摘要:近年来,有机发光二极管(OLED)被广泛应用于智能手机等中小尺寸显示屏,并逐步进入电视等大尺寸显示领域和照明市场。随着OLED平板显示新时代的到来,对显示屏的彩色化与图案化研究提出了更高要求。与传统真空蒸镀技术相比,喷墨打印技术更容易实现大面积器件的彩色化和复合功能材料的图案化,且工艺简单,成本低廉,并可进行柔性器件加工。本文综述了采用喷墨打印技术制备OLED显示屏的研究现状,并系统介绍了喷墨打印设备的发展历程,通过优化bank结构提高显示屏的分辨率,优化墨水配方及组成配比抑制喷墨液滴的“咖啡环”效应,从而提高显示器发光均匀性,最后对国内外该技术产业进行了概述与展望。
关键词:喷墨打印;OLED;像素结构;发光材料
1 引 言
OLED具有高亮度、高对比度、广视角、画面响应速度快、能耗低和柔性加工等优势,OLED显示技术在智能手机和电视上已取得了巨大的成功,被认为是下一代主流显示技术[1]。目前国际制备OLED显示屏的两种主流技术分别是FMM (Fine metal Mask) 掩模板真空蒸镀RGB像素和蒸镀白色OLED+RGB彩膜。但对于高分辨率显示器而言,高精度掩模板制作成本极高,造成OLED显示屏价格居高不下。喷墨打印是一种重要的实现RGB三原色像素的溶液加工技术[2-3]。采用喷墨打印技术路线制备的新型OLED显示屏工艺较传统方法更为简单,且材料利用率更高,生产成本更低、生产周期较短,在OLED产品应用普及方面更具优势,但喷墨打印制备OLED显示屏时,功能材料的飞行过程和干燥形貌直接影响器件中薄膜的图案化及性能[4]。
20世纪70年代,人们发明了DOD (Drop On Demand) 喷墨打印技术,通过对打印喷头施加一定的压力信号,使打印墨水材料形成墨滴并沉积在基板表面,形成图案化的文字或图片。1990年Burroughes等[5]在剑桥大学卡文迪许实验室发现旋涂的聚合物PPV(poly(p-phenylene vinylene))可产生发光现象。自此之后,溶液成膜技术成为制备有机发光二极管的重要发展方向。1998年,Hebner等[6]研究出了通过旋涂与喷墨打印技术共同制备的OLED显示屏,并首次展示了采用喷墨打印技术制备的全彩OLED显示屏。随后引发世界范围内的研究热潮,多家公司先后通过喷墨打印技术制备出彩色OLED显示屏。
喷墨打印制备OLED显示屏是未来面板制造的理想技术。该技术具有大量优势:多个打印喷头或喷嘴同时工作,可简化生产过程,节省生产时间,可进行大尺寸的生产;无需掩模板就可实现全彩色,降低了生产成本;重复定位准确度高,提高了显示屏分辨率[7]。随着各种发光材料和传输材料被陆续通过喷墨打印的方式用于制备OLED,喷墨打印制备OLED显示屏成为当前相关髙校和面板制造企业追逐的核心黑科技。然而,采用喷墨打印技术制备OLED屏幕距离进入产业化生产,无论在技术上还是在工程上依然存在很多需要解决的难题[8-9]:(1)开发性能可靠、可用于产业化的喷墨打印设备及多驱动打印喷头;(2)高精度像素结构排列方式及制作过程的简化;(3)研发可喷墨打印材料及提高薄膜厚度均匀性与光电性能。许多实验室针对喷墨打印技术的研究做了大量的尝试与改进,但要真正意义上走上产业化道路,还需要相关领域的研究者进行不懈的努力。
目前,利用喷墨打印制备高精度OLED显示屏的研究工作主要包括:功能墨水材料的研发、组份优化和墨滴沉积形貌的研究;随着喷墨打印设备和技术的持续开发,可用于喷墨打印的材料种类也不断扩大;通过研究不同的基板预处理方式,在喷墨打印制备OLED显示屏过程中,对沉积薄膜的形貌进行优化,进而提高打印屏幕的分辨率。本文主要综述了喷墨打印技术的发展历程,高精度像素结构的制备工艺及可喷墨打印功能墨水的研究进展。
2 喷墨打印设备
喷墨打印是一种材料节约型沉积技术,是目前最主要的数字化沉积技术之一,其打印方式为非接触式。基本工作原理是按照预先设计的图案,使墨滴在计算机控制下从微小的打印喷头喷射出,落在承印物的指定位置。在打印过程中,打印喷头与墨滴沉积所在的基板不发生任何接触[2]。
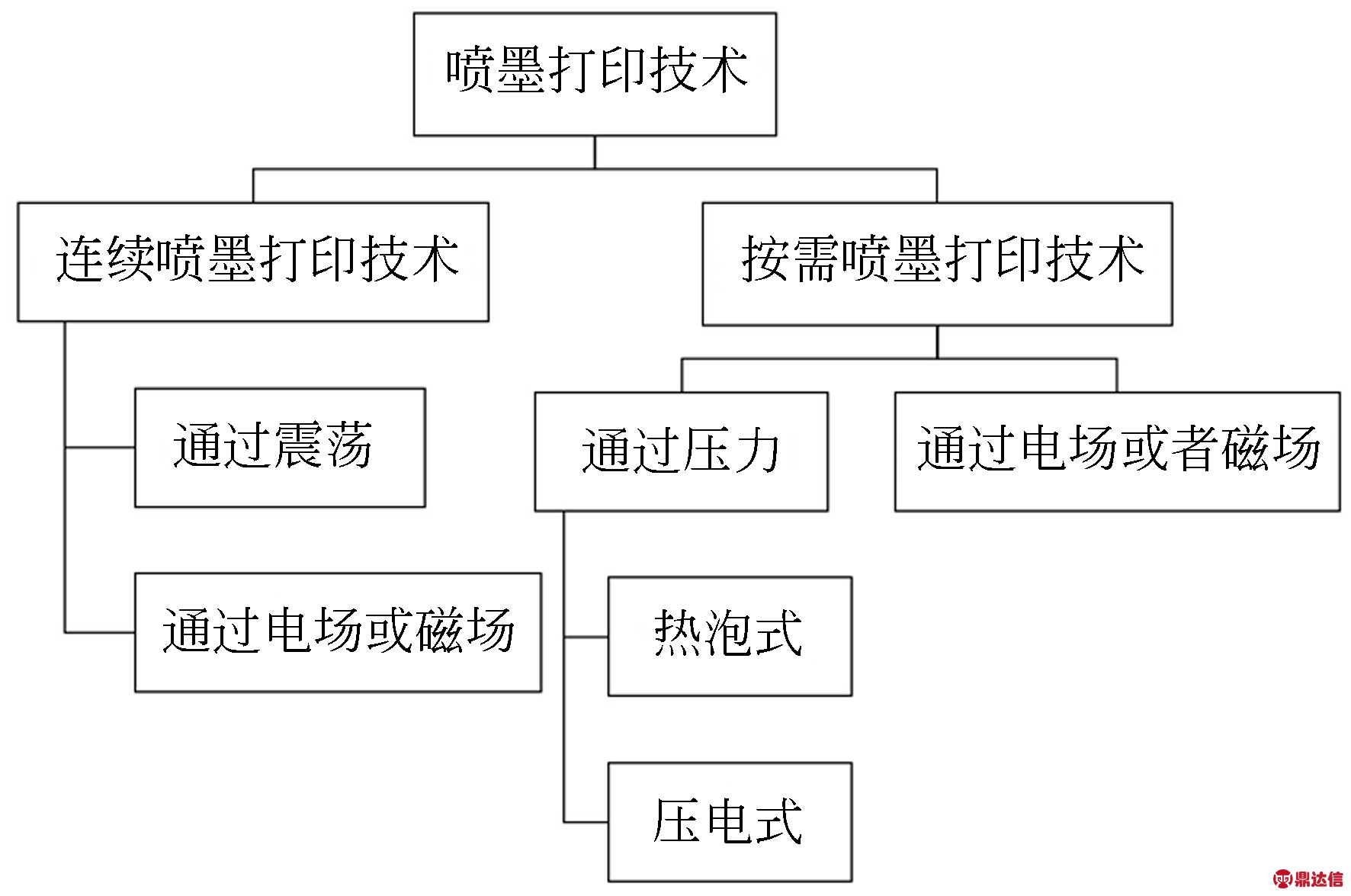
图1 喷墨打印技术的分类
Fig.1 Classification of inkjet printing technology
喷墨打印技术按照喷墨方式的不同可分为连续喷墨和按需喷墨两种[10],具体如图1所示。连续喷墨是指打印喷头在设备工作过程中不断喷墨,并将多余的墨水进行储存回收;按需喷墨打印喷头则是在接收到驱动信号时才进行工作,只在需要位置喷墨成像,因此不需要安装回收装置,是目前广泛应用的喷墨方式。
连续喷墨打印是最早出现的喷墨打印技术,其墨滴以相同的尺寸和间距连续不断喷射,打印速度方面相比按需喷墨打印方式更快。但连续喷墨技术所需要的喷头结构较为复杂,价格昂贵,浪费材料,导致生产成本增加。相较连续喷墨打印技术,按需打印技术更有优势。它的打印喷头结构大幅简化,墨滴喷射过程中,其墨滴的直径和体积与相邻两液滴的打印距离均可进行调节,且墨水材料的利用率达到90%以上。
按需喷墨打印一般通过电脉冲信号控制墨滴的产生和喷射,只在需要沉积的位置喷射墨滴,其工作原理如图2 所示。当对压电材料施加一定电压时,墨滴腔室中的压力产生变化从而实现喷墨;当外加电压为零时,压电材料恢复原形[11]。与热泡式喷墨打印技术相比,压电式喷墨打印技术不会对墨水材料的性质造成影响,且打印形成的墨滴体积更小,显示屏的分辨率更高[12]。因此喷墨打印OLED行业目前普遍采用压电式喷墨打印技术。
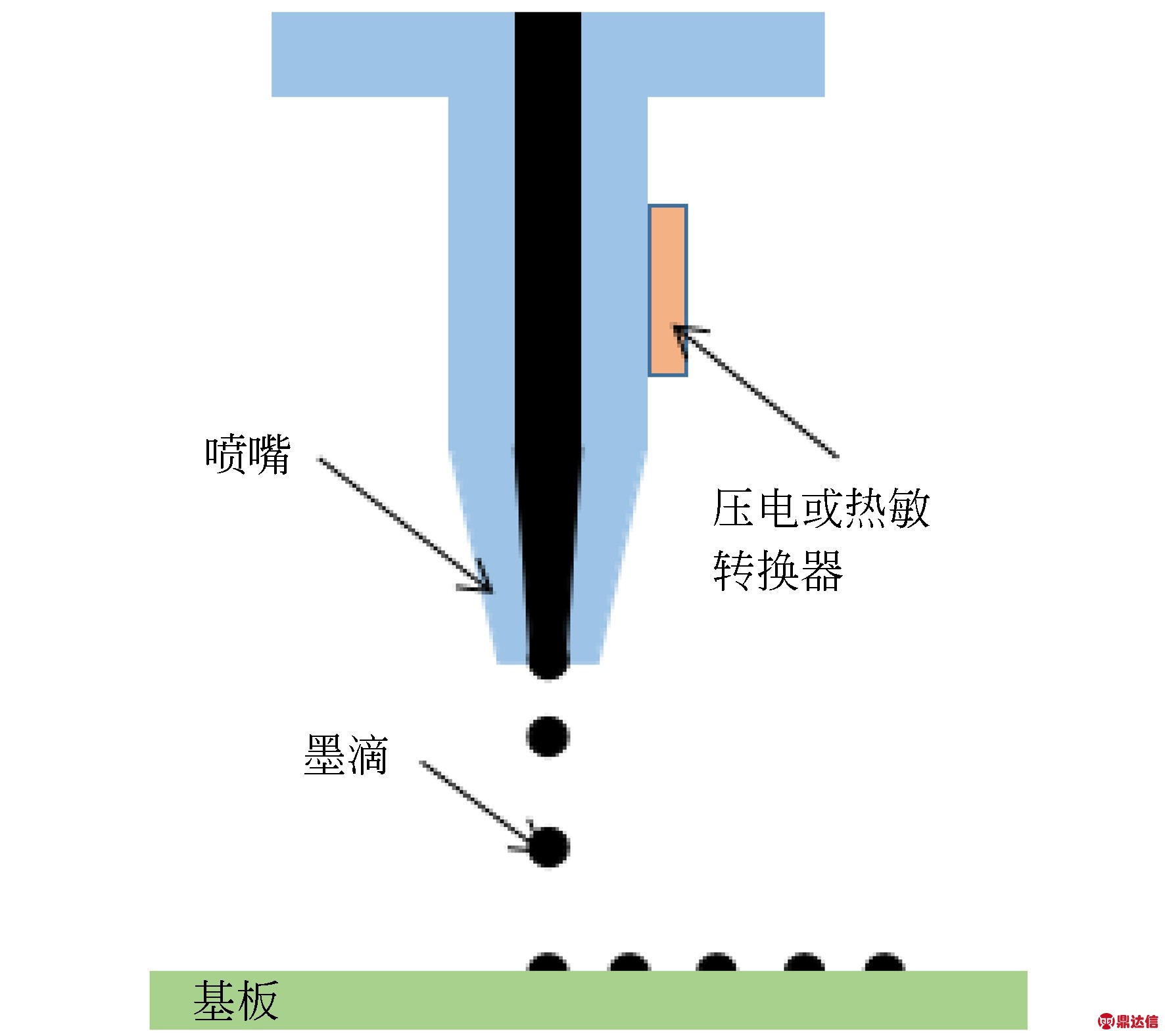
图2 按需喷墨打印工作原理图
Fig.2 Schematic of inkjet print-on-demand
由于采用喷墨打印方式制备OLED显示屏具有突出的工艺优势,针对该产业和研究领域的普遍需求,Chang等[12]研究了压电波形中的稳压时间对喷墨打印墨滴的影响;Tekin等[13]研究了喷墨打印聚合物和无机颗粒的图案化;很多机械设计制作厂商也开始着手研究专业的喷墨打印设备[14]。
随后,美国的Kateeva公司、Microfab 公司,日本真空公司(ULVAC)旗下的Litrex公司等相继研发出了适用于电子领域的专业喷墨打印设备。Kateeva公司在2010年首次提出了喷墨打印制备显示屏的概念,“YIELDJet”打印机是世界上第一台可以实现喷墨打印OLED显示屏的设备。该喷墨打印设备如图3所示。YIELDJet喷墨打印的整个过程均在氮气环境下运行。据称该技术可以更好地保护显示屏,延长其工作寿命并降低生产成本。为喷墨打印制备OLED显示屏的制造工艺带来了全新革命。
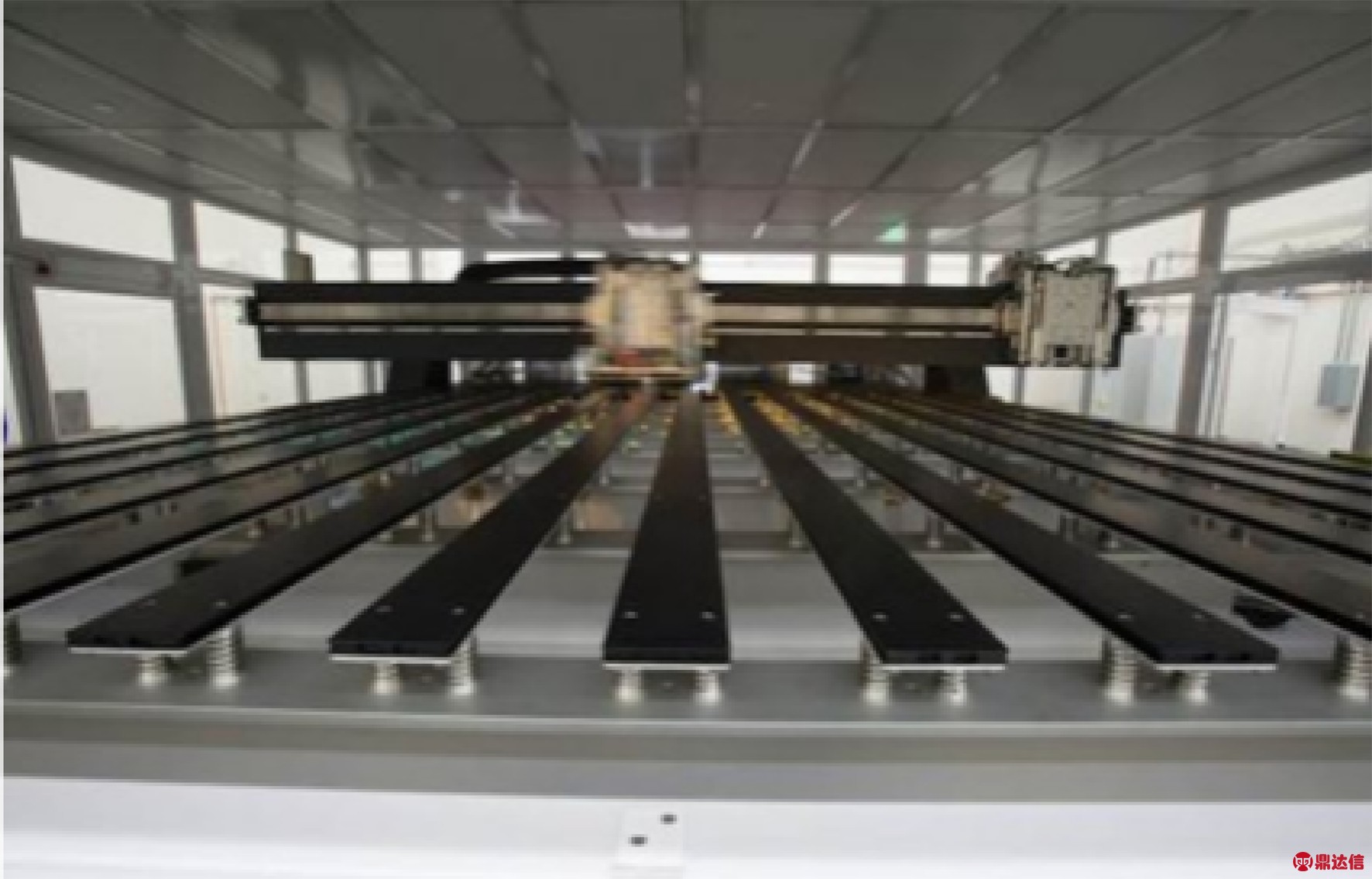
图3 YIELDJet喷墨打印系统
Fig.3 YIELDJet inkjet printer
Microfab公司目前提供的喷墨打印设备包括单喷头和多喷头两种不同喷射方式。Microfab的Jetlab系列设备是专为实验室所设计的,可研究单喷头微小墨滴的喷射及流动过程。其中Jetlab II 是所有系列中功能最为强大的机型,该设备如图4所示。其可在实验室科研及工业化生产过程中对喷墨打印过程进行细节观察及工艺参数优化,放置基板的平台尺寸为160 mm×120 mm,基板水平方向的定位误差为±30 μm,墨滴沉积精度为±3 μm。
Litrex公司目前共有4套喷墨打印设备,可用于LCD (Liquid Crystal Displays)、OLED显示屏的制备。其中,Litrex M-Series打印设备采用多打印喷头喷射的方式,可用于高分辨率、大尺寸OLED显示屏的制备,放置基板的平台尺寸为2 400 mm×2 400 mm,基板水平方向的定位误差为±15 μm,最高打印速度为1 000 mm/s,适用于G3到G8的玻璃基板。
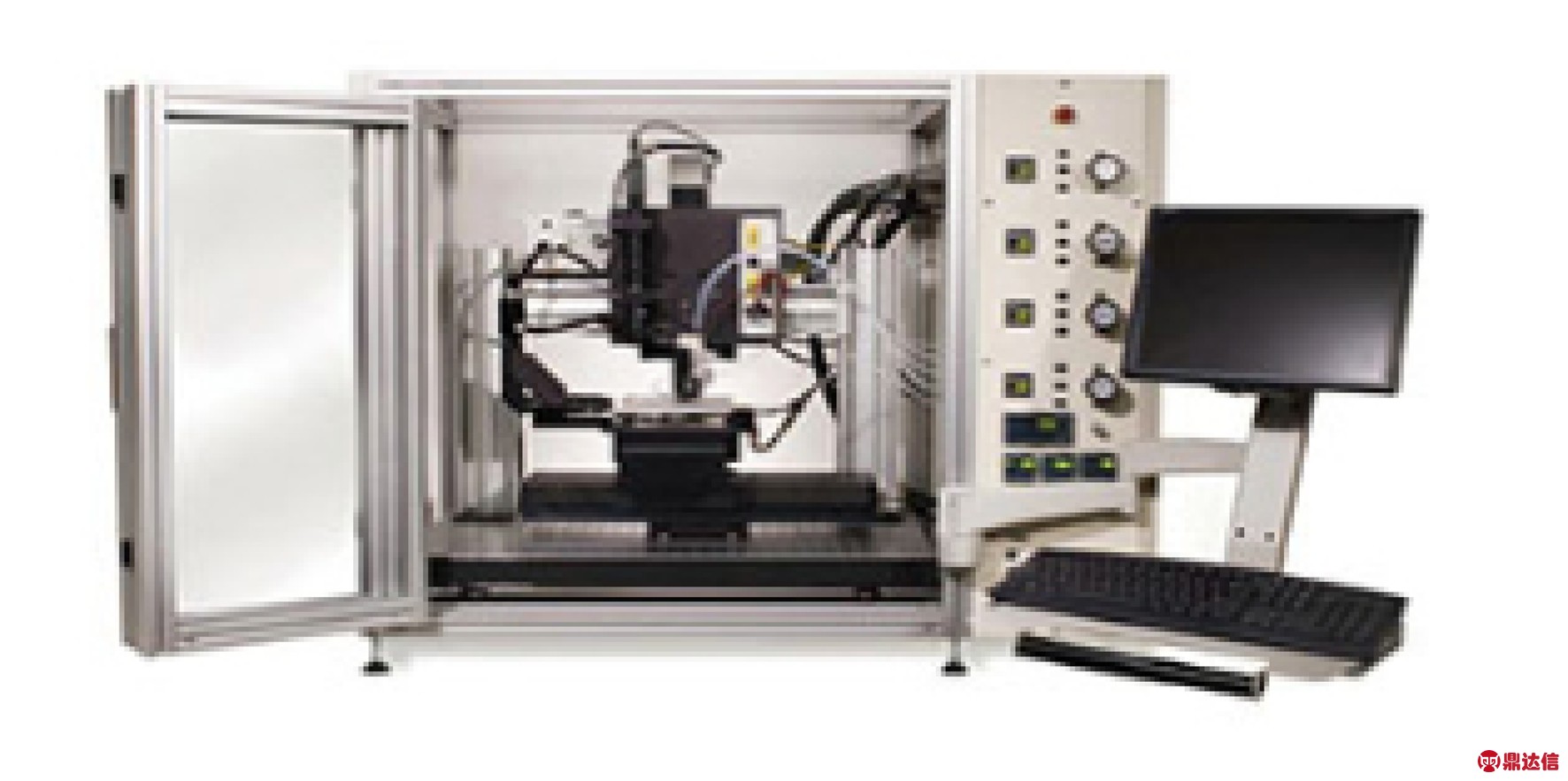
图4 Jetlab II喷墨打印设备(来源:microfab网站)
Fig.4 Jetlab II inkjet printer(Source:microfab website)
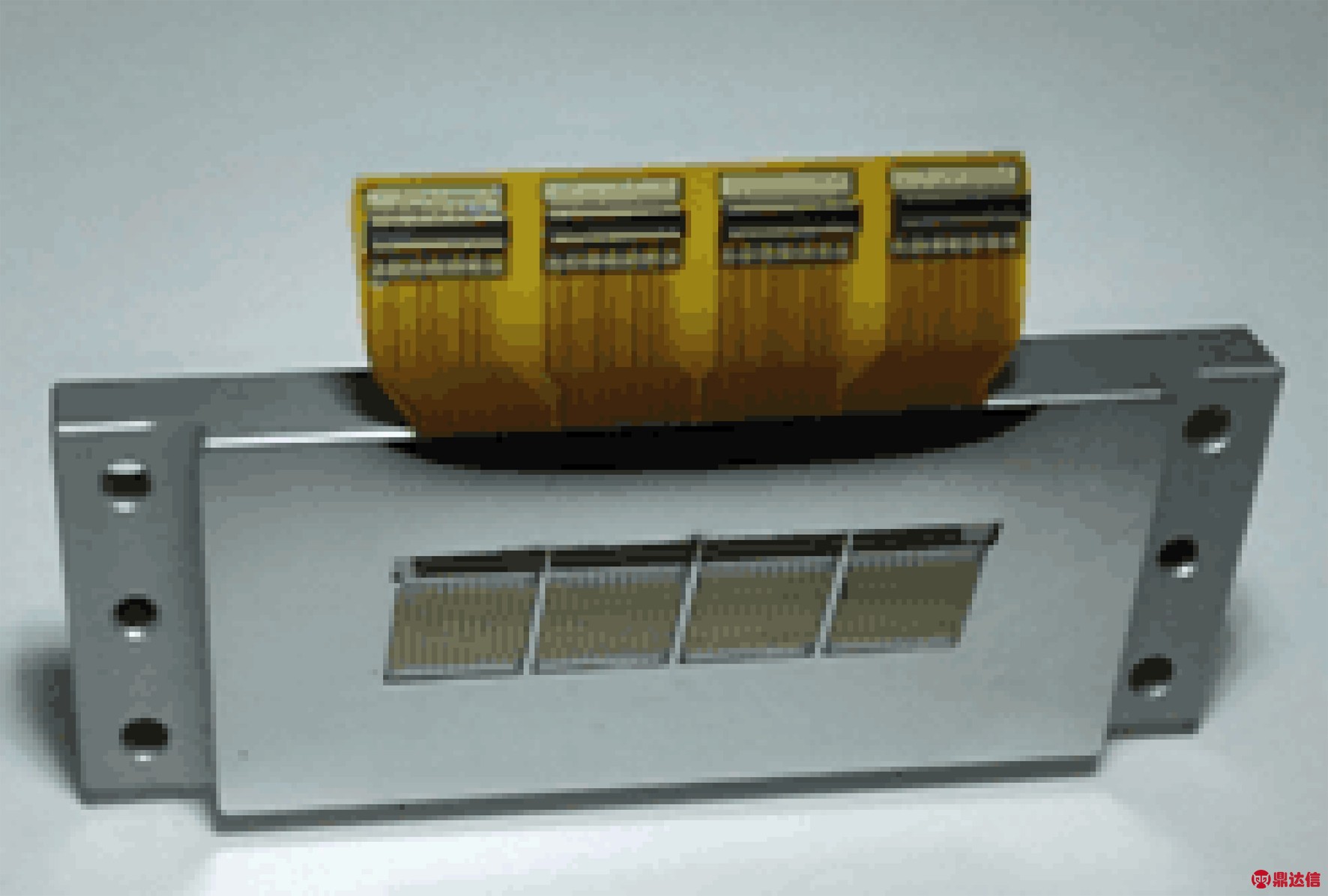
图5 SUREjet-T7680V喷墨打印喷头(来源:sina网站)
Fig.5 SUREjet-T7680V inkjet printer nozzle(Source:sina website)
喷墨打印喷头的质量是检验喷墨打印设备性能的重要标准之一,一般高校研究所采用单喷嘴打印喷头进行喷墨打印,工业界采用多喷嘴的打印喷头进行喷墨打印。相比与单喷嘴打印喷头的打印模式,多喷嘴式的打印喷头可显著减少打印时间,提高打印效率并降低生产成本。因此,目前工业制备OLED显示屏都采用多喷嘴式的打印喷头[15]。Epson提供的MLP MACH打印喷头是一种典型的压电式多喷嘴喷墨打印喷头,其360个喷嘴共分为2行,每行180个喷嘴。2018年12月16日,苏州锐发与中国科学院苏州纳米技术与纳米仿生研究所联合,自主研制了首款国产工业级热发泡喷墨打印喷头,型号为SUREjet-T7680V,该喷头如图5所示。它一共有7 680个独立控制的喷嘴,可保证稳定的喷射速度与墨滴体积,具有高速和高均匀性的特点,且喷嘴耐腐蚀性强,据称其打印速度是同类产品的4倍。
3 OLED基板像素结构
为实现全彩化显示,OLED显示屏由许多可单独控制亮灭的像素构成,而每个像素可水平分解为红绿蓝3个子像素。由于子像素的尺寸非常小,当单独控制每个子像素的亮灭时,红绿蓝三色混合就会产生需要的彩色图案[16-17]。理论上子像素的排列方式是没有限制的,但实际操作中一般采用“红绿蓝”或者“蓝绿红”的排列方式。图6(彩图见期刊电子版)为OLED显示屏普遍采用的子像素排列方式。
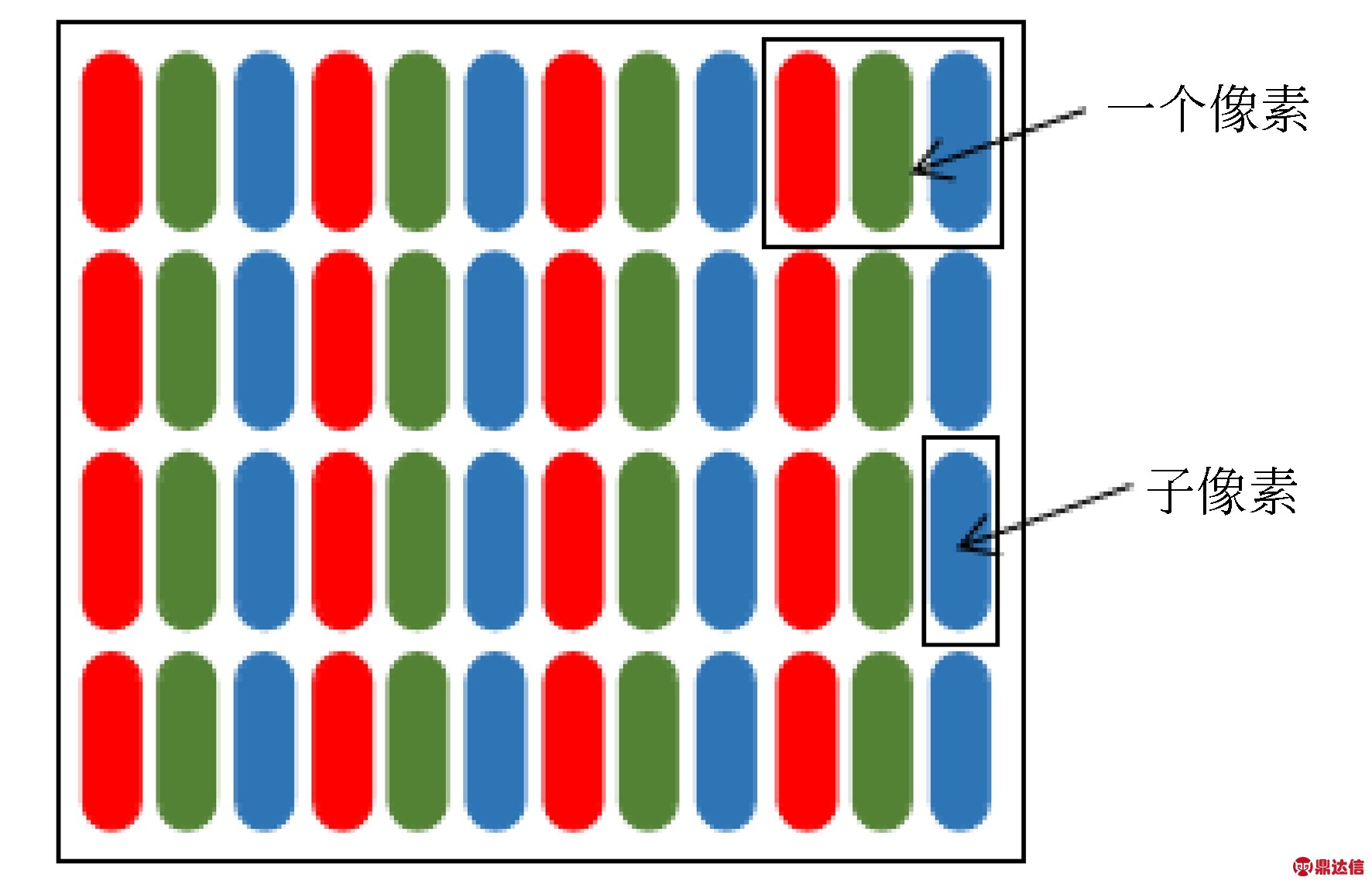
图6 OLED显示屏的彩色像素结构
Fig.6 Pixel structure of color OLED
由于蓝色子像素点的寿命最短,许多厂商采用将单个蓝色子像素的面积增大,同时缩减某些子像素点面积的方式,让不同子像素点的寿命趋于平均,从而提升蓝色子像素的寿命。就OLED像素排列而言,除了上述的三色条状排列,通常OLED显示器采用Pentile排列的方式,Pentile排列包括双条型RGB排列和钻石型RGB排列,如图7(彩图见期刊电子版)所示。传统的RGB像素排列方式中,红绿蓝子像素面积比为1∶1∶1;而Pentile像素排列方式中红绿蓝子像素的面积不等,红色和绿色子像素的面积为蓝色子像素面积的二倍。在显示图像时,通过“借”用相邻子像素的另一种颜色来构成三基色发光。韩国三星公司在产品S4系列显示屏中对像素单元采用了Pentile排列,这大大提高了OLED显示屏的分辨率。
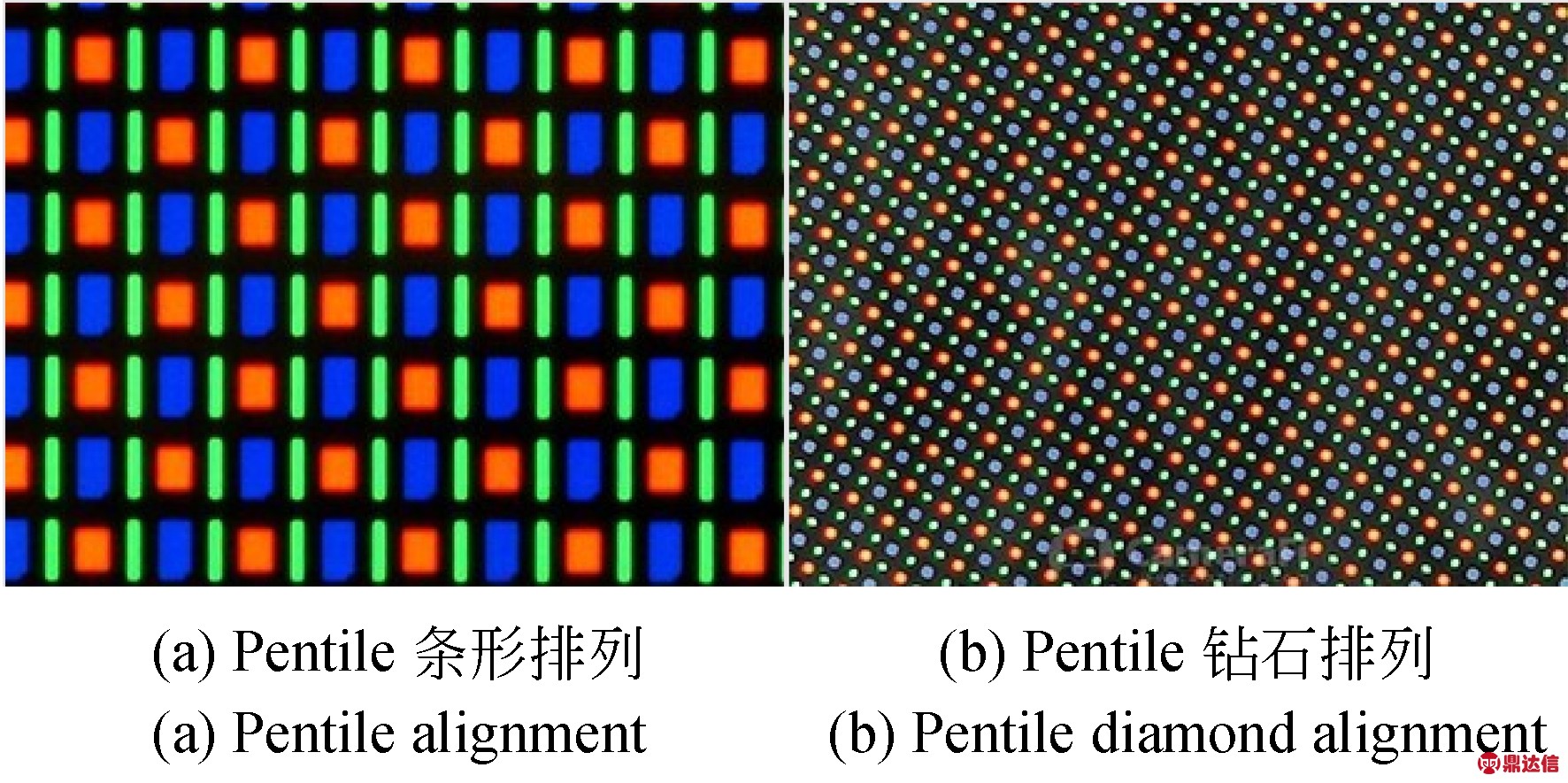
图7 OLED像素排列方式(来源:PC online网站)
Fig.7 Pixel alignments of OLED(Source:PC online website)
为实现三原色像素喷墨打印的图案化,并满足高分辨率的要求,需要在基板上制作一些bank结构,从而使墨水能够在精细的像素槽内沉积成膜而不与相邻像素点混合。同时在制作PM-OLED (Passive Matrix OLED)器件时,还需要在基板上构造隔离柱以制作阴极条形电极[18-19]。
目前使用范围最广的像素结构是由日本先锋公司发明的,其结构由正梯形绝缘像素坑和倒梯形隔离柱构成,图8为单个像素侧面结构示意图。在制作OLED基板像素结构时,首先通过光刻技术把不需要的ITO (Indium Tin Oxide)薄膜部分去除,仅留下条状的ITO电极;之后在条状ITO电极上涂覆绝缘材料聚亚酰胺(PI),并对PI层进行光刻;最终露出像素化的ITO阳极。Wang等[20]采用喷墨刻蚀技术,将一种特殊的氟化溶剂喷墨打印在绝缘聚合物层上,溶剂蒸发后原位形成微凹槽。这种方法避免了曝光工艺,简化了生产流程,为bank结构的设计提供了更多选择。
传统bank形状是长宽比为3∶1的操场形像素[6]。如图9(a)(彩图见期刊电子版)所示。与矩形结构相比,墨水在操场形像素的拐角处可更好地铺展成膜,但这种排列方式会造成基板面像素结构开口率较低。为了提高像素开口率,华南理工大学课题组[21-22]设计了一种线形像素结构,其结构如图9(b)(彩图见期刊电子版)所示,这种设计方法可减少基板表面一半的像素壁,使打印墨水材料可形成连续的线形薄膜,减少了打印时间、优化了打印薄膜形貌,并提髙了器件的开口率。
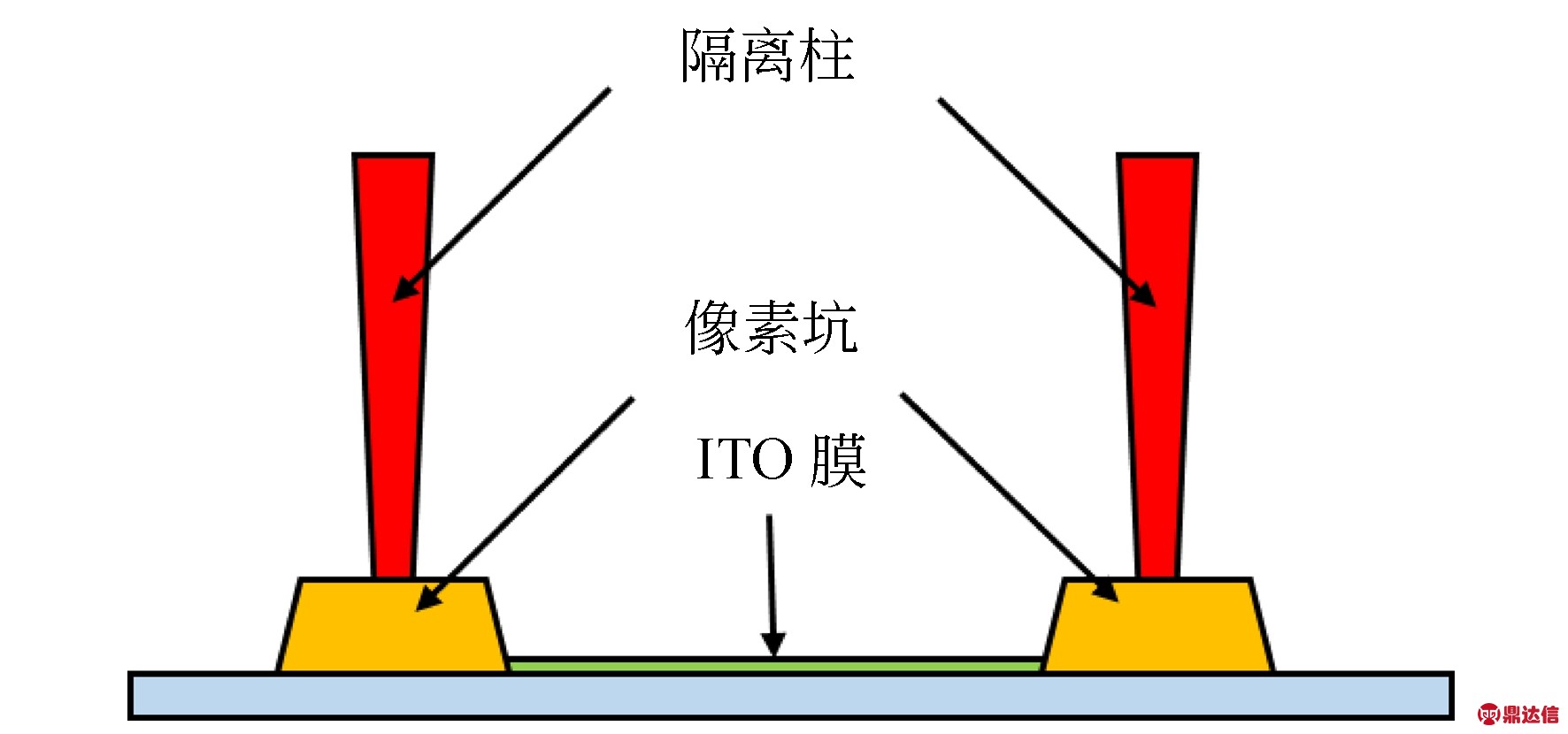
图8 单个像素侧面结构
Fig.8 Cross-section of a single pixel
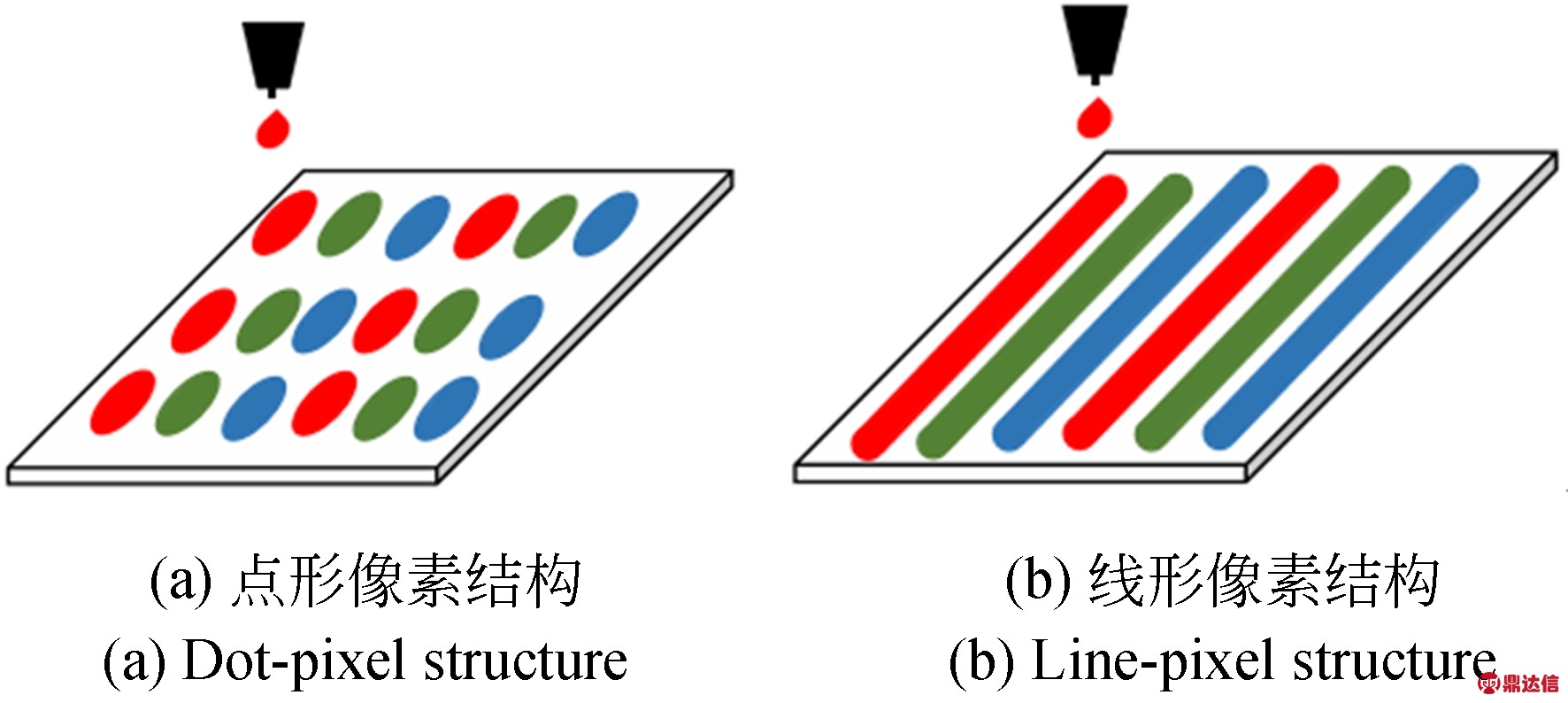
图9 OLED像素结构
Fig.9 Pixel structures of OLED
对于点阵形像素,如像素阵列为1 080×1 920、尺寸为94~165 cm的高清电视机,TFT(Thin Film Transistor)背板上的bank尺寸分别为140 μm和250 μm;对于像素阵列为480×800、尺寸为7.37~9.65 cm的智能手机等移动设备,TFT背板上的bank尺寸分别为26 μm和35 μm。通常打印喷头的直径决定了产生墨滴的体积,因此,可根据bank的尺寸调整打印喷头直径的大小。由于打印墨水材料的浓度和单个墨滴的体积都是已知的,因此,根据每一层所需的薄膜厚度可计算出每一个bank内需要打印的墨滴的滴数。Gensler等[23]通过调整喷头的驱动波形和电压,打印了宽为10 μm的像素结构,最终实现了分辨率为310 PPI(Pixels Per Inch)的AM-OLED(Active Matrix OLED)器件。Kim等[24]提出,现如今喷墨打印设备的精度可达到2 μm,采用微透镜阵列可提高OLED显示屏的光提取能力。基于这种打印精度,通过设置像素定义层(Pixel Definition Layer,PDL)的模式,可使RGB像素打印分辨率超过500 PPI的OLED显示屏。
对于线形像素,Mu等[25]设计了宽为50.5 μm,长为8 mm的线形bank结构,在可变化的墨滴间距设置中引入简单的等差数列,以抑制线中心位置处的溶质聚集,沿长轴方向喷墨打印出均匀的导电聚合物聚(3,4-乙二氧噻吩)-聚苯磺酸(PEDOT:PSS)线形薄膜,将薄膜表面形貌从凸起转变成平坦,并将蓝色聚合物PFSO(poly(dibenzothiophene-S,S-dioxide- co-9,9-dioctyl-2,7-fluorene)作为发光层旋涂在PEDOT:PSS层上,整个线形薄膜亮度均匀。此外,采用固定间距打印的像素线,PEDOT:PSS层的厚度从中间向两边逐渐减小,线形像素的边缘区域几乎不发光。
4 喷墨打印的墨水材料
4.1 可打印墨水的物理属性
对于喷墨打印制备的高分辨率OLED显示屏,不仅要求产生的墨滴尺寸小,还要求墨滴能够稳定下落并精确定位到基板的指定位置。溶剂型墨水在喷射至基板表面时会发生润湿基板、墨滴铺展、溶剂蒸发、溶质颗粒沉积及干燥成膜几个阶段[26]。在喷墨打印制备OLED显示屏的过程中,墨水的物理性质如表面张力、粘度、惯性对墨水的可打印性和墨滴形貌的变化起着至关重要的作用。不适合打印的墨水会引起各种问题,如堵塞打印喷头喷嘴、形成卫星点等,影响墨滴质量和打印显示屏成品率。为了研究从打印喷头喷出的墨滴,Fromm等[27]开发了Navier-Stokes表达式,如式(1)、(2)所示,其中,Re表示雷诺数,为墨水材料的惯性力与粘性力之比,We表示韦伯数,为墨水材料的惯性力与表面张力之比。
(1)
(2)
其中,ρ表示打印墨水材料的密度,v表示墨滴离开打印喷头后的飞行速度,η表示打印墨水材料的粘度,d表示打印喷头直径,σ表示打印墨水材料的表面张力。打印墨水粘度过低时,在墨滴喷射过程中液柱难以聚集无法形成规则的液滴,但打印墨水的粘度过大时,墨滴在喷嘴处聚集,喷射速度减慢。打印墨滴的表面张力决定了墨滴从打印喷头喷射出时墨滴的形状。打印墨滴的表面自由能和运动惯性决定了墨滴脱离喷嘴后的形状。
奥内佐格参数Oh是雷诺数(Re)与韦伯数(We)的平方根之比。如式(3)所示:
(3)
一般用Oh的倒数Z=1/Oh来表征墨滴的性质。Fromm等[27]给出了墨水的可打印Z值范围为1~10;2009年,Jang等[28]通过观察不同流体在不同Z值下的液滴形成过程,确定了可打印墨水Z值的范围为4~14;Singh等人[29]采用聚(3,4-乙二氧噻吩)-聚苯磺酸(PEDOT:PSS)这种导电聚合物材料喷墨打印制备太阳能电池,发现当Z值为4.63和5.37时,分别经过45 s和65 s的观察才形成了稳定液滴。墨水材料若用于喷墨打印,其需要具有一定的参数范围:墨水的粘度为1~20 mPa·s,墨水的表面张力为35~60 mN/m。很少有研究小组报告物理性质超出常规范围1<Z<14的流体可以稳定喷射[30]。
4.2 喷墨打印有机功能层
有机功能层薄膜的质量决定了喷墨打印OLED器件的亮度均匀性与寿命。通过优化喷墨打印时的电压波形、打印喷嘴与基板距离、打印液滴间距等工艺参数,减小因薄膜不均匀造成的显示屏bank内发光不均匀,甚至短路不发光的问题。喷墨打印过程中墨滴的形成与墨滴的粘度、表面张力等物理性质有关。喷墨打印过程中墨滴与基板的接触会产生反弹、铺展与飞溅3种情况,Mundo等[31]通过引入参数K用以划分液滴反弹、铺展与飞溅的界限。参数K的表达式如下式(4)所示。
(4)
当3<K<57.7时,墨滴能够铺展成膜;当K<3时,墨滴发生反弹;当K>57.7时墨滴发生飞溅。Sonin等[32]将液滴铺展分为惯性力起主导作用的铺展与毛细流力起主要作用的铺展。为保证墨滴在bank内铺展的均匀性,需保证墨滴与ITO的接触角小,与bank的接触角大。喷墨打印的墨滴随着溶剂的挥发干燥成膜。Deegan[33]等将墨滴的干燥成膜划分为恒直径模式和恒接触角模式,恒直径模式中由于墨滴边缘与中间部分的溶剂挥发速度不同,溶液从中心向边缘流动形成了边缘厚中间薄的咖啡环现象,而恒接触角模式中未发生钉扎,形成的薄膜均匀。
溶液加工法制备的小分子OLED显示屏,因具有高效率和长寿命等良好的器件性能而备受关注。Xia等[34]将喷墨打印方法用于加工真空蒸镀小分子材料,并打印磷光小分子发光材料制备显示屏。因此,越来越多的人把研究重点放到小分子发光材料的喷墨打印技术上[35-36]。荷兰研究机构Holst Centre的Gorter等[37]研究了喷墨打印制备小分子电致发光器件及其影响因素,制备了结构为ITO/PEDOS:PSS/NPB/Alq3/LiF/Al的器件,并对比了真空蒸镀和喷墨打印方法制备的NPB/Alq3功能层对器件性能的影响,发现喷墨打印所形成的有机薄膜成膜性较差,形貌均一度低,制备的器件发光效率小于0.1 lm/W。针对这个问题,学术界做出了大量研究,如对小分子材料掺杂长的烷基链进行修饰,增加材料的溶解性,进而提高墨水的成膜性[38];或将如聚苯乙烯(UHMW-PS)这种分子量极大的材料加入到小分子溶液中,改善小分子材料的成膜性能[39-40]。相比有机小分子材料,聚合物发光材料可阻止材料中晶体颗粒的析出,且材料的选择范围广泛、可按照自身需求设计分子结构、可对材料能带进行调控,容易进行加工且稳定性高[41-42]。迄今为止,研究报道的最多且最常用的聚合物电致发光材料主要有聚芴类、聚噻吩类、聚乙炔类和聚对苯类等。Singh 等[43]采用含大分子磷光材料作为器件发光层、聚(9-乙烯咔唑)作为器件空穴传输层、PBD(2-(4-Biphenylyl-5-phenyl-1,3,4-oxadiazole)作为器件电子传输层,采用喷墨打印技术制备OLED显示屏,其屏幕最大发光亮度可达6 000 cd/m2,当发光亮度为5 cd/m2时,器件所需的电压为6.8 V。
由于OLED具有空穴传输层、电子传输层、发光层等多层膜结构,传统的溶液处理常常会造成层间墨水的混合,导致之前沉积层的腐蚀。因此,把可溶的前驱体转变为交联的、不可溶的聚合物,可有效解决层间混合和腐蚀问题。Xie 等[44-45]采用交联电子传输材料TV-TmPY ((5-(4-vinylphenyl)pyridine-3-yl) benzene) ((5-(4-乙烯基苯基) 吡啶-3-基)苯)在空气中喷墨打印制备了OLED器件,交联薄膜具有良好的空气稳定性,最高外量子效率(EQEs)达到了8.5%。S.Oliviera等[46]研究了不同的溶剂混合物对墨水性质的影响,将具有交联性质的空穴传输层材料QUPD_((N4,N40-Bis(4-(6-((3-ethyloxetan-3-yl)methoxy)hexyloxy)phenyl)-N4,N4′-bis(4-methoxyphenyl)biphenyl-4,4′-diamine))溶于比例为8∶1∶1的甲苯/异丙醇/苯甲醚溶剂中,通过喷墨打印制备了两种不同尺寸(0.44 cm2和4 cm2)的高效(18 lm/W)的绿色OLED显示屏。
在喷墨打印的过程中,由于墨水材料具有一定的流体特性,在墨滴飞行及沉积时,容易造成薄膜形貌不均匀、咖啡环等问题。Sun等[47]对现有克服“咖啡环”效应的方法进行了系统总结,主要包括减小外向毛细流动、增加内向马拉哥尼流动和引起三相接触线的滑移三个方面;Li等[48]从流体动力学的角度分析了液滴干燥过程中“咖啡环”的形成机理;Crivoi等[49]开发了一种模拟胶体液滴中的颗粒蒸发钉扎沉积方法,并分析了环形墨滴轮廓对墨水中溶质颗粒浓度的依赖性;Wu等[50]基于亲水基板和疏水基板之间表面能的差异,通过改变钉扎模式对沉积薄膜的3D形态进行控制;Soltman等[51]在温度不同的基板表面打印线形结构的PEDOT:PSS薄膜,当基板温度较低时,沉积薄膜的截面图形为平滑或凸起的状态,当基板温度较高时,沉积薄膜的界面为凹陷的形状,具有明显的“咖啡环”现象;Xing等[52]通过改变喷墨打印墨水溶剂组份,在异丙苯中添加高沸点、高粘度的环己基苯作为第二组份溶剂,增大马拉哥尼流动以有效抑制“咖啡环”效应,提高了打印薄膜的均匀性。
4.3 喷墨打印的金属电极
通常情况下,OLED显示屏的阴极采用真空蒸镀设备完成,然而真空蒸镀设备价格高昂,与之相比,采用喷墨打印方式可大幅度降低生产成本。目前采用全溶液法制备OLED显示屏的报道较少,科研人员主要采用喷墨打印制备OLED显示屏的有机功能层[53-54]。
受设备中打印喷头直径、墨滴喷射量的限制,喷墨打印对所制备的OLED显示屏的尺寸和分辨率有一定的范围要求。为了制作窄的辅助电极,Kwan-Hyun等[55]采用狭窄的亲水轨道,在不产生断线现象的情况下制备了宽18 μm的银栅极,使OLED显示屏的亮度均匀性提高了10%左右。Tao等[56]在Ag纳米线电极的顶部插入喷墨打印的Ag栅格,用其连接松散的Ag纳米线,增强其机械稳定性和导电性,并采用此方法成功制造了OLED显示屏的电极。
5 喷墨打印产业现状
日本INCJ、JDI、SONY、Panasonic公司于2014年共同建立了JOLED公司,采用喷墨打印作为量产方式,于2016年下半年开始试产,并于白山建立G6生产线。JOLED公司在2018年4月发布了全球首款通过喷墨打印技术制备的OLED显示屏样机,该样机如图10所示,为具有4K(3 840×2 160)分辨率的21.6 inch医用显示屏。据称与以往的制备方法相比,喷墨打印技术降低了约20%的生产成本。JOLED也成为世界上第一家通过喷墨打印技术制备OLED显示屏的公司。
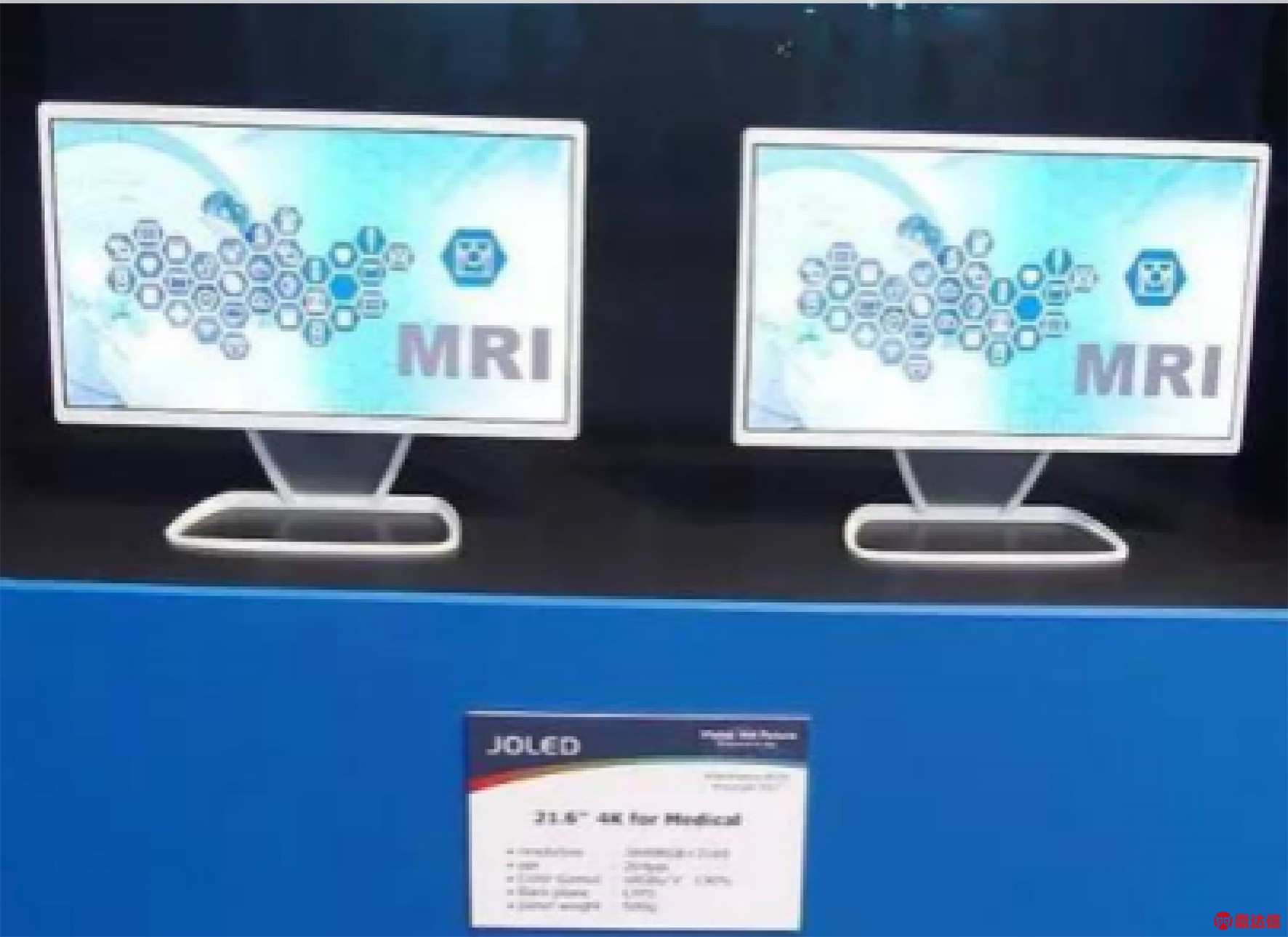
图10 JOLED 21.6英寸喷墨打印显示屏
Fig.10 JOLED 21.6-inch inkjet-printing screen
我国京东方科技集团股份有限公司于2010 年开始开发喷墨打印OLED 显示屏技术,是国内首家进入此领域的技术开发企业。京东方公司在2012至2015年期间,分别点亮了5 inch、14 inch、17 inch和30 inch等多种规格的喷墨打印OLED显示屏样机,并搭建G8.5喷墨打印制备OLED显示屏生产线。京东方在2018年11月发布了中国首款采用喷墨打印技术制备的55 inch OLED显示屏,率先将喷墨打印技术应用于显示终端产品,该样机如图11所示。据报道称该显示屏的对比度达1 000 000∶1,色域为96.8%NTSC(National Television Standards Committee)。
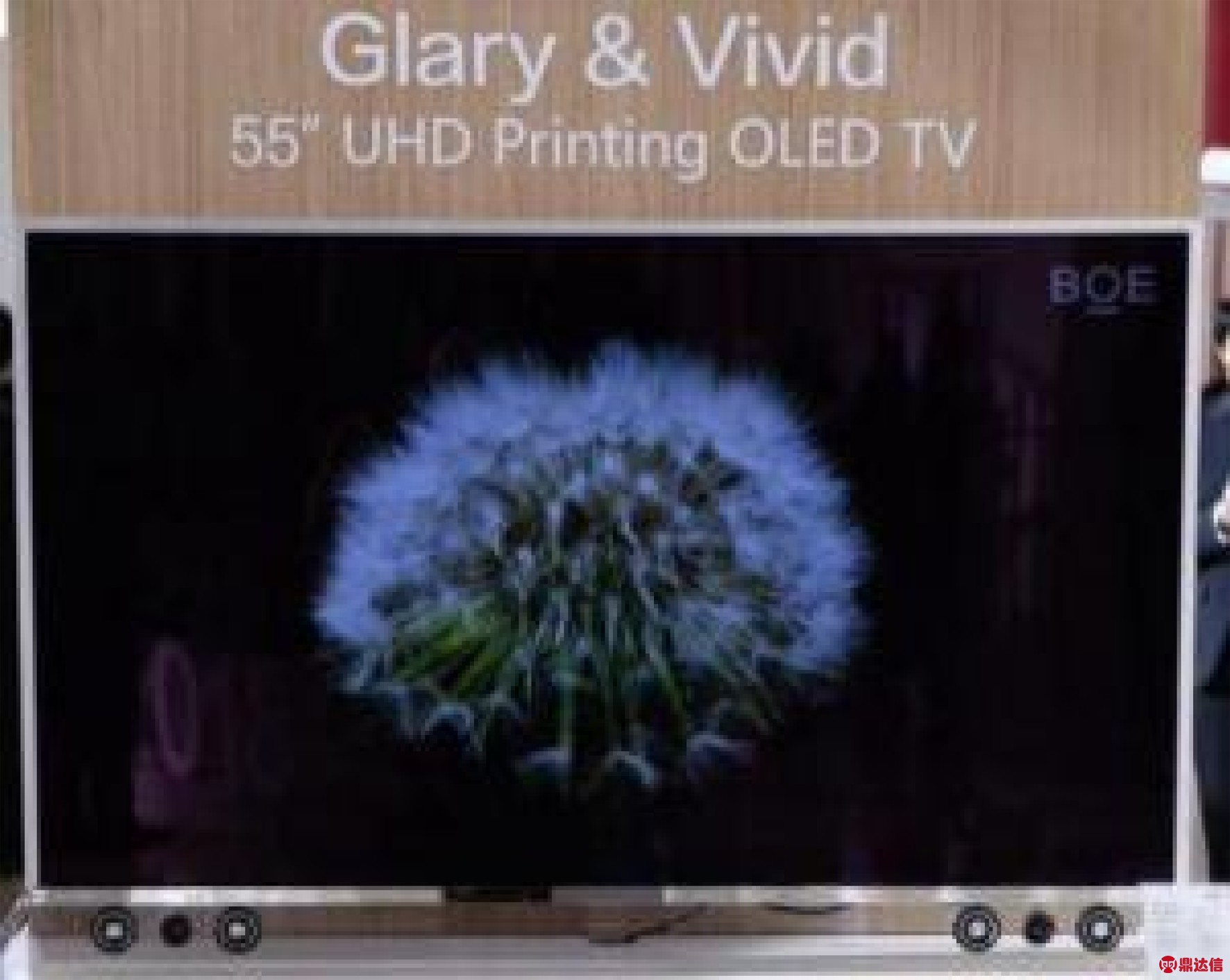
图11 BOE 55英寸喷墨打印显示屏(来源:IT homel网站)
Fig.11 BOE 55-inch inkjet-printing display screen(Soure:IT homel website)
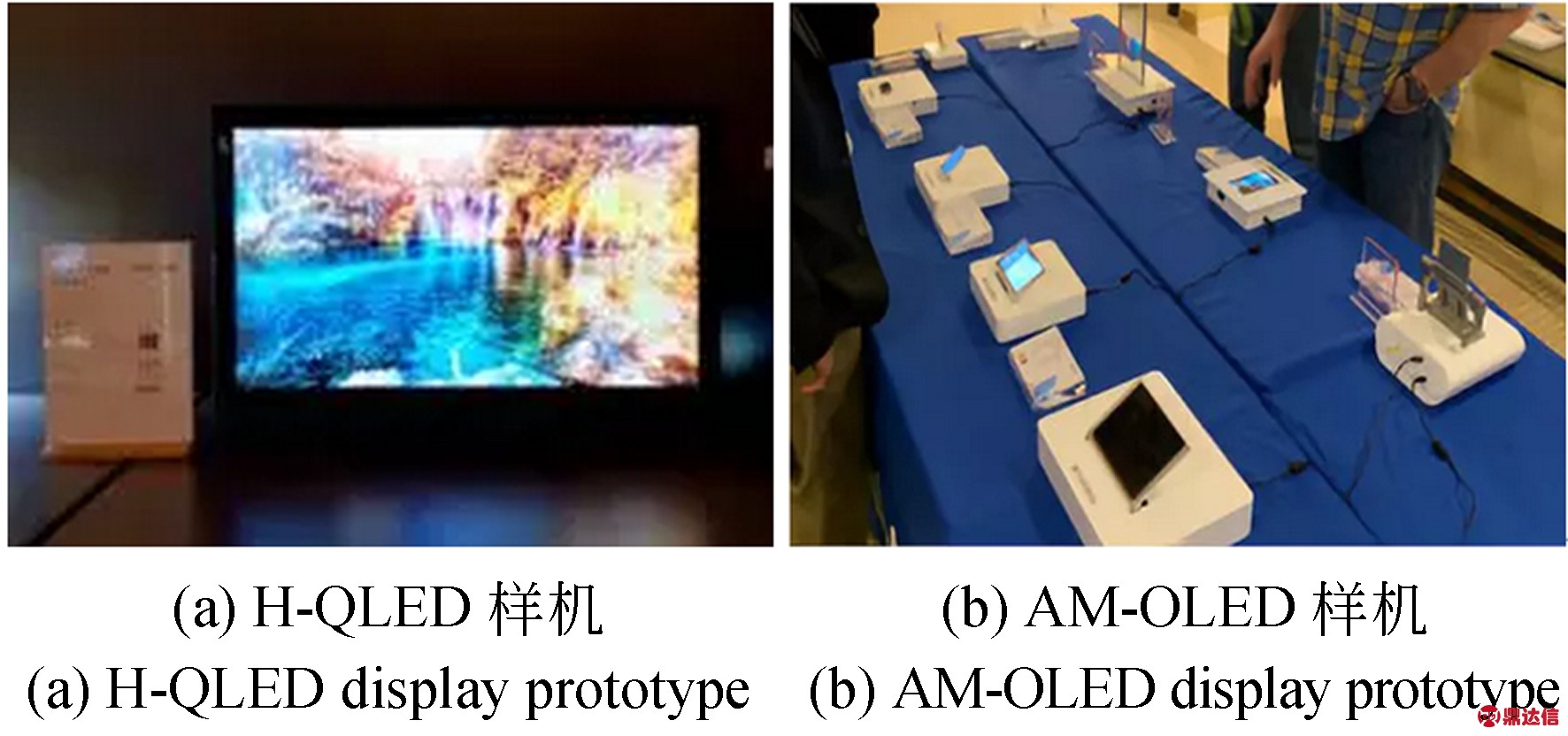
图12 CES喷墨打印显示屏(来源:zol网站)
Fig.12 Inkjet-printing display screen of CES(Source:zol website)
聚华公司采用生产与研发同步进行的方式,并与国内30多家从事喷墨打印和柔性显示的高校研究所、公司企业进行合作。在2019年1月,聚华公司在美国拉斯维加斯举办的国际消费类电子产品展览会(CES)上展示的采用量子点(QD)与OLED共同喷墨打印的31 inch H-QLED显示屏样机,是世界上第一台同时具备QD与OLED优势的显示屏,该样机如图12(a)(彩图见期刊电子版)所示,发光层的红、绿色发光材料为量子点材料,蓝色发光材料为有机材料,开口率达到50% 以上,分辨率达到4K;同时还展示了由聚华公司联合天马微电子公司共同研发推出的尺寸为4.92 inch的高分辨AM-OLED显示屏样机,该样机如图12(b)(彩图见期刊电子版)所示。其发光模式为顶发光模式,开口率达到60%,显示屏的亮度大于250 nit,分辨率高达403 PPI,在目前已知采用喷墨打印制备的OLED显示屏中,是分辨率较高的屏幕之一。分辨率的提高,将采用喷墨打印技术制备的显示屏从之前中大尺寸向小尺寸的应用推进,同时促进了喷墨打印技术的产业化进程。
6 结论及展望
喷墨打印作为新世纪显示技术的发展方向,其制作的显示屏具有绿色环保、简单轻薄、视角广、分辨率高等特点,是显示行业未来的重要发展方向。喷墨打印技术非常适合生产柔性显示器,特别是未来可以开发卷对卷的生产工艺,就像印刷报纸一样,这项技术的突破将彻底颠覆传统显示器的生产方式。随着5G、物联网、人工智能等信息技术的快速发展,柔性显示器与穿戴应用将紧密结合,显示器与传感器将高度集成,从而呈现出显示器“无处不在、无所不能”的应用场景。
自从2004年日本精工爱普生公司使用喷墨打印技术制备了当时世界上第一台大尺寸(40英寸)全彩高分子OLED原型机,到今天JOLED,三星,友达光电,京东方和聚华等一批企业在喷墨打印OLED/H-QLED显示器领域取得的多项进展,这项技术已经持续开发了15年。正如前面提到的,当前喷墨打印OLED技术尚有一些关键问题亟待解决,包括业界一致认同的可喷墨打印高性能的发光墨水,电子空穴注入和传输墨水,喷墨打印机的精确定位,打印机和打印头的稳定性,喷墨打印基板亲水和疏水预处理,像素成膜工艺的控制,以及提高材料和器件的寿命等等。当这项技术步入市场,新面临的核心问题也逐步会从技术领域延伸到工程领域,包括墨水与喷头一体化的喷墨稳定性,上百万像素打印后的器件均匀性,多层膜堆栈的界面可控性,打印像素缺陷的智能检测和修复,生产成品率的控制和管理,以及薄膜封装工艺的优化和器件寿命的进一步提高等。据媒体报道,目前国际和国内已有多家企业正在规划和建设以喷墨打印技术为主体的OLED显示器生产线,产品定位在特殊应用的中大尺寸显示屏,如医用显示屏和仪器仪表显示屏及电视。综上所述,这项技术的最终完善以及它在市场上获得成功,还有待于学术界和工业界在未来几年的齐心协作,共同推进。