摘 要:分析了平面铣、型腔铣/深度加工轮廓、固定轮廓铣曲面驱动、HOLE_MILLING 四种操作在孔铣削方面的异同。剖析了THREAD_MILLING牙型和螺距四种类型(从模型、指定、从表、从刀具)在螺纹铣削加工方面的差异,并比较了THREAD_MILLING、HOLE_MILLING的异同点。
关键词:曲面驱动;孔铣削;螺纹铣削
0 引 言
目前,虽然孔加工可通过车削、铰制等工艺方法获得,螺纹可采用板牙、丝锥、滚制、螺纹车削加工制取,但在一定程度上存在着诸如表面质量差、加工效率低、尺寸精度难以保证的问题。随着数控设备的普遍推广和应用,一把镗刀可以镗削不同公称直径孔,一款螺纹铣刀可以加工同螺距不同规格内、外螺纹,孔及螺纹铣削技术具有效率高、质量好、刀具通用性强的优点。
1 孔铣削加工
UG软件中常见可实现铣削孔操作有平面铣操作、型腔铣/深度加工轮廓操作、固定轮廓铣曲面驱动三种。对于平面铣、型腔铣/深度加工轮廓操作而言,螺旋铣孔需要通过非切削移动参数的巧妙设置实现。在操作界面“非切削移动”→“进刀”→“封闭区域”→选择“沿形状斜进刀”,“斜坡角”与“高度”控制铣削一周切削深度。为控制程序刀轨一圈切削深度,可通过“屏幕距离”大致测量,如图1所示[5]。平面铣、型腔铣/深度加工轮廓操作实现螺旋铣孔的刀轨路径如图2(a)所示。孔铣削可覆盖大部分尺寸的孔加工,实现开粗、扩孔,以铣代铰、代镗半精、精加工,对尺寸精度的控制,与钻削依旧是孔加工效率最高的方法。
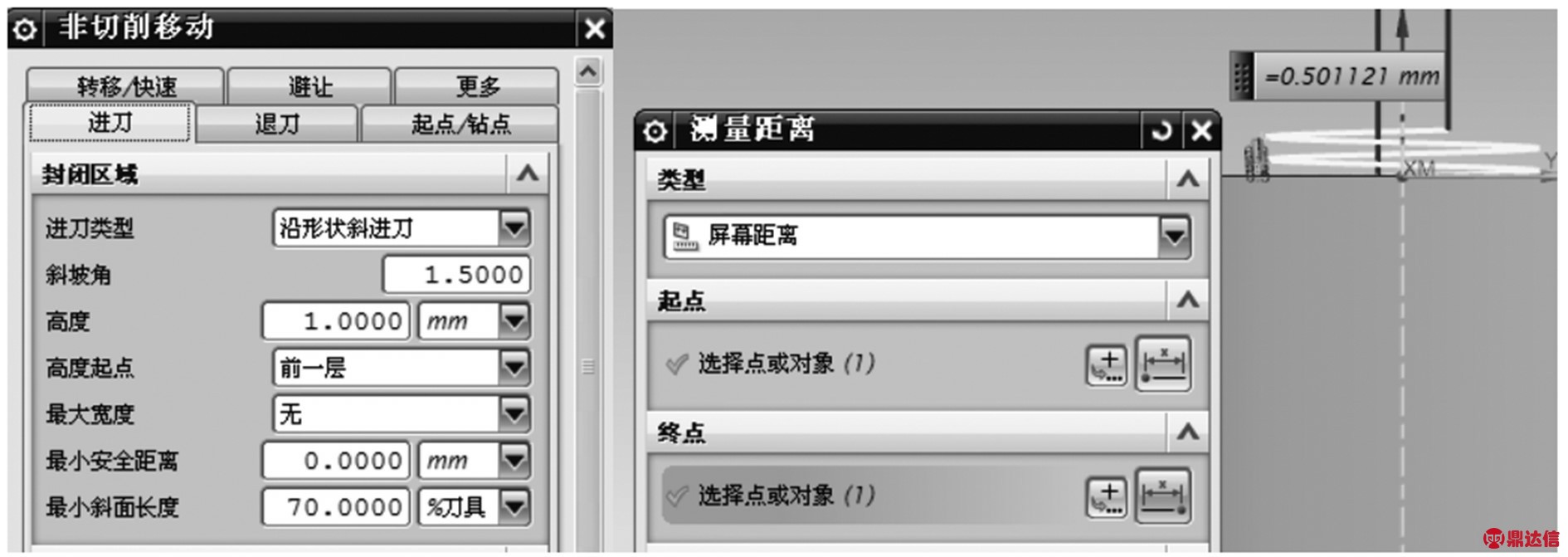
图1 非切削移动界面设置及屏幕距离测量一圈切削深度量
二者差异在于:平面铣针对2D轮廓线进行加工,部件与毛坯材料侧含义完全相反,部件材料侧为非切削区域(材料保留侧),对于非封闭区域材料侧还与轮廓线箭头方向有关。型腔铣/深度加工轮廓为3D加工操作,需选择加工部件、加工区域。
1.1 固定轮廓铣曲面驱动操作
在固定轮廓铣曲面驱动操作中实现螺旋铣,通过“切削模式”→“螺旋”设置实现[1]。切削深度通过“步距”→“数量”调整,每圈切深=孔深/数量[1-2]。为提高孔加工精度,需将“切削步长”指定为“公差”,根据加工精度设置内外公差值。同时为避免进退刀与孔壁干涉,需将“非切削移动”中进退刀设置为孔中心作为进退点,刀具由孔中心点线性移动至切入点,待铣削完成内孔线性移至孔中心直线抬刀,切削效果如图2(b)所示。
1.2 专用铣削孔HOLE_MILLING操作
HOLE_MILLING为UG8.0版本后出现的专门用于铣削孔或凸台的操作,一般放置在“MILL_PIANAR”和“DRILL”模板中。进入HOLE_MILLING操作界面,点击“指定孔或凸台”图标,进入快捷菜单:在“类型”中选择“孔”,“位置”→点击“选择对象”选择视图中要加工的孔口圆,系统自动创建点位坐标,在“直径”框内输入加工部位孔直径值,“深度”输入待加工孔深度值,点击确认退出“孔或凸台几何体”快捷菜单;“工具”→“刀具”,选用已创建刀具或创建新刀具;“刀轨设置”→默认“螺旋”;“毛坯直径”→“距离”→“毛坯距离”相当于壁单侧余量,“毛坯直径”→“直径”→“起始直径”即为铣削前底孔尺寸;“轴向”→“每转深度”或“斜坡角”均用于控制每圈刀具轴向切深值;“径向”控制径向切削层数。当实际加工中只进行一次精镗,HOLE_MILLING操作界面“刀轨设置”中的轴向、径向保持默认;“切削参数”可控制顺逆铣、刀轨在顶层、底层的延伸量、孔壁余量。一般情况,非切削参数等可保持默认。
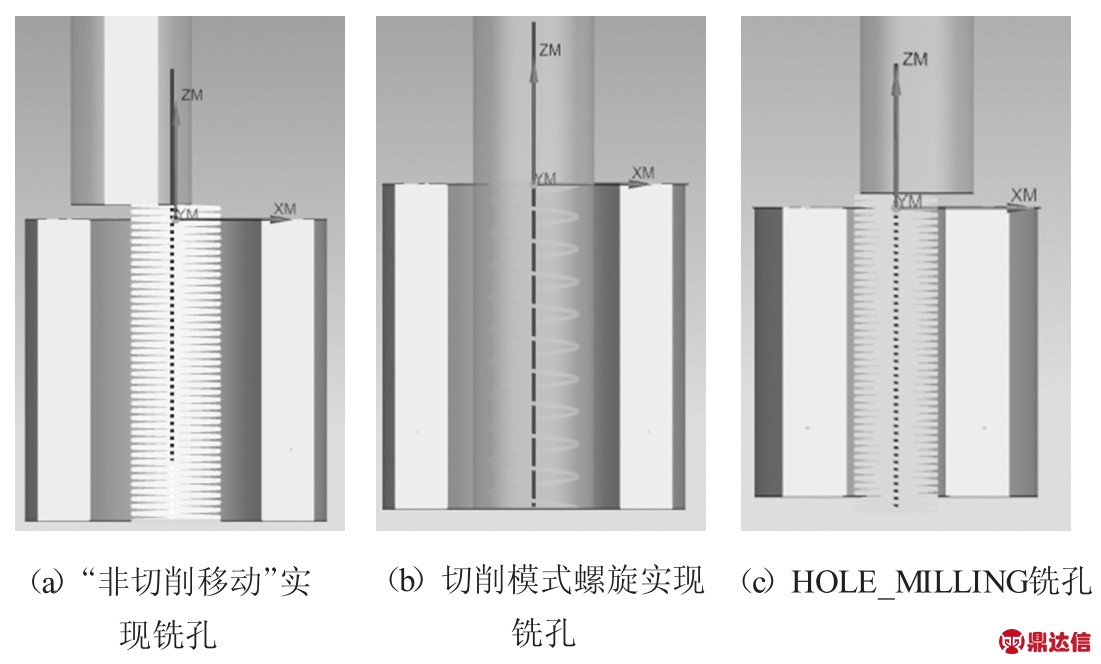
图2 孔铣削
虽然,平面铣、型腔铣/深度加工轮廓、固定轮廓铣曲面驱动操作与HOLE_MILLING操作均可实现孔、凸台铣削功能,但前3种操作设置繁琐,精确控制切深值较为困难[2]。HOLE_MILLING参数设置简单,切深易于调整,进退刀方式合理,在软件版本支持的情况下,首选HOLE_MILLING铣削孔。
2 螺纹铣削加工
2.1 THREAD_MILLING操作
THREAD_MILLING是专门用于螺纹孔或螺纹凸台铣削的加工模块。进入操作界面,点击“指定孔或凸台”图标,可选择加工类型(螺纹孔或螺纹凸台),“常用参数”→“牙型和螺距”,有四种类型(从模型、指定、从表、从刀具)。每种类型设置差异性大,熟练使用存在一定难度,现具体剖析如下:
1)“从模型”类型。首先,要求部件螺纹由螺纹特征创建;其次,操作菜单中“常用参数”→“牙型和螺距”→选择“从模型”,“位置”→“选择对象”点选部件螺纹特征,相关参数将自动获取到“孔或凸台几何体”菜单中(见图3左);在螺纹铣操作菜单中“刀轨设置”→“轴向步距”→“牙数”输入1,即单头螺纹;最后,螺纹铣刀螺距需与模型螺距匹配。同时注意,界面中“丝锥大小”为螺纹底孔尺寸。THREAD_MILLING“从模型”类型,要求数模中的螺纹几何特征必须严格按照螺纹标准参数创建,在一定程度上增加了编程难度。
2)“从刀具”类型。在THREAD_MILLING操作“常用参数”→“牙型和螺距”→选择“从刀具”,“位置”→“选择对象”指定上端孔口圆,“丝锥大小”输入螺纹底孔尺寸。以M16×2内螺纹为例,螺纹尺寸按螺纹规范依次填入:“大径”16 mm,小径13.9 mm,长度20 mm(见图3右);创建一把螺距为2的螺纹铣刀,如D10×2螺纹铣刀。在螺纹铣操作菜单中“刀轨设置”→“轴向步距”→“牙数”输入1,即单头螺纹,涉及的螺纹参数需严格遵循螺纹规范要求。
3)“从表”类型。在THREAD_MILLING操作“常用参数”→“牙型和螺距”,选择“从表”,“位置”→“选择对象”指定上端孔口圆,螺纹尺寸中“标准”选择“Metric Coarse”。以M16×2内螺纹为例讲解,其中界面中“大小”选择M16×2,指定“径向进刀”为0.75(如图4左);创建一把螺距为2的螺纹铣刀,如D10×2螺纹铣刀。在螺纹铣操作菜单中“刀轨设置”→“轴向步距”→“牙数”输入1,即可单头螺纹铣削,该类型适用于标准规格螺纹数控编程。
4)“指定”类型。在THREAD_MILLING操作“常用参数”→“牙型和螺距”,选择“指定”,“位置”→“选择对象”指定上端孔口圆,螺纹尺寸按螺纹规范依次填入。以M16×2内螺纹为例讲解,界面中大径16 mm,小径13.9 mm,长度20 mm,创建一把螺距为2的螺纹铣刀,如D10×2螺纹铣刀。在螺纹铣操作菜单中“刀轨设置”同上,生成的螺纹刀轨如图4右。“指定”类型可根据需要创建不同螺距的螺纹,只要刀具与螺纹螺距参数匹配即可,一般优先推荐选用。
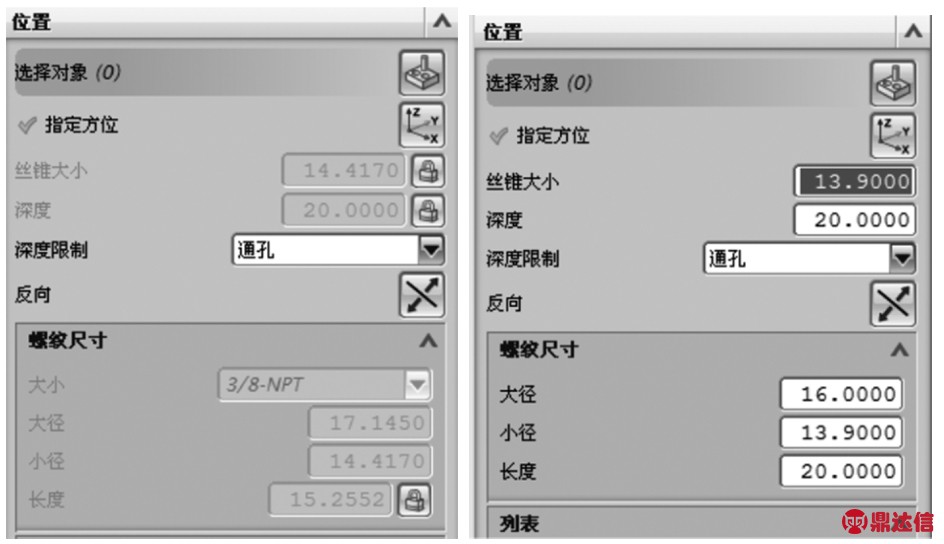
图3 “从模型”位置自动获取与“从刀具”位置参数设置
2.2 HOLE_MILLING铣螺纹
HOLE_MILLING实现螺纹铣削,需在“切削参数”中取消“添加清理刀路”选项,建议内外螺纹非切削运动设置为线性从中心进退刀。螺纹铣削刀轨通常需在顶层、底层延伸一个数值。为保证螺纹旋向正确性:内螺纹右螺纹用逆铣,右旋外螺纹用顺铣。其他操作与HOLE_MILLING铣削孔设置相同。
THREAD_MILLING可通过一把螺纹铣刀生成具有相同螺距的一系列螺纹刀轨,大大减少了刀具数量,且多齿螺纹铣刀铣削比车削可获得更好的表面质量,比板牙、丝锥具有更高加工效率,对于大规格螺纹更倾向THREAD_MILLING螺纹铣削编程加工。特别是作为THREAD_MILLING“指定”类型编程时,具有相对简单的参数设置、调整灵活性高的特点,被广大数控编程人员广泛采用。
表1 公称直径16 mm的公制螺纹规格
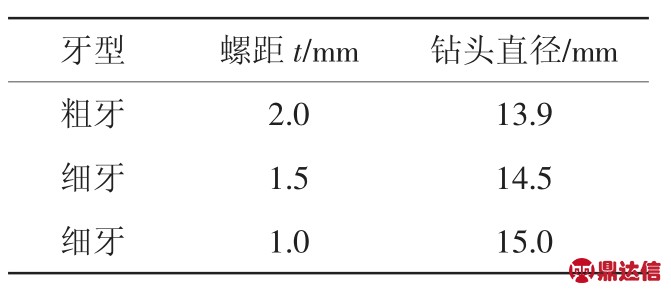
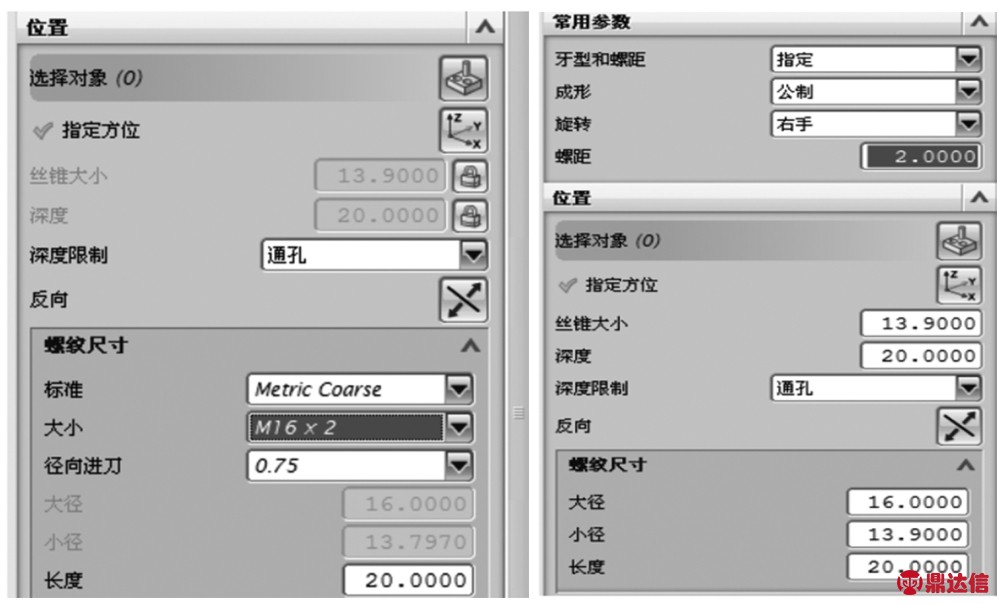
图4 “从表”与“指定”位置参数设置
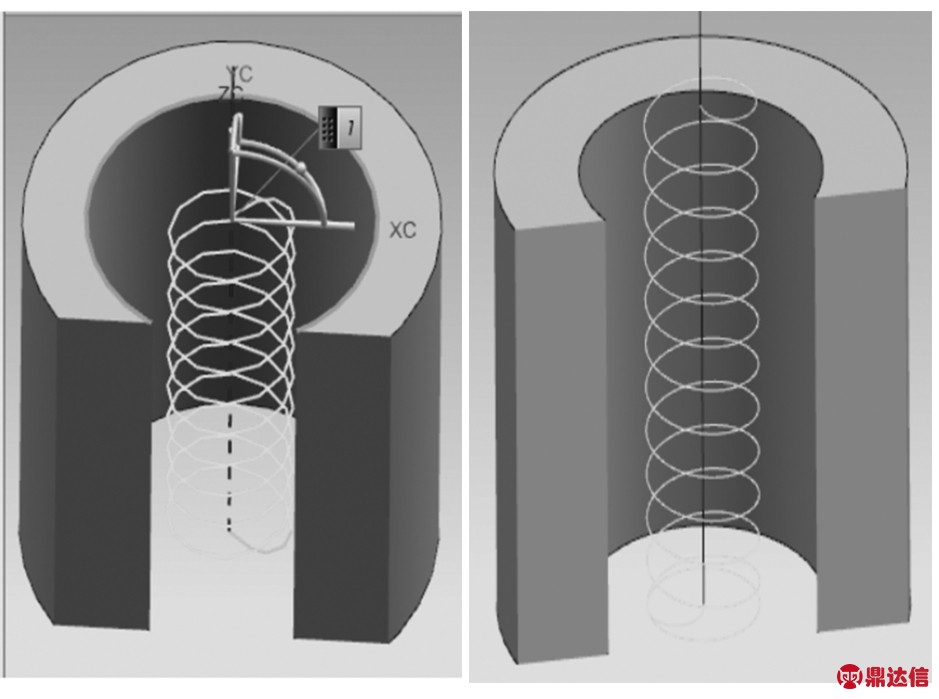
图5 THREAD_MILLING与HOLE_MILLING铣削螺纹
THREAD_MILLING与HOLE_MILLING操作(图5),虽然均可用于铣削螺纹,但是HOLE_MILLING需要手动设置刀路顺、逆铣方向来保证螺纹旋向的正确性。两者刀路在进退刀方面也有差异,HOLE_MILLING由孔口螺旋铣至孔底,而THREAD_MILLING则由孔底螺旋铣至孔口。相比而言:HOLE_MILLING擅长孔、凸台铣削,而THREAD_MILLING适合螺纹铣削。两者在多孔腔、空间孔、空间螺纹等几何特征的软件编程方面更加便捷,进退刀方式更为安全,较之传统手工宏编程更佳可靠,加工效率较之传统钻削更高,刀路调整更灵活。
3 结 语
为大力推广孔、螺纹铣削技术应用,文中对比分析
了平面铣、型腔铣/深度加工轮廓、固定轮廓铣曲面驱动、HOLE_MILLING的在孔加工编程中的异同,剖析了THREAD_MILLING牙型和螺距四种类型在螺纹加工方面的差异,并通过简单案例进行了设置说明。希望文中的编程经验和技巧能对孔、凸台、螺纹铣削加工带来技术借鉴和参考