摘 要:目前中继阀的检测主要依靠整体制动机试验台,且检测步骤繁琐,测试精度、效率无法保障。针对中继阀由总风遮断阀、管座、双阀口式中继阀3部分组成的结构,采用自动控制与数字信号处理技术,设计一套中继阀性能检测系统。基于PCI数据采集控制卡,设计计算机数据采集控制系统,开发LabVIEW中继阀数据采集控制软件,搭建中继阀实验平台。模拟中继阀在缓解充气、缓解保压、制动、制动保压、过充5种状态下,实现对总风遮断阀动态响应、列车管阶段增压减压、活塞灵敏度、供气阀供气、排气阀排气、过充等6项测试,并采用差压法对其密封性进行测试。测试得到总风遮断阀平均动态响应时间为0.206 s,活塞灵敏度平衡性能最大压力不确定度为0.849 kPa,供气阀供气性能最大压力不确定度为0.864kPa,排气阀排气性能最大压力不确定度为0.854kPa,过充最大压力不确定度为0.851kPa。实验结果表明:系统性能稳定,满足中继阀各性能测试要求。
关键词:中继阀;数据采集;计算机控制;自动化;不确定度
0 引言
中继阀是轨道交通制动系统的关键部件,是轨道车辆对列车管压强的间接控制机构,它直接将空气制动的控制信号放大输出到执行机构,采用膜板活塞加双阀口的机构形式,其性能好坏将直接影响列车制动与行车安全。面对数额庞大的轨道车辆,其制动机普遍存在构造复杂、检修手段落后等问题[1]。哈尔滨铁路局齐齐哈尔科研所研制的机车制动系统工况检测仪[2]、兰州交通大学设计的基于虚拟仪器的嵌入式机车空气制动机试验台[3]都包含对中继阀的检测项,西南交通大学杨连宇等研制的中继阀试验台[4],这些测试台或是对各型整体制动机试验台的改进,或是测试项目不明确,无法满足对中继阀测试效率与测试精度的要求。采用自动控制、测试,数字信号处理等技术并通过计算机对中继阀各参数进行数据采集、处理、输出可以实现对中继阀性能检测水平的升级,同时也摆脱了原有对制动机整体检测台的依赖,能有针对性地对中继阀各性能指标进行严格的检测。
1 测试需求分析
为有针对性设计中继阀性能检测系统,本文选用国内某厂家生产的JZ-7型中继阀,其由总风遮断阀、管座和双阀口式中继阀3部分组成。结构如图1所示。
1.1 密封性需求分析
JZ-7型中继阀的密封膜片、管座与壳体等均存在泄漏的可能,需要对中继阀的密封性进行测试。原技术方案中采用气泡法检测各管口气密性,无法实现自动定量测漏且测量精度低、效率差,经比较,差压法具有检测压力高且能检测到微小泄漏等优点[5-6],所以本文采用差压法。测试项包括控制口、输入口非工作状态气密性与输入口全工作、半工作状态气密性。测气密性时,设置平衡时间为15s,测量时间为30s,得到泄漏量结果。
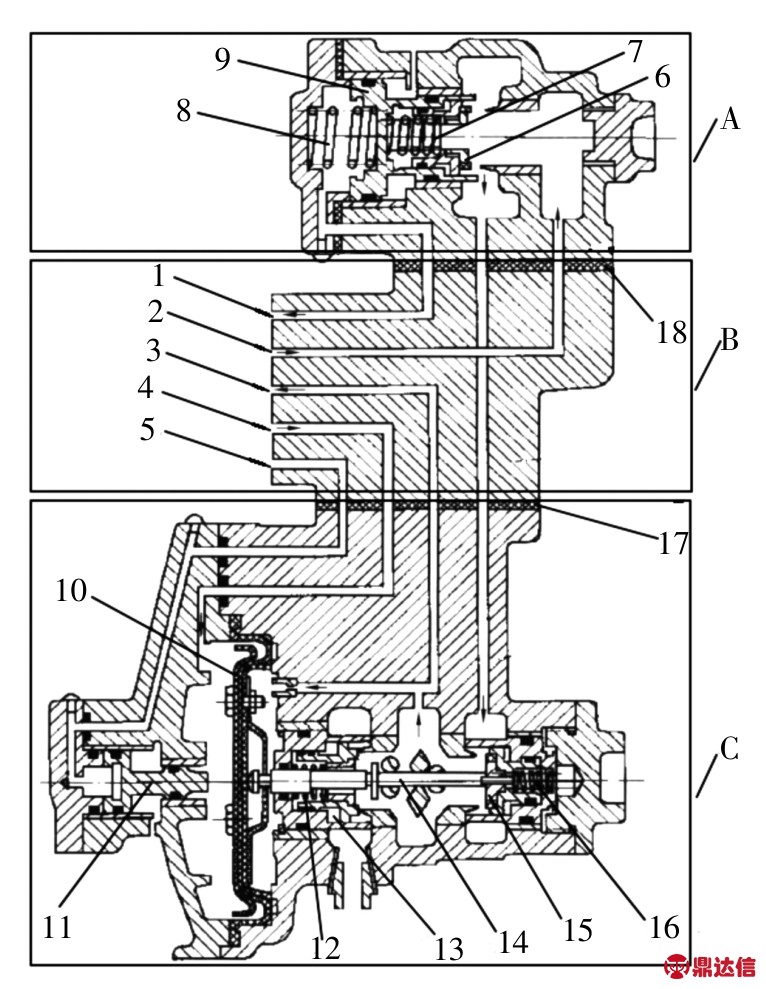
图1 中继阀结构简图
A.总风遮断阀;B.管座;C.双阀口式中继阀;1.遮断阀管;2.总风缸管;3.列车管;4.中均管;5.过充管;6.遮断阀;7.遮断阀弹簧;8.遮断阀套;9.作用弹簧;10.主活塞及膜板;11.过充柱塞;12.排气阀弹簧;13.排气阀;14.顶杆;15.供气阀;16.供气阀弹簧;17、18.橡胶垫片。
1.2 功能特性需求分析
总风遮断阀动态响应测试:总风遮断阀起着控制总风口(输入口)通断的作用。总风遮断管口加额定气压时,输入口关闭;通大气时,瞬间打开,测试输出口压力开始上升的时间。
列车管阶段增压阶段减压测试:对列车管口(控制口)循环进行升压与保压直至达到额定工作气压500kPa,之后进行循环减压与保压,直至250 kPa停止,每0.05s气压变化15kPa,测试输出口气压的变化,根据铁道行业标准对JZ-7中继阀的要求,测试过程中控制口与输出口的压力差应始终小于10kPa。
活塞灵敏度测试:中继阀工作时,当输出口压力达到额定气压,使输出口减压后关闭排气阀,测试输出口压力变化曲线。根据技术标准,输出口减压5kPa后关闭排气阀压力应能恢复。记活塞灵敏度平衡压力为P10。
引理1.3[8] 设τ1,τ2为集合X上的两个拓扑且τ1⊆τ2,则CIrrτ2(X)⊆CIrrτ1(X)。
归因理论既关乎我们的日常生活,又影响着教育教学活动的开展与更新。思想政治教育工作者理应根据当代大学生实际境况,结合归因理论进行思想政治教育。
供气阀供气测试:总风口作为输入口,当各管口正常打开后,瞬间向总风管口通入额定输入气压,测试输出口气压随时间变化的曲线。依据指标,输出口气压由0上升到480kPa的时间应不大于3s。记供气阀供气平衡压力为P20。
Exclusion criteria:case reports,experts'experience,reviews,animal studies,systematic reviews,and meta-analysis were excluded.
排气阀排气测试:中继阀控制口定压为500kPa时,当控制口减压250kPa,输出口压力由500kPa降至与控制口压力平衡的时间应不大于3s。记排气阀排气平衡压力为P30。
过充测试:过充管口作为JZ-7型中继阀特有的管口,当过充管口通入额定气压时,可使得列车管(输出口)获得超过规定压力25~40kPa的过充压力,从而缩短列车初充气和再充气的时间。当不通气时,列车管的过充压力能自动缓慢消除且不会引起机车的自然制动。记过充压力为P40。
2 中继阀性能检测系统设计
检测系统的设计包括测试管路设计与数据采集控制系统设计。
2.1 测试管路设计
中继阀工作位置分为以下5个状态:缓解充气位、缓解后保压位、制动位、制动后保压位与过充位。由于测试管路较多,40 L储气罐可以满足所有气路的测试要求。为达到更好的测试效果,除过充管口外与气密性阀板上采用电磁阀外,管路其他控制阀为满足快速充气响应这一要求,统一采用气控阀,并独立于气密性测试管路。为了精确控制气压,除在各个管路分别设置减压阀外,在控制口还设置电气比例阀以满足测试时的特殊供气需求。为达到阶段增压、减压,系统采用SMC的ITV3050-313CL型电气比例阀,其控制电压输入为0~10V,压力输出范围为0.005~0.9MPa。
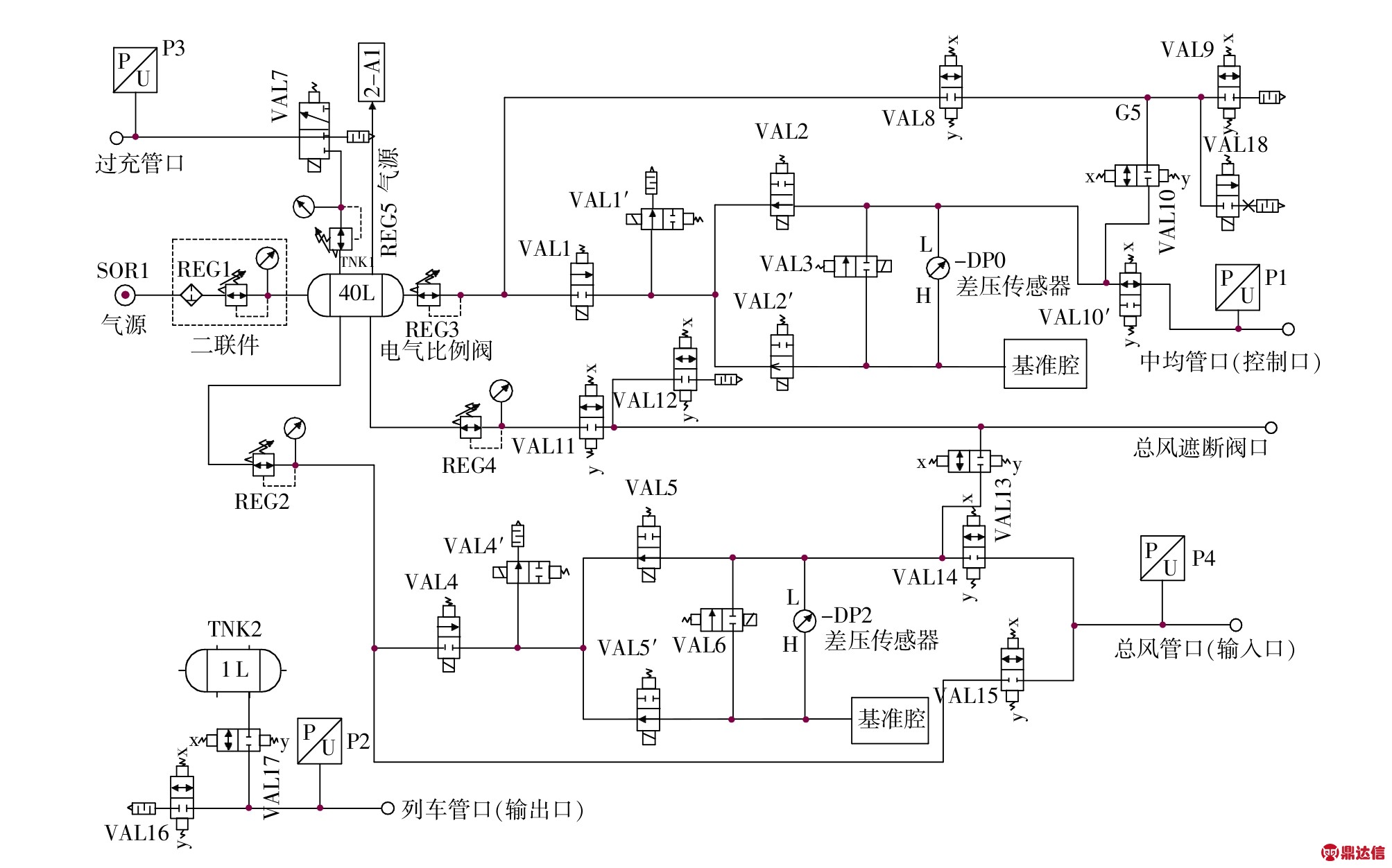
图2 管路系统原理图
P1、P2、P3、P4.气压传感器;-DP0、-DP2.差压传感器;TNK1.储气罐40L;TNK2.储气罐1L;REG1.二联件;REG3.电气比例阀;REG2、REG4、REG5.调压阀;VAL7.二位三通电磁阀;VAL1、VAL1′、VAL2、VAL2′、VAL3、VAL4、VAL4′、VAL5、VAL5′、VAL6、VAL18.二位二通电磁阀;VAL8、VAL9、VAL10、VAL10′、VAL11、VAL12、VAL13、VAL14、VAL15、VAL16、VAL17.气控阀。
根据测试需求,中继阀性能检测系统管路原理如图2所示,主要由气压传感器、电磁阀、气控阀、电气比例阀、减压阀、消音器和基准腔组成。中继阀过充管口、列车管口、总风管口、中均管口装有气压传感器,可实时监控气压变化;气控阀与消音器可实现快排功能,电磁阀与节流孔则可模拟慢排气的工作情况;电气比例阀可以实现对进气气压的精确调整;在列车管口(输出口)连接一储气罐,负责模拟负载的工况。
2.2 数据采集控制系统设计
系统采用两块数据采集卡:PCI-1711U带有最高采样率可达100kHz的12位A/D转换器、2通道12位模拟量输出与16通道数字量输入/输出;PCI-1730具有32路隔离数字量I/O,负责数字量输出控制的需要[7]。
开关电源、线性电源、数据采集卡与工控机组成了数据采集控制系统。开关电源与线性电源分别为电磁阀与传感器供电。工控机为系统的核心,结合PCI-1711U与PCI-1730两块数据采集卡,通过板卡的AO输出电压给电气比例阀;AI通道采集传感器信号;DI用于系统检测故障与处理用户操作;DO用于控制电磁阀的通断与信号报警灯。数据采集控制系统如图3所示。
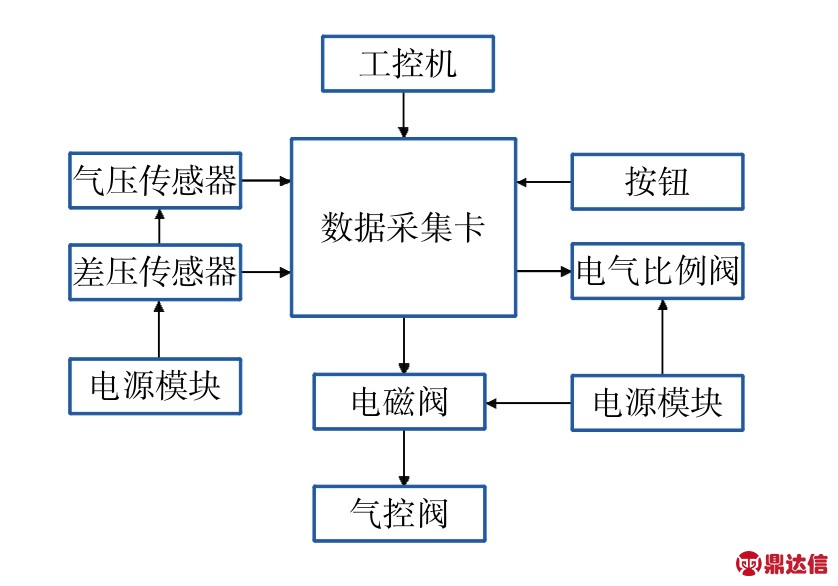
图3 数据采集控制系统硬件框图
3 测试数据分析
3.1 密封性测试分析
采用差压法对控制口、输入口非工作状态与输入口半工作、全工作状态的气密性分别测试10次,记录的气密性测试结果如表1所示。
3.2 特性测试分析
3.2.1 总风遮断阀动态响应测试
总风遮断阀动态响应测试曲线如图4所示,测试前控制口通入500kPa压力,顶杆将供气阀打开,但此时总风口因总风遮断阀口通入600 kPa压力而关闭,列车管口无压力。测试时将总风遮断管口通大气,输入口瞬时打开,往供气阀室供气,当压力达到控制口输入值时,供气阀关闭,保持与控制口压力一致。图中列车管压力瞬时超过500 kPa是由于供气阀关闭瞬间,挤压了供气阀室的空间,使得供气阀室与列车管相连通的整体空间压力有了一个瞬时升高。此时顶杆带动排气阀打开排气,使得列车管压力最终保持与控制口一致。总风遮断阀动态响应时间是指从总风遮断阀口通大气排压到列车管口(输出口)开始升压的时间,具体如表2所示,测试10次所得的平均响应时间为0.206s。
表1 密封性测试结果
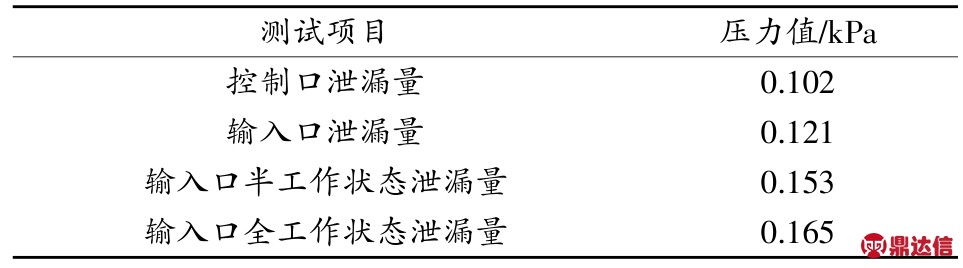
测试项目 压力值/kPa控制口泄漏量 0.102输入口泄漏量 0.121输入口半工作状态泄漏量 0.153输入口全工作状态泄漏量 0.165
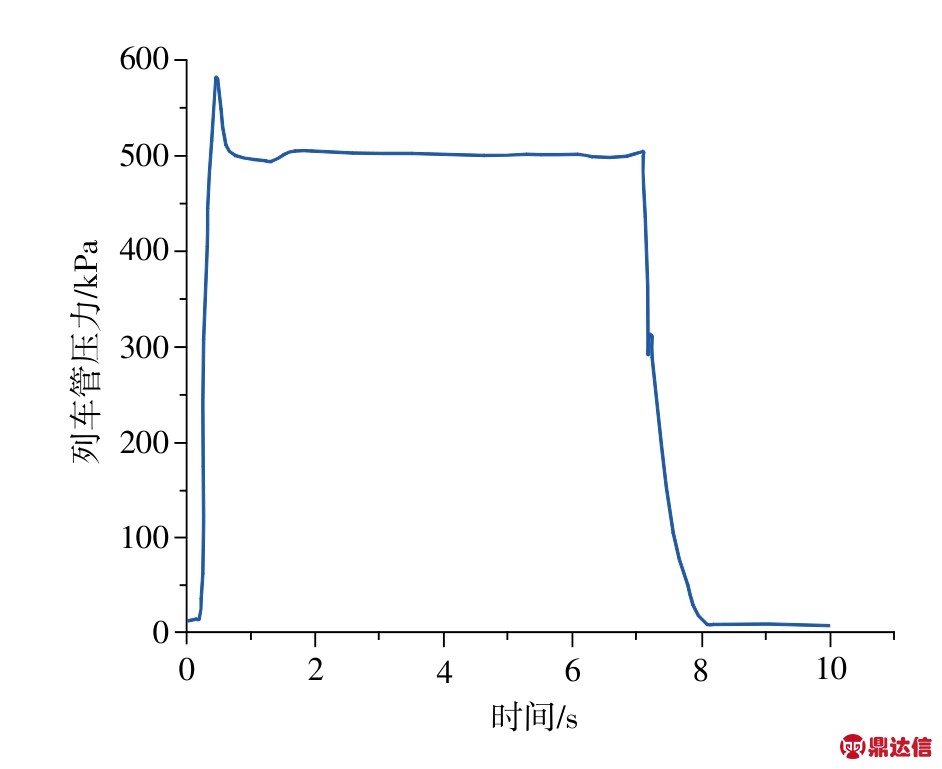
图4 总风遮断阀动态响应测试图
表2 总风遮断阀动态响应时间
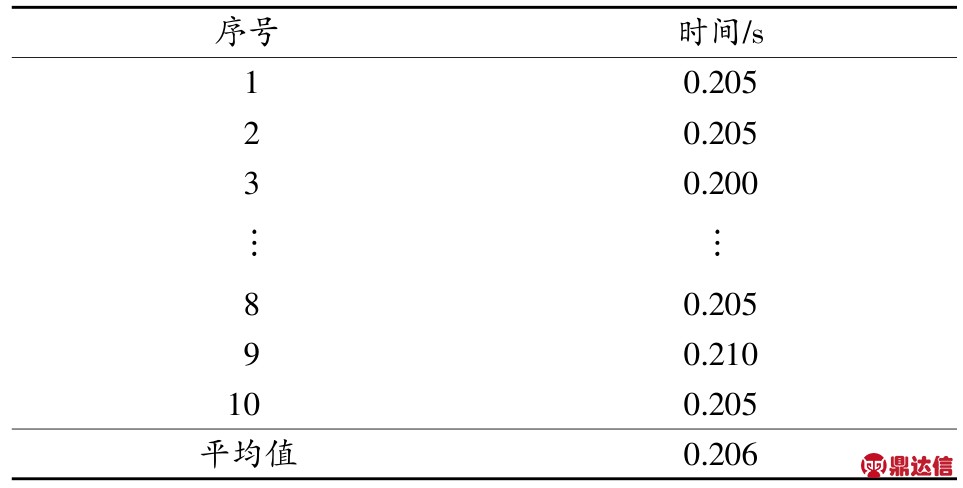
序号 时间/s 1 0.205 2 0.205 3 0.200 0.205 9 0.210 10 0.205平均值 0.206 8
3.2.2 列车管阶段增压、减压测试
列车管阶段增压、减压测试曲线如图5所示,设定输入口气压为505 kPa,测试时,通过电气比例阀使控制口实现增压-保压-增压与减压-保压-减压过程;由图5可知,输出口压力随着控制口不断变化。在升压阶段,输出口压力跟随性较好;减压阶段输出口压力跟随性略逊于增压阶段。增压阶段输出口压力变化虽落后于控制口,但在保压阶段能够达到与控制口一样的压力值;减压阶段输出口压力跟随性明显不如增压阶段,但仍然达到了压力差值不超过10kPa的测试标准。
3.2.3 活塞灵敏度测试
活塞灵敏度测试曲线如图6所示,当压力稳定后,4.5 s时使输出口泄压5 kPa,由图可知,活塞对于5 kPa的压力有响应,压力下降,随后压力逐渐恢复,活塞灵敏度达到测试要求。
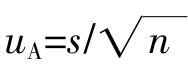
图5 列车管阶段增压阶段减压测试图
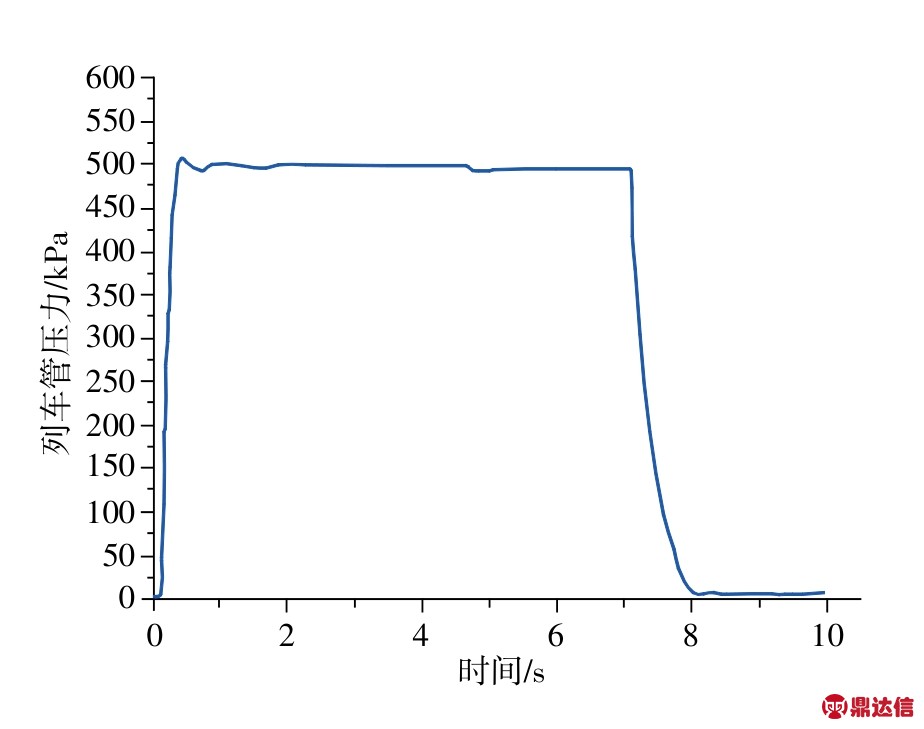
图6 活塞灵敏度测试图
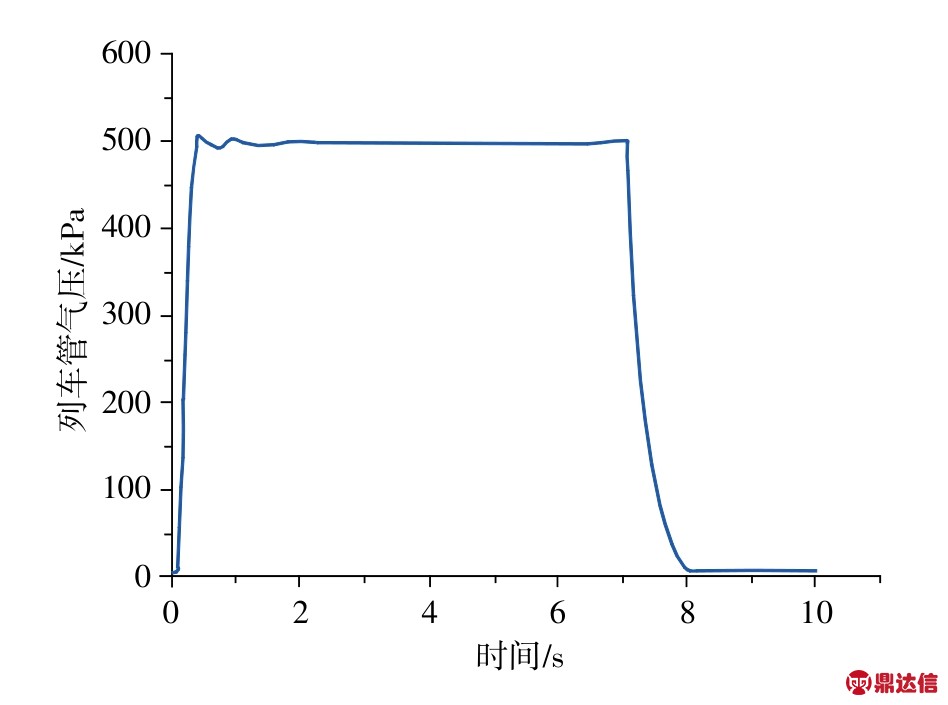
图7 供气阀供气测试图
表3 增压过程时间
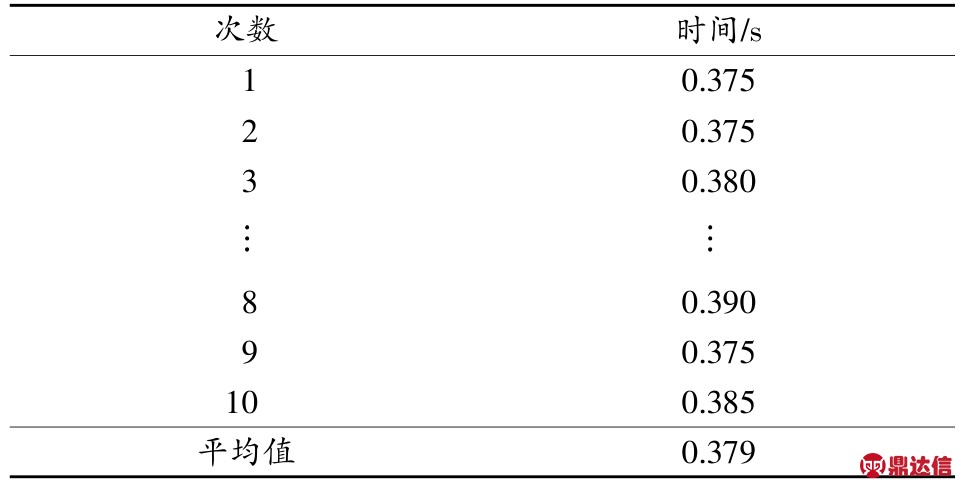
次数 时间/s 1 0.375 2 0.375 3 0.380 0.390 9 0.375 10 0.385平均值 0.379 8
3.2.4 供气阀供气测试
考察团出席了申办答辩会,听取了我的申办汇报和中国数学会、上海市数学会、华东师范大学领导以及相关团体领导的表态,提出问题并听取了答辩,考察了场馆、食宿设施和相关的城市基础建设,会见了上海市领导、上海市教委领导以及上海市普陀区领导.Fernaidando Arzarello主席和Angel Ruiz副主席还出席了华东师范大学主办的数学教育研究生论坛,并作了学术报告.
供气阀供气测试曲线如图7所示,曲线达到稳定气压前的波动是由电器比例阀自身PID调节造成的,并不会对测试造成过多影响(以下测试曲线同理)。从图中可知,对控制口快充气使得供气阀快速打开,列车管口(输出口)压力由0上升到480kPa的时间明显小于3s。测试10次得增压过程时间如表3所示,平均升压时间为0.379s,达到测试要求。
2) 在B、E两点同时发生串扰时,CW与CCW的相位差为2lBEΔβ,与主波列的相位差均为lBEΔβ,显然与主波不相干,产生强度型偏振误差,引起的陀螺输出误差在10-7°/h左右.
3.2.5 排气阀排气测试
凋亡调节蛋白[7](Bax)属于bcl-2的一种对抗剂,通过对细胞凋亡进行有效调节,使细胞的寿命得以缩短。通常较为正常的子宫内膜中,Bax主要表现为周期性变化,其增生期通常比分泌期高,但是在AM中,Bax的表现为明显比正常子宫内膜中的低,而且不会受到卵巢所具功能的影响,不会出现周期性的变化[8]。通常Bax与bcl-2之间的关系呈现为负相关性,bcl-2呈现增强,Bax就会呈现减弱,这就会使细胞凋亡的平衡被破坏,并使细胞凋亡减少,增加增殖,从而致使AM疾病发生。
排气阀排气测试曲线如图8所示,当列车管压力稳定在500kPa后,控制口瞬时减压240kPa,此时顶杆顶开排气阀进行排气,列车管压力降至与控制口压力相同时间为0.485s,符合压力平衡时间不超过3s的测试要求。
1.2.5.1 诠释执行力:管理者对全科护理人员角色定位,增强责任意识;要强调什么,明确检查什么;其实,很大程度上讲,员工不会做你希望的,但会做你要检查的;不检查等于不重视。
对照组每日静脉推注奥美拉唑40 mg+9%氯化钠注射液100 mL 2次,观察组每日在对照组基础上静脉推注奥曲肽100 μg+9%氯化钠注射液100 mL,之后每日增加至300 μg+9%氯化钠注射液100 mL 2次,滴注速度保持在25~50 μg/h,所有患者均进行止血、补液等处理,待治疗72 h之后比较两组患者的临床疗效。
3.2.6 过充测试
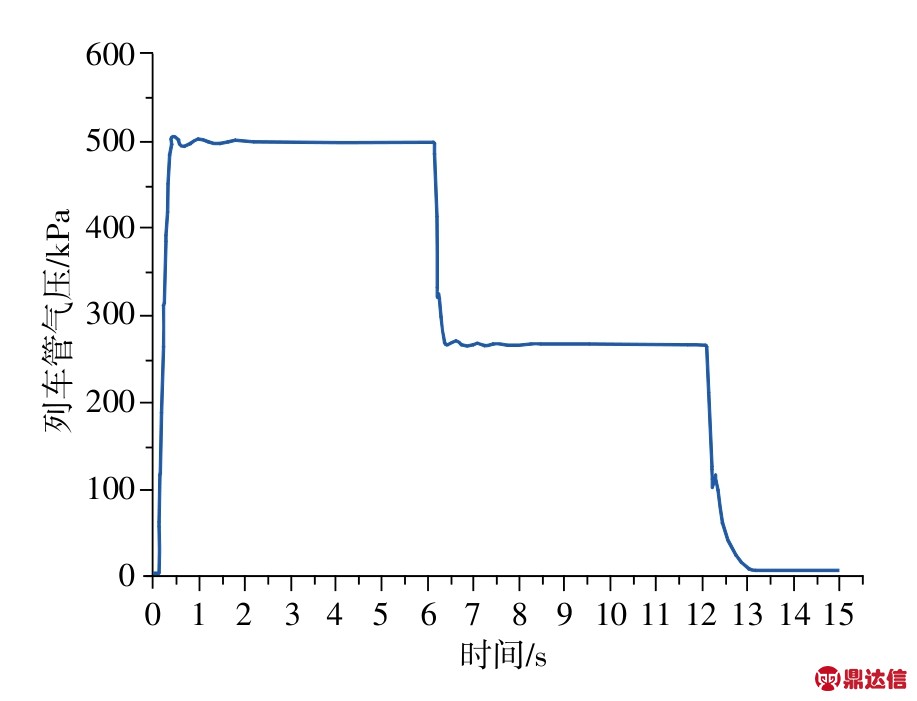
图8 排气阀排气测试图
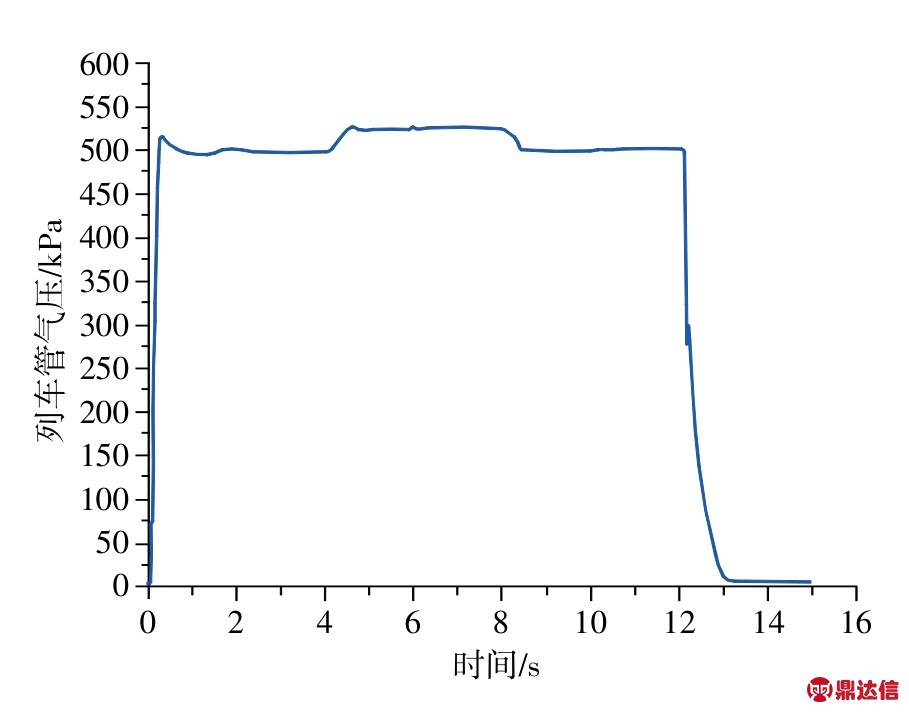
图9 过充测试图
过充测试曲线如图9所示,列车管达到控制口压力500 kPa后,向过充管口加600 kPa压力,此时过充口压力推动过充柱塞顶在中继阀膜板活塞上,使活塞左侧压力增加25.78kPa,延长供气阀口开启时间,从而使列车管过充25.78kPa。从图中可知,当过充管口压力排尽后,过充压力逐渐降低并消除,列车管压力恢复至500kPa。
上述测试数据与图像表明,中继阀性能检测系统满足了设计需求,实现了对中继阀各项性能指标的测试并给出了具体量化的测试结果,被测中继阀经检测合格。
3.3 不确定度分析
分析测试系统的误差源主要有气压传感器、差压传感器的测量误差,数据采集过程中的量化误差、偏移误差、增益误差[8]。JJF 1059——2012根据《测量不确定度评定与表示》中不确定度的定义及评定要求[9],对中继阀性能检测系统进行不确定度评定[10]。对活塞灵敏度平衡压力为P10、供气阀供气平衡压力为P20、排气阀排气平衡压力为P30、过充压力为P40分别测试10组数据记录于表4。
表4 综合性能评估测试结果
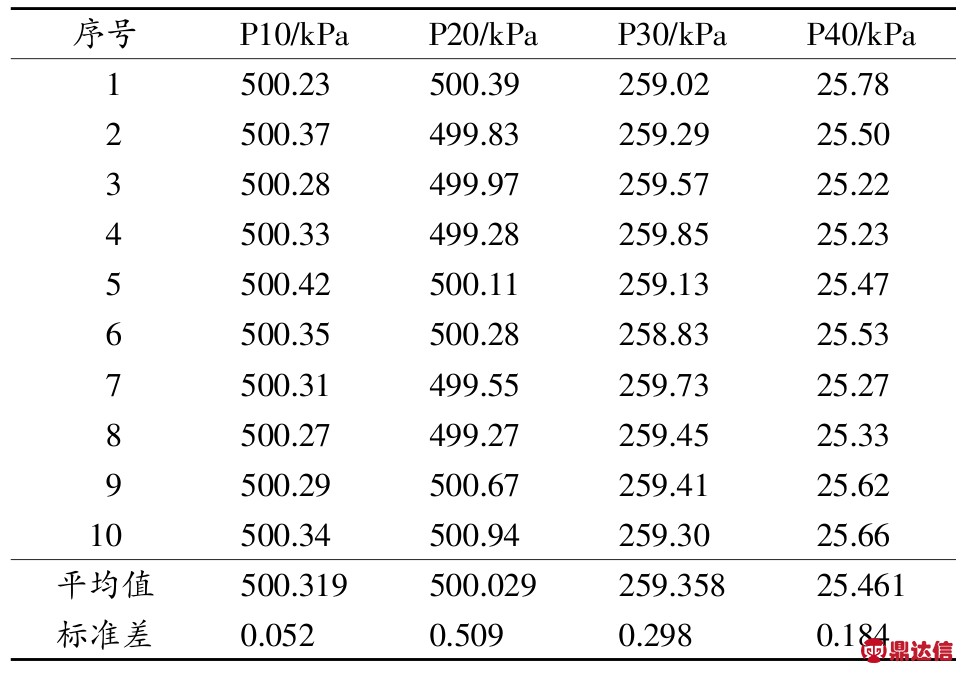
序号 P10/kPa P20/kPa P30/kPa P40/kPa 1 500.23 500.39 259.02 25.78 2 500.37 499.83 259.29 25.50 3 500.28 499.97 259.57 25.22 4 500.33 499.28 259.85 25.23 5 500.42 500.11 259.13 25.47 6 500.35 500.28 258.83 25.53 7 500.31 499.55 259.73 25.27 8 500.27 499.27 259.45 25.33 9 500.29 500.67 259.41 25.62 10 500.34 500.94 259.30 25.66平均值 500.319 500.029 259.358 25.461标准差 0.052 0.509 0.298 0.184
测试系统的误差主要由测量重复性、气压传感器、差压传感器、数据采集卡引起。测量重复性引起的不确定度分量uA用A类评定;气压、差压传感器带来的不确定度分量u1与数据采集卡带来的不确定度分量u2采用B类评定[11]。
根据A类评定公式可以求得,P10-P40的由测量重复性引起的不确定度分量分别为0.0164,0.1609,0.0942,0.0582kPa。
气压传感器的精度、线性、迟滞和重复性的总和小于±0.3%FS,在量程内引起的最大误差为2.7kPa,属于均匀分布,所以气压传感器的不确定度分量u11为0.577kPa,同理可得差压传感器产生的不确定度分量 u12为 0.0001kPa。
数据采集卡的量化误差、偏移误差与增益误差合成后对气压传感器和差压传感器产生的不确定度分量分别为u21为0.623kPa、u22为0.004kPa。
测试系统合成标准不确定度uc[12]采用以下公式

根据上式计算各合成不确定度如表5所示,实验重复性较好,满足测试要求。
综上所述,本文针对F市H社区的公共消防安全供给问题进行描述和分析,根据H社区当前公共安全服务供给的现状,以及在探索新模式的过程出现的一些问题,提出了公共消防安全联动机制供给的新思路。 城市公共安全服务供给的总体趋势是社会化多元主体共同供给,从“指令型”逐步向“开放型”社会联合供给模式转变,社区居委会和消防中介组织是其中不可或缺的参与力量,只有体制内和体制外两股力量形成合力,里应外合,形成三位一体的联动机制,才能满足人民群众日益增长的多样化公共消防安全需求,提高基层政府供给效率和能力,使得基层的公共消防安全的供给真正服务于人民、受惠于民。
然而,在国际单位制7个基本量中,千克是目前唯一依靠实物基准进行复现的。实物基准往往容易受到环境的影响,在长期稳定性方面存在局限性。
表5 合成标准不确定度

项目 P10 P20 P30 P40不确定度/kPa 0.849 0.864 0.854 0.851
4 结束语
本文设计了一套中继阀性能检测系统,实现了对中继阀各性能测试项的检测,测试过程高效、精确、自动化程度高。实验结果表明,该测试系统满足设计要求,测试数据准确可靠,已成功投入到企业生产中。弥补了JZ-7型中继阀技术条件中一些检测项模糊的检测标准,对后续新标准的制定具有借鉴意义。