摘要:结合圆柱状摄像机支座塑件内、外壁不同特征的脱模需要,设计了一种四板式三次开模、三次顶出冷流道注塑模具。针对塑件外壁侧凹特征,应用位于动模一侧的先抽芯杆驱动定模滑块进行先抽芯脱模;针对外壁采用哈弗滑块进行抽芯脱模。针对内壁的双层内螺纹的脱模,应用了一种复合式内收式滑块机构进行脱模,通过模板的开启及顶出板的顶出,分别驱动机构的中央型芯及2组共6个滑块分两次来实现内螺纹的内收抽芯脱模,6个滑块的成型部分拼合成塑件内螺纹的整环螺纹,其抽芯动作分为三步,最终通过第三次顶出板推动动模推板将塑件从上型芯上完全顶出脱模。
关键词:内螺纹;哈弗滑块;内收抽芯;模具结构;脱模
对于圆柱状塑件且其一端增设有非对称型结构特征的塑件,在设计注塑模具时,塑件外表的脱模方式一般采用哈弗滑块进行侧抽芯脱模[1–2],但外壁的中央部位会留下两半哈弗滑块碰合的分型痕迹,即熔融塑料容易在两半哈弗滑块拼合的部位漏胶,消除的办法是提高滑块的碰合精度和提高对滑块的锁紧强度[3–5]。另外,针对圆柱状塑件内壁上内螺纹特征的脱模[6–9],有以下几种方式可以实施,其一是常见的内螺纹型芯旋出脱模方式,其二是分滑块内收脱模方式,其三是滑块内收+斜顶顶出脱模方式。在塑件内无法应用螺纹型芯旋出方式脱模时,一般依据塑件内螺纹的实际情况采用第2,3种方式来进行脱模。对于需要进行定模先抽芯特征的脱模,一般在多板模结构中,利用先打开的模板来驱动其上的先抽芯驱动件实施对侧型芯成型件的抽芯,保证塑件从型腔中脱出之前,完成其侧凹特征的先行脱模[10–12]。模具结构设计的复杂性跟塑件结构的复杂性息息相关,当塑件上各种需采用侧向抽芯方式进行脱模的特征较多时,需要对塑件的各个特征进行分类及合并等措施,以简化抽芯机构的结构设计,同时,需要合理安排侧抽芯机构的动作顺序,以简化模具的整体结构,达到降低模具制造成本,保证模具实用可靠的目的。笔者以某摄像机支座塑件为例,结合其注塑模具结构及其特殊脱模机构的设计为同类塑件的模具设计提供参考。
1 塑件分析
某摄像机支座塑件结构图如图1所示。塑件的主体为Ø60.20 mm的圆柱,总高度为133 mm。平均壁厚1.8 mm,材质为丙烯腈–丁二烯–苯乙烯塑料。塑件的上端侧边增设了一个圆柱台。在设计塑件模具时,塑件最合理的布局方式是按图1中D–D所示放置,在此布局下影响塑件模具结构设计的主要问题是塑件的脱模,其主要表现为以下几个方面:①塑件主体为锥形柱体,在其侧边圆柱台的影响下,塑件外壁的脱模变得复杂;②圆柱台侧边外凹槽需要采用侧抽芯方式脱模;③外壁上,E–E剖面位置的侧向沉台、F–F剖视所示位置的阵列槽孔须侧向抽芯;④内壁上小下大,且在中部存在缺口;⑤内壁下段存在上、下两层内螺纹。以上这些特征的存在,影响着塑件分型方式的选择,脱模方式及脱模机构的选用,进而影响到模具整体结构的设计。
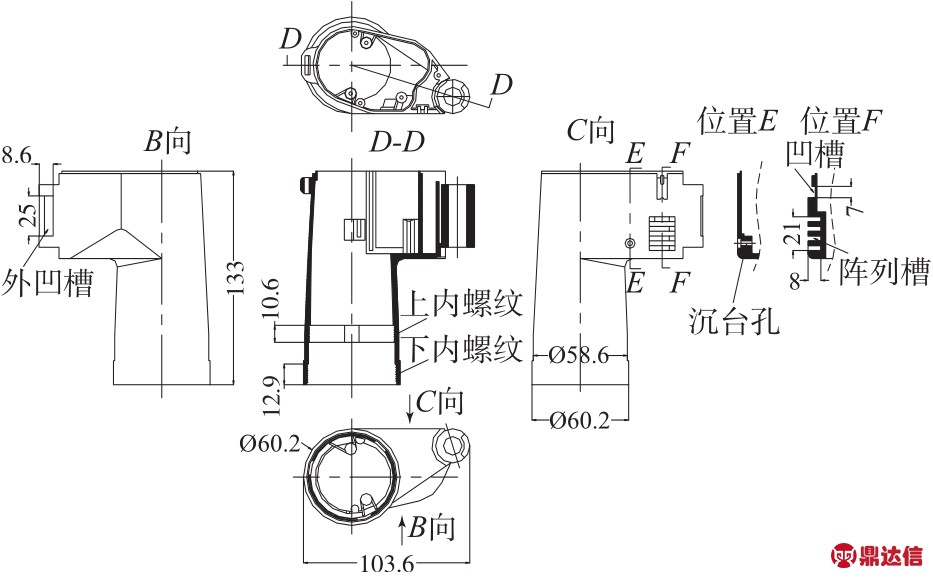
图1 塑件结构
2 分型设计
针对上述塑件的脱模难点,采用如图2所示的分型设计:①塑件的主分型面采用2个分型面,如图2中的上分型线、下分型线所在的分型面。②针对塑件外壁采用哈弗滑块来进行成型和侧抽芯脱模;哈弗滑块的上端为上分型线所示的位置,其下端为下分型线所示位置;哈弗滑块的对半分型线选用图2所示的滑块分型线进行劈分,劈分后的成型块分成左、右两半哈弗滑块,其沿各自对应的抽芯方向抽芯时,能实现整个塑件外壁的脱模;采用哈弗滑块的另一个好处是,通过在右哈弗滑块上设置沉台孔、阵列槽的成型镶件,能同步实现此两处特征的侧向抽芯脱模。③针外凹槽单独采用1个型腔侧抽芯机构来实施侧抽芯脱模。④针对内壁下段存在的上、下两层内螺纹特征,采用内收式滑块内收方式来进行脱模。
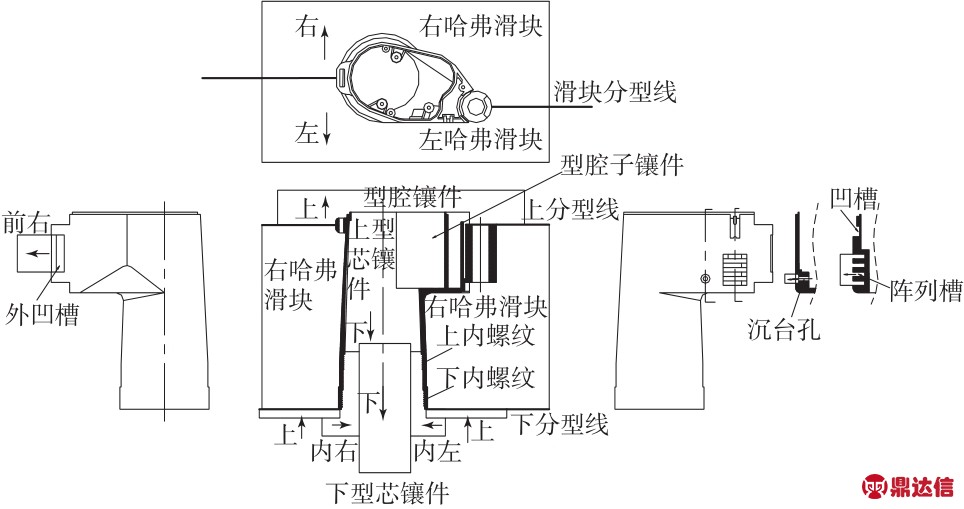
图2 分型设计
按照上述分型路线,具体的脱模过程为:①先对外凹槽进行侧抽芯脱模;②哈弗滑块进行侧面抽芯,完成外壁及沉台孔、阵列槽的脱模;③型腔镶件从塑件中抽出,完成塑件上部部分外表面的脱模,型腔子镶件从塑件中抽出,完成塑件上部空槽的脱模;④下型芯镶件抽出,用于上、下内螺纹成型的镶件内收,完成内螺纹的脱模;⑤塑件被顶起,从上型芯镶件上完全顶出脱模。
因此,塑件脱模机构设计的重点为3个:①外凹槽先抽芯机构;②外壁哈弗滑块抽芯机构;③内螺纹滑块内收脱模机构。模具整体结构设计的难点在于如何保证上述3个机构的按序动作及塑件的整体完全脱模。
3 模具结构设计
模具整体结构如图3所示。模具采用一模两腔及冷流道浇注系统,浇口形式为侧边矩形尖嘴浇口;排气采用镶件间隙进行排气;冷却采用水冷方式进行均衡冷却;模架选用龙记CI标准BCI四板式大水口模架。模具分三次打开,三次顶出:第一次打开用于外凹槽的侧抽芯脱模及下型芯镶件的先行抽芯,第二次打开用于哈弗滑块的侧面抽芯,第三次打开用于塑件的完全顶出;顶出时,第一次顶出用于辅助内螺纹脱模机构的内收抽芯动作,第二次用于内螺纹抽芯机构的两次顺序内抽芯动作,第三次顶出用于塑件的完全顶出。
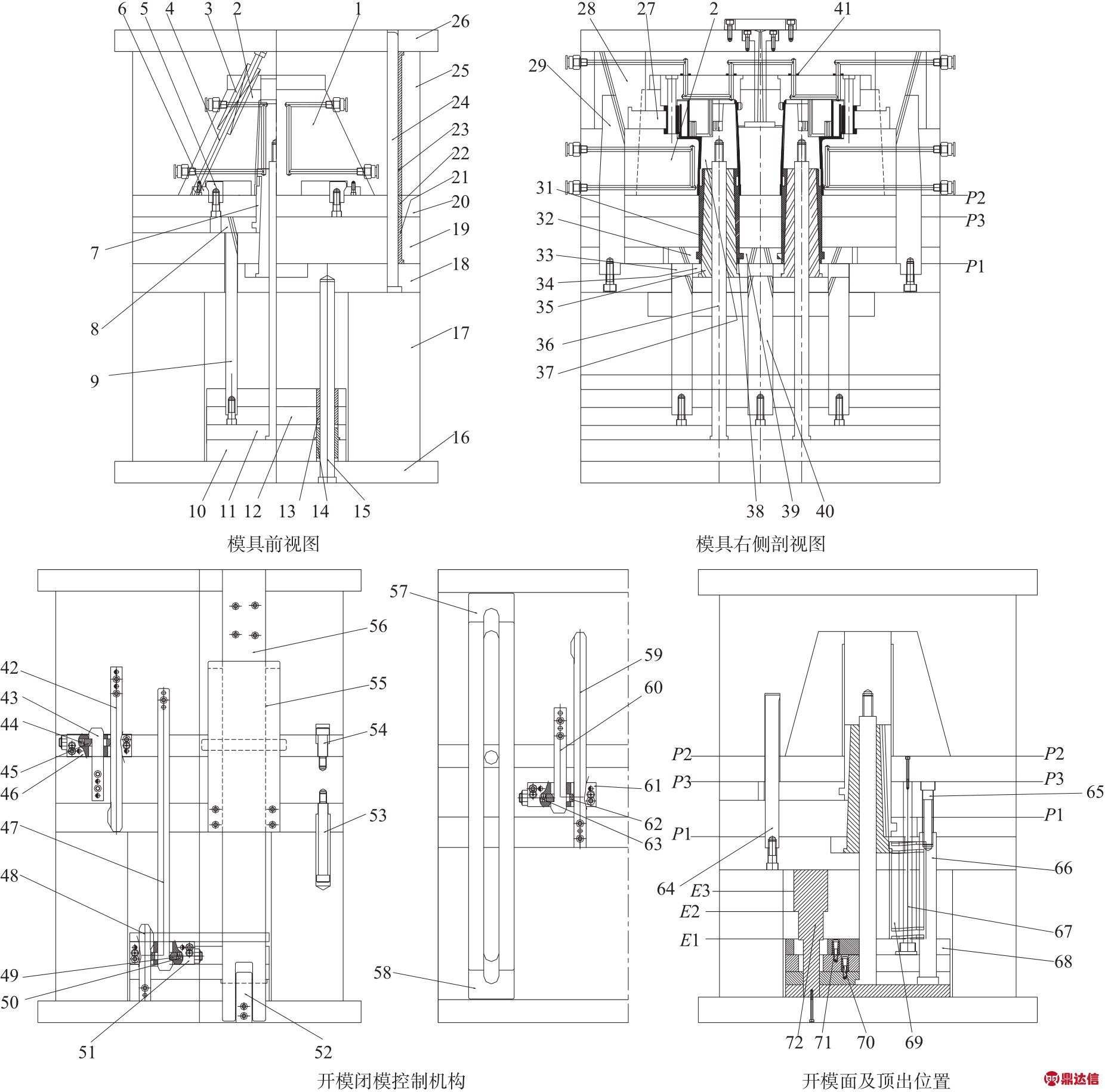
图3 模具整体结构
1—哈弗右滑块; 2—哈弗左滑块; 3—滑块弹簧; 4—滑块斜导柱; 5—滑块锁钩; 6—锁块; 7—内收小滑块螺纹型芯; 8—内收小滑块;9—小滑块驱动杆; 10— 一次推板; 11— 一次推板盖板; 12—二次推板; 13—二次推板导套; 14— 一次推板导套; 15—推板导柱; 16—底板;17—模脚; 18—动模垫板; 19—动模板; 20—动模推板; 21—动模板导套; 22—动模推板导套; 23—定模板导套; 24—导柱; 25—定模板;26—面板; 27—外凹槽型芯; 28—外凹槽滑块; 29—外凹槽滑块驱动杆; 30—滑块压条; 31—内螺纹大型芯; 32—大型芯滑块;33—大滑块驱动杆; 34—下型芯压紧块; 35—下型芯; 36—上型芯拉杆; 37—上型芯; 38—内螺纹大型芯(中央); 39—大型芯滑块(中央);40—中央驱动杆; 41—密封圈; 42—第二插杆; 43—第二锁钩; 44—第二锁芯; 45—第二锁芯弹簧; 46—第二锁体块; 47—第三锁钩;48—第三插杆; 49—第三锁芯; 50—第三锁芯弹簧; 51—第三锁体块; 52—顶出板复位块; 53—动模板定距拉杆; 54—动模推板定距拉杆;55—导向板; 56—顶出板先复位插板; 57—推板定距板; 58—动模定距拉板; 59—第一插杆; 60—第一锁钩; 61—第一锁芯; 62—第一锁芯弹簧;63—第一锁体块; 64—小推杆; 65—螺丝; 66—动模板连杆; 67—动模推板连杆; 68—三次推板; 69—复位杆弹簧; 70—第二次开闭器;71—第三次开闭器; 72—顶出限位定距柱;P1~P3—开模面; E1~E3—顶出面
3.1 模腔布局
图4为模腔布局。如图4所示,模腔布局采用一模两腔、上下对称分布方式,这种分布方式可使模具天地侧较多的剩余空间得到有效利用,以便于A1,A2两个用于外凹槽特征抽芯机构在模架上的安装。在模具的动模部分,针对单个模腔的内螺纹脱模,采用2组6个内收滑块来实施内螺纹的内收抽芯脱模,如图4b所示。以上腔为例,第1组内收滑块由B1,B2,B3三个小滑块组成,第2组内收滑块由C1,C2,C3三个大滑块组成,大、小滑块之间间隔排列,6个滑块的成型部分构成塑件上、下两层内螺纹的整圈成型件。
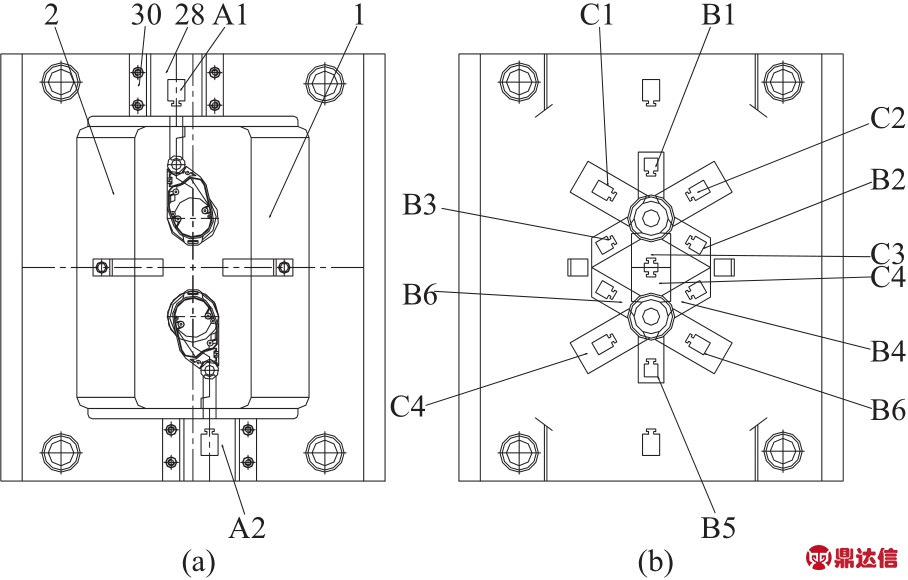
图4 模具布局
A1,A2—外凹侧抽芯滑块组件; B1~B6—小滑块组件;C1~C6—大滑块组件a—模具俯视图; b—模具仰视图
6个滑块做此布局的作用是先让小滑块内收,以留出大滑块内收的空间,而后大滑块再内收,从而实现内螺纹完全脱模。哈弗右滑块1和哈弗左滑块2为滑出型哈弗滑块,滑块安装于定模型腔一侧。
3.2 模架结构
模架结构如图3所示,模架为四板模架,模架的导柱采用倒装式安装,导柱24安装于动模垫板18上,以利于型芯成型件的保护。定模板25采用厚模板,以便于哈弗右滑块1和哈弗左滑块2安装于其内;因内螺纹有分次脱模动作的需要,在模架上的一次推板10、一次推板盖板11构成的顶出板上,再增设一块顶出板二次推板12以安装内螺纹抽芯机构的驱动零件(小滑块驱动杆9、大滑块驱动杆33、中央驱动杆40)。
3.3 哈弗滑块机构
针对塑件外壁的侧抽芯脱模所设计的哈弗滑块机构在模具上的安装如图3所示。哈弗右滑块1、哈弗左滑块2安装于定模板25开设的腔槽内,两哈弗滑块的前后侧通过T型块滑动连接安装于腔槽的T槽内。以哈弗左滑块2的结构组成为例,其结构组成零件包括哈弗左滑块2、滑块弹簧3、滑块斜导柱4、滑块锁钩5 (其通过螺钉紧固安装于动模推板20)、锁块6 (其通过螺钉紧固安装于哈弗左滑块2底端)。在开模时,动模推板20和定模板25之间打开,由滑块锁钩5拉住锁块6,锁块6再拉动哈弗左滑块2向斜向下滑出,哈弗左滑块2滑出一定距离后,滑块锁钩5、锁块6脱离,哈弗左滑块2由滑块弹簧3独立驱动,直至抽芯动作完成。
3.4 定模外凹槽先抽芯机构
该机构在模具上的安装如图3中模具右侧剖视图所示,机构主要组件包括外凹槽型芯27、外凹槽滑块28、外凹槽滑块驱动杆29、滑块压条30。外凹槽型芯27紧固安装于外凹槽滑块28后,外凹槽滑块28通过滑块压条30安装于定模板25上,外凹槽滑块28上开设有斜T型槽,该斜T型槽与外凹槽滑块驱动杆29滑动配合,由其进行驱动,外凹槽滑块驱动杆29穿过动模板19、动模推板20及定模板25上孔,其下端通过螺钉紧固安装于动模垫板18上。模具在动模垫板18、动模板19之间打开时,外凹槽滑块驱动杆29能从外凹槽滑块28上抽出,驱动其向外侧抽芯以实现塑件外凹槽特征的脱模。
3.5 六滑块错位内收内螺纹抽芯机构
为实现塑件内壁上、下内螺纹的脱模,其机构设计成一种6个滑块错位内收抽芯脱模形式,结合图4b所示的内抽芯机构的布局,第1组内收滑块由B1,B2,B3三个小滑块组成,第2组内收滑块由C1,C2,C3三个大滑块组成。以其中一个模腔内的该机构为例,B1,B2,B3三个小滑块的结构相同,C1,C2,C3三个大滑块的结构组成也相同。
对于B1小滑块机构,其组成零件主要包括内收小滑块螺纹型芯7、内收小滑块8、小滑块驱动杆9。内收小滑块螺纹型芯7为内螺纹的局部成型件,同时对塑件内螺纹的上下两层局部内螺纹进行成型;内收小滑块螺纹型芯7与内收小滑块8紧固连接,内收小滑块8通过滑动槽安装于动模板19上,由定位玻珠对成型位置及抽芯脱模后停留位置进行定位。B1小滑块由通过螺钉紧固安装于二次推板12上的小滑块驱动杆9进行驱动,小滑块驱动杆9的上端设置有与内收小滑块8配合的斜T型槽,通过该T型槽,小滑块驱动杆9驱动内收小滑块8内收抽芯。
对于C1大滑块机构,其组成零件包括内螺纹大型芯31、大型芯滑块32、大滑块驱动杆33。内螺纹大型芯31与大型芯滑块32紧固连接,由大滑块驱动杆33驱动,大型芯滑块32通过压条安装于动模板19下层。C1,C2,C3三个大滑块安装于动模板19的下层。结合图3所示,要实现6个滑块的内收抽芯,必须先让B1,B2,B3三个小滑块内收抽芯,留出空间后,才能让C1,C2,C3三个大滑块内收抽芯,从而实现整圈内螺纹的抽芯。因而,为保证两组滑块的先后顺序抽芯,小滑块驱动杆9与大滑块驱动杆33、中央驱动杆40同样安装于二次推板12上,小滑块驱动杆9的上端距离驱动内收小滑块8的距离为1 mm,而大滑块驱动杆33、中央驱动杆40与大型芯滑块32、大型芯滑块39 (中央)的距离为10 mm,保证一定的延后时间。上型芯37通过上型芯拉杆36与二次推板12连接。
3.6 模板开闭动作顺序控制机构
结合前述,塑件要实现完全自动脱模,达到自动化生产的目的,模具模板的开启须按P1→P2→P3的顺序来开启,顶出板的顶出按E1→E2→E3顺序顶出。复位则按相反顺序执行。为此,设计了以下机构来实现这个动作。
(1)模板开启顺序机构。
模板按P1→P2→P3顺序开启,其由2个机构控制,2个机构都为插杆锁销式锁闭机构,第1个机构的组成零件为图3中的零件59~零件63,第2个机构的组成零件为图3中的零件42~零件46。这2个机构的作用是:当模具在P1面打开时,第一锁钩60将动模板19、动模推板20、定模板25可靠地锁在一起,直到P1面打开一定的距离后,第一插杆59将第一锁芯61打开,模具中的三个模板才能进行分开,而此时,第二锁钩43将动模板19、动模推板20锁紧在一起,故而,模具只能在P2面打开;只有当P2面打开一定距离后,第二插杆42将第二锁芯44推动,从而将动模板19、动模推板20打开,即P3面才能打开。动模板定距拉杆53用于控制P1面的打开距离,动模推板定距拉杆54用于控制P3面的打开距离,推板定距板57用于控制P2面的打开距离,动模定距拉板58用于控制P1,P3面的打开总距离。在此2个机构的控制下,复位时,模板按P3→P2→P1的顺序闭合。
(2)顶出控制机构。
顶出板分三次顶出,顶出顺序按E1→E2→E3顺序依次顶出。一次推板10、一次推板盖板11、二次推板12、三次推板68构成模具的三次顶出板,其中一次推板10、一次推板盖板11通过螺钉紧固组合在一起。为保证P1面打开时,顶出板不跟随动模后退,设置一个位置保持锁闭机构,该机构组件包括图3中的零件47~零件51,该机构的作用是:动模在P1面打开时,保持三个顶出板同定模板25的距离不变,维持闭模时的状态位置,只有当注塑机顶杆推动三次推板68,带动一次推板10、二次推板12向上顶出一定距离后,第三插杆48才能打开第三锁钩47使之开锁,便于二次推板12的独立运动。一次推板10、二次推板12、三次推板68向上顶出时,由第二次开闭器70、第三次开闭器71将三者临时吸紧闭合保持联动,由顶出限位定距柱72对三者逐级分离。动模板连杆66将二次推板12与动模板19连在一起保持联动,动模推板连杆67将三次推板68与动模推板20保持联动。复位时,由复位杆弹簧69推动一次推板10、二次推板12、三次推板68一次按E3→E2→E1顺序闭合,顶出板先复位插板56保证顶出板先复位后模具模板才能按P3→P2→P1顺序闭合。
4 模具工作过程
(1)注塑。
模具闭合,注塑机对模具的模腔进行注塑,完成注塑、充填、保压、冷却等过程,等待开模。
(2) P1面打开。
模具在注塑机动模的拉动下后退,模具首先在动模一侧的P1开模面处打开,此时,外凹槽滑块驱动杆29将拉动外凹槽滑块28向外抽芯,完成塑件外凹槽的侧抽芯脱模;同步地,下型芯35也被同步拉出,留出中心空间给6个内抽芯滑块;同步地,第三锁钩47勾住第三锁芯49使顶出板与定模板25之间保持静止状态。P1面打开距离为140 mm,由动模板定距拉杆53进行定距。
(3) P2面打开。
P1面打开完毕后,动模继续后退,第一插杆59将第一锁芯61打开,第二锁钩43对动模板19、动模推板20依旧进行锁紧,模具将在P2面处打开,在滑块锁钩5拉住锁块6的情况下,哈弗左滑块2、哈弗右滑块1被拉动向斜向下滑出,完成塑件外壁的侧面抽芯脱模,同时塑件上部内部局部区域先完成脱模,塑件留于上型芯37上。此时第二锁钩43解除第二锁芯44对动模板19、动模推板20的锁紧。P2面打开距离为90 mm。
(4) E1面顶出。
E1顶出面不进行顶出,只进行向上0.5 mm的辅助移动,主要用于保证上型芯37与动模板19的同步。
(5) E2面顶出。
P2面打开完成后,动模继续后退,注塑机顶杆推动三次推板68带动带动二次推板12向上顶出,顶出一定距离后,上型芯37与下型芯35完全分离,此过程中,小滑块驱动杆9先驱动内收小滑块螺纹型芯7、内收小滑块8先向中央收缩抽芯,而后,内螺纹大型芯31驱动大滑块驱动杆33和大型芯滑块32完成剩余内螺纹的抽芯,直到顶出限位定距柱72将二次推板12挡住,实现塑件内壁上下两层内螺纹的脱模。
(6) E3面顶出(P3面打开)。
动模继续后退,注塑机顶杆继续推动三次推板68向上顶出,三次推板68通过动模推板连杆67推动动模推板20将塑件从上型芯37上完全顶出脱模。
(7)模具复位。
复位时,三块顶出板先被推回复位,而后是模板按P3→P2→P1顺序闭合,模具闭合,等待下一注塑循环。
5 结语
针对塑件结构复杂、内外特征脱模都比较困难的问题,设计了一种四板式三次开模、三次顶出冷流道注塑模具。针对塑件外凹特征的脱模,采用位于动模一侧的先抽芯杆驱动定模滑块进行先抽芯脱模;针对塑件外壁整体脱模困难的问题,采用哈弗滑块进行抽芯脱模,简化了外壁脱模机构的设计;针对塑件双层内螺纹的脱模,采用一种复合式内收式滑块进行脱模,机构由2组共6个滑块及相应控制构件组成,6个滑块的成型部分拼合成塑件内螺纹的整环螺纹,通过分次抽芯的方式,实现了塑件内壁上下层整圈螺纹的内收抽芯脱模;最终通过第三次顶出板推动动模推板将塑件从上型芯上完全顶出脱模。通过分步分类型设计脱模机构的设计方法简化了模具的结构设计,实现了塑件的自动化注塑生产,为同类塑件的模具设计提供了有益参考。