摘要:针对国内铝型材静电喷涂生产线自动化程度不高的问题,开发了一套自动化生产线控制系统。搭建了基于工控机、PLC(可编程逻辑控制器)、CAN(控制器局域网)模块与喷枪从站的控制系统硬件平台,并以PLC 为下位机,实现了生产线自动运行、传感器信息采集、逻辑控制等功能,同时以工控机为上位机,设计了上位机与CAN 模块和PLC 的通信软件,完成了喷涂参数设置、喷枪从站控制、人机交互等功能的开发,最后在企业进行了实际应用。结果表明,该生产线控制系统能长时间稳定运行,实现了铝型材静电喷涂的自动化加工,提高了企业的生产效率。
关键词:铝型材;静电喷涂;自动化生产线;控制系统
随着制造业的不断发展,企业在生产中对铝型材的要求越来越高[1],不仅要求型材能防锈防蚀,还要求型材表面有足够的硬度和耐磨性[2],这就需要对型材表面进行处理。传统的处理方式是空气喷涂,而随着现代喷涂技术的发展,效率更高、喷涂质量更好、更环保的静电粉末喷涂正逐步取而代之[3]。静电喷涂的原理是静电场对电荷的作用[4]:将工件接地作为阳极,喷枪作为阴极,即在喷枪上施加负电压,令喷枪与工件之间形成静电场,粉末从喷枪喷出时带上负电荷,在电场力的作用下附着在工件上而形成均匀的薄膜[5],多余的粉末通过回收系统回收。其效率高,经济效益好,对环境也很友好[6]。
采用自动化生产线进行铝型材的静电喷涂加工可以显著提高粉末的利用率和生产效率。国内部分高校和企业设计了基于编码器和PLC(Programmable Logic Controller,可编程逻辑控制器)的自动喷涂生产线[7-8],能实现生产线的半自动喷涂,但很多操作仍需人工完成,喷枪参数调整很繁琐,人机界面比较简陋,不够方便、友好。国外进口的喷涂生产线虽自动化程度高,但购买和维护成本不低,不适用于对成本敏感的中小型企业。
根据铝型材静电喷涂的特点和企业的实际需求,设计和开发了一套铝型材静电喷涂生产线控制系统,能方便快捷地在生产线上对喷枪的喷涂参数进行调整,实现喷枪的自动喷涂控制,有效降低了企业的人力和物力成本,解决了国内中小型铝型材加工企业生产线自动化程度不高的问题。
1 硬件架构
如图1 所示,该系统主要由研华PPC-3120S 工控机、意普兴ESN14810L1N0-S 光幕传感器、欧姆龙E6B2-CWZ6C 旋转编码器、西门子S7-200 Smart PLC、广成科技GCAN-202 模块和汉哲涂装Milepost 喷枪从站等组成。
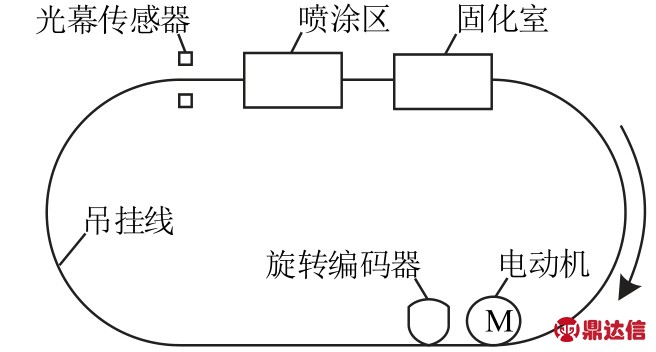
图1 控制系统硬件架构
Figure 1 Hardware architecture of control system
PLC、CAN(Controller Area Network,控制器局域网)模块、工控机均通过以太网与交换机连接,实现数据的传输与交换。光幕传感器、旋转编码器与PLC 相连,输出信号到PLC。上位机软件安装在工控机上,通过TCP 协议读取PLC 寄存器数据,由程序处理后经过CAN 模块1 将喷涂参数发送给各喷枪从站,每个喷枪从站连接一把喷枪。由于现场干扰较大,因此引入CAN 模块2,当最后一个从站接收到数据后,由软件读取CAN 模块2 的数据并与CAN 模块1 发送的数据同步比对,进行纠错。
2 PLC 控制系统的设计
PLC 是编码器、光幕传感器与工控机之间的桥梁,承担着传递信号和处理信息的任务[9]。为了满足生产线的工作流程和自动化的控制要求,PLC 控制系统设计包括生产线布局、PLC 控制逻辑、PLC 程序流程3 个方面。
2.1 生产线布局
合适的生产线布局是满足PLC 控制系统设计的关键。如图2 所示,铝型材固定在由电动机驱动的吊挂线上,光幕传感器用于检测工件的位置,由于喷涂区内粉尘较大,传感器安装在喷涂区之外。控制系统通过旋转编码器的脉冲信号和光幕传感器的电平信号对工件进行位置控制,由PLC 程序和上位机软件程序进行开关枪判断,工件喷涂后进入固化室固化处理[10]。
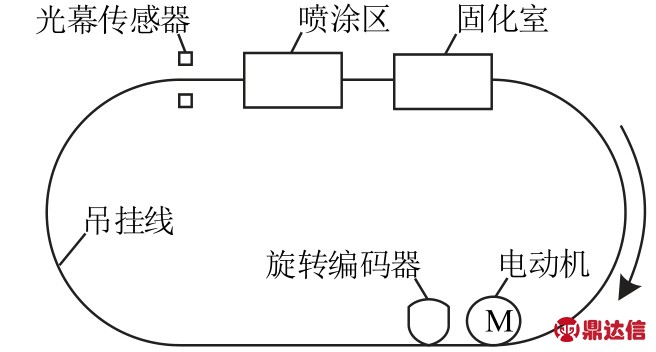
图2 生产线布局
Figure 2 Layout of production line
2.2 PLC 控制逻辑
为了确保铝型材表面涂层厚度均匀,需要在铝型材到达喷枪前一定距离就开启喷枪,在离开喷枪后一定距离才关闭喷枪,所以在PLC 上对提前开枪和延迟关枪的时机进行设计。如图3 所示,喷枪设置在喷涂区里,工件宽度为d,喷枪2 到光幕传感器的距离为L,预先设置的提前开枪和延迟关枪距离均为l。
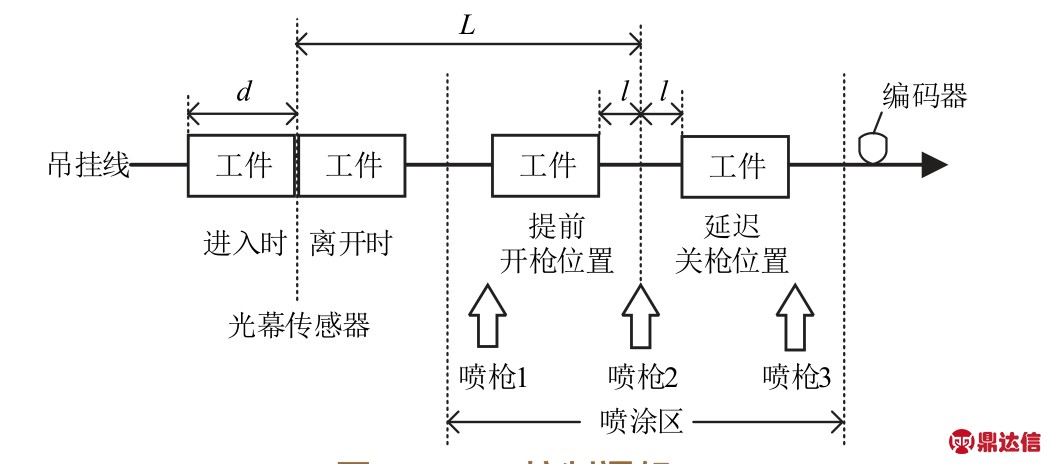
图3 PLC 控制逻辑
Figure 3 PLC control logic
当工件在吊挂线上运行至其前沿接触到光幕传感器时,PLC 记录下此时编码器的脉冲数值,当工件整体离开光幕时,PLC 再次记录下此时编码器的数值。以喷枪2 为例,经过(L - l - d)的距离后,喷枪2开枪提前喷涂;再走过(2l + d)的距离后喷枪2 关枪。为了提高喷涂效率,可根据实际生产需要,在喷涂区同侧或两侧交错设置多把喷枪,同时在PLC 程序上写入多把喷枪的子程序,上位机读取每把喷枪的开枪标志位寄存器状态即可判断喷枪的开关枪。
2.3 PLC 程序流程
PLC 的输入信号有光幕传感器(输入电平信号),旋转编码器(输入脉冲信号)以及急停、启动、暂停按钮(输入IO 数字信号,24 V);输出信号为启动、关闭喷枪信号。控制系统开始运行后,上位机软件读取位置参数文件,将各参数写入PLC 的相应寄存器中,第一把喷枪的位置寄存器地址为VD0,提前值寄存器为VD4,延迟值寄存器为VD8,开枪标志位寄存器为V1500.0,第二把喷枪的位置参数寄存器地址分别为VD12、VD16、VD20、V1500.1,以此类推,最多支持60 把喷枪的参数设置。光幕传感器输入为I0.6,编码器数值的寄存器为VD1620。
如图4 所示,设置完位置参数后PLC 开始读取光幕传感器信号,当铝型材进入光幕时(光幕输入信号由低电平转变为高电平,上升沿)记录当前编码器的脉冲数值(起始位置),并置位一个开始记录标志位。当开始记录标志位有效且工件离开光幕时(光幕输入信号由高电平转变为低电平,下降沿),记录当前编码器的脉冲数值(结束位置),复位开始记录标志位。工件到达开枪位置时,PLC 开枪标志位置位。工件到达关枪位置时,开枪标志位复位。如此循环往复,直到喷涂结束。
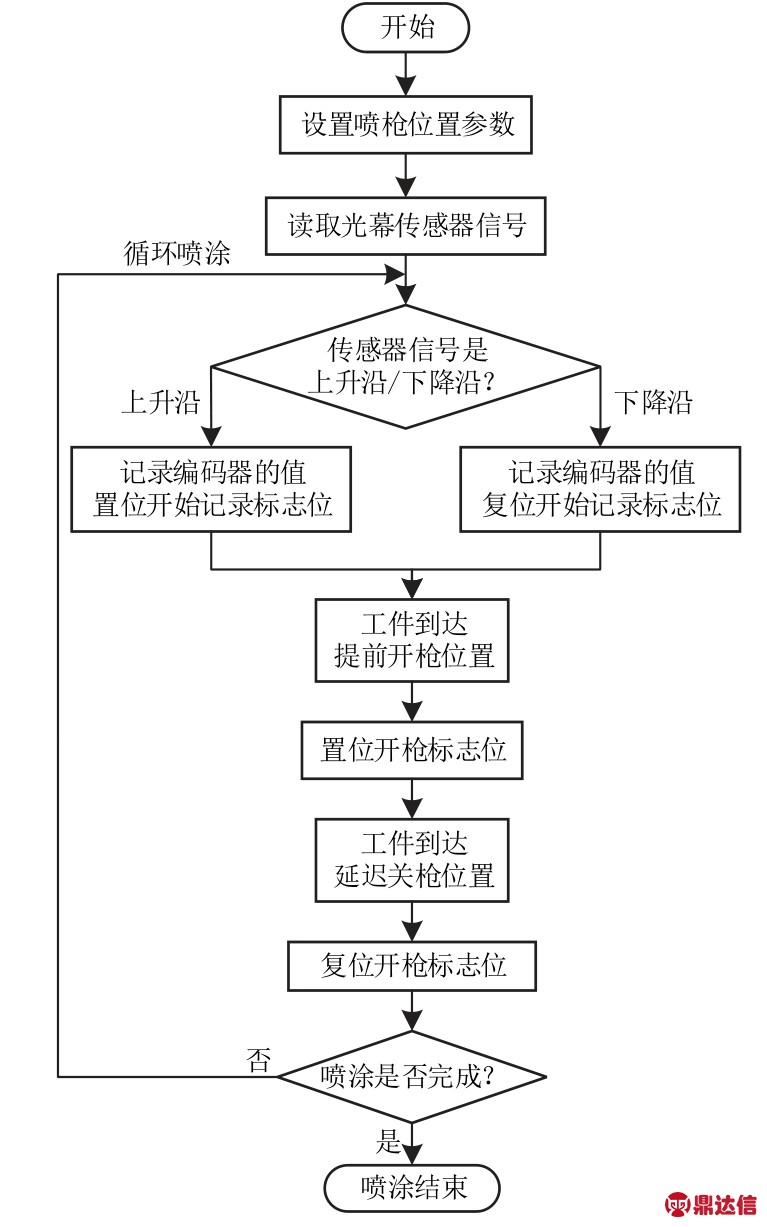
图4 PLC 程序流程
Figure 4 Flowchart of PLC program
3 上位机软件的设计
上位机软件作为整个生产线控制系统的核心组成部分,功能众多。基于Windows 操作系统,以Qt 5.12 为开发平台设计了界面美观、交互友好的上位机软件。软件的开发包括人机界面设计、CAN 模块通信设计和PLC 通信设计。
3.1 人机界面设计
如图5 所示,人机界面实现了吊挂线速度、系统运行状态、运行模式、工件识别参数、CAN 模块状态、PLC 状态的显示,2 个喷位喷涂参数的调整,喷涂配方的设置,每把喷枪的位置管理,系统的配置以及日志等功能。
在实际生产过程中,由于控制系统实现了自动开关枪的功能,用户只需要根据经验和铝型材状态判断膜厚情况,在人机界面上改变粉量、雾化(空气流量)、高压、电流4 个参数,通过上位机与喷枪从站的数据传输即可实时调整喷枪的喷涂状态。

图5 上位机软件的人机界面
Figure 5 Human-machine interface of upper computer software
3.2 CAN 模块通信设计
CAN 模块选用广成科技GCAN-202,该型号支持TCP/IP 协议,开发基于标准的Socket 套接字规范,能够实现以太网数据和CAN-BUS 总线数据的相互转换,是喷枪从站与上位机软件的媒介。PC 通过以太网与CAN 模块连接,IP 地址为192.168.1.5,端口为56043,CAN 模块的工作模式都设置为TCP Server,模块1 的IP 地址为192.168.1.10,端口1 为4001,端口2 为4002,而模块2 的 IP 地址为192.168.1.12,端口1 为4001,端口2 为4002。上位机与2 个模块的通信通过Qt 中的QTcpSocket 类实现,在软件中新建TCPControllerDevice 类,继承于QTcpSocket。开设 2 个独立线程类CANControllerModule 和CANReceiverModule,前者服务于CAN 消息发送,后者服务于CAN 消息接收,在这2 个类中分别创建2 个TCPControllerDevice 类的实例,调用connectToHost(QHostAddress &address, quint16 port)函数分别连接对应模块的2 个端口,使用waitForConnected(int msecs)函数判断是否连接成功,成功则返回true,否则为false。发送消息时,上位机通过write(const char *data, qint64 maxSize)函数将数据帧写入Socket 缓存,利用waitForBytesWritten()函数将缓存中的数据发送到CAN 模块。若要断开Socket 连接,则通过disconnectFromHost()函数实现。
如图6 所示,上位机软件与CAN 模块建立通信后,将喷涂参数以数据帧的形式发送到CAN 模块。数据帧包括13 个字节,第1 个字节为帧信息,用来标识数据帧的长度;第2 至第5 个字节为喷枪从站的ID 和开关枪信息;第6 至第13 个字节为数据帧的数据信息,雾化、粉量、高压、电流、清扫气等喷涂参数存储在此字节段。用户在界面上设定的参数通过以太网传输到CAN 模块,模块将数据帧转换成CAN-BUS 数据发送给喷枪从站,由从站内置的CAN-BUS 模块进行分析处理,识别到喷涂参数的改变后对喷枪进行参数调整。
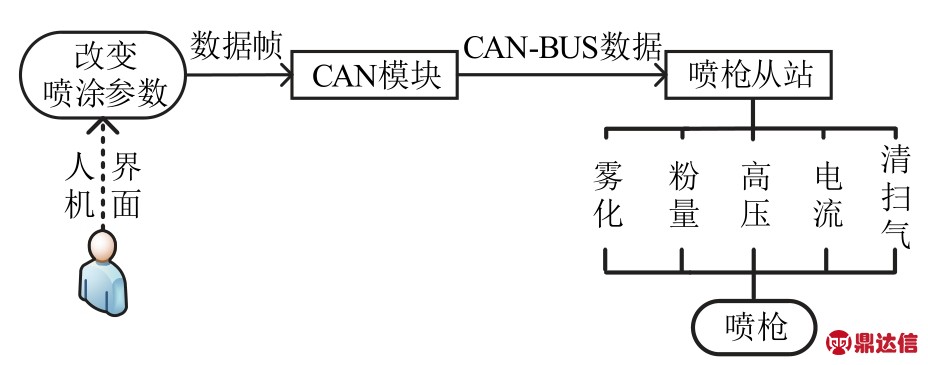
图6 喷涂参数的发送过程
Figure 6 Process for sending the spraying parameters
3.3 PLC 通信设计
在工业自动化生产中,西门子的S7 系列PLC 由于功能强大、运行速度快、扩展性强而应用广泛。选用西门子S7 系列中S7-200 Smart 型号的PLC。它拥有12 点输入、8 点继电器输出、以太网口,能满足系统控制和通信的需要;拥有高速计数器对编码器的脉冲进行计数,能满足程序设计的需求;并且具有价格低廉、性能稳定的优势。
S7-200 Smart 可以通过以太网口与PC 进行程序的下载和数据的交换,数据传输所用到的通信协议是西门子的S7 Communication 协议(简称S7 协议)。PC 与PLC 的通信分为3 个阶段:
(1) 握手阶段。当PC 与PLC 通过Socket 建立连接时,会在此阶段进行“3 次握手”,这是标准的TCP 连接方式,由Socket 自动完成。
(2) 通信请求和确认阶段。在握手阶段之后,并不能马上进行数据交换,还需要经过通信请求和确认过程。这个过程包含两次报文交换:第一次,PC 发送S7 协议的“握手包”COTP(Connection Oriented Transport Protocol,面向连接的传输协议)连接包给PLC,连接包的类型为CR(Connect Request,连接请求),请求与PLC 进行连接,而PLC 反馈COTP 连接包,连接包的类型为CC(Connect /confirm/i,连接确认),确认与PC 进行连接,同时PLC 明确所连接PC 的IP 地址和端口;第二次,PC 发送S7 协议中类型为“Setup communication(建立通信)”的作业请求,PLC 反馈“连接确认”的数据响应,从而建立起PC 与PLC 的通信。
(3) 交换数据阶段。在此阶段,根据控制需要对PLC 发送作业请求,作业类型包括Run(运行)、Read(读取)、Write(写入)、Stop(停止)等,在PC 发送作业请求之前,S7 协议会自动发送一个类型为DT(即Data──数据)的COTP 功能包,表明后续要发送的帧为数据帧,PLC 不会对此功能包进行反馈;PC发送作业请求后PLC 反馈报文,确认数据响应,回复报文内容为成功、失败或是PC 读取某个寄存器返回的数据内容。
上位机软件开设一个独立线程类PLCControllerModule,在类中创建一个TCPControllerDevice 类的实例,软件启动时连接PLC 的IP 地址和端口,PLC 的IP 地址为192.168.1.11,端口为102,经过“握手阶段”、“通信请求和确认阶段”建立与PLC 的通信。在“交换数据阶段”,上位机软件通过S7 协议中的“Run”作业请求运行PLC,PLC 返回“success”后继续通过“Write”作业请求对PLC 各位置值、各提前延迟值寄存器进行数据的写入,并设置一个定时器m_pPlcReadDataTimer,每隔100 ms 发送一次“Read”作业请求,读取从V1500.0 开始的各开枪标志位的寄存器状态,PLC 返回“1”时上位机软件向对应从站发送开枪消息,返回“0”时发送关枪消息。喷涂结束后,软件发送“Stop”作业请求停止PLC的运行。
4 实际应用
以广东肇庆某铝型材加工企业为例,铝型材静电喷涂生产线控制系统如图7 所示,24 个喷枪从站、工控机、CAN 模块、PLC、交换机均安装在左侧电柜,右侧电柜为供粉中心。系统应用于该企业的2 个喷涂区(如图8 所示),每个喷涂区高10 m,为了便于回收粉末,区域设置为三角形,24 把喷枪交错设置在同侧,由往复机带动上下喷涂。
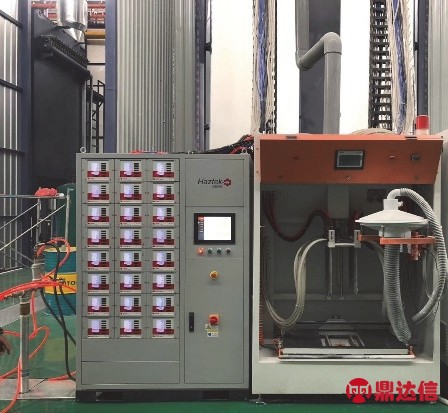
图7 铝型材静电喷涂生产线控制系统
Figure 7 Control system for aluminum profile electrostatic powder spraying production line
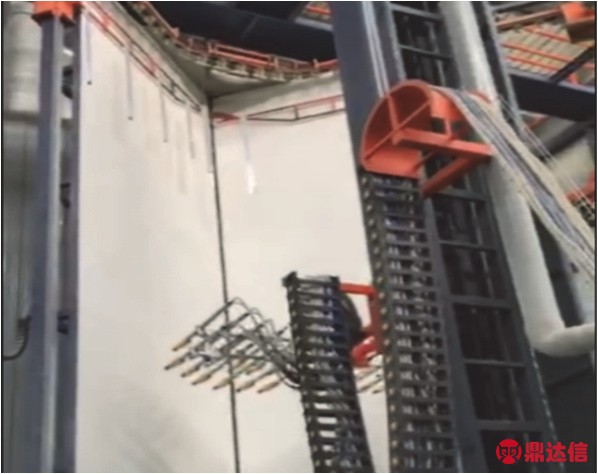
图8 喷涂区
Figure 8 Spraying area
现场设置的光幕传感器距离喷涂区内第一把喷枪5 000 mm,往复机上喷枪之间间隔150 mm,用户在上位机软件上写入每把喷枪的位置参数,提前延迟值设置为200 mm,静电喷涂参数设置如下:粉量60%,雾化(空气流量)2 Nm3/h,高压70 kV,电流40 mA。喷涂过程中,当涂层较薄时可适当增大粉量、高压和电流,从而增加粉末的数量和带电量;当涂层较厚时,适当增大雾化以扩大粉末的雾幅、分散粉末涂料,或是减小粉量、高压和电流。
待加工铝型材长7 000 mm、宽100 mm、厚50 mm,铝型材之间距离为100 mm。喷涂过程如图9 所示,此时铝型材处于往复机上左侧12 把喷枪的开枪范围内,但未进入右侧12 把喷枪的开枪范围,所以左侧喷枪开启,右侧喷枪关闭。生产线连续运行72 h 后,上位机软件、PLC、CAN 模块等仍正常工作,表明控制系统性能稳定,满足了自动化加工的控制要求。
GB/T 5237.4-2017《铝合金建筑型材》规定铝型材表面应光滑、有光泽[11],不允许出现鼓泡、腐蚀、裂纹、起皮等现象,涂层厚度应在40 ~ 120 μm 范围内。从图10 可以看出,由控制系统加工后的铝型材表面光滑,随机选取20 个点用天星ED300 型测厚仪测得涂层厚度为60 ~ 80 μm,符合国标的要求。
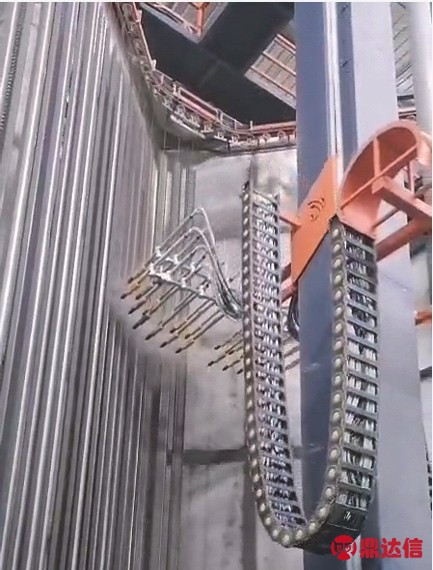
图9 喷涂过程
Figure 9 Spraying process
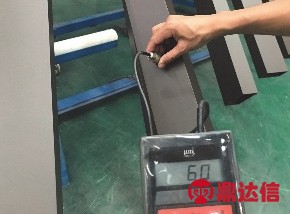
图10 喷涂结果
Figure 10 Spraying result
5 结语
根据铝型材静电喷涂的特点和企业的实际需求开发了一套铝型材静电喷涂自动化生产线控制系统,完成了硬件平台的搭建、PLC 控制系统的设计和上位机软件的开发。控制系统性能可靠,成本低廉,已投入企业实际生产4 个多月,运行稳定,实现了铝型材静电喷涂的自动化加工,提高了企业的生产效率和粉末的利用率,且加工后的铝型材质量符合国标要求,是中小型铝型材加工企业对静电喷涂生产线进行自动化升级改造的理想方案,具有良好的应用前景。