摘 要:以真空部件为主体并结合自动化控制技术搭建了气体传感器测试系统. 该系统采用静态测量模式,提高了样气配制、响应与恢复时间测量以及测试气压控制的精度. 系统功能全面,可同步测量样品的光学和电学参量对目标气体体积分数、工作温度、湿度、气压、光照等变量的响应,并可开展批量样品的长期稳定性测试.
关键词:气体传感器;真空技术;静态测量模式
气体传感器在安全环保、健康医疗以及智能家居等领域有广阔的应用前景,是国家重点发展的高新技术之一. 目前研究的重点为气敏材料[1]及传感器结构[2],对传感器测试技术则较少关注[3-6]. 而当前普遍采用的动态配气技术依靠调节不同气路的流量比来配制样气,难以配制痕量气体;而且测试腔内气氛更换耗时较长,无法准确测定响应与恢复时间. 为解决上述难题,基于真空和自动化控制技术研发了一套高精度、多功能气体传感器自动化测试系统. 本文介绍了该系统的工作原理及软硬件配置,探讨了动态及静态测量模式的利弊,并结合测试实例展示了部分系统功能.
1 测试系统设计与实现
1.1 系统结构
图1是测试系统的结构框图. 系统主管路为6.35 mm不锈钢管, 其上的箭头表示气体流动方向,内含数字的圆为真空两通电磁阀,P和H分别代表气压和湿度传感器,所有测试腔体均为真空标准件. 在典型测试过程中,目标气体和载流气体经质量流量计(MFC)和阀门后到达气体混合腔,被配制成特定体积分数的样气后进入测试腔体,样品的电学和光学响应被同步测量并记录. LabVIEW程序通过温度、湿度、气压传感器实时监控各腔体状态,并且控制MFC、阀门及加热器以实现自动化测试. 系统采用模块化设计且主要软/硬件均符合国际通用标准,可以依据测试需求灵活改动.
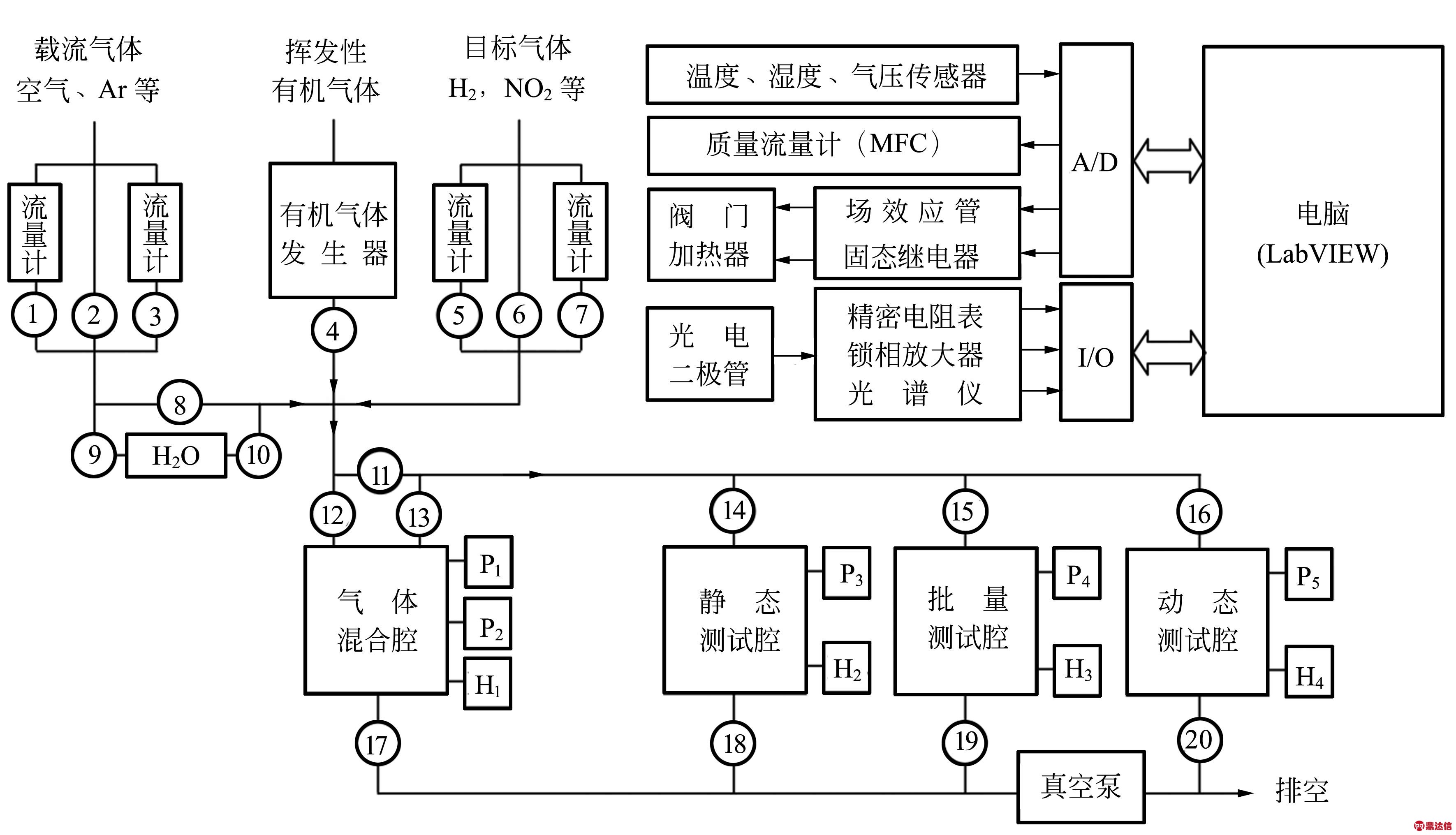
图1 气体传感器测试系统结构框图
1.2 系统硬件
对于空气、氩气等载流气体以及氢气、二氧化氮等常规目标气体,系统采用瓶装气源. 对于甲醛、甲苯等挥发性有机气体(VOCs),以有机气体发生器为气源(Owlstone,V-OVG). 气体发生器通过加热装载有固态或液态有机原料(如多聚甲醛或苯)的密闭渗透管产生VOCs气体,通过控制加热温度和载流气体流量实现对VOCs气体体积分数的调节. 采用有机气体发生器提高了系统的VOCs气体配制精度和自动化程度. 载流气路和目标气路各配置了2个不同量程的MFC(Bronkhorst,F-201CB),载流气路为2 000 cm3/min和200 cm3/min,目标气路为200 cm3/min和20 cm3/min. 这一组合在保障配气精度的前提下扩大了体积分数可调范围.
气体混合腔体是内径200 mm、高100 mm的圆柱形不锈钢腔体,两端配有ISO200真空法兰. 为保障气压测试精度,系统配置了2种不同量程的绝对压力传感器. P1为电容型(Setra,730G-010T,量程0~1 333 Pa),P2~P5为MEMS型(Setra,5350-S,量程0~1.6×105 Pa). 采用绝对压力传感器可保证气压测量不受气体种类影响. H1~H4是相对湿度传感器(Honeywell,HIH-4000),用于监控各腔体内的相对湿度.
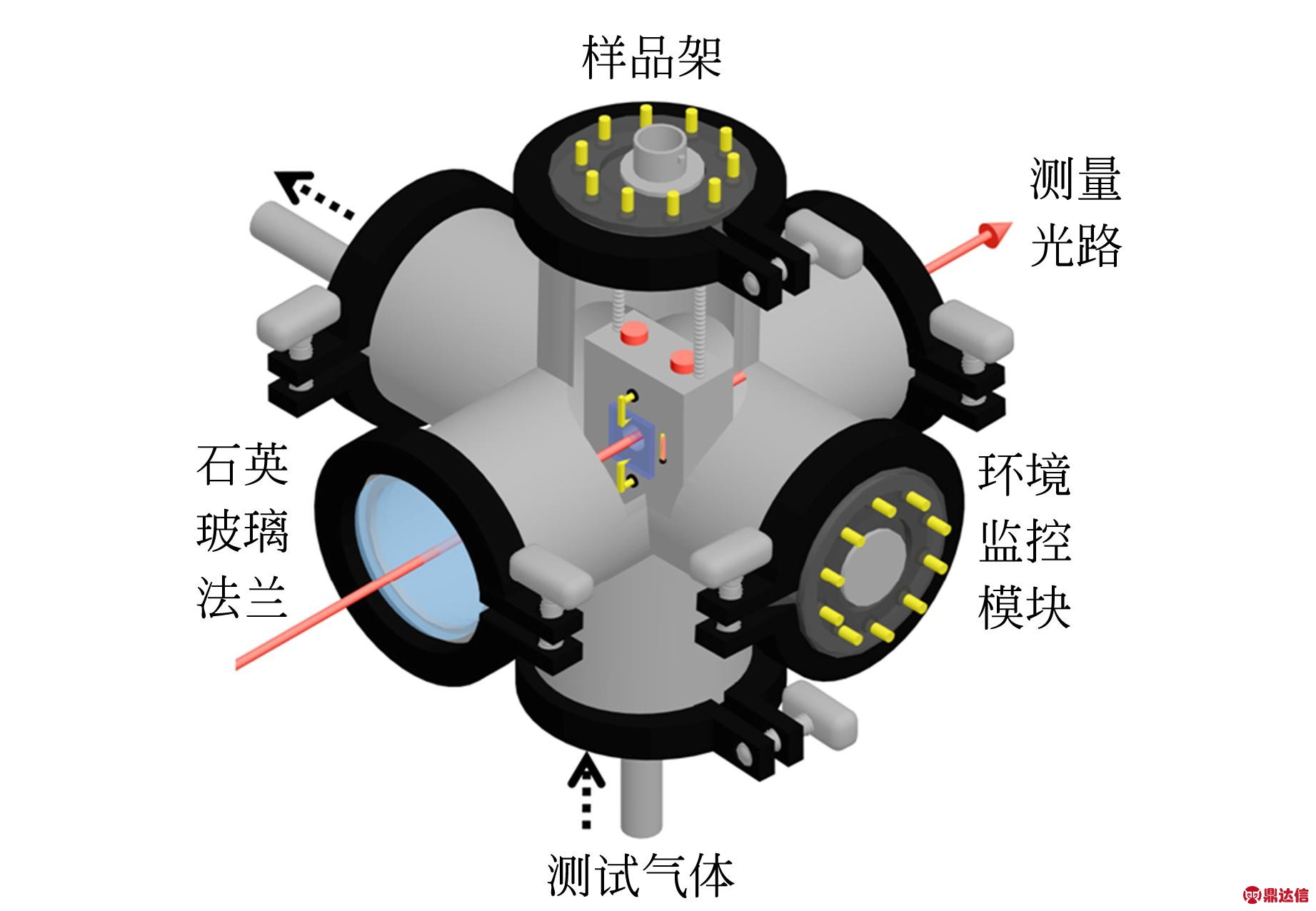
(a)KF40不锈钢六通静态测试腔
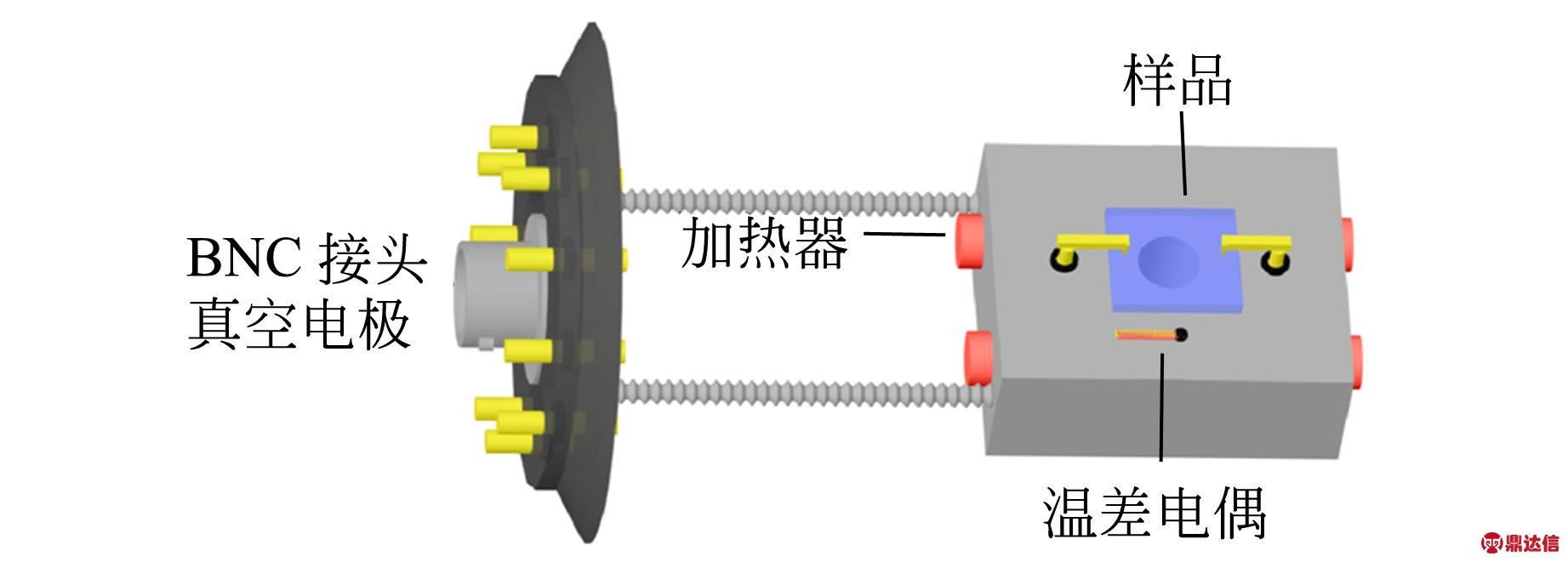
(b)样品架
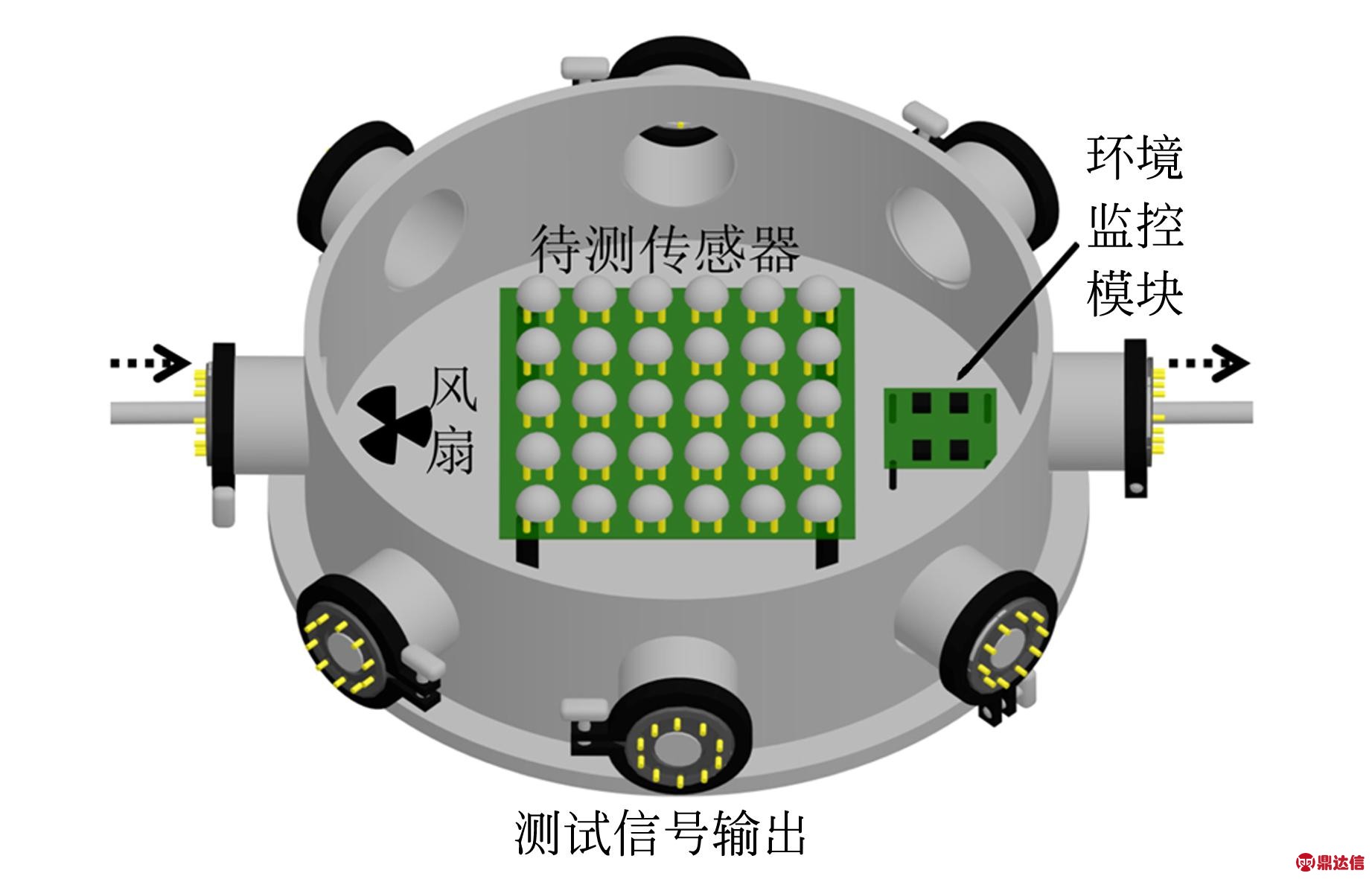
(c)不锈钢批量测试腔
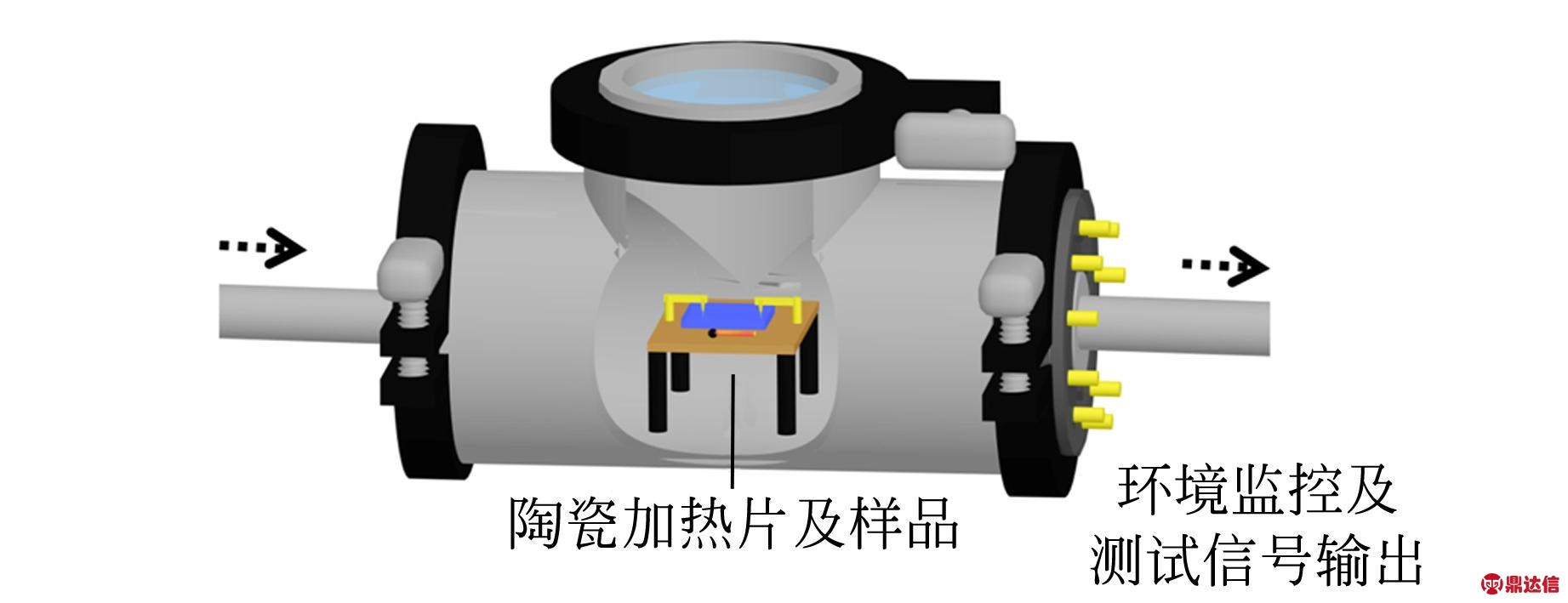
(d)KF40不锈钢三通动态测试腔
图2 测试腔体组件的三维结构图
系统配置了3个测试腔体以满足不同测试需求. 静态测试腔[图2(a)]是KF40不锈钢六通,主要用于静态测量模式. 其顶部为样品架安装位置,底部和左部为进/出气口. 右侧为真空电极法兰,内接气压和温/湿度传感器以监控腔内环境变化. 前后均装配熔融石英法兰,可测量样品透过率. 图2(b)是样品架的三维示意图,其顶部为改装的KF40盲板法兰,配有橡胶圈密封的BNC接头及真空电极. 样品架为不锈钢材质,耐高温,耐腐蚀. 样品台内嵌2个子弹型加热器(Omega,CSH-102150),最高加热温度为500 ℃. 样品旁配有温差电偶,用于实时监控样品温度. 测试探针通过BNC接头连接至Keithley 6517B高阻表以测量样品电学参量.
批量测试腔[图2(c)]是内径为250 mm、高为150 mm的不锈钢腔体,两端为ISO250真空法兰,侧壁焊接8个KF40真空电极法兰,用于测量信号输出. 进气口内侧配有风扇,以提高腔内气氛均匀度. 待测传感器安装在中心的PCB测试板上,右侧配有温度、湿度和气压传感器. 动态测试腔[图2(d)]为KF40不锈钢三通,顶部为熔融石英法兰,用于观察样品并提供光辐照. 左右两侧法兰分别为进出气口,右侧法兰还配有真空电极以输出样品及环境传感器的电学信号. 受腔体内部空间限制,其内配置直径25 mm的薄片型陶瓷加热器.
1.3 自动化控制
系统所有测试操作均由LabVIEW软件控制完成. 在软件中输入目标气体体积分数设定值后,系统自动将其转换成MFC的设定值(动态测量模式)或气体混合腔内气压设定值(静态测量模式). 各腔体内的气压、温度、湿度传感器的探测信号经模拟/数字信号(A/D)转换模块(NI,USB 6343)输入电脑. LabVIEW软件实时对比气压传感器的实际值与设定值,并通过A/D转换模块控制MFC及阀门以完成测试操作. MFC由A/D模块的模拟输出信号控制,而阀门则通过数字输出功能控制场效应管作为开关来控制. NI USB 6343 A/D转换模块具有32路模拟输入、4路模拟输出及48路数字输入/出,可以监控16个传感器,控制4个MFC及48个阀门. 样品的电学和光学参量分别由Keithley 6517B高阻表和光电二极管及配套锁相放大器或光谱仪实时测量并被LabVIEW程序记录.
2 高精度静态测量模式
系统具有动态与静态2种测量模式. 在动态测量模式下,目标气体和载流气体经MFC和阀门后直接到达动态测试腔. 目标气体体积分数由载流和目标气路的流量比决定. 该模式操作简单,流速可调且与静态模式相比更接近实际使用环境,是普遍采用的测量模式. 但是,该模式的目标气体体积分数可调范围有限,不利于痕量气体的配制,且测试腔内气氛更替耗时较长,降低了响应和恢复时间的精确测量. 为解决上述问题,利用该系统与真空兼容的优点发展了独特的静态测量模式,其基本操作步骤如下:
1)开启阀门17,真空泵对气体混合腔抽气,当腔体气压小于10 Pa时关闭阀门17.
2)开启目标气路MFC、阀门5或7及阀门12向气体混合腔内充入目标气体. 绝对压力传感器P1和P2实时监测腔内气压,当目标气体分压达到设定值时,关闭MFC及所有阀门.
3)开启载流气路MFC、阀门1或3及阀门8和12向气体混合腔内充入载流气体. 混合气体的相对湿度由H1监测并由阀门8~10的相对开启时间及含水腔体的加热温度控制. 当载流气体分压达到设定值时,关闭MFC及所有阀门,样气配制完毕.
4)开启阀门18,真空泵对静态测试腔抽气,当腔体气压小于10 Pa时关闭阀门.
5)阀门13和14同时开启,样气以自由膨胀的形式由混合腔向静态测试腔扩散,当气压达到平衡时关闭阀门.
6)样品与气体反应,其电学或光学参量被实时测量并记录. 与此同时,重复1)~3)步,开始下一周期的样气配制.
与动态模式相比,静态模式在以下3方面具有更高精度:
1)样气配制. 在动态模式下,当载流气路MFC为最大流量2 000 cm3/min,目标气路MFC为最小流量20×2%=0.4 cm3/min时,可将目标气体稀释2 000/0.4=5 000倍. 而在静态模式下,系统先将少量目标气体以最小流速0.4 cm3/min通入混合腔. 若可稳定重复的最短阀门开启时间为10 s,则最小目标气体通量为0.067 cm3(标准状态). 而气体混合腔和静态测试腔的总容积为3 400 cm3,当通入载流气体且混合腔和静态测试腔压强均为105 Pa时,目标气体可被稀释3 400/0.067=51 000倍. 因此,静态测量模式的目标气体体积分数控制精度提高了10倍以上.
2) 响应与恢复时间测量. 当测试腔内气氛置换时间短于传感器和气体的反应时间时方能准确测定响应和恢复时间. 图3对比了动态和静态测量模式下,超声膨胀纳米团簇束流沉积技术(SCBD)制备的WO3薄膜在Pd催化下(Pd/WO3)对氢气体积分数为2%的氢气/空气混合气体的电阻响应曲线. 动态模式下测试腔内气氛更替依赖缓慢的气体置换. 因此薄膜电阻响应达到饱和所需时间较长,不利于响应和恢复时间的准确测量. 而在静态模式下,测试腔更换气氛时总是先被抽成真空,随后气体由混合腔以自由膨胀的形式向测试腔内扩散并迅速达到平衡. 因此薄膜电阻响应在该模式下达到饱和所需时间更短,响应与恢复时间测量结果更准确.
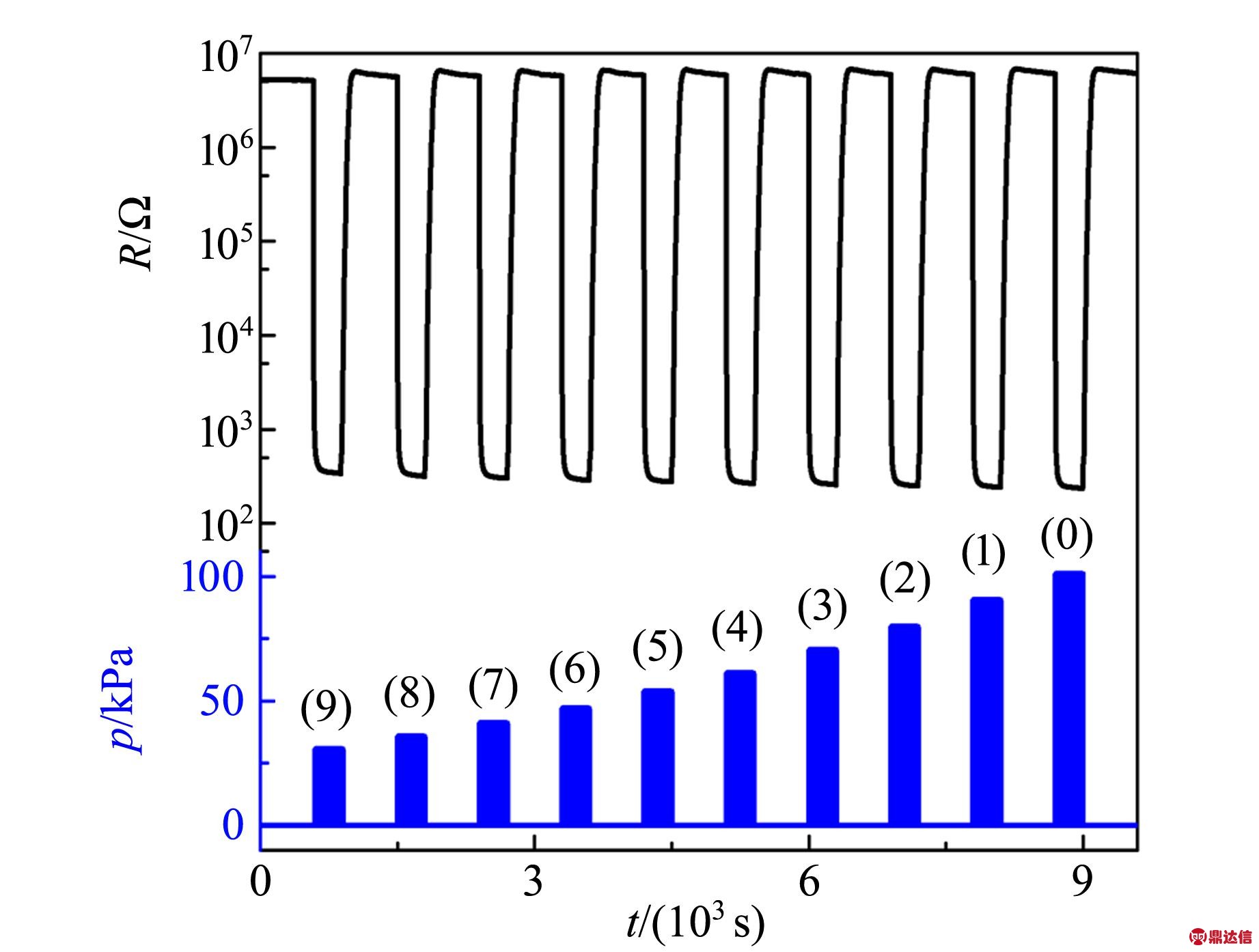
图3 Pd/WO3薄膜在动态与静态测量模式下氢气体积分数为2%的氢气/空气混合气体的电阻响应曲线
3) 测试气压控制. 在动态模式下,测试腔体与外界连通,即使在腔体末端加配气压控制阀门也难以精确调控腔内气压. 而静态模式下测试腔体与外部隔绝,在传感器反馈控制下测试腔内气压可在10~1.2×105 Pa的范围内精确控制,能模拟不同海拔或反应器等特种环境. 但是,密闭的测试腔体也给静态模式带来弊端,如二氧化碳、氯气等高密度气体倾向于沉降在测试腔体底部,进而影响测量精度. 研究结果表明:对于高密度气体,当体积分数低于0.01%且测量时间小于1 h时可使用静态模式. 这一测试条件可以满足二氧化氮、二氧化硫、砷烷等剧毒高密度气体的常规测试要求. 高于此体积分数则建议使用动态测量模式.
3 测试结果与讨论
3.1 气敏材料的光-电敏感性能同步测试
得益于独特的静态测试腔设计,系统可同步测量气敏材料的光学和电学响应,有助于研究特定材料的气敏机理及开发新型气体传感器. 例如,现有文献对WO3氢敏机理是表面吸附反应[7]还是体反应[8]存在分歧. 本文同时测量了磁控溅射Pd/WO3薄膜对氢气体积分数为4%的氢气/氩气混合气体的电阻和透过率响应. 如图4所示,通入氢气1 s内Pd/WO3薄膜的电阻从~1011 Ω降低到~108 Ω,随后电阻变化趋缓,60 s后电阻再次发生突降. 与此同时,薄膜透过率在最初的60 s内由88%缓慢降低至86%,随后与电阻同步发生突降. 上述结果表明:Pd/WO3薄膜与氢气的反应至少存在2个过程. 我们认为这分别对应于表面吸附反应和体反应[9],具体反应机理有待进一步研究. 此外,灵敏度测试结果表明Pd/WO3薄膜的电阻响应信号在氢体积分数为0.15%时就趋于饱和,但响应时间较短(<1 s),而其透过率响应对体积分数高达4%的氢气都不会饱和,但响应速率较慢. 基于电学和光学响应的互补特性可研发新型光电耦合传感器,以获得更好的氢气检测效果.
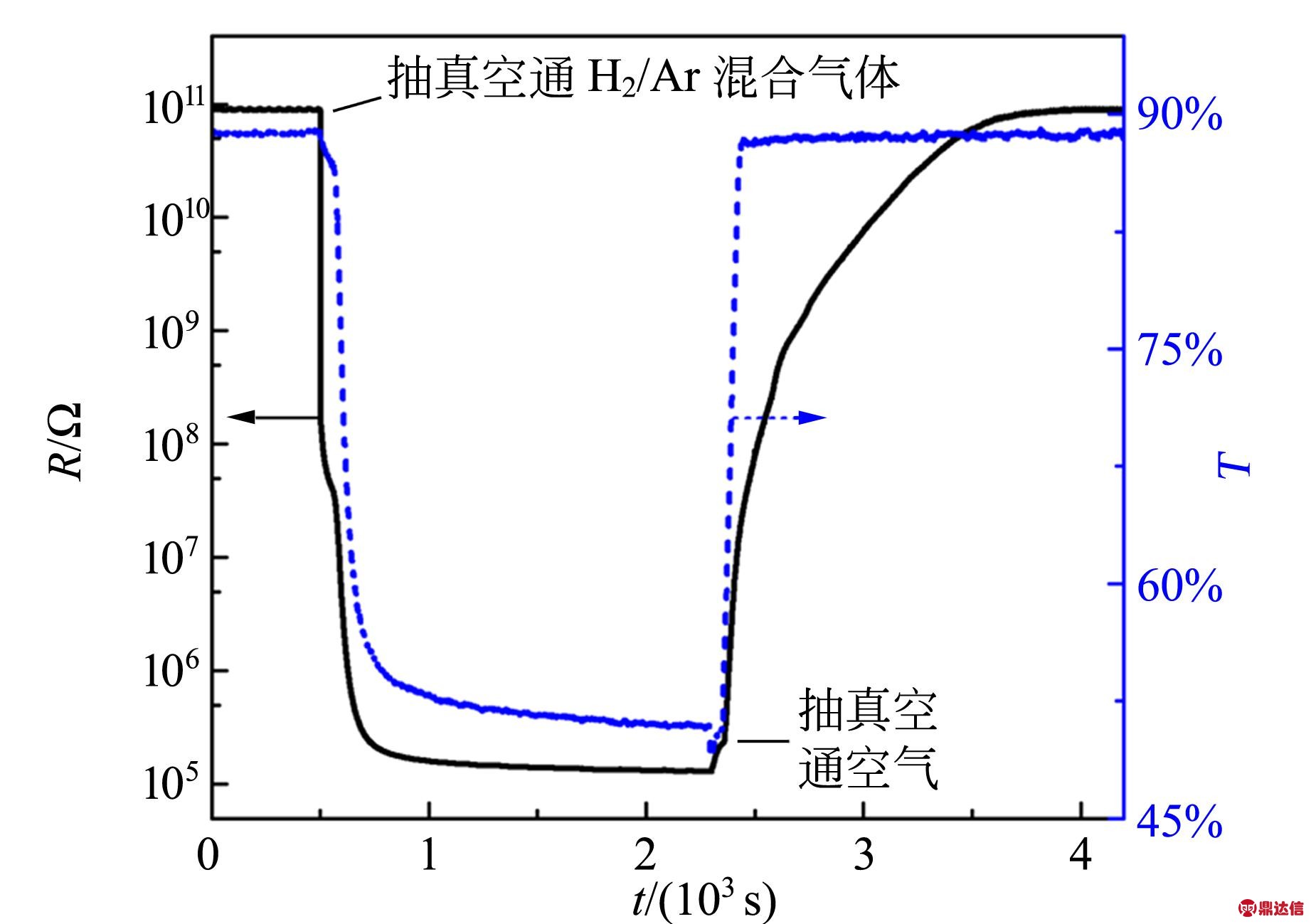
图4 Pd/WO3薄膜的电阻和透过率(λ=633 nm)对氢气体积分数为4%的氢气/氩气混合气体的响应曲线
3.2 测试系统的环境控制能力
除温度、湿度等常规环境参量外,测试系统还能精确控制环境气压. 这一优势可用于模拟不同海拔高度或反应器等特殊应用环境,有重要实际意义. 图5是SCBD方法制备的Pd/WO3薄膜对压强为30~101 kPa 氢气体积分数为2%的氢气/空气混合气体的电阻响应曲线,图中括号内数值为相应海拔高度(km). 如图5所示,该薄膜对环境气压不敏感,可在30~101 kPa的气压范围内稳定工作.
测试腔体还配置了熔融石英法兰以引入不同光源用于光辅助气敏响应研究[10]. 图6是SCBD方法制备的ZnO薄膜在365 nm紫外光辐照下对甲醛的电流响应曲线. 没有紫外光辐照时,该薄膜对甲醛几乎没有响应(结果未显示). 在紫外光辐照下,该薄膜对甲醛体积分数为0.004%和0.008%的甲醛/空气混合气体的响应电流分别增大了9.25倍和13.6倍,表现出了较好的甲醛探测能力.
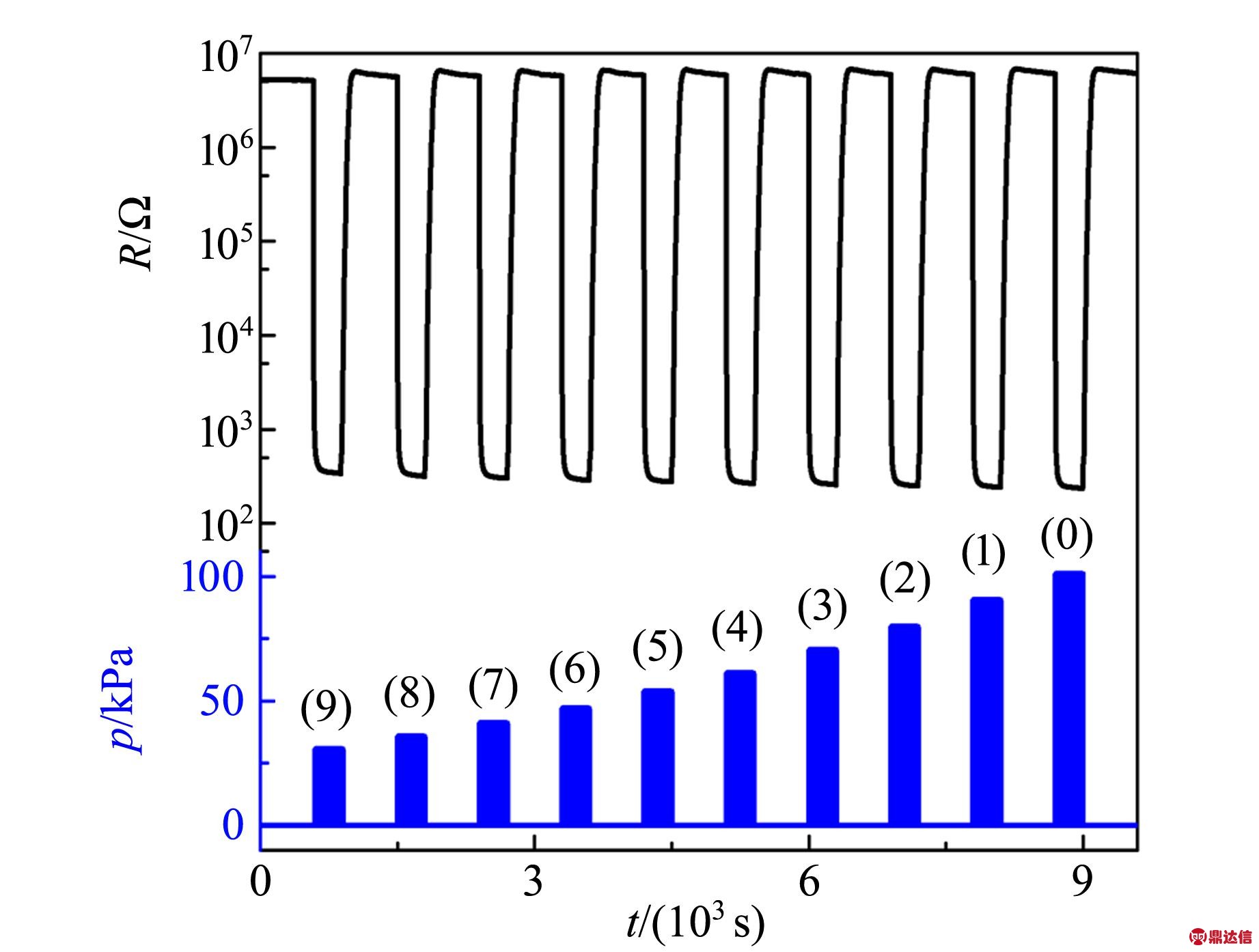
图5 Pd/WO3薄膜对压强30~101 kPa 氢气体积分数为2%的氢气/空气混合气体的电阻响应曲线
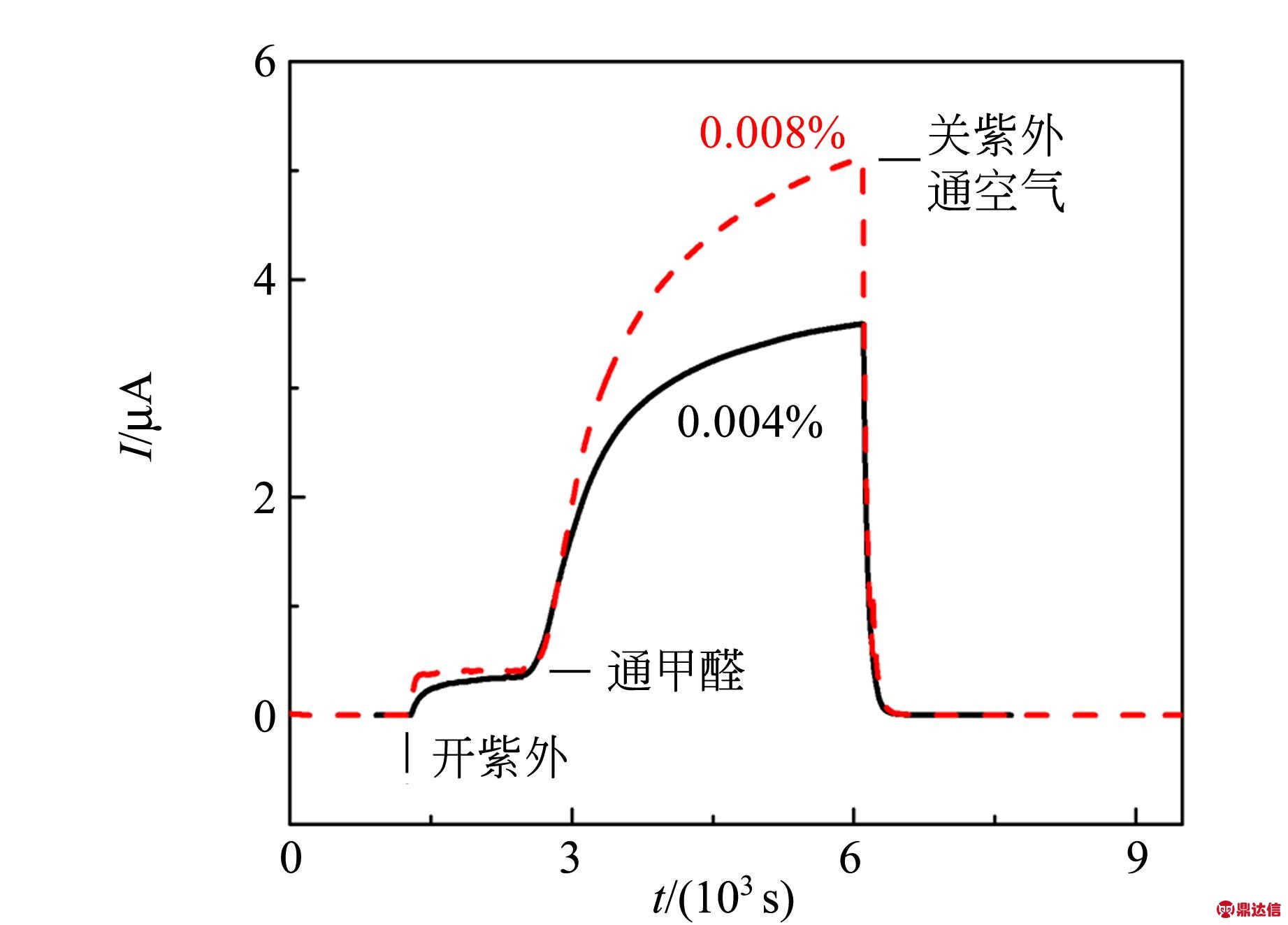
图6 Pd/ZnO薄膜在365 nm紫外光辐照下甲醛体积分数为0.004%和0.008%的甲醛/空气混合气体的电流响应曲线
3.3 传感器稳定性测试
金属氧化物气体传感器的稳定性问题是科研成果转化必须攻克的难题. 但是由于稳定性研究费时费力,现有研究较少涉及[10]. 文献报道的稳定性研究通常将传感器置于工作状态并且以一定的时间间隔对其进行测试. 本系统的批量测试腔体就是为了开展此类测试而设计的. 此外,课题组还 开展了Pd/WO3薄膜的加速稳定性测试,所用气体为氢气/空气混合气体. 在图7(a)的测试中氢体积分数固定在2%,以观察样品在高频响应状态下的稳定性. 在图7(b)的测试中,氢气体积分数在0.02%,0.2%和2%之间循环,以表征传感器对不同体积分数氢气的响应重复性.
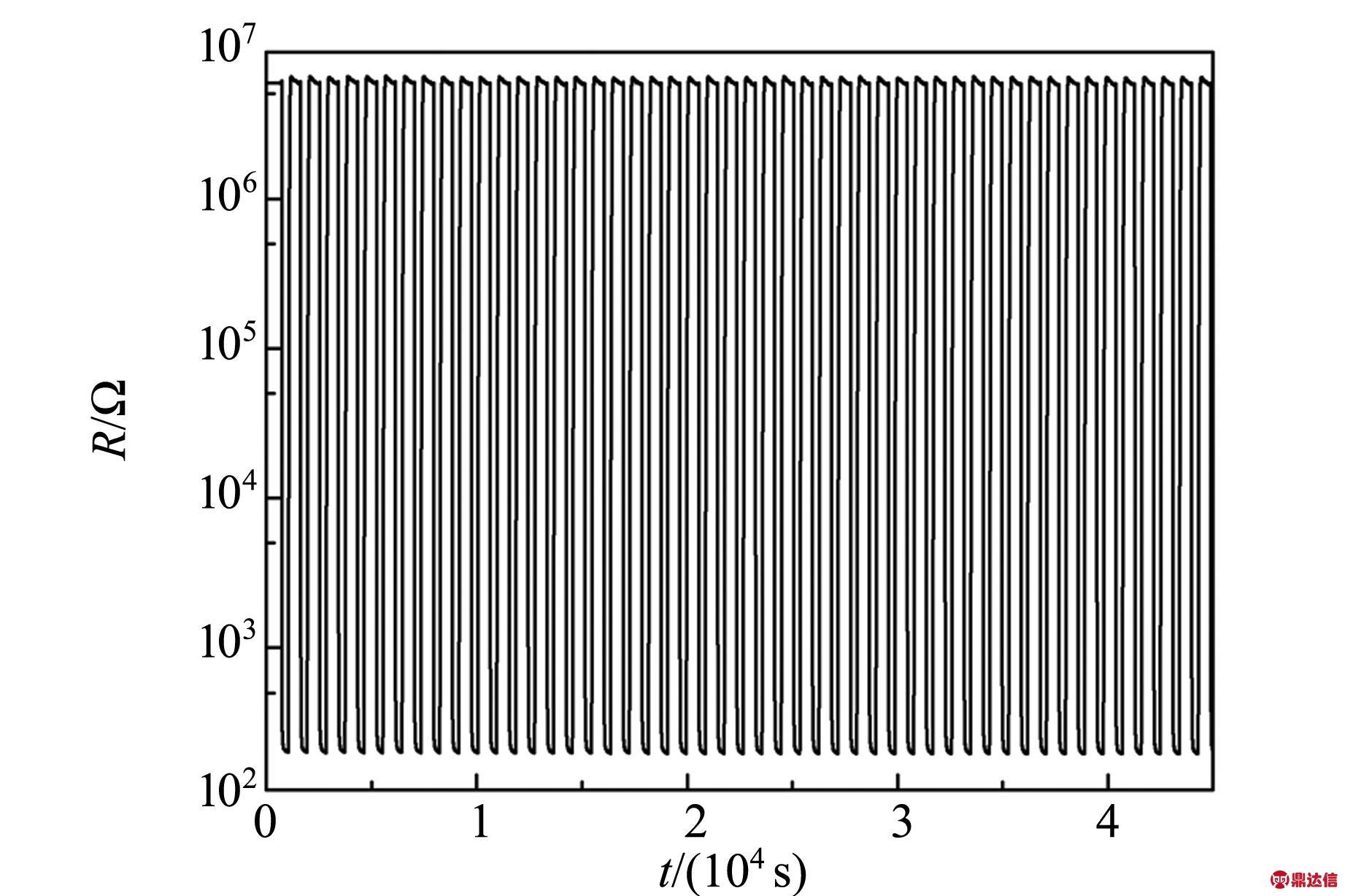
(a)氢气体积分数固定在2%
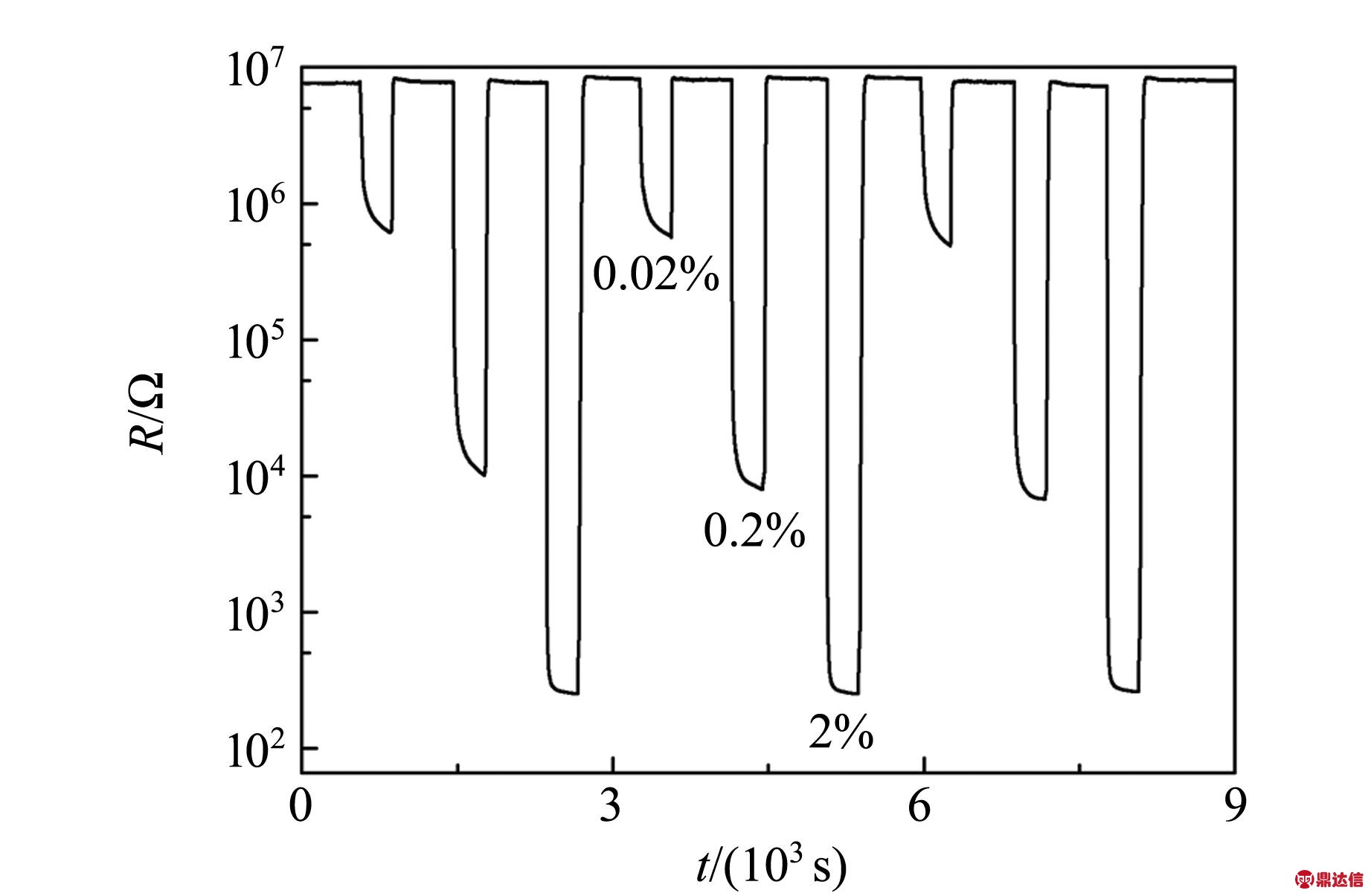
(b) 氢气体积分数在0.02%,0.2%和2%之间循环
图7 Pd/WO3薄膜氢敏性能的加速稳定性测试
4 结 论
基于真空和自动化控制技术设计并组建了气体传感器测试系统,利用系统与真空兼容的特点发展了高精度静态测量模式. 该模式的样气配制精度比动态测量模式提高了10倍,且响应与恢复时间测量及环境气压控制都更精确. 独特的测试腔体设计使得系统可同步测量气敏材料的光电响应随气体体积分数、工作温度、环境湿度、压力、光照等参量的变化. 自动化的测试过程也有利于开展气体传感器的长期稳定性测试. 系统采用模块化设计且由标准真空部件搭建而成,可以满足多样化的测试需求,为发展通用的测试系统提供了参考.