摘要:针对饮料包装瓶盖件的内螺纹结构、外观要求及工艺分析,设计了延伸式热流道系统和内螺纹自旋脱模的倒装式注射模。模具为一模八腔,采用H型布置浇注系统,选择在产品内表面由延伸嘴尖的直通热喷嘴进料,以解决狭小型腔热嘴安放空间不足和热量传导的问题。螺纹型芯采用镶嵌组合设计,成型瓶盖产品设置的6个防转凹槽结构实现塑件止转。模具分三个面由定距拉板组件依次顺序开模,同时由定模外侧的电机驱动链条链轮传动模内齿轮组件,实现塑件与螺纹型芯的相对旋转脱模,最终由推板完全将产品推出。分型面的精密定位辅件和导向机构为模具精准合模和受力支承提供保证。经生产实践证明,模具结构紧凑合理,工作稳定安全可靠,实现了内螺纹瓶盖件完整的自旋脱模和高产量高质量精密注塑。
关键词:内螺纹塑件;热流道技术;延伸式热嘴;自旋脱模
全球对瓶盖和密封产品的需求大约以每年4.6%的速率稳步增长,在食品、饮料和医药品包装领域中,80%以上的都是使用塑料瓶盖[1]。当具有内螺纹的塑料瓶盖注射成型时,由于产品牙内螺纹与模具的粘模力较大,易出现产品皲裂、内螺纹拉裂、螺纹缺失、无法脱模等问题。因此,内螺纹塑件的自动脱模机构设计是此类注塑模具设计的难点,而且内螺纹塑件自动脱模机构制造成本高、生产稳定性差、经济效益低。工业上一般采用活动螺纹型芯或旋退脱模机构如马达电机驱动齿轮齿条、蜗轮蜗杆或液压油缸驱动链轮链条等方式实现螺纹的自旋脱模,脱螺纹的形式、机构布局、螺纹型芯运动等设计细节决定了模具整体布局及生产成本[2–7]。苏瞧忠[8]针对内有螺纹外有倒扣的滤芯盖三板式模具,在定模侧采用液压马达通过齿轮副传动完成自旋螺纹脱出,通过加强冷却系统设计避免模具零件热胀咬死。对于在动模型芯包紧力较大的深腔瓶盖类模具,可采用“油缸+齿条+齿轮”及二次脱模机构,螺纹芯片由液压驱动导向螺母引导旋转脱模,最后由推管完成二次脱模[9–10]。沈忠良等[11]设计了新型蜗杆驱动螺纹机构,将模具动作时的直线动力转化成螺纹型芯转动的动力,利用模具开模动力驱动齿轮抽芯,代替油缸驱动且降低模具结构尺寸而达到自动脱模的目的。
由于塑料瓶盖有外观质量要求或防止划伤手掌等,不允许浇口痕迹留在内螺纹制件的外表面,浇口必须设在制件的内表面,浇注系统的选择对此类精密注塑的成品质量至关重要。若采用普通冷流道模具,需在定模侧考虑浇注系统的顶出和内螺纹的脱模机构,倒装模具运动机构增多,结构复杂并磨损严重。如果采用热流道设计不需将浇注系统取出,可节约原材料,减少分型开模运动及熔体长距离的流动压力,能解决制品难以成型和质量不佳的问题[12]。但热流道系统的安放与脱模机构同在定模侧,顺序开模机构和脱模动力设计也是热流道倒装模具实施的难点。周慧兰等[13]针对面像识别机外壳模具进行冷、热流道的注塑模流分析,确定热流道浇注系统方案,最后采用动模倒装定距分型拉杆推板机构实现制品反向推出。对于汽车储物盒和电视机面壳等大型制件的倒装热流道模具,张维合[14]采用液压油缸与推杆推板二次推出保证产品平稳脱模。国内外专家学者对于热流道倒装模具的研究,主要应用于平板类或大型制件,热流道系统和定模推出机构的设计空间相对宽裕[15–17]。
但是,针对大批量生产及高质量要求的内螺纹包装瓶盖件,因产品模腔狭小,并要求内侧浇注,需要在模具的定模侧同时实现螺纹脱模机构的自动旋退和热流道系统的安置,无疑增大了模具设计和制造的难度,是内螺纹塑件热流道注塑倒装模具的新挑战。基于相关研究成果,笔者进行了内螺纹瓶盖自旋脱模的热流道倒装注塑模设计。
1 塑件结构分析
饮料包装用瓶盖产品结构如图1所示,用于饮料包装瓶的瓶盖件重约4 g,高约21 mm,外侧表面的直径为25.70 mm,内侧表面的直径为20.70 mm。瓶盖的内表面底部有几圈凸起的圆环,最高4.4 mm,直径8 mm。产品内侧需成型右旋螺纹长17.8 mm,螺距3 mm,用于旋紧密封药品,需设计内螺纹的脱模机构。另外,为便于留在螺纹型芯上的塑件在脱模时止转,制品口部需成型6个3 mm×1.2 mm的方形凹槽。为防划伤手掌及满足尺寸精度、外观质量要求,根据产品应用场合及使用要求,保证尺寸精度和外观质量,不允许从外表面浇注。塑件年产量100万件,材料为聚丙烯(PP),收缩率为1.0%~2.5%,从加工性能分析,熔料流动性好、吸水性小、容易成型。
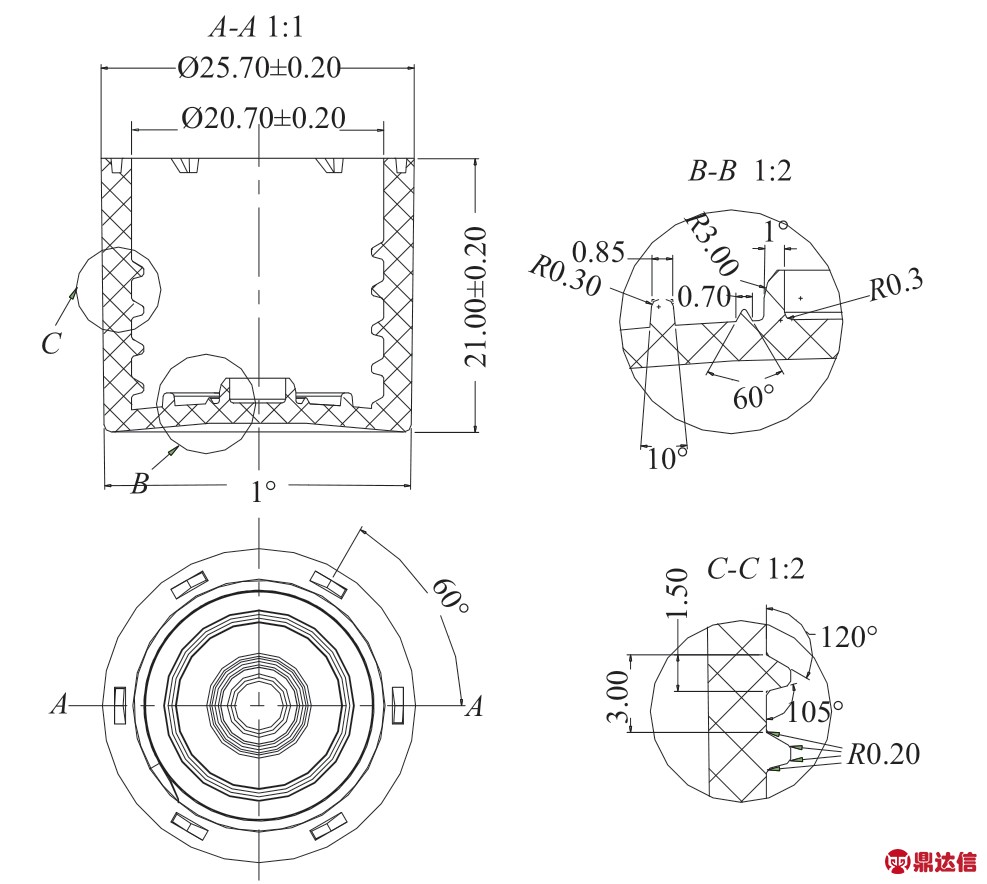
图1 饮料包装用瓶盖产品图
2 模具总体结构设计
瓶盖产品总尺寸不大,但由于产品外观质量和浇口设置要求,只能从产品内侧中心进料,开模后塑件留在定模侧,需在定模侧设置螺纹旋退和推出机构。由于采用倒装的脱模机构,如果采用普通冷流道的三板模注射成型,浇注系统流程较长,注塑压力损失大,浇注凝料较多。而且,模具需多次分型开模,运动机构增多,模具结构复杂并加重磨损。
综合考虑产量和质量需求,为实现全自动化生产,模具运作时无浇注系统凝料并能实现螺纹自动旋退顶出,采用倒装螺纹脱模的热流道注塑技术。
在两板模架的基础上,增加了热流道系统和电机、链轮及齿轮旋退螺纹机构,模具的总体装配机构如图2所示。模具以一模八腔均衡布置结构,采用H型热流道系统以延伸式直通的热喷嘴浇注,塑料在进入浇口的流动通道内一直保持熔融,不仅节约原材料、提高生产率、优化塑料的流动性能及产品表面质量,而且能显著降低注塑机的注塑压力及锁模力;也能简化模具结构为单分型面结构,从而减少模具的运动机构和限位分型的复杂程度。由于制品的脱出方式为定模侧倒装结构,需设计定距拉板组件实现各分型面的依次打开,采用模具外侧的电机驱动链条链轮,并采用传动模内齿轮脱模的螺纹自旋退方式,实现塑件与型芯的相对旋转将产品脱出模具。
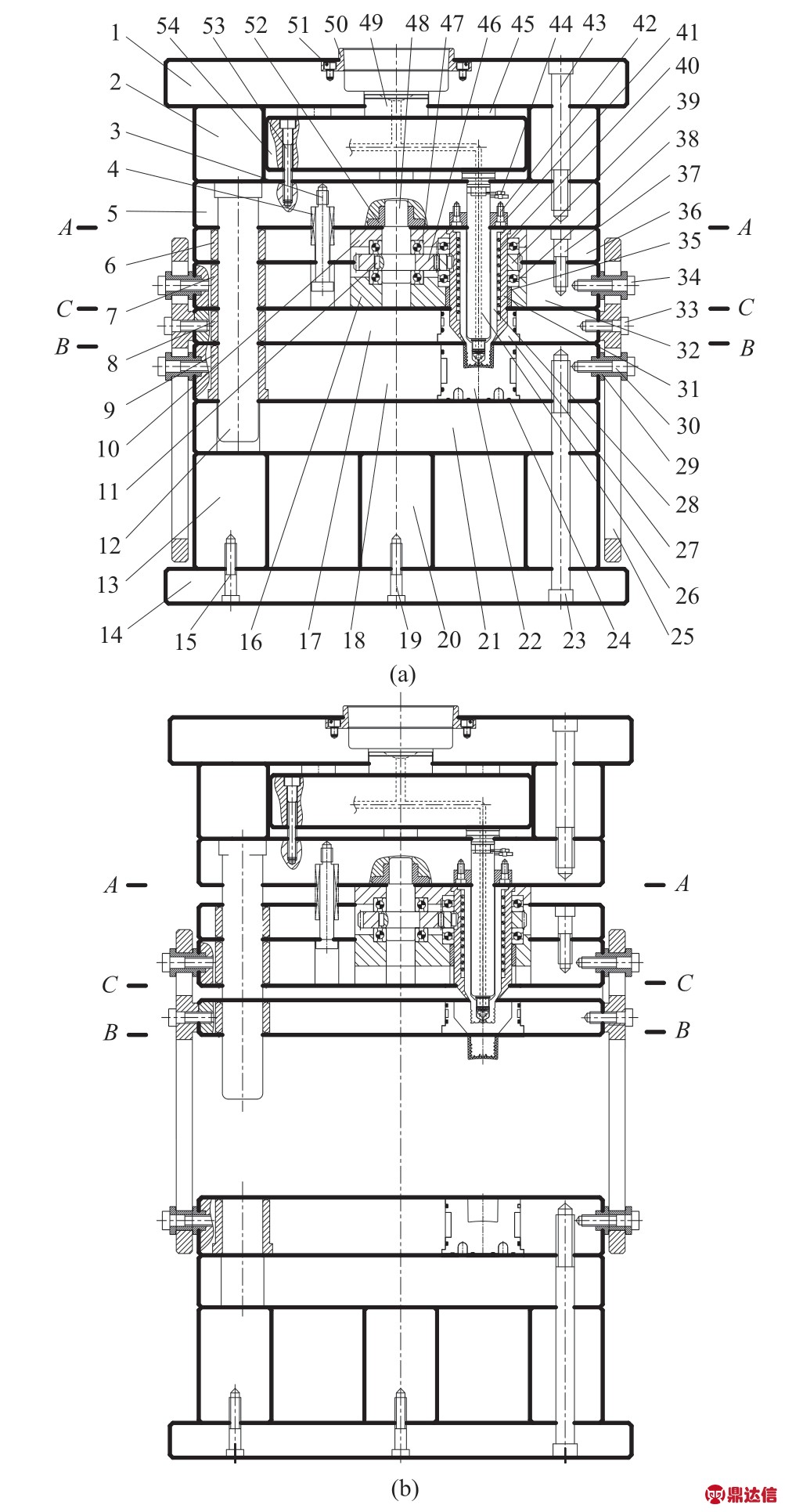
图2 定模侧倒装内螺纹自旋脱模的热流道注塑模具结构
1—定模座板;2—支撑板;3—限位螺钉;4—开模弹簧;5—热嘴固定板;6,7,8,9—导套;10—齿轮轴支板A;11—键;12—开模导柱;13—垫块;14—动模座板;15,19,23,33,37,42,43,51,53—螺钉;16—齿轮轴支板B; 17—推件板;18—动模板;20—支撑柱;21—动模垫板;22—动模镶件;24—密封圈;25—定距拉板;26—延伸式热喷嘴;27—定模镶件;28—螺纹型芯;29—螺钉衬套;30—定距螺钉B;31—旋退螺纹镶件;
3
2—定模板 ;34—定距螺钉A;35—衬套;36—定模垫板;38,47—滚动轴承;39—脱模齿轮;40—压缩弹簧;41—热嘴固定环;44—热流道温控线路;45—隔热承压块;46—从动齿轮;48—齿轮轴;49—主喷嘴;50—定位圈;52—轴套;54—热流道板
A,B,C—分型面
a—合模状态;b—开模状态
3 模具组成机构设计
3.1 成型零件设计
由图2可见,螺纹型芯28、动模镶件22、定模镶件27和旋退螺纹镶件31构成的封闭型腔用于塑料注入成型瓶盖产品。考虑加工及装配方便,成型零件采用镶嵌组合设计,并在分型面的模具周边设有辅助定位块实现精密定位。旋退螺纹镶件31主要成型产品上设置的6个防转凹槽结构,其能在开模时在齿轮带动下将产品自旋脱模。利用压缩弹簧40在螺纹型芯28和定模垫板36上形成的预紧力,可防止反复旋转脱模对旋退螺纹镶件31造成松动。为适应模具高精度、高产量、耐磨和抛光的要求,型芯型腔镶件材料选用S136,热处理硬度48~52HRC。装配定模螺纹型芯镶件后的热喷嘴组件如图3所示。
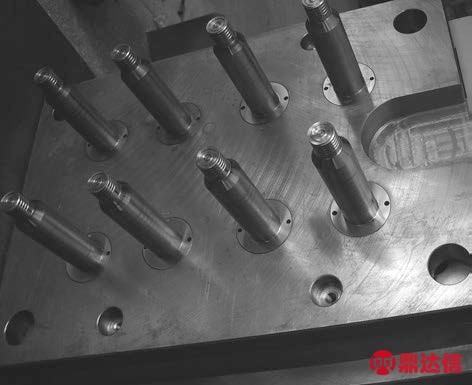
图3 装配定模螺纹型芯镶件后的热喷嘴组件
3.2 浇注系统设计
浇注系统采用延伸式直通浇口的热流道系统,见图2,塑料在有加热及温控系统的主喷嘴49、热流道板54和延伸式热喷嘴26的流动通道里保持熔融,熔体经主喷嘴49进入热流道板54,再经H型分流道转向均衡进入8个安装在热嘴固定板5上的延伸式热喷嘴26,熔体最后注入由动模镶件22、螺纹型芯28、定模镶件27和旋退螺纹镶件31所构成的型腔内。
(1)热流道系统的结构创新设计。
热流道系统的结构和组成如图4所示,相比于传统热流道系统,为顺利从产品内侧底部浇注,在热嘴部分做了创新的延伸设计,热流道组件主要由中心主喷嘴3、热流道板1、延伸式热嘴9、隔热承压块5、中心定位垫块10及加热温控元件等组成。热流道板内流动通道采用H型对称布置,单侧一级流道下设4个热嘴总共需8点浇注。因浇口设在产品内侧狭小的螺纹型芯镶件内,普通热嘴主体的安放空间受限,故采用延伸式热嘴9将物料送达浇口。中心定位垫块10和圆柱销11的槽型定位防止热流道板转动及整体偏移,将热流道板两侧的8颗紧固螺钉安装固定在热嘴固定板上。每个热嘴独立控温,加上热流道板的2组加热温控元件,热流道系统共设10个区,由外置温控器精确控温,保证物料在流动通道内的持续熔融。
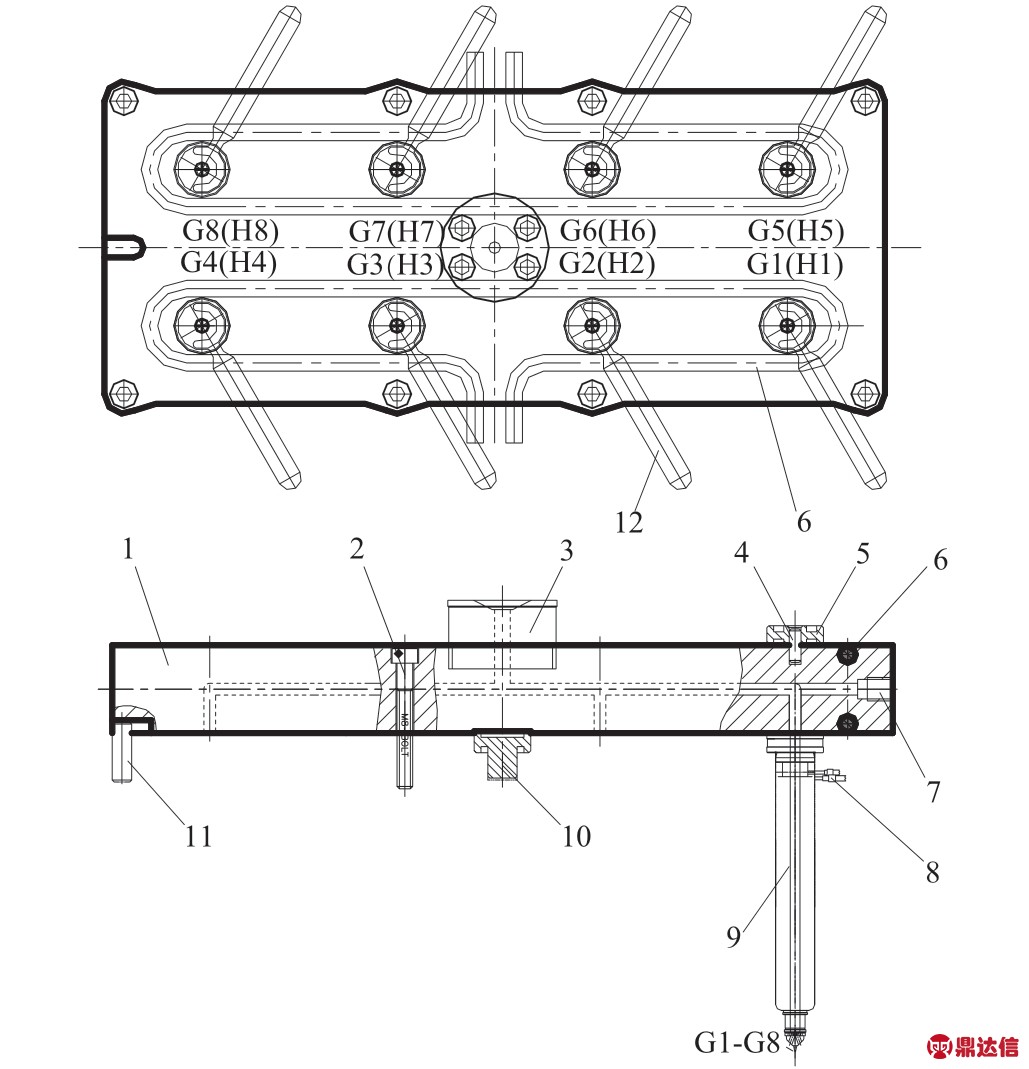
图4 延伸式热流道系统的结构与组成
1—热流道板;2—螺钉;3—中心主喷嘴;4,11—圆柱销;5—隔热承压块;6—热流道板发热器;7—流道塞头;8—温控线路;9—延伸式热嘴;10—中心定位垫块;12—热嘴发热器端头
生产时的延伸式热嘴头部如图5所示,为平稳将熔融塑料从产品内侧表面送入型腔,热嘴嘴尖相比常规热嘴延长20 mm,为保证延长部分的嘴尖无加热和温控元件导致物料温差,此嘴尖需采用热传导性能优异的铍铜合金加工。
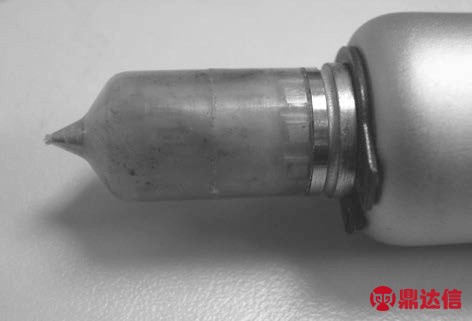
图5 注塑后的延伸式热嘴头部
(2)热流道系统的定位和隔热措施。
隔热支承块和中心定位块的结构和装配如图6所示。考虑受热膨胀的影响,中心定位块和热嘴以精度H7/g6与热嘴固定板过渡配合定位。隔热支承块10和圆柱销9,热流道板8和定位销4采用H7/m6将热流道板可靠定位并防转。
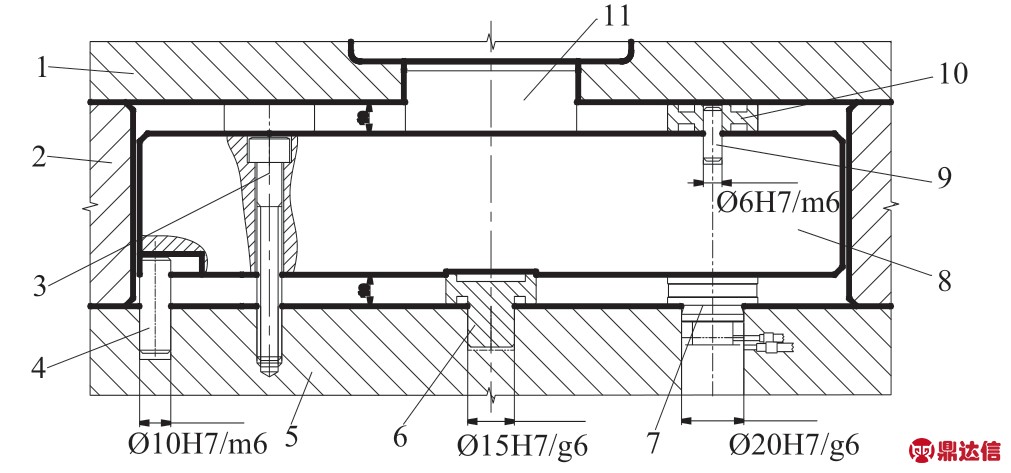
图6 隔热支承块和中心定位块的结构和装配
1—定模座板;2—支承板;3—螺钉;4—定位销;5—热嘴固定板;6—中心定位块;7—热喷嘴;8—热流道板;9—圆柱销;10—隔热支承块;11—中心主喷嘴
为避免热量散失和保证加热器在额定功率下工作,热流道系统与其它模具零件之间应能较好的隔热,除定位、支撑、型腔密封等需要接触的部位外,热流道系统应尽量减少贴合面积,隔热方式可采用空气隔热或绝热材料隔热[18]。
热喷嘴的隔热空气间隙为3 mm,并且热嘴主体上的隔热衬套会进一步减少热嘴内加热器的热量散失。热流道系统支撑板不仅需设置加热器出线槽和压线槽,还需设计隔热空气间隙10 mm以上,如图6所示。热流道板与定模座板之间的隔热支承块,以及流道板与热嘴固定板之间的中心定位块,不仅对热流道板起定位和支承作用,还可以尽量减少与定模座板的接触面积。
3.3 内螺纹自旋脱模机构设计
该模具采用电机、链轮和齿轮机构,驱动旋退螺纹镶件实现内螺纹的自旋脱模。内螺纹自旋脱模机构如图7所示,螺纹自动旋退机构采用模数m=1.5的齿轮系(齿轮21,22,24,26)互相啮合,由4组滚动轴承23支撑各个传动轴上载荷和扭矩。开模时,模具外侧电机28通过链轮A(件1)、链条5和链轮B(件8),驱动链轮从动轴6上的齿轮A(件26) 沿线依次传递力矩给齿轮B(件24)、齿轮C(件22)和齿轮D(件21)。在2个从动齿轮B,D驱动下,8个脱模齿轮16带动旋退螺纹镶件20使瓶盖塑件17作回转运动,使塑件从螺纹型芯18上脱出。采用电机-链轮-齿轮传动的自旋脱模机构,虽然模具结构复杂,零件精度要求高,加工费时,但易于实现自动化,适合大批量制品生产。
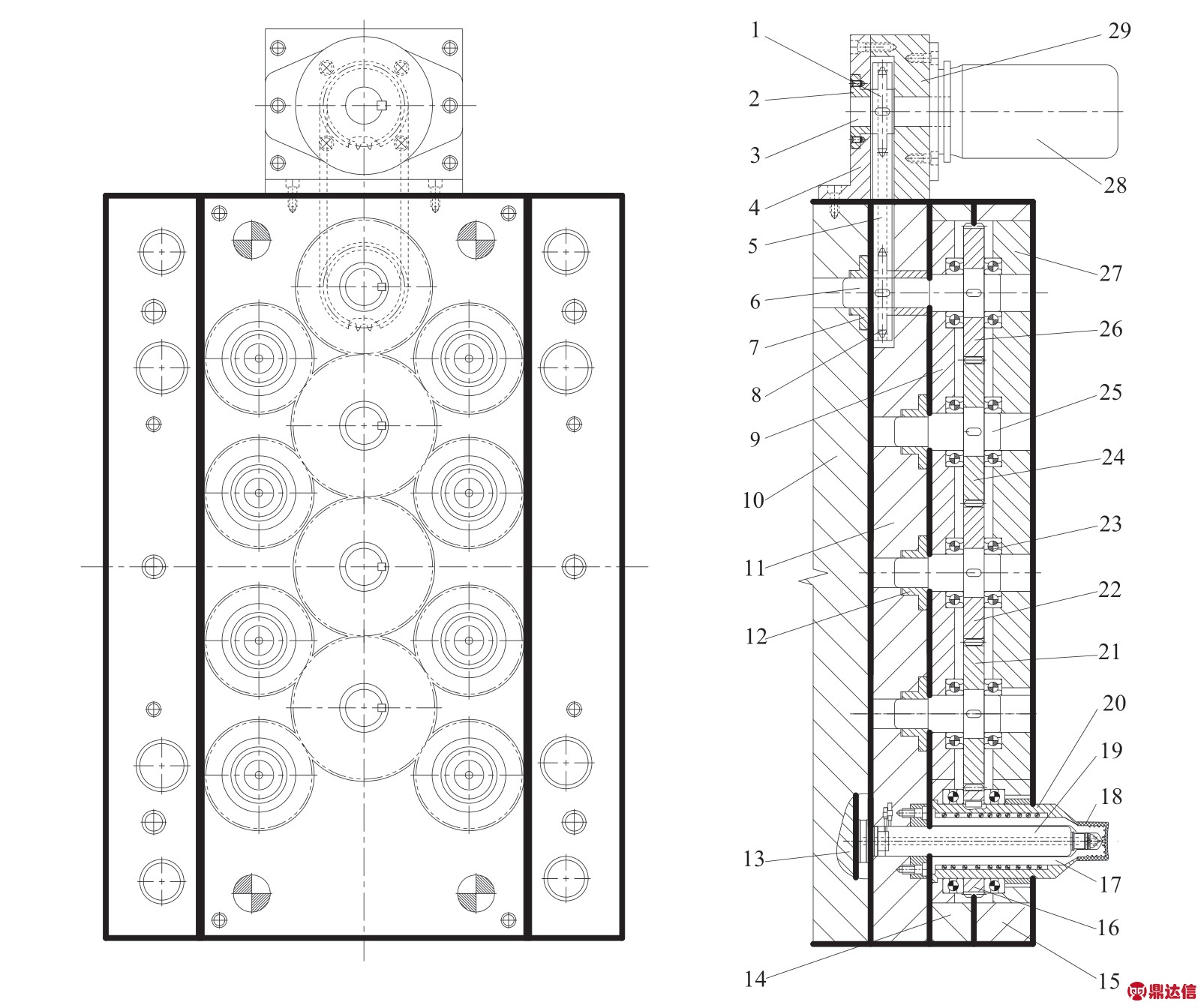
图7 链轮齿轮传动的内螺纹自旋脱模机构
1—链轮A;2—链轮轴盖;3—链轮主动轴;4—电机座板;5—链条;6—链轮从动轴;7—链轮轴套;8—链轮B;9—齿轮轴支板A;10—支撑板;11—热嘴固定板;12—轴套;13—热流道板;14—定模垫板;15—定模板;16—脱模齿轮;17—瓶盖塑件;18—螺纹型芯;19—延伸式喷嘴;20—旋退螺纹镶件;21—齿轮D;22—齿轮C;23—滚动轴承;24—齿轮B;25—齿轮轴;26—齿轮A;27—齿轮轴支板B;28—电机;29—电机固定板
螺纹型芯转动圈数U 由式(1)确定[19–20]:

式中:U——螺纹型芯转动圈数;
Us——安全系数,为保证完全旋出螺纹所加 工余量,一般取0.25~1;
L——螺纹牙长;
P——螺纹牙距。
根据产品图中螺纹参数要求,L=13.8 mm,P=3 mm,取Us=0.4带入式(1)计算得螺纹型转动圈数U=(13.8/3+0.4)=5圈。
3.4 顺序开模机构设计
模具的顺序开模、螺纹旋退和塑件推出需要限位机构完成。由图2可见,生产时,注塑后的塑件经保压、冷却和定型后,模具在导向机构开模导柱12和导套6,7,8,9的作用下,由开模弹簧4作用首先从A-A分型面打开,产品从动模镶件22上将外表面脱出。行至一段距离时,限位螺钉3作用定模垫板36和定模板32停止,B-B分型面打开,在内螺纹自旋脱模组件的链轮链条和齿轮系的传动下,从动齿轮46与脱模齿轮啮合,在旋退螺纹镶件31作用下,塑件与螺纹型芯28发生相对运动自旋脱模。动模开模继续前行,当定距螺钉B(件30)触及定距拉板25限定位置时,C-C分型面打开。当定模板32运行至定距螺钉A(件34)设定距离,由推件板17将产品局部旋凹结构从螺纹型芯28上完全推出,开模状态见图2b。
3.5 冷却系统设计排气机构及冷却水道设计
该热流道模具需要控制塑件在模温80℃下注射成型,这有利于改善成型工艺、稳定尺寸精度和提高制品表面质量。如图2所示,该模具型腔镶件和型芯镶件周围均布置环形水道,并加设管套密封和密封圈。
3.6 导向及支承零件设计
为保证动、定模之间的开、合模导向和推出机构的运动导向,该模具采用直径为35 mm的直导柱导套机构。因动模侧不需推出机构,并且为保证动模部分的刚度和强度,减少热喷嘴射胶时对模具型腔的作用力,故在动模侧热嘴对应位置设计8个Ø65 mm支撑柱。
4 结语
基于饮料包装瓶盖件的结构、外观及工艺要求,设计了定模侧浇注的倒装内螺纹自旋脱模的热流道注射模。采用8点延伸式热流道系统在产品内侧浇注,限位螺钉拉板顺序开模,以电机链轮链条齿轮驱动方式,方便快速实现内螺纹塑件的自旋脱模。该模具总体结构虽然复杂,对模具设计和制造要求更高,但简化了传统模具定模侧脱模时的多次顺序分型取件的机构设置,经模具投入生产验证工作稳定顺畅,比传统模具,产品成型脱出的螺纹平稳完整,不仅减少螺纹损坏使外观质量更优,而且降低原材料成本,生产效率提升了30%适合大批量全自动化生产。