[摘 要]针对电站锅炉过热器和再热器管滑块焊趾裂纹检测工况复杂检测难度大的问题,本文在分析过热器和再热器管滑块焊趾裂纹产生机理的基础上,采用爬波检测技术,开发了爬波检测探头、试块及检测工艺。对某电厂锅炉滑块焊趾裂纹进行实际检测,结果表明,5P(9×16)×2的爬波探头对Φ50.8 mm×8.5 mm锅炉管滑块焊趾裂纹的检测识别效果好,检出率高。该爬波检测技术简便、灵活、适用于现场工况复杂的检测环境,裂纹反射波易识别,消除了滑块焊趾裂纹的不可探区域。
[关 键 词]爬波检测;过热器;再热器;滑块;裂纹;反射波
电站锅炉的过热器和再热器管屏采用双面滑块式结构固定,每个滑块均焊接在管子上,相邻两滑块间以卯榫结构固定,防止管子出列错位。由于滑块和管子采用焊接连接,焊缝长期处于受力复杂的炉内高温烟气环境,在滑块焊趾处易出现横向裂纹,因此在锅炉检修期间需加强对焊趾部位的裂纹检测。实际检修中针对管子排列紧密、滑块焊趾的检测空间受限的问题,检修人员通常只对管子外表面进行外观检测[1-2]。为解决上述检测难题,本文开展了锅炉管滑块焊趾裂纹的爬波检测研究。
1 滑块焊趾裂纹案例
国内某电厂锅炉过热器、再热器管排由滑块卯榫连接固定,分隔屏过热器管材为T22,Φ51 mm×8.5 mm;高温再热器管材为TP304,Φ57.15 mm×3.81 mm;滑块材料为310S奥氏体不锈钢。累计运行6万h后,分隔屏过热器和高温再热器滑块区域发生多次泄漏,滑块焊趾处泄漏形貌如图1所示。图1中焊趾为焊缝表面与母材连接部位,原始漏点均位于滑块焊缝焊趾处。
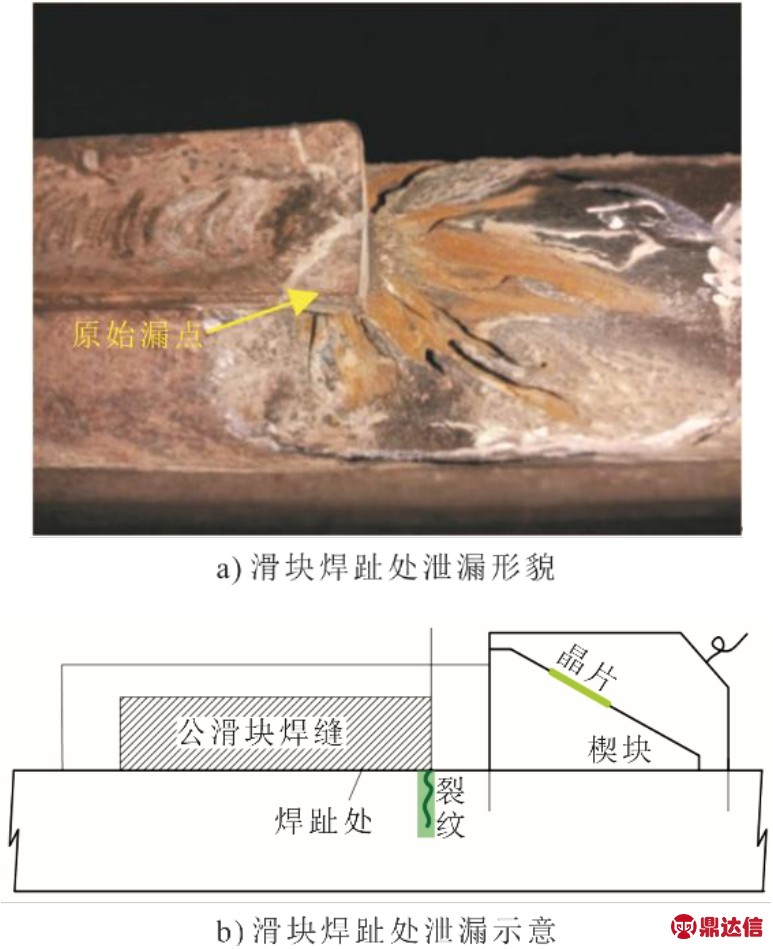
图1 滑块焊趾处泄漏形貌及示意
Fig.1 The leakage morphology and schematic diagram of the welding toe of pipe slide block
图2为滑块与母材连接方式。由图2可见,滑块分为公滑块和母滑块,分别焊接在相邻的管子上,通过卯榫连接方式在径向固定两管。
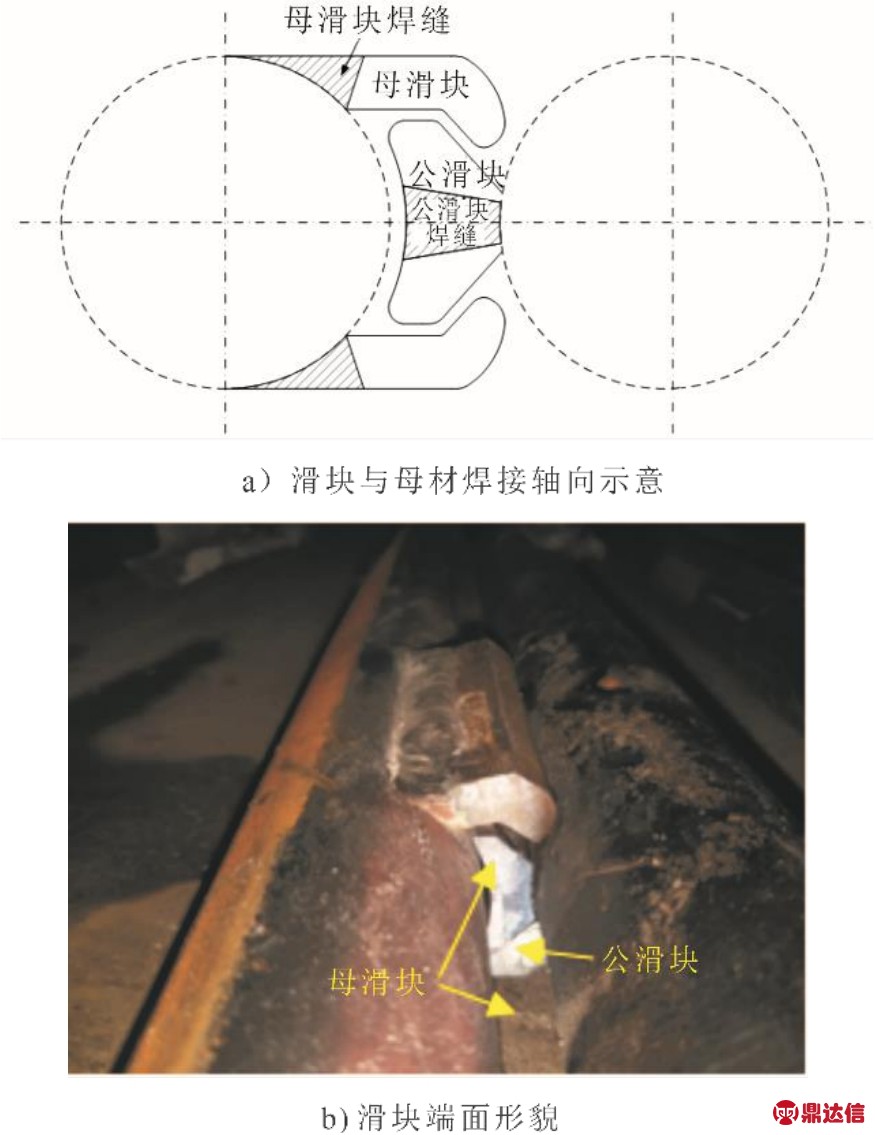
图2 滑块与母材连接方式
Fig.2 Connection mode between the slider and the base material
对滑块泄漏处检测时发现漏点为裂纹,位于滑块焊趾处。图3为高温再热器滑块泄漏处裂纹解剖形貌。由图3可见,裂纹根部较宽,端部较为尖锐,裂纹萌生部位靠近滑块侧,呈树枝状延伸。
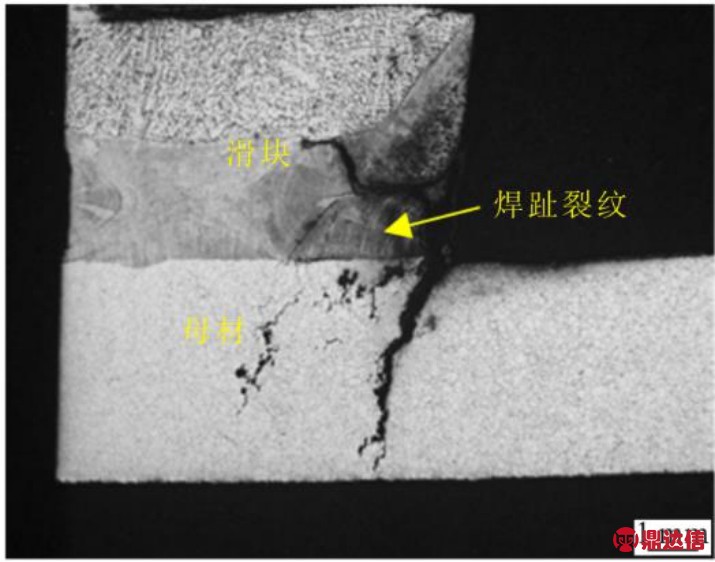
图3 高温再热器滑块泄漏处裂纹解剖50倍形貌
Fig.3 Morphology of the crack at the leakage point of the high temperature reheater slide block with 50 times magnification
1.1 原因分析
该锅炉分隔屏过热器、高温再热器的变形管子通过滑块卯榫连接对相邻管子施加拉应力,因此滑块焊趾处为应力集中点[3]。随着服役时间增长,管子变形加剧,滑块端部所受拉应力增大。在机组启停和负荷变化造成的交变应力作用下,部分母材与母滑块沿焊缝熔合线开裂并逐步扩展,最终导致脱焊。失去母滑块固定的管子在管排中相对位置出现变化,这种位置变化产生新的拉应力,并通过未脱焊的滑块卯榫连接作用于相邻管子母材上。因此随着继续服役管子母材性能下降,未脱焊的滑块结构中公滑块焊趾处更易产生裂纹,裂纹逐渐扩展最终穿透管壁,发生泄漏。
裂纹多发生在累计运行时间达到6.3万h后,表1为运行时间与滑块焊趾泄漏统计。滑块焊缝端部在拉应力反复作用下,易产生疲劳裂纹[4-5]。
表1 运行时间与滑块焊趾处泄漏统计
Tab.1 Statistics of running time and base material leakage under weld end of the slider
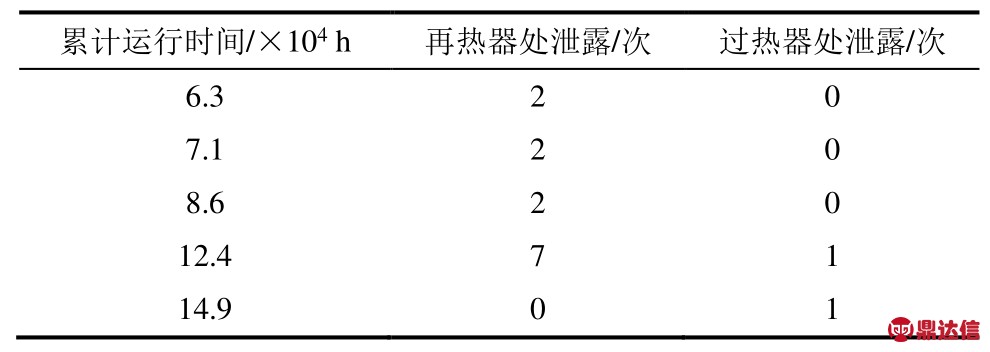
1.2 检测现状
由图1a)可知,泄漏部位裂纹呈垂直管轴向的横向分布,裂纹距离滑块端部约5 mm,位于公滑块焊缝焊趾处。原始漏点在裂纹横向扩展泄漏前,由于裂纹上方公滑块的遮挡,在检测时裂纹部位无法进行金属打磨,导致外观检测、渗透检测、磁粉检测均难以实施。
采用射线检测时,滑块结构和裂纹特征决定了只能采用椭圆成像方式,裂纹只能成像于椭圆的3点和9点位置,但是3点和9点位置缺陷检出率最低,加之滑块和滑块焊缝的存在,其两者射线影像与裂纹影像在底片上重叠,增大了裂纹影像的识别难度,因此,射线探伤也不适于该类缺陷的检测。
采用超声横波检测技术时,常规使用的小径管横波探头(5 MHz,6×6 K3探头)的直射横波无法覆盖裂纹,底面反射横波覆盖裂纹时,滑块焊缝产生的反射波会大大增加裂纹反射波的识别难度,易造成检测结果的误判或漏判[6]。
2 爬波检测
2.1 爬波检测介绍
爬波检测是超声纵波在第一介质中以第1临界角入射到第二介质中,在第二介质中产生超声波,当纵波以第1临界角α(25.0°~27.6°)入射到界面时,在被检钢制工件中会产生爬波和横波(图4),其中以近表面传播的爬波为主,角度为70°~80°,横波范围为30°~50°。文献[7]表明,爬波在钢制工件表面的垂直分量具有一定的渗透深度。
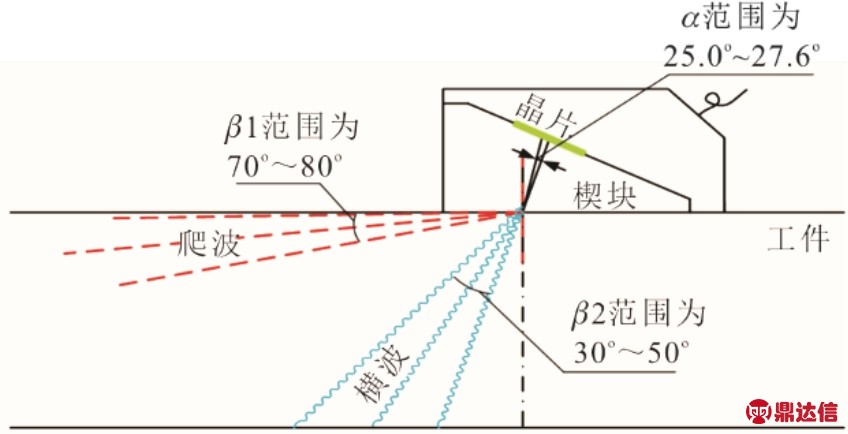
图4 爬波探头声场示意
Fig.4 Schematic diagram of sound field of the crawling wave probe
在纵波声速为5 900 m/s的45号钢船型试块上,将4 MHz、4 mm×4 mm双晶片并列爬波探头放置在图5所示位置,选用4PΦ14直探头作为接收器,将接收到的反射波信号调至屏幕高度的80%,记录仪器的增益值。
根据测试结果绘制爬波指向特性如图6所示。由图6可见,爬波探头的主声束能量主要集中在70°~80°之间,其最大幅值方向与表面呈一定角度,在选用双晶爬波探头时,最大幅值方向与表面的夹角约15°。
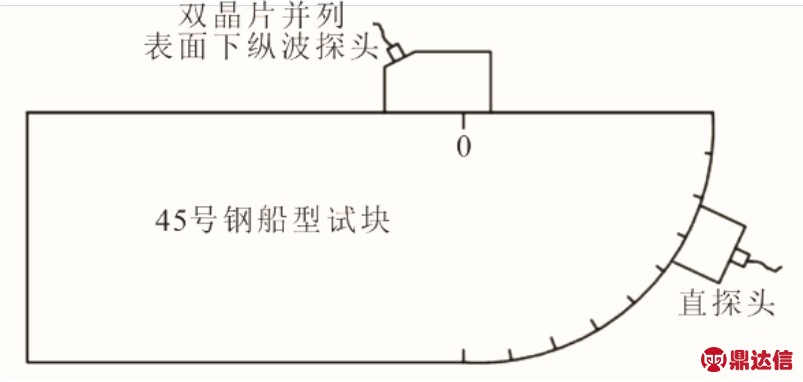
图5 爬波指向性测试
Fig.5 The subsurface longitudinal wave directivity test
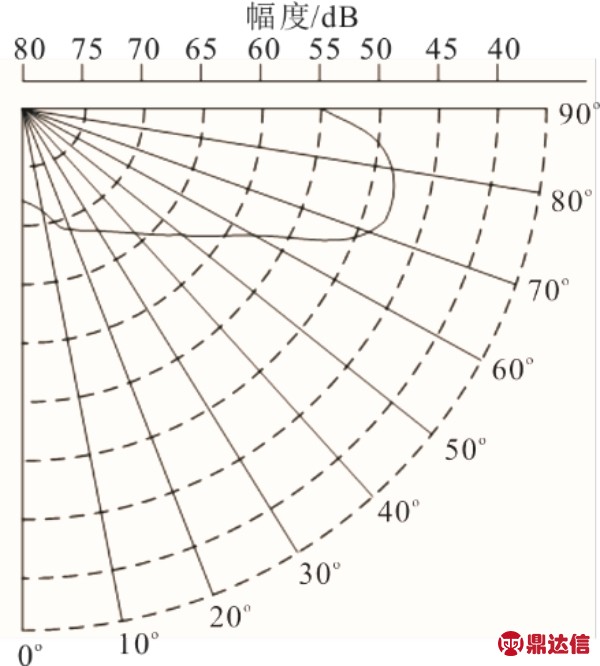
图6 爬波指向特性
Fig.6 The pointing characteristics of compressional wave under surface
2.2 爬波检测原理
双晶探头由内部2个单晶探头组成,一般由锆钛酸铅等激发声场性能较好的压电材料制备,一个用于发射信号,另一个用于接收信号。2个晶片之间由隔声层阻隔,减少了发射声波和反射波的互相干扰。2个晶片的理论声场交汇的棱形区为缺陷检出率最高的检测区。
双晶探头产生的爬波在表面下传播,受固体上表面状况(如粗糙度、油膜、附着层等)干扰较小,有利于检测表面下的缺陷。根据相关文献可知:改变爬波探头的频率和晶片大小乘积值,可以改变探头对表面下缺陷的敏感程度,通过双晶片一发一收的探头模式可以提高探头的灵敏度[8-9]。
爬波探头的主声束能量主要集中在70°~80°之间,在传播过程中,不受管子表面状况干扰,适用于检测滑块焊趾裂纹。图7为爬波超声检测滑块下裂纹示意。由图7可见,若滑块下存在裂纹,当探头端面与滑块贴合,探头无需前后移动即可探测出滑块下裂纹反射波。若滑块不存在裂纹,则在仪器屏幕上无缺陷反射波出现。在爬波检测滑块裂纹时,唯一出现的反射波只有裂纹反射波,这样裂纹反射波易识别,并且现场检测效率高。
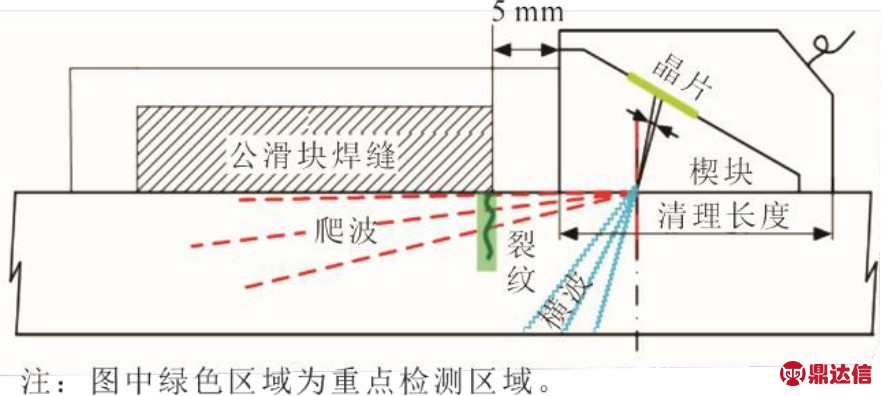
图7 爬波超声检测滑块下裂纹示意
Fig.7 Schematic diagram of the slide-block under surface p-wave ultrasonic detection
2.3 检测前准备
重点检测区域是公滑块焊趾处母材,图7中绿色区域为裂纹易出现区域,检测前用钢丝刷对滑块端部进行打磨清理,打磨清理轴向长度为50 mm,周向宽度为滑块侧管子的1/3周长。清理后,确保探头接触母材处不存在飞溅、铁屑、油漆及其他杂质,接触面平整,便于探头耦合,表面粗糙度应不大于6.3 μm。利用游标卡尺测量管子外径,取测量3次平均值,再根据管子外径选取适配爬波探头。
2.4 检测工艺
检测设备调整 采用A型脉冲反射式超声检测仪双晶爬波检测模式。爬波探头结构如图8所示。
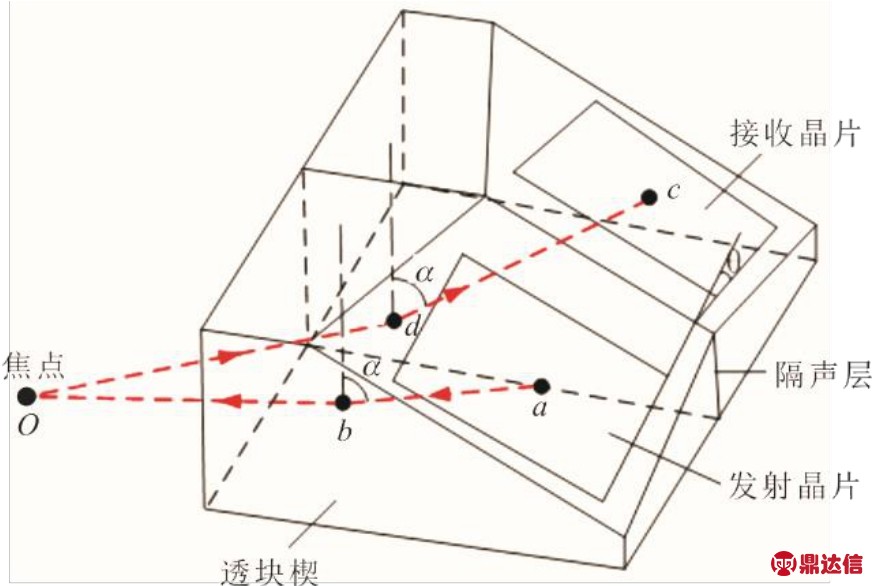
图8 爬波探头结构示意
Fig.8 Schematic diagram of the p-wave probe under the surface
图8中爬波探头内含发射晶片和接收晶片,晶片频率为5 MHz,晶片材料为PZT(锆钛酸铅压电陶瓷),晶片尺寸为9 mm×12 mm。发射晶片和接收晶片通过隔声层分开布置,其在楔块内入射角α范围为25.0°~ 27.6°,夹角θ为4°。检测声束路径为a→b→o→d→c(图8中红色线条为声束路径),若焦点O处无缺陷时,屏幕上无反射波出现,若焦点O处存在缺陷时,屏幕上会出现缺陷反射波。
灵敏度对比试块 爬波在钢制工件表面下有垂直分量,即爬波能量在钢制工件表面下具有一定渗透深度,故须在试块内壁加工一个周向矩形槽。该试块是从被检测管子上截取一段加工而成,截取后剖成两半,然后从外壁加工出矩形槽,槽自身高度1.0 mm,槽宽度0.2 mm,槽周向长度5.0 mm。
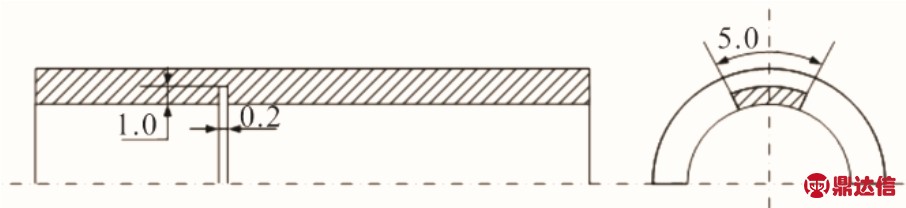
图9 灵敏度对比试块结构示意(mm)
Fig.9 Structural diagram of the sensitivity pair test block
水平线性调整 根据被测管径和壁厚,选用与试块弧面匹配的探头置于灵敏度对比试块上,找出距离外壁矩形槽5 mm时的反射波,将反射波调整至超声探伤仪器屏幕中间。
灵敏度调整 在水平线性调整后,在此参数下找出距离内壁矩形槽5 mm的反射波,再将矩形槽反射波调整至屏幕高度的80%,再增益3 dB,作为检测灵敏度。检测时内外波的差值不超过3 dB。
缺陷位置及定量 如图7所示,将探头贴合在滑块上,探头沿管子周向移动1/3周进行扫查。在设置的检测灵敏度下,同时满足2个条件则可以判定为裂纹:1)缺陷反射波幅值高于屏幕高度80%;2)缺陷反射波在管子周向长度大于5 mm。
3 现场检测
3.1 过热器滑块检测
现场检测采用5P(9×16)×2爬波探头对分隔屏过热器滑块进行裂纹检测。图10为分隔屏过热器滑块焊趾裂纹的反射波。取下分隔屏过热器裂纹滑块管段后,对图11中裂纹反射波位置的管子表面进行渗透检测,发现滑块焊缝焊趾处存在裂纹,裂纹距离滑块端面约5 mm。对图11中裂纹反射波位置管子内壁进行渗透检测,发现滑块焊缝焊趾处母材内壁存在裂纹显示痕迹,内壁裂纹长度为11 mm。
3.2 再热器滑块检测
图12为高温再热器管子滑块焊趾裂纹的反射波。取下高温再热器裂纹滑块管段后,将管段滑块去除后打磨,外观检查发现表面存在1处管子周向裂纹,长度为6 mm。
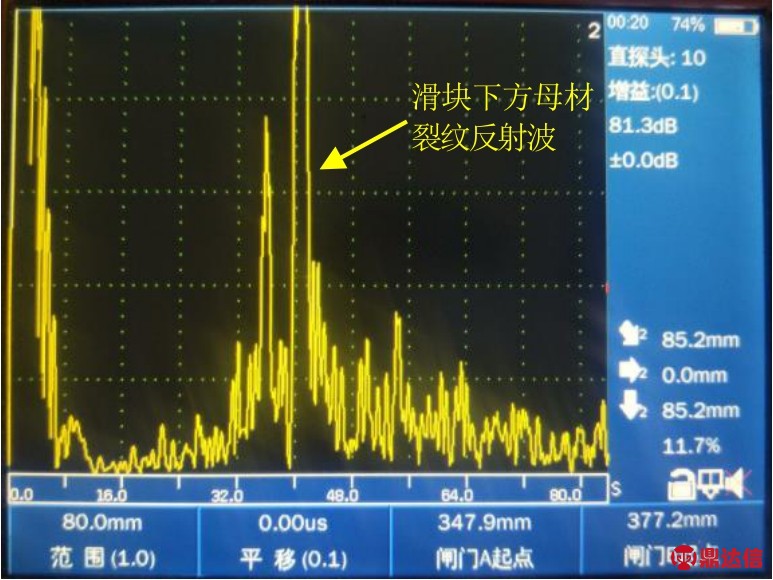
图10 分隔屏过热器滑块焊趾裂纹的反射波
Fig.10 The reflection wave of crack in welding toe under divider slider
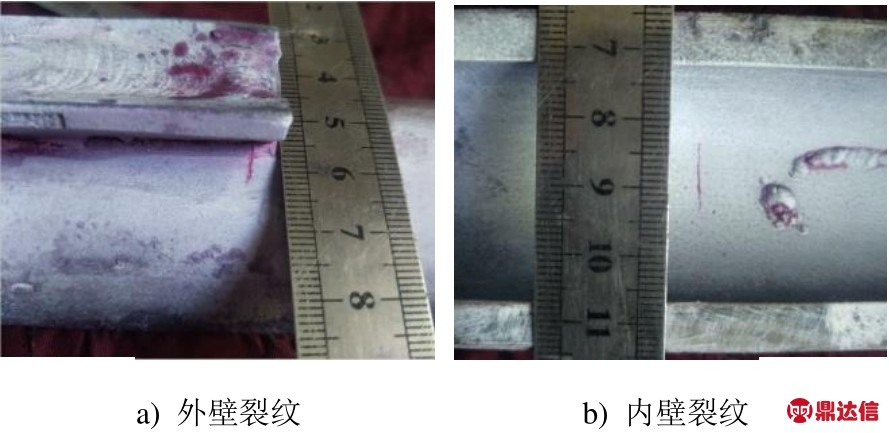
图11 分隔屏过热器滑块焊趾裂纹
Fig.11 The welding toe crack 1 on slide block of spacer superheater

图12 高温再热器滑块焊趾裂纹的反射波
Fig.12 The reflected wave of crack in welding toe under high temperature reheater slider
4 结 语
爬波检测可用于检测过热器和再热器管滑块焊趾裂纹,该方法简便、灵活、适用于现场工况复杂的检测环境,裂纹反射波易识别,检出率高,消除了滑块焊趾裂纹的不可探区域,有效减少了因过热器和再热器滑块焊趾裂纹扩展泄漏而引起的机组非计划停运次数和时间,提高了设备安全运行的可靠性,延长了设备的使用寿命。