摘要:旋风分离器对5 μm 以下颗粒的分离效率有待提高。通过雷诺应力模型和随机轨道模型研究1 μm 颗粒在超高旋风分离器内的浓度分布。结果表明细颗粒在上行流和准自由涡的重叠区聚集,形成浓度高峰。分析不同轴向位置和不同时刻的颗粒径向分布,发现其形成机制有二:一是高度与自然旋风长不匹配导致旋涡尾端扫壁,引起大量颗粒返混,然后在内旋流的分离作用下向外移动;二是下行流向心汇聚对细颗粒的裹挟作用。机制一对颗粒浓峰的贡献更大。大部分浓环颗粒在上行过程中会继续外移,汇入下行流后再次经受外旋流的分离作用,少部分颗粒在上行流或短路流的裹挟下逃逸。抑制颗粒返混是改善颗粒浓环的关键,可通过优化高度或增加内购件的方式实现。
关键词:旋风分离器;离心分离;颗粒;浓度分布;运动轨迹;计算流体力学
引 言
热解是低阶煤高效清洁利用的主要技术路线之一[1]。低阶煤颗粒在热解过程中易受热发生热爆和崩析,产生大量粉尘。如果后续的分离装置无法有效除去这些粉尘,则其会与焦油尤其是流动性差的重质焦油一同堵塞下游装置和管道,造成装置无法长时间连续运行[2]。目前,很多煤热解工艺装置都从循环流化床工艺有所借鉴,除尘技术亦如此。旋风分离器是循环流化床工艺中不可或缺的除尘设备,在煤热解工艺中也有诸多应用,但除尘效果有限[2]。中国石油大学在旋风分离器技术领域有长期的积累,开发了适配石油催化裂化(FCC)装置的旋风分离器[3],为我国的炼油工业做出了巨大贡献。但目标颗粒不同,同一旋风分离器表现出的捕集效率也不同[4]。要借鉴其有益经验提高煤热解工艺装置中旋风分离器的除尘性能,需要分析二者颗粒特性的不同之处。FCC 工艺装置中,催化剂平均粒径约为65 μm[5],催化剂的碰撞、磨损等虽然会产生小颗粒粉尘,但经旋风分离器的高效捕集,气流含尘率很低,且几乎不含8 μm以上的颗粒[6],不影响装置的长周期运行。在粉煤热解工艺中,原料颗粒虽然略大于FCC 催化剂,但热爆对颗粒的破碎效果强于碰撞和磨损。这对旋风分离器能捕集5 μm 以下小颗粒的效率提出了更高的要求[2]。为进一步提升效率,需要细致分析小尺寸颗粒的逃逸过程。
由于小尺寸粒度的运动易受气流干扰,很难精确统计其运动路径。现有研究多是通过探讨颗粒在旋风分离器内的浓度分布分析其运动规律。宋健斐等[7]利用计算流体力学(CFD)方法研究中位粒径为12.74 μm 颗粒的浓度分布特征。结果表明,径向上从中心向外依次分为低浓度的中心颗粒逃逸区、次低浓度的中间颗粒分离区和高浓度的边壁颗粒捕集区。各个区间分界会随操作条件的改变而变化。万古军等[8−9]的研究表明压力增大,低浓度区范围扩;温度升高,低浓度区范围减小。在局部二次流较严重的区域,颗粒浓度也较高,浓度值也受到操作条件的影响。Xue 等[10−11]研究的颗粒中位粒径同样为12.74 μm,发现含尘浓度增加会增大短路流处颗粒浓度,温度增加会在轴向加大短路流域和颗粒返混域。上述文献所研究的颗粒中位粒径均大于10 μm,5 μm 以下颗粒占比较低。文中所述颗粒浓度分布特征是多粒径颗粒表现出的总体特征,而非5 μm 以下颗粒的浓度分布。进一步分析文献报道发现5 μm 以下颗粒(下文简称“细颗粒”)沿径向的分布并非边壁高中心低,与多粒径颗粒的总体浓度分布特征略有不同。
Wan 等[12]使用CFD 方法分析了45 μm 滑石粉中不同粒径在分离空间内的分布,发现在上行流域内,小于4 μm 颗粒浓度较高。吴小林等[13]通过等速抽气采样法测定了中位粒径为10.46 μm 的滑石粉在旋风分离器内的颗粒浓度分布,在中心颗粒逃逸区观察到2 μm 颗粒浓度更高。吴飞雪等[14]利用激光粒子成像技术测定了1~10 μm的高效液相色谱载体颗粒在旋风分离器内的浓度分布,在分离空间内,2 μm 颗粒在排气管壁附近的浓度要高于中间颗粒分离区,并将其归因于灰斗返气夹带。
上述文献虽然报道了细颗粒浓度分布存在的一些特殊现象,但并没有对其成因和演变开展细致的分析,因而很难描绘出细颗粒的逃逸过程。为此,本文以1 μm 颗粒为代表,研究细颗粒在旋风分离器的浓度分布特征,了解颗粒与流场之间的相互作用,分析颗粒在分离器内的运动过程,为提高旋风分离器对细颗粒的分离能力提供指导。
1 模型与数值计算
1.1 几何模型
研究对象是平顶、180°蜗壳筒锥型旋风分离器,如图1所示。其中入口尺寸a=130 mm、b=54 mm,筒体直径D=300 mm,筒体高度H=1500 mm,锥体高度Hc=600 mm,排气管直径De=120 mm,插入深度S=130 mm,排尘口直径B=120 mm。通常,分离器的总高度为3~4 倍筒体直径。Hoffmann 等[15]研究表明增大高度可以提升分离效率。但鲜有文献报道分离器高度增加后颗粒浓度分布会产生怎样的变化。因此,本文将分离器增高至7倍筒体直径,观察细颗粒的浓度分布。
1.2 湍流模型
旋风分离器内流场呈强旋湍流状态,RSM(Reynolds stress model)湍流模型能够对其做出较为准确的描述[16−19]。其控制方程描述如下。
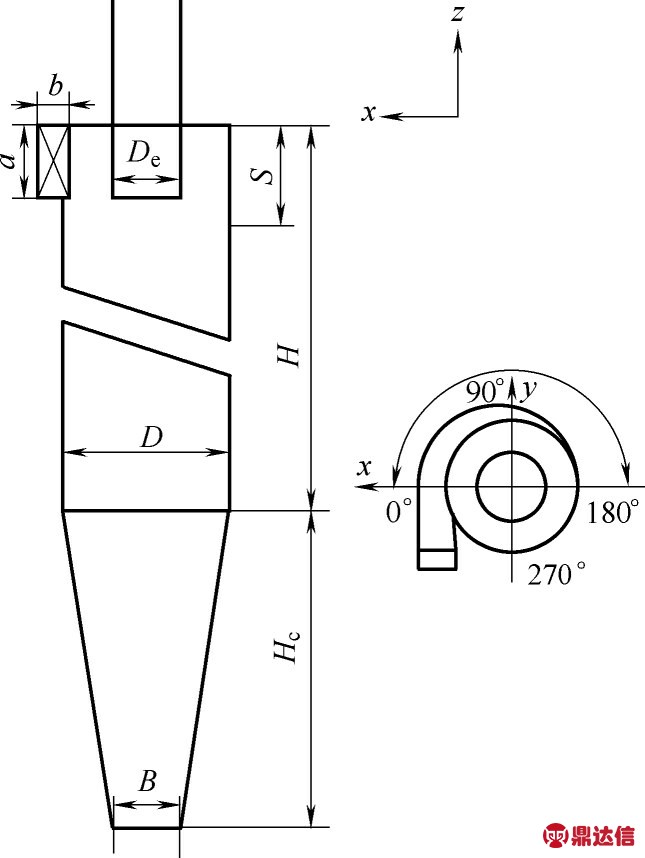
图1 旋风分离器几何模型
Fig.1 Geometric model of cyclone separator
(1)连续性方程
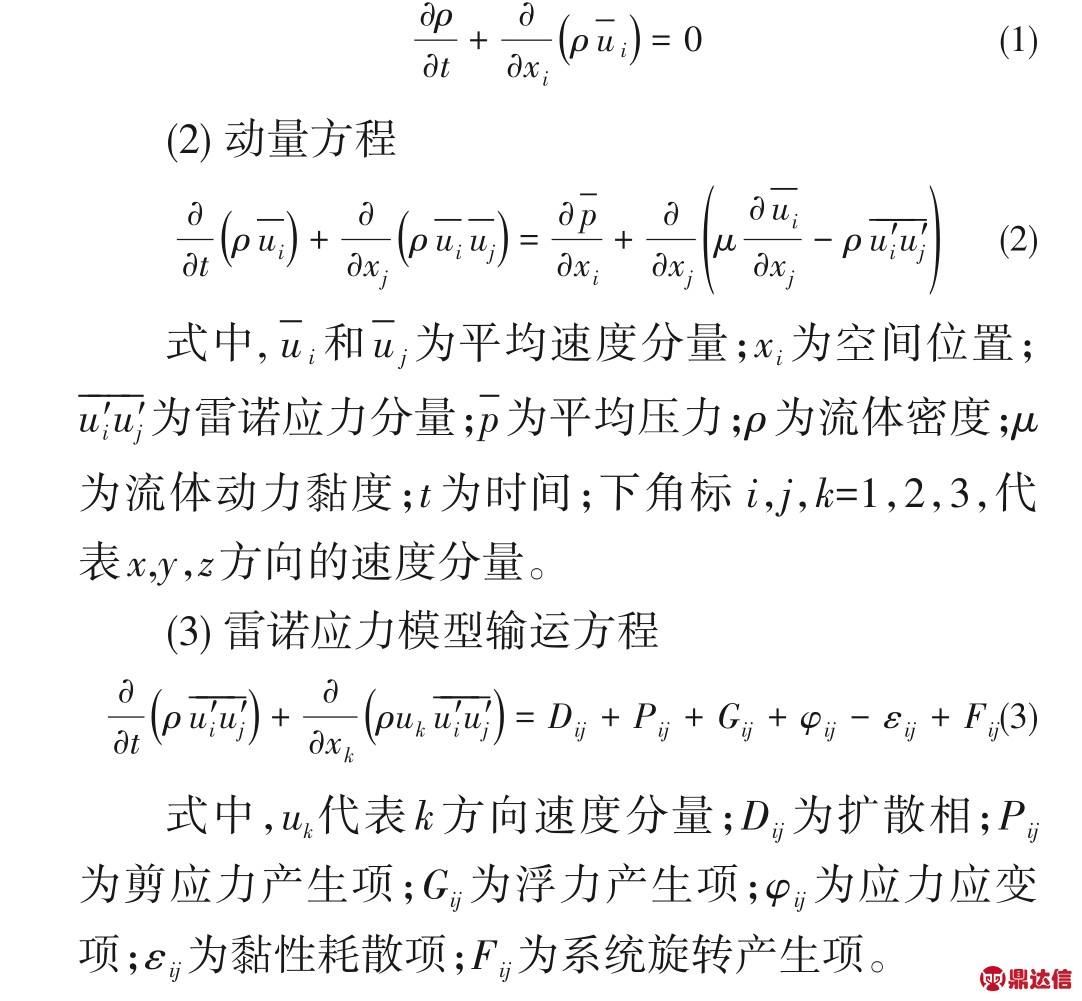
1.3 颗粒运动方程
采用离散相和颗粒随机轨道模型模拟颗粒在气相流场中的运动[20−23],忽略颗粒的旋转,颗粒之间的相互摩擦、碰撞和团聚,仅考虑气相与颗粒之间的相互作用力。离散相运动方程表示如下:


式中,r0为半径,颗粒距设备中心线的距离;up、vp、wp分别为颗粒的轴向、径向和切向速度;ug、vg、wg分别为气相的轴向、径向和切向速度。
1.4 边界条件
本文模拟所采用的气体介质为常温常压下的空气。采用速度入口边界条件20 m/s,水力直径为85.77 mm,湍流强度3.78%,分别采用式(8)和式(9)计算:
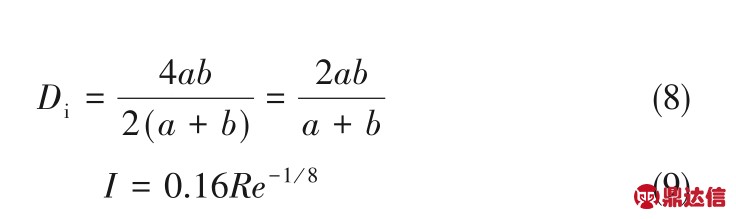
出口边界条件为outflow,为保证这一条件得到满足,将排气管向外延伸至自身直径的10倍。分离器壁面采用无滑移边界条件,锥体段反弹系数为0.6,筒体段反弹系数为0.8,分离器顶板和排气管反弹系数为0.95。
由于其流场的非稳态特性,采用瞬态模拟,时间步长采用0.0002 s[24],收敛残差为10−4。入口颗粒浓度为0.01 kg·m−3,颗粒密度2700 kg·m−3。先对纯气相进行模拟,计算过程中监测排尘口处最小静压值,待其波动周期和幅值基本稳定后,再加入颗粒。
1.5 验证
吴小林等[13]利用等速抽气采样法测量了中位粒径为10.46 μm 的滑石粉中,不同粒径颗粒在旋风分离器内的浓度分布。使用上述计算模型,在21 m·s−1的入口气速、10 g·m−3的气流含尘浓度条件下,分析了4 μm 滑石粉颗粒在分离器内的浓度分布。实验和模拟结果如图2 所示。在轴向位置z=−600 mm处,实验和模拟结果都呈现出越靠近边壁,颗粒浓度越高的趋势。当r<75 mm 时,实验数据和模拟结果吻合较好;当r>75 mm 时,除边壁处外,模拟值略高于实验值。本文主要关注靠近中心的颗粒浓度分布。此处模拟值和实验值吻合较好,可以认为RSM模型和随机轨道模型的计算结果是可信的。
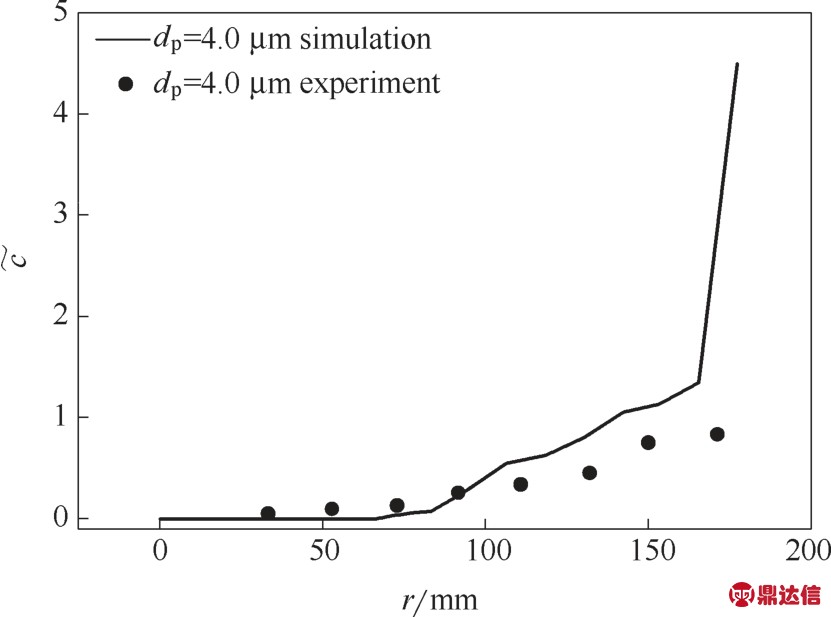
图2 模拟结果与实验数据对比
Fig.2 Comparison of simulation result and experimental data
2 结果与讨论
2.1 颗粒浓度在分离空间的径向分布
如图3(a)所示,在靠近中心的径向位置,出现了明显的颗粒浓度高峰(以下简称“颗粒浓环”),在不同轴向位置都能观察到这一颗粒浓峰,且越靠近排尘口,峰值越高。一些颗粒浓度径向分布的观测实验也报道了同样的现象。黄学东[25]通过灰斗加料,利用等速抽气采样法测量了颗粒在分离空间的径向分布,如图3(b)所示。在r/R=0.4 附近,存在和模拟结果相似的颗粒浓环。另外,吴飞雪等[14]从入口加料的实验也观察到相似的现象。显然,颗粒浓环所处的位置是旋风分离器主要的工作区域。因此,认识其形成机制将有助于理解细颗粒的逃逸规律,进而改进设计以提高分离器捕集细颗粒的能力。
宋健斐等[7]将分离空间分为:低浓度的中心颗粒逃逸区、次低浓度的中间颗粒分离区和高浓度的边壁颗粒捕集区。对照此划分规则,图3(a)所示颗粒浓峰出现在颗粒浓度最低的中间颗粒分离区。颗粒条件的不同可能是形成两种径向分布状态的主要原因之一。宋健斐等[7]采用的是多粒径混合颗粒,其中位粒径为12.74 μm,其中虽包含了5 μm 以下的细颗粒,但占比很低,导致细颗粒的分布特征被淹没。因此,有必要结合实验和模拟结果,重新归纳小颗粒的径向浓度分布特征。
如图3所示,在几何中心附近,颗粒浓度几乎为零,称之为中心洁净区,即图3(a)中的区域(1);近壁面处沉积了大量被分离的颗粒,浓度很高,称之为边壁颗粒捕集区,即图3(a)中的区域(4)。这两个区域与宋健斐等[7]提出的划分规则基本一致。二者之间出现了颗粒浓环和另一个颗粒浓度较低的区域。结合气流的切向和轴向速度分布[图3(c)]可以发现,颗粒浓峰恰好处于上行流和准自由涡的重叠区域。因此,利用上、下行流分界线界定出中间颗粒二次分离区[图3(a)中的区域(2)]和中间颗粒一次分离区[图3(a)中的区域(3)]。
2.2 颗粒浓环形成机制
图4(a)为旋风分离器锥体段不同轴向位置上颗粒浓度沿径向的分布。从中可以发现,越接近排尘口,颗粒浓环和中心洁净区越不明显,最终在排尘口附近消失;除边壁捕集区外,排尘口附近颗粒浓度分布在径向上趋于均匀。由分离器纵截面静压云图[图4(b)]可知,在z=−1900 mm 位置处,旋涡尾端弯向壁面,同时由图4(c)可见,切向速度呈现明显的不对称性,且速度值明显减小。导致了边壁附近的大量颗粒发生横向掺混[26],颗粒浓度分布趋于一致。说明旋涡尾端摆动等气相流场特征对细颗粒的浓度分布有决定性影响。
由图4(c)可以发现,在靠近旋涡尾端的位置,即z=−1900 mm,其切向速度的轴对称分布特征很弱,而越远离旋涡尾端,其切向速度的轴对称分布特征越明显,如z=−1700 mm,并且速度值要大于z=−1900 mm 位置。对比z=−1700 mm 和z=−1900 mm处颗粒浓度沿径向的分布[图4(a)],在z=−1900 mm处,颗粒浓度在径向上较为均匀,而在z=−1700 mm处,四区域的浓度分布特征已基本呈现。说明返混颗粒在随气体上行的过程中被准强制涡推向外围,向准自由涡侧聚集。因此,颗粒返混及准强制涡的分离作用是形成颗粒浓环的第一个机制。
不同时刻分离器内两相流场如图5所示。不同时刻排尘口附近的颗粒浓度如图5(a)所示。在4 s时,即加入颗粒1 s后,排尘口中心没有颗粒,此时旋涡尾端处于料腿底部,没有明显摆动[图5(c)],还没有产生颗粒返混。即浓环颗粒的第一个来源还未有所贡献。但观察筒体空间横截面的径向浓度分布[图5(b)]可以发现,4 s 时筒体空间中上行流和准自由涡重叠区域内已经存在一定浓度的颗粒。由文献[27]可知,部分气体在下行的过程中会向中心汇聚,并入上行流,同时加剧涡核的非稳态运动。在向心汇聚气流的裹挟下,部分下行颗粒会进入中间颗粒二次分离区,这是形成颗粒浓环的第二个机制。
随着计算时间的增加,中间颗粒二次分离区的颗粒浓度逐渐升高,10 s 时出现典型的四区域分布特征。在这一演变过程中,排尘口中心的颗粒浓度逐渐升高[图5(a)],这说明返混颗粒逐渐增多,机制一的作用从无到有,逐步增强。机制二则持续发挥作用。对比图5(a)、(b)可以发现,排尘口中心处颗粒浓度越高,对应时刻下颗粒浓环就越明显。说明机制一和颗粒浓环的强化过程在时间上是同步的。因此,浓环颗粒主要来自于返混颗粒的二次分离,少部分来自于下行流内颗粒的向心汇聚。
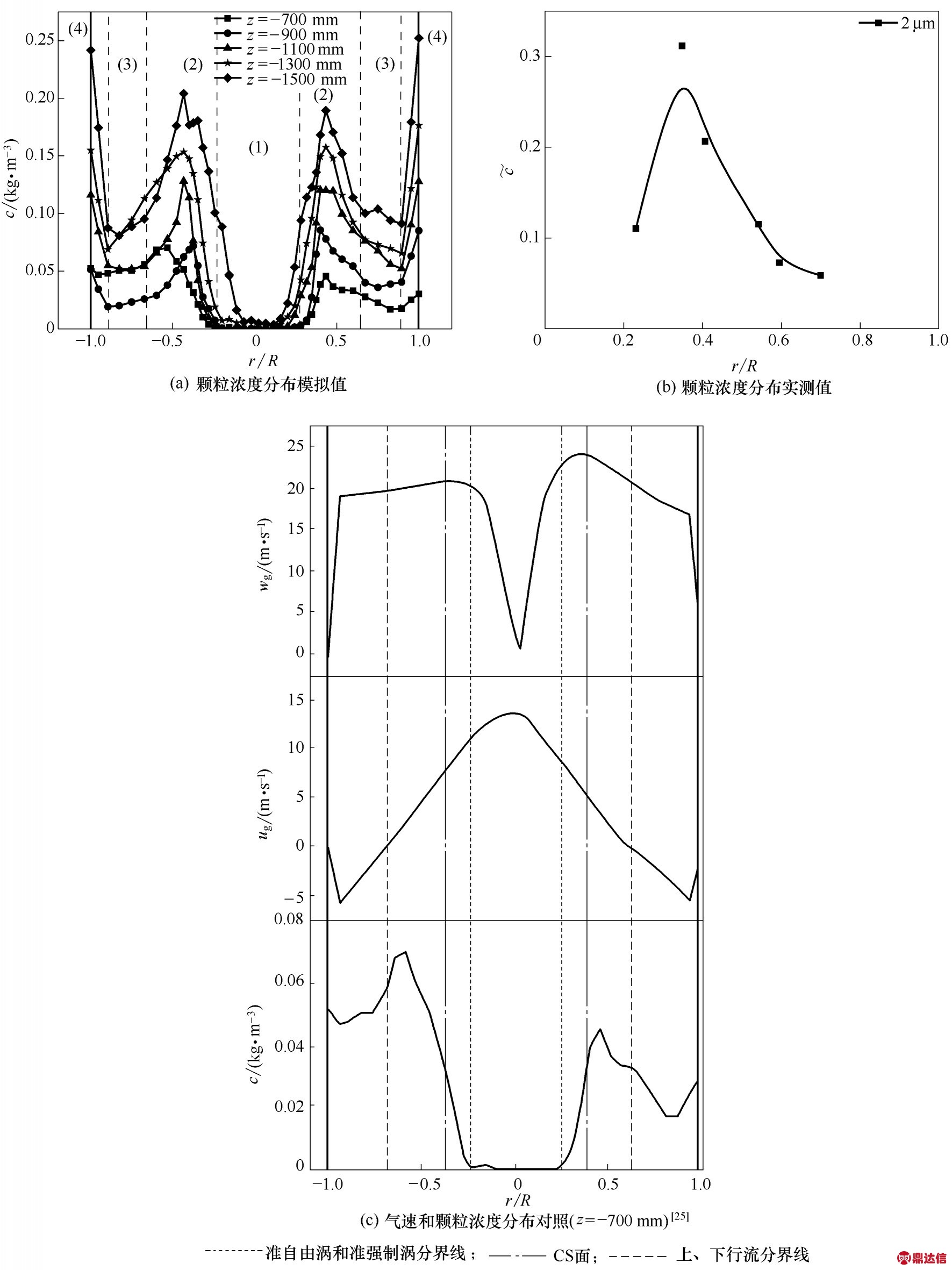
图3 气相速度和颗粒浓度沿径向位置分布
Fig.3 Distribution of gas velocity and particle concentration along radial position
2.3 浓环颗粒的循环及逃逸
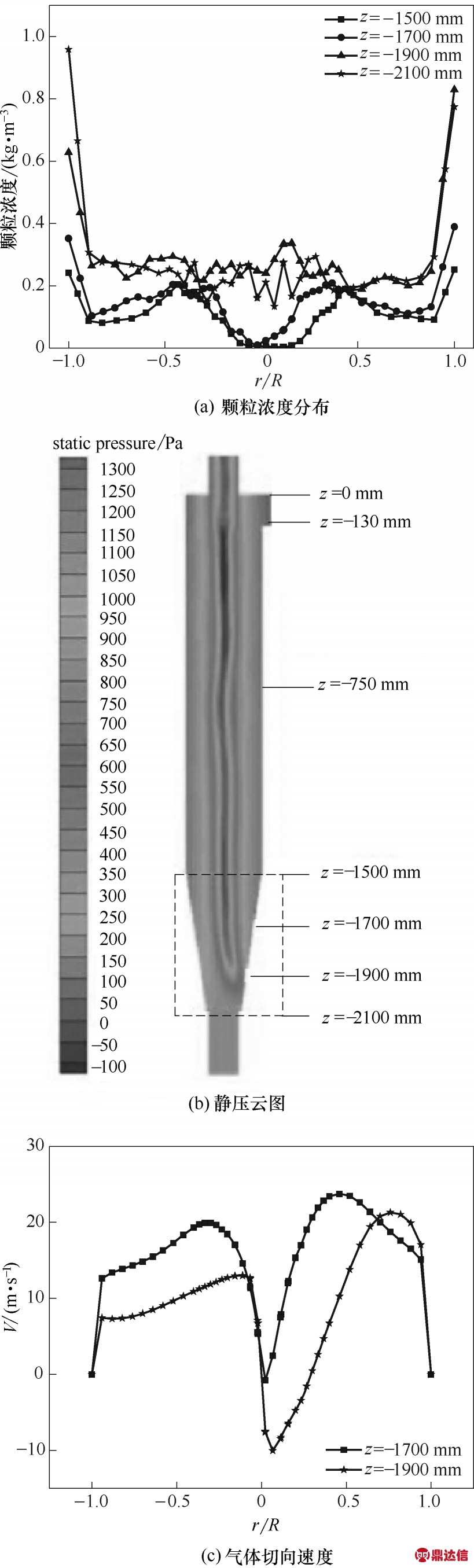
图4 锥体段的两相流场
Fig.4 Two−phase flow field of cone segment
观察图3(a)可以发现,中间颗粒二次分离区内的颗粒在随上行气流运动过程中,浓度峰值逐渐降低,说明虽然此处颗粒的分离难度比其他位置更大,但是分离作用仍然存在。由于这一分离过程位于上行流内,晚于颗粒下行过程中的分离,并且主要是对返混颗粒的分离,因此在文献中被称作二次分离[3,9]。被二次分离的颗粒其中一部分会再次汇入下行流,与新进入的颗粒共同运动,形成如图6所示的循环流动轨迹:颗粒从入口进入分离空间内,大部分颗粒在随气体下行的过程中,经过一次分离,部分颗粒被分离至壁面,另一部分细颗粒会随径向汇流进入上行流内。当壁面颗粒随气流运动到旋涡尾端处,由于受旋涡尾端摆动等流场的非稳态特性的影响,只有一部分颗粒会从排尘口流出分离器,另一部分颗粒被重新卷扬至几何中心处,被上行流裹挟上行。上行过程中,随着流场逐渐稳定和离心作用的增强,返混颗粒被准强制涡甩向壁面,形成中心洁净气流和其外侧的高浓度区域。径向上,颗粒浓集区大部分在CS 面(排气管向下延伸而成的虚拟圆柱面)外侧,上行至排气管口时其中的部分颗粒再次汇入下行流,重复上述流动过程。
而位于CS 面内侧的浓集颗粒则直接从排气管逃逸,形成图6 中所示的颗粒直接逃逸轨迹。在分离器顶板附近的流体会沿排气管外壁向下流动,直接从排气管下口处进入排气管内,构成短路流[28]。在短路流裹挟下,位于CS面外侧的部分浓环颗粒也会跳出循环,逃逸出分离器,形成图6中的短路带逃颗粒轨迹。
由于强制涡的分离作用,分离器几何中心存在较为洁净的气流,其径向尺寸小于排气管直径,因此部分返混的小颗粒与其混合进入排气管排出。而如能将其单独引出,则会降低排出气流的含尘量。可以利用中间颗粒二次分离区聚集小颗粒的特点实现对不同尺寸颗粒的分选。
值得注意的是:本研究所用旋风分离器的高度大大高于常用值,造成旋涡尾端出现在分离空间的状态,由此造成颗粒大量返混。如果分离器高度能与自然旋风长匹配恰当[15,29],或者增设内构件削弱旋涡尾端摆动[30],都能大大削弱颗粒返混,从而改善颗粒浓环。
3 结 论
针对高度为7倍筒体直径的平顶蜗壳式旋风分离器,利用计算流体动力学的方法分析1 μm颗粒的径向浓度分布,得到以下结论。
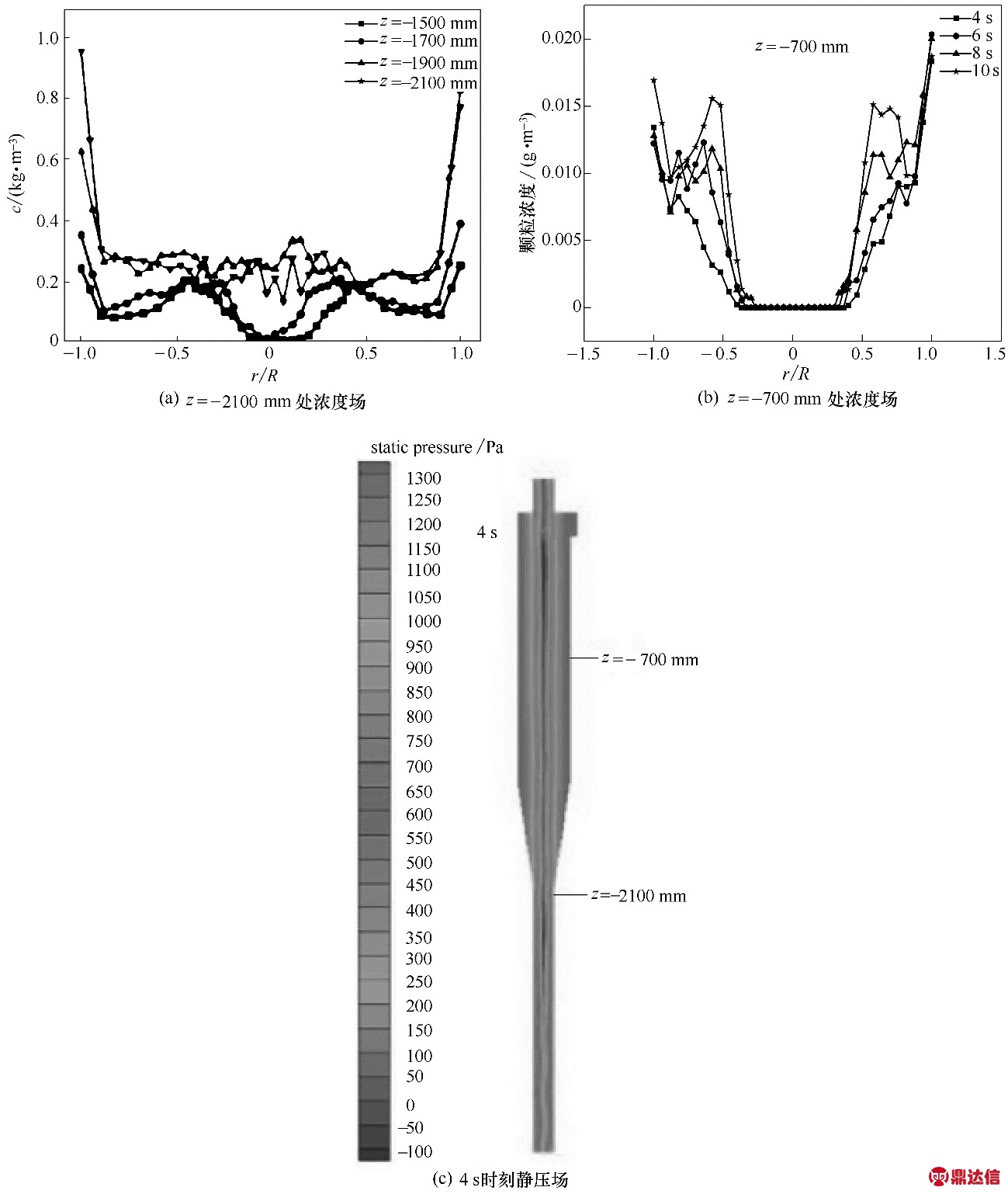
图5 不同时刻分离器内的两相流场
Fig.5 Two−phase flow field in the separator at different times
(1)细颗粒在径向上存在四个浓度不同的区域,从内向外依次是最清洁的中心洁净区,存在浓度次高峰的中间颗粒二次分离区,浓度较低的中间颗粒一次分离区,浓度最高的边壁颗粒捕集区。其中,中间颗粒二次分离区对应于气体的上行流与准自由涡的重叠区域。
(2)促使中间颗粒二次分离区形成浓度高峰的机制有二:一是高度与自然旋风长不匹配导致旋涡尾端扫壁,引起大量颗粒返混,然后在内旋流的分离作用下向外移动;二是下行流向心汇聚对细颗粒的裹挟作用。机制一对颗粒浓峰的贡献更大。
(3)颗粒浓峰的峰值在随气流上行过程中会逐渐降低。到达排气管附近后,一部分颗粒汇入下行流,再次经历分离或返混上行的过程,另一部分则受上行流或短路流裹挟而逃逸。
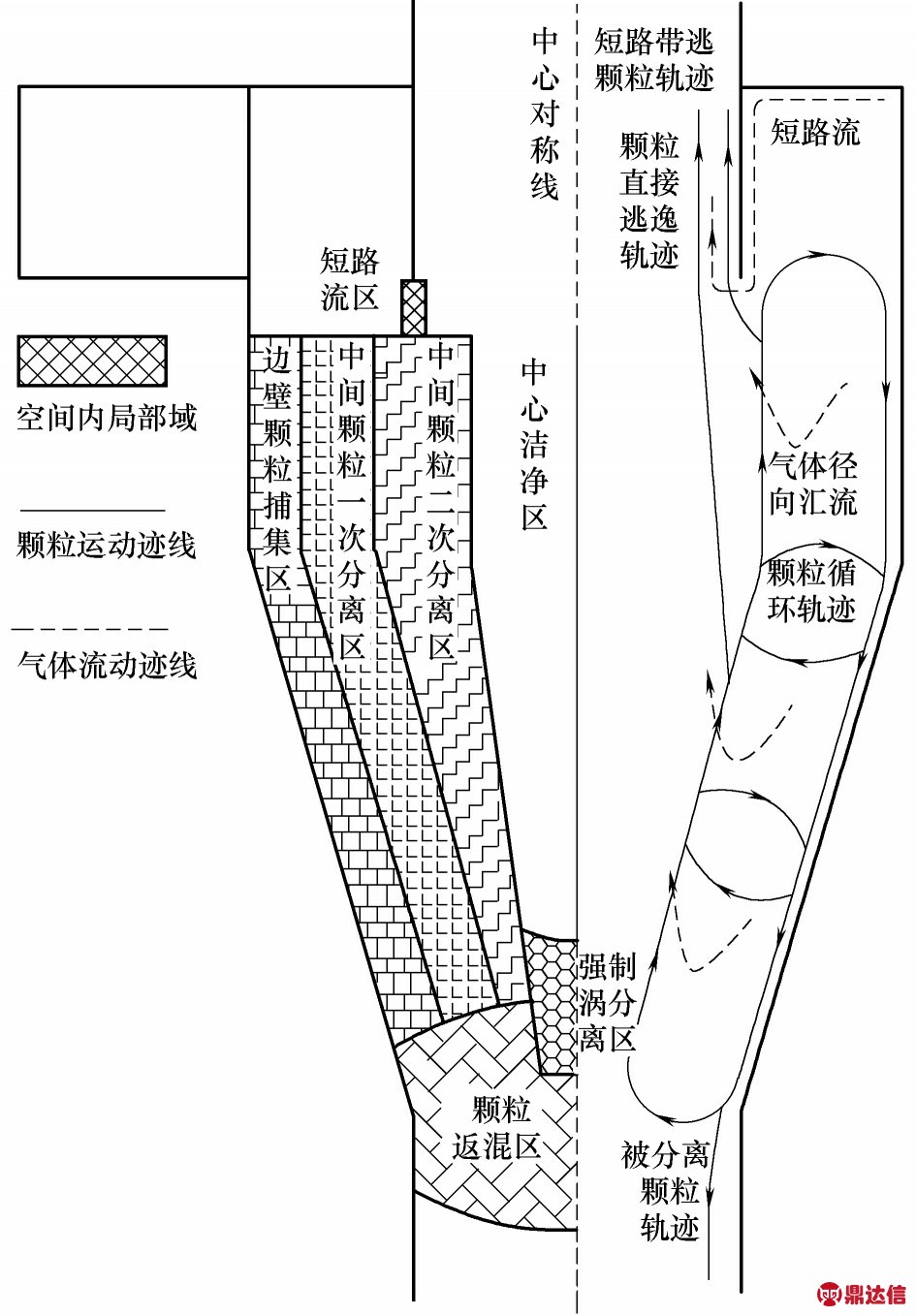
图6 分离空间内细颗粒的运动轨迹
Fig.6 Trajectory of fine particles in the separation space
(4)颗粒返混是形成中间颗粒二次分离区颗粒浓峰的关键,可通过合理匹配高度与自然旋风长,或增设内构件稳定旋涡尾端的方式削弱颗粒返混,从而抑制颗粒浓峰。
符 号 说 明
a——入口高度,mm
B——排气管直径,mm
b——入口宽度,mm
CD——曳力系数
c——颗粒浓度,kg∙m−3
c͂——颗粒浓度与入口浓度比
D——筒体直径,mm
De——排气管直径,mm
Di——水力直径,mm
dp——颗粒直径,m
g——重力加速度,m∙s−2
H——筒体高度,mm
Hc——锥体高度,mm
I——湍流强度,%
Re——Reynolds数
Rep——颗粒Reynolds数
S——插入管深度,mm
u,v,w——分别为轴向、径向和切向速度,m∙s−1
μ——流体动力黏度,N·m−2
ρ——流体密度,kg∙m−3
ρp——颗粒密度,kg∙m−3
τ——颗粒松弛时间,s