摘 要 为减少纺织机器人所占空间并提高其控制性能,研制了一款用于落纱理管的新型纺织机器人腰部关节。采用有刷电动机为动力源,以STM32F103T8U6为主控芯片,以L9110S为驱动芯片,利用磁编码器AS5600与安装在输出轴末端的磁铁产生霍尔效应,实现腰部关节速度、位置的检测;通过对比单速度闭环控制和转速、电流双闭环系统,在控制算法上采用转速、电流双闭环比例积分(PI)控制系统进行调速;采用控制器局域网络(CAN)总线通信,以减少多关节布线的复杂程度。结果表明,所设计的机器人关节能有效减小体积,体现微型化设计,且使用范围更广泛,双闭环控制系统达到稳态的时间比单闭环控制缩短了30%。
关键词 纺织机器人; 机器人腰部关节; 有刷电动机; 双闭环控制; CAN总线
随着消费水平的提高,人们对服装的需求量越来越大,对劳动力需求也随之增大,纺织机器人的出现极大地提高了服装产业的效率。2006年智能机器人被列入先进制造技术行业,标志着中国机器人行业进入快速发展阶段。至2019年,工业机器人市场规模达到57.3亿美元[1-2],在2020年国家重点研发计划中,机器人再次被重点关注,但由于机器人控制系统起步晚,关键核心技术受制于人,对高精尖机器人控制研究具有深远意义[3-5]。
在纺纱环节中,通常由人工拔管、插管、落纱,造成劳动强度大,劳动成本高。为实现省时省力、提高生产效率,目前大都采用落纱理管机器人[6],其常常工作于高速轻载有冲击的场合。纺织机器人常用结构中包含大量机器人关节,特别是落纱理管机器人关节广泛采用电动机加齿轮传动系统组合设计,其中直流电动机具有良好的调速性能,可以得到较大的启动转矩,具有极高的性价比。针对电动机控制等领域开展了大量研究,如:顾万里等[7]针对电动机在运转过程中的摩擦力和负载扰动对电动机控制性能的影响,设计了基于扰动补偿的自适应滑膜控制器,有效改善了在瞬态和稳态时对有刷电动机的控制效果;李宗俐等[8]设计了直流电动机转速跟踪器,特别针对电动机在面临电压电流过载时,仍能满足快速跟踪期望转速;Chen等[9]针对水下机器人系统参数在某些条件下可能变化,提出了一种自适应神经网络控制方案,提高了系统稳定性;Zhao等[10-12]针对多机器人的学习跟踪控制,提出了一种较优跟踪控制方法,可以在短时间内训练多个机器人学习。
现阶段大部分研究没有将电动机与机械传动系统结合考虑,本文针对纺织落纱理管机器人中驱动整个躯干转动的腰部关节进行研究,以期设计机器人腰部关节运动控制可以满足特定工况下的强度要求,并具备良好的速度、位置控制精度。
1 总体方案设计
本文设计的纺织机器人腰部关节分为关节本体部分和运动控制部分[13-15],如图1所示。机器人腰部关节本体设计包括结构设计和驱动板设计。根据结构设计需求进行三维建模,然后基于该模型进行有限元仿真,设计满足要求后进行实体加工;电路板集成设计首先需选择合适的主控芯片以及实现功能的元器件,然后分析各元器件间的布线方式,设计电路图,绘制集成电路,最后将加工好的各个实体零件和电路板进行装配。
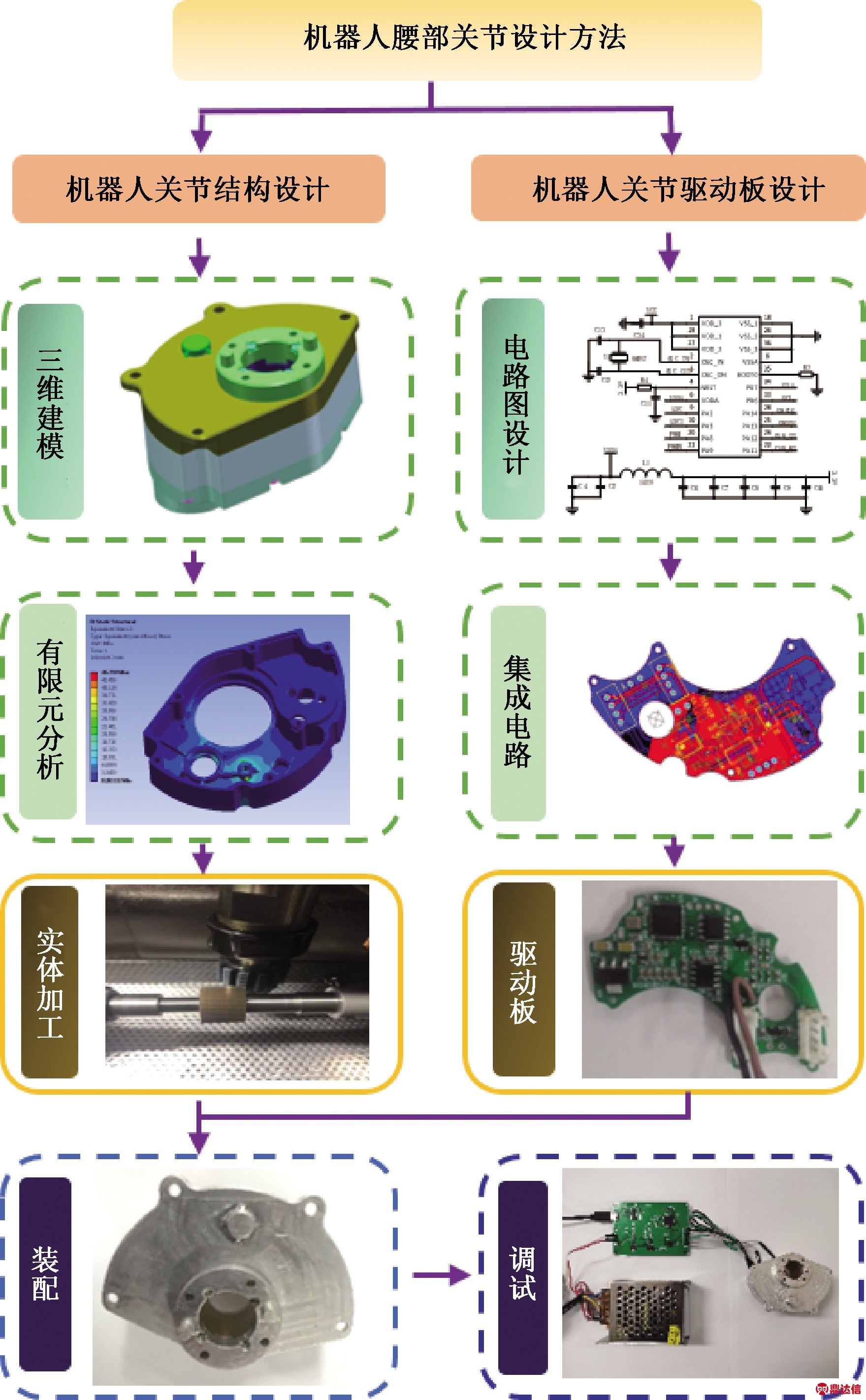
图1 机器人腰部关节设计流程图
Fig.1 Flow chart of design of waist joint of robot
运动控制主要由上位机、控制模块、驱动模块、电流采集模块、过温保护模块、通信模块、位置检测模块、电源模块等组成。其中:电源模块内含2级降压电路,分别为7.4 V降压到5 V和5 V降压到3.3 V,为各个模块供电;控制模块和驱动模块都采用STM32为控制芯片,控制模块为实现多路控制、便于扩展采用STM32F103RCT6,驱动模块为减小驱动板体积采用36引脚的STM32F103T8U6作为主控芯片。硬件系统框图如图2所示。
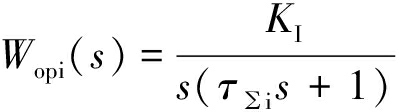
图2 硬件系统框图
Fig.2 Block diagram of hardware system
工作原理为:1)开机并由电源供电,系统初始化;2)上位机通过串口发送要达到的位置指令;3)控制板接收到信号并解析指令,再将信号通过控制器局域网络(CAN)[16]广播的方式传送到每一个关节驱动器;4)驱动器识别到呼叫自己的广播后接收控制板的指令,驱动器将接收到的数据与磁编码器检测到的当前位置数据进行对比,通过比例积分微分(PID)计算后产生脉冲宽度控制(PWM)信号控制电动机转动[17],磁编码器一直将变化的数据发送给单片机;5)驱动模块通过模数转换器(ADC)实时采集电动机的温度,当实际值超过预定值时,立即关断产生PWM信号引脚,停转电动机,从而起到保护电动机的目的。
2 系统硬件电路设计
2.1 有刷电动机驱动电路设计
有刷电动机具有调速简单,控制方便,价格低廉等优点,在伺服器中也大量使用。有刷直流电动机稳态下的电气方程为
U1=E1+IdR
(1)
式中:U1表示驱动电动机外部直流电源的电压,V;E1表示电动机在稳态下的感应电动势,V;Id表示电动机在稳态下的电枢电流,A;R表示电动机电枢电阻,Ω。有刷直流电动机电枢绕组的感应电动势为
E1=Cenφ
(2)
式中:Ce为电动势常数,由电动机结构决定;n为电动机转速,r/min;φ为励磁磁通,T·m2。由此可推导出有刷直流电动机的转速表达式:
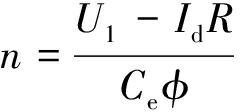
(3)
由式(3)可知,有刷直流电动机调速的方法有:改变驱动电动机外部直流电源的电压U1;改变电动机电枢电阻R;改变电动机励磁磁通φ。本文采用PWM方波控制电动机转速,即通过改变输入电动机的电压改变电动机转速,在利用桥式电路的基础上选用STM32F103T8U6芯片作为主控芯片,利用高级定时器改变驱动电动机平均电压来改变转速。桥式电路采用集成“H桥”芯片L9110S,该芯片将分立电路集成在单片集成电路(IC)中,可以减小电路设计复杂程度,提高系统稳定性。
2.2 降压模块设计
降压模块为7.4 V降压至5 V、再由5 V降压至3.3 V。其中7.4 V降压至5 V电路采用LM317降压芯片,5 V降压至3.3 V电路采用AMS1117降压芯片,以满足不同模块对电压的需求。LM317降压芯片为可调节降压芯片,两端的电压差最大可达到40 V,本文实验中的压差为2.4 V,完全符合要求。LM317降压芯片输入输出电压差值计算公式为
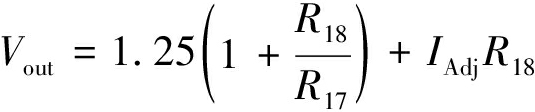
(4)
式中,Vout为降区芯片输出端电压,V;R17为降压芯片输出引脚电阻,Ω;R18为降压芯片调节引脚处电阻,Ω;IAdj为调节引脚输出电流,A。由于IAdjR18<<Vout,可忽略不计,则7.4 V降压到5 V的降压模块电阻R17、R18的阻值分别为100、300 Ω。AMS1117降压芯片选用的是可以直接降压到3.3 V固定值的芯片,该芯片不需要电阻进行调压,所允许的最大电压为15 V、最大电流为1 A,本文实验是从5 V降压到3.3 V,可以达到实验要求。
2.3 通信模块设计
通信模块主要用于上位机与控制板通信及控制板与驱动板通信。上位机与控制板通信采用串口通信,所用芯片为CH340C,实现USB-TTL电平转换,其特点为采用5 V电压源供电,内置晶振,外围电路连线简单。控制板与驱动板通信采用CAN通信,所用芯片为TJA1050和SN65HVD230D,主要区别为供电电压不同。TJA1050为5 V电压供电,放置于控制板;SN65HVD230D为5 V通用芯片和3.3 V通用芯片,放置于驱动板。采用CAN总线通信传递信号,采用串联方式在总线的起始和末端分别加装120 Ω的电阻,可以实现多关节串联控制,相较于PWM通信降低了连线的复杂程度。
2.4 位置检测模块设计
在机器人关节控制中,位置检测具有重要地位,常用的位置检测元件有:码盘式位置检测元件(如光电编码器)、霍尔式位置检测元件。其中,霍尔式位置检测元件具有结构简单、性能可靠、成本低廉等优点。本文采用AS5600磁编码器,其采用霍尔原理,利用的是磁性检测的方式获取位置信号。测量角度的范围为0°~360°;采用12位数字模拟转换器(DAC)输出分辨率,精度可达0.01°;其应用范围广、性价比高。对于磁场的采集有PWM模式和集成电路总线(IIC)通信方式,为提高采样精度和传输效率,选择IIC通信方式。
2.5 电流采集模块设计
在电流环实验中,设计电流采集电路,所用芯片为MAX44248。其中,OUTA和OUTB表示输出通道A和B,INA+和INA-分别表示通道A的正负输入,VSS表示接地,VDD表示5 V供电接口,INB+和INB-分别表示通道B的正负输入,电流采集电路如图3所示。在驱动芯片的接地端串联一个采样电阻,R8、R9、R10、R11和C24组成差分滤波电路,为了抑制零点漂移,在R12电阻上接了一个0.8 V的抬升电压。采样点处的电压U0经过采样电路后进行ADC采集,采样得到的电压表达式为
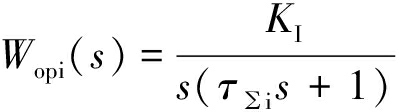
(5)
将读取到的电压进行运算,反向求出采样点的电流。差分放大器采用集成IC芯片MAX44248,并在ADC采集点加R13和C20组成输出一阶滤波,D1为输出电压钳位,可以起到输入输出保护的作用,同时可以利用软件实现过流保护。
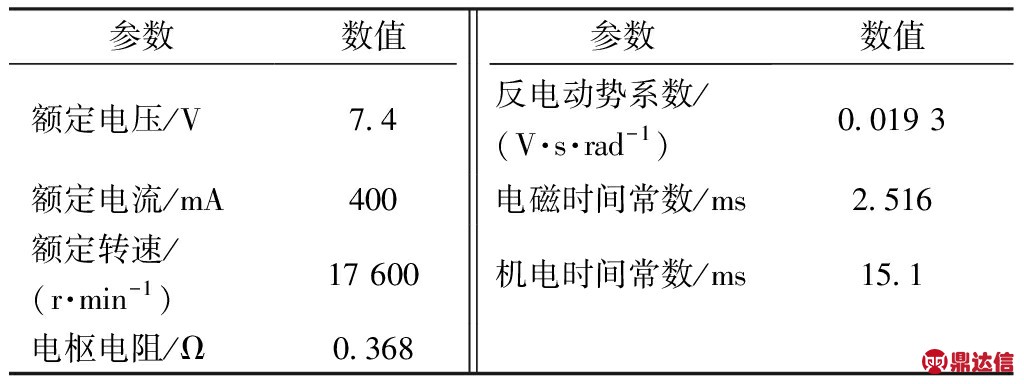
图3 电流采集模块电路图
Fig.3 Circuit diagram of current acquisition module
2.6 驱动控制模块设计
驱动电路控制模块采用的控制芯片为STM32F103T8U6芯片,该芯片具有性能高、接口丰富、功耗低、封装体积小、性价比高等优点。其中晶振频率为8 MHz的无源晶振采用高级定时器1产生PWM方波,两引脚为电动机正反转PWM和互补PWM控制输出端,同时可以通过改变占空比控制电动机的转速和刹车。CAN通信、IIC通信通过专用引脚接口与外设相连。为方便程序烧录调试,采用串行调试(SWD)模式。
3 系统软件设计
机器人关节电路部分主要由控制板和驱动板组成,控制板相当于中转站,将上位机与驱动板建立联系;驱动板主要用于驱动电动机转动,实时监测电动机运转情况,其控制流程如图4所示。
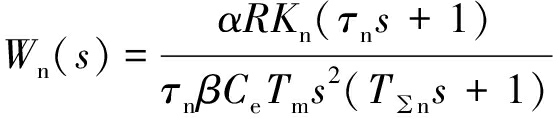
图4 控制程序流程图
Fig.4 Control program flow chart.
(a) Control board flow chart; (b) Drive board flow chart
上位机的信号通过串口发送给控制板,控制板再将信号通过CAN总线发送给驱动板,同时还可以进行信号的反向传递。主程序包括串口中断和CAN中断,其工作流程如图4(a)所示。驱动板主要负责驱动机器人关节的一切动作,并实时检测电动机温度电流,程序中主要包含CAN中断、外部中断、高级定时器中断等,其中温度保护和电流保护设为最高级中断。主要控制过程为:驱动板接收到控制板通过CAN通信发来的信号,立即产生CAN中断,将数据与磁编码器的位置信号进行比较,驱动电动机转动到该位置,其工作流程如图4(b)所示。
4 转速与电流双闭环控制设计
机器人关节在运动时经常需要电动机正反转,在单转速比例积分(PI)调节时虽然有限流电路的保护,但在到达位置时,电流立即下降将导致停靠位置不准确。为此,引入转速、电流环双闭环控制,并通过实验将单速度环与转速、电流双闭环控制系统进行对比分析。其中,ASR为转速调节器、ACR为电流调节器[18-19]。在实际双闭环调速系统中加入滤波环节,用于抑制各种扰动量对系统的影响,同时在调节器输入端加入同等时间常数的惯性环节以平衡延迟作用。
4.1 电流环设计
参照工程设计方法设计转速、电流双闭环控制,遵循先内环后外环的设计原则,即先设计电流环再设计速度环。在电流环中有2个相差较大惯性环节的控制对象,采用PI调节器的典型Ⅰ型系统,PI调节器的传递函数为
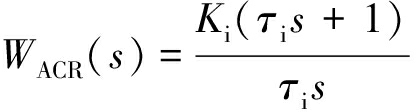
(6)
式中:Ki为ACR比例系数;τi为ACR积分时间常数;s为传递函数经过拉普拉斯变换后与时间相对应的空间变量。典型Ⅰ型系统的开环传递函数为
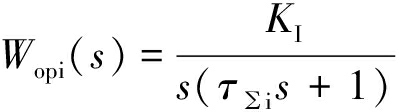
(7)
式中:τ∑i=Ts+Toi;Ts为PWM方波滞后时间常数;Toi为电流反馈时间常数。
通常希望电流超调量σi≤5%,可选阻尼比ξ=0.707,KITΣi=0.5,则KI为
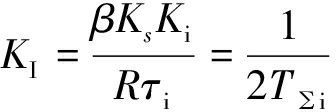
(8)
式中,β为电流反馈系数。令τi=Tl,可得比例系数表达式:
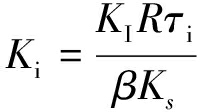
4.2 转速环设计
和电流环设计相同,为实现无静差,在电流环中已经有一个积分环节基础上必须再加入一个积分环节。显然,工程Ⅰ型系统已经达不到要求,所以转速环设计必须采用工程Ⅱ型系统,转速环的设计也采用PI闭环调节,其传递函数为
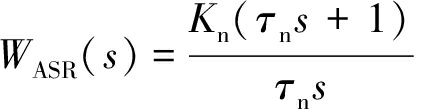
(9)
式中:Kn为ASR比例系数;τn为ASR积分时间常数。转速环的开环传递函数为
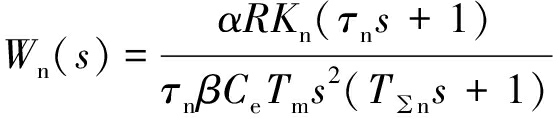
(10)
式中:T∑n=1/KI+Ton,Ton为转速反馈时间常数;α为转速反馈系数;β为电流反馈系数;Ce为反电动势系数;Tm为机电时间常数。
令转速开环增益KN为
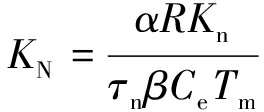
(11)
ASR的参数包括Kn和τn,典型Ⅱ型系统参数公式为:
τn=hT
(12)
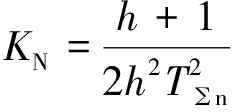
(13)
故可推出
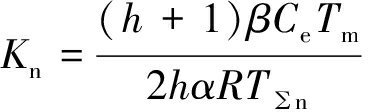
其中,h为中频宽,由动态性能要求决定。
5 实验分析
为验证实验的可行性,首先针对机器人关节结构部分进行设计,根据机器人腰部关节设计流程图,采用五级减速齿轮组,电动机采用1718型精密空心杯电动机作为动力源,具体参数如表1所示。针对使用位置,设计为扇形结构,优化内部齿轮排布方式,三维图如图5机器人驱动关节所示。输出端转动速度为0~40 r/min,转动角度为0°~360°。
表1 电动机参数
Tab.1 Motor parameter
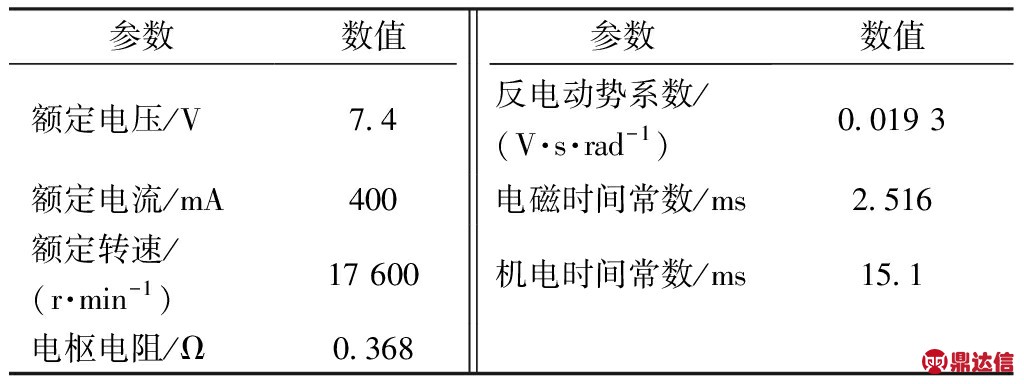
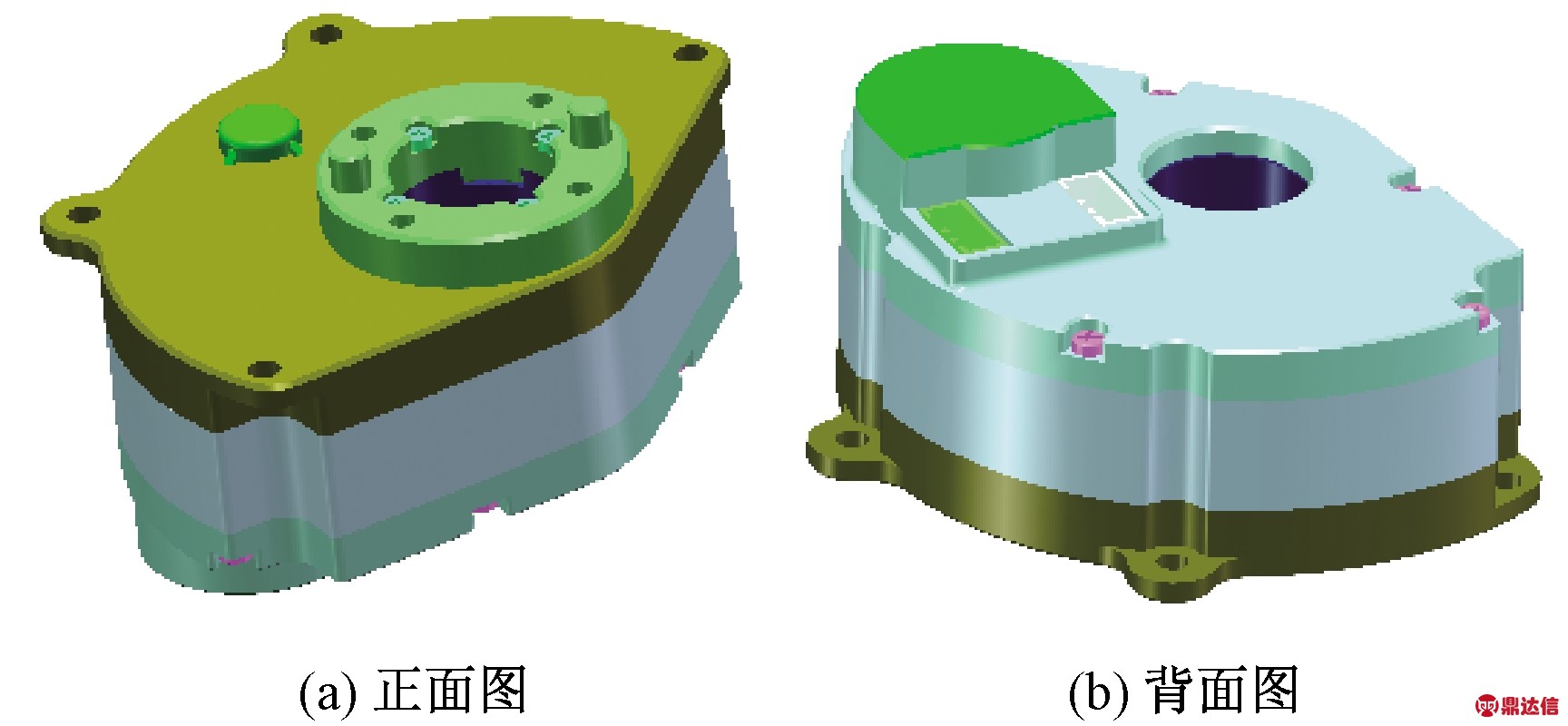
图5 机器人腰部驱动关节
Fig.5 Robot waist drive joint.
(a) Front view;(b) Rear view
通过运用有限元分析,机器人腰部关节各部分应力在材料允许范围之内,即机器人关节壳体、轴、齿轮满足日常的使用要求。最后进行实体加工,壳体采用铝合金材料进行铣削加工,齿轮采用铜合金材料进行滚齿加工。
控制电路方面,为实现所要求的功能,结合上述元件原理运用Altium Designer 15进行电路板设计;为减小占用面积采用双层板设计,驱动板集成电路如图6所示。
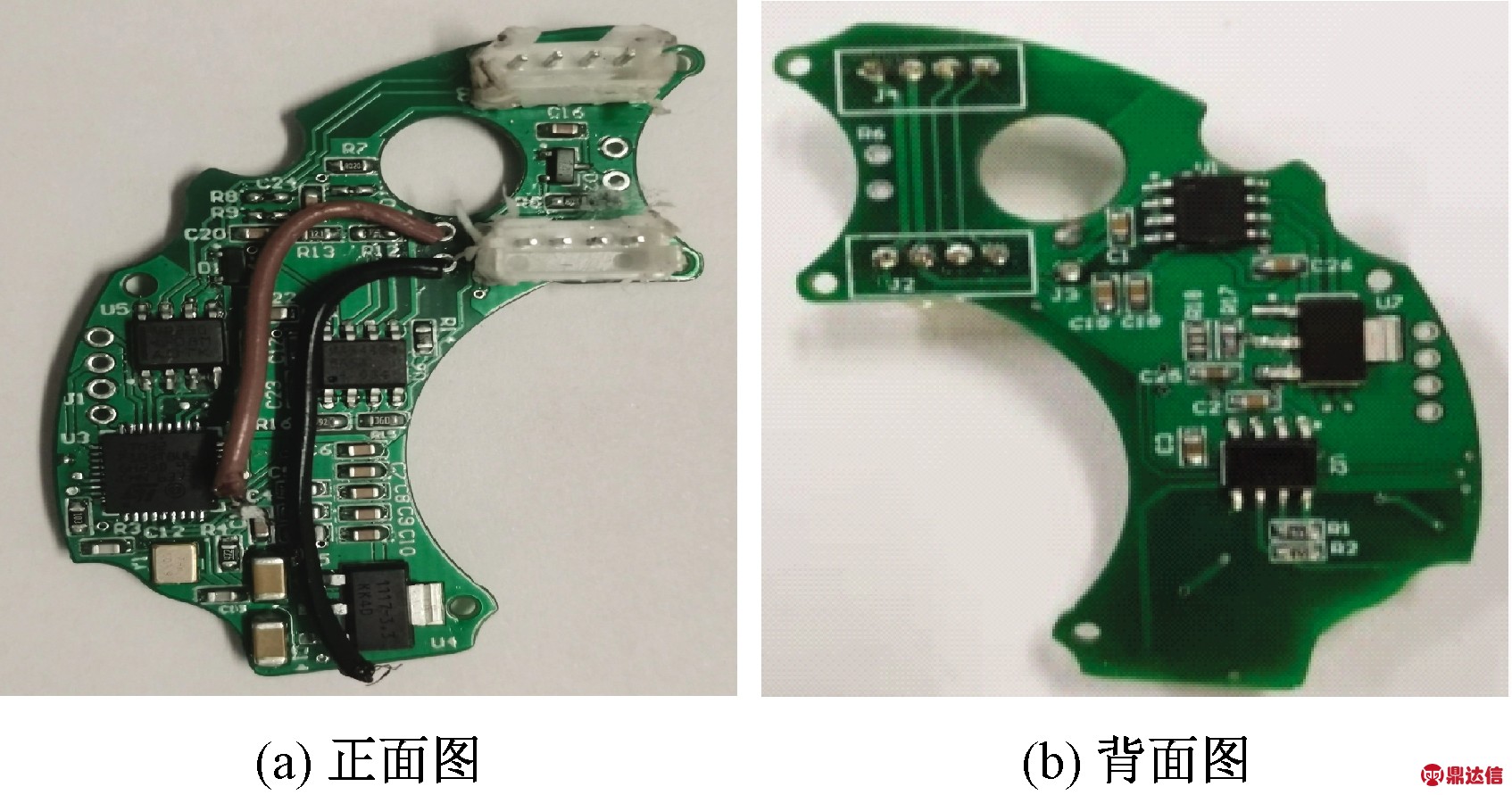
图6 驱动板集成电路图
Fig.6 Driver board integrated circuit diagram.
(a) Front view; (b) Rear view
最后,将各个部件进行装配调试,完成所有硬件部分的设计,装配实体如图7所示。
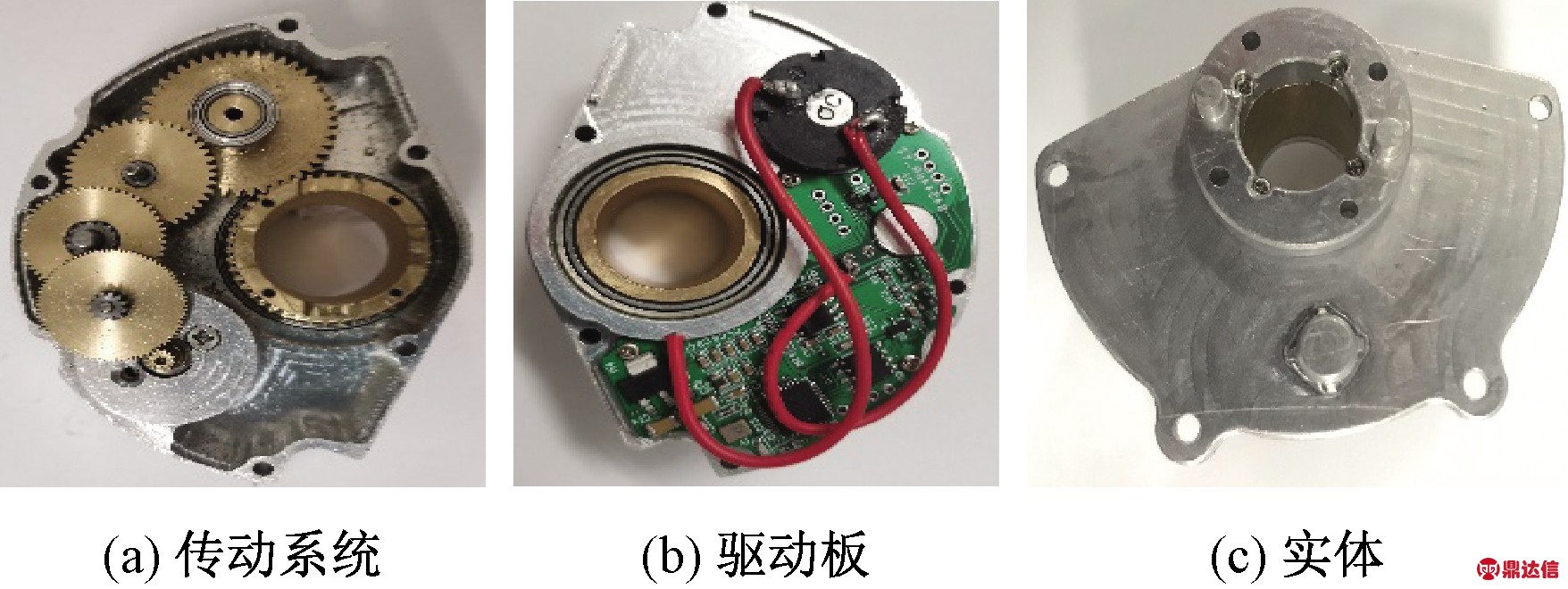
图7 机器人腰部关节实物图
Fig.7 Physical map of waist joint of robot.
(a) Transmission system; (b) Drive board; (c) Entity
为验证纺织机器人腰部关节运动的准确性和稳定性,利用Keil软件编写程序,将程序烧录到驱动板,实现单转速闭环控制和转速、电流双闭环控制,搭建如图8所示的实验硬件连接图。
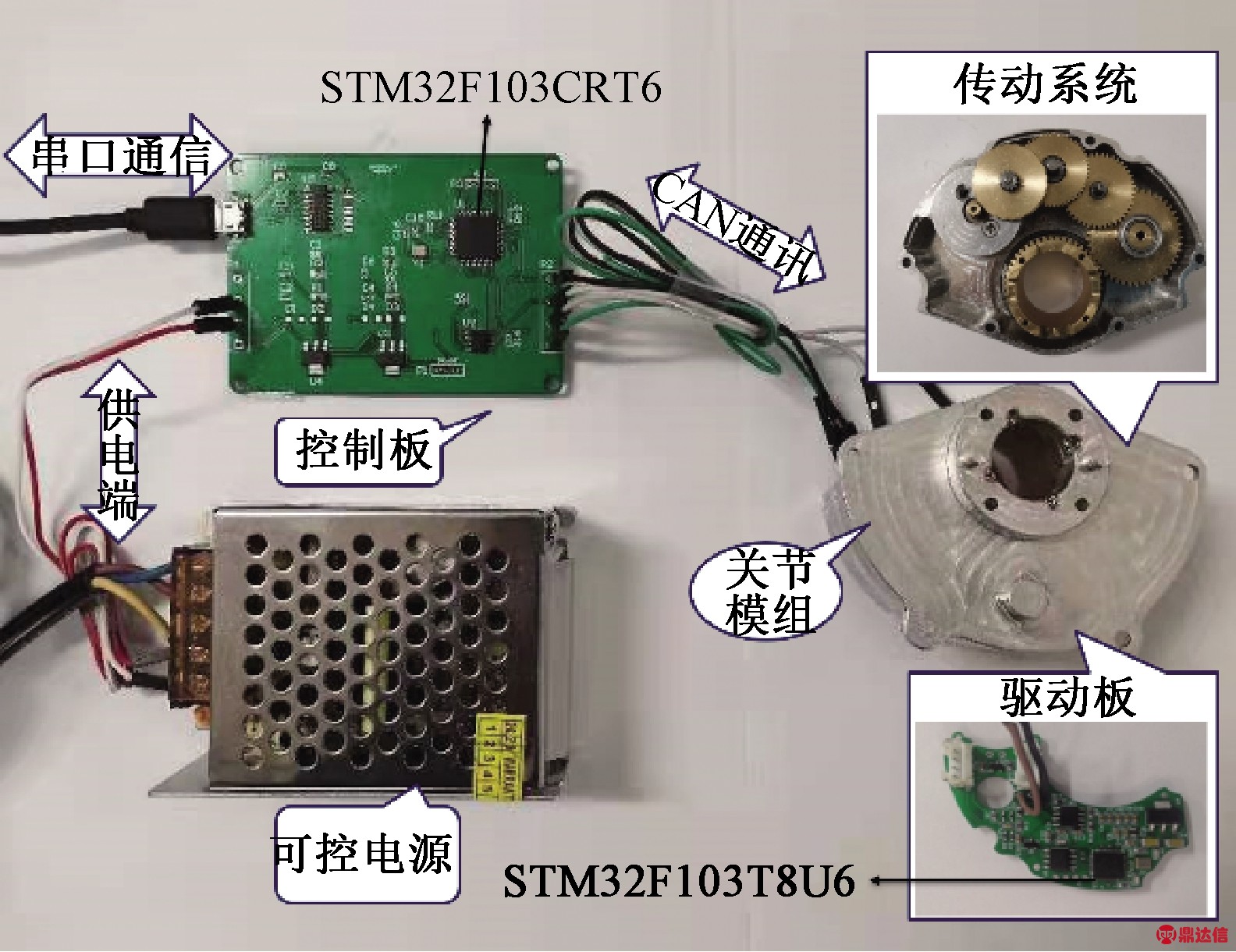
图8 实验硬件连接图
Fig.8 Experimental hardware connection diagram
Mo等[20]对控制电动机的硬件进行了对比研究。为检验不同控制方案下的电动机响应情况,同时观察电流的变化情况,采用不同的控制方式进行实验,结果如图9所示。
在单转速环控制时,由图9(a)可知,速度在很快的时间就可以达到额定转速,且超调量并不大;由图9(b)可知,在启动瞬间电流非常大,是额定电流的62.5倍。机器人关节为频繁启动部件,启动电流冲击加速元器件的老化,并对传动系统造成冲击,严重影响机器人关节寿命,故在工程中应尽量避免此类情况的发生。
在此实验基础上加入带电流截止的负反馈,将最大电流限制在额定电流的1.5倍,测量在额定工况空载时的转速,如图9(c)所示。可以看出,转速的响应时间明显加长,并且在进入稳态之前有多次抖动使得进入稳态时间变长,主要原因是对电流不能进行动态控制。
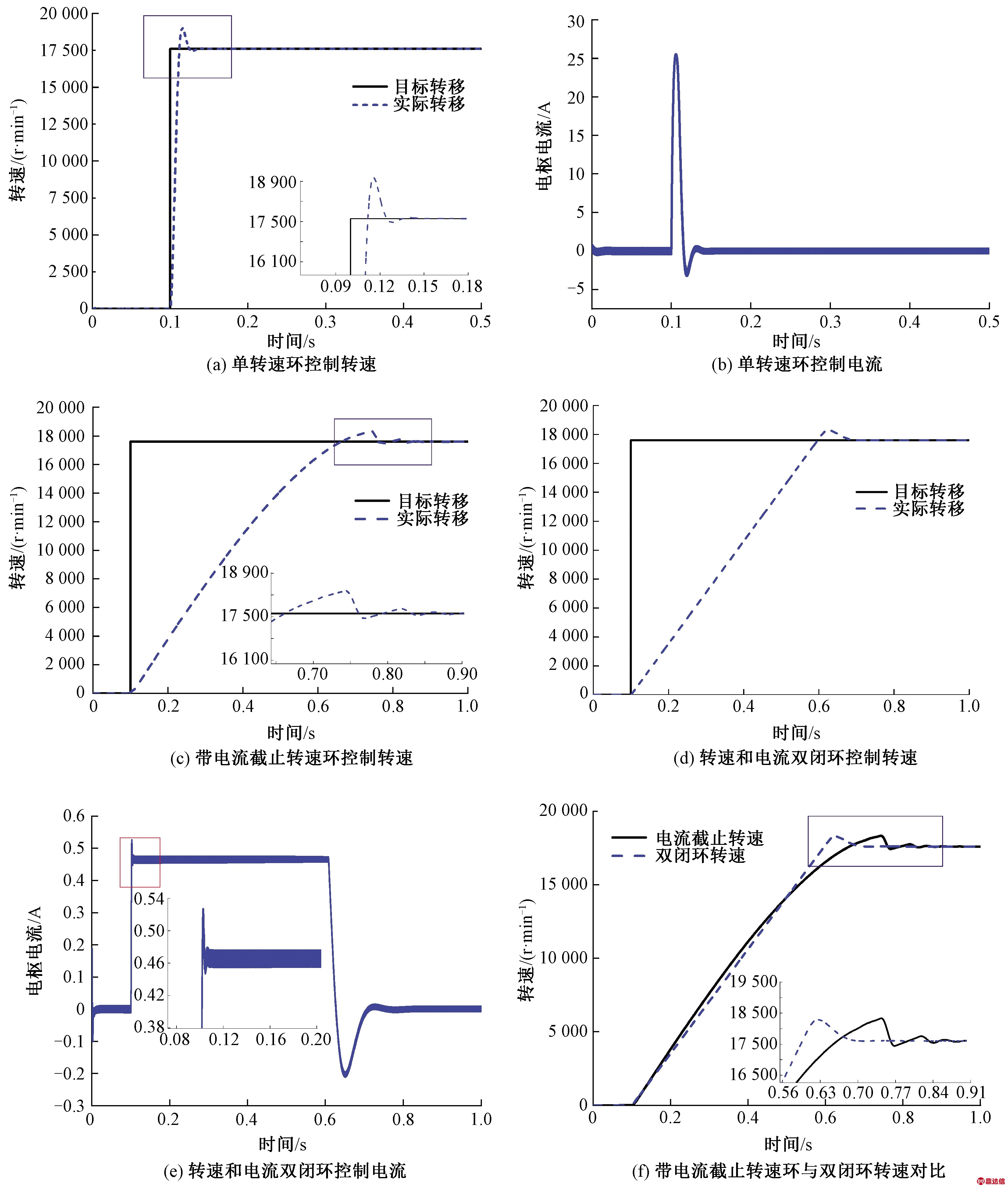
图9 额定工况下不同控制方案电动机响应
Fig.9 Motor response of different control schemes under rated conditions.
(a) Single speed loop control speed;(b) Single speed loop control current; (c) Speed control with cut-off current speed loop; (d) Speed and current double closed loop control speed; (e) Speed and current double closed loop control current; (f) Speed comparison between speed loop with cut-off and double closed loop
针对带电流截止的速度环中转速存在抖动,引入转速和电流双闭环控制,如图9(d)、(e)所示,电动机在启动的过程中电流环对电流进行动态调节,转速在达到预定转速后快速进入稳态。将转速和电流双闭环调速与带电流截止的单转速环调速进行对比,如图9(f)所示,双闭环调速比带截止电流转速环调速更快地达到额定转速,并且对超调量的抑制效果更加明显,可大大提高机器人关节运动的平稳性,故最终采用转速和电流双闭环调速。
为检测在设定不同转速时转速和电流双闭环动态调节的响应情况,分别测试500、1 000、5 000 r/min下的转速、电流响应曲线,输出波形如图10所示。在转速为500 r/min时电流没有达到截止电流就已达到设定转速,同时也率先进入稳态;在转速为1 000 r/min时,电流刚刚达到设定的电流最大值就达到了设定转速,达到稳态的时间会比500 r/min转速时长。对比3种转速可以看出,随着转速的提高,电动机进入稳态的时长变长。在转速图上,3条曲线都很快进入稳态,并且在转速和电流双闭环控制下电动机在500 r/min时,转速误差为±0.5 r/min;在1 000 r/min时,转速误差为±1 r/min;在5 000 r/min时,转速误差为±2 r/min。可见,电动机的转速提高其相对误差减小,对于高控制精度的机器人关节应尽量采用大传动比以减小相对误差带来的影响。本文中机器人关节减速比为395,大大降低了相对误差带来的影响,该机器人关节可以满足运动控制要求。
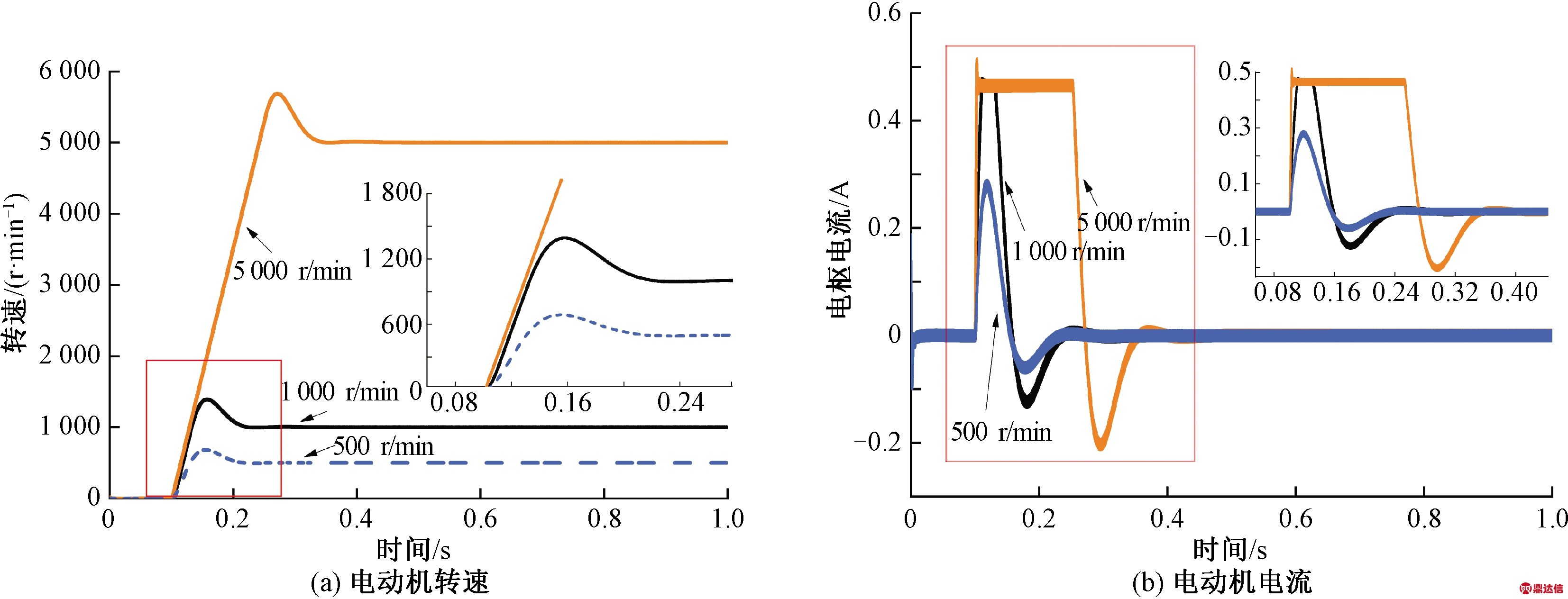
图10 不同转速下电动机响应
Fig.10 Motor response at different speeds.
(a) Motor speed; (b) Motor current
6 结 论
本文以纺织机器人腰部关节为研究对象,对现有关节进行优化,完成了三维模型设计和加工,针对驱动电路原理进行分析,设计关节驱动电路板,实验证明该驱动关节具有较高性能和效率。
针对机器人关节为频繁启动部分,为防止电流产生严重超调并满足运动控制高效、可靠的要求,可采用转速和电流双闭环控制。在多关节联动控制方式上,采用CAN总线方式进行串联通信,可避免采用PWM总线方式的并联通信,为多路机器人关节的联动控制简化了系统布线。测试证明,转速和电流双闭环控制能满足运动控制的需要。为减小转速相对误差,设计时尽量采用高减速比使电动机工作在高转速区。