摘要:生产工艺对丁腈橡胶粘合性能有一定的影响。本文用实验模拟生产过程,通过测试粘合强度和附胶率,研究了预热温度及硫化时间对丁腈橡胶粘合性能的影响。结果表明,预热温度在90℃以下对粘合性能没有影响,高于90℃时,粘合强度随温度升高而降低;硫化时间在4h以内不影响粘合,长于4h会对粘合强度产生影响。
关键字:粘合性能;预热温度;硫化时间;粘合强度;附胶率
近年来,橡胶热硫化粘合剂在橡胶工业及石油化工等领域有着广泛的应用,橡胶与金属之间化学结构和力学性能巨大的差异,使获得具有高强度的粘接有着很大的困难,随着技术的进步,一些高性能的粘合剂已经能够很好地将橡胶与金属粘接在一起。除了粘合剂本身,生产工艺对粘合效果也有较大的影响,不合理的生产工艺将会导致粘接失败。本文以实验为基础,分析了生产过程中主要的工艺条件对粘合性能的影响,并给出了合理的工艺参数范围,为实际生产过程中橡胶与金属的粘接工艺提供一定的参考。
1 实验部分
1.1 主要原材料及设备
丁腈橡胶混炼胶,用于制造采油单螺杆泵的丁腈橡胶混炼胶;Chemlok 205粘接剂(上海洛德化学有限公司产品);Chemlok 220粘接剂(上海洛德化学有限公司产品);丁酮(A.R.);二甲苯(A.R.)。
平板硫化机,50t;热老化烘箱;拉力试验机;喷砂机。
1.2 粘接试片的制作
按下面的步骤准备粘接实验试样:(1)按照GB/ T7760-2003《硫化橡胶或热塑性橡胶与硬质板材粘合强度的测定》的要求准备60×25×2的金属板(45#钢即可);(2)对金属板材进行喷砂处理,砂粒直径0.4~0.8mm,使其达到一定的粗糙度;(3)立即用丁酮对金属表面进行清洗,脱脂;(4)脱脂完成后,立即浸涂Chemlok 205底涂粘接剂,并完全干燥;干燥完全后,浸涂Chemlok220面涂粘接剂,并干燥;(5)按照GB/T7760-2003的要求,在平板硫化机上制作粘接实验试片;(6)在拉力试验机上对粘接试样进行剥离,测试其粘合强度和附胶率。
1.4 预热温度实验
在工业生产过程中,用于粘接的金属基体在粘接前往往需要预热处理。以制造采油单螺杆定子为例,其定子管内表面涂有粘接剂,中间橡胶从管两端注入,为了保证定子橡胶能够顺利注入,定子管在注胶前都需要预热,确定一个合理的预热温度对提高粘合强度有重要意义。
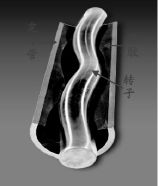
图1 螺杆泵剖面图
Fig.1 Sectional view of screw pump
实验用金属板模拟用于粘接的金属基体,将其按要求涂好粘接剂(包括底涂Chemlok205和面涂Chemlok220),并放在烘箱内进行预热,预热时间设置为达到均匀预热所需的50min,预热温度分别设置为60、90、120、150℃,完成预热后,立即在平板硫化机上制作粘接试样,每个温度等级制作粘接试样3片,将粘接试样在室温下放置16h以上,用拉力试验机测试其粘合强度,并检查其附胶率。试验结果见表1。
表1 不同预热温度下的粘合强度和附胶率
Tab.1 Adhesive strength and adhesive rate under different preheat temperatures
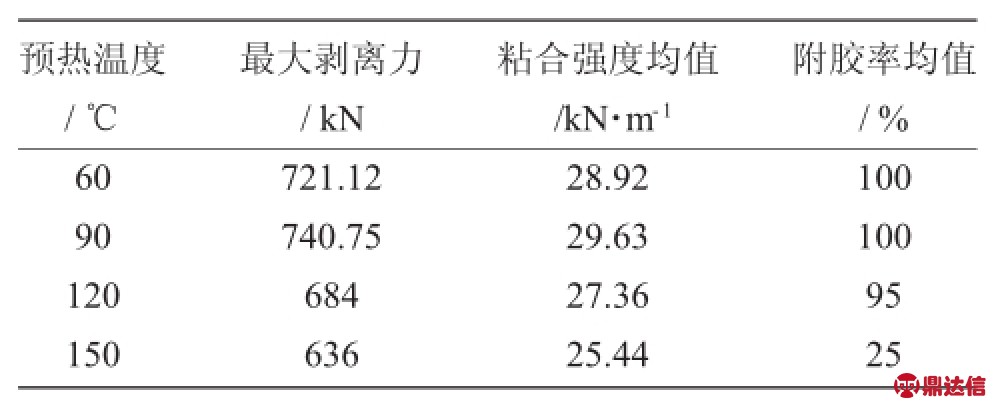
1.5 硫化时间实验
在橡胶制品的加工过程中,硫化是必须的工序,由于橡胶的配方不同以及橡胶制品的厚度不同,硫化时间往往不同,硫化速度慢的厚橡胶制品比硫化速度快的薄橡胶制品需要更长的硫化时间。以采油单螺杆泵的硫化为例,其定子橡胶由于配方不同和橡胶厚度的不同,硫化时间从1h到3h不等。橡胶硫化通常在150℃以上的温度下进行,在此温度下,不同的硫化时间是否对粘合强度有影响也是需要注意的问题。实验以生产采油螺杆泵的丁腈橡胶为基础,在150℃的温度下按照要求制作标准试样,不同试样的硫化时间不同,分别为2、3、4、5和6h。将粘接试片在室温下放置16h以上,用拉力试验机测试其粘合强度,并检查其附胶率。试验结果见表2。
表2 不同硫化时间下的粘合强度和附胶率
Tab.2 Adhesive strength and adhesive rate under different curing time
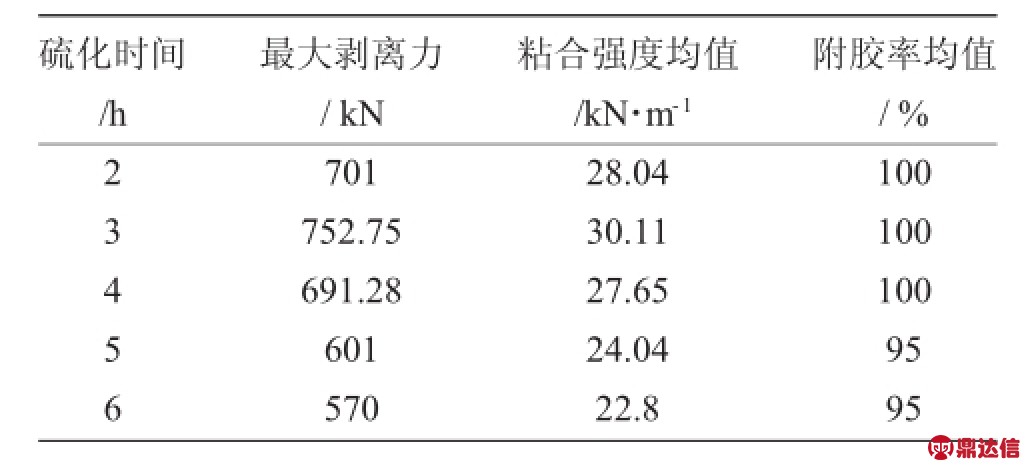
2 结果与讨论
2.1 预热温度对粘合性能的影响
从上面的实验得出,不同的预热温度对粘合强度和附胶率有一定的影响,它们之间的影响关系见图2。
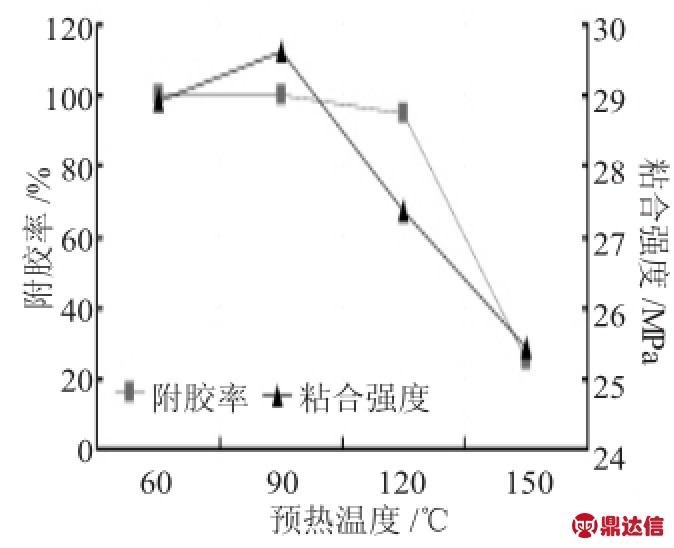
图2 预热温度对粘合的影响
Fig.2 Effect of preheat temperature on adhesion
从图2看,在低于90℃的温度下预热,附胶率保持在100%以上,试样剥离时都是从橡胶一侧裂开,橡胶与金属之间的粘合剂层的抗拉强度大于橡胶材料本身的强度,达到理想的粘合效果,预热没有对粘合造成影响。当预热温度超过90℃以后,无论是粘合强度还是附胶率都出现下降趋势,附胶率低于100%,试样剥离时,有一小部分从面涂粘合剂层与橡胶之间裂开(橡胶剥离实验时,主要有以下几种破坏方式:R-橡胶破坏;RC-橡胶与粘合剂之间剥离;CP-粘合剂间破坏;PS-粘合剂与基体剥离),这表明橡胶与粘合剂层之间的粘合强度已经低于橡胶材料自身的强度,在受到外力作用下首先发生破坏,预热温度已经开始对粘合产生影响,随着温度的进一步升高,这种影响作用愈发明显,到150℃时附胶率只有25%,已经严重影响橡胶与金属的粘合。伴随着附胶率的降低,橡胶与金属之间的粘合强度也随之降低。
2.2 硫化时间对粘合性能的影响
从实验来看,不同的硫化时间对粘合强度和附胶率也有一定的影响,它们之间的影响关系见图3。
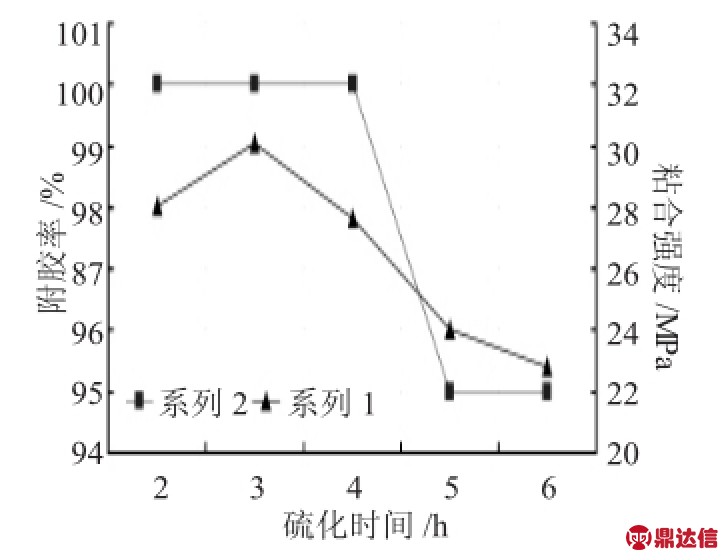
图3 硫化时间对粘合的影响
Fig.3 Effect of curing time on adhesion
随着硫化时间的延长,附胶率开始时稳定在100%,当硫化时间超过4h后,附胶率有一个下降,粘合强度随硫化时间的延长,先上升后下降,最大的强度点出现在3h。分析原因,在4h以前,附胶率能达到100%,粘合强度大于橡胶材料自身的强度,硫化时间对粘合性能影响不大,当硫化时间超过4h时,粘合剂层出现老化,附胶率降低,破坏形式是底涂粘合剂层与金属基体之间剥离。粘合强度在附胶率100%时主要体现的是橡胶材料自身的强度,粘合强度的升高主要是由于橡胶在进一步加热过程中,交联密度进一步提高所致;当附胶率低于100%时,粘合强度体现橡胶与金属之间的附着力,随着附胶率的下降,粘合强度又开始出现降低。
3 结论
实验来看,用Chemlok205作底涂粘合剂,Chemlok220作面涂粘合剂粘合丁腈橡胶与金属时,预热温度及硫化时间在一定范围内对粘合性能有影响,具体影响如下:
(1)低于90℃时,预热温度对橡胶与金属之间的粘合性能没有影响,预热温度高于90℃时,预热温度对橡胶与金属之间的粘合性能有一定影响,随着温度升高,影响作用越来越显著,破坏形式主要是面涂与橡胶之间剥离。因此,在设计预热工艺时,预热温度尽量不要高于90℃,以免影响粘合性能。
(2)硫化时间在短于4h时,对粘合性能没有影响,长于4h时,对粘合性能有一定的影响,主要破坏形式是底涂粘合剂与金属基体之间剥离,因此,在设计橡胶配方和硫化工艺,特别是大型橡胶件时,一定要考虑硫化时间对粘合的影响,硫化时间尽量不要超过4h。
参考文献:
[1]王勇,瞿连辉.橡胶/金属硫化粘接失效原因分析及对策[J].特种橡胶制品,2008,29(4):30-33.
[2]刘锦春,姜尚奇.橡胶与金属粘接性能的影响因素[J].粘接,2003,24(5):10-12.
[3]江畹兰.橡胶与金属或其他基材粘接时其表面处理方法[J].世界橡胶工业,2005,32(2):34-35.
[4]贾剑珉.对混炼胶粘合问题的再认识(一)[J].世界橡胶工业,2006,(6):26-29.
安监总局筹建专家查隐患制度
日前,国家安监总局党组书记、局长杨栋梁在安全生产调度会上提出,要建立安全生产专家查隐患促整改工作机制,用“铁制度”力避安全生产大检查形式主义。
杨栋梁说,安全管理工作具有很强的专业性。安全隐患往往具有隐蔽性、复杂性、反复性,外行查不出隐患,内行不深入同样查不出隐患。形式主义的安全生产大检查外表轰轰烈烈,却只是蜻蜓点水、雨过地皮湿,不仅查不出隐患、劳民伤财,而且还会助长企业的侥幸、应付心理,埋下长期的事故隐患。
据杨栋梁介绍,筹建专家查隐患工作机制,必须首先建立专家库。日前国家安监总局刚刚组建技术委员会,各地各部门各行业也要逐步建立一支业务过硬、责任心强的专家队伍。今后由国务院安委办或安监总局组织的安全督查、执法检查和暗查暗访,都将依靠专家队伍,使专家检查与政府执法有机结合。
专家查隐患制度也将成为企业落实安全生产责任的重要内容。杨栋梁提出,企业要定期组织内部和外部专家开展安全隐患排查会诊。特别是高危行业领域的生产经营企业,每年都应当邀请专家对本企业的安全生产状况进行集中会诊,全面体检。企业必须根据专家意见认真整改,并建立严格的隐患整改责任制,向属地安监部门备案有关情况,强化政府监督落实。
此外,国家安监总局还将探索发挥专业中介组织作用、第三方专家团队查隐患模式。