摘要:无屑攻牙的关键技术之一是预孔孔径的合理确定,当前,还没有统一认知的理论计算模型求解无屑攻牙预孔孔径,多通过试验或丝锥厂家推荐确定。为此,研究了螺纹接触高度比与内螺纹小径、螺纹联接强度之间的关系。发现现行的内螺纹小径标准规范是在切削螺纹基础上制定的,其对应的螺纹接触高度比范围基本上为75%~100%。总结出无屑攻牙预孔孔径与螺纹接触高度比之间的数学关系。依据无屑攻牙内螺纹强度显著高于切削攻牙螺纹的现象,适度降低其螺纹接触高度比,从而更精准地平衡螺纹联接强度、内螺纹小径精度和丝锥寿命等因素,及有的放失地放宽预孔孔径加工精度范围,降低预孔加工难度。
关键词:无屑攻牙;丝锥;螺纹接触高度比;预孔孔径
0 引言
螺纹联接在电子产品中的应用极其广泛,对电子产品来说,零件内螺纹的加工一直以来有一个困扰:电子产品对金属废屑极为敏感,攻牙废屑掉落在印刷线路板或电子元件上,即可能引发短路,造成产品毁损。切削攻牙加工时,尽管花费大量的人力和物力清除废屑,但废屑残留在内螺纹中,在零件组装时才掉落在产品内部的情况还是时有发生。无屑攻牙加工后的内螺纹基本无金属屑残留,很容易清理干净。无屑攻牙又称挤压攻牙,无屑攻牙发明于1936年,但目前我国还没有普遍应用,无屑攻牙的预孔设计数据大都依赖于国外知名丝锥厂家的经验值和推荐值。本文将以公司实际产品的内螺纹预孔设计为例,对应用螺纹接触高度比计算无屑攻牙预孔直径的方法进行了分析与探索。
1 无屑攻牙丝锥的组成及工作原理
无屑攻牙丝锥的种类很多,但结构基本相同,其垂直于轴线的横截面呈多棱形,通常为4~6条,其高点称为棱脊。无屑攻牙丝锥的工作部分由导入锥、挤压锥和校准锥组成[1]。直径不大于10 mm的无屑攻牙丝锥的导入椎型式通常采用外顶尖型式(图1),其长度约为0.7倍螺纹公称直径;挤压锥的工作是攻出螺纹,最常用的型式为C型,其牙数为2~3牙,只有最后一牙牙型完整;校准锥全部是完整的牙型,其工作是校准及修光螺纹轮廓,并起导向作用。挤压锥最前端的牙到达的深度为攻牙深度,校准锥最前端的牙到达的深度为有效牙深度,有效牙深度与攻牙深度之间的螺纹不完整。

图1 外顶尖型式
攻牙时,在攻牙扭矩的作用下,挤压锥的棱脊首先挤入零件预孔的壁面,并挤出沟痕,随后各棱脊依次逐渐将沟痕加深加宽,形成内螺纹的牙底,同时被挤出的金属朝着受力最小的方向作塑性流动,直至充满螺牙的空间形成内螺纹的牙顶,最后经校正锥校正,便形成完整、符合要求的内螺纹[2],如图2所示。与切削攻牙比较,无屑攻牙具有明显的优势:不会产生废屑,挤压锥棱脊的多次反复挤压,减小了内螺纹的应力集中;内螺纹表层在成型过程中产生冷作硬化,形成强化层;内部金属纤维连续,牙型部分内应力较小,内螺纹强度显著增强;表面粗糙度低,内螺纹表面质量较好[3];螺纹精度较高,通常可达到5H~6H[4]。
从无屑攻牙的工作原理可看出,无屑攻牙是一种冷挤压加工方式,它要求被加工零件的材料必须具有一定的塑性。据国外资料介绍,被加工零件材料延展率应不低于8%[5]。
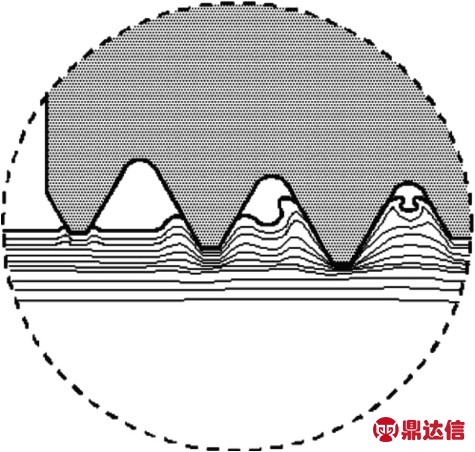
图2 无屑攻牙
2 无屑攻牙而成的内螺纹
无屑攻牙而成的内螺纹牙型与切削攻牙而成的内螺纹牙型有所不同,由于金属塑性流动的原因,无屑攻牙而成的螺纹牙型顶部呈“U”形。如图3所示,通常实际无屑攻牙而成的螺纹牙型的高度约为基本螺纹牙型高度的65%~75%[6];如图4所示,如预孔孔径偏小,则材料过度挤压,甚至无处可去,攻牙扭矩过大,丝锥剧烈磨损或折断,所得的内螺纹小径偏小;反之,如图5所示,如预孔孔径偏大,则材料挤压不够,牙型不饱满,螺纹强度降低,所得的内螺纹小径偏大。因此,要获得合格的内螺纹小径,预孔孔径一定要控制得相当精准。
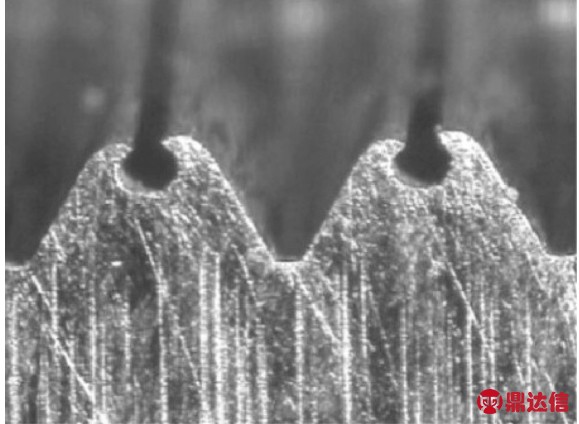
图3 “U”形
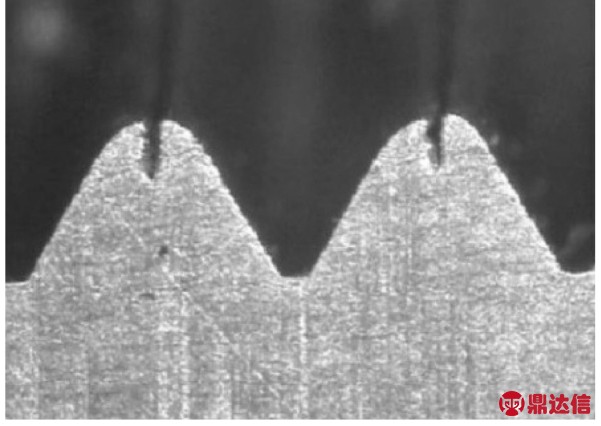
图4 内螺纹小径偏小
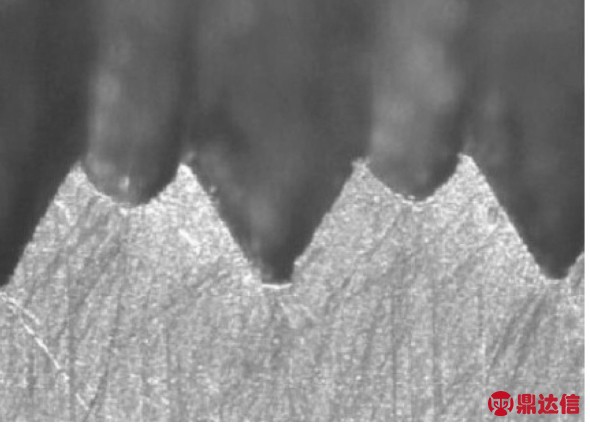
图5 内螺纹小径偏大
3 螺纹接触高度比
内螺纹与外螺纹牙型的有效接触高度与螺纹基本牙型高度的百分比称为螺纹接触高度比,螺纹接触高度比又称螺纹牙高率、螺纹饱牙率、螺纹嵌合率。其计算公式如式(1)所示:

其中f为螺纹接触高度比;d为螺纹公称直径;d0为预孔直径,螺纹接触高度比是根据切削攻牙的原理推导出来的,因此,公式中的预孔直径即内螺纹小径;H为螺纹牙型理论三角形高度;P为螺距。
基本牙型是指削去原始三角形的顶部和底部所形成的内、外螺纹共有的理论牙型,基本牙型高度为5/8 H,H=0.866 025P[7]。
根据中等螺纹等级的内螺纹小径标准规范,算得其螺纹接触高度比范围基本上为75%到100%,如M3内螺纹小径的最大值为2.599 mm,根据以上公式,算得对应的螺纹接触高度比为74.09%。
长期的生产实践发现:实际上螺纹接触高度比很难达到100%,事实上,也没必要达到100%。螺纹联接的强度与螺纹接触高度比之间的关系不是单纯的正比关系,如100%的螺纹接触高度比的内螺纹与75%的螺纹接触高度比的内螺纹比较,螺纹联接强度仅高出5%左右,但攻牙扭矩却要高出3倍;83%的螺纹接触高度比的内螺纹和65%的螺纹接触高度比的内螺纹比较,螺纹联接强度仅高出2%左右,但攻牙扭矩却要高出2倍。
4 应用螺纹接触高度比计算无屑攻牙预孔的方法
内螺纹小径与预孔孔径密切相关,切削攻牙的预孔孔径等于内螺纹小径,而根据螺纹成型机理,无屑攻牙的预孔孔径显然要比内螺纹小径大,但具体大多少,目前还没有统一认知的理论计算模型,丝锥厂商主要是根据大量的试验数据,总结得出预孔孔径推荐值的。预孔孔径决定了内螺纹小径,而内螺纹小径与螺纹接触高度比相关,螺纹接触高度比又与螺纹联接强度密切相关,螺纹联接强度取决于产品技术要求。简言之,预孔孔径与螺纹接触高度比是休戚相关的。因此,了解产品的螺纹联接强度技术要求后,根据需要可以选择适当的螺纹接触高度比,进而确定预孔孔径。在查阅、比较了多家知名丝锥厂家公开的设计方法和经验数据后,本文引入螺纹接触高度比的概念,确定无屑攻牙预孔直径的理论值计算方法如式(2)所示:

根据现行的内螺纹小径标准规范,螺纹接触高度比只能选择75%~100%,但是,现行的内螺纹小径标准规范是在切削螺纹的基础上制定的,根据螺纹成型机理可知:同等材料无屑攻牙的螺纹强度显然高于切削攻牙的螺纹强度,理论上来说无屑攻牙的内螺纹允许更小的螺纹接触高度比,即更低的螺纹牙型高度,也即更大的内螺纹小径。适当降低螺纹接触高度比,虽然内螺纹小径超出现行的螺纹标准,但同样满足螺纹联接强度要求,而且可以大幅延长丝锥寿命,放宽预孔加工精度范围,降低生产成本。实践证明:65%的螺纹接触高度比的无屑攻牙内螺纹足以满足电子产品的螺纹联接强度要求。
表1 内螺纹孔检测结果
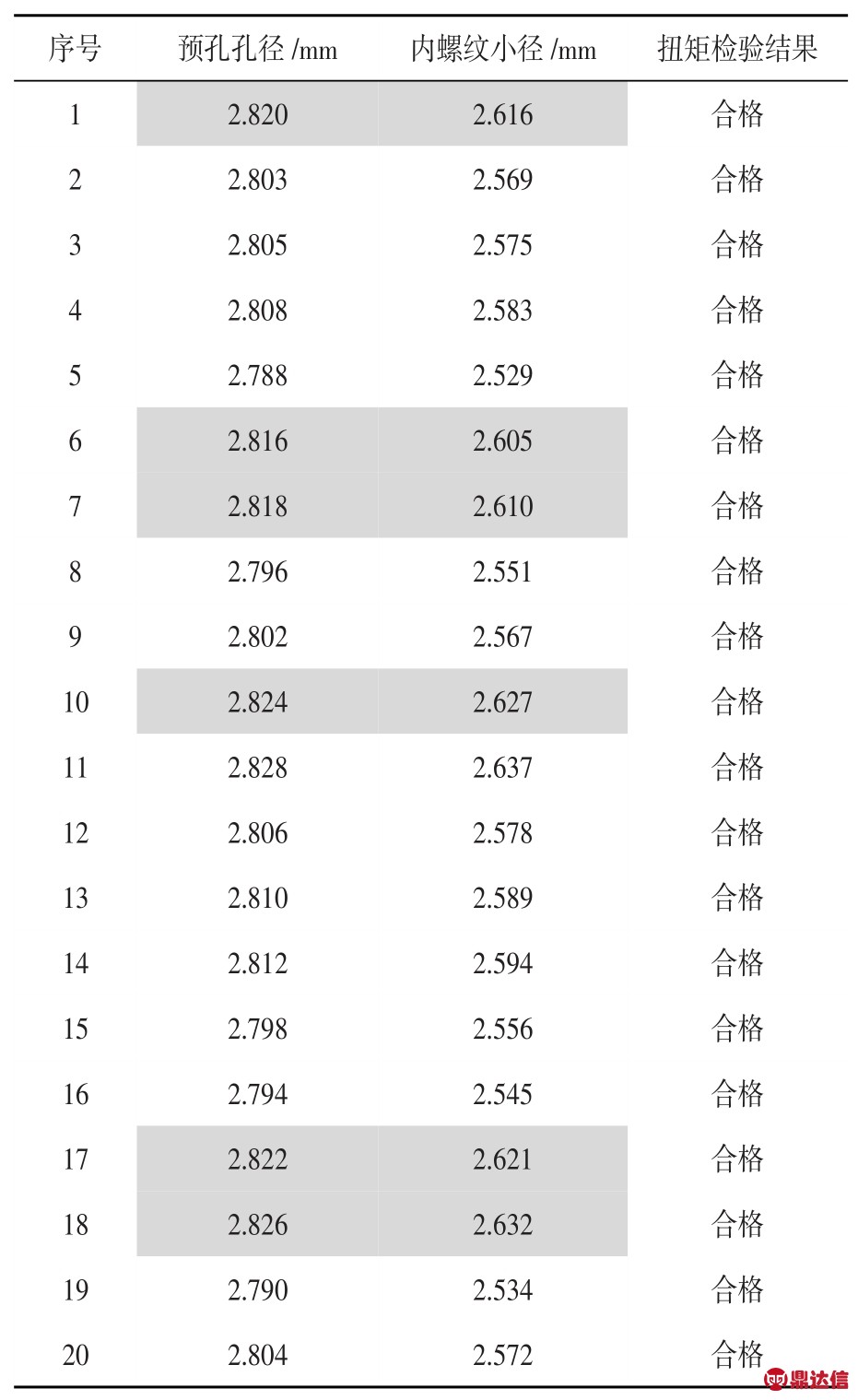
5 设计验证与分析
笔者公司产品螺纹联接零件主要为钣金零件,通常通过冲压成型的翻边孔与螺钉联接,以获得大于板厚的螺纹旋合长度。采用65%~100%的螺纹接触高度比设计无屑攻牙预孔孔径,如近期开发生产的某型一体式电脑产品,其后框分布大量的M3内螺纹孔,以锁固内部元器件。现行的M3内螺纹小径标准规范为2.459~2.599 mm,根据上述论述,选择75%~100%的螺纹接触比高度,M3螺纹丝锥精度号选用5号,算得其预孔孔径范围为2.762~2.812 mm,预孔加工精度范围较窄;选择65%~100%的螺纹接触比高度,则算得其预孔孔径为2.762~2.833 mm,预孔加工精度范围有所放宽。经过多批次生产监测(表1为第5批次抽测20个内螺纹的检测结果),完全符合设计要求。M3螺钉标准拧紧扭矩为0.5 N·m,用0.8 N·m的拧紧扭矩作为内螺纹可承受的扭矩检验标准,重复拧紧5次,用牙规检查内螺纹是否变形或损坏。从检测结果可以看出:对应75%~100%螺纹接触高度比的内螺纹小径均在标准规范范围内,牙规和扭矩检验均为合格,对应65%~75%螺纹接触高度比(灰色部分)的预孔孔径,其对应的内螺纹小径虽然已超出现行的螺纹标准规范,但牙规和扭矩检验同样合格。
6 结束语
本文从适当降低螺纹接触高度比对螺纹联接强度的影响微乎其微的角度出发,设计无屑攻牙预孔时,将螺纹接触高度比与内螺纹小径联系在一起,从而更精准地平衡螺纹联接强度、攻牙效率和丝锥寿命等因素,并适当放宽了预孔加工精度范围,降低了预孔加工难度,降低预孔加工成本[8]。笔者公司应用螺纹接触高度比计算的无屑攻牙预孔直径的产品符合客户的产品技术要求并已大量交付使用,目前,该方法正推广应用于其他产品。面对国外的技术封锁,唯有在理论分析、精确计算的基础上长期进行试验研究,才能从根本上掌握无屑攻牙预孔设计。希望本文的探索对大家在设计无屑攻牙预孔时有所帮助。