摘 要:针对微型离心泵泵叶塑件成型模具设计困难的问题,设计了一种改进型三板点浇口模以用于该泵叶塑件的成型。塑件的浇注成型应用3个点浇口来进行平衡注塑,以控制塑件成型变形。模腔布局为1模1腔。针对塑件叶槽区域脱模困难问题,设计了一种3层3次复合抽芯脱模用于难脱模叶槽部位特征的脱模,机构中,将叶槽部位特征的成型块分割成2层成型件后,机构的第一次抽芯动作由弹簧驱动上层滑块实施上层成型块的抽芯;机构的第二次抽芯由斜导柱驱动实施下层成型块的抽芯;最后,由弯销驱动基座滑块带动2个侧抽芯滑块向外抽芯,以让出塑件完全顶出脱模的运动空间。第二次抽芯、第三次抽芯的驱动动力分别由模架模板的第三次开模、第四次开模打开来进行驱动。塑件的最终脱模由油缸驱动顶针板及顶杆顶出而实现塑件的完全脱模。基于塑件、流道脱模及抽芯机构的动作需要,将典型三板点浇口模架改进为四板4次开模点浇口,从而能使塑件、流道废料及驱动滑块机构分次按序来实施抽芯脱模。模具脱模机构动作设置合理,机构结构设计巧妙,模具整体工作可靠,有较好的设计参考价值。
关 键 词:多层式抽芯;三板模;结构改进;机构设计;注塑模具
0 前言
一般的三叶螺旋塑件叶片的模具制造难点在于叶片的分型及成型件的加工。而对于更为复杂的塑件叶片,则需要在塑件的脱模和模具的整体结构简化方面做更多的设计研究[1-3]。叶片分型设计的难点在于叶片为曲面造型,为防止注射时产生漏胶及飞边等问题的出现,其分型面需要对叶片面进行延拓来设置,防止曲面间结合而产生段差,而导致成型件加工后合模时合不拢而产生较大的型腔闭合间隙;对于复杂一点的叶片,由于叶片的形状缘故,叶片的脱模方向形式较多,有些可能是旋转脱模,有些可能是分级抽芯脱模,还有的可能是多步联动式脱模,脱模的困难将导致模具的结构也跟着变得复杂,加工制造成本急剧升高;这些问题的解决,需要模具设计师从一定程度上做出结构创新设计来解决[4-7]。本文拟结合某离心泵泵叶的注射成型模具设计来对此作出案例设计参考。
1 离心泵塑件叶片
某微型离心泵为用于污水采样、大流量液体转移、低噪音连续工作场所的一种轻工用泵产品,其应用场合包括大型、特大型水族馆、小型游泳池、蓄水池补水、喷泉等。该泵的设计中,针对泵叶使用性
能要求为:①流量超大:135~145 L/min;②体积小;③有排气孔设计,真准确保超大流量;④直流潜水,噪音超小;⑤可抽含颗粒、杂质、油分等液体;也可抽黏度较大液体;⑥潜水泵直接放入水里。塑件注射成型中,针对叶片类塑件的模具设计是相对比较复杂和困难的。
针对这些要求,所设计的泵叶零件结构形状如图1所示。该泵叶应用工程改性塑料丙烯腈-丁二烯-苯乙烯共聚物(ABS),通过注塑的方式来进行成型。塑件的成型精度要求为MT5,产量总量为105件。泵叶为圆盘状,采用整体式构造,泵叶由6个叶片组成,叶片通过上槽边和下槽边组合在一起,叶片与叶片之间的空间为叶槽,叶槽为液
体的流入通道,泵叶外围为进液口,泵叶中央为用于安装驱动电机中心轴的轴套孔。

图1 泵叶塑件
Fig.1 Pump blade plastic parts
2 塑件模塑成型分析
2.1 模塑成型分析
泵叶塑件的注射成型设计,需要结合塑件的具体结构尺寸情况来决定塑件的成型模具方案[8-10]。如图2所示,塑件的最大外形轮廓尺寸为φ56 mm,总高度为17 mm,在生产精度要求为MT5等级要求下,为保证成型精度,模腔布局以1模1腔布局较为妥当。考虑到塑件为“三明治”形式的多层组合体,注塑时,料流在腔体内的流动情况比较复杂,冷却收缩后,容易引起区域间的变形不一致而导致最终的成型尺寸产生较大的尺寸“超差”,因而浇注设计时,考虑采用多点浇注较为合适,对于圆盘类塑件,多点浇注时,一般采用3点点浇口来进行平衡式浇注。塑件成型的最大难点是6个叶槽的脱模,导致叶槽脱模困难的尺寸如图2中A-A剖视图所示,叶槽的形状为从内到外的喇叭口形状,喇叭出口高度8 mm,跨度弦长26 mm,且为螺旋线旋出走势。叶槽的上端面,即上槽边为平面形式,而下槽边则为由外向内为下延伸槽形式,其下降锥度为15°,从外圆周到内圆周的径向长度为12 mm。
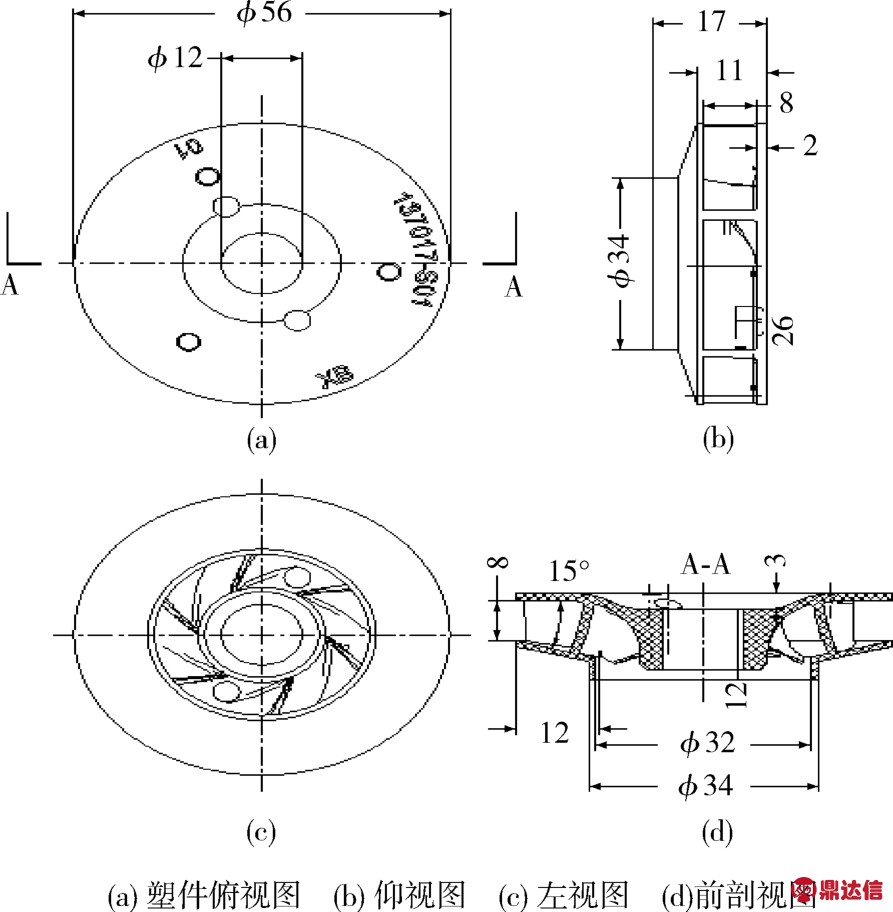
图2 脱模尺寸分析
Fig.2 Analysis of the demoulding dimension
从叶槽的结构形状分析可以得出以下脱模结论:①单个叶槽成型件的形状为内尖外宽,这有利于叶槽型芯的抽芯抽出;②叶槽喇叭口的高度为8 mm,型芯的强度可能不够,需要采用高强度合金钢材料;③下槽边按锥度15°下降成槽,形成内宽外窄的倒扣形状,不利于叶槽型芯的抽出,强制抽芯抽出会破坏塑件[10-13],因而该叶槽型芯只能设计成组合型芯,通过分步抽芯的方式来将型芯抽出,才能保证塑件的成型完整性,这也是本塑件成型模具结构及机构设计的重点和难点所在。
2.2 浇注系统设计
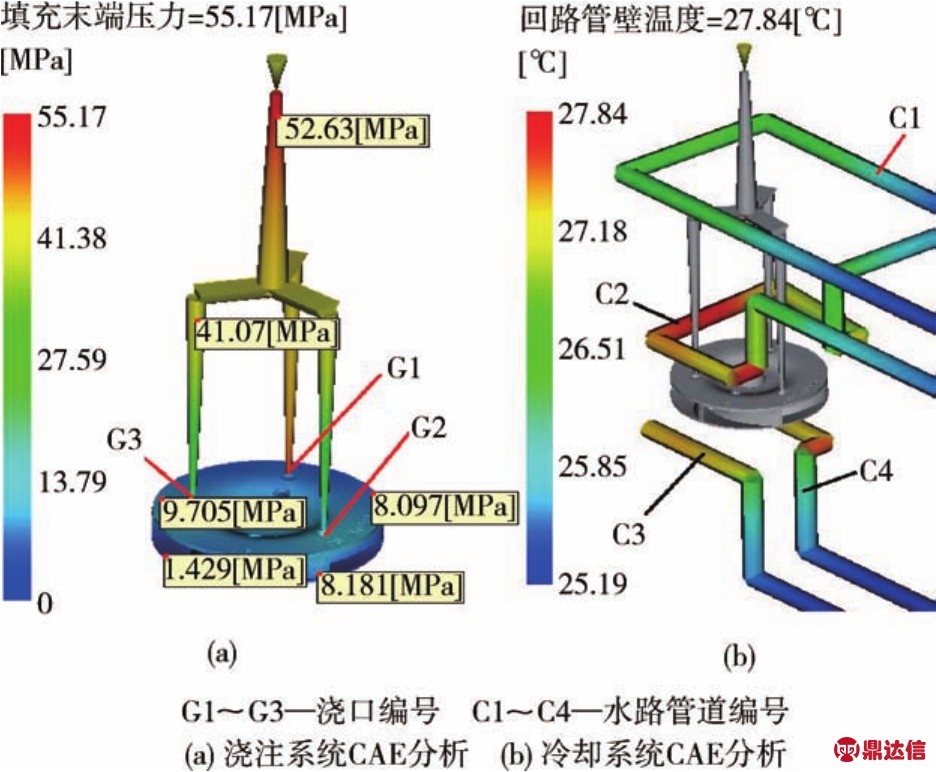
图3 模流分析
Fig.3 Analysis of the mold flow
如图3(a)所示,浇注开设3个点浇口进行均衡浇注,从浇注的末端充填压力结果可以看出,3个浇口在同圆上成120°布置进行浇注,能保证塑件的各充填末端达到均衡充填的目的,且查看其余计算机辅助工程(CAE)分析结果可以得知,翘曲变形为0.75 mm,收缩率0.65%,浇注系统能满足本次成形需要。
2.3 冷却系统
冷却系统设置4条管道来对模腔进行冷却,冷却管道包括4条,如图3(b)所示,4条管道直径为φ8 mm,冷却管对模腔进行冷却后,管道进出口的温度差在3℃以内,冷却有效。
3 模具设计
模具的整体设计为三板式点浇口模具,模腔布局为1模1腔。针对塑件的叶槽脱模困难问题[11-13],对应地设计了6个滑块机构S1~S6来完成6个叶槽的脱模,6个滑块机构的结构相同,但机构设计不同于普通的滑块机构,其结构设计有较大的难度。以下,是模具结构的具体设计组成,在综合塑件的浇注、脱模、排气、及冷却需要的基础上[14-16],所设计的模具结构如图4所示。
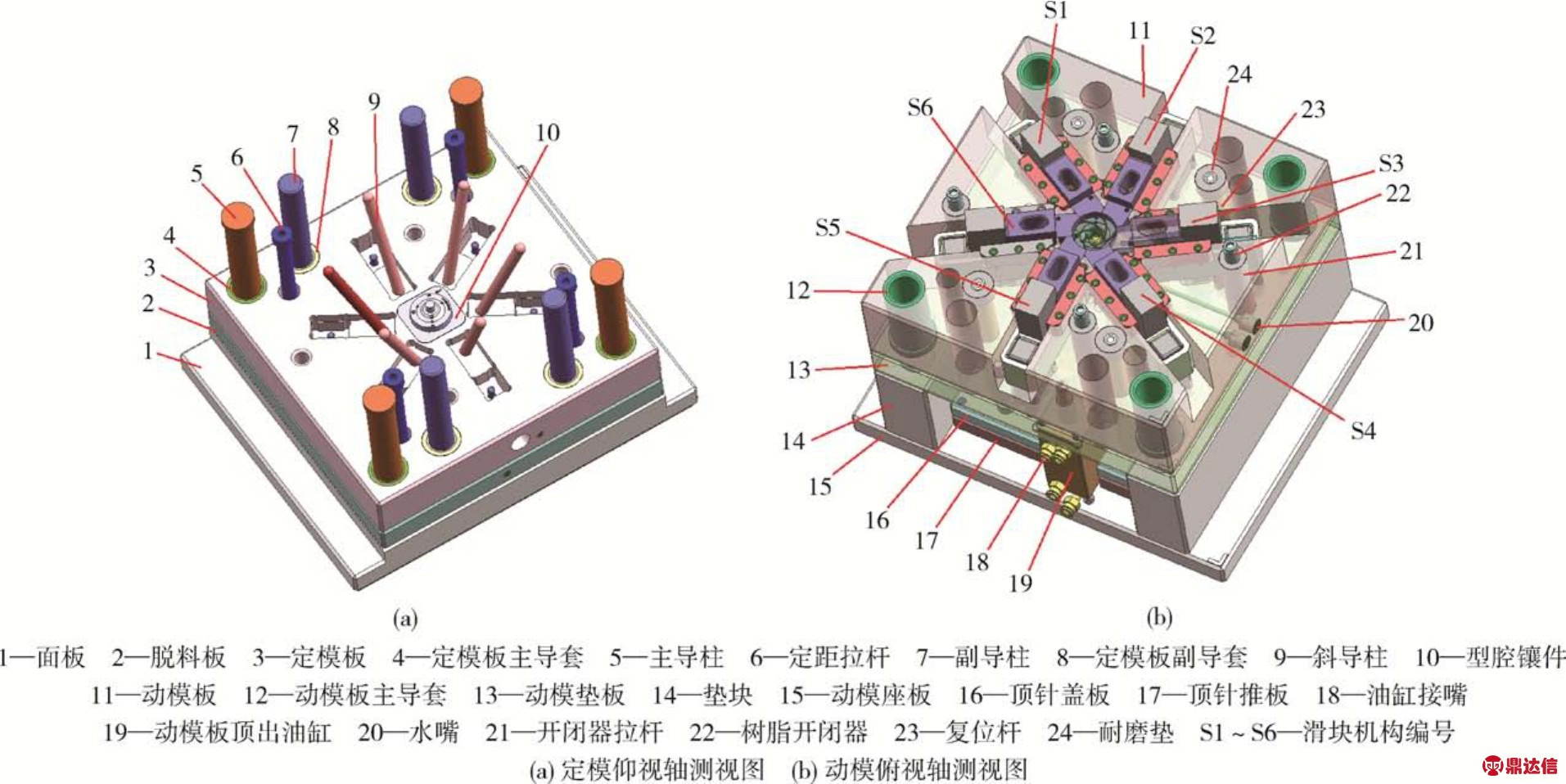
图4 模具结构
Fig.4 Mould structure
3.1 模架的改进设计
模架的选用结合了S1~S66个滑块机构的抽芯动作需要来选用,在通用型三板模架的基础上,增设了一块动模垫板13,从而能保证动模板11与动模垫板之间可以实施一次分型打开即P4开模面的打开,P4开模面的打开用于S1~S6滑块机构的弯销驱动其主体滑块实施侧抽芯动作,如图5(a)所示。模架的打开共分4次打开,按序依次为:P1→P2→P3→P4,其闭合书序则为:P1→P2→P4→P3。
模架采用2种结构的导柱来对运动模板进行运动导向,第一种为成型件安装模板的导柱机构,第二种为定模一侧的定模板3、脱料板2的运动导柱机构,该导柱机构也是4副导柱机构。
模架中,顶出机构主要由顶针盖板16、顶出推板17来实施,该顶出板需要设置由导柱45、导套46构成的4副导向机构来进行运动导向。顶针盖板16上,安装了4个复位杆23,且复位杆23的上端加装了4个耐磨垫24,耐磨垫24的作用有2个,其一是防止复位23的顶端被磨损而造成顶出的板16、板17不能完全复位,其二是在注塑机顶出拉杆在将板16、板17拉回复位时,能将动模板11也可靠地拉回复位,即P3开模面闭合前,将P4开模面先进行闭合。
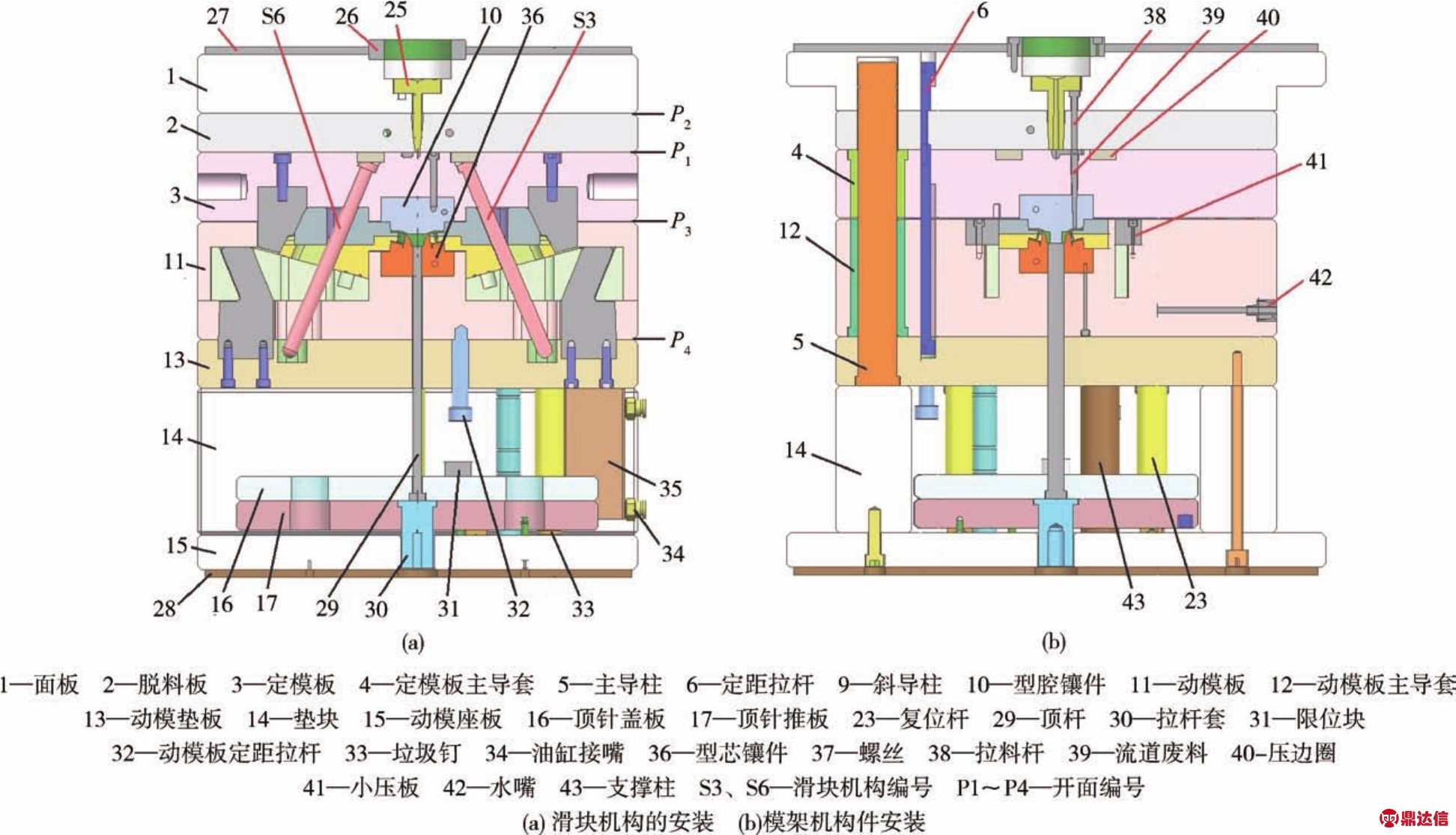
图5 模架机构件安装
Fig.5 Installation of the mold base mechanism
结合顶出板16、板17的顶出需要,设置了限位块31以调整此两板的顶出高度,设置了垃圾钉33以防止此两板复位时产生撞击变形。动模垫板13下方增设了8个支撑柱43以通过动模座板15来增强其强度,防止型芯镶件36在注塑压力下,产生向下凹的变形如图5(a)、图5(b)所示。
模架中,P4开模面打开由安装于动模垫板13下方的油缸35向上顶出而实施分型打开,其打开距离由动模板定距拉杆32进行限制,定模板3和动模板11打开的P3开模面的打开距离由拉杆6的下端螺杆的长度进行限制,脱料板2与面板1的打开距离则由拉杆6的上端螺杆长度进行限制,如图6(b)所示。
模架在P1、P2开模面打开时,定模板3、动模板11、动模垫板13的闭合则由安装于动模垫板13上的开闭器拉杆21通过其上的树脂开闭器22与定模板3的摩擦吸紧而实现,这样设置主要保证P4面的打开在P3面打开后才能打开,如图6(a)所示。
3.2 成型件
成型件由型腔镶件10、型芯镶件36及S1~S66个滑块机构的滑块头构成。如前所述,6个滑块头的尺寸由于塑件对应位置的高度仅为8 mm,为保证此滑块头的强度,滑块头的材料选用德国进口模具钢牌号为1.2344,型腔镶件10的材料则为1.2344HH,型芯镶件36的为1.344,如图5(a)所示。
3.3 S1~S6滑块机构
模具中,S1~S66个机构的结构组成相同,此6个机构在模具中的安装如图6(b)和图7(a)所示。以S6机构的结构为例,如图6(b)所示,机构由件47~件55构成,滑块48和滑块51的头部构成叶槽的成型件,其抽芯动作顺序是,先由滑块48抽出叶槽上层成型块,然后再由滑块51抽出叶槽下层成型块,最后由滑块50带着滑块48、滑块51一同抽芯抽出,为塑件从型芯镶件36上完全顶出而让出位置空间。其安装情况为:结合图7所示,滑块48通过T型槽配合安装于滑块51上,其抽芯方向为水平方向,其驱动力由弹簧55提供,其抽芯行程由滑块48上安装的限位玻珠52与滑块51上的2个限位窝配合来执行。滑块51为斜抽芯滑块,其下端通过T型槽配合安装与滑块50上,由斜导柱47进行驱动,其抽芯行程由安装于滑块50上的限位弹簧56进行限制,如图。滑块50为水平抽芯滑块,其通过压条53导向安装于动模板11的滑动槽内,其驱动由安装于动模垫板13上的弯销54进行驱动,抽芯行程则由P4开模面的打开距离来限定。
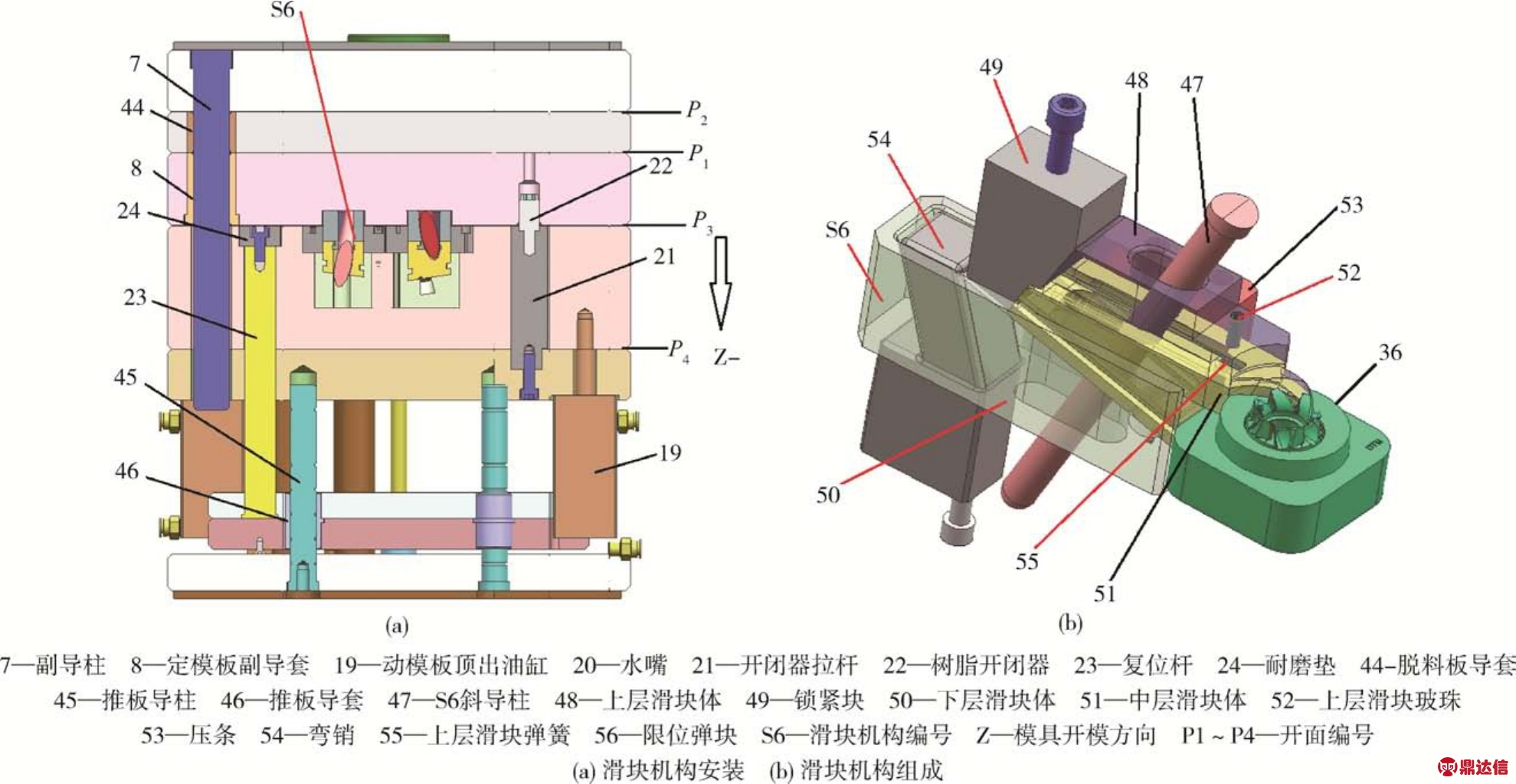
图6 模具结构
Fig.6 Mould structure
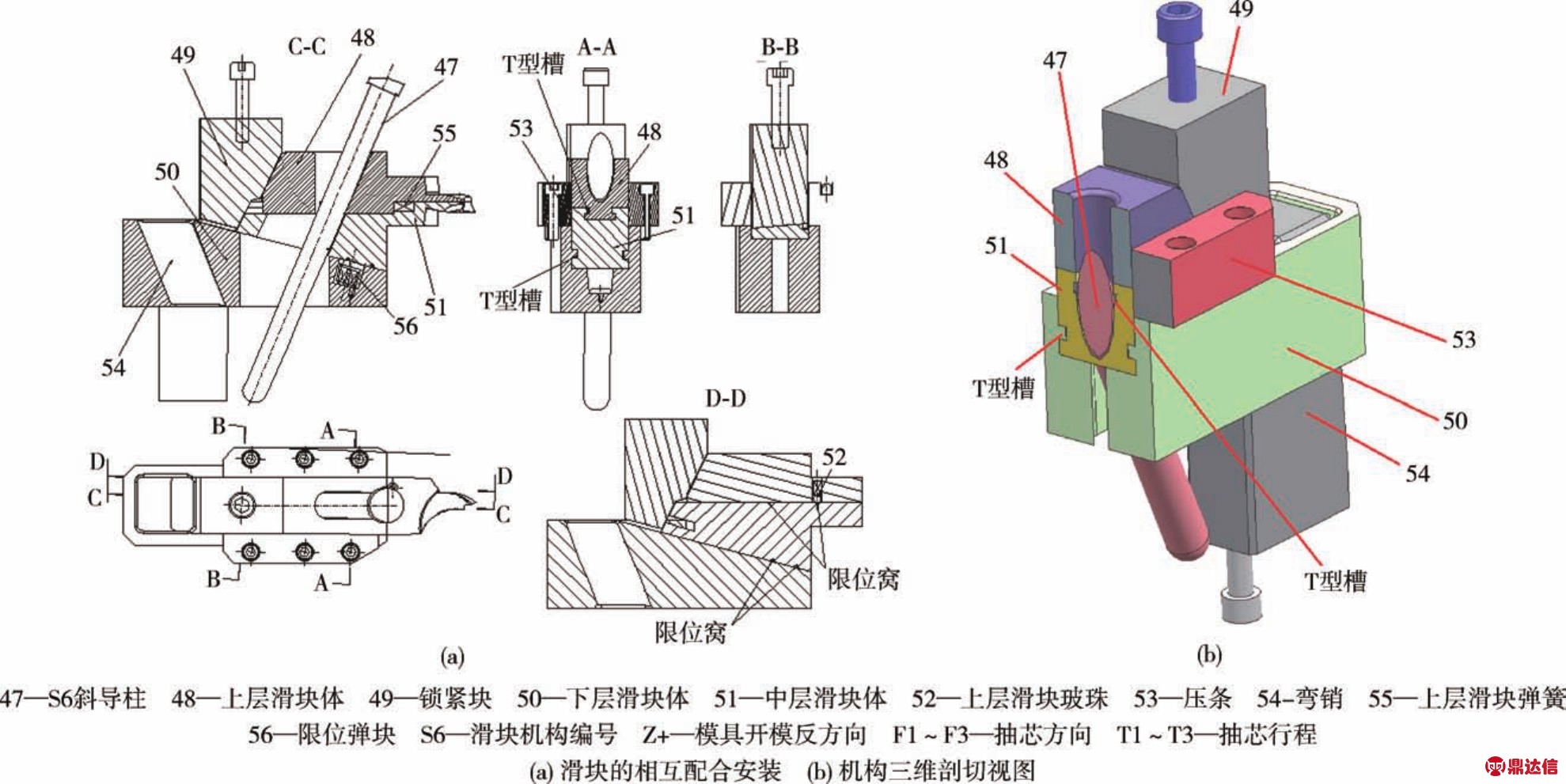
图7 滑块机构设计
Fig.7 Slider mechanism design
S6机构的工作原理为:如图8所示,模具在P3开模面处打开时,安装于定模板3上的锁紧块49、斜导柱47按Z+方向不移动,动模板11则带着机构上其余零件一下往Z⁃方向移动,此时,由于锁紧块49与滑块48、滑块51的后背锁紧面脱离,弹簧55将驱动滑块48做F1向的抽芯,其抽芯距离为T1,在此期间,斜导柱47不对滑块51实施驱动,直到T1行程抽芯完毕,此时,滑块48完成叶槽上层区域的抽芯脱模;而后,斜导柱47驱动马上驱动滑块51按F2向的斜向抽芯,其抽芯行程为T2距离,从而,滑块51完成叶槽下层区域的抽芯脱模,在此过程中,滑块48跟随滑块51一起运动。待滑块51抽芯完成后,油缸19、油缸35将动模板11顶起,P4开模面打开,从而,弯销54驱动滑块50座F3向的水平抽芯运动,为塑件的顶出让出空间。滑块50抽芯完毕,弯销54的弯头停留在滑块50的弯销槽内。复位时,其过程相反。
4 模具工作原理
结合图5~图8,如图9所示,模具的工作原理为:
①模具开模时,注塑机动模板驱动模具动模朝Z⁃方向运动,模具首先在P1开模面处打开,打开时,流道与塑件在点浇口处崩断。
②动模继续后退,模具在P2开模面处打开,流道板2将流道废料从拉料杆38上拔出而使其自动脱模。
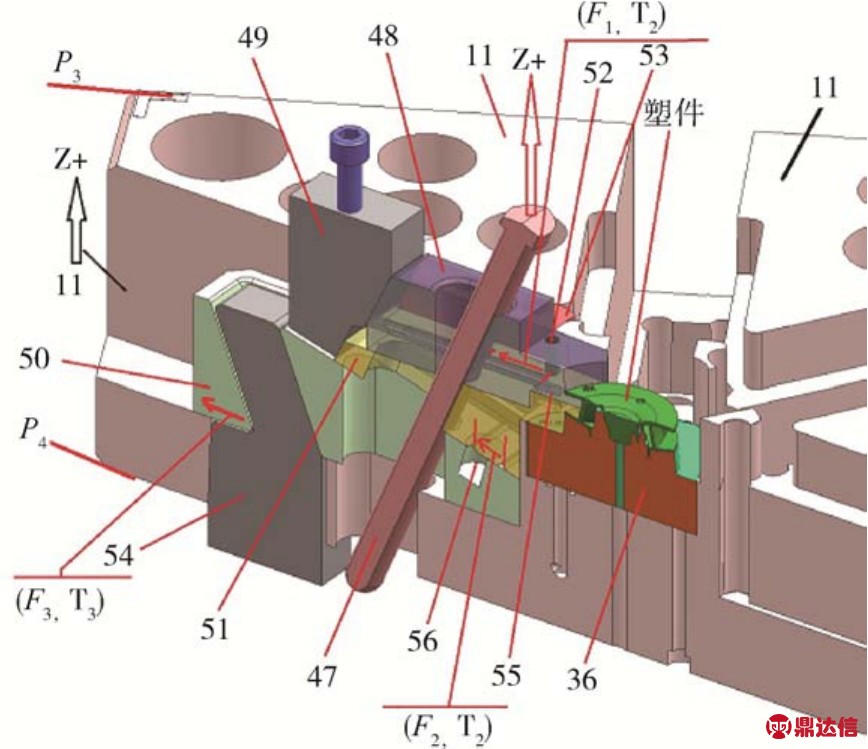
图8 滑块机构工作原理
Fig.8 Working principle of the slider mechanism
③动模继续后退,模具在P3开模处打开,打开过程中,上层滑块48先完成抽芯,而后斜导柱47驱动中层滑块51完成抽芯。
④P4打开完毕,P3打开完毕,油缸19、油缸35动作,将动模板11向上顶出,6个滑块的弯销54将滑块50向外抽出,完成整个滑块的侧抽芯。
⑤顶出。注塑机顶杆推动顶出板推动其上的顶杆29将塑件从型芯镶件36上顶出,从而实现塑件的完全脱模。
⑥复位时,顶出板16、板17先复位,而后模具按P1→P2→P4→P3顺序复位。模具完全闭合,等待下一个注塑循环。
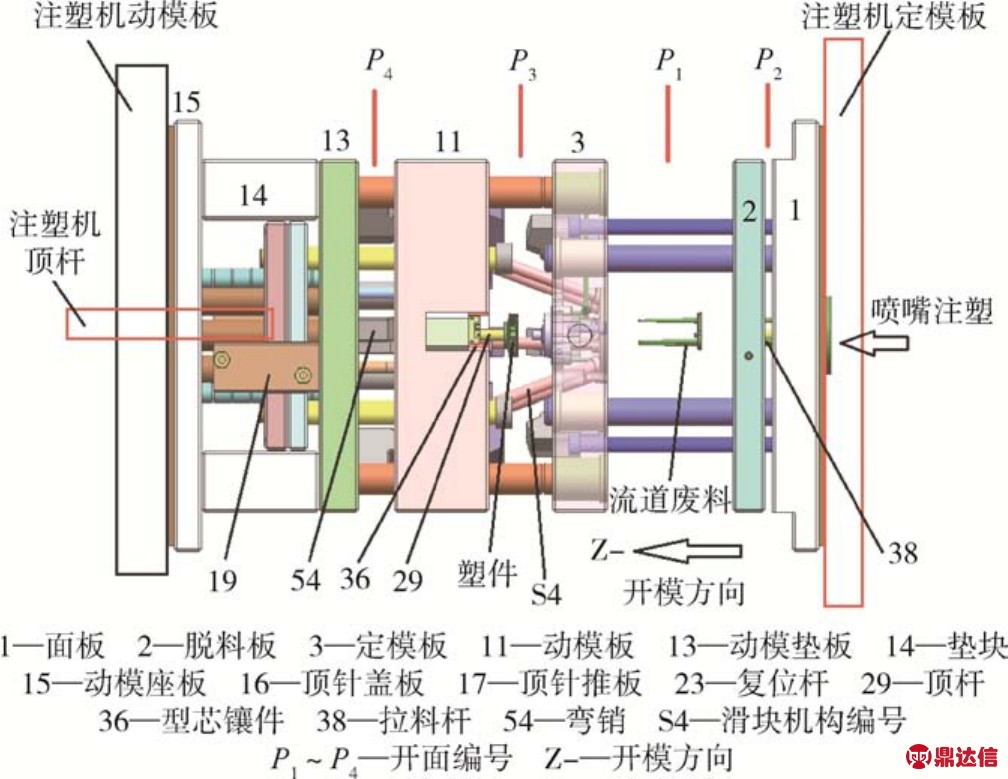
图9 模具工作原理
Fig.9 Working principle of the mould
5 结论
(1)针对塑件的结构特点及成型精度要求高的问题,设计了一种改进型3板点浇口模用于成型泵叶塑件,塑件的浇注成型应用3个点浇口来进行平衡注塑,以控制塑件成型变形;模具的布局为1模1腔;
(2)针对塑件叶槽区域脱模困难问题,在将叶槽成型分割成2层成型块后,设计了一种3层3次复合抽芯脱模,机构的第一次抽芯动作由弹簧驱动上层滑块实施抽芯;第二次抽芯由第三开模面打开后,由斜导柱驱动中间层滑块实施抽芯;第三抽芯在第四开模面打开后,由弯销驱动2个成型滑块再次抽芯抽出,为后续的顶出让出运动空间;塑件的最终脱模由油缸驱动顶针板及顶杆顶出而实现塑件的完全脱模;
(3)基于抽芯机构的动作需要,将典型3板点浇口模架改进为4板4次开模点浇口,从而能驱动滑块机构分次按序来实施抽芯脱模;模具中,脱模机构动作设置合理,机构结构设计巧妙,模具工作可靠,适宜于复杂塑件的成型模具结构及机构设计做参考。