摘要: 煮茧是缫丝生产的重要环节,煮茧质量直接影响到生丝质量、原料茧消耗、产量完成水平。元朝以前的缫丝生产,煮茧和缫丝混合在一起进行,通过热水传导能量,软化丝胶。工业革命后,日本发明了以千叶式为代表的煮茧机设备,使用蒸汽煮茧。进入21世纪后,中国研制出减压自动煮茧机,采用真空技术,将蒸汽能量传导到茧层内部,极大提高了煮茧均匀性。纵观发展历程,煮茧质量的提高是通过煮茧设备及工艺技术提高来完成的。文章回顾了古代煮茧技术,着重分析了近代以来各个时期的煮茧设备、性能及对未来的展望。
关键词: 煮茧;设备;工艺;回顾;展望
煮茧是缫丝生产的重要环节,其原理和作用是将茧置于水中,利用水、热或助剂的作用,经一定时间处理后将茧丝丝胶适当膨润溶解,减弱丝胶粒子间结合,使其胶着力降低,胶着不匀改善,以便缫丝时茧丝能按胶着点连续不断地顺次离解,并集束抱合成生丝。煮茧质量的高低关系到生丝质量、原料茧耗、产量完成水平。元朝以前缫丝是煮、缫不分家,边煮边缫,蚕茧生熟不匀。随着科学技术发展和工业技术水平的提高,到20世纪20年代,日本发明了煮茧机,将蒸汽运用到煮茧中,大幅度提高了蚕茧煮熟均匀性,从而奠定了现代煮茧技术及煮茧设备基础,使缫丝生产从手工作坊转向工业化,产品质量、生产效率得到极大提高,原料茧消耗大幅降低。中国的煮茧设备经历了木制煮茧机、水泥煮茧机、圆盘煮茧机、不锈钢煮茧机、减压煮茧机发展历程,对缫丝生产的技术进步起到了极大推动作用。
1 煮茧的起源及煮茧方式的演变
据《中国丝绸史(通论)》考证表明[1],中国从新石器晚期就开始了缫丝生产,一直到农耕时代,没有专门的煮茧设备。古代时期,煮茧和缫丝混合在一起,煮茧器具极其简陋,先将蚕茧放在盛有水的铁锅内,锅下以薪燃之,使茧膨润软化,溶解丝胶,用手提拉抽出茧丝,卷于丝框以作绩丝、织绸之用。
周代还只能利用鲜茧缫丝,至秦、汉,采取阴摊等办法延缓化蛾,或日晒杀蛹。商、周时期,缫丝工艺已逐步完备。西汉时已经用沸水煮茧了,凭目测掌握煮茧水的温度,即以水面出现蟹眼大小的气泡为宜。在《礼记·祭仪》中对煮茧缫丝工艺有比较详细的记载:“及良日,夫人缫,三盆手,遂布于三官夫人世妇之吉者,使缫。”说明周代或周代以前,在煮茧工艺操作中为使蚕茧渗透均匀,采取多次浸渍。
进入隋唐五代后,煮茧、缫丝技术又有了新发展。唐代诗人李郢在《浙河馆·一作暮春山行田家歇马》中有“雨湿菰蒲斜日明,茅厨煮茧掉车声”诗句,这一期间使用手摇缫丝。自宋代起,使用了脚踏缫丝,脚踏缫丝车是在手摇缫丝车的基础上发展起来的,它的出现标志着古代手工缫丝机的新成就,生产效率得到提高。
元朝大统一的局面则促进了南北交流。北方缫丝采用“热釜”,南方采用“冷盆”。热釜是煮茧缫丝一个锅,冷盆的工具较多,主要包括盆、釜、灶等。其中的釜其实是用于煮茧的,盆就是缫丝盆,又称串盆,区别在于煮茧的水温较高,缫丝温度低。冷盆缫丝的最大特点是,煮茧与缫丝分开进行,这是中国古人在长期的实践中总结出来的一种缫制高质量生丝的重要技艺。此法缫出的丝比热釜者“有精神,又坚韧”,可防止煮茧太熟、丝胶脱净、丝纤维软弱无力。
明清时期,煮茧缫丝的技术承继宋元以来的发展,使用脚踏缫车进行缫丝。缫车的基本装置包括加热的火炉、烧水煮茧的热锅、集丝的竹针眼、导引丝缕的星丁头、勾挂丝缕的送丝竿、绕集丝缕的丝架,还有带动丝架绕转的脚踏板连杆。
2 煮茧机的诞生及日本煮茧机
2.1 千叶式煮茧机
日本明治维新以后,加快了工业革命进程,政府大力推进丝绸产业,于1904年发明立缫机,但至20世纪20年代才发展为多绪缫丝机。这个时期日本的缫丝设备达到世界最先进水平,缫丝的配套设备也获得了相应发展。20世纪20年代日本发明了千叶式和长工式两种煮茧机,两者结构及原理相似。千叶式煮茧机是日本千叶县生产的煮茧设备,该煮茧机为铁木结构,茧笼为鼠笼式,可以自动循环回转。该煮茧机分为水煮型和蒸汽型,由于蒸汽的能量更容易进入到蚕茧内层,提高了煮茧质量,因此逐步改为蒸汽型。自使用蒸汽型煮茧后,在煮茧机结构上进行了功能区分,即渗透、蒸煮、调整保护,奠定了现代煮茧设备及工艺基础。
千叶式煮茧机的技术特征是:茧笼采用循环传动,提高了工作效率;蒸汽煮茧代替了水煮茧,在渗透部吸水后的蚕茧,进入蒸煮室,接触到高温蒸汽,茧腔内气泡迅速受热膨胀而吐水。蒸汽热能使茧层及其空隙间所含有的水分温度迅速提高,使丝胶软化和膨化,对蚕茧内层煮熟起到了极大的作用,提高了内外层煮熟程度的均匀度。千叶式煮茧机也是现在使用的不锈钢长笼煮茧机的鼻祖。
煮茧机的出现使得煮、缫生产工序分开,对缫丝业来说具有里程碑式的意义。
2.2 V型煮茧机
为了能够进一步煮熟蚕茧内层、保护外层,提高煮茧质量,日本在20世纪70年代研制了V型煮茧机[2-3](图1),设备型号为H-2V型,主要特征是煮熟部具有加压装置,调整部为V形槽结构,并配合自动加茧、配茧、出茧、调温、调压、水温调节、水温预热、水中pH值调节及电气设备保护等装置;工艺调整比较完善,生产效率高。该机型一度成为日本的常用煮茧设备。
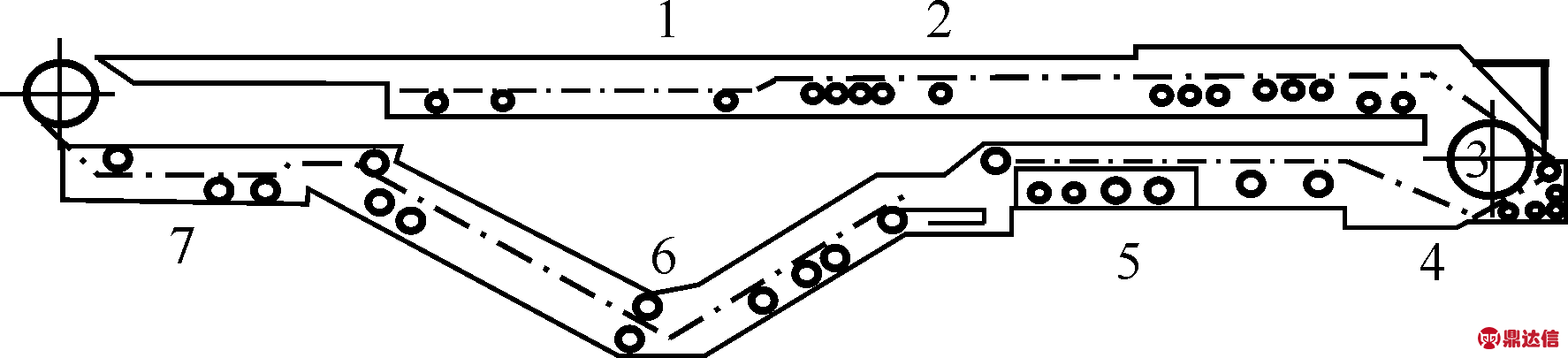
1-第一浸渍部,2-第二浸渍部,3-触蒸部,4-低温渗透部,5-煮熟部(蒸煮部),6-V型调整部,7-出口保护部
图1 日本H-2V型煮茧机全机示意
Fig.1 The schematic diagram of Japanese H-2V-type cocoon-cooking equipment
3 中国煮茧设备及技术发展历程
中国近代缫丝工业从引进西方和日本的近代技术与设备开始,其发展的基本轨迹是从座缫到立缫,再到自动缫。座缫又是从意大利式的大直缫发展到日本式的小
复摇。1925年,浙江一丝厂(浙丝一厂)首家引进千叶式煮茧机。1929年,江苏无锡的永泰丝厂向日本引进了一台千叶式煮茧机,由永泰丝厂机修车间安装使用[4]。这种设备能减少缫丝过程中的切断,使茧渗透均匀,吨丝茧耗约降低30 kg,大幅降低了成本,而且生丝的产量和质量都有了显著提高。永泰丝厂当时缫制的生丝,完全符合国际生丝市场要求,与日本的优质丝不相上下。这说明煮茧设备及工艺技术的进步会极大地影响到生丝质量、原料茧耗。国内纺机行业对日本煮茧机消化吸收和改进后,生产的煮茧设备逐渐在缫丝行业中大面积推广应用。
3.1 木制蒸汽循环煮茧机
1954年,中国上海生产了蒸煮循环式煮茧机。煮茧机壳体采用银杏木材,一台煮茧机约4.5立方木材[5],制作要求高。但密封性差,易漏气,使用时间为4~5年。该机有104笼,整机长度14 m左右,设总蒸汽阀门一个,用于蒸汽压力的调节,由人工控制,煮茧车速通过变速箱手动调节。由于煮茧机机壳采用木制,因此又习惯称为“木制煮茧机”(图2)。
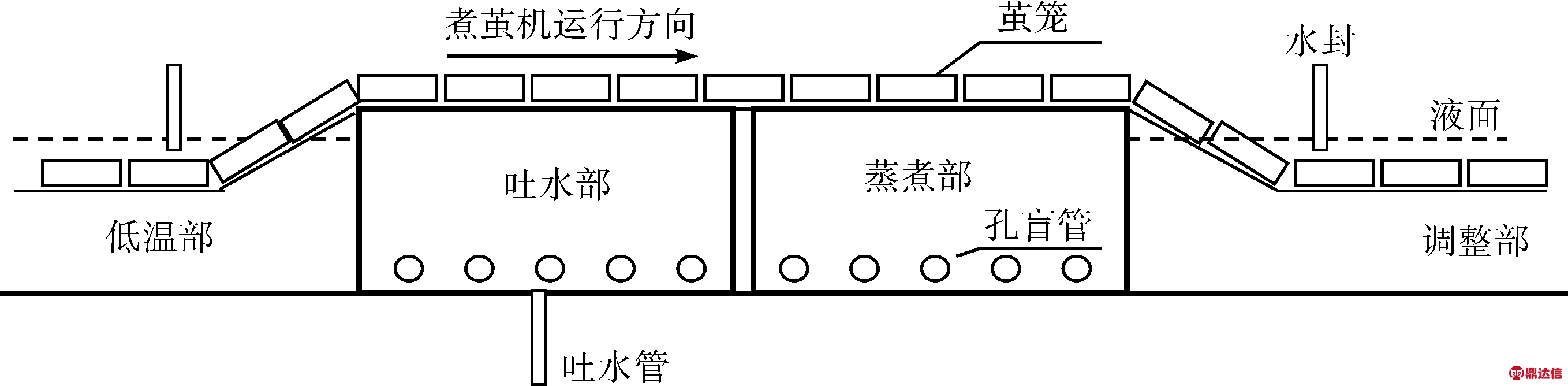
图2 木制蒸汽循环煮茧机蒸煮室结构示意
Fig.2 The schematic structure of cooking and steaming chamber in wooden steam cycle cocoon-cooking equipment
采用蒸汽煮茧后,在煮茧机设计结构上,分为渗透、蒸煮、调整保护等功能区域。渗透采用温差方法,在高温渗透部位,蒸汽通过反射管对蚕茧进行喷射,蒸汽进入到茧腔,排走空气。在低温渗透区,茧腔里的蒸汽遇冷急剧收缩,使水进入到茧腔,完成渗透作用。立缫一般要求蚕茧呈斜立状态,温差渗透能够满足立缫半沉半浮的生产要求。蒸煮室结构分为吐水和蒸煮两部分。吐水方式分为热汤吐水和蒸汽吐水,热汤吐水由于容易伤害蚕茧外层,因此茧耗大、万米吊糙多,逐步被淘汰。吐水、蒸煮分别安装温度计,通过温度来控制蒸汽压力。管道配置有孔管、盲管。在低温渗透和调整部分别有水封,便于蒸煮室密封。调整保护部的作用是进一步煮熟蚕茧,除去过敏性丝胶,逐步降温,保护外层,凝固丝胶。调整部的结构分为中水、动摇、静煮三个区段,温度依次降低。在每个区段上都有洒水管及溢水口,以利于温度的降低,调整部的温差对煮茧质量有极为密切的关系。
随着科学技术的发展,人们对蚕丝的丝胶、丝素进行了系统的科学研究。日本学者小松计一提出丝胶的分类[6],茧丝丝胶在茧层中呈层状分布,由外到内依次为丝胶Ⅰ、Ⅱ、Ⅲ、Ⅳ,水溶性逐渐减小,为研究和掌握茧丝丝胶分布及溶解程度建立了理论基础,也为煮茧质量的提高起到了积极作用。中国现有的制丝学教科书,基本是以木制蒸汽循环煮茧机、立缫缫丝方式为基础而形成的。各地根据蚕茧质量情况,在煮茧机内部结构上也有自行改造的,如在吐水段,增加上喷射管道,形成双面喷射蒸汽,使吐水更加充分。在长期的生产实践中,总结出“充分渗透、充分煮熟、充分冷却”的指导思想,制定了各区段工艺参数范围[7-8]、煮茧质量适煮检测指标及外观煮熟质量判断方法[7]。
3.2 水泥煮茧机
由于木材易腐烂,价格贵,制作成本高,水泥煮茧机从20世纪70年代中期取代了木质煮茧机。水泥煮茧机的水槽壳体用水泥预制板代替木材,煮茧机的机电结构、煮茧各段功能并没有发生改变,密封性差、漏水、漏气问题仍然没有得到根本性解决,只是壳体的使用寿命延长了。另外,墙板中预留的管道孔容易发生损伤,而且墙板上开孔难度大,很难进行局部技术革新。
3.3 圆盘煮茧机
中国于20世纪70年代研制开发出D211圆盘煮茧机[9](图3),与传统长笼式煮茧机相比,具有机械化程度较高,能改善劳动条件,降低劳动强度,节省铜材、木材等优点。外形呈圆筒形,整个圆周均匀排列15个煮茧桶,煮茧时,15个桶围绕主轴作圆周运动,自动完成装茧密封、进气、排气、进水、排水、出茧等过程。但由于当时的控制技术水平有限,设备故障率高,煮熟部调节余地小,调整部短,工艺稳定性不好,生丝的产、质、耗完成水平不如循环煮茧机,因此70年代中后期就没有再使用了。
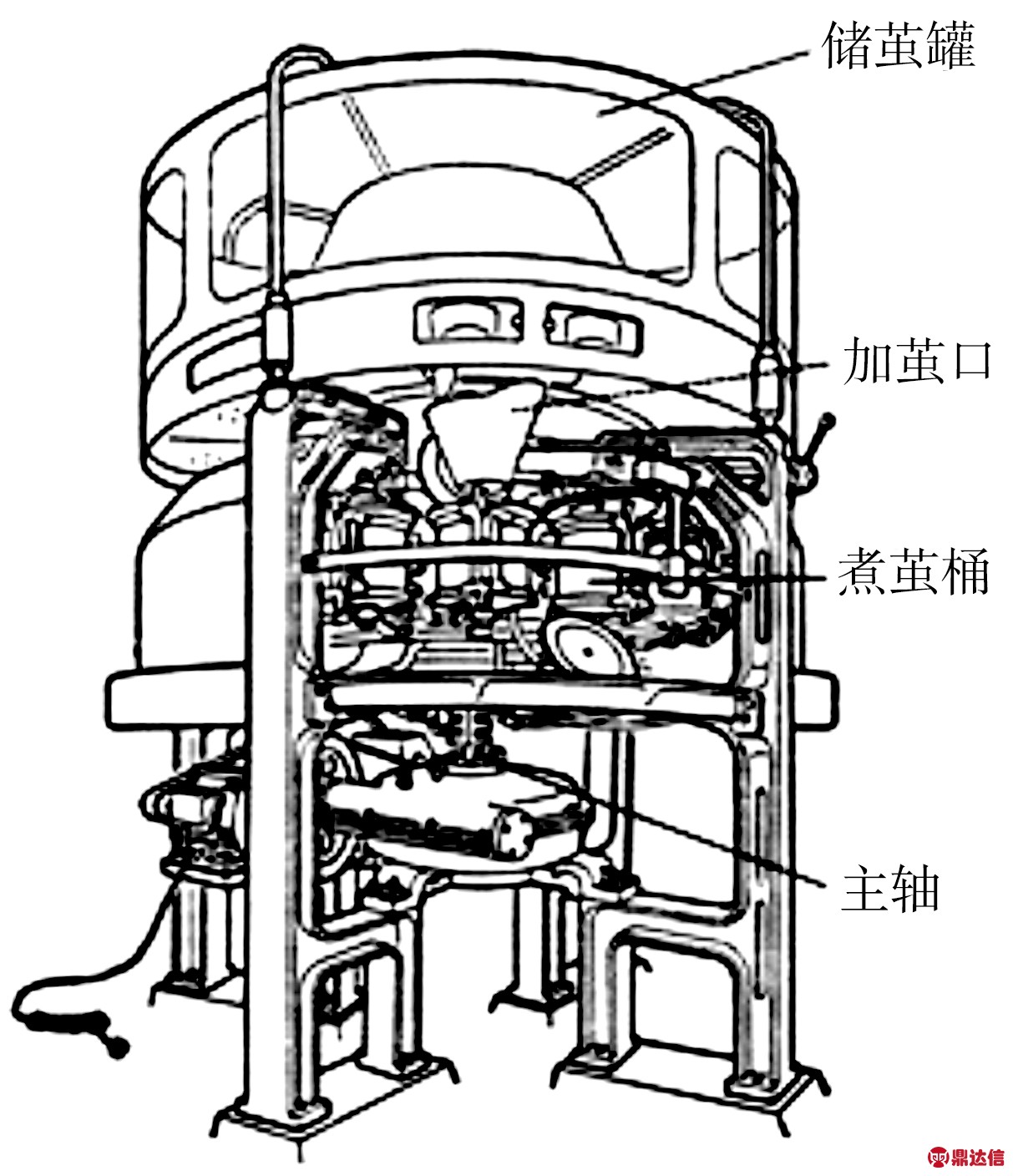
图3 圆盘煮茧机结构示意
Fig.3 The schematic structure of disc-type cocoon-cooking equipment
3.4 不锈钢煮茧机
20世纪80年代中期,由于中国不锈钢材料的生产和加工工艺的提高,不锈钢煮茧机开始全面取代水泥煮茧机(图4)。当时主要设备生产地区是江苏、浙江、四川,设备型号分别是:江苏的JD-104G高效节能不锈钢煮茧机、浙江的ZB104不锈钢煮茧机、四川的CD100A不锈钢煮茧机[10-12]。不锈钢煮茧机的主要优势:壳体采用不锈钢,密封性、保温性得到大幅度提高,煮茧质量提高,用汽减少;广泛使用了上槽,有利消耗降低[13-15];煮茧机轨道、茧笼使用不锈钢材料,增加了设备使用寿命;在蒸煮室设有观察窗,可以观察蚕茧吐水、蒸煮时的状况;使用了调速电机,方便煮茧车速的调整。CD100A不锈钢煮茧机对蒸汽总压力采用微机控制方法,这是煮茧设备首次采用自动控制技术,提高了煮茧的稳定性。
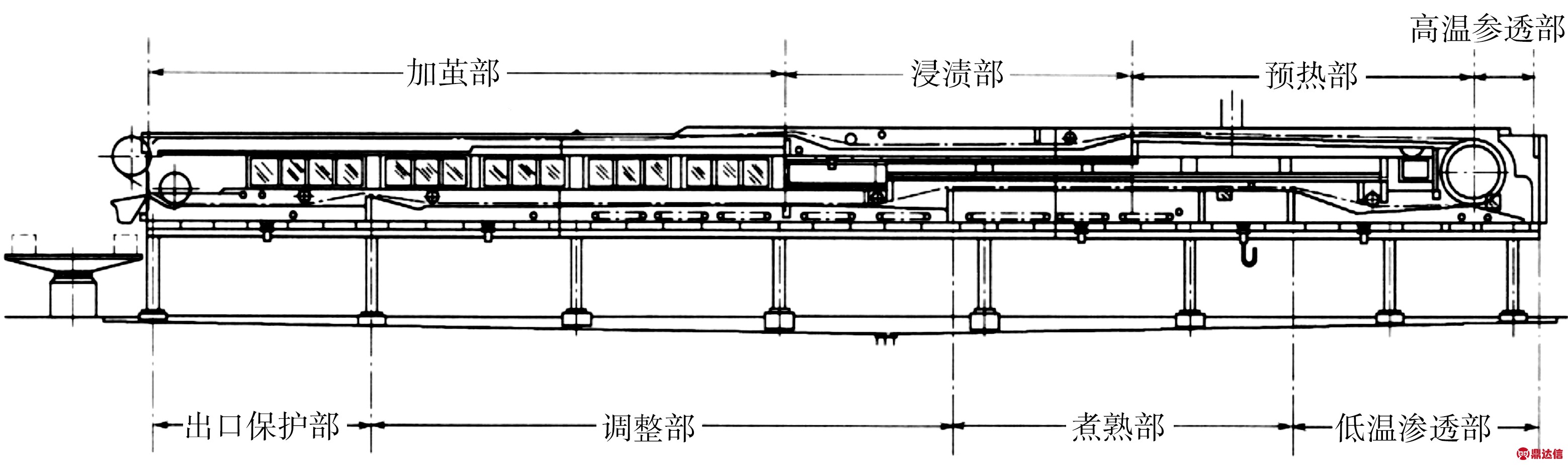
图4 不锈钢蒸汽循环煮茧机整机结构示意
Fig.4 The schematic structure of stainless steel steam cycle cocoon-cooking equipment
3.5 V型煮茧机
在20世纪80年代中期,山东和浙江从日本引进了H-2V型煮茧机,其优点是调整部的温差可以拉开。20世纪90年代中期,浙江、江苏、四川都有生产,其中FD301V型煮茧机列入国家“七五”重点攻关项目。由于中国与日本的蚕茧质量有一定差距,中国的蚕茧茧层薄、茧丝短、薄头茧多,通过V型煮茧机煮出的蚕茧万米吊糙偏高,同时,茧笼过桥多,运行负荷大,故障相对也多,因此该机型没有得到广泛使用。
进入21世纪,中国又先后研制出2种新型的V型煮茧机,分别是飞宇201V型煮茧机(图5)、新型双面蒸煮V型煮茧机[16-19]。这两种设备的研制,是基于中国自动缫得到普及,生丝等级主要由清洁、洁净定等,对提高生丝的清洁、洁净成绩起到一定的作用,控制水平也得到提高。飞宇201V采用机内温差渗透,新型双面蒸煮V型煮茧机取消了渗透结构,采用机外真空渗透。
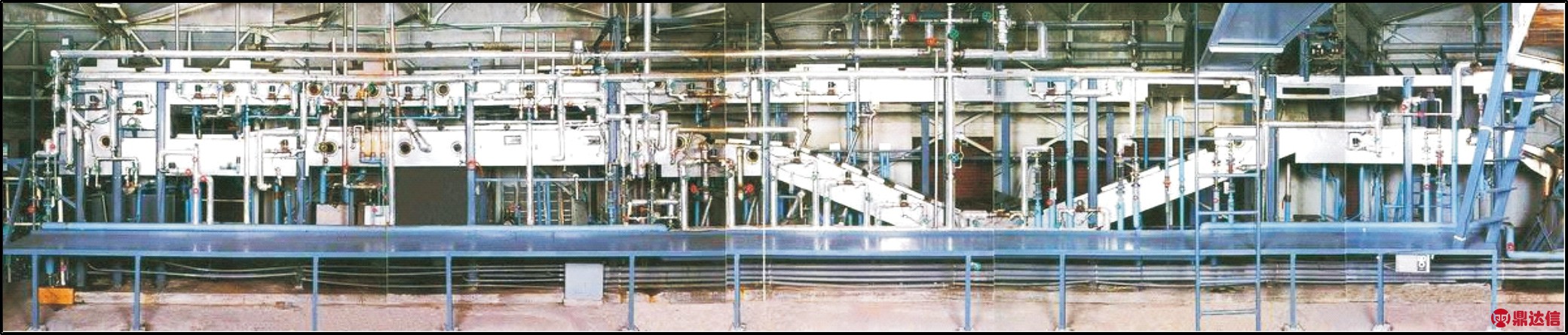
图5 飞宇201V型煮茧机实物
Fig.5 The photo of FEIYU 201V type cocoon-cooking equipment
3.6 真空渗透、真空渗透+长笼循环不锈钢煮茧机
真空渗透工艺是将容器及茧腔内的空气抽走,然后进入一定温度的水,继续抽真空到当地海拔最高真空度,停止真空,复压过程中,水进入到茧腔,完成渗透。蚕茧采用真空渗透比温差渗透更加均衡,瘪茧显著减少。真空渗透的设备由真空泵及管路系统、真空罐、水箱、接茧斗组成。自动缫丝机的普及带动了真空渗透设备推广,自动缫要求沉缫方法,真空渗透满足了这个要求。从真空泵类型来看,有滑油泵、射流泵、水环泵、罗茨泵。目前广泛使用的真空设备是水环泵+罗茨泵二级真空,主要优点是真空度高、瘪茧少、生产效率高、设备维护简单、维修成本低。当前有部分厂家不使用长笼煮茧机,原料茧只经过真空渗透后就直接缫丝。由于真空渗透只有渗透功能,没有煮熟功能,通过缫丝机车头进行补充煮熟,丝胶膨润很不充分、很不均匀,造成生丝强伸力、抱合、清洁、洁净等成绩差,只能生产低端生丝。
目前中国的大部分工厂采用真空渗透+长笼循环不锈钢煮茧机(图6),机外真空渗透,机内完成蒸煮、调整保护。
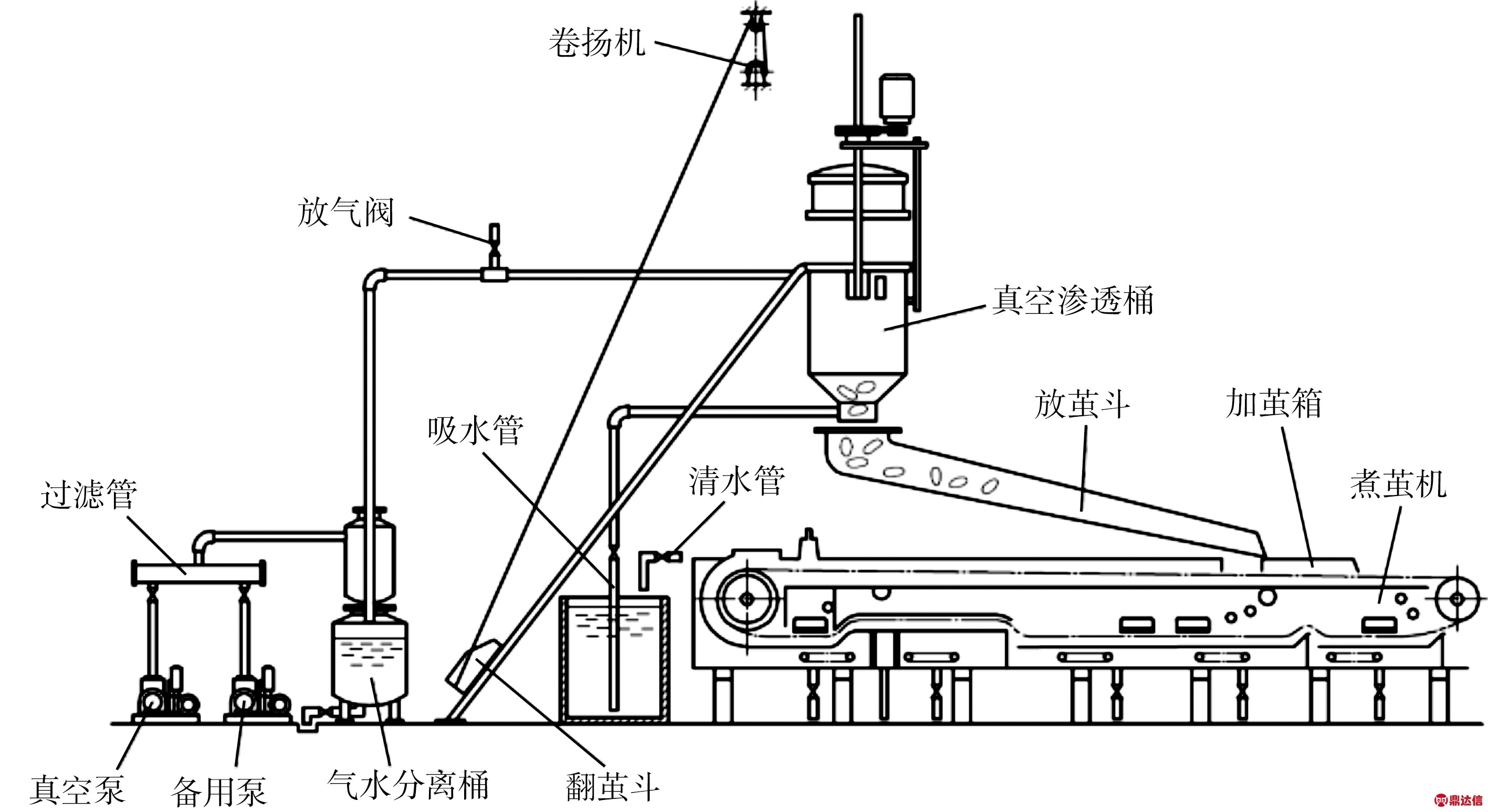
图6 机外真空渗透+长笼循环煮茧机结构示意
Fig.6 The schematic structure of long cage cycle cocoon-cooking equipment & independent vacuum infiltration equipment
1970年和1977年中国蚕茧和生丝生产量分别超过日本,成为世界上最大的蚕茧、蚕丝生产国,制丝生产的设备研制逐步转移到中国。从20世纪70年代起,中国高等院校、科研机构、生产企业对煮茧设备及工艺进行了深入研究。对水三次进出茧腔,如何让丝胶得到有效的膨润、溶解、控制等,徐帅等[20]对蚕茧吐水时,茧腔内外温度进行了研究;董雪等[21]对丝胶膨润性、溶解性进行了研究,为煮茧设备及工艺提高起到了积极作用。在这期间,对应用微波、红外线、超声波辅助煮茧[22-23]做了一些研究探索;在运用化学助剂方面,对质量差的蚕茧,辅助一些化学助剂[24-25];煮茧前触蒸处理[26]对改善洁净有一定作用,但使用工艺不当,会导致茧耗增大、万米吊糙增加[27]。
3.7 减压自动煮茧机
针对煮茧生产中存在的煮茧质量不稳定、煮茧机结构冗长、自动化程度低、适应性差,不能满足自动缫煮熟、煮匀的要求等问题,四川省丝绸科学研究院从20世纪90年代末期开始组织科研人员进行新型煮茧机的研制[28-31]。研究着重于提高煮茧质量,消除分体煮茧、提高煮茧装备一体化、自动化水平,满足生产高等级生丝质量要求,降低原料茧消耗,提高缫丝企业经济效益。经过对真空(减压)煮茧相关工艺及设备多年的研究,确立了在同一设备内完成“减压吸水(渗透)、减压+蒸汽状态下煮熟(蒸煮)、减压下吸水(调整保护)的煮茧工艺技术路线,完成了减压自动煮茧的机理研究及新型煮茧机的设计研制。
3.7.1 减压煮茧工艺技术的研究
由于蚕茧丝胶内层膨润、膨化比外层困难,因此煮茧工艺技术要解决的主要难题是如何实现蚕茧内层得到充分能量,打开丝胶胶着点,而之前的煮茧技术及设备是无法解决这一难题的。采用传统的设备,为了生产高等级生丝,通过增强蒸煮能量,在牺牲原料茧消耗情况下获得煮熟内层,来提高清洁、洁净成绩;蚕茧内层如果煮熟不充分,高等级生丝生产就无法实现。减压煮茧技术从以下几方面入手:一是在完成减压(真空)吸水后进行茧腔减压吐水,采用“减压+蒸汽”方式吐水(图7),吐水温度比长笼煮茧机低30 ℃以上,可以避免长笼煮茧机高温吐水对蚕茧外层带来的伤害,也可以减少蛹酸浸出;二是在减压状态下对茧层进行双向蒸汽蒸煮,在真空的导流下,确保蒸汽迅速扩散渗透到茧层的各个部位,提高了蚕茧内层煮熟质量;三是蒸煮后减压真空降温,在真空状态下,蚕茧的温度一致,进入到主罐内的水表面张力降低,水的沸点降低,产生汽化,水分子能够均匀地进入到茧层茧腔(图8),同时蚕茧在真空状态下有向四周拉的膨胀张力,吸水呈现高通透状态。通过适量热水、冷水的交换拉开了温差,起到保护丝胶的作用。减压技术应用到煮茧全过程。
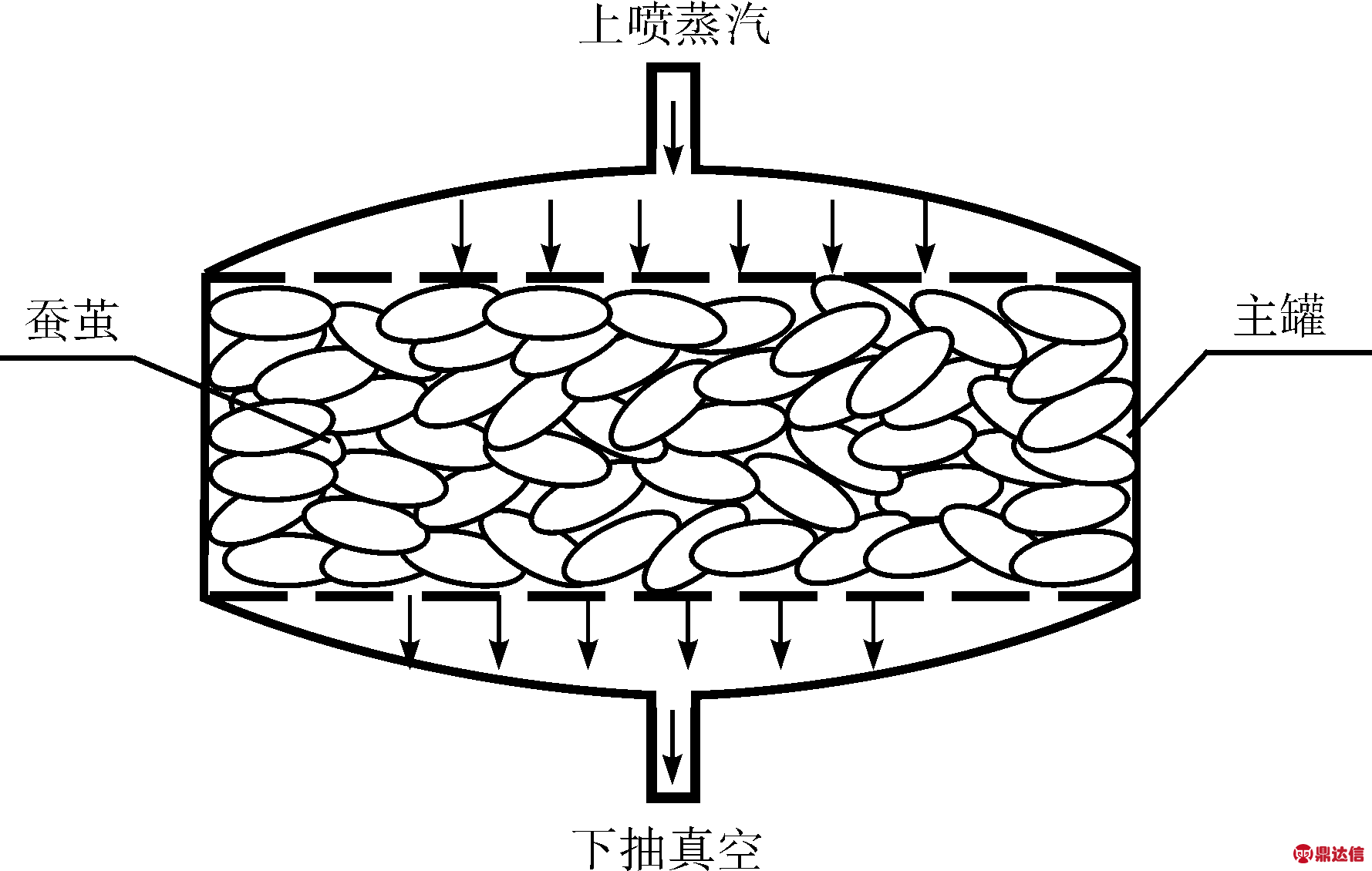
图7 减压吐水示意
Fig.7 The schematic diagram of decompressed guttation of cocoon-cooking equipment
3.7.2 减压煮茧设备的研究设计
减压自动煮茧机采用一体化的罐式主机结构,主要由工艺处理系统、水汽真空复合系统和自动控制系统组成。根据确立的工艺技术路线和各种工艺要求,通过计算机程序控制工艺处理系统和水汽真空复合系统等单元,进行不同组合来满足不同煮茧工艺的工况要求,适应不同茧质和不同区域的需求,实现在同台设备中完成真空渗透、茧腔减压吸水、吐水、蒸煮、调整保护等煮茧全过程。自动控制系统由人机界面、PLC控制器、执行机构及监测装置等组成。
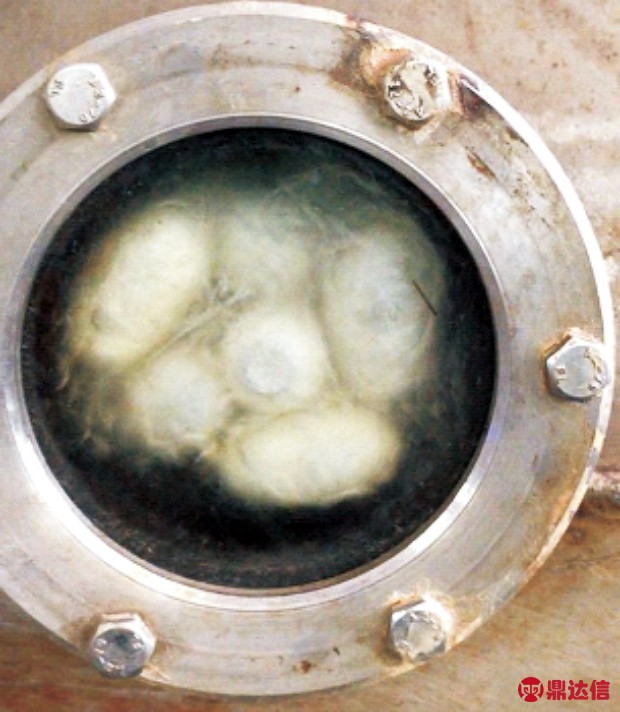
图8 减压煮茧机吐水状态
Fig.8 The state of cocoon guttation in the decompressed cocoon-cooking equipment
3.7.3 减压煮茧机实际生产效果
减压煮茧机与长笼煮茧机对比,生丝清洁、洁净成绩提高0.5分以上,原料茧消耗下降5~8 kg,万米吊糙降低0.2~0.5次,生产效率提高2%~5%,减少蒸汽用量60%,减少用水40%,减少用工30%以上,吨丝效益比传统设备煮茧提高0.8~1.5万元。因此,减压煮茧机在提高生丝质量、降低缫折、提高生产效率、减少水汽消耗、增强原料适应性、提高缫丝企业经济效益等方面,与传统工艺设备相比具有明显优势。
减压自动煮茧机由于在设备结构、工艺技术等方面的创新,以及计算机控制技术的应用,煮熟了蚕茧内层,保护了外层,显著降低了原料消耗,清洁、洁净成绩大幅提高,攻克了长期困扰高等级生丝生产的质量瓶颈,将煮茧设备和工艺技术提高到新的高度,目前已在全国推广(图9)。
图9 减压自动煮茧机装备工厂
Fig.9 The automatic decompressed cocoon-cooking equipment installed in the factory
4 煮茧设备及工艺发展展望
煮茧机诞生到目前已接近100年的历史。煮茧机的发明,推动了缫丝生产方式的变革、生丝品质的提升、原料茧消耗的降低和生产效率的提高。煮茧缫丝的历史证明,煮茧技术的每一次革命,都是由于新的煮茧设备产生带来的。
中国煮茧机的研发起步虽晚于日本,但发展较快,目前其煮茧设备工艺技术已处于世界领先地位,为中国国民经济建设及世界丝绸业的发展做出了重要贡献。
随着全球绿色、低碳发展理念的普及,茧丝绸产业转型升级出现了强劲势头。作为缫丝生产的重要环节,煮茧设备及工艺技术的不断进步和创新,为茧丝绸行业的更好更快发展奠定了基础。但是,随着社会的发展和科技的进步,不断涌现出的一些新技术、新材料也为中国煮茧机设备及工艺的发展提出了更新和更高要求。因此,要牢牢把握茧丝绸产业转型升级机遇,集中技术力量加强对茧丝丝胶的膨润溶解、煮茧的机理和新工艺的进一步研究,不断降低原料茧缫折及能耗,提高自动缫生产效率和生丝的清洁、洁净、抱合、强伸力指标,满足高速织机对生丝品质的需要。要继续研究自动化、智能化煮茧设备,进而实现无人化自动煮茧。运用大数据技术,建立煮茧工艺优选数据库,实现在线工艺检测、诊断、修正,远程工艺优选,满足现代煮茧缫丝生产需要,为茧丝绸产业发展提供支撑。