摘要:针对我国大型变压器叠片工艺效率低和叠片质量不稳定的情况,设计了一种自动叠片机器人,由机械系统、控制系统和料片运输系统组成。该机器人的机械手斜向吸盘可自动调整方向,以适应不同类型料片,设计的翘曲式风刀机构可解决薄片连片问题。采用视觉相机与光栅尺相结合的方法,能快速准确的测量铁芯整体垂直度以及窗宽,提高了叠片机器人的智能化水平,保证了叠片的质量。自动叠片机器人叠片速度可达23片/min,而人工叠片需要6个人,叠片速度为19片/min,数据表明叠片速度得到显著提高。
关键词:大型变压器;自动叠片机器人;视觉相机;智能测量
1 引言
变压器铁芯是变压器主要组成部分之一,起到限定主磁场闭合磁路的作用[1]。大型变压器铁芯通常由近万片硅钢片叠装而成,铁芯叠装工序不仅耗费大量的工时、人力,而且叠装质量会直接影响到变压器的铁损和噪音等性能指标,变压器铁芯的叠装效率和质量是决定变压器生产效率及其质量的重要因素[2]。
德国乔格已设计出用于叠片工艺的机器人,在叠片机器人的帮助下,变压器的生产进一步朝着低损耗、节约原材料和提高生产效率的方向发展;在我国,叠装工艺由人工完成,铁芯的叠装效率与叠装精度得不到保障,铁芯叠装工序已成为制约变压器生产效率及产品质量提高的瓶颈。
为了提高变压器叠片效率和叠片质量,设计了一种叠片机器人,在设计的过程中解决了连片分片、机械手适应多种片料与智能化测量铁芯整体垂直度与窗宽等技术难点。目前人工叠片需要6个人,叠片速度为19片/min,而叠片机器人的叠片速度可达23片/min;叠片机器人采用视觉技术进行实时检测,叠片质量明显优于人工叠片。叠片机器人达到了实际生产要求,具有较高的经济效益。
2 叠片机器人
2.1 叠片机器人的组成
自动叠片机器人为龙门直角坐标机器人,具有行程大、负载能力强、运行平稳、支撑刚性好的特点[3]。叠片机器人机械构成包括支柱、桥架、叠片机械臂、龙门机架、AGV以及翻转台五部分(见图1)。
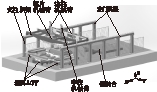
图1 大型变压器自动叠片机器人
龙门机架总长15000mm,由12根400mm×400mm的工字钢支柱支撑。桥架在龙门机架上的位移行程为8600mm,传动方式采用齿轮齿条直线运动单元,该直线单元可承受大负载,重复定位精度可达0.1mm。桥架的Y向横梁结构为等强度设计,在满足刚度要求的同时,有效节省了材料。边柱机械臂和中柱机械臂可沿桥架的Y方向做平移运动,轭片机械臂沿桥架的X方向做平移运动,四个机械臂的传动方式采用滚珠导向的同步带直线运动单元,最大运动速度可达5m/s,重复定位精度可达0.02mm[4]。桥架上安装了绝对式光栅尺,用以检测机械臂的实时位置。
2.2 叠片流程
叠片机器人的目的是将四组硅钢片叠成“E”形,每组包含约3000片硅钢片。四组硅钢片包括两组边柱,一组中柱和一组下轭(见图2)。
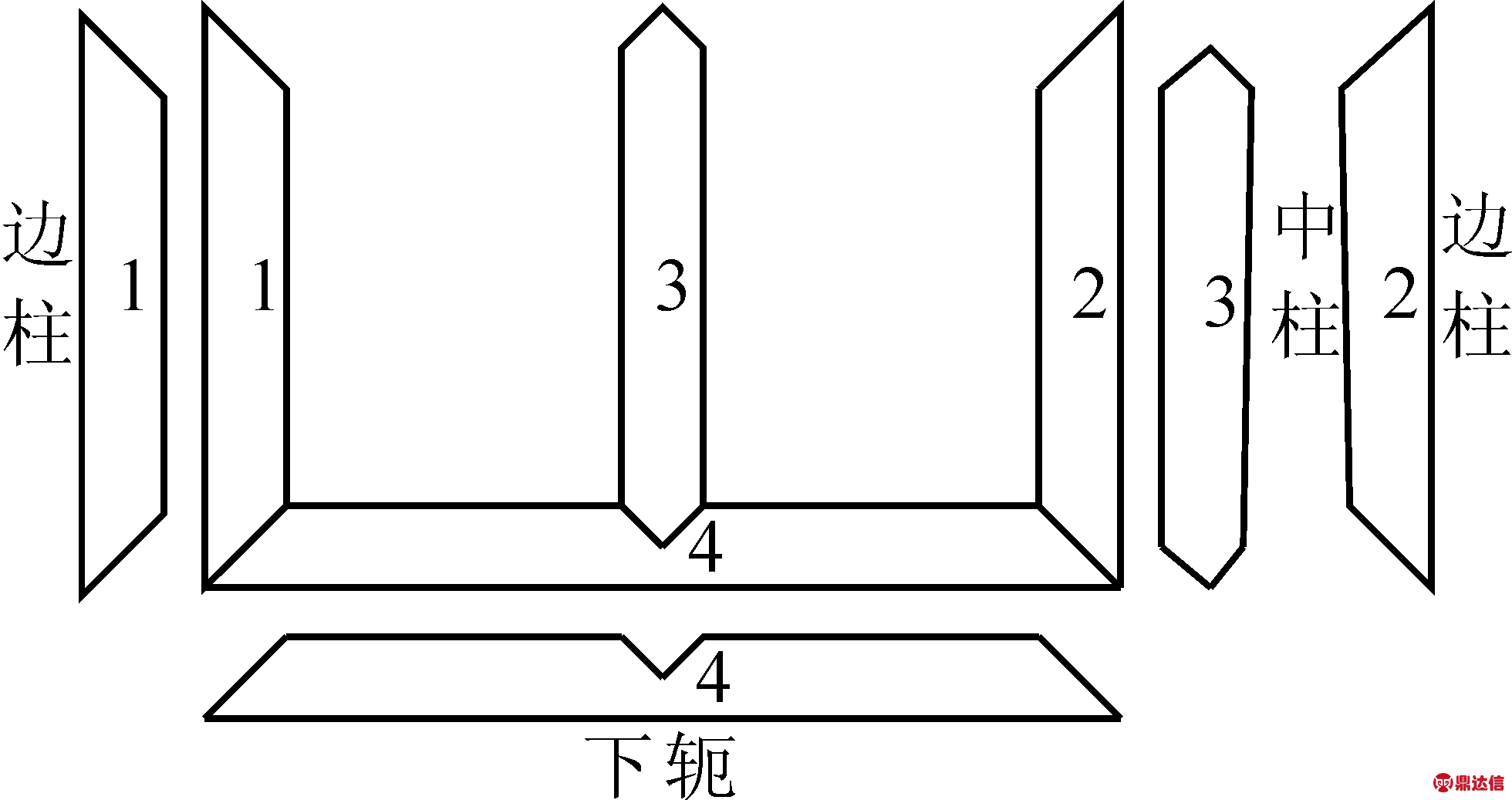
1.2.边柱料片 3.中柱料片 4.下轭料片
图2 硅钢片叠放示意图
叠片步骤:
(1)边柱机械臂和中柱机械臂同时分别抓取边柱料片和中柱料片,叠到“E”形垛的指定位置,轭片机械臂在下轭料片上方位置等待。
(2)边柱机械臂和中柱机械臂运动返回到相应的料片位置,为下轭机械臂提供活动空间,同时准备下一次叠片。
(3)下轭机械臂抓取下轭料片,将料片叠放到“E”形垛指定位置,然后运动返回到下轭料片位置上方,准备下一次叠片。
2.3 叠片机械手的设计
减小机械臂的重量不仅可以减小其惯性,易于控制,而且还可以降低桥架的负载,因此机械臂系统材料采用铝合金。每个机械臂都具有四个自由度,边柱和中柱机械臂包含X、Y、Z三个方向的移动和绕Z轴的旋转,X方向的位移可达1500mm,Z方向的位移可达1200mm,旋转角度可达360°;下轭机械臂包含X、Y、Z三个方向的移动和绕Z轴的旋转,在Y轴的方向可达1500mm,在Z方向的位移可达1200mm,旋转角度的范围是0°-360°。每个机械臂都包含一个真空抓手,用于抓取铁芯片和高精度堆垛。真空抓手机构主要由鱼骨型支架、6排4列真空吸盘、安装在叠片支架上的三套气缸压紧装置及料片厚度检测传感器和视觉相机组成。鱼骨型支架为整个真空抓手的安装支架,采用铝合金制成。6排4列真空吸盘通过真空发生器通断控制实现料片的吸取与放下,中间4排4列呈直线布置,两侧两排呈一定角度布置,与料片斜端边平行。叠片机械手的结构见图3。
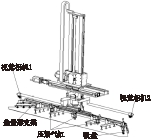
图3 叠片机械手
真空抓手抓取料片有两个难点:第一是硅钢片的厚度只有0.25-0.3mm,机械手抓取硅钢片时,硅钢片容易与其下方的硅钢片发生粘连,导致无法精确叠装;第二是不同类型硅钢片斜边的角度不同,要求机械手能适应不同的硅钢片。针对第一个难点,设计了翘曲式风刀分片机构解决,其分两套布置在真空抓手两端,主要由连片检测传感器、翘曲驱动气缸、多层柔性吸盘及风刀式吹风装置组成。连片检测传感器安装在叠片臂上,料片吸取后与连片检测传感器接近,即可实现是否连片的检测。连片检测传感器选用德国KLASCHKA 公司BDIG系列产品,可通过参数设定检测不同厚度料片的连片,当检测到连片时,两侧翘曲驱动气缸驱动与其连接在一起的多层柔性吸盘向上运动,使料片两端发生翘曲,叠片臂上的其余吸盘不动,保证料片中间静止,同时风刀装置吹气,实现料片的分片。多层柔性吸盘具有较大的柔性,可在料片发生翘曲时适应其翘曲度,保证不损伤料片。针对第二个难点,设计了斜向吸盘偏转装置,其为一气缸驱动的连杆装置,气缸伸缩带动斜向吸盘支架运动完成吸盘的角度调整(见图4)。
当叠片机械手放置料片后,气缸压紧装置压紧料片,防止叠放好的料片发生移动,然后机械手臂上升,气缸压紧装置收回压杆(见图5)。
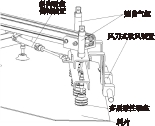
图4 分片机构及吸盘偏转机构

图5 压紧气缸示意图
3 垂直度及窗宽的智能检测方法
在叠片的过程中,需要实时检测铁芯的整体垂直度和铁芯的窗宽,以便及时做出调整保证产品质量。通过安装在各叠片臂上的视觉检测相机结合叠装机械手位置测量光栅尺来进行测量。视觉测量单元主要包括智能相机、LED光源和图像处理计算机。影响视觉测量精度的因素很多,如现场光照环境、机械手重复定位精度、相机分辨率、相机内部参数标定误差和图像算法后处理精度等[5]。
视觉检测单元的主要任务是识别料片的边缘和角点。视觉检测的精度主要由相机分辨率和图像处理算法决定,提高相机分辨率的成本较大,利用软件算法提高检测精度是比较有效经济的方法,对边缘和角点的识别可以应用亚像素的图像处理算法提高边缘的检测精度[6]。亚像素概念是将一个像素点进行细分,从而获得更多的图像像素,常用的细分值为1/2、1/3和1/4[7]。利用亚像素边缘检测算法的精度可达到1/10个像素精度[8],选用UN1401相机,该相机的分辨率为4384×4384,像素距离为0.12mm,因此利用亚像素检测算法其检测精度是0.012mm。
产品整体垂直度测量原理如图6所示。通过两叠片臂上的视觉相机测量边柱及中柱上的特征点与视觉相机的位置关系,再根据光栅尺得知两机械臂的相互位置。由于视觉相机安装在各叠片臂上的位置提前标定,所以可以得知各视觉相机的相互位置,最终实现整体产品不同柱上特征点之间的位置关系测量。图6中两柱间的对角线尺寸a,利用余弦定理可求出边柱1与底轭的夹角,同理,利用该方法可以求出中柱、边柱2与底轭的夹角。
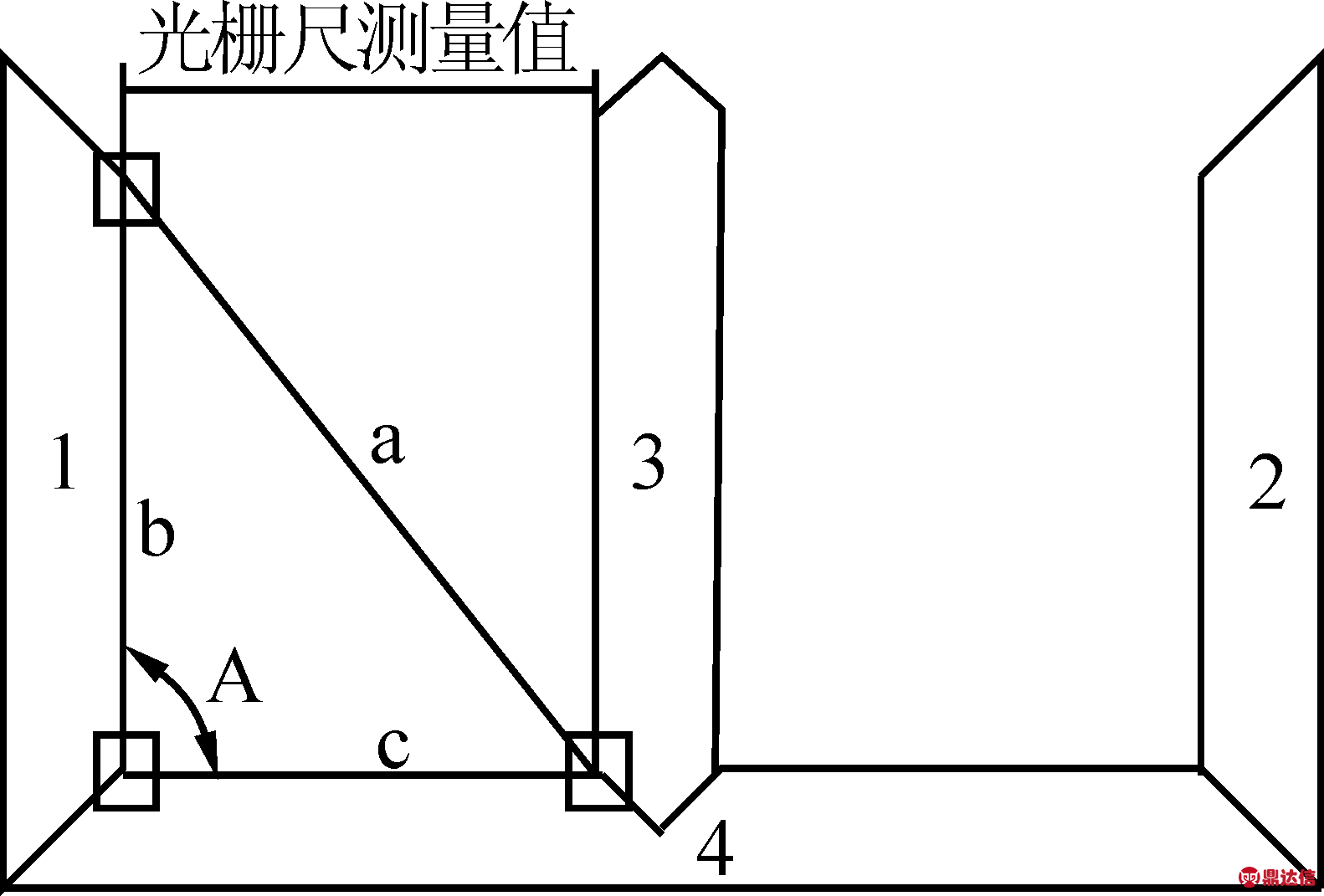
1.2.边柱 3.中柱 4.底轭
图6 产品整体垂直度测量原理
窗宽(MO尺寸)或柱宽检测原理见图7。同样为通过两叠片臂上的视觉相机识别特征点的位置,再根据叠片机械手测量光栅尺得知两视觉相机的相互位置,从而计算得知不同柱特征边之间的距离。
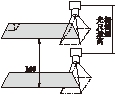
图7 窗宽检测原理
4 结语
为了提高大型变压器叠片工艺的自动化水平,设计了一种直角坐标式自动叠片机器人,叠片速度可达23片/min,高于人工叠片速度19片/min,不仅提高了叠片效率,还节省了人力。
针对抓片过程中的技术难点,创造性地设计了翘曲式风刀分片机构和吸盘偏转机构,解决了硅钢片连片和抓取多种类型硅钢片的问题。运用视觉检测技术,结合光栅尺定位技术准确快速地检测铁芯的整体垂直度和窗宽这两个重要的质量指标。保证了叠片质量,提升了叠片效率,提高了机器人的智能化水平。