摘要: 针对内部设有中心体的轴流式气-液旋流分离器,根据液滴在分离器内部旋流场的受力情况,建立分离器分离效率模型。实验发现,当液滴直径大于10 μm时,通过理论模型求得的液滴粒级分离效率与实验值吻合较好;在一定气速范围内,减小导流叶片出口角、增加中心体直径以及减小排气管直径均能够提高分离效率,即对于一定结构的分离器,存在相应的临界气速能够使分离器的分离效率达到最大值,随气速继续增大,分离效率呈下降趋势。根据实验结果提出分离器在不同工况下的设计准则,当气速高于临界气速时,为保证分离器分离效率,维持较低压降,设计导叶出口角为45°,中心体直径与筒体直径比为0.5,排气管直径与筒体直径比为0.85,分离器长度与筒体直径比为3。当入口气速低于临界气速时,可根据理论模型对分离器结构参数进行调整。
关 键 词: 轴流式;气-液分离;分离效率;理论模型
近年来,随着海洋油气田的持续开发,采出气中的游离水和凝析液含量逐渐增多,在海上平台空间受限的背景下,为满足气-液分离要求,发展紧凑型气-液分离器已经成为新的趋势。轴流式气-液旋流分离器因其占地面积小、易安装、操作灵活、运行稳定连续、无易损件、维护方便、经济成本及运行费用低等优点,在海洋石油工业领域中得到广泛应用[1-2]。
轴流式分离结构最早应用在旋风除尘领域,Gauthier等[3-5]研究了导流叶片、设备长度与排气管等结构参数对轴流式旋风除尘器性能的影响,并根据实验结果优化出最佳设计结构。Maynard等[6-8]针对轴流式旋风分离器结构特点,结合离散相颗粒在分离器内部运动机理,提出相应的分离效率理论模型,得出分离效率与分离器内外筒径、分离腔长度、叶片角度等结构参数以及切向气速、气体黏度、颗粒密度等操作参数的定量关系。其中Muschelknautz等[9-10]在传统反转式分离器平衡轨道模型以及边界层理论模型基础上,提出内含导流叶片的轴流式旋流分离器的分离效率理论模型,但由于轴流式旋流分离器内部流场的特殊性,得到的模型存在一定缺陷。
通过实验测量轴流式旋流分离器内部流场,相对于传统反转式分离器,轴流式旋流分离器内部设置导流体和导流叶片,气体与离散相颗粒运动方向相同,在导流体后部中心处形成分离死区。分离死区内气体轴向速度为零且出现回流,并且影响气体在分离区内的稳定旋转。实验中发现,分离器导流体和排气管的长度对分离器内部流场有较大影响[11-13]。
为改善分离器内部流场分布,去除导流体尾部回流区,笔者在上述研究的基础上,将分离器导流体延伸形成中心体,与外部筒体形成环状分离区。针对内置中心体的轴流式气-液旋流分离器,通过分析液滴在分离器内部旋流场的受力情况,建立分离效率理论模型。并通过实验研究分离器结构与操作参数对分离器分离效率的影响,为分离器的工艺设计提出一定的设计准则与方法。
1 理论模型推导
图1为轴流式气-液旋流分离器结构示意图。雾状来流经过入口导叶起旋作用后,由于气-液两相的密度差异,液滴受离心力作用运动至筒体壁面形成液膜,最终通过集液腔得到分离,气体则通过排气管流出。
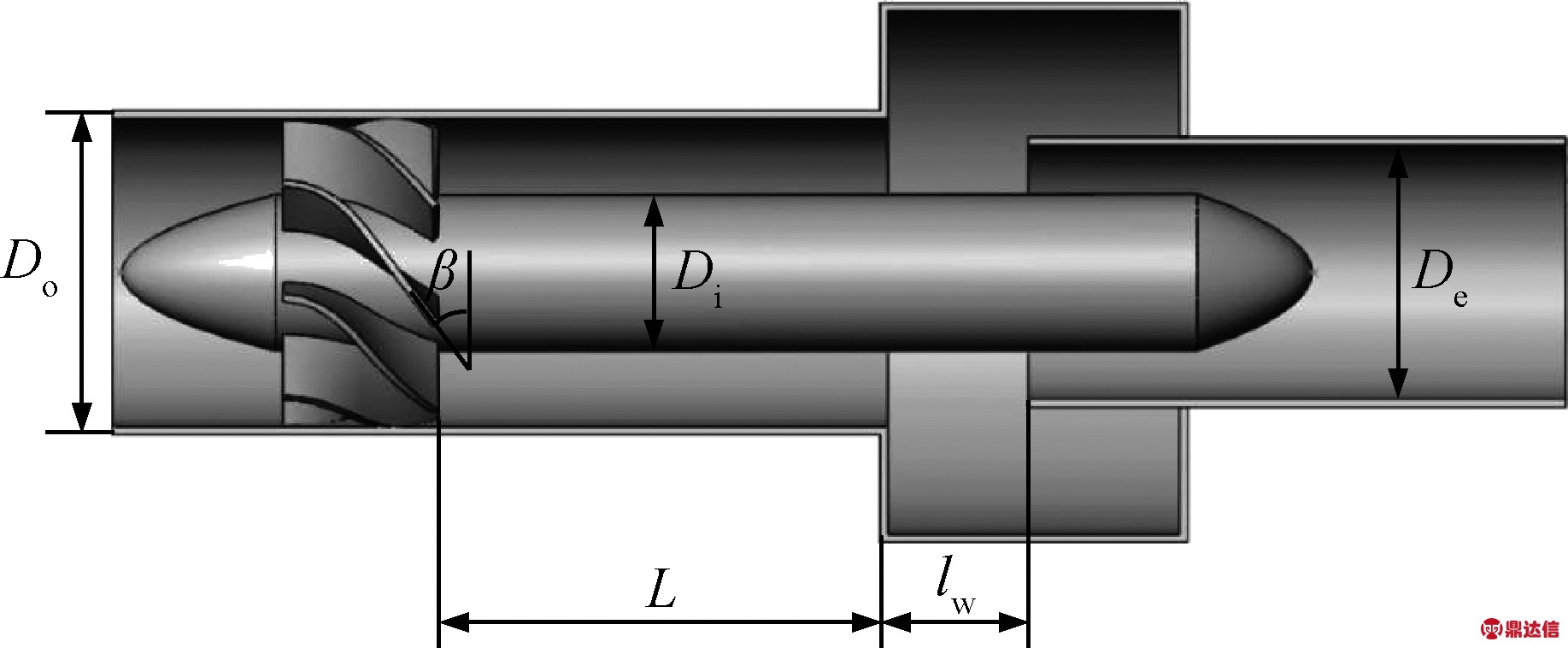
图1 轴流式气-液旋流分离器结构示意图
Fig.1 Structure diagram of the axial flow cyclone separator
1.1 旋流场分析
分离器入口导流叶片采用圆弧段与直线段组合方式,导流叶片出口角为β,其诱导的旋流作用于整个分离过程。在一定入口气速vg下,导流叶片出口截面处轴向速度和切向速度
为[14-15]:
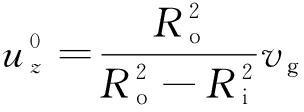
(1)
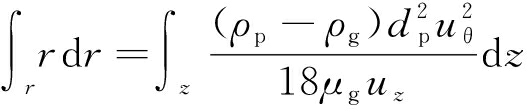
(2)
1.2 液滴受力分析
在进行分离器理论模型计算时,忽略影响液滴运动的次要因素,做出以下假设[16]:(1)液滴分散粒子为球形,且在运动中不变形,忽略液滴的碰撞、聚并以及液膜的影响;(2)液滴相互之间及液滴与器壁之间没有相互作用力,一旦液滴被壁面捕捉,认为液滴得到分离。

图2 环形分离区内液滴受力分析示意图
Fig.2 Schematic diagram of droplet force analysis in annular separation zone
如图2所示,在中心体与外筒体构成的环形分离空间内,直径为dp的液滴做环向圆周运动,在半径r处运动液滴受到离心力Fp为:
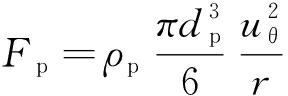
(3)
在流场中,液滴的速度矢量与气体的速度矢量往往不一致。液滴直径越大,气体速度大小与方向变化越大,气-液两相间相对作用力也越大。如果只考虑曳力对液滴的影响,作用在液滴上的曳力FD(t)为[17]:

(4)
其中Vg-Vp表示某一时刻气体与液滴矢量速度差,假设液滴颗粒较小且在强旋作用下,液滴夹带在气流中随气体一起运动,气-液之间的切向速度和轴向速度几乎相同[18-19]。CD为气体对液滴的阻力系数。研究表明,假设颗粒为光滑圆球情况下,颗粒阻力系数仅与液滴运动雷诺数Re相关。在实际情况下,旋流分离器内液滴雷诺数可达到10~20,在计算时并不符合斯托克斯定律的应用条件,但是在强旋流场中,由于离心场的稳定性,液滴径向上湍流强度十分有限,因此在液滴后面不会有尾流和分离流发生,取CD=24/Re。根据液滴径向所受斯托克斯力公式得到[8]:
FD(t)=3πμg|Δu|dp
(5)
|Δu|表示旋流场内气体与液滴径向上的速度差,相对于液滴径向运动速度ur,气体在径向上速度可忽略不计,即|Δu|=ur。
液滴在半径r处旋流场中受气体浮力Ff为:
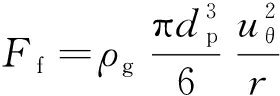
(6)
根据液滴受力建立液滴径向运动方程:

(7)
假定液滴为准稳态运动过式(7)化解为:
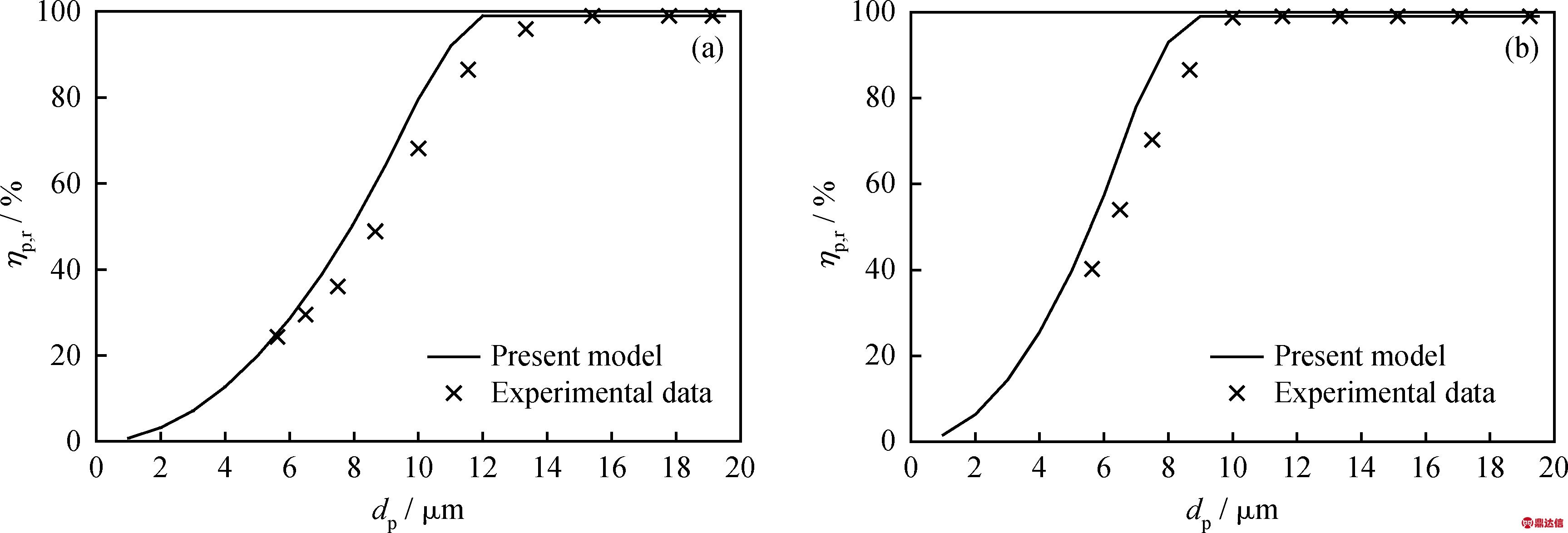
(8)
根据分离器内液滴在轴向和径向运动间关系,得到:
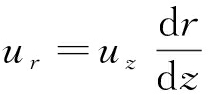
(9)
将式(8)代入式(9)并积分得到:
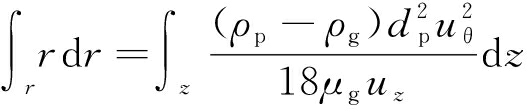
(10)
王鲁平[21]测定分离区内部流场发现,分离器环形分离区内部切向速度呈“n”型分布,即除了外筒体内壁面以及中心体表面处速度较低外,其余均保持较高的切向速度且沿径向方向速度变化不大。由于分离器分离区长度较短,气体切向速度沿轴向变化不明显[22],因此对于环形分离区内部流场速度可近似认为:

液滴在分离器内部运动过程中,能够得到分离的关键是当液滴轴向运动至排气管处时,径向上能够运动至外筒壁面或排气管外侧,从而避免液滴随气体直接通过排气管排出。基于以上因素,将式(10)进行积分,假设液滴从中心体半径Ri处进入分离器,轴向运动距离为环形分离区长度L,将能够完全分离的液滴直径dp,c定义为临界直径,得到:

(11)
由式(11)可知,临界直径dp,c与分离器结构参数和操作条件相关。对于分离器结构参数,增加中心体半径Ri,减小排气管半径Re,减小导流叶片出口角β,增加环形分离区长度L均能够提高分离器对小直径液滴的捕捉效率。同样对于操作参数,增加气体流量也有利于分离效率的增加。
1.3 粒级效率与整体分离效率
基于临界直径的计算方式,对分离器粒级分离效率进行分析,在上述分离器结构参数情况下,只要入口液滴直径dp,r大于临界直径dp,c,液滴均能得到分离。当dp,r<dp,c时,环形分离空间内必然存在某一径向位置Ri<Rr≤Re,使得直径为dp,r的液滴全部分离。在液滴均匀分布的情况下,液滴直径为dp,r的分离效率ηp,r可以通过以下方法计算:

(12)
其中Rr通过式(11)变换得到:

(13)
最终得到:

(14)
在此基础上,得到分离器总体分离效率ηp为:

(15)
其中Fm(dp)是液滴dp的质量分数。
2 实验测试
为明确分离器理论模型的准确性以及研究分离器结构参数和操作参数对分离器分离性能的影响,设置实验装置如图3所示:
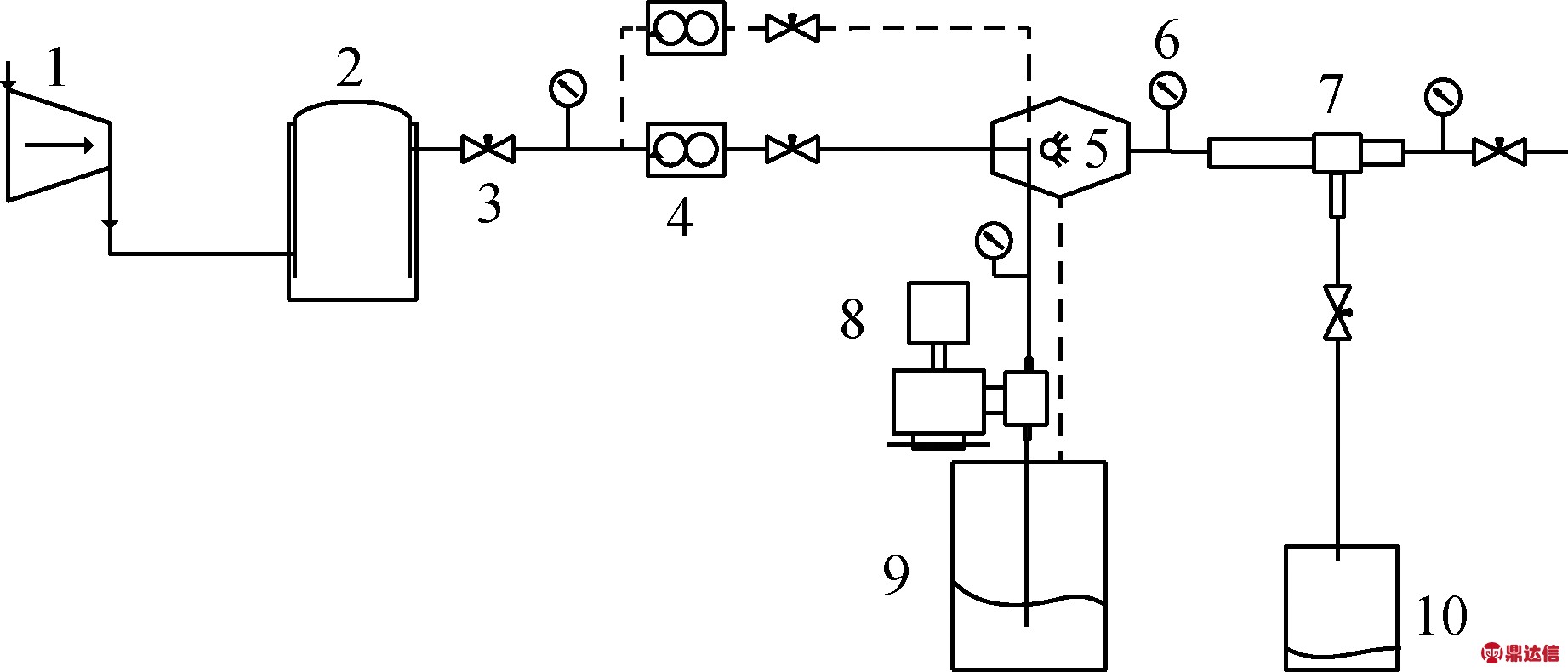
图3 轴流式气-液旋流分离器的实验流程图
Fig.3 Flow chart of the axial flow cyclone separator
1—Compressor; 2—Buffer tank; 3—Valve;
4—Orifice flowmeter; 5—Two-fluid spray nozzle;
6—Piezometer; 7—Test cyclone; 8—Metering pump;
9—Feeding tank; 10—Liquid container
实验设备主要由供气系统、雾化系统、分离系统和测量系统组成,调节压缩机入口折算气速为3~11 m/s。实验中采用双流体雾化喷嘴造雾,如图4 所示,保持喷嘴液相支路流量2.7 kg/h,并控制喷嘴调节阀得到不同粒径分布的液滴群。为避免液体蒸发对分离效率的影响,采用挥发性较低的低黏白油-空气体系进行实验。
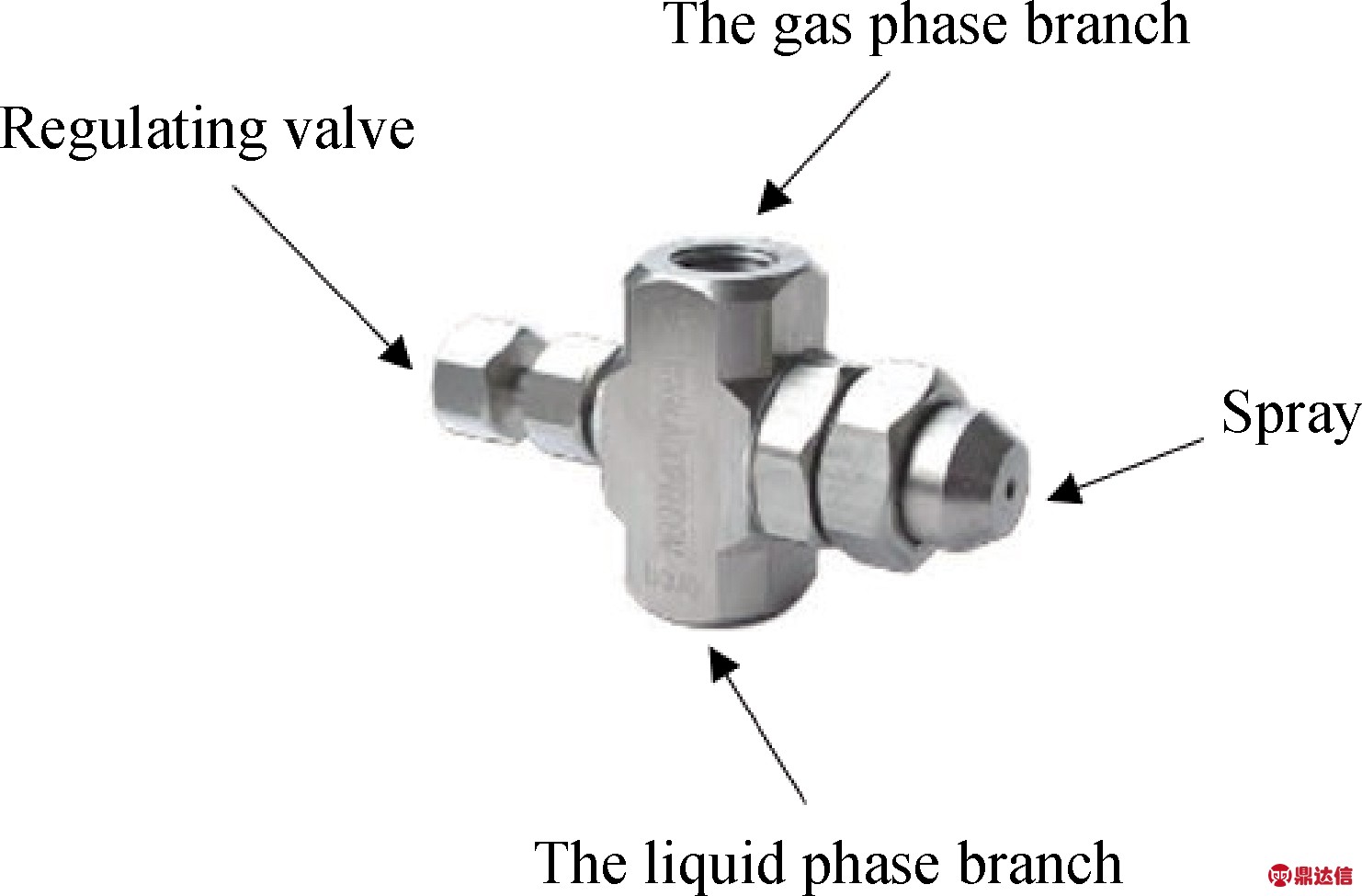
图4 喷嘴结构图
Fig.4 Nozzle structure diagram
实验中轴流式气-液旋流分离器外筒直径Do=0.08 m,中心体直径与筒体直径比Di/Do=0.5,排气管直径与筒体直径比De/Do=0.85,环形分离区长度与筒体直径比L/Do=3,导流叶片出口角β=45°。分离器整体分离效率通过集液罐与供液罐质量变化比值进行计算,其中实验前、后供液罐液体质量减少为m1,通过分离器后集液罐质量增加为m2,总体分离效率为:
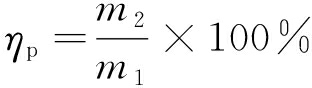
(16)
图5为入口气速分别为5 m/s和10 m/s时,Malvern-Insitec在线激光粒度仪测量得到分离器出口处的液滴粒径分布。由图5可知,气速增加时出口处液滴粒径分布整体稍向左偏移,说明液滴的分离效率有所提升,但是当入口气速为10 m/s时出口处检测出有超过1000 μm的大液滴存在,分析认为此时分离器内分离液膜在气体作用下开始破碎,携液现象发生。
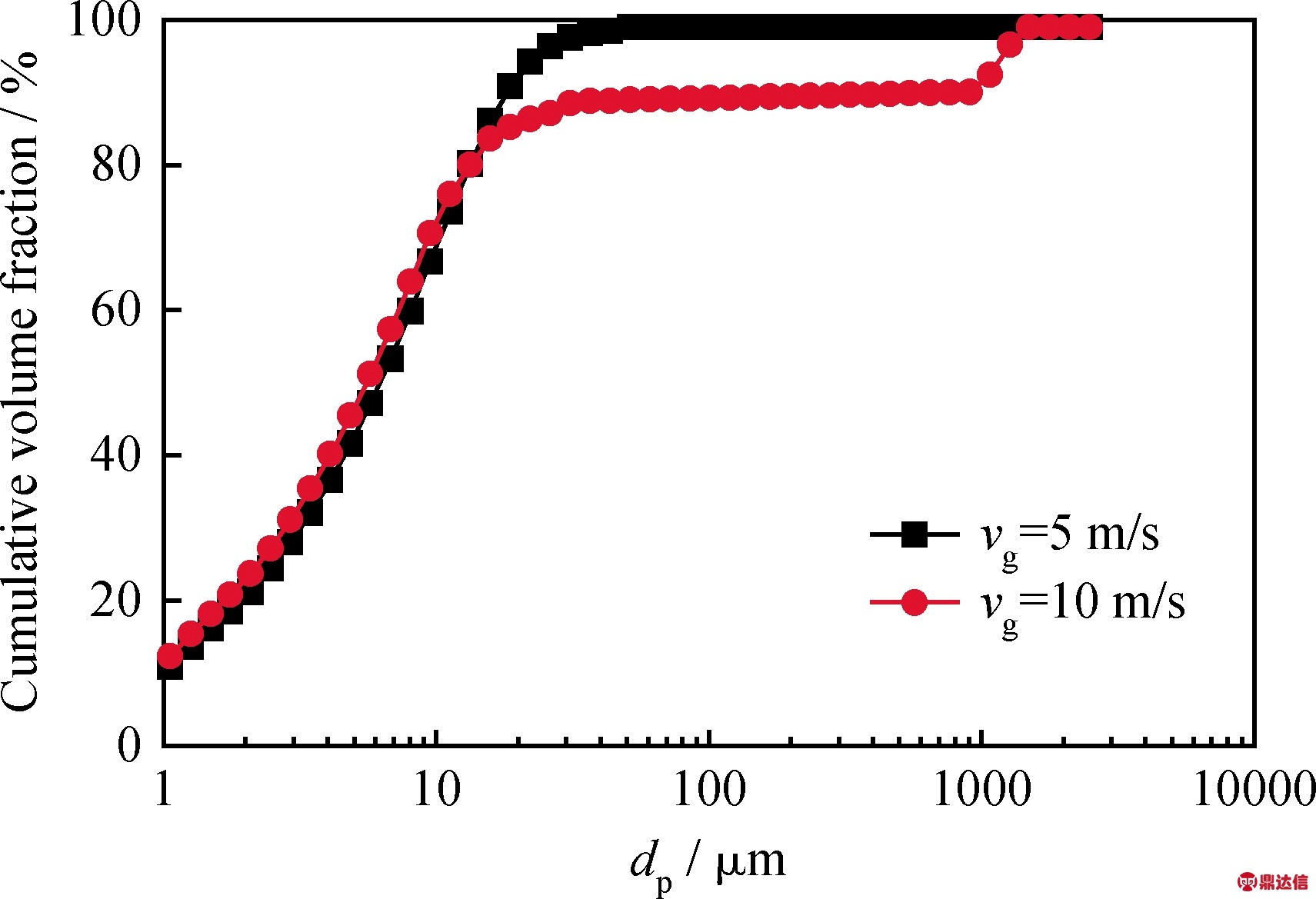
图5 不同气速下分离器出口液滴粒径分布
Fig.5 Particle size distribution of separator outlet at different gas velocities
为研究分离器对液滴的分离情况,根据实验前、后供液罐和集液罐液体质量变化以及分离器进、出口液滴体积概率分布,分析不同粒径液滴经过分离器后的分离效率。由于实验过程中液滴在分离器入口存在碰壁现象,同时液膜在高气速下易破碎形成大液滴,影响分离器出口液滴体积概率分布,可能导致实验得到的液滴粒级分离效率偏低。
笔者单纯考虑分离器进出口液滴粒径分布,忽略上述因素的影响,得到实验条件下液滴粒级分离效率,并与计算值进行对比,如图6所示。由图6可知,入口气速为5 m/s和10 m/s时,分离效率的实验值与理论计算值吻合良好,由于液滴受分离器内部气体湍流作用的影响,分离效率计算理论值略高于实验值。通过实验发现,当气速较低时,理论模型能够较好地预测分离器的分离效率。
3 结构对分离器分离效率的影响
从分离效率模型能够看出,影响分离效率的主要因素是分离器本身的结构参数以及外界操作参数,上述理论模型的建立主要基于受力液滴的径向小雷诺数运动,但是实际现场工况复杂,尤其分离器内部湍流强度较高时会发生携液现象,影响分离器分离效率,因此有必要测试分离器在不同工况下的分离性能,为现场分离器应用提供设计依据。
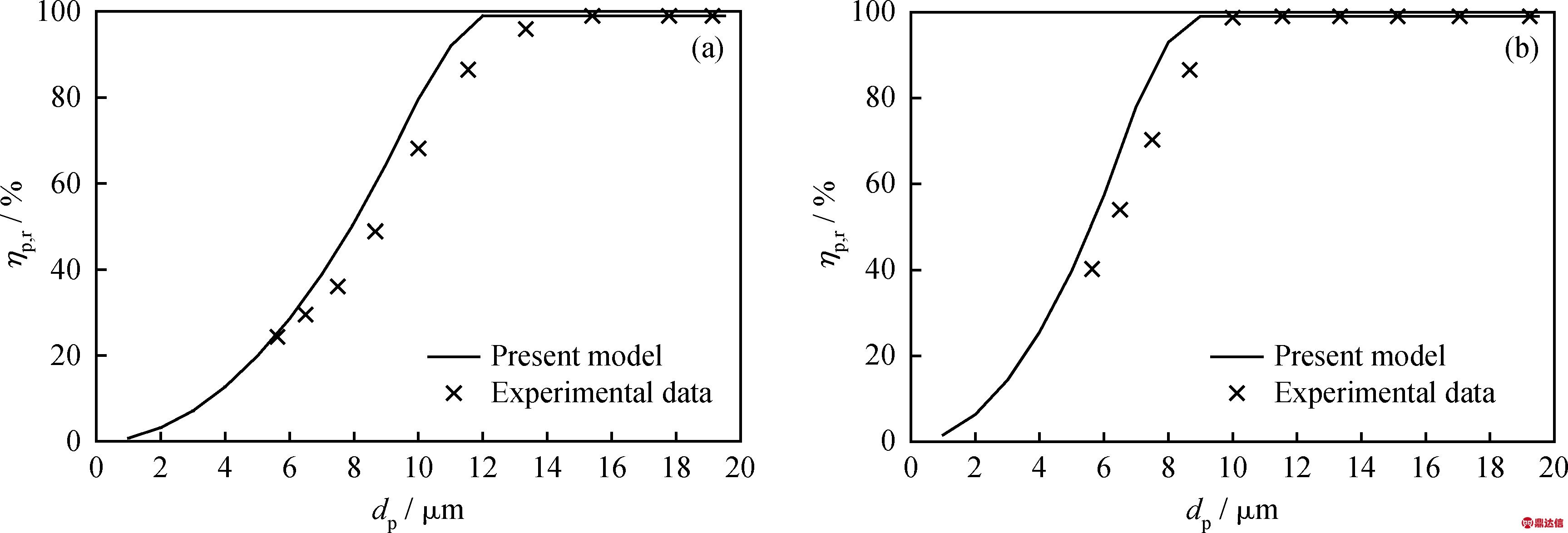
图6 分离器分离效率实验值与计算值对比
Fig.6 Comparison between experimental and calculated grade efficienciesvg/(m·s-1) (a) 5; (b)10
3.1 导流叶片影响
在上述实验的分离器结构基础上,改变导流叶片出口角β分别为30°、45°、60°,并进行实验,测试不同气速下分离器的分离性能,结果如图7所示。由图7可知,当入口气速低于7 m/s时,减小导流叶片出口角,分离效率增加。这是由于在相同气速、相同液量下,导流叶片出口角减小,流体切向速度增加,分离器内部旋流强度增大,液滴在离心力作用下更容易向壁面移动,分离效果增强。
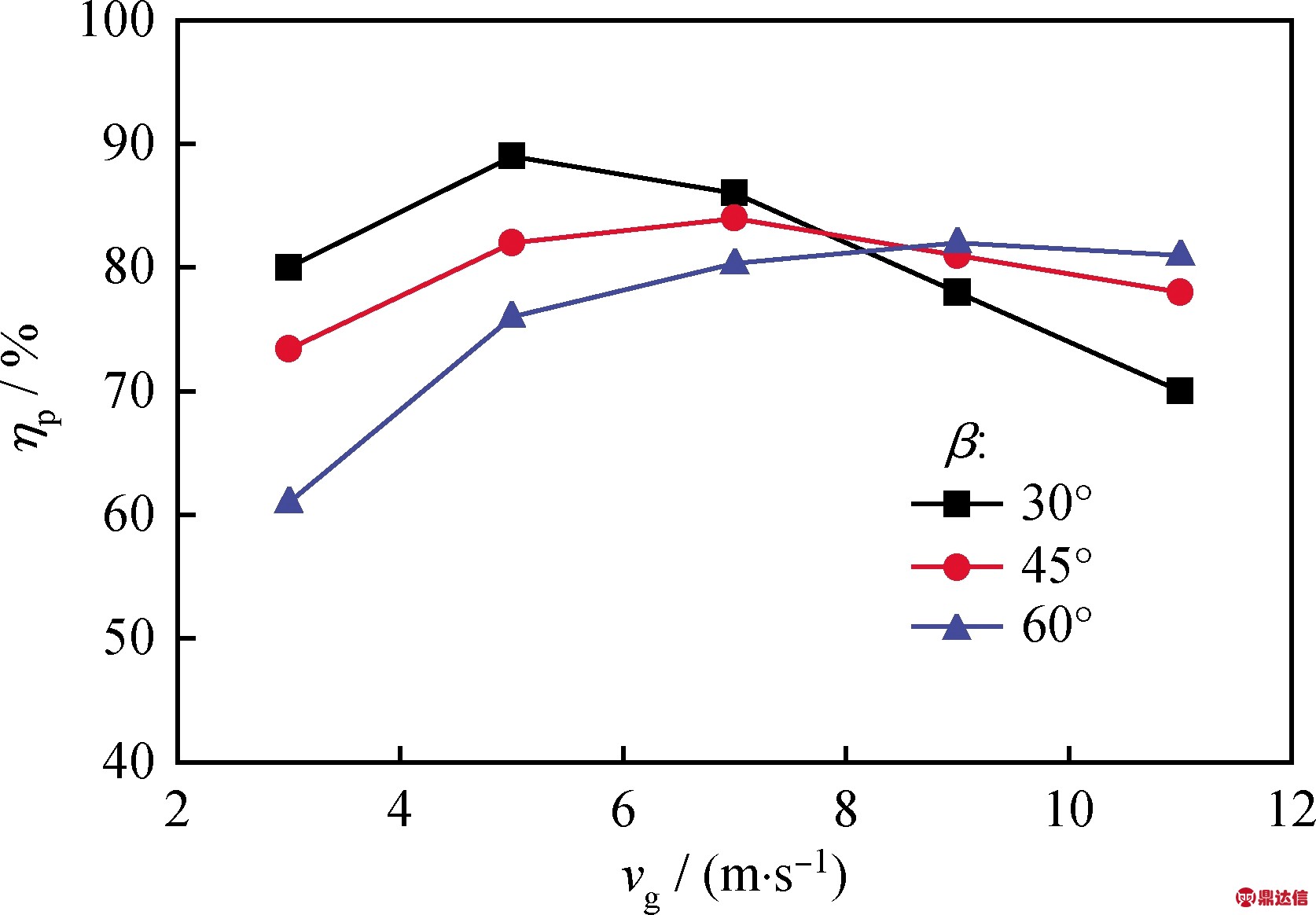
图7 不同导流叶片出口角下总分离效率随入口气速的变化
Fig.7 Variation of overall separation efficiency with inlet velocity at different vane anglesDi/Do=0.5; De/Do=0.85; L/Do=3
在分离器导流叶片出口角一定的情况下,随着入口气速逐渐增加,分离效率达到一定值后开始出现下降趋势。尤其导流叶片出口角为30°时,分离器效率达到最高值后继续增加气速,分离效率显著降低,是因为当导流叶片出口角较小时,分离器内部切向速度过大,湍流作用增强,对液膜剪切作用加剧,造成液体的二次夹带,分离效率降低。
图8为不同导流叶片出口角下压降随入口气速的变化。由图8可知,随着入口气速增加,分离器压降增加,且在同一气速下,导流叶片出口角越小,压降越大。这是因为导流叶片出口角减小时,气体在导流叶片出口处流向发生偏转角度增加,导流叶片出口角处局部损失增加,同时导流叶片出口角的减小也增加了气体与导流叶片及分离器壳体壁面的摩擦损失。
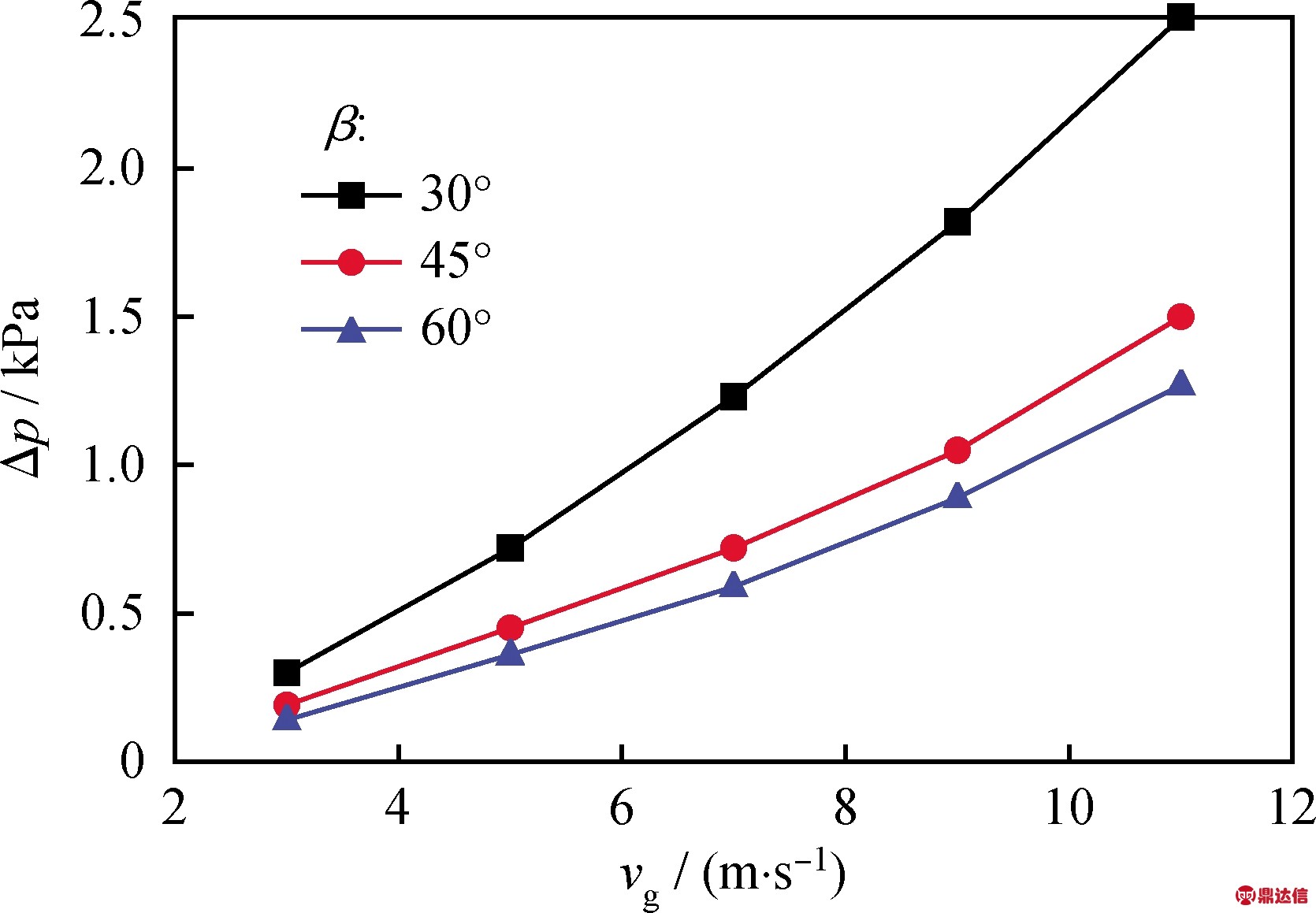
图8 不同导流叶片出口角下压降随入口气速的变化
Fig.8 Variation of pressure drop with inlet velocity at different vane anglesDi/Do=0.5; De/Do=0.85; L/Do=3
3.2 中心体直径对分离性能的影响
在分离器内部设置中心体能够明显改善分离器内部流场,消除导流体后的分离死区。中心体与外部筒体形成环形分离区,流体在环形区域内流动稳定,且保持较高的切向速度。
中心体直径大小关系到分离区环形流通面积,中心体直径增大,液滴径向运动到壁面的距离变小,切向速度增大,离心力加强,利于液滴的分离。但是流通面积减小也导致轴向速度增大,减少了流体在分离器内部停留的时间。为研究中心体直径对分离效率的影响,测试中心体直径与筒体直径比Di/Do 分别为0.5、0.6、0.7时分离器的分离效率,结果如图9所示。

图9 不同Di/Do比下分离器总分离效率随入口气速的变化
Fig.9 Variation of overall separation efficiency with inlet velocity at different Di/Do ratiosβ=45°; De/Do=0.85; L/Do=3
由图9可知,当入口气速低于7 m/s时,增加中心体直径能够有效提高分离器分离效率。是因为随着中心体直径增加,分离区内切向速度增加,旋流强度增大,有利于液滴的分离。对于一定中心体直径分离器,当分离效率达到最高值后继续增加气速,分离效率呈下降趋势,尤其当Di/Do=0.7时,气速对分离效率影响非常明显。
图10为不同Di/Do比下分离器压降随入口气速的变化。由图10可知,分离器压降随气速的增加而增大。在一定气速下,随着中心体直径增加,压降提升幅度增加。因此在设计中心体直径时,在保证分离效率的前提下,尽量保持Di/Do<0.7。
3.3 排气管直径对分离性能的影响
图11为分离器在不同De/Do比下总分离效率随入口气速的变化。由图11可知,低气速下,当De/Do从0.85减小为0.75时,分离器分离效率有所提高,这是因为排气管直径减小,减少了气体中部分液滴的直接逃逸。当De/Do=0.65时,分离效率随气速的增加急剧下降,是由于排气管直径减小,与中心体构成的气体流通面积减小,气体节流作用增强,排气管内部与分离区形成较大压力梯度,因此气体中的液滴以及液滴与排气管外壁接触形成的蠕动液膜更容易进入排气管,造成分离效率下降。
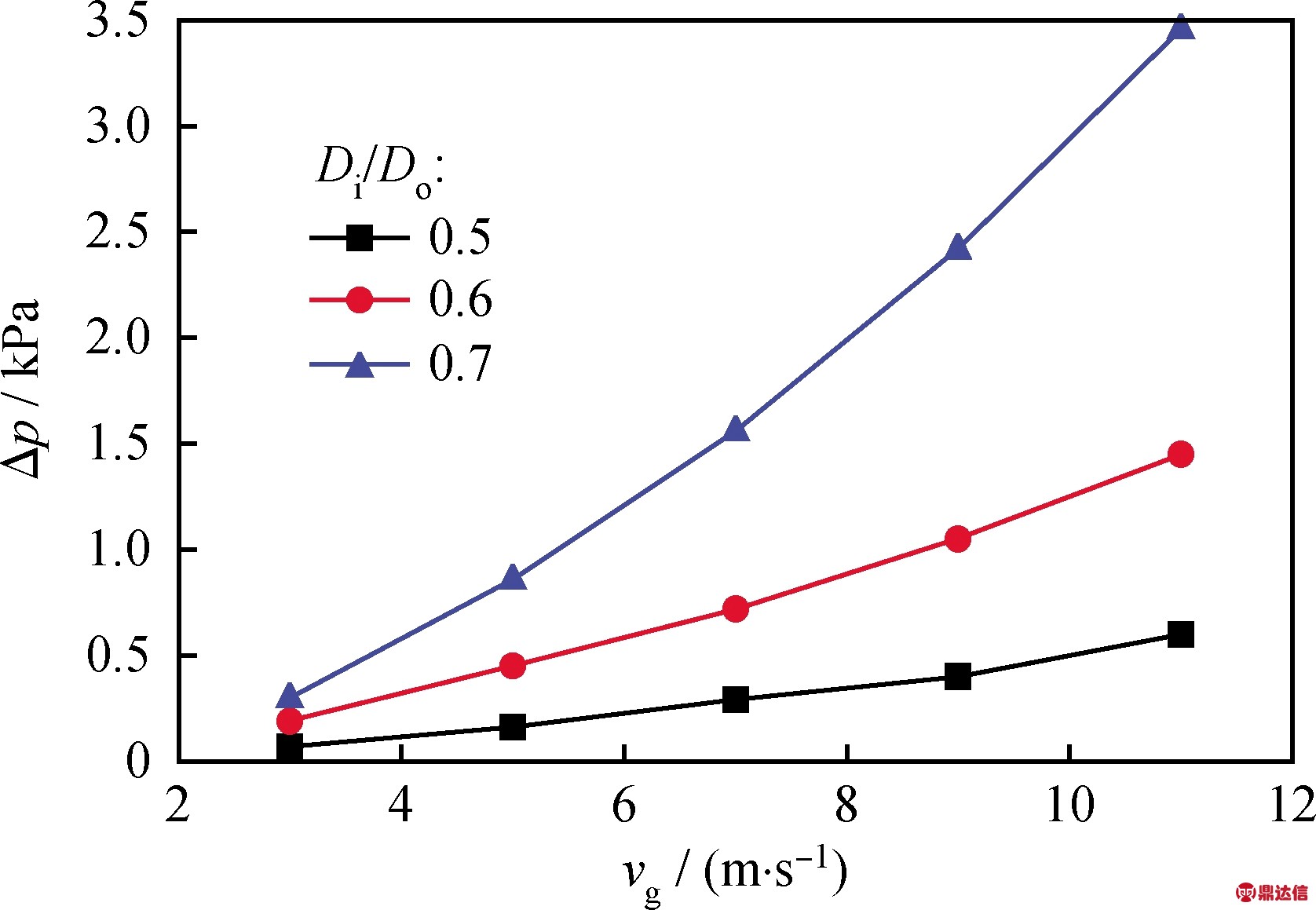
图10 不同Di/Do比下分离器压降随入口气速的变化
Fig.10 Variation of pressure drop with inlet velocity at different Di/Do ratiosβ=45°; De/Do=0.85; L/Do=3
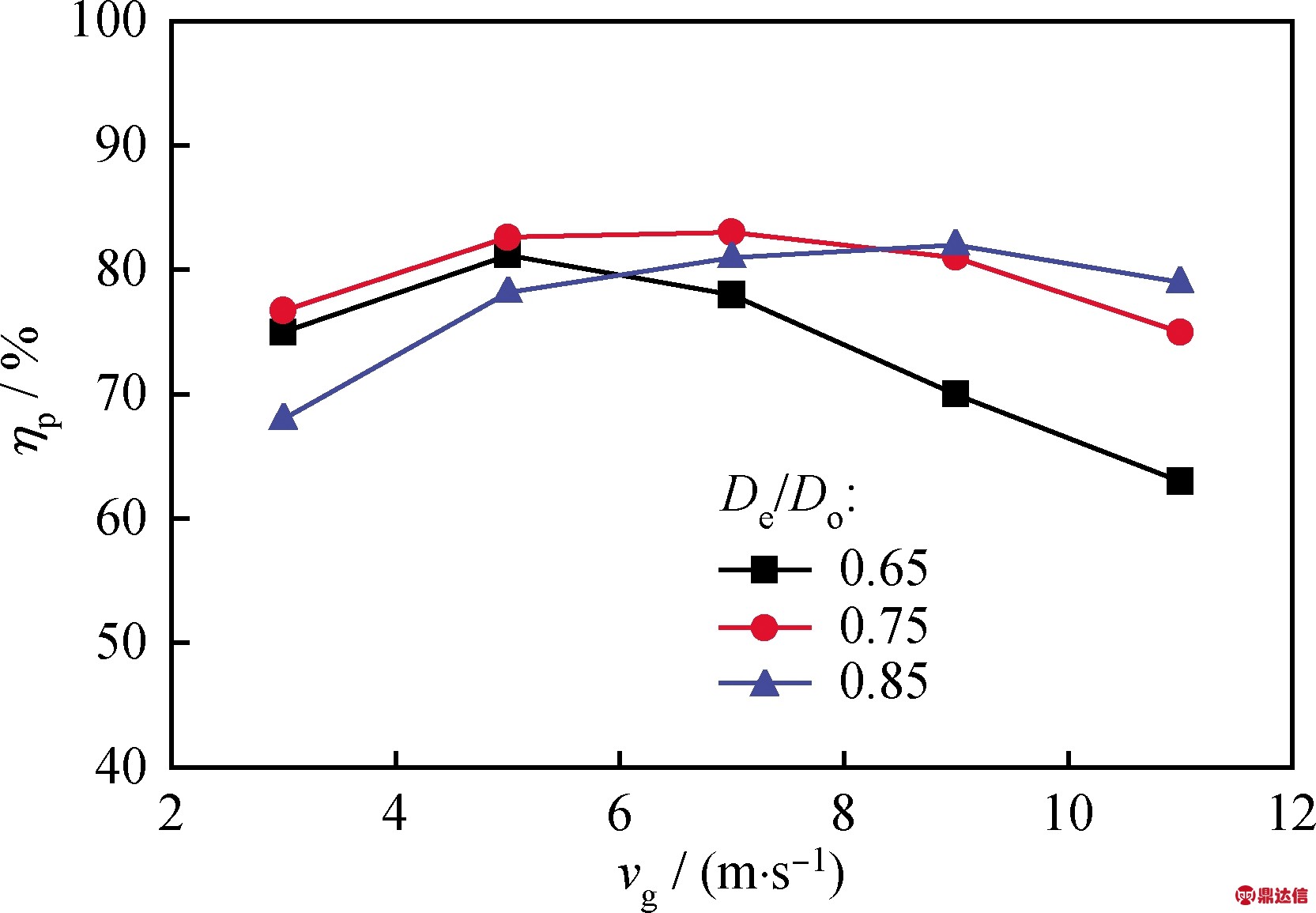
图11 不同De/Do比下分离器总分离效率随入口气速的变化
Fig.11 Variation of overall separation efficiency with inlet velocity at different De/Do ratiosβ=45°; Di/Do=0.5; L/Do=3
图12为不同De/Do比下分离器压降随入口气速的变化。由图12可知,当De/Do=0.65时,随着气速增大,分离器压降急剧增加。这是因为随着排气管直径的减小,内部气体流速增加,能量的湍流耗散增加。同时排气管流通面积减小也造成排气时气体流动截面积突然缩小,造成大量的节流损失。因此对于排气管设计,在保证分离效率的前提下,适当增加排气管直径。
通过上述实验发现,对于内置中心体的轴流式旋流分离器,在低气速下,减小导流叶片出口角、增大中心体直径、减小排气管直径均能够提高分离器的分离效率,并且存在相应的气速使特定结构分离器的分离效率达到最大。随气速继续增加,分离器分离效率开始下降,压降急剧增加。对于实验所用分离器,当vg>7 m/s时,设计分离器Di/Do=0.5、De/Do=0.85、L/Do=3、β=45°,分离器内旋流强度适中,压降相对不大,分离效率较高且逐渐稳定。
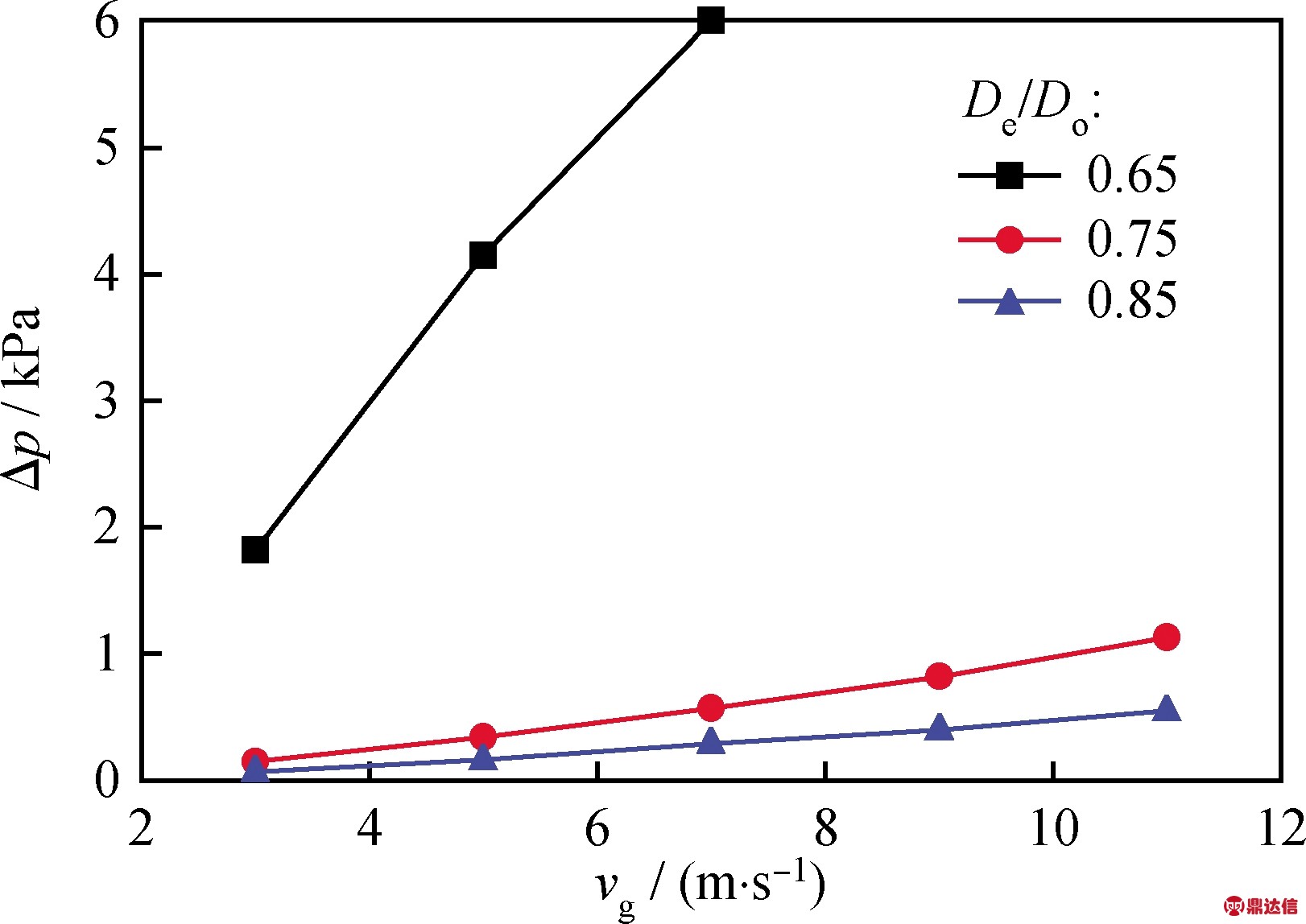
图12 不同De/Do比下分离器压降随入口气速的变化
Fig.12 Variation of pressure drop with inlet velocity at different De/Do ratiosβ=45°; Di/Do=0.5; L/Do=3
4 结 论
(1)针对内部设置中心体的新型轴流式气-液旋流分离器,根据分离器内部流场分布以及液滴的受力分析,建立了分离器分离效率的理论模型。实验发现,通过模型求得的液滴粒级分离效率的理论值与实验值一致性较高,可用于液滴分离效率的计算。
(2)研究表明,轴流式分离器分离效率与结构参数和操作参数相关。在低气速下,减小导叶出口角、增加中心体直径以及减小排气管直径均能够有效提高分离效率。对于一定结构分离器,存在相应的临界气速使分离效率达到最大,随气速继续增加,分离效率呈下降趋势。因此对于处理量较大的情况,可通过增加分离结构尺寸,以满足分离要求。
(3)根据实验结果,提出不同工况下分离器的设计准则,当入口气速较低时,可根据理论模型对分离器结构参数进行调整。当入口气速高于7 m/s时,分离器内部发生携液现象,设计导叶出口角为45°,中心体直径与筒体直径比值为0.5,排气管直径与筒体直径比值为0.85,分离器长度与筒体直径比值为3,能够保持分离效率较高且逐渐稳定,压降在合理范围内。
符号说明:
CD——气体对液滴的阻力系数;
dp——液滴直径,m;
dp,c——液滴临界直径,m;
dp,r——计算液滴直径,m;
De——排气管直径,m;
Di——中心体直径,m;
Do——筒体直径,m;
FD(t)——液滴所受曳力,N;
Ff——液滴受浮力,N;
Fm(dp)——液滴直径为dp的质量分数;
Fp——液滴受离心力,N;
lw——排液间隙,m;
L——环形分离区长度,m;
m1——供液罐液体减少质量,kg;
m2——集液罐增加质量,kg;
Δp——分离器压降,kPa;
r——液滴径向位置半径,m;
Re——排气管半径,m;
Ri——中心体半径,m;
Ro——筒体半径,m;
Rr——计算液滴径向位置半径,m;
Re——雷诺数;
导叶出口截面轴向速度,m/s;
导叶出口截面切向速度,m/s;
uθ——环形分离区液滴切向速度,m/s;
uz——环形分离区液滴轴向速度,m/s;
ur——环形分离区液滴径向速度,m/s;
|Δu|——气体与液滴径向速度差,m;
vg——入口气速,m/s;
Vg——气体矢量速度,m/s;
Vp——液滴矢量速度,m/s;
β——导流叶片出口角,°;
ηp,r——计算液滴分离效率,%;
ηp——总体分离效率,%;
μg——气体运动黏度,kg/(m·s);
ρp——液滴密度,kg/m3;
ρg——气体密度,kg/m3。