摘要:对于大型储罐焊缝缺陷自动化检测,爬壁机器人需完成自动化全方位扫查。针对储罐爬壁机器人在不同运行工况下的受力状态,建立爬壁机器人力学模型,分析获得不下滑、不纵向倾覆、不横向侧翻以及复合状态下失稳状态危险点,应用Maxwell软件对永磁吸附轮受力状态进行仿真与优化设计,使之满足吸附要求。同时,设计具有辅助吸附功能的编码轮结构,在反馈位置信息的同时,补充安全吸附力的裕度,以增加其越障和抗失稳能力。最后,依据设计模型制造出爬壁机器人本体并进行测试实验,实验结果证明该机器人能在各种危险点处实现带负载稳定全向驱动运行。
关键词:储罐焊缝检测;永磁体吸附;爬壁机器人;电磁仿真
0 引言
大型储罐是化工企业常用的关键存储设备,长期使用会产生腐蚀、裂纹等缺陷,进一步扩展开裂会发生泄漏甚至爆炸,导致严重的安全生产事故,因此相关法规强制规定了储罐需定期检测。目前,对大型储罐的检测仍采用传统的人工检测方式,劳动强度大、危险性高,亟待自动化设备替代。
近年来,爬壁机器人的发展日新月异,部分进口成形产品被应用于大型储罐缺陷的检测,携带探头进行扫查动作,完成缺陷的检测任务[1-4]。同时,在爬壁机器人的吸附、越障、驱动等领域均有研究成果报道[5]。爬壁机器人可以从吸附方式分为仿生吸附、负压吸附、静电吸附、磁吸附等。朱佩华等[6]以典型生物的足部特征为仿生对象,模拟黏附、抓附、吸附时的运动特征建立GPL模型,解决了仿生爬壁机器人路径规划问题,整体采用摆动爬行,可适应多种壁面;彭晋民等[7]针对吸附力利用效率问题,分析了运动结构对吸附力配置影响,研制出基于负压吸附的密封机构;谢理[8]将传统履带移动机制和新型静电吸附有机结合,利用静电吸盘与壁面的电场力实现吸附,负载力大,但壁面过度能力较差,需高压模块,功耗大且不稳定。在石油化工、船舶行业,大部分爬壁机器人都采用磁吸附方式,其优点在于磁力平稳,适应大部分铁磁性材料表面[9-10]。赵军友等[11]对油罐除锈进行研究,设计了一种新型电磁吸附单元,形成吸附履带结构,所带负载较大,但机动性能较差,不适合全方位检测工作。朱世强等[12]研制了一款永磁体充气轮爬壁机器人,并开展了翻越过程动力学建模研究,研究吸附力、轮胎压力与越障量之间的关系,保证了优良的越障性能,但永磁体提离间隙大,所带负载有限。ABDULKADER等[13]提出一种名为Sparrow的船体自主检测机器人,依靠四个电磁轮吸附,并在不同厚度的金属板上表现出优良性能。目前国内相关研究都集中于爬壁吸附本身,对检测机器人所需的机动性、越障性、复合动作等综合分析较少[14]。永磁体吸附和电磁吸附作为磁吸附的两个分支,各具特点,对于大型储罐的检测,永磁体磁力持久,不受电源影响,且便于维护。基于此,本文设计了一种基于磁力吸附的储罐爬壁机器人。
1 爬壁机器人本体结构设计
1.1 机器人运动性能分析
如图1所示,大型储罐的检测按照NB/T 47013.3—2015标准作业,需对储罐全部焊缝接头进行超声检测。大型储罐规格有500、1000、2000、5000、10000 m3不等,母材材料多以Q345R、Q370R、18MnMoNbR为主,其厚度在10~50 mm范围变化,焊缝接头形式也常随母材厚度而设计成Y形、双Y形、双V形、双U形焊缝等。以B级检测为准,需预先对储罐焊缝检测区域打磨光滑,再对纵向缺陷、横向缺陷全面扫查,同时对焊缝交汇处母材测厚以观察内壁腐蚀情况。
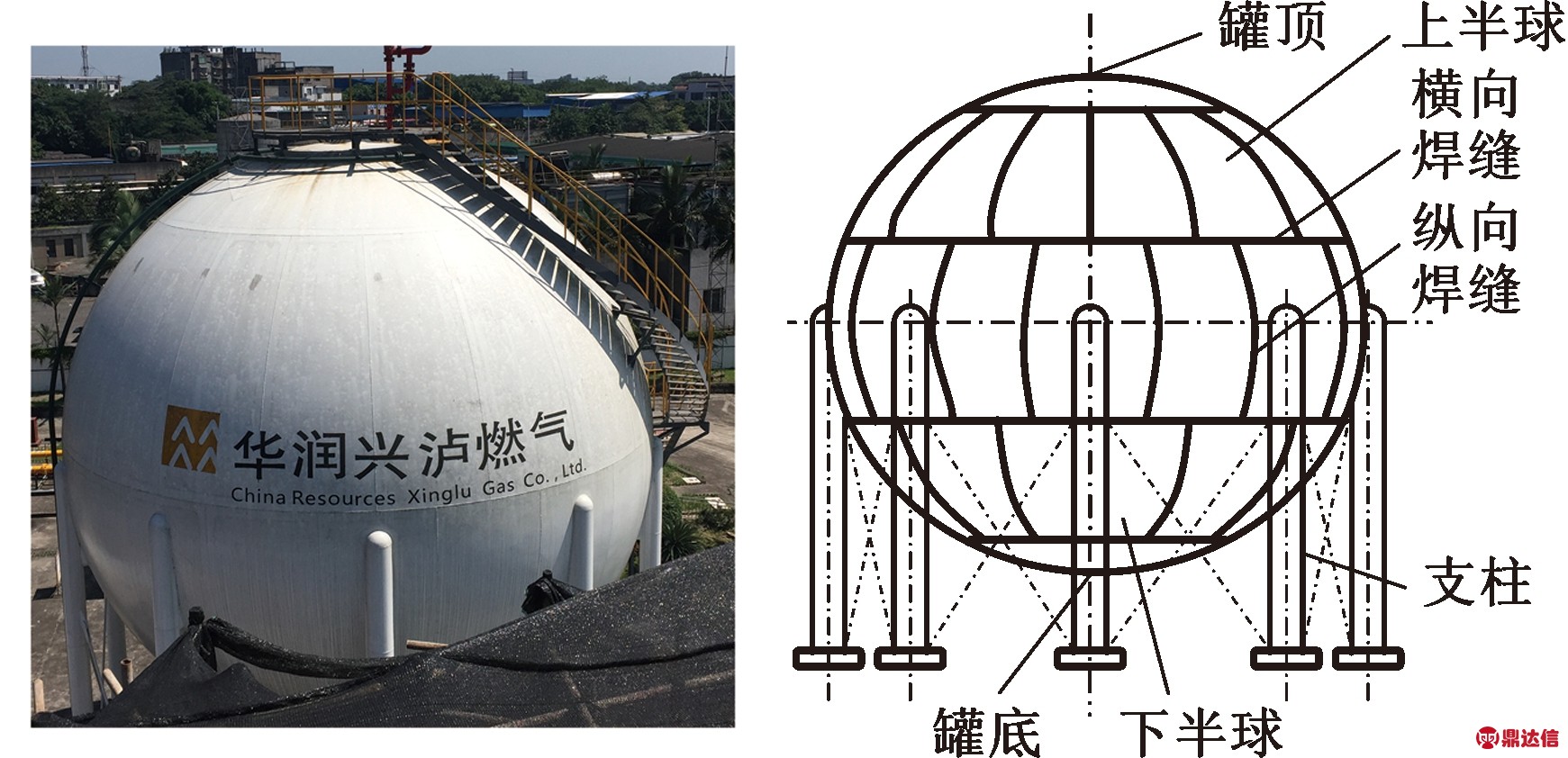
(a)1000 m3球罐实物图(b)桔瓣型球罐焊缝分布模型
图1 球罐实物及模型结构图
Fig.1 Photo and model structure diagram of spherical tank
实现储罐全覆盖扫查需布置4个探头(2个检测横向缺陷、1个检测纵向缺陷、1个测厚探头)。考虑运动方式及探头布置,机器人自重为25 kg,搭载装备质量为10 kg(包括控制及供电线缆、检测仪器等)。因此,为保障设备在实际工况使用下的安全性及稳定性,以40 kg满载质量作为机器人总体设计目标参数。
1.2 机器人整体方案
根据现有超声检测标准,为保障在储罐各位置上吸附的稳定性,主动元器件皆采用轻量化标准件,爬壁机器人整体结构如图2所示。机器人主体由车身车架、定位循迹模块、驱动吸附单元、超声检测探头组件、中控模块及相关支承件组成。在车架底部安装有4个对称布置的永磁驱动轮组件,由4个电机独立驱动,可实现前后移动、转向等不同运动方式。在机器人前端布置有激光传感器单元,以实现基于焊缝轮廓实时反馈的自动循迹。
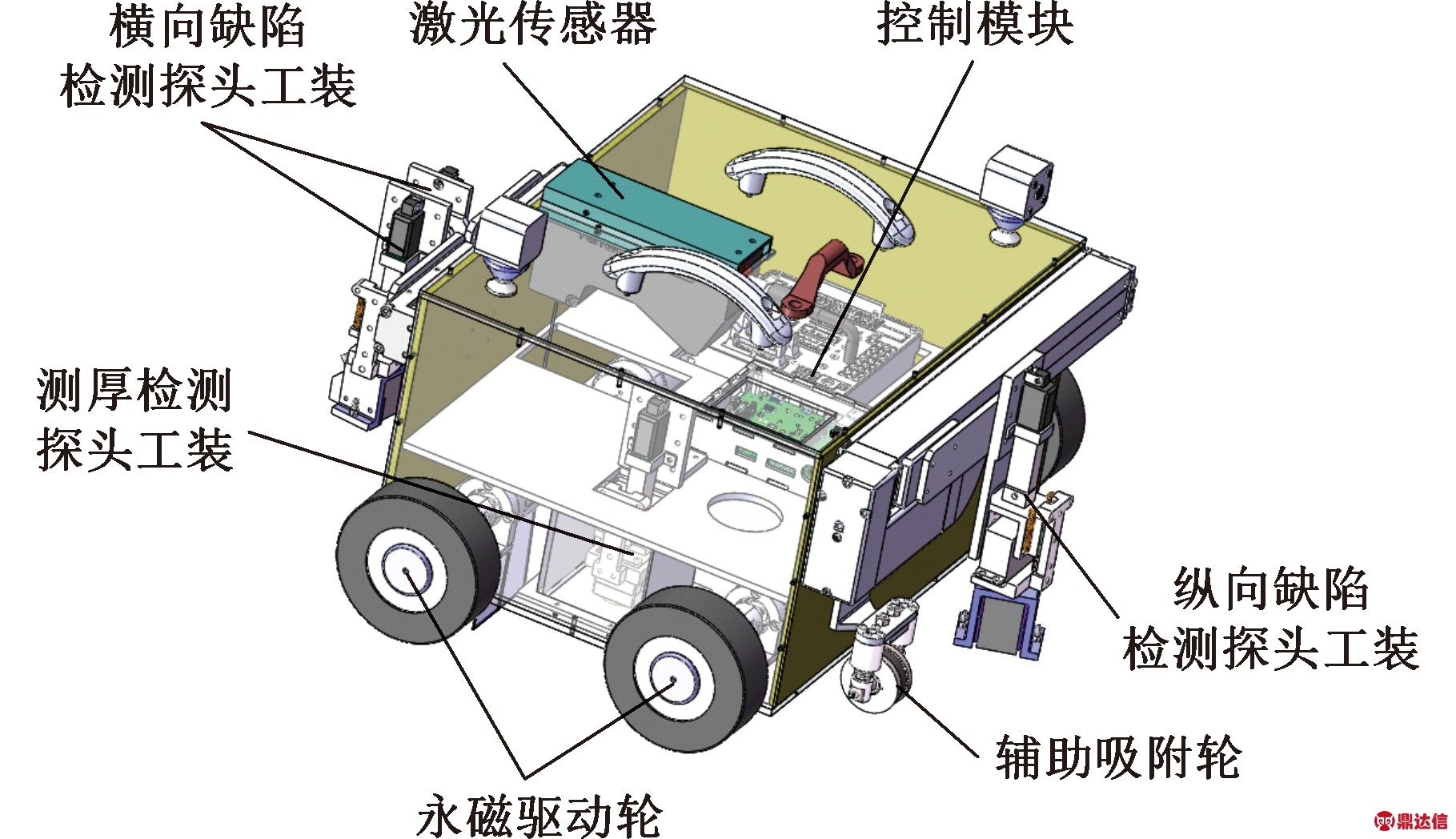
图2 爬壁机器人三维结构图
Fig.2 3D structure diagram of wall-climbing robot
1.3 永磁驱动轮结构设计方案
单个永磁驱动轮组件由永磁吸附轮、驱动电机、联轴器、法兰盘、轴承座组成,如图3所示。
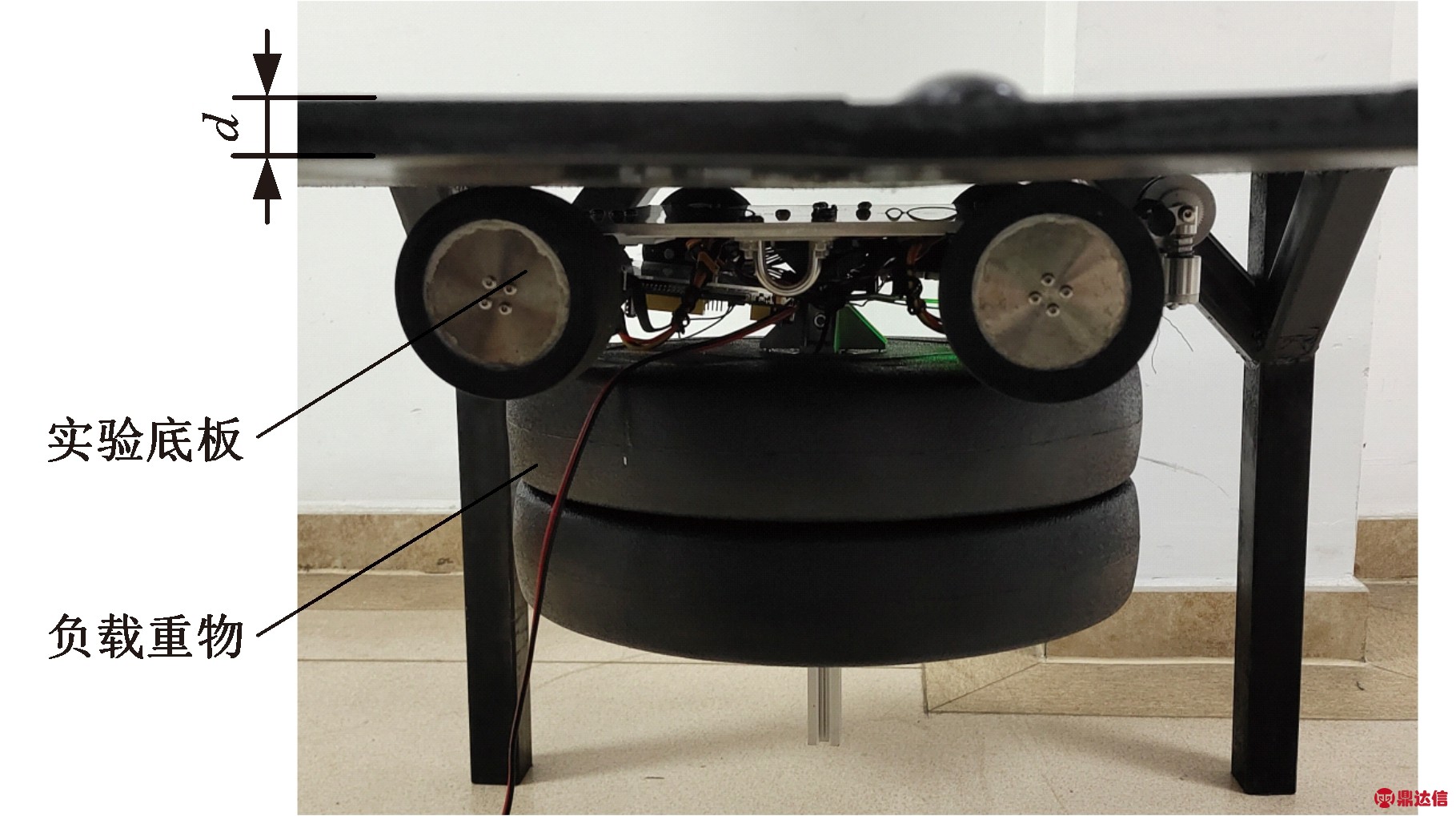
图3 永磁驱动轮组件结构
Fig.3 Structure diagram of permanent magnet driving wheel assembly
永磁体磁力稳定可靠,但吸附力随着提离间隙的增大会急剧减小。轮式结构可实现恒定提离值吸附,以增加吸附的可靠性。另外,在吸附轮结构设计时,应充分考虑吸附力与转向摩擦力两者的平衡,既要保证吸附稳定性,又要避免吸附力过大造成电机过载。驱动吸附轮结构如图4所示,由两个N35H永磁体环作为磁极,以内外衔铁、导磁环导通磁回路,实现与壁面的稳定吸附。内外衔铁除了兼具导磁和固定导向的作用外,还与电机输出轴法兰稳定连接,实现大扭矩的持续输出。同时,在长期服役使用过程中,由于负载较大,所需吸附力较大,故衔铁高度会比磁环高度略高一些,可避免磁环受力挤压破碎。另外,在磁轮表面包覆橡胶垫可以减少衔铁与铁磁表面的振动冲击,延长使用寿命,增大摩擦因数。
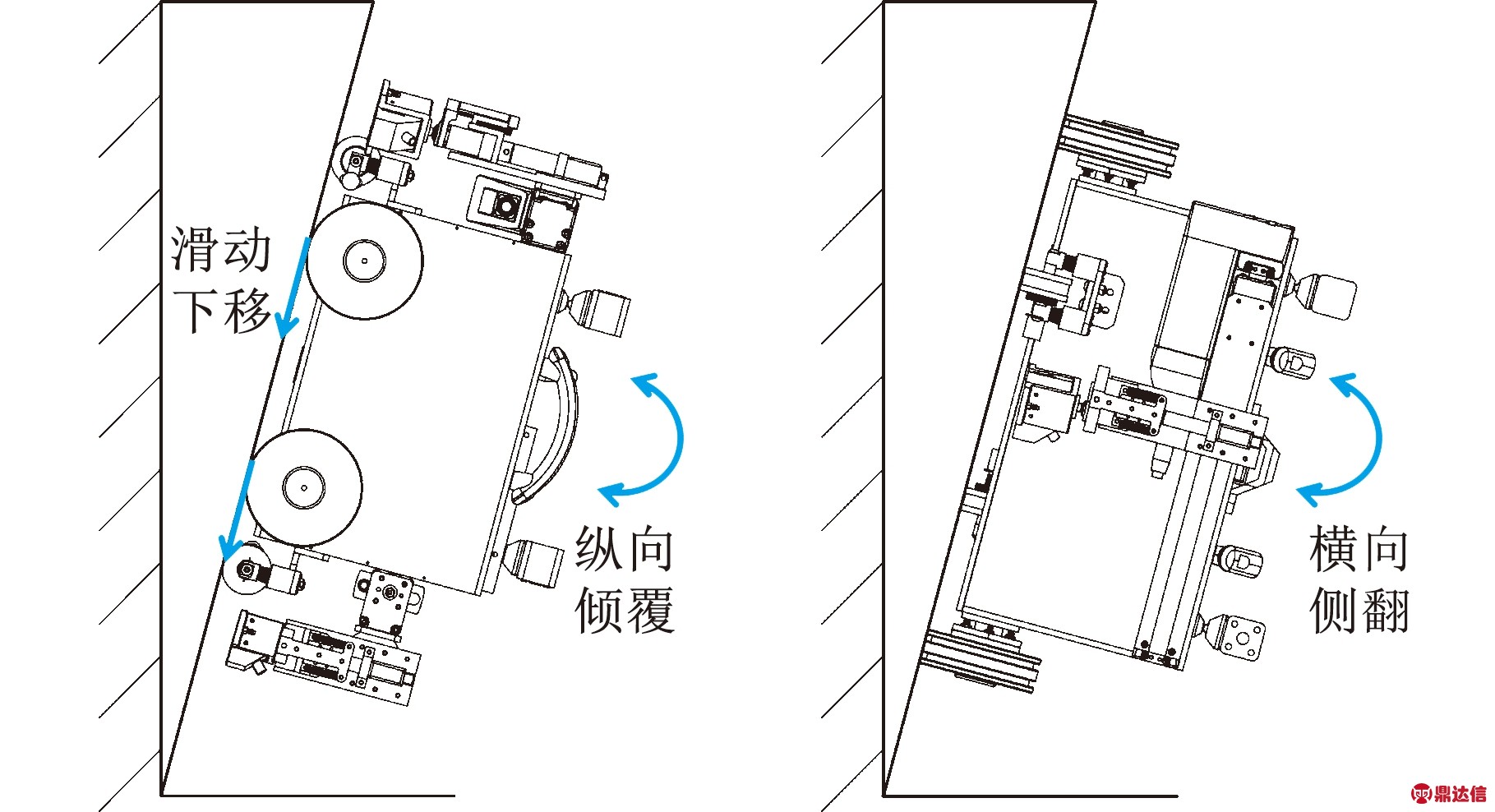
图4 驱动吸附轮结构图
Fig.4 Structure diagram of driving adsorption wheel
1.4 辅助吸附轮结构设计方案
如图2所示,为提高爬壁机器人的吸附能力,设计了辅助吸附轮结构,对称布置于前后面板上,如图5所示。避振器增加结构的阻尼系数,大幅降低机器人在越障过程中的振动,保证了机器人本体的平稳,同时有利于超声探头的连续检测。该辅助吸附轮也参照驱动吸附轮的衔铁-磁环-衔铁结构,且在轮上安置有尼龙齿轮组,啮合传动到编码器上。该辅助吸附轮依靠压簧及自身吸附力预紧,与吸附面紧密接触防止打滑,提高位置定位精度。
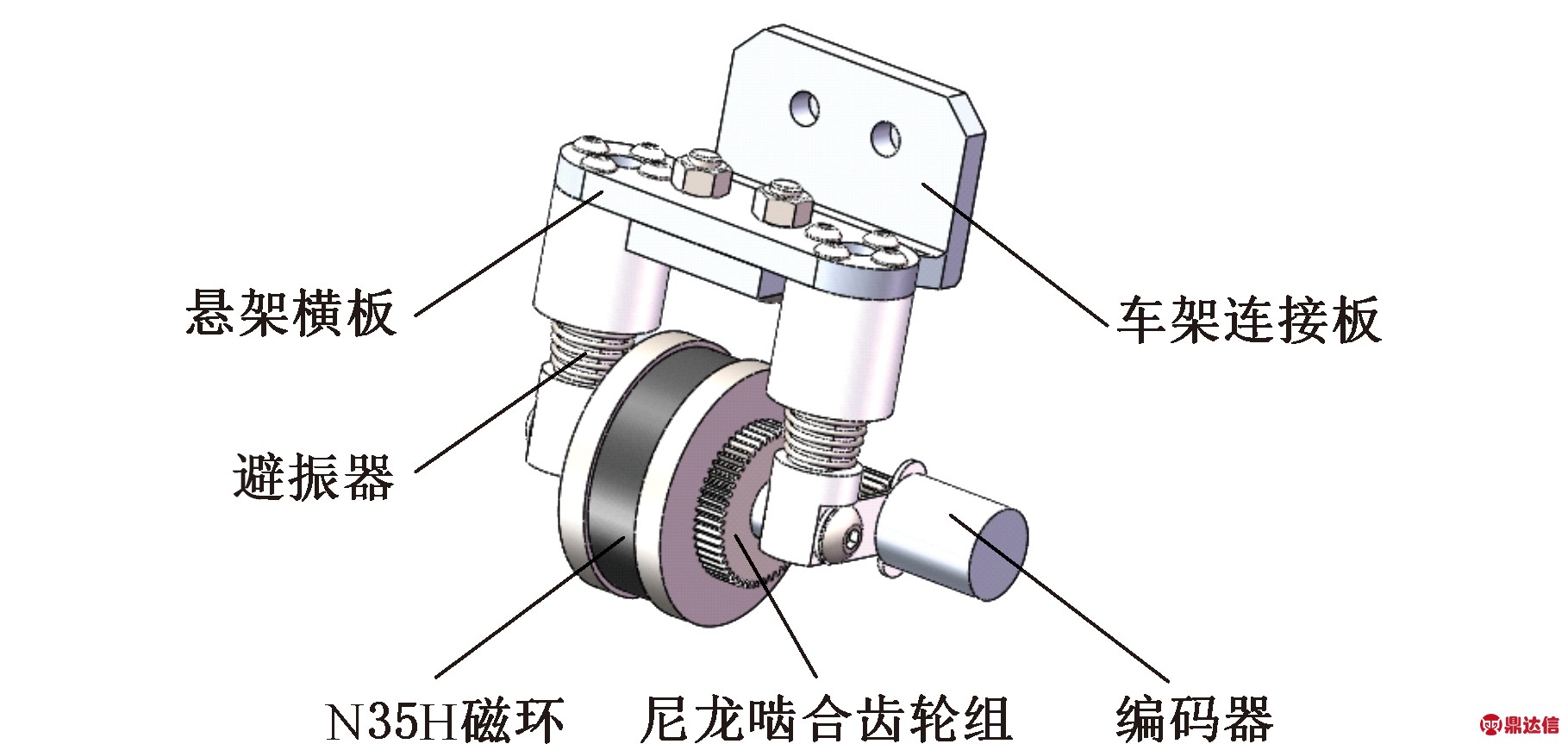
图5 辅助吸附轮结构图
Fig.5 Structure diagram of auxiliary adsorption wheel
2 爬壁机器人静力分析
爬壁机器人失稳状况主要分为滑动下移、纵向倾覆、横向侧翻[15]和复合状态,如图6所示。针对以上情况分别建立机器人的受力模型,分析获得失稳情况下所对应的极限吸附力。下列分析过程未考虑辅助吸附轮的受力情况,实际测试过程辅助吸附轮提供的部分吸附力及摩擦力作为安全裕量储备。
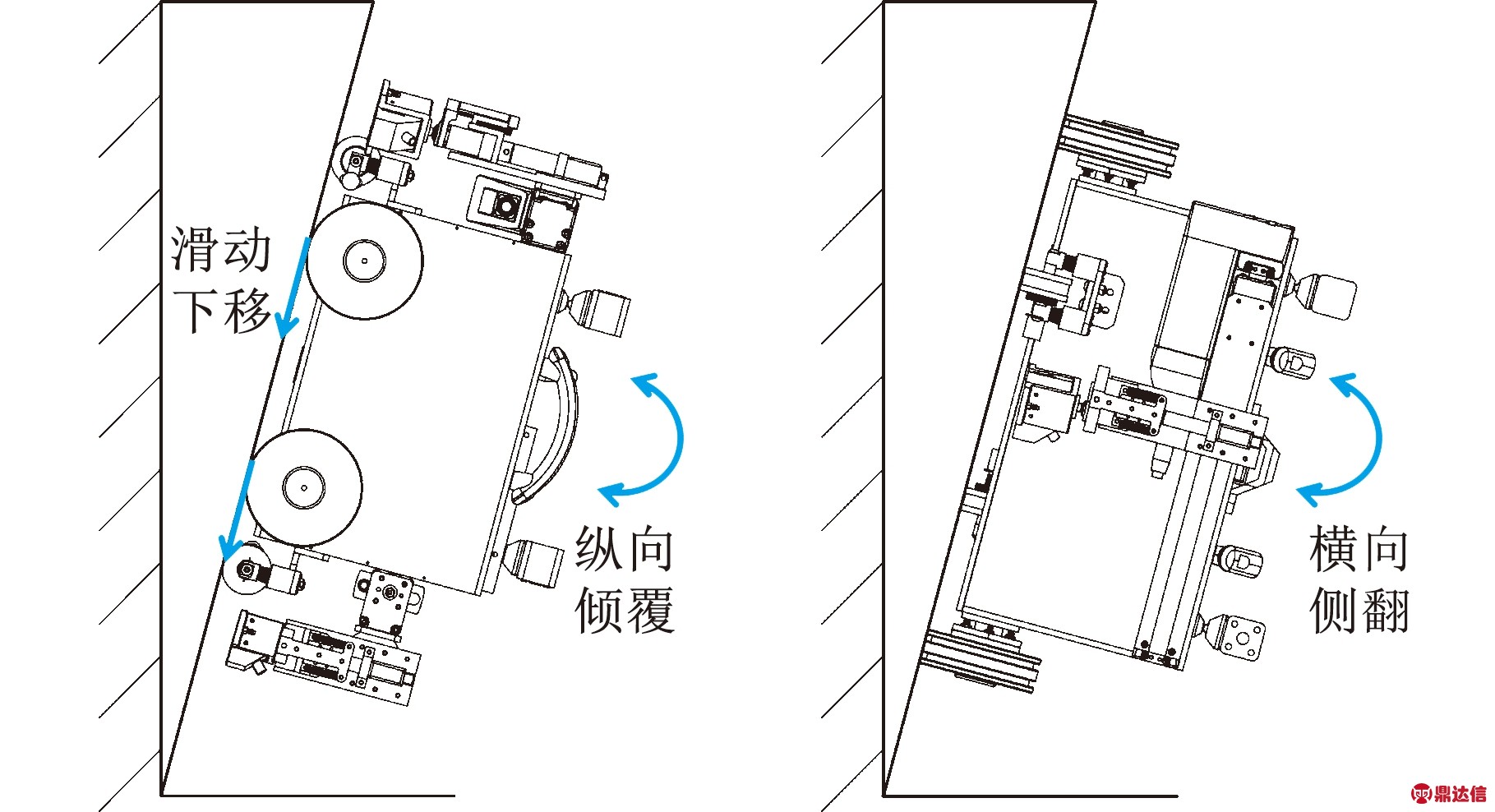
图6 爬壁机器人失稳状态示意图
Fig.6 Schematic diagram of instability state of wall-climbing robot
综合考虑吸附轮系、电缸探头、车身钣金、激光传感器等的空间位置及质量,经初步计算,机器人重心与本体中心重合,进一步建立各失稳模型。
2.1 滑动下移受力分析
驱动轮自身可通过减速箱和驱动电机自锁,故不考虑驱动吸附轮滚动下滑情况。因球罐壁面为圆弧形,机器人在左右半球受力情况是对称的,且在上半球时吸附力和重力的分力共同提供正压力,其裕量充足,因此分析机器人在右下半球的状态来建立极限滑动模型。静摩擦力大小与不同角度下永磁体轮吸附力和重力的合力大小及橡胶垫与壁面的静摩擦因数紧密相关。对极限静摩擦情况的机器人进行受力分析,如图7所示。
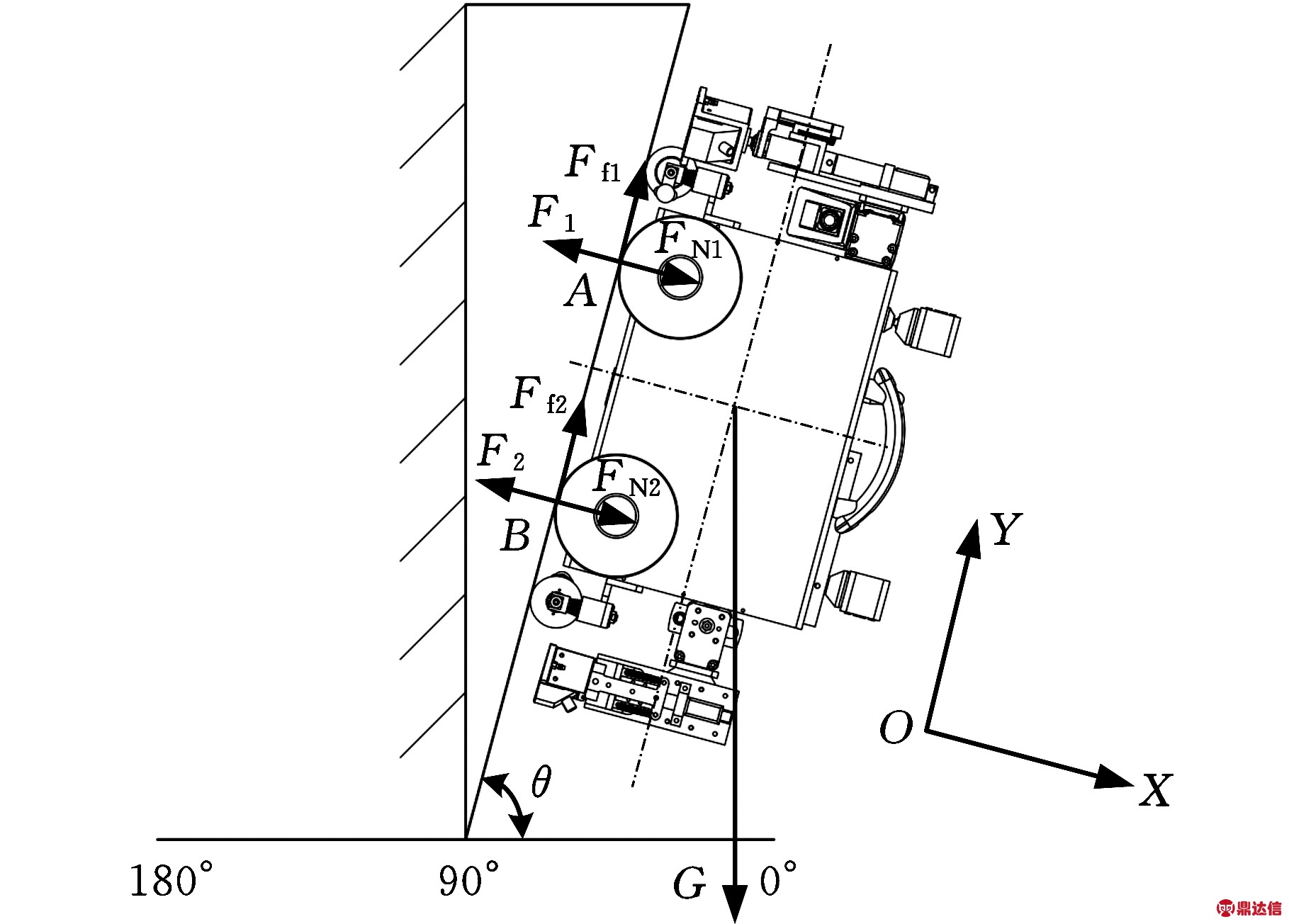
图7 向下滑动受力分析
Fig.7 Force analysis of model sliding downward
图7中,以壁面法向及切向建立坐标系OXY;储罐壁面与水平面夹角为θ;F1、F2分别为机器人前方、后方单侧吸附轮的吸附力总和;FN1、FN2分别为机器人前方、后方单侧吸附轮所受支持力总和;Ff1、Ff2分别为机器人前方、后方单侧吸附轮所受最大静摩擦力总和;G为机器人设计满载总重力;A为前方吸附轮与壁面之间的接触点;B为后方吸附轮与壁面之间的接触点。
在OXY坐标系中根据机器人受力情况建立受力方程,在即将发生向下滑动时,沿Y轴方向应该满足以下条件:
Ff1+Ff2-Gsin θ=0
(1)
Ffi=μFNi
(2)
式中,μ为驱动吸附轮与储罐壁面间的摩擦因数。
机器人沿X轴方向应该满足以下条件:
F1+F2-Gcos θ-FN1-FN2=0
(3)
此种情况假设前后两端的吸附力F1、F2,支持力FN1、FN2对称,即两两相等,以此计算在不同θ角度下,所需永磁体吸附力的极限值。
2.2 纵向倾覆受力分析
机器人纵向爬行发生倾覆的主要原因是重力矩大于前后侧两轮吸附力力矩而发生纵向失稳。随着壁面角度不同,发生失稳难易程度也不同,由理论分析可知,机器人在大型球罐下半球爬行时相比上半球更容易发生倾覆,因此主要考虑在右下1/4半球机器人的爬行情况。对不同θ角度下的受力进行分析,如图8所示。由图可知,倾覆情况按照前轮、后轮接触点分为两种。
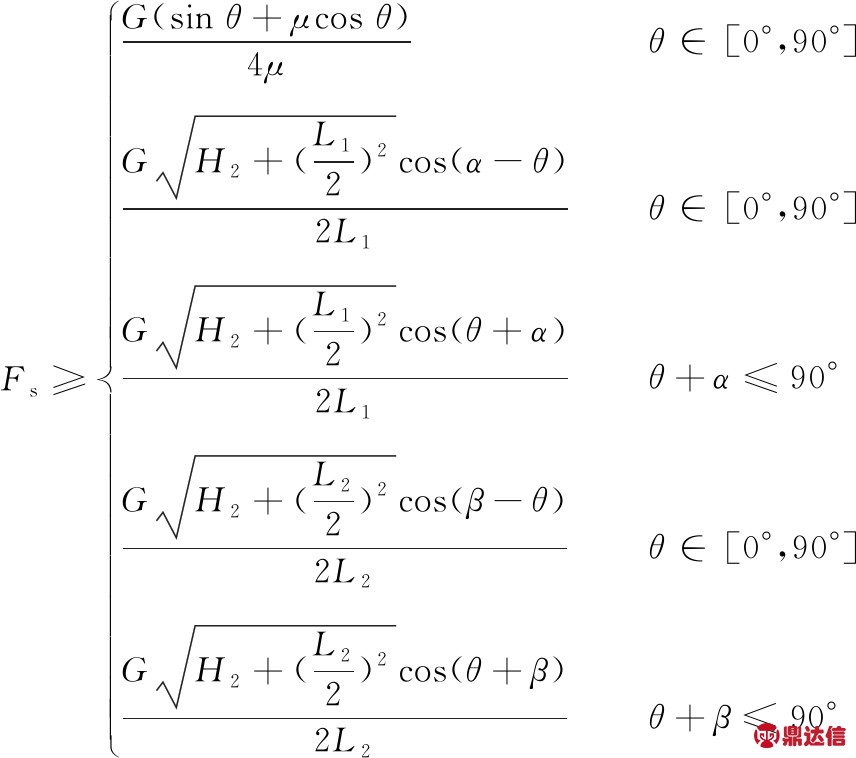
图8 纵向倾覆受力分析
Fig.8 Force analysis of model longitudinal rollover
图8中,A为以前方吸附轮作为旋转中心的倾覆点;B为以后方吸附轮作为旋转中心的倾覆点;L1为A、B两点间沿壁面距离;H为重心距离壁面的垂直高度;α为重心与A点的连线与壁面的夹角。
(1)若以A点作为倾覆点,则机器人只会在θ角度较小时发生纵向倾覆,当θ增至重心与A点连线为竖直向下时,倾覆力矩和防倾覆力矩同向,不会再发生倾覆。当机器人处于即将发生纵向倾覆的临界状态时,FN2大小为零,此时机器人整体应满足以下条件:
MF2-MG=0
(4)
即
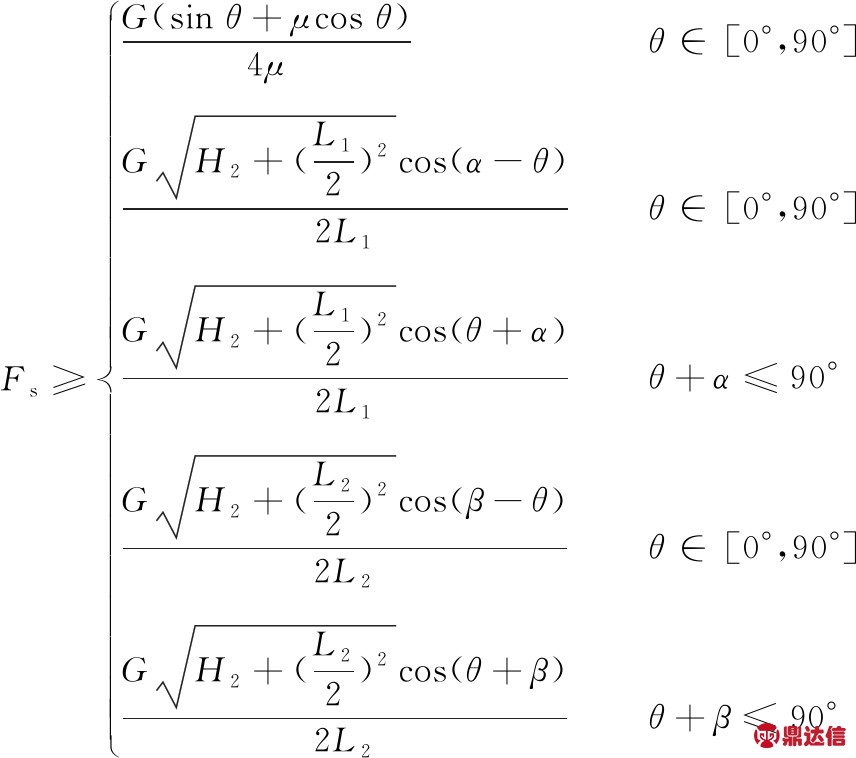
(5)
式中,MF2为抗倾覆力矩;MG为重力矩。
当θ+α≤90°时,可能会发生此种倾覆情况。
(2)若以B点作为倾覆点,则当机器人处于即将发生纵向倾覆的临界状态时,FN1大小为零,此时机器人整体应满足以下条件:
MF1-MG=0
(6)
即
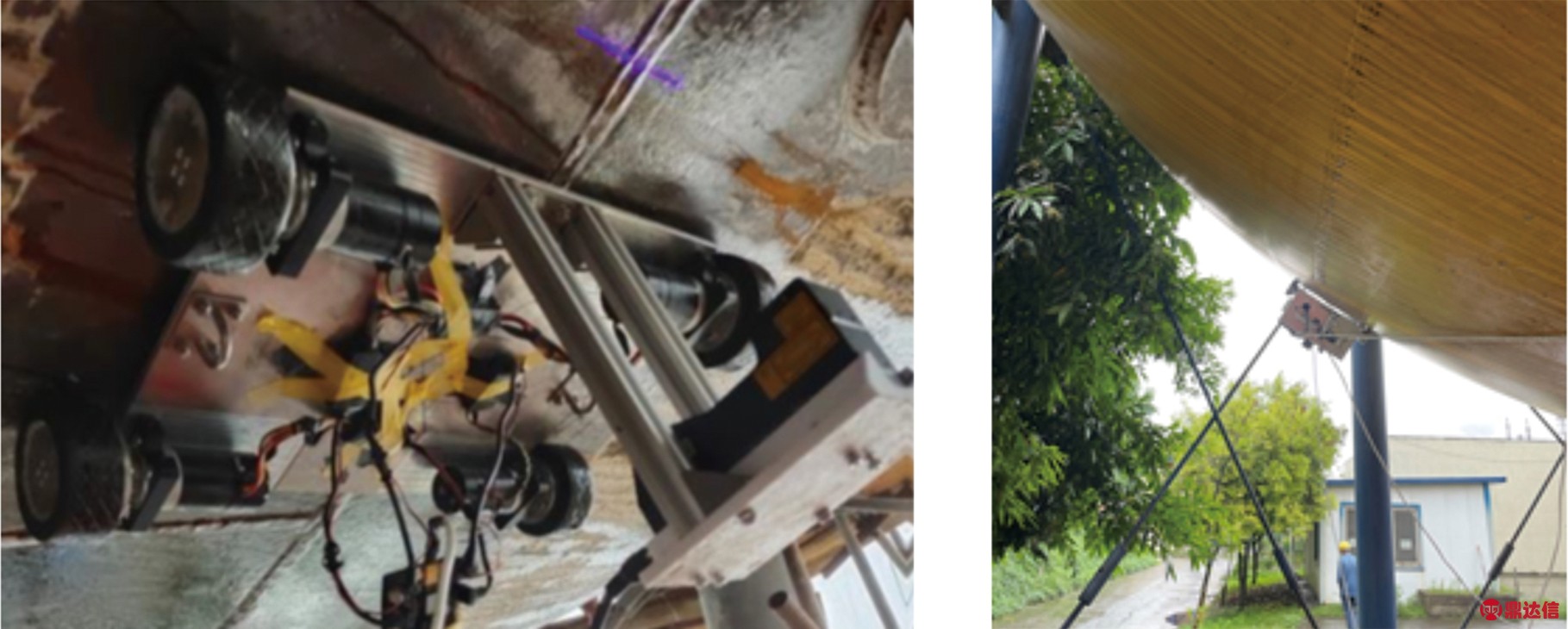
(7)
式中,MF1为抗倾覆力矩。
该倾覆情况对θ∈[0°,90°]都适用。
2.3 横向侧翻受力分析
对于机器人横向爬壁过程,其横向侧翻主要源于左右侧两轮的防倾覆力矩与重力倾覆力矩相互平衡。和纵向倾覆情况一致,机器人在球罐上半球运行时不易发生翻转,此处仍主要针对右下半球的情况进行分析。壁面角度θ∈[0°,90°],机器人所受重力倾覆力矩随之变化,总体分析思路和纵向倾覆情况一致。对不同θ角度下的受力进行分析,如图9所示。由图可知,翻转情况按照上侧、下侧接触点分为两种。
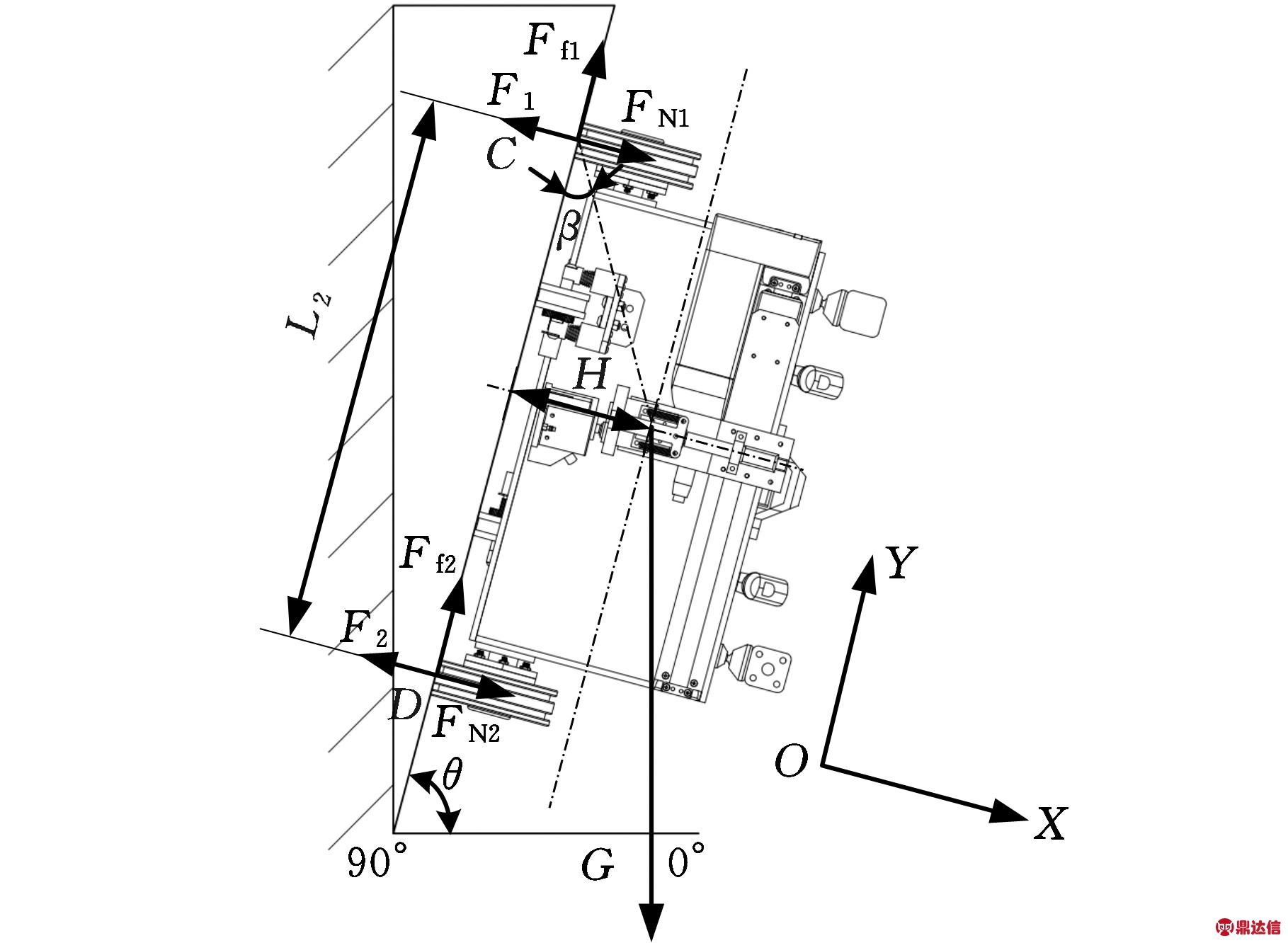
图9 横向侧翻受力分析
Fig.9 Force analysis of model lateral rollover
图9中,C为以上侧吸附轮作为旋转中心的倾覆点;D为以下侧吸附轮作为旋转中心的倾覆点;L2为C、D两点间沿壁面距离;β表示重心与C点的连线与壁面的夹角。
(1)若以C点作为倾覆点,则当θ+β≤90°时下侧吸附轮可能发生脱离失稳。在即将发生脱离的临界状态,下侧两轮所受壁面的支持力FN2大小为零,此时机器人受力应满足以下条件:

(8)
(2)若以D点作为倾覆点,则在上侧吸附轮即将发生脱离时,上侧两轮所受壁面支持力FN1大小为零,此时机器人整体应满足以下条件:

(9)
式中,F1为上侧吸附轮吸附力。
该倾覆情况对θ∈[0°,90°]都适用。
2.4 复合运动状态受力分析
上述三种失稳情况皆对应单一状态,为实现大型储罐的全覆盖检测,对机器人提出了全向驱动要求。在机器人转向过程中,会综合涉及多种受力状态。现对转向过程机器人建立运动模型。为了方便分析,提出以下假设简化模型:①附着系数充分,驱动吸附轮不存在打滑现象;②转向过程不考虑横向滑动;③在任意姿态下驱动轮阻力系数相同。
该机器人由4个驱动吸附轮组件独立驱动,转向过程通过双侧驱动电机差速来实现。如图10所示,假设该机器人的上下两侧驱动轮线速度为v1、v2,则当v1>v2时,机器人以旋转中心O′做右向转动;当v1<v2时,机器人左转;当v1=-v2时,机器人原地转动。当机器人本体中心O做匀速转向时,上下侧驱动轮存在恒定差速,若不考虑驱动吸附轮打滑及横向侧滑现象,则机器人的运动速度存在如下关系:
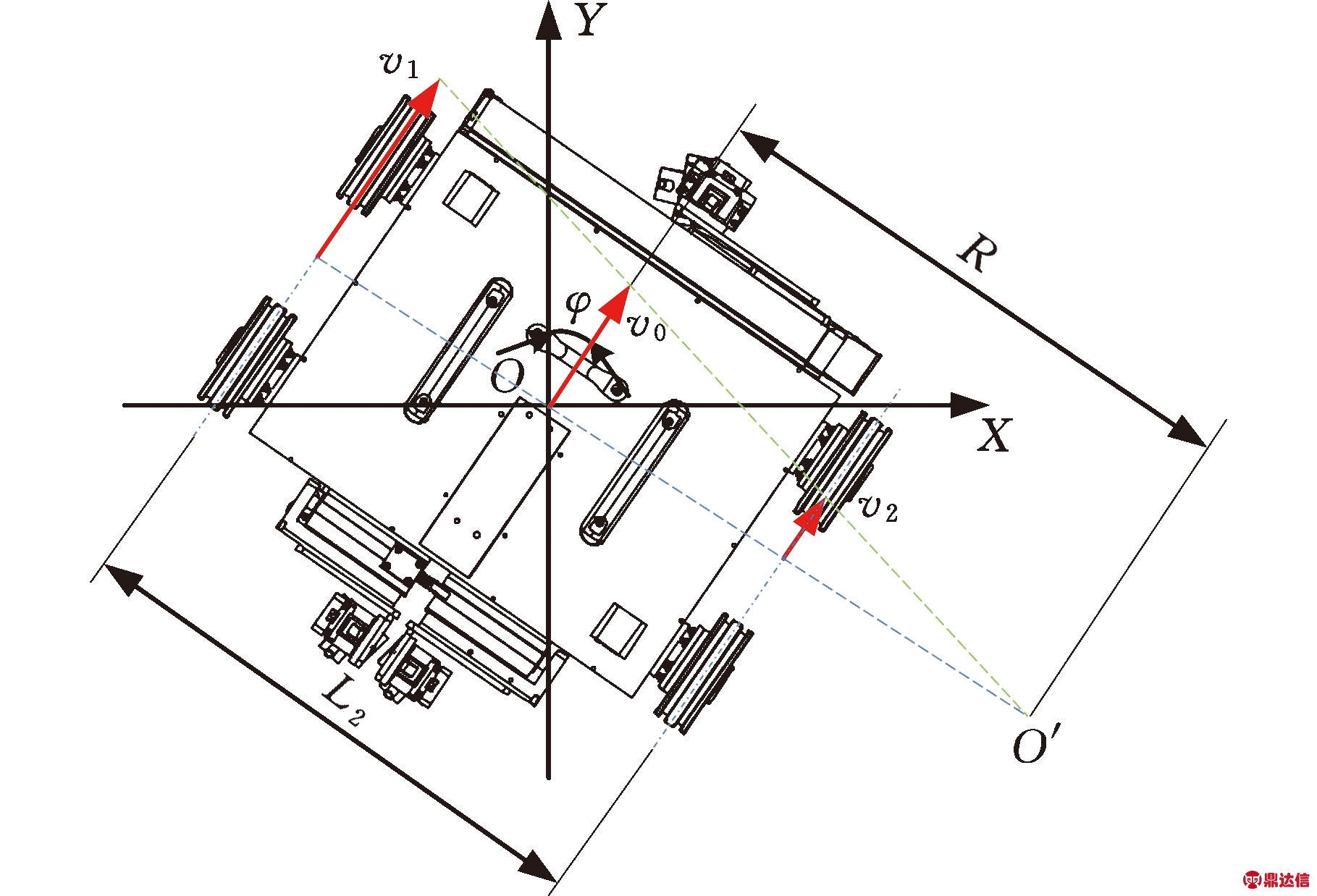
图10 转向示意图
Fig.10 Steering diagram
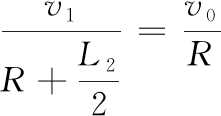
(10)

(11)
式中,v0为转向过程本体中心瞬时线速度;R为机器人理论转向半径。
由于检测过程机器人低速转向,故不考虑冲击振动。对转向复合运动过程的机器人建立力学模型。φ为0°或180°对应机器人处于纵向爬行状态;φ为±90°对应机器人处于环向爬行状态。角度在各象限范围变化时,对应机器人各种转向姿态。
对于不下滑情况,当重力方向与驱动轮周向平行时,即φ为0°或180°,静摩擦力方向与吸附轮线接触垂直,最易发生失稳,与前述不下滑模型一致,此处不再讨论。对于转向过程的不倾覆与不侧翻情况,当角度φ变化时,四个驱动吸附轮所处位置相对于重心的高度差不同,各轮吸附力的力矩都在[0,L2/2]范围变化,且不会同时有两个驱动轮处于极限脱离状态。仅在φ为0°、±90°或180°(即纵向、横向失稳状态)时,会有两个吸附轮处于同一高度,其中φ为0°或180°失稳力矩最大。因此,对低速转向过程分析可得,以纵向倾覆作为极限情况。
2.5 永磁体吸附力理论计算
结合上述几种运动模型受力分析,总结各种情况下的最小极限吸附力值,得到单个驱动吸附轮的吸附力仿真值Fs应满足以下条件:
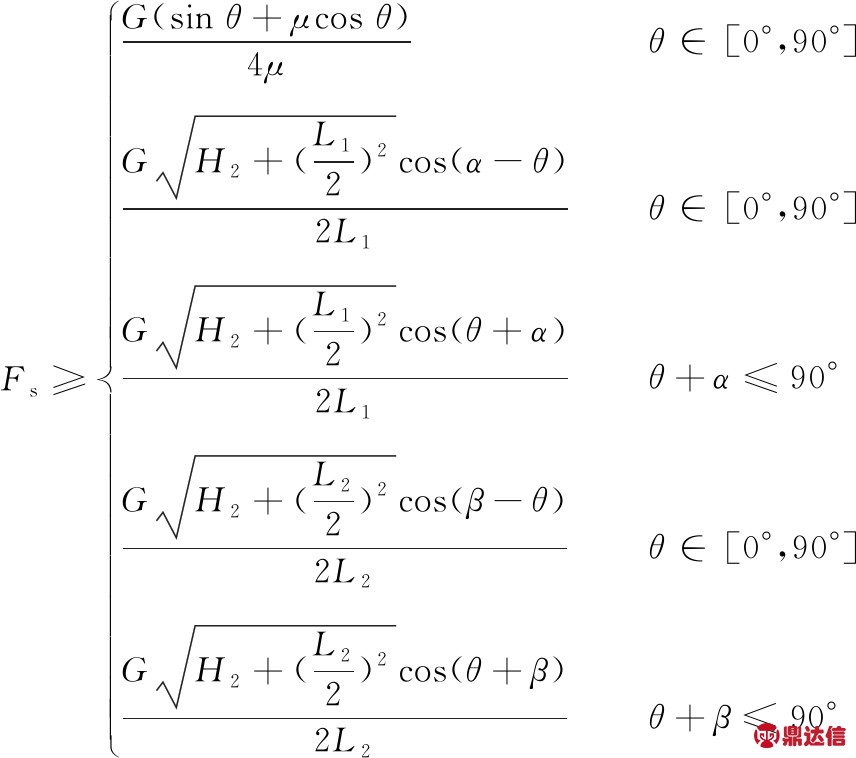
(12)
通过对失稳状态下单个驱动轮吸附力目标值的计算,确定最佳吸附力范围,从而设计出最优的永磁体吸附结构,提高机器人运行的可靠性和机动性。机器人参数初步取G=392 N、H=100 mm、L1=250 mm、L2=430 mm、μ=0.80。以此计算获得受力分析结果曲线,如图11所示。其中Fs1~Fs5依次为滑动下移、以A点纵向倾覆、以B点纵向倾覆、以C点横向侧翻、以D点横向侧翻在不同壁面倾角θ所对应的单个吸附轮吸附力仿真值;Fsmax为上述情况对应的单个吸附轮吸附力所需的最大值。
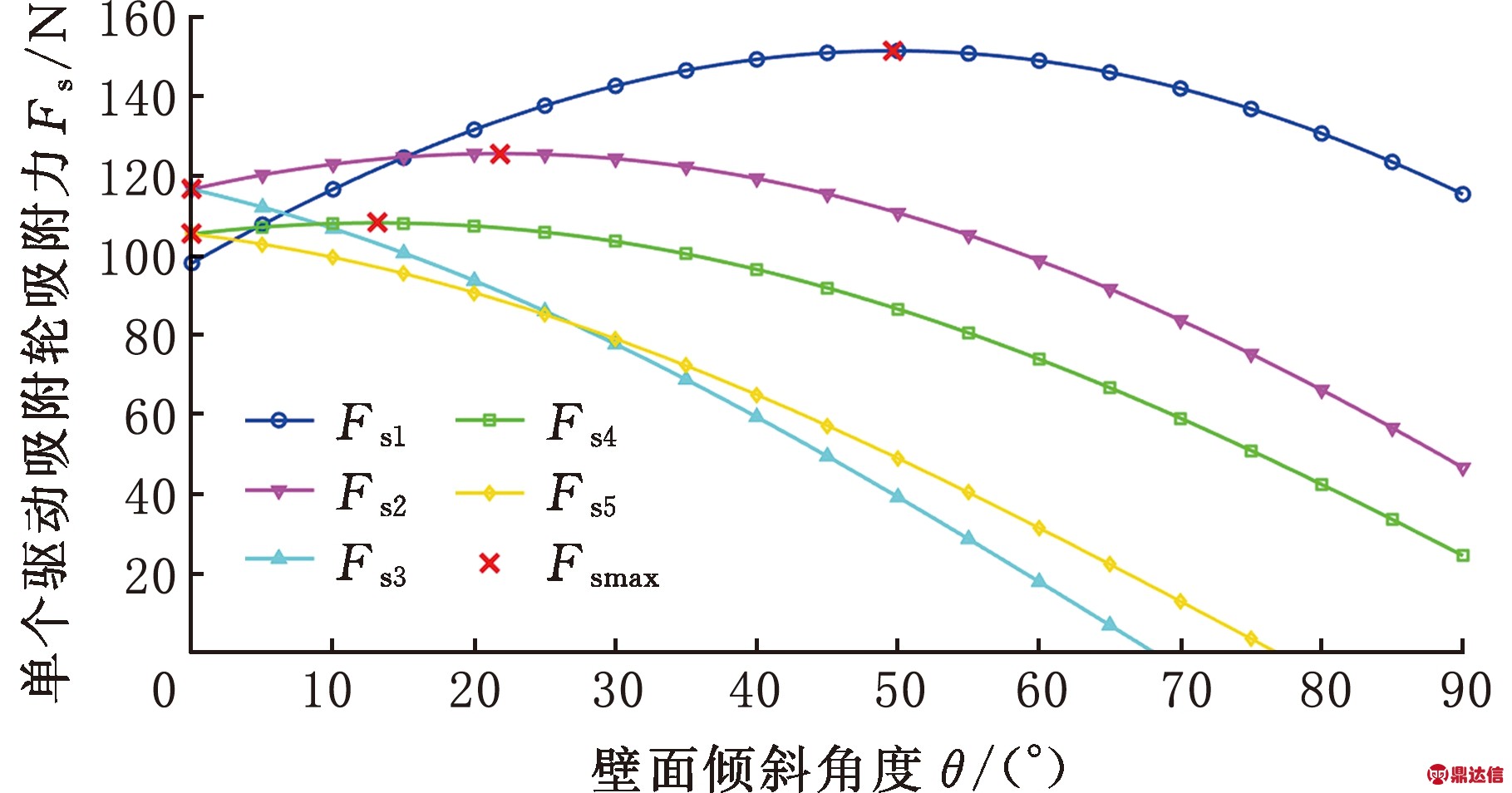
图11 单个驱动吸附轮吸附力Fs随θ变化曲线
Fig.11 Variation curve of adsorption force Fs of a single drive adsorption wheel with θ
由吸附力分析曲线可知,滑动失稳状态下所需极限吸附力最大;纵向倾覆和横向侧翻失稳在θ=0°时,上下两个危险点沿重力法线方向对称,吸附力值相等。单个驱动吸附轮极限吸附力Fsmax计算数值如表1所示。
表1 失稳状态受力分析计算结果
Tab.1 Force analysis and calculation results in unstable state
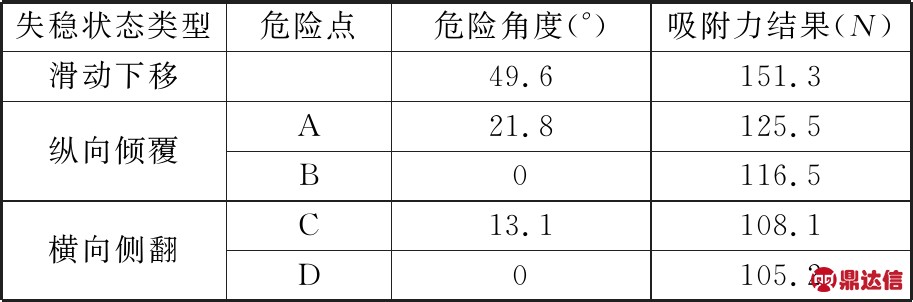
运行过程中,仅线缆会影响机器人重心位置。在超程检测距离下,考虑线缆极限长度为30 m,对应RG174信号线及RVV双芯电源线总质量约为5 kg,约占比机器人本体质量的1/5,对机器人重心偏移影响较小。
在静止下滑情况,柔性线缆与壁面的摩擦力不会影响机器人本体受力;在纵向倾覆或横向侧翻情况,受到尾部线缆重力拖拽,机器人本体重心会向后下端倾斜,这对抗失稳性能是有利的。
在线缆影响最大的纵向倾覆极端情况下(θ=21.8°),线缆重心偏移高度H增大约20%,计算出驱动轮吸附力极限增加10%,仍小于静止下滑吸附力的最大极限,因此在受力分析过程中可以简化为本体中心与重心重合。
综上,驱动吸附轮结构设计应优先满足滑动下移要求,单个永磁体吸附力应大于151.3 N。另外,永磁体轮的布置也会影响机器人的稳定性,此处仅对既定参数L1、L2、H来分析各失稳状态,通过参数化扫描可确定相关尺寸的最佳参数,L1、L2增大,H减小可有效降低各种失稳风险。
3 永磁体吸附磁力仿真及结构优化设计
永磁体吸附力值与烧结材料牌号和质量体积相关。为增强驱动吸附轮的吸附能力,提高结构磁质比,采用图12a所示的对向磁极布置磁回路结构[16],并使用Ansoft Maxwell软件对永磁体轮结构磁力线分布进行仿真,如图12b所示。
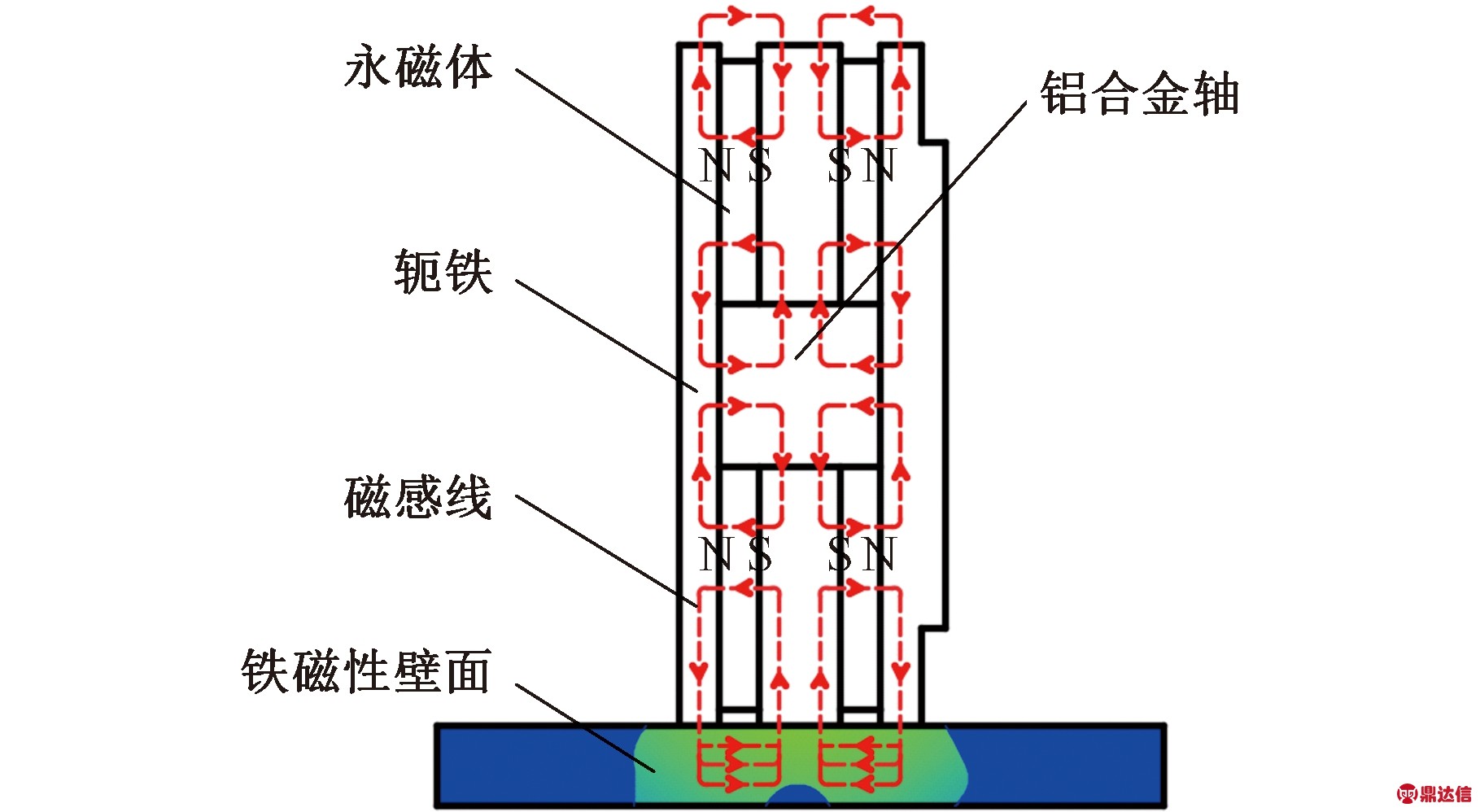
(a)驱动轮磁路设计原理模型
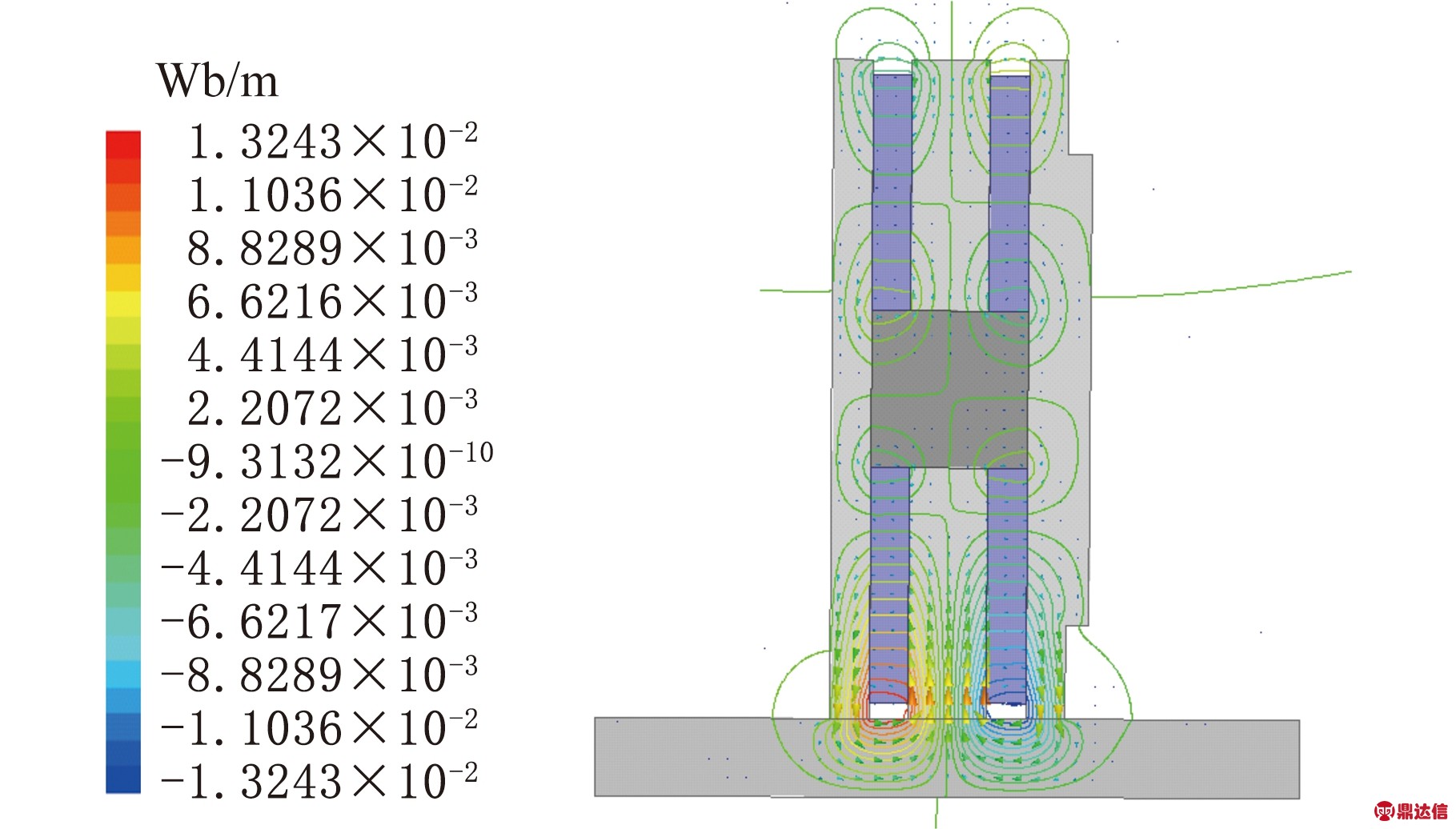
(b)驱动轮磁力线分布
图12 驱动吸附轮磁路模型及磁力线分布
Fig.12 Magnetic circuit model and magnetic field lines distribution of driving adsorption wheel
3.1 永磁体驱动轮建模分析
参照图4所示的永磁体驱动轮结构,综合机器人底板高度及负载要求,现拟定永磁轮尺寸参数。永磁体材料为烧结钕铁硼N35H[17],永磁体环内径26 mm,外径80 mm,宽度5 mm;衔铁材料Q235,内径20 mm,外径84 mm,厚度5 mm;导磁环内外径参数与衔铁一致,厚度10 mm;橡胶垫厚度2 mm(带滚花槽深度1 mm);隔磁轴及套筒材料为6061铝合金。设定吸附壁面材料为Q345R、最小壁厚10 mm,对驱动轮结构磁感应强度进行仿真,如图13所示。
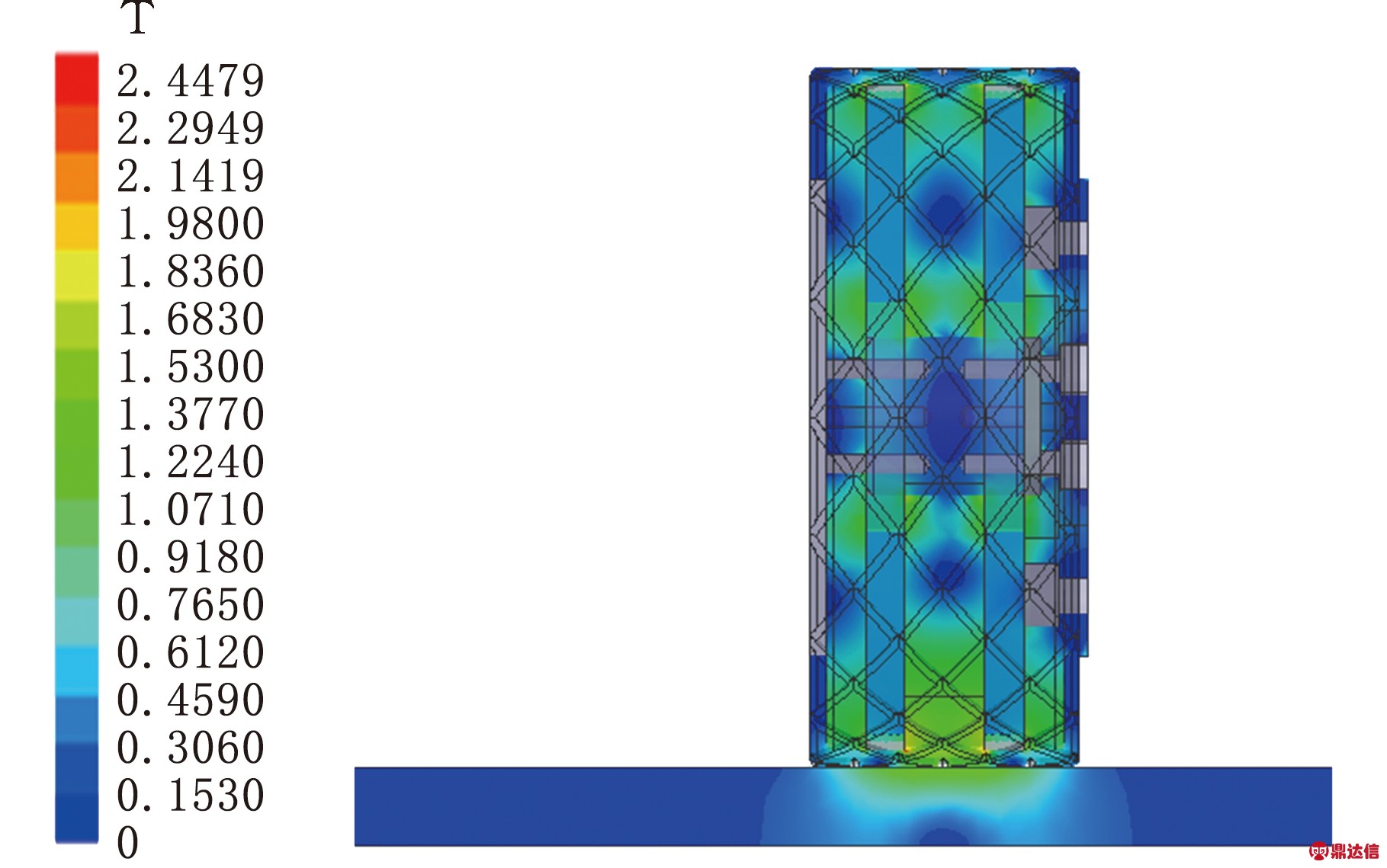
图13 驱动轮磁感应强度云图
Fig.13 Magnetic induction intensity cloud map of driving wheel
3.2 永磁体驱动轮参数化优化扫查
爬壁机器人应适用于各类标准规格的储罐,因此结合不同使用工况对吸附效果进行仿真分析。打磨后的焊缝余高为0~4 mm,机器人在跨越焊缝时存在抬离间隙增大而脱离壁面的危险。储罐壁厚随容积变化集中于10~40 mm。故对0~4 mm提离间隙、0~40 mm壁面厚度作参数化扫查仿真,如图14所示。
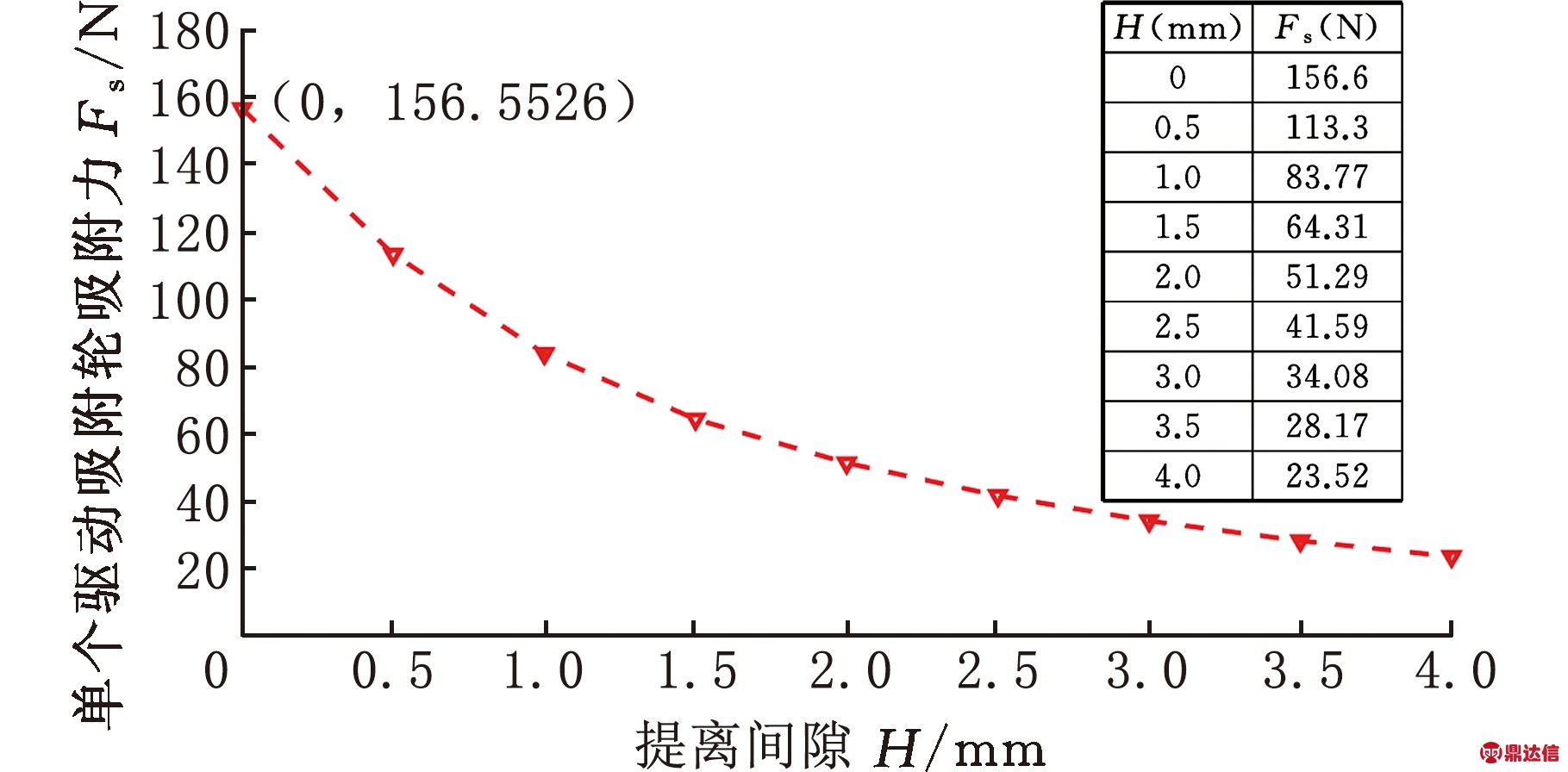
(a)随提离间隙的变化
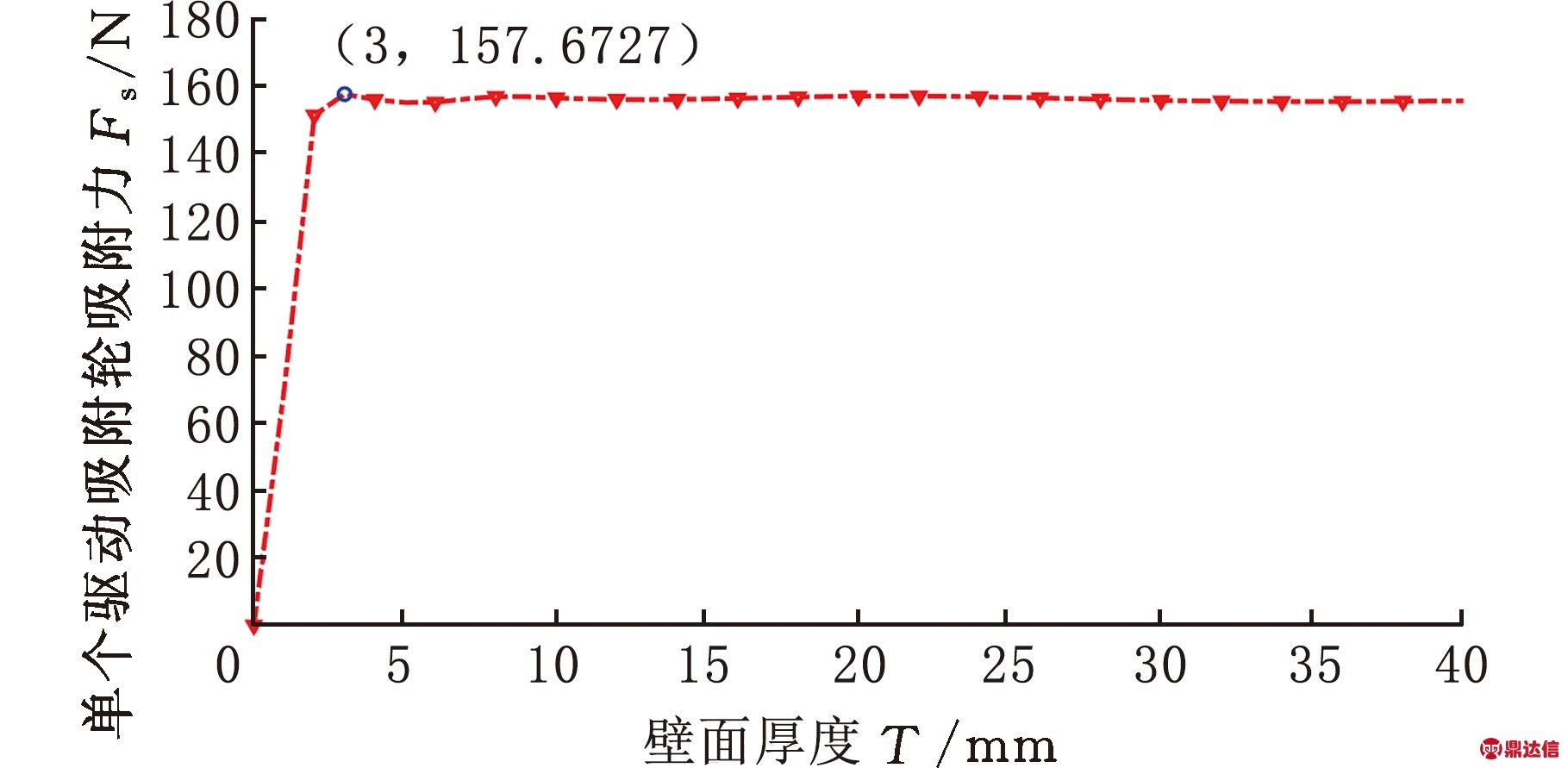
(b)随壁厚的变化
图14 驱动吸附轮吸附力变化曲线
Fig.14 Adsorption force curve of driving adsorption wheel
由参数优化仿真结果可知,当壁厚大于3 mm时,接触面上磁感线已趋近饱和,随着壁厚的进一步增大吸附力波动不明显,在壁厚为10 mm时吸附力为156.6 N,满足要求,因此对各容积的储罐检测应着重考虑焊缝余高对机器人越障性能的影响。
分析提离间隙对吸附力的影响,吸附力有明显减弱现象,前侧轮同时跨越焊缝时,如果运行初速度较大,受重力向心力的影响,两侧前轮极易脱离焊缝壁面。越障时,驱动轮的运行过程可以分为接触焊缝、离开壁面、再次接触壁面、离开焊缝。其外覆橡胶垫在吸附力和重力共同作用下变形,最大变形量为0.5 mm,以之作为越障脱离间隙,此时对应驱动吸附轮的吸附力为113 N,变化差值为43 N,则前侧双轮共同吸附力减小86 N。此时需由一个辅助吸附结构来补偿该吸附轮损失,避免机器人失稳坠落。
3.3 辅助吸附轮建模分析
结合前述各种失稳状态计算及驱动吸附轮越障过程分析,辅助吸附轮提供储备吸附力,避免越障失稳。为补充越障时的吸附力损失,单个辅助吸附轮吸附力需达到86 N。取安全系数为0.8,拟设计辅助吸附轮吸附力为107.5 N以上,通过压簧结构自适应壁面高度上下浮动调整吸附力,保证机器人本体总体吸附力的恒定。现对辅助吸附轮结构进行静磁场仿真,如图15所示,其磁感应强度可以满足安全裕度需求。
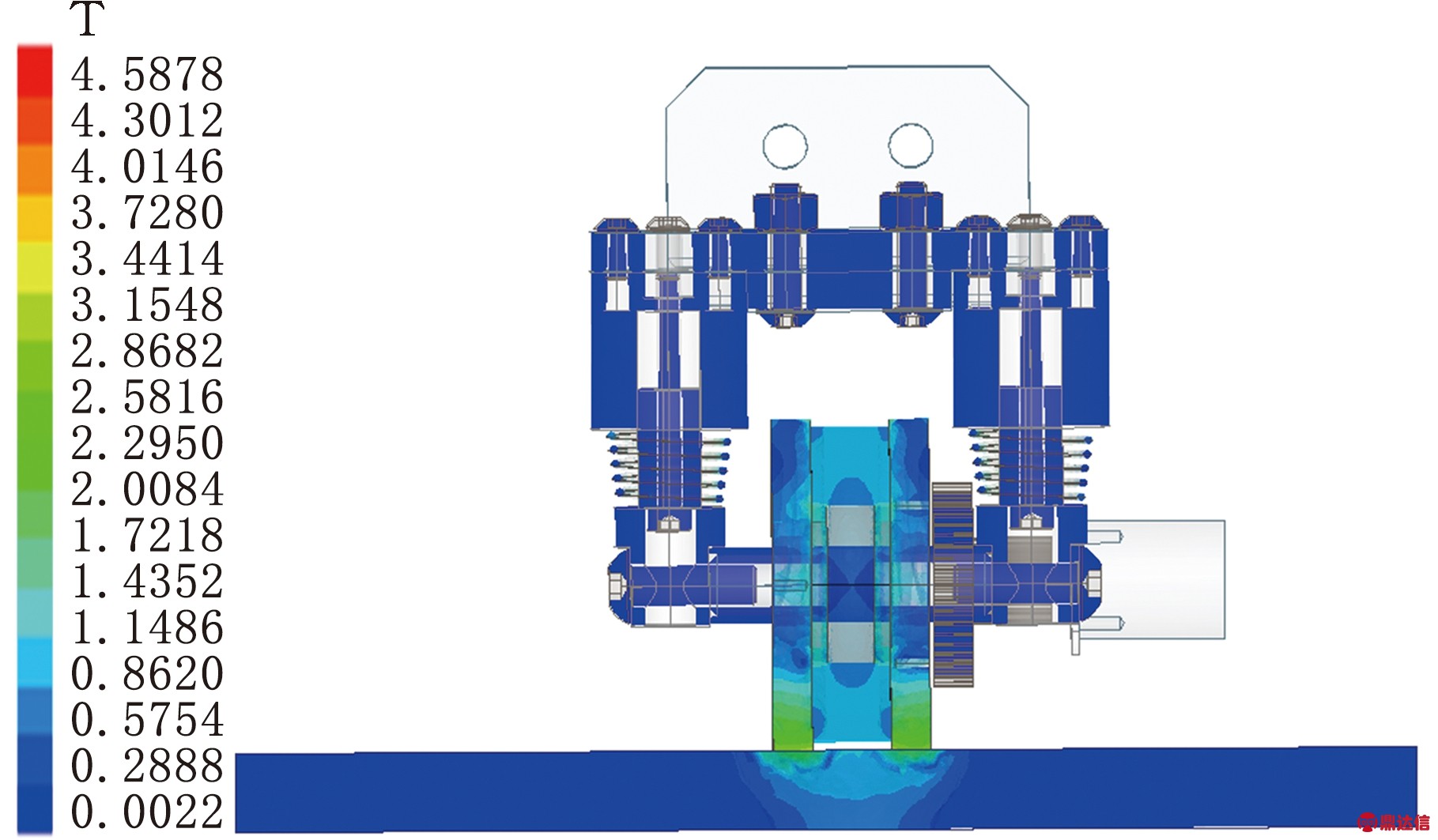
图15 辅助吸附轮的磁感应强度云图
Fig.15 Magnetic induction intensity cloud map of auxiliary adsorption wheel
4 爬壁机器人性能测试实验
根据优化仿真结果,设计加工机器人本体,如图16所示。在此基础上,开展实验验证机器人本体的吸附、驱动、扫查性能。
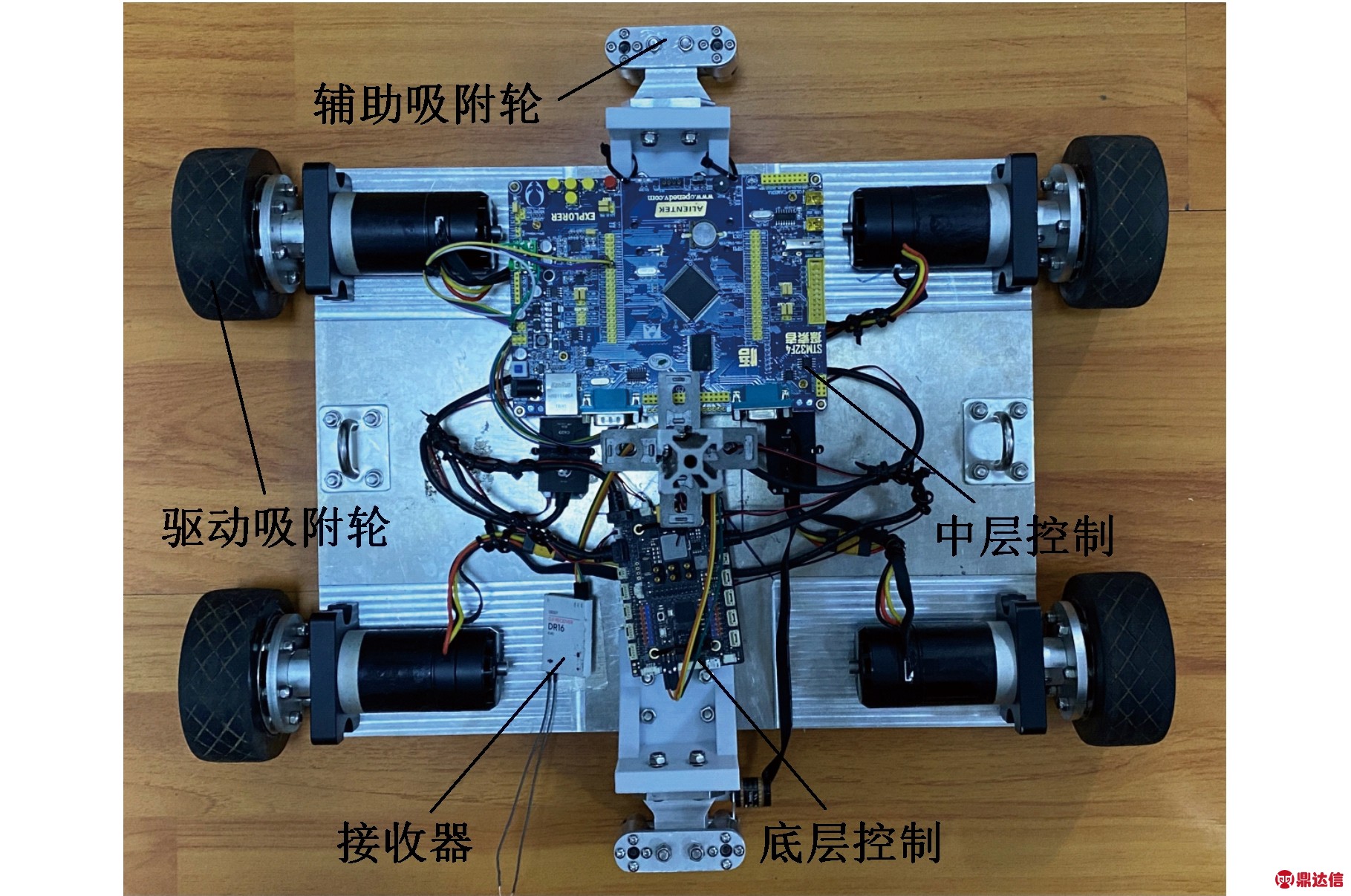
(a)机器人底板结构
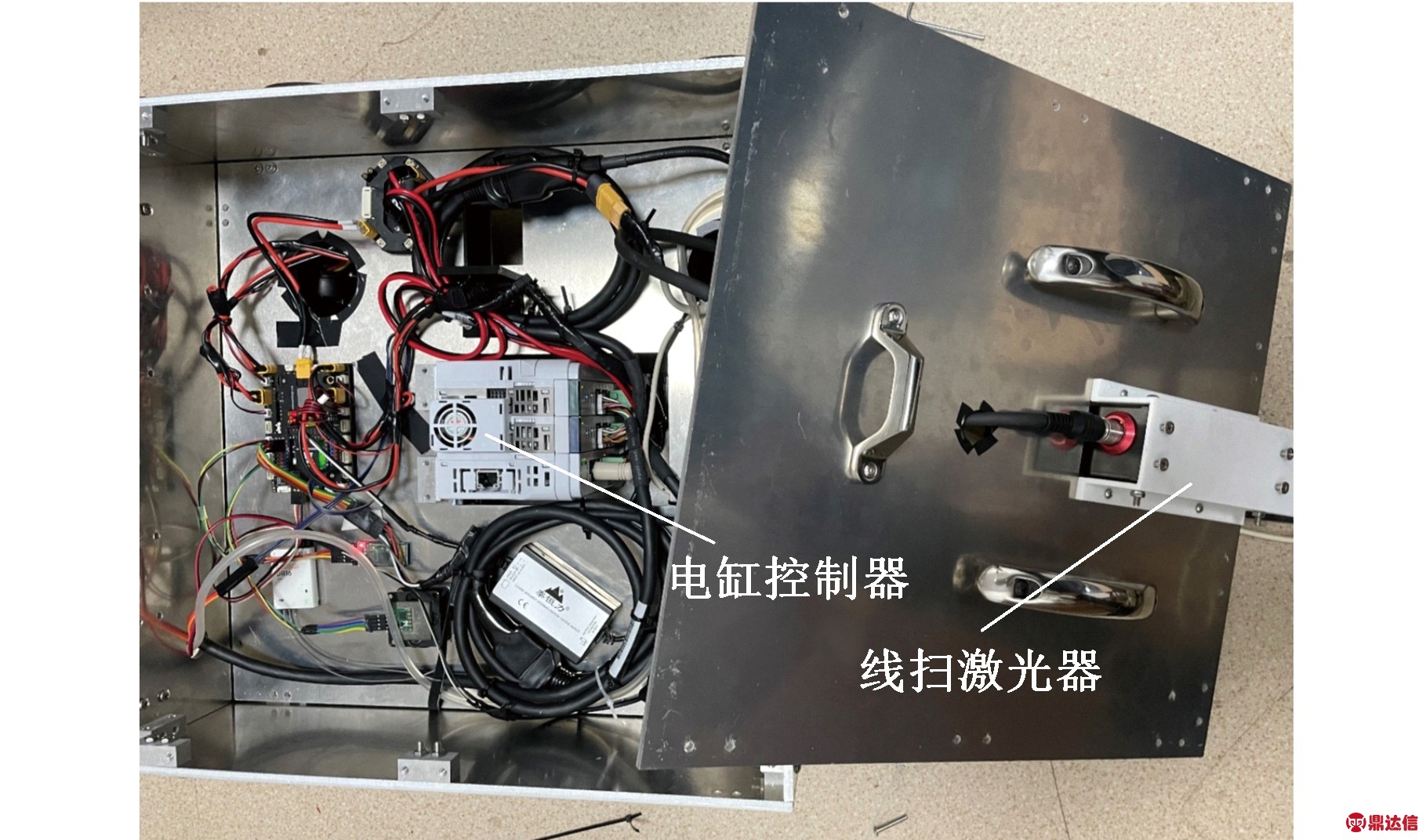
(b)机器人组装结构
图16 爬壁机器人本体实物图
Fig.16 Photos of the wall-climbing robot body
4.1 静态吸附力测试
试块壁面材料为Q235,厚度d=10 mm。机器人吸附于壁面下方,实验底板整体质量为10 kg,以不同质量的杠铃片递增负载来测试,如图17所示。
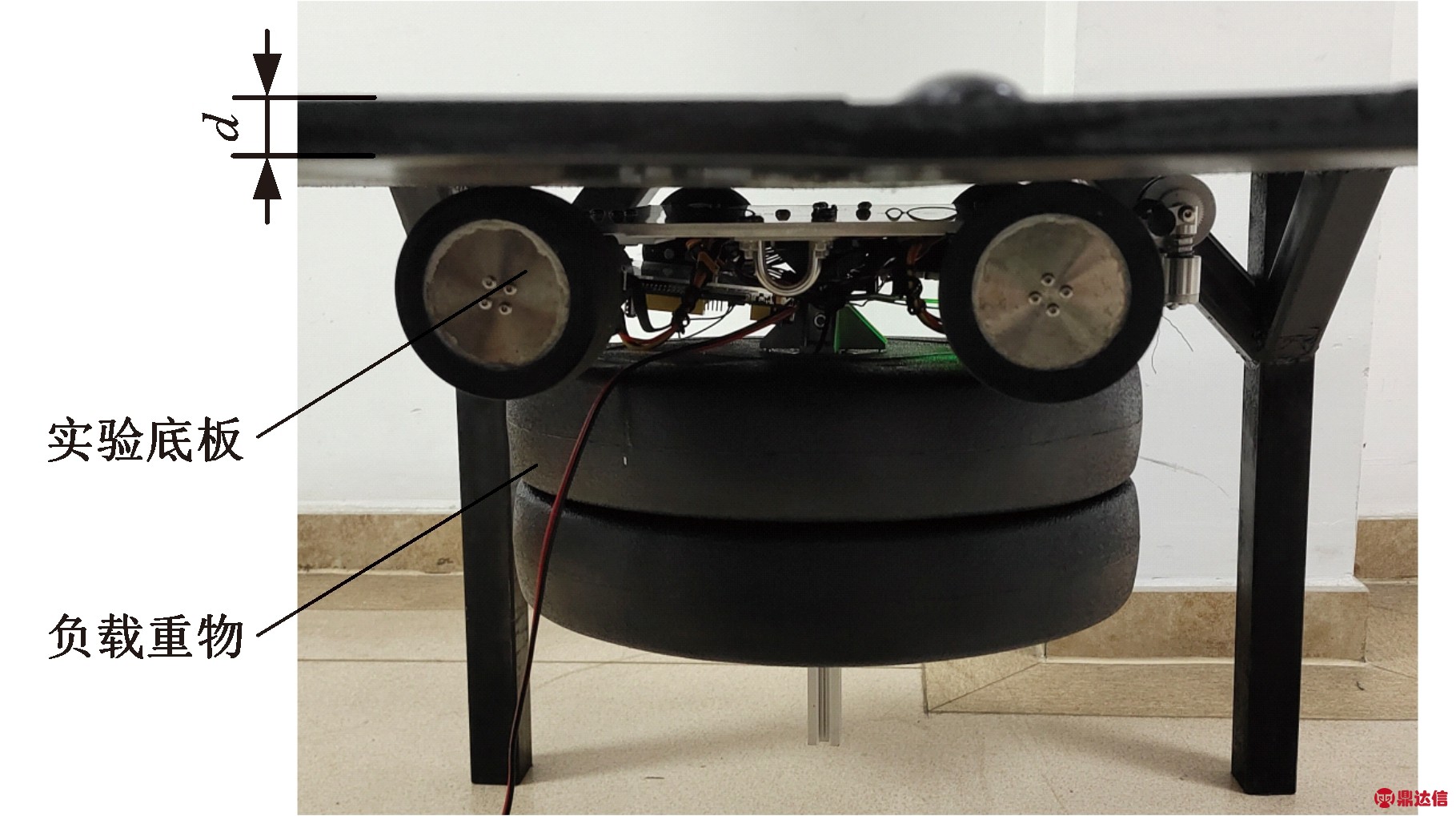
图17 底板静态吸附测试
Fig.17 Chassis static adsorption test
以整机质量为10 kg、25 kg、40 kg进行测试实验。结果表明,在40 kg满载情况下,机器人具有良好吸附效果。
4.2 性能测试
对满负载整机质量40 kg的机器人进行失稳状态性能测试,如图18所示。图18a所示为在50°壁面上进行滑动下滑测试,通过电机上电自锁,驱动轮输出被锁止,吸附力带来的摩擦力能克服自身重力防止吸附轮下滑。图18b所示为对垂直壁面横向防侧翻模拟,由驱动电机间差速可实现底板任意多方向转向。图18c所示为对垂直壁面驱动电机爬坡、越障性能测试,电机由电调输出控制电流信号,闭环控制转速,保证底板的运转精度,在垂直壁面上匀速向上爬行,驱动性能良好,未出现低速爬行现象;在跨越焊缝时,辅助吸附轮的预紧结构接触和离开焊缝会上下波动,减少冲击,越障过程平稳。图18d所示为底板吸附于壁面底面,壁面角度为13°,电机满足0~300 mm/s调速范围,底板在驱动实验中牢固吸附于表面,跨越焊缝时未发生倾覆现象。图18e所示为机器人本体携带传感器扫查在役球罐焊缝,提取坐标信息调整各驱动轮差速转向,实时沿焊缝爬行。图18f所示为中机器人在储罐危险角度上爬行测试,完成正反向及转向运行。实验表明,该爬壁机器人能满足大型储罐的检测需求,在各种壁厚的壁面的各种位置上自适应吸附、转向,具有一定的越障能力及抗冲击性,可完全覆盖储罐焊缝缺陷的扫查区域。
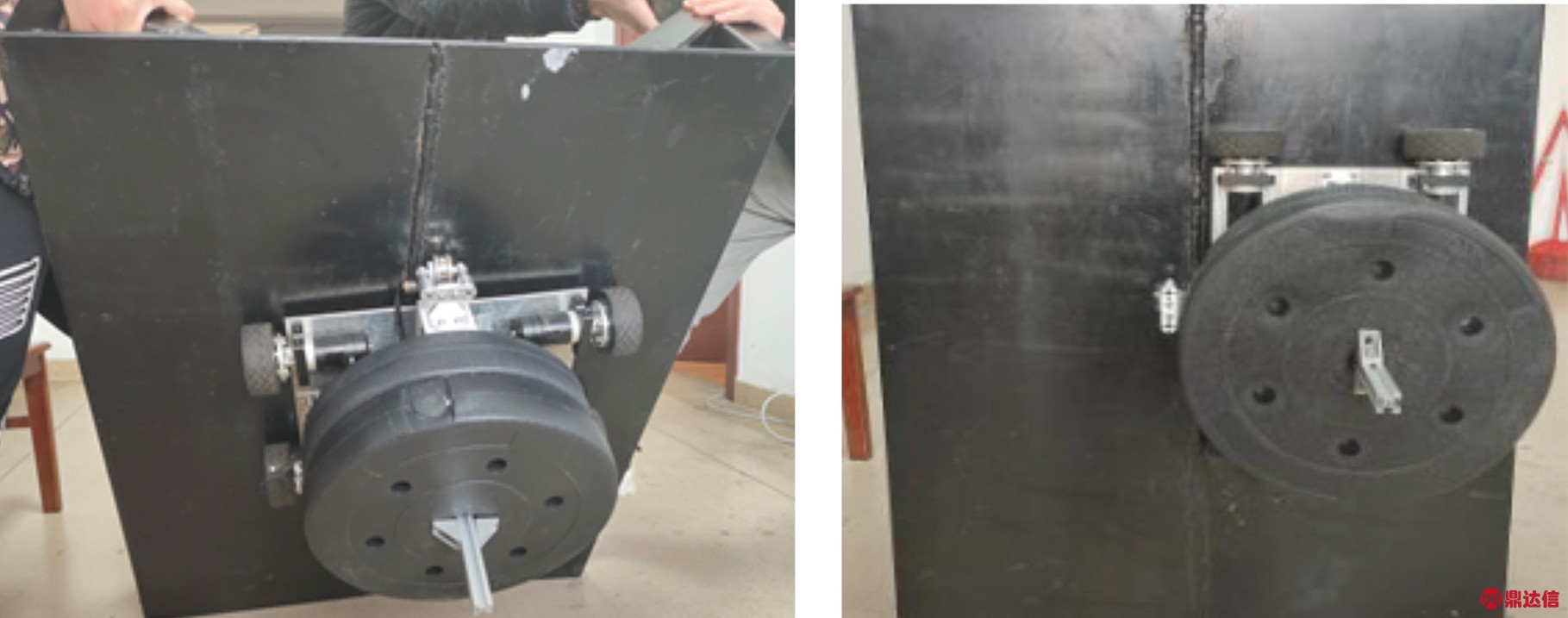
(a)防滑动测试 (b)横向防翻转测试
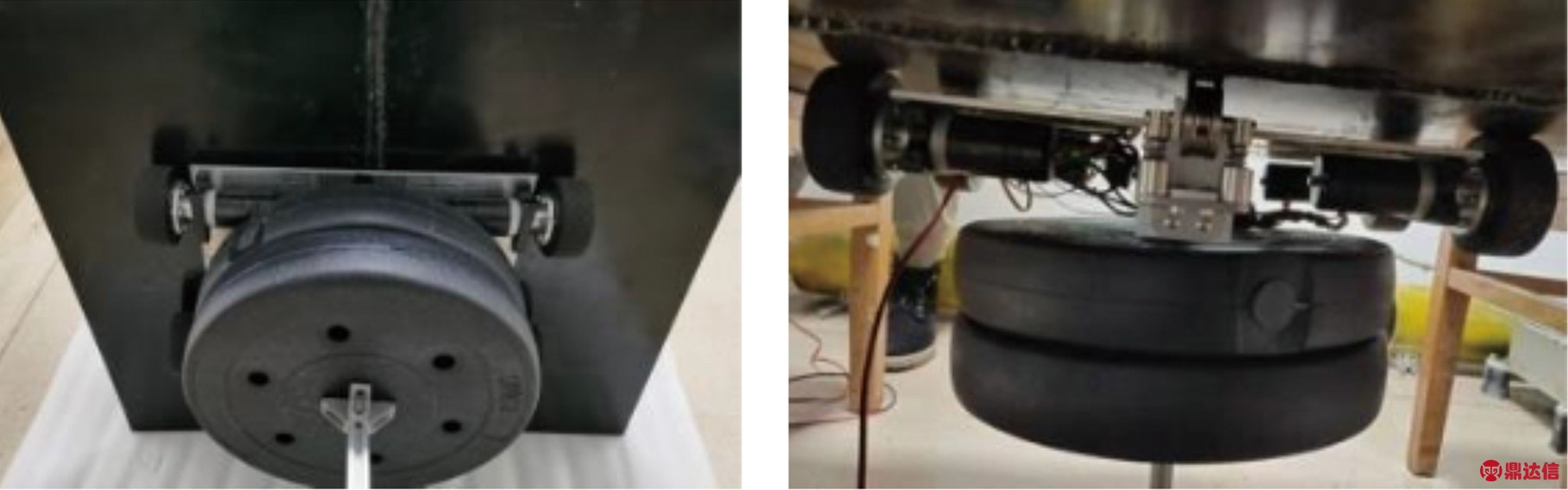
(c)垂直驱动越障测试 (d)纵向防倾覆测试
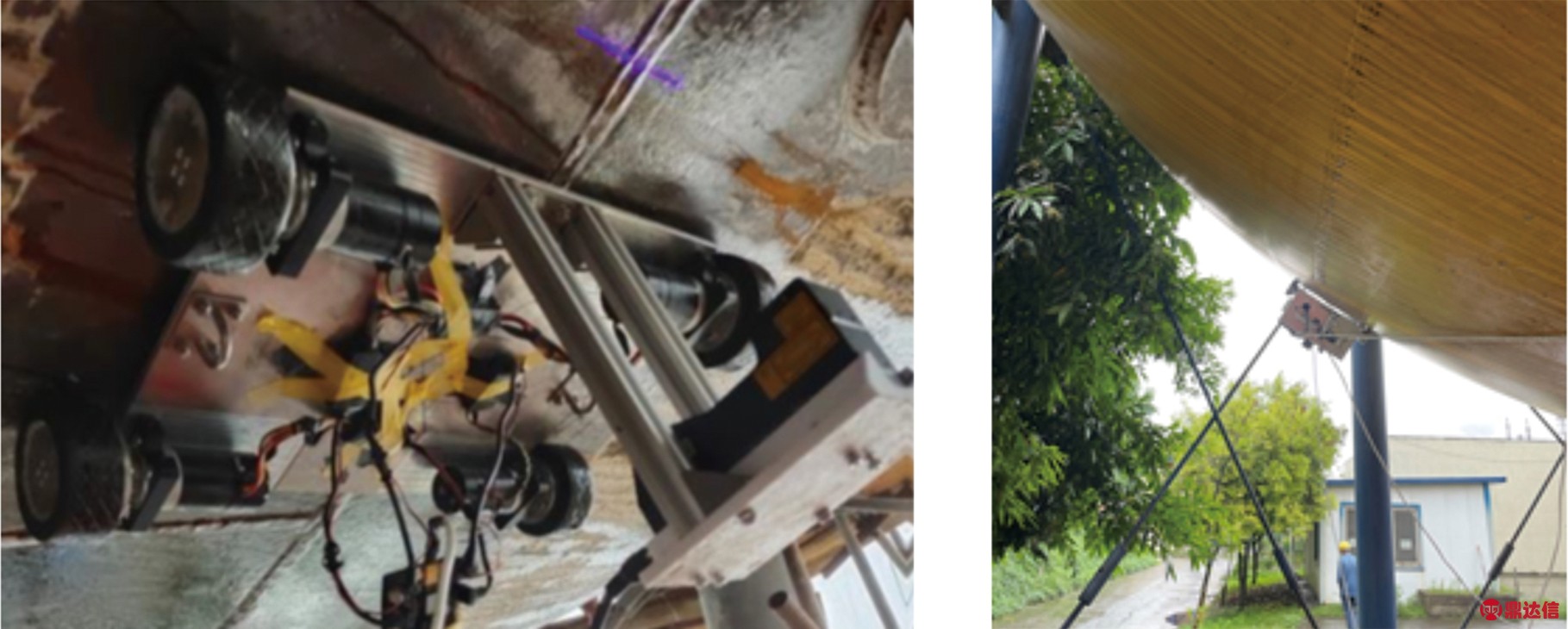
(e)在役储罐焊缝检测测试(f)在役储罐全覆盖驱动测试
图18 爬壁机器人性能测试
Fig.18 Wall-climbing robot performance test
5 结论
(1)本文以大型储罐焊缝缺陷检测为背景,通过计算各失稳状态下的极限吸附力,设计出一款能满足大型储罐焊缝检测需求的爬壁机器人。通过力学分析及仿真,球罐爬壁机器人在下半球49.6°处为吸附危险点,对于满负载本体,单个驱动轮吸附力需满足151.3 N。实际测试时对此关键点反复测试确保安全性。
(2)由本体性能实验可知,在极限工况下该爬壁机器人能满足检测需求。在满负载情况下,机器人能完成驱动、越障、转向、循迹、定位等功能。
(3)辅助吸附轮能增强机器人抗失稳能力。在爬壁机器人装配辅助吸附轮后,增大整体吸附力及防倾覆力矩,等效延长吸附力力臂,从而适应各姿态下的吸附爬行。
在后续工作中将进一步搭载超声检测探头,实现对焊缝区域全面覆盖自动化检测。