摘要:液压阀领域进行不同部件装配时会有端面密封的要求,大部分端面采用在平面密封槽内装配密封圈实现密封。目前,各行各业都在积极探索实现自动化装配的技术和装备,端面密封圈装配工艺在自动化方面有了一定的进步。本文通过对装配工艺的深入研究和创新,形成了全自动装配端面密封圈的的方法,并成功研制出一套运行稳定可靠的自动化装配装置。
关键词:端面密封;密封圈柔性装配;真空吸取;旋转式压入
1 前言
液压阀领域密封圈起到了至关重要的作用,运动部件之间的相对运动对密封有要求的情况下,绝大部分产品采用O型密封圈实现密封。装配后的密封圈能否可靠工作直接关系到产品质量和寿命。引起液压产品组件端面静密封泄漏的主要原因,是O型密封圈圆周上每点的压缩率不同所造成的,压缩率与密封槽的加工精度和密封圈的装配质量有关。国内研究主要集中在密封圈使用技术和过程的研究,目前,大部分O型密封圈的装配都是采用撑开O型密封圈的方式进行密封圈的拾取和装配,部分采用视觉配合机器人的方式进行装配。国内外针对不同装配方法对装配质量的影响做了大量的仿真分析,对平面压入的密封圈无切圈的风险。
本文对平面密封条件下O型密封圈的自动化装配工艺过程进行实验分析,为液压阀领域密封圈装配提供了技术借鉴。
2 组装工艺研究
传统装配液压阀平面槽内的密封圈方式为人工手动将密封圈放到平面槽上上部,使用工具压平,装配后的效果如图1所示。
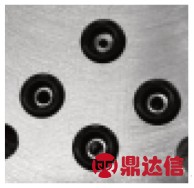
图1 人工装配后效果图
2.1 O型密封圈拾取工艺研究
为实现自动化装配,对装配工艺过程进行了深入研究。首先,对如何取密封圈做了多种备选方案分析,其中包括夹爪涨开式、真空吸取式、棒料套取式等。经过实验验证,真空吸取式机构是较简单可靠且易于释放密封圈的方式。
2.2 O型密封圈在平面槽内的装配工艺研究
传统装配工艺使用工装夹具压入时,由于人员手部的柔性和感知,可实现全方位压平密封圈。但自动化设备对于带感知的柔性机构要求较高。本文提出了一种采用旋转压入的方法,可实现密封圈在平面槽内的可靠装配。
装配过程中,对密封圈旋转压入的角度分别设置为270°、180°、90°、30°、10°及5°进行试验,除了5°条件下,其余结果均可满足安装需求。理论上旋转压入的度数越大,密封圈安装越到位。但旋转度数越高,节拍时间越长,因此,确定旋转压入的角度为10°。图2为旋转5°时密封圈的压入状态,图3为旋转10°时密封圈的压入状态,对比可知,图3装配合格。
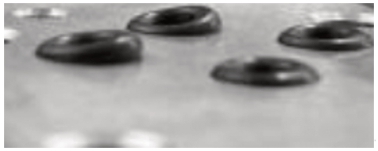
图2 旋转5°时密封圈压入状态
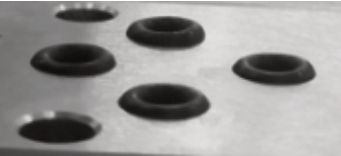
图3 旋转10°时密封圈压入状态
装配完成后,使用放大镜检查在装配过程中拾取工具是否对密封圈有损坏,如密封圈有破损、断裂等情况。在将密封圈取出后,对每个密封圈进行检查,检查图片如图4所示,右侧为未装配密封圈,左侧为装配后取出密封圈。经过对比整个装配过程,未对密封圈产生损伤。
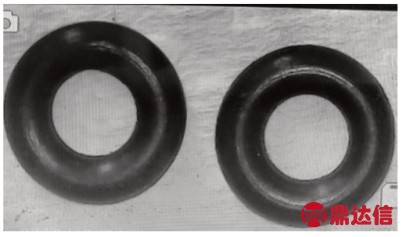
图4 装配后密封圈的检测
3 设计方案
3.1 O型密封圈上料分离机构设计
O型密封圈是软质材料,在物料自动分离时,需要无油的环境,否则,密封圈会黏连在一起,无法保证可靠分离成单个物料。本文采用常用的振动盘和直线振动器方式实现O型密封圈的有序排列输出,设计带有检测密封圈有无及防止密封圈推挤导致堆积的机构,将密封圈可靠地分离成单个物料。
由于密封圈比较光滑且质量较轻,分离时机构的切出速度不宜过快,更不宜产生较强冲击,否则,会导致密封圈飞离取料位置。根据惯性公式,气缸停止时的加速度计算如下:
ma≤mgf→a≤gf=10×0.9=9mm/s2
即,气缸停止时的加速度应小于9mm/s2,通过调节调速节流阀的开合程度控制气缸的切出速度。
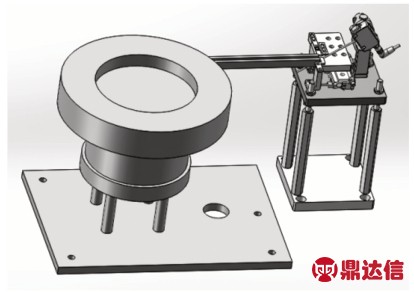
图5 O型密封圈上料分级机构示意图
3.2 O型密封圈的取料机构设计
本文采用真空吸取的方式拾取分离后的单个O型密封圈。结构如图6所示,机构设计有吸附密封圈中径处的小孔,与真空发生器通过接头和气管连接,侧面设计真空破坏气路(图7),防止装配后的密封圈与吸附机构发生黏连。
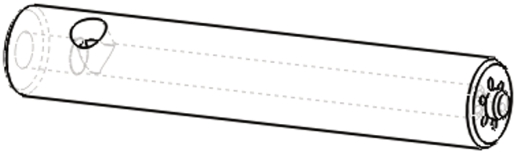
图6 真空吸附密封圈机构示意图
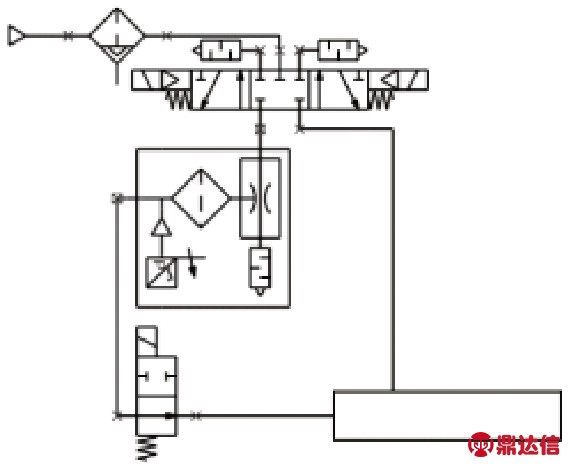
图7 真空破坏气路
根据实验结果,采用四轴机器人带动密封圈吸取机构到密封圈分离机构处吸取密封圈,见图8。四轴机器人带动密封圈吸取机构旋转下压密封圈,角度设置为10°(顺时针),见图9。
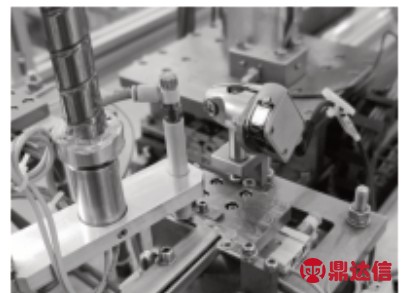
图8 真空吸取密封圈
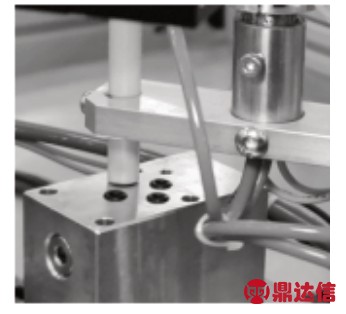
图9 旋转下压密封圈
4 结语
本文实现了O型密封圈自动上料及装配的技术,并研制出一套自动装配设备(图10),现场使用稳定可靠、装配质量稳定,减员增效效果显著,具有较好的社会效益和经济效益,为液压阀类端面密封领域提供了技术参考。
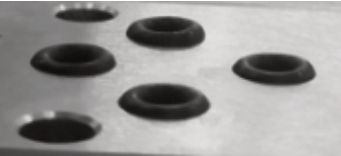