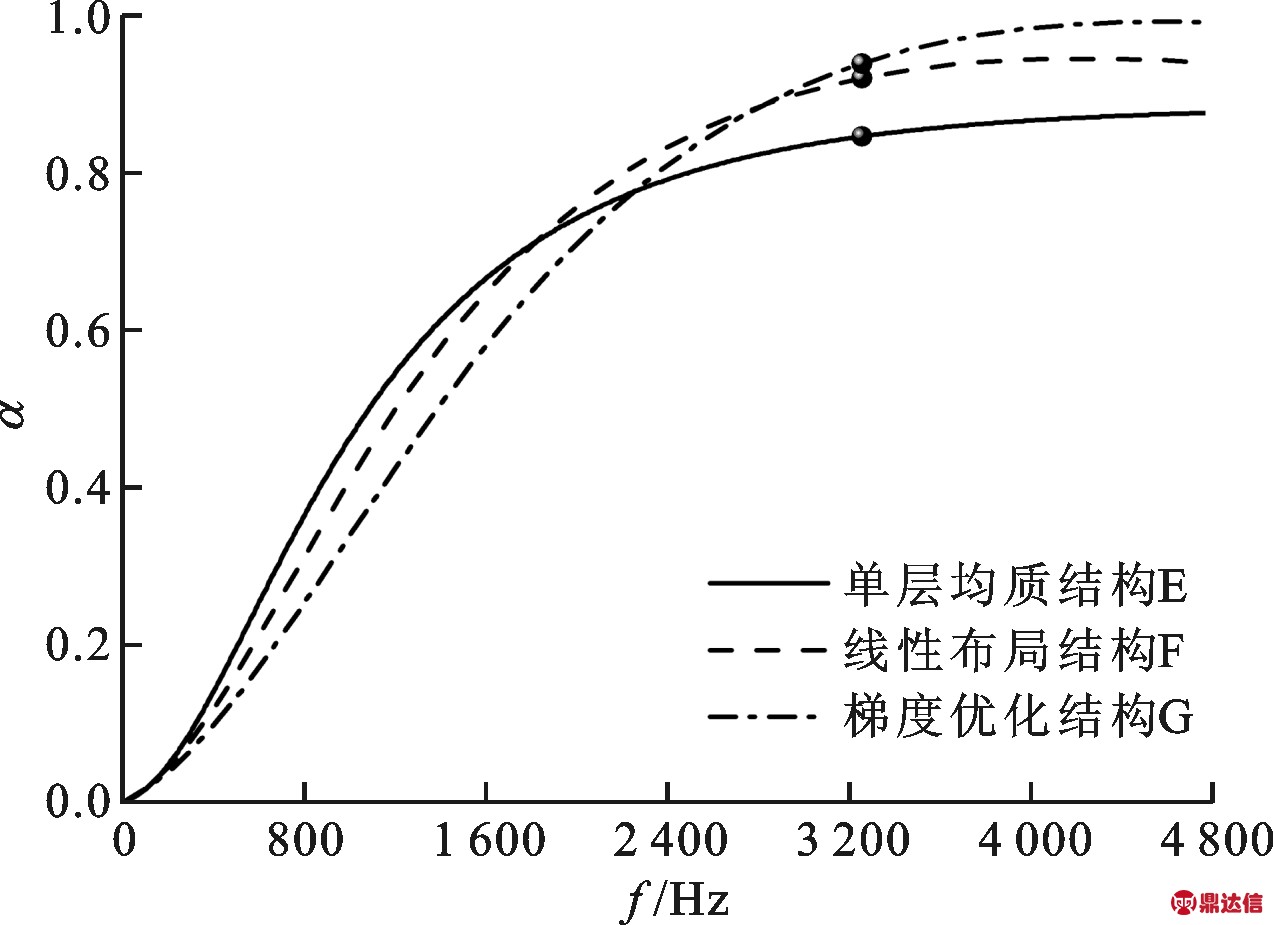
(16)

(17)
式中:Tve为空气分子振动特征温度,取值为3 100 K;R为气体常数,取值为8.314 J/(mol·K)。
由等式cp=cv+R,可得比热比为

(18)
热传导系数由Sutherland公式[10]计算可得
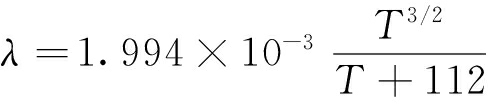
(19)
结合式(7)、(14)、(19),可得近似普朗特数
Pr=0.566T0.04
(20)
将受温度影响的各参数带入经典Johnson-Allard模型中,即可得到高温环境下多孔金属纤维声学性能理论模型。
2 多孔金属纤维吸声系数测量
2.1 实验原理
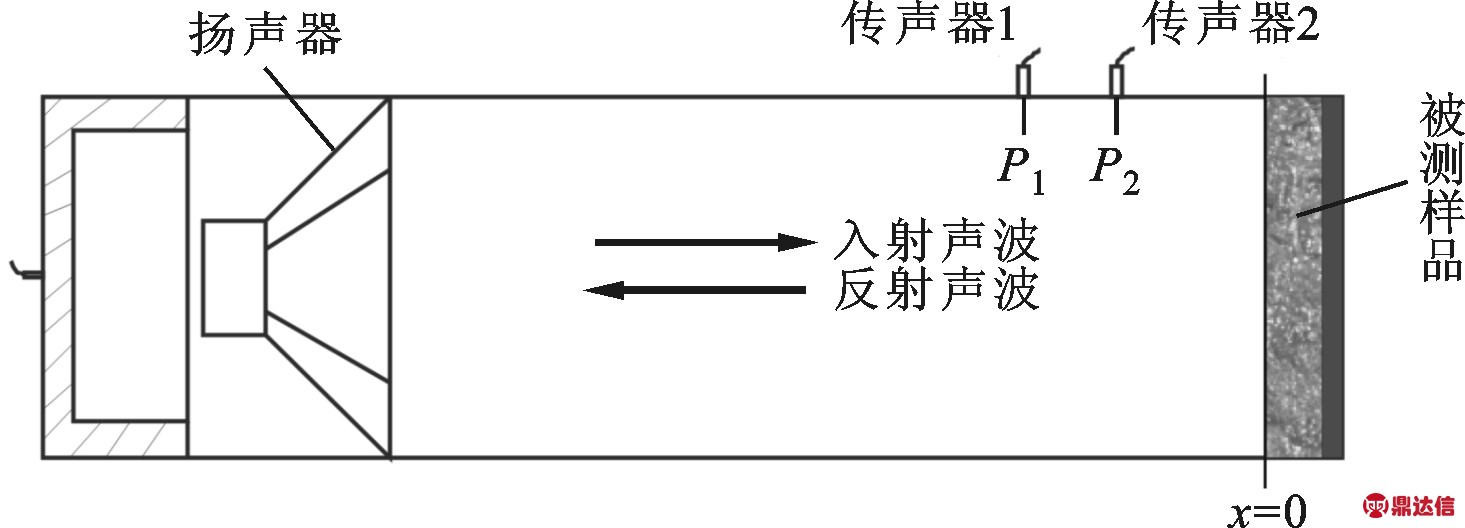
图1 阻抗管结构示意图
Chung等提出了双传声器传递函数法用来测量吸声系数[13],应用该测试的理论方法设计高温阻抗管测量装置,阻抗管结构示意图如图1所示。测试样品安装在平直、刚性的阻抗管的一端,管中的平面声波由声源(随机噪声、伪随机序列噪声或线性脉冲)产生。通过测量样品附近2个位置P1、P2处的声压来获得2个传声器信号的声传递函数,并结合P1、P2的位置关系,可计算法向入射声波的反射系数r,样品的吸声系数α可由反射系数表示为[13]
α=1-|r|2
(21)
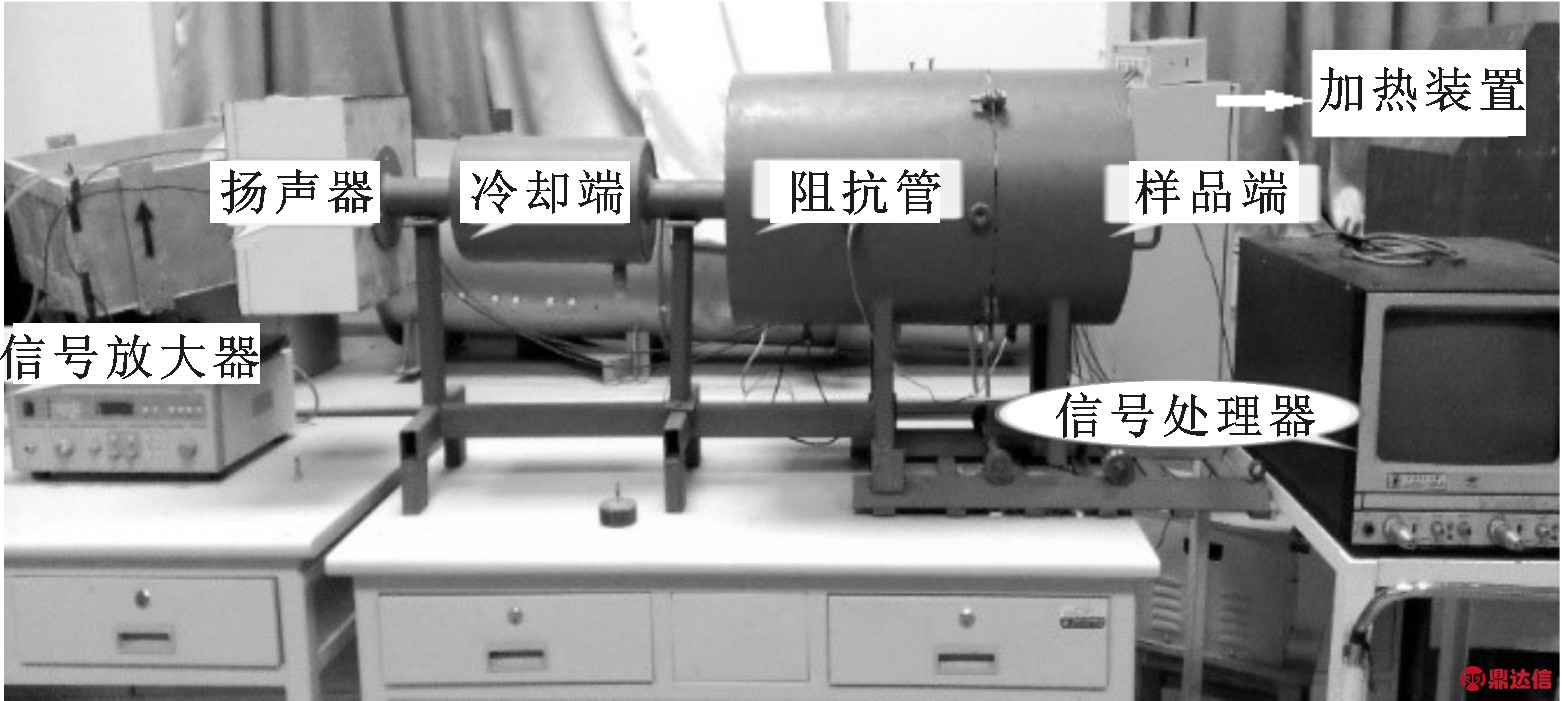
图2 高温阻抗管测量装置
2.2 实验装置
高温阻抗管包括最前端的信号生成模块,中间的扬声器、冷却管及阻抗管、样品端,信号处理模块和加热装置模块,测量装置如图2所示。根据双传声器传递函数法设计理论,本实验装置在室温下的测量范围为350~5 000 Hz,高温下为400~5 000 Hz。本文在测量时将下限取为800 Hz,上限取为4 800 Hz,以保证测量范围处于设备的最佳测试频段范围内。在实际高温测量过程中,当阻抗管内温度升到设定温度值后还需要保温3 h,以确保阻抗管内温度分布均匀,从而减少实验误差。
多孔金属纤维材料由直径为几微米到几百微米的金属纤维丝,经过剪切、无纺铺制、叠配及真空高温烧结而成。在制备过程中,控制其铺制、叠配的密度和方向可改变其孔隙率、曲折度和孔形系数等参数,从而影响其吸声性能。研究所用试件为西北有色金属研究院制备的圆饼形多孔金属纤维材料,试件直径为50 mm,厚度为50 mm,孔隙率为93%,纤维丝直径为50 μm,曲折因子、孔形系数由常温下的实验数据进行拟合得到,值为1.148、0.945。
3 理论与实验结果对比
为了验证理论模型的准确性,采用高温阻抗管设备测量了试件。在实验测试中,选用了100 ℃、300 ℃、500 ℃这3种代表性温度,在800~4 800 Hz频段内,试件在3种温度下的吸声系数理论值与实验值比较如图4所示。图4中实验值与理论值吻合得好,验证了该高温理论模型的适用性、准确性。
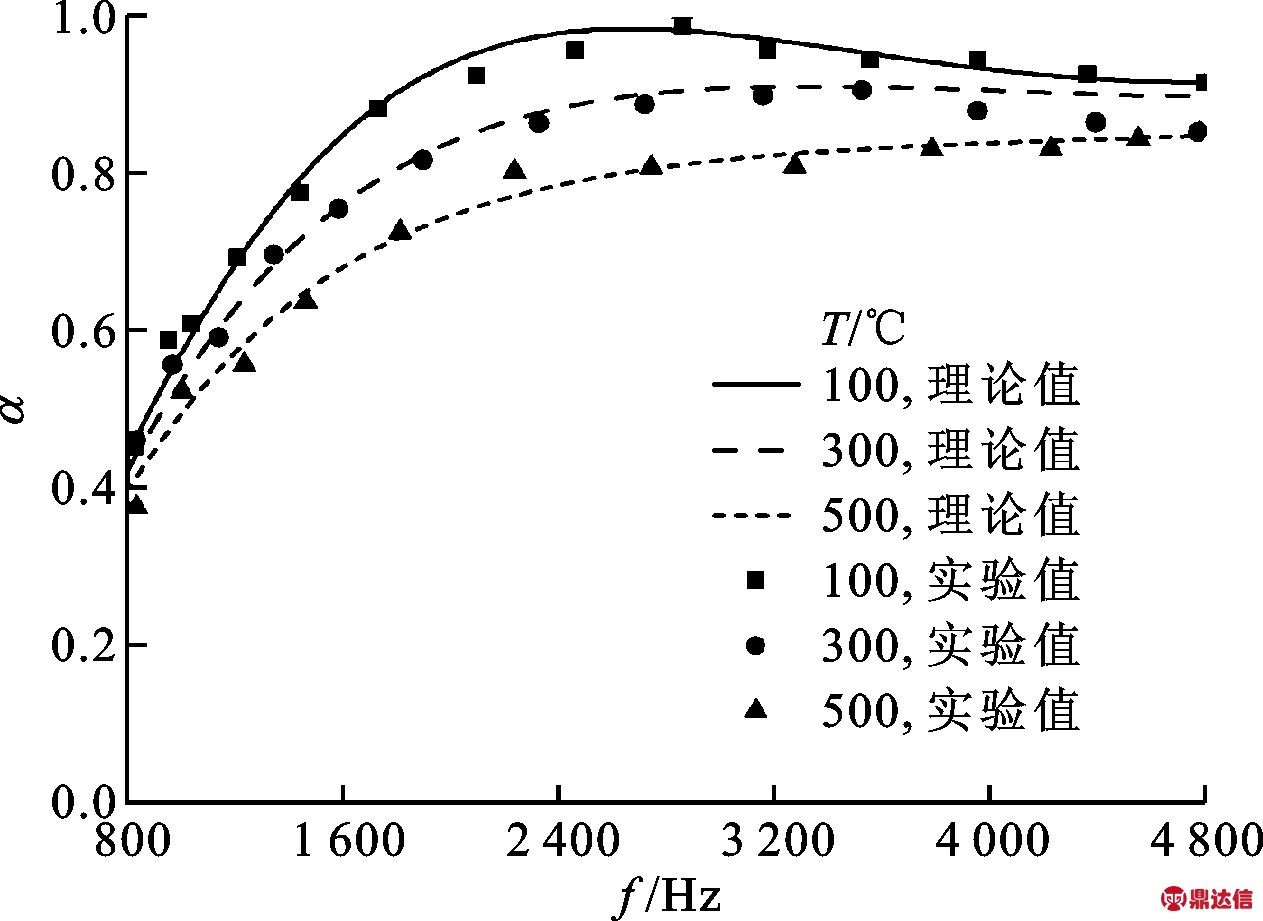
图3 3种温度下吸声系数理论值与实验值的比较
对于多孔材料吸声,随着频率的增加,吸声系数呈现波动变化,当多孔材料厚度为多孔材料内声波1/4波长整数倍时,吸声系数曲线会出现波峰,多孔材料中声波波长为
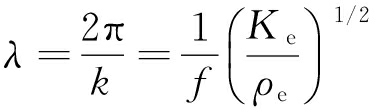
(22)
式中:f为声波频率;k为多孔材料中声波波长;ρe、Ke为多孔材料的等效密度、等效体积模量。第1个吸声共振波峰出现在d=λ/4时,对应的吸声波峰频率为[14]
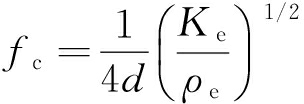
(23)
则多孔材料的吸声共振波峰出现在如下频率处,即

(24)
由式(22)可知,多孔材料内部的声波波长由等效密度和等效体积模量决定,而等效密度和等效体积模量由多孔材料的孔隙率、纤维丝径、曲折因子和孔形系数等几何构型参数及温度等环境因素决定。由式(22)~(24)可知,给定材料厚度,多孔材料吸声曲线上的波峰波动变化由多孔材料的几何构型参数及环境因素决定。当多孔材料的第1个吸声共振峰频率fc较高时,吸声曲线较为平滑;当fc较低时,吸声曲线波动较为剧烈。
在本文多孔材料几何构型参数及环境因素下,fc值相对较高,吸声曲线在0~4 800 Hz范围内较为平滑,在高温环境下,fc值会进一步增大,吸声曲线变得更为平滑。
4 结果与讨论
本节将应用本文所建理论模型来研究更宽频率范围内温度、孔隙率及纤维丝直径对多孔金属纤维材料吸声性能的影响,进而发展多层梯度结构理论模型,研究其高温吸声效果,并对梯度结构进行优化设计。
4.1 温度对单层均匀结构吸声系数的影响
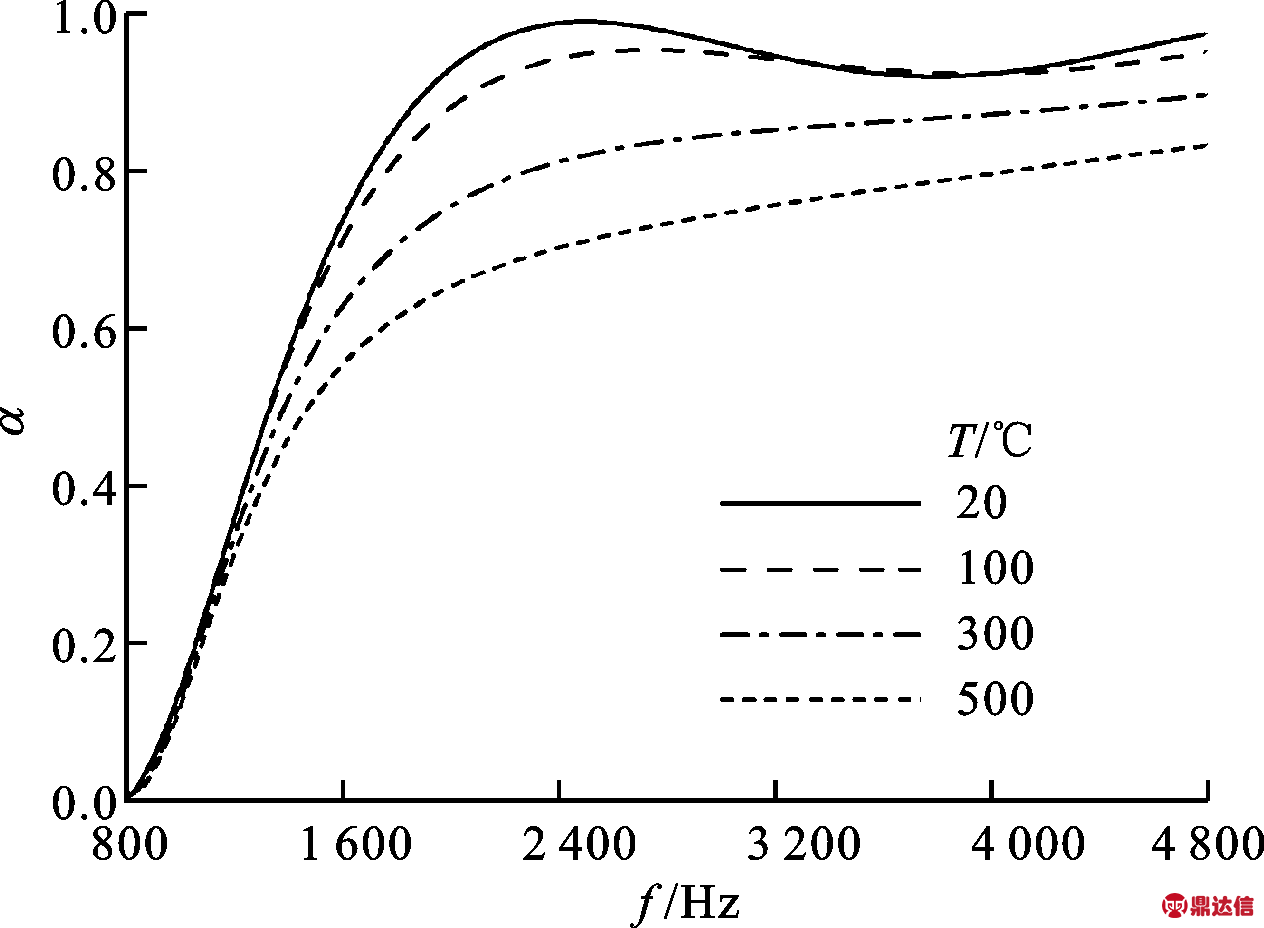
图4 不同温度下材料3的吸声系数理论预测
本节计算所用5种多孔金属纤维材料的几何参数如表1所示。材料3在不同温度下吸声系数理论预测结果如图4所示。材料3无量纲表面声阻(声阻抗实部)、声抗(声阻抗虚部)在不同温度下随频率变化的曲线如图5所示。由图4、5可知,温度升高时,声阻、声抗绝对值增大,导致材料表面声阻抗随着温度升高而增大,使得声波更难传入材料进行吸声损耗,反射声能增大,因而吸声系数减小。温度越高,空气黏性系数越大,流阻越大。
表1 材料的几何参数
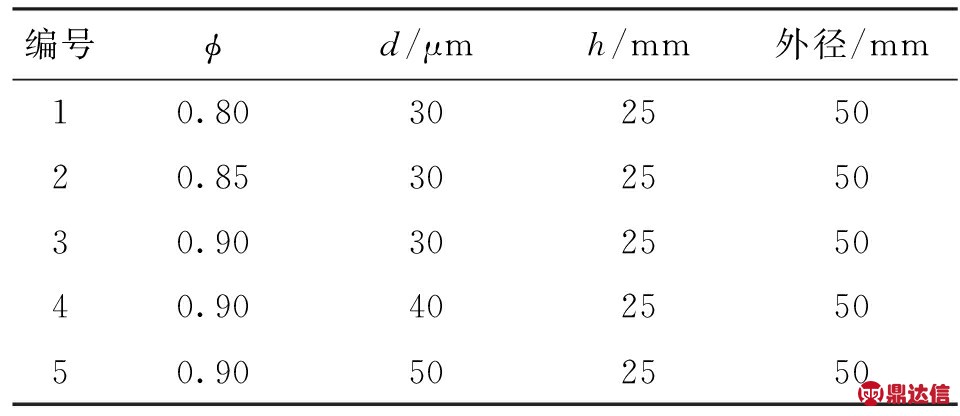
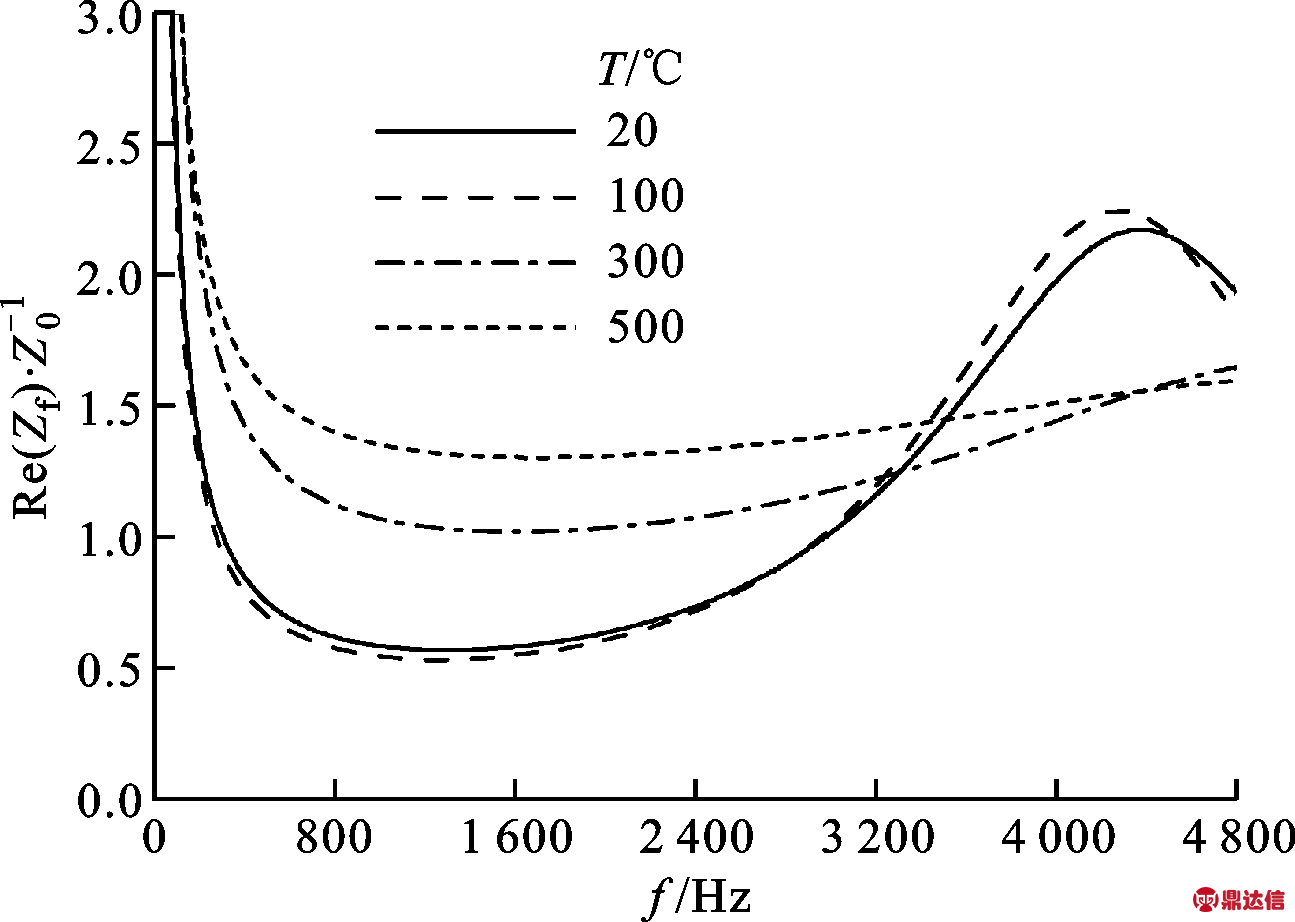
(a)表面声阻
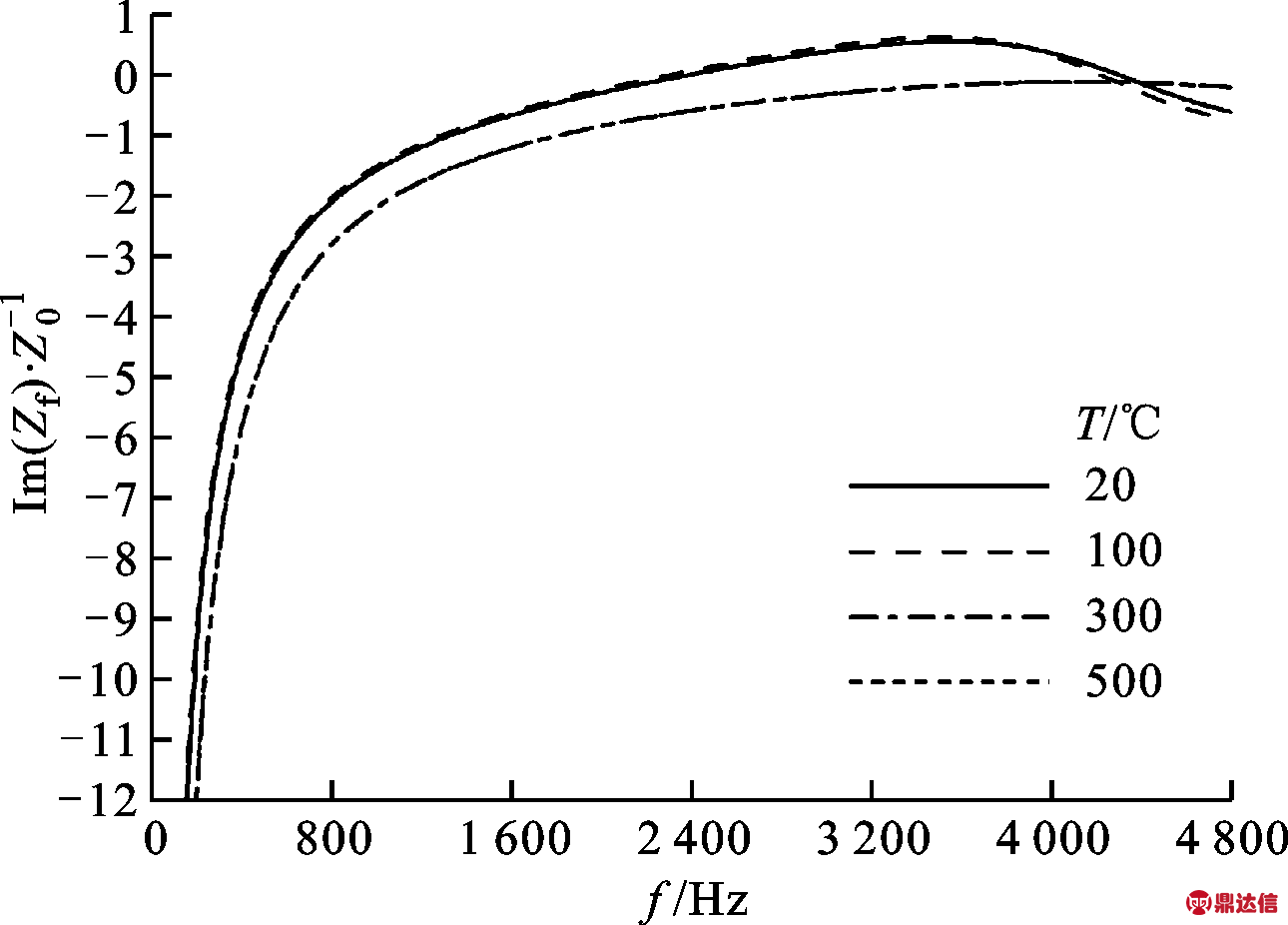
(b)表面声抗
图5 不同温度下材料3表面声阻、声抗的变化曲线
4.2 高温下材料参数对吸声系数的影响
300 ℃时材料1、2、3的吸声系数随频率变化的理论值曲线如图6所示。材料1、2、3只在孔隙率上有所变化,孔隙率分别为0.8、0.85、0.9。材料无量纲表面声阻、声抗随频率的变化曲线如图7所示。由图6可知:当频率小于600 Hz时,孔隙率越大,吸声系数越小;而当频率大于800 Hz时,则孔隙率越大,吸声系数越大。由图7可知,在考虑的频率内,当孔隙率增大时,声阻、声抗的绝对值都随之减小,使得吸声系数增大。这是因为孔隙率增大导致多孔金属纤维内部孔径增大,内表面积增大,从而在中高频时吸收更多的声能。在低频段时,热耗散起主导作用,孔隙率增大时,热耗散减小,因而吸声系数降低;高频段时,黏性耗散起主导作用,孔隙率增大时,黏性耗散增大,因而吸声系数增大。
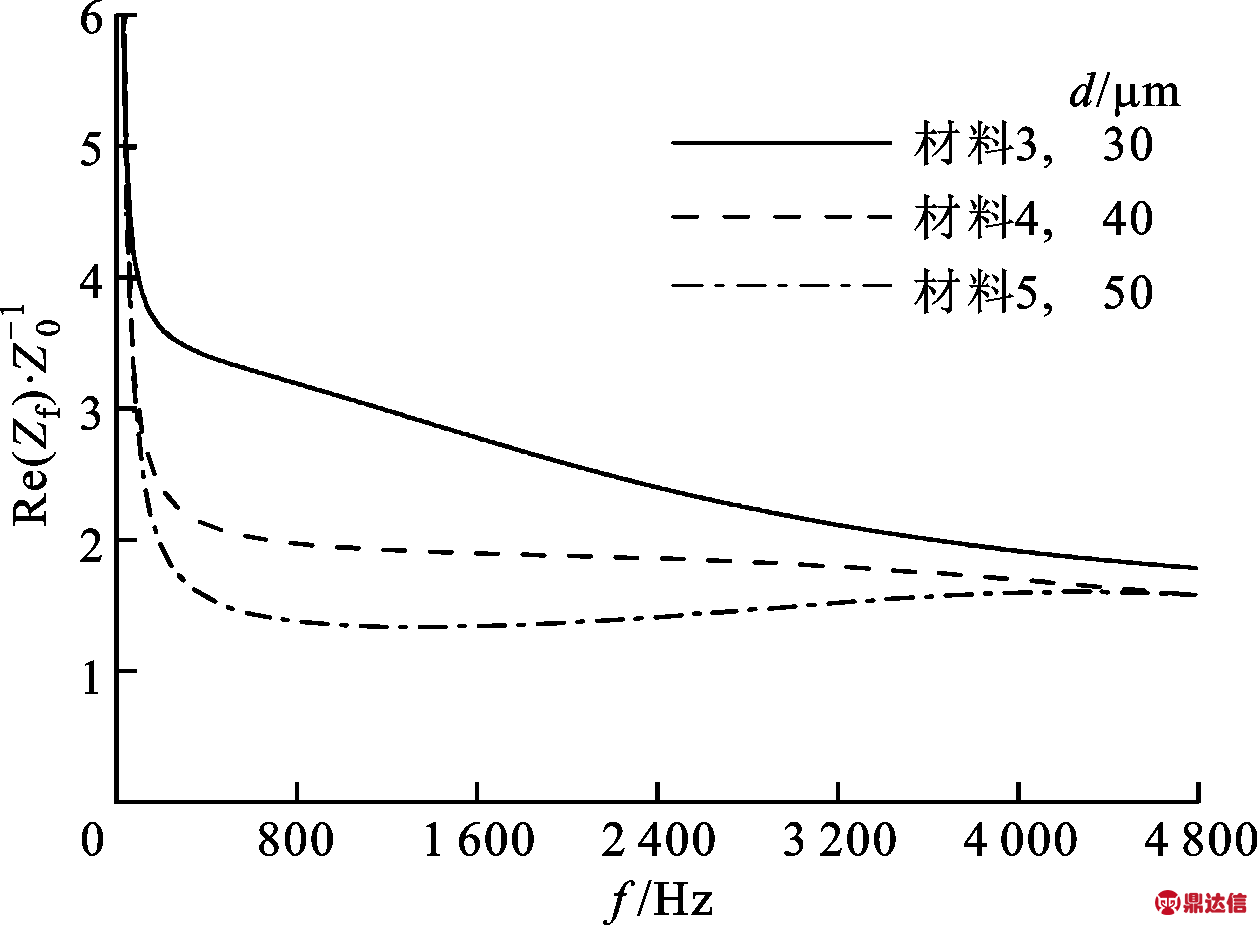
图6 300 ℃时不同孔隙率的多孔金属纤维板吸声系数理论值变化曲线
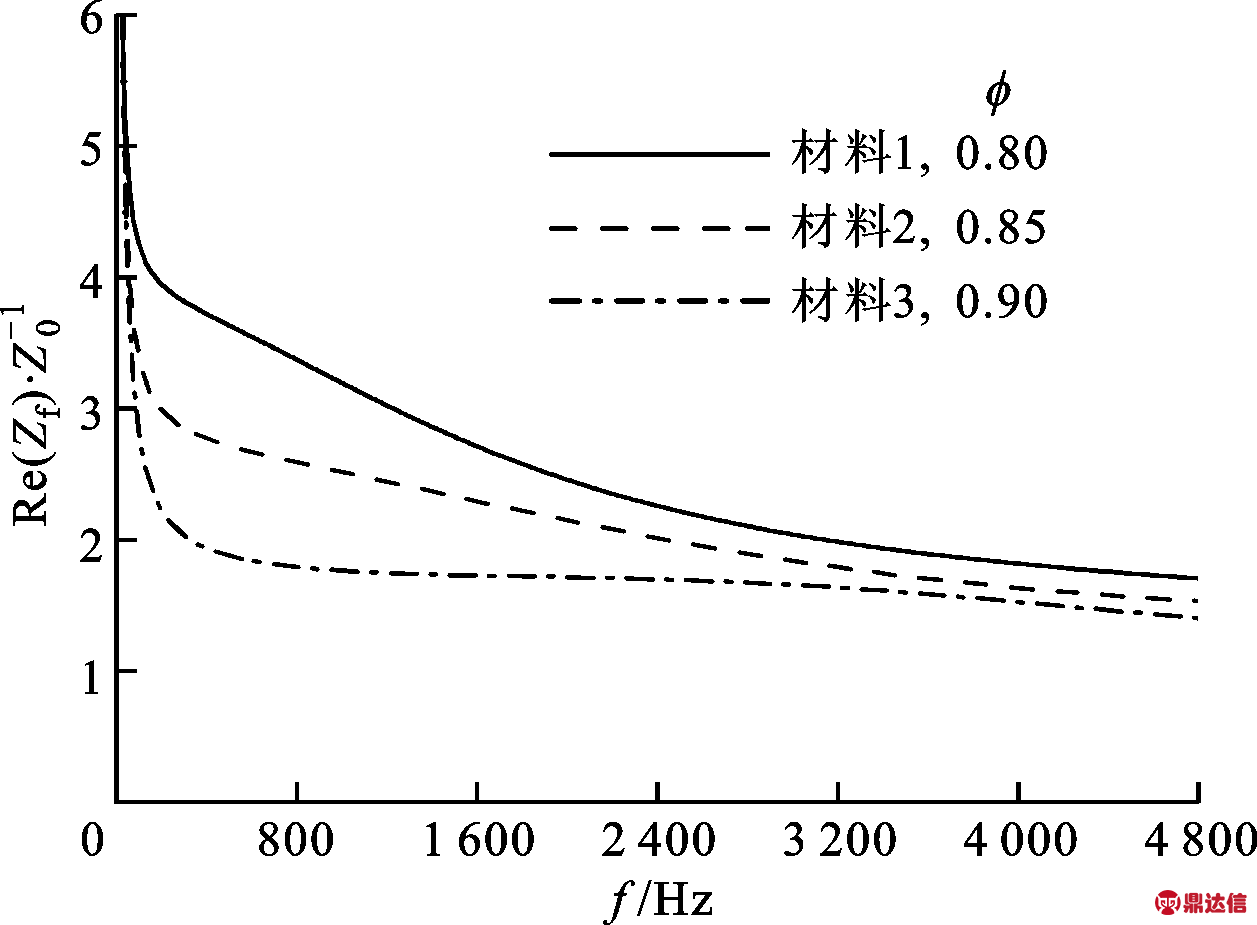
(a)表面声阻
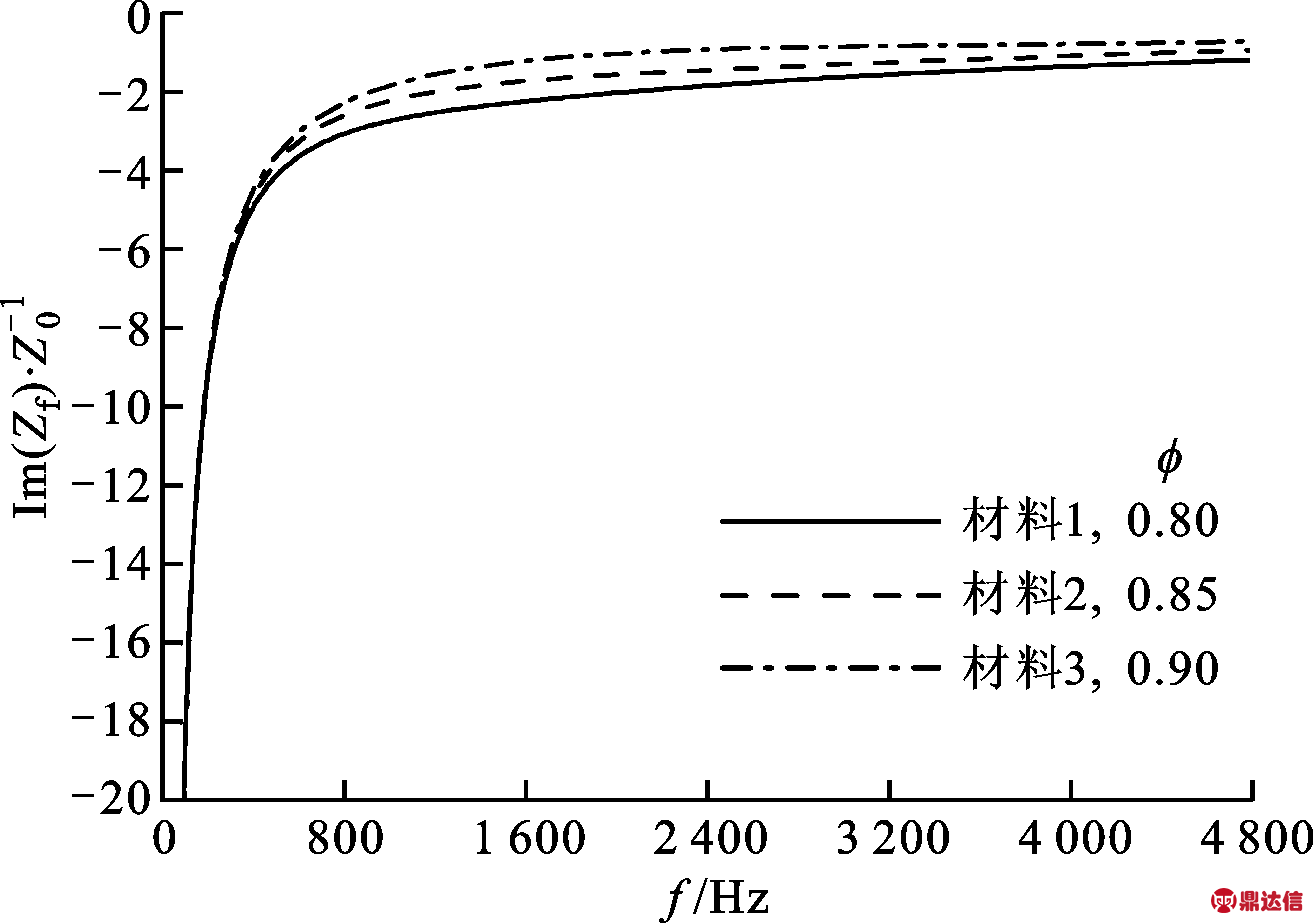
(b)表面声抗
图7 300 ℃时不同孔隙率的材料表面声阻、声抗的变化曲线
500 ℃时材料3、4、5吸声系数随频率变化的理论值的变化曲线如图8所示,无量纲表面声阻、声抗随频率的变化曲线如图9所示。由图8、9可知,在本文考虑的特定材料、温度及频率区间内,纤维丝直径对多孔金属纤维吸声系数的影响与孔隙率呈现相似的规律,改变孔隙率和丝径对材料的内表面积和表面声阻抗影响基本一致,从而影响其黏性耗散、热耗散来改变吸声效果。而在不同的频率段,黏性耗散、热耗散起不同的主导作用,导致材料丝径的变化在低频段及高频段对吸声系数的影响不同。
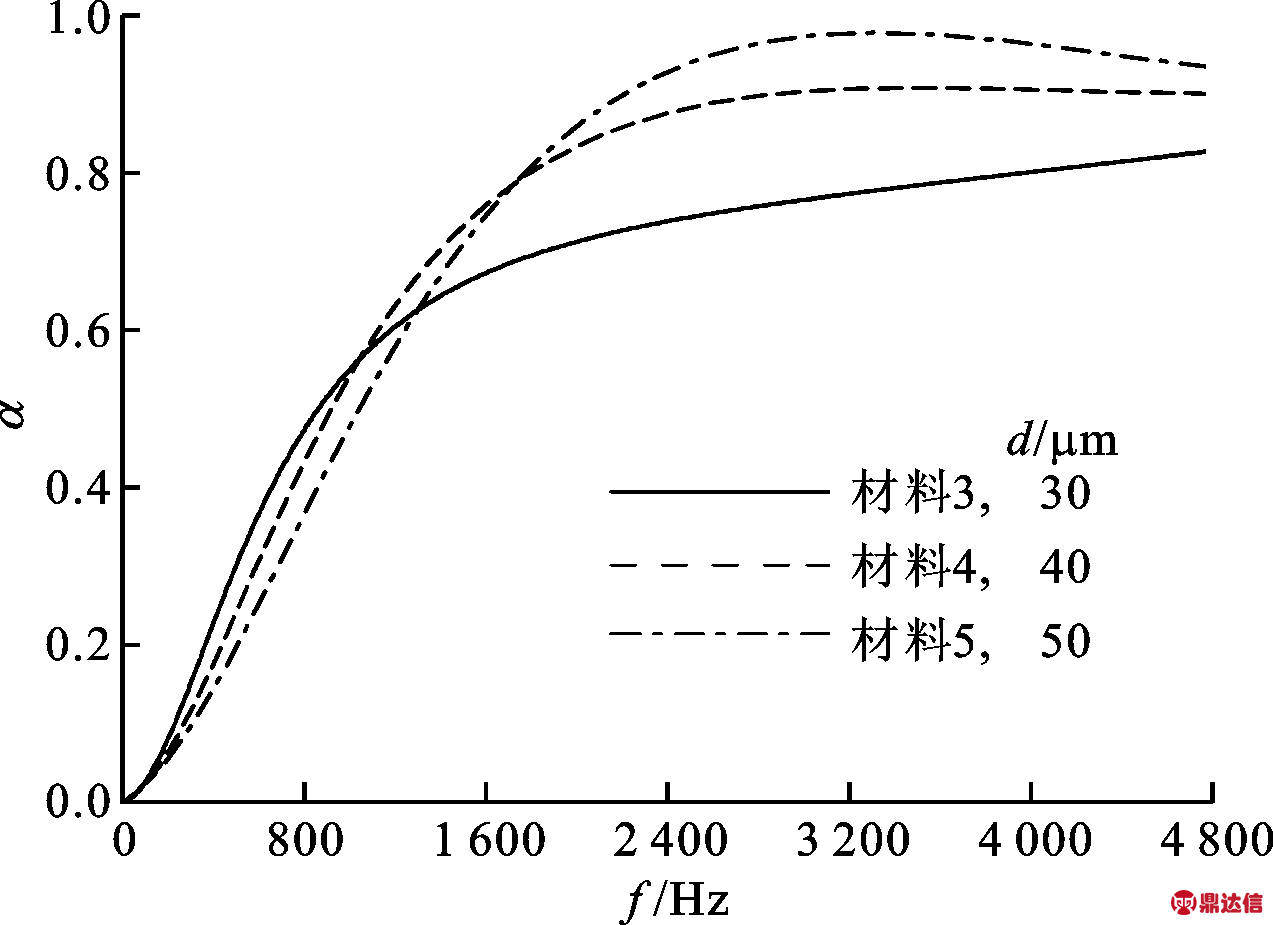
图8 500 ℃时不同纤维丝直径的多孔金属纤维板吸声系数理论值的变化曲线
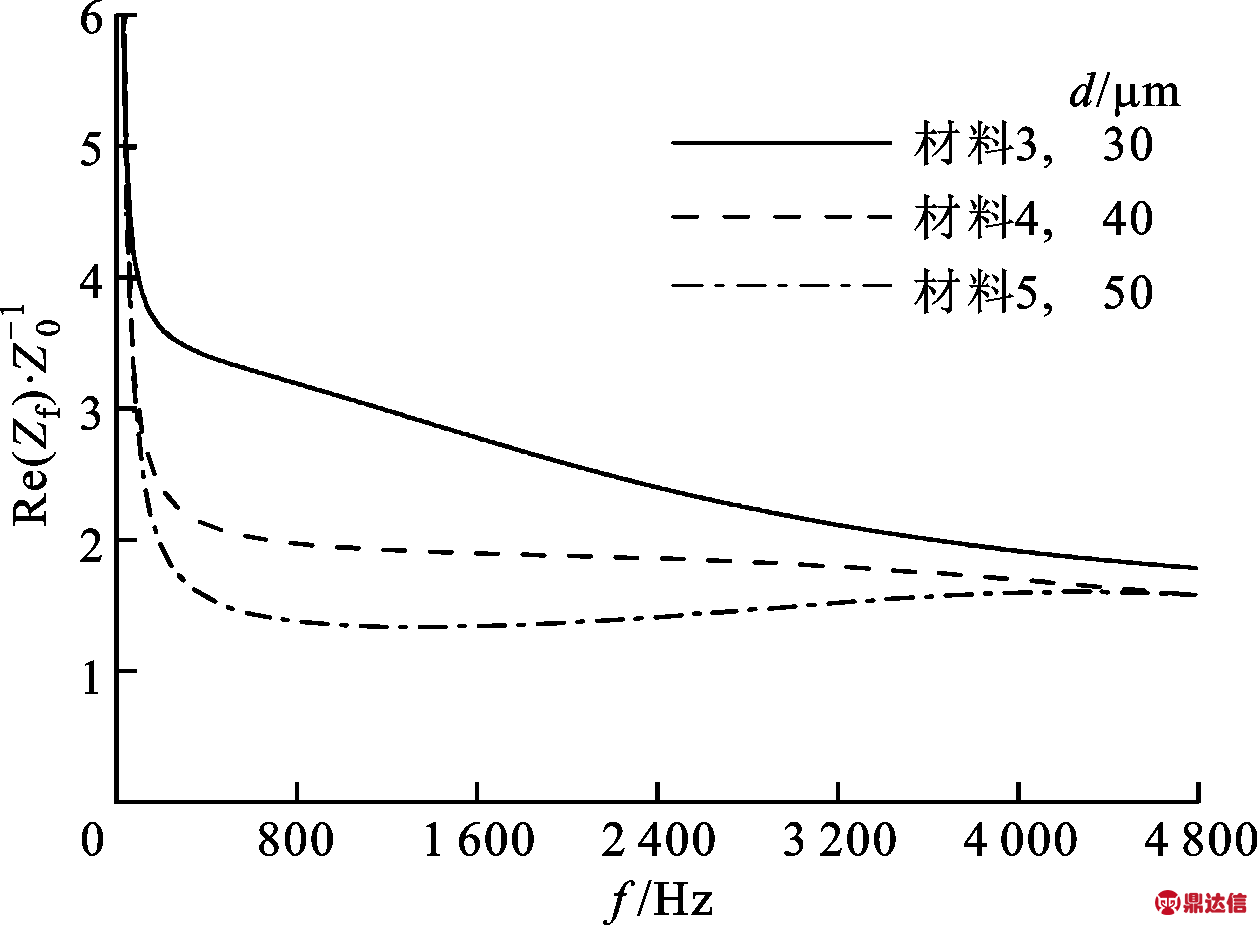
(a)表面声阻
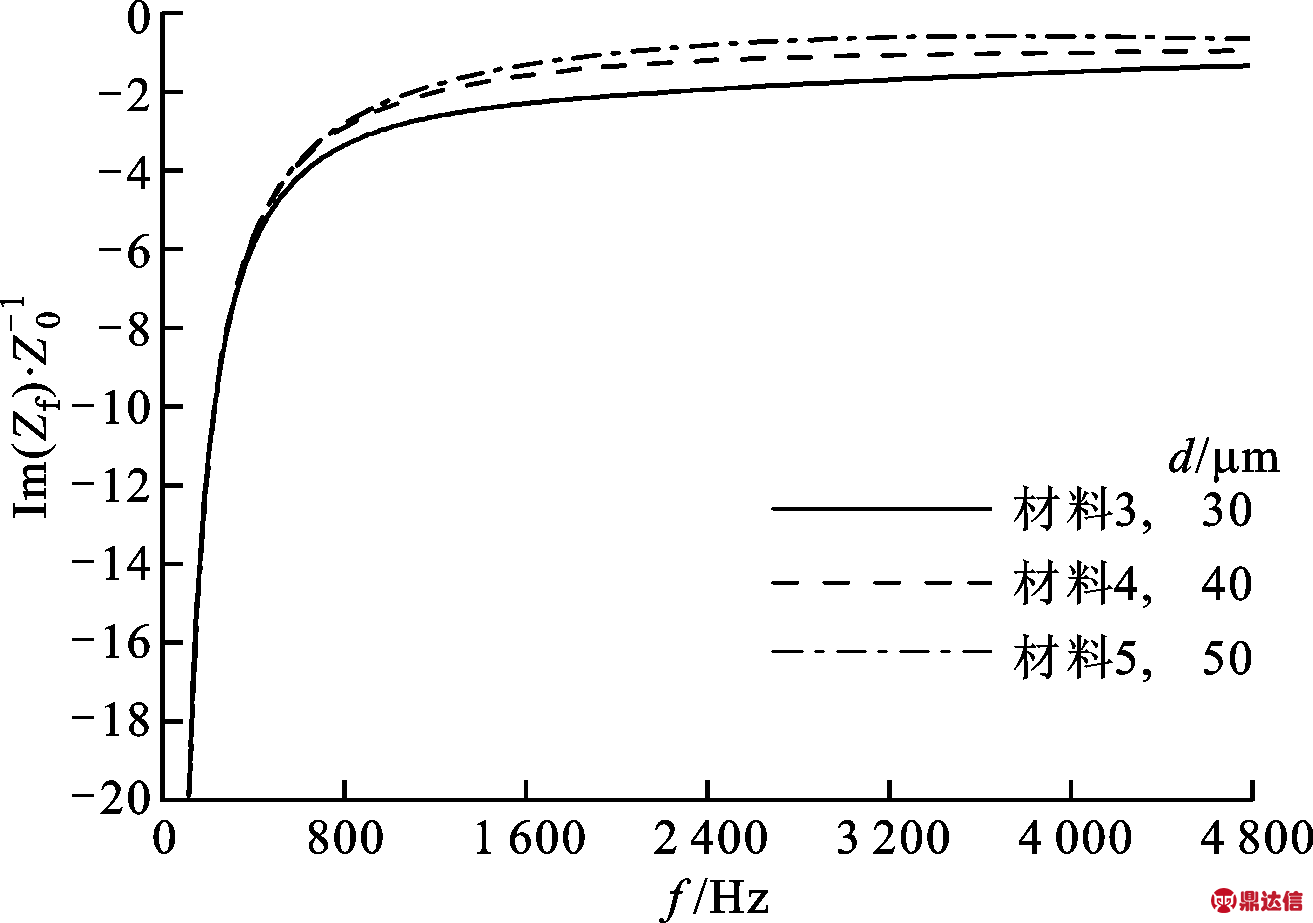
(b)表面声抗
图9 500 ℃时不同纤维丝直径的材料表面声阻、声抗的变化曲线
4.3 高温下多层梯度结构吸声性能分析
多层梯度结构的各层参数不是均匀一致的,有更多的设计自由度,可通过设计达到更好的吸声效果。首先针对3层吸声结构来分析梯度结构的吸声效果,然后进行优化设计。本节讨论的多孔金属纤维材料所处温度均为500 ℃,多孔金属纤维3层结构的简化示意图如图10所示,M1~M6分别为3层材料内表面或外表面上的某点,材料厚度分别为h1、h2和h3,M1处为刚性背衬。
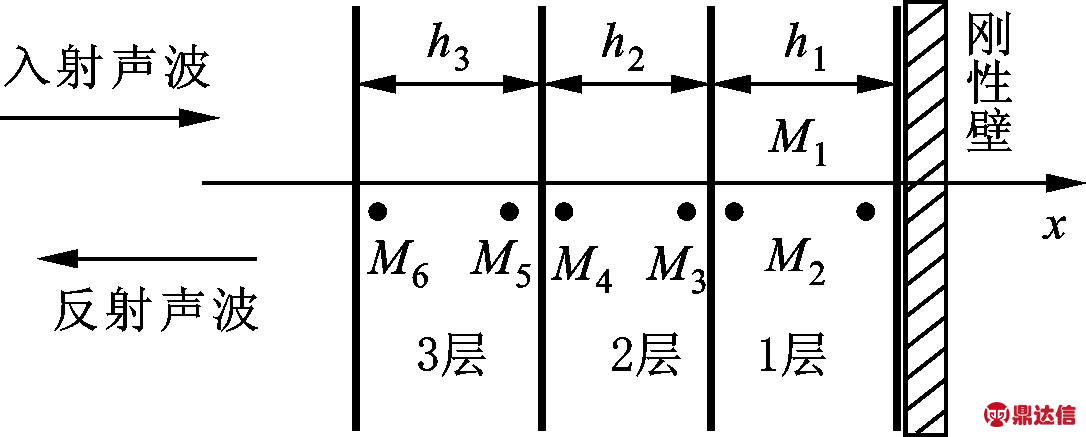
图10 多孔金属纤维3层梯度结构简化示意图
Z(M1)~Z(M6)分别为M1~M6处的表面声阻抗,不同材料连接处的界面考虑为理想界面,即在界面连接处满足声压和速度连续性的条件,因而具有相同的表面声阻抗,具体计算式为[4]

(25)
M1处为刚性背衬,因而有
Z(M3)=Z(M2)=-jZc1cot(k1h1)
(26)

(27)

(28)
式中:ki为第i层(i=1,2,3,…,n)的复波数;Zci为第i层的特征声阻抗;Z(M6)为3层结构表面声阻抗。假如为n层结构,则第n层与第n-1层的表面声阻抗之间关系为

(29)
本节涉及的材料A、B、C均为单层结构,其平均丝径分别为15、10、20 μm,厚度均为15 mm,D为3层结构,第1、2、3层的平均丝径分别为10、15、20 μm,厚度均为5 mm,孔隙率均为0.90,结构的纤维丝直径从内表面向外表面呈递增分布。不同吸声结构A、B、C和D的吸声系数理论计算结果的变化曲线如图11所示。由图11可知:对于单层结构A、B、C,随纤维丝直径增大,吸声系数在高频提高,而在低频降低;除了400 Hz以下频段,D的吸声效果要好于单层结构,相比于单层结构,多层梯度结构有利于增强材料吸声性能。
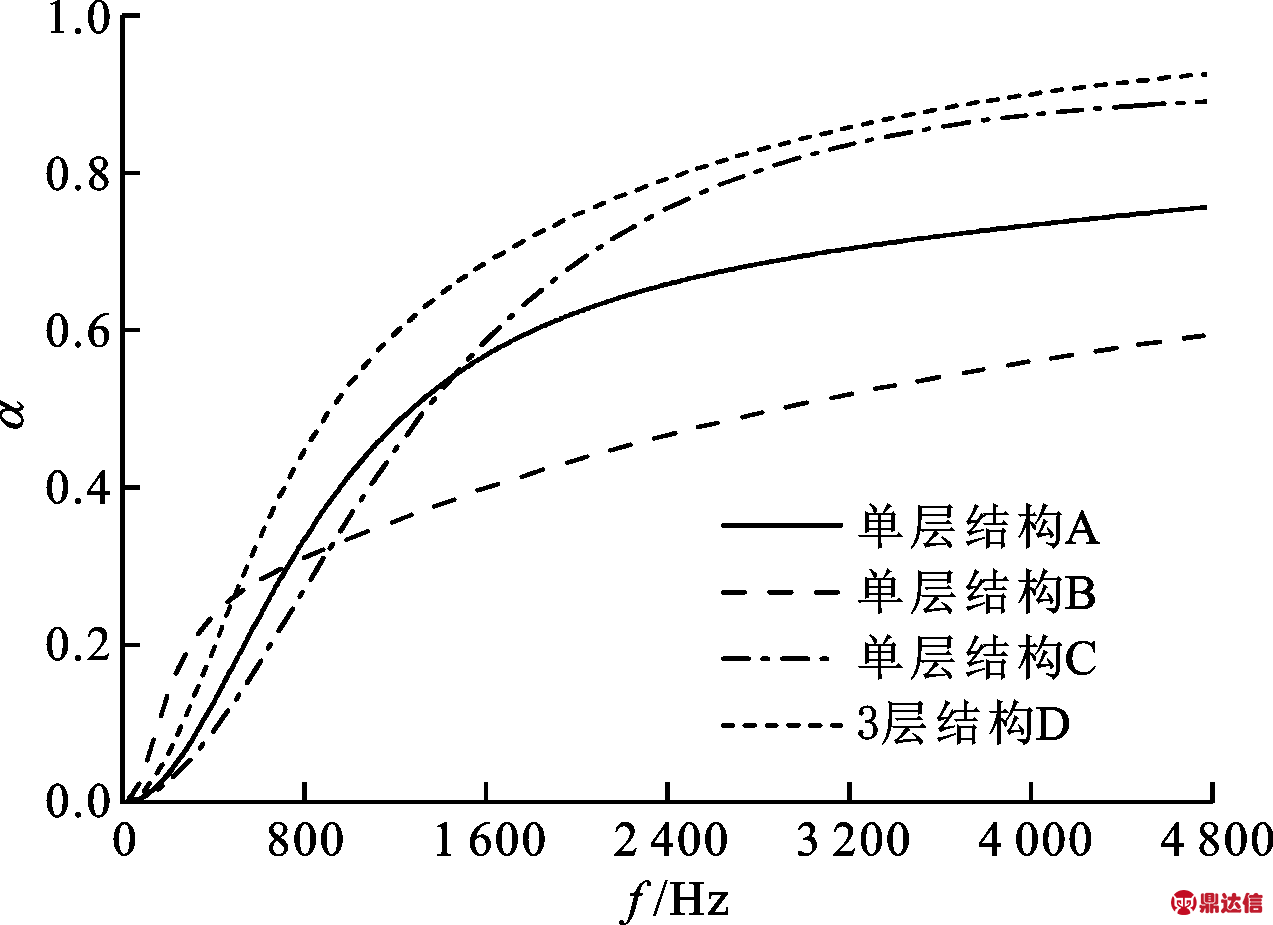
图11 吸声结构A、B、C和D的吸声系数计算结果的变化曲线
在实际应用中,吸声材料的质量、厚度均受特定环境及条件的限制,特别是在航空发动机的狭小空间内,因此吸声结构的优化设计尤为必要。所讨论的基本约束条件是材料总厚度固定,即其中hi为第i层材料的厚度。在此基础上,同时单频率、频率段优化多孔金属纤维的孔隙率和纤维丝直径的分布。
在单个频率下针对孔隙率布局和纤维丝直径分布进行优化,目标函数吸声系数α可写为[9]
maxf(d1,φ1,h1,…,dn,φn,hn)=
α(d1,φ1,h1,…,dn,φn,hn)
(30)
式中:α(d1,φ1,h1,…,dn,φn,hn)为多层梯度金属纤维板的吸声系数;di、φi、hi(i=1,2,…,n)分别为第i层金属纤维的直径、孔隙率和厚度;n为总层数。
在特定频率段内,同时针对纤维丝直径和孔隙率分布进行优化,目标函数为频率段内吸声系数的积分,即[9]
maxf(di,φ1,h1,…,dn,φn,hn)=
α(d1,φ1,h1,…,dn,φn,hn)df
(31)
式中:f1、f2分别为优化频率段的下限、上限。式(30)、(31)的约束条件为
di≥6.5×10-6, 0<φi<1, di<hi<hp,
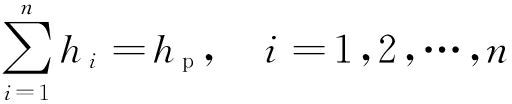
多孔金属纤维实际加工最小丝径为6.5 μm,孔隙率在0和1之间,每一层厚度要大于丝径而小于总厚度,结构总厚度固定。
为了同时优化孔隙率及纤维丝直径的分布,设定材料总厚度均为15 mm,选择优化的单频率为3 200 Hz,频率段为2 400~4 000 Hz。
本节涉及的多孔金属纤维材料结构的几何参数如表2所示,其中E为单层材料,F为线性分布结构,G、H为优化后的梯度结构。多孔金属纤维单层结构、线性布局结构及梯度优化结构吸声系数的变化曲线如图12所示。由图12可知:优化梯度结构G在3 200 Hz时的吸声效果明显好于单层结构E,线性分布孔隙率结构F的吸声效果也有明显提升,
表2 吸声结构E、F、G和H的参数表
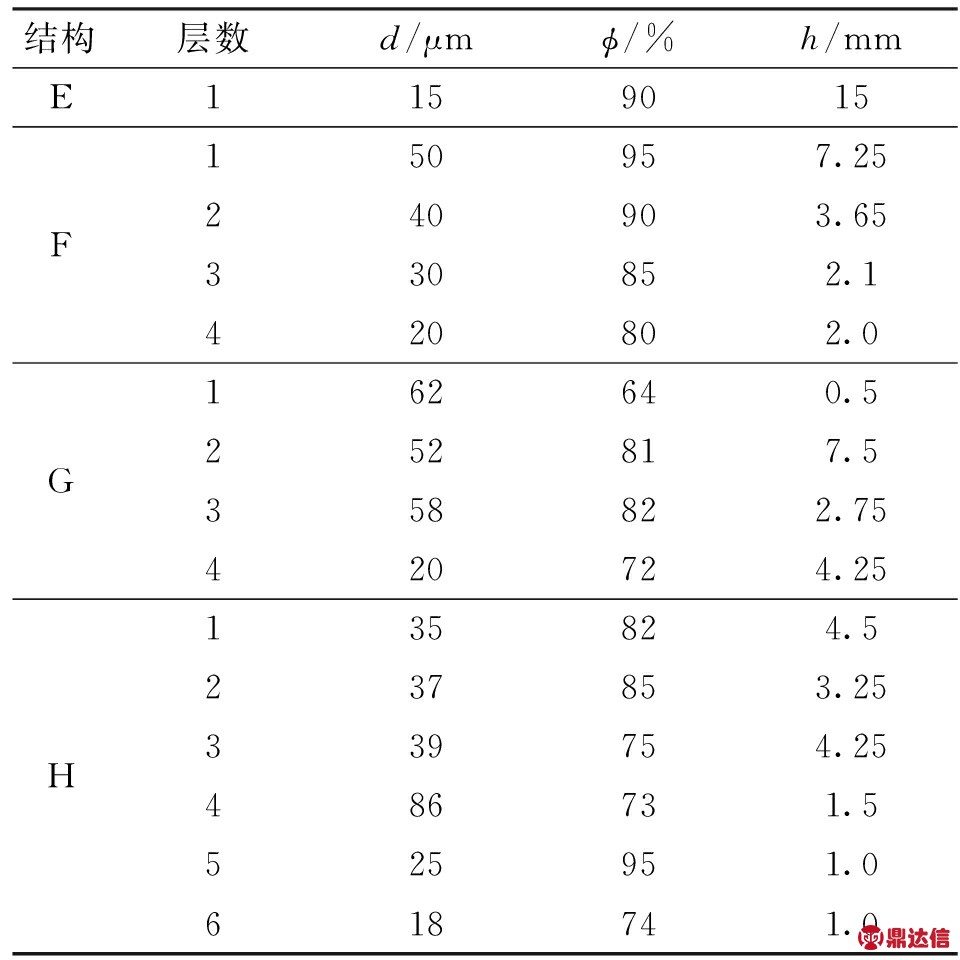
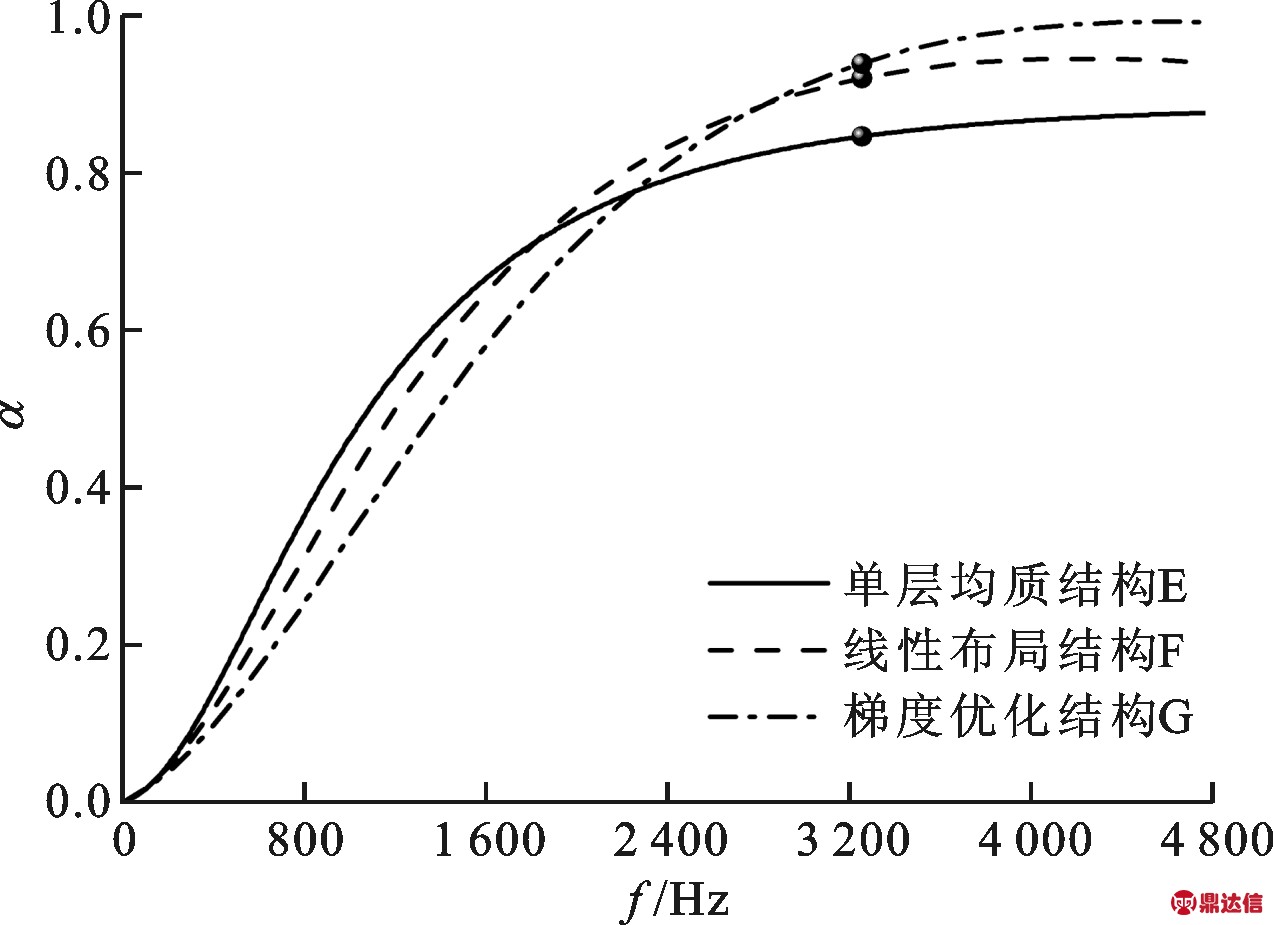
(a)单频率(3200 Hz)优化
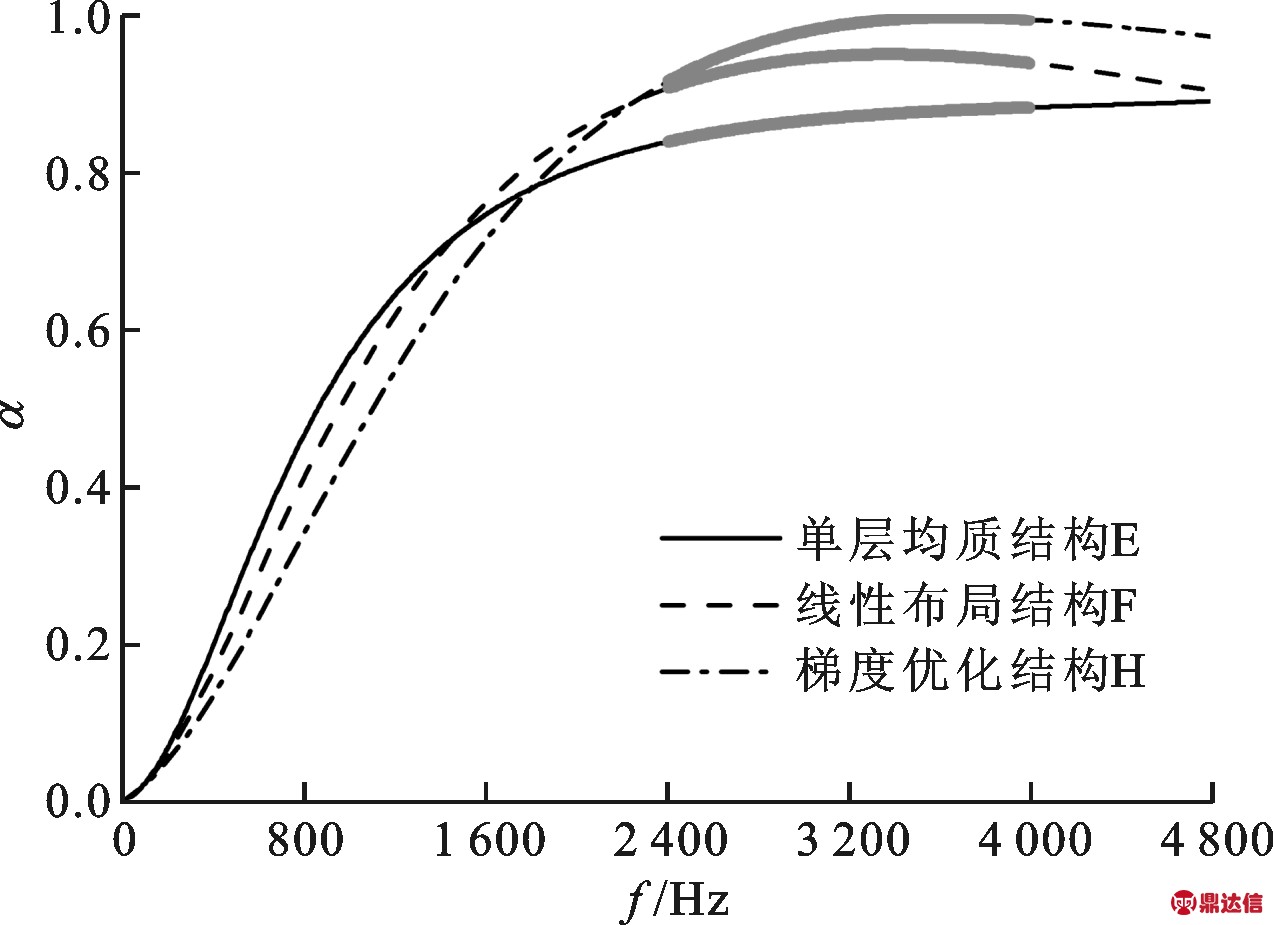
(b)宽频段(2 400~4 000 Hz)优化
图12 多孔金属纤维单层结构、线性布局结构及梯度优化结构吸声系数的变化曲线
但不如梯度优化结构G的吸声效果;在优化频段内,优化梯度结构H相较于未优化的单层结构E吸声效果有明显的提高,线性结构F也有一定的提高,但相比于多层梯度优化结构H,提升不明显。因此,优化多层梯度结构在单频及优化频段内都能够实现更好的吸声效果。
5 结 论
本文以高温环境下航空发动机内的吸声降噪为应用背景,以多孔金属纤维为研究对象,基于Johnson-Allard模型并考虑温度对各声学参数及空气热物性的影响,建立了适用于高温环境的吸声理论模型,并且通过实验测试验证了理论模型,并在此基础上建立了多层梯度结构高温吸声理论模型和优化设计策略,进而应用理论模型研究分析了高温环境下各参数对材料结构在中低频域范围内吸声性能的影响,主要结论如下:
(1)环境温度升高会导致多孔金属纤维吸声效果变差,在高温环境下,随着材料孔隙率的增大,材料吸声系数在低频段降低,而在中频段升高;
(2)孔隙率、纤维丝直径对材料吸声性能影响显著,受吸声曲线波动特性影响,在本文考虑的特定材料、温度及频率区间内,随着孔隙率或纤维丝直径的增大,材料吸声性能在低频段降低,而在中频段有所提高;
(3)多孔金属纤维多层梯度结构的吸声效果明显好于单层结构,且经过优化设计后,材料吸声效果在特定频率点以及特定频率段内都显著增强,这对实际应用中吸声结构各物理参数的优化选择有重要的指导意义。