摘 要 为了缩短某装置包装线的包装机故障信号的判断时间并降低维护工作量,在不改变原程序的基础上,利用原OMRON CQM PLC的空闲寄存器资源进行编程,同时将故障代码通信至新增数码管显示器进行显示,实现了包装线包装机故障信号的自动判断,使得故障处理过程标准化,并增强了维护工作的通用性。
关键词 故障判断 包装机 顺控程序 标准化 通用性
某生产装置的包装机于1999年投用,已连续使用十五年,现场检测和执行元件多、动作频率高、控制系统内部逻辑复杂且故障不易判断。目前,主流包装机的称重和台车送袋部分,均以伺服电机作为执行机构。而该包装机的下料称重部分采用气缸实现粗流和精流调节,台车送袋也由气缸控制。长时间的使用和频繁动作使得气缸和相应的机械部件磨损严重,时常有机械位置不到位,而检测元件却无法检测到信号的情况发生。信号线、控制柜电气元件和现场检测元件老化,硬件故障率逐年上升。
包装机现场利用各类光电和接近开关作为检测元件,通过OMRON CQM PLC内部控制程序输出信号至电磁阀,控制气缸完成各类动作的执行。该套PLC无上位监控设备,PLC程序的在线监测功能需要安装有CX-PROGRAMMER编程软件的笔记本电脑,通过PLC自带串口通信实现。PLC的输入输出卡件利用内部固态继电器进行隔离,长时间使用造成输入输出通道工作不可靠,增加了故障处理难度。
1 包装机维护工作现状
OMRON CQM PLC系统的集成度高,操作工和维护人员对其内部程序无法实现实时监测。操作人员对工艺条件不满足造成的故障无法进行快速判断,只能通过仪表维护人员对故障进行排除来确定引发故障的原因,如包装机输入风压波动,造成运行时不能正常夹袋;操作人员停电顺序不当使得真空泵管线进水,真空度降低,开袋真空开关未检测到正常真空,出现反复吹袋等现象。由于工艺和机电仪综合故障的频发,致使维护人员工作量增加。
若出现检测元件自身原因或机械位置未到位而造成的故障,由于包装机故障隐蔽性较强,判断方法没有明确的参考标准,维护人员通过简单现象分析故障原因需要花费较长时间。当故障无法判断时,只能通过编程软件对PLC中的程序进行在线测试来判断输入输出信号是否到位。由于部分故障的判断涉及到复杂的逻辑,因此日常维护经验在故障分析中起到了决定性的作用。该类包装机相比其他常规仪表的维护工作来说,通用性较低。
2 增加信号故障自动判断功能的目的
为了使包装机的故障判断与处理过程实现标准化,降低工作人员的维护经验在故障判断过程中的作用比重,降低包装线的整体维护工作量,需要使包装机信号故障判断过程实现自动化,让操作人员和无该类设备维护经验的工作人员能够通过故障代码快速对故障进行判断和处理。
3 包装机信号故障自动判断功能的实现
由于该包装机由PLC进行逻辑控制,所以笔者采用PLC内部丰富的空闲寄存器资源,在不变更原程序和增加过多外部设备的基础上,实现包装机信号故障自动判断的功能。根据包装机的动作过程具有周期性的特点,以全部程序执行一次作为一个程序周期。在一个程序周期内所有动作的执行都环环紧扣,某个动作不到位会使下一个或下几个动作都无法正常执行。依据这一特点,对信号的翻转状态进行锁定。每实现一个动作便对标志位进行累加,将前一步的判断标志作为下一步的判断条件,使所有判断程序实现顺控功能,已锁定的信号便可以按照动作顺序实现同步累加。
首先按照实际动作顺序合理划分程序段,并且提取每个动作的判断条件。然后将每个判断条件对应一个锁存位,按照顺序依次定义判断程序,最后增加复位和通信功能。通过对原程序的观察可以判断,在包装机正常工作时所有的检测元件在一个程序周期内至少会翻转一次。当某个信号发生故障时,包装机会保持当前状态不再继续动作,后续动作的检测信号在该程序周期内便不可能发生翻转。在包装程序正常执行时,累加值会随动作的传递自动累加,在不发生故障的情况下,每当包装机执行完一个程序周期后,借助包装机最后一个动作的标志位,对累加值和锁存标志位进行自动清零和复位,即可实现判断程序的自动循环。
3.1 实现步骤
3.1.1 程序段的划分
图1为原包装机程序树形图,以原程序的编程顺序为基础,按照不同动作的执行顺序划分。图2为增加动作判断程序段后的树形图,该树形图在包装机原程序段不变的基础上,按照包装机执行顺序分为30段,加一个复位段,共新增31个程序段。30个程序段代表一个程序周期内包装机正常运行必须执行的30个动作。
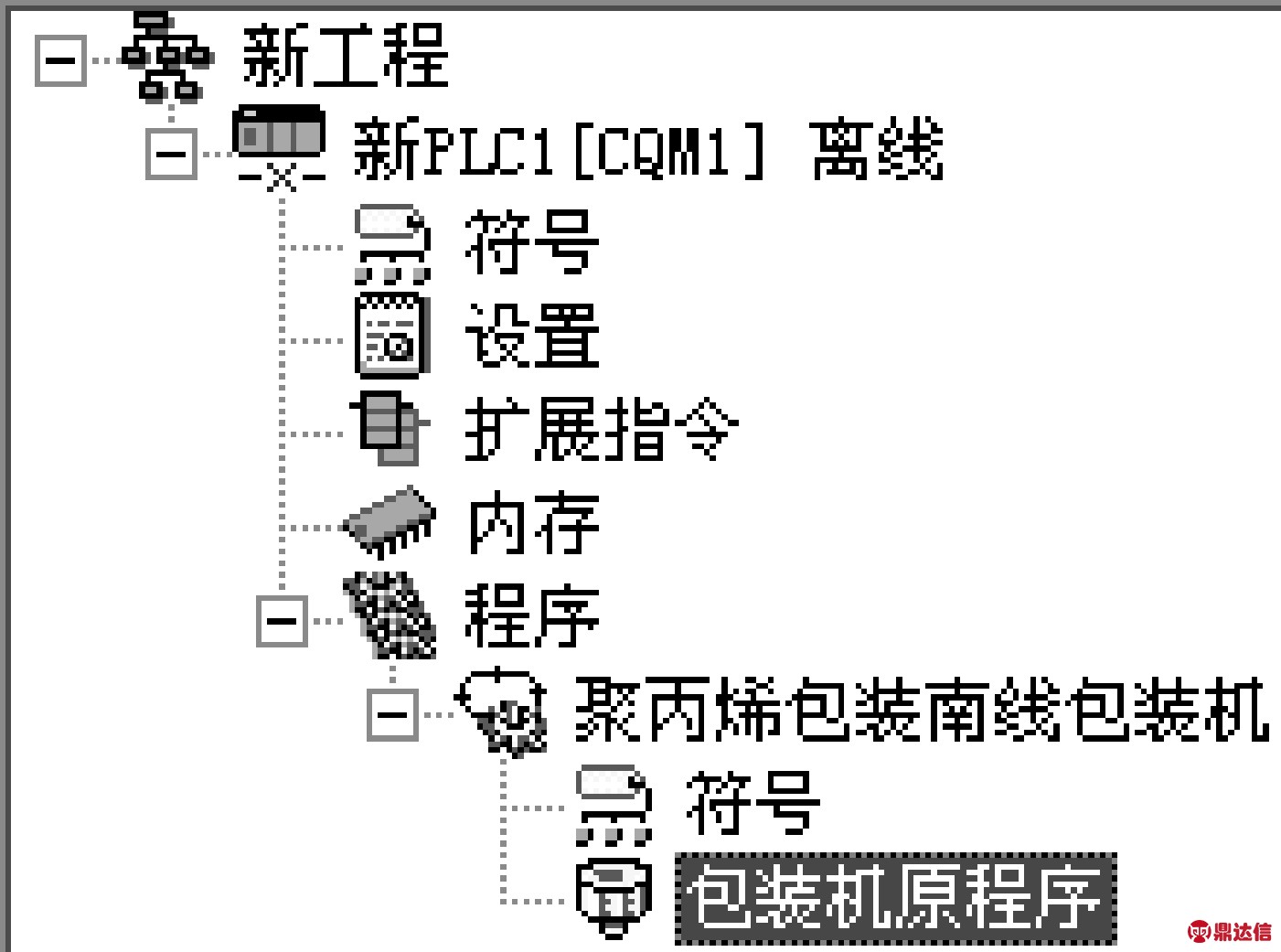
图1 原包装机程序树形图
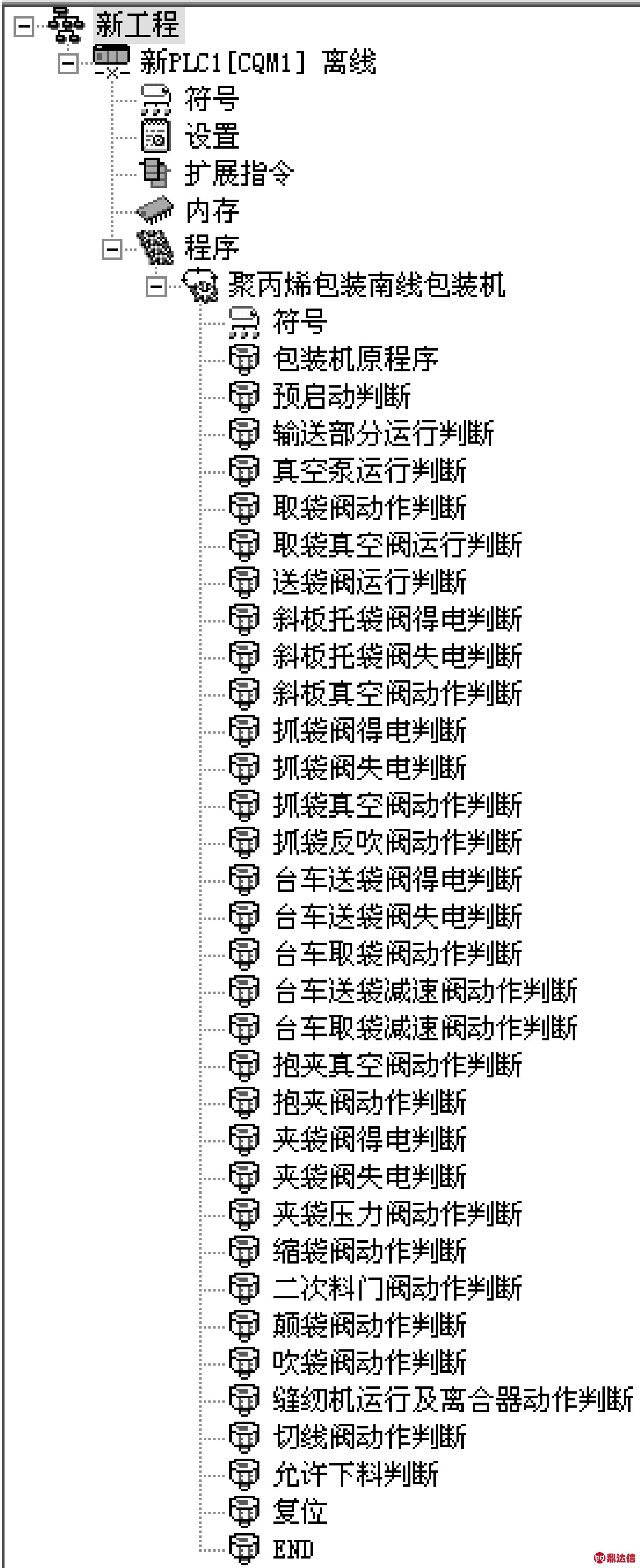
图2 增加动作判断程序段后的树形图
3.1.2 判断条件的提取
图3为原程序预启动逻辑,是包装机原程序中第1个必须执行的动作。以该动作为例来说明判断条件的提取方法,线圈116.00为预启动中间变量的线圈,可以看出,影响116.00线圈得电的条件有0.09(包装系统启动按钮)、0.08(包装系统停止按钮)和0.06(手动抱夹选择开关)。使原程序中常开和常闭点的状态保持不变,在预启动判断程序段中编程,如图4所示,分别将每个条件对应一个锁存位。0.09常开点对应输出4.01,0.08常开点对应输出4.02,0.06常闭点对应输出4.03。4.01、4.02、4.03均为空闲寄存器。“SET”指令表示只要输入条件满足,便会对相应位进行置位,即使信号丢失,不会影响锁存位的状态,达到了锁存效果。
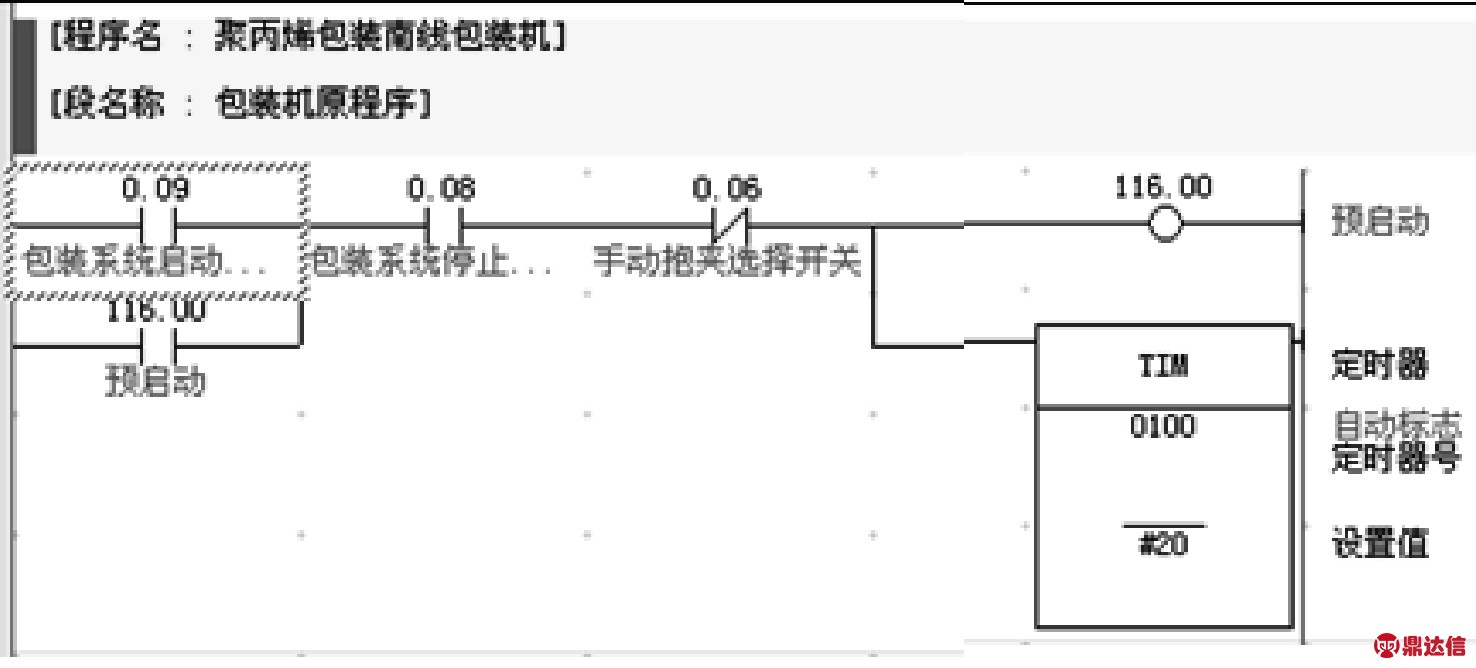
图3 原程序中预启动逻辑
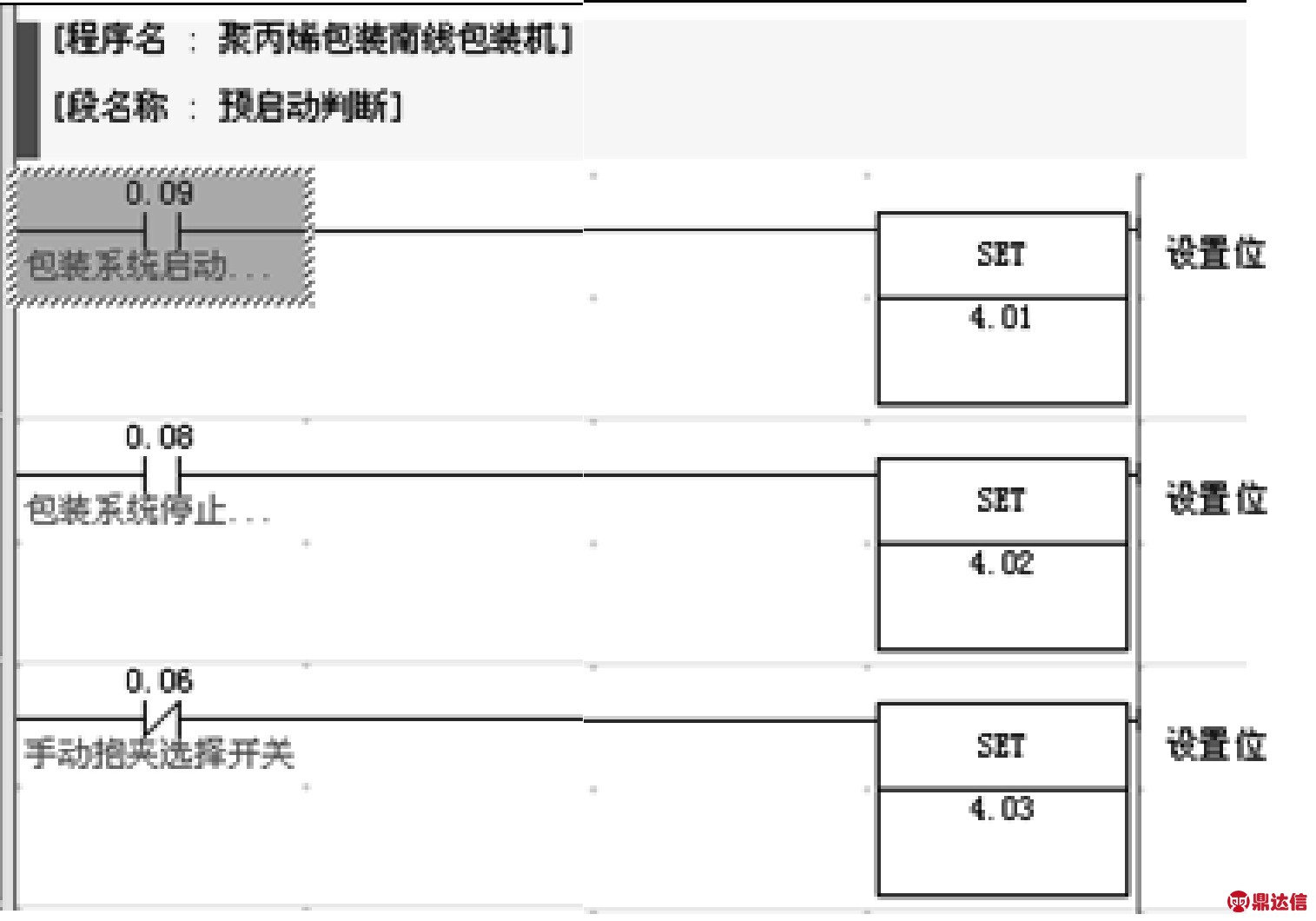
图4 预启动判断锁存逻辑
由于部分判断条件参与了不同动作的判断,就造成部分故障代码可能重复出现。如果将重复条件删除,对判断条件进行重新排序,则会出现一部分动作无可用判断条件的情况。因此,为了简化判断条件的提取过程,同时使判断条件与包装机的实际动作同步,判断条件完全按照原程序的结构和顺序进行提取。一个故障可能有多个不同的故障代码,但并不影响实际故障判断效果。
3.1.3 标志位的累加与转换
结合图4的预启动判断锁存逻辑与图5的启动条件判断逻辑,当包装系统启动按钮0.09输入信号未到位,即包装机还未启动之前,4.01常闭点处于闭合状态,中间变量34.01线圈得电,其常开点闭合,使带有下降沿微分判断功能的34.02线圈得电。34.02下降沿微分常开点不满足条件不闭合,联锁逻辑段未得电,不执行其逻辑段内程序。联锁逻辑段IL和ILC之间的程序包括一个BCD码累加功能块和一个数据转换块。
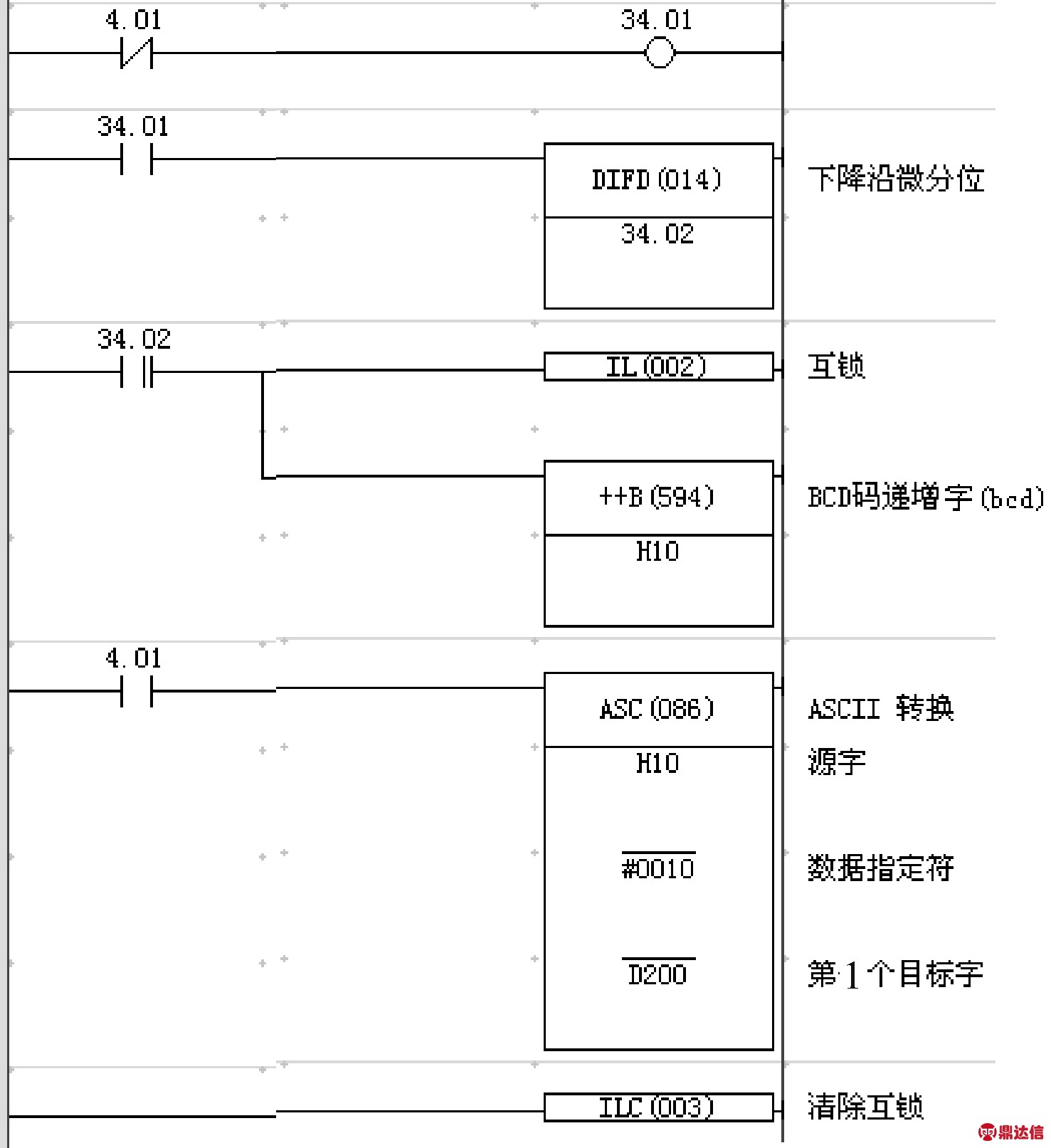
图5 启动条件判断逻辑
当包装系统启动按钮0.09输入信号到位后,4.01置位1,同时4.01位的常闭点断开,34.01线圈失电。34.01常开点断开,34.02线圈失电。当34.02下降沿微分常开点检测到失电信号后,其状态发生翻转,互锁程序段满足条件后执行,累加标志加1,同时将累加值转换为ASCII码,存于地址D200中。
3.1.4 判断条件之间顺控功能的实现
由于包装机PLC系统上电后,所有检测信号的初始状态不可能完全一致,部分检测信号在PLC上电后就处于得电状态。说明PLC在上电瞬间,部分检测信号便实现了锁存位的置位,若只对置位的判断条件进行简单累加,则累计标志无法和实际动作同步。因此,只有在信号判断锁存的基础上按照包装机正常的动作顺序,在各个判断信号之间加入顺控条件,才能实现判断功能与实际动作的同步。
结合图4的预启动判断锁存逻辑和图6的停止条件判断逻辑,当包装系统停止按钮0.08信号到位后,4.02置位1,4.02位的常闭点断开。从程序中可以看出,启动按钮的中间变量34.01与4.02的常闭点并联后输出控制34.04位,两者为“或”的关系。要使34.04线圈失电,4.02的常闭接点和34.01的常开接点要同时断开,说明该程序段中停止按钮信号的判断条件受到上一步的影响。如果前一步启动按钮判断条件未满足,使34.01线圈处于得电状态,即使当前步的判断条件4.02到位,其常闭接点断开,34.04线圈也不会失电,当前判断程序的标志位便不会实现累加。因此,在每个判断条件的程序段中,加入前一个动作判断条件的中间变量,是触发当前判断程序段的必要条件。前一个动作判断条件的翻转使当前程序段成为活动程序段,实现了与顺控程序相同的功能。

图6 停止条件判断逻辑
为了增强累加标志判断的可靠性,在每一个累加标志位的输入条件中加入上一步的锁存位,即当前步的中间变量34.05和前一步的锁存位4.01共同满足,才能使当前步累加标志位实现累加。
表1是截取的部分连续判断条件锁存位,以此为例,假设了包装机某个动作瞬间判断条件的状态。当包装机由于4.03信号故障停止后,它之后的判断条件无论是否为1,均不会累加进标志位,也就是说标志位累加到4.03便停止了。同时,也说明4.03之前所有的判断条件必定为1。当前累加标志位的值为2,是4.01和4.02之和,2作为4.03信号故障代码,与实际故障信号同步。较为特殊的是首个信号的故障代码,当第1个信号发生故障时,故障代码便是累加的最大值,说明第1个判断信号故障。
表1 锁存位累加判断示例

3.1.5 累加值的清零和锁存标志复位
当包装机由于某个信号故障而停止动作后,标志位的累加值便是当前故障信号的代码。当故障消除后,重新启动包装机时PLC内部程序会从头执行,在此之前,必须通过手动输入按钮对当前累加值进行清零并将动作锁存标志复位,才能使包装机动作和判断程序都回到起始位置,实现判断功能与实际动作的同步。
当包装机正常工作时,在未出现信号故障的情况下,所有锁存位均会置位1,累加值是个动态累积过程。一个程序周期结束标志着一次判断过程也同时结束,这时需要对该判断过程的锁存位进行复位,并对累加值清零,以便在下一个程序周期内继续实现累加和锁存功能。如图7所示,当一个程序周期执行完毕后,以最后一个动作输出线圈101.4和最后一个信号锁存位33.5共同作为累加值清零和锁存位复位的条件。
3.1.6 通信输出和显示
通信输出利用该PLC CPU自带的RS232串口实现,外接数码管显示器,属第三方设备,因此采用无协议通信方式,通过PLC的TXD指令直接输出至显示设备。显示设备为LED_COM-01-RS232型串口数码管电子看板LED数码显示器,由于显示设备只接收ASCII代码,因此需要每个判断程序段将当前累加值转换为ASCII格式。通信程序段的累加值转换和通信逻辑如图8所示。
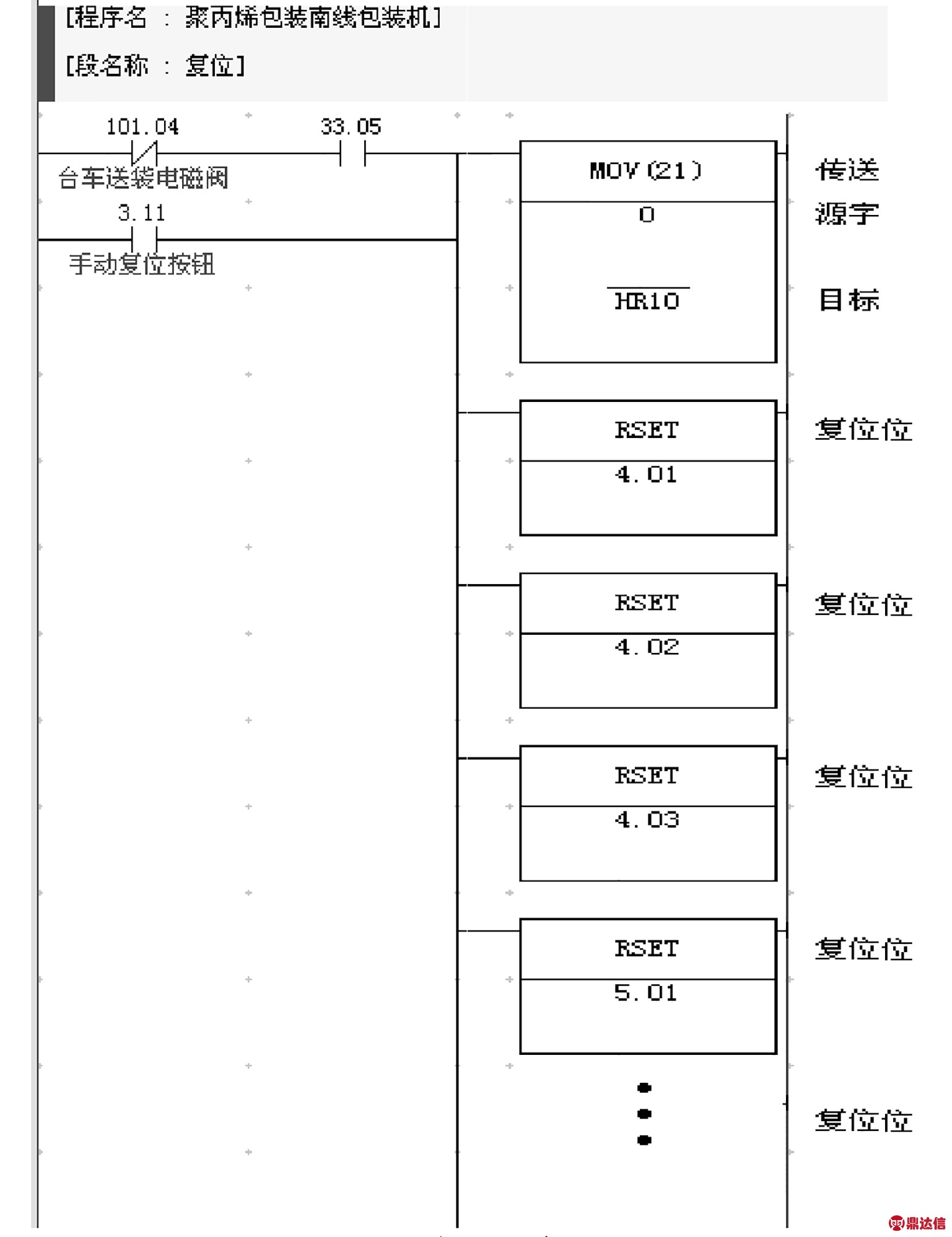
图7 判断条件复位逻辑
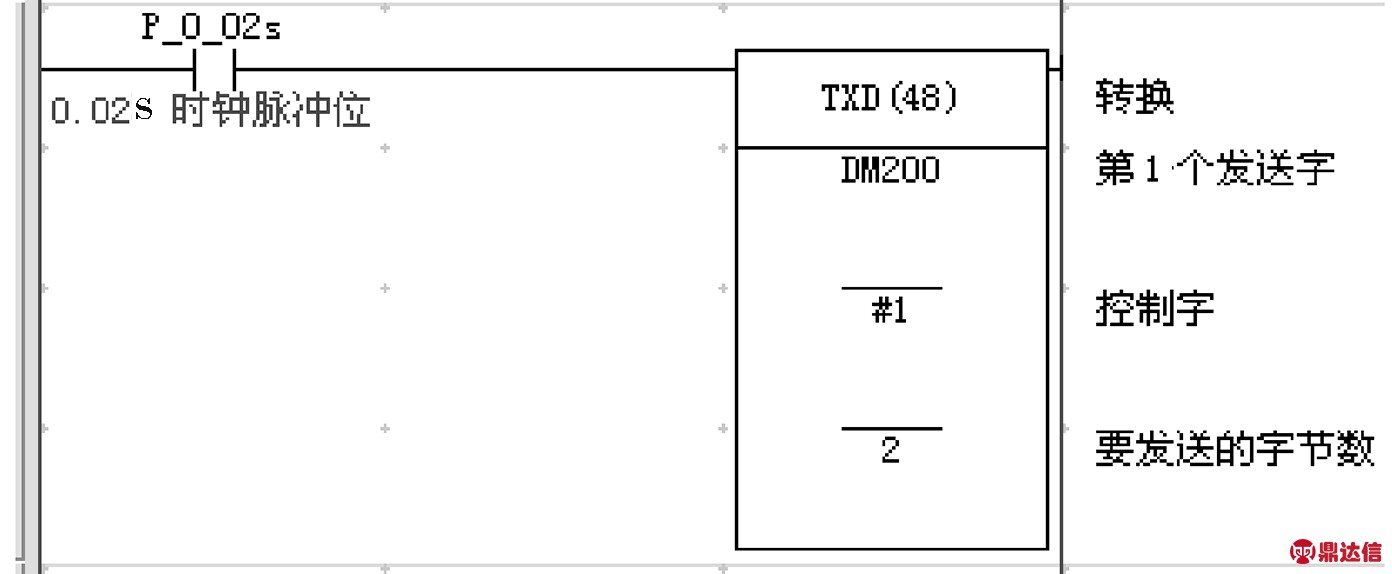
图8 累加值转换和通信逻辑
3.2 故障信号查询和故障处理方法
将每个判断条件对应的故障代码进行整理,制作表格并张贴在包装机操作台附近。若包装机在正常运行过程中突然停止,操作人员应当首先确定包装机控制柜上数码管所显示的故障代码,然后根据故障代码查找出对应信号的地址和名称,并根据实际情况,判断该信号故障的原因是否由于工艺条件未满足造成,如某个真空开关接点未翻转,可以先判断真空系统是否存在故障,若存在故障,对故障进行排除后,按下数码管显示器旁的复位按钮,对故障代码进行复位,然后重新开机。若包装机仍然出现相同的故障代码,则联系仪表维护人员对故障进行进一步查询。
仪表维护人员根据故障代码检查相应判断信号条件是否满足,即前一步动作是否执行到位。若不到位,检查并测试前一步动作相关执行机构是否正常工作,包括电磁阀信号是否到位、电磁阀是否正常切换及气缸是否正常动作等。若前一步动作到位,则检查该故障信号通道是否正常,包括信号检测元件供电、接线是否完好、PLC通道指示灯是否正常等。
4 结束语
信号故障自动判断功能的增加可以促进实际操作更加规范。当出现由于操作疏忽造成的故障时,操作人员可以通过故障信号的指示快速判断。仪表维护人员处理包装机故障的过程也更为标准,使检修标准化程度提高,包装机检修方法的通用性也随之增强。
利用PLC系统的逻辑运算功能,按照实际使用要求灵活编程,可以使故障处理过程标准化,并增强维护工作的通用性,具有较高的应用价值。由于PLC型号和编程者水平的限制,部分功能的程序编写较为繁琐,如,该型号PLC中的复位指令只能对每一位进行,造成编程工作量增加。实现信号故障自动判断功能的编程方法并非仅此一种,根据不同机型,可以用更先进的指令和更加简洁的方法简化程序,这里只是重点对编程思路进行介绍。信号故障自动判断功能并不局限于某一类控制系统,可以基于软件层面,利用各类控制系统强大的软件资源对输入信号进行快速准确的判断,来满足实际生产要求,使控制程序更为智能化,优化复杂逻辑的判断方法,提高生产设备整体可靠性。立足于不同控制系统,将信号故障判断程序模块化应用是今后的发展方向。