摘要:针对目前大尺寸高精度伺服机构蓄压器壳体和活塞存在的手工装配困难问题,对高精度尺寸测量、轴线自动调整、柔性夹具等方面进行了研究。设计了一种自动对中装配设备,利用双向测头测量了壳体内壁和活塞外壁尺寸,减小了测量误差,以带锁紧机构的球绞实现了被动柔性,使用闭环控制的精密X-Y滑台和柔性夹具共同实现了轴线的自动调整,利用研制的对中装配设备进行了实物装配测试。研究结果表明:该设备能实现大尺寸蓄压器壳体和活塞的高精度对中装配,可以有效地减小装配过程中的侧向受力从而避免了切损密封圈或壳体内壁划伤,并能实时记录装配过程数据。
关键词:活塞装配;精密对中;密封;蓄压器
0 引 言
我国航空航天等领域中的作动机构广泛使用了液压伺服机构,目前多数采用手工装配作业。随着产量的增加且对质量要求的提高,手工装配质量一致性差、过程数据缺乏且难以追述的缺点越发显得突出,特别是在尺寸大、重量重,且精度要求较高的对中装配如蓄压器壳体与活塞、油箱壳体与活塞、作动器壳体与活塞的装配过程中,由于零件重量重、配合间隙小,靠人力难以精确控制且装配过程中涉及到多道密封圈的压入,使得装配力大、手感差从而容易导致密封圈切损、壳体内壁划伤等问题。这些装配缺陷由于处于密封腔内部,难以直接观察检查,将对后续工作带来隐患。
针对精密配合且要求高可靠密封的壳体及活塞类高精度高可靠的装配需求[1],设计精密自动装配系统,可有效解决因人工装配导致的系列问题。
近年来,国内外学者对自动精密装配进行了大量的研究。一方面采用基于视觉的精密装配技术[2-4],主要解决尺寸测量、对中定位问题;另一方面采用基于柔顺力控制的装配技术[5-6],主要解决测量不精确时可自适应装配问题。但是对于蓄压器壳体及活塞的装配,由于壳体和活塞尺寸大间隙小,形状复杂且有油膜,采用视觉测量和柔顺力控制技术均有一定的困难和局限性。
针对液压类壳体及活塞的装配过程,国内外学者及机构进行了一定的研究。德国弗劳恩霍夫协会模具和成型技术研究所的SIEBEN C等人[7]对O型密封圈装配过程中的弹性摩擦力进行了研究,给出了单一O形密封圈装配力随位移的变化曲线;北京精密机电控制设备研究所的胡逸洲等[8]对伺服机构大尺寸组件自动装配技术进行了研究,采用机械测头进行了测量定位,采用主动柔顺控制夹具,并设计了完整的卧式装配设备。
本文中装配对象属于轴孔装配,配合间隙较小,带有多道密封圈,装配行程长且装配过程中不允许金属间发生磕碰。实现其自动装配,需要两个必要功能:(1)能够实现壳体和活塞的高精度对中;(2)实现活塞的压入动作,并在压入过程中能够监测装配力,并可根据装配力进行适当的调节。
针对精密对中装配工艺的核心问题“测量和对中装配”,本文将提出相应的解决方法并进行工艺实践。
1 壳体和活塞精密对中装配方法
需要装配的蓄压器壳体内孔直径为140 mm,壳体和活塞之间的间隙不大于0.05 mm,活塞两端各装有1个截面为X形的密封圈以及1个聚四氟乙烯挡圈,装配行程200 mm,要求测量精度为 0.005 mm、运动控制精度为0.01 mm。
蓄压器壳体及活塞装配原理如图1所示。

图1 蓄压器壳体及活塞装配原理
图1中,装置下方附有X-Y滑台(图中未展示),用于调整活塞水平方向的位置以对准蓄压器壳体。
装配时首先通过装配系统的机械工装保证壳体和活塞轴线基本平行,具体步骤如下:
步骤1。固定好蓄压器壳体后,通过微距测量装置测量壳体孔口位置,以此为装配基准;
步骤2。测量活塞上部的位置,通过X-Y滑台调节活塞水平位置,将此两者位置偏差调节到要求的范围内,则可进行活塞压入动作,同时用力传感器监测压入力,如果压入力出现不均衡,继续调节活塞的水平位置消除此不均衡,直到将活塞的上密封圈压入壳体中;
步骤3。在活塞的上密封圈压入蓄压器壳体后,松开活塞下部的球铰,使活塞有全角摆动的自由度,此时由于活塞上部密封圈已经进入壳体中,该截面处壳体和活塞的中心已经自动对准,这样此处壳体和活塞密封圈处截面可以看成是铰接;
步骤4。继续压入活塞,活塞轴线和壳体轴线会因形位公差存在一定的不同轴,但是上部密封圈处一定是对中的,此时下部球铰松开,会产生微小的被动摆动,通过测量装置实时测量马上要进入壳体中活塞处的位置,如果活塞和壳体不同轴较大的话,调节活塞水平位置,使活塞对准壳体孔口,确保测量装置测量壳体基准测点的位置靠近测量活塞测点的位置,减少因测头运动和不同轴带来的误差,保证了测量的精度;
步骤5。当活塞压入到第2道密封圈,进入壳体边缘时,松开X-Y滑台,使活塞可以沿水平向有个很小的自由活动量,继续推入活塞,活塞将自动移动以补偿可能存在的微小偏差,继续压入活塞直到规定位置,完成活塞压入过程。
2 精密对中装配的关键问题解决
2.1 高精度对中测量
为实现蓄压器壳体和活塞的对中测量,本文研制了一套对中测量系统,其中主要包括了一种微距测量装置,并提出了一种相对测量方法。
对中测量系统主要由Z向(蓄压器壳体轴向)移动的“测量升降平台”以及平台上的4套测量装置构成,4套测量装置沿壳体周向呈90°均匀分布。
测量系统结构如图2所示。
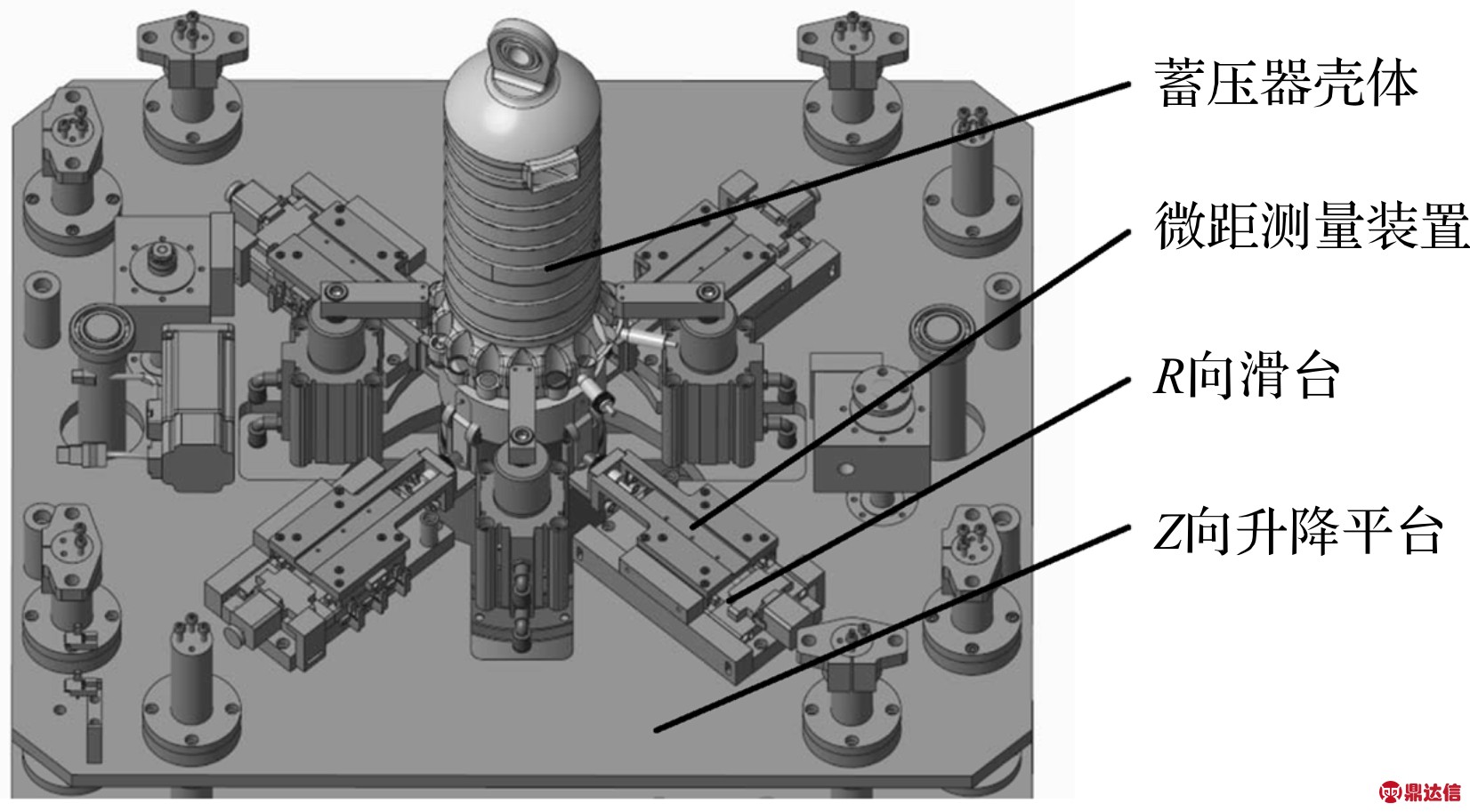
图2 测量系统结构
每一套测量装置由1个微距测量装置和1个可测距离的R向(蓄压器壳体径向)滑台组成。测量装置工作时由R向滑台上的光栅尺测出大位移距离,由微距测量装置上的电涡流传感器测量细小位移量。
由于测量装置既需要测量蓄压器壳体的内径,也需要测量活塞的外径,为减小误差,希望这两个尺寸使用同一个传感器进行测量,为此本文采用了双侧红宝石测头,并利用杠杆机构将微位移量传递给电涡流传感器以供测量。
测量时,驱动Z向测量升降台和R向滑台,将微距测量装置向上和向内运动,升高到蓄压器壳体下沿内部,再向外运动,可以测量得到蓄压器壳体下沿附近4个测点位置。驱动R、Z动作机构,将4个微距测量装置向下,向外运动待用,然后升起活塞到壳体下沿附近,但尚未进入壳体,此时将4个微距测量装置向内运动,测出活塞4个测点的位置。
通过和蓄压器壳体4个测点的位置比较,可以得到活塞和壳体中心点偏差。然后控制X-Y滑台向偏差减小方向移动,再重新测量活塞外沿,获取新的偏差,直到偏差进入允许范围。
这种以蓄压器壳体内壁为基准的相对测量方法,其壳体和活塞位置是否对正的测量误差只和测头位置测量、测头两个测点长度、微距测量装置的精度有关,而与其他基本无关。测头位置采用光栅尺测量,测量精度可以达到±1 μm。测头两个测点长度预先用千分尺测量,测量精度可以达到±1 μm。电涡流位移传感器分辨率可达0.25 μm,且重复度较高,经2次曲线标定后,微距测量装置的整体精度可以达到±2 μm,所以对中测量的综合测量精度可以满足0.005 mm的要求。
2.2 对中装配的轴线调整
在活塞的上密封圈进入蓄压器壳体后,活塞在蓄压器壳体内可以视作一个球铰。由于压入工装和蓄压器壳体的中轴线存在微小的偏移和夹角,活塞在蓄压器壳体内亦存在微小的偏角,这会导致活塞的压入摩擦力偏大且极易引起活塞和蓄压器壳体硬接触导致壳体内壁划伤。为此,本文考虑在第1个密封圈进入壳体后,在压入工装内引入一个球铰,并通过X-Y滑台的调整以补偿活塞和蓄压器壳体中轴线的偏差。
当即将压入第2个密封圈时,本文对活塞位置进行再次测量,由伺服机构对X-Y滑台进行调整,以保证压入的顺利性。当密封圈全部压入后,活塞已能够实现在蓄压器壳体内的自动定位,此时的X-Y滑台将切换为自由状态,不再受伺服电机驱动,自由状态的滑台将自动补偿偏移量,实现完全对中,保证最后压入的顺利性。
轴线调节装置主要由球铰及球铰锁定机构和X-Y滑台组成。当球铰锁定机构将球铰锁定时,上面的活塞没有摆动的自由度。当锁定机构将球铰松开时,活塞可以被动沿铰点进行全角摆动。X-Y滑台可以驱动连接在夹具上的活塞沿X-Y向运动,滑台上也具有一个锁紧装置,松开锁紧装置可以使夹具沿X-Y向有一个微小的活动量。
装置最下方为一组3个120°均布的力传感器,可以测量装配过程中的装配力及偏置力矩。如果装配力不平衡或超出设定范围,说明未对中,则需要进一步调整活塞位置以保证装配质量。
3 工艺验证及结果分析
3.1 精密对中装置实验
根据前述的测量和对中方法,本文研制的精密对中装配工艺设备如图3所示。

图3 精密对中装配工艺设备
该工艺装备满足测量精度0.005 mm、运动控制精度0.01 mm、行程200 mm的要求。
3.2 精密对中装配测试数据及分析
本文利用图3所示的设备,进行蓄压器壳体和活塞的对中装配试验。
分两次控制,并测量蓄压器壳体和活塞经调整后的间隙,如表1所示。
表1 蓄压器壳体和活塞经调整后的间隙
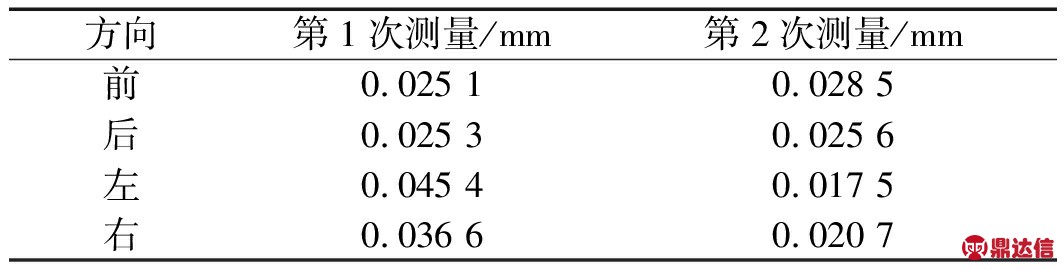
在两种间隙情况下压入活塞。
第1次测量未精密对中时的装配力和活塞位置曲线如图4所示。

图4 未精密对中时的装配力和活塞位置曲线
第2次测量已精密对中的装配力和活塞位置曲线如图5所示。
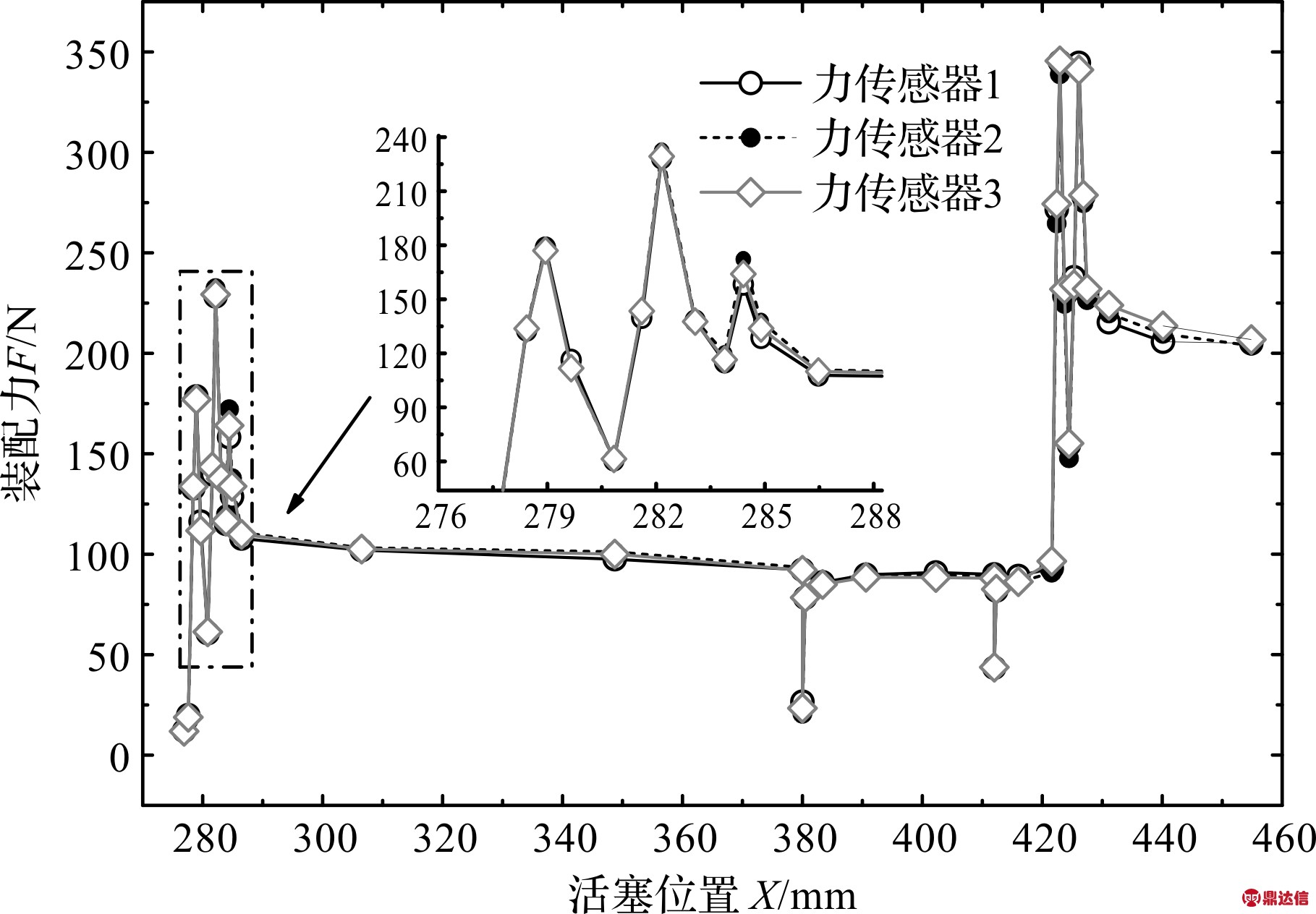
图5 已精密对中时的装配力和活塞位置曲线
从图(4,5)可以看出:装配时如果没有精密对中,活塞和蓄压器壳体在各个方向上的间隙差距较大,将导致密封圈在各方向上的挤压变形程度不一致,使得各向装配力会产生较大差距。显然,这种情况下装配对密封圈是不利的。此时,需要调整活塞位置使得各向间隙相当来减小装配力,确保装配质量。
装配时,有两个装配力明显增大的阶段,这两个阶段恰好是第1个和第2个密封圈进入蓄压器壳体的时候。每道密封圈进入蓄压器壳体时的装配力,连续出现3个增大峰,这是由活塞上的X型圈和挡圈引起的[9-11]。
活塞上的X型圈和挡圈形式和位置如图6所示。
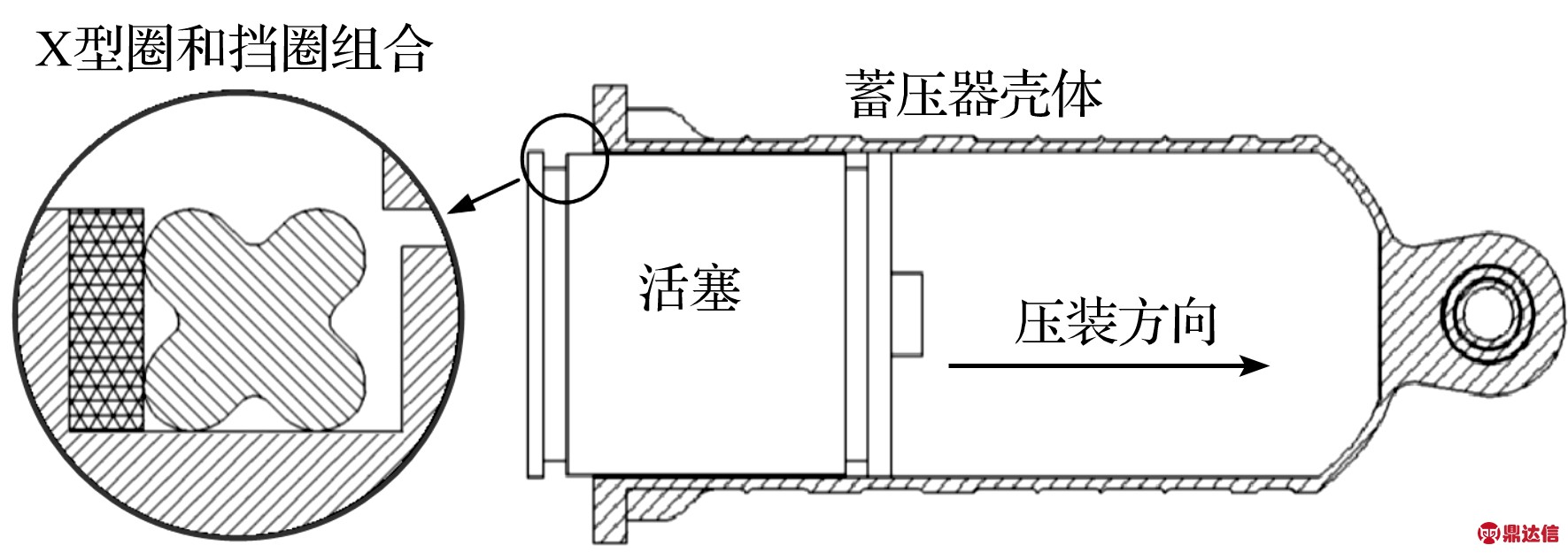
图6 X型圈和挡圈
图6中,当X密封圈的两个凸起和挡圈依次进入蓄压器壳体时,由于挤压变形,产生较大的摩擦力,这样就出现了3个力增大峰。
4 结束语
针对液压伺服机构中大尺寸蓄压器壳体和活塞的高精密对中装配的问题,本文采用同一传感器测量内孔和外径、利用光栅尺和涡流传感器组合等方法,解决了精密测量问题,以高精度X-Y滑台结合被动柔性夹具解决了装配过程中轴线调整问题。
本文通过研制的工艺设备对蓄压器壳体和活塞进行了精密对中装配试验,结果表明:该试验可以达到0.005 mm的测量精度,以及0.01 mm的装配运动控制精度,满足高精度装配的需求,且能实时监控装配力大小,便于对装配质量进行预测。