摘要:为解决模块化机器人重构后误差的快速补偿问题,对模块化机器人几何误差来源进行分析,将其划分为模块参数误差和模块间装配参数误差。基于指数积公式和齐次变换对关节模块、连杆模块及模块间装配位姿进行数学描述,建立关节-连杆子装配体的实际运动学模型。给出一种基于精密球和外部测量的模块参数及模块间装配参数辨识方法,完成子装配体运动学参数的辨识。针对两种典型构型的关节-连杆子装配体进行参数辨识和验证试验。试验结果表明,经误差补偿后子装配体的平均定位误差约为补偿前误差的1/30。
关键词:模块化机器人;几何误差分析;参数辨识;误差补偿
0 引言
模块化机器人由关节模块和连杆模块等组成,能够通过标准化的接口实现机械和电气连接,面向任务组装成不同构型、自由度的机器人以满足不同工作需求。生产过程中的制造公差、装配误差、重构产生的装配误差和使用过程中产生的磨损等,导致模块化机器人重构后实际运动学模型偏离理论模型,不利于离线编程应用和高精度轨迹控制。目前,针对模块化机器人重构后位姿误差补偿的研究主要有两种思路。
第一种思路是将重构后的模块化机器人作为普通串联机器人进行运动学参数标定[1-6]。这种方法可以有效补偿重构后机器人的位姿误差,但每次重构后会引入装配误差,需要专业的技术人员根据重构后机器人的具体构型设计标定试验,再次进行标定,操作繁复。
第二种思路是针对模块化机器人的组成模块进行参数标定,通过对由模块或子装配体构成的多个机器人进行联合标定[7-8],实现组成模块的参数辨识,并根据标定值对重构后的机器人运动学模型进行修正。这种方法可以补偿由经过标定的模块或子装配体组成的机器人的位姿误差,但工作量大,操作繁琐,在引入新的模块或模块发生磨损后,需对所有模块或子装配体进行重新标定。文献[9]设计了一种模块接口,通过测距传感器测量模块接口,利用传感器测量值与接口间的几何关系,实现了模块间装配误差的测量解耦,但仅在平面内考虑装配误差,不能实现位姿误差的补偿,并且未对模块参数标定展开详细研究。
本文分析模块化机器人的几何误差来源,将其划分成模块参数误差和模块间装配参数误差,并基于外部测量给出一种模块化机器人组成模块参数和模块间装配参数的辨识方法。
1 误差分析
影响机器人位姿精度的误差来源可分为几何误差和非几何误差。几何误差主要来自生产环节的加工、装配误差。非几何误差主要来自关节和连杆的柔性、齿轮侧隙及温度造成的热变形等。几何误差占据了机器人定位误差来源的90%左右[10]。对于模块化机器人,其定位误差主要来自生产过程和重构过程产生的几何误差[8]。
1.1 关节模块误差分析
在关节模块的输入端、输出端机械零位以及输出端电子零位分别定义输入坐标系(下标JI)、输出坐标系(下标JO)和电子零位坐标系(下标JD),如图1所示。以输出坐标系相对输入坐标系的位姿矩阵TJ表示理论关节位姿,电子零位坐标系相对输出坐标系的位姿矩阵TD表示理论关节零位位姿。理论上,关节电子零位与机械零位重合,TD为单位矩阵。关节理论运动学模型根据指数积公式[11]可表示为
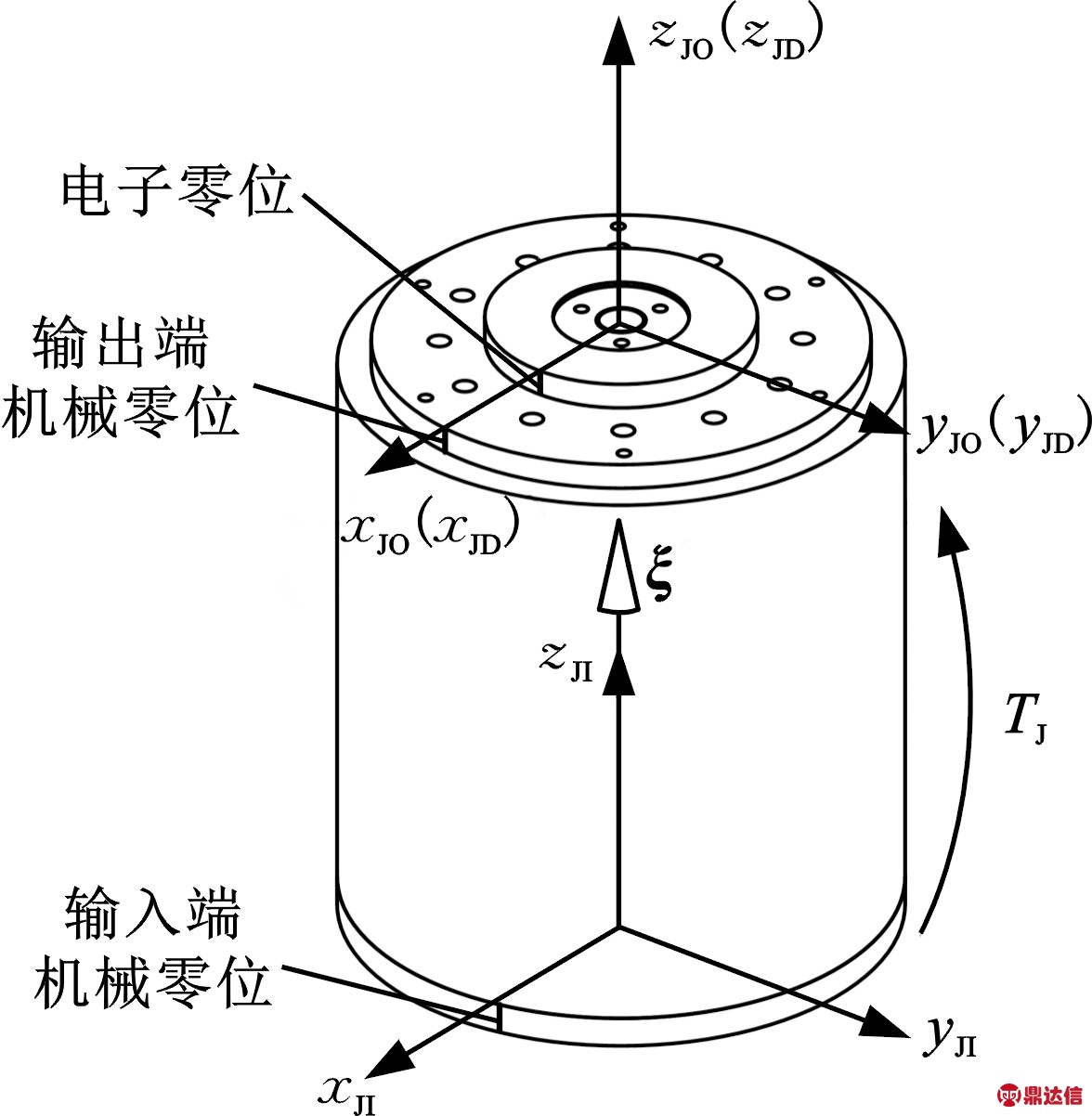
图1 关节坐标系定义
Fig.1 Definition of joint frame

(1)
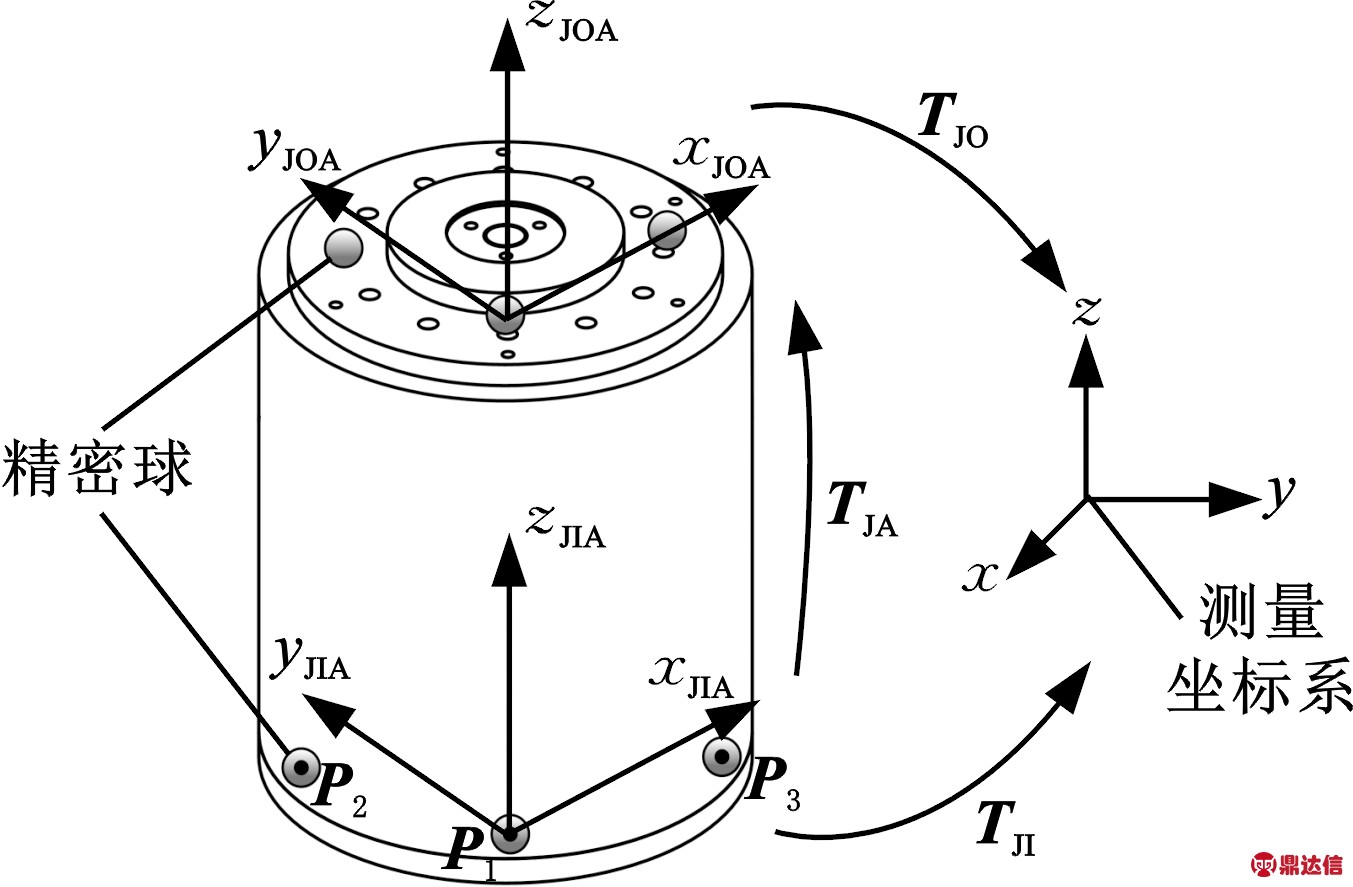
ω=[ω1 ω2 ω3]T ν=-ω×r


式中,θ为关节角;为关节运动旋量在关节输入坐标系中的表示;ω为单位向量;
是一个反对称矩阵;r为关节轴线上一点在关节输入坐标系中的坐标。
关节模块几何误差可以分为以下四类。
(1)关节位姿误差。关节零件的制造公差使关节尺寸、形状偏离理论值,导致实际关节输入坐标系(下标JIA)和关节输出坐标系(下标JOA)偏离理论位置,如图2a所示。实际关节位姿用TJA表示。
(2)关节旋量误差。制造公差和关节零件的装配使得关节轴线偏移导致关节旋量误差,如图2b所示。实际关节运动旋量坐标用ξa表示。
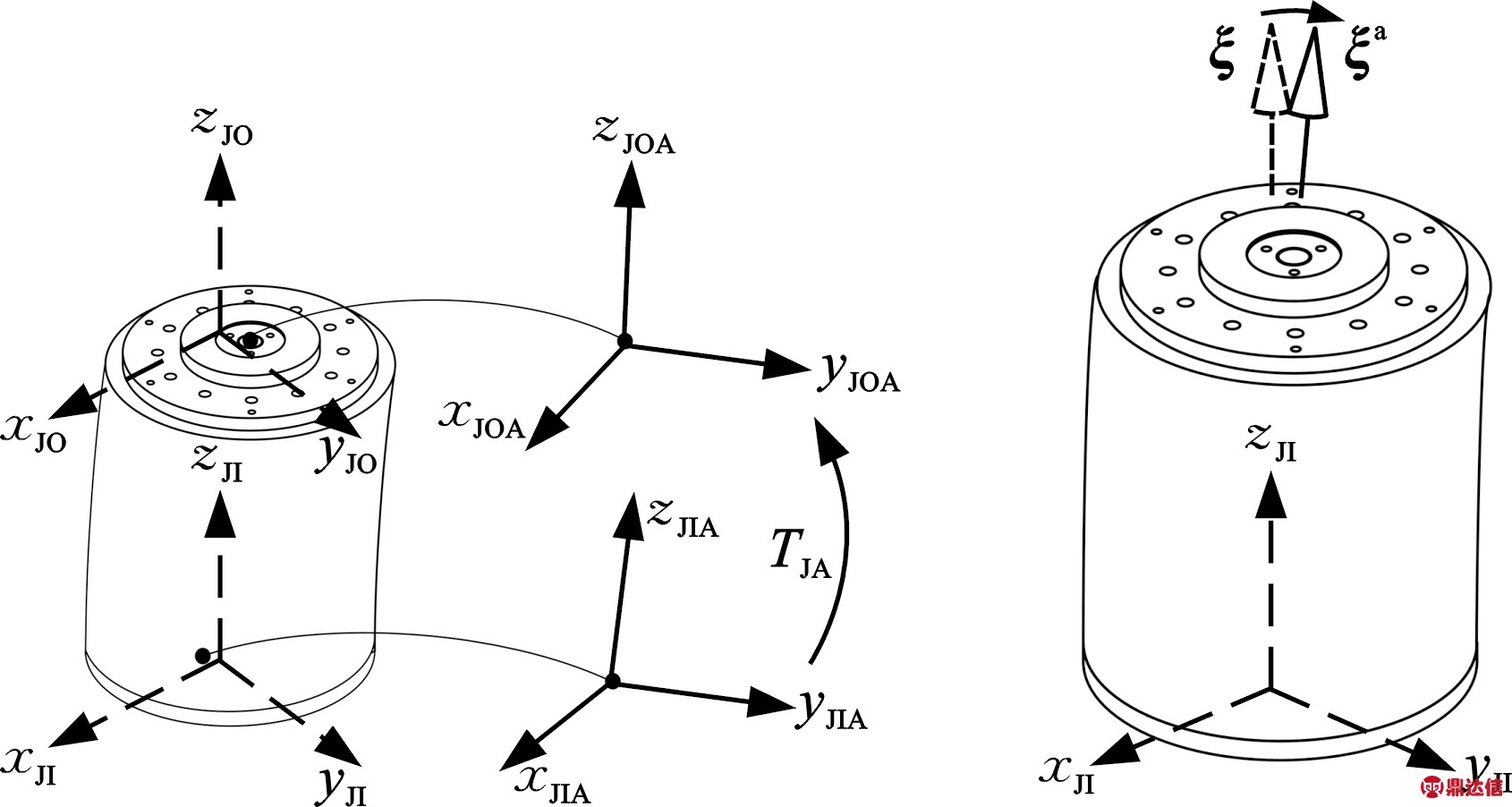
(a) 关节位姿误差 (b) 关节旋量误差
图2 关节位姿误差与旋量误差
Fig.2 Joint pose error and twist error
(3)关节零位误差。关节零位误差由电子零位触发位置不准确导致,使电子零位坐标系相对输出坐标系绕z轴偏转误差角Δθ′,如图3所示。实际关节零位位姿用TDA表示,并且TDA=Rot(z,Δθ′)。

图3 关节零位误差
Fig.3 Joint zero position error
(4)关节角误差。关节角误差主要由关节传动链存在的误差引起[12],实际关节角可表示为
θa=kaη
(2)
式中,ka为实际关节角(rad)与关节内部编码器的脉冲数之比(简称计数比),与关节减速器的减速比、编码器线数有关;η为关节内部编码器的脉冲数。
实际应用中,应对计数比ka进行标定。
因而,关节的实际运动学模型可表示为

(3)
1.2 连杆模块误差分析
连杆坐标系定义与关节坐标系定义类似,如图4所示。连杆位姿用齐次变换矩阵TL表示。
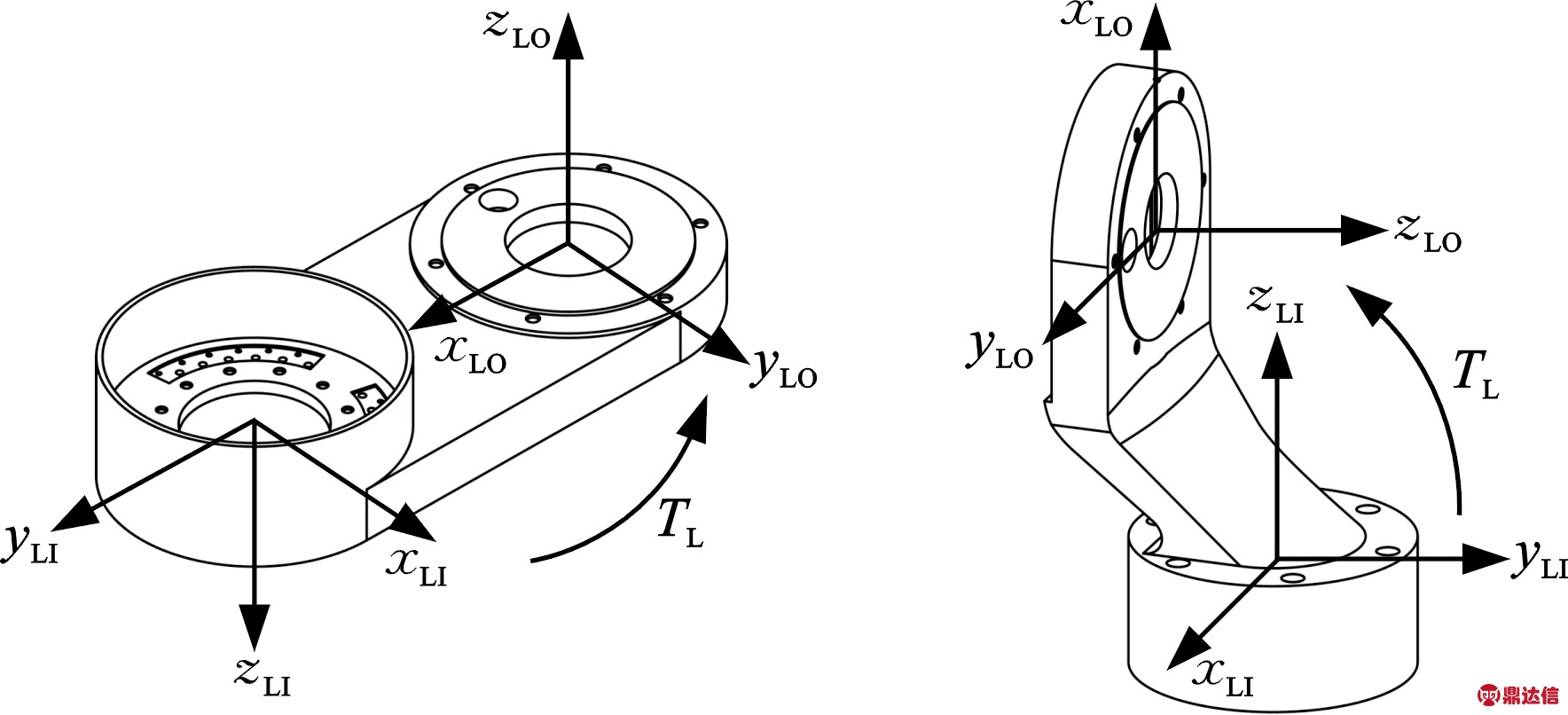
(a) 平行连杆 (b) L型连杆
图4 连杆坐标系定义
Fig.4 Definition of link frame
制造公差的存在,导致连杆模块输入坐标系(下标LI)、输出坐标系(下标LO)从其理论位置偏离至实际位置(下标LIA,LOA),如图 5所示。连杆实际位姿用齐次变换矩阵TLA表示。
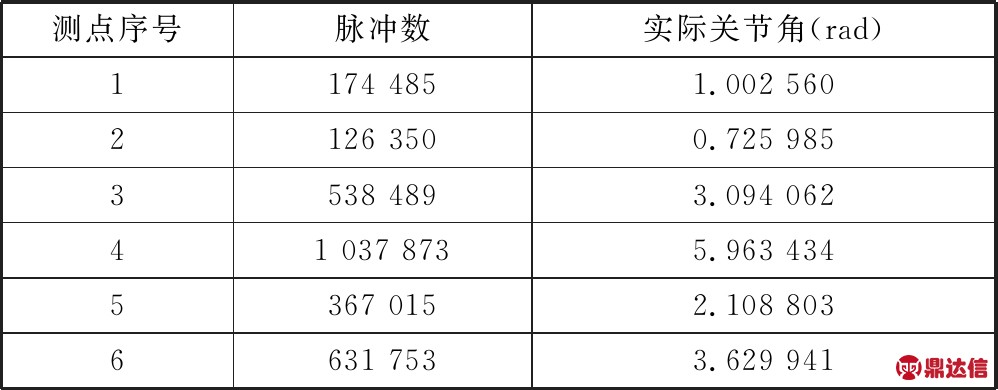
图5 实际连杆位姿
Fig.5 Actual link pose
1.3 模块间误差分析
以由一个关节模块和一个连杆模块组成的子装配体为例,装配后,理论上连杆输入坐标系与关节输出坐标系重合,如图6所示。在两模块不存在误差的情况下,子装配体的理论运动学模型fn为

图6 模块间理论装配位姿
Fig.6 Nominal assembly pose between modules

(4)
实际应用中,模块连接处主要存在以下三种误差。
(1)周向定位误差Δθ″。由相邻模块安装时接口处无周向定位导致,使连杆输入坐标系(下标LI)相对关节电子零位坐标系(下标JD)绕z轴偏转角度Δθ″,如图7a所示。
(2)关节零位误差Δθ′。如图7a所示,关节零位误差导致关节电子零位坐标系相对关节输出坐标系(下标JO)绕z轴偏转角Δθ′,使关节输出坐标系与连杆输入坐标系不重合,所以关节零位误差应归结为模块间误差。并且关节零位误差只存在于关节输出端与连杆输入端连接处。
(3)配合设计导致的装配误差。为了方便装配,模块化机器人模块接口处通常设计为小间隙配合。间隙导致连杆输入坐标系偏离关节电子零位坐标系,两坐标系间存在位置误差(dx,dy,dz)和姿态误差(dθx,dθy,dθz)[9],如图7b所示。
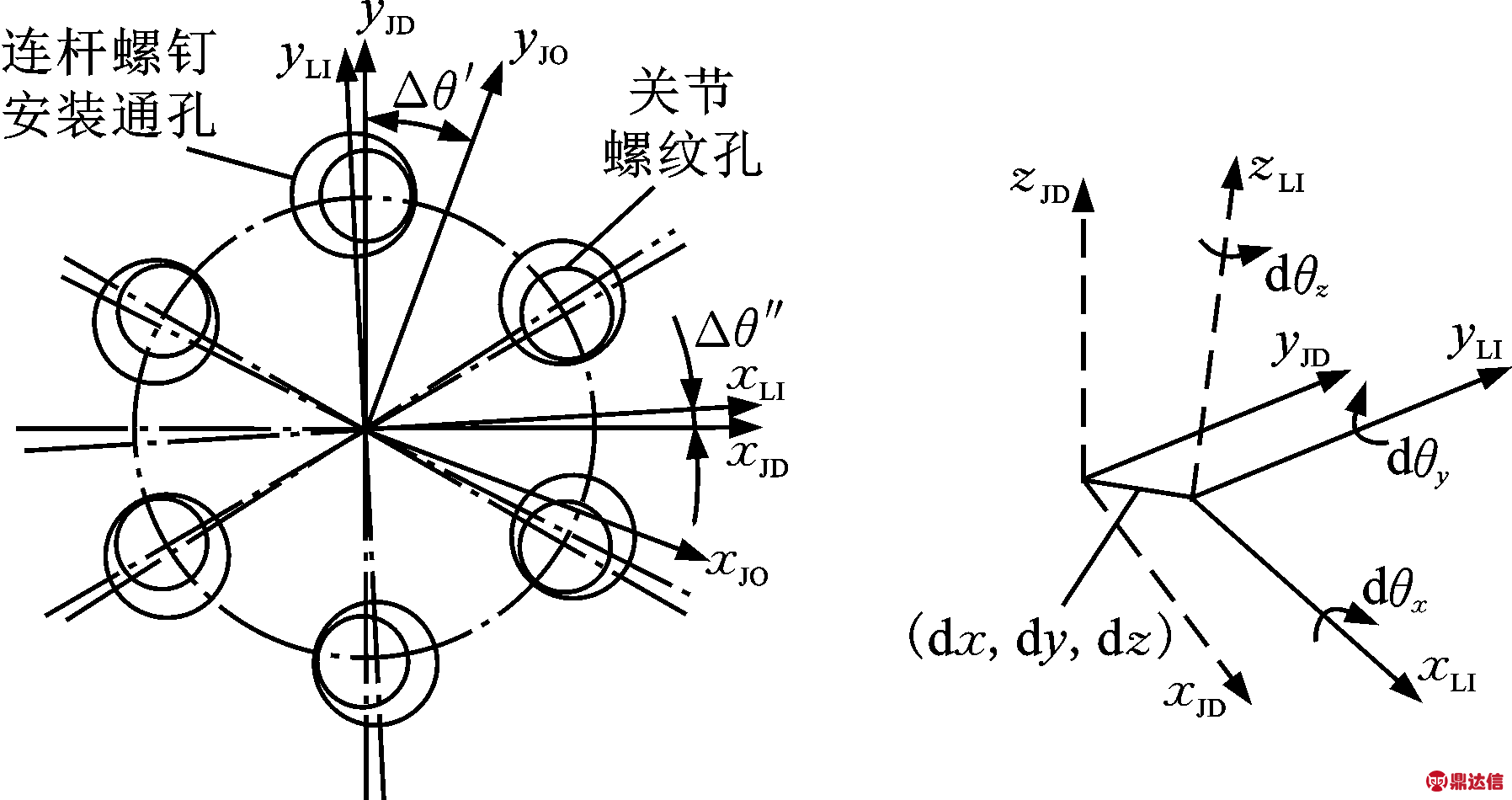
(a) 周向定位误差与关节零位误差 (b) 配合设计导致的装配误差
图7 模块间误差
Fig.7 Errors between modules
模块间误差由上述误差叠加而成,导致实际关节输出坐标系(下标JOA)与实际连杆输入坐标系(下标LIA)不重合。两坐标系间位姿即两模块间实际装配位姿可用一个齐次变换矩阵ΔT表示,如图8所示。子装配体的实际运动学模型fa为
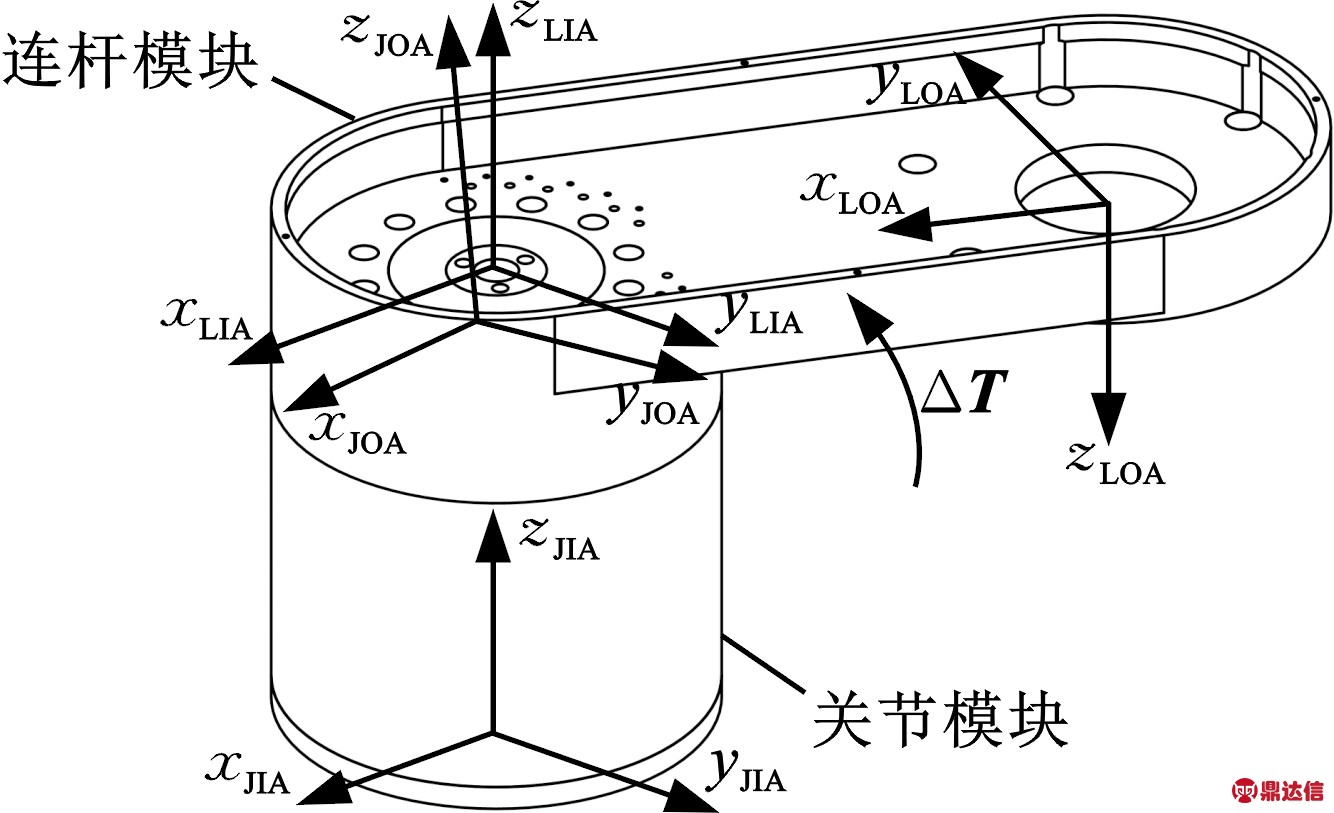
图8 模块间实际装配位姿
Fig.8 Actual assembly pose between modules

(5)
由式(5)可知,关节模块需辨识实际关节位姿TJA、实际关节运动旋量和关节角θa。关节零位误差归结为模块间误差,不必单独识别;连杆模块需辨识实际连杆位姿TLA。两模块装配在一起后仅需辨识相邻模块间装配位姿ΔT即可获取子装配体的实际运动学模型。
2 几何参数辨识方法
2.1 关节模块参数辨识
(1)关节实际位姿TJA辨识。关节实际位姿由其输入、输出坐标系间关系确定。如图9所示,在关节模块输入端、输出端各固定3个精密球。以关节模块输入端坐标系(下标JIA)定义为例,设关节模块输入端3个精密球的球心在测量坐标系中的坐标分别为P1、P2和P3,其形式均为3×1的列向量。以点P1为关节模块输入坐标系原点,向量P1P3为x轴,三点所在平面的法向量n为z轴。n=P1P3×P1P2,y轴方向通过右手定则确定。则关节输入坐标系相对于测量坐标系的位姿可用一个齐次变换矩阵TJI来表示:
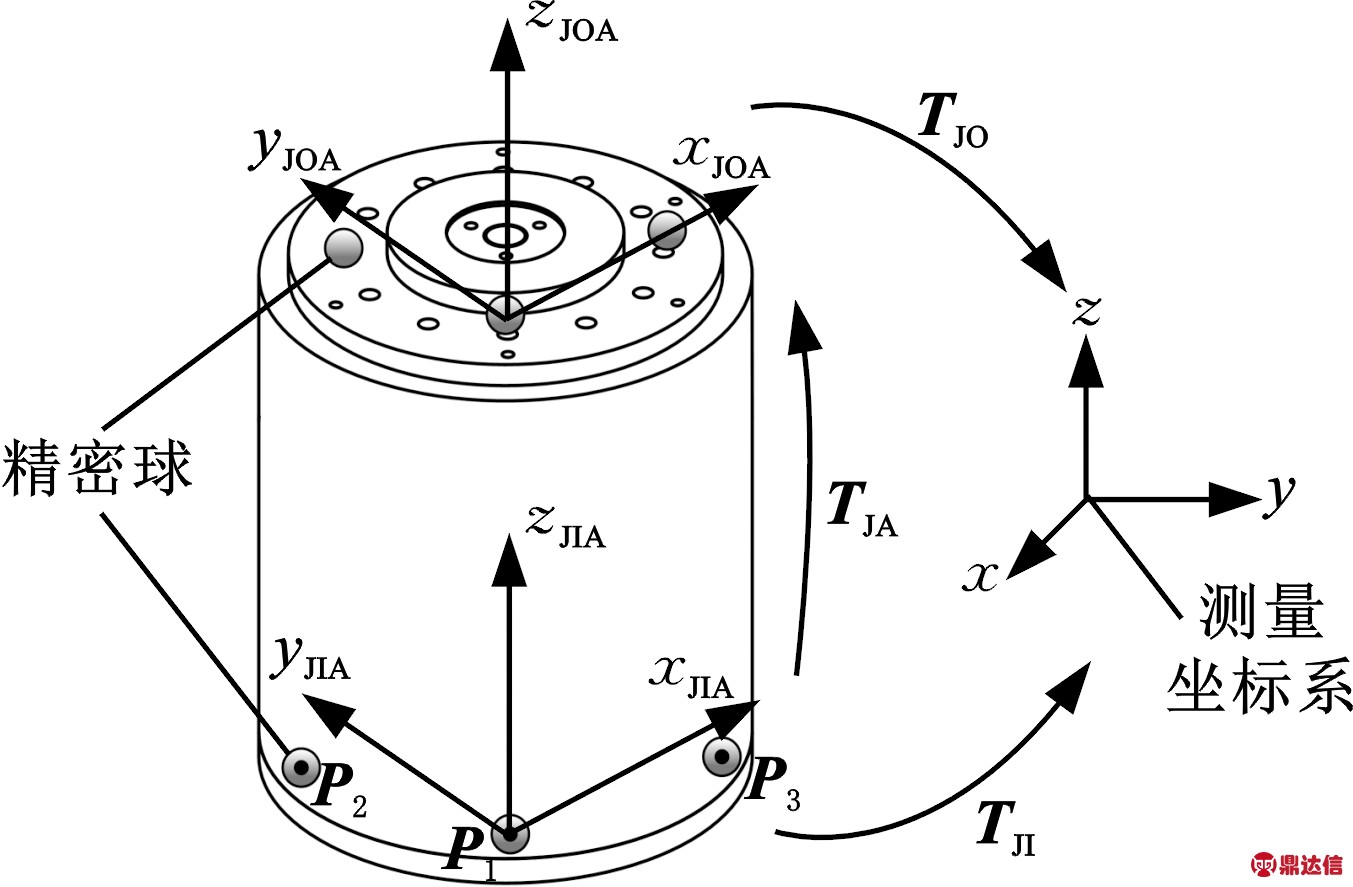
图9 关节位姿辨识
Fig.9 Joint pose identification
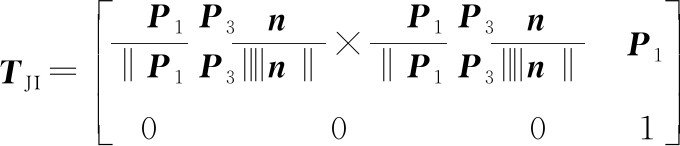
(6)
关节输出坐标系(下标JOA)定义与关节输入坐标系定义类似。关节输出坐标系相对于测量坐标系的位姿可用一个齐次变换矩阵TJO表示。则关节实际位姿可以表示为

(7)
(2)关节实际旋量辨识。对模块化机器人单个关节模块进行辨识时,由于关节运动轨迹完整且受柔性影响较小[13-14],故能准确体现关节运动学参数。采用关节运动轨迹法对关节旋量进行辨识。辨识需获取一系列关节轨迹测量点。转动关节运动轨迹为空间圆,如图10所示,实际关节运动旋量坐标ξa= (ω,-ω×r)T,其中ω为空间圆轴线单位方向向量,r为空间圆圆心。测量点拟合函数[15-16] 为
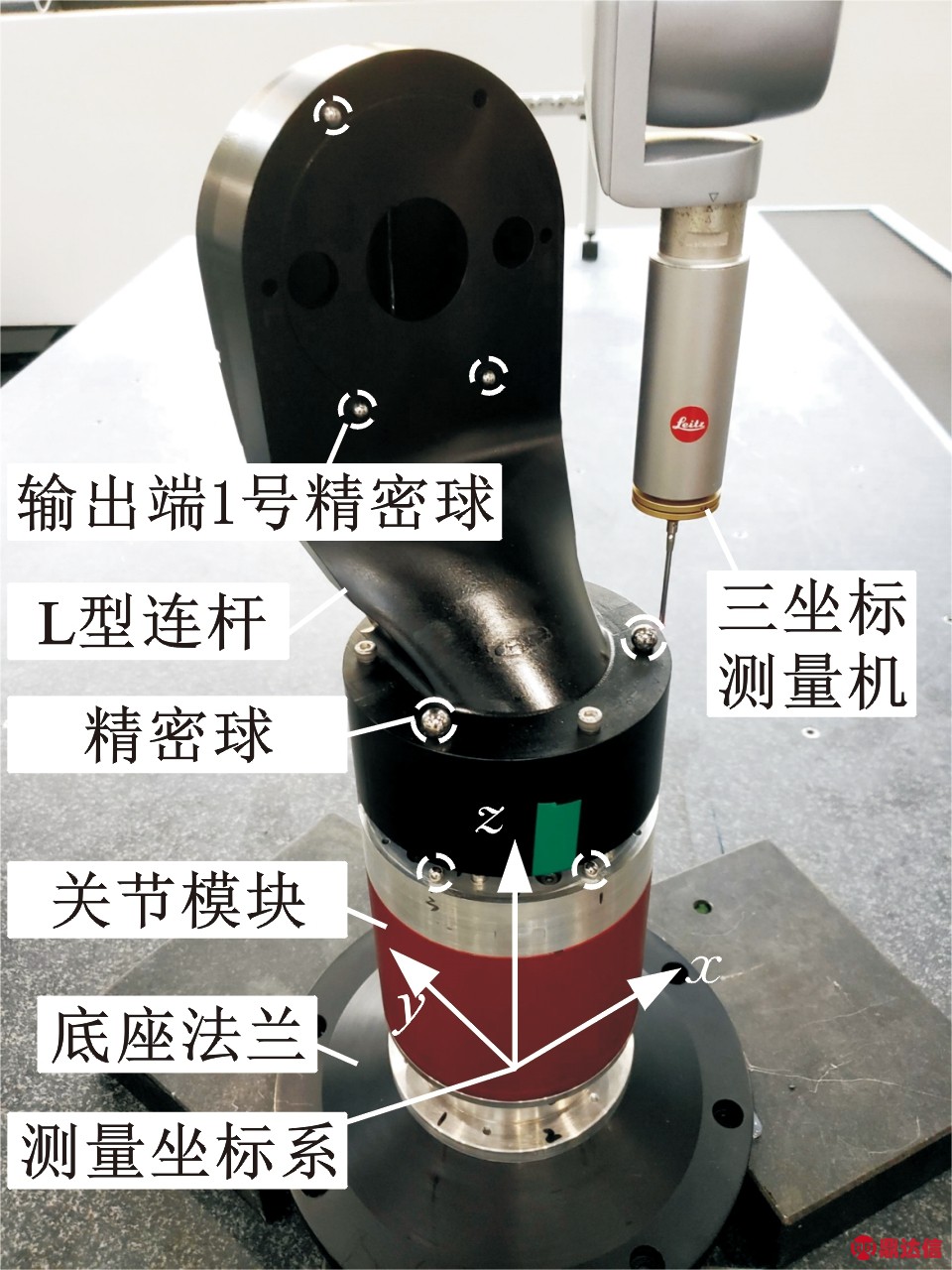
图10 关节旋量辨识
Fig.10 Joint twist identification

(8)
其中,R为拟合圆半径。
(3)实际关节角θa辨识。辨识实际关节角只需辨识计数比ka。将上述步骤(2)中的各测点Pi投影到拟合圆所在平面上,记为Oi。连接拟合圆圆心r与各投影点Oi,交拟合圆于点Qi。则ka可由下式计算得到:

(9)
式中,ηi为关节在第i个测点时的编码器的脉冲数;η1为关节在第1个测点时的编码器的脉冲数;rQi为拟合圆圆心r指向点Qi的向量;n为测点个数。
θa可通过式(2)计算得到。则关节模块的实际运动学模型表示为

(10)
2.2 连杆模块参数辨识
与关节位姿辨识类似,在连杆输入端、输出端分别固定3个精密球,如图11所示。连杆输入坐标系与连杆输出坐标系相对于测量坐标系的位姿可以分别用齐次变换矩阵TLI和TLO表示。则连杆实际位姿可表示为
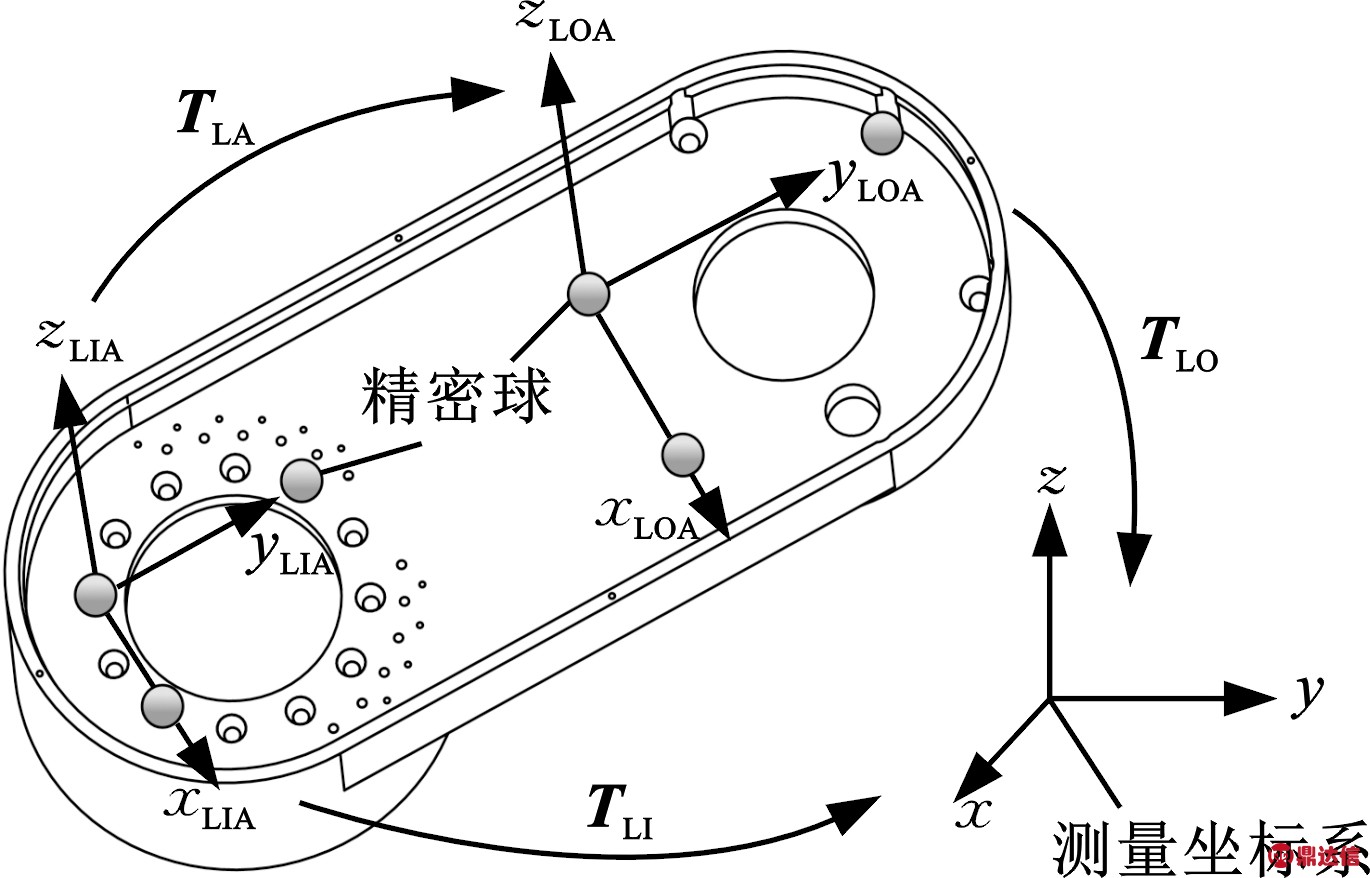
图11 连杆位姿辨识
Fig.11 link pose identification

(11)
2.3 模块间装配参数辨识
模块实际装配参数也可通过相邻模块连接处输入、输出端精密球确定。与2.1节中关节模块输入坐标系定义方式类似,定义装配后关节输出坐标系、连杆输入坐标系,如图12所示。记关节输出坐标系与连杆输入坐标系相对于测量坐标系的位姿变换矩阵分别为TJOB与TLIB,则关节输出端与连杆输入端装配关系可表示为
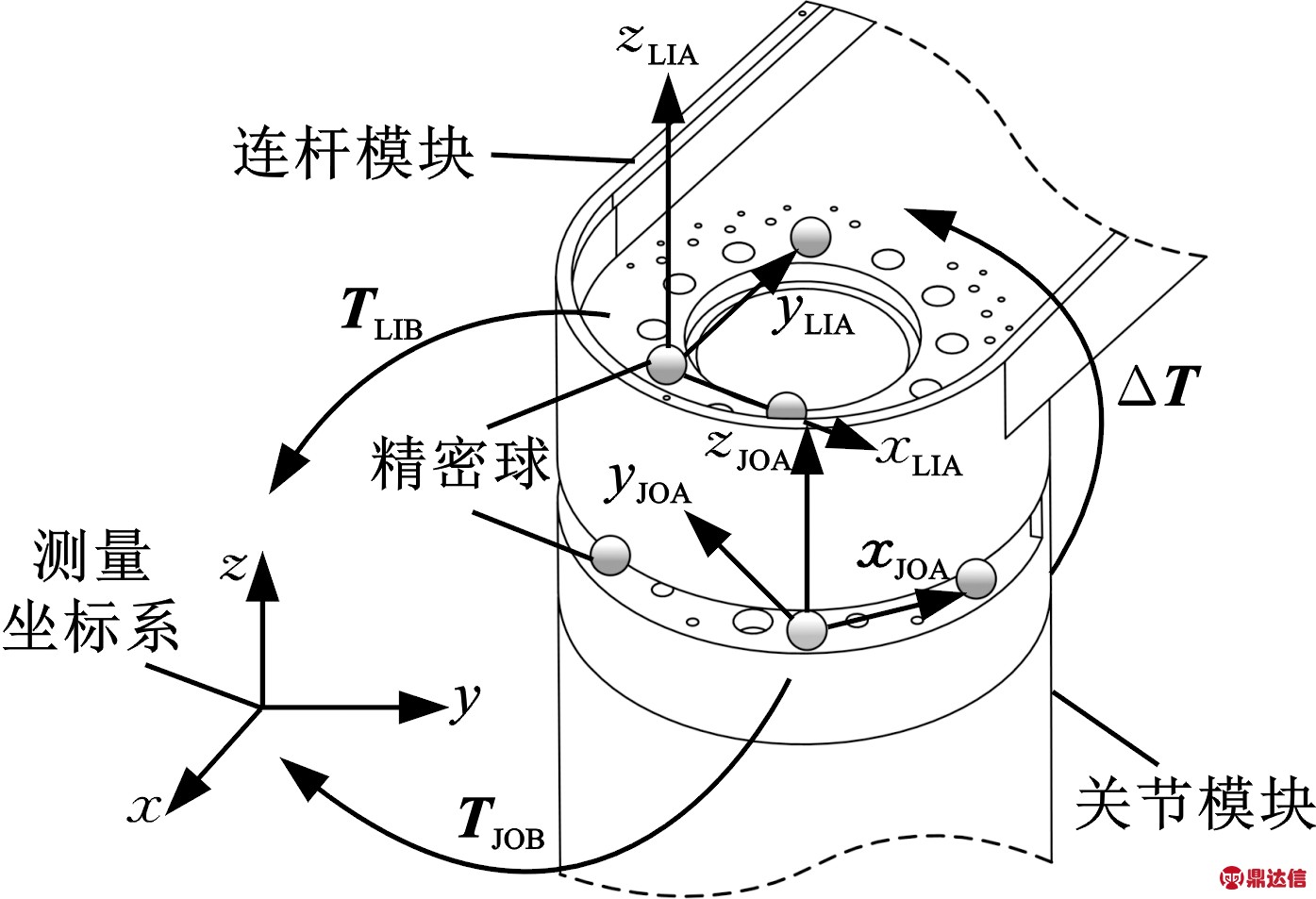
图12 模块间装配参数辨识
Fig.12 Identifying assembly parameters between modules
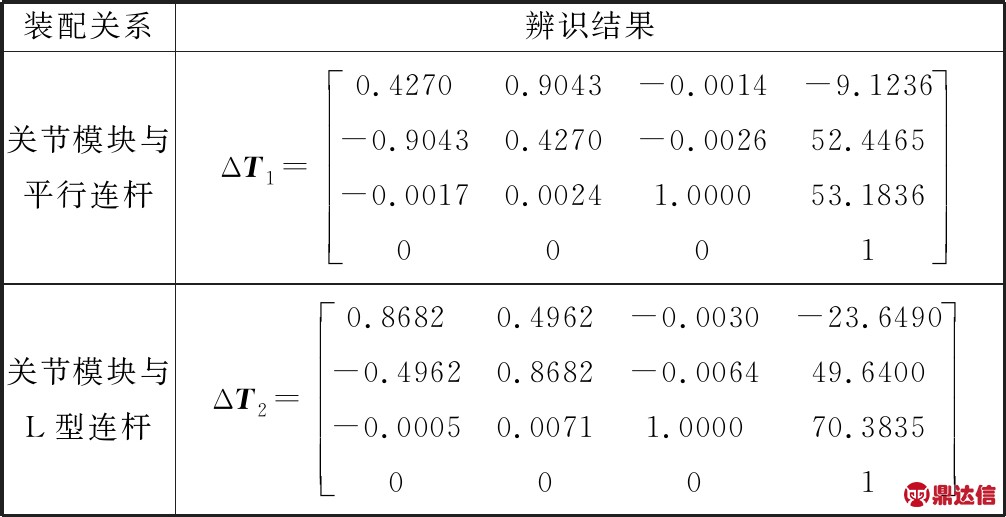
(12)
将式(10)~式(12)代入式(5)可得辨识后子装配体的运动学模型f为

(13)
模块化机器人运动学模型的获得与子装配体运动学模型的获得类似,首先对模块化机器人各模块参数进行辨识,在重构后只需测量相邻模块间装配位姿即可获得模块化机器人实际运动学模型。该方法相较于将模块化机器人重构后作为普通串联机器人进行标定的方法,无需根据机器人重构后的构型设计复杂的标定试验,只需测量相邻模块间的精密球即可获得实际运动学模型;相较于针对模块化机器人组成模块进行参数标定的方法,在更换某个模块时只需标定所更换模块与其相邻模块间的装配参数,无需对所有模块重新进行标定,就能够实现位姿误差的补偿。
3 试验及结果分析
以笔者所在课题组研制的一套模块化机器人为试验平台,用其中一个转动关节、一个平行连杆和一个L型连杆分别组成两种典型构型的子装配体进行试验验证。测量设备采用海克斯康GLOBAL S07.10.07桥式测量机,测量精度为±(1.7+4.0L/1000) μm。精密球型号为椿中岛SUS440C,精度等级为G28(JIS B1501标准)。
3.1 测量坐标系建立
将关节模块与平行连杆模块装配组成平行连杆子装配体,固定在三坐标测量机工作平台上。如图13所示,以关节轴线与底座法兰上平面的交点为原点,底座法兰上平面法向量为z轴,关节轴线与平行连杆输出端接口轴线与底座法兰上平面交点的连线为y轴建立测量坐标系。
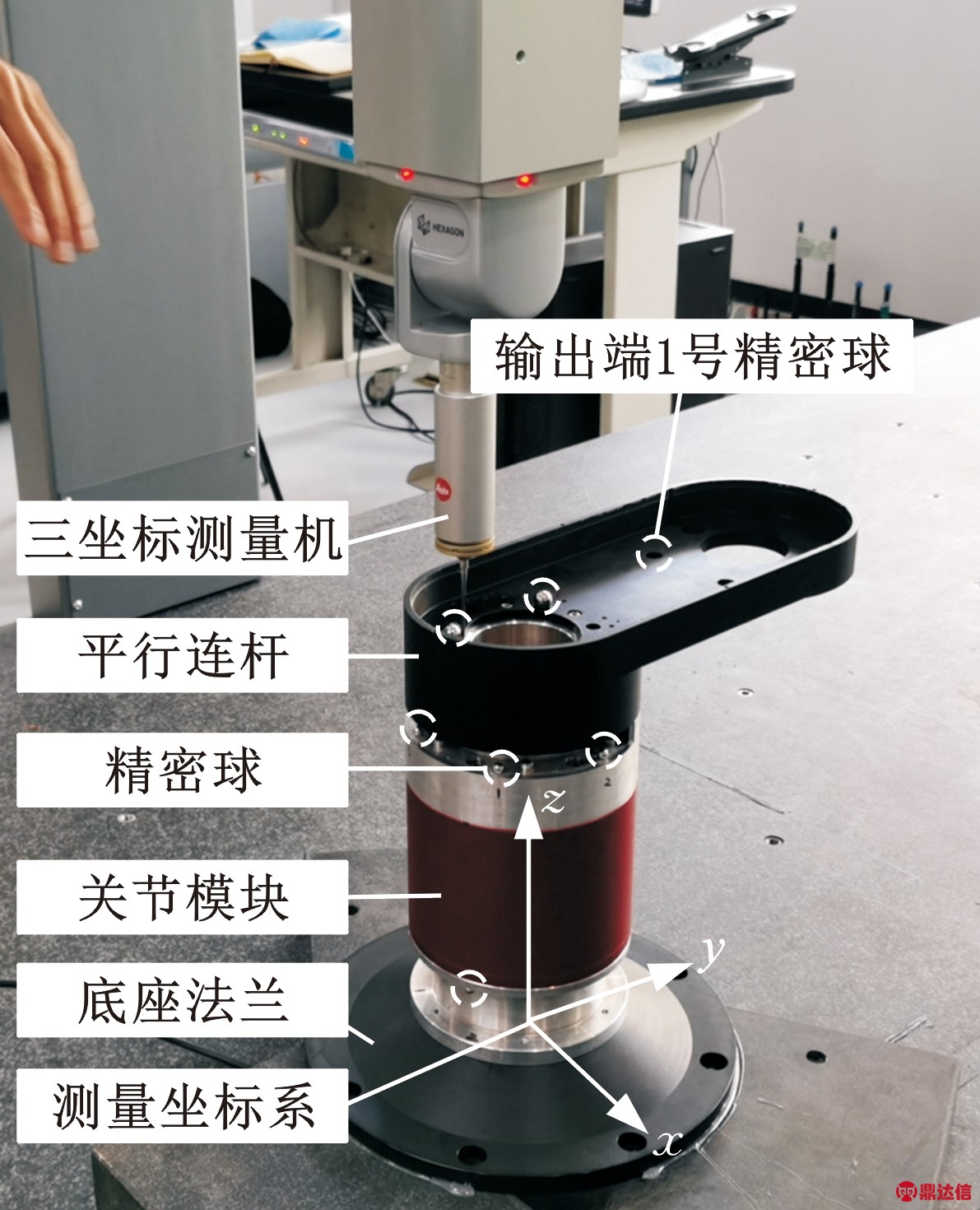
图13 平行连杆子装配体
Fig.13 Subassembly with parallel link
3.2 模块参数辨识
(1)模块位姿辨识。利用三坐标测量机测量各模块上精密球球心,按2.1节、2.2节分别对关节模块、平行连杆模块和L型连杆模块进行位姿辨识,辨识结果如表1所示。
表1 模块位姿辨识结果
Tab.1 Identified results of module pose
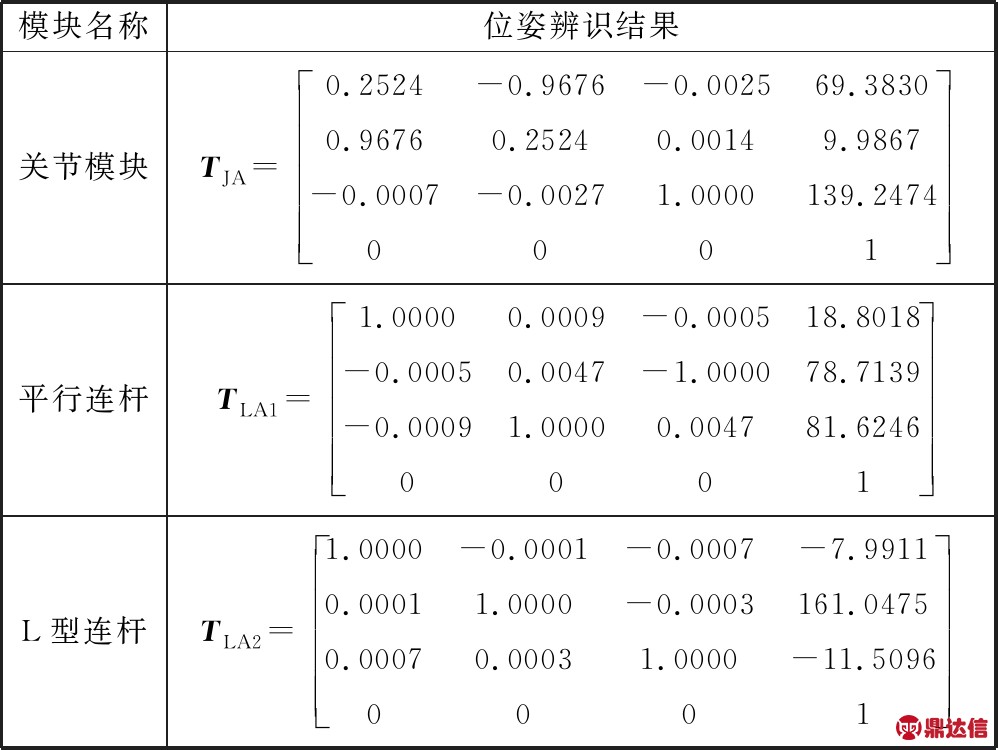
(2)辨识关节旋量与计数比。驱动关节带动平行连杆转动一周,每隔30°测量平行连杆输出端1号精密球球心,并将数据转换到关节输入坐标系中。记录每个位置关节编码器的脉冲数。通过式(8)计算实际关节运动旋量坐标ξa。按式(9)计算实际计数比ka。辨识结果如表2所示。
表2 关节旋量与计数比辨识结果
Tab.2 Identified results of joint twist and count rate

3.3 模块间装配参数辨识
分别测量平行连杆子装配体关节输出端、平行连杆输入端精密球球心。按2.3节对模块间装配参数进行辨识。将关节与平行连杆拆开,与L型连杆装配在一起组成L型连杆子装配体,如图14所示。关节与L型连杆间装配参数辨识同上。辨识结果如表3所示。
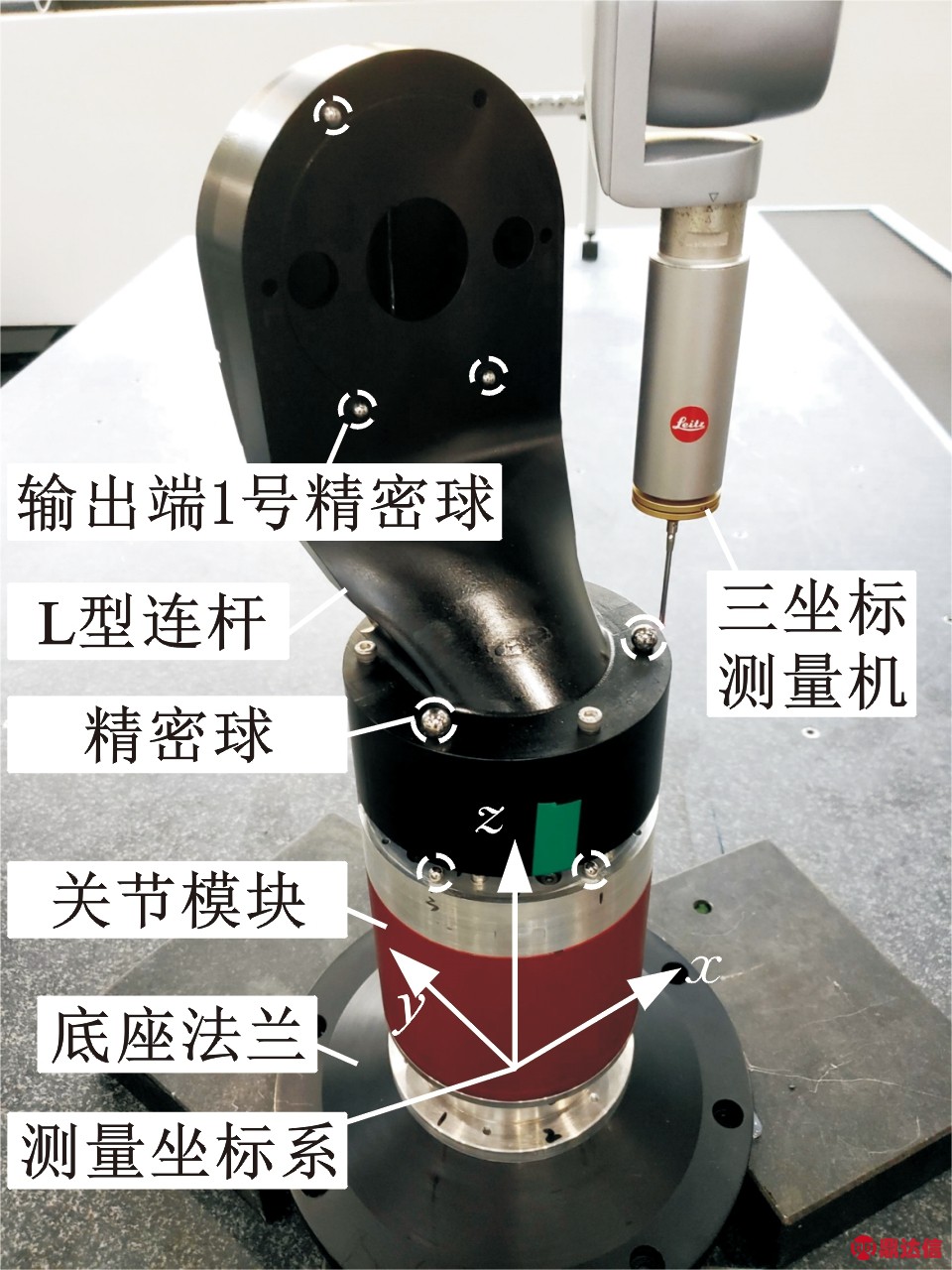
图14 L型连杆子装配体
Fig.14 Subassembly with L link
表3 模块间装配参数辨识结果
Tab.3 Identified results of assembly parameters between modules
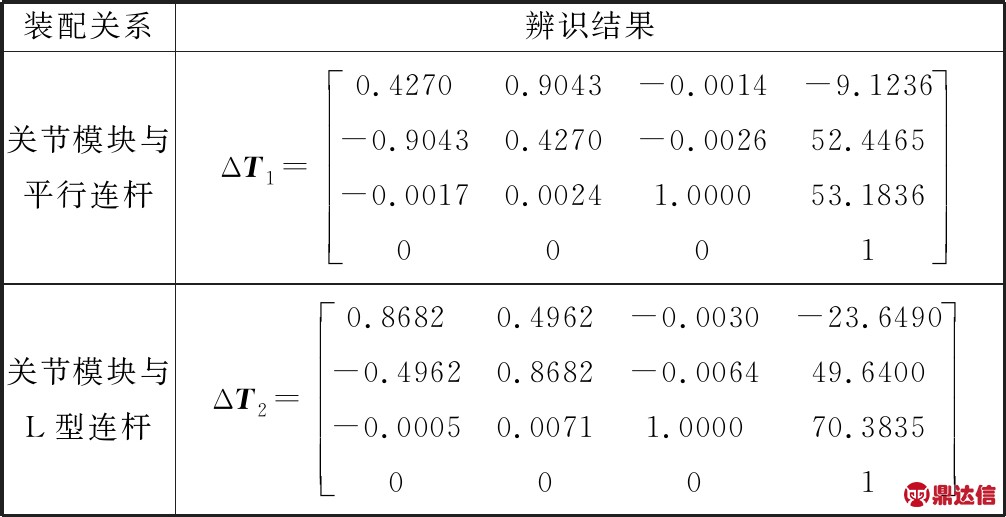
3.4 验证试验
驱动关节带动平行连杆随机运动到6个不同位置,记录关节在每个位置时的脉冲数,乘以ka得到关节实际角度值。脉冲数和实际关节角如表4所示。以每次运动后平行连杆输出端1号精密球的球心作为测试点。将测得坐标值从测量坐标系转换到关节输入坐标系中,记为实际坐标值。各测试点的理论坐标值与补偿后坐标值分别可以通过式(4)与式(13)计算得到。将6个测试点的理论坐标值和补偿后坐标值分别与实际坐标值相减,可得误差补偿前后的位置误差值。图15所示为补偿前后6个测试点的位置误差值的模(简称位置误差模)。6个测试点的理论坐标值、实际坐标值、补偿后坐标值如表5所示。
表4 平行连杆子装配体测试点脉冲数及实际关节角
Tab.4 Pulses and actual joint angles of the test points of subassemblies with parallel link
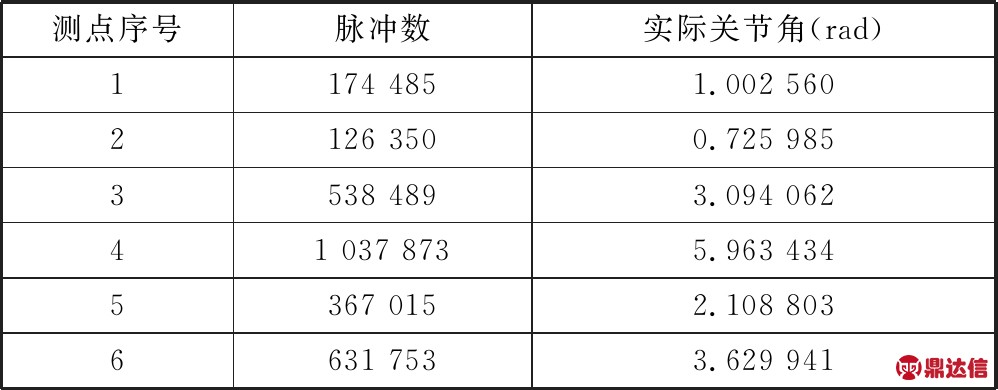
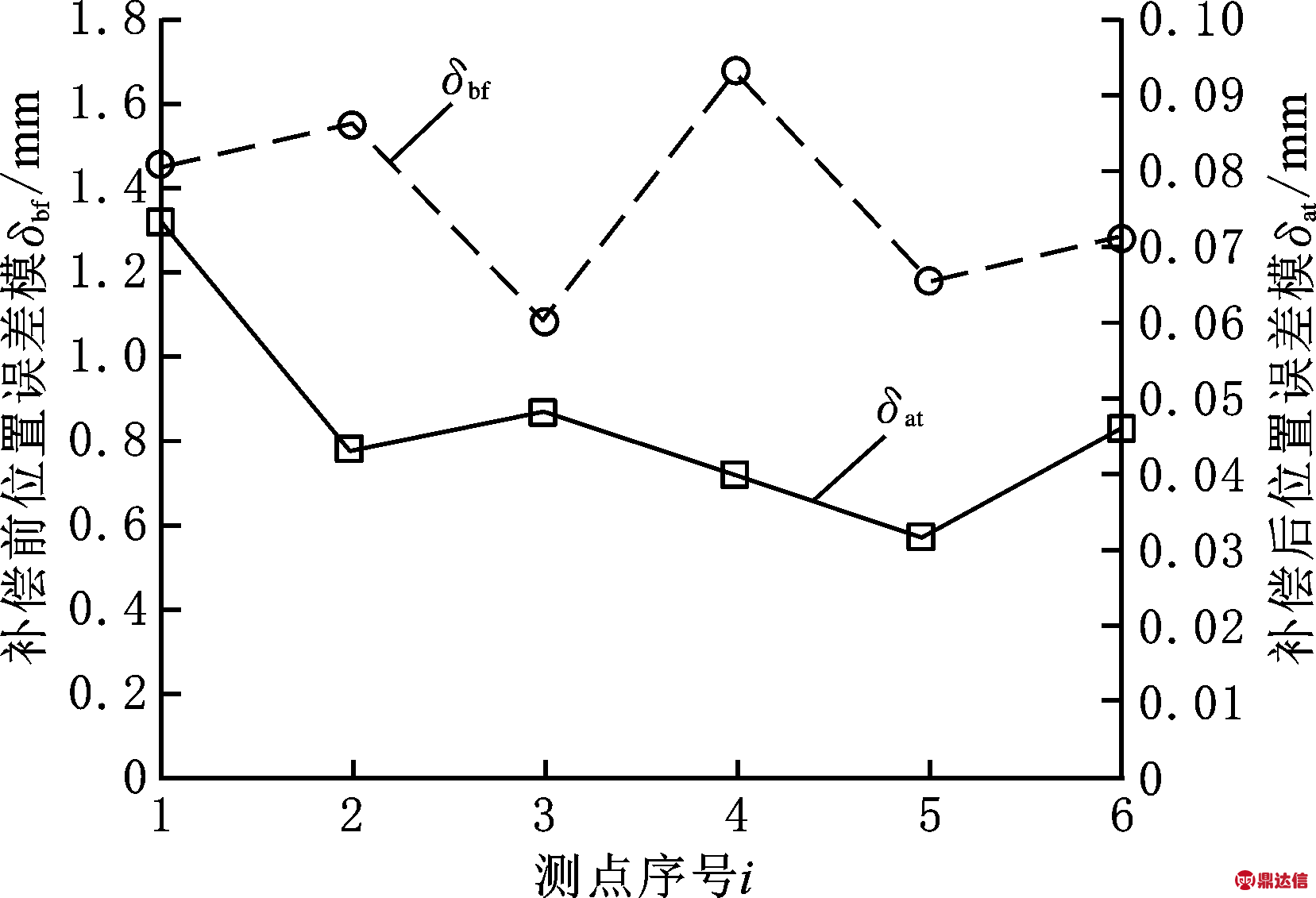
图15 平行连杆子装配体位置误差模
Fig.15 Norm of position error of parallel link subassembly
表5 平行连杆子装配体测试点理论坐标值、补偿后坐标值、实际坐标值
Tab.5 Nominal coordinate values,compensated coordinated values and actual coordinate values of the test points of subassemblies with parallel link mm

与平行连杆子装配体误差补偿方法类似,对L型连杆子装配体进行补偿试验。6个测试点的脉冲数和实际关节角如表6所示。图16所示为补偿前后6个测试点的位置误差模。6个测试点的理论坐标值、实际坐标值、补偿后坐标值如表7所示。
表6 L型连杆子装配体测试点脉冲数及实际关节角
Tab.6 Pulses and actual joint angles of the test points of subassemblies with L link
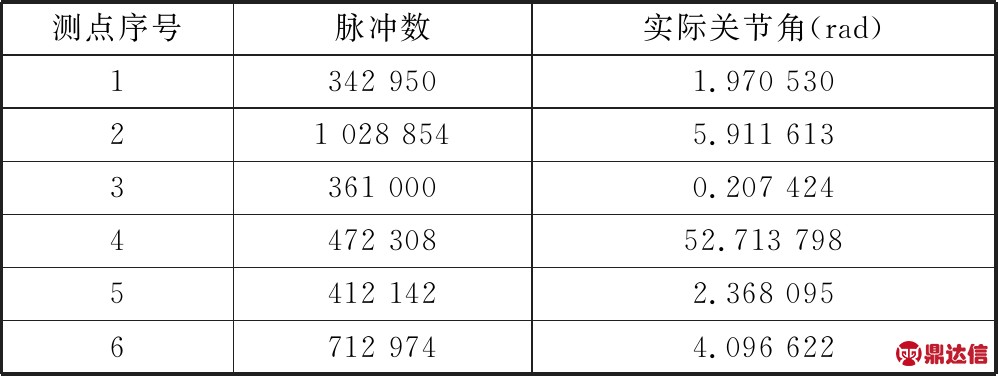
表7 L型连杆子装配体测试点理论坐标值、补偿后坐标值、实际坐标值
Tab.7 Nominal coordinate values,compensated coordinated values and actual coordinate values of the test points of subassemblies with L link mm
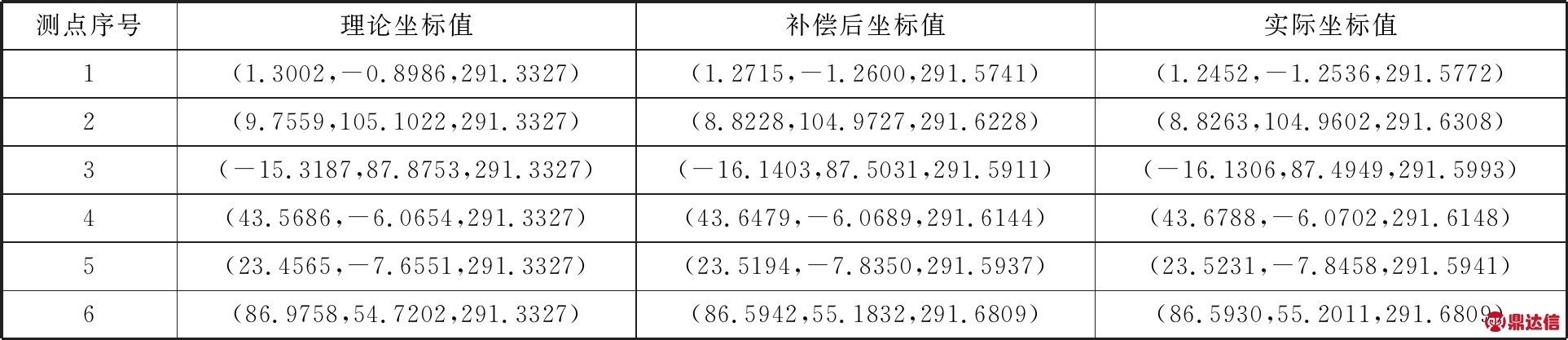
3.5 结果分析
通过图15与图16可以看出,两子装配体各测试点的定位精度经补偿后得到明显提高。补偿前平行连杆子装配体与L型连杆子装配体的测试点位置误差模的平均值分别为1.3717 mm、0.6130 mm,补偿后平均值分别为0.0497 mm、0.0186 mm。补偿前误差分别为补偿后误差的27.6倍和33.0倍,并且补偿后两子装配体的位置误差稳定在较低水平,无明显波峰波谷,可以表明该补偿方法是稳定有效的。
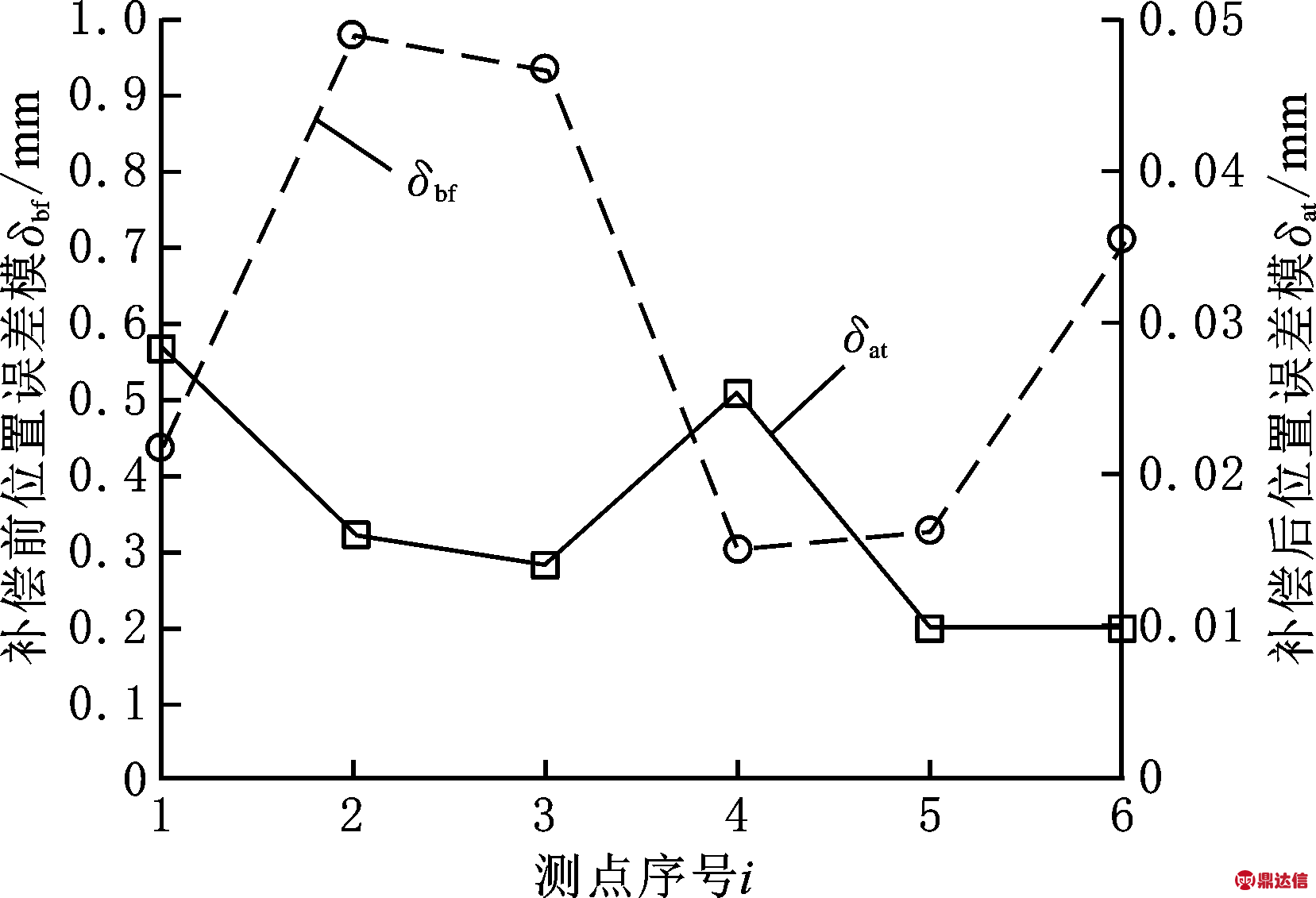
图16 L型连杆子装配体位置误差模
Fig.16 Norm of position error of L link subassembly
实际应用中采用三坐标测量机测得模块参数,在各模块装配后或机器人重构后,为了适应机器人作业环境,可采用关节臂式测量机测得模块间装配位姿。
4 结论
(1)本文将模块化机器人各组成模块误差及模块间误差划分成模块误差和模块间误差,给出了一种基于精密球和外部测量的模块化可重构机器人模块参数、模块间装配位姿辨识方法;针对两种典型构型子装配体进行参数辨识和验证试验,试验结果表明平均定位误差约为原来的1/30。
(2)本文给出的补偿方法不依赖于模块和接口的精度设计。通过事先单独对模块化机器人各模块进行参数识别,在各模块组装成机器人后或者模块化机器人重构后,通过外部测量设备直接测量相邻模块间精密球球心即可完成模块间装配位姿的识别,从而获得重构后机器人的实际运动学模型。本研究为模块化机器人重构后精度的快速补偿提供了一种新思路。