摘 要:在火箭发动机壳体等关键部件中应用广泛的D406A超高强度钢是典型的难加工材料,尤其是该材料的内螺纹加工,对加工刀具及数控加工工艺提出了很高的要求。本文选用高性能TiAlN和TiN涂层刀具,采用内螺纹铣削加工方式及优化的走刀工艺,实现了D406A超高强度钢的高效、高质量内螺纹铣削。研究结果表明,TiAlN和TiN涂层材料硬度显著高于硬质合金材料,在切削加工润滑条件下与D406A超高强度钢对摩的摩擦系数仅为0.09和0.11,略低于硬质合金材料 (0.12),因此两类涂层刀具在实际切削加工应用中具有明显优于未涂层刀具的加工寿命和加工质量。采用内螺纹铣削加工方式及优化的走刀工艺,可显著提高加工效率,获得较好的表面质量,缓解对刀具的冲击,避免接刀痕的出现。
关键词:超高强度钢;内螺纹铣削;涂层刀具;走刀工艺
1 引言
超高强度钢一般是指屈服强度在1370 MPa (140 kgf/mm2) 以上,抗拉强度在1620MPa (165 kgf/mm2)以上的合金钢。超高强度钢一般可按照其合金化程度和显微组织区分为低合金中碳马氏体强化超高强度钢、中合金中碳二次沉淀硬化型超高强度钢、高合金中碳Ni-Co型超高强度钢、超低碳马氏体时效硬化型超高强度钢、半奥氏体沉淀硬化型不锈钢等。
406、406A、D6AC超高强度钢等均是典型的低合金超高强度钢,在工业领域有着广阔的应用前景,尤其是自上世纪50年代以来,在固体火箭发动机壳体上得到了广泛应用。相比之下,D406A超高强度钢具有更加优异的综合性能,其经热处理强化后的硬度高达48~52HRC,抗拉强度大于1620MPa,作为固体火箭发动机壳体可以有效保证壳体构件的高强度、轻重量和耐高压性能,应用于军工领域可为导弹武器提供较长的射程及较高的速度,从而提高其打击范围和突防能力[1]。
D406A超高强度钢优异的综合性能决定其具有极佳的应用效果,但是也表明其为典型的难加工材料,对其进行切削加工,尤其是铣削、钻削和螺纹加工非常困难,其中尤以螺纹加工为甚。机械加工中常用的螺纹加工方法包括攻丝、冷挤压成形、螺纹车削和螺纹铣削等[2]。随着数控机床技术的发展,利用数控机床的螺纹插补功能进行螺纹加工的螺纹铣削工艺逐渐成为机械加工中比较流行的一种螺纹加工方法,相比于其他方法,螺纹铣削具有以下典型优点:(1) 同一把螺纹铣刀可以加工螺距相同,不同直径、旋向、精度的内外螺纹;(2) 加工效率高,采用高速切削和高速进给可以有效节省加工时间;(3) 可以获得良好的表面质量;(4) 消耗功率小,应用小型机床也可以加工较大的螺纹;(5) 切屑较短,可有效缓解在攻丝加工中经常出现的因为长切屑缠刀而导致的断刀现象,即使刀具折断或破损也不会影响零件质量,刀具破损的部分可以很容易地从工件中取出;(6) 没有无效牙长,适用于盲孔到底的螺纹加工;(7) 对于难加工材料和淬火材料,选择螺纹铣削是最佳的解决方案[3]。综上所述,针对D406A超高强度钢的内螺纹加工问题,首选内螺纹铣削工艺进行加工。
采用传统的高速钢或硬质合金刀具进行 D406A超高强度钢内螺纹铣削加工过程中面临的主要问题是刀具磨损较快、加工质量不稳定,刀具涂层技术是随着机械加工工艺的发展逐渐兴起的一种刀具表面改性及强化技术[4],其中硬质及超硬涂层的选用可有效提高刀具表面硬度,提升刀具耐磨损性能,延长刀具使用寿命,部分涂层还具有更低的摩擦系数和优异的摩擦学特性,可以缓解切削加工过程中刀具与工件材料的相对摩擦磨损,改善加工表面的质量[5]。对于超高强度钢加工而言,含有 Ti、Al、Si等金属元素的一元或多元碳化物涂层是常用的刀具表面涂层材料。
本文选用高性能TiAlN和TiN涂层硬质合金内螺纹铣刀作为加工刀具,首先对刀具涂层材料进行了检测对比,然后对内螺纹铣削的走刀工艺进行了优化设计,据此完成了D406A超高强度钢的高效、高质量内螺纹铣削。
2 螺纹铣刀涂层选择
螺纹铣刀铣削时刀具受到的径向分力特别大,所以螺纹铣削适用于短而粗的孔,螺纹孔深径比一般不超过3,选用的螺纹铣刀的直径也应当尽量大。一般而言,硬质合金材料的刚性及硬度均要优于高速钢,因此加工小孔径螺纹时多选用整体式硬质合金螺纹铣刀,而在硬质合金螺纹铣刀表面涂镀硬质或超硬涂层制备而成的涂层铣刀兼具硬质合金和表面涂层的优点,在超高强度钢螺纹铣削加工中有着越来越广的应用前景。
本研究选取的市售TiAlN和TiN涂层硬质合金内螺纹铣刀典型实物图如图1所示,其中刀刃部分为金黄色的螺纹铣刀是Φ 12 mm的TiN涂层螺纹铣刀,刀刃部分为紫灰色的螺纹铣刀是Φ 10 mm的TiAlN涂层螺纹铣刀,实际内螺纹铣削加工过程中针对实际的工况需求制备了表面沉积两种不同涂层的、不同规格的涂层螺纹铣刀。
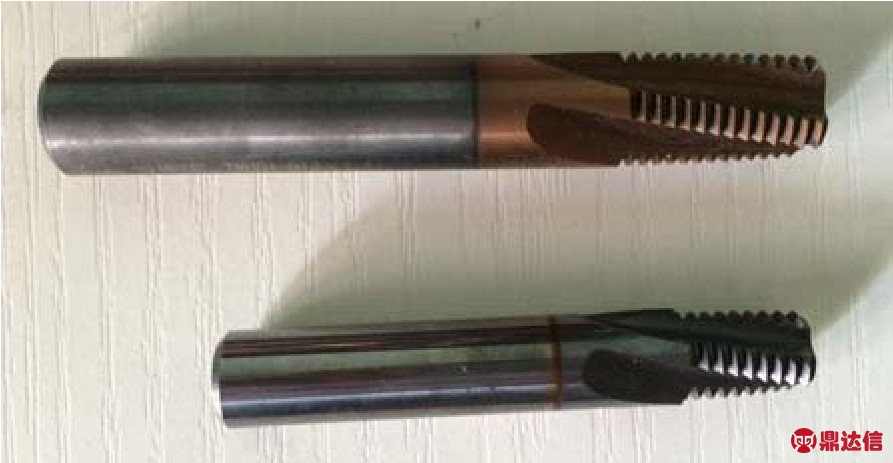
图1 TiAlN和TiN涂层内螺纹铣刀实物图
应用蔡司公司的ULTRA55场发射扫描电子显微镜(Field Emission Scanning Electron Microscopy, FESEM)观测刀具涂层的表面形貌,检测结果如图2所示,可见在TiAlN和TiN涂层表面均存在明显的晶粒状形貌,采用FESEM内集成的能量散射谱仪(Energy Dispersive Spectrometer, EDS)针对图2中所示的采样点进行检测可得到涂层的元素成分构成,如表1所述,TiN涂层中的氮原子和碳原子个数比约为0.59,当该比值小于1时,说明非金属的亚晶格中存在有高浓度的空位,该类TiN涂层的硬度相对较高;TiAlN涂层中除了含有Ti、Al和N元素外,还有少量的Si元素,在TiAlN涂层中加入Si可以起到细化晶粒的作用,提高涂层的硬度和抗氧化性,此外还会形成非晶态的Si3N4,提高TiAlN的分解温度,提高涂层的高温硬度。
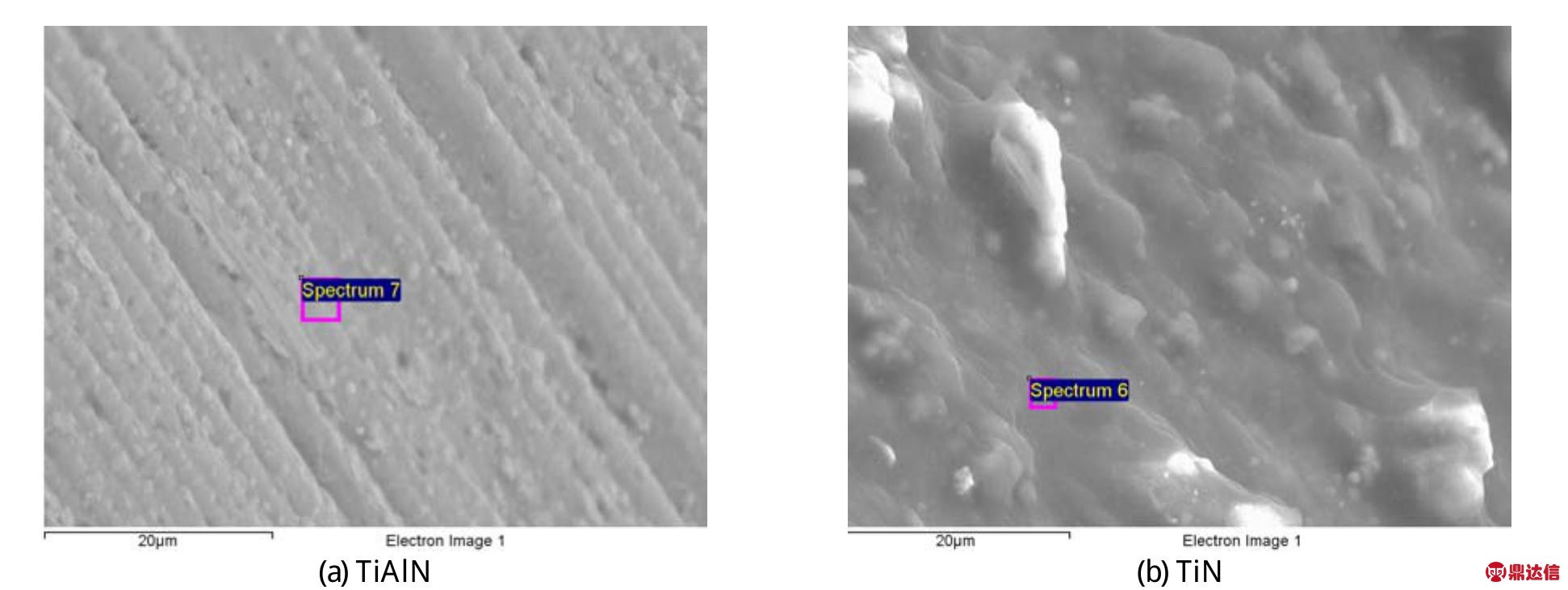
图2 TiAlN和TiN涂层内螺纹铣刀的表面形貌
本研究还选取了具有相同特性的TiAlN和TiN涂层硬质合金平片样品以及未涂层硬质合金平片样品进行硬度和摩擦系数的测定,硬度测量采用的是维氏硬度计,摩擦系数测量采用的是球盘旋转式标准摩擦磨损试验机,上试样为D406A超高强度钢制成的销,下试样为TiAlN和TiN涂层硬质合金平片样品以及未涂层硬质合金平片样品,加载载荷为6 N,相对速度为0.5 m/s,润滑条件为切削加工冷却液润滑。试验测定的材料特性参数参见表2,可见两种硬质涂层的硬度都要高于常规硬质合金材料,在冷却液润滑条件下与D406A超高强度钢对摩的摩擦系数要略小于硬质合金,二者相比,TiAlN涂层的硬度更高,摩擦系数更小,具有更优异的机械性能。
表1 TiAlN和TiN涂层的元素构成

表2 试验测定的材料特性参数

3 内螺纹铣削走刀路径优化
螺纹铣削加工是通过刀具的自转与机床的螺旋插补相互结合实现的,是利用数控机床的三轴联动功能结合G02或G03圆弧插补指令,螺纹铣刀绕螺纹轴线作X、Y方向圆弧插补运动走螺旋曲线,同时轴向方向(Z或W)作直线运动来完成螺纹加工。
本研究基于常用的数控镗铣床,针对D406A超高强度钢的内螺纹铣削优化设计了通用的走刀路径工艺方案,优化工艺方案示意图如图3所示,其中D1为螺纹大径,D3为螺纹小径,Dc为刀具直径,A=(D1-Dc)/2,ae为径向切削深度,ae=(D12-D32)/4(D1-Dc),ae/Dc%为刀体啮合百分数,一般不应超过40%,Dc与D3越接近,啮合百分数越大,速度要降低,Dc一般为D3的80%。

图3 D406A超高强度钢内螺纹铣削走刀路径优化工艺方案
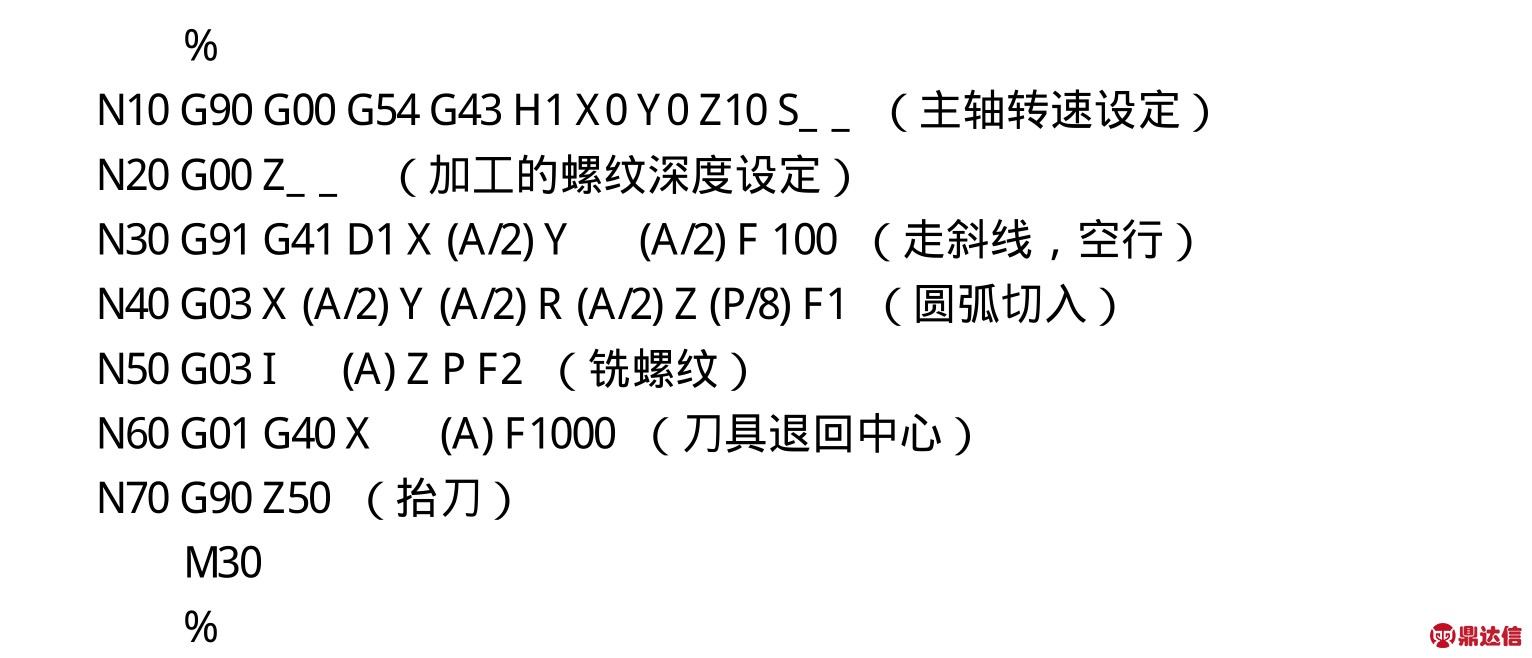
基于上述走刀路径进行刀具中心编程思路如下:程序中的F2指的是刀具中心轨迹、即图中双点划线的移动速度,F2与刀具切削的进给速度vf的关系为:F2/vf=2A/D1=(D1-Dc)/D1;vf=nf (mm/min);螺纹铣刀切削线速度vc=nπDc/1000 (m/min);n为转速,f为每转进给量;圆弧切入速度F1一般取F2的30%~50%;P为螺距。
该优化工艺方案中选用圆弧切入、切出,可以有效避免直线切入对于刀具的冲击,切入、切出非常平稳,振动较小,为了避免加工的螺纹存在接刀痕,切入圆弧应当与螺纹插补的整圆相切。
内螺纹铣削加工过程涉及铣削方向的选择问题,一般而言,顺铣的加工质量好,切削力较小,排屑较好,在机床丝杠无间隙、工件表面无黑皮和硬壳的情况下优选顺铣,本试验及加工中所采用的数控镗铣床采用的是滚珠丝杠,因此选用顺铣的铣削方向,如上述程序中,铣削右牙内螺纹,采用的是G03逆时针旋转圆弧插补指令。
4 切削试验及结果对比
D406A超高强度钢内螺纹铣削加工过程中的切削力较大,因此切削系统的整体刚性对于刀具振动和刀具寿命也有着显著影响,为了保证切削系统的刚性,在进行切削试验及实际加工时应当考虑如下因素:刀具装夹时,尽可能使刀具悬伸最短;尽可能减少刀具和主轴的跳动;保证夹具具有足够的刚性;尽可能不采用中心架装夹工件;保证刀具及工件装夹牢固可靠。
带涂层的整体式硬质合金螺纹铣刀是典型的多刃刀具,因此装夹时要注意装夹精度,使用高精度、夹持力大的刀柄,可以显著改善加工质量,提高刀具使用寿命。
D406A超高强度钢内螺纹铣削加工过程中的切削热也比较大,因此需要选用冷却效果好的水基切削液,并连续充分浇注,切削液兼具冷却和润滑的作用,尤其是对小孔径内螺纹加工而言,半封闭式的加工环境对于冷却提出了更高的要求,在条件允许的情况下,最好是采用内冷的方式,可以直达切削区域,并且可以强制排屑。
对比切削试验在TK6920数控镗铣床上进行,选用的刀具为Φ 12 mm的TiAlN和TiN涂层硬质合金内螺纹铣刀及未涂层硬质合金内螺纹铣刀,螺纹铣刀螺距为1.5 mm,用于加工螺纹大径D1=14 mm,螺纹小径D3=12.5 mm的内螺纹,具体采用的切削参数及程序如下:主轴转速 n=1200 r/min,加工的螺纹深度为14mm,刀具中心轨迹移动速度F2=300mm/min,圆弧切入速度F1=150mm/min,P= 1.5。
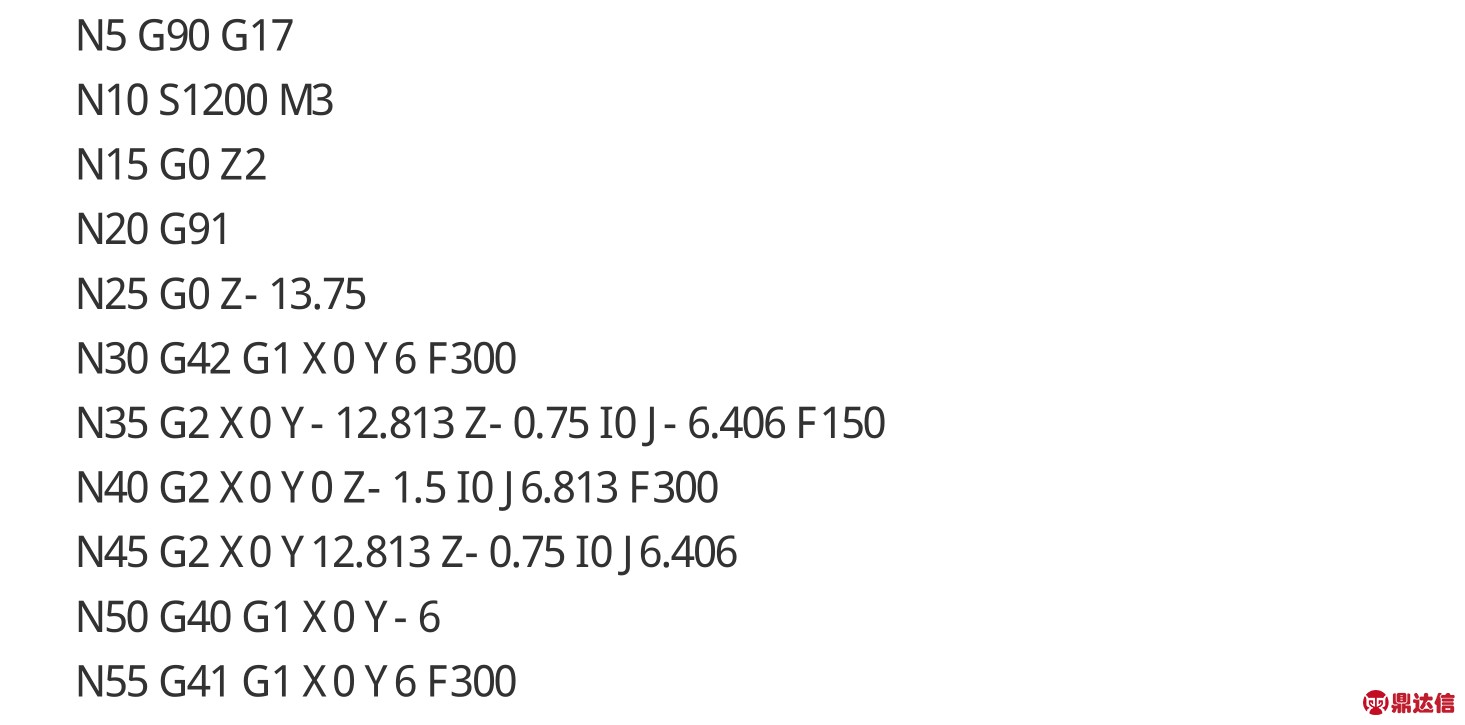
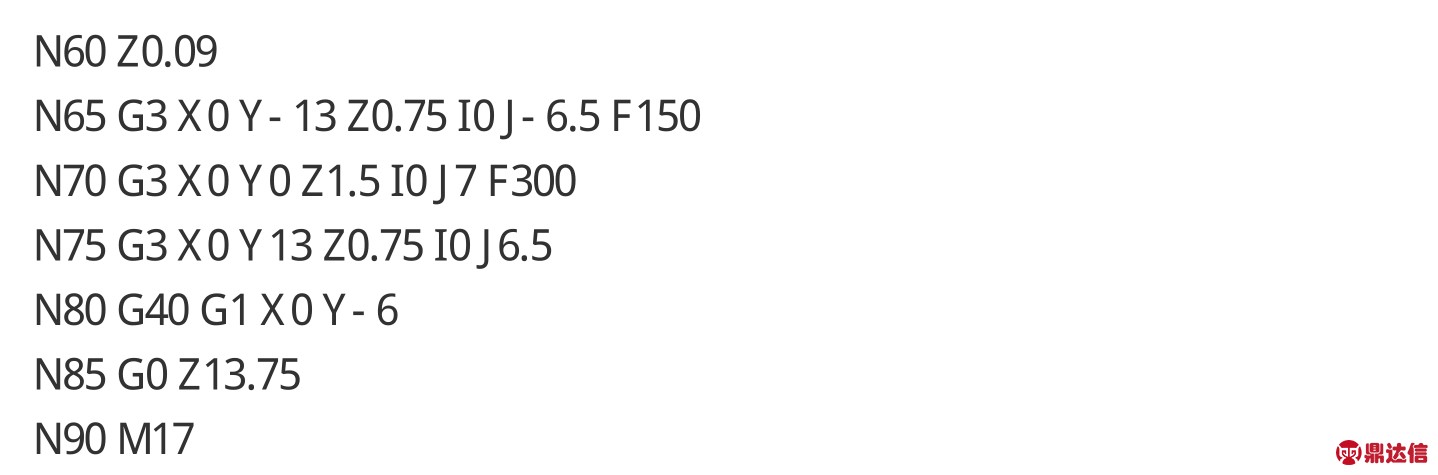
内螺纹铣削对比试验结果表明,由于具有较高的表面硬度,TiAlN和TiN涂层硬质合金内螺纹铣刀在实际切削加工应用中表现出明显优于未涂层刀具的刀具寿命,其中TiAlN涂层铣刀的刀具寿命最长,甚至可达到未涂层硬质合金刀具的2倍;由于较小的摩擦系数和良好的摩擦学特性,采用TiAlN和TiN涂层硬质合金内螺纹铣刀加工获得的内螺纹表面还具有较高的表面质量。此外,采用内螺纹铣削加工方式及优化的走刀工艺,确实可以显著提高加工效率,缓解铣削加工对于刀具的冲击作用,试验过程中没有接刀痕出现。
5 结论
TiAlN和TiN涂层的硬度高于硬质合金,在冷却液润滑条件下与D406A超高强度钢对摩的摩擦系数略小于硬质合金,因此用作螺纹铣刀表面保护涂层可提高刀具寿命,改善加工质量。
基于内螺纹铣削的加工方式,采用优化的走刀工艺,合理选择铣削方向、切削参数及润滑方式,可以显著提高加工效率,获得较好的表面质量,缓解对刀具的冲击,避免接刀痕的出现。