摘 要 针对超临界流体萃取过程中高压环境下的密封问题,设计了一种具有仿生凹坑特征的新型密封圈。将仿生学原理应用到橡胶圈密封技术中,通过软件对光滑与非光滑表面密封圈进行数值模拟,观察在不同压缩量、不同凹坑直径和间距时,密封圈的接触应力和Von-Mises等效应力变化情况。计算结果表明,当压缩率为12%时,光滑和非光滑密封圈产生的接触应力均达到了超临界萃取过程工作的介质压力8 MPa,其中凹坑直径为2.0 mm、凹坑间距为3.0 mm的模型具有最好的密封性能和耐磨性。
关键词 超临界流体萃取 仿生凹坑 橡胶密封圈 有限元分析
0 引言
超临界流体萃取技术具有节能、安全、高效等诸多优点,现如今在食品、香料、油脂萃取等行业得到了广泛的应用。超临界流体萃取过程在高压环境下进行,故需要选用合适的密封形式来保证装置的密封性。温皓白[1]设计了一套高压往复动密封设备进行试验,并通过ANSYS软件对O型圈密封过程进行模拟,验证了O型圈的密封可靠性。何广德等[2]论述了矩形密封圈的密封机理,并通过有限元分析技术,验证了矩形密封圈的密封可靠性。
仿生学理论对减小物体间的摩擦阻力、增加耐磨性和提高能源的利用率等方面具有重要作用。JIANG等[3]设计了一系列基于鸟翼的密封沟槽,利用有限差分法研究了仿生沟槽干气密封的静密封性能,结果表明在高速低压条件下,仿生团螺旋槽比普通螺旋槽具有更高的薄膜刚度和更低的泄漏率。GU等[4-6]为了解决气动灭火炮的发射过程中的密封问题,基于仿生学理论,建立了仿生凹坑密封圈模型,对其进行了模拟,发现了具有凹坑特征的密封圈对灭火炮的密封性能没有负面影响。赵建英[7]、许国玉等[8]建立了一种以三角形方式排布的仿生凹坑密封圈模型,并对其密封性能和减阻特性进行模拟,证明了仿生凹坑密封圈相对无凹坑光滑密封圈的减阻能力有很大提升。赵军[9]将动物表面信息抽象,建立了仿生非光滑表面模型,计算了多个速度下非光滑表面的减阻效果并对其机理进行了研究,结果表明,仿生非光滑表面具有显著的减阻效果。
本文以超临界流体萃取装置中的料仓密封圈为研究对象,以龙虱科昆虫凹坑型非光滑体表结构为仿生原型,建立具有仿生凹坑特征的密封圈模型,对其进行数值模拟,分析仿生凹坑对密封圈密封性能及耐磨性的影响。
1 料仓密封圈的仿真模型
图1所示为超临界流体萃取设备中一个独立料仓的结构示意图。
经简化,建立料仓密封圈仿真模型,由缸体、料仓壁及密封圈组成,如图2所示。根据仿生非光滑表面形貌,结合密封理论,采用半球形凹坑结构的橡胶密封圈。
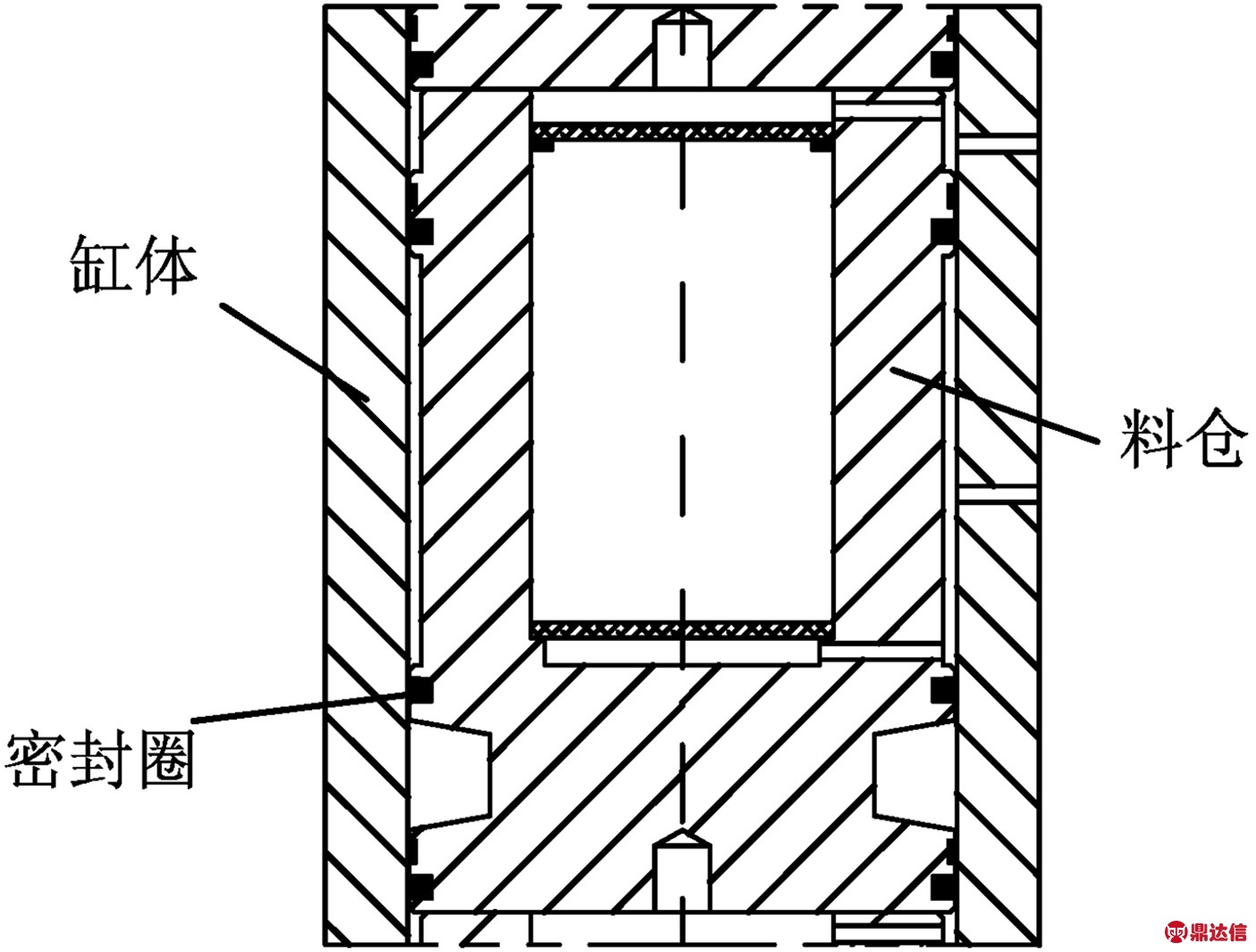
图1 料仓整体结构示意图
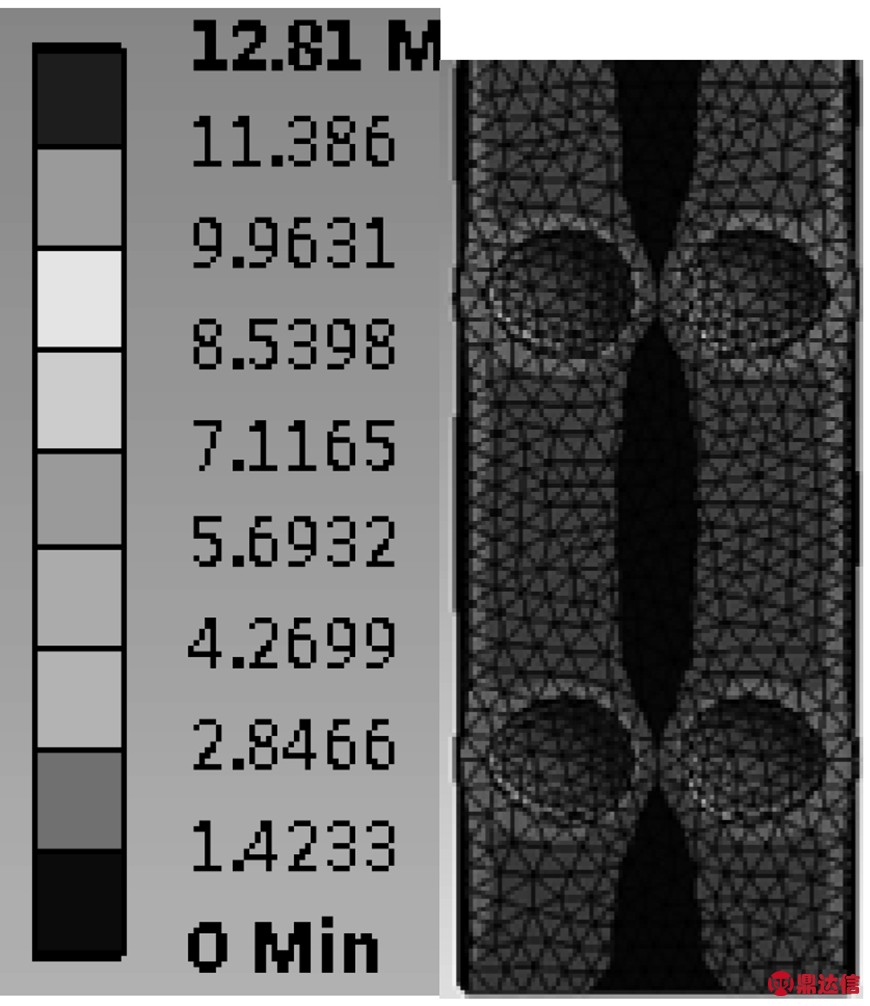
图2 料仓密封简化模型
1.1 模型参数
根据已知料仓结构参数,采用外径为250 mm,内径为237 mm,厚度为6.73 mm的矩形橡胶密封圈。仿生凹坑分布方式如图3所示,密封圈一周共有两排90个凹坑均匀分布,每个凹坑对应圆心角为4°,为计算方便同时不影响计算结果,本文截取8°为一个单元进行分析研究。凹坑直径参数分别为1.0mm,1.5 mm,2.0 mm,2.5 mm,凹坑间距参数分别为3 mm,3.3 mm,3.6 mm。
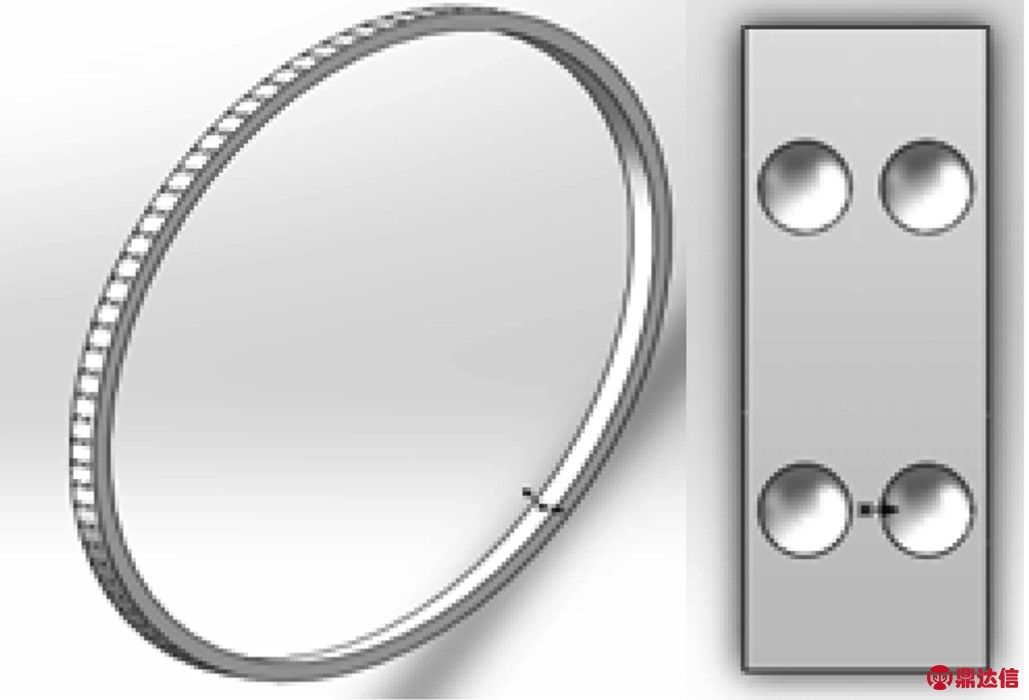
图3 仿生凹坑分布特征
1.2 建立有限元模型
如图4所示为料仓密封圈的有限元模型,为简化计算,采用轴对称模型,由于缸体和料仓壁相对密封圈的变形较小,可设置为刚体。
料仓密封圈材料本构模型选用Mooney-Rivlin模型[10],本文使用的C10、C01分别为2.35 MPa和0.58 MPa。材料的不可压缩参数D1取0,即仅发生弹性变形。
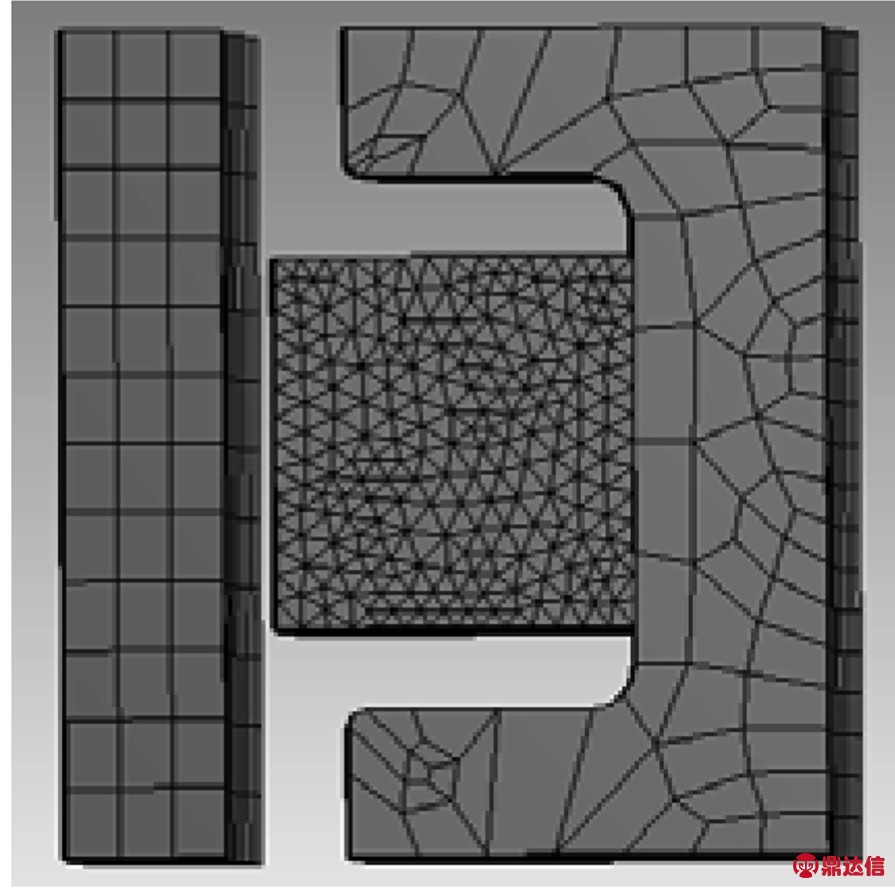
图4 矩形密封圈有限元模型
1.3 设置边界条件
为了确定密封圈的安装预压缩量,在密封圈安装状态下,料仓壁固定不动,对缸体施加向下的位移约束,压缩密封圈,其他方向位移为0。缸体向下的位移量为密封圈的压缩率,从0%运动至16%,取密封圈与缸体料仓壁间摩擦力为0.2。
2 密封性能研究方法
通过改变密封圈压缩率,观察仿生凹坑非光滑橡胶密封圈受压时产生的接触压力,是否能达到介质工作压力8 MPa,满足密封需要,以确定橡胶密封圈的安装压缩量。密封失效的准则为[11]:
(σx)max≥p
由于凹坑单元改变了原本密封圈的表面特征,减小了实际的接触面积。因此,通过改变凹坑直径和凹坑间距,研究凹坑直径和凹坑间距对密封性能的影响。
3 模拟结果分析
3.1 不同凹坑直径对密封圈性能的影响
对仿生凹坑非光滑密封圈的压缩过程进行数值模拟,得到不同压缩率下不同凹坑直径模型最大接触应力变化曲线,如图5所示。
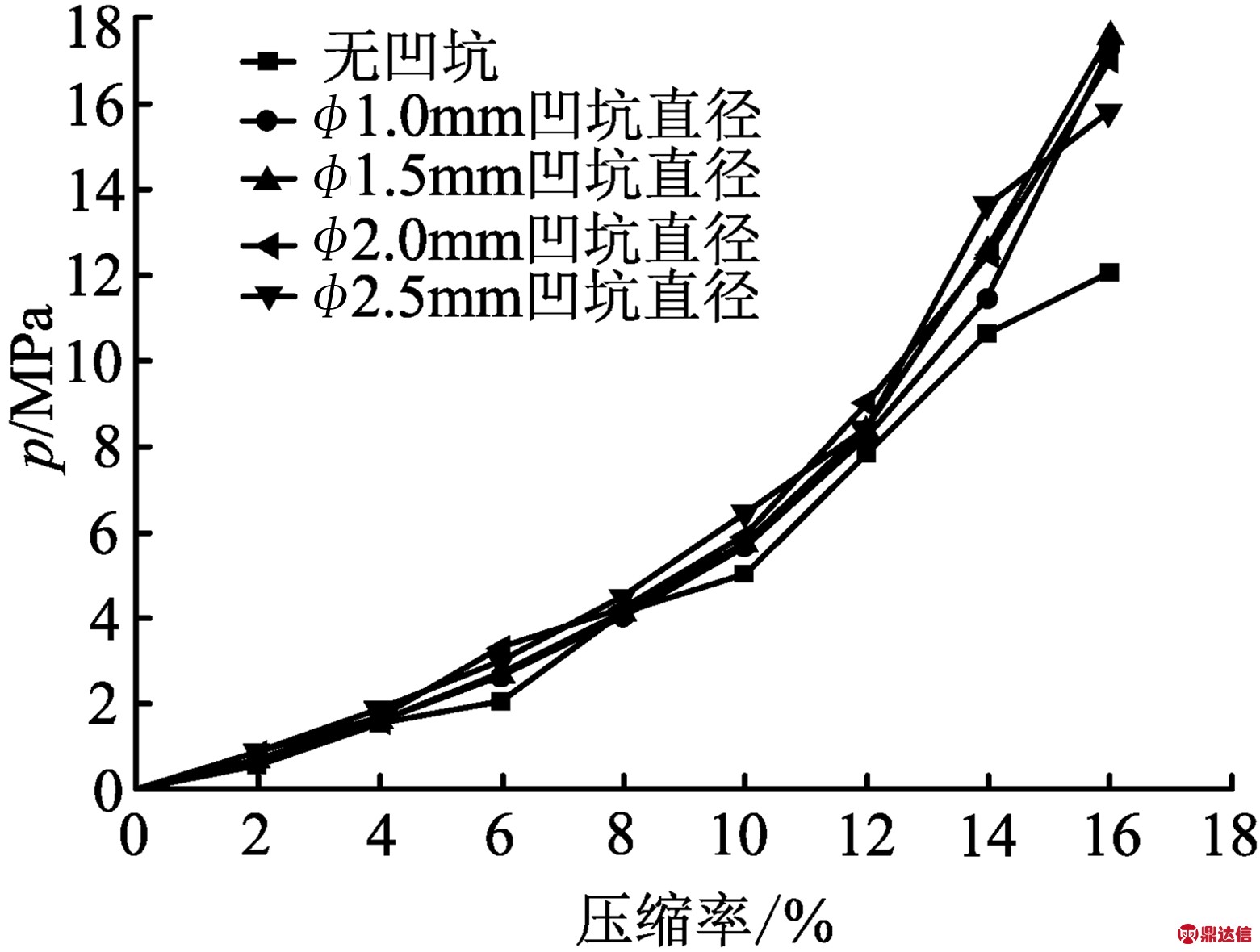
图5 不同凹坑直径模型最大接触应力
由图5可知,各模型在压缩率增大的同时,接触应力都在增大,当压缩率在0%到10%过程中增长较缓慢,呈线性趋势;12%到16%过程中增长较迅速,呈非线性趋势,使模型产生了极大的应力变化,橡胶密封圈正是考虑了橡胶的大变形和小变形规律,一般的密封问题都是在橡胶密封圈小变形范围内进行研究的[7]。在压缩率从0%到10%时,各模型均不能达到密封要求;在压缩率为12%时,各模型接触压力均大于工作介质的压力8 MPa,满足料仓工作的密封要求,且有凹坑模型接触应力比无凹坑模型更高,具有更好的密封性能,其中φ1.0 mm凹坑模型具有最高的接触压力,密封性能最好。
图6所示为不同压缩率下不同凹坑直径模型最大Von-Mises等效应力变化曲线,由图可知,随着压缩率的增大,各模型Von-Mises等效应力也会增大,Von-Mises等效应力值越大,表明密封圈越容易磨损,当各模型达到密封要求时,有凹坑模型的Von-Mises等效应力比无凹坑模型更大,表明有凹坑的密封圈耐磨性较差,有凹坑模型中φ2.0 mm凹坑模型Von-Mises等效应力最小,耐磨性最好。
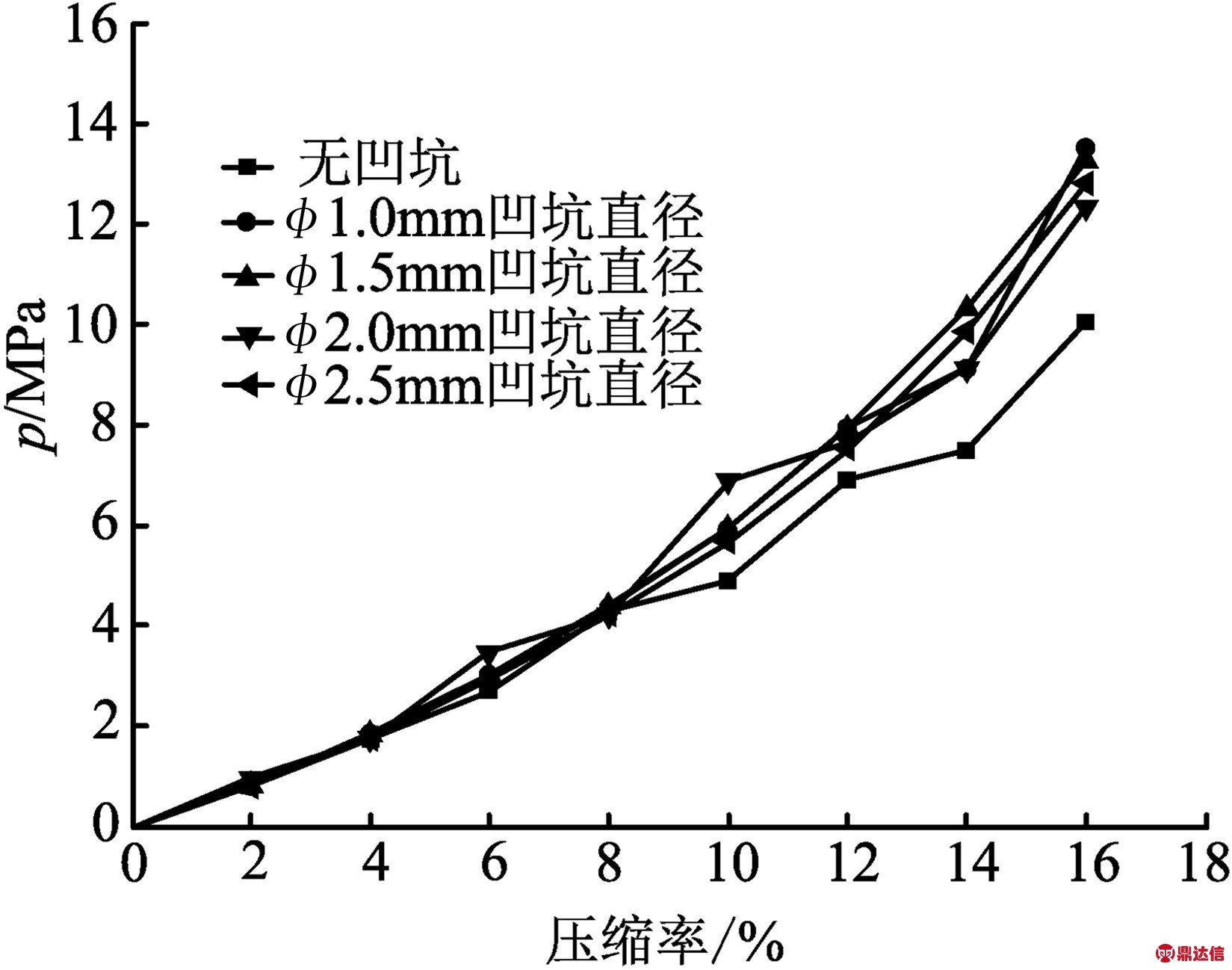
图6 不同凹坑直径模型最大Von-Mises等效应力
图7所示为压缩率为12%时不同凹坑直径模型Von-Mises等效应力分布情况,由图可知无凹坑模型的Von-Mises等效应力呈对称分布,中间部分最小,两侧最大,应力分布较为均匀。有凹坑模型的Von-Mises等效应力分布则发生了较大改变,在凹坑的边缘产生了一定的应力集中,不过对密封圈性能并没有太大影响。观察密封圈的变形情况,发现φ 2.5 mm凹坑模型边缘有较大变形,已有损坏的趋势,由此,凹坑直径的选择不宜过大。
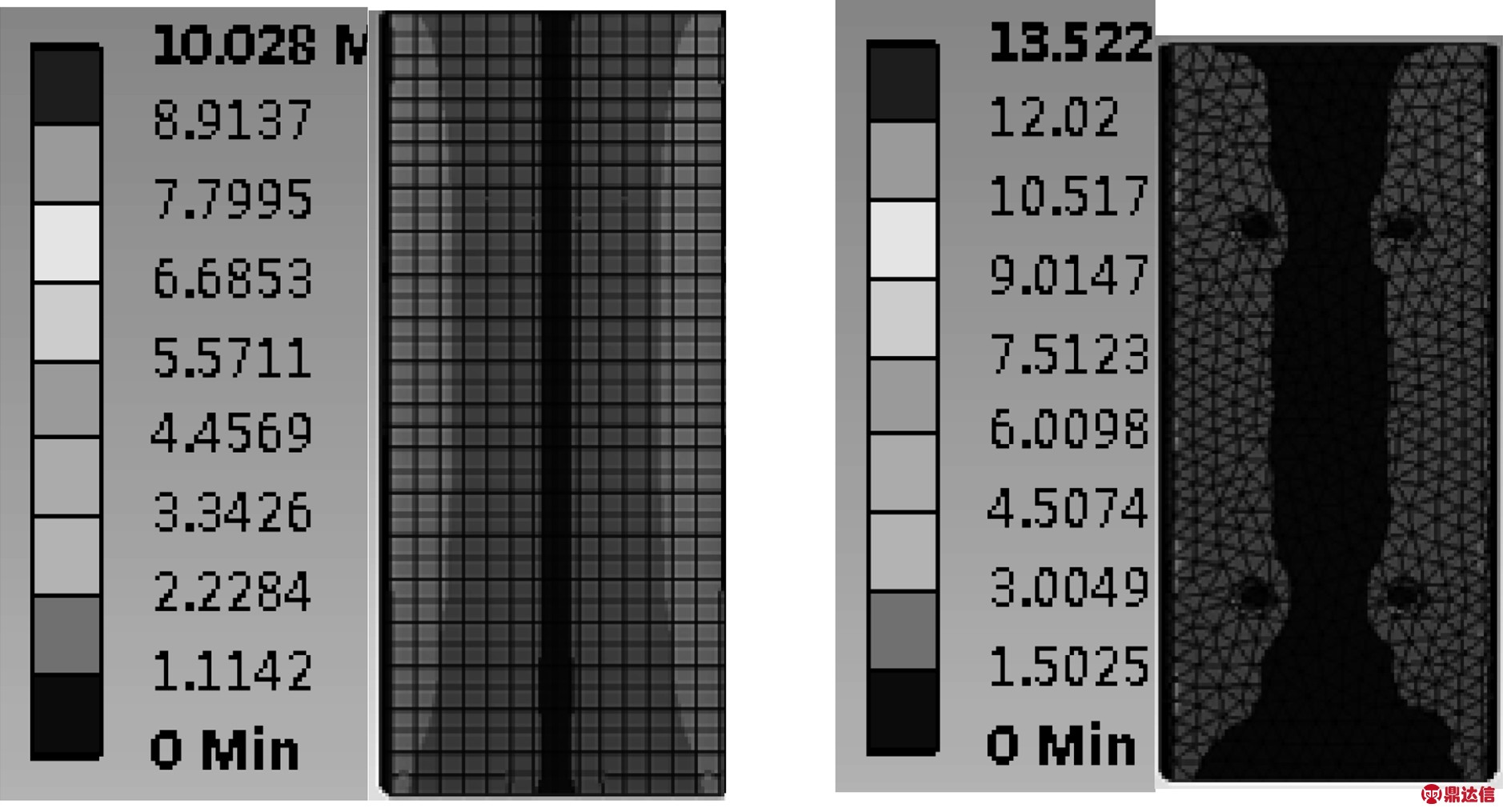
(a)无凹坑模型 (b)φ1.0 mm凹坑模型

(c)φ1.5 mm凹坑模型 (d)φ2.0 mm凹坑模型
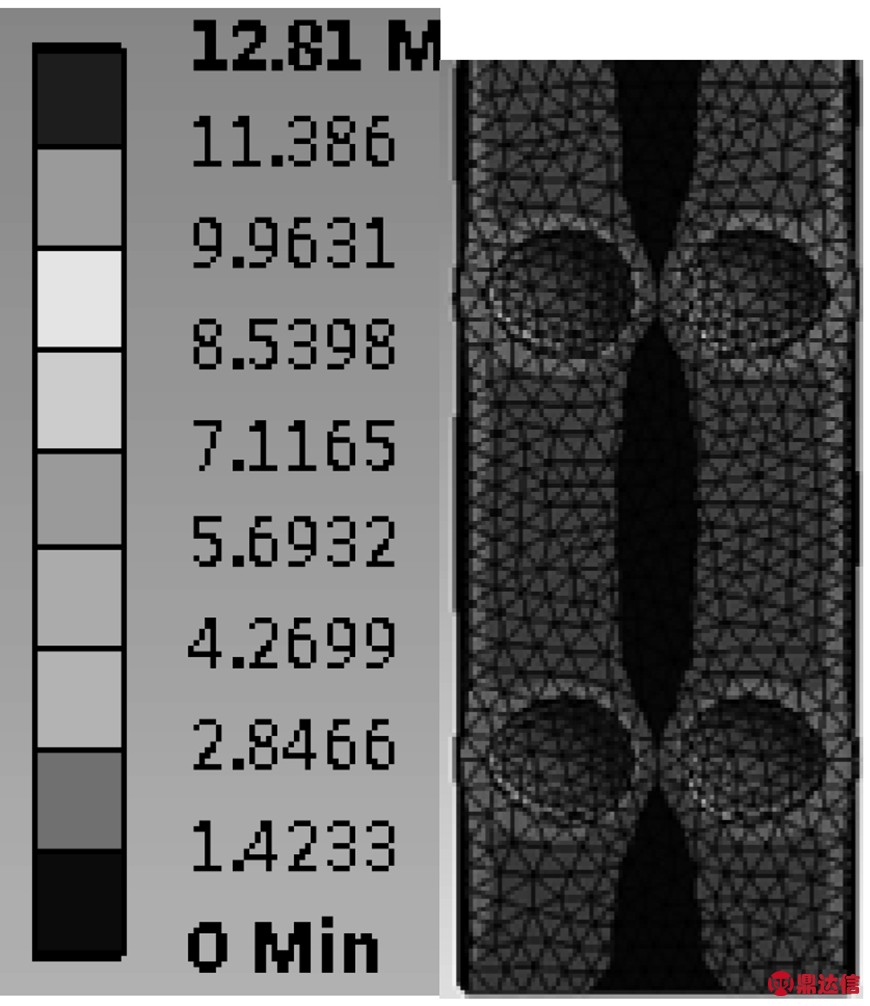
(e)φ2.5 mm凹坑模型
图7 压缩率12%时各模型Von-Mises等效应力分布
3.2 不同凹坑间距对密封圈性能的影响
对仿生凹坑非光滑密封圈进行压缩数值模拟,得到不同压缩率下,相同凹坑直径(φ2.0 mm)下不同凹坑间距模型最大接触应力变化曲线,如图8所示。
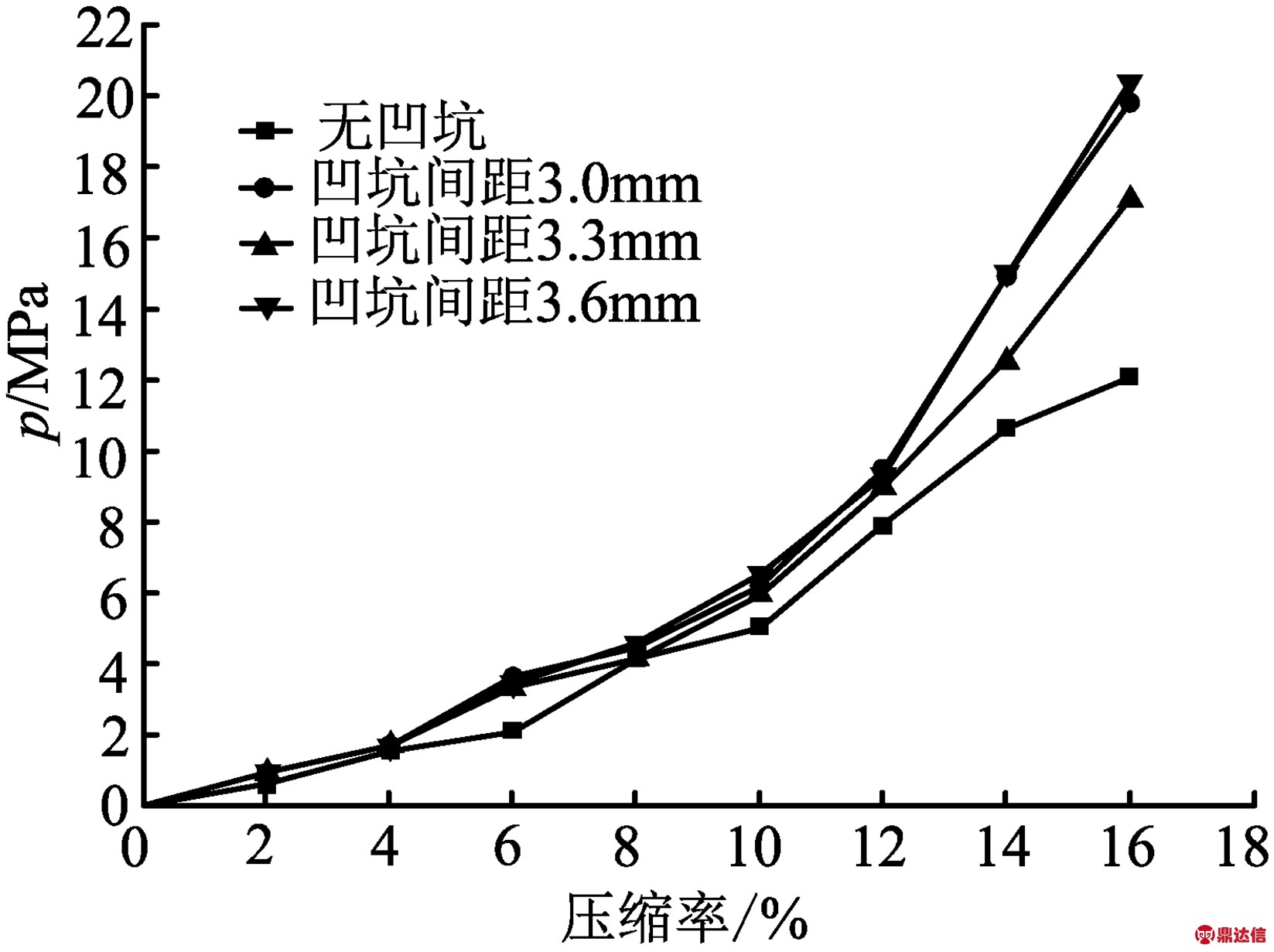
图8 不同凹坑间距模型最大接触压力
如图8所示,各模型随着压缩率增大,接触压力也在增大,当压缩率从0%到12%过程中增长呈线性趋势,12%到16%过程中增长呈非线性趋势;当压缩率为12%时,各模型接触压力均大于8 MPa,达到密封要求,其中凹坑间距为3.6 mm时接触压力最大,密封性能最好。
图9所示为不同压缩率下不同凹坑间距模型最大Von-Mises等效应力变化曲线,由图可知,随着压缩率的增大,各模型Von-Mises等效应力也在增大。当压缩率为16%时,凹坑间距3.0 mm模型具有最小的Von-Mises等效应力,耐磨性最好,比无凹坑模型耐磨性提高了18%。
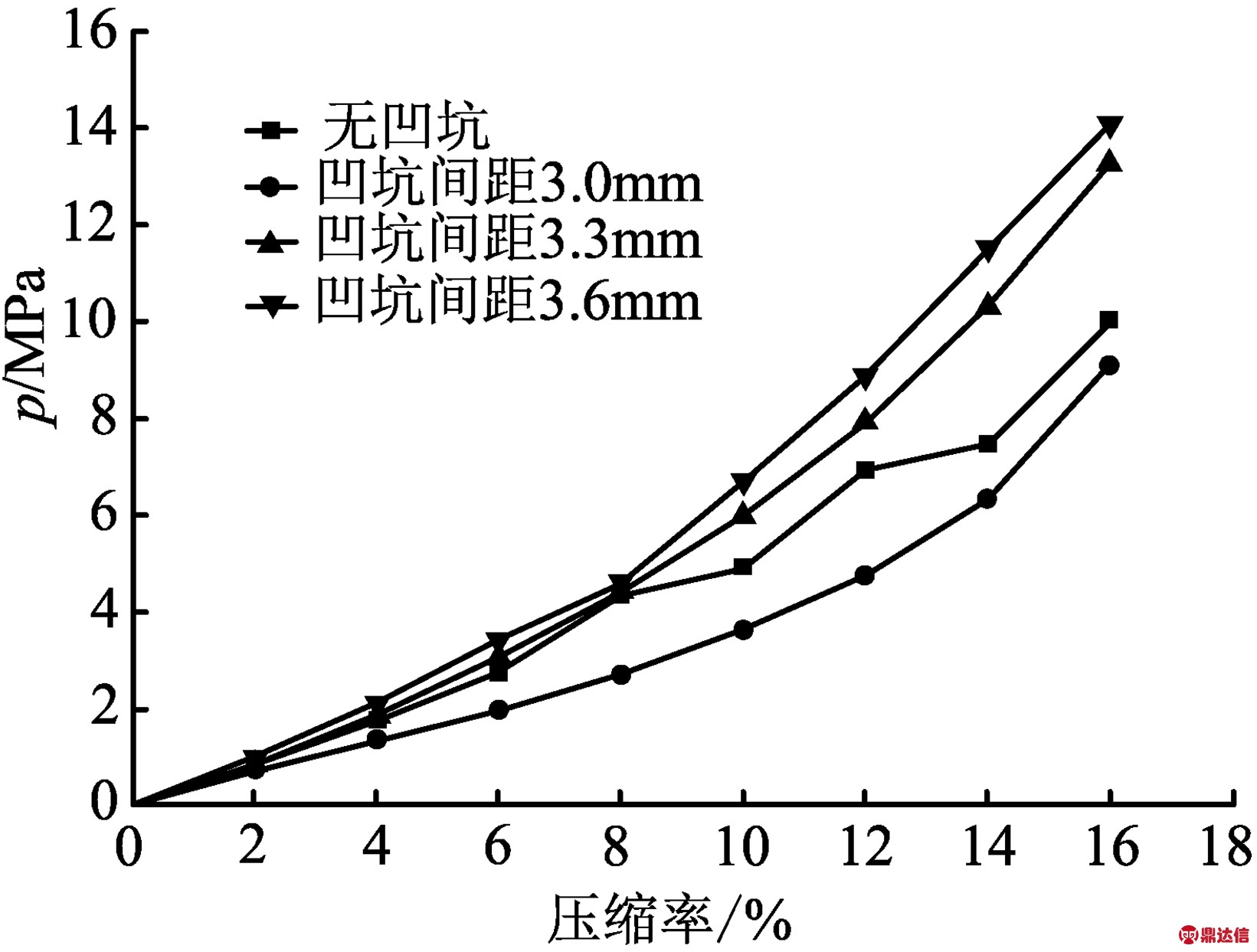
图9 不同凹坑间距模型最大Von-Mises等效应力
4 结论
(1)当密封圈模型压缩率从0%至12%时,接触压力和Von-Mises等效应力变化呈线性趋势,当压缩率由12%到16%时,变化呈非线性趋势;当压缩率为12%时,密封圈两侧的接触应力值大于8 MPa,各模型均满足密封要求。因此,仿生凹坑的存在对密封圈的密封性能没有负面影响。
(2)当压缩率为12%时,观察最大Von-Mises等效应力变化曲线,凹坑直径为2.0 mm,凹坑间距为3.0 mm的仿生凹坑非光滑表面密封圈模型具有最小的Von-Mises等效应力,耐磨性最好,比无凹坑模型耐磨性提高了18%。因此,合理的凹坑排布对密封圈的耐磨性有一定提高。