摘要: 以某型号船用低速机为对象,基于多体动力学和混合润滑耦合建模,研究了十字头滑块和十字头轴承的摩擦动力学性能。利用MEBDF算法对高度非线性和刚性的摩擦动力学方程组进行了求解,得到了各个摩擦副在一个工作循环中的摩擦动力学性能,讨论了滑块供油孔尺寸和十字头轴承宽度对低速机摩擦动力学的影响。计算结果表明:十字头滑块承担发动机的侧推力,摩擦损失较大;十字头轴承在上止点和下止点附近摩擦功率较高;滑块供油孔的半径会影响其摩擦动力学特性;适当降低轴承宽度,能够降低十字头轴承摩擦损失。
关键词: 船用低速机;摩擦动力学模型;十字头滑块;十字头轴承;低摩擦设计
0 概述
在航运业中,20%的燃料能量被用来克服船舶摩擦,这导致了巨大的能源浪费[1]。船舶摩擦可以分为内摩擦和外摩擦[2]。内摩擦是指船内各种机器的关键摩擦副产生的摩擦,外摩擦则主要是指船体与海洋之间产生的摩擦。研究表明,船用柴油机关键摩擦副产生的摩擦是内摩擦的主要来源[2-4]。随着能源紧缺和环境污染问题[5-9]的日益严重,发动机制造商对船用柴油机低摩擦技术提出了更高的要求。
船用低速大功率十字头柴油机(简称船用低速机)标定转速在100 r/min以下,输出功率可高达数万千瓦,成本占到造船总成本的10%~15%[10-11],是船舶最重要的配套设备。因具有热效率高、稳定性好、可以燃烧劣质渣油等优点,船用低速机被广泛应用在商用船舶上作为推进动力设备。据统计,全球95%以上的远洋货轮选用低速机装船,市场需求量很大[12]。船用低速机中关键摩擦副的摩擦学问题对船舶运营的安全性、经济性和稳定性有重要影响。一旦关键摩擦副发生严重故障如拉缸、胶合等,会直接威胁海上人身财产安全;此外降低发动机的机械摩擦损失对提高燃油经济性及减少有害气体排放具有重要作用。对四冲程汽车发动机的类似研究表明,摩擦损失每降低10%,燃油经济性可提高约5%。另外,关键摩擦副如活塞-缸套、十字头滑块-导板和十字头轴承的动力学性能也对整机的振动、噪声有重要影响,需要重点关注[13-14]。
然而,目前国内外对船用低速机摩擦学的研究文献较少,耦合动力学和摩擦学的理论分析十分有限。综合来看,目前缺乏船用低速机的摩擦动力学性能预测模型和试验手段。这使得在船用低速机的设计制造阶段,缺乏一套完整的摩擦学设计工具,制约了其低摩擦长寿命性能的进一步发展。
文献[15-17]中做了十字头滑块摩擦学研究的早期工作,基于雷诺方程,建立了滑块摩擦学分析的简化求解模型,可以对滑块的最小油膜厚度、摩擦损失进行预测。然而,其研究中没有精确考虑船用发动机的动力学,也忽略了各个摩擦副的耦合作用。本研究中考虑了十字头滑块的二阶运动及活塞裙-缸套摩擦副和十字头滑块-导板摩擦副之间的耦合作用,建立了更精确的摩擦动力学模型来分析十字头滑块在标定条件下的性能[4,14]。研究结果表明,连杆惯性对十字头滑块的摩擦动力学性能有重要影响;适当的十字头滑块型线可以有效减小其摩擦损失。文献[18-19]中则针对十字头轴承,结合理论仿真和试验,对轴承摩擦性能展开了讨论。研究结果表明,增大十字头轴承的供油压力可以有效提高油膜厚度,适当的十字头轴承椭圆度可以提高其承载能力。目前来说,针对船用低速机中的活塞环-缸套摩擦副的研究文献相对较多,学者们主要探讨了织构、贫油、缸套变形等因素对活塞环的摩擦学特性的影响[20-23]。研究结果显示,在船用低速机顶环上加工合适的织构,可以有效降低磨损;贫油效应对活塞环的性能有显著影响。另外,近些年对主运动系中连杆大头轴承和主轴承的研究工作也取得了较大进展[24]。
本研究中首先基于达朗贝尔原理对船用低速机中活塞、活塞杆、十字头销和十字头滑块的动力学展开建模;然后利用平均流量模型和经典G-T微凸体接触模型对十字头滑块-导板摩擦副、活塞裙-缸套摩擦副和十字头轴承的摩擦学行为展开了精确描述,建立了船用低速机主运动系中关键摩擦副的摩擦学模型;而后,将动力学模型和摩擦学模型耦合,得到摩擦动力学模型。在高效数值求解算法的帮助下,可以对低速机各种工况下摩擦副的油膜厚度、摩擦力、微凸体接触力等参数进行有效预测,为船用低速机的摩擦学性能理论预测提供了工具。利用提出的船用低速机摩擦动力学模型,对典型摩擦副(十字头滑块、十字头轴承)的性能做了深入分析,首次讨论了十字头滑块供油孔尺寸和十字头轴承宽度的影响,为十字头轴承和十字头滑块的低摩擦设计打下了理论基础。
1 船用低速机摩擦动力学模型
船用低速机是典型的多体机械系统。图1(a)显示了船用低速柴油机的简图,图1(b)则展示了主要运动部件。如图1(b)所示,活塞杆的顶部通过螺栓与活塞刚性相连,底部也通过螺栓连接到十字头销,这使得活塞-活塞杆和十字头销构成一个整体。连杆将活塞的往复运动转换成曲轴的旋转,从而推动船舶前进。十字头滑块和十字头轴承是十字头组件的重要组成部分。十字头组件的详细信息如图1(c)所示。可以看出,十字头组件主要包括十字头销、十字头滑块和十字头轴承。十字头销通过旋转副连接到连杆,形成十字头轴承。同时,十字头销也通过旋转副与十字头滑块连接。十字头滑块和导板构成一个移动副。除了在纵向方向上的往复运动之外,十字头滑块还存在如图1(d)所示的摆动和横向移动,这称为二阶运动。可以通过十字头滑块的顶端和底端的横向位移(图1(d)中的et,eb)来描述。与之相似,活塞裙-缸套摩擦副也存在类似的情况:活塞不仅仅在纵向往复运动,还会在横向伴随着位移etp和偏摆ebp,称为活塞的二阶运动,如图1(d)所示。另外,活塞-活塞杆-十字头销在Y方向的位移用Yp表示;滑块的Y方向位移用Yc表示;连杆小头圆心的Y方向位移用Yr表示, 横向位移用er表示;滑块的偏转角度用γc表示,活塞偏转角为γp,连杆偏转角为θ。
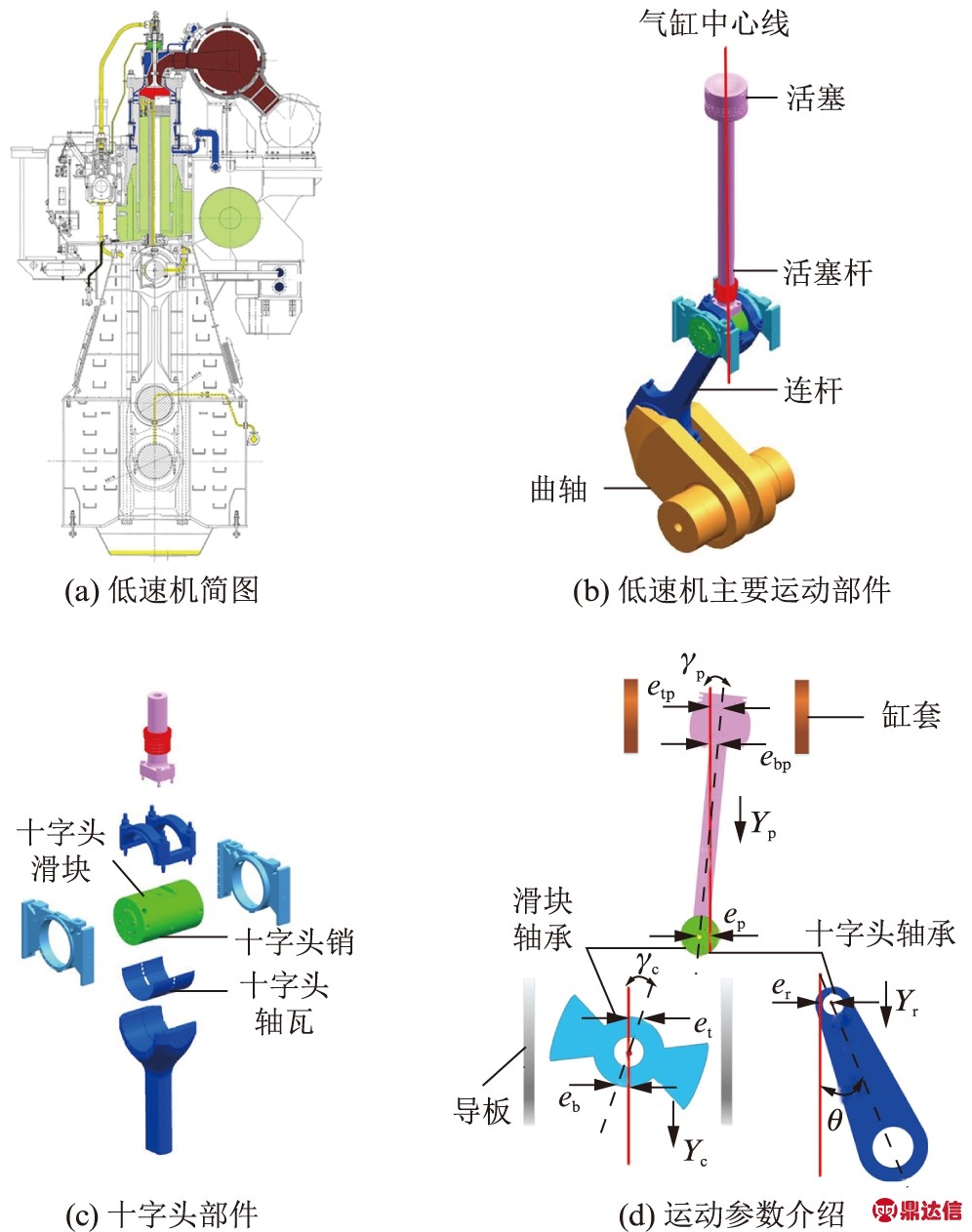
图1 船用低速机结构及摩擦副示意图
在之前的工作中,将十字头组件、活塞组件和连杆的动力学与十字头滑块-导板摩擦副和活塞裙-缸套摩擦副耦合在一起,建立了分析十字头滑块和活塞裙的摩擦动力学模型,并开发了高效的数值求解算法,可以对以上两个摩擦副的摩擦动力学模型进行快速准确的预测。在发动机标定工况下,对十字头滑块-导板和活塞裙-缸套的摩擦动力学进行了分析[4,14,25-26]。在本文中,十字头轴承的摩擦动力学特性也被进一步耦合。
1.1 动力学建模
低速机的主运动系结构[27]主要包括活塞组件、十字头组件、连杆和曲轴。主运动系中的关键摩擦副对低速机的运行安全性、经济性和稳定性有重要影响,值得深入研究。本节将建立包括活塞-缸套摩擦副、滑块-导板摩擦副、十字头轴承和滑块轴承的摩擦动力学模型。
图2给出了十字头销、十字头滑块和连杆的受力分析,活塞和活塞杆的受力分析可以参考文献[4,14,25-26]。图中,Fx2、Fy2、M2为十字头销顶部螺栓的X方向约束力、Y方向约束力和约束力矩;Gcp、Ficp1、Ficp2分别为十字头销的重力、竖直方向惯性力和横向惯性力;Fcbx、Fcby为十字头轴承的X方向和Y方向载荷;Fcgx、Fcgy为滑块轴承处的受力;Mcgf、Mcbf分别为滑块轴承摩擦力和十字头轴承摩擦力对十字头销心的摩擦力矩;Gc、Fic1、Fic2分别为十字头滑块重力、滑块竖直方向惯性力和横向惯性力;Fc、Fcf为作用在十字头滑块上的法向力和摩擦力;Mic为十字头滑块惯性力矩;L3为滑块长度;为滑块高度,如图2(b)所示;Ficrx、Ficry分别为连杆的横向和竖直方向的惯性力;Gcr为连杆重力;Fcsx、Fcsy为曲轴对连杆大头轴承的作用力;Micp和Mic分别为十字头销和十字头滑块的惯性力矩;r、s和t分别为连杆小头中心、连杆质心和连杆大头中心。
列出各个构件的动力学方程并进行数学整理后,最终可以得到包含各个摩擦副作用力的船用低速机动力学模型。相关建模细节可以参考文献[4,14,25-27],在此不做赘述。

图2 船用低速机构件受力图
在对每一个构件做了受力分析、力矩分析和运动学分析后,得到最终的摩擦动力学模型如下。
Fp+2Fcgx+Fcbx
(1)
2Fcgy+Fcby+mqg
(2)
Mcbf+2Mcgf
(3)

(4)
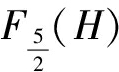
(5)

(6)
Fcbxlrtcosθ+Micr-Mcbf-
(7)
式中,ep为十字头销中心横向位移,如图1(d)所示;为十字头销中心横向加速度;Fg为作用在活塞上的缸压力;L1、L2分别为活塞质心到活塞裙上端和下端的距离;L为活塞杆长度;Rpin为十字头销半径;mp、mrod、mc、mcp和mcr分别为活塞、活塞杆、滑块、活塞销和连杆的质量;mq为活塞、活塞杆和十字头销的质量,mq=mp+mrod+mcp;g为重力加速度;lrt为连杆长度;lrs为连杆小头中心到连杆质心的距离;lst为连杆大头中心到连杆质心的距离;
和
分别为连杆转角、转动速度和转动加速度;Micr为连杆转动的惯性力矩;Ip、Irod、Icp分别为活塞、活塞杆和十字头销的转动惯量,Iq为三者之和;Ic为十字头滑块转动惯量;Mp和Mpf分别为Fp和Fpf关于活塞质心的转矩,要通过求解活塞裙-缸套的混合润滑模型确定;Mc和Mcf为Fc和Fcf关于滑块质心的转矩,要通过滑块-导板的混合润滑模型确定;Fcbx、Fcby和Mcbf要通过求解十字头轴承的混合润滑模型得到;Fcgx、Fcgy和Mcgf要通过求解滑块轴承的混合润滑模型得到。关于该模型更详细的解释参见文献[27]。
1.2 混合润滑建模
上述的动力学模型中,包括了活塞裙-缸套、十字头滑块-导板、滑块轴承和十字头轴承4个摩擦副的油膜作用力及微凸体作用力。滑块和活塞裙的相关计算方法可参考文献[4,14]。与文献中不同的是,本文中计入了滑块供油孔的影响,供油孔为圆形,圆心位于滑块中心。
对轴承的计算方法简述如下。考虑粗糙度影响的轴承的平均雷诺方程可以表达为[28-29]:
(8)
式中,x、y为轴承局部坐标系的周向和轴向;φx、φy为压力流量系数;φs为剪切流量因子;φc为接触因子;h为油膜厚度;为平均油膜压力;σ1为轴承表面和轴径表面的综合粗糙度;μ为润滑剂动力黏度;u1和u2为轴径表面和轴承表面的滑动速度;t为时间。φx、φy和φs的计算方法可以参考文献[28-29],φc的计算方法可以参考文献[30],计算公式如式(9)~式(13)所示。

(9)

(10)

(11)

(12)

(13)
式中,H=h/σ,其中σ为两个表面的综合粗糙度;γ 为X、Y方向相关长度的比值;E和r为γ的函数,如表1所示,在本文中γ取值为1;D1、β1、β2、β3、D2为γ的函数,如表2所示;c为十字头轴承半径间隙,c=Rb-Rpin,其中R1为十字头轴承轴瓦半径;β为连杆小头连体坐标系上的圆周方向角度,如图3所示;和
为连体坐标系(OXcYc)下十字头销中心相对连杆小头中心在Xc方向和Yc方向的位移。
表1 φx与φy的相关计算参数

表2 φs的相关计算参数
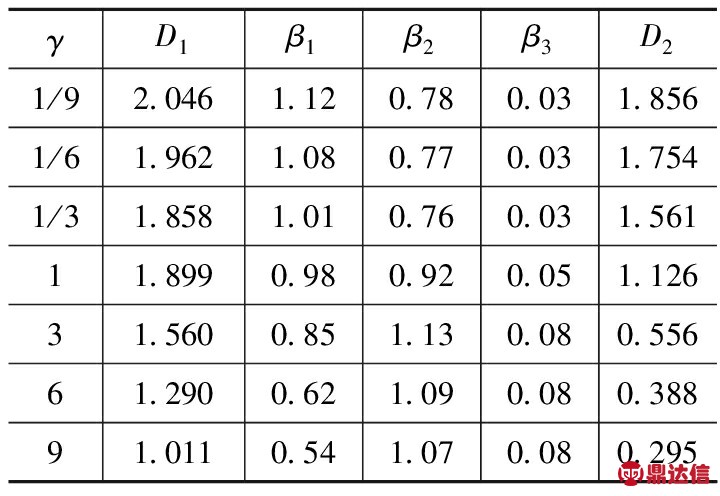
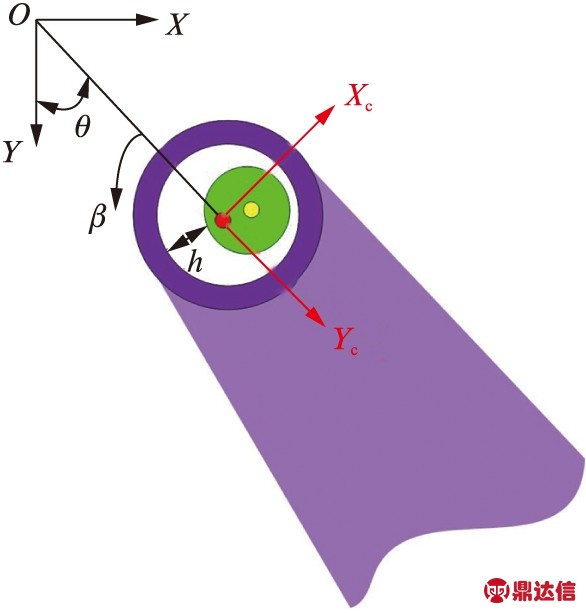
图3 十字头轴承油膜厚度
十字头轴承下瓦上布置有油槽,上瓦上则开有供活塞杆安装的槽,这些开槽会对轴承的摩擦动力学行为产生影响,需要详细考虑。轴瓦上开槽的详细情况如图4所示。图中φ1、φ2分别为安装活塞杆槽、周向供油槽的持续角度;W1、W2和W3分别为安装活塞杆槽的轴向长度、周向油槽的宽度和轴向油槽的宽度。

图4 十字头轴承轴瓦展开(开槽示意)图
轴瓦开槽的具体参数为φ1=φ2=60°,W1=142 mm,W2=24 mm,W3=2.4 mm。
平均雷诺方程是椭圆型方程,在数值求解过程中必须指定边界条件。雷诺边界条件在求解轴承问题中展现出了较好的精度且容易编程计算,故本文中将使用这种边界条件进行计算,具体公式可参见文献[31]。
微凸体作用力采用G-T模型计算,具体计算方法可简述如下[32-34]:

(14)
式中,pc为微凸体接触压力;η为微凸体密度;β′为微凸体平均尖端半径;E′为两个接触表面的平均弹性模量,其中E1和E2分别为两个接触表面的弹性模量;υ 1、υ 2为泊松比;
为高斯概率密度函数 可以写为式(15)[35]形式:

(15)
通过求解十字头轴承的油膜压力场和微凸体接触压力场后,可以进一步计算轴承载荷及十字头销摩擦力矩[29,36-37]:
Fcbx=∬A1[p(x,y)+pc(x,y)]sin(β+θ)dxdy
(16)
Fcby=∬A1[p(x,y)+pc(x,y)]cos(β+θ)dxdy
(17)
(18)
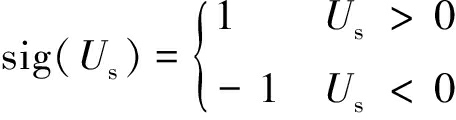
(19)
式中,μf为微凸体接触摩擦系数;A1为十字头轴承的润滑区域;为十字头销表面的粗糙度(Rq);Us为轴径表面相对轴承表面的滑动速度,Us=u1-u2;φf、φfs为文献[28]中定义的剪切应力系数。
在求解了滑块和活塞裙的混合润滑模型后,相应的力和力矩(Fc、Fcf、Mc、Mcf、Fp、Fpf、Mp、Mpf)可以被进一步确定(具体处理方法可以参见文献[4,14],在此不再赘述),而后便可以对各个摩擦副的摩擦动力学性能进行求解。
值得注意的是,本文中利用平均雷诺方程求解油膜压力场时,各个流量因子的计算是基于平面粗糙峰高度满足高斯分布的假设,非高斯分布下的求解可参见文献[38-41]。
2 数值求解策略
上文提出的摩擦动力学模型是高度非线性、刚性的常微分方程组,求解方法有龙格-库塔法、多步法等。近年来提出的MEBDF方法[42]在求解摩擦动力学问题上表现出了很好的求解精度和求解效率[43-44],本文中将采用MEBDF方法对模型进行求解。MEBDF求解的步骤可参见文献[4,14],在此不再赘述。
3 结果展示
对船用低速机的摩擦动力学模型进行求解后,十字头滑块、活塞裙、十字头轴承、滑块轴承的摩擦动力学特性都可以得到,本文中主要对十字头滑块和十字头轴承的计算结果进行展示。发动机的主要设计参数如下:Ic=9.6 kg·m2,Icp=4.12 kg·m2,Ip=1.319 kg·m2,Irod=86.63 kg·m2,Icr=245.57 kg·m2,L=2.074 m,L1=0.029 5 m,L2=0.029 5 m,L3=0.40 m,lrt=1.60 m,mc=141.0 kg,mcp=274.54 kg,mp=94.05 kg,mrod=193.79 kg,mcr=546.82 kg,b=0.30 m,R=0.17 m,Rc=0.80 m,Rpin=0.17 m,=0.65 m。其中,Icr为连杆转动惯量,b为十字头轴承宽度,R为活塞半径,Rc为曲柄半径。
各个摩擦副的计算参数如下:十字头轴承半径间隙C1=100 μm,滑块-十字头销轴承半径间隙C2=200 μm,十字头滑块-导板间隙C3=50 μm,活塞裙-缸套间隙C4=50 μm,十字头销和轴承衬表面综合粗糙度σ1=1 μm,十字头销和滑块孔表面综合粗糙度σ2=2 μm,十字头滑块和导板表面综合粗糙度σ3=2 μm,活塞裙和缸套表面综合粗糙度σ4=2 μm,微凸体接触摩擦系数μf=0.12,滑块-导板润滑剂动力学黏度μ=0.08 Pa·s。图5展示了发动机一个工作循环中气缸压力的变化情况。船用低速机配有专门的润滑油冷却系统,不断向十字头滑块和十字头轴承输送经过冷却的润滑油,因此本文中将十字头滑块和十字头轴承润滑剂的温度视为一个定值。润滑剂温度对摩擦学性能有一定影响[25],适当升高润滑剂温度会使得其黏度降低,有利于摩擦力的降低,但过高的温度会破坏油膜的承载力,导致微凸体接触,接触摩擦损失随之急剧上升。
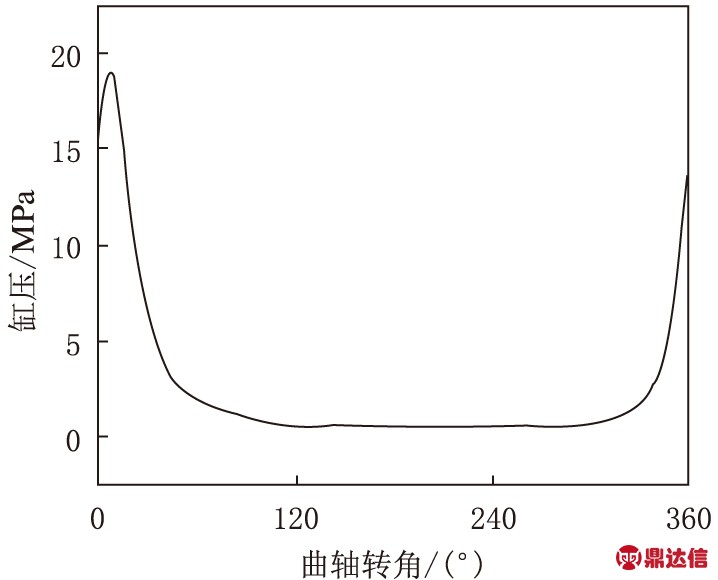
图5 发动机缸压图
3.1 十字头滑块计算结果
图6给出了船用低速机一个工作循环中十字头滑块的摩擦动力学特性计算结果。由总侧向力的变化情况可以看到,滑块承担巨大的发动机侧推力,在发火上止点后达到最大。在上行冲程中部,270°曲轴转角附近,由于惯性力的作用,滑块的侧向力也达到较大值。滑块巨大的侧向力结果证明了在船用发动机中发动机侧推力由十字头滑块承担。滑块的摩擦力由流体剪切力导致,仿真计算中没有发现滑块产生微凸体接触。在冲程中部,滑块速度较大时刻滑块摩擦力较大,这是因为流体剪切应力随着速度的上升而增大。由滑块的横向位移和速度曲线可以看到,在发火上止点后,滑块产生了较大的横向位移和速度。值得一提的是,在上行冲程末期,约300°曲轴转角处滑块也产生了较明显的二阶运动,通过载荷分析不难看出,这是因为此时滑块横向载荷发生了换向,产生横向运动,因此受到了较大的影响。
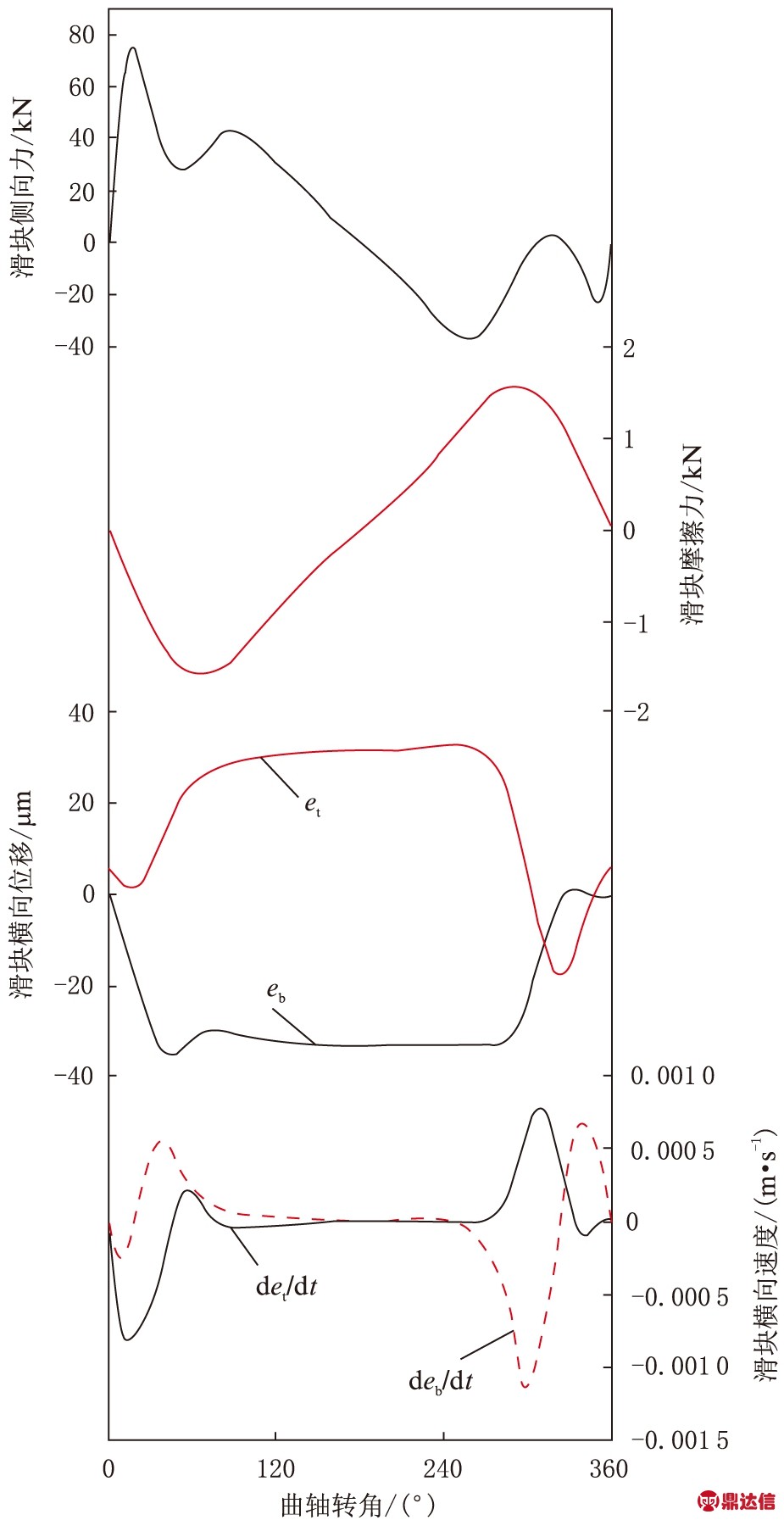
图6 十字头滑块摩擦动力学特性计算结果
3.2 十字头轴承计算结果
图7(a) 给出了十字头轴承在一个工作循环中的横向(X方向)和竖直方向(Y方向)的载荷情况。可以看到,竖直方向的载荷远大于横向。另外需要指出的是,十字头轴承X方向载荷在300°曲轴转角处换向,这将对轴承的动力学行为产生影响。图7(b)展示了十字头轴承一个循环中的流体摩擦转矩和摩擦功率的变化情况。可以看到,0°曲轴转角和180°曲轴转角附近流体摩擦力和摩擦损失较高,这主要是由于此时连杆摆动速度较大。图7(c)给出了十字头销心相对连杆小头中心的运动位移。由于本文中选择向下为Y方向的正方向,所以大部分时刻十字头销心位于轴承中心的下方。在上行冲程末期(300°~360°曲轴转角),由于连杆惯性的作用,轴承X方向载荷发生换向,十字头销相对连杆小头的运动发生了较大的变化。
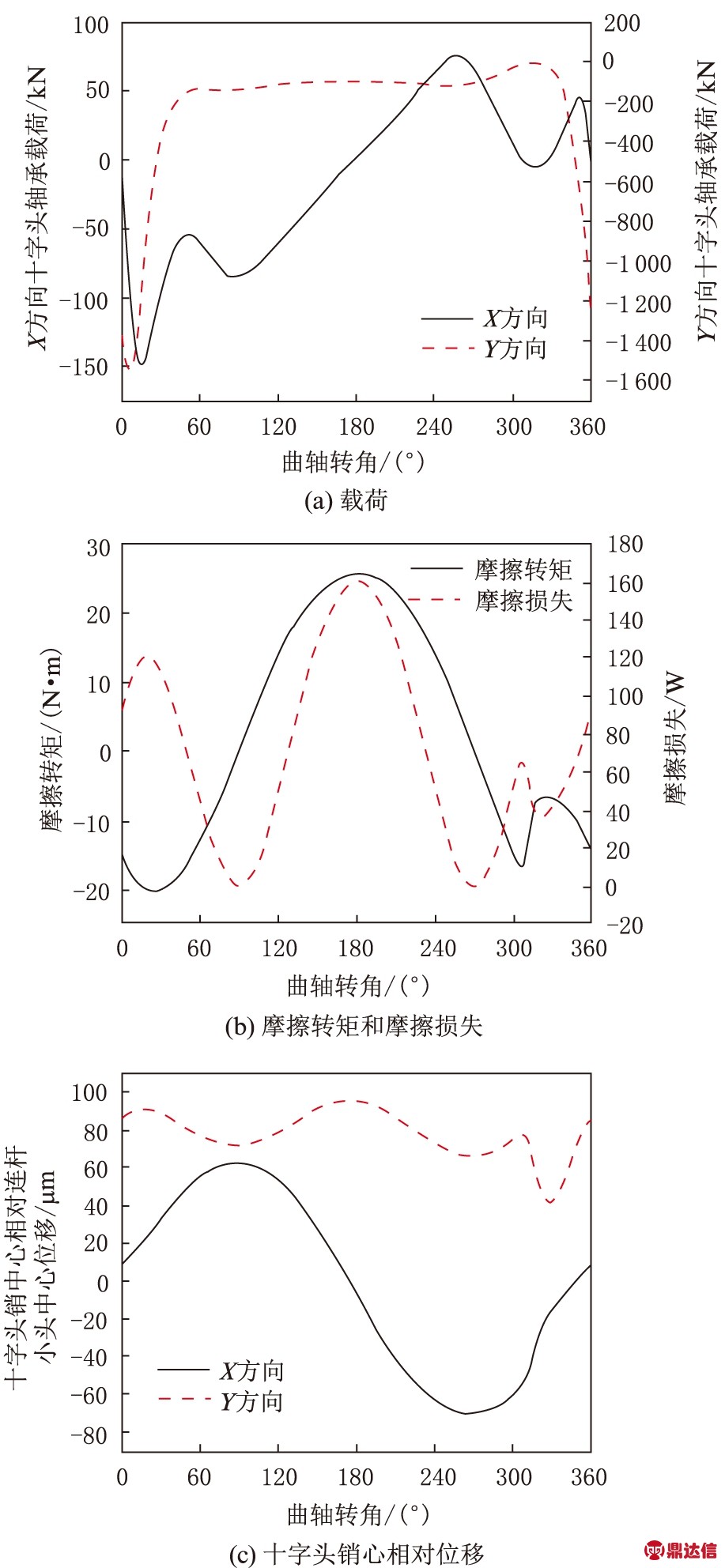
图7 十字头轴承摩擦动力学特性计算结果
图8展示了十字头轴承在30°和330°曲轴转角时刻的润滑油膜压力场。发火上止点后,在巨大的气体压力下,油膜压力场建立在轴承下方且数值很大,如图8(a)所示。然而,在330°曲轴转角附近,由于轴承载荷较小,油膜压力场较小,且主要分布在下方供油槽附近,如图8(b)所示。
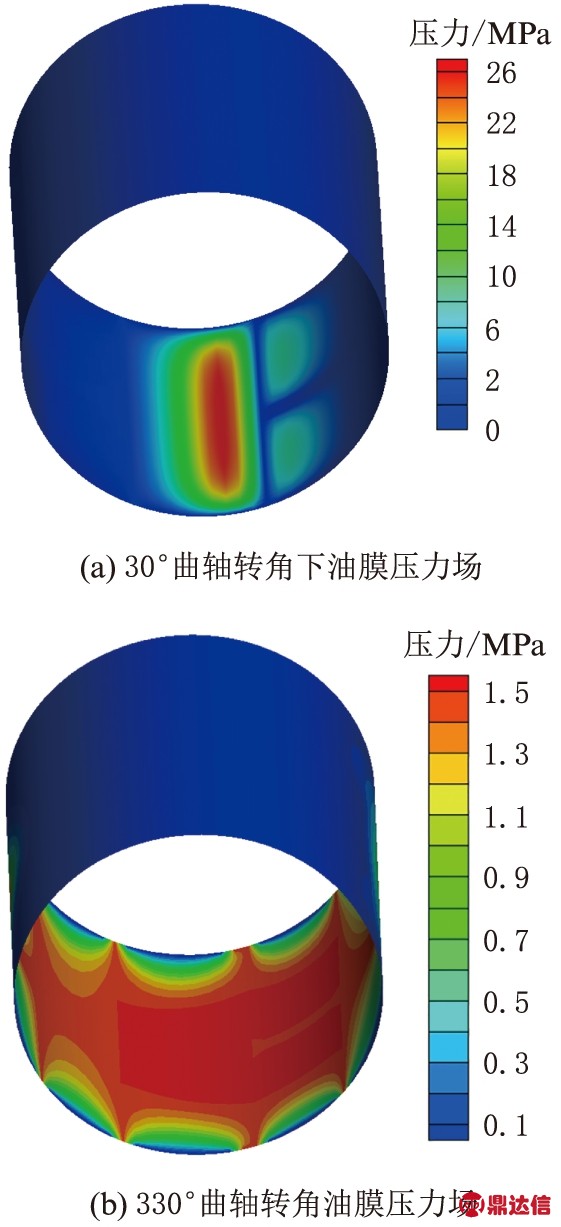
图8 十字头轴承润滑油膜压力场
4 十字头滑块及十字头轴承的优化设计
4.1 十字头滑块供油孔尺寸的影响
文献[14]中研究表明较大的滑块-导板间隙会使滑块的横向运动幅值增加,由于滑块-导板工作在流体动压润滑状态下,适当增大间隙可以起到较好的降低流体剪切力的效果,使得摩擦损失显著降低。在十字头滑块表面加工一种对称的二次型线,可以起到较好的降低摩擦损失的效果。此外,适当升高润滑剂的温度和将曲轴向主推力侧偏置,也是较理想的选择[26]。在上述研究中,没有考虑滑块供油孔的作用。本文中将重点关注滑块供油孔的半径对滑块摩擦动力学特性的影响。本研究中选用的船用低速机滑块供油孔的半径为5 mm,为了研究供油孔大小的影响,本文中设置了3 mm、5 mm、7 mm和9 mm这4种供油孔半径,油孔的供油压力为0.5 MPa。
图9展示了油孔半径对滑块二阶运动的影响。由图9可以看到,供油孔的大小对十字头滑块的动力学行为有一定的影响。随着供油孔直径的增大,滑块的横向位移幅值稍有增大。在300°曲轴转角附近滑块侧向力换向的时刻,随着滑块供油孔半径的增加,滑块的横向运动速度幅值有增大的趋势。较大的横向运动会加剧振动,不利于发动机的稳定运行,因而从动力学角度考虑,供油孔的尺寸不宜过大。
图10展示了滑块侧向力和摩擦力随着供油孔半径的变化情况。可以看到,侧向力受滑块油孔半径的影响很小,滑块侧向力主要由作用在活塞上的气体压力决定。随着油孔尺寸的增加,在发火上止点后滑块的摩擦力稍有增加。这表明,无论从动力学优化还是降低摩擦损失考虑,供油孔的尺寸都应该尽量小。
图11展示了30°曲轴转角时刻滑块供油孔尺寸对滑块油膜压力场的影响。可以看到,油膜的最大压力变化并不大,但是油膜压力分布情况有较大区别。较大的滑块油孔尺寸将油膜压力场分割成了明显的两块区域。
4.2 十字头轴承宽度的影响
据统计,十字头轴承是船用低速机中故障发生最多的轴承,因而在设计阶段要对其展开深入的理论研究,为性能优化提供潜在的解决方案。利用提出的低速机摩擦动力学模型,对轴承宽度的影响进行了讨论。
图12展示了不同轴承宽度下十字头轴承的轴承载荷和摩擦功耗情况。由于十字头轴承的载荷是由发动机缸压、活塞-活塞杆-十字头销的重力和惯性力决定的,因而轴承宽度不影响轴承载荷。但是,轴承宽度对轴承的平均面压无疑是有影响的。当轴承工作在流体动压状态时,减小轴承宽度会降低黏性阻力,适当的降低轴承宽度能够降低十字头轴承的摩擦转矩和摩擦损失,但是轴承宽度过小可能会导致油膜承载力不足,轴承发生微凸体接触,导致接触摩擦阻力急剧上升。
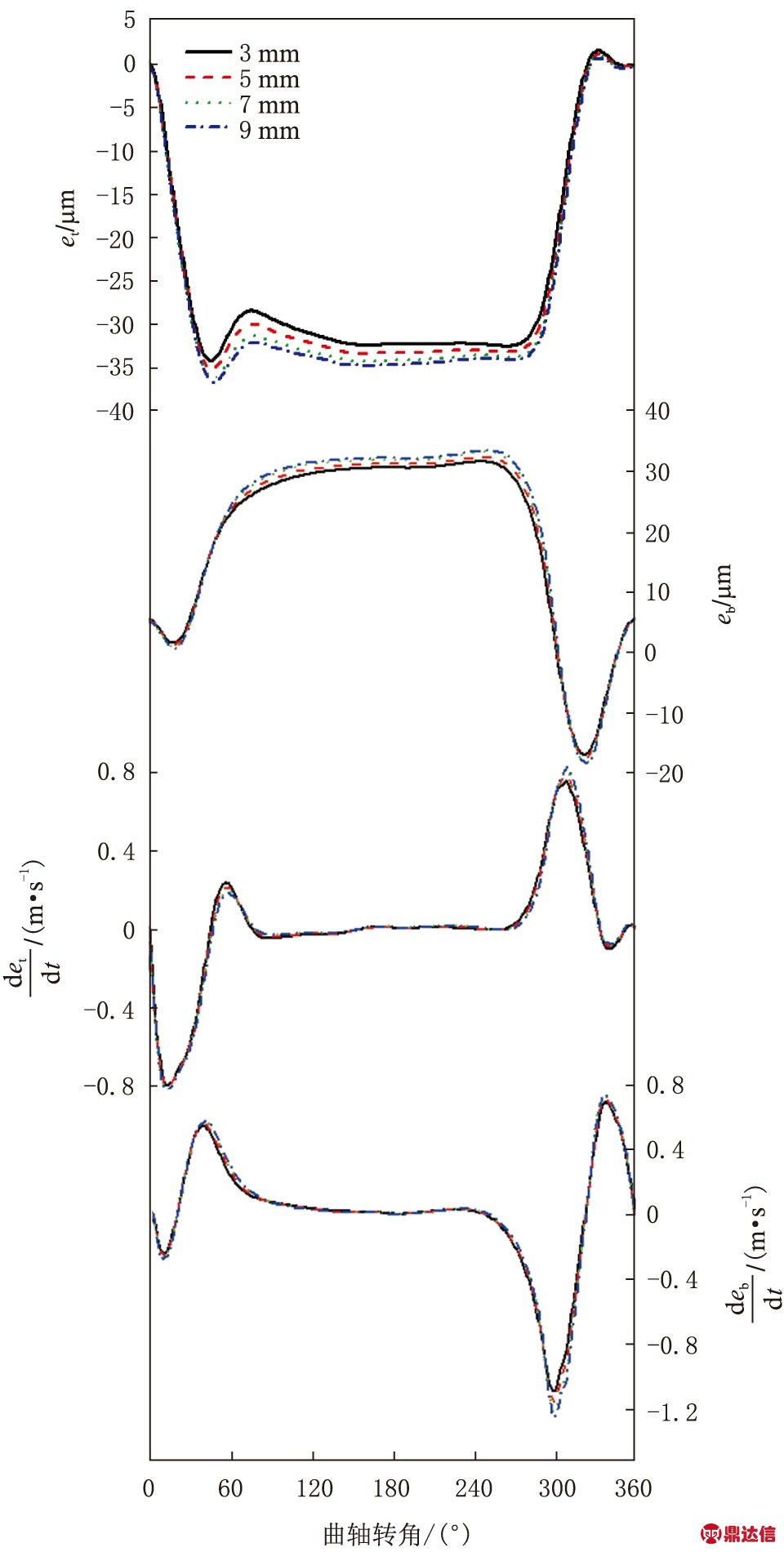
图9 不同油孔尺寸下滑块动力学性能
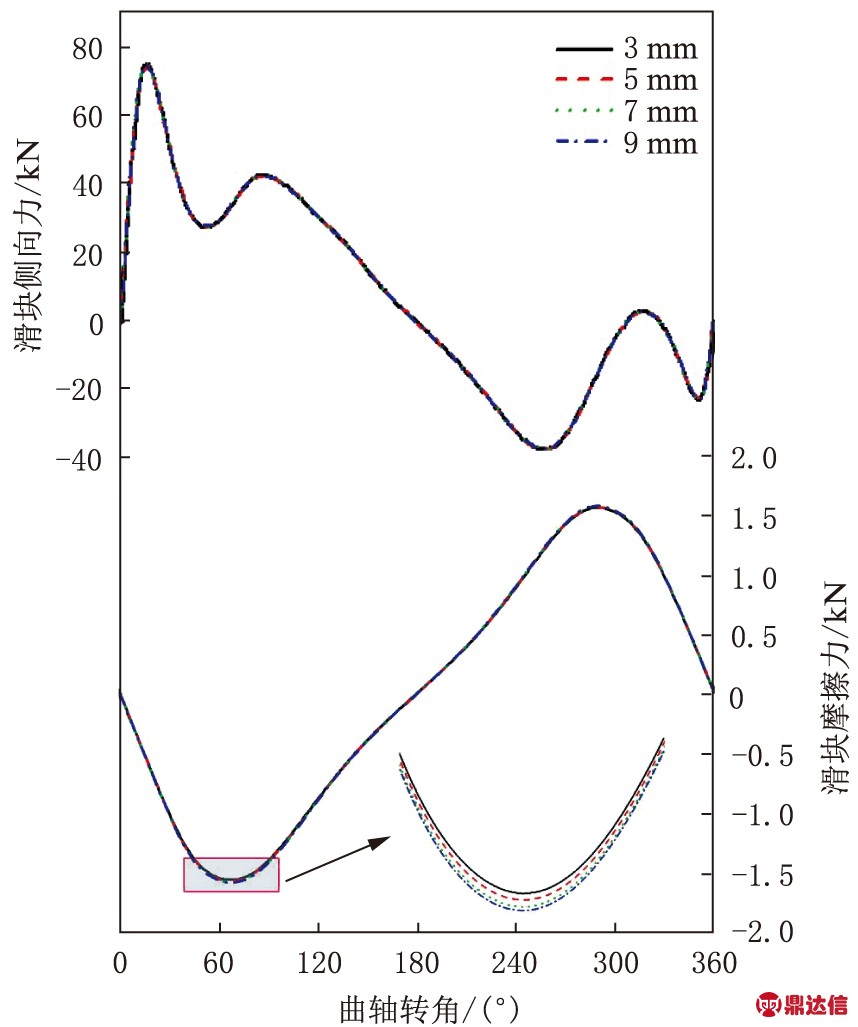
图10 不同油孔尺寸下滑块侧向力和摩擦力
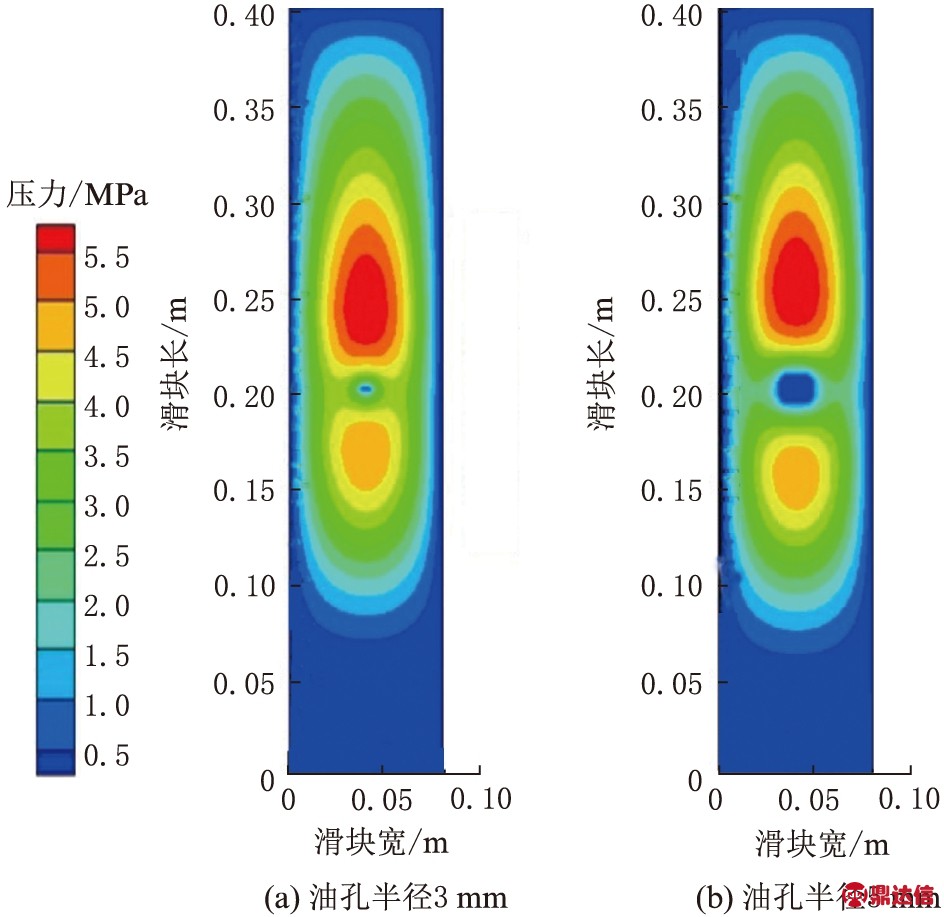
图11 不同油孔尺寸下滑块油膜压力场
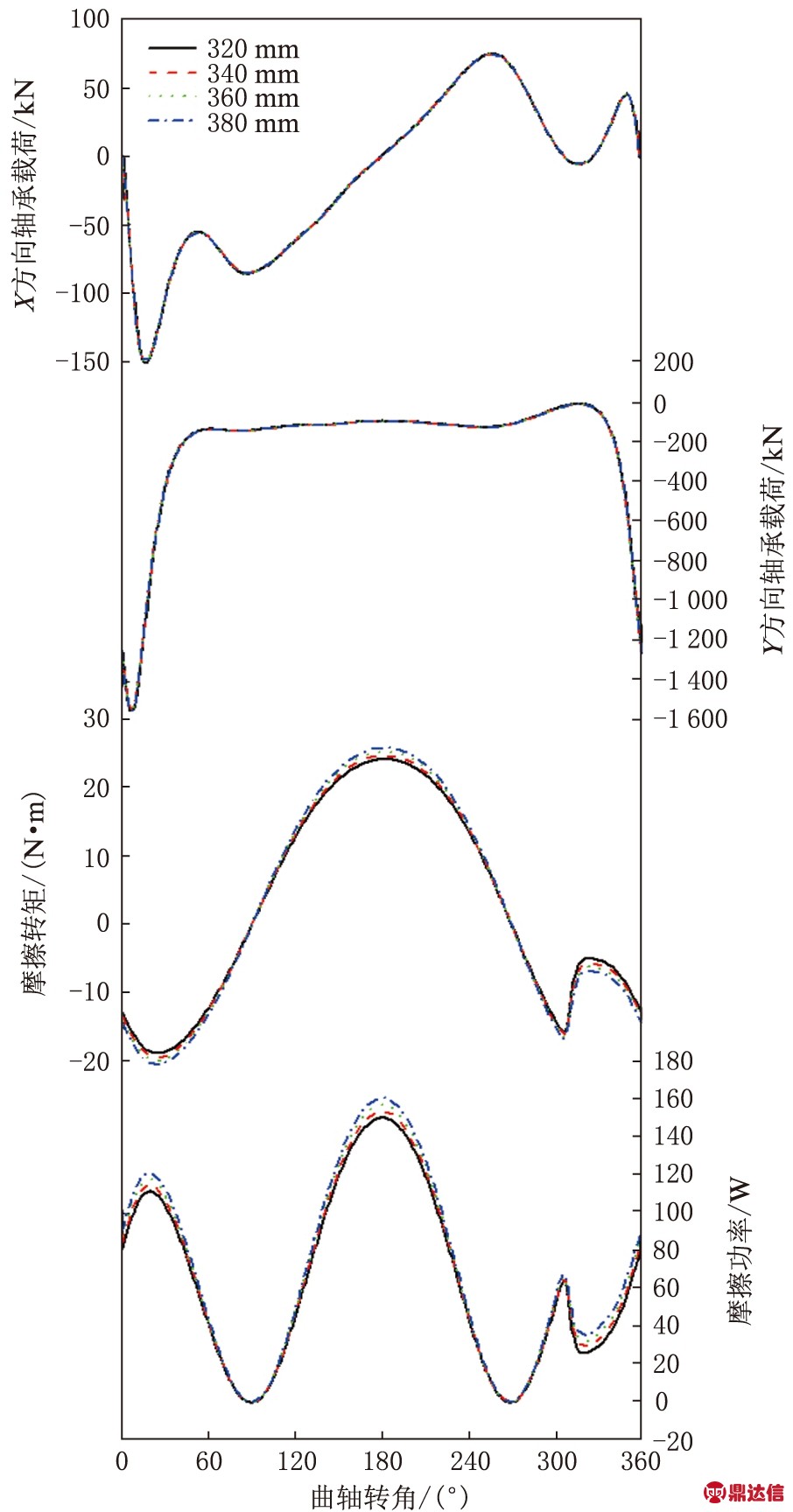
图12 不同宽度下十字头轴承载荷与摩擦功耗
图13展示了不同轴承宽度下十字头轴承的动力学特性。由图13可以看到,轴承宽度的影响主要出现在上行冲程末期。随着轴承宽度的降低,十字头销心相对连杆小头中心的运动趋势明显加强。
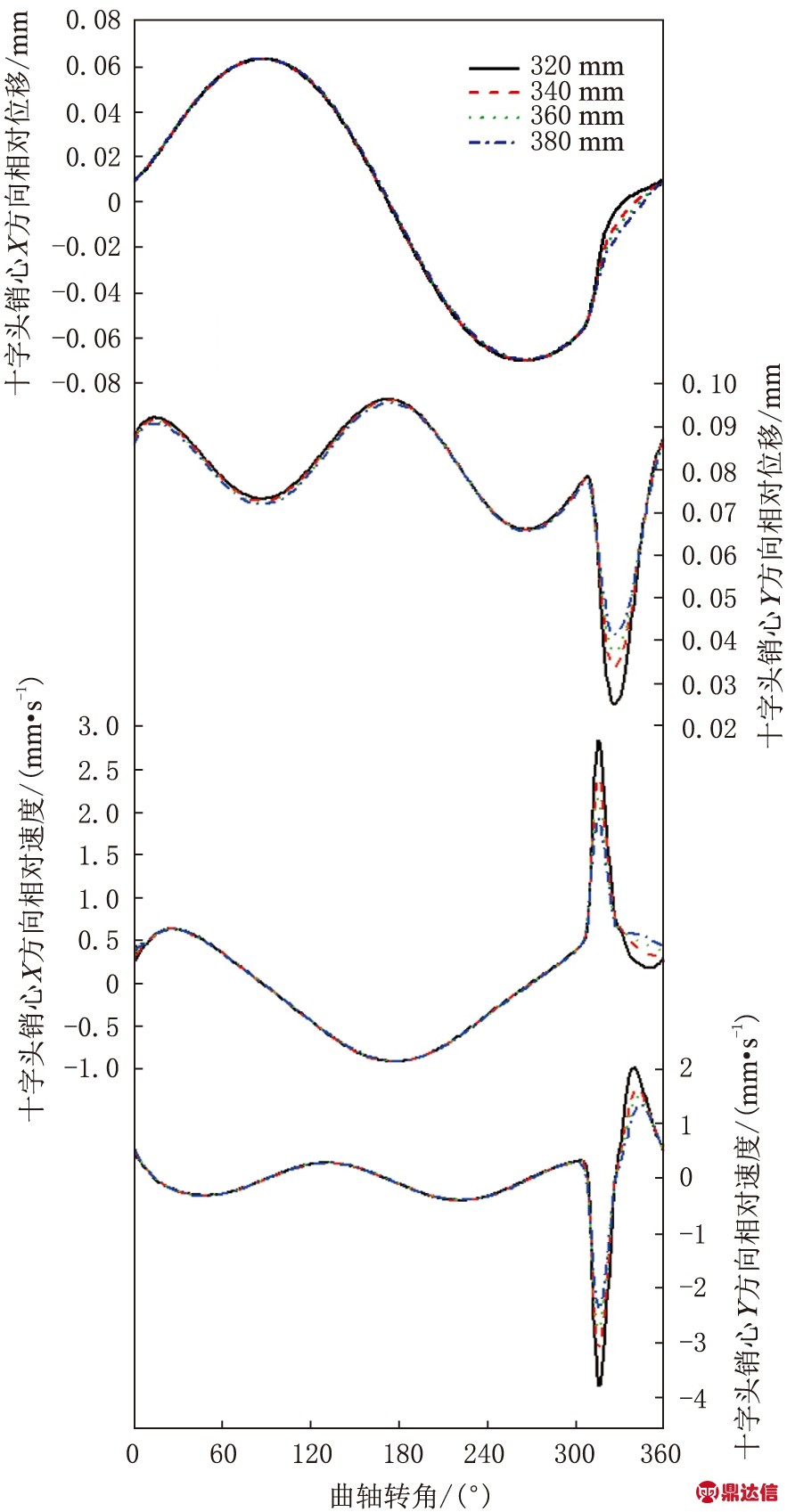
图13 不同宽度下十字头轴承动力学特性
5 结论
(1) 十字头滑块承担发动机巨大的侧推力,在滑块运动速度较大的时刻,滑块摩擦力较大。在上下止点附近,滑块横向运动剧烈。
(2) 由于十字头轴承载荷大,相对转动速度小,不容易形成良好的动压润滑。在发火上止点和下止点附近十字头轴承的摩擦损失较高。
(3) 滑块的供油孔设计对滑块的摩擦动力学特性有影响,适当降低油孔半径能够降低发火上止点后的摩擦力。
(4) 适当降低轴承宽度,能够减小十字头轴承的摩擦损失。随着轴承宽度的降低,上行冲程末期十字头销心相对连杆小头中心的运动有增强的趋势。