摘 要:为满足城轨车辆部件轻量化、小型化、集成化的要求,通过对城轨车辆牵引变流器的功能进行分析,明确了牵引变流器控制单元应具备系统级和逆变器级控制、通讯、信号处理和故障诊断等功能,从而提出以控制系统模块、数据处理和监控模块、信号处理模块组成的紧凑型牵引控制单元架构。在硬件设计中,采用微控制单元(MCU)完成系统级控制;采用数字信号处理器(DSP)完成逆变器级控制;采用可编程逻辑器件(FPGA)作为MCU和DSP的协处理器,并负责所有对外部电路的接口;采用开关量处理电路、模拟量采集和处理电路、脉冲输出及反馈处理电路,对牵引变流器的各类型信号进行处理,完成控制系统模块指令的输出和系统状态的采集。通过型式试验和牵引系统地面联调试验,验证了牵引变流器控制单元的性能符合设计要求,适用于集成度较高、空间相对紧张的场合。
关键词:城轨车辆;牵引变流器;控制单元;系统结构;模块设计
牵引变流器(简称变流器)是城轨车辆牵引传动系统的核心设备,其控制方式通常是基于脉冲宽度调制(PWM)技术,将直流电源转化为调压调频的电源以驱动异步电机(简称电机)。控制单元是变流器的重要组成部件,其作用是通过采集供电直流电压、电机相电流以及功率模块温度,从而控制、监控、保护变流器。随着技术的不断进步,城轨车辆部件正在向轻量化、小型化、集成化发展,如复合牵引功率模块,需将逆变器功率部件和制动斩波器功率部件及驱动、直流环节电容等通过复合母排进行安装,同时集成电压电流传感器和变流器控制单元共同作为变流器的核心部件。
传统的控制单元一般采用模块化设计,将模块的功能通过不同类型的板卡实现,并将这些板卡统一安置于1台控制单元机箱内,然后通过各板卡的对外接口与变流器的各类信号线连接,再通过背板总线的方式实现板卡的内部连接,统一完成控制功能。这种结构非常成熟,并且具有良好的扩展性,可依据机组要求的不同增减相应板卡,但其对空间的需求较高,在变流器设计时需要预留控制单元室。因而,这种控制单元的结构特点和接线方式决定了其不适合与复合牵引功率模块配合使用。
本文在分析变流器控制单元功能需求的基础上,针对采用复合牵引功率模块的城轨牵引变流器,研究1种采用底板加少量扣板的紧凑型控制单元设计方法,并用于DC1 500 V供电制式的牵引变流器。
1 控制单元的设计需求分析和基本架构
城轨车辆典型DC1 500 V牵引传动系统的总体结构如图1所示。图中:虚线箭头标出的是控制单元需要采集或控制的信号。该牵引传动系统为架控模式,由高速断路器、变流器和电机组成。变流器采用强迫风冷方式,冷却风机安装在箱体内部。
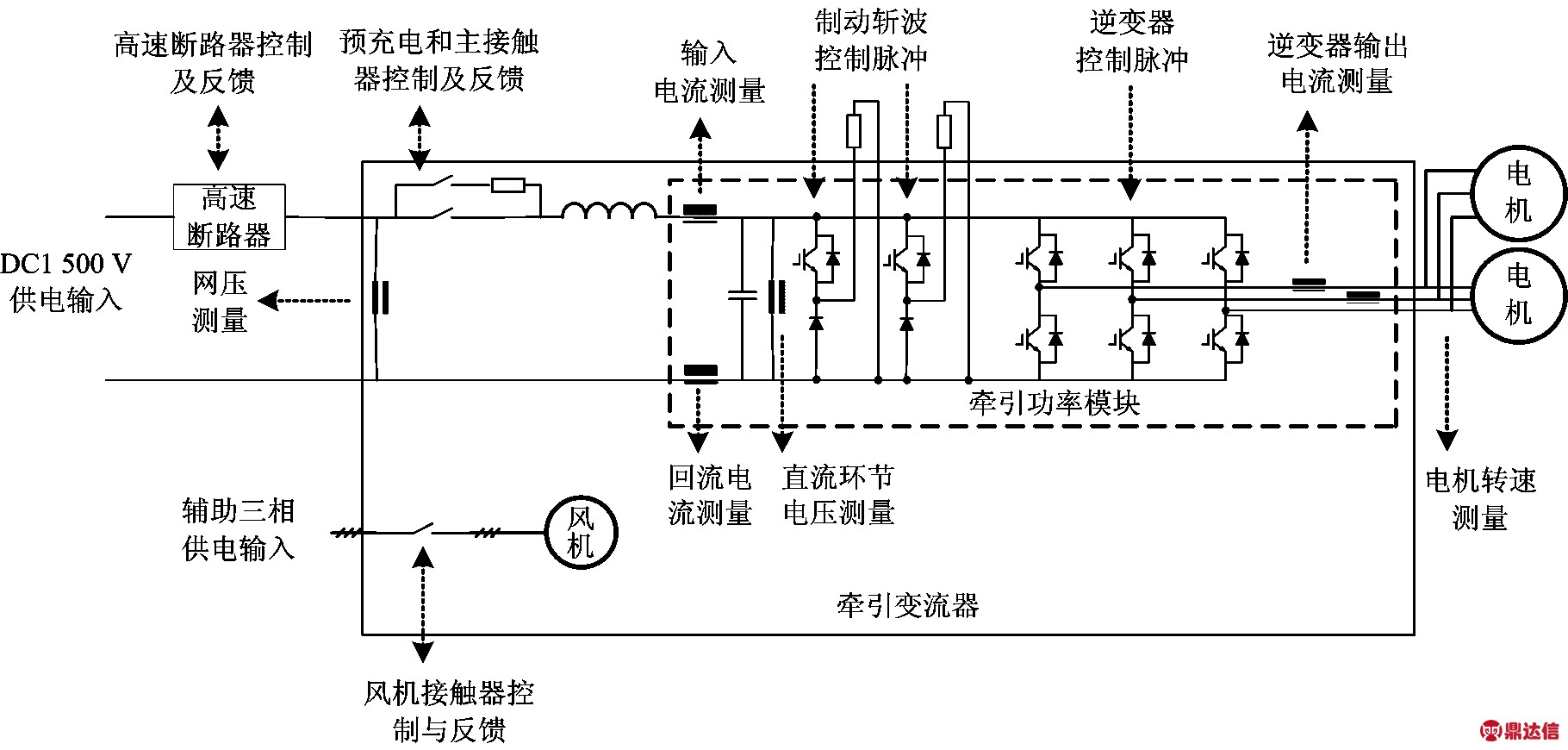
图1 城轨车辆典型1 500 V牵引传动系统结构图
变流器的主电路包括功率输入电路和牵引功率模块。
运行过程中,控制单元需对图1中的各类信号进行测量和监控,驱动各类执行机构,完成对变流器的控制。根据上述分析,可将变流器控制单元的需求概括为:接收上位机或列车网络的控制指令,驱动执行机构,完成如闭合断开各类接触器、启停逆变器和制动斩波装置等变流器系统级操作;执行牵引控制算法,产生牵引功率模块的PWM驱动脉冲,完成电机转矩的闭环调节;在机组运行时,实时监测系统的网压、直流侧电压、直流侧电流、电机电流、转速、变流器模块温度、各接触器状态反馈等信息,执行软件故障判断、保护。
控制单元的需求可从功能上分解为3个模块加以实现:控制系统模块、数据处理和监控模块以及信号处理模块。
(1)控制系统模块,包括系统级控制和逆变器级控制两部分:系统级控制,包括与车辆总线进行通讯,从车辆总线接收当前车辆运行方向、当前载荷以及手柄力矩指令值,从而结合设计特性曲线、给出电机输出转矩的正负和大小,执行各种逻辑控制,包括接触器闭合断开,逆变器和制动斩波器激活封锁等指令,完成故障诊断等任务;逆变器级控制,包括逆变器驱动控制和对制动斩波装置的控制,是牵引传统系统的核心部分,根据转矩、磁链预置值,结合采集到的电压、电流、速度等数据,执行控制算法,实现PWM控制和脉冲生成、电机控制、黏着控制、参数辨识等功能,执行牵引算法,驱动逆变器和电机,控制制动斩波电路等。
(2)数据处理和监控模块:是连接控制系统模块和信号处理模块的桥梁,并行处理和执行控制系统模块发出的针对不同控制对象的控制指令,同时对信号处理模块的输出进行统一处理,将其转换为控制系统模块可读的数据。
(3)信号处理模块,包括3部分:开关量处理电路、功率半导体器件的驱动控制和反馈状态监测,通过触点控制各类断路器和接触器;模拟量处理电路,负责各类模拟量的采集和处理,将系统中传感器输出的模拟量转换为处理器可读的数字量,以完成牵引计算,同时对关键模拟量进行监控,用以系统保护;脉冲输出及反馈处理电路,将控制脉冲从控制单元发送至功率开关器件的驱动部件,驱动各开关管,并通过读取反馈状态对开关管进行监控。
综合考虑上述功能,1个基本的控制单元的架构如图2所示。
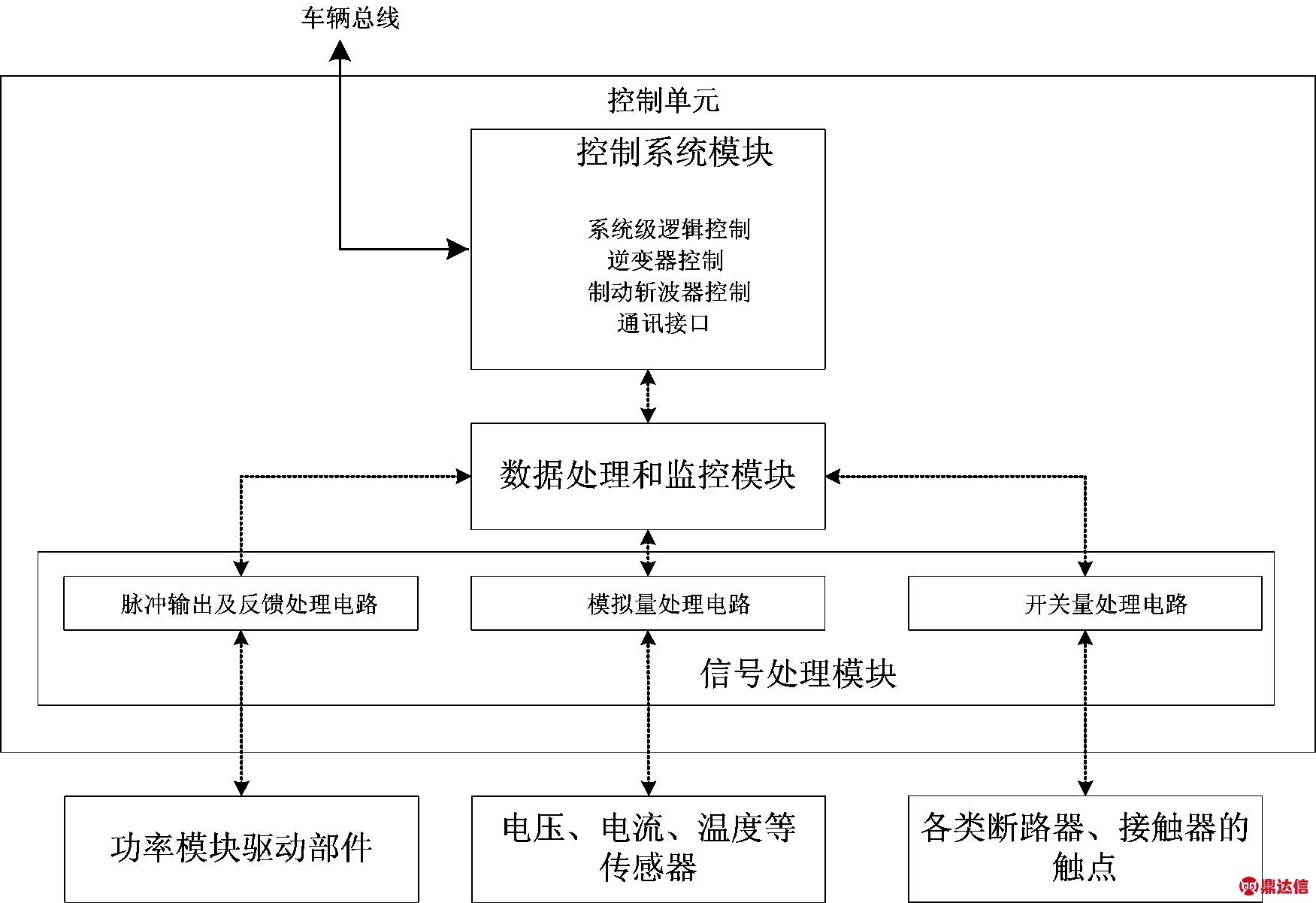
图2 城轨车辆变流器控制单元架构
2 控制单元的硬件设计
控制单元各模块的硬件设计在结构上采用底板加扣板的方式,底板直接面向变流器,集成各类信号处理电路和对外通讯接口;功能相对独立的部分可设计为扣板。统一的硬件平台可节约成本,便于维护。
2.1 控制系统模块
系统级控制和逆变器级控制要求的是2种不同的能力。系统级控制要求的是较强的逻辑处理能力和处理通讯协议的能力,为此使用具备顺序执行程序结构和丰富外设、广泛应用于工控领域的微控制单元(Micro Controller Unit,MCU)完成系统级控制;逆变器级控制要求的是强大的实时计算能力,为此使用具备专门的乘加结构、大量运算单元、实时计算能力强大的数字信号处理器(Digital Signal Processor,DSP),逆变器驱动控制处理器之间的通信可通过共享RAM完成,共享RAM和数据采集处理可在数据采集处理和监控模块中一并实现。
出于行车安全和故障诊断的考虑,使用非易失性存储器存储故障数据,以配合MCU存储故障信息。此外,视处理器芯片类型,考虑配备相应的程序存储器。
目前主流的MCU和DSP芯片的接口电压均为3.3 V,内核电压一般为1.2和1.8 V等级,在硬件设计时应使用带有电压监测功能的稳压器为处理器供电,在任何电压等级发生异常时都应触发系统复位信号。同时为防止软件故障引起系统工作异常,控制系统的复位源也应包括从MCU和DSP引出的看门狗信号。2个处理器及其外围电路构成的控制系统模块如图3所示。
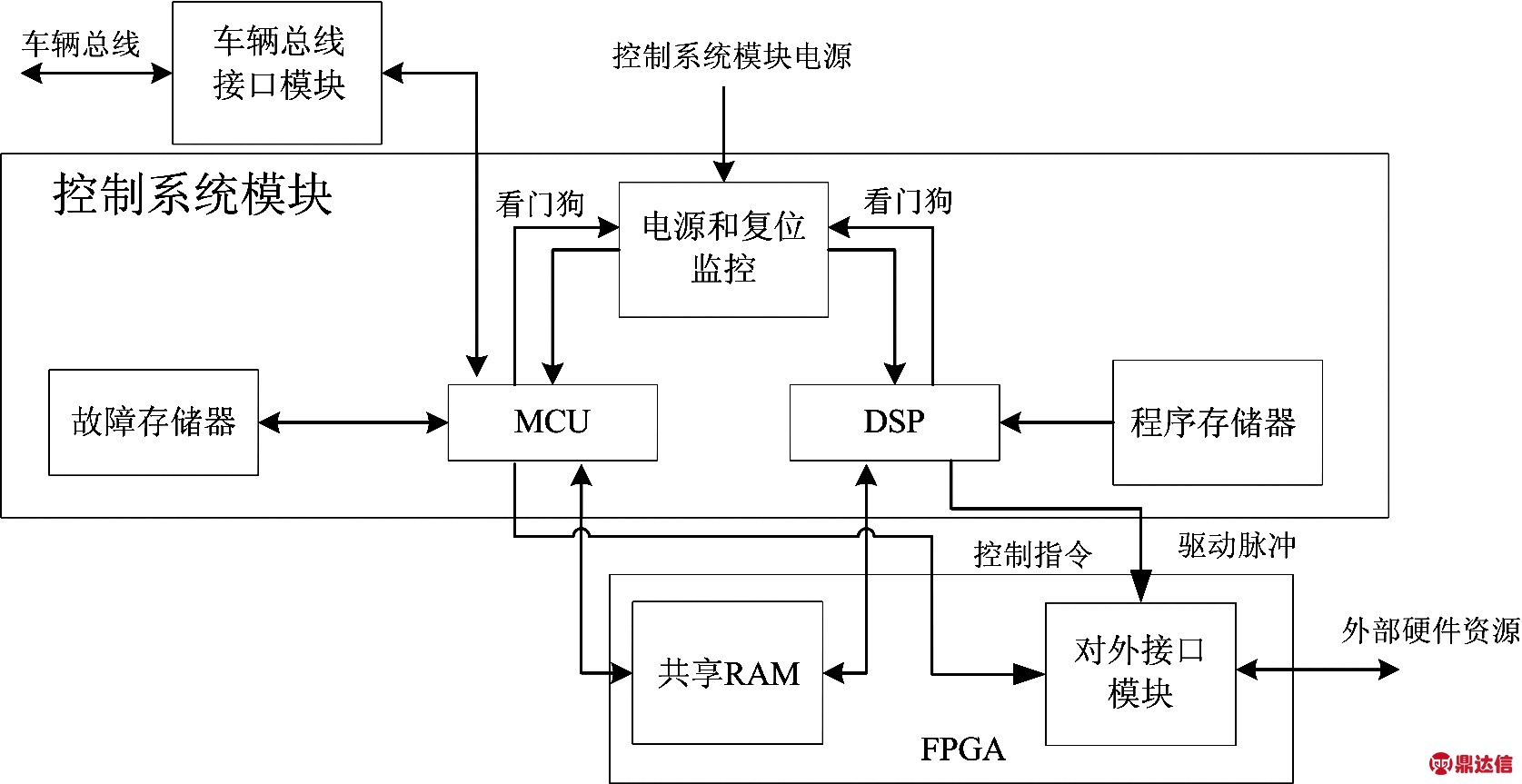
图3 控制系统模块简图
2.2 数据处理和监控模块
控制单元面对的控制对象和监控对象由于种类各不相同,而且彼此之间相对独立,MCU和DSP的功能相对固定,不具备大规模的并行处理能力,因此采用具备丰富的接口、大量的存储器和高速并行处理能力并可灵活对硬件功能进行编辑的可编程逻辑器件(Field Programmable Gate Array,FPGA)作为MCU和DSP的协处理器,负责所有对外部电路的接口。FPGA的结构特点决定了它可同步对其所有的输入进行监测,因此也很适合对牵引传动系统运行中的关键数据进行监控,并执行时效性要求较高的保护动作。MCU和DSP可统一通过FPGA与外部资源进行交互,基于FPGA的IP软核可搭建用于 MCU,DSP和FPGA之间通讯的双向三口RAM[1]。
2.3 信号处理模块
针对变流器不同类型的信号进行处理,完成控制系统模块指令输出和系统状态的采集。
2.3.1 开关量处理电路
控制单元面对的开关量主要是主断路器、接触器等。控制单元通过控制接触器线圈的得电、失电,驱动接触器主触点的闭合、断开,同时检测辅助触点的状态反馈。依据应用场合的不同,接触器线圈的电压等级一般为110或24 V,辅助触点的电压等级一般为24 V。从设计思路看主触点和辅助触点的驱动并无区别,即首先必须在控制单元的信号侧和接触器的线圈侧进行隔离,这一般是通过光耦或继电器实现的。选择光耦和继电器时,应充分考虑到其能承受的电压和电流是否满足目标接触器线圈的需求。同时,为保护光耦或继电器不被冲击和浪涌损坏,应在输入、输出端设计过压吸收电路[2]。开关量输出信号由控制系统模块结合数据处理和监控模块发出,通过缓冲电路增强驱动能力,再通过光耦或继电器对线圈电流的通断进行控制;开关量输入信号经过压吸收回路后,通过分压调整为适合输入光耦的电压等级,经缓冲电路反馈给控制系统模块。
2.3.2 模拟量采集和处理电路
变流器的模拟量信号一般包括电压、电流、速度和温度信号。需根据每类信号的传感器输出类型和信号用途分别进行信号调理,并确定其采样和模数转换的方式。
电压和电流的测量通常使用磁平衡式的霍尔传感器,一般为双极型供电,输出电流信号。以图1为例,使用电流型传感器测量的模拟量包括网压、中间直流环节电压、网侧输入电流、网侧回流、逆变器输出U相和V相电流。对上述模拟量的处理可分为如下3个方面。
(1)信号采集和调理:尽管传感器的供电电压不同,但是均输出电流信号,因此采集和调理方式可采用同一种设计。由控制单元提供采样电阻,将输入的电流信号转换为电压信号,再通过调理电路调整为合适的电压范围。
(2)A/D转换:将采集和调理后的模拟量通过A/D转换转成数字量,并存入数据处理和监控模块,以供控制系统模块读取。常用的A/D转换方式包括逐次比较法和压频转换法。
采用压频转换方式时,其转换精度与阻容电路中的电容值精度有关,电容值的精度一般不高且易受到温度变化的影响,需要对其进行周期性的校正[3]。这种转换方式从硬件和软件上都需要进行更多的工作,但其优异的抗扰性能和取平均值的特性使其成为在执行牵引控制算法时很好的选择。
(3)电压电流的超限保护:以上模拟量既是完成牵引控制算法的必要数据,也是系统运行的关键,必须加以监控,以防发生过压、过流等严重故障,损坏机组。当故障发生时,由于软件运行时有其固有的周期,难以在第一时间发现故障并进行保护,需要在硬件设计时搭建模拟量超限保护模块,以便用最快的速度识别故障,执行保护动作。保护模块通过将调理后的模拟量信号与预先设定的保护限值进行比较,由数据处理和监控模块读取比较的结果,可在采集的模拟量超出限制值时的第一时间做出保护动作。
当监控的模拟量为交流量时,对其负半周也需要检测是否超过限制值,因此需对模拟量作绝对值处理。
设定保护限值时,可分级设定。通过参考电压结合可调电阻进行分压,或者采用DA转换器方式灵活设置保护限值,但最高一级的保护限值应使用固定阻值的电阻对参考电压进行分压,保证可靠性。
电流型传感器通道的总体设计方案如图4所示。
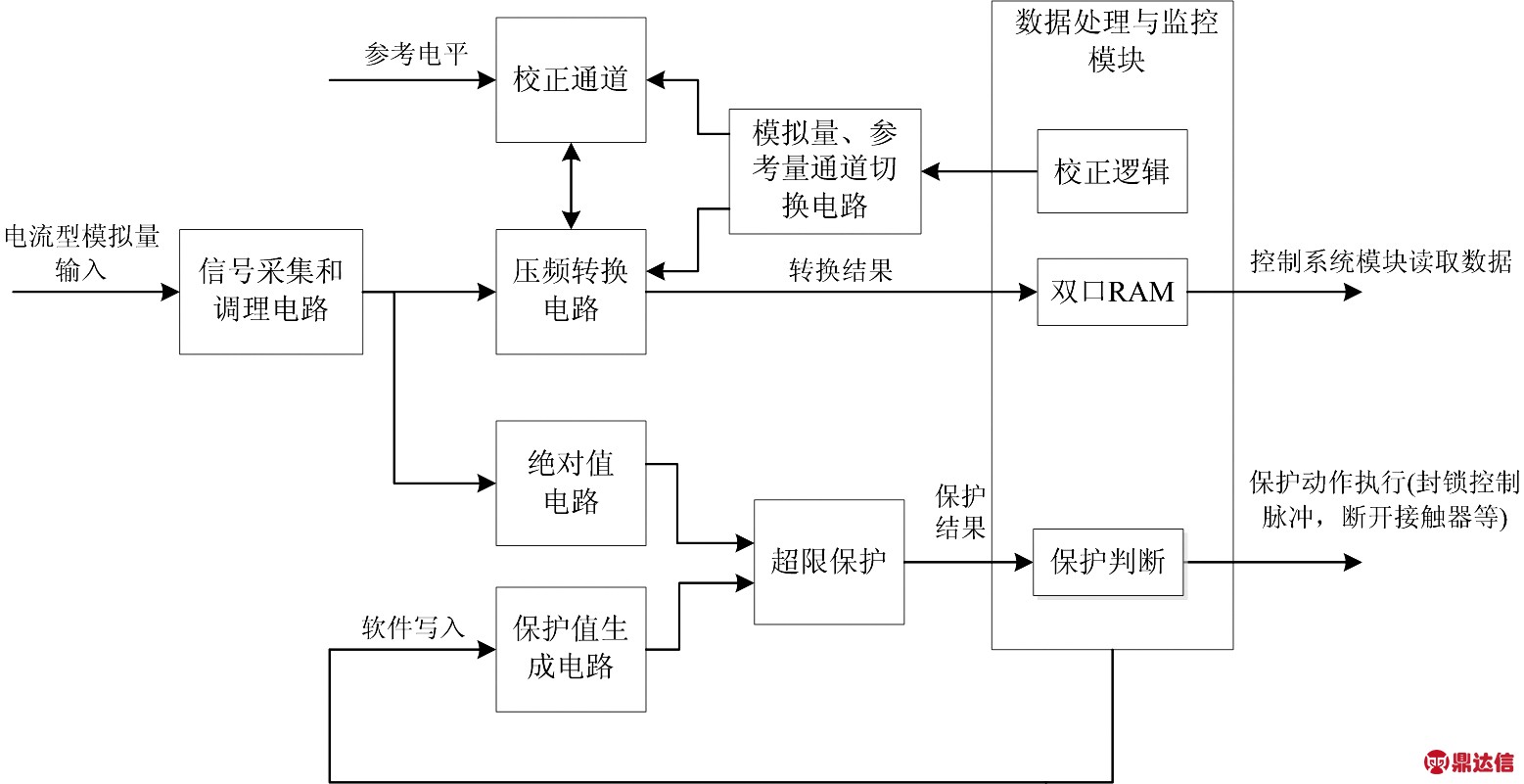
图4 电流型模拟量采集和处理电路设计方案
速度信号来自电机的速度传感器,各电机的速度传感器供电均取自控制单元,在控制单元的速度传感器供电电源侧应加以隔离。若输出的速度信号为正弦波,可预设1个低于输出信号峰值的参考电压,当输出信号高于参考电压时输出高电平,低于参考电压时输出低电平,从而将正弦波信号转换为方波信号。在数据处理和监控模块中建立计数器,并行地对各路方波信号按照测周法进行测量。可以以同一组速度信号中的某一路为基准,在其上升沿到来时测量另一路信号的状态,从而判断车辆运行方向。变流器中测量温度的传感器以Pt100型温度传感器较为常见,使用恒流源给其供电,并测量两端电压,得出电阻,再求出温度。由于Pt100型温度传感器的布置一般位于功率模块或进出风口附近,与控制单元的距离较远,需要较长的引线,而其温度系数只有0.385 Ω·℃-1,引线电阻产生的测量误差可能影响测量的准确性,可采用四线制接法,从传感器两端引出2组线,将电流线和测量线分开,测量线上的压降极小,可较好地测出电阻两端的压降。
2.3.3 脉冲输出及反馈处理电路
在变流器中,控制单元将控制脉冲发送给功率模块的驱动电路,驱动IGBT的门级,而IGBT的工作电压可达到数千伏。因此在选择控制脉冲输出和反馈的实现方式时,需要满足主电路和控制单元的高压隔离要求。城市轨道交通领域中广泛使用光电隔离的方式,这包括光耦隔离和光纤隔离方式。光耦隔离具有体积小、电路结构简单、成本较低的优点,但存在隔离电压不高、传输延时较大、容易老化等缺点。光纤隔离可实现长距离的完全电隔离传输,具有抗电磁干扰能力强、隔离电压高、可靠性高等优点[4],但光纤的强度不高,对走线的弧度、线束的固定和插头的连接可靠性有更严格的要求,在变流器箱体和功率模块设计时需要注意。在条件允许的情况下,推荐使用光纤隔离方式。
控制单元在硬件功能分配上,由电机控制的微处理器直接发出控制脉冲,在可编程逻辑器件中进行死区时间、最小脉宽的设置(部分微处理器也可在脉冲生成时就进行这些设置)。由可编程逻辑器件判断脉冲反馈状态,在反馈状态异常时,封锁脉冲,保护IGBT模块,并将故障状态反馈给控制系统模块。
3 设计实例和试验验证
依据上述设计思路,结合城轨车辆变流器的研制,设计了1台城轨牵引控制单元,考虑到通用性,将控制系统模块设计为1块扣板,使其可应用于不同类型控制单元的底板,称为核心板;电压、电流传感器的信号采集和调理部分设计为1块扣板,称为采样板,以方便更换;因为数据处理和监控模块与信号处理模块联系密切,所以将二者设计为底板。将高速电路置于中心位置,低速部分置于外围,免除了采用背板设计时高低速信号混杂的情况,降低了走线难度;同时将传统的箱体加背板式的控制单元对“体积”的要求转换为了底板对“面积”的要求,极大减小了控制单元的实际体积,可以很方便地集成于牵引功率模块上。
3.1 部分电路功能设计实例
3.1.1 压频转换通道设计实例
图5给出1个压频转换通道设计实例。采用压频转换器AD654搭建转换电路,其中Uin为待测输入电压,fout为输出频率,选取输入电压限流电阻R1=39 kΩ,参考电压限流电阻R2=10 kΩ,运放负反馈电阻R3=10 kΩ,接地电阻R4=10 kΩ,谐振电容C=680 pf,参考电压Uref=-5 V。根据其芯片手册提供的公式,可得其压频转换公式为
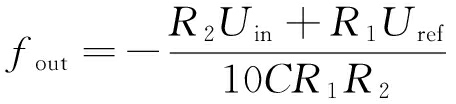
(1)
分别调节待测输入电压U in的值,并对输出频率fout进行测量,结果如图6所示。从图6可见,该转换电路具有良好的线性度,便于建立转换公式,完成从模拟量到数字量的转换。
这种转换方式本身是1个积分过程,相当于经过了低通滤波[5],对高频干扰有着天然的滤除作用。对压频转换电路分别输入5 V的直流电压和叠加频率为50和100 kHz、峰值为800 mV高频谐波的5 V直流电压,其转换结果如图7所示。由图7可见,在被测模拟量中含有高频谐波时,也能较真实地反映出基波分量的大小。
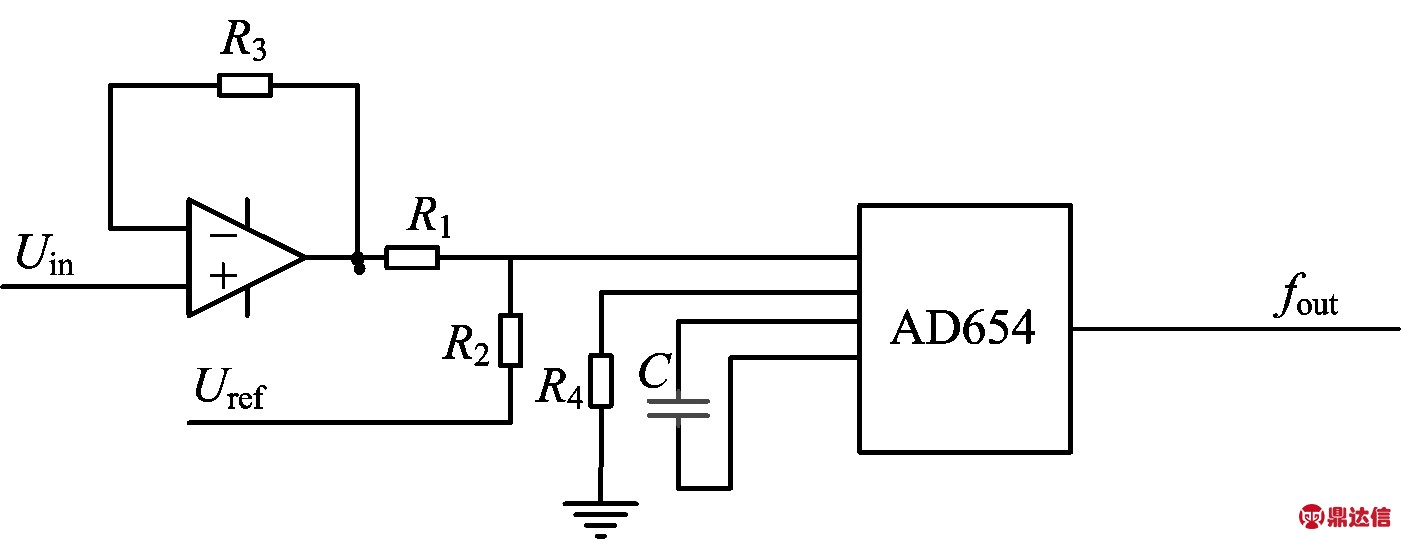
图5 压频转换通道设计实例
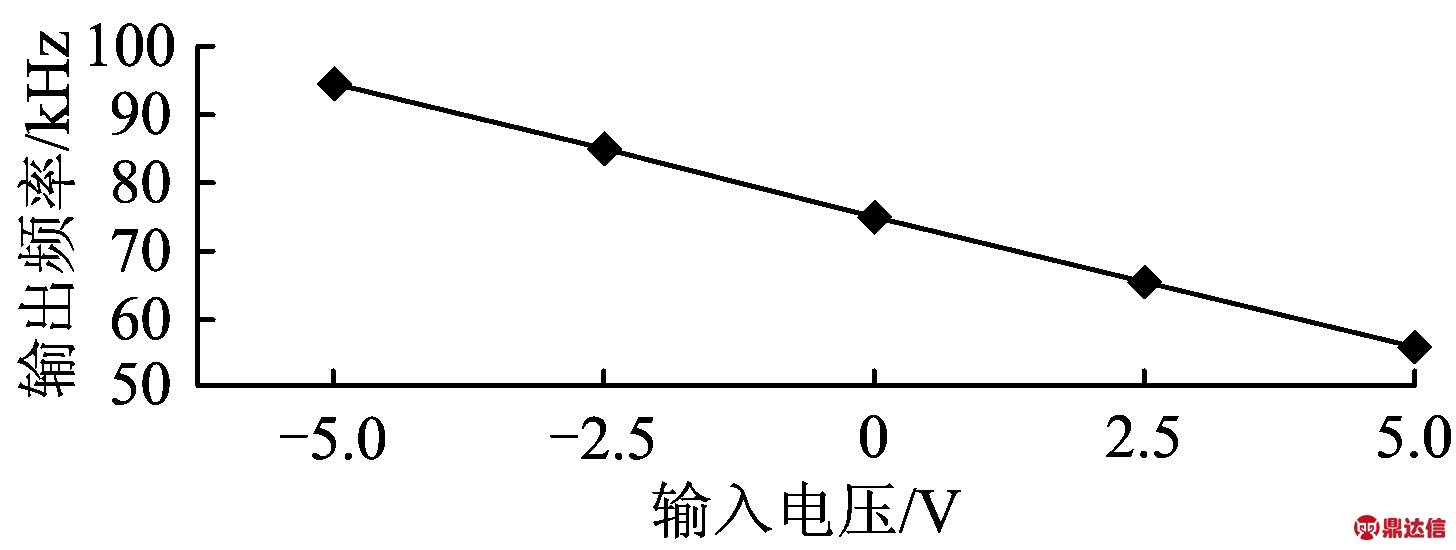
图6 典型输入电压的压频转换结果
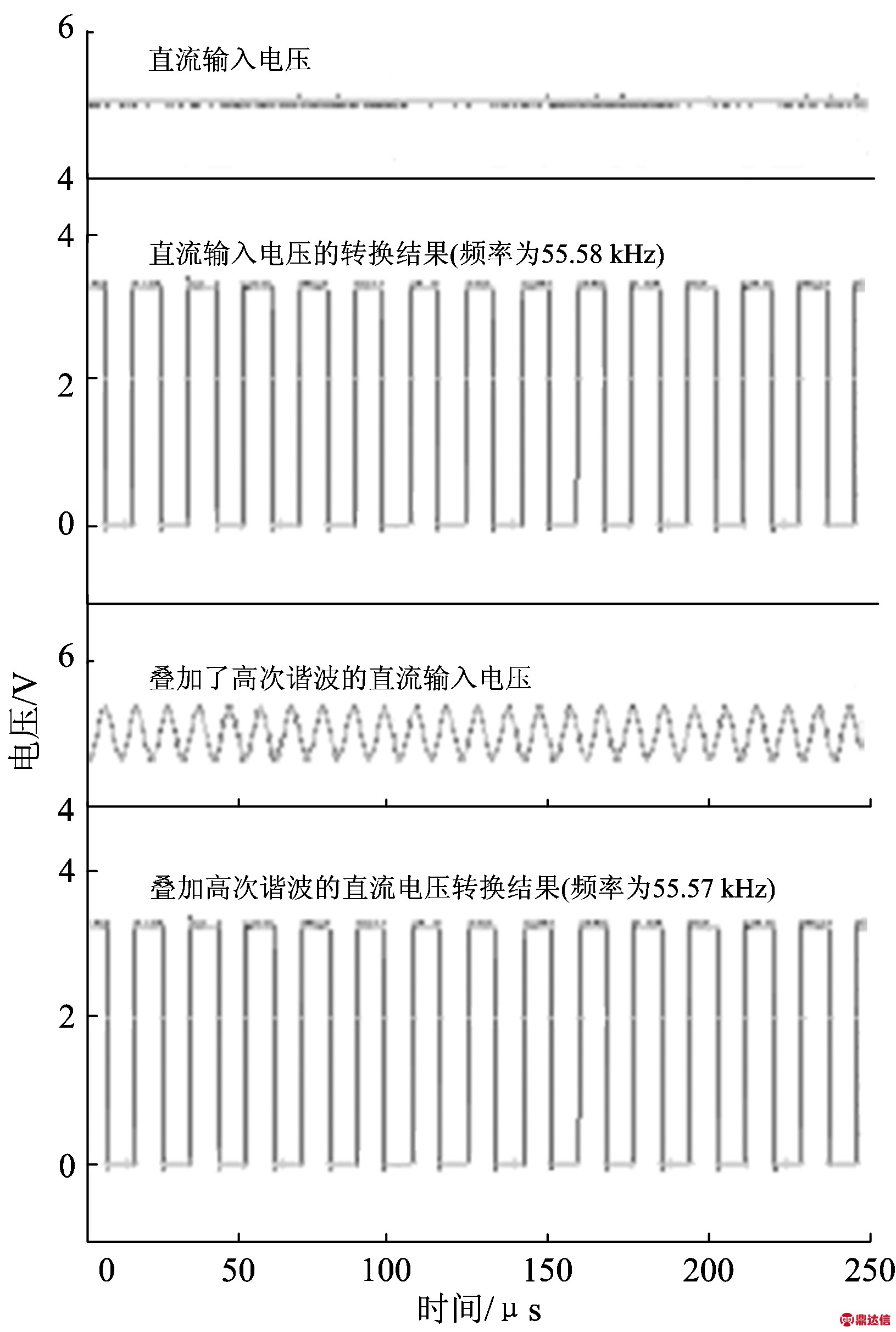
图7 5 V直流输入电压和叠加了高次谐波的5 V直流输入电压与转换结果的对比
3.1.2 绝对值生成电路设计实例
绝对值生成电路可通过运算放大器和二极管搭建,如图8所示。图中的各运放匹配电阻R选取10 kΩ。
该电路的思路是将1个输入同时通过1个同相放大器和1个反相放大器,并依靠二极管的特性,使它们分别在输入电压的正半周和负半周进行有效输出,从而产生取绝对值的效果。其转换结果如图9所示。由图9可见,该电路具有良好的特性。
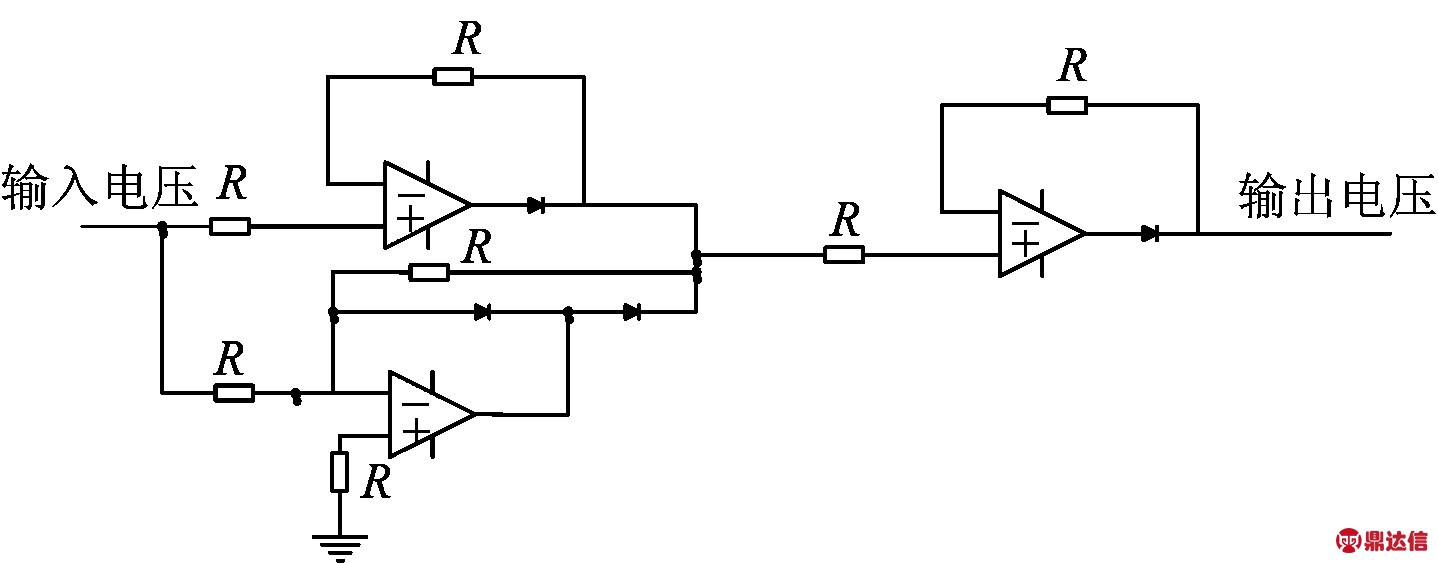
图8 绝对值生成电路
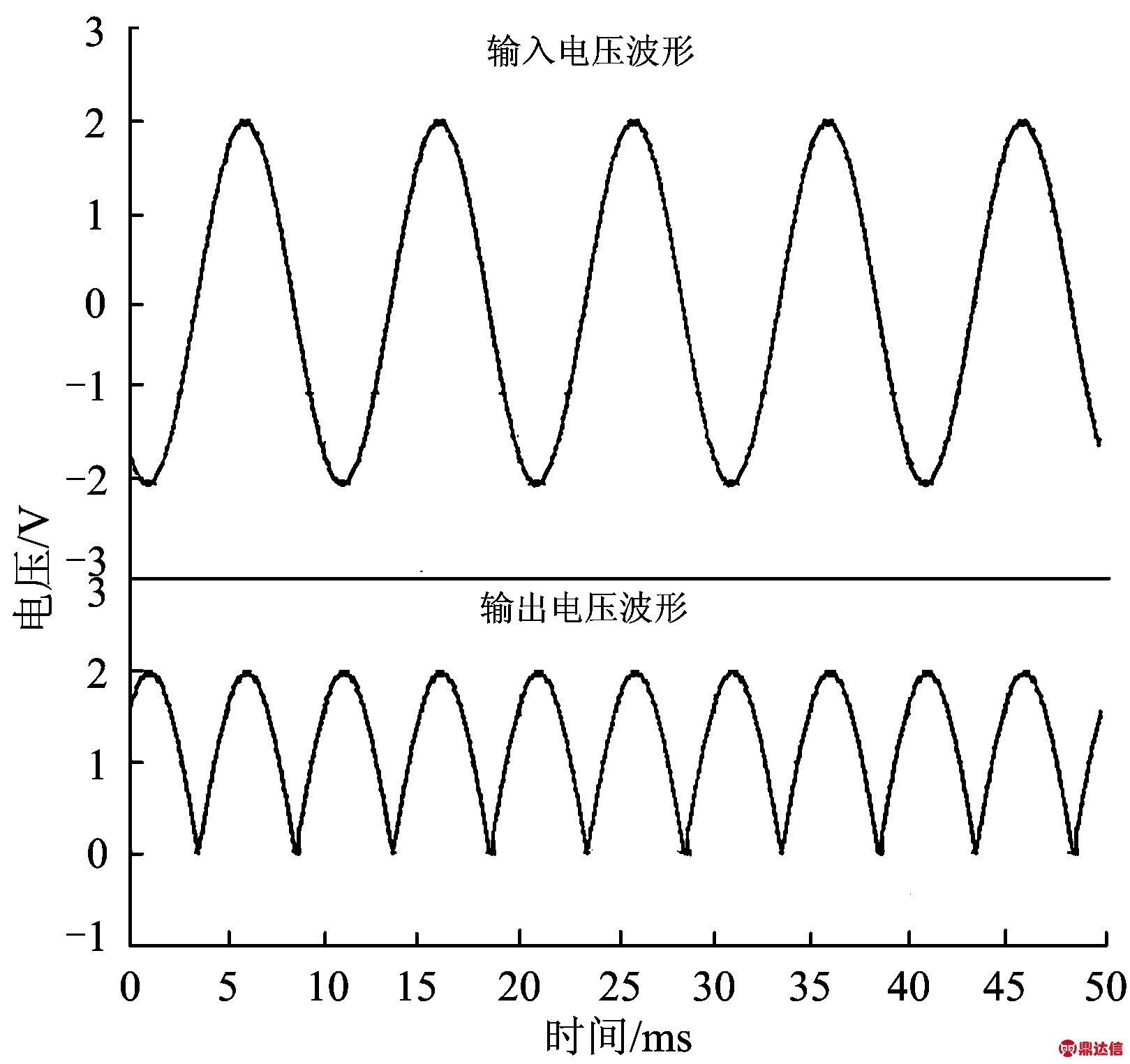
图9 ±2 V正弦波绝对值转换结果
3.2 控制单元硬件资源一览
控制单元的主要硬件设计说明见表1。
表1 控制单元的主要硬件设计说明
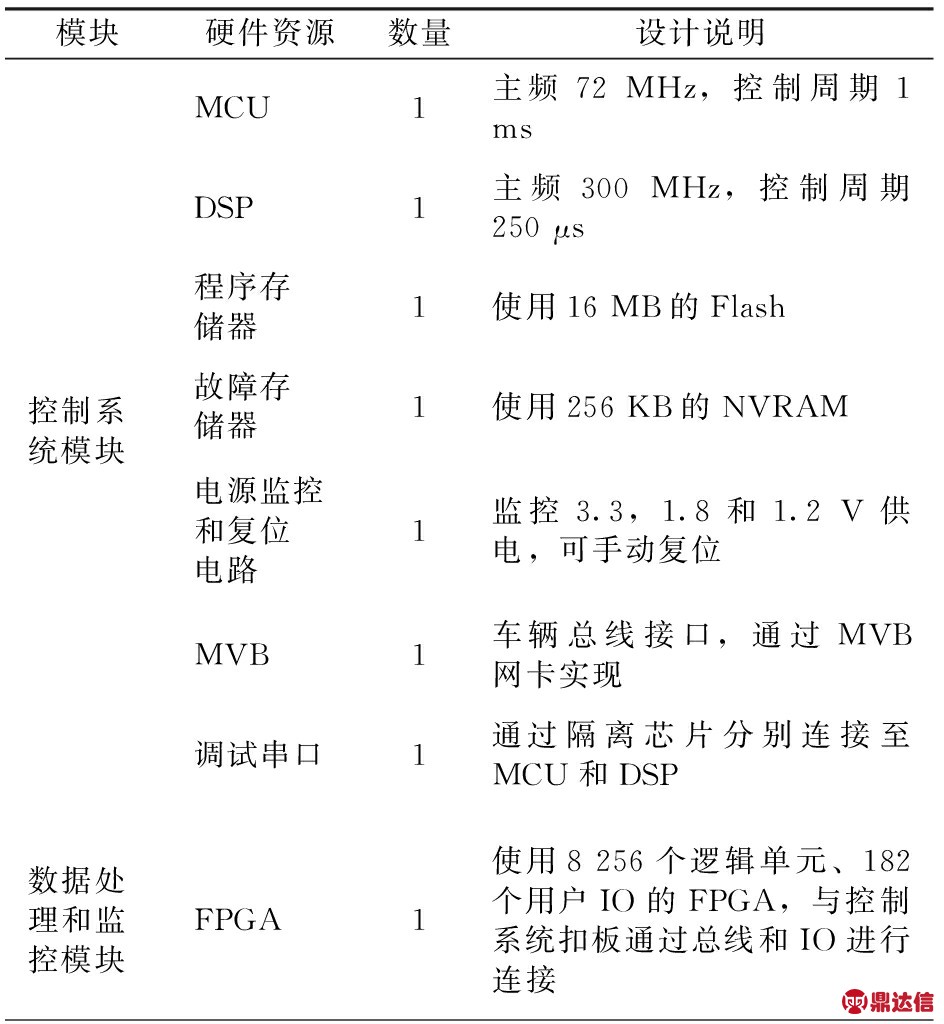
续表1
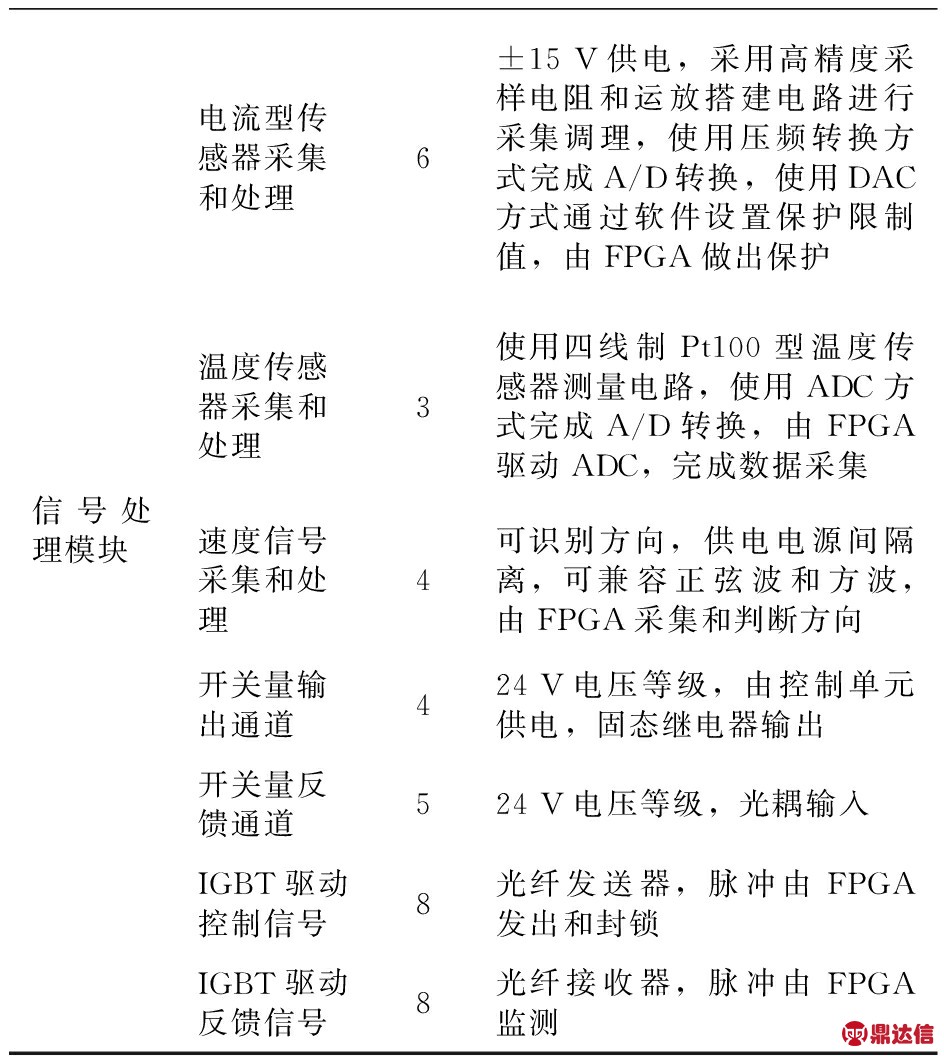
控制单元整体效果如图10所示。
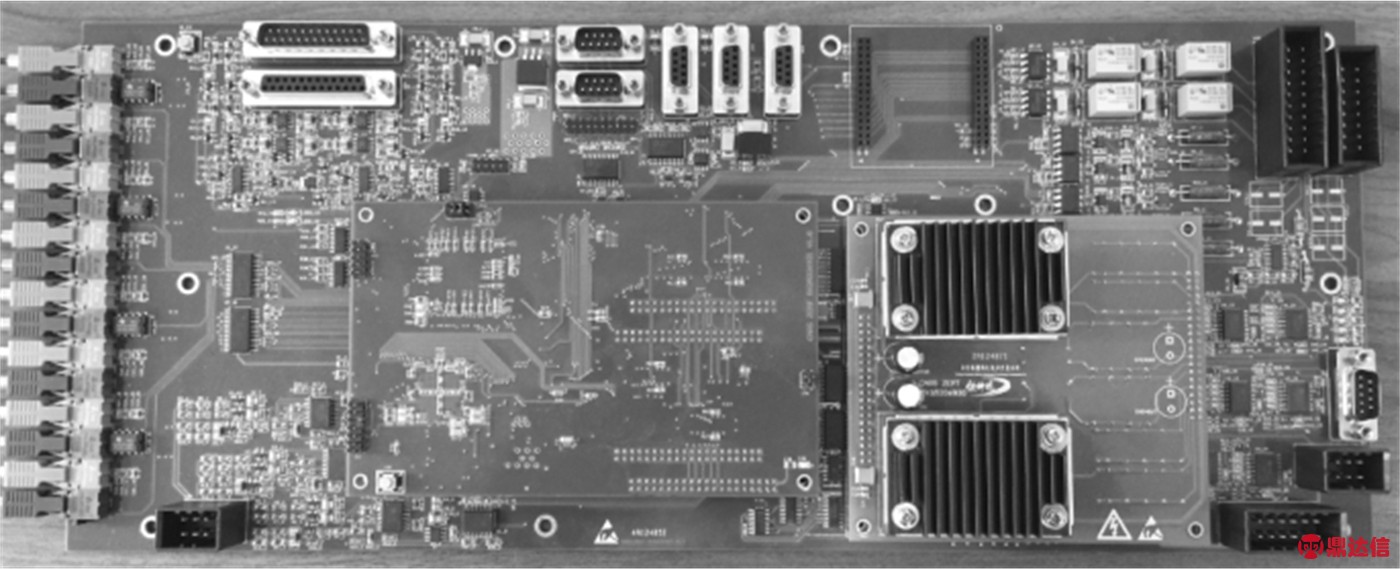
图10 控制单元整体效果图
3.3 试验验证
搭载图10所示控制单元的自主研发1 500 V变流器完成了型式试验。在预充电启动过程中,直流侧电压的变化及特定速度点持续运行期间变流器输出电流及直流侧电压的波形分别如图11和图12所示。试验过程中,机组运行稳定,符合预期。
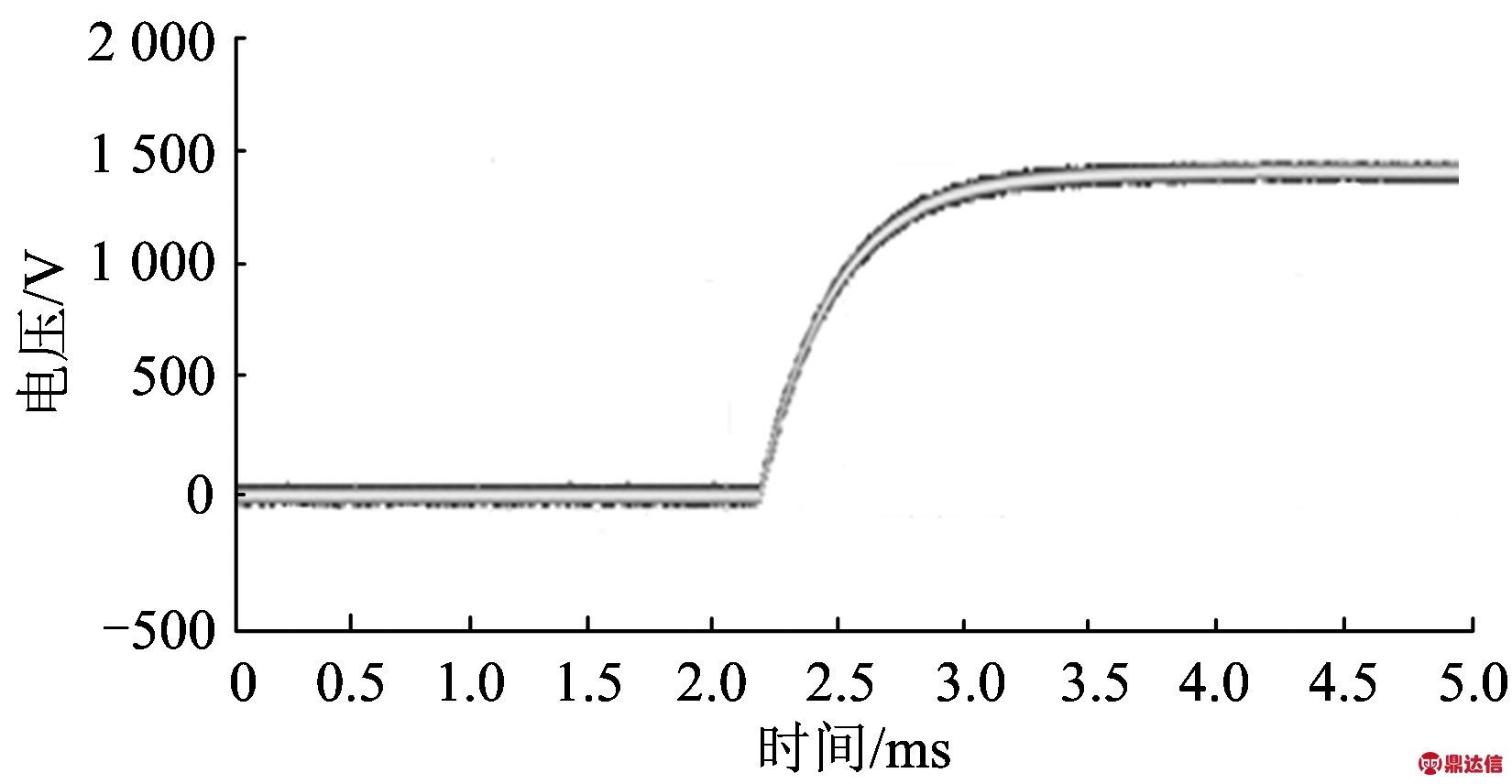
图11 预充电启动过程中直流侧电压波形

图12 持续运行过程中,直流侧电压和变流器输出U相、V相的电流波形
4 结 语
本文在分析城轨牵引变流器控制需求的基础上,讨论了1种与传统背板加箱体模式控制单元体积更小、模块数量更少、结构更加简单的紧凑型控制单元设计方法,并设计实现了1种可安装于牵引功率模块的控制单元,搭载此控制单元的牵引变流器已完成了相应的变流器型式试验和牵引系统地面联调试验,性能符合设计要求。