摘 要:基于开发研制ZP- 375 转盘的需要,设计制造了90kW 大型数显式温控加热油炉。该油炉利用温度指示调节仪和传感器,实现油炉温度的自动控制。可用于加热轴承、齿轮件和转台组件,在现场应用中取得了良好的效果,为转盘的批量化生产提供了有利的保障。
关键词:大型;加热油炉;设计
1 引 言
宝鸡石油机械有限责任公司依据自身的加工特点和优势,为满足钻机配套的需求,开发、研制了系列转盘。按照工艺要求,转盘中的轴承、大齿圈、转台组件都必须热装并保温处理,制作一台既能加热轴承,又能加热转台组件的加热炉成了当务之急。经过调查了解,公司常用的加热设备有二类,一是箱式炉,二是油炉。箱式炉成本较高,不能加热轴承类零件;而油炉不仅造价低,易于制造,而且升温均匀,温度可控制在0℃~300℃范围内,能满足转盘热装工艺的要求。为此,笔者设计了一台90kW 大型温控加热油炉,该油炉投入使用以来,已累计完成了上千台转盘的组装任务,为转盘的批量化大生产提供了有利的保障,结束了我公司长期外购转盘的历史,提高了我公司钻机在市场上的竞争力。
2 加热油炉的设计
2.1 确定加热油炉尺寸规格
加热油炉采用金属电加热元件加热,加热介质选用闪点较低的机械油。为避免加热元件与被加热零件之间接触、碰撞,考虑将加热元件安装在炉子底部,在加热管上部用支架和均布小孔的钢板分隔开被加热零件。
所设计的转盘中转台的最大直径是1730mm,高度为510mm,考虑到炉子底部加热管的安装,将炉子尺寸确定为:2000mm×2000mm×1700mm。
2.2 加热油炉功率的计算
(1)将油加热至工作温度所需热量[1]:
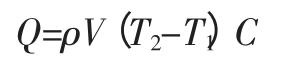
式中:Q-被加热介质所吸收的热量,kJ;ρ-被加热介质的密度,kg/m3;选用46#机械油,ρ=0.95×103kg/m3;V-被加热介质的体积,m3;T2-被加热介质的工作温度,℃,根据ZP-375 转盘工艺要求,同时为保证安全生产,取T2=170℃;T1-被加热介质的初温,℃;取冬季车间温度T1=10℃;C-被加热介质的比热容,C=2.1kJ/(kg·℃)。(2)根据油炉所需热量计算油炉功率
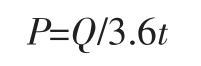
式中:P-总功率,W;t-加热时间,h。
通过计算,为满足转盘工艺要求,油炉设计功率确定为90kW。
2.3 金属电加热元件的设计计算
(1)金属管状电加热元件
金属管状电加热元件是将电能转变为热能的发热元件[3]。它用金属管作外壳,内置合金电阻丝作发热体,填充具有良好绝缘和导热性能的结晶氧化镁。其工作原理是:电阻丝通电后产生热能,经氧化镁绝缘,传递至金属外壳,被加热介质吸收。它可加热静止的或流动的空气、水及其它液体。最高工作温度达300℃。形状有棒形、U型、W 型等。
油炉设计功率是90kW,则选择两组三相380V 三角形接法,每组功率为45kW。通过计算得知,并联三角形接法的功率最大,总功率P=3nP0(P0 为单个加热元件的功率)。
(2)功率分配
加热元件选择并联三角形接线方法,按照P0=P/3n 进行计算,那么每相功率就是15kW。假设每相是两个加热管并联,每个加热管的功率是7.5kW;若每相是3 个加热管并联,每个加热管的功率是5kW;若每相是4 个加热管并联,每个加热管的功率是3.75kW;依次类推。可见,加热管的功率选择得越小,数量就越多,为避免油的渗漏,加热元件数量不宜过多。综合考虑,将每个加热管的功率选定为5kW,即每相3 个加热管并联,每组9 个加热管,两组共计18 个加热管。
(3)油炉功率的调节
常用的功率调节方法有:间断供电、改变炉子供电电压、采用两组电热元件控制,如表1 所示。通过对比得知采用两组三相电热元件加热,功率可调节范围大且常用,即选择方案3 最好。具体实施方案:炉子在升温阶段使用两组电热元件加热,达到工作温度后,切断一组电热元件进行保温,由另一组实现自动温控。加热元件必须均匀分布,以保证在切断一组时,炉子温度均匀。
表1 油炉功率的调节方法
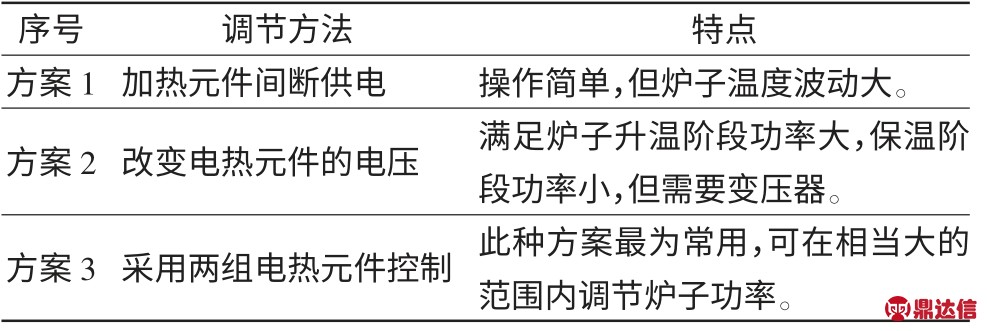
3 加热油炉的电气控制设计
3.1 电气原理图的设计
(1)采用三相50Hz、380V电源,操作回路采用220V电源。
(2)数字式温度指示调节仪
采用XMT-122 型数字温度指示调节仪,进行温度测量和自动控制,配上相应的传感器,可用于温度的显示和调节。
(3)传感器
传感器选用热电阻,测量范围:0℃~300℃,分辨力:1℃。使用前在室温下测其电阻值为110Ω。
(4)金属管状电加热元件
本设计采用一批非标准的安装距为400mm 的双W型电加热管。使用前应测其绝缘电阻,不可低于1MΩ。
3.2 油炉工作原理
(1)推上低压隔离刀闸,将主令开关搬至开的位置,控制柜上红色指示灯亮。
(2)合上空气开关,A组加热管得电工作,指示灯XD1亮。
(3)调整数字式温控仪,首先将开关拔至“下限设定”处,旋转相对应的下限设定旋钮,此时数字显示的是所需的下限温度值,按工艺要求调至80℃;再把开关拔至“上限温度”处,旋转相对应的上限设定旋钮,此时数字显示的是所需的上限温度,如果加热轴承,可调至120℃,如果加热大齿圈可调至170℃。调好后,把开关拔至“测量”处,此时数字显示的是油炉的实际温度值。
(4)当油温低于下限温度80℃时,控制柜上绿灯亮,温控仪的下限继电器“总低”通,B 组加热管得电工作,此时油炉功率为90kW。
(5)当油温高于80℃而低于120℃时,温控仪的下限继电器“总低”断,接触器触头自锁,油炉继续加热。
(6)当油温高于上限温度120℃(或170℃)时,控制柜上红灯亮,温控仪的上限继电器断开,自动温控仪控制的B 组加热管自动断电。此时将控制A 组加热管的空气开关断开,油炉处于保温状态。
(7)当油温低于80℃时,下限继电器又一次接通,B组加热管工作,此时油炉功率仅为45kW。当油温高于120℃时,B 组加热管断电,一直到保温结束,切断控制柜电源。
3.3 电源线的安全选用
为保证油炉正常工作,避免因线路过热引发火灾事故,必须合理选择导线截面积,达到安全运行,降低电能损耗的目的。
(1)线路中电流的计算
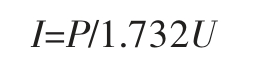
式中:I-线电流;P-总功率,P=45kW;U-线电压,U=380V。
(2)选择导线的截面积
选择导线截面积,主要是根据导线的安全截流量,对于纯电阻性负载,还应考虑其环境温度对安全载流量的影响,与上面计算的电流比较接近的安全截流量如表2所示,考虑到油炉的环境温度,选择25mm2 塑料铜芯软线,管子内径为32mm。
表2 聚氯乙烯绝缘电线安全载流量
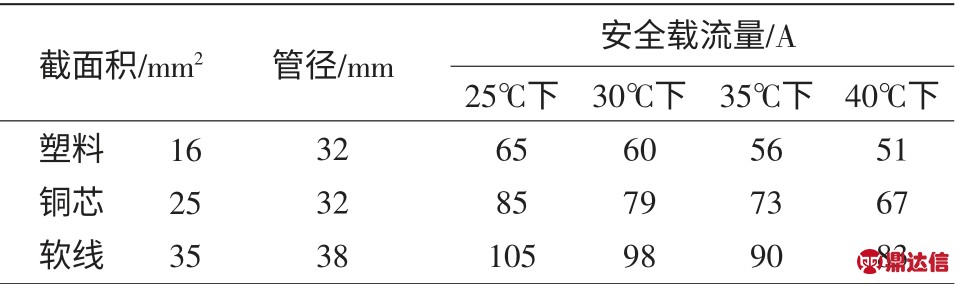
4 技术优势及经济效益
4.1 技术优势
(1)它在我公司同类加热油炉中,体积最大,功率最大,达到90kW。可广泛用于加热各类大型轴承、齿轮件和转台组件。
(2)采用数字式温度指示调节仪,通过传感器,自动显示油炉加热温度。
(3)该油炉不仅能按工艺要求自动升温,还具有自动保温功能,实现了双温控制。
(4)电器系统操作简单,安全可靠。油炉的上、下限温度可根据工艺要求在0~300℃范围内任意调节。由于采用了双温控制线路,可避免大接触器频繁启动造成的安全隐患,延长了接触器的使用寿命,基本上达到零故障。
4.2 经济效益
该油炉自几年前投入生产以来,使用情况良好,转盘的组装工序全部在分厂内部进行,加快了系列转盘产业化的进程。从2002 年至2010 年底累计生产各类转盘上千台。该油炉的投入使用,节约产品周转费、热装费用共约上百万元,是公司节能减排的拳头产品之一。