[摘要] 考虑到干式双离合器自动变速器(DCT)同步器作动电机霍尔位置传感器易受环境影响和维修不便,本文中在选挡过程对其进行故障诊断和容错控制,以保证DCT 车辆平稳换挡和安全行车。 首先搭建并验证了干式DCT 同步器作动电机仿真模型,设计模糊滑模观测器对其线反电动势进行实时估计,并利用无刷直流电机线反电动势与转角信号间的关系,实现了对同步器作动电机位置的间接估计。 接着,基于估计值与传感器实际输出的偏差对霍尔传感器进行了故障诊断,通过解析冗余实现了对同步器作动电机霍尔传感器故障的主动容错控制。 最后,对所提出的霍尔位置传感器故障诊断方法分别进行了仿真和试验验证,结果表明,所重构的霍尔位置信号延迟小于5.5%,该方法可用于同步器作动电机霍尔传感器的故障诊断和相应的容错控制。
关键词:干式DCT;同步器无刷直流作动电机;模糊滑模观测器;故障诊断;容错控制
前言
干式双离合器自动变速器同步器作动电机为无刷直流电机,其具有功率密度高、效率高、速度范围宽、起动转矩大和过载能力强等诸多优点,相比于有刷直流电机,无刷直流电机以电子换向器取代了机械换向器,减少了机械摩擦,提高了电机寿命,有效地避免了机械换向带来的火花、噪声和无线电干扰等问题[1]。 DCT 奇偶挡位分别连接不同离合器,其换挡过程包含特殊的预选挡过程。 而DCT 车辆平稳换挡的关键在于同步器的精确控制,作动电机安全可靠工作是保证同步器控制精度的前提。 在选挡过程中,若同步器作动电机发生故障,不仅会影响电机本体和同步器使用寿命,还有可能导致选挡失败,影响发动机动力传递。 在选挡过程中对同步器作动电机进行实时故障诊断,并针对故障情况制定相应的容错控制策略,保证DCT 车辆在同步器作动电机发生故障后继续安全运行,对于提高行车安全具有重要意义。
车辆运行工况复杂多变,随着时间的推移,换挡次数的累加会导致同步器作动电机发生故障的概率逐渐增大。 在车用环境中电机有可能出现各种故障模式,按照故障发生的部位可分为传感器故障、逆变器故障和定子绕组故障等。 传感器故障的主要表现形式是霍尔位置传感器故障。 霍尔位置传感器结构简单且成本低廉,基于霍尔位置传感器的转子位置测量在无刷直流电机中得到了广泛的应用[2]。 考虑到霍尔位置传感器信号易受温度、湿度、灰尘和电磁干扰等环境影响而不能正常工作,加之维修不便,且其故障将直接导致电机位置反馈失效,进而引起剧烈的机械振动和异常的大电流,造成换挡作动系统的进一步损坏[3]。 因此,文中将结合干式DCT 同步器作动电机,探讨其霍尔位置传感器故障诊断与解析冗余方法。
Tashakori 等[4]基于电机线电压的离散傅里叶变换分析方法对霍尔位置传感器进行故障诊断,然而该方法计算过程复杂且准确度较低。 Scelba等[5-6]通过分析霍尔位置传感器在正常和故障工况下的输出信号特征,总结出了一种基于霍尔状态序列监测的故障诊断方法,该方法可有效诊断霍尔位置传感器故障,但检测周期较长,且容错过程中须存储大量的霍尔状态序列信息,因此效率较低。 Dong等[7]基于电机转向估计和霍尔位置信号重建的故障诊断方法,有效诊断出了单个或两个霍尔位置传感器故障,以减小故障发生瞬间系统输出性能的波动,但由于其重构的霍尔信号与正常霍尔信号并未解耦,针对因供电或接地出现问题而导致霍尔传感器均出现故障的情况,该方法无法重构霍尔信号。 温嘉斌等[8]提出利用神经网络方法对霍尔传感器换相信号的提前、延时和缺失等情况进行故障诊断,但并未具体到某个霍尔传感器是否发生故障。 傅安琪等[9]提出了基于霍尔信号变化规律的霍尔传感器故障诊断方法,由于霍尔传感器故障较为复杂,针对每一种故障需要开发相应的诊断方法,较为繁琐。
本文中针对干式DCT 同步器作动电机霍尔位置传感器故障,提出并设计了模糊滑模观测器对该电机的线反电动势进行了实时估计,结合线反电动势与霍尔位置信号之间的对应关系,实现了霍尔位置信号的重构和解析冗余。 根据重构霍尔位置信号与实际霍尔位置信号之间的偏差,对同步器作动电机霍尔位置传感器进行有效故障诊断和解析冗余。
1 同步器作动电机仿真模型搭建与验证
图1 所示为无刷直流电机驱动系统示意图,其主要由电机、功率逆变电路、转子位置检测和驱动电路组成。 功率逆变电路由6 个MOSFET 组成,实现电压直流交流的变换;驱动电路为功率逆变电路提供驱动信号;转子位置检测为驱动电动提供正确的换相信息。
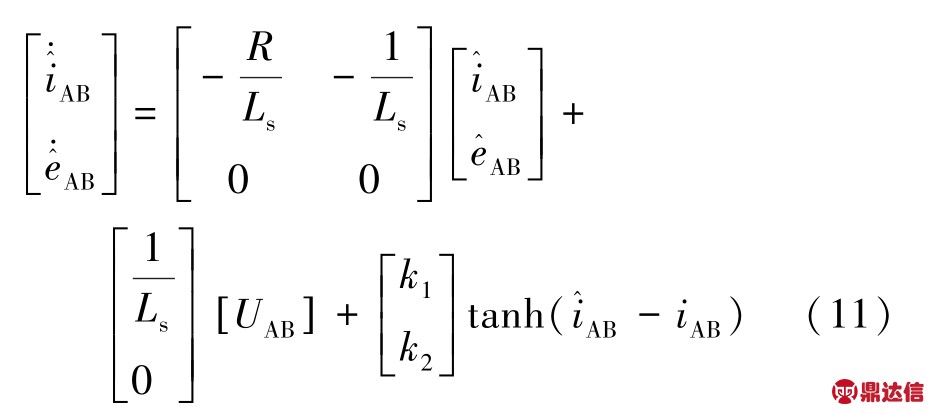
图1 无刷直流电机驱动系统
文中基于 MATLAB/Simulink 仿真平台,利用Simscape 库中相关模块搭建无刷直流电机仿真模型[10]。 为验证所搭建的无刷直流电机仿真模型的准确度,须对其进行模型验证。 根据图1 中所搭建的无刷直流电机仿真模型,在12 V 供电电压下,对电机施加不同的负载并进行仿真,结果如表1 所示。
表1 不同负载下无刷直流电机仿真结果
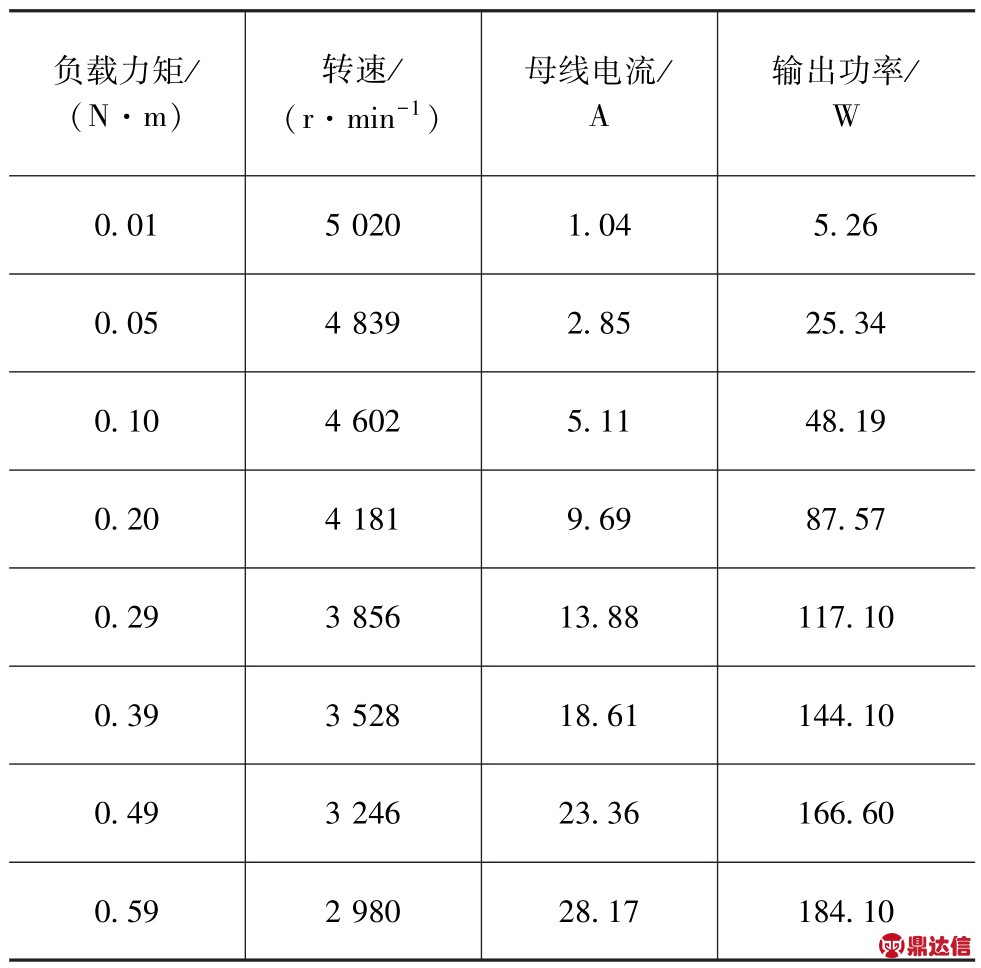
根据表1 中仿真测试数据,分别得到电机转速、母线电流和电机功率随负载力矩变化的散点图,并对其进行数据拟合。 图2 所示为电机供应商提供的试验测试数据与文中仿真测试数据的对比结果。
从图2 可知,在不同负载下,仿真得到的电机转速、母线电流和电机功率与实际试验测试的结果误差较小,数据拟合出的曲线变化趋势一致性好,基于MATLAB/Simulink 平台搭建的无刷直流电机仿真模型与实际试验测得的结果误差在8.0%以内,具有一定的准确度,为后续仿真验证无刷直流电机故障诊断算法奠定了模型基础。
2 同步器作动电机故障诊断
同步器作动电机在换挡过程会频繁启停和堵转,有可能致使电机出现高频振动和温度升高,从而引发霍尔位置传感器出现的霍尔器件磁灵敏度漂移、半导体材料失效、负载电流突变等现象,此外,变速器振动的机械冲击也有可能引发霍尔位置传感器定位不平衡[4,11],导致霍尔位置信号波动甚至缺失。任意一路霍尔位置信号的波动或缺失将会导致电机驱动性能的下降甚至停机[12]。 因此,对霍尔位置传感器进行实时诊断对于提高换挡系统可靠性非常重要,文中通过重构霍尔位置信号以对霍尔位置传感器进行诊断。

图2 无刷直流电机仿真结果与测试结果对比
2.1 无刷直流电机霍尔位置信号重构策略
在基于反电动势过零检测法的无刷直流电机无位置传感器控制中,通常根据未导通相绕组反电动势的过零点来确定无刷直流电机转子的位置信息,进一步确定6 个换相时刻,图3 所示为反电动势与霍尔位置信号间对应关系示意图。
由图3 可见,电机相反电动势的过零点与霍尔位置信号的换相点未完全对应,电机相反电动势过零点提前于霍尔位置信号换相点30°电角度,若根据电机相反电动势来重构霍尔位置信号,会存在30°电角度的相移角。 然而,线反电动势的过零点与霍尔位置信号的换相点相对应,不存在相移角的问题,且线电压比相电压更容易测量,因此可以通过实时估计无刷直流电机的线反电动势,根据线反电动势的过零点来实时重构电机的霍尔位置信号。 当线反电动势为正值时,相对应的重构霍尔位置信号为1;当线反电动势为负值时,相应的重构霍尔位置信号为0。 线反电动势的过零点对应无刷直流电机的换相点。
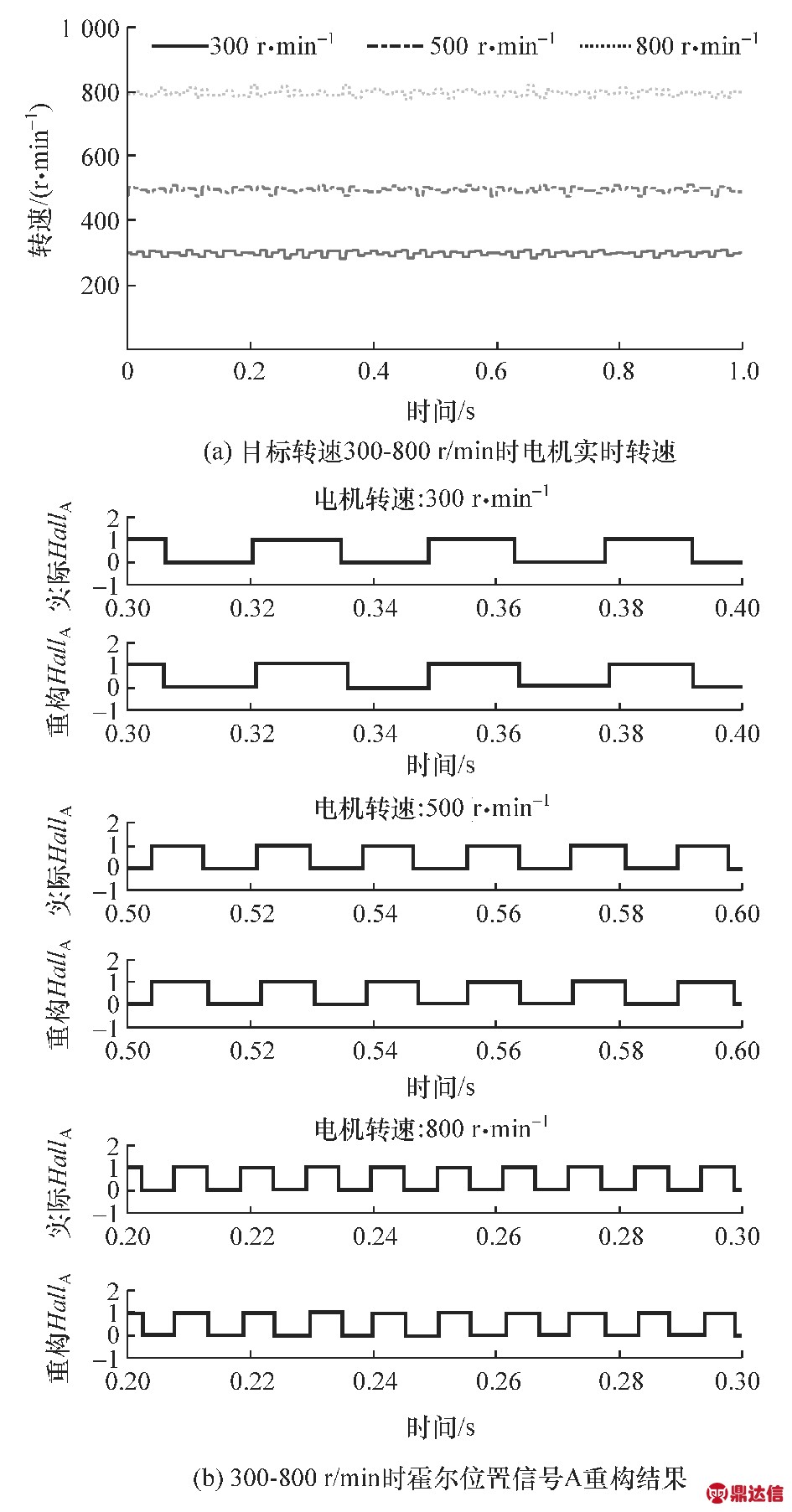
图3 反电动势和霍尔位置信号示意图
2.2 基于模糊滑模观测器的无刷直流电机线反电动势估计
2.2.1 无刷直流电机等效数学模型
由于无刷直流电机的磁通呈梯形波分布,转子d-q 轴参考系模型对其并不适用,故采用相变量数学模型更为适合。 在建立无刷直流电机等效数学模型前,做如下假设[13]:
(1)忽略齿槽效应,定子绕组采用Y 连接,三相绕组完全对称且呈集中分布;
(2)忽略磁路饱和,不计涡流、磁滞损耗等杂散损耗;
(3)功率逆变电路中的功率晶体管和续流二极管都具有理想的开关特性;
(4)忽略电枢反应,气隙磁场分布近似为平顶宽度为120°电角度的梯形波;
(5)转子的磁阻不随转子的位置变化而变化,各相的自感、互感完全相等。
基于上述假设,利用图1,并根据基尔霍夫定律可得各端电压数学模型为
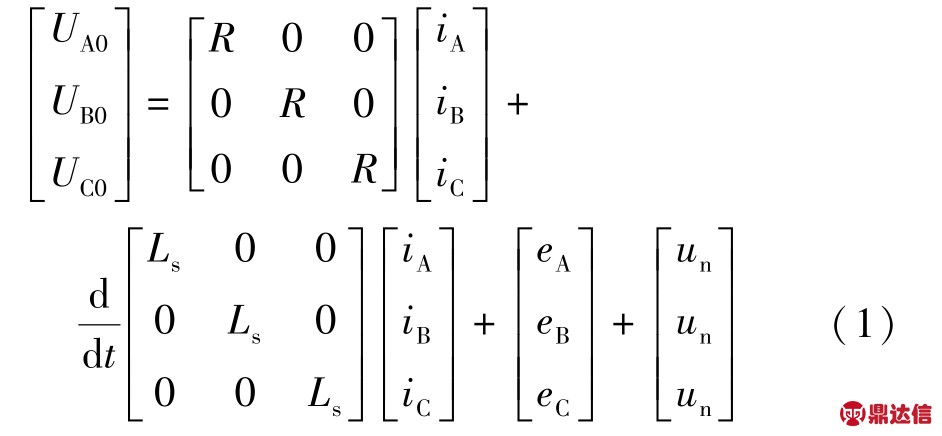
式中:UA0、UB0、UC0 分别为电机 A、B、C 3 相对地电压;R 为定子每相绕组的电阻;iA、iB、iC 分别为电机A、B、C 3 相电流;Ls 为定子等效电感,Ls =L-M,L 为定子每相绕组的自感,M 表示任意两相绕组之间的互感;eA、eB、eC 分别为 A、B、C 3 相绕组的反电动势,un 为电机中性点对地电压。
电机的电磁转矩方程为

式中:p 为电机的极对数;ωr 为电机的电角速度。
电机每相绕组反电动势的峰值正比于电机的角速度,即

式中Ke 为反电动势系数。
考虑到无刷直流电机工作在任意时刻,忽略续流,均为2 相绕组导通、1 相绕组关断,尽管每相绕组的反电动势为梯形波,相电流为方波,但导通2 相绕组中的反电动势和相电流之和始终保持不变。 因此,电机的电磁转矩方程可表示为
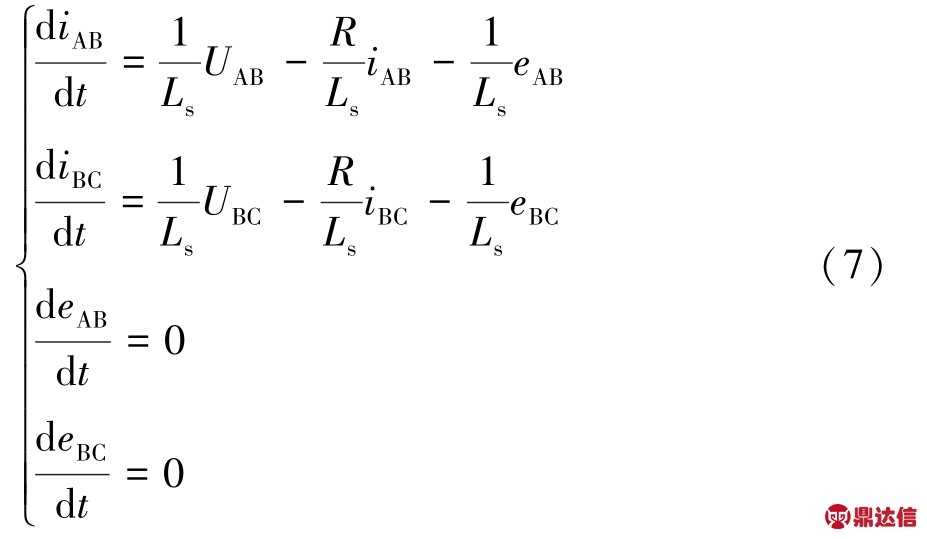
式中:KT 为转矩常数;Id 为逆变器直流侧母线电流。
电机的动力学方程为

式中:J 为电机等效转动惯量;B 为电机的等效阻尼系数;TL 为电机的负载;ωm 为电机的机械角速度。
2.2.2 无刷直流电机线电压模型的建立
由2.1 节可得,通过实时估计无刷直流电机反电动势可实时重构出霍尔位置信号,文中采用滑模观测器估计无刷直流电机的反电动势,设计反电动势滑模观测器的前提是构建合适的无刷直流电机数学模型。 在2.2.1 中,根据基尔霍夫定律得到了无刷直流电机端电压模型,但由于中性电压难以测量和电机本身并未引出中性点,因此须将式(1)改写为如下无刷直流电机线电压模型:
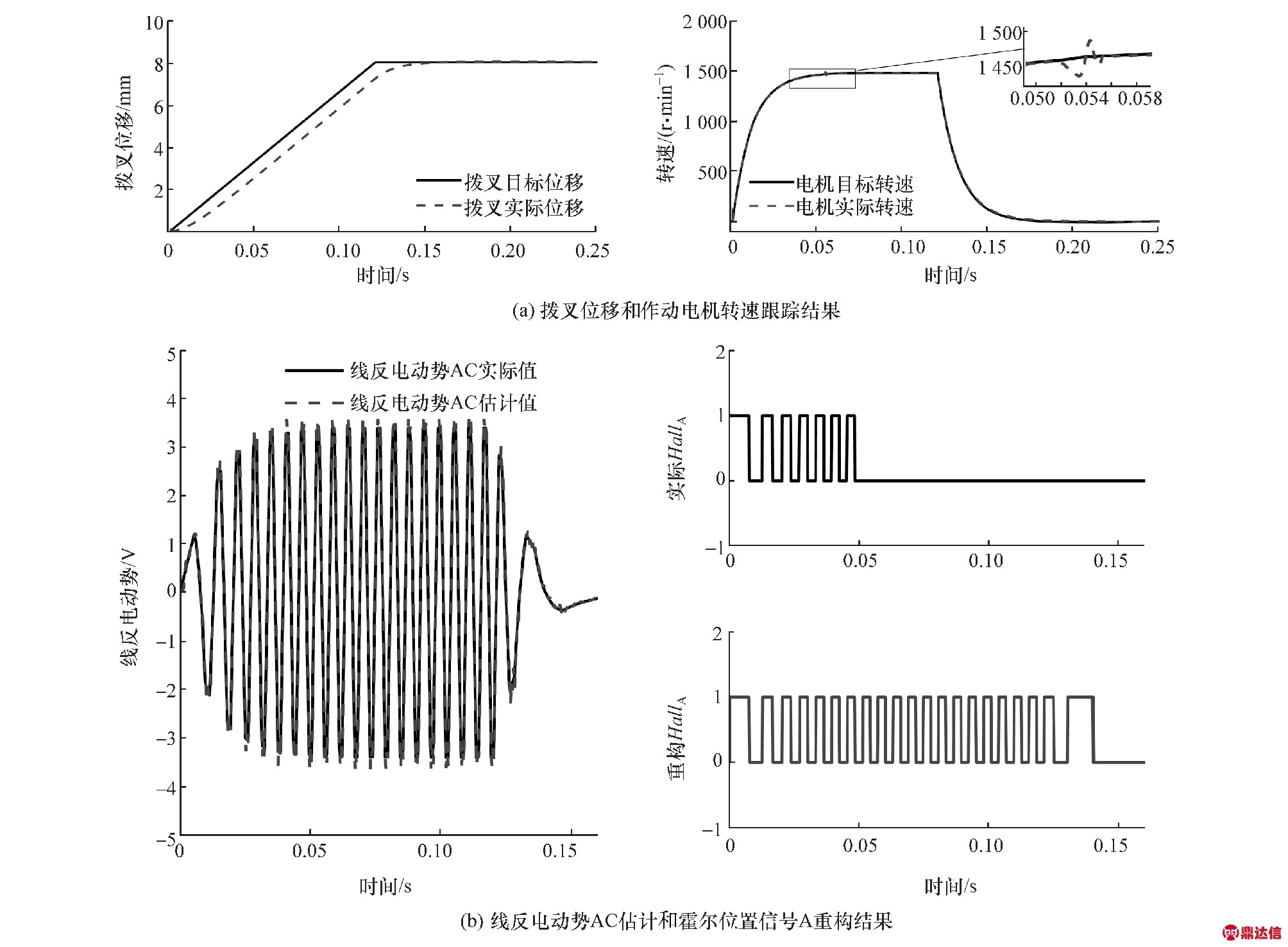
式中:UAB、UBC、UCA 分别为线电压;eAB、eBC、eCA 分别为线反电动势;UAB = UA0-UB0,UBC = UB0-UC0,UCA =UC0-UA0,iAB = iA-iB,iBC = iB-iC,iCA = iC-iA,eAB = eA-eB,eBC =eB-eC,eCA =eC-eA。
根据式(6),无刷直流电机线电压模型本质上是两个线性无关的1 阶微分电流方程。 当采样周期明显小于电气时间常数和机械时间常数时,可近似认为反电动势在每个采样周期内是恒定的[14-15],因此式(6)可进一步写成如下形式:
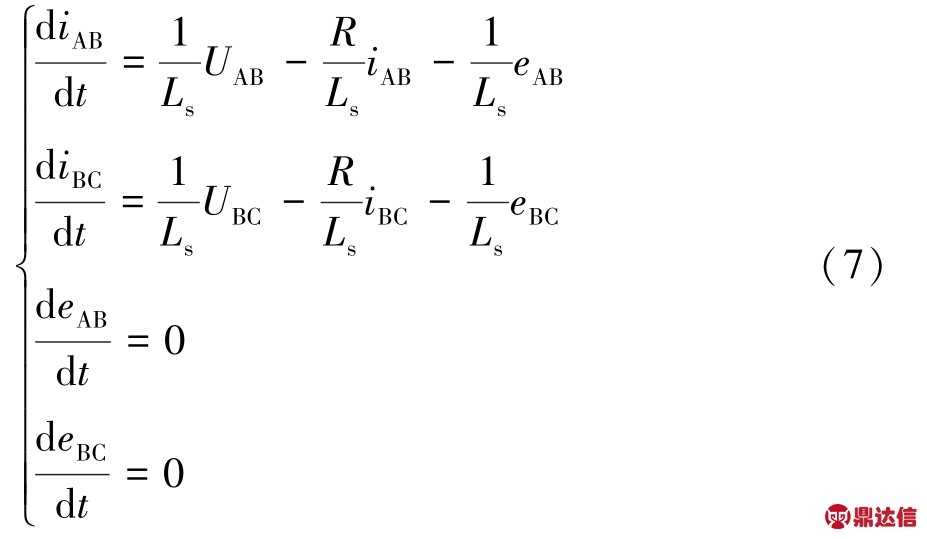
其中 eAB + eBC + eCA =0
根据式(7)可知,线电动势可直接通过线电压和相电压差计算得到。 但由于电流微分项的存在,开环计算会造成很大的计算误差,因此,须采用观测器对线反电动势进行闭环估计,以减小电流微分项对计算误差的放大,进而提高线反电动势的估计精度。
2.2.3 线反电动势滑模观测器的设计
若将线反电动势视为状态变量,线反电动势的计算问题实质上就是状态观测问题,可采用状态观测器对无刷直流电机的电动势进行观测。 滑模观测器是在龙伯格观测器的基础上,引入滑模控制理论的一种观测方法[16]。 采用传统的符号函数作为状态误差反馈的滑模观测器方程为

式中:A、B 分别为系统矩阵、输入矩阵;K 为滑模增益矩阵;sgn(·)表示符号函数。
以AB 相为例,根据式(7)将电机的线电压作为系统的输入,相电流差和相反电动势作为系统的状态变量,相电流差作为系统的输出,整理可得状态空间表达式:

其中

由于符号函数sgn 存在不连续性,容易造成系统高频的抖振。 因此,本文中采用具有光滑连续特性的双曲正切函数代替符号函数[17],如式(10)所示,系统偏差较大时,运动点尽快地运动到滑模面,当系统偏差较小时,放慢运动点的速度,以减小抖振,从而提高滑模观测器的品质。

由式(7)~式(10),线反电动势滑模观测器为
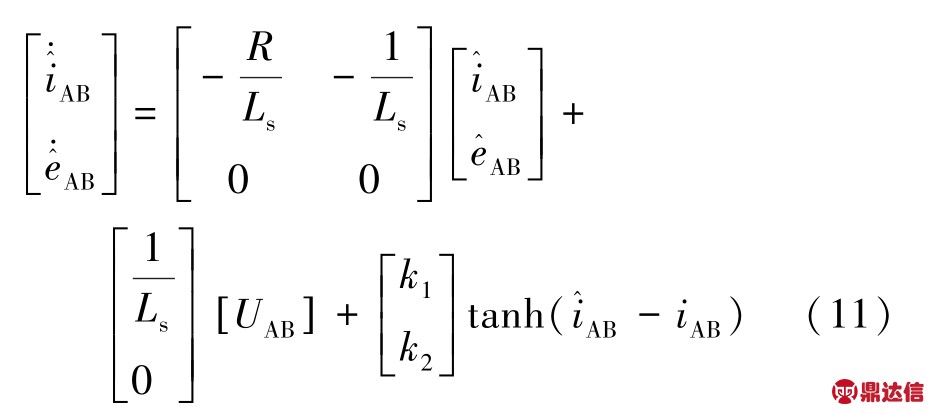
选取相电流差的误差为滑模面:

将式(11)减式(9),可得观测误差方程为
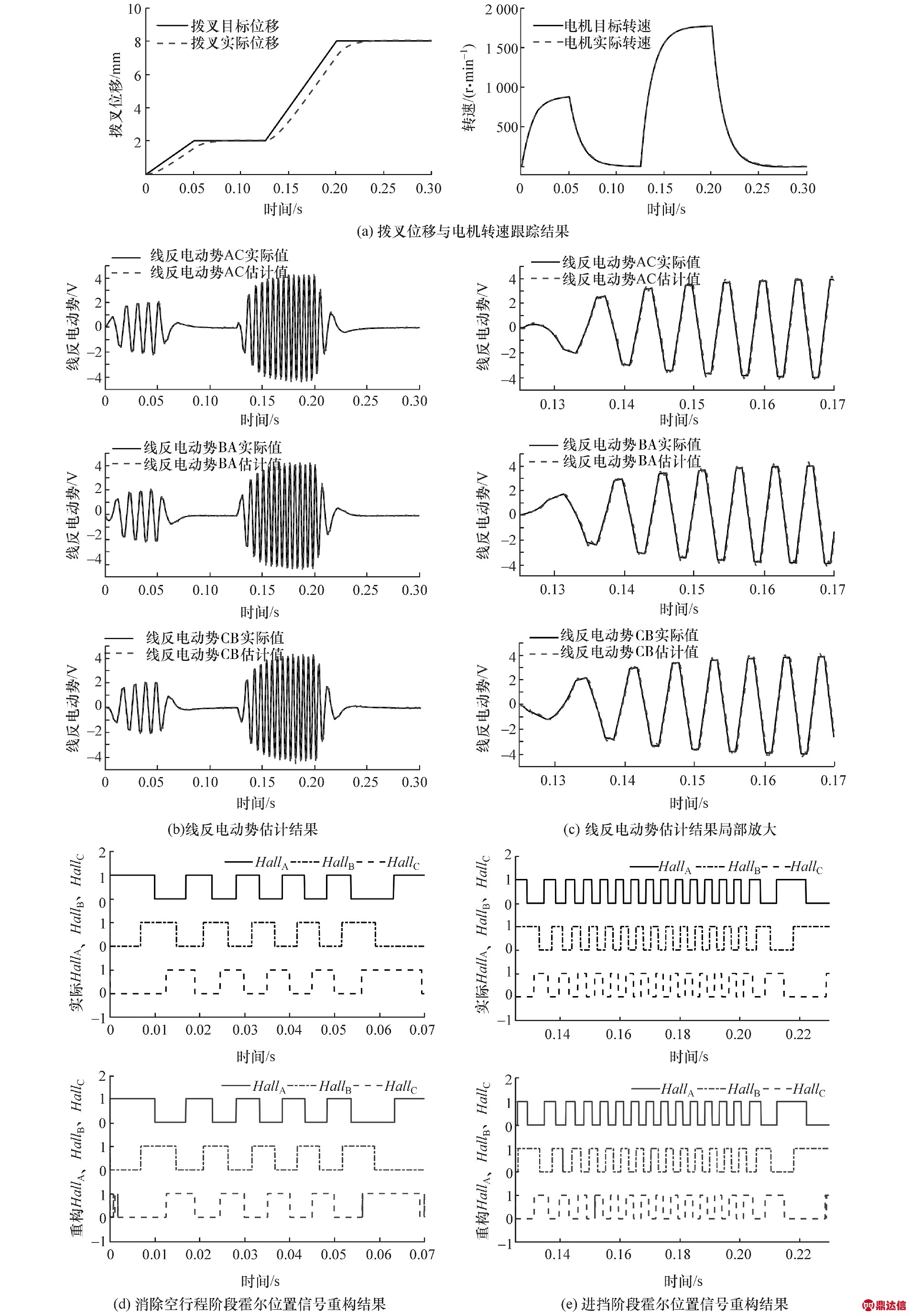
滑模观测器进入滑模状态的条件为

将式(13)代入式(14)中进行不等式求解,可得

由于εi 与双曲正切函数符号一致,且始终第1项恒小于零,根据不等式原理,当满足式(16)时,。

根据式(16),观测器进入滑模状态的条件为

当系统进入滑模状态时,根据等效控制原理,线电流差的误差及其导数满足以下方程:

根据式(13)和式(18)可得

取李雅普诺夫函数:

对式(20)进行求导,并代入式(19),可得

当<0 时,无刷直流电机的线反电动势误差逐渐收敛到0,因此需要满足

2.2.4 模糊控制滑模增益设计
式(17)和式(22)中给出了滑模增益系数的取值范围,然而无刷直流电机的反电动势随转速的变化而变化,转速高时,反电动势大,当转速低时,反电动势小。 在满足增益系数的取值条件下,为满足不同转速下滑模观测器的稳定条件并提高滑模观测器的品质,文中选用模糊控制系统设定滑模增益系数。
利用梯形隶属度函数确定各参数隶属函数曲线,并构建系数k1 和k2 模糊控制规则,如表2 和表3 所示。 模糊控制器系统的输入为转速N 和转速变化率RN,系统的输出为滑模增益系数k1 和k2。 速度论域[0, 300]对应于模糊子集[ZR(零), VS(很小), S(小), M(中), L(大), VL(很大)],速度变化率论域[-1000, 1000]对应于模糊子集[NL(负大), NS(负小), ZR(零), PS(正小), PL(正大)],系数k1 论域[-20000, 0]对应于模糊子集[NVL(负很大), NL(负大), NM(负中), NS(负小), NVS(负很小), ZR(零)],系数 k2 论域[0, 20000]对应于模糊子集[ZR(零), PVS(正很小), PS(正小),PM(正中), PL(正大), PVL(正很大)]。
表2 k1 模糊规则表
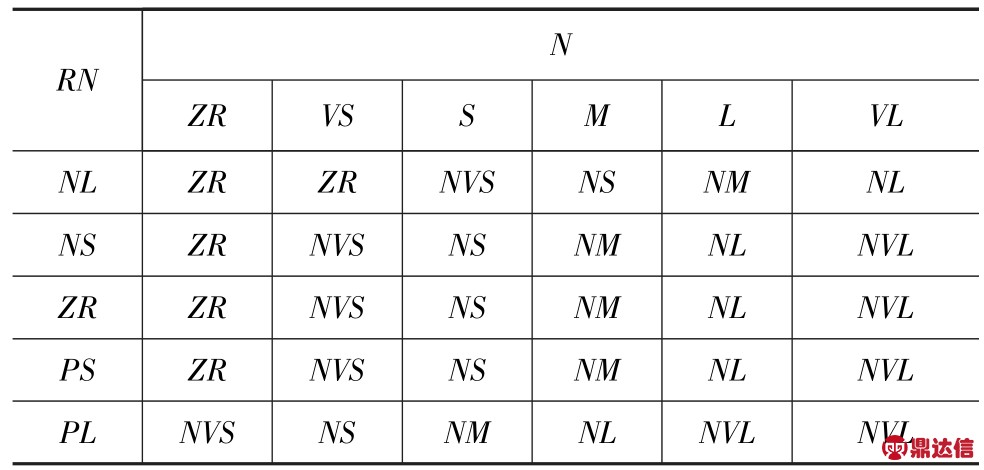
表3 k2 模糊规则表

3 离线仿真与结果分析
基于上述在MATLAB/Simulink 平台上搭建的同步器作动电机仿真模型,对所提出的基于模糊滑模观测器同步器作动电机线反电动势估计和霍尔位置信号重构算法进行验证。 仿真架构如图4 所示,仿真结果如图5 所示。
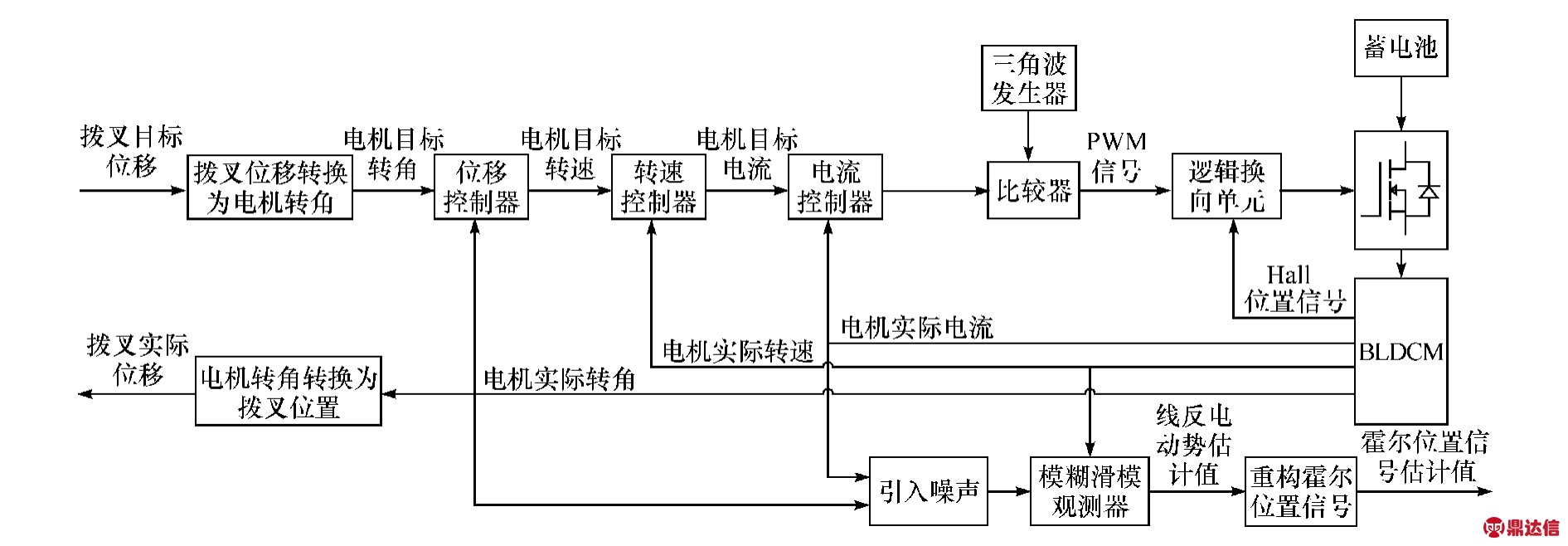
图4 同步器作动电机线反电动势估计及霍尔重构信号估计仿真架构
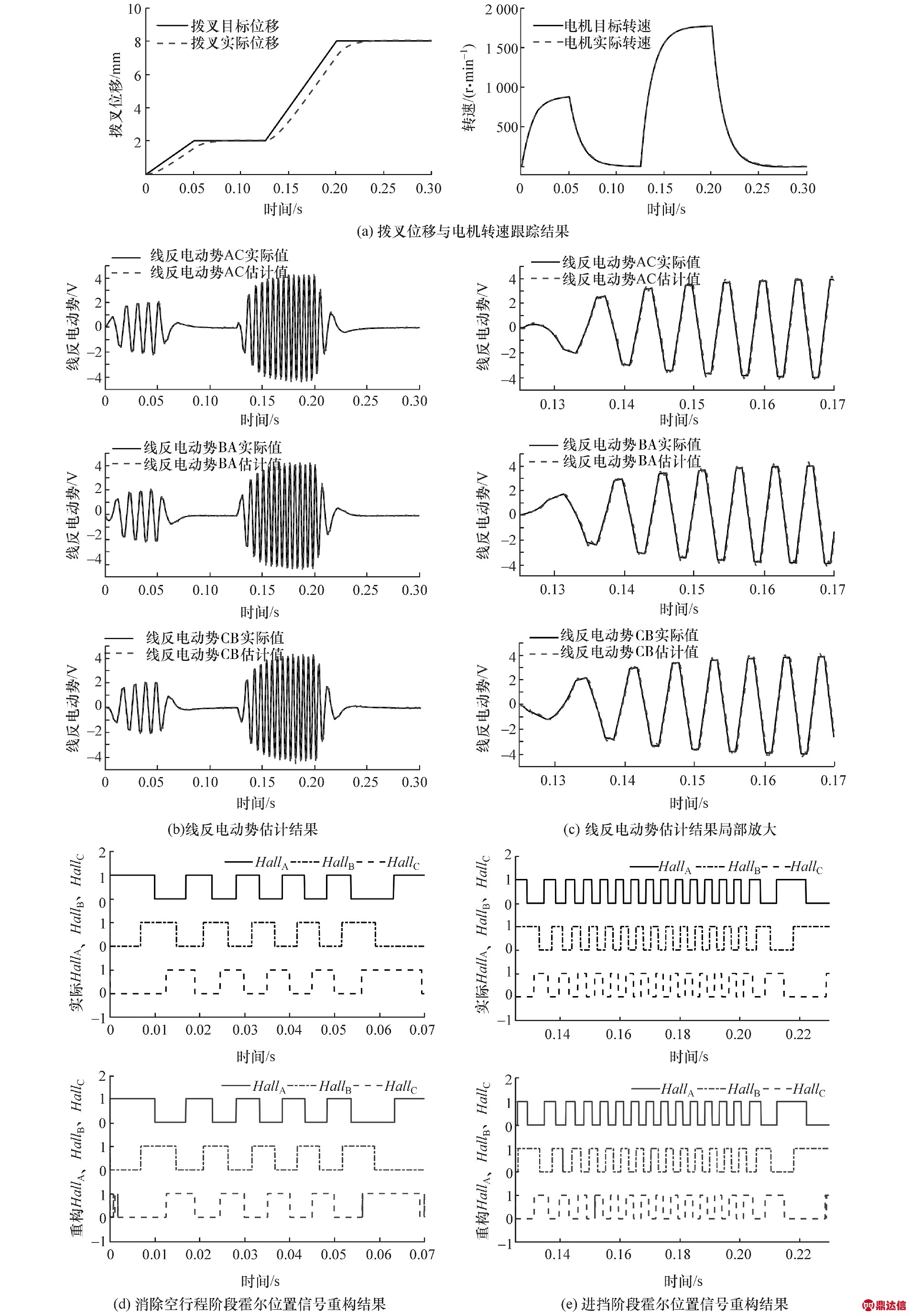
图5 基于模糊滑模观测器同步器作动电机线反电动势估计及霍尔位置信号重构仿真结果
由图5(a)拨叉位移跟踪结果可以看出,在给定的同步器拨叉目标位移下,所设计的同步器作动电机三闭环控制方法可使同步器拨叉在消除空行程阶段、同步阶段以及进挡阶段较为准确地跟踪目标位移。 由图5(a)作动电机转速跟踪结果可以看出,三闭环中的转速环可使作动电机精确地跟踪位移控制器所决策的电机目标转速。
由图5(b)中电机线反电动势的估计结果可以看出,在给相电流和线电压引入白噪声的情况下,所采用的模糊滑模观测器可较为精确地估计并跟踪电机的线反电动势。
由图5(c)中电机线反电动势估计结果的局部放大图中可以看出,在电机转速由0 开始运转时,线反电动势的估计结果相对较差,这是因为此时电机正在启动,观测器处于调整阶段,之后线反电动势的估计值能较好地跟踪上真实值,仅在线反电动势的幅值处出现轻微的抖动,由于文中关注的是线反电动势的过零点,所以线反电动势的幅值处出现轻微的抖动并不影响霍尔位置信号重构的结果。
由图5(d)和图5(e)中同步器消除空行程阶段和进挡阶段同步器作动电机霍尔位置信号重构结果可以看出,文中所设计的估计算法可实时准确地重构出电机的三路霍尔位置信号,仅在电机启动时出现轻微误差,待转速上升后,重构信号很快地跟踪上实际信号,重构信号的延迟在一个周期的1.5%以内。
为进一步验证模糊滑模观测器估计电机线反电动势和重构霍尔位置信号的有效性,在同步器摘挡阶段,将霍尔位置信号A 置0,以模拟霍尔位置传感器长时间不换相故障。 当检测到故障发生后,利用重构霍尔位置信号A 对实际霍尔位置信号A 进行校正,并向逻辑换向单元发送信号。 图6 所示为霍尔位置传感器发生故障后电机线反电动势估计和霍尔位置信号重构结果。
由图6(a)拨叉位移跟踪结果和作动电机转速跟踪结果可以看出,当检测到霍尔位置传感器发生故障后,采用观测器重构的霍尔位置信号对故障的霍尔位置信号进行校正,电机进入半无位置传感器控制状态,拨叉可较好地跟踪目标位移且没有出现抖动,电机转速在0.05 s 霍尔位置传感器发生故障后出现轻微抖动,之后随着观测器对实际霍尔位置信号的校正,电机转速跟踪恢复正常,转速跟踪效果较好。
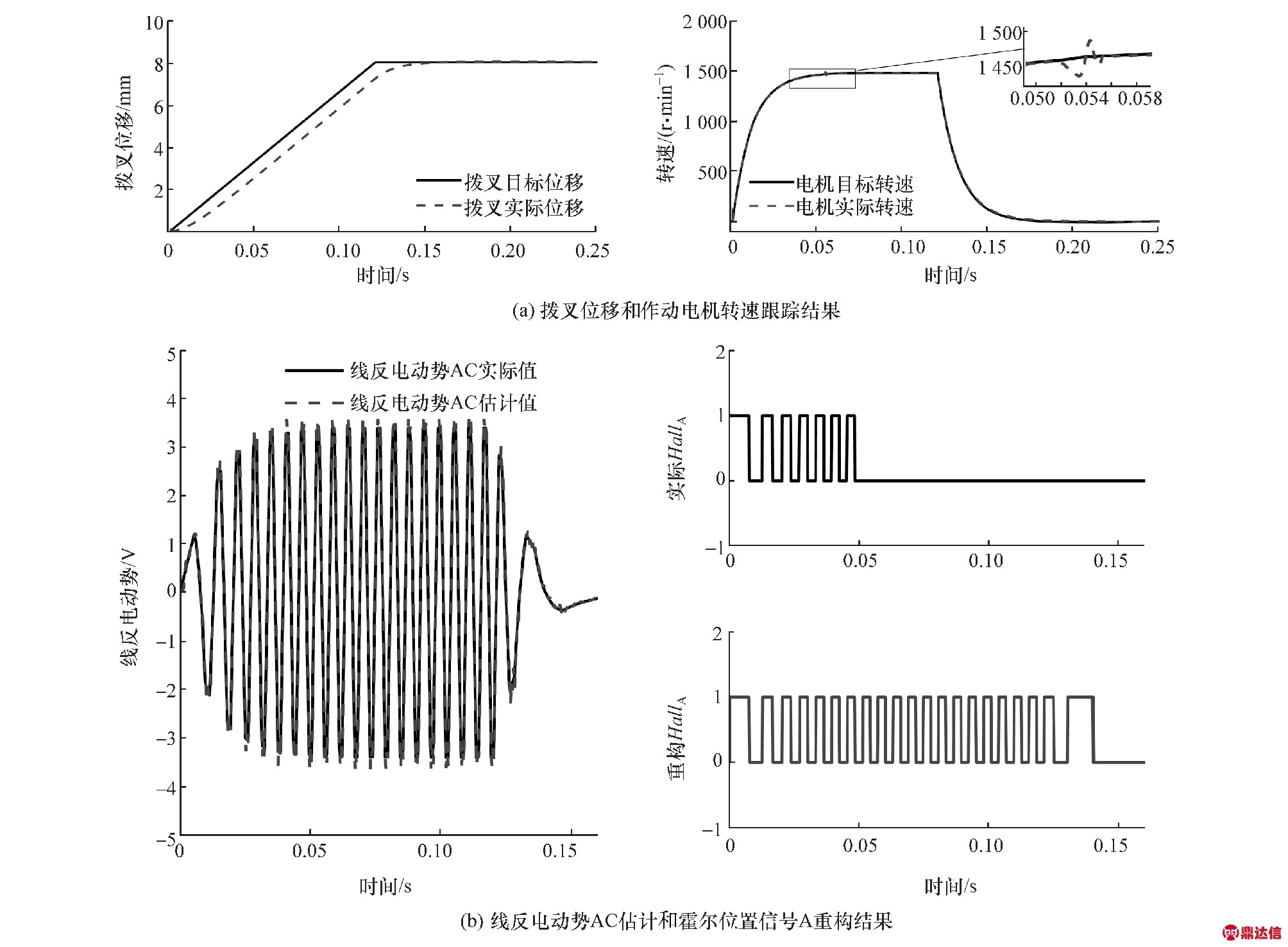
图6 霍尔位置传感器发生故障后同步器作动电机线反电动势估计和霍尔位置信号重构仿真结果
由图6(b)线反电动势估计和霍尔位置信号重构的结果可以看出,在霍尔位置传感器发生故障前和故障后,观测器能较为精确地估计并跟踪电机的线反电动势。 通过对比重构的霍尔位置信号和实际的霍尔位置信号,可检测出霍尔位置传感器发生长时间不换相故障。
综上所述,模糊滑模观测器可对电机霍尔位置传感器故障进行有效的诊断,并能对其故障信号进行有效的校正。
4 试验与结果分析
为进一步验证所设计故障诊断方法的有效性,自主设计并搭建了同步器作动电机传感器故障诊断试验平台,如图7 所示。
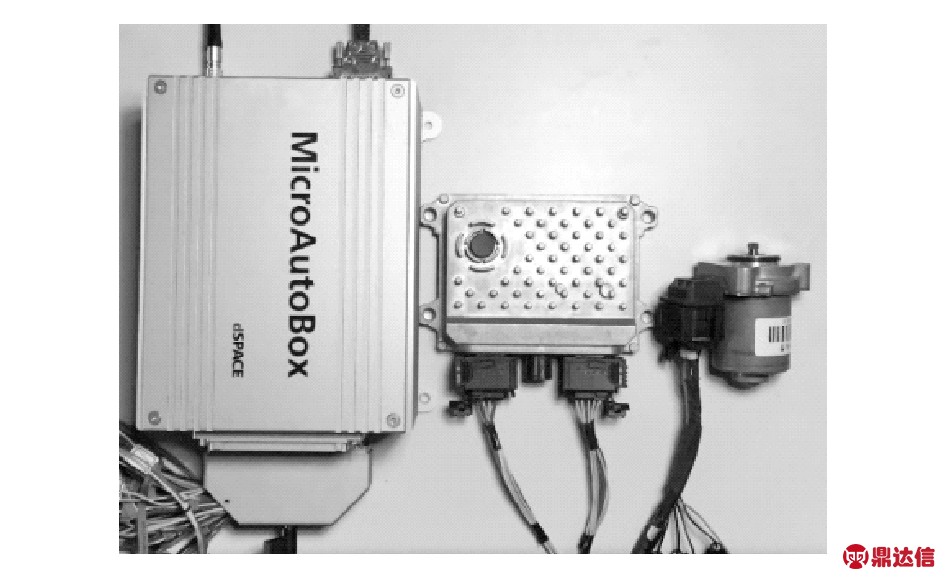
图7 同步器作动电机传感器故障诊断试验平台
试验平台的硬件部分由MicroAutoBoxⅡ、E9IHL-12 无刷直流电机及其控制器组成。 试验过程中,以MicroAutoBoxⅡ为核心控制器,通过CAN 总线发送给电机控制器转速请求信号,同时电机控制器实时反馈电机的实际转速,MicroAutoBoxⅡ分别通过霍尔电流传感器、取样电阻采集电机三相电流信号、三相对地电压信号。
由图8(b)可见:当电机转速为300 r/min 时,重构的霍尔位置信号延迟为350 μs,重构信号的延迟在一个周期的1.5%以内;电机转速为500 r/min 时,重构的霍尔位置信号延迟为500 μs,重构信号的延迟在一个周期的2.8%以内;当电机转速为800 r/min 时,重构的霍尔位置信号延迟为600 μs,重构信号的延迟在一个周期的5.5%以内。
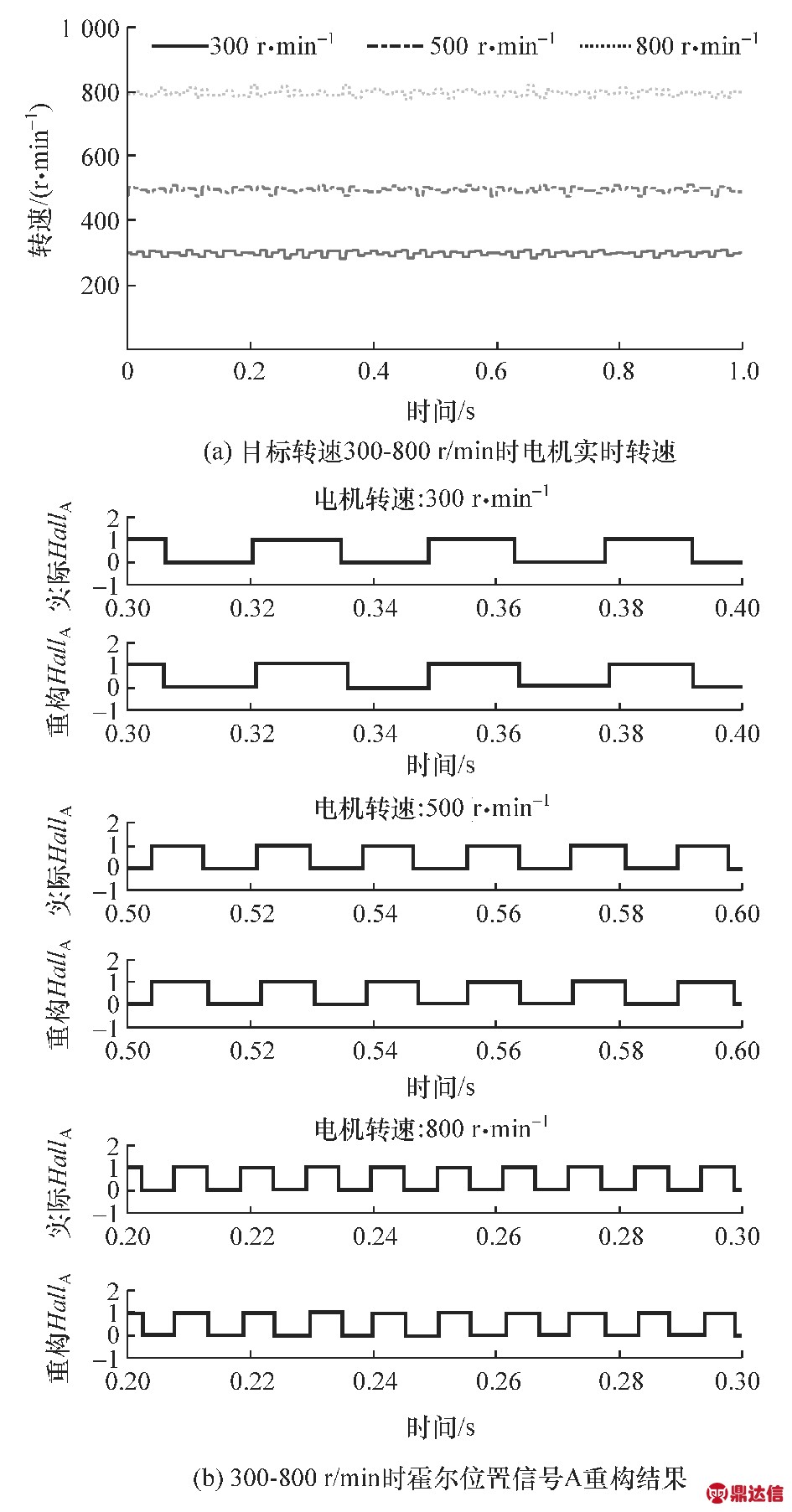
图8 基于模糊滑模观测器的无刷直流电机霍尔位置信号重构试验结果
5 结论
(1)基于无刷直流电机反电动势与霍尔位置信号之间的对应关系,并提出了基于模糊滑模观测器的无刷直流电机线反电动势估计和霍尔位置信号重构方法,根据重构结果可实现对无刷直流电机霍尔位置传感器的故障诊断与解析冗余。 在MATLAB/Simulink 平台上进行离线仿真验证,结果表明,所提出的反电动势估计和霍尔位置信号重构方法可精确估计电机的线反电动势并对霍尔位置信号进行有效重构,重构的霍尔位置信号延迟在一个周期的1.5%以内,且在单个霍尔位置传感器发生故障后可有效地对同步器作动电机霍尔位置传感器进行主动容错控制。
(2)自主设计搭建了同步器作动电机霍尔传感器故障诊断试验平台,对基于模糊滑模观测器的无刷直流电机线霍尔位置信号重构方法进行了试验验证,结果表明,在电机不同的运行转速下,该方法可较准确地重构出霍尔位置信号,由于模型参数的不确定性等因素,重构的霍尔位置信号延迟在一个周期的5.5%以内。
仿真与试验结果对比表明,试验结果中的重构霍尔信号延迟高于仿真结果中的重构霍尔信号延迟,但延迟仍较短,且所提出的方法能较为准确地重构出霍尔位置信号,可满足实际应用过程中对同步器作动电机霍尔位置传感器的故障诊断与解析冗余需求,进一步验证了该方法在实际应用过程中的实时性与有效性,为干式DCT 车辆行驶过程中同步器作动电机出现霍尔传感器故障提供了解决方法,保证车辆稳定安全行驶。