摘 要: 采用数值模拟方法研究液压滑阀内的高压空化流动特性,分析了进口压力的改变对液压滑阀内的高压空化流动特性的影响。结果表明:在高压入口条件下,液压滑阀节流槽区域内及其出口处存在多个空化区域。随着进口压力的增加,液压滑阀内的空化流场会从稳态向非稳态转变;当液压滑阀内的空化流场处于非稳态时,其空化流动结构的变化具有明显的周期性,可明显区分出空化初生、发展和衰退阶段。进口压力越高,节流槽出口处的空化区域和强度越高,空化流动周期性变化的时间越短,且会出现云空化脱落现象。
关键词: 液压滑阀;空化流动;数值计算;节流槽;空化模型
引言
液压滑阀是液压系统中的重要控制元件,在中、高压系统中的应用广泛。在高压工况下,滑阀内介质的流动状态对其操作性能和可靠性具有重要影响。由于液压滑阀操作频繁、内部流道结构多变,且高压液压油在流经节流槽时易发生空化现象,导致其内部流动状态十分复杂,难以进行理论求解。
随着计算流体动力学(Computational Fluid Dynamics,CFD)理论和计算方法的发展,数值模拟技术被大量应用于液压滑阀内流场特性的研究。柯坚等[1]计算得到了不同阀口开度、节流槽深度和工作压差下液压滑阀内的高速射流区域。郑长松等[2] 计算获得了滑阀不同开度的流场特性与稳态液动力变化规律。杨秀萍等[3]发现液压滑阀阀口处存在附壁流和自由流,且阀口射流角、滑阀流量系数直接受阀口开度的影响。由于液压滑阀的阀芯操作频繁,在高压、小开度工况下极易产生空化现象,因此数值模拟技术也进一步用于对液压滑阀内空化流场特征的分析研究。冀宏等[4]对V形节流阀口瞬态空化特性进行数值研究,分析了背压对阀内空化现象的抑制作用。孙泽刚等[5]采用动网络技术,研究了V形节流槽楔形角和夹角对液压滑阀内空化流动的影响,并获得了小开度和大开度条件下节流槽空化发生的位置和区域。王辉等[6]对锥形阀口滑阀内流场进行了数值分析,提出可通过改变阀口开度来抑制阀内的空化和旋涡,以降低滑阀的压降和能耗。上述空化流场的建模和计算过程中采用了二维或三维对称简化模型,且入口压力较低,难以准确描述液压滑阀内介质的相变和流动状态,高压条件滑阀内的空化流动特性仍有待于进一步研究。
本研究采用数值计算的方法,研究液压滑阀在高压条件下阀内的空化流动特征。在构建空化流动数学模型的基础上,分析在不同进、出口压差下,液压滑阀内部的高速射流区、空化区、旋涡区域,明确液压滑阀内云空化的时-空演化机制,为液压滑阀的耐空蚀优化设计提供理论参考。
1 研究方法
1.1 计算几何模型和网格划分
液压滑阀的几何结构和尺寸详见图1。采用ICEM CFD前处理软件对计算域进行网格划分。为保证进出口流动的充分发展,液压滑阀的进、出口管道长度设为180 mm(15D)。进出口长直管道和阀体部分均采用正六面体结构化网格,同时对液压滑阀节流槽附近的网格进行局部加密。网格总数约为400万。为排除计算域网格数量对计算结果的影响,采用增加网格数量的方法开展网格无关性验证。当液压滑阀的进口压力为40 MPa,节流槽长度L和宽度W分别为3 mm 和0.8 mm,开度k为1.5 mm时,分别采用400万、600万和800万的网格数量开数值计算。结果表明:液压滑阀内最高流速分别为182.0, 183.8, 184.5 m/s,相对误差小于2%,且液压滑阀内的云空化特征长度和变化周期等关键流体动力学参数并未发生明显改变。因此,认为数值计算满足网格无关性要求,在后续计算中采用400万的网格数量。
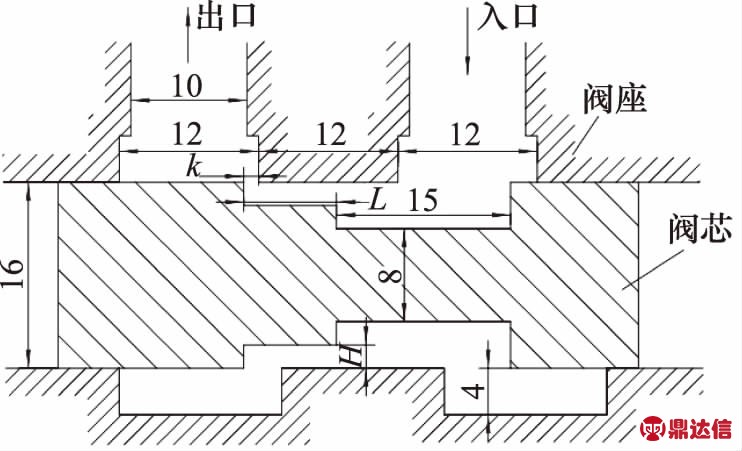
图1 液压滑阀的几何结构及尺寸
1.2 数值计算模型和方法
在数值计算过程中,由于阀内存在环形流,采用RNG k-ε双方程湍流模型构成封闭方程组,并利用有限体积法对控制方程组进行离散[7]。由于RNG k-ε湍流模型中的密度设为恒定,难以准确描述空化所在位置的实际流场变化情况,因此需要对模型中的混合密度和湍流黏度进行修正。修正后的混合密度和湍流黏度分别如式(1)和式(2)所示:
(1)
μt=f(p)Cμk2/ε
(2)
式中, ρv—— 气相密度
ρl —— 液相密度
ρ —— 混合密度,n=10,为经验常数
采用Z-Wart空化模型计算液压滑阀内高压液压油在流经节流口时发生的气液相变。该模型考虑了空化发生位置和蒸汽体积分数间的联系,忽略了空泡表面张力,同时修正了蒸汽的体积分数。Z-Wart空化模型的相间空化率方程如下:

(3)

(4)
式中, αnuc—— 成核位置体积分数
RB —— 空泡半径
Rc —— 蒸汽凝结率
Fcond —— 凝结系数
Fvap —— 蒸发系数
计算过程中,空化模型参数的取值按文献[8]中给出的数值。其中,空泡半径RB为0.5 μm,成核位置体积分数αnuc为0.09,蒸发系数Fvap为0.4,凝结系数Fcond为0.01。同时,假设液压滑阀及其进、出口管道内壁均为光滑壁面,忽略流动过程中的热量损失。液压滑阀进出口的边界条件分别设为压力进口和压力出口,液压滑阀的背压设为0.5 MPa。速度和压力的耦合计算采用SIMPLEC方法,压力、动量、湍动能和湍流耗散率均采用二阶迎风格式进行离散。
计算步骤如下:
(1) 计算稳态条件下阀内的高压液压油流场,当液压滑阀的进、出口质量流量差低于1×10-4 kg/s且出口压力监测点的变化小于3%时,进入步骤2;
(2) 在步骤1的基础上,加入Z-Wart空化模型,时间步长为1×10-5 s,单个时间步长内最大迭代次数为200次,通过时间步长的累积,计算非稳态条件下液压滑阀内的空化流场。
1.3 介质物性参数
计算过程中所采用介质为46号耐磨液压油,清洁度为NAS 7级。忽略油液中颗粒对于空化的影响。
液压油的密度为860 kg/m3,动力黏度为0.046 Pa·s,饱和蒸气压为600 kPa;发生气液相变后,气相的密度为1.2 kg/m3,动力黏度为1.2×10-3 Pa·s。
2 结果与分析
2.1 液压滑阀内部流场分析
以4种进口压力pin(10, 20, 30, 40 MPa)为例,分析液压滑阀内部流场。不同进口压力下滑阀内的压力分布云图如图2所示。
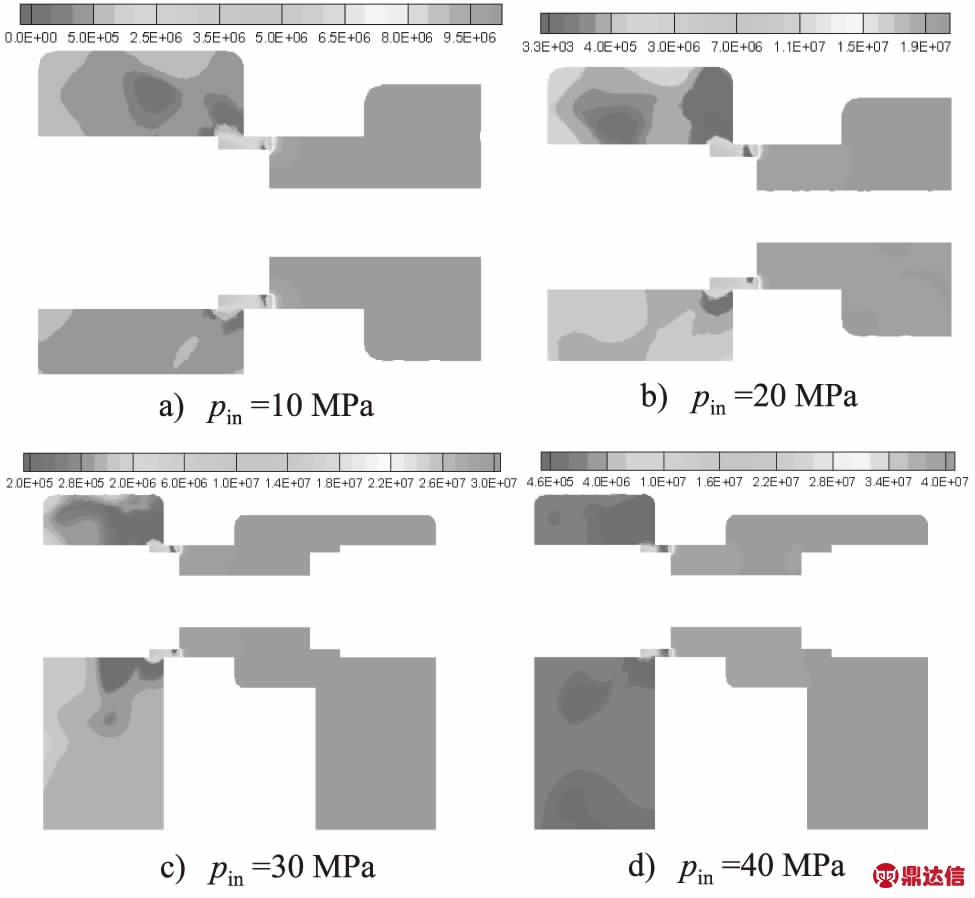
图2 液压滑阀内压力分布云图
分析可知,节流槽入口处的流道结构为缩流结构,高压液压油在流经节流槽口前,压力损失很小;在进入节流槽口后,由于流通面积迅速减小,流速迅速提高,压力降低。在节流槽的前端,出现了小面积的低压区域;随着液压油在节流槽内流动距离的增加,低压区域的后方出现了较为明显的压力恢复区;随着进口压力的增加,低压区的压力值相应降低;压力恢复区的压力值要比低压区域高1~2个数量级。
节流槽出口处的流道结构为扩张结构。在出口处及下游区域,出现了较大面积的低压区域。低压区域内压力值约为0.2~0.4 MPa,低于液压油的饱和蒸汽压(0.6 MPa),易发生空化现象。并且,随着进口压力的提高,低压区域的面积进一步扩大,且进一步向下游延伸。
综上可知,液压油在流经节流槽前后,流道变化十分剧烈,会导致流场压力的突变和较为复杂的流动结构。流动结构的不对称性会导致液压滑阀内的压力分布不均匀且存在多个低压区域。
图3为在不同进口压力下,液压滑阀内的速度分布云图和流线图。分析可知,在节流槽入口处流线骤然变窄,出现高流速区域。高流速区域贯穿整个节流槽区域,并向下游发展。随着液压滑阀进口压力的增加,阀内最高流速相应提高。当进口压力分别为10, 20, 30, 40 MPa,对应的最高流速分别为92.4, 133.0, 162.5, 182.0 m/s。
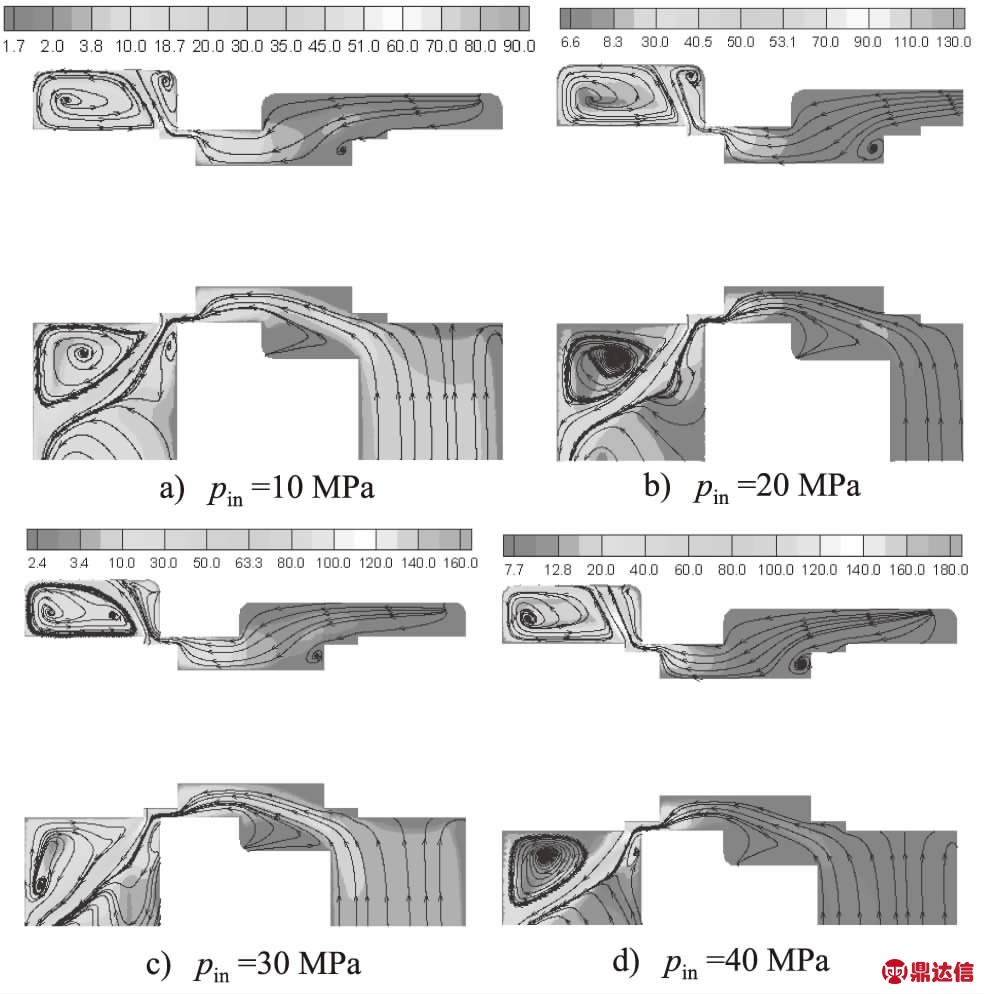
图3 液压滑阀内速度分布云图和流线图
在节流槽出口处,受出口拐角的影响,液压油的流动方向发生改变,介质在拐点处折流后会形成第二个高流速区域。受流体惯性影响,高流速介质会直接冲击对侧的壁面,之后贴壁面流动。
结合图2可知,节流槽出口处存在明显的压力梯度。在沿液压滑阀出口管道的流动方向上,压力逐渐回升。因此,在节流槽两侧的出口区域,均会出现介质回流。回流区均位于节流槽出口高流速区域的两侧,区域内介质的流动方向与主流方向相反,且占据了较大的流场空间。同时,对比图3a~图3d可知,液压滑阀进口压力的变化不会显著影响回流的数量和分布。由于阀门的流通能力直接受阀内旋涡数量和分布的影响[9],在出口压力给定的条件下,液压滑阀的流量系数受进口压力的变化较小。
2.2 液压滑阀内稳态空化流场分析
图4为当液压滑阀进口压力为10 MPa时,阀内的稳态空化流场。可知,空化从节流槽入口区域开始发生,并紧贴在阀芯表面。节流槽两侧的空化区域基本呈对称分布,其中上侧空化区域的气相体积分数略高于下侧。在空化核心区域内,气相的体积分数范围为0.55~0.60,空化强度较弱。并且,在该入口压力条件下,液压滑阀内的空化流动状态较为稳定,随着流动时间的增加,节流槽两侧的空化形态和气相体积分数基本保持稳定,未发生明显改变。
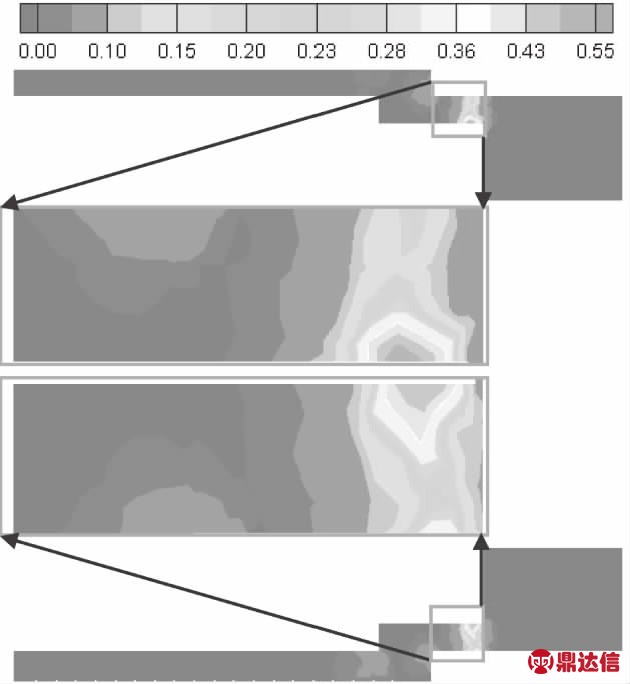
图4 液压滑阀内空化区域分布
2.3 液压滑阀内非稳态空化流场分析
图5为当液压滑阀进口压力为20 MPa时,阀内的非稳态空化流场。此时,阀内的空化区域发生明显变化。在节流槽的出口处的两侧出现了新的空化区域,空化流场特征更加复杂。节流槽入口处空化核心区域的气相体积分数为0.65~0.68,与入口压力为10 MPa时相比,略有增加;在节流槽出口处两侧空化区域内,空化强度相对较弱。
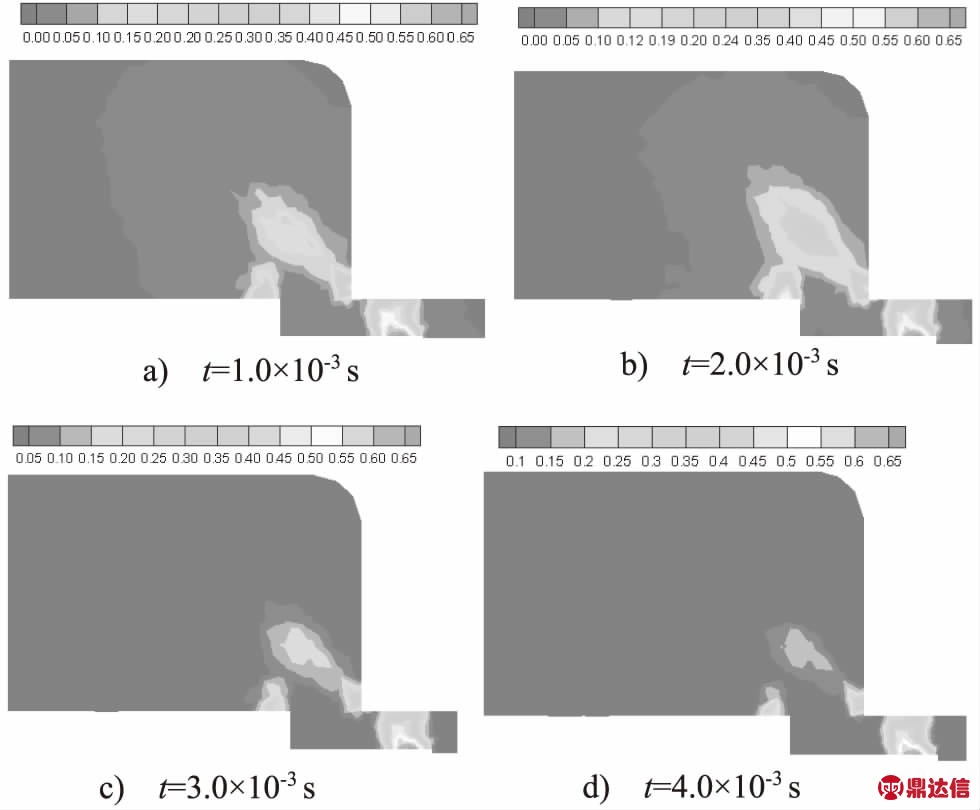
图5 液压滑阀内的非稳态空化流场(pin=20 MPa)
对比图5a~图5d可知,该进口压力条件下,液压滑阀节流槽出口处的空化具有明显的周期性。其中图5a、图5b和图6c分别为空化的初始阶段、充分发展阶段和衰退阶段,其变化周期约为4.0×10-3s。在整个变化周期内,空化的区域和强度均出现了较为明显的变化。特别是在空化充分发展阶段,节流槽出口纺锤型云空化核心区域的气相体积分数达到了0.42~0.45。
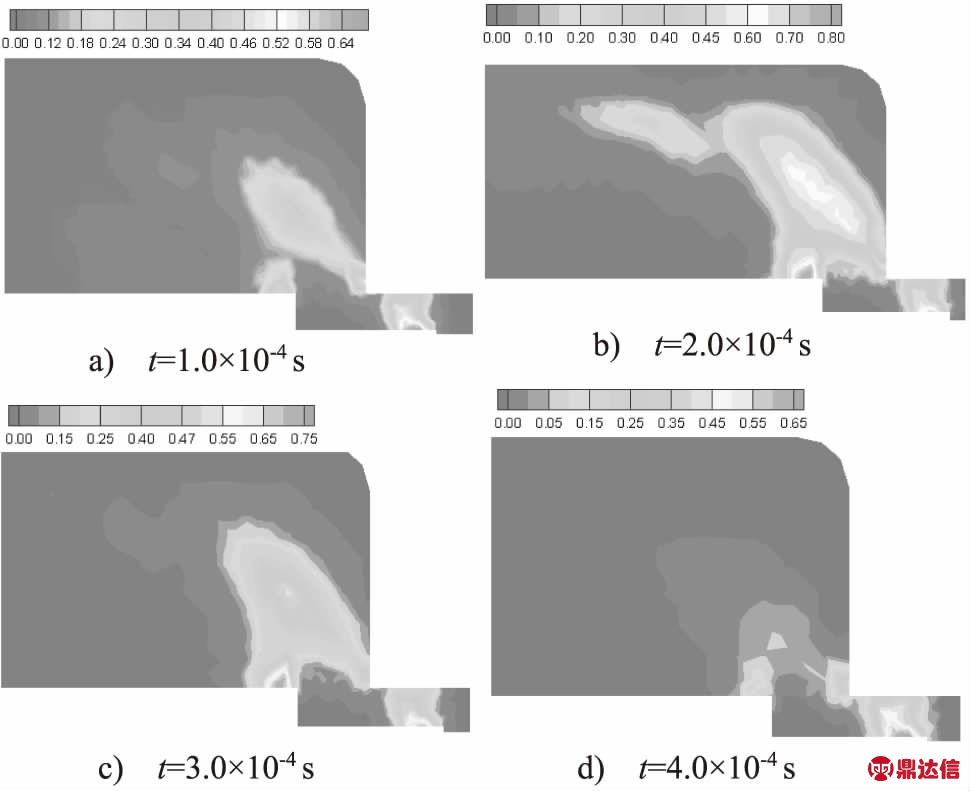
图6 液压滑阀内的非稳态空化流场(pin=30 MPa)
图6为当液压滑阀进口压力为30 MPa时,阀内的稳态空化流场。可知,在较高的入口压力下,液压滑阀内的空化区域和空化强度进一步增加。例如,在空化充分发展阶段,节流槽出口处两侧空化核心区域的气相体积分数分别达到了0.60和0.80。同时,节流槽出口处的空化流动也具有明显的周期性,其变化周期约为4.0 × 10-3s。与进口压力为20 MPa时相比,变化周期缩小了1个数量级。
由图6b可知,在空化充分发展阶段,在纺锤型云空化的末端,出现了空化脱落现象。脱落的空化区域呈条状,会在下游的压力恢复区发生溃灭。由图6c可知,在空化衰退阶段,节流槽出口处两侧空化区域的范围和空化强度均显著减少;当空化流动时间为4.0×10-3 s时,基本恢复至空化初生水平。
上述数值计算结果对液压滑阀空化流动试验的指导意义在于:通过计算分析,获得了液压滑阀内空化流动从稳态向非稳态转变的临界压力区间;确定了在不同进口压力下,高速摄影仪拍摄阀内空化流动的重点区域及采样频率;由于在高压条件下液压滑阀内存在云空化脱落现场,需要考虑由此导致的流体振荡现象对压力、流量等数据测量精度的影响,合理布置数据采集点。
3 结论
通过计算不同入口压力下液压滑阀内的空化流动特征,得到以下结论:
(1) 液压油流经节流槽时,流速和压力会发生突变。节流槽内及其出口区域存在多个低压区域,易发生空化;
(2) 当液压滑阀的进口压力为10 MPa时,阀内空化流场为稳态;当进口压力为20 MPa和30 MPa时,阀内的空化流场为非稳态,空化流动具有明显的周期性;
(3) 随着液压滑阀进口压力的提高,阀内的空化区域和强度明显增加。同时,云空化的周期性变化的时间显著减少。当进口压力达到30 MPa时,出现云空化的脱落现象。