摘 要:阀体作为自动变速器液压控制系统的核心零件,由于工作功能原因,导致本身结构形状复杂,内部孔系较多,产品尺寸精度要求高。阀孔均为多级台阶,贯穿孔较多,孔壁较薄,在加工过程中容易出现变形及毛刺。以PCD铰、刀加工阀体的阀芯装配孔的为例,利用切削仿真软件对刀具切削加工进行模拟仿真,分析刀具切削参数及几何结构参数对切削力、切削温度的影响规律,以此作为优化刀具结构参数及切削参数方向。对原有刀具结构尺寸进行改进,最终获得保证阀芯装配孔加工质量的工艺方案及刀具。
关键词:PCD刀具;阀芯装配孔;切削仿真;精密加工
随着汽车整体技术的发展,变速器也进行着升级,从早期的手动变速器到后期的自动变速器、双离合变速器及CVT变速器。阀体作为自动变速器的核心零件,它的加工过程质量控制也变得尤为重要。
某款CVT变速器,在前期的试制过程中,阀体加工过程中经常出现表面出毛刺,贯穿孔出毛刺,阀芯装配孔直线度、圆度、圆柱度不合格的现象。严重影响了产品性能,并且制约了项目的总体进度。为了保证产品试制成功,对其他相似制造企业、刀具厂家进行调研,并对现场的切削过程进行分析,结合刀具切削参数及刀具几何结构参数对产品加工质量的影响,利用切削仿真软件进行加工过程模拟,根据模拟结果对刀具及工艺方案进行重新设计,加工出满足图纸要求产品。
1 PCD刀具特点
1.1 PCD刀具特点
PCD 是用金刚石加入一定成分的催化剂,在高温、高压下烧结而成的一种多晶金刚石聚合体,具有极高的硬度、抗压强度高、导热性及耐磨性好等特性。使用PCD制作的刀具具有以下优点:①刃口非常锋利,热膨胀系数小,切削力小,加工产品变形小,切削加工表面质量好;②具有极高的硬度和耐磨性、极低的摩擦系数,刀具寿命长;③加工参数高,加工效率高[1-2]。
这位导事,在念诵《指路经》(死者入棺时念诵)之后,就不再参与仪式的其他环节。剩下的祭奠活动,交给其他的人完成。
等到人群散去,我才跑过去调侃他,说:“你现在跟以前完全不一样了,简直是脱胎换骨。看来大学把你改造得挺好啊!”
由于材料本身的特性,PCD刀具在制作和使用中也存在很大的局限性。主要包括以下几个方面:①韧性差,在切削过程中经常会因冲击或者切削力不均匀而崩刃,在使用过程中要保证加工系统的刚性,尽量减小刀具的悬长。②尽管常温下PCD硬度很高,但切削过程中随着温度上升硬度下降很快,所以切削时需要冷却液来冷却刀具,保证其红硬性。③PCD刀具都为焊接刀具,焊片的长度制约了切削余量的大小,所以只能完成尺寸变化较小的加工。④PCD硬度高,加工性能差,用其制作的刀具结构简单,几何参数不像硬质合金、高速钢等材料刀具那么复杂[2-4]。绝大部分PCD刀具的前刀面都是平面,尤其是钻头、铰刀、焊接立铣刀,前角和刃倾角都以0°居多,影响加工的主要几何参数只有刃带、刀尖倒角、后角及倒锥等尺寸。
1.2 PCD刀具在铝合金上的应用
由于PCD与有色金属的亲和力小,加工过程中不易粘屑,PCD刀具已经是镁铝等有色金属及其合金加工的主选刀具[2,4]。PCD面铣刀加工铝合金的线速度可以达到8 000 m/min,部分厂家生产的PCD面铣刀一次寿命可以加工20 000个缸盖,PCD铰刀加工铝合金的线速度可以达到400 m/min,粗糙度可以达到Ra0.2 μm,而且刀片可以重新焊片或者修磨,这些性能都已经远远高于常规刀具。采用先进的PCD刀具,不仅能降低单件刀具成本,而且能提高加工质量及生产效率,从而大大降低生产成本。
2 阀芯孔的加工问题
2.1 阀芯孔的特点
某款自动变速器阀体材料采用铸造铝合金,毛坯可能存在硬点及气孔,这些都容易导致加工过程中刀具异常。其中阀芯孔有5个阶梯,孔径在φ12~16 mm,孔径公差最严在6级精度以内,圆度最严要求为0.004 mm,跳动最严要求为0.01 mm,位置度要求为φ0.2 mm,圆柱度要求为0.005 mm,粗糙度要求为Ra0.4 μm。
阀芯孔加工具有:①孔径小,深度长,刀具长径比大,悬伸长。②工件为多层断续切削,断屑困难,排屑不易。③铸件槽间存在拔模斜度,刀具易“让刀”,从而影响直线度和圆柱度。④加工需穿过多层铸造表面,刀具寿命受铸件质量影响较大。⑤加工内容多,加工长度长,刀具加工参数对节拍影响大等特点,几乎涵盖了所有孔加工刀具的难点[5]。
实践无止境,探索无止境。国防动员联结军地双方,关乎国家安全和发展,具有联合攻关、集团作战的特殊优势,理论研究的空间和自由度更大。必须以党在新时代强军目标为统领,着眼新形势新任务新要求,积极探索科学有效的理论创新运作机制,促进国防动员理论和实践创新发展。
2.2 阀芯孔的加工问题
加工阀体采用的机床为卧式加工中心,主轴型式为HSK-A63,工件夹具采用液压夹紧方式,切削液采用乳化液(见图1)。阀芯孔加工使用2把刀(刀具均有内冷)完成加工:第1把刀为半精加工刀具,结构为带法兰连接的焊接PCD铰刀,刃数为3刃,主要加工内容为1、2、3孔精加工及4、5孔半精加工,4、5孔精加工余量为0.3 mm,切削参数转速n=6 000 r/min,进给Fz=0.15 mm/z;第2把刀为带法兰连接的PCD铰刀,刃数为6刃,主要加工内容为4、5孔的精加工,切削参数转速n=6 000 r/min, 进给Fz=0.1 mm/z(见图2)。
3)充分体现了虚拟与实验的紧密结合、教学与科研的紧密结合,使学生早日了解科研的手段和方法,初步了解科研过程,为国家培养高层次人才奠定基础。
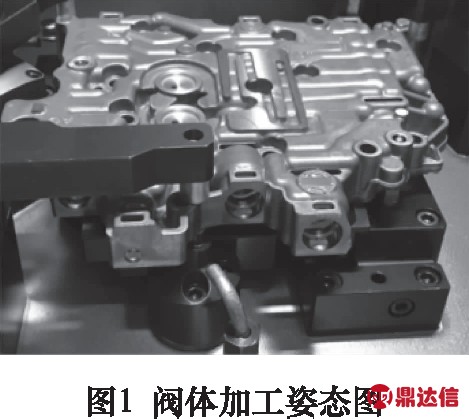
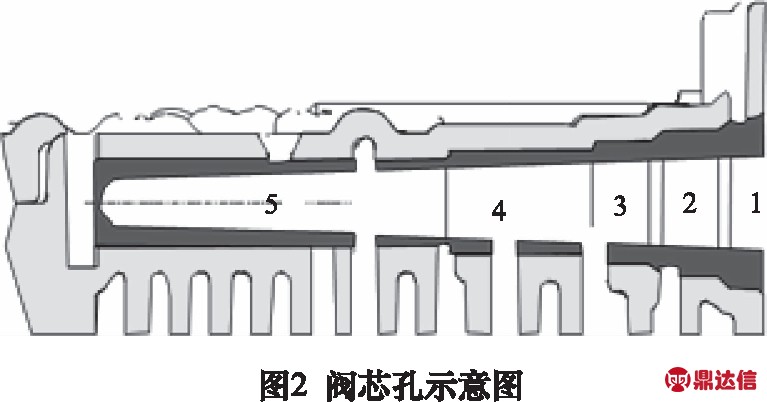
按照预定方案程序进行加工,加工完成后对零件进行检测,发现如下问题:①4、5孔孔口有毛刺;②5孔孔壁有黑印;③孔位置度不好;④孔圆度圆柱度不好。对夹具、切削液、毛坯及机床主轴等因素进行排查后,确定产生上述问题的主要原因为工艺参数及刀具。后经多次更改切削参数,孔壁有黑印及位置度不好的问题得以解决,孔口毛刺、圆度及圆柱度虽有改善,但是加工效果仍不理想。除上述问题,在优化切削参数时,还发现部分零件孔壁存在振纹情况。
3 加工的优化及实现
经过对产品及加工过程分析,导致产品加工不合格的原因有如下几个方面:①阀芯孔直径在12~16 mm,孔深将近120 mm,长径比过大,加工过程容易出现“跑偏”现象。②毛坯孔铸造余量不均匀,容易造成刀具加工中振动,产生振纹或者“跑偏”现象。③第1刀加工余量较大,容易出现振纹。④第1刀加工余量不均匀,容易出现毛刺及铝环现象。⑤第2把刀具几何参数不合理,容易出现毛坯及铝环现象。⑥第2把刀具几何参数、切削参数不合理,切削温度和切削力过大,导致工件变形。根据以上分析,从加工工艺及刀具两方面着手进行优化改进。
3.1 工艺顺序的优化
根据分析,将原来的2刀加工改为3刀加工,在第1把刀前面增加引导刀具,可以减少第2把刀具的加工余量,防止“跑偏”、振纹及粗加工出现铝环、毛刺现象,同时增加了第2把刀的修正能力,能进一步保证精加工刀具的加工效果,保证产品的圆度及圆柱度要求。具体如下:第1把刀为引导刀,结构为整体焊接成型PCD刀具,刃数为3刃,主要加工内容为阀芯孔粗加工,将毛坯铸造孔的斜度去掉,并对1、2、3孔留精加工余量0.5 mm,切削参数转速n=6 000 r/min,进给Fz=0.1 mm/z;第2把刀为半精加工刀具,使用之前方案第1把刀具;第3把刀为带法兰连接的PCD铰刀,几何参数待定,主要加工内容为4、5孔的精加工,切削参数转速n=6 000 r/min, 进给Fz=0.1 mm/z。
3.2 刀具的优化
经过上述分析,增加引导刀具后,仍需对精加工刀具进行优化。由于影响工件变形的主要因素是切削力及切削温度,利用仿真软件对刀具进行模拟仿真,在考虑刀具制作难点及生产效率情况下,寻找切削力及温度尽量小的刀具几何参数。利用三维软件UG进行刀具建模,刀具几何尺寸如下:均布等分六刃直槽铰刀(前角为0°),D=12 mm,刀尖倒角为0.2 mm,倒角角度为45°,后角为6°,刀具倒锥为0.008。将刀具模型导入切削仿真软件AdvantEdge FEM中,进行3D仿真。加工类型选择钻削(钻削与较削加工方式相同,在后期工件设置时增加预孔设置,如图3所示),刀具材质选择Diamond,没有涂层,工件材质选择AL380(US),切削参数选择转速n=6 000 r/min, 进给Fz=0.6 mm/r,切削温度选择26 ℃,如图4所示。加工方式为盲孔加工,设定加工深度6 mm,摩擦系数选择默认数值,冷却选项参数设置如图5所示,其他仿真设置选择如图6所示,点击执行键进行仿真,如图7所示。同时,将铰刀从6刃改为4刃、3刃,其他几何尺寸不变,分别按照上述参数进行仿真切削。得到切削力及温度模拟情况如图8所示。
经过上述实验研究,得到对于3号水基钻井废弃泥浆样品来说,最佳药剂投加固化方案为:AP破胶剂2.0%+32.5硅酸盐水泥20.0%+HHJ活性剂+CA促凝增强剂5.0%。

由于仿真实验与实际加工过程存在着工件材料、切削液、环境温度、机床状态及加工系统刚性方面的差异,导致实验结果与实际值有一定差异,仿真实验结果仅仅可以作为研究刀具切削参数、几何参数对切削力、切削温度影响的趋势参考[6-7]。通过仿真结果可以看出3刃铰刀的切削力及切削温度都低于6刃铰刀及4刃铰刀,所以选择铰刀设计刃数为3。
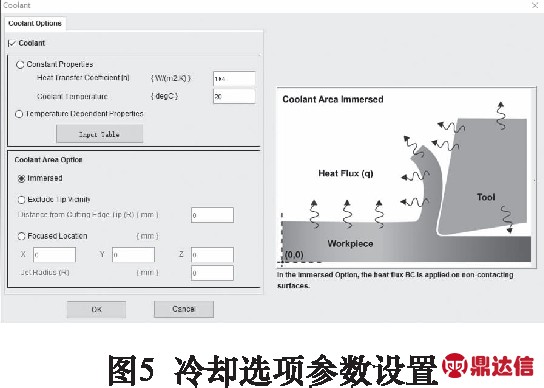
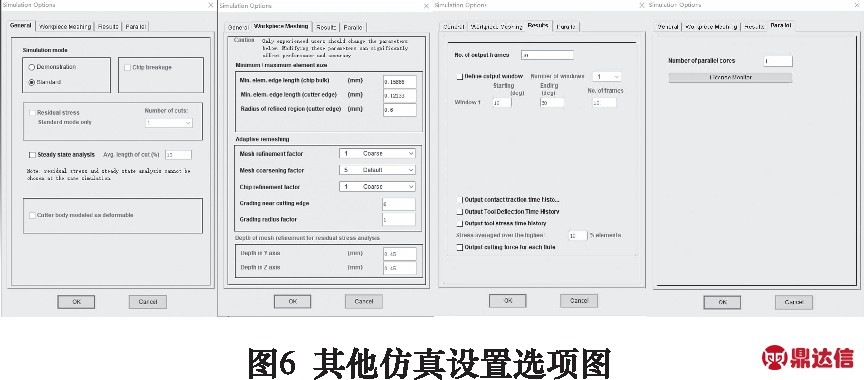
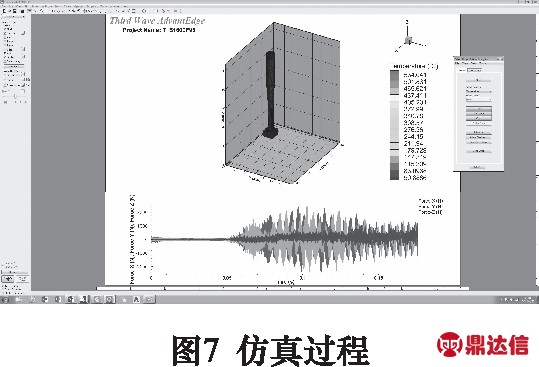
按照如上的实验过程,铰刀刃数选择3刃,更改部分刀具几何参数分别进行实验,具体更改明细如下:①仅更改刀尖倒角为0.2 mm和0.6 mm;②仅更改后角为8°和10°;③仅更改倒角角度为30°和60°;④仅更改刀具倒锥为0.01和0.012。实验结果及选择结果见表1。由于倒角可以改变切削力方向,选择60°倒角可以增加轴向力,减小径向力对工件的影响,根据受力方向计算,可以降低出口毛刺的风险[6-7]。为了进一步保证产品加工的圆度,根据厂家以往经验,将3刃铰刀每个切削刃后增加2个支撑导条,如图9所示。
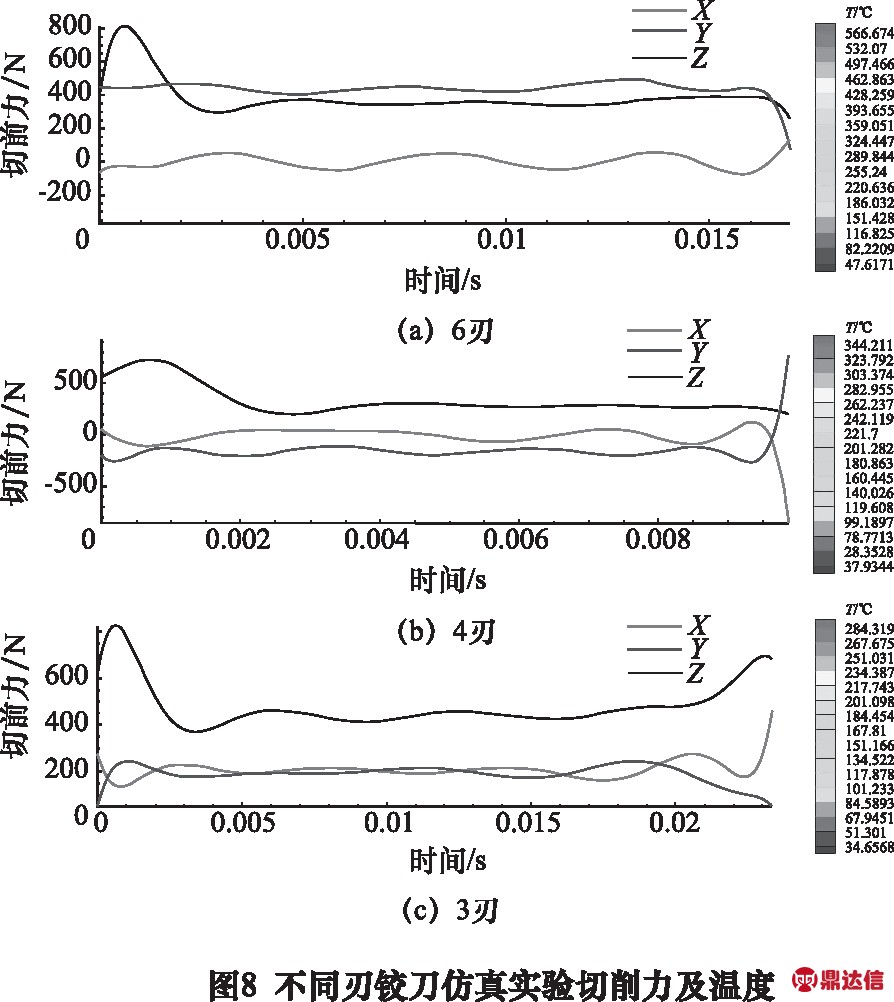
表1 仿真实验结果
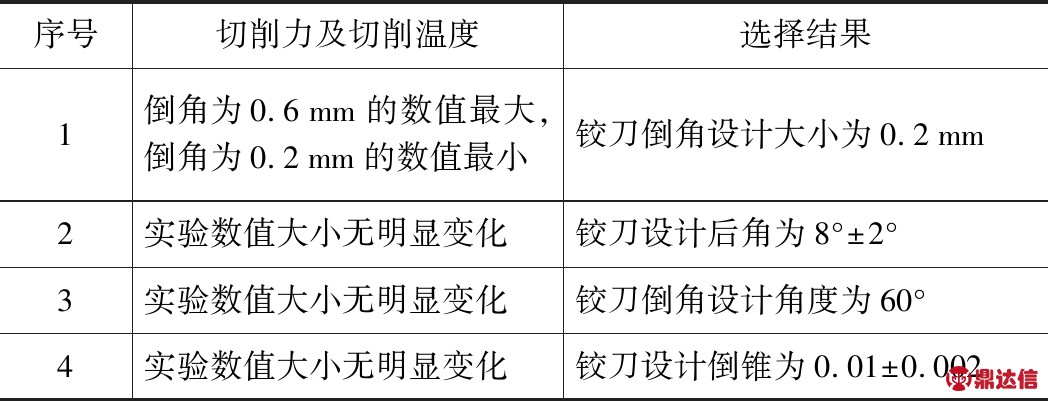
序号切削力及切削温度选择结果1倒角为0.6mm的数值最大,倒角为0.2mm的数值最小铰刀倒角设计大小为0.2mm2实验数值大小无明显变化铰刀设计后角为8°±2°3实验数值大小无明显变化铰刀倒角设计角度为60°4实验数值大小无明显变化铰刀设计倒锥为0.01±0.002
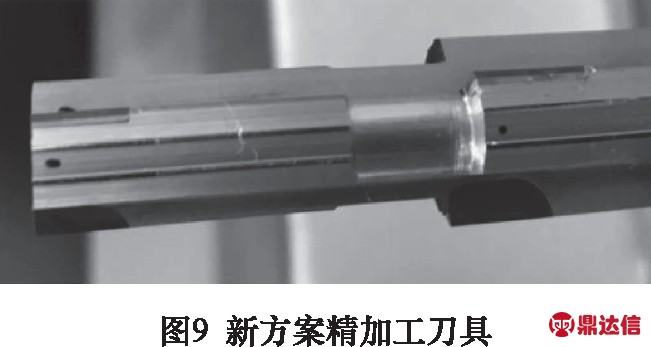
根据仿真实验结果结合实际情况制作新刀,按照3.1中所述新方案进行加工,经过试切后对工件进行检测,产品的尺寸精度要求得到了保证,而且孔的圆度要远远好于原方案刀具加工效果,如图10所示。
4 结语
孔加工是一个复杂过程,影响产品加工质量的因素错综复杂,导致经常出现加工不合格的现象。为了保证加工质量,复杂的孔系加工方案在前期实施时需要对加工方式、切削参数、刀具几何参数中进行反复优化,在这期间会造成大量的机物料和时间的浪费。如何避免这种浪费以及加快方案实现是很多企业迫切需要解决的问题,切削仿真软件的应用可以很好地解决这一难题。利用切削仿真软件模拟加工过程,根据模拟结果(包括切屑温度、切削力、扭矩及残余应力等)选择合理的刀具几何参数是刀具设计、加工方案设计优化的主要发展趋势。随着切软件技术的越来越成熟,切削仿真软件的实验结果与实际情况差异将会越来越小,刀具的研发速度将比过去提高数倍,复杂孔系加工方案的制作速度和准确率都会有大幅提高,同时避免了制作试验刀具造成的资源浪费,是绿色制造不可缺少的一环。
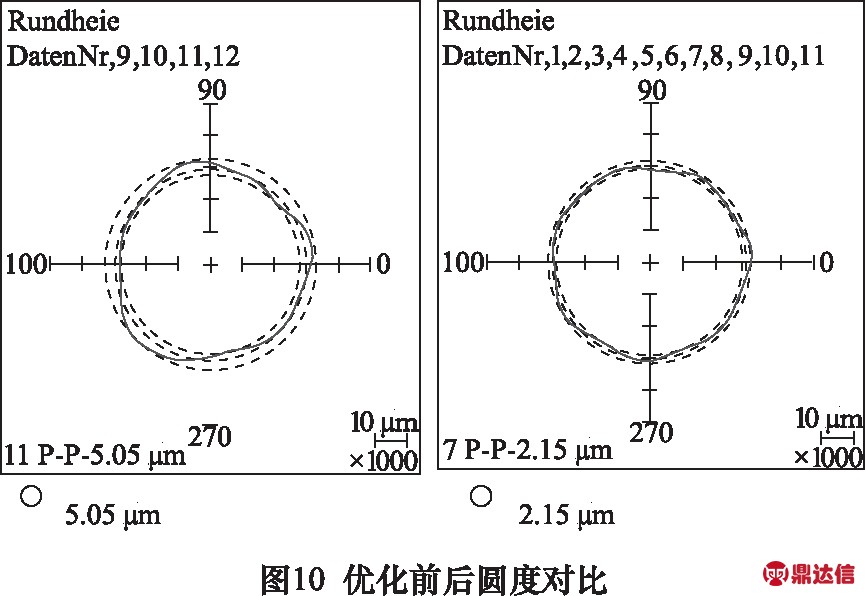