摘 要: 通过单次压痕试验与有限元模拟相结合的方法,结合反向分析方法与模拟退火粒子群算法,从获得的载荷-深度曲线加载部分提取材料的塑性参数,基于Ludwig硬化模型预测了不同金属材料的强度,并与单轴拉伸试验结果进行对比。结果表明:模拟得到的载荷-深度曲线与试验得到的几乎重合,二者的相对误差小于0.5%,说明模拟退火粒子群算法可有效地从压痕载荷-深度曲线中提取出金属材料的塑性参数;基于Ludwig硬化模型,利用反向分析方法从压痕载荷-深度曲线中提取的真应力-真塑性应变曲线不是唯一的,但从真应力-真塑性应变曲线计算得到的强度具有明显的收敛趋势;采用压痕试验得到不同金属材料的强度均接近于由拉伸试验得到的,屈服强度与抗拉强度的最大相对误差分别为5.9%,4.3%,说明采用压痕试验法可以准确地评价金属材料的强度。
关键词: 压痕试验法;反向分析法;金属材料;屈服强度;抗拉强度
0 引 言
强度是材料的基础力学性能,该性能对压力容器的设计及结构完整性的评估至关重要[1]。强度通常是由常规拉伸试验获得的,在测试过程中需要制备标准的拉伸试样,但是在试样较小或者无法取样的情况下则难以进行该测试。为了解决这一难题,压痕试验法应运而生。压痕试验是从硬度试验发展而来的,其试验过程是将一个标准的压头压入被测材料表面,同时记录下压入材料的深度和对应的载荷[2]。通过分析得到的载荷-深度曲线,得到材料的力学性能。压痕试验方法具有微损或者无损的特性,被测材料表面仅有一个小于压头尺寸的凹坑残留;压痕试验操作简单,不需要另外取样,可对在役设备进行现场测试;利用该方法可以测得材料的多种力学性能[3-7]。因此,压痕试验方法具有广阔的应用前景。
目前,各国学者对采用压痕试验获得材料强度进行了广泛研究,并提出了不同的方法。TABOR[2]通过表征应力应变法获得金属材料的强度,该方法需要准确地确定压头与试样的接触面积,这是因为压头附近材料的堆积-沉陷现象会严重影响测试结果的准确性[8];一次压入过程只能获得一个表征应力-应变点,因此需要多个压入过程以累积足够数量的表征应力-应变点。在TABOR提出的方法基础上,为了更加方便地获得表征应力-应变点,FILED等[9]通过压痕试验得到的卸载曲线计算压头与试样的接触面积,并采用多次加卸载方式累积足够数量的表征应力-应变点;该试验方法也称为连续压痕法,广泛用于表征应力-应变点的测量,但该方法需进行多次加卸载试验,操作比较繁琐。
随着计算机技术的发展,反向分析方法得到了研究者的青睐。反向分析方法通常结合最优化算法,将模拟获得的载荷-深度曲线逐步逼近试验测得的曲线,进而提取出相应的应力-应变曲线,最终计算出材料的强度[10]。但是由于多条应力-应变曲线对应相似的载荷-深度曲线,因此需要结合额外的试验信息才能得到唯一的应力-应变曲线,如压痕形貌[11]、卸载曲线的斜率[12]、能量变化[13]等。如何通过单次压痕试验的载荷-深度曲线获得准确的金属材料强度,仍是目前研究的难点与热点。模拟退火粒子群算法是智能优化算法的一种,结合了粒子群算法和模拟退火算法的优点,能够快速搜索到全局最优解。传统粒子群优化算法虽然能够快速搜索到最优解,但是容易陷入局部收敛。模拟退火算法则在搜索过程中具有概率突跳的能力,能够有效避免搜索过程中陷入局部最优值。粒子群算法和模拟退火算法结合可有效避免计算陷入局部收敛,从而得到全局最优解[14]。基于此,作者通过单次压痕试验与有限元模拟相结合的方法,结合反向分析方法与模拟退火粒子群算法,从得到的载荷-深度曲线加载部分提取材料的塑性参数,基于Ludwig硬化模型预测了不同金属材料的强度,并与单轴拉伸试验得到的结果进行对比。
1 试样制备与试验方法
试验材料包括Q345R钢、3Cr1MoV钢、2.25Cr1Mo钢和14MoV63钢,均取自于服役后的设备,化学成分如表1所示。在试验钢上截取尺寸为30 mm×30 mm×15 mm的试样,采用SPT-10型仪器化压痕测试仪进行室温压痕试验,该设备位移和载荷传感器精度分别为1 μm和0.1 N,最大载荷为5 kN,下压速度设定为0.2 mm·min-1,以确保变形速率处于准静态应变范围。采用直径1.0 mm的碳化钨球形压头,压入深度为0.3 mm,压痕比为0.6。
表1 不同试验材料的化学成分(质量分数)
Table 1 Chemical composition of different testmaterials (mass fraction) %
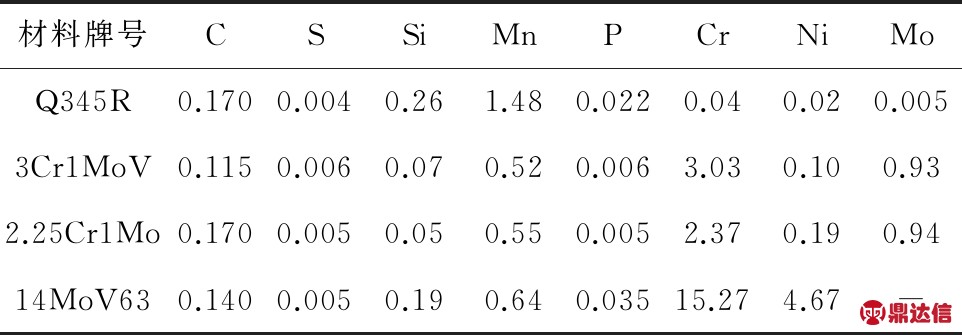
按照GB/T 228.1-2010,在试验钢上截取尺寸为φ6 mm×30 mm的光滑圆棒拉伸试样,在Instron 8800型拉伸试验机上进行室温拉伸试验,拉伸速度为1 mm·min-1。
2 有限元模型的建立
采用ABAQUS软件进行压痕试验过程的模拟。由于压头与试样的结构具有轴对称性,因此为节省计算时间,采用二维轴对称模型。在试样中只取压头正下方略大于5倍压头半径的区域建模,此时可忽略边界条件对模拟结果的影响[15]。压头视为解析刚体,试样为变形体,其表面尺寸为4 mm×4 mm,采用4节点轴对称缩减积分单元(CAX4R)划分网格。约束试样底部y方向的位移(Uy=0),同时为压头施加固定位移约束。压头与试样之间建立面-面接触,摩擦因数设为0.2,并用过渡网格细化接触区域的网格。所建立的有限元模型如图1所示。
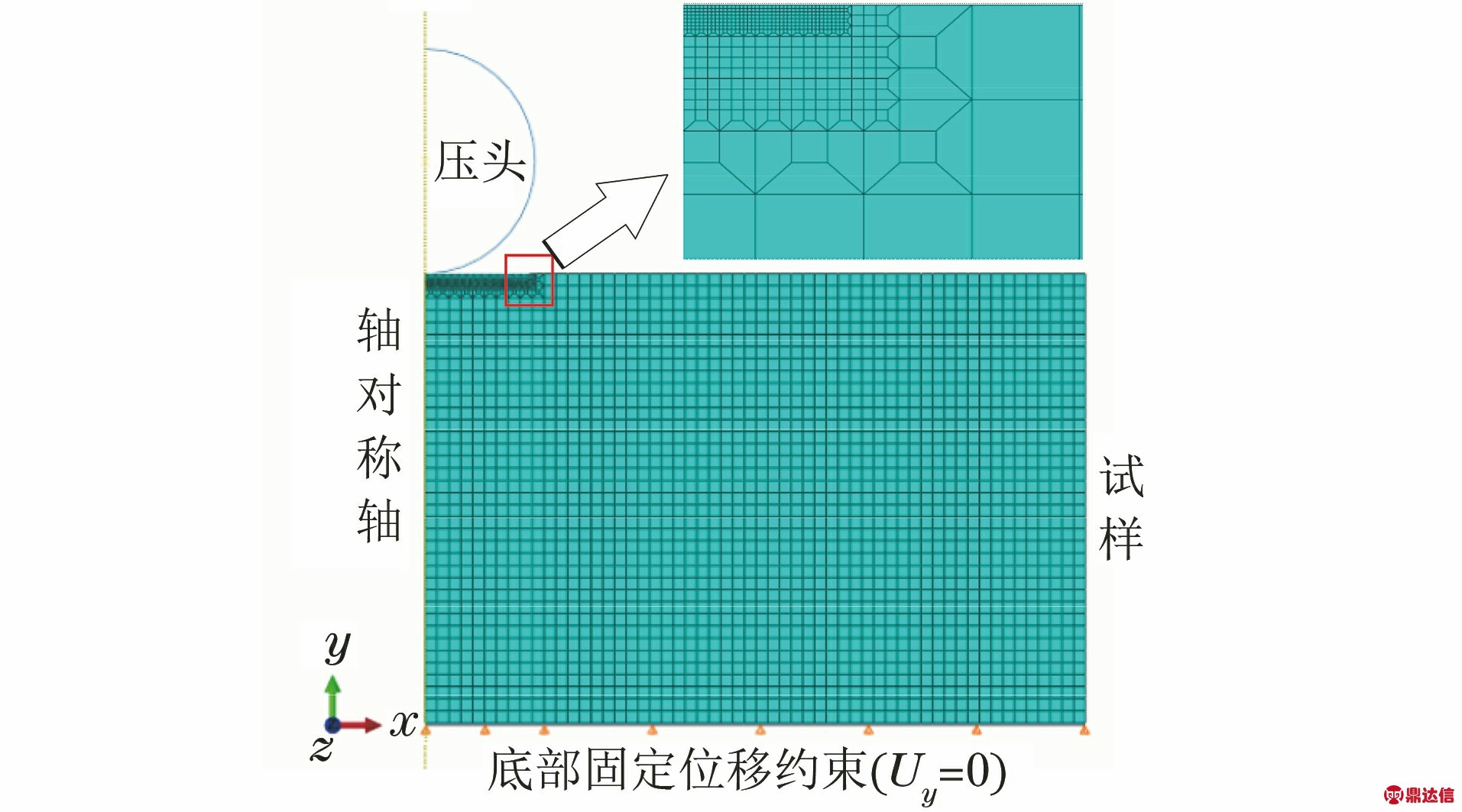
图1 压痕试验有限元模型网格划分示意
Fig.1 Meshing diagram of finite element model of indentation test
3 强度计算方法
3.1 本构方程的确定
由于研究准静态条件下材料的强度时不需要考虑材料的动态响应及损伤,故采用基本的弹塑性本构方程。同时由于多数金属材料及合金的真应力与真应变关系可用幂指数进行拟合,因此采用Ludwig硬化模型[16],其表达式为
(1)
式中:εP为材料的真塑性应变;σ和σ0分别为材料的真应力和初始屈服应力;K,n分别为材料的强化系数和应变强化指数。
3.2 材料参数的识别
通过对压痕试验曲线的反向分析得到材料的强度。将由压痕试验得到的载荷-深度曲线视为材料参数σ0,K,n的函数,模拟曲线与试验曲线间的相对误差[17]可表示为
(2)
式中:F为模拟曲线与试验曲线的相对误差;N为ABAQUS软件中请求输出的数据点的个数;Fj,FE和Fj,Exp分别为某一压入深度下由模拟和试验得到的载荷。
采用模拟退火粒子群算法从压痕载荷-深度曲线中提取真应力-真塑性应变[18],其具体过程为:1)预设一组材料参数σ0,K,n,并将其输入ABAQUS软件中模拟出对应的载荷-深度曲线;2)将模拟得到的曲线与试验得到的曲线进行对比,用式(2)计算出相应的误差函数;3)判断误差函数的大小,若其值小于给定的值(此处设为0.5%)则计算终止,若该值大于给定的值则根据模拟退火粒子群算法改变σ0,K,n,重新计算误差函数的大小,直到满足要求为止。
3.3 强度的计算
由于材料的强度是根据工程应力-应变曲线确定的,因此所提取的真应力-真塑性应变曲线需先转换为工程应力-应变曲线,转换公式为
εE=exp(εP+σ/E)-1
(3)
(4)
式中:εE为工程应变;σE为工程应力;E为弹性模量。
将式(1)和式(3)代入式(4)中,得到工程应力与真塑性应变的关系:
(5)
对于应力-应变曲线上无明显屈服平台的材料,其屈服强度通常取工程塑性应变0.2%所对应的应力。0.2%工程塑性应变对应的真塑性应变也约为0.2%,将εP=0.002代入式(5)中即可计算出材料的屈服强度。
材料的抗拉强度取拉伸试验中材料达到最大载荷时所对应的工程应力,应用拉伸失稳的概念[19]得到材料处于最大载荷处时满足:
(6)
将式(6)变换为
(7)
由式(1)可以得到:
(8)
由于ε=εP+σ/E,结合式(7)和式(8),式(6)最终可变换为
(9)
联立式(1)和式(9),即可得到εP及其对应的抗拉强度,其详细推导过程参考文献[18]。
4 结果与讨论
由图2可以看出:由模拟得到的载荷-深度曲线与试验得到的几乎重合,且模拟曲线与试验曲线的相对误差F均小于0.5%,说明模拟退火粒子群算法能有效地从压痕载荷-深度曲线中提取出材料的塑性参数。由图3可以看出:即使模拟得到的载荷-深度曲线与试验得到的高度重合,但由反向分析方法提取出的真应力-真塑性应变曲线仍不是唯一的,这说明仅从单次压痕试验获得的载荷-深度曲线中并不能提取出一组唯一的塑性参数,与前人的研究结果一致[12,20]。这是由于模拟曲线是在假定材料是均匀的、各向同性的条件下得到的,而实际材料并未完全符合该假设,而且实际材料的硬化关系也不能完全符合给定的硬化模型。
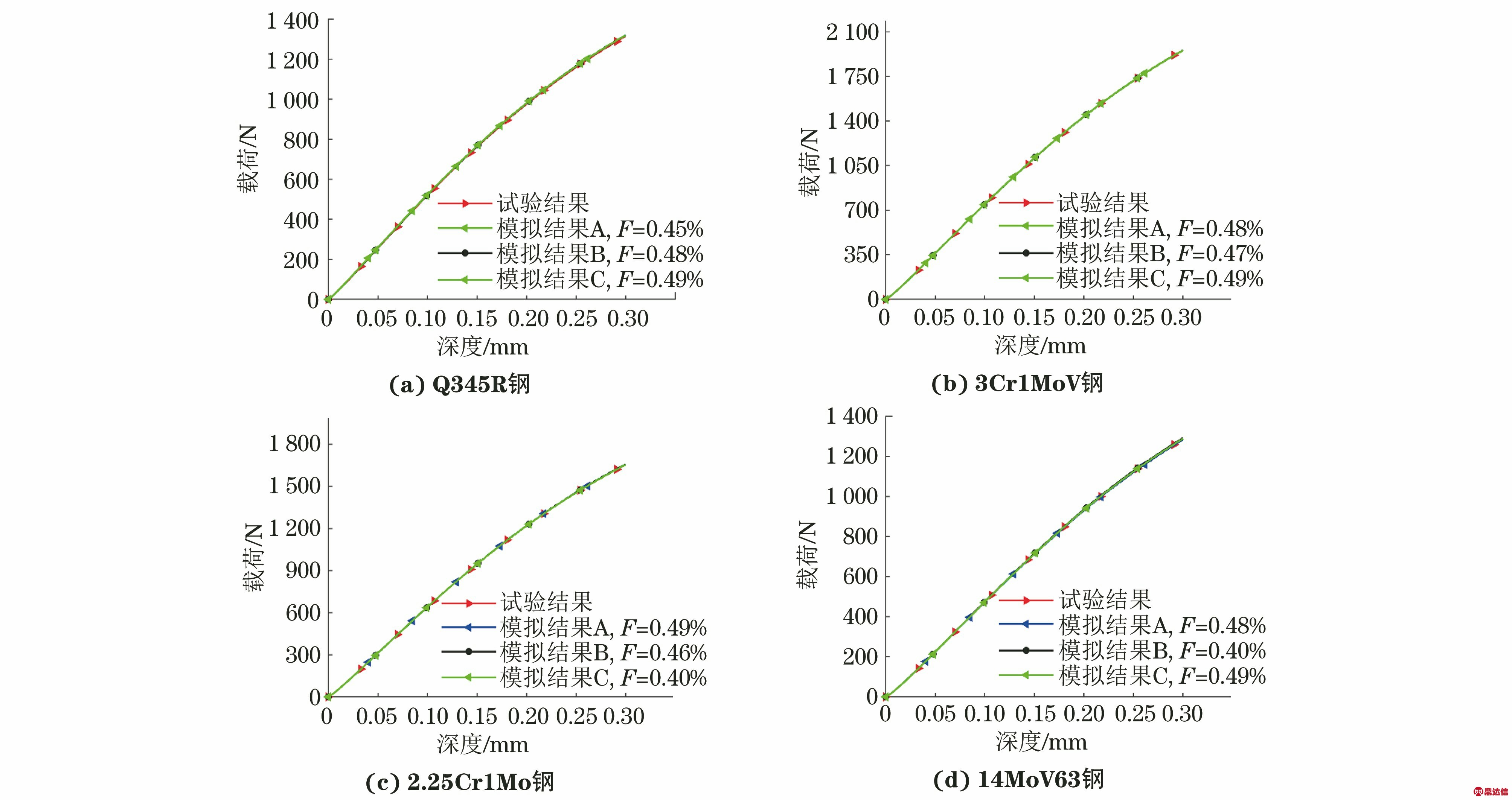
图2 由模拟和试验得到不同试验钢的载荷-深度曲线
Fig.2 Load-depth curves of different test steels obtained by simulation and tests: (a) Q345R steel; (b) 3Cr1MoV steel; (c) 2.25Cr1Mo steel and (d) 14MoV63 steel

图3 基于载荷-深度试验和模拟曲线应用反向分析方法提取得到不同试验钢的真应力-真塑性应变曲线
Fig.3 Extracted true stress-true plastic strain curves of different test steels by inverse method based on tested and simulated load-depth curves: (a) Q345R steel; (b) 3Cr1MoV steel; (c) 2.25Cr1Mo steel and (d) 14MoV63 steel
由于从载荷-深度曲线提取到的真应力-真塑性应变曲线不具有唯一性,因此从真应力-真塑性应变曲线计算得到的强度也具有明显的分散性。以2.25Cr1Mo钢为例,列出了当F分别为0.5%,1.0%,1.5%,2.0%,2.5%时,由真应力-真塑性应变模拟曲线计算得到的屈服强度和抗拉强度。由图4可以看出:当F为0.5%时,计算得到的2.25Cr1Mo钢的屈服强度在440462 MPa,抗拉强度在581605 MPa;当F增大至2.5%时,其屈服强度在390518 MPa,抗拉强度在558628 MPa。可以发现,随着F的增大,强度的分散性也增大。由此推论,当F取0时可获得唯一的强度。
为更加清晰地反映强度与F的关系,对F不大于6.0%条件下模拟得到不同试验钢的屈服强度和抗拉强度进行统计。由图5与图6可知,随着F的减小,强度的分布范围减小,且趋近于某一个数值,同时强度存在明显的上下边界线,即由真应力-真塑性应变曲线计算得到的强度具有明显的收敛趋势。这是由于随着F的减小,从载荷-深度曲线提取出的真应力-真塑性应变曲线逐渐趋近于材料的真实应力-应变曲线。
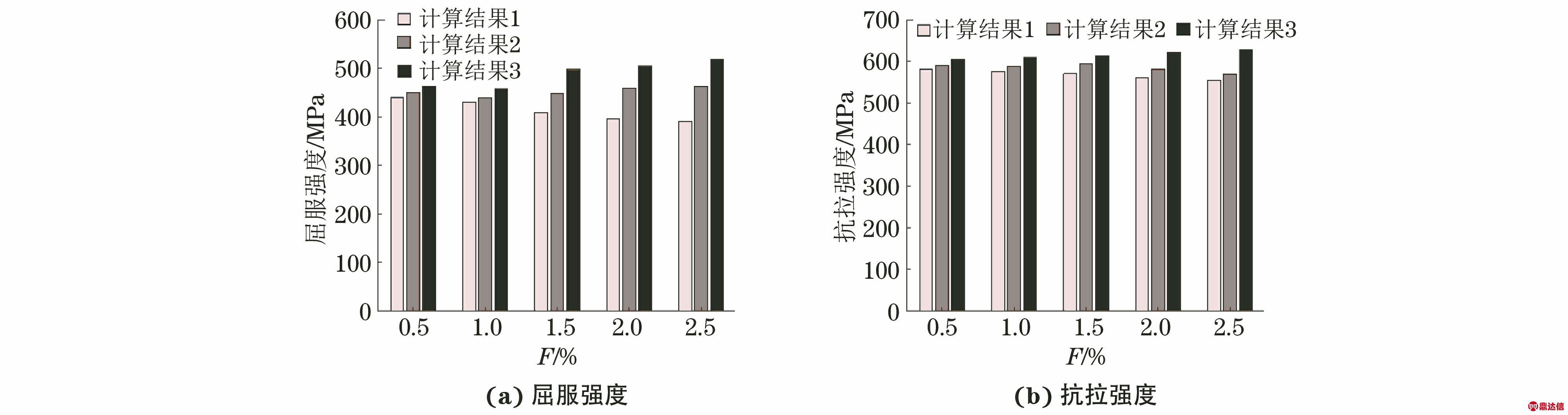
图4 由真应力-真塑性应变模拟计算得到不同F条件下2.25Cr1Mo钢的屈服强度与抗拉强度
Fig.4 Yield strength (a) and tensile strength (b) of 2.25Cr1Mo steel under different F conditions calculated from simulated true stress-true strain curves
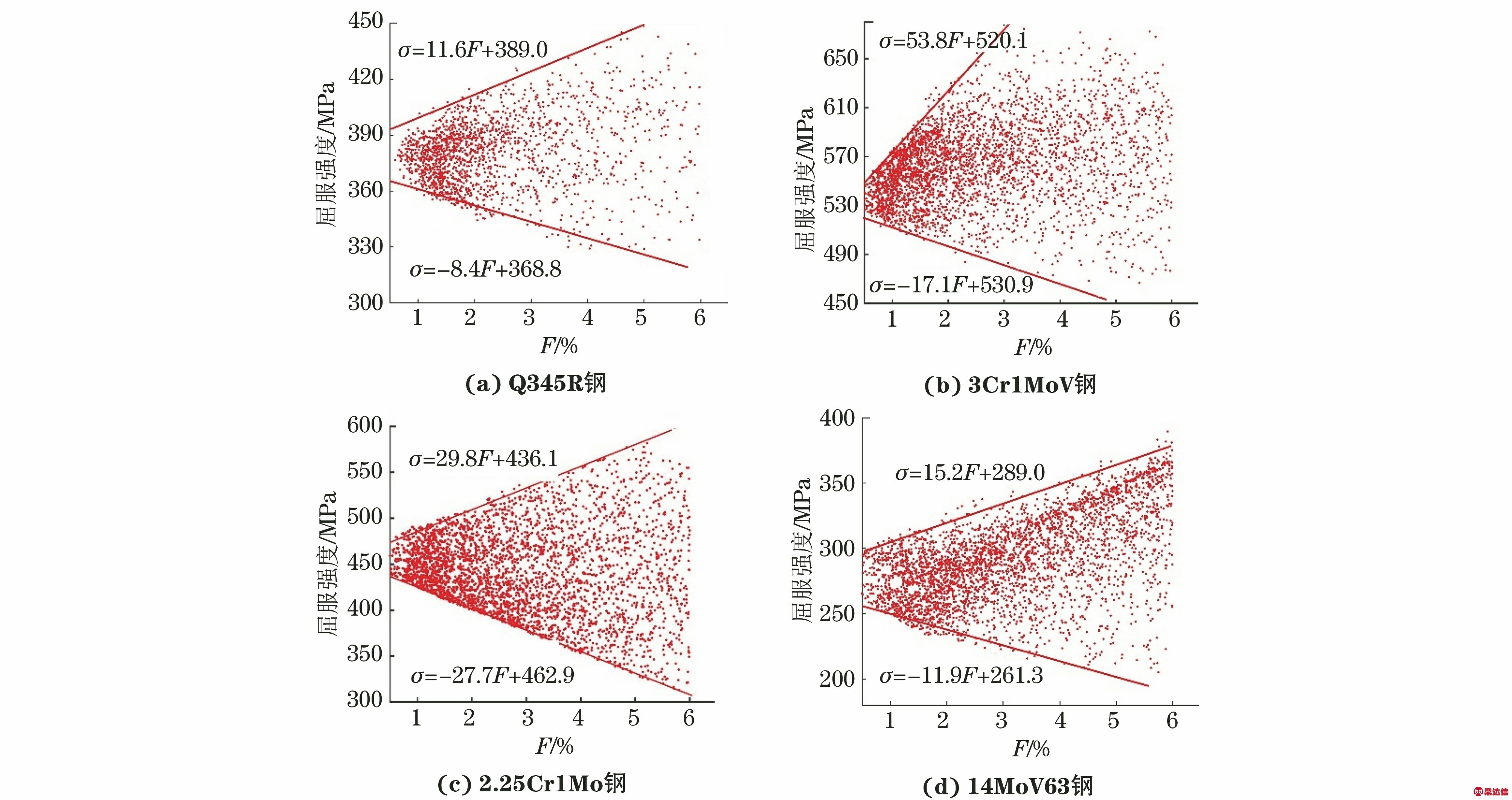
图5 模拟得到F不大于6%条件下不同试验钢屈服强度的统计结果
Fig.5 Statistical yield strength of different test steels by simulation under condition of F less than 6%: (a) Q345R steel; (b) 3Cr1MoV steel; (c) 2.25Cr1Mo steel and (d) 14MoV63 steel
求解图5与图6中上下边界线的交点,即可得到材料的强度。由表2可知,采用压痕试验法得到不同试验钢的强度均接近真实强度,屈服强度的最大相对误差为5.9%,抗拉强度的最大相对误差为4.3%。这说明采用压痕试验法可以准确地评价金属材料的强度。
由于多次试验得到的载荷-深度曲线并不能保证高度重合,因此为研究试验误差对结果的影响,对2.25Cr1Mo钢进行了2次压痕试验,得到的载荷-深度曲线(A和B)如图7所示。将图2(c)中的载荷-深度试验曲线作为参考曲线,通过式(2)计算得到曲线A和曲线B与参考曲线的相对误差为1.24%和2.10%。由图7中各曲线得到的强度如表3所示。由表3可以看出:压痕试验所得载荷-深度曲线与参考曲线的相对误差越大,计算得到的强度偏离由参考曲线计算得到的强度的程度越大,且曲线的相对误差在2.10%时,计算得到强度的相对误差为2.4%,满足工程实际要求。
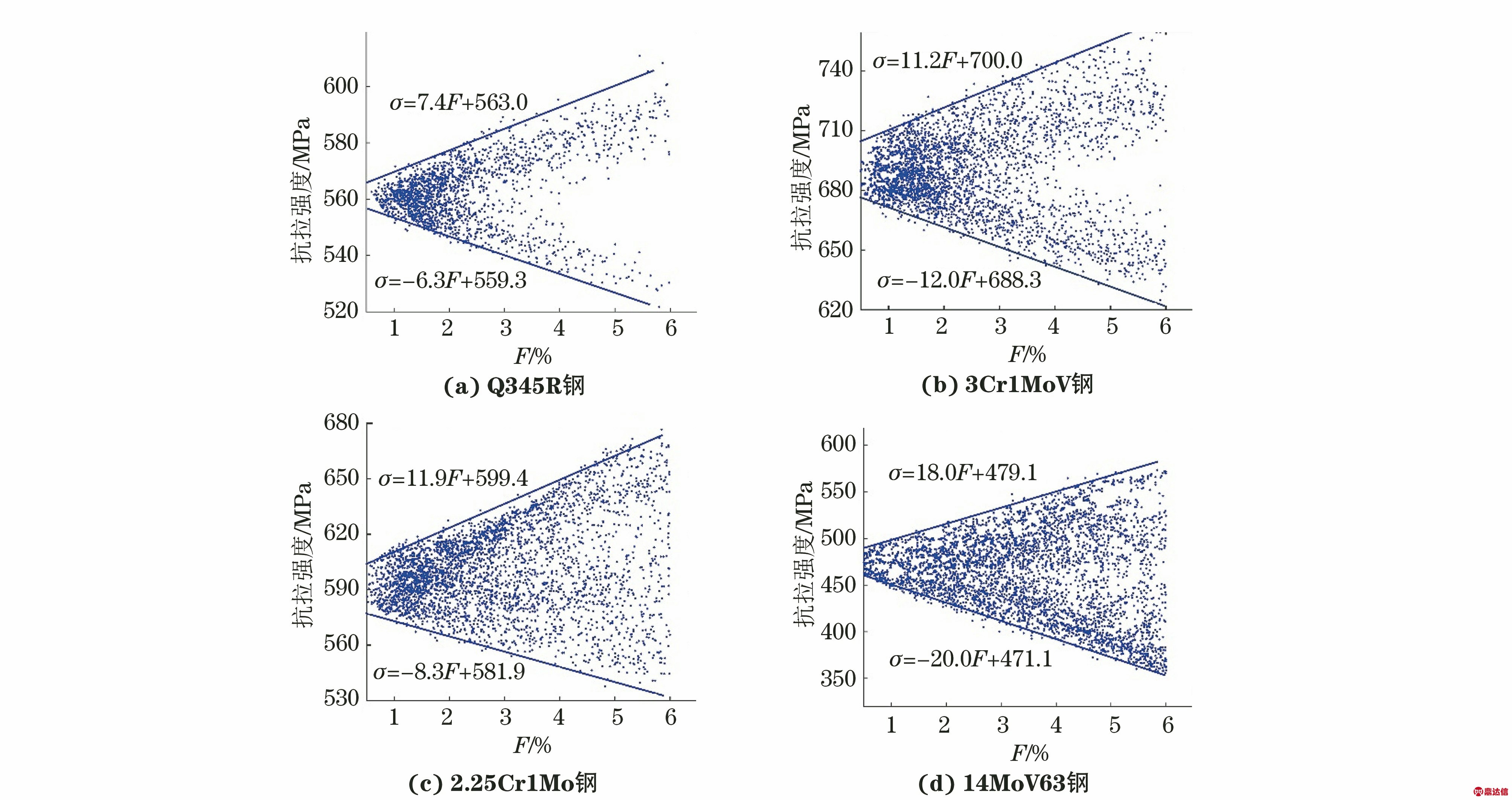
图6 模拟得到F不大于6%条件下不同试验钢抗拉强度的统计结果
Fig.6 Statistical tensile strength of different test steels by simulation under condition of F less than 6%: (a) Q345R steel; (b) 3Cr1MoV steel; (c) 2.25Cr1Mo steel and (d) 14MoV63 steel
表2 采用压痕试验法计算得到不同试验钢的强度与拉伸试验得到强度的对比
Table 2 Comparison between strength of different test steelscalculated by indentation test and obtained by tensile test
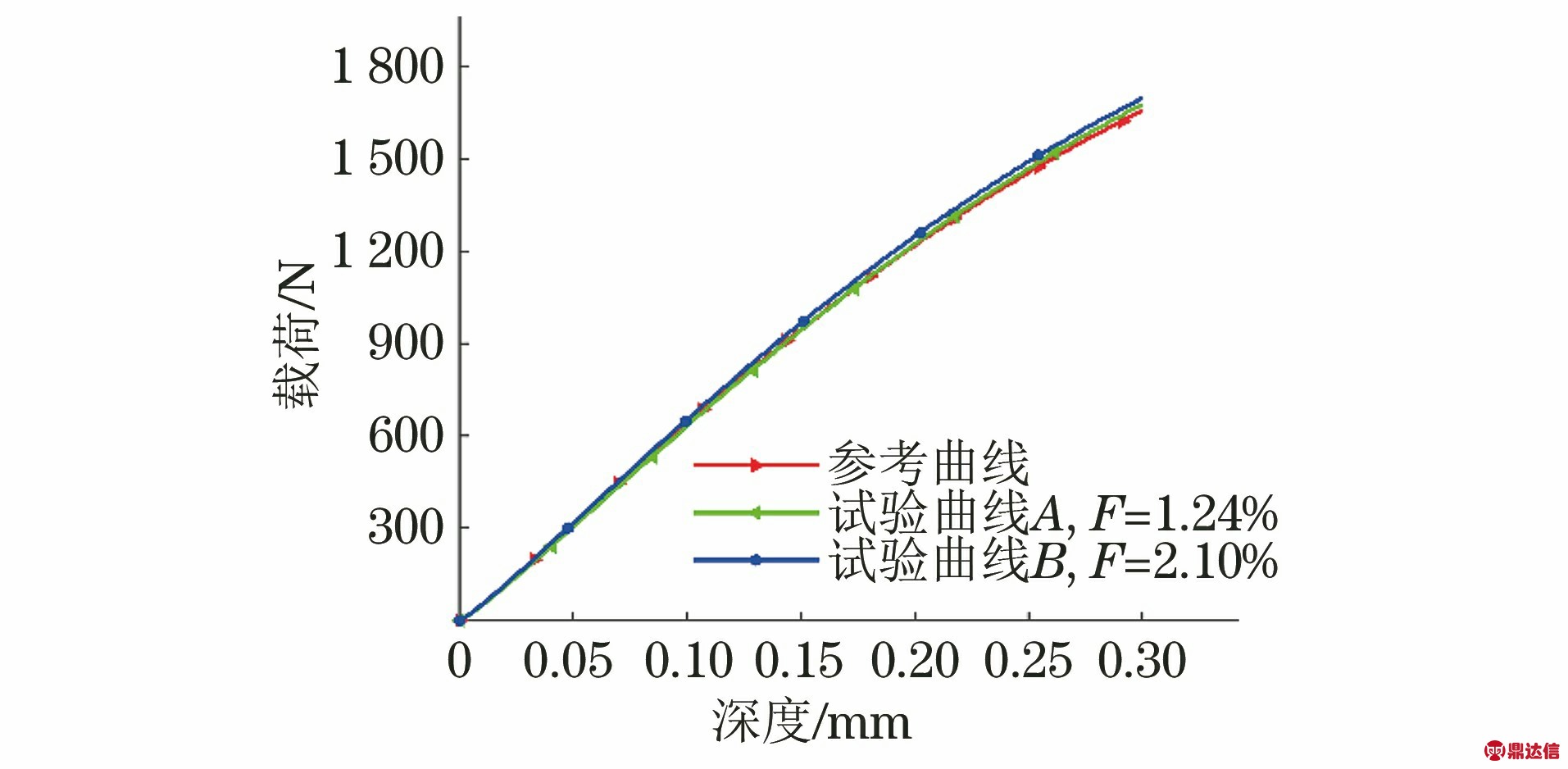
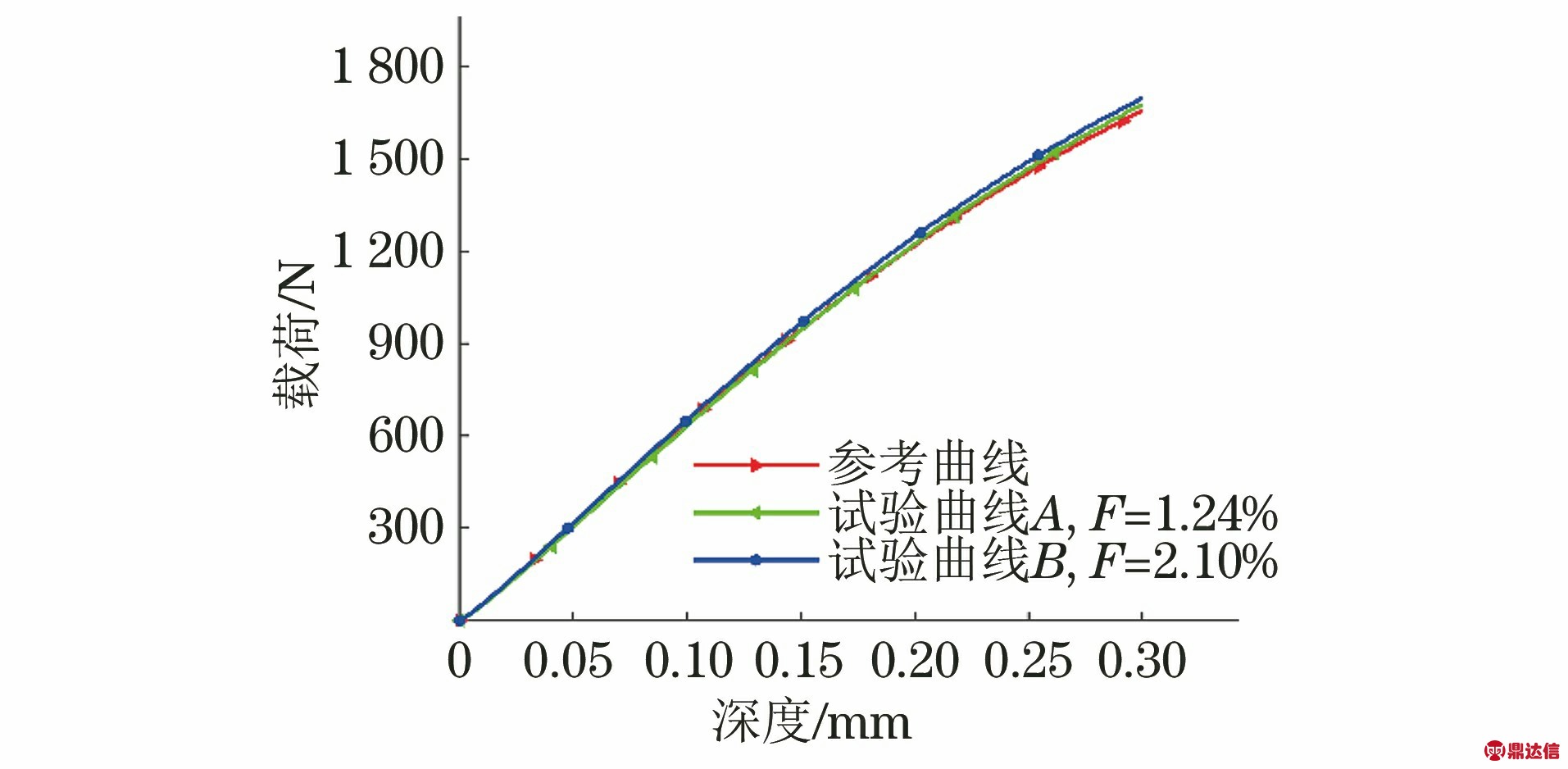
图7 不同压痕试验获得2.25Cr1Mo钢载荷-深度曲线的对比
Fig.7 Comparison of load-depth curves of 2.25Cr1Mo steel obtained by different indentation tests
5 结 论
(1) 有限元模拟得到的载荷-深度曲线与试验得到的几乎重合,且模拟曲线与试验曲线的相对误差均小于0.5%,说明模拟退火粒子群算法可有效地从压痕试验载荷-深度曲线中提取出金属材料的塑性参数。
表3 基于图7中不同载荷-深度曲线计算得到2.25Cr1Mo钢的强度
Table 3 Strength of 2.25Cr1Mo steel calculated fromdifferent load-depth curves in Fig.7
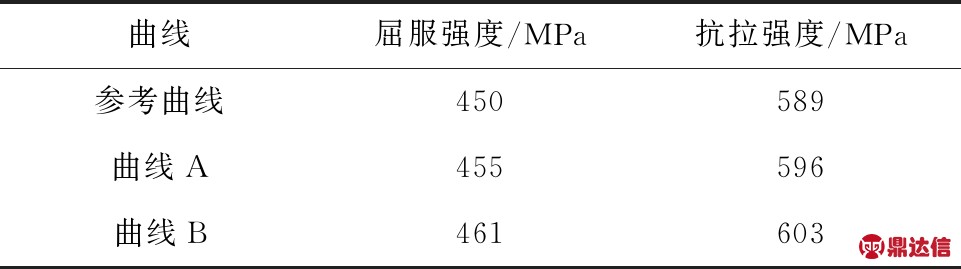
(2) 基于Ludwig硬化模型,利用反向分析方法从压痕试验载荷-深度曲线中提取的真应力-真塑性应变曲线不是唯一的,但从真应力-真塑性应变曲线计算得到的强度具有明显的收敛趋势。
(3) 采用压痕试验法得到不同金属材料的强度均接近于由拉伸试验得到的强度,屈服强度与抗拉强度的最大相对误差分别为5.9%,4.3%,说明采用压痕试验法可以准确地评价金属材料的强度。