摘 要:旋压成型是目前内螺纹铜管加工的一种主要方法,通过对无缝内螺纹铜管加工过程中的受力分析,借鉴金龙集团在实际生产中的经验,同时参考理论公式,总结出部分影响大螺旋角内螺纹铜管的成型因素,供设计内螺纹成型工艺时参考。
关键词:内螺纹;螺旋角;旋压
内螺纹铜管是目前制冷用空调领域应用最广泛的一种热传导管,之前使用的是光面铜管。为了提高热传导效率,20世纪 70年代末,日本率先将内螺纹铜管应用到空调行业,目前,空调换热器中内螺纹铜管的占用量接近 80%,并且有不断增长的趋势。
内螺纹铜管的齿形有很多种,有普通齿、瘦高齿、交叉齿、断续齿、M型齿、高低齿等,真正产业化的也就前三种,内螺纹齿形螺旋角多为 15°至 25°,可以说齿形方面的开发已经走向了极致。但近年来,高效、节能减排成为制冷领域的一个方向,超过 30°螺旋角的内螺纹铜管开始越来越多的应用到空调上。尤其是日本,30°螺旋角以下的内螺纹铜管被认为是低附加值产品。
1 螺纹芯头的设计
目前行星钢球旋压法是生产无缝内螺纹铜管的主要方法,其原理是铜管在钢球的旋压力作用下,内螺纹芯头在铜管内壁上旋压出螺纹。内螺纹芯头的尺寸有外径、齿深、螺旋角、齿顶角、齿条数、齿槽宽,尺寸要求很严格。外径计算公式
式中:d—螺纹芯头外径,mm;
d0—旋压后铜管外径,mm;
t—铜管底壁厚,mm。
考虑到满球旋压过程中钢球之间存在间隙,计算外径比实际外径略小,一般在 0.02~0.05mm左右。
螺纹芯头螺旋角的计算公式:
式中:γ—螺纹芯头的螺旋角,(°);
β—成品内螺纹铜管的螺旋角,(°);
dc—成品内螺纹铜管的外径,mm;
λ—从旋压到定径后的延伸系数。
公式 (1-2)可以演变为:
从公式(1-2)和(1-3)中可以看出,在其它参数一定的条件下,tgβ正比于 tgγ,而在实际生产中,γ越大,成型越困难,拉伸速度越低,因而并不主张通过提高γ来增加β,经验告诉我们,当γ>45°时,内螺纹铜管的齿形严重不良。因此,在设计螺纹芯头时,螺旋角小于 45°即可。增大成品内螺纹管材的螺旋角可以通过减小螺纹芯头的外径,选择合适的旋压工艺来实现。
2 内螺纹旋压过程中的受力情况
内螺纹成型过程示意图如图 1,螺纹芯头受力图见图2。
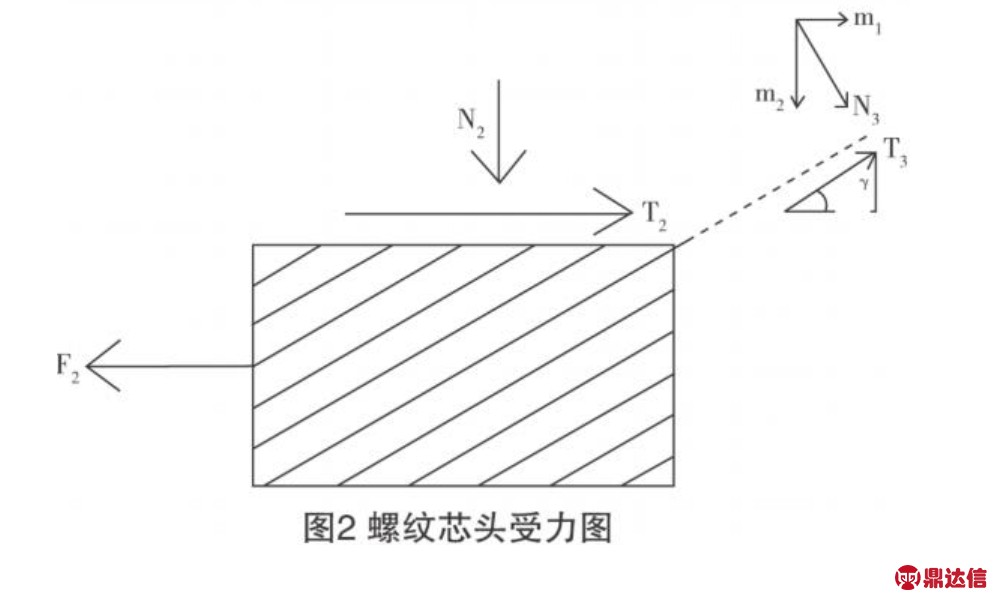


式中:F2—螺纹芯头旋压过程中轴向克服力
T2—螺纹芯头旋压过程中表面摩擦力
N3—螺纹芯头旋压过程中金属沿螺旋线方向对齿槽挤压力
T3—螺纹芯头旋压过程中槽底沿螺旋线方向摩擦力

μ—金属与齿槽内的摩擦系数
公式 (2-3)的计算相当复杂,从公式很难看出∑F2受螺旋角γ的影响趋势,但在∑T2保持恒定的情况下,取γ=0°、30°、45°分别代入计算∑N3(μcosγ+ sinγ)得出:
γ=0°时,∑N3(μcosγ+sinγ)=∑N3μ;
γ=30°时,
γ=45°时,μ)
摩擦系数μ<1,从以上计算可以看出,在 0°<γ <45范围内,随着γ的增加,∑F2有增加的趋势。因此,增大成品内螺纹管材的螺旋角除了减小螺纹芯头的外径外,尽可能在 0°<γ<45°范围内,选择较小的螺旋角。
3 钢球直径对成型过程的影响
旋压环中钢球在高速旋转时就相当于一个压缩区为圆弧形的拉伸模。目前国内最常用的内螺纹成型工艺中钢球数量是五球和六球,也有部分管型采用四球工艺,而日本通常是四球和五球,甚至有三球工艺。一般情况下,铜管外径减径量越大,旋压过程中往齿槽内部的挤压力也就越大,所需钢球的直径就越大。
满球情况下,钢球和旋压环直径理论计算公式如下:

公式(3-2)中,
四球工艺时,α=45°;
五球工艺时,α=36°;
六球工艺时,α=30°。
公式 (3-1)和 (3-2)中,
d1—旋压环内径,mm;
d2—钢球直径,mm;
d3—旋压后铜管直径,mm;
k—钢球之间的间隙,一般取 0.02~0.05mm。
以金龙集团的新产品 9.52×0.30-35°为例:该产品是大螺旋角产品,主要应用于制冷行业冷凝器,选择生产工艺时用的是五满球,钢球直径 15.08mm,旋压环内径 40.78mm,产品质量良好。若用传统的六满球工艺,球径 11.1125mm,旋压环内径 33.40mm,旋压后铜管的外径大,因此在设计螺纹芯头时,就要增加螺纹芯头的螺旋角,给生产造成一定的困难,容易使产品齿形缺损,严重不良。
从 2008年至 2009年金龙集团开发了多种规格的大螺旋角产品,包括 7mm、7.94mm以及 9.52mm系列,在选择生产工艺时尽可能采用大球工艺,日本同行业的经验告诉我们,减小螺纹芯头外径,增加钢球直径是提高产品螺旋角的有效方法。
4 电机转速的影响
电机转速对管材螺旋角的影响是和拉拔速度有一定关系的。电机转速和拉拔速度的比值称之为旋模比,螺旋角小于 30°的管材在内螺纹成型时一般选用 400~600的旋模比,大于 30°螺旋角的管材旋模比要相应提高。旋模比的提高不仅对提高管材的螺旋角有好处,还可以增加内螺纹的齿高。目前国内内螺纹成型用的高速电机转速多在 35000转/分左右,也有 24000转/分,可依据管型选择不同的高速电机,但要生产小管径、大螺旋角的内螺纹产品,上述二种电机转速并不能满足生产需要,目前日本多用 42000转/分的电机生产高难度的内螺纹铜管。
5 结论
通过对以上影响大螺旋角内螺纹成型因素的分析以及金龙集团在开发大螺旋角内螺纹管材方面的经验可以得出以下结论:
⑴缩小成品管材外径与旋压后铜管外径值之差,减小螺纹芯头的外径尺寸;
⑵螺纹芯头的螺旋角在 0°~45°范围内,尽量靠近成品管材螺旋角;
⑶较大的钢球直径利于大螺旋角内螺纹成型;
⑷相对于普通螺旋角的内螺纹管材,设计拉拔工艺时在高速电机转速范围内适当地提高旋模比。