摘 要:以优化真空断路器传动尺寸链设计,提高产品性能和降低尺寸管理成本为目的,介绍了一种基于Tolerance Manager(以下简称TM)和SolidWorks软件的新型先进设计技术,提出了功能条件、功能尺寸和功能尺寸的权重及敏感度等概念,通过设定断路器的行程为功能条件,根据传动结构中各零件的接触关系,确定功能尺寸。给出了在SolidWorks软件中构建机构简图、在TM软件中提取并调整非线性尺寸链的方法,结合TM软件的规则,实现了应用TM软件分析、进行功能设计的先进方法。该方法以尺寸链理论为基础,以统计分布法为原理,避免了传统公差设计中查手册、周期长的缺陷,不仅使零件标注更切合实际加工工艺,同时使检测过程得到简化,有效降低了零件的不合格率和尺寸管理成本。
关键词:功能设计;真空断路器;传动机构;尺寸链
真空断路器是输配电系统中的重要保护部件,其性能的优劣直接影响到整个电力系统的可靠性和安全性[1],因此,研究如何提高断路器的性能具有重要的实际应用意义。对于真空断路器而言,决定其性能最重要的指标是断路器触头的运动特性,即分闸运动速度特性和合闸运动速度特性。它们是满足断路器开断和关合性能的重要保证。而真空断路器触头的运动特性又是由操动机构和传动结构决定的[2],因此,操动机构和传动结构的关键尺寸和公差设计就显得尤为关键。
本文介绍的功能设计方法使用TM和SolidWorks软件做为公差设计与优化的重要工具,对产品功能和制造可变性进行模拟,在满足产品功能的前提下,尽可能用大的公差带去降低制造成本。在项目早期运用功能设计方法,能有效避免产品在大批量生产阶段出现装配缺陷及功能缺陷,为企业赢得时间和节省项目费用。
1 功能设计方法介绍
产品在装配过程中会受到重力、内力(如弹簧、紧固连接的压紧力等)的作用。在各种力的作用下,零件不可能停留在理想状态(如零件悬空装配、不与其他零件接触)。任何零件在装配形成产品后,都应与周围的1个或多个零件接触,形成稳定的、功能上需要的接触关系,从而处于一个平衡状态,因此,产品装配完成后,各个零件的位置由零件本身的结构特征、特征上的尺寸名义值、尺寸公差带及尺寸的几何公差决定,而与装配顺序无关。功能设计方法是在尺寸链的基础上,根据零件的接触关系构造线性尺寸链或者非线性尺寸链,并以TM软件为工具对产品的尺寸链进行分析。
1.1 功能设计方法的基本参数
1)功能条件(Functional Condition,FC)。其与传统尺寸链计算的封闭环的概念类似,但是在传统的尺寸链计算理论中,封闭环往往是一个物理距离或角度[3],而功能条件则包括的范围更大,它可以是产品在特定状态下两两零件间的关系,如接触压力、搭接量和轴孔配合间隙(见图1)均可作为产品的功能条件;同时,也可以是其他可量化、可测量的物理量,如速度、电流等。
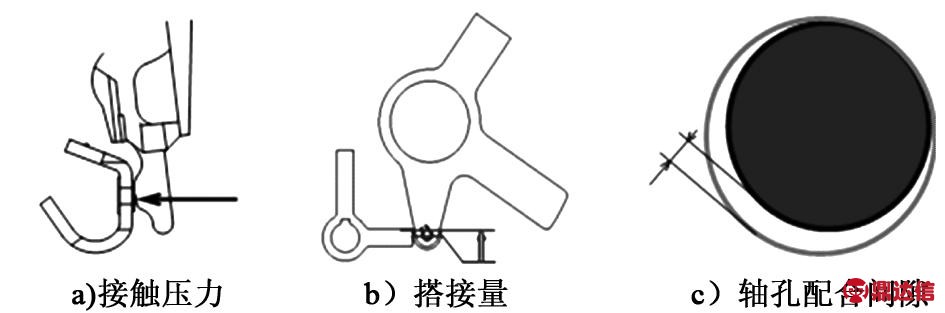
图1 不同情况的功能条件
产品在完成装配后,就具有了自身特定的功能。而要满足产品的不同功能,应控制产品不同的功能条件。用螺栓将零件1和零件2紧固在一起的装配如图2所示。根据装配要求,需要控制的FC共有4个:a.FC1为装配间隙要求,保证螺栓顺利装入;b.FC2为保证零件1和零件2能够被压紧的功能条件;c.FC3为安全要求,确保压紧后,在外界条件(如震动)的作用下,螺栓不会松动;d.FC4保证零件1和螺栓台阶可靠定位,防止螺栓头部陷入零件1内。
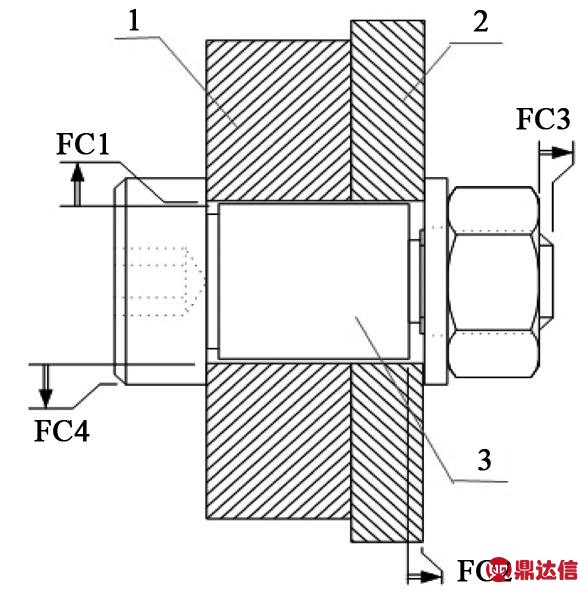
图2 零件紧固装配
2)功能尺寸(Functional Dimension,FD)。其是同一个零件上接触特征到接触特征之间的尺寸。它与传统尺寸链中组成环的概念类似。功能尺寸来自尺寸链的计算,是产品功能条件的变量。
功能尺寸是在单个零件上的实现产品功能的尺寸,是设计中需要找到、分析和控制的尺寸。它通过对产品的功能条件造成影响,从而影响到产品的质量和性能,同时对产品的成本也有较大影响,功能尺寸越多,零件的制造、控制和测量等成本就越高。功能尺寸应根据产品装配后的功能条件进行确定,如根据图2中的功能条件确定出螺栓的功能尺寸(见图3)。图3中尺寸φ25、φ20、21和36分别是根据功能条件FC4、FC1、FC2和FC3进行确定的。
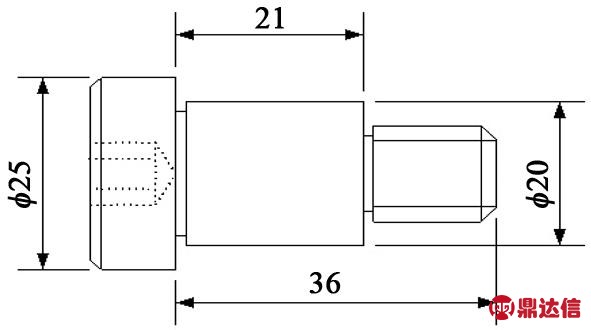
图3 螺栓的功能尺寸
3)敏感度(Sensitivity)。其也称影响系数或偏导数,传统尺寸链计算理论称为误差传递比,表征功能尺寸的变化对给定的功能条件的影响。敏感度有正有负。
敏感度Sen的计算公式为:

式中,FC是功能条件;xi是功能尺寸。
4)权重(Weight)。其是指功能尺寸的变化范围在整个功能条件限制范围中的影响,用来表征功能尺寸的重要性。其计算公式如下:
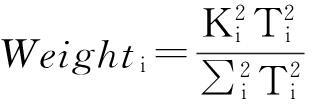
式中,Ki是功能尺寸敏感度;Ti是功能尺寸公差带宽度。
1.2 构造尺寸链的几何形式
功能设计方法中的尺寸链和传统尺寸链一样是一个矢量环。在尺寸链里,功能尺寸和功能条件都当作矢量处理,有大小和方向。根据尺寸链相关的功能条件及功能尺寸的关系,尺寸链可分为线性尺寸链与非线性尺寸链。
1)线性尺寸链。其是指功能条件和功能尺寸之间的关系是线性的。和传统尺寸链一样,功能尺寸也分为增环和减环,其含义同传统尺寸链。通过零件间接触关系可构造出线性尺寸链。构造方法如下:a.根据零件的接触特征,如轴孔、平面和圆弧等,识别零件的接触区域;b.从功能条件FC的起点开始画第1个功能尺寸FD,方向指向零件自身的接触面;c.依次画出所有的功能尺寸,注意功能尺寸的矢量是同一个零件上接触特征到接触特征间的尺寸;d.尺寸链上最后一个尺寸指向功能条件的终点,所有功能尺寸和功能条件形成一个最短的闭环。
根据上述方法,可以确定功能条件和功能尺寸(见图4),并列出尺寸链方程如下:
J1=L01A-L01B-L01C

图4 线性尺寸链几何形式
用这种靠接触关系确定功能尺寸的方法,能确保不同的人针对同一个装配和功能条件,构造出相同个数和位置的功能尺寸,构造出的尺寸链方程也必然是唯一的。
2)非线性尺寸链。其较为复杂一些,但仍可通过零件间的接触关系构造出尺寸链,方法如下:a.找出机构的平衡状态,或者某一个特定的状态,该状态下,每个零件在平衡力的作用下处于静止位置,注意不能是运动过程的中间状态;b.通过接触分析,确定和功能条件相关的零件和功能尺寸;c.将和功能条件相关的零件用基本要素的形式描绘出必要的形状;d.列出简化假设(如是否考虑配合间隙、零件受力变形及几何公差等因素);e.在机械接触特性分析之后,识别特殊点(如轴孔配合时,轴和孔必有一个共同接触的点、圆弧和平面相切时的切点等);f.写下几何学上定义特殊点的尺寸,每个尺寸应与零件上的几何学规范相关联,能在图样中正确地表达出来;g.应用几何构造原理等知识构造出尺寸链方程。
根据上述方法,可以确定功能条件和功能尺寸(见图5),并列出尺寸链方程(此处假设为理想模型,即不考虑轴孔配合间隙、所有零件几何公差等因素)如下:

+L01P

图5 非线性尺寸链几何形式
1.3 尺寸链的分析
图5中的传动机构较为简单,功能条件只有一个,功能尺寸数量不多,因此,构造功能条件和功能尺寸的非线性尺寸链方程并不困难。对于集成程度高、结构复杂的产品,功能条件和功能尺寸的数量繁多,如断路器机构、工业机器人空间机构等,要推导出某个功能条件与其对应的功能尺寸的函数关系是比较困难的,不仅需要较长的时间,而且求解过程复杂,工作量巨大,容易出错。
运用TM软件可根据由功能条件和功能尺寸构成的尺寸链简图自动提取出尺寸链方程,并利用其独立的公差模拟及优化界面进行计算。通过分析每个尺寸的权重和敏感度等,很容易判定每个尺寸在尺寸链中的作用,并根据计算输出的功能条件结果,找出整个传动链中尺寸和公差不合理的地方,进行分析并优化,直至达到设计要求。
2 功能设计方法在真空断路器上的应用
2.1 功能条件(计算目标)的选择
产品的功能条件与产品的性能参数息息相关。断路器的分闸状态如图6a所示,合闸状态如图6b所示。在2种情况下,断路器各零部件均保持在平衡状态。S1和S2分别是断路器绝缘拉杆相对主轴的位移,两者的差是断路器动触头的行程,其大小关系到断路器的合闸和分闸特性,从而影响到断路器的开断性能和绝缘性能;因此,选择S0为断路器的功能条件,S0=S2-S1。
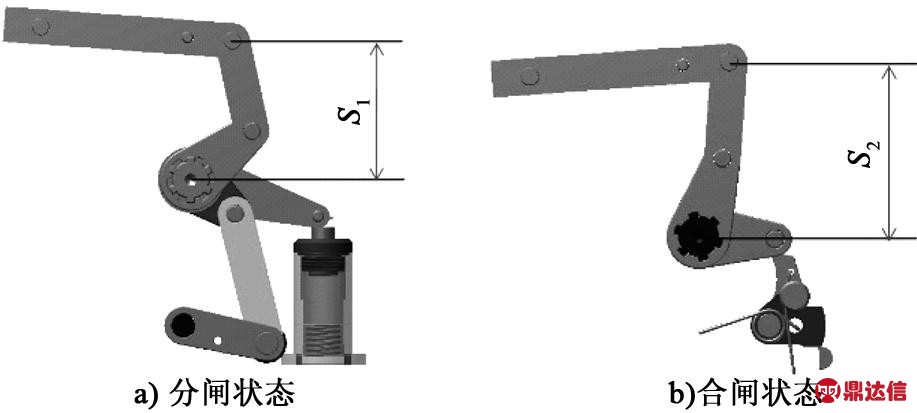
图6 功能条件示意图
2.2 建立尺寸链模型
机构进行非线性尺寸链分析的目标之一就是找到零件上对功能条件有影响的、符合图样表达标准的尺寸。这些尺寸就是零件上最重要的尺寸,即功能尺寸。按照上述介绍的接触关系确定功能尺寸,机构接触关系与SolidWorks软件草图图元之间按如下对应关系进行约束:轴孔配合→相同点;滑动配合→点在线上;平面接触→相同点;圆弧/平面接触→相切;圆弧/圆弧接触→相切;同一零件上相同特征的尺寸→等长;同一零件上相互平行的尺寸→平行;同一零件上相互垂直的尺寸→垂直。
最终确定出断路器合闸位置和分闸位置的尺寸链模型如图7、图8所示。
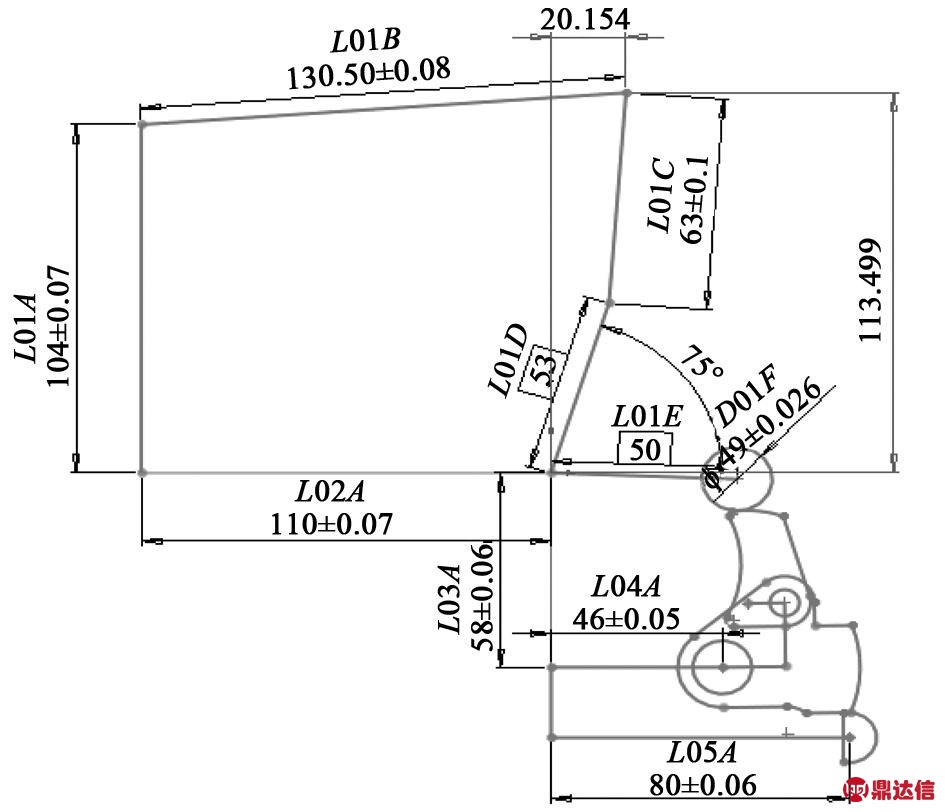
图7 合闸位置尺寸链模型
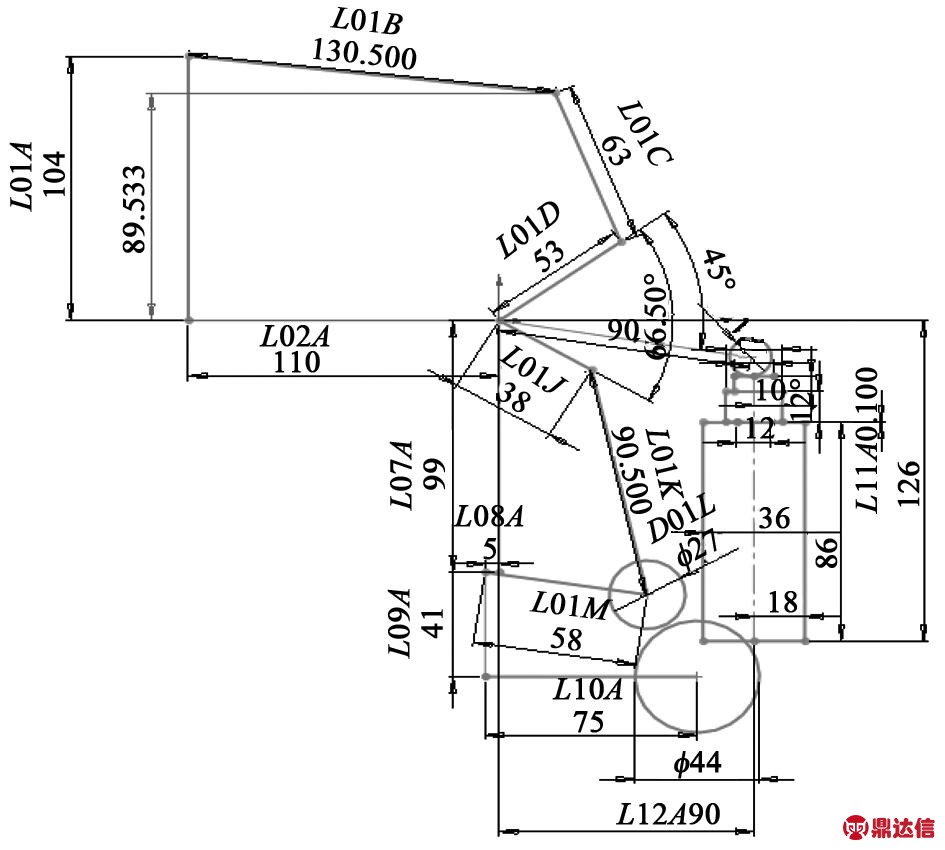
图8 分闸位置尺寸链模型
2.3 模型的计算及分析
尺寸链堆栈文件是在SolidWorks软件中,由TM软件的尺寸链计算器自动计算草图模型生成的,包含尺寸链所有的功能条件、功能尺寸及功能尺寸敏感度的数据包集合,是TM进行独立的公差管理的输入。
TM自动计算之后,输出功能条件的正态分布图,根据正态分布图和功能条件的要求,可判断出设计结果是否符合要求。功能条件的计算结果如图9所示。在图9中,横坐标代表功能尺寸的具体值,最上端为正态分布曲线形状,表示功能尺寸应遵循的规则。由上到下3个矩形分别代表计算结果的统计公差带、算术公差带和功能条件的统计公差带要求。由图9可以看出,设计要求的功能条件S0范围为23~27,计算结果的算术公差带范围为22.88~25.05,统计公差带范围为23.59~24.34。虽然统计公差带落在设计要求范围内,但数值基本在设计要求的下限,我们希望计算结果的中值落在设计要求的中值25左右,而计算结果的上限为24.34;因此,应对尺寸链进行优化。
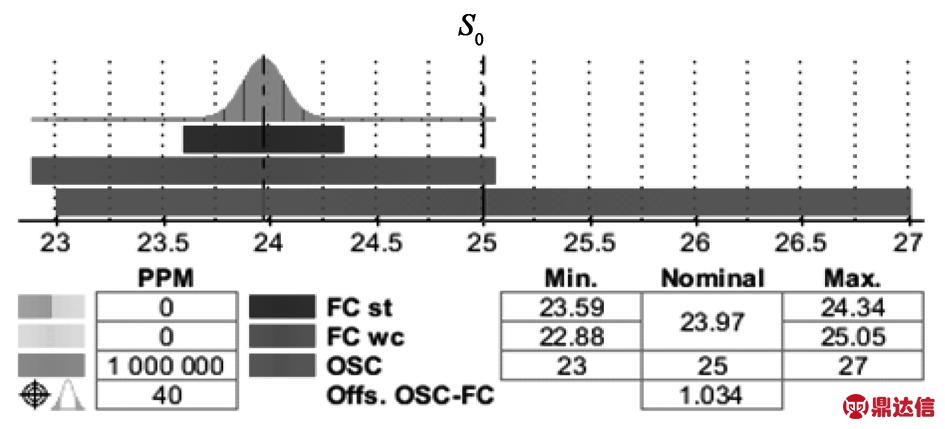
图9 功能条件计算结果分布图
2.4 功能尺寸的优化
功能尺寸优化的目的是使计算的功能条件结果满足设计要求的功能条件范围。改变功能尺寸的名义值可以使计算结果的名义值与功能条件要求的名义值对齐,这样可以使功能尺寸在满足功能要求的前提下,功能尺寸的公差带范围尽可能的大,从而可有效降低尺寸管理的成本。
调整功能尺寸的名义值,实际上在数学上就是计算方程的可行性,也就是对机构进行优化设计。
假设功能尺寸设为x1,x2,…xn,功能条件为y1,y2,…,yn;x1对y1,y2,…,yn的敏感度分别为kx1y1,kx1y2,…,kx1yn,xi对y1,y2,…,yn的敏感度分别为kxiy1,kxiy2,…,kxiyn,那么。
假设x1,x2,…,xn的调整量分别为Δ1,Δ2,…,Δn,进行尺寸链调整的实质就是寻找这些调整量的值,使得下列各式成立。


……

式中,是功能要求的名义值。
通过上述分析可以知道,在复杂的尺寸链项目中,一个尺寸可能对十几个功能条件都有影响,这样的尺寸就是“牵一发而动全身”的尺寸,调整尺寸名义值就变成一个多变量、多约束的复杂的数学优化问题。通常选择那些对功能条件影响个数少且敏感度大的功能尺寸进行调整。
在TM软件中,可利用Flags和Curve等2种简易方式来调整功能尺寸名义值。Flags是查看功能尺寸的敏感度及其与功能条件关系的工具,通过它可大致判断出需要优化的功能尺寸。功能条件S0的Flags标识结果如图10所示。由图10可知,最大的敏感度尺寸A02J对S0贡献最大,但是该尺寸为装配尺寸,不适合进行优化;而尺寸L01D在所有的功能尺寸里对S0的敏感度排在第2位,对S0影响最明显,故应首先考虑优化尺寸L01D。
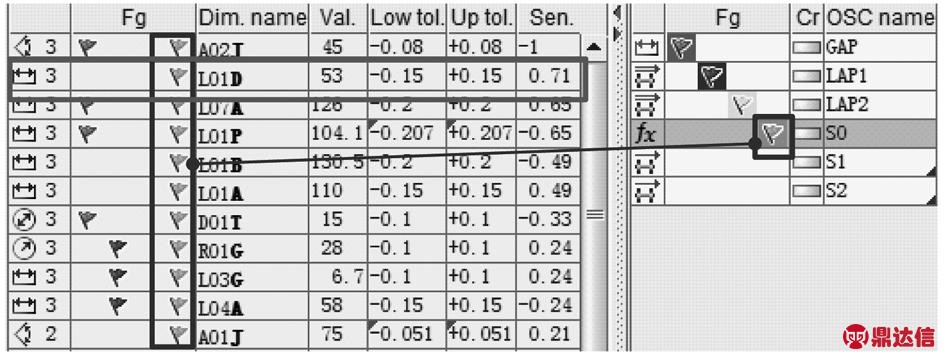
图10 功能条件S0的Flags标识结果
选择尺寸L01D对S0使用Curve工具,结果如图11所示。取L01D=54.4(优化前为53), 重新计算,得到的结果如图12所示。由图12可知,S0=24.97,与设计要求的中值25非常接近,可以满足要求。
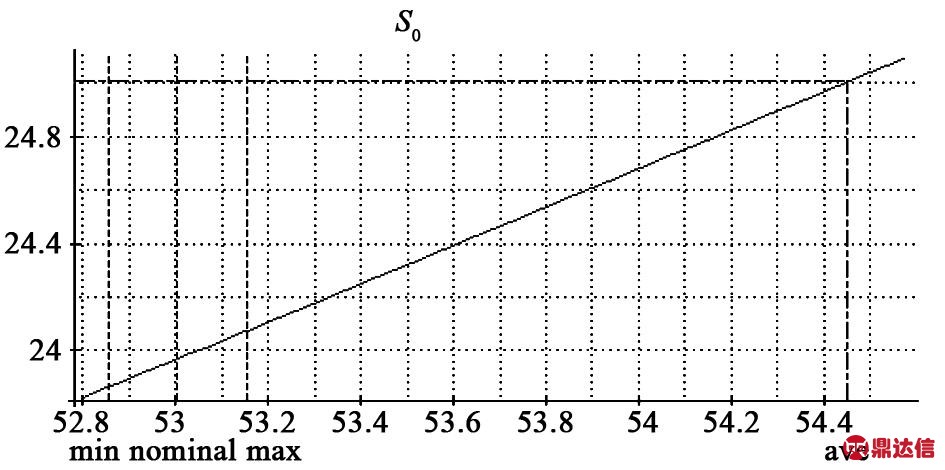
图11 尺寸L01D对S0的Curve结果
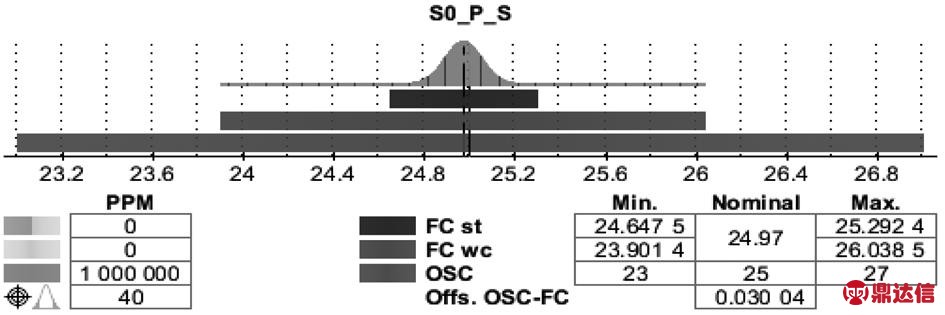
图12 优化后功能条件S0的计算结果
3 结语
尺寸链分析设计计算作为产品研究开发过程中非常重要的一个环节,将会朝着自动化程度更高、针对性更广和可靠性更高的方向发展。本文介绍的功能设计方法,运用零件的接触关系确定功能尺寸和功能条件,应用SolidWorks软件构造产品的尺寸链简图,并以TM软件为工具进行尺寸链的分析和优化。该方法以尺寸链理论为基础,以统计分布法为原理,避免了传统公差设计中查手册、周期长的缺陷,提供了一种新的公差设计在产品研发中的设计方法。