摘 要:在NASA的SR-3桨扇构型基础上,生成了一种8叶桨扇模型。通过准定常数值仿真,得到了不同工况下该桨扇的总体气动性能变化规律及其流场特征,并研究了设计工况下,桨扇叶片数对桨扇总体性能及叶片气动性能的影响。结果表明:该桨扇模型具有较高的推进效率,可为进一步的工程应用提供参考。
关 键 词:桨扇;对转螺旋桨;桨叶设计;气动性能;数值仿真
作为传统的飞行器推进器,空气螺旋桨具有推进效率高、起降性能好等优点,因此从其诞生的1903年至今的一个多世纪里,空气螺旋桨一直是中低速飞机的主流推进器。但巡航马赫数一直制约着空气螺旋桨的进一步发展,限制了其应用场景[1]。
随着先进螺旋桨设计方法及一系列超临界翼型的提出,将螺旋桨作为推进器应用于高亚音速飞行成为可能。这种全新设计的螺旋桨具有小直径、高载荷、可变桨矩等特点。这种桨叶的外形介于传统螺旋桨和风扇之间,故称为桨扇[1]。
研究表明,相较于先进涡扇发动机,采用桨扇发动机作为推进器可以节省20%以上的燃油[2]。随着巡航速度的进一步下降,桨扇的推进效率还能进一步提升。若采用更加先进的构型——对转桨扇,桨扇的总体推进效率还能提高8%~10%[3]。因此,发展桨扇技术在经济和军事上都具有重要意义。
国外对桨扇的研究源于对传统螺旋桨的改进,20世纪60年代末,NASA刘易斯研究中心和汉胜公司在研究中发现相较于传统螺旋桨,螺旋桨的后掠特征有提升推进效率和降低噪声的效果[4]。1970年,作为一种新型推进器,“桨扇”的概念被首次提出。随后,由于1973年能源危机的发生,美国政府批准了NASA的先进涡桨项目(advanced turboprop project,ATP),桨扇的研究进入黄金发展期[4]。几乎同一时期,NASA研发了螺旋桨气动性能预测[5]、强度校核[6]、噪声预测[7]的相关程序。在1976年首先提出SR-1(single rotation,SR)桨扇构型并进行了风洞测试,研究表明:在设计状态下(0.8 Ma,10.688 km),该桨扇的推进效率可达77.7%,证明了桨扇构型的可行性[8]。随后,NASA又提出一系列改进方案并进行了风洞实验,其中SR-3桨扇在设计状态下性能最佳,降噪效果最为明显[9]。因此,SR-3桨扇成为桨扇设计中的标准构型,在国内外有关桨扇气动性能和噪声水平的相关研究中,大都以此为研究对象[10-17]。目前,国外相关研究主要集中在对转桨扇非定常特性研究,旨在降低对转桨扇的噪声和振动。Kim等[14]采用时域方法对桨扇产生的噪声进行了预测。Veldhuis[15]将等效盘方法引入桨扇计算中,证明了等效盘方法在桨扇计算中的可行性。Nallasamy[16]采用数值仿真和实验相结合的研究方法,研究了不同马赫数桨扇表面的压力波动。可以看出,国外对桨扇的研究致力于解决桨扇噪声和结构强度问题,公开的文献中对有关气动性能的研究仅局限于巡航工况整体性能预测,且无流场细节研究。
相较于国外,国内对桨扇的研究起步较晚。20世纪90年代中后期,北京航空学院的朱年国[18]评述了桨扇设计参数的选择原则以及参数选择对性能的气动和声学性能可能产生的影响,指出了国内桨扇发展存在的问题以及进一步发展的方向,但并没有提出实质性的设计方法或研究结论。接着,他在另一篇文章中提出用于设计和分析桨扇的螺旋桨-吊舱相关法[11]。几乎在同一时期,刘导治[19]对桨扇的气动设计问题以及桨扇气动计算方法进行了总结性论述。王波等[10]对一桨扇模型进行了风洞实验,定性研究了桨扇前、后掠对桨扇气动和声学性能的影响。周人治等[20]采用压气机的设计方法,初步设计了对转桨扇构型并进行了三维流场仿真,但其研究仍属探索性质,如采用内流设计软件设计属于外流的桨扇,以及没有分析对转桨扇的气动性能和流动状况。刘政良等[12]采用改进的螺旋桨片条理论初步完成了桨扇的设计,并对其进行了初步数值仿真,得到桨扇的总体性能曲线。
不难看出,对于桨扇的研究,国内还处于基础状态,主要为技术论证以及探索性研究。在桨扇设计方面,尚不存在统一的设计规范和成熟的设计软件;在气动仿真方面,仅有一些有关总体性能的探索,尚缺少对桨扇流场以及性能规律的研究。要进一步发展对转桨扇技术,亟需掌握不同工况下桨扇运行时气动参数的变化规律及其流场的流动特征。本文在文献[9]公布的部分桨扇参数的基础上进行了型面设计和流场数值仿真,分析了不同来流马赫数条件下,8叶桨扇的性能变化规律及桨扇周围流场的流动特征,并研究了设计来流马赫数工况下叶片数对桨扇整体及单叶片气动性能的影响。
1 术语定义
主要介绍桨扇的设计参数:叶片工作系数AF,叶片积分升力系数CLi;表示桨扇工况的参数进距比J和吸收功率P;表示气动性能的参数压力系数CP、功率系数CP和效率η。
1.1 桨扇设计参数
1)叶片工作系数AF

其中:b表示叶素弦长;D表示桨盘直径。AF决定桨扇载荷。
2)叶片积分升力系数CLi

其中CLD为叶素设计升力系数。
1.2 表示桨扇工况的参数
1)进距比J

其中:u0为来流速度;ns为秒转速。该式的物理意义为来流速度与叶尖切向速度之比,决定叶素的相对气流攻角。
2)功率P

式中M为推动桨扇旋转所需扭矩。该式表示桨扇旋转吸收的发动机功率。
1.3 气动性能参数
1)压力系数Cp
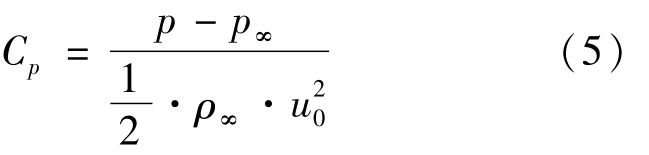
式中,p∞和ρ∞分别为远场压强和密度。
2)功率系数CP

3)桨扇效率η

式中T为桨扇产生的拉力。效率为桨扇旋转的推动功与桨扇吸收发动机的功率之比。
2 模型生成
本文研究对象为一叶尖后掠角为45°的8叶桨扇,其主要参数与NASA Hamilton研究中心研发的SR-3桨扇相同。SR-3桨扇的主要参数列于表1。
表1 SR-3桨扇的主要参数
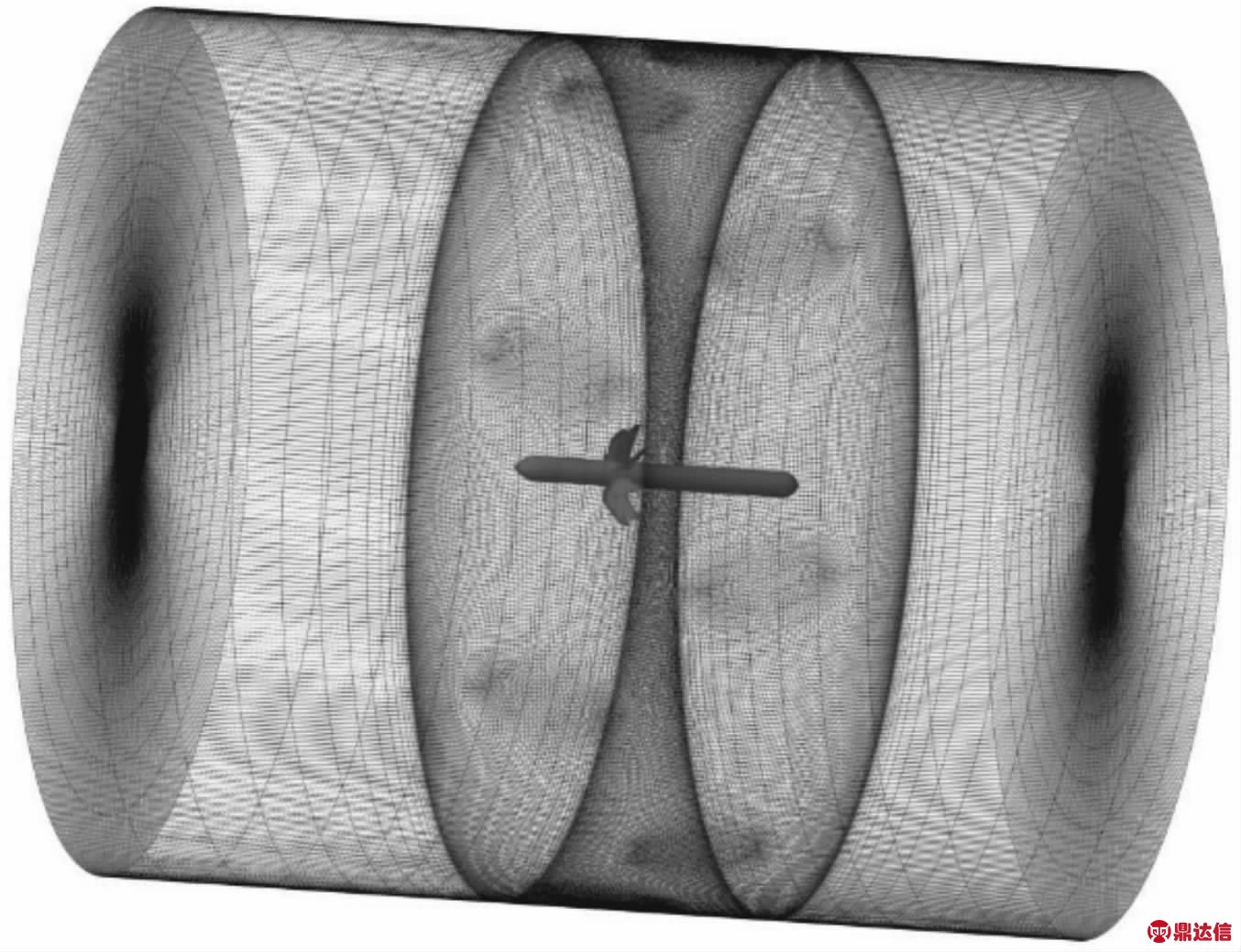
在原设计中,由叶根到相对叶高为0.37处,采用NACA-65翼型,在相对叶高在0.37~0.53处,无叶素分布,为过渡段,而在相对叶高在0.53~0.10处,采用超临界翼型NACA-16系列。
本文主要研究叶片性能变化及流场分布,根据已有经验,轮毂的不同对桨扇性能的影响较大。在实际应用中,轮毂因桨扇及短舱布置的不同而不同,因此在本文的研究中采用最广泛应用的钝头圆柱而非NASA实验中的内凹钝头锥体作为轮毂。因此,桨扇的工况类似于平面叶珊。图1为设计工况下,各相对叶高叶素截面的相对马赫数(不考虑诱导速度),横轴表示相对叶高,纵轴表示相对马赫数,由图可知由于来流马赫数较大且桨叶较小,各相对叶高的绕流速度差很小。
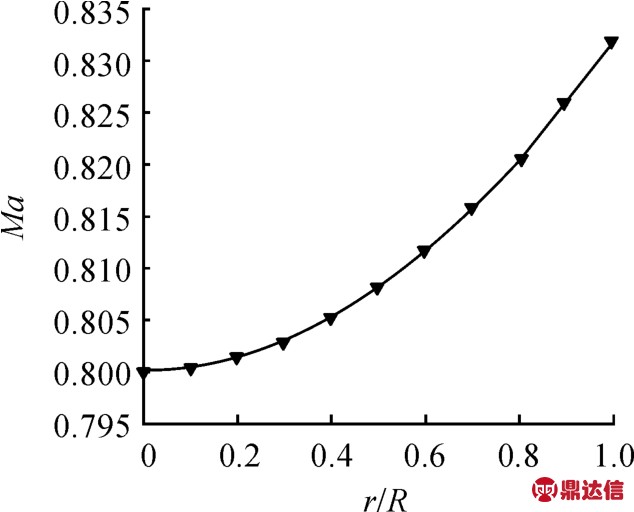
图1 Ma0=0.80,J=3.5时,不同叶高叶素截面的相对马赫数
本文将叶根处的叶素用NACA-16系列替换,同时对叶素厚度、升力系数和叶素扭转角做出了一定调整,为了保证AF值保持不变,弦长的分布与SR-3保持一致。须指出,桨扇参数的调整是一个迭代的过程,经过一系列调整,最终得到沿叶高方向叶素参数分布如图2所示。
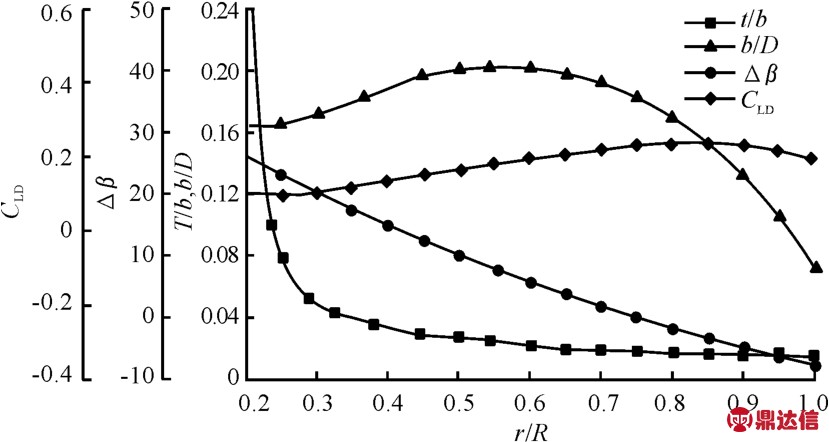
图2 沿叶高方向桨扇特征参数分布
生成叶片时,先将不同高度的叶素导入并平移,使所有叶素的重心线重合。然后沿重心线将叶素扭转一定的角度,该角度由扭转角决定。
然后根据不同叶高处后掠角的分布,将叶素沿各自弦线平移。不同叶高处后掠角分布如图3所示。从图中可以看出:r/R=0.45处的后掠角为0‴,从叶根至该高度的后掠角均小于0,从该处至叶尖的后掠角均大于0,因此该桨扇呈“月牙状”,在接下来有关后掠的讨论中,仅介绍分界点到叶尖处的后掠操作,其余部分的后掠操作与之相同。
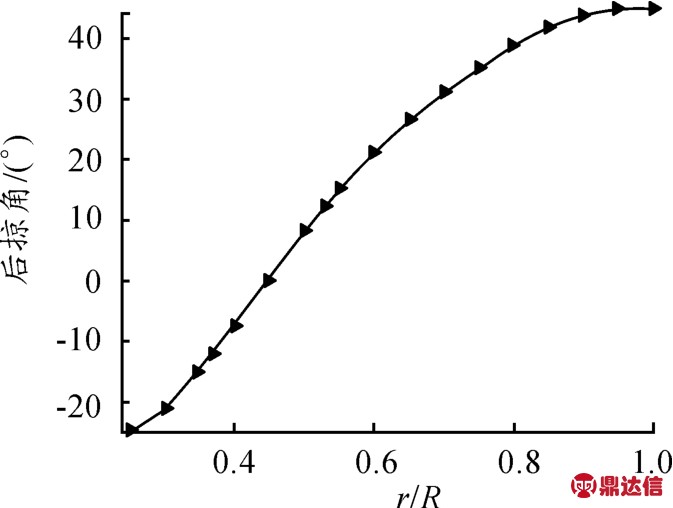
图3 SR-3不同叶高处后掠角分布
首先,从基准点(r/R=0.45)开始,根据相邻叶素的高度差Δz和对应位置的后掠角,按顺序求出沿来流方向后掠的长度Δx,然后根据各个叶素的扭转角和沿来流方向后掠的长度Δx,求出沿弦长的后掠距离L,后掠示意图如图4所示。
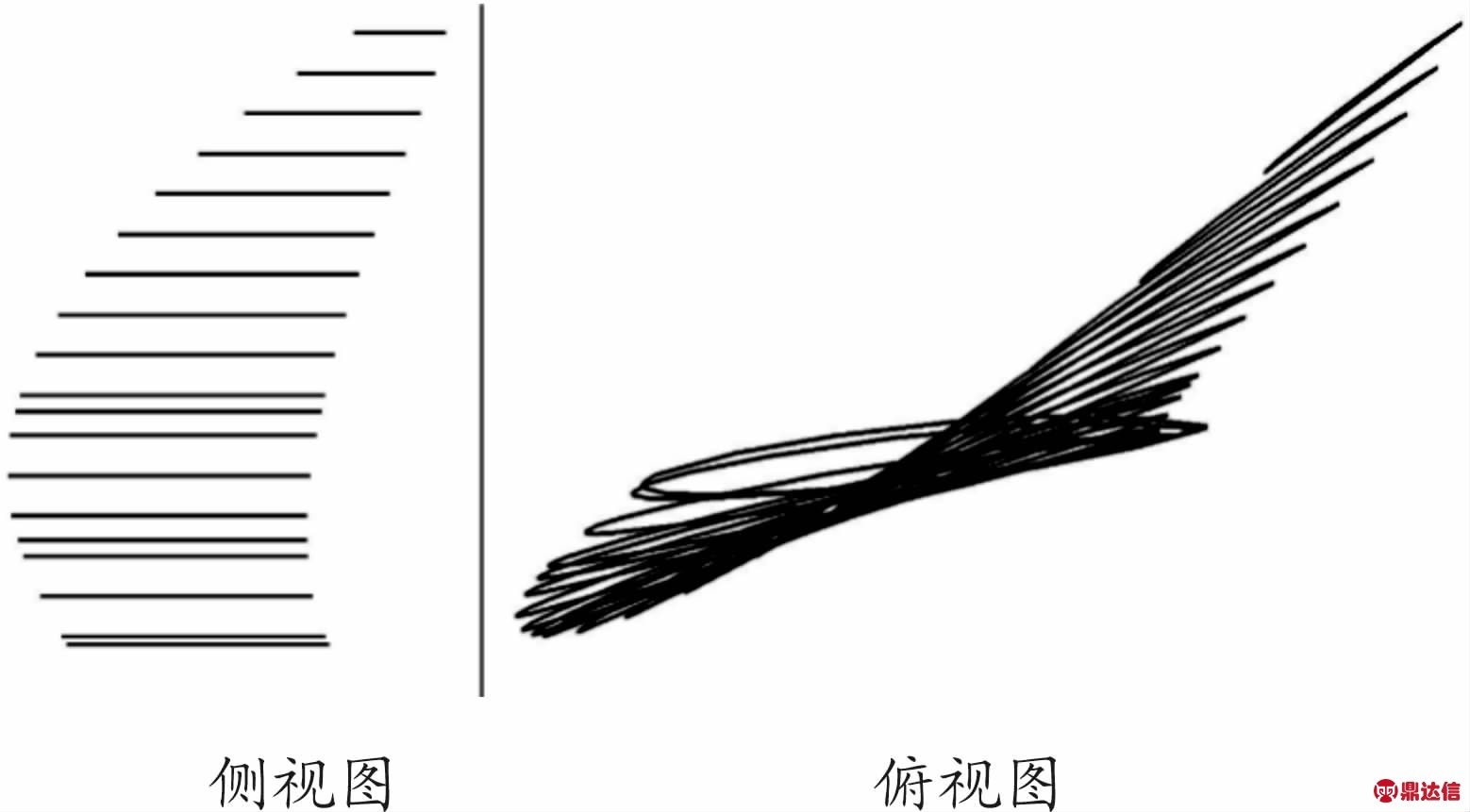
图4 后掠示意图
最后,采用CATIA中的“多截面曲面”工具生成螺旋桨叶片。图5和图6分别为最终排布的叶素以及根据这些叶素生成的桨扇叶片。图7为仿真所用模型。
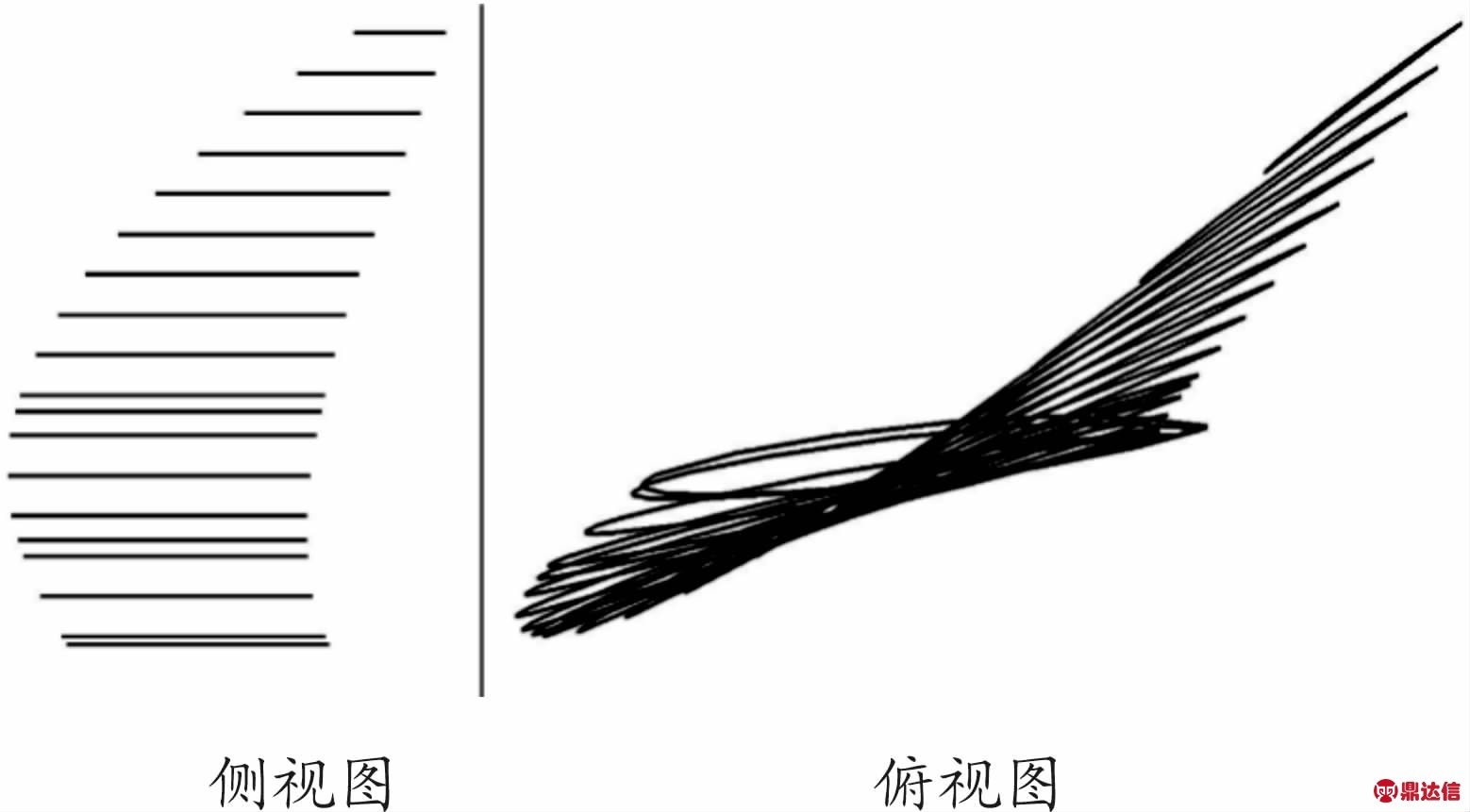
图5 合理排布的叶素
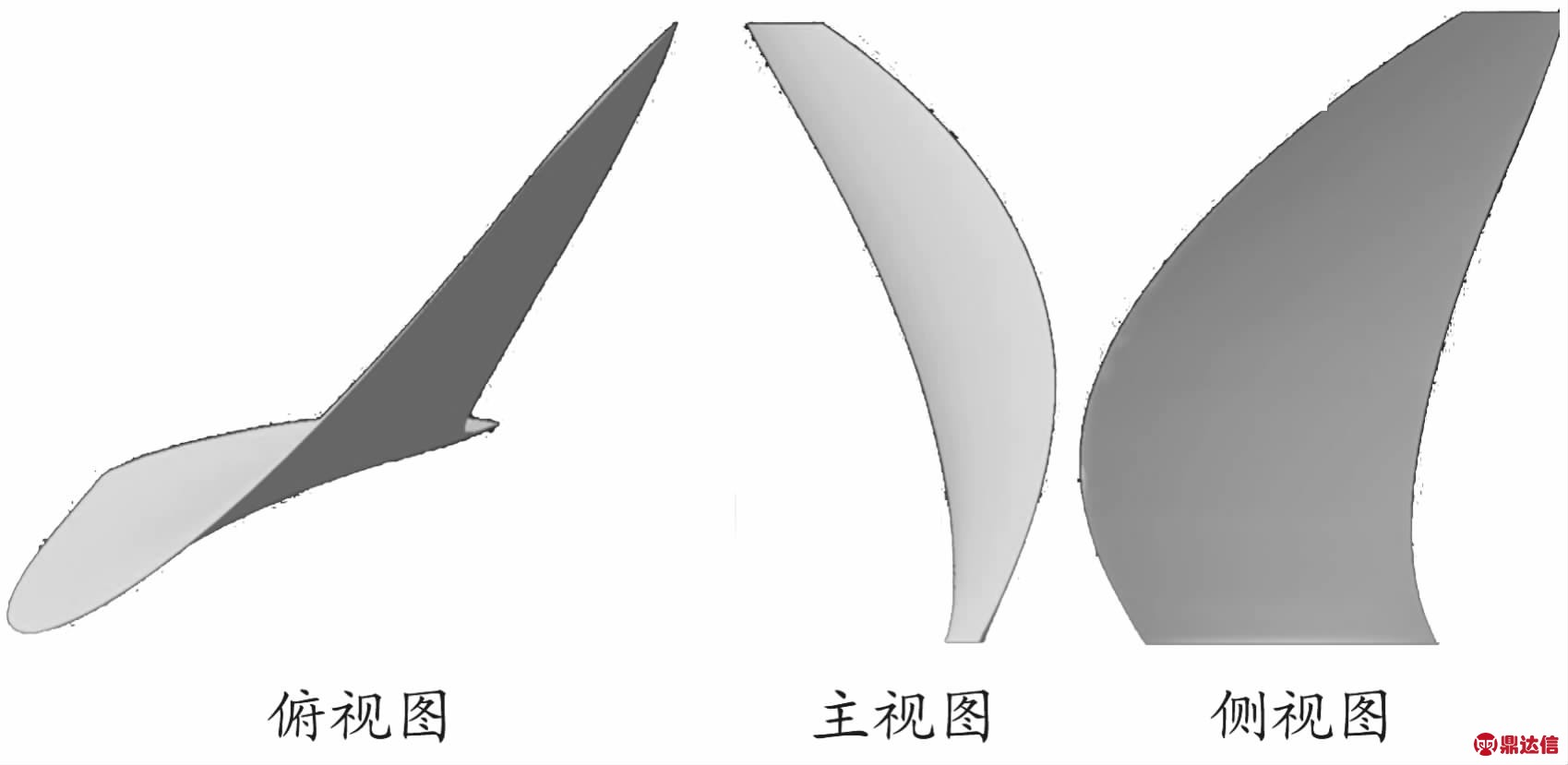
图6 最终生成的叶片
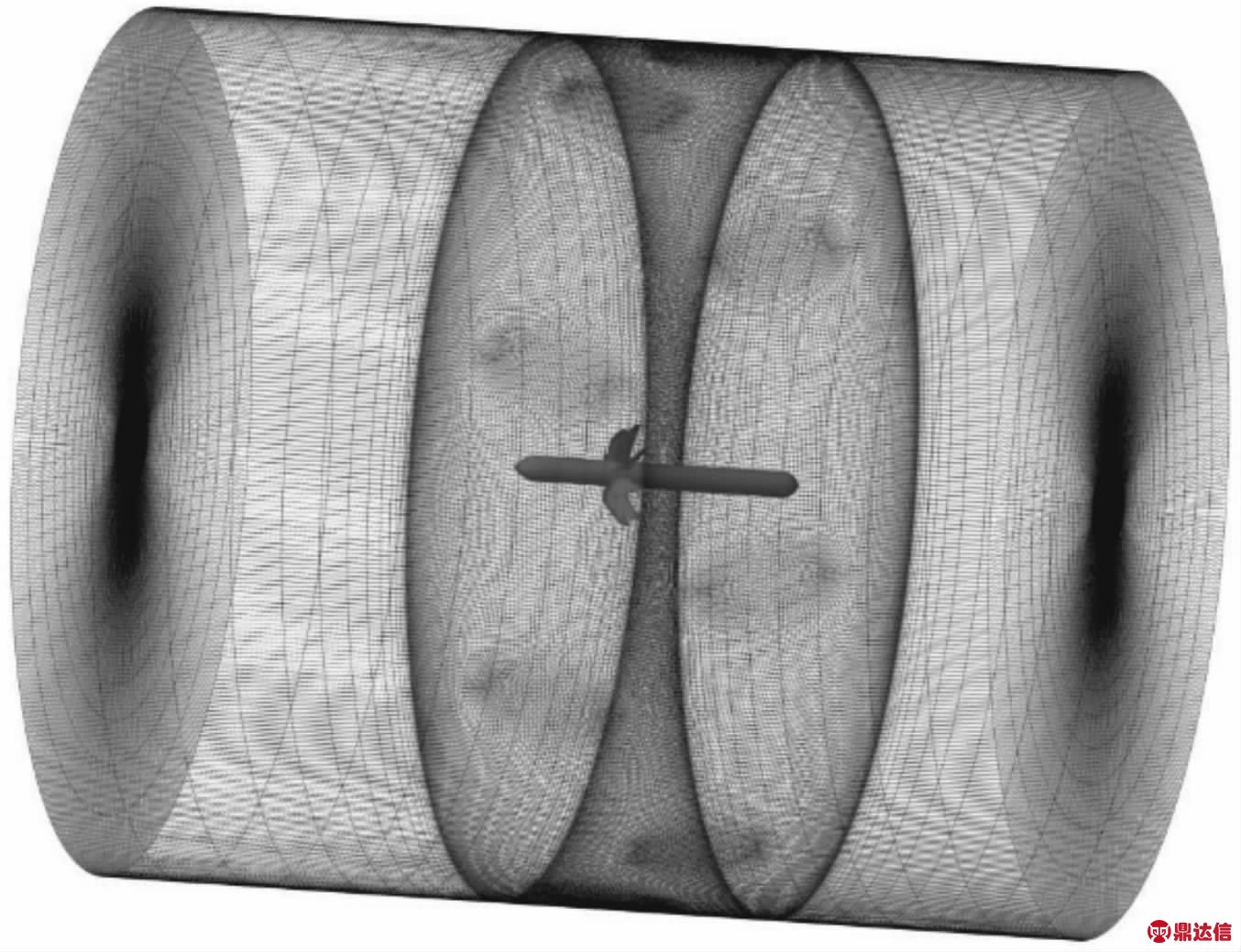
图7 最终生成的桨扇模型
3 数值计算方法
采用NUEMCA的EURANUS(欧洲空气动力学数值求解器)求解三维雷诺平均N-S方程组(RANS),并采用多重网格加速技术,多重网格法可以显著提高计算效率,加速收敛。
壁面条件采用无滑移条件,限定远场的来流速度和压强,并限定不同工况下桨叶的旋转速度即可[21]。
在有关气动/旋转机械的仿真中,最常见的是Spalart-Allmaras模型,但经校核,在巡航状态下,流经桨扇的流动是高雷诺数流动。根据NUMECA软件的相关教程,对于高雷诺数流动,宜选用带壁面函数的湍流模型,结合相关工程经验,在计算中采用 Spalart-Allmaras(Extended Wall Function)湍流模型。
由于桨扇的旋转是一种周期性运动,且本文着眼于气动性能,并不涉及与非定常现象有关的噪声或振动研究,因此采用准定常计算方法以节省计算资源。设定迭代残差为10-5时算例收敛。
4 网格生成
采用NUMECA公司的AutoGrid结构网格生成器生成该螺旋桨的结构型网格。由于桨扇是一种高度扭曲且后掠的螺旋桨,因此在生成网格时采用AutoGrid5中的对转桨扇模块,该模块对模型宽容性较高,可用于复杂外形螺旋桨网格的生成,网格质量好,生成速度快,网格参数易调整。为了使用多重网格技术,需要在划分网格时限定每个块的网格网格层数,建议值为3~4。当网格层数为N时,相应方向上的网格数必须满足以下规律:

在生成网格时,只需导入一个叶片型面即可旋转生成任意多叶片。选用适用于旋转机械的圆柱体远场,圆柱中心轴穿过螺旋桨的旋转中心。来流方向为z坐标轴正向,沿中心点向前/后延伸10倍半径生成远场,远场半径亦为10倍桨盘半径。设置第1层网格高度为3×10-5 m,最终生成的网格量为700万。检查生成的网格,可知该其满足NUMECA的计算需求。整体及局部网格示于图8、9中。
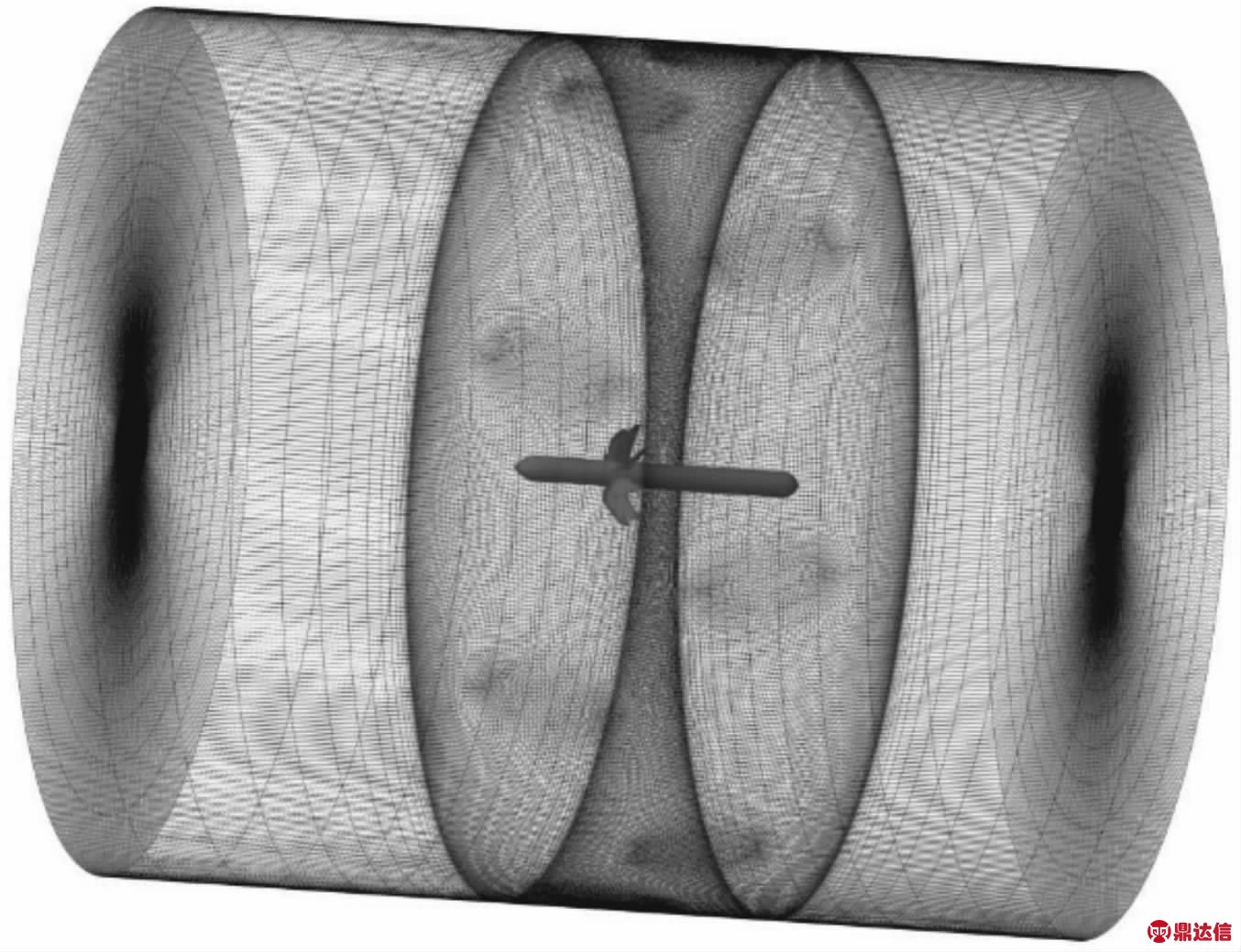
图8 远场网格
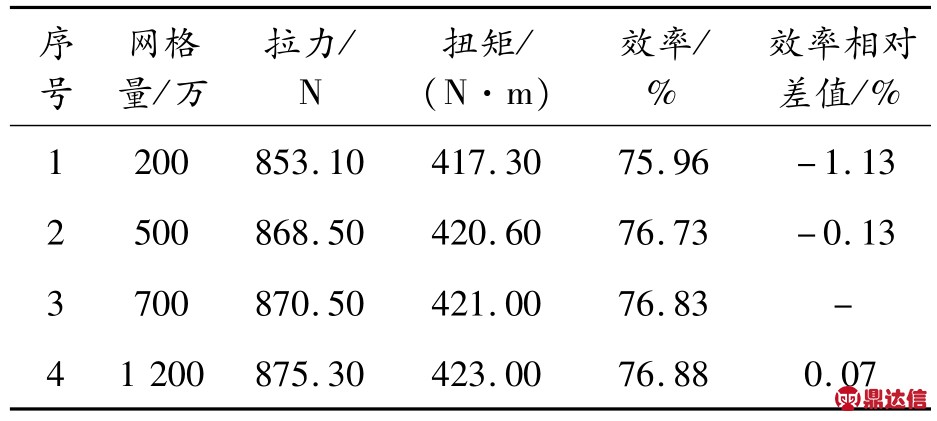
图9 桨扇叶片的整体网格及局部网格细节
5 网格敏感性分析
采用不同网格量的网格对同一桨矩的桨扇在同样条件下进行了数值仿真。计算条件如表2所示,即海平面高度的标准大气条件作为仿真条件,桨扇旋转轴攻角为0°。
表2 网格敏感性分析的计算条件
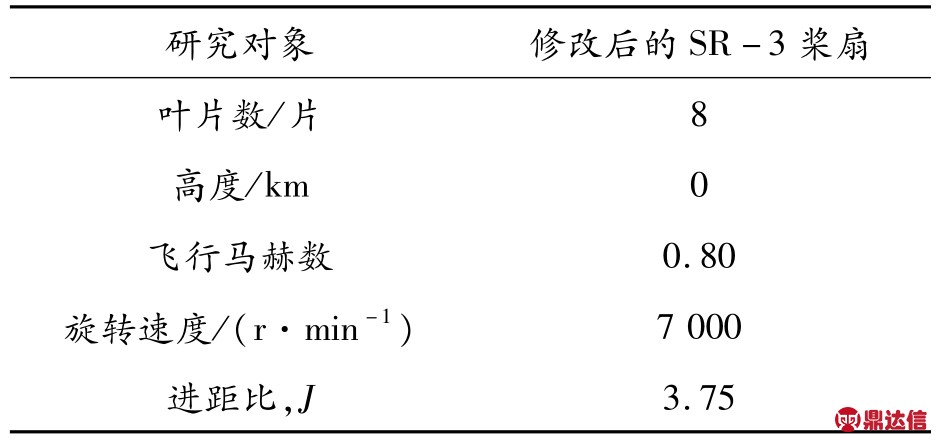
表3为用不同网格量的网格仿真得到的结果。选用桨扇最重要的气动参数推进效率η为评判依据。可以看出:当网格量超过700万后,继续加密网格,推进效率的相对变化量小于0.1%,但所需的计算时间和存储资源却成倍增加。因此,在接下来的计算中,为了节省计算资源,对于单转子桨扇,均采用网格量为700万的网格进行仿真。
表3 采用不同网格量网格得到的计算结果
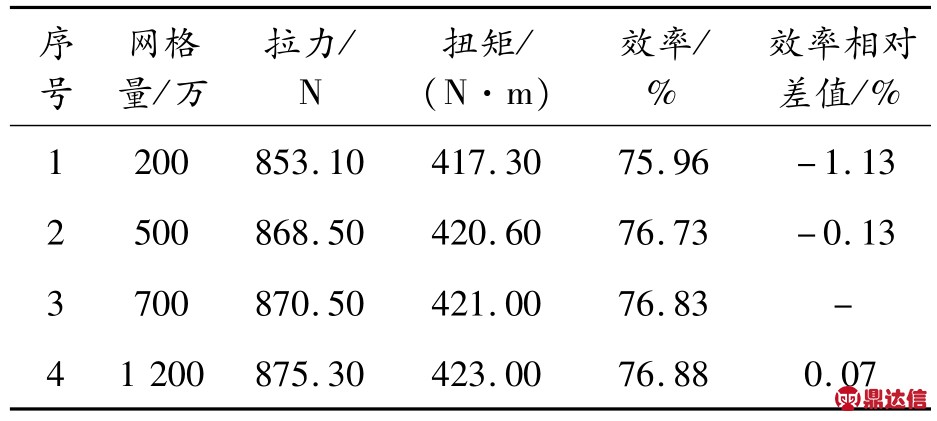
对于特定湍流模型,要得到能令人信服的仿真解,需要固壁表面的y+处于特定范围内,对于S-A(Wall Function)湍流模型,需要y+处于20~50范围内。图10为对700万量级网格仿真得到的y+分布,可以看出y+的分布可以很好地满足S-A(Wall Function)湍流模型的计算需要,因此该网格得到的结果具有一定的可靠性。
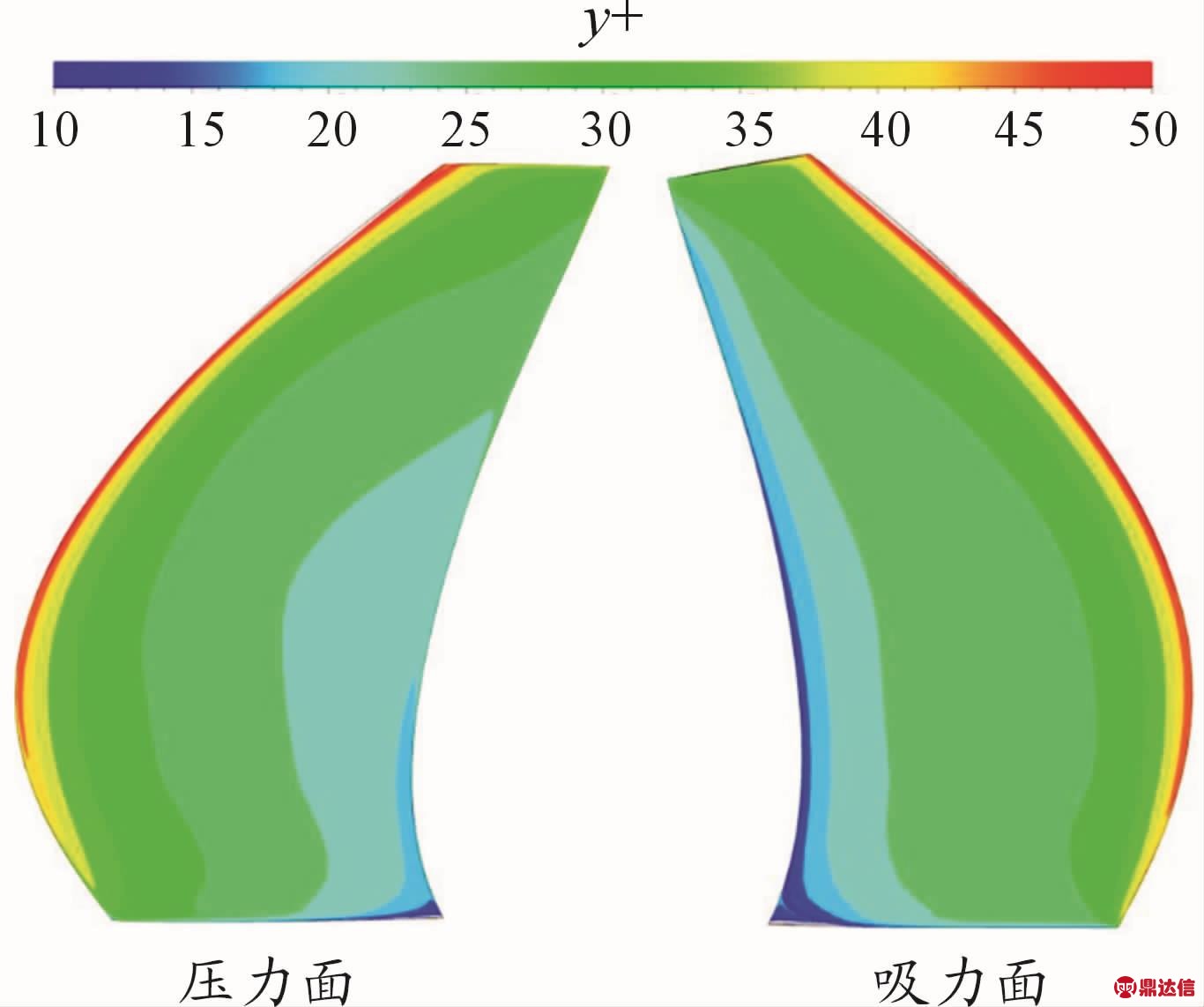
图10 叶片表面的y+分布
6 计算结果分析
首先,研究了两种典型工况下8叶桨扇的性能:对于滑跑状态,主要研究桨扇的拉力特性和载荷变化;而对于巡航状态,主要研究桨扇性能随工况的变化,即总体推进效率的变化。然后,改变螺旋桨叶片数,在巡航工况下对不同叶片数的桨扇进行数值仿真,研究叶片数对桨扇性能的影响。
6.1 滑跑工况下螺旋桨的性能
设定来流马赫数为 0.2,桨矩为 38‴[9],改变桨扇转速,得到桨扇拉力和功率系数随转速的变化曲线如图11所示。

图11 桨扇拉力和功率系数随转速的变化情况
在滑行状态下,桨扇拉力随转速的增大而增大,同时,桨扇吸收的功率也随转速的增大而增大。
图12为滑跑状态下桨扇效率随转速的变化情况。由图可知:随着转速的增大,桨扇效率逐渐减小。
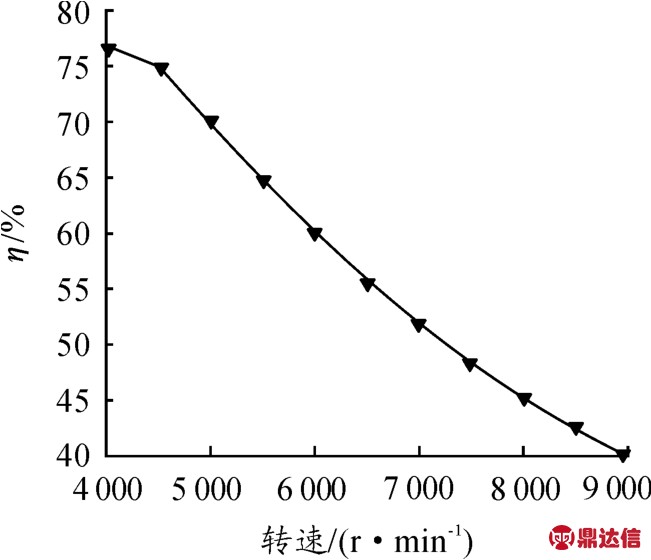
图12 滑跑工况下(Ma=0.20),桨扇效率随转速的变化情况
图13 为不同转速下桨扇特征截面叶素的绕流情况,特征截面位于75%叶高处,图中白色区域为叶素,黑色实线为流线,观察图中流线,可知随着桨扇转速的增大,流线逐渐远离壁面,产生分离区,因此桨扇效率随着转速的增大而下降。
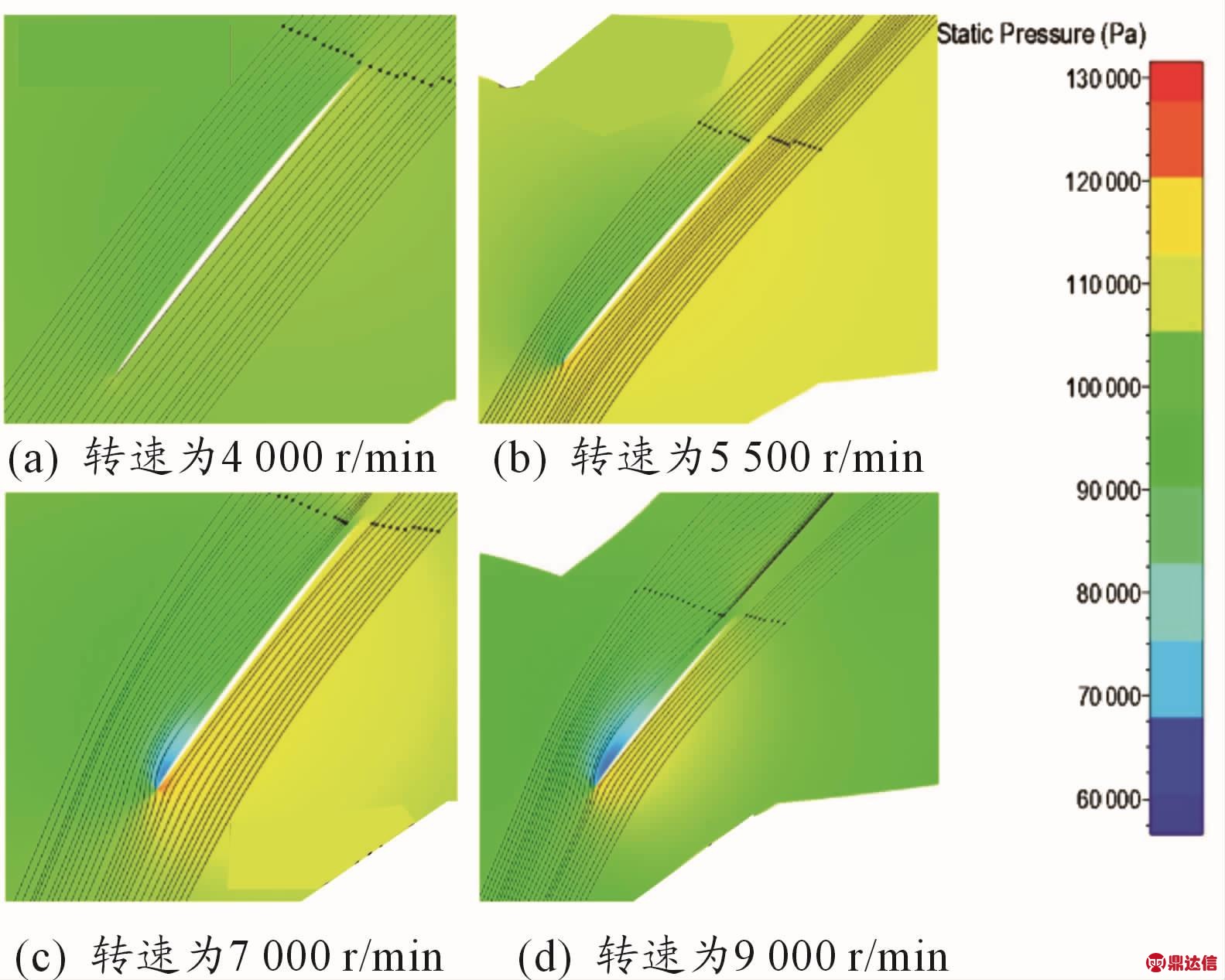
图13 滑跑工况下(Ma=0.20),不同转速下桨扇特征截面(r/R=0.75)叶素的流线分布
6.2 高空巡航状态下螺旋桨性能
根据文献[9]中的NASA风洞实验数据,设定巡航状态下桨矩为60.5°。图14为来流马赫数为0.8时,不同叶高截面叶片表面压力系数的分布曲线。可以看出,在所有叶高均有可以产生拉力的压差产生,尤其在叶根区域,不存在由于根部堵塞产生的负拉力。因此,可以得出结论:该设计方案可以调动所有叶高的叶素产生拉力,满足桨叶设计的基本需求。
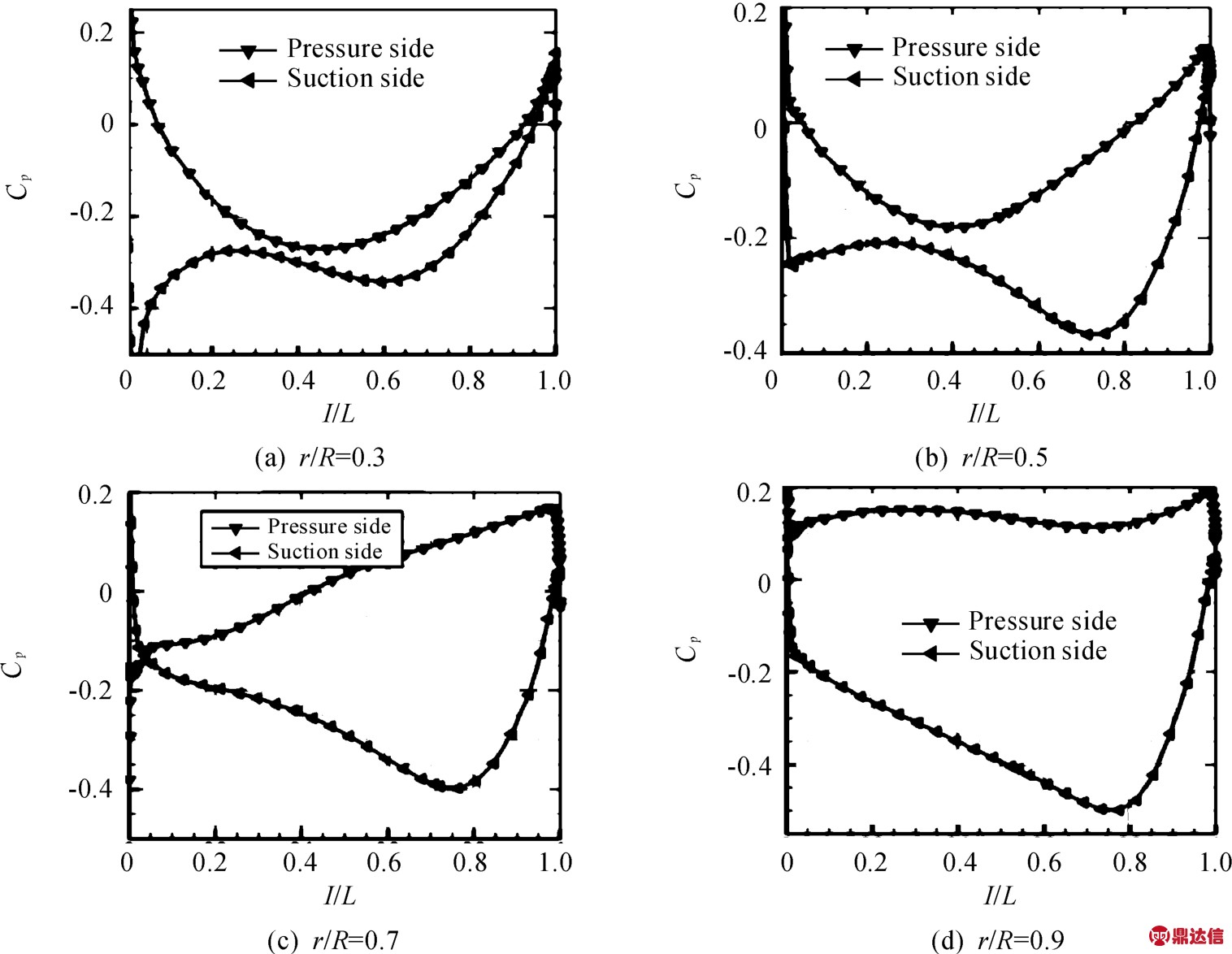
图14 来流速度为0.8 Ma时,不同叶高截面固壁表面压力系数随相对弦长的分布曲线
分别设定来流马赫数为0.70、0.72、0.75和0.80,调整转速,使不同来流状态下进距比保持不变。得到不同来流情况下,桨扇总效率随进距比的变化曲线如图14~16所示。
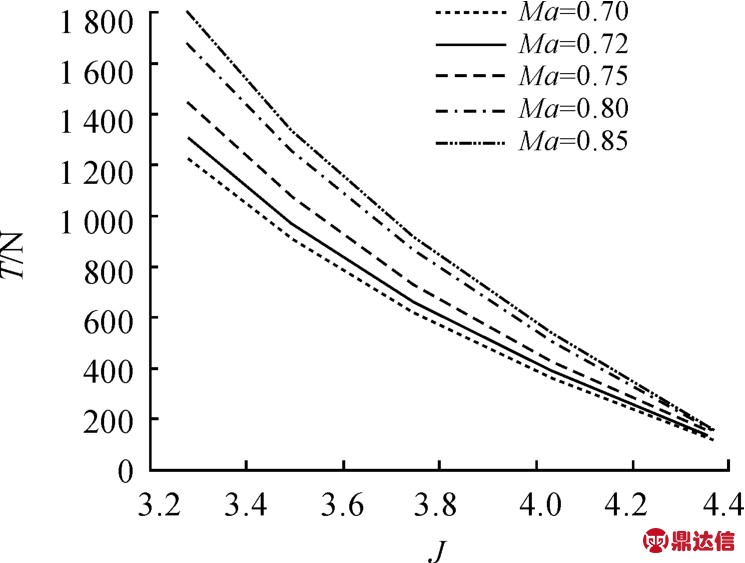
图15 不同马赫数下,桨扇拉力随进距比的变化情况
由图15、16可以看出:对于相同的来流速度,拉力和功率系数均随进距比的增大而减小。由进距比的表达式可知:对于相同来流马赫数,螺旋桨转速随着进距比的增大而减小,因此不难得出结论,拉力随桨扇转速的增大而增大,这与滑跑状态下桨扇的力学规律相同。
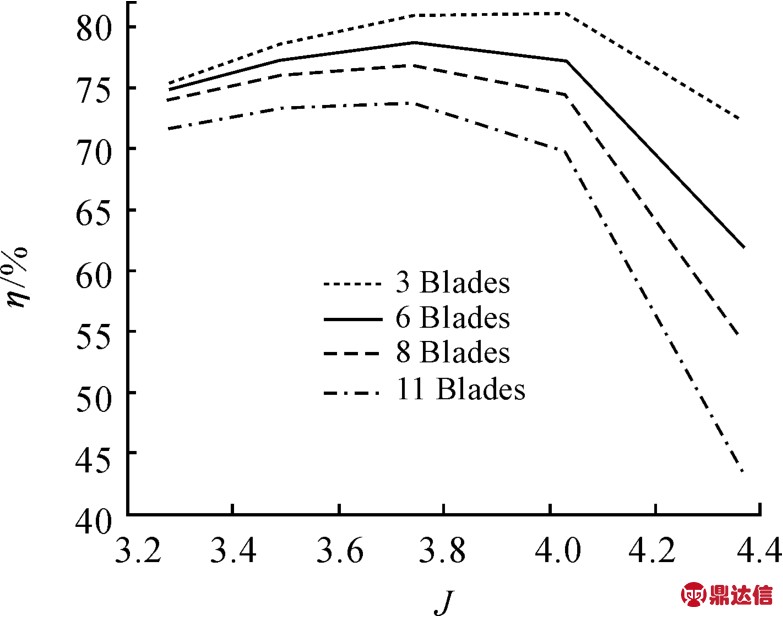
图16 不同马赫数下,桨扇功率系数随进距比的变化情况
同时,对于同一进距比,来流速度越大,拉力和功率也越大,这是因为在不产生分离和强激波时,叶素产生的升力与绕流速度成正比。而进距比相同时不同叶素绕流攻角一致,因此叶素产生的升力随来流马赫数的增大而增大。同时也可以看出:当来流马赫数不同时,不同马赫数的拉力之间的差异随着进距比的增大而减小。
因此在来流马赫数保持不变时,降低进距比可以增加拉力;当保持进距比不变时,增大飞行速度也可以增加拉力,但当进距比过大时,该效果不再明显。
图17为不同来流马赫数下桨扇效率随进距比的变化情况,保持进距比不变,桨扇总效率随马赫数的增大而降低,但马赫数从0.70到0.80的变化过程中,效率降低较小,继续增大来流马赫数,效率陡降。

图17 不同马赫数下,桨扇效率随进距比的变化情况
当来流马赫数保持恒定,改变进距比时,桨扇效率先增大后减小,这是由于当限定马赫数保持不变时,改变进距比便是改变不同叶高叶素的来流攻角。对于一类叶素,如NACA-16系列,存在叶素的最佳攻角,在此攻角下,叶素的气动性能最佳,超过该攻角,会出现流动分离,产生阻力,使效率下降。
6.3 巡航状态下桨叶数对螺旋桨性能的影响
不同于大直径传统螺旋桨,桨扇直径较小,为了充分吸收发动机产生的功率,桨扇的叶片数一般远多于传统空气螺旋桨。但增加叶片数会造成桨扇重量的增加,同时叶片之间的干涉也可能更加严重,另外,增加叶片数也会加重根部堵塞。因此,叶片数并不是越多越好。如果可以得到巡航状态下桨扇性能随叶片数的变化情况,便可以为桨扇的定型提供参考,因此选用巡航马赫数(Ma=0.80)为计算条件,改变桨扇叶片数,得到桨扇整体性能以及单桨叶性能随叶片数的变化规律很有必要。
图18~20为巡航状态下,全桨扇整体气动性能的变化曲线,分别为拉力、功率系数和效率。由图18、19可知:桨扇拉力和功率系数随叶片数的增大而增大,说明随着叶片数的增加,桨扇吸收发动机功率和做功的能力均有增大。且这种趋势随着进距比的增大而增大,这与本文第2节中不同马赫数下8叶桨扇的拉力分布类似,这是因为在高进距比工况下,桨扇旋转所做功占流过叶素表面气流合动能中的比重降低,做功绝对值较小,对总拉力的影响较小,反之亦然。
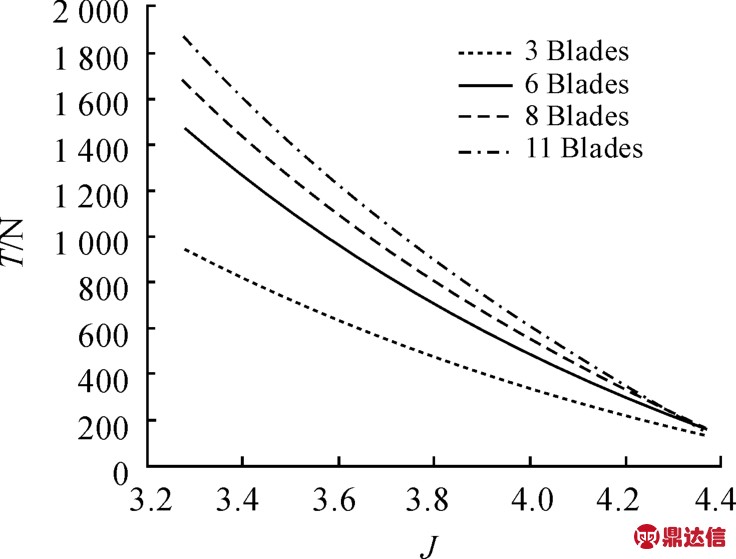
图18 巡航状态下(Ma=0.80),全桨扇拉力随叶片数的变化情况
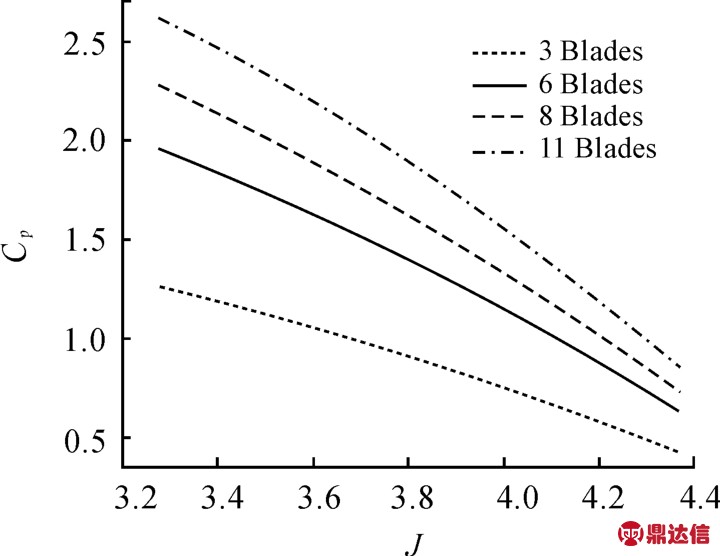
图19 巡航状态下(Ma=0.80),全桨扇功率系数随叶片数的变化情况
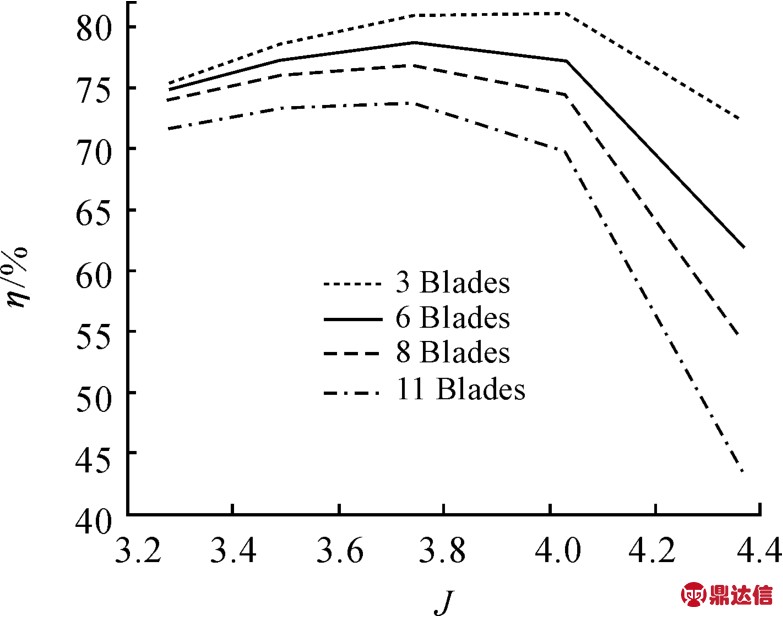
图20 巡航状态下(Ma=0.80),全桨扇效率随叶片数的变化情况
图20 为桨扇总体效率的变化情况。由图可知:桨扇叶片的变化并不影响桨扇性能曲线的整体趋势,即桨扇整体效率随进距比的增大先增大后减小,存在一个峰值点。另外,随着叶片数的增大,各个进距比下,桨扇效率逐渐下降,这是由于随着叶片数的增多,根部堵塞加剧,且叶片之间存在相互干扰,也会影响整体效率。
图21和图22分别为巡航状态下,桨扇叶片拉力和功率系数随叶片数的变化情况。随着叶片数的增大,单桨叶产生的拉力和吸收的功率均有所减小。因此,当桨叶数过少时,叶片所受应力较大,容易产生震动和噪声,甚至出现强度失效。因此,在应用桨扇至飞行器时,应多方面权衡,合理确定参数。
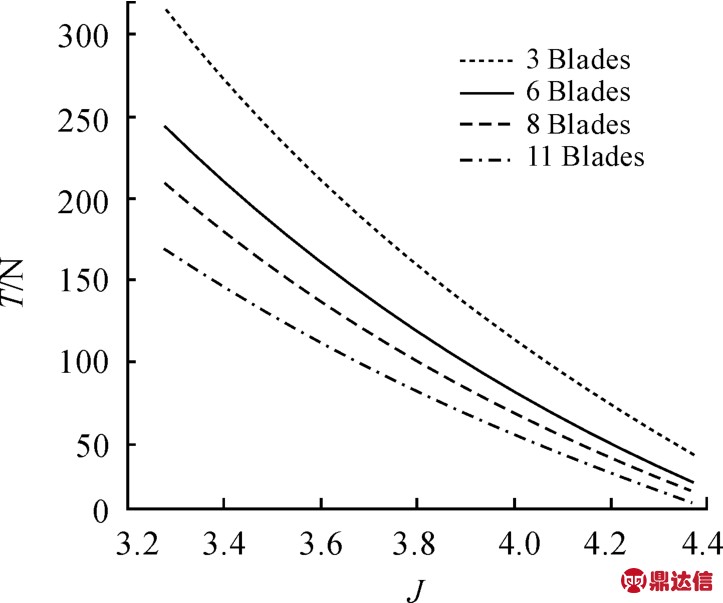
图21 巡航状态下(Ma=0.80),单片桨扇叶片拉力随叶片数的变化情况
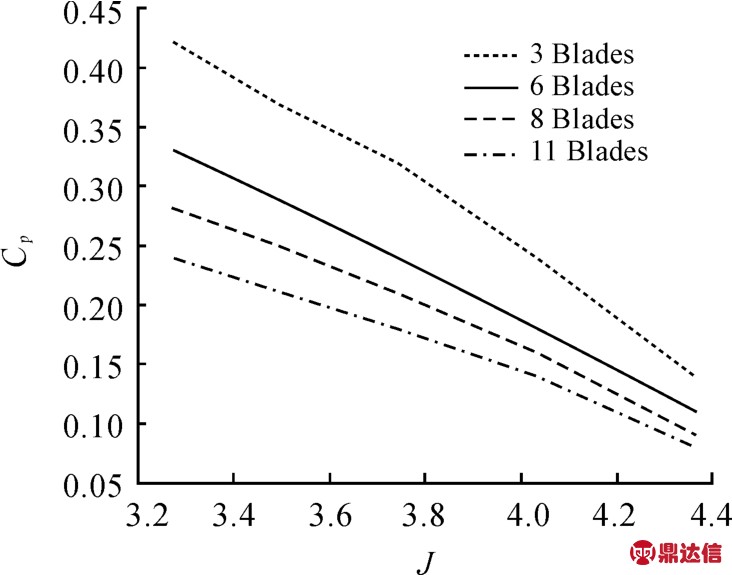
图22 巡航状态下(Ma=0.80),单片桨扇叶片功率系数随叶片数的变化情况
7 结论
在NASA的SR-3桨扇的基础上生成了一种桨扇构型。采用定常数值模拟方法,研究了起飞状态以及巡航状态下桨扇的气动性能变化,并针对设计点,研究了叶片数的影响,得到以下结论:
1)生成的桨扇构型在设计Ma=0.80时,最高效率为77%。
2)滑跑状态下,进距比J在0.70~1.65范围内,桨扇拉力和功率均随转速的增大而增大,效率随转速的增大而减小,最高效率为76.7%。
3)巡航状态下,对于同一进距比,拉力和功率随来流速度的增大而增大,随着进距比的增大,该效应逐渐减弱;随着进距比的逐渐增大,桨扇效率先增加后减小,存在峰值,最高效率为77%。
4)对于Ma=0.80的巡航状态,桨扇总拉力和总功率随叶片数的增大而增大,桨扇总效率随叶片数的增大而降低;单个叶片的拉力和功率随叶片数的增大而减小,平均每增加一片叶片,单个叶片的拉力降低9.2%,功率降低7.8%。